
2 minute read
Root crops benefit from foreign material detection
Developed in response to specific customer challenges, the Tomra 3A (3A) delivers a new level of foreign material removal.
The sorter is typically used at the entrance to a potato storage shed, where it provides a final clean up after the freshly harvested crop has passed through a mechanical grader and soil removal equipment.
The unit employs an in-flight inspection and ejection process to detect and remove stones, soil clods and other debris from the incoming product. The 3A is designed to operate at high capacity. This is due to the time pressures of a short harvesting season. It gently moves the product without risk of damaging or bruising it.
Jim Frost, product manager at Tomra Food says, ‘In developing this machine, we learnt from working with farmers in this sector and adopted market-leading technologies proven Tomra Food’s new 3A sensor-based sorting machine offers potato growers excellent sorting capabilities, dependability and affordability.
in some of our other sorting applications. This machine gives farmers exactly what they’ve told us they want: greater capacity; green potato removal; no product bruising; robustness and excellent reliability; ease of use; movability; additional data and statistics and lower cost of ownership.’
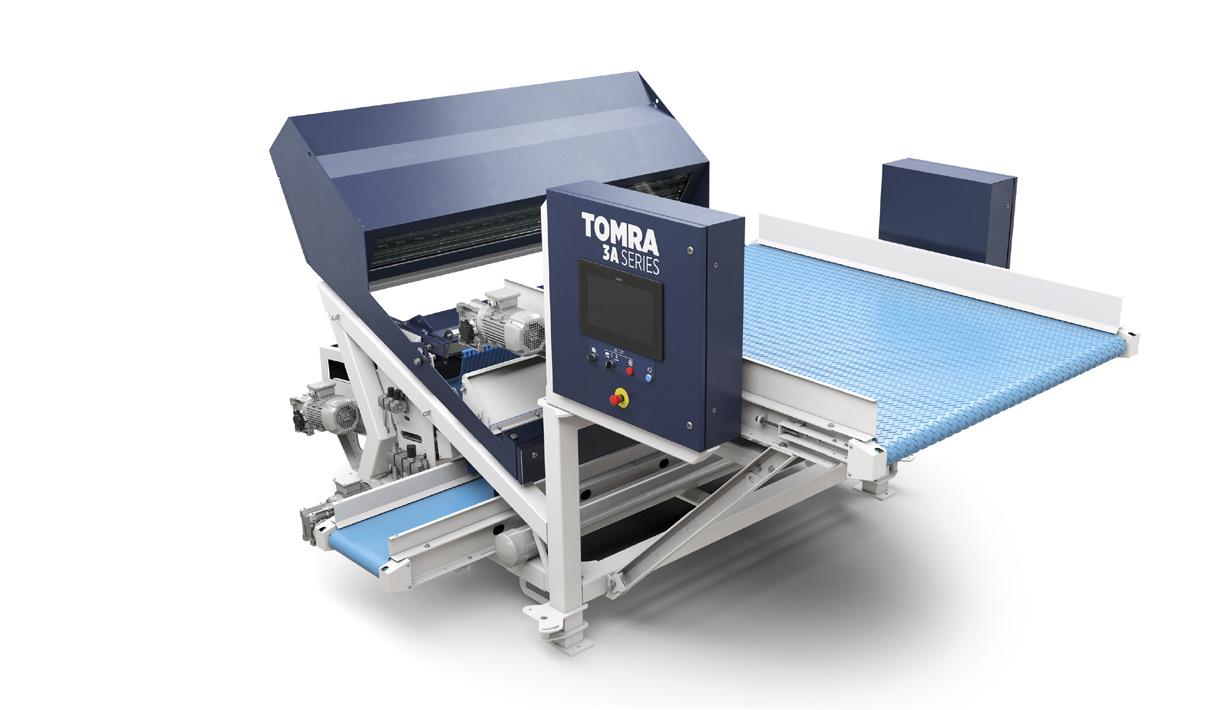
Tomra’s 3A sensor-based sorting machine
SOPHISTICATED IMAGING TECHNOLOGY ON THE UP
The 3A’s sophisticated imaging system, unlike the FPS’s, has colour-detection capabilities to identify unwanted green potatoes. Solid-state, pulsed LED illumination technology with highresolution cameras can distinguish between the crop and foreign material. Amongst the range of signal responses from multiple tailored LED frequencies (some visible and some non-visible infrared), advanced software analysis detects the presence of gross green on sun-exposed potatoes. The sorter is tolerant of overhead lighting effects and eliminates sensitivity to changes in light levels through daylight, evening, and night production.
The optical system has no moving parts when in operation, which improves reliability. The fully-sealed camera enclosure is tolerant of environmental conditions such as rain, wind, dust and heat.
Newly developed Tomra technology such as automated camera alignment and calibration guarantee the sorter’s stability. Optical temperature control ensures consistency of optical signals. This delivers excellent sorter stability and efficiency from the cool of the morning into the heat of the day.
The 3A performs well when pushed to meet the tight deadlines of a short harvesting season, with capacity increased by up to 30 per cent. To accommodate a range of input capacities, the sorter is available in three widths, with a 1 200mm, 1 600mm and 2 400mm infeed conveyance. This enables throughput of up to 45, 65 and 100 tonnes per hour.