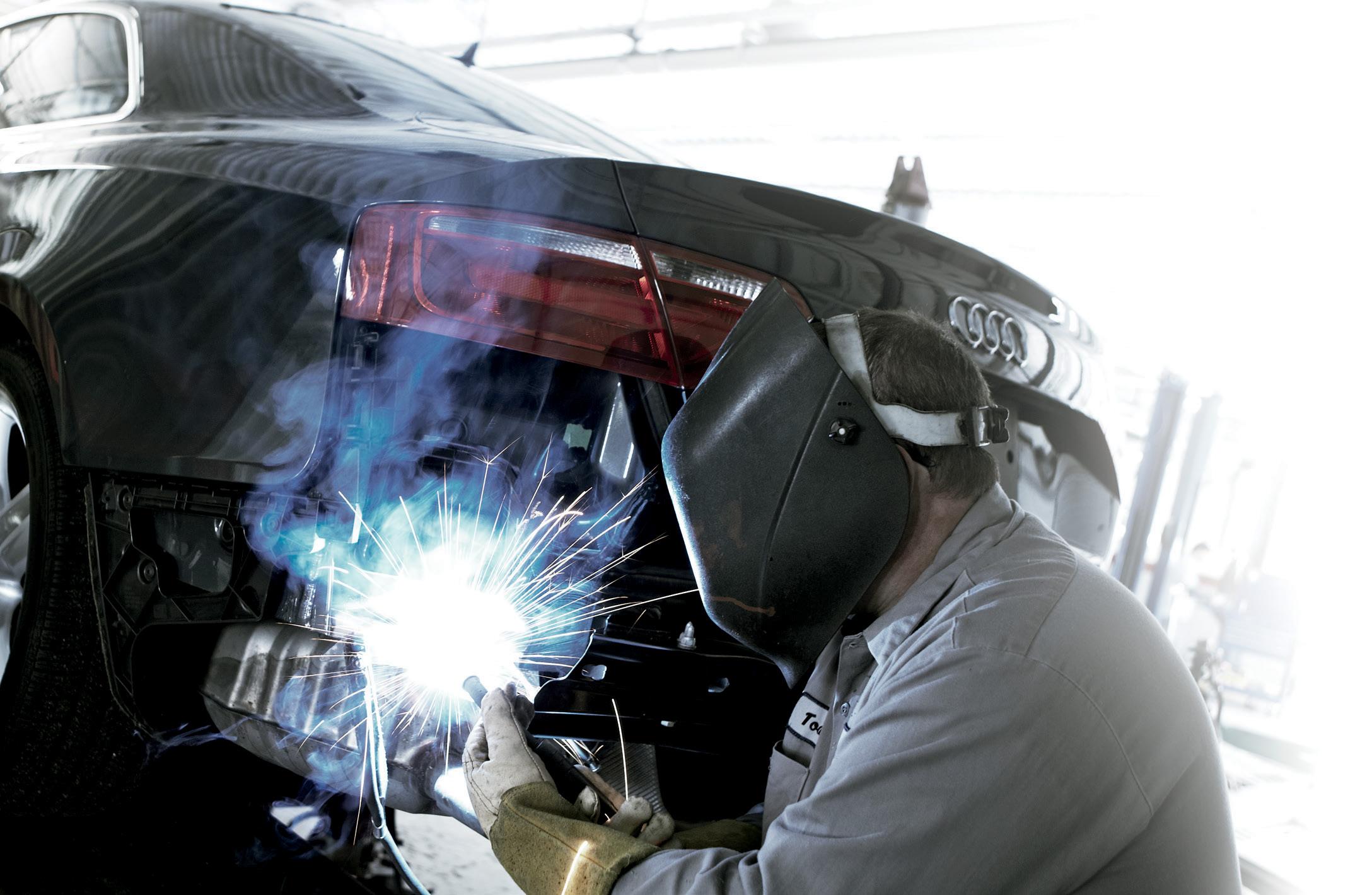
5 minute read
Audi dealers strive to make you an Audi Genuine Parts fan
• Audi Parts Professionals are your subject matter experts on collision parts, replacement components and mechanical items.
• Many Audi dealers offer technical service support hotline access that can reduce your repair times and help you meet an on-time promised delivery.
• Installing Audi Genuine Parts contributes towards improved cycle time that makes both your customer and their insurance company happier.
Helping
Ciocca Parts Warehouse
8 Minneakoning Road
Flemington, NJ 08822
Toll Free: 800-221-1256
Fax: 908.782.1795 rmuir@cioccadealerships.com www.cioccaparts.com
Paul Miller Audi 179 Route 46 East Parsippany, NJ 07054
Toll Free: 800.35.MILLER
Parts Direct: 973.575.7793
Fax: 973.575.5911 www.paulmiller.com
Bell Audi 782 Route 1 Edison, NJ 08817
732.396.9360
Fax: 732.396.9090
DCH Millburn Audi
2211 Millburn Ave
Maplewood, NJ 07040
Toll Free: 800.553.9250
Direct: 973.762.0262
Fax: 973.762.2381 www.dchmillburnaudi.com www.bellaudi.com
Town Motors Audi 400 South Dean Street
Englewood, NJ 07631
201.227.6506/6536
Fax: 201.541.0314 www.townmotors.com
Jack Daniels Audi of Upper Saddle River 243 Route 17 Upper Saddle River, NJ 07458
201.252.1500
Fax: 201.254.1552 tbabcock@jackdanielsmotors.com www.jackdanielsmotors.com
Audi Bridgewater 701 Route 202-206 N Bridgewater, NJ 08807 929.600.9156
Fax: 908.595.0237 parts@audibridgewater.com www.audibridgewater.com
The pandemic itself may be largely behind the collision repair industry; however, its lingering side effects may have left deep enough scars that won’t fade anytime soon.
Parts delays is one issue which came about predominantly due to pandemic-fueled supply chain issues. The way things stand today, not much has really changed or improved. In many cases, waiting for parts is now routine for collision repair shops. Same goes for the parts suppliers, whose job as the middlemen between the manufacturers and the shops has also evolved. As some local experts explain to New Jersey Automotive, there is much more hand-holding – not to mention aggravation –than ever before.
“Since the COVID pandemic, I now get 10 times as many phone calls regarding locating parts than I ever did before,” reports Mike Kaufmann of the Mike Kaufmann Dealer Group. “Ford, Chrysler and General Motors’ warehouses are shorthanded, probably at 70 percent.
Backordered parts normally would be at a 90-percent fill rate, but it’s actually at 60 percent. The problem stems from top to bottom. The companies that make the parts are short-handed; the warehouses are short-staffed. All of the ‘Big Three*’ have said they don’t even have enough trucks to deliver the items.” Kaufmann adds that the situation seems a bit better with Japanese OEMs, such as Toyota and Nissan, who report being back to about a 95-percent fill rate.
Ciocca Parts Warehouse Wholesale Parts Director Howard Meeks sees improvement since the pandemic began, but back order issues and significant supply chain problems continue to crop up.
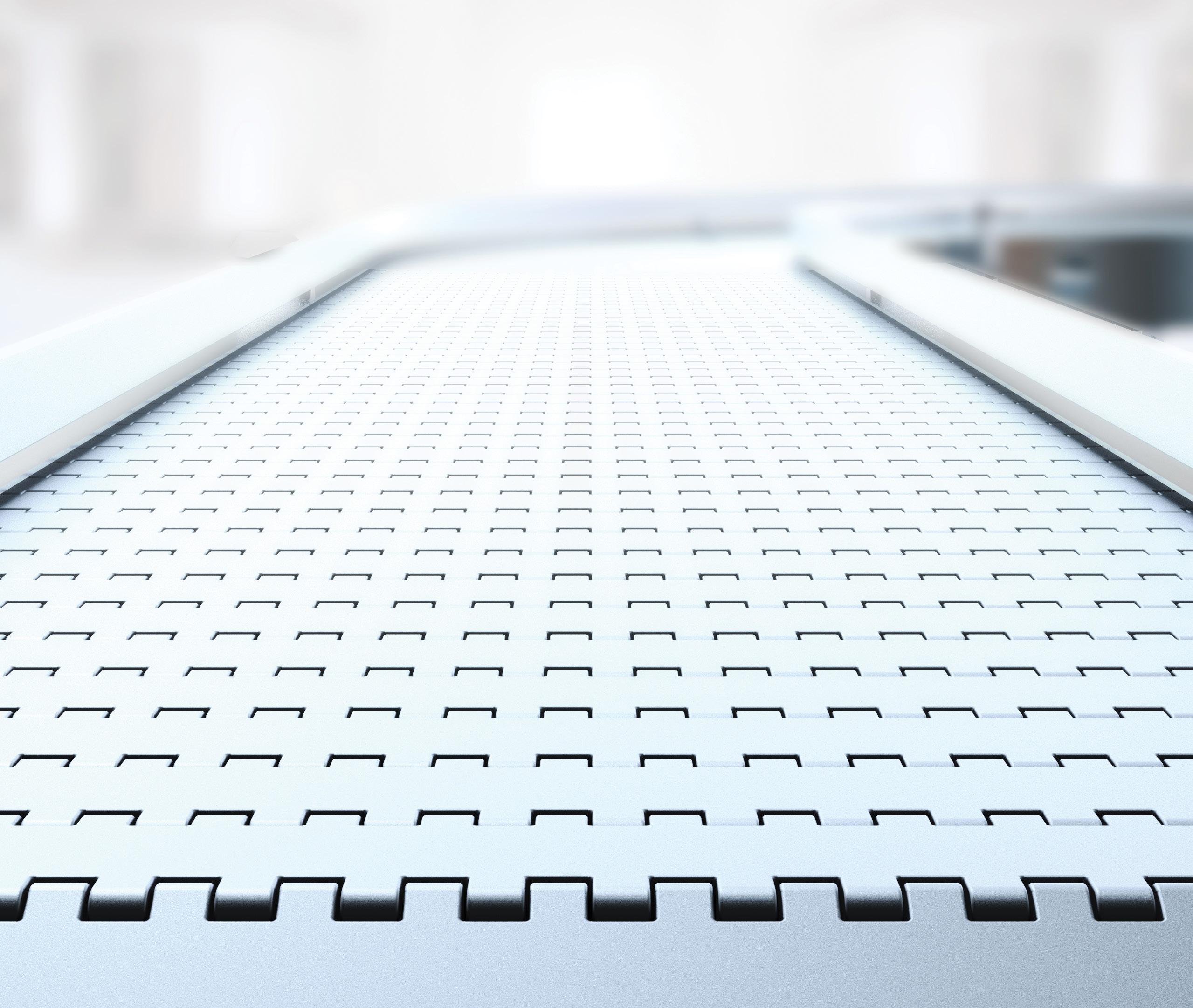
“Usually, we aren’t forewarned, so it could be any product line so that’s the problem,” he explains. “It’s not like it’s one thing; it generally goes across the board from sheet metal to mechanical to just basic items we sell every day. The manufacturers are still struggling with ETAs. For us, obviously our customers want to know when they are going to get the part, but it’s a struggle to get an accurate
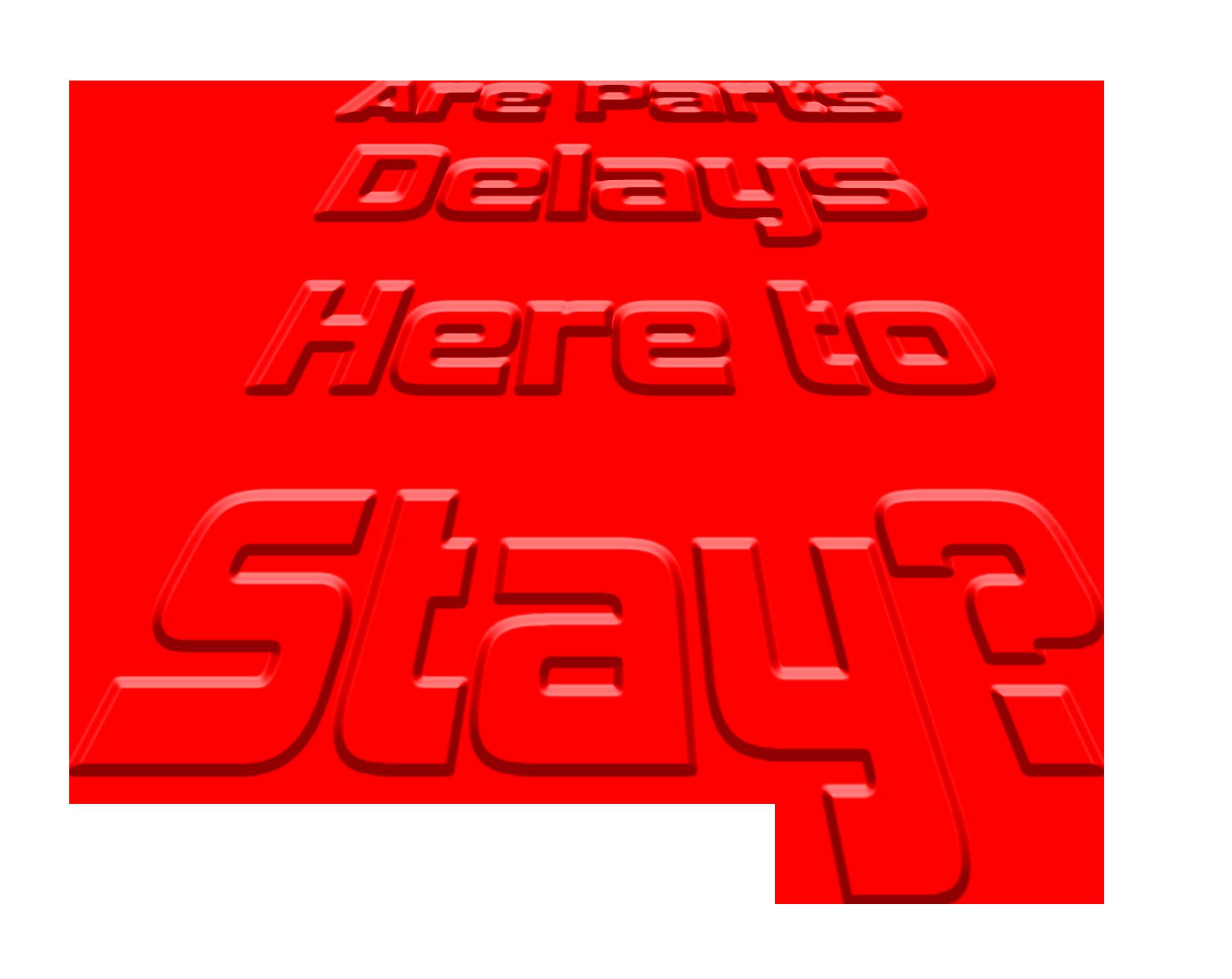
ETA from most of the vendors and that creates a big problem. We can tell a customer we’ll have a part in by the end of the month, but that can get delayed another two weeks and now it’s another month out. It’s frustrating for us because we can only give them the information we receive, and I know it’s frustrating for the customer, for sure.”
Rick Weber of Maxon Buick-GMC-Hyundai shares a similar point of view.
“Things are better, but they have not returned to preCovid levels,” he shares. “It’s not nearly as bad as it was at the height of the pandemic, but we are still seeing a backlog. Several pages of backorders are not abnormal, and it’s always the same part numbers. Cars are down for weeks as we try to obtain the parts necessary to fix them. Unfortunately, we have to be the bearer of bad news because we are at the control of the supplier, and the suppliers have not been so great. It’s gotten better but it’s still very difficult to do business.”
The frustrations may not be ending anytime soon, but suppliers are beginning to hear less complaints as shops seem to have been accustomed to delays being a normal part of today’s business operations.
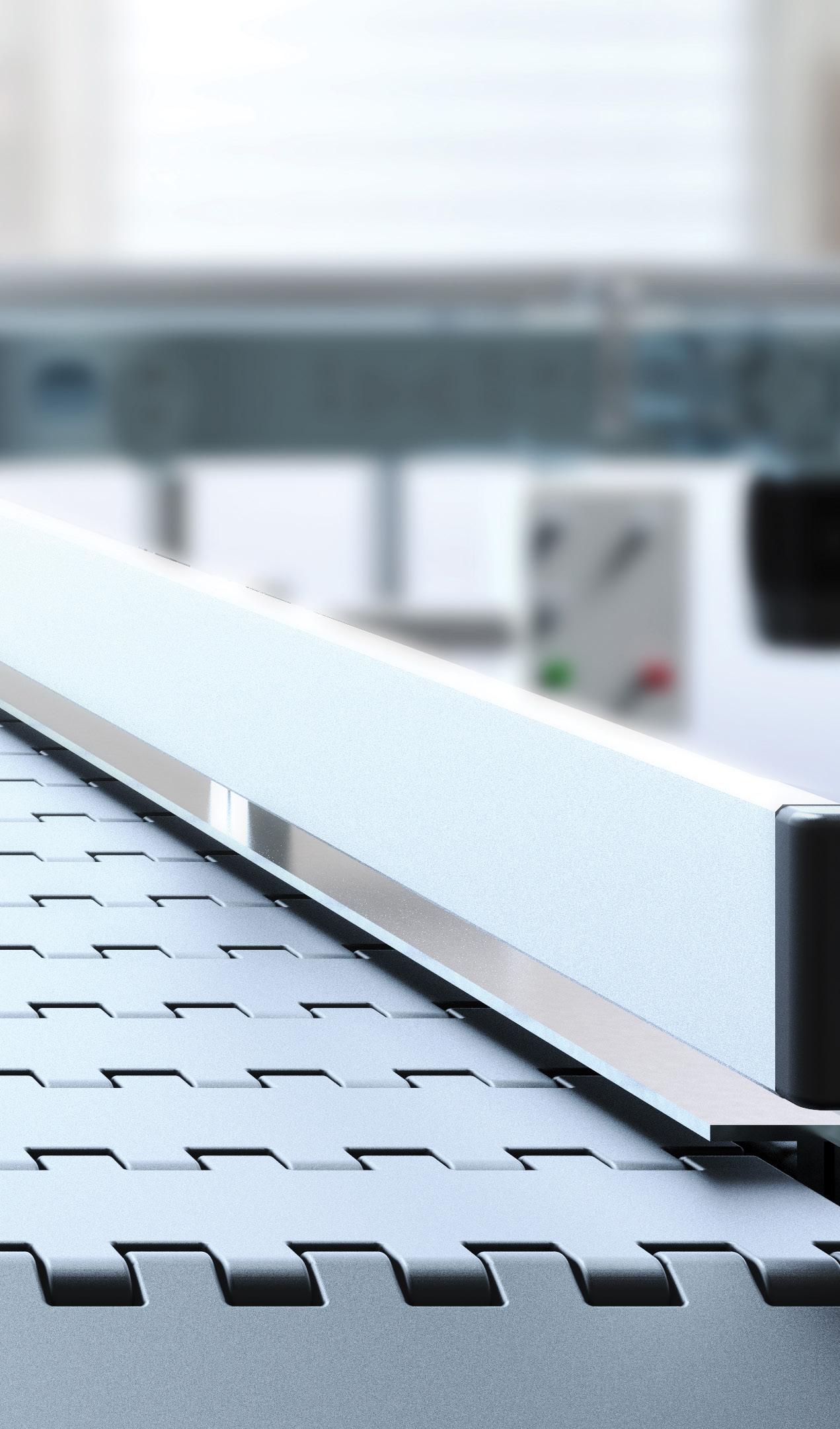
As discussed last month (grecopublishing.com/ new-jersey-automotive-july-2023), shops seem to have resigned themselves to this being a new part of doing business and are finding ways to work around expected parts delays.
“Shops are accepting it,” suggests Kaufmann. “They are used to it now. What they really want to know is when a part will come in, but there is no ETA. I can get as many as five calls a day to locate parts. Even though the dealership tries to locate the part, if they can’t find it, shops call me to try to find it. I’m doing the same thing the dealership is, but the shop may trust me more as the middleman. But it’s not the dealer’s fault if they can’t locate a part.”
Although body shops may be holding on to their parts suppliers’ hands tighter than before, some see a difference in the way the overall dynamic between shops and suppliers have changed as the “new normal” came about.
“The relationship has changed,” Weber admits. “Everything is internet driven. If I don’t have the part - or if it’s not the right part - someone is going to get it from someone else. That is the way business is right now. Everything is pretty much profit-oriented, and we are a capitalist society, so that’s the way things are. We do the best we can and sometimes it’s beyond our control.”
“I do think shops are more patient now and I think they understand it better,” Meeks recognizes. “Before it was a one-off; now it’s a little bit more of a practice we deal with every day. I think it’s become more normal to them and then obviously more normal for us.”
Ciocca Parts Warehouse is being proactive about ongoing parts issues.
“We are putting together a position that we have never done before here,” Meeks explains. “It’s just for procurement, looking for backorder parts and things that we can’t get from the manufacturer, to see if we can locate them through another dealership or directly through a vendor. We are investing into trying to alleviate some of the problem. It’s a position that we never would have thought to take on before all this.”
In this ever-changing industry, the only solution may just be to adjust and roll with the times. Weber sums it up best: “The business has changed dramatically in the 40 years since I’ve been doing it; the only thing that doesn’t change is change. If we don’t evolve and follow the trends, and change the way we do business, then we will fail. The businesses that evolve and learn that this is the new normal will be the ones who do well and be successful.”
*At press time, there are currently talks of the United Auto Workers preparing to launch a strike against the “Big Three” US auto makers. New Jersey Automotive will continue to follow this story and will report on developments in an upcoming next issue.
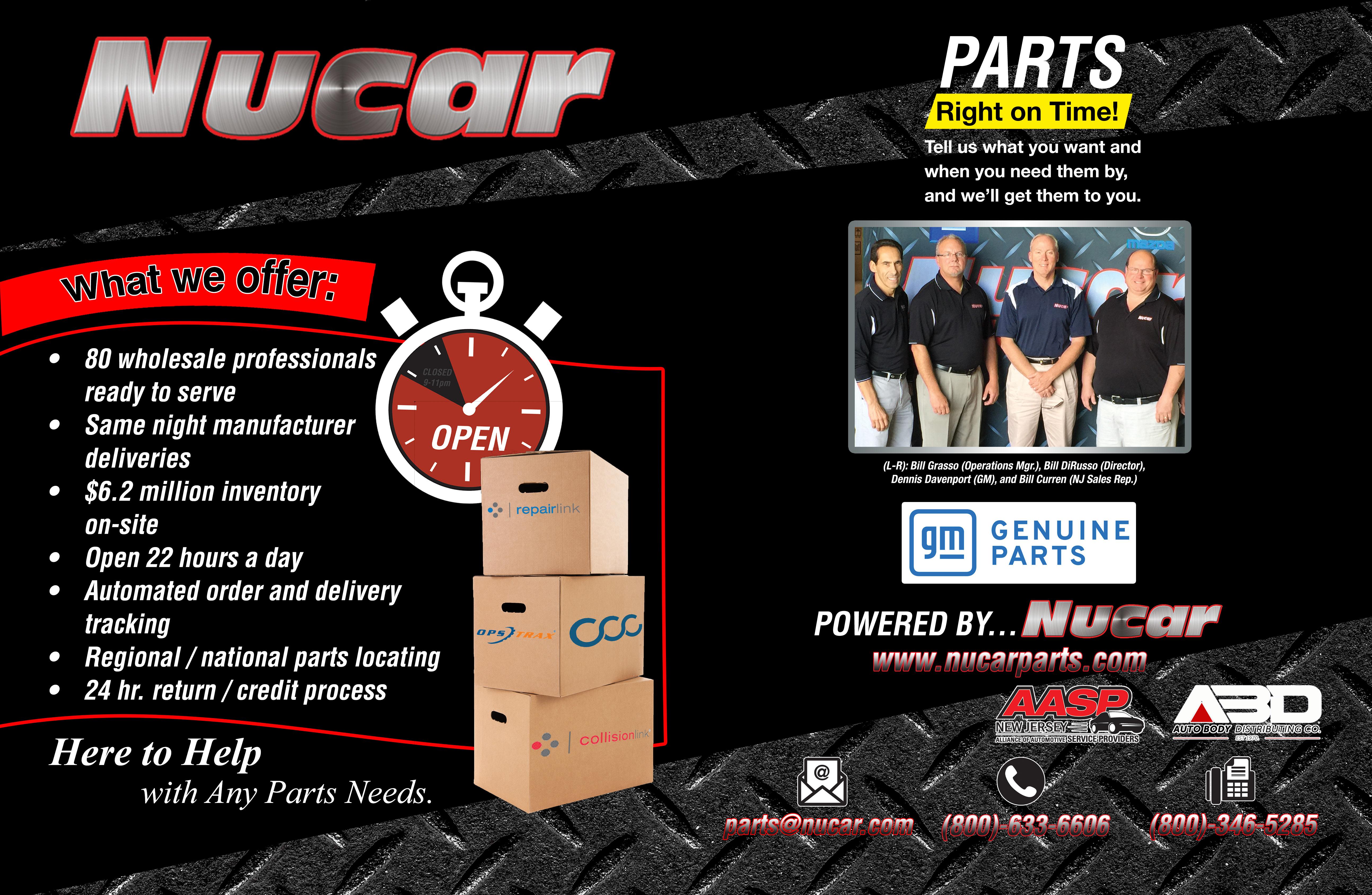
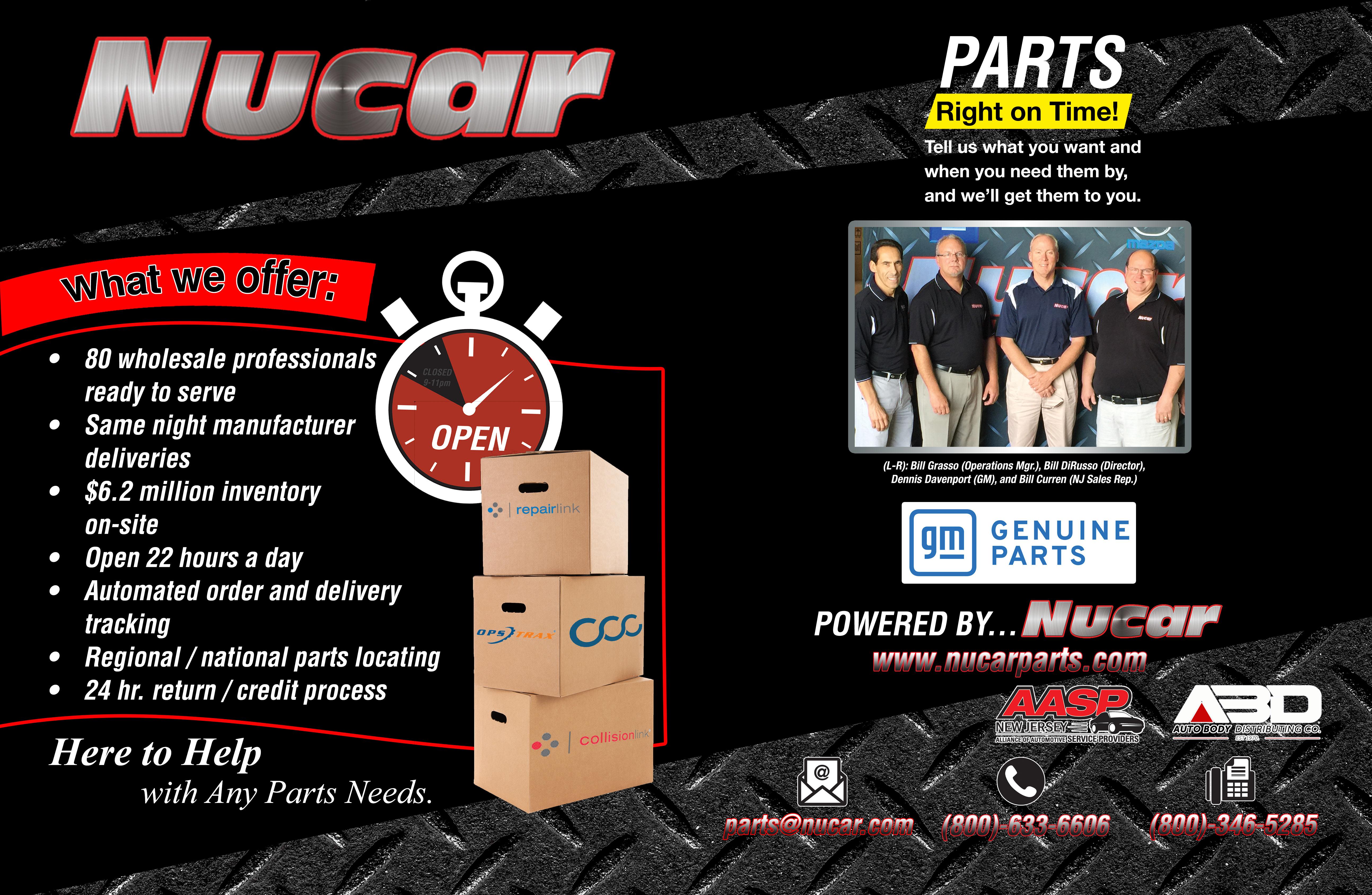
