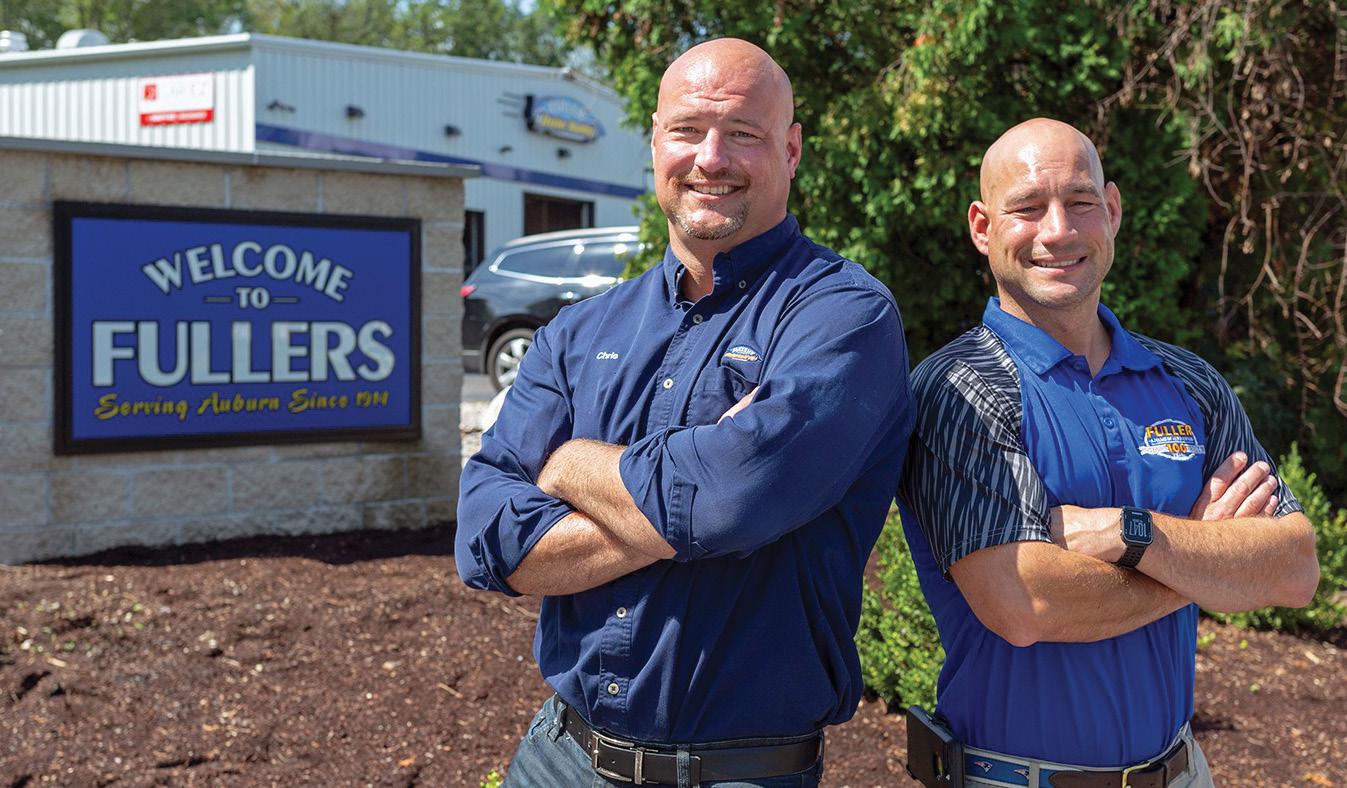
6 minute read
Fuller’s Collision Center, Auburn
The Fuller name has been a go-to in the Massachusetts automotive world for more than a century. Josh Fuller is a fourthgeneration member of a family that has mastered the art of servicing customers in the areas of collision repair, mechanical and towing in the Auburn and Worcester areas.
“We’ve been a name in auto repair since 1914 since my greatgrandfather,” says Josh who owns and operates Fuller’s Collision Center in Auburn. “We are very thankful that our customers have created a great history of needing our service over the years.”
Just about every aspect of automotive repair has been handled by the Fullers over the past century. His father, Richard, dedicated his time to his towing operation, rust proofing business and auto repair. He fondly remembers his father and grandfather going out of their way to help others. His grandfather always went above and beyond for customers like the time he loaned his own vehicle to a police officer who crashed his police cruiser until it could be fixed. Josh has many memories of his dad working around the clock to serve customers.
“My dad towed vehicles 24/7 when I was a kid,” he recalls. “He’d wake up at all hours of the night to tow vehicles, and then during the day hours, he’d be at the shop solving automobile problems. Solving problems and the entrepreneurial spirit are well alive and full in the Fuller blood.”
That entrepreneurial spirit is what led Josh into the family business.
“I didn’t grow up around cars or work for my father when I was young,” he shares. “I actually didn’t know much about what he did outside of knowing he towed vehicles. I was never forced into the business. I just followed the entrepreneur route at a young age. I must have had about six jobs in high school, doing things like landscaping, shoveling walks and retail.
“I studied finance in college and worked in corporate accounting at Liberty Mutual for two years. Then I chose to come back into the family business,” he adds. “The drive to serve people is what drew me back.
It’s what I grew up around.”
Josh joined his father in 2003 and officially took the reins of the business in 2012.
He operates the collision repair center, while his brother, Chris, operates Fuller’s Auto and Tire Center, which mostly deals with mechanical repairs, located right next door. Josh works very closely with their sister, Kerry Cunningham, who serves as his OEM compliance manager and also handles the marketing and community advocacy for the Fuller brand. The operation continues to grow as they recently opened ADAS Diagnostic Solutions in Worcester.
“ADAS technology is growing, and our team chose to be one of the first shops in the area to focus on calibrations,” Josh explains. “They started out small and have now expanded to operating in a full retail business where 50 percent of the calibrations they perform come from other body shops.”
Keeping up with training and technology is key to the success of the Fuller brand. On top of training with I-CAR, the team goes above and beyond what they can learn and explore. Every employee is required to take at least two professional training classes, such as OEM or specific tool training related to their area of expertise, annually.
Josh believes it’s the people on their team that helps make the business stand out as a success. Their leadership team members in particular have been on board over 12 years. Working and growing together as they have all gone through marriages and having children, all around the same time, has developed a strong bond. Josh feels fortunate to have them on board. The Fullers strive to drive a stable and consistent culture where people can grow both professionally and personally.
In 2013, Josh took his industry involvement even further by joining AASP/MA as a member of its Board.
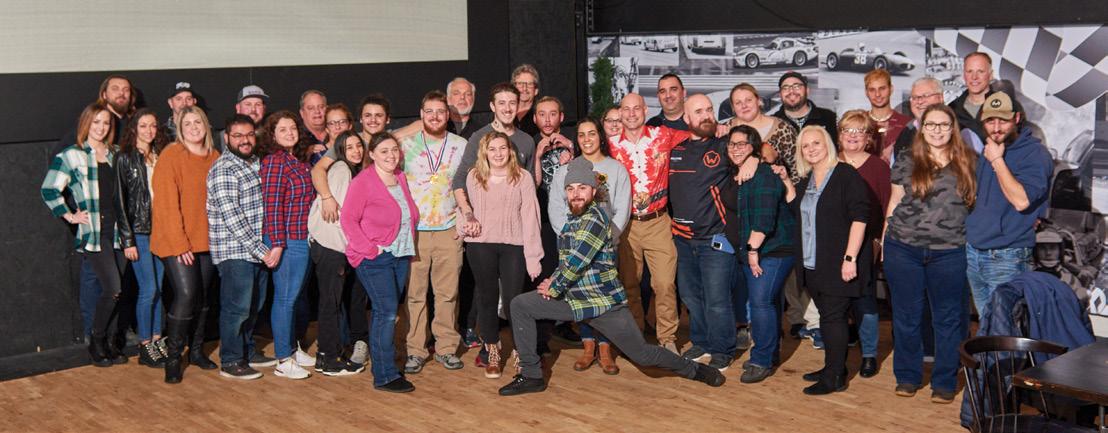
“It’s great to be involved and help drive the direction of our industry and our state. We’ve had a lot of challenges and wins too.”
Josh spent a lot of time behind the scenes as a Board member playing an active role in helping to enforce the goals of the Alliance, including growing the Vendor Affinity Program as chairman, as well as contributing toward the association’s legislative efforts.
A father to three children (ages 11, 10 and six), Josh is very active in their activities which demands a lot of his available time outside of running his business. As a result, he has taken a step back from the AASP/MA Board, though he remains an active member and maintains a passion for protecting and educating consumers while working to improve the industry for all.
“It’s about creating awareness, not only within the industry, but with consumers about what we bring to the industry and how important we are as service providers and communicating some of the challenges we face.
by Alana Quartuccio
“We have a sign in our lobby that depicts the hourly labor rates of similar area service providers, such as electricians, mechanics and lawn mower repairers, along with our labor rate and information on how some insurance companies are creating challenges and what some of their tactics are. Once people look at it, they realize it’s no different than the health insurance industry. We work to serve the consumer and fix their cars correctly to OEM standards, and we deserve to get paid to do so. That’s the challenge. How do you align performance with compensation to be able to pay workers – the tradesman and craftsman – something competitive when they can go out into other fields? We work on complex computers on wheels with a lot of mechanical devices, and they are expected to be repaired to pre-accident condition, yet the compensation isn’t even close to being aligned with what it should be.”
Despite those challenges, the thing Josh loves most about his work in collision repair is serving people.
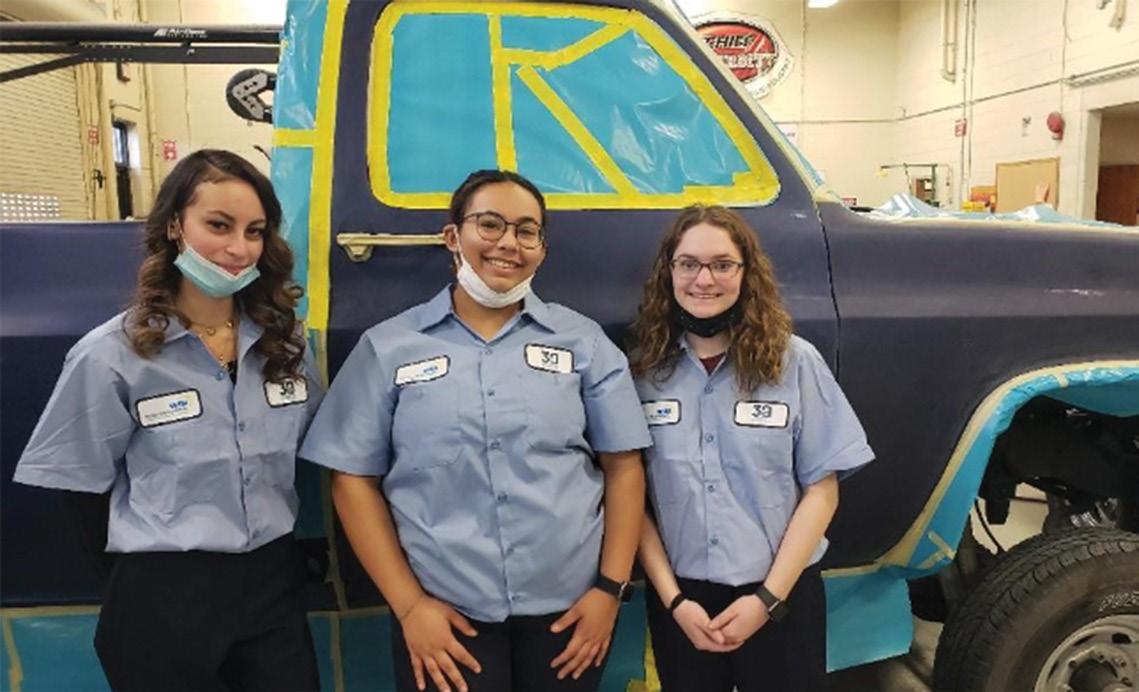
“We are assisting people in navigating through a difficult time. Getting into an automobile accident is a traumatizing experience, and the repair experience soon thereafter is even more complex. We help them navigate through the challenging insurance process and ensure that their vehicle is returned to manufacturer repair specifications and all ADAS systems have been calibrated correctly. Being an advocate for our customer is rewarding.”
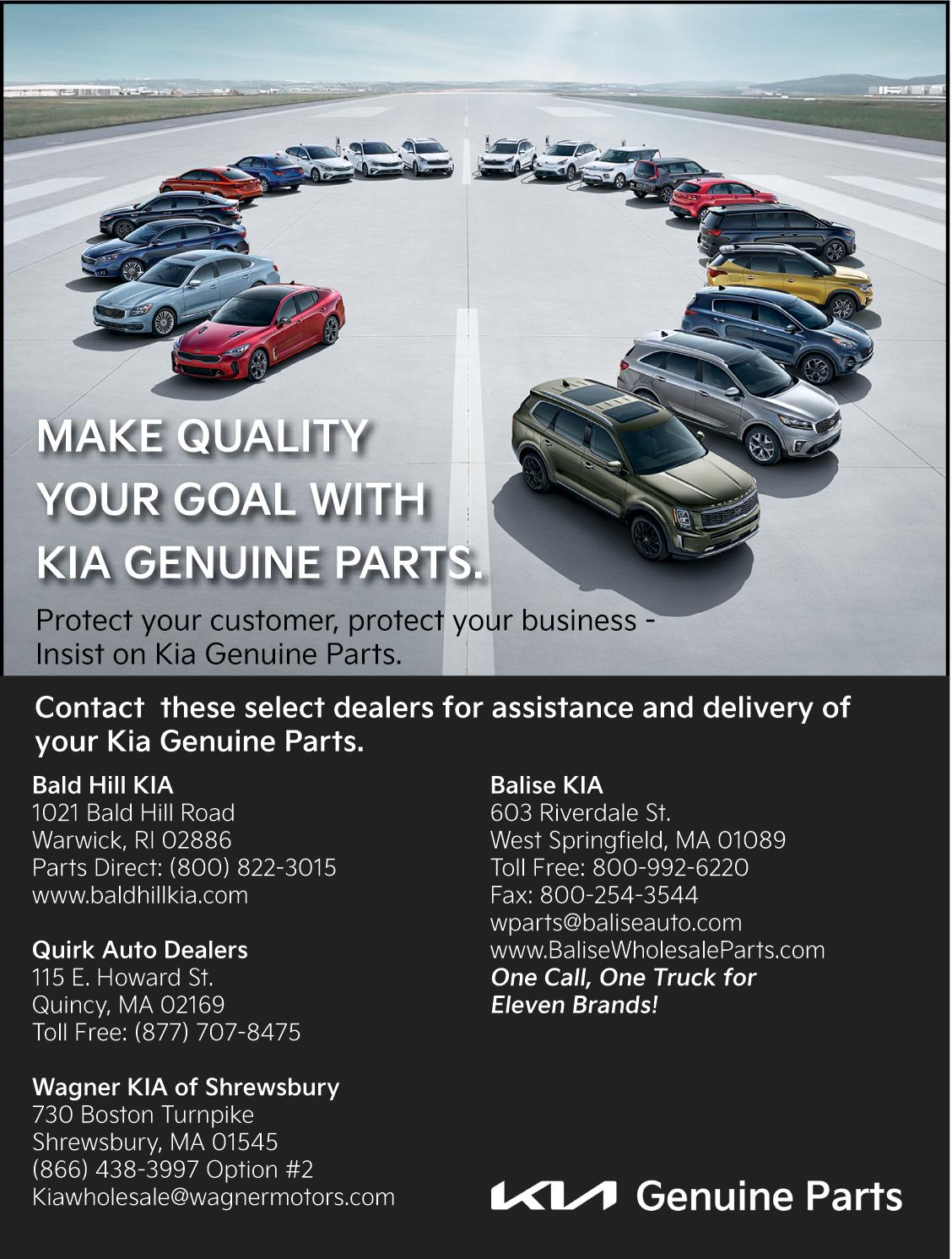
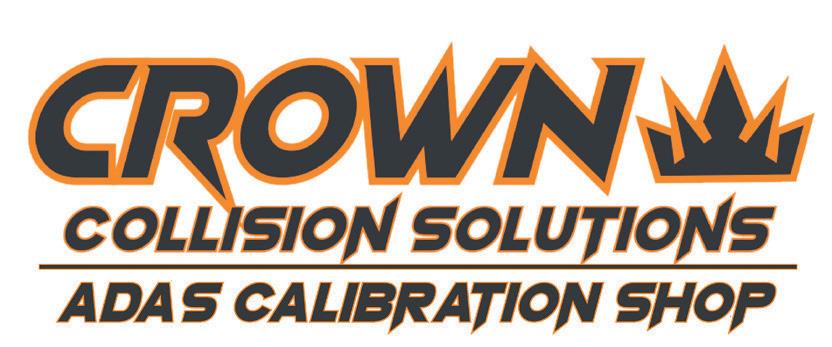
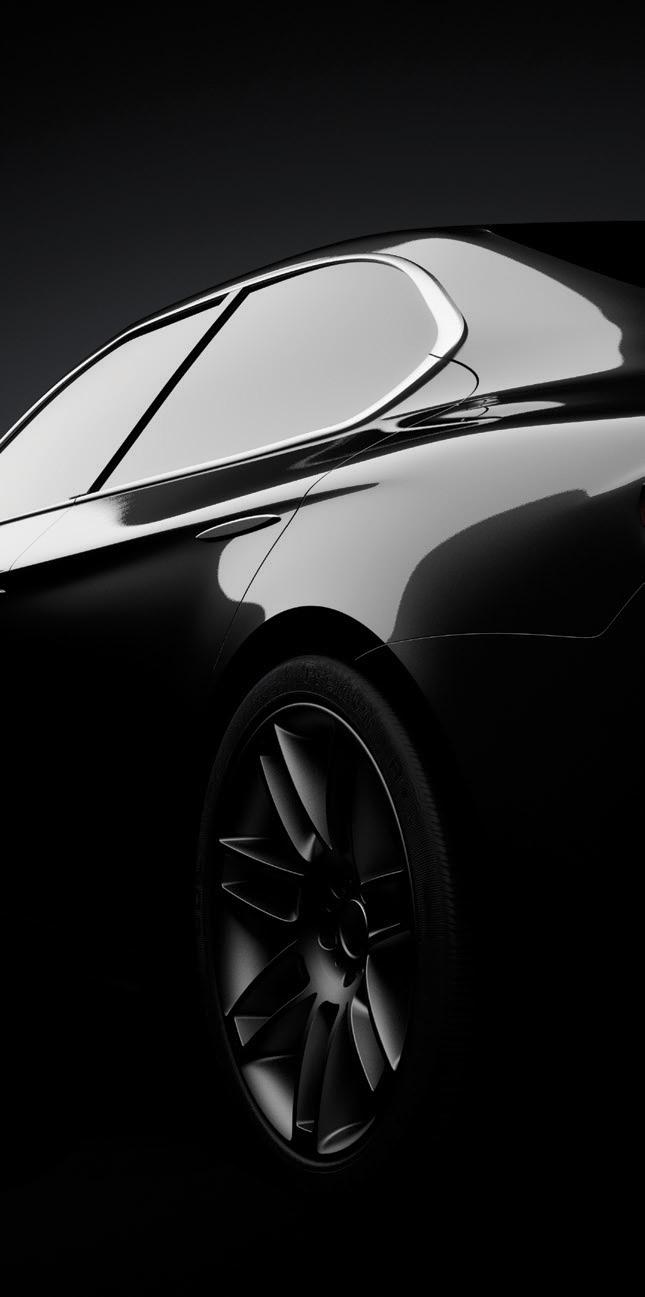
In a state where the labor reimbursement rate is the lowest in the country – despite contending with one of the highest costs of living – many shops have found that simply educating their customers about the egregious under-indemnification issues that run rampant amongst insurance companies allows them to collect a copay to get reimbursed for the hard work exerted into safely and properly restoring vehicles to their pre-accident condition.
It’s not surprising that shops were taken aback at allegations that, by doing so, they might be behaving illegally and could potentially lose their collision shop registration!
That’s exactly what happened near the end of 2022 when an uproar arose among registered collision repair shops throughout the Commonwealth who felt threatened by an email circulated via the Division of Standards (DOS). With a subject line of Motor Vehicle Repair Shops and Motor Vehicle Glass Repair Shops Registered with the Division of Standards, the email cautioned shops about communications “with customers or potential customers regarding the amount of compensation, if any, that claimants may expect to receive from insurers.”
Specifically, the DOS Notice asserted, “Some Repair Shops have suggested to customers or potential customers that if a customer pays the Repair Shop the difference between the Repair that may have been misstated in the Notice and clarifying issues of law addressed in the Notice.”
Castleman specifically identified that it is legal for a shop to inform customers that they may request reimbursement for copays, that customers may legally request those amounts and that insurers may be required to pay or reimburse the consumer “for all or part the difference between what their insurer has paid or allowed and what their repair shop is charging and/or that the customer has agreed to or paid.”
After reviewing three documents (sent by three consumers to three different insurance companies requesting reimbursement for repair work performed by ONE shop) provided as evidence of the allegations, Castleman found “no evidence whatsoever that the repair shop is suggesting that ‘insurers must reimburse or pay to claimants all of the amount of money claimants pay’ to the shop. Nor is there any evidence whatsoever, that the shop has suggested that a ‘claimant is entitled to compensation’ for the difference between the shop’s charges and the amount that their insurer is paying for the work. Nor is there any indication [...] of ANY other repair shop having made ANY representations to ANY insured that their insurer must make additional payment to them, or that they are entitled to any additional payment.”
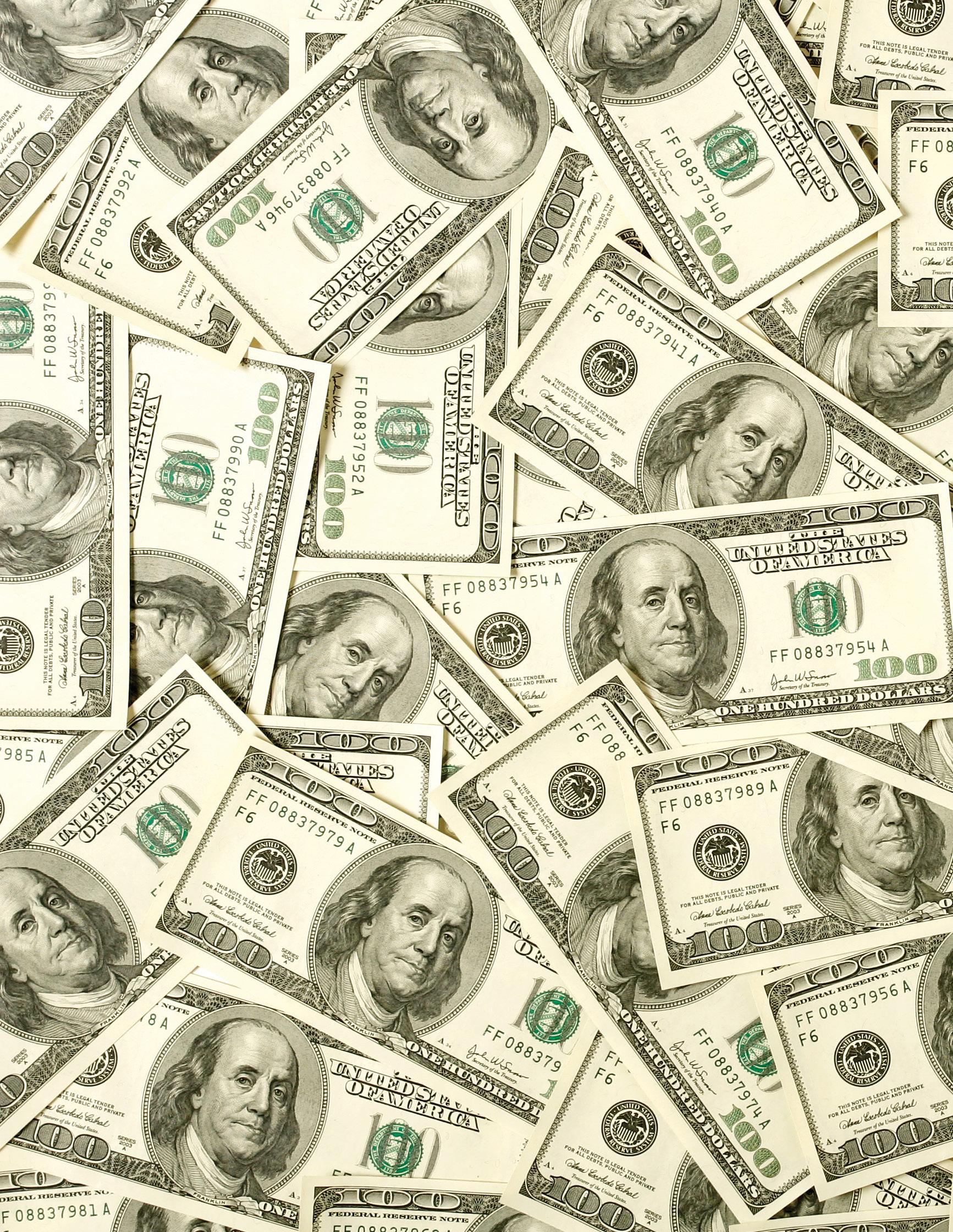