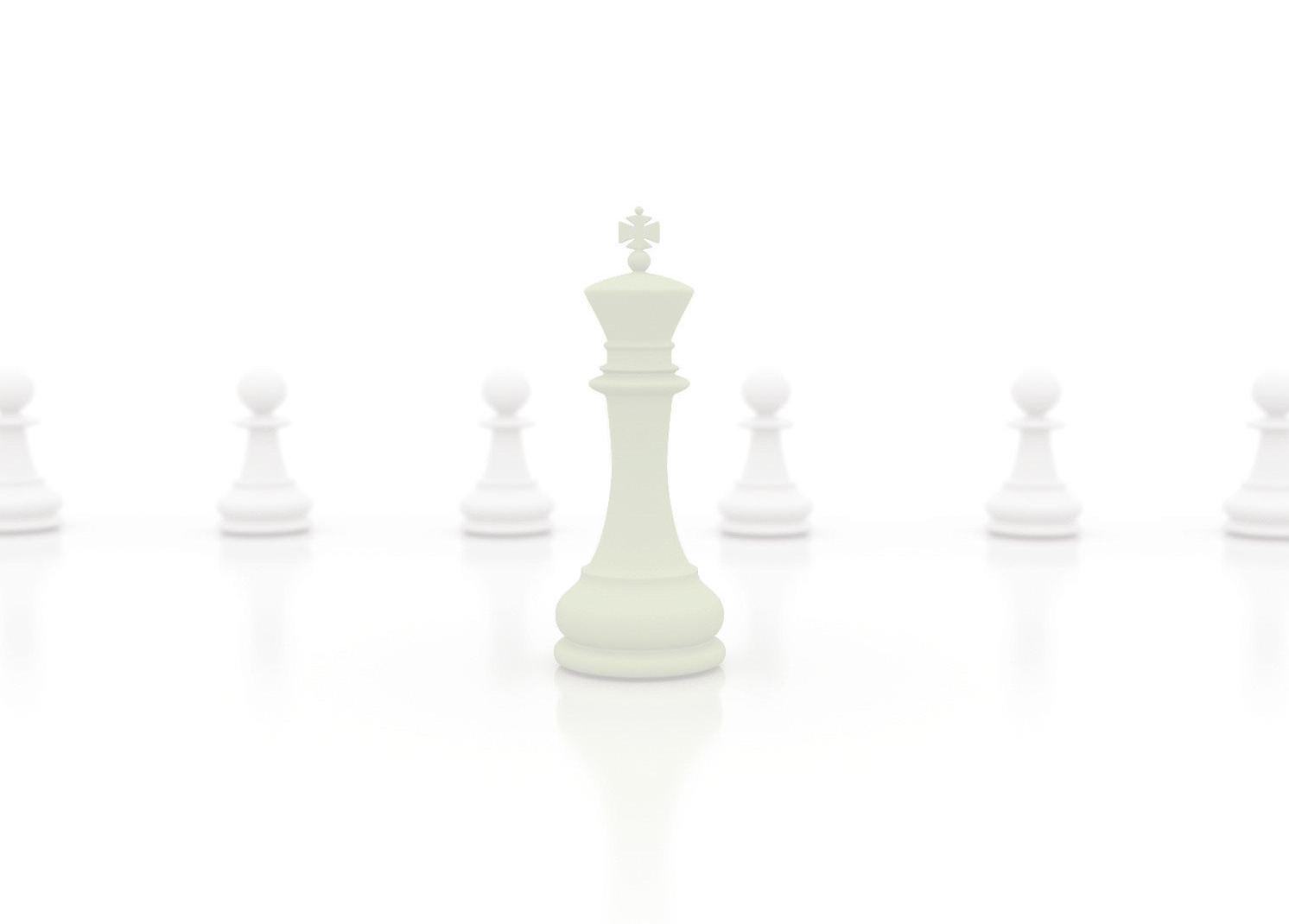
8 minute read
COMPLETE HEALTH , ENVIRONMENTAL & SAFETY SERVICES C.H.E.S.S
The Hierarchy of Controls
by Janet L. Keyes, CIH and Carol A. Keyes, CSP
If you could eliminate a hazard, would you do it? The expected answer is, “Of course I would!” But the real answer is, “It depends.” You weigh the trade-offs. Get rid of all flammable paint, and you eliminate the hazard of paint vapors starting a fire. Eliminate vehicle lifts, and you eliminate the risk of a car falling off a lift. But you can’t refinish cars if you can’t paint, and nonflammable clearcoats are hard to find. Getting rid of vehicle lifts certainly eliminates one potential hazard, but it replaces it with others. If employees need to work under vehicles, they either will try to work in that cramped, dark space under cars or they will use jacks. Are those safer? I don’t think so.
We won’t ask you to eliminate all hazards. That’s futile. A more practical approach is to use the hierarchy of controls. Eliminate the hazard if you can. Substitute – use something similar but safer. Use engineering controls to separate people from the hazard. Change the way work is done – use administrative controls. And if none of those will do the job, resort to requiring
personal protective equipment.
Why is personal protective equipment the last choice? It’s the least effective. It only protects one person,
the person using it. And it only protects if it is used correctly. It often is the most cumbersome to use. And, the most difficult to enforce. Walk into your shop. How many people doing noisy tasks are using hearing protection? If you think they don’t need hearing protection, go talk to them. Do they need to stop what they’re doing to converse? If so, hearing protection was needed. Why aren’t they using it? It’s uncomfortable. It’s too hot. It’s too inconvenient. AASP0720_CHESS.qxp_Layout 1 6/18/20 1:13 PM Page 1 It didn’t seem that loud. See the problems with relying on personal protective equipment? Administrative controls are considered more effective than requiring personal protective equipment. How could you use that to control noise exposure? You could try to limit how long people spend at the noisiest tasks. That’s not very practical. But there are tasks and times when administrative controls are very effective. Frequent breaks or reducing production expectations during hot weather is an administrative control. Where is your air compressor? Is it in a corner of the main shop? Or does it have its own sound-insulated room? If the latter, you’ve applied a very effective engineering control. Choosing quieter tools that have noise control built into them is an engineering control. Dust extraction systems used for sanding and buffing are engineering controls. Spray booths reduce fire hazards and can reduce employee exposure to paints – they count as engineering controls.
Turn your safety stalemate into a checkmate with CHESS, INC
CHESS is your solution for OSHA& MPCAcompliance! Working with the automotive repair industry for over 25 years.
Are you aware you need...
An AWAIR program by July 2020*
Annual Right to Know / Hazard Communication Training A COVID-19 Prevention Plan by July 2020**
*By July 2020, automotive repair facilities must have A Workplace Accident and Injury Reduction (AWAIR) program **Essential businesses must have a written COVID-19 Prevention Plan
We Can Help
Contact us today for help with your shop’s safety, health and environmental needs. (651) 481-9787 chess@chess-safety.com www.chess-safety.com
If you can substitute a less hazardous chemical or a less hazardous way of doing a task, you reduce the risk to employees. Using a vehicle lift is a good substitute for relying on jacks and jack stands and chocking wheels. The lift must be in good condition, have working safety latches and be used correctly. Given that, it is less likely to drop a car onto an employee’s head than some poorly placed hydraulic jacks. Changing to waterborne base coats is another example of substitution. The waterborne paints are not free from hazards, but they greatly reduce the fire and health risks.
Elimination is the most effective control measure, but the hardest one to do. Do you need to use that chemical at all? Can you stop doing that task?
Do you have a sandblaster in your shop? How can we use the hierarchy of controls with that?
You could use personal protective equipment to protect against the noise, the very high dust levels and the particulates flying around. The only type of protection OSHA allows for abrasive blasting is a type CE airline respirator – a helmet connected to a clean air supply. We’ve never seen that type of respirator in auto shops. The hood we often see does not provide enough protection against the dust levels.
You probably limit how much time is spent blasting. That can be an effective control – if you aren’t using silica or coal slag (the black products). Coal slag contains a trace amount of beryllium, which can cause a progressive and disabling lung disease. Dust levels can be so high during blasting that only four minutes of blasting could result in overexposure to beryllium. Less than a minute can cause overexposure to silica. This administrative control may not be the best option.
Instead of blasting out in the open, you could change the type of equipment. Cabinet blasters contain and capture the dust. As long as the cabinet is maintained in good condition (an administrative control!) and used with a dust collection system, your employee can blast away without eye protection, without respiratory protection and without fear of being overexposed. If you want to keep doing a lot of blasting, you could switch to wet blasting, using pressurized water, with or without blasting media mixed in. The water isn’t enough to create puddles, but it is effective at keeping dust levels down. You could substitute a different blasting media than silica sand or coal slag. This is one of the easiest control measures to implement. Silica sand and coal slag are the cheapest abrasives, but unless you’re doing a lot of blasting, the cost difference is insignificant - and a lot less than the cost of lung damage.
Maybe you can eliminate blasting altogether. Grinding off rust has its own hazards, but it isn’t as noisy as blasting and doesn’t create the same lung hazard. Many shops have figured out how to avoid this task completely.
Abrasive blasting is just one example of using the hierarchy of controls. You can probably come up with more. Are you using a very corrosive wheel cleaner? Could you switch to something that is not as nasty? Can you encourage employees to buy quieter tools? That could reduce the need for hearing protection. Make personal protective equipment your last line of defense when all the others aren’t quite enough. Don’t make it your first choice.


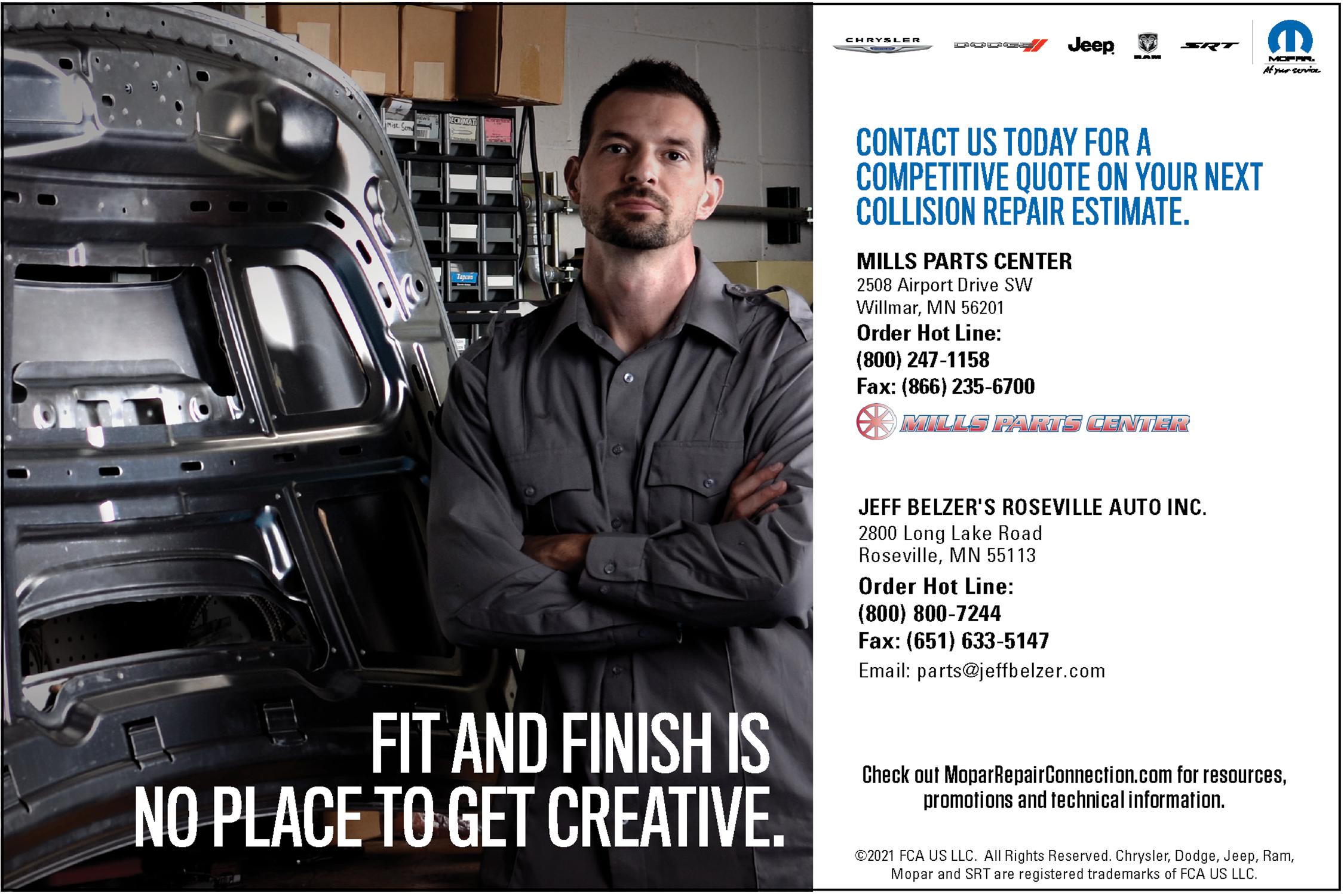
continued from pg. 4 excellence in all that we do. We apply best practices, meet high standards and take pride in our work.
As we now return to “post pandemic” normalcy in our society and our businesses, I wish you all the best in everyday life and business success in future months and years.
released 2022 Lang Aftermarket Annual for an analyses of consumer generational differences that are shaping eCommerce, o2o Auto Repair, Mobile Repair and other key aftermarket areas.
Auto Parts Store Losses & COVID-19
The total count of Auto Parts Stores has changed over the past 10 years, with dramatic shifts in the mix of Jobbers and Retail Auto Parts Stores. Six Major Takeaways: • Two major types of Auto Parts Stores supply the car and light truck aftermarket: Jobbers and Retail Auto Parts Stores. • The mix of Auto Parts Stores (Jobbers and Retail Auto Parts Stores) has changed dramatically since 2010. • The Jobber population fell by approximately 600 between 2010 and 2019. At the same time, Retail Auto Parts Stores increased their number by more than 1,750. • Despite the decline in Jobber outlets, the number of Auto Parts Stores nationwide (Jobbers and Retail Auto Parts Stores) increased by approximately 1,150 between 2010 and 2019. • COVID-19 prompted the closing last year of over three times more Jobber stores than Retail Auto Parts Stores. This reflected differences in DIFM and DIY business volume and the impact on the respective performances of these two groups of Auto Parts Stores during a year when DIFM and DIY annual sales moved violently in opposite directions. • Lang Marketing projects that Retail Auto Parts Stores will climb to 55 percent of the total Auto Parts Store population by 2022, with Jobbers falling to a 45 percent outlet share.
NATIONAL NEWS
continued from pg. 10 continued from pg. 6
The Doctrine of Respondeat Superior applies in the employeremployee relationship just as it did in the franchisor-franchisee relationship in the Washington case.
The underlying message is that shops are well advised to carefully monitor and update staff knowledge of vehicle conditions as part of your inspection program. It is also likely that any customer whose vehicle enters your shop for repair might reasonably expect you to notice and inform them of any flaws which could create a safety issue when they take their vehicle back out on the road.
This also begs the question of whether repair shops should have customers sign off on a disclaimer verifying that the shop’s repair work was focused on a very specific set of mechanical or collision repairs and that the shop was specifically asked to complete repairs only to the extent requested and authorized by the vehicle owner.
We have worked with AASP-MN in the past to prepare such disclaimers. We will be reviewing this issue with individual members in the coming weeks to determine if there is merit for the association to establish some parameters/disclaimers for inspection procedures.
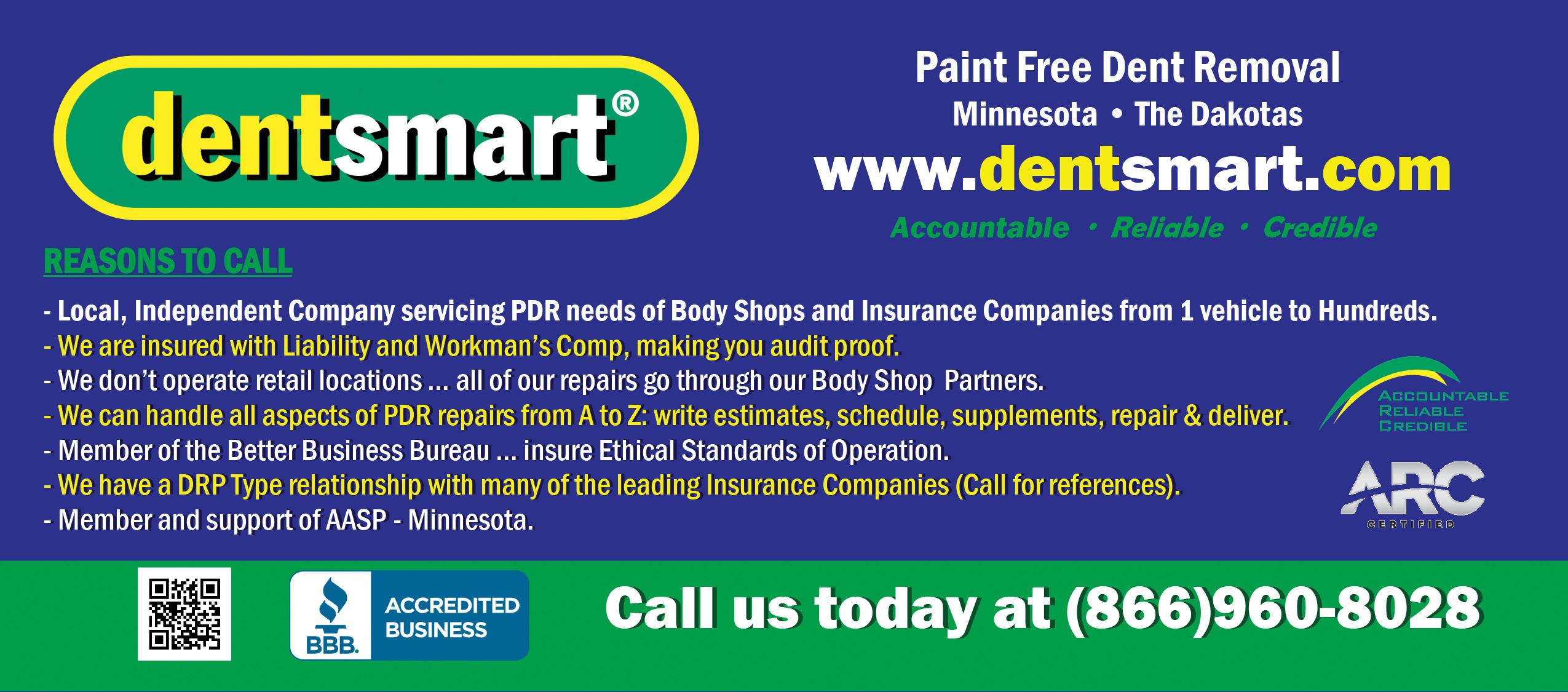