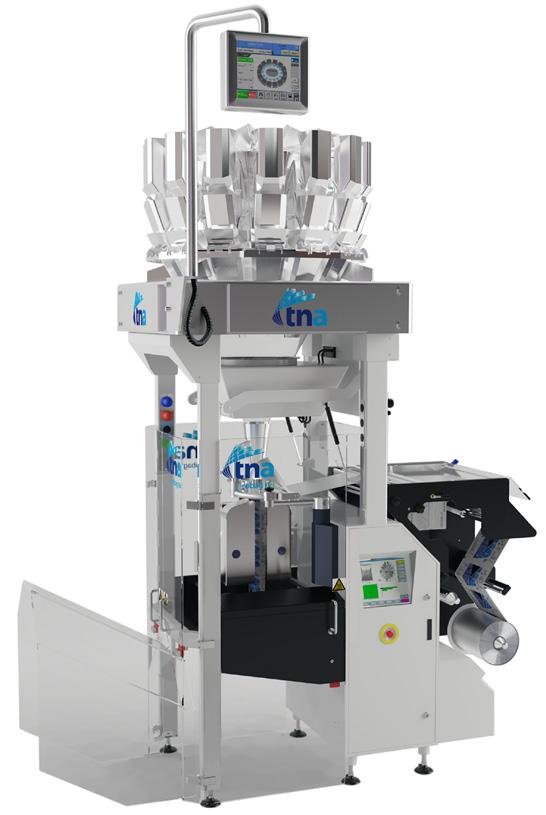
3 minute read
Effectively optimise packaging lines to increase productivity
Technological advances such as the Internet of Things, self-learning software and artificial intelligence are fuelling the development of next- generation packaging equipment.
By Matthew Walters
With the ability to streamline all components of the packaging line, the latest technologies allow operators to control a complete system from a single, intuitive user interface (UI) to promote greater productivity, reliability and serviceability.
As packaging lines become more automated, effective control measures must be implemented to identify and address inefficiencies, maximise overall equipment effectiveness (OEE) and uphold operational profitability.
ACHIEVING 360° VISIBILITY
The gold standard for calculating productivity, OEE, measures the performance (speed and throughput), machine uptime and product quality of a packaging line. A score of 100% means that only high-quality products without defects are bagged as fast as possible, with zero downtime. One of the most promising ways to achieve high OEE is to implement electrical controls integration and reporting technology, such as supervisory control and data acquisition (SCADA) systems.
These solutions provide full visibility of the entire packaging line and deliver comprehensive diagnostics (for each piece of equipment) to a single platform, where the information is logged on a central database to create detailed reports. Easily accessible from a clear and concise human machine interface (HMI), the analysis of these documents can help operators expose inefficiencies, and develop a correction plan.
WORKFORCE VS TECHNOLOGY
Most packaging facilities employ a human workforce alongside automated systems to ensure processes run smoothly, issues are dealt with promptly and maintenance and repair tasks are carried out efficiently to keep production downtime to a minimum.
A good coordination of human labour and technology is crucial to ensure operational viability and profitability. Staff might be occupied with repetitive tasks that could be more accurately performed by a machine. An effective HMI can detect faults much quicker than the human eye and allow operators to react quickly to issues. This not only reduces the margin for human error and improves productivity, but also frees up time for personnel to focus on more challenging projects that require human intervention.

Tna’s Robag 8
REDUCING WASTE EFFECTIVELY
As automation becomes a central part of many packaging lines, products are bagged at unprecedented speeds, increasing the chances of damage or breakage. Often caused by inaccurate control equipment or badly tuned processes, material waste is a significant problem for many plant managers and can affect the entire packaging cycle. If unnoticed, just one fault could cause damage to many goods, resulting in lengthy production breaks and excessive wastage.
With a detailed user requirement specification (URS), control system providers can help identify the required key performance indicators (KPIs) that an individual manufacturing process requires. Once analysed, the URS is then translated into a functional design specification (FDS) that can be used to tighten the process. The result is a much smoother and more reliable product flow that minimises waste and production downtime, contributing to greater OEE.
Innovative equipment elements such as stripper tube closures, product-in-sealdetection (PISD) software and intelligent air-free date coders with built-in verification technology can also be implemented to keep waste to an absolute minimum. The stripper tube closures guarantee a fast and accurate product transfer with minimum waste by ensuring no products are lost by falling through the seal area, while PISD software monitors products in the seal and jaw area and immediately alerts the operator if the seal integrity is compromised.
This allows plant managers to remove bags quickly from the line for inspection, ensuring that each bag meets the highest quality standards and minimising waste. Thanks to real-time image processing, the latest date coder technology can automatically detect print defects. A mismatch between the intended and the captured image will be evaluated on the spot and trigger an alert, so issues can be addressed promptly to reduce waste and downtime.
TAKING SUSTAINABILITY TO THE NEXT LEVEL
With increasing automation comes a rise in energy consumption. While this is inevitable to some extent, leading technologies can help operators significantly lower a packaging line's energy usage and carbon footprint. By implementing power-saving software, the partial and phased shut down, and power-up components of equipment can be automated, which optimises the use of resources — from power to compressed air consumption. This helps plant managers improve economic efficiency, while lowering their operations’environmental impact.
PARTNERING FOR SUCCESS
To maximise productivity and minimise wasteand energy usage, while also upholding the profitability of operations, it is fast becoming essential to implement controls across the packaging cycle. Joining forces with the right turnkey partner can help operators select and install the best-suited system, as well as effectively maintain equipment to support continued production efficiency. The result: consistently high productivity rates, while continuing to work sustainably. •
TNA Solutions – www.tna.com