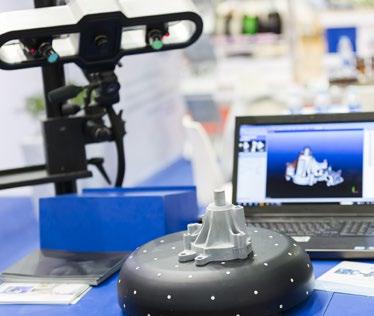
3 minute read
Hogyan segít a szkenner a pontosabb fémipari öntvények létrehozásában ?
A fémipar célja, hogy olyan alkatrészeket állítson elő, amelyek megfelelnek az ügyfelek elvárásainak, és a szükséges tűréshatárokon belül vannak. Ehhez nyers öntvényeket állítanak elő, amelyeket megmunkálnak és validálnak. A maradékanyagok okozta plusz költségek csökkentése érdekében az öntvény méretét megmunkálás előtt ajánlatos alaposan felmérni. Az optikai mérőműszerek, például a hordozható 3D szkennerek, több információt szolgáltatnak a fémfeldolgozó ipar számára, és lehetővé teszik az ellenőrző személyzetnek, hogy több öntvényt gyorsabban mérjenek.
Az öntvények előállítása olyan bonyolult folyamat, amelyben minden szakasz kritikus szerepet játszik az ügyfelek igényeinek megfelelő végső alkatrészek létrehozásában. Így a fémipar hozzájárulása a gyártási folyamathoz elengedhetetlen és nélkülözhetetlen. Olyan nyers öntvényt kell készítenie, amely elegendő anyaggal rendelkezik a megmunkálási folyamathoz, hogy a végső alkatrészek megfeleljenek az ellenőrzési előírásoknak. Ráadásul mindezt úgy kell elérnie, hogy közben minimalizálja az ellenőrzési időt és az elutasított alkatrészekkel járó gyártási költségeket.
Advertisement
Hogyan ellenőrizhető a teljes felületi profil – nem csak egyes pontok – annak biztosítása érdekében, hogy az alkatrészek illeszkedjenek a szükséges tűréshatárokhoz? Hogyan szerezhetők be a szükséges információk ahhoz, hogy az öntvényeket mihamarabb sikeresnek vagy sikertelennek minősítsék, mielőtt több időt és pénzt fektetnének beléjük? Cikkünkben ezekre a kérdésekre keressük a választ, kiemelve az optikai mérések szerepét a folyamatban.
Kihívások
Az alkatrészek előállítása során a nyersöntvények felületét megmunkálják, míg a belső rész érintetlen marad. A megmunkálás optimalizálása és a jobb minőség biztosítása érdekében ezeknek a felületeknek elegendő anyaggal kell rendelkezniük; ellenkező esetben a mechanikus érintkezők hibásak lehetnek, és a tűréshatárok nem teljesülhetnek. Éppen ezért a feldolgozóiparban fontos szerep jut az öntvények megmunkálás előtti és utáni ellenőrzésének is. Megmunkálás előtt kell megtörténnie a méretek ellenőrzésének, hogy az anyagmennyiség elegendő-e az adott felületeken. Megmunkálás után a teljes öntvényről kell átfogó képet készíteni, és ellenőrizni a teljes felületet. A cél természetesen olyan alkatrészek gyártása, amelyek megfelelnek az előírt tűréshatároknak.
Ennek ellenére néhány gyártó egészen odáig elmegy, hogy megvizsgálja magát az öntőformát is, és akár komolyabb, költséges módosításokat is eszközölhet annak érdekében, hogy jobb nyersöntvényeket hozzon létre. Ez viszont egyáltalán nem hatékony módja a minőségjavításnak.
A CAD fájl szerint épített névleges sajtolóforma magas kidolgozottsága azért nem elégséges előfeltétele a tökéletes végeredménynek, mert az öntvények előállításakor több kiszámíthatatlan jelenség is előfordulhat, amire a formának nincs ráhatása – ilyen például a zsugorodás. Mivel a fémfúzió komplex jelenség, a gyártási folyamat nem követ lineáris, pontosan megismételhető utat az öntőformától a végső fázisig. Az ügyfelek tökéletes alkatrészeket kérnek, nem pedig tökéletes öntőformát. Ezért mindig jobb, ha először magát az alkatrészmintát (nem az öntőformákat) vizsgáljuk meg, majd utána ehhez kalibráljuk a szerszámgépet.
A gyártási folyamat összes állomásának minőségi ellenőrzése ambiciózus feladat. Számos előre nem látható jelenséggel kell számolni, amelyeket nehéz ellenőrizni, ez pedig lehetetlenné teszi a végső eredmény előrejelzését. Ha nem megfelelő alkatrészeket szállítanak nagyobb mennyiségben az ügyfelekhez, az pénzügyi és jogi problémákat is felvet. Az ügyfelek saját maguk védelme érdekében sokszor minden fázisról külön minőségi ellenőrzési jelentést követelnek. Az optikai mérőeszközök pedig nagy segítséget nyújthatnak ebben a fémipar számára.
Öntésvizsgálat optikai mérőeszközökkel termelési környezetben
Az optikai mérőeszközökkel a fémipar hordozható, könnyen használható, gyors és hatékony eszközt kap az öntvények mérésére, ellenőrzésére és validálására, a megmunkálás előtt és után is. A hordozhatóság azért fontos, mert így közvetlenül a szerelőüzemben nyílik lehetőség a mintavételre, nincs szükség az alkatrész kiemelésére, szállítására. Ezen hordozható 3D szkennerekre jellemző tulajdonságok miatt az öntvényeket már nem kell a koordináta-mérőberendezésbe (CMM) vinni, így gyakorlatilag idő takarítható meg vele, ami további ellenőrzéseket tesz lehetővé.
További nagy előny, hogy az ilyen eszközök könnyen kezelhetőek, mivel a hordozható 3D szkennerek digitális „Go – No Go” funkciót kínálnak, amely lehetővé teszi a felhasználók számára a méretmérések gyors értékelését és az előírt tűréshatárokon kívüli alkatrészek egyszerű azonosítását. Ily módon könnyen felismerhetők azok az öntvények is, amelyek a megmunkálás előtt nem tartalmaznak elegendő anyagot, valamint azok, amelyek a megmunkálás után nem felelnek meg az előírt tűréshatároknak. Így az ellenőrök még időben tudnak visszajelzést adni arról, hogy az alkatrészek megfelelőek-e, még mielőtt a gyártó további energiát fektetne a megmunkálásukba.
Az optikai technológia hozzájárulhat az ellenőrzési idő csökkentéséhez. A szkennerek kis mérete és egyszerű használhatósága folytán az ellenőrök laptopok vagy táblagépek képernyőjének megtekintésével pillanatok alatt ellenőrizhetik az adott munkafázisban lévő termékeket. Ezért a méretváltozás validálása sokkal gyorsabb, mint a hagyományos mérőeszközöknél, ami hozzájárul az értékes CMM-idő felszabadításához, a szűk keresztmetszet problémáinak megoldásához.
Hegyi Heni NEW technology magazin