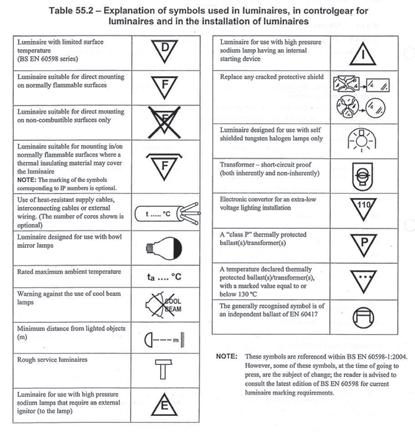
8 minute read
The installation of extra-low voltage tungsten halogen lighting
from Connections - Summer 2016
by NICEIC
Fully charged
Objective
Although a lighting installation designed to operate at extra-low voltage (ELV) may not present a risk of electric shock to the user, as outlined in this article unless correctly installed in accordance with BS 7671 it may not only fail to function properly but, in some cases, it could be a fire hazard. For these reasons, particular requirements for extra-low voltage lighting installations are contained in Section 715 of BS 7671 – Special installations or locations.
This article considers some of the factors that should be taken into account for the installation of a typical ELV tungsten halogen lighting installation, supplied from the secondary output of a transformer positioned remotely from the luminaires. Luminaires supplied by electronic drivers, such as those used for LEDs, are not considered.
For an ELV1 lighting installation the protective measures extra-low voltage provided by SELV or PELV should be used; however, where the luminaires have no provision for the connection of a protective conductor, they should be supplied from a SELV system (Regulation 715.414 refers). It should be noted that a FELV system does not satisfy the safety requirements of SELV or PELV and so is prohibited by Regulation 715.411.7.201. It should be recognised that compared with operation at 230 V, a load operating at ELV will demand a proportionally higher current; for example, a 50 W lamp will demand over 4 A when operating at 12 V. Should a loose or high-resistance termination develop, signifi cant heating (I2 R) will occur, which, if undetected in concealed areas such as loft spaces, may ignite surrounding combustible materials.
To minimise such risks all terminations and connections of an ELV lighting installation should be made in accordance with Regulation 526.2, and except for appropriate systems that use visible bare conductors complying with the requirements of Regulation 715.521.106, they should be suitably enclosed in accordance with Regulation 526.5.
For suspended systems, terminations and connections of conductors should be made using screw terminals or screwless clamping devices complying with BS EN 60998-2-1 or BS EN 60998-2-2 (Regulation 715.521.107 refers).
Fig 1 ELV suspended
lighting system
Voltage drop
Excessive voltage drop can adversely aff ect the performance of an ELV lighting installation, therefore, careful consideration should be given to the rating and number of luminaires supplied and the lengths of circuit supplied from an ELV source.
For compliance with BS 7671, the voltage drop between the transformer and the furthest luminaire should not exceed 5% of the nominal voltage of the ELV installation (Regulation 715.525).
Table 1 shows the minimum values of crosssectional area (copper conductors) permitted by Regulation 715.524.201 for an ELV lighting installation; however, these values may need to be increased to comply with voltage drop.
Table 1: Minimum permitted cross-sectional area for ELV copper conductors
General Flexible cables of a length not exceeding 3 m Suspended flexible cables or insulated conductors (for mechanical reasons) Composite cables consisting of braided tinned copper outer sheath, having a material of high tensile strength inner core 1.5 mm2
1.0 mm2
4.0 mm2
4.0 mm2
Note: Larger conductor sizes may be required in some cases to meet the requirements of Regulation Group 433.1 for co-ordination between conductor and overload protective device.
Lamp selection
Where insertion of a lamp into a particular fi tting is possible, this does not necessarily mean it is a suitable type or of the correct rating. Consideration should be given to the high operating temperatures of tungsten halogen lamps.
Two common types of halogen refl ector lamps are generally interchangeable, but the intense heat produced by the lamps is refl ected very diff erently. The dichroic (cool beam) lamp refl ects visible light forwards but most of the radiated heat backwards, whereas the aluminium lamp refl ects both light and heat forwards.
A consequence of inadvertently inserting a dichroic lamp into a downlighter (both recessed and surface-mounted) is that most of the heat would be projected backwards. Where such a downlighter is recessed, this will project the heat into the ceiling void rather than away from it, creating a risk of fi re. Because of the risk, manufacturers place warnings on fi ttings not suitable for use with cool-beam lamps (refer Fig 2).
Similarly, where heat is refl ected forwards from the lamp, consideration should be given to the proximity of luminaires to combustible materials such as curtains, and its eff ect on the environmental conditions (Regulation 421.1.2 refers). For example, the heat from a number of luminaires targeted into an enclosed space, especially where mounted on or in a low ceiling, could increase the ambient temperature within the location, signifi cantly aff ecting the well-being and productivity of employees. Furthermore, in some cases the operation of mechanical ventilation or air-conditioning units may be required in order to reduce the ambient temperature.
Fig 2 An extract from Chapter 55 of BS 7671
Location of luminaire
The selection and erection of a luminaire should take into account the thermal eff ects of radiant and convected energy on the surroundings (Regulation 559.4.1 refers).
A luminaire may not be suitable for mounting on or in a fl ammable surface, such as a timber panelled ceiling, as the heat produced from the luminaire in normal operation may, over time, cause ignition of the surface. Likewise, a luminaire covered by thermal insulation may be unable to dissipate heat eff ectively and subsequently overheat; for example, insulation installed in the loft spaces of dwellings is commonly laid over the backs of downlighters.
Manufacturers identify whether luminaires are designed to operate in such conditions in accordance with BS EN 60598-1. Table 55.3 of BS 7671 provides details for a range of BS EN 60598-1 symbols applicable to luminaires and control gear.
A luminaire that is unsuitable for a particular location, such as for mounting on a fl ammable surface, should be identifi ed in accordance with BS EN 60598-1. As shown in Fig 2, the 2008 edition of BS EN 60598-1 identifi es this unsuitably using
Fully charged
symbols overmarked with an ‘X’. Further guidance on the impact of an electrical installation on the fi re performance of domestic premises can be found in Best Practice Guide 5, issued by Electrical Safety First.
Issues of compatibility
The operating characteristics of transformers, electronic converters and controls can vary considerably. Therefore, to prevent issues of compatibility, careful consideration should be given to the particular equipment manufacturer’s instructions (Regulation 134.1.1).
Issues relating to compatibility, such as ambient temperature, can cause lamps to fl icker or fl ash, unwanted operation of protective devices, or overheating of equipment.
Among other factors, consideration should be given to the following equipment characteristics: • the maximum VA rating of the transformer (this should not be exceeded), • de-rating factors for control switches (switches should be rated for inductive loads), • transformer voltage regulation (variations in voltage can reduce the lamp life), • the minimum operating load (burden) of the transformer and associated control devices, such as dimmer switches (operation below this minimum value may not only lead to non-function but is likely to cause overheating and lead to component failure), • the in-rush current characteristic of the transformer/controls (such currents can cause unwanted operation of protective devices –nuisance tripping), and • whether lighting controls such as dimmers incorporate soft -start features to limit the magnitude of switch-on current.
Transformers
Transformers should comply with the relevant product standard (Regulation 715.414 refers), and be positioned and mounted to minimise the risk of overheating. Where mounting on a fl ammable surface is required, then a ‘class P’ thermally protected or temperature protected transformer should be used (Regulation 559.6 refers).
For thermal protection under fault conditions Regulation 715.422.106, transformers supplying ELV luminaires should be either: • protected on the primary side by a fail-safe protective device that monitors the power demand of the luminaires (and automatically disconnects the supply in the event of one of a number of specifi ed fault or failure conditions, as detailed in Regulation 715.422.107.2), or • inherently and non-inherently short-circuit proof.
Summary
Luminaires supplied from an ELV source are subject to levels of heat generation that may be transmitted either to the rear of the luminaire (into the ceiling void) or forwards. To minimise the risks associated with ELV tungsten halogen lighting systems, the design and installation of such systems should satisfy the relevant requirements of BS 7671, in particular, due account should be taken of the equipment manufacturer’s instructions with regard to installation and lamp choice (Regulation 134.1.1 refers).
The NICEIC and ELECSA publishing team
Derek Cooney, technical author Derek is a time-served electrician who spent many years electrical contracting on domestic, commercial and industrial installations before becoming a college lecturer. He joined NICEIC as a technical operations engineer in 2009.
Chris Long, technical engineer Chris is a gas professional responsible for providing a technical overview of all gas-related articles and publications. He lives in Hampshire with his family and outside of work is a motorbike nut.
John Clark, senior engineer John started out by serving a fi ve-year apprenticeship before spending some time installing plant in power stations. He then took a degree in electrical and electronic engineering before becoming a lecturer. He now works as senior engineer, helping to develop the learning guides. Tim Benstead, principal technical author Tim worked in contracting and maintenance prior to spending some 16 years as a lecturer. He began working for the Electrical Safety Council in 2006 as a senior engineer.
Mike Burling, senior engineer A former JIB technician, Mike had his own NICEIC-registered electrical contracting business before becoming a college tutor and NVQ assessor. He now works as a senior engineer.
Alex Whitworth, technical illustrator Alex has been a professional designer and illustrator for 15 years, working on projects including fashion advertising, book publishing and even cigar packaging.
Terry Bratley, technical author Terry is a time-served electrician who worked on domestic, commercial and industrial installations. He then taught BTEC and HNC courses before joining Certsure.