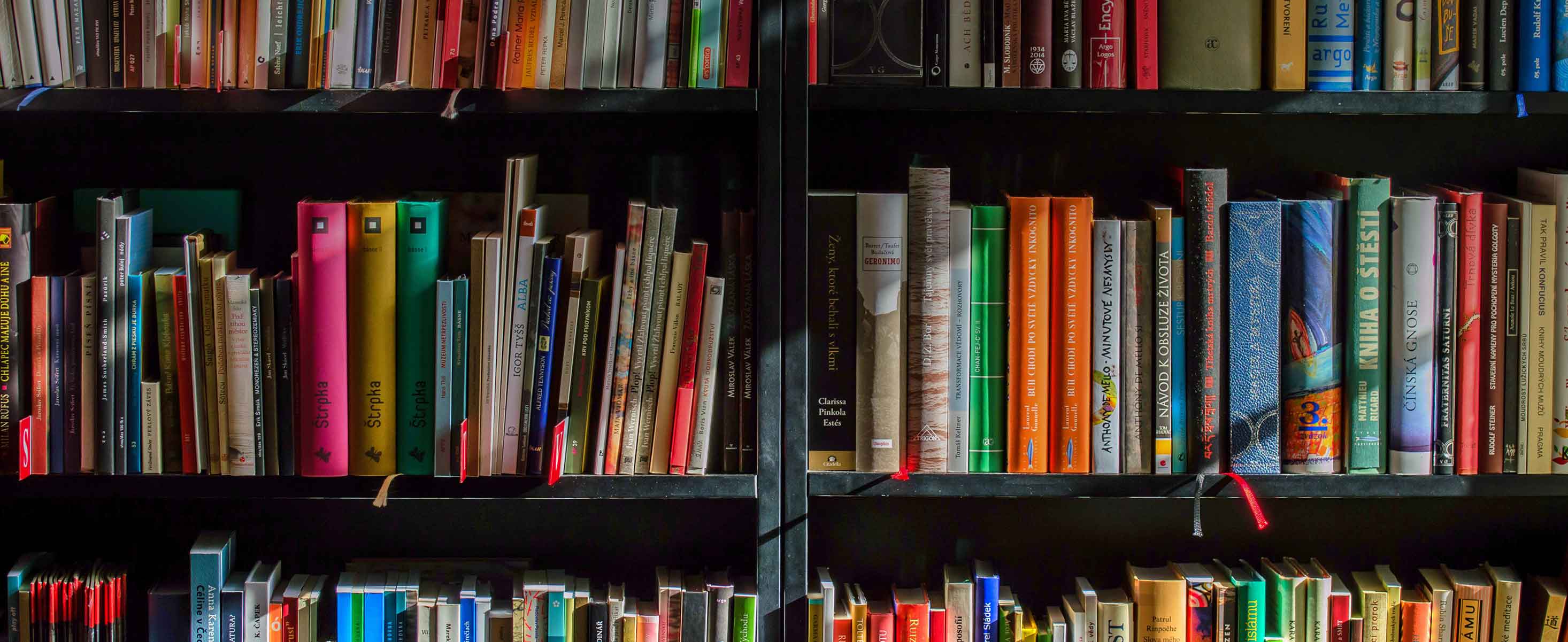
5 minute read
How to compile a Product Information File
In accordance with Regulation 6(1), a PIF should be compiled for each cosmetics product manufactured. The PIF must include all of the necessary particulars relating to the identity, quality, safety to human health and the effects claimed for the product. By Anina van der Walt of Lumen Regulatory Solutions
The cosmetics industry is well aware of the draft regulations of the South African Foodstuffs, Cosmetics and Disinfectants Act,1972 (Act no. 54 of 1972), relating to the Labelling, Advertising, and Composition of Cosmetics, R. 1469.

The draft regulations were published in August 2016 and again redrafted for industry comment in December 2017.Regulation 6(1) states ‘…The ResponsiblePerson, prior to placing a cosmetic product on the South African market and for control purposes, must keep a ProductInformation File (PIF) for each cosmetic…’.
Since local cosmetics legislative promulgation did not occur and enforcement rules are not yet recognised, product owners are either cautiously starting to collect information, or they’re unsure of where to start.The latter is a ‘buried head in the sand approach’ in the hope a PIF will neither be required nor requested by a regulatory authority.
Don't fear the PIF
The process to compile a PIF should not cause trepidation, although it currently does. A review of the legislative aspects followed in various other countries reveals the process to compile a PIF should be clearly structured and planned.
The idea is not to reproduce another technical document using all and sometimes irrelevant information. PIF objectives are to identify the cosmetics product, determine the quality, establish safety to human health and the effects claimed for it to create a dossier applicable to a specific product and formulation type.
The PIF should contain data and information in a format that is practical to maintain throughout the product lifecycle (and after). It should be compiled in such a way that it’s easily reviewed by an evaluator.
PIF structure explained
For illustrative purposes, a PIF should contain the following sections and data.1. It is advised the section on administrative information should contain all the relevant basic company information, such as a contact person, physical address and contact details, including:
• product owner
• responsible person (RP)
• manufacturer and the manufacturerstatement of relevant GMP compliance
• market distributor (where applicable)
• importer (where applicable).
2. Even though some of the product information included in the ProductGeneral Information section may seem obvious to the brand owner, the PIF should also be structurally set out to assist with either a product evaluation or the safety assessment, as required. The following information may be included:
• target population (healthy women, men, adults, children, shaving adults, middle aged woman etc.)
• intended use and general purpose(body lotion, face cream, or shampoo etc.)
• main action (e.g. cleansing, anti wrinkle, or depilating)
• formulation type (an emulsion, cream, butter or oil etc.)
• the type of exposure (Leave-on or rinse-off)
• foreseeable application area (body, face, or hands etc.).
3. The Product Composition (and Manufacturing Method) section should include qualitative and quantitative formulation information. This includes the trade name, INCI name, function and percentage of the ingredients used. This is also a relevant section to indicate the ingredients included in the product comply with legislative requirements where restrictions or permitted use apply. The manufacturing method of the product and process description should also be noted.
4. For packaging (specifications) and labelling it is important to note the following:
• packaging type identification (pump, spray, tube or jar etc.)
• pack size specification
• type of packaging, primary packaging material specification and composition, including technical substances
• identification of technically unavoidable impurities
• information about the packaging material (SDS, TDS and COA)
• for primary packaging, it is beneficial to provide a ‘Food or Pharma Grade’ statement where available or applicable.
5. The physico-chemical and microbiological specifications of raw materials are important. The information in the raw material or ingredient specification section should typically include:
• identification of nano materials where applicable
• physico-chemical ingredient specifications
• supplier information including theSafety Data Sheet (SDS), Certificate of Analysis (COA) and IFRA certificate(where applicable)
• microbiological specification of the raw materials supplied by the manufacturer of the raws
• carcinogenic, mutagenic and Reprotoxic (CMR) information
• identification of raw material impurities.
6. Finished product specifications are dependent on product type and may include colour, odour, appearance, pH, water content, viscosity and density/SG etc. The following information should be included in this section:
6.1 Finished product stability based on stability testing procedures representative of the transport and storage conditions to which final products will be subjected after manufacturing, during distribution and storage and when purchased and used by the consumer. Stability test protocol design depends on product type, ingredient/ final product properties and packaging material. Product stability must include the physico-chemical parameter assessments (accelerated, normal conditions and cyclic temperature stress tests), packaging compatibility and microbial assessments. Stability assessments should include calculations and/or an estimation of period after opening (PAO) or date of minimum durability (DOMD) and expiry date. Experimental and/or theoretical values are applicable. It is also suggested the stability test report should conclude to indicate optimal storage conditions.
6.2 Packaging compatibility applies to the primary packaging. If no ‘food grade statement’ is available, a packaging compatibility test should be performed as well as a migration test on the finished product in its primary packaging, which will be used by the consumer. Possible interactions between the product and packaging material need to be verified. A package leak test and a visual inspection should be performed to determine possible packaging damage or product contamination.
6.3 Test results and the methods used for microbial quality assessments should be included. Microbial testing using the relevant approved ISO or SANS standard methods should include as a minimum and where applicable:
• a preservative efficacy test to ensure system efficacy
• total microbial count to determine possible contamination
• assessment and identification of moulds and yeast or bacterial organisms – various guidance documents are available for this.
7. Data and information on any animal testing performed either on the final product or the ingredients used in the formulation.
8. The evaluation and testing of a cosmetic formulation's intended purpose is to validate cosmetic label claims. This information should serve as substantiation of claims and the efficacy testing should be performed on the finished product. Include reports of clinical testing and if adverse effects were reported during clinical testing.
9. According to draft legislation, Regulation 4, the Cosmetic Product Safety Assessment and Report (CPSR) must be performed by appropriately trained person, such as a cosmetics product safety assessor. As a minimum, the CPSR should contain the following:
• the qualitative and quantitative composition of the physical and chemical characteristics as well as the stability of the product
• microbiological quality
• impurities and trace information about the packaging material
• intended use of the product
• exposure to the cosmetics product
• exposure to the substances
• toxicological profile of the substances
• undesirable and serious undesirable effects
• other information such as label claims, warnings and instructions for use
• assessment conclusion
• the assessor’s credentials and approval.
10.Undesirable effects on human health as per Regulation 4 (4) Safety Cosmetic Product Safety Report, the Undesirable Effects (UE) and Serious Undesirable Effects (SUE) should be recorded in the section on post marketing surveillance. Standard Operating Procedures are recommended for a Complaint Management System and data collection, data analysis and reporting. When sections one to 10 are set out and maintained, a well planned R&D project will ensure the appropriate and relevant product information required to complete the PIF will be obtained. Thorough coordination and proper planning are necessary to ensure the time and funding required from initial concept to finished product are neither increased nor delayed. •
Lumen Regulatory Solutions – anina@lumen.co.za