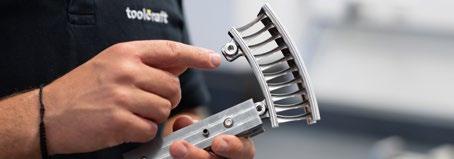
5 minute read
Az MBFZ toolcraft GmbH a ZEISS 3D ManuFACT megoldásával végzi additív gyártási folyamatainak átfogó minőség-ellenőrzését
Az additív gyártás számos vállalatnál ismeretlen terep, de nem így az MBFZ toolcraft GmbH esetében. A dél-németországi Georgensgmündben található vállalat csúcstechnológiás, precíziós alkatrészeket gyárt, egyebek mellett, a repülőgép-, autó-, orvos technológiai és félvezető ipar számára, 2011 óta pedig 3D nyomtatással is készít alkatrészeket. Ez a frissen kialakuló gyártástechnológia igazi kihívás minőségbiztosítási szempontból. A gyártóüzem a ZEISS 3D ManuFACT segítségével küzdi le ezt kihívást, mely jelenleg a piacon egyedülálló megoldást kínál az additív gyártás folyamatos minőségbiztosítására.
Forróság, zaj és olajszag: az ipari termelés elválaszthatatlan része, akár a Jin és Jang. Mégis egészen más légkör fogad a georgensgmündi toolcraft üvegcsarnokában. Bárki lépjen is be ide, biztosan nem hall semmit. És szagokat sem érez. Itt nem az öntött vagy kovácsolt tömbökről fúrják, marják vagy esztergálják le a formát, az additív gyártás pont az ellenkező irányból közelíti meg a folyamatot.
Advertisement
Az üzem tizenkét darab 3D nyomtatójának kis ablakain betekintve, láthatjuk, ahogy a fényes lézernyalábok táncolnak az ostyavékony fémpor felett. Ahova a fénypont esik, a por egy szemvillanásnyira megolvad, majd azonnal újra megszilárdul, és jöhet a következő réteg. A 3D lézeres olvasztás során hajszálvékony rétegek ezreiből állnak össze „kivitelezhetetlen” alkatrészek, melyeket hagyományos megmunkálással képtelenség lenne előállítani. Míg egy évtizeddel ezelőtt mindössze prototípusok és formaterv tanulmányok készültek additív megmunkálással, a repülőgép-turbinák, versenyautók vagy orvosi berendezések gyártói egyre nagyobb mértékben építették be közvetlenül a sorozatgyártásba.
A minőségbiztosítás kihívásai
Mint minden új technológia piaci felbukkanásakor, itt is felmerülnek kérdések. Az egyik ilyen, a minőségbiztosítás. Az egyik monitoron két képet láthatunk, melyek a ZEISS Axio Imager fénymikroszkópjával készültek ötvenszeres nagyításban. A bal oldalon egy jó alkatrész metszete látható. Nem érzékelhetők nagyobb hibák, mindössze kisebb pórusok. A fém egyenletes, homogén szerkezetet alkot. A jobb oldali egy olyan keresztmetszet, ahol levegőzárványok, hegedési hibák mutatkoznak. Itt maga a gyártási folyamat optimális volt, vagyis a hibák az olvadék szilárdulásakor keletkeztek.
„Nagy terhelésnél repedések léphetnek fel”, figyelmeztetett Jens Heyder, aki már tíz éve dolgozik anyagmérnökként a toolcraft anyagvizsgáló laboratóriumában. Kollégáival közösen a felhasznált fémpor szemcseméretének eloszlását vizsgálja. Közreműködik a gyártási folyamat optimalizálásában, céljuk, hogy ne keletkezhessen hiba az alkatrészben az olvadás és a megszilárdulás során. Minden egyes folyamatlépést vizsgálat követ: miután egy alkatrész elhagyja a nyomtatót, a hőkezelés és a végső formára marás után, majd mielőtt az alkatrészt kiküldenék a megrendelőnek.
És egyvalami biztos: ahol alkatrészt vizsgálnak, ott ZEISS logós berendezéssel teszik. Ezek több ponton is megtalálhatók a vállalatnál, például a mérőszobában vagy a gyártótérben: két mikroszkóp (ZEISS Axio Imager és ZEISS Axio Zoom.V16), több koordináta-mérőgép (két ZEISS ACCURA, egy ZEISS CONTURA és egy ZEISS DuraMax), valamint egy optikai 3D szkenner.
Egységes adatok
A toolcraft precíziós alkatrészeket és egységeket szállít be a ZEISS félvezető gyártástechnológiai (SMT) optikáihoz, melyek a félvezetőgyártásban használatos expozíciós berendezésekhez szükségesek. Christoph Hauck, a vállalat egyik ügyvezetője így indokolja, hogy e tényen kívül még miért kizárólag ZEISS méréstechnológiát alkalmaz a vállalat: ez az egyetlen méréstechnológiai beszállító, amely az additív gyártás teljes folyamatláncát átfogja, ezzel biztosítva az adatok teljes körű konzisztenciáját.
Ezt forgalmazza a ZEISS 3D ManuFACT néven. Egyetlen komplett megoldásban egyesíti a ZEISS termékválasztékának elemeit – a pásztázó elektron – és fénymikroszkópoktól a komputertomográfokon és koordináta-mérőgépeken át egészen az optikai 3D szkennerekig – mindezt a ZEISS CALYPSO és ZEISS PiWeb szoftver égisze alatt.
Hauck felel az új piacok, technológiák és ügyfelek felkutatásáért. Ide tartozik, az additív gyártási technológiába vetett bizalom erősítése az ügyfelek körében „hiszen minden új gyártástechnológiát fenntartásokkal fogadnak különösen, amikor a fejlődés ennyire gyors”. 2005 tájékán a technológia minősége „még hagyott kívánni valót”, és csak prototípusok esetében alkalmazták. Manapság már a megrendelőknek leszállított alkatrészeket a repülőgépipar vagy az orvostechnológia szigorú előírásai szerint minősítik, és éppoly működőképesek és tartósak, akár a hagyományos technológiával gyártott darabok.
Feltárt feszültségek
Ugyanakkor, maga az eljárás még bonyolultabbá teszi a minőségellenőrzést. A mérőszobában, a két ZEISS ACCURA berendezés mellett található két régebbi, egyéb gyártmányú koordináta-mérőgép, de ezek nem alkalmasak ilyen összetett lapátgeometriák letapogatására. – A ZEISS lapátmérő szoftvermodulját használjuk ezekhez – mondja Markus Miehling. A minőségbiztosítási vezető a GOM 3D szkennerével nyer gyors áttekintést a lapátcsomag alakjáról.
A szkenner kék fénysugarakat vetít az alkatrészre, a szoftver pedig a visszavert fényből kiszámítja a felületet, és bemutatja a CAD modell által meghatározott névleges felülettől való eltérést. A lézeres olvasztás alatt fellépő folyamatos hevítés és hűtés hatására fellépő feszültségek a fémben az alkatrész vetemedését okozhatják. Nyomást követő hőkezelés oldja ezeket a feszültségeket, azonban nem szünteti meg maradéktalanul.
A minőségbiztosítási folyamat az anyagvizsgáló laboratóriumban kezdődik, ahol speciális maratási eljárásokat dolgoznak ki az egyes anyagok szemcseszerkezetének
vizsgálatára az alkatrészen belül. A mikroszkóp alatt látható struktúra számos tekintetben alapvető eltéréseket mutat az öntött vagy szerszámgéppel megmunkált darabokhoz képest. A túlmelegedés okozta égésfoltok ZEISS Axio Zoom V16 fénymikroszkóppal vizsgálhatók és dokumentálhatók.
Végső tapintó vizsgálat
Ha egy ügyfél előírja minden egyes alkatrész vizsgálatát, azok bekerülnek a minőségbiztosítási terem két ZEISS ACCURA berendezésének egyike alá. Az additív gyártással készült alkatrészek tapintásos mérése szintén speciális felületkezelést kíván. Amikor közvetlenül a nyomtatóból kerülnek ki, bizonyos mértékig még durvák a megszilárdult porszemcsék miatt. Letapogatásos mérésre, ahol a tapintó folyamatosan érintkezik a felülettel, nincs lehetőség. Ehelyett egyedi pontok bemérésével határozzák meg az alkatrész reprezentatív pontjainak helyzetét. Ha az alkatrész jó, bekerül a kötelező felületmegmunkáló folyamatba, amely során a forgácsoló szakemberek forgácsolási technológiákkal alakítják a meneteket, optimalizálják a sugarakat és „finomítják” a felületeket. Ezután már alkalmazható a ZEISS ACCURA berendezés szkennelő-tapintó érzékelője az újabb mérés elvégzésére. A mérőgép gyorsan képes váltani a különböző érzékelők között. Egy optikai vezeték-érzékelő szintén használatra készen várakozik a szenzorcserélő-tárban.
Jóllehet a technológia igazán izgalmas, a toolcraft mégis ragaszkodik egy alapelvhez: kizárólag olyan alkatrészeket gyártanak additív technológiával, melyeknél ez ésszerű. A nagy mennyiségben rendelt, hagyományos megmunkálási folyamatokkal előállítható alkatrészeket mind a mai napig így gyártják.
A ZEISS 3D ManuFACT portfóliójában olyan eszközök is megtalálhatók, melyeket a gyárban most még nem használnak: például pásztázó elektronmikroszkóp vagy komputertomográf. Hogy a toolcraft milyen mérőberendezéseket szerez be a jövőben, azt még nem döntötték el, de az biztos, hogy ZEISS készülékek lesznek.
„A ZEISS az egyetlen méréstechnológiai beszállító, amely az additív gyártás teljes folyamatláncát átfogja, ezzel biztosítva az adatok teljes körű konzisztenciáját.”
Christoph Hauck
Tudjon meg többet a ZEISS 3D ManuFACT teljes körű megoldásairól, látogasson el a https://zeiss.ly/3D_manufact oldalra!