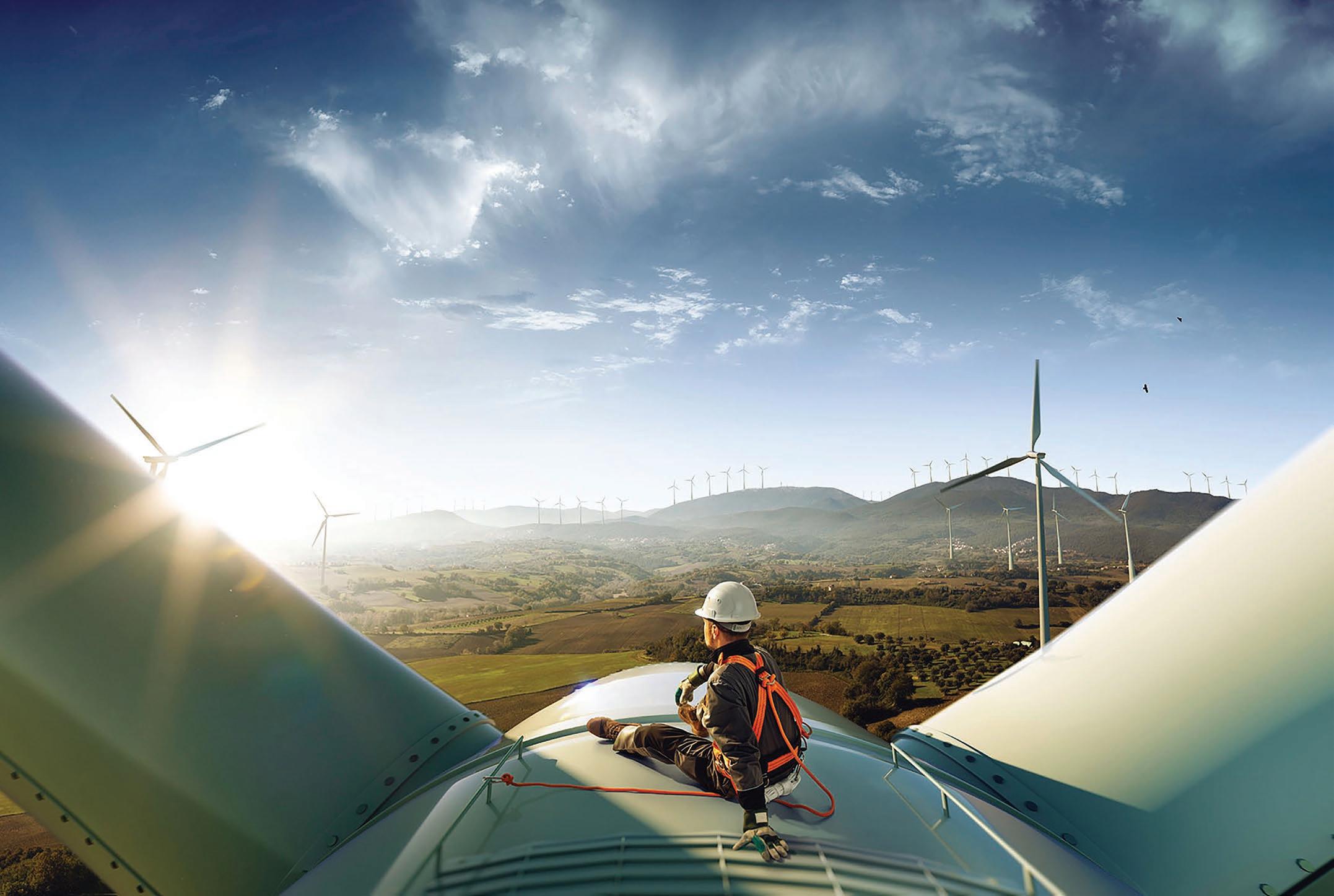
5 minute read
Wind of Change: The digital transformation of wind energy
Wind of Change
The digital transformation of wind energy
The share of U.S. electricity generation from wind energy has grown from less than 1 percent in 1990, to about 10.2 percent in 2022. To achieve this accomplishment over the past two decades, the wind industry had to increase the rated capacity of wind turbines by 350 percent by installing turbines in 2022 with an average capacity of 3.2 megawatts.
At the same time, the industry saw a 173 percent increase in the average rotor diameter to an impressive average of 131.6 meters in 2022. Yet, turbine size continues to grow. Specifically, the latest generation of offshore turbines is reaching a rated capacity between 12 and 15 megawatts, and a rotor diameter between 260 – 236 meters to optimize project cost and performance (Figure 1). These : important measurements keep the wind industry competitive with other energy sources.
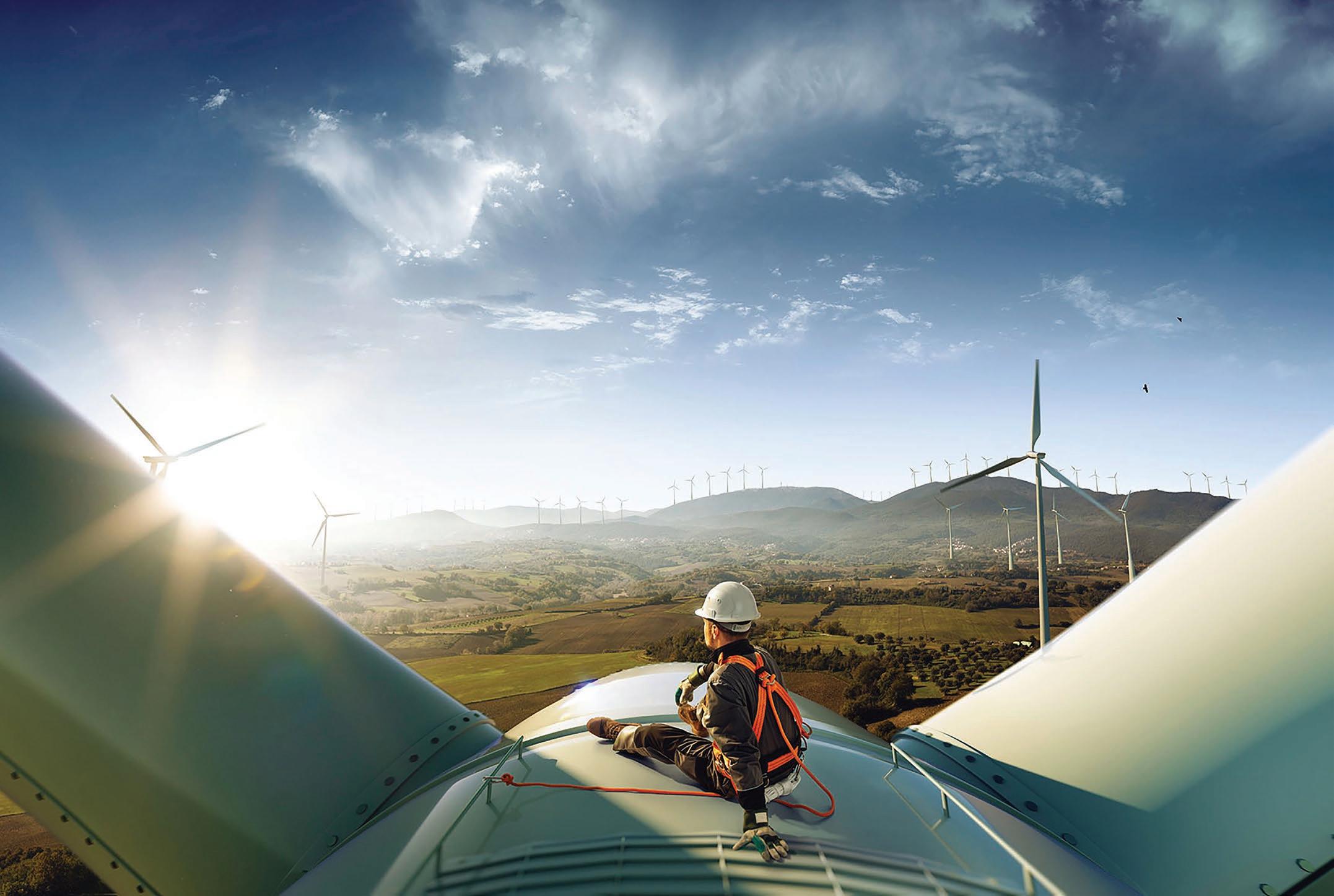
The evolution of the digital twin
Bigger wind turbines usually face higher loads and are subject to harsh environmental impacts. They require multiple sensors to ensure a safe and reliable operation within the specification during normal and extreme weather conditions. A “digital twin” is a digital map of the sensors in the field, making it possible for decisionmakers to access important data to make informed decisions (Figure 2).
The density and technology of these sensors has changed dramatically over the last two decades. Turbine manufacturers changed from low-frequency, simple digital sensors to analog sensors that measure the exact pressure, temperature, acceleration, or position. The latest generations of smart sensors even come with an integrated communication interface, such as MODBUS, PROFINET, or IO-Link, to simplify the integration and communication of complex applications.
Digital tools like weather forecast and simulations provide additional external information for power predictions, maintenance planning, and safety enhancement. All these trends support the framework of the digital twin at scale. But how does this help?
Leveraging data for maximum impact
A good example of the impact was the deployment of drivetrain condition monitoring systems (CMS) in the last decade. This was necessary to detect an anomaly or damage signature at an early stage so operators could react with necessary measurements to avoid expensive repairs or long downtimes.
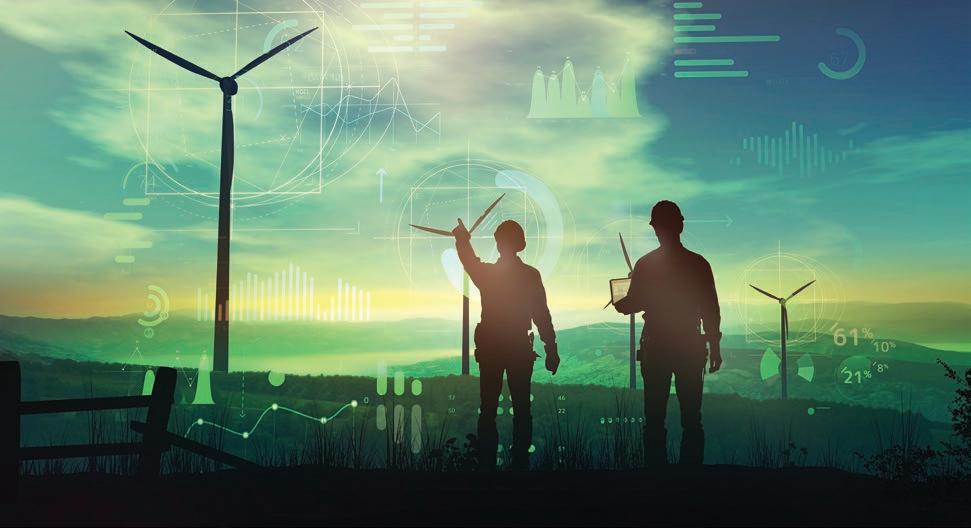
Currently, the industry is seeing a similar successful trend with structural health monitoring systems. Structural health monitoring measures important KPIs during the turbine operation. These systems continuously learn and compare multiple turbine parameters that help to accurately detect a structural issue on the blades, tower, or foundation.
Environmental monitoring systems like lightning monitoring systems and ice detection systems are also gaining importance in the wind industry. Both of these monitoring strategies help tremendously to increase turbine safety and reliability (Figure 3).
Turbine manufacturers usually offer a modular package of different monitoring modules to tackle site-specific challenges. Asset managers also have the option to retrofit specific equipment, so they can use deep analytics to improve performance and reliability further.
Challenges and future trends
The bottleneck of these strategies is the performance and openness of existing network infrastructure. To support the digitalization efforts at specific sites, operators usually deploy a separate network due to the limited flexibility and bandwidth of the existing network infrastructure. There are several ways and technologies to establish or upgrade communication over a reliable and safe network, from fiber optics to wired or wireless communication. The latest technology developments such as Single Pair Ethernet, Private 5G, LoRaWAN, and satellite Internet, are significant for improving the connectivity/data transmission of remote monitoring applications in a new ecosystem.
With the digital adoption of additional monitoring technologies, operators face challenges in managing, integrating, and protecting the additional amount of data. These rapidly expanding ecosystems are exposed to constantly evolving cyber attacks. With the increasing complexity, networks require stronger security governance than ever before.
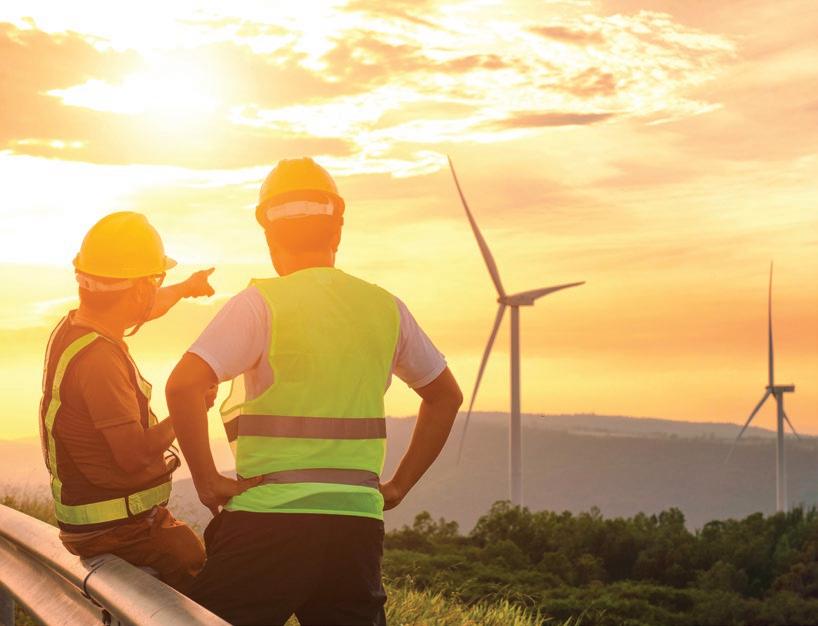
Important success factors
In digitalization, the keys to success are openness, modularity, and flexibility. A risk assessment and evaluation of your strategic goals will help you to define the required scope of your measurements. Utilize data from a variety of sources to track your improvement and measure performance.
Several cost-efficient small black box solutions are available, but they are usually designed for a specific task or challenge and share only a limited amount of data. Other solutions promise to detect several different impacts, but are not accurate because they don’t consider important turbine operation conditions that can cause false alarms or even missed damages.
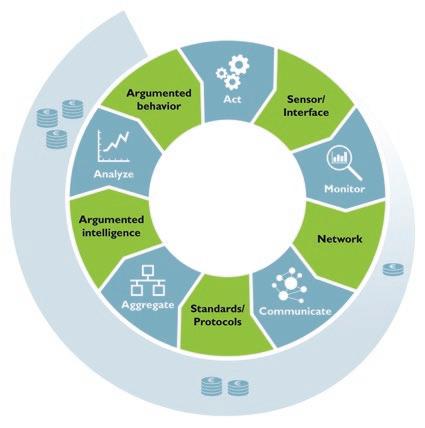
It is important to implement edge applications that support state-of-the-art communication protocols and interfaces. Additional data analysis and diagnostic services paired with inspection services (drones, for example) are crucial tools to empower predictive maintenance strategies that enhance asset reliability and reduce the risk of costly unplanned downtime.
In the end, it really depends on your operation and maintenance strategy, your budget, and your desired results. The IoT value loop (Figure 4) shows how asset operators can generate savings and improvements by taking a holistic and seamless digitalization approach through all data stages. This approach will allow operators to deploy predictive maintenance strategies that will lower the operation risks and cost of a wind turbine site and optimize the asset performance, leading to improved assets and reduced operational risk.
Heinrich Dyck is Senior Business Development Manager – Wind Energy at Phoenix Contact USA, which offers companies intelligent monitoring applications for their wind farms.