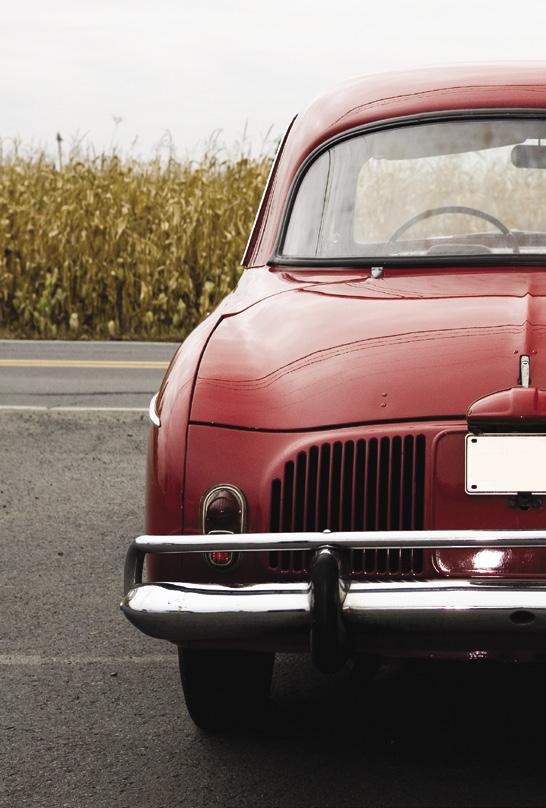
6 minute read
COVER STORY
THE EV REVOLUTION:
EXPLORING THE NEXT WAVE OF SERVICE AND REPAIR - PART ONE
There will be more changes impacting the collision repair and auto service industries over the next four years than in the last four decades combined.
Although there are several things driving the statement above, the proliferation of electric vehicles (EVs) on American roadways is easily the biggest trend that anyone in the auto repair business needs to follow now to prepare for a new level of technology, training and specialization that will surpass anything that’s hit their profession in the past.
Why EVs are Here to Stay
When all is said and done, 2021 will go down in history as the year of EVs. In January, President Biden pledged his support of electric vehicle technologies, announcing plans (via a report in Reuters and other sources) to eventually switch the roughly 650,000 vehicles in the U.S. Government’s fleet to electric. As he noted in a January 25 statement, “The Federal Government […] owns an enormous fleet of vehicles, which we’re going to replace with clean electric vehicles made right here in America, by American workers.”
The start of the new year also saw major news from General Motors (GM), which made headlines by stating it would not only explore EVs but make them the primary focus of production moving forward. As reported by CNBC, the automaker plans to stop making gasoline and dieselpowered vehicles by 2035. GM drove home its commitment to EVs in a statement posted on its consumer-facing website (gm.com/electric-vehicles.html):
GM is on its way to an all-electric future, with a commitment to 30 new global electric vehicles by 2025. We are aggressively going after every aspect of what it takes to put everyone in an EV, because we need millions of EVs on the road to make a meaningful impact toward building a zero-emissions future. GM is positioned to design, engineer and produce EVs for every style and price point, and we are rapidly building a competitive advantage in batteries, software, vehicle integration, manufacturing and customer experience.
Naturally, the push toward EV manufacturing will lead to substantial changes in what technicians traditionally know about vehicle repairs and handling. As just one example, internal combustion engines are comprised of more than 2,000 moving parts, while EVs have fewer than 20. This jaw-dropping comparison came courtesy of insurance industry veteran Jimmy Spears (now head of automotive at Tractable) during his presentation at a recent virtual Collision Industry Conference (CIC).
“We’re going to have a significant amount of [additional] sensors [and] electronics,” he shared. “As we well know, these types of things absolutely increase the total cost of repair […] Not only do we have a sophisticated electronic part that is damaged, we also have a recalibration. We will certainly also have a more educated and probably a more demanding, higher-cost labor source.”
Fellow CIC presenter Bob Augustine (Opus IVS) added that “the OEMs have made a huge shift” over the last 18 to 24 months and are now greatly increasing their production of battery electric vehicles.
“All of the electronics going on board right now are creating a very different world for the collision industry […] It’s no longer a small number of models within a small number of manufacturers. The EV production is now getting ramped up to be mainstream.”
What the Industry Can Do
With EVs destined to hit repair and service facilities at greater volume in the months and years to come, the best and most immediate advice everyone should follow is to go straight to the OEMs for the appropriate procedures, training and equipment information. As longtime industry consultant Mike Anderson (Collision Advice) sees it, there are far too many nuances to an EV repair for a technician to rely on past education and practices to guide them through it.
“I was looking at a Fiat electric vehicle, and the procedure said that when you go to paint that vehicle, you don’t want the battery to have more than a 20 percent charge,” he recalled. “If the vehicle is fully charged, you need to drive it in circles with accessories added to it to bring the charge down. Everybody talks about researching OEM procedures from a collision perspective, but I can absolutely see how we need to be doing it on the refinish side. And that’s not new – that’s something we should have been doing all along.
“In the case of one European auto manufacturer with a lithium battery, you need to check the vehicle’s temperature near the battery area multiple times after repairs to ensure the temperature is maintained,” he added. “If it isn’t, then you have to quarantine the vehicle and call in a specialist from the manufacturer. That’s been around for years in the OEM repair procedures; it’s just that most people haven’t been doing it or thinking about it.”
Look for Part Two of this feature in next month’s AASPMN News.
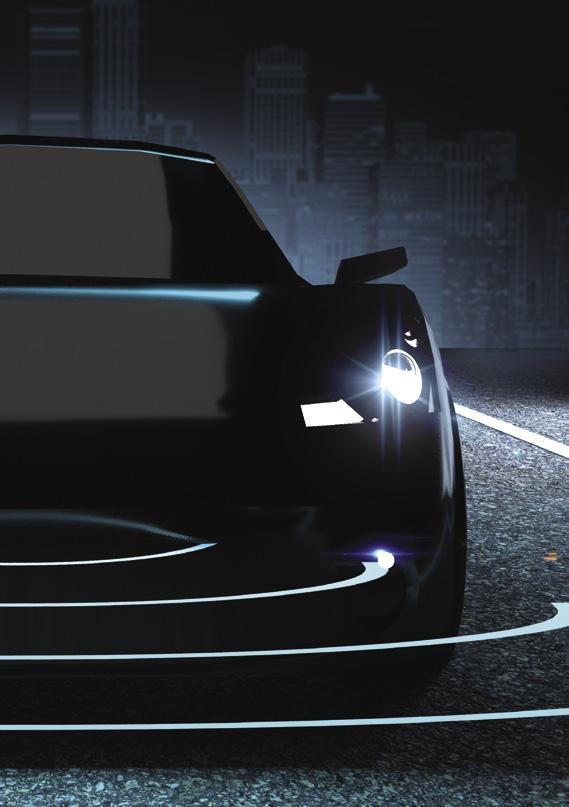
continued from pg. 19 was told to the inspector.
At the end of the inspection, the inspector will hold a closing conference, where findings and potential citations will be reviewed. If you think the inspector got something wrong, discuss it then. This is not the last word on citations – the inspector will propose citations but those have to be reviewed and approved by OSHA supervisors. The inspector will ask how soon you can get a problem corrected. That will become your abatement date, so you want to ask for a generous but reasonable amount of time.
Our basic rules for the inspections: 1. Accompany the inspector. 2. Don’t be unreasonable. Don’t argue. Don’t be belligerent. 3. Don’t hide, don’t cover up, but don’t volunteer. 4. Take good notes and take pictures. 5. Correct what you can fix immediately.
Problems found!
Not all OSHA inspections result in citations. Inspectors do not have quotas. But if you were cited, you’ll receive a letter by certified mail, listing those citations and the process you need to follow. Once you receive that letter, keep track of time. You have deadlines to meet. If you miss the deadlines, fines can go up tenfold.
• You need to post the citations near the hazard, so employees can see them. • You must correct the hazard. • You must file progress reports, telling OSHA it has been fixed. • You may need to pay a penalty. • If you think the citation was wrong, contest it. Even if you admit that you were dead wrong, you can contest the severity, the amount of penalty or the abatement dates.
We usually recommend contesting the citation. OSHA doesn’t get mad if you contest and doing so is likely to result in lowered penalties. The one time we typically advise against contesting citations is when we think the citations were justified and you are offered an expedited informal settlement agreement (EISA). An EISA, offered only for the not-so-bad inspections, reduces your penalty by 30 percent in exchange for you agreeing to not contest the citations.
You will survive
OSHA inspectors are usually pretty nice people – they go into this job because they care about people. Their aim isn’t to intimidate you, but to help you do the right thing and keep employees from harm. By law, they must cite you and fine you if violations are found. They take into consideration if they think you are trying to run a safe operation, if you show you care about your employees’ safety and health and if you’ve made some effort to comply. They also take into consideration the size of your business. Be respectful, pay attention to deadlines and you will survive it. And you’ll probably find it less painful than a sales tax audit.
Check out AASP-MN’s educational resources on this topic, including “How to Prepare for an OSHA Inspection” and “Creating an AWAIR Program for Your Shop,” found at elearning.autoserviceproviders.com.
For more information, contact Carol Keyes at (651) 4819787 or carkey@chess-safety.com.
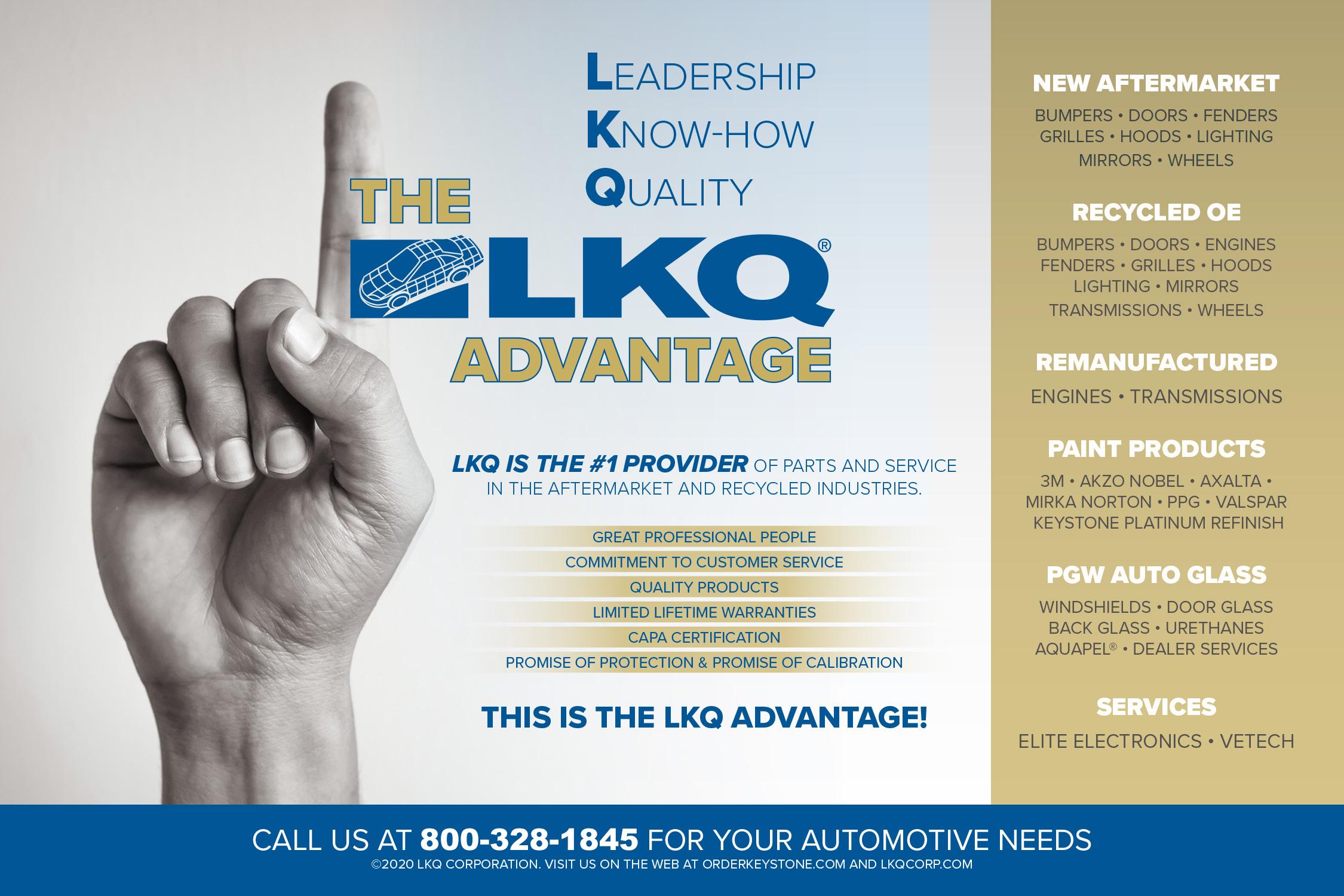