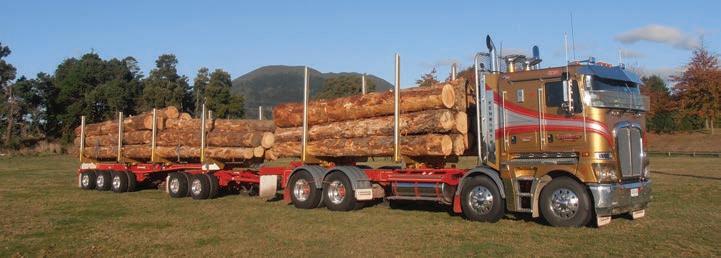
32 minute read
FOREST TALK
from NZ Logger April 22
by nzlogger
Overseas investment reform questioned
THE FOREST OWNERS ASSOCIATION (FOA) IS QUESTIONING WHY
the government needs to reintroduce more process around overseas investment for conversions from pasture to plantation forests.
Associate Minister of Finance, David Parker, says the government is changing the application process for conversions.
FOA President, Phil Taylor, says he hopes that this will not lead to a protracted and cumbersome process that kills off interest in New Zealand by overseas investors.
“Minister Parker acknowledges the need for overseas investment in our primary sector, given that there is a limited amount of capital within New Zealand. The government in its previous term realised that the application process was bureaucratic and pointlessly expensive and so brought in the special forestry test. Now it’s changing it back again for new planting.”
Since the special forestry test was introduced in late 2018 the Overseas Investment Office (OIO) has approved a total of 23,402 hectares of pasture for forest conversion, which is an average of 600 hectares a month.
“That is a very modest rate in the context of a total hill country estate of 8.5 million hectares,” Mr Taylor says.
“My main concern though is that the government is sending mixed signals about the need for an expansion of plantation forests.
“Minister Parker says it’s important that we have a ‘strong forestry sector’. We agree of course. That must mean an expansion. The Climate Change Commission says we need to grow the area by another 380,000 hectares for New Zealand to meet greenhouse gas emission goals.
“The government has also set lofty goals for increased export income from forestry. An emerging bio-economy and the widespread adoption of modern engineered timber will also drive extra consumption, here and overseas.”
Federated Farmers, on the other hand, believes the new requirements for overseas investors buying New Zealand farmland for forestry are encouraging but are only step one of a suite of changes required.
“For years Feds and other organisations have been calling for a reversal of rules that exempt overseas buyers intending to convert our farmland into forestry from the ‘proof of benefit to New Zealand’ requirements that apply when buyers intend continuing farm production land use,” Federated Farmers Meat & Wool Chairperson William Beetham says.
“That chorus has grown ever louder as tens of thousands of hectares of productive farmland are blanketed in pine trees, in large part because of the chase for carbon credit revenue.
“We’re glad the government is listening and taking action. But more must be done,” he says.
Federated Farmers supports a ‘right tree, right place’ philosophy and agrees there is an important role for production forestry, and for farmers to have the option to choose to integrate more sequestration into their farms by planting out land that they see as being marginal to their farming systems.
“Increasing the integration of vegetation into farms can bring biodiversity, animal welfare and environmental benefits, including sequestering carbon to fight climate change,” says Mr Beetham.
“What we oppose is interventionist government policies – and in particular ETS settings – that lead to a skewed, unfair playing field. Employment and the viability of rural communities are being destroyed as good production farmland is blanketed in pines in a chase for short-term profit.
“It’s not even sound policy in the long-term on the climate change front because such offsetting means polluting industries have less incentive to develop more emissions-friendly ways of doing business.
“As well as getting the ETS settings right, there are options for even-handed treatment in terms of resource consent conditions between production forests and ‘carbon-only’ forests, and the treatment of forestry in terms of the rates income requirements of local councils,” he adds.
For more on the carbon forestry debate, turn to our feature on page 30. NZL
Container shipping to Russia suspended
SHIPPING GIANTS, SWITZERLAND-BASED MSC, DENMARK’S
Maersk and France’s CMA CGM have all halted non-essential cargo bookings to and from Russia until further notice.
This covers the Baltics, Black Sea and Far East Russia, says MSC. These steps taken by the world’s largest container shipping lines effectively cut Russia off from a large chunk of the world’s shipping capacity. However, essential supplies, such as food, medical equipment and humanitarian goods will still be delivered.
They are among many corporates boycotting that country over the invasion of Ukraine, including our own Fonterra which has suspended shipment of product to Russia and closed its Moscow office.
The escalating conflict and Russian sanctions are expected to have a significant impact on the shipping industry for some time. NZL
Small relief for diesel users
THOUGH RECENT GOVERNMENT MEASURES
saw 25 cents per litre of tax removed from the price of petrol and a three-month reduction in Road User Charges, the National Road Carriers Association (NRC) warns that relief for freight costs may be months away.
NRC Chief Operations Officer, James Smith, says that as there is no excise tax on diesel, Road User Charges (RUCs) have been chosen by the Government to be the method to get relief to users of diesel.
“It is important to remember RUCs are bought in advance so there will be a lag until the discounts are seen by users. It will be a complex set of calculations to convert the announced 25 cents per litre reduction into a dollar per thousand-kilometres RUC reduction.
“Users will then need to work through the process of refunds and paperwork to access the lower rates. A significant portion of the diesel fleet purchases RUCs manually so there is no easy solution.”
Mr Smith says there are also a significant number of diesel vehicles that do not use public roads so do not pay RUCs. National Road Carriers is working with officials on practical options to get relief to users of diesel.
He adds that up until the tax cuts were announced recently, New Zealand had experienced the sharpest increases in fuel prices since the 2008 Global Financial Crisis. Since January diesel had increased in price by over 55 cents per litre.
“On top of these fuel and additive pricehikes, the cost of labour is going up because we have a serious shortage of truck drivers in New Zealand, so companies are having to pay more to attract and retain drivers. And the cost of parts is increasing because of supply chain hold-ups. No costs are going down.
“These increases blow right through the supply chain, adding cost to everything consumers buy, from groceries to clothing to building supplies,” he says, adding, “Every single carrier is different, so it’s not possible to talk generically about the freight cost increases.”
National Road Carriers offers fuel discounts through MobilCard and Z Energy and has cost calculators to assist its 1,800 members who collectively operate 16,000 trucks throughout New Zealand. NZL
Safety doesn’t happen by accident. Safety doesn’t happen by accident. Falcon Claw grapple carriages now in stock. Falcon Claw grapple carriages now in stock.
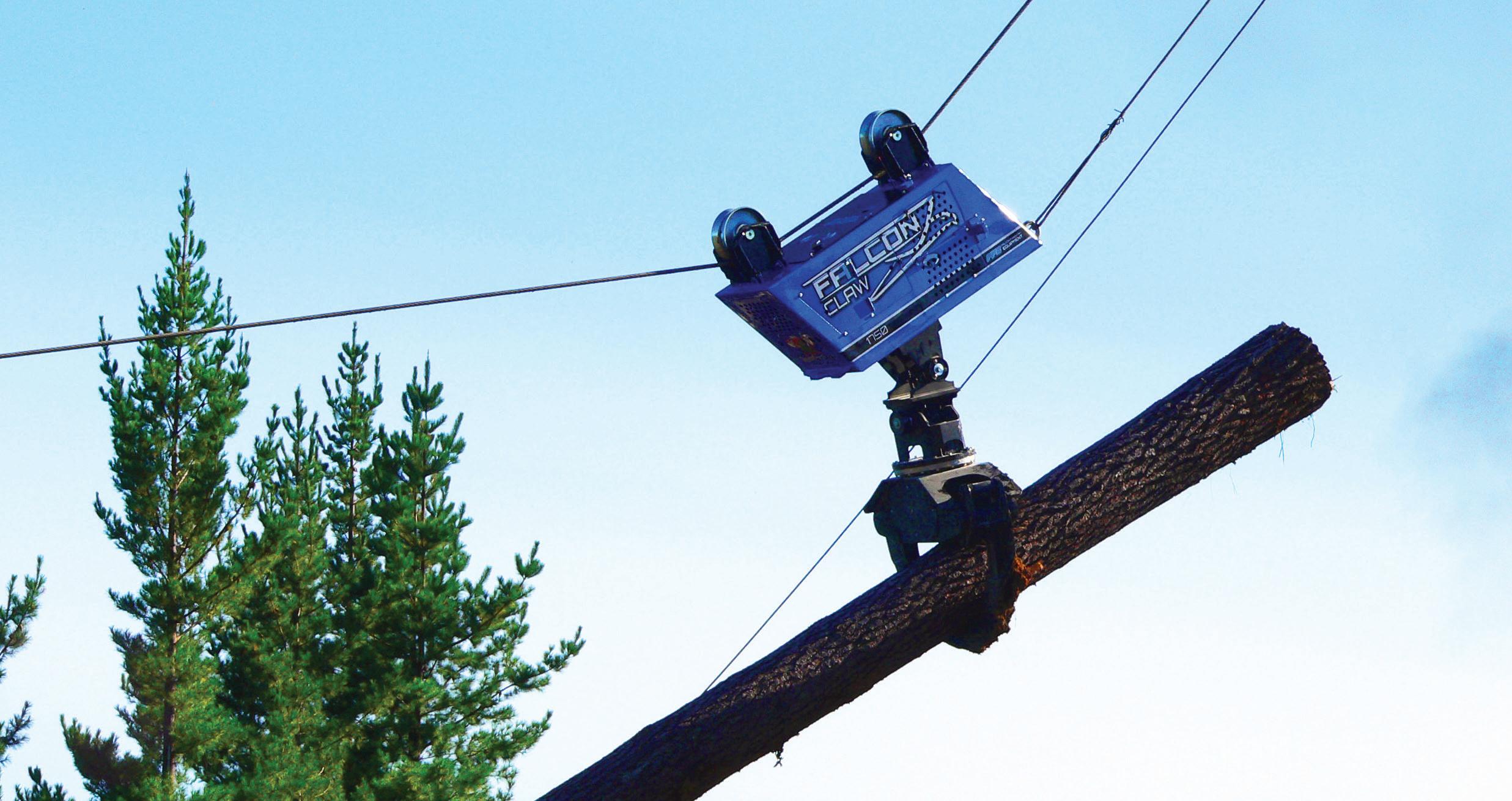
Championing timber
THE CREATION OF AN INDUSTRY ADVISORY
service for building designers will promote and facilitate greater use of timber in New Zealand buildings, says Te Uru Rākau – New Zealand Forest Service Deputy Director General, Jason Wilson.
“This advisory service, called the Timber Design Centre, is a milestone for increasing the use of timber in the design and construction of building projects, particularly in non-residential structures such as offices, hotels and multistory apartments.”
The Centre is an initiative between Te Uru Rākau – New Zealand Forest Service and a consortium comprising Scion (Crown Research Institute), the Wood Processors and Manufacturers Association, New Zealand Timber Design Society and BRANZ.
“Through this collaboration, the Centre will provide information on timber design guidance, research and development, and specialist technical advice to increase and speed up the use of timber in buildings. A great example of what is possible to be achieved through designing in wood is the world-leading Scion headquarters in Rotorua,” Mr Wilson says.
He says the initiative builds on international experience and learnings and will drive the shift to using timber to its full technical potential in New Zealand, particularly in mid-to-high rise buildings.
“The Centre will also provide an independent forum for fostering connections across the forestry and construction sectors and can develop local expertise, knowledge, techniques, and skills on all aspects of using engineered timber in our buildings.
“By overcoming barriers to using timber in design and construction, New Zealand has the opportunity to replace steel and concrete with wood, lower carbon emissions, and support our country’s drive to greater environmental sustainability.
“The Centre is also a pathway to increase long-term demand for New Zealand wood products and support greater investment in domestic wood processing.”
Te Uru Rākau – New Zealand Forest Service is funding the Centre as part of the Government’s Fit for a Better World roadmap. The Centre is one of several key initiatives underway this year to help transform the forest and wood processing sector.
“By providing an innovative and inspiring source of the latest expert advice and information, the Timber Design Centre will inspire building owners and property developers to commission wooden buildings,” says Mr Wilson.
“This is an exciting step to supporting design professionals to specify timber in building designs and enabling builders and contractors to build high-quality wooden buildings which not only support our economic potential but will also deliver strong environmental outcomes for the future.”
The Timber Design Centre is currently virtual, so head to timberdesigncentre.co.nz to find out more and get involved. NZL
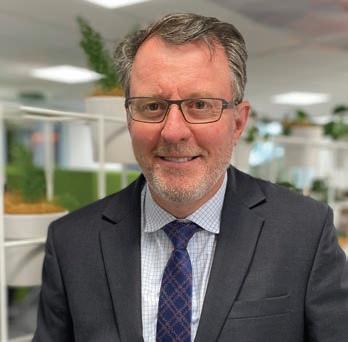
Top axeman to take on world title
A CHANCE AT A 10TH WORLD TITLE FOR
Jason Wynyard came as he won the 2022 New Zealand Stihl Timbersports National Championships last month.
The victory means he has earned the right to represent New Zealand at the Stihl Timbersports World Championships in Sweden in October – a tournament he last won five years ago.
Since 2017 Mr Wynyard has battled debilitating arthritis in his hip, but now following nearly three years’ break from full-time competition – involving stem cell treatment and a hip replacement – the ninetimes world champion is on the comeback at the age of 48!
“I had this goal to try and qualify for the World Champs for some time now since hip replacement and stem cell treatment and it’s pretty cool to take that next step and qualify, but I realise that there’s a lot of work ahead of me,” he says.
He dedicated his victory to fellow international competitor, Martin Komarek of the Czech Republic, who recently died tragically in a forestry workplace accident overseas. He was very well known to the New Zealand Timbersport community, having competed here.
Over the years Mr Wynyard has won over a hundred world titles in the sport.
He received the Order of Merit for services to the sport of wood chopping in 2017. NZL
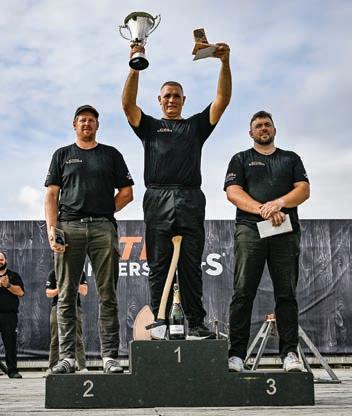
Left: Jason Wynyard with second place winner Shane Jordan and Nathan McDonald coming in third. Right: Jason Wynyard in action.

Foresters join forces with firefighters
Fire training.
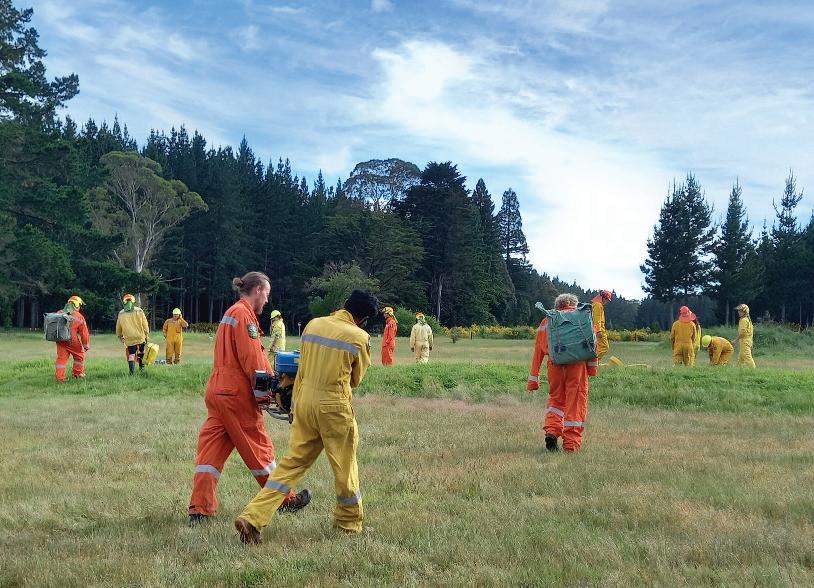
FORESTRY COMPANIES ONEFORTYONE NEW ZEALAND, TASMAN
Pine Forests and PF Olsen have signed an agreement allocating funding, people resources, training and equipment to manage fire risk in the Nelson Tasman region.
Fire and Emergency District Manager, Grant Haywood, says the new agreement with forestry companies has formalised and extended local arrangements that have existed for several years.
“Forestry companies are valued partners in fighting rural fires all around New Zealand, and it’s no exception in our District,” he says. “They bring valuable skills and knowledge in tackling forests and vegetation fires, and we appreciate being able to call on forestry crews to work alongside our firefighters.”
In November last year, Fire and Emergency took over the management of all rural fire services in Nelson Tasman that had previously been contracted to the Rural Fire Network (RFN). Now RFN is working with the forestry companies and supporting the implementation of the new agreement.
Based at the Tapawera Fire Store, Manager of RFN, Ian Reade, says there are 50 fire-trained forestry contractors available to assist in the event of a fire: “Along with their knowledge of local terrain and forests, the forestry contractors are hill fit, meaning if there is a prolonged fire event in rugged terrain they can keep fighting fires safely day after day without excessive fatigue.
Forestry company employees could also fill roles in an Incident Management Team if needed during an extended fire response, he says: “Roles such as GIS fire mapping, machinery and operations management, technical fire behaviour, planning and logistical functions are all skills that closely relate to a forester’s day-to-day work.”
Another agreement between the forestry companies and Fire and Emergency New Zealand allows for the continued operation of the Richmond Hill Lookout for the 2021/22 fire season.
Local Lookout Attendant Robbie Campbell is based at the lookout full-time during the fire season. His job doesn’t just focus on watching for fires. He also acts as a local communications hub for firefighters, forestry personnel and the public. Richmond Hill is one of a network of four lookouts that are still in place, maintained and sometimes used in very high fire danger situations.
Mr Haywood says in spite of any wet weather, rural fires remain a constant risk over summer and the relationship with forestry companies is an important part of building resilience in the community. “Our firefighters have been working alongside forestry crews for many years. We know we can rely on each other and that’s important for our region.” NZL

Field trip with OneFortyOne and Fire and Emergency New Zealand. (View from Richmond lookout.)
Robot drone swarm to detect fires
Source: The National Land Survey of Finland.
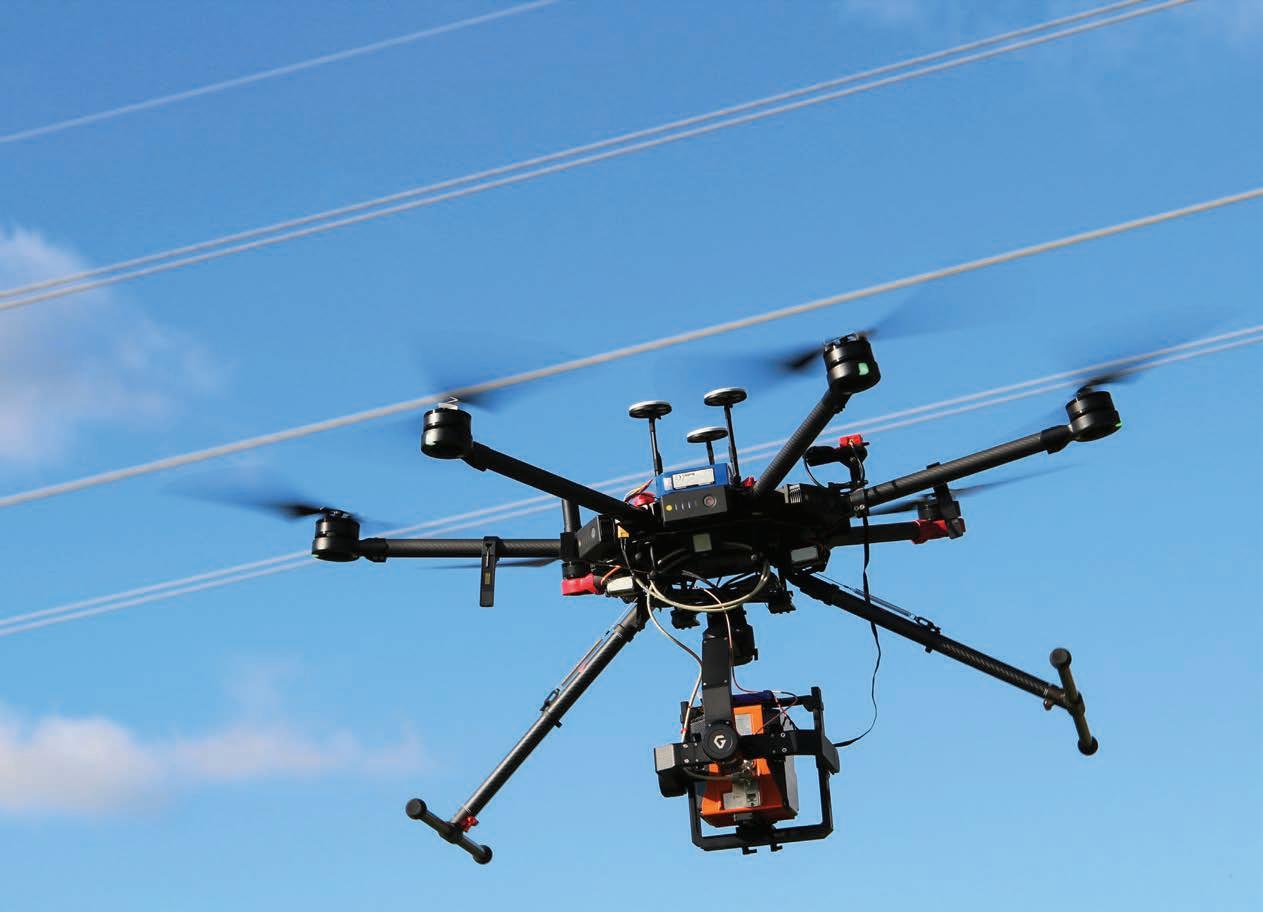
AMONG THE WORLD LEADERS IN DRONE RESEARCH, FINNISH
researchers are developing the technology to use a swarm of coordinating drones equipped with Artificial Intelligence (AI) to detect and prevent forest fires.
Geospatial data is crucial in preventing, monitoring and extinguishing forest fires. However, while information on current forest fires is already available using satellites, there are no efficient methods to quickly detect small and recently started forest fires and monitor the fire in real time.
How can a forest fire be detected early enough? How can up-to-date information on the progress of the fire and a forecast of how it will spread in the next hour be obtained?
That’s what the FireMan consortium formed by the Finnish Geospatial Research Institute (FGI) of the National Land Survey of Finland (NLS), the University of Jyväskylä, the University of Oulu and the researchers from VTT Technical Research Centre of Finland are attempting to answer. The project will run from 2022 to 2024, funded by the Academy of Finland.
“We’re developing a new AI-based drone technology to quickly detect forest fires and provide situational awareness when extinguishing the fires,” says Professor Eija Honkavaara from NLS, who is leading the project.
“Drones can help us in providing real-time information on how the fire front is progressing, and how high and hot the flames are. We’re developing methods to locate a swarm of drones and produce remote sensing data in real time. In addition, we’re developing sensor technology that surpasses the ability of the human eye in terms of seeing through smoke,” Prof Honkavaara explains.
Associate Professor Ilkka Pölönen of the University of Jyväskylä adds, “Forest fire progression can be modelled numerically, considering topographical features, vegetation and wind direction. In this project, we use forecast models to teach the AI so that it can assess the fire progression based on remote sensing data collected in real time.”
The performance of the broadband connection from the device to the network will also be crucial, with connections having to work reliably in remote areas and at typical flight altitudes.
Drones must be able to monitor wide forest areas and react and act independently as required in fire situations. It is essential that the drones operate as a group in a fire situation, say the researchers who will be testing the swarm of drones in practice.
In the FireMan project, the researchers will test the drones in practice. Material will be collected during prescribed burning by Metsähallitus and the Finnish Forest Centre. The first drone flights will take place as early as the European spring of 2022.
A demonstration of the drones operating as a group observing and monitoring a forest fire will be held at the end of the project.
Records show that more than 400,000 hectares of forest burned down in 2019, which was the worst year for forest fires in Europe. This grim record was broken last year: by the end of October, half a million hectares of forest had already burned down in Europe. Forest fires are expected to increase due to global warming so forest fire control is naturally of interest in Finland – with 75% of its land area being forest. NZL
From left: Penske New Zealand General Manager, Brent Warner, Kaumatua Sonny Ranapia and Kaumatua Des Tata.
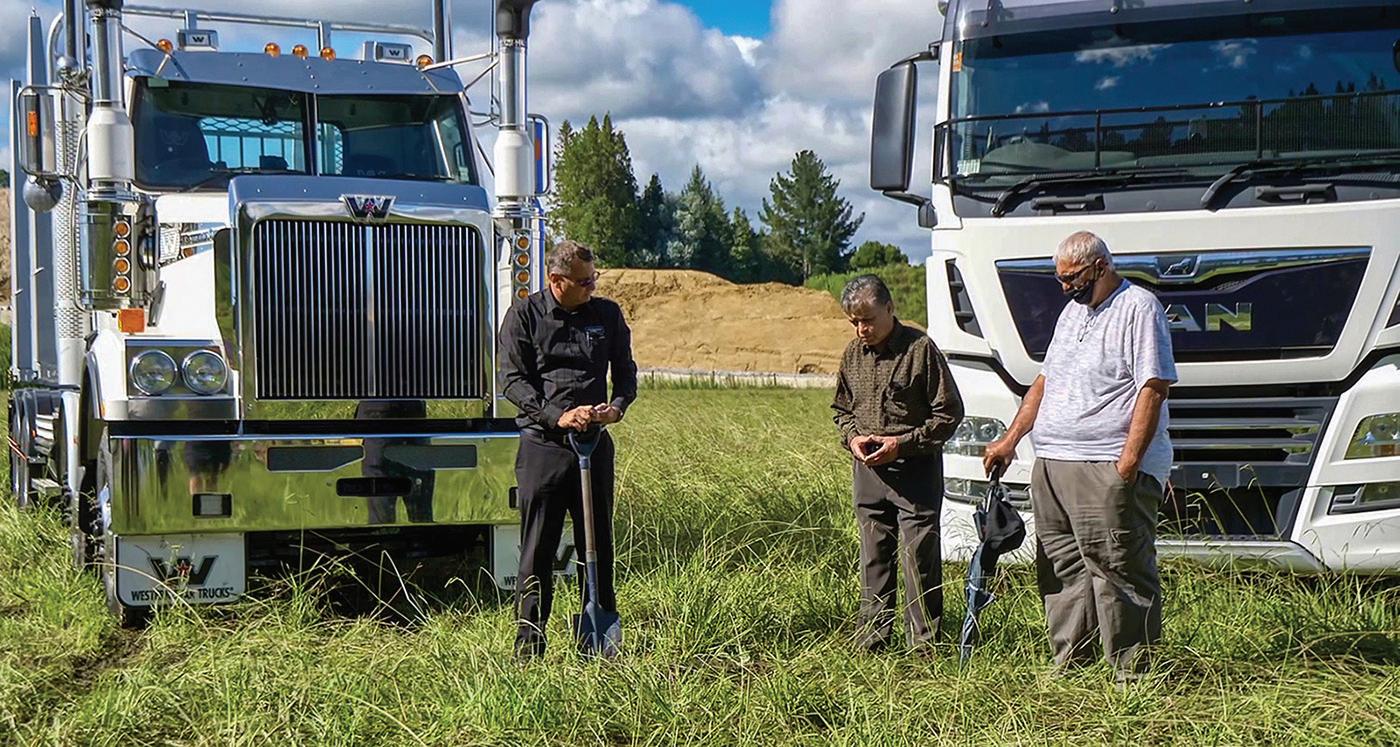
Breaking new ground
PENSKE NEW ZEALAND HAS BROKEN GROUND ON THE SITE OF ITS
new Tauranga facility. Providing full retail sales, parts, and service support for the Western Star Trucks, MAN Truck & Bus, Dennis Eagle, mtu, and Detroit brands, the new facility will be located at Kaweroa Drive, Tauriko.
Situated on 13,167 m2 of land, the purpose-built facility will comprise 2,550 m2 of workshop space, a 700 m2 parts warehouse, and 800 m2 of retail and office space, including a drivers’ lounge.
The new Tauranga branch will also house 17 30-metre truck bays, a machine shop, a drive-through wash bay, a full-length service pit, and two built-in hoists, along with a certificate of fitness (CoF) and a heavy vehicle entry compliance certification bay.
“It’s very exciting to have broken ground and commenced the construction phase of our new Tauranga facility,” says Brent Warner, General Manager of Penske New Zealand.
“And having Kaumatua Des Tata of Ngai Tama Rawaha Hapu and Kaumatua Sonny Ranapia of Rangi Ranginui Iwi undertaking a blessing ceremony on site was an incredibly special experience.
“We look forward to welcoming our customers to our new site in early 2023 and demonstrating our ongoing investment and commitment to the New Zealand transport industry and the Bay of Plenty region.” NZL
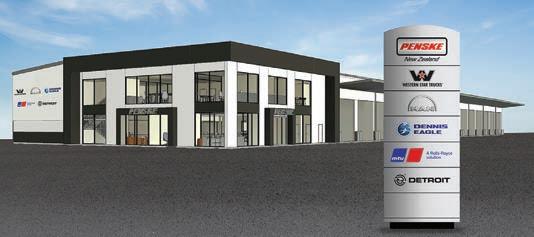
Proposed new Tauranga site.
Waratah to offer Moipu branded products
WARATAH AND MOISIO FOREST OY, A
Finnish-based forest machine attachment and accessory manufacturer, have signed a co-operation agreement for sales, marketing and distribution of Moipu branded products.
Waratah will begin marketing and selling the well-known Moipu energy wood solutions through its global distribution network primarily in Europe and Asia-Pacific, with some sales in other global markets. Moipu products sold through Waratah dealers will be supported by Waratah dealers and field teams, with spare parts available through Waratah’s distribution network.
“With the addition of the Moipu brand, we’ve added new solutions to our portfolio, which will help our customers get more products for their forestry operations – plus they have the added benefit of our extensive dealer and field team for parts and support,” says Markku Ojaniemi, Manager, Waratah distribution Europe, Russia, South America, and Japan.
Moisio Forest Oy will continue to sell products jointly with Waratah in Nordic and Baltic countries as well as in the UK and Ireland. The new collaboration will expand the Moisio Forest Oy distribution as well as the Waratah portfolio.
Moipu energy wood heads were first built in the 1990s and applications include energy wood harvesting, early thinning, roadside cleaning, rail side cleaning and riverbank cleaning. Moipu products are designed to be installed on practically any carrier and most of the products operate without a control system or electricity. Compatible carriers include forwarders, harvesters, excavators, timber trucks, or any carrier with a crane and suitable hydraulic oil flow. NZL
Grappling with safety
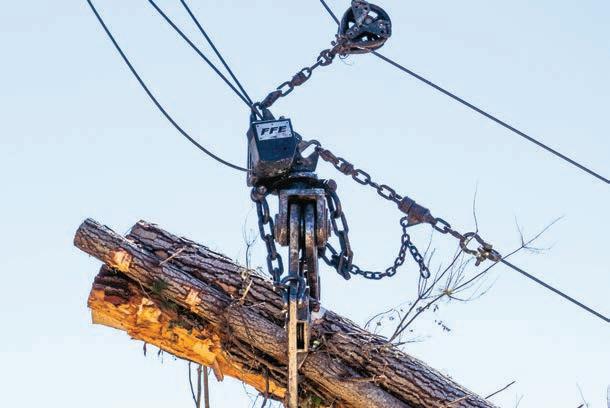
GETTING WORKERS OFF STEEP HILLS, AWAY FROM HAZARDS ON
the ground, is still proving to be a tough ask for some crews around the country, particularly when it comes to extraction, with manual breaking out often required where there are no alternatives.
But it doesn’t necessarily have to be like this, according to forestry contractor and new technology champion, Dale Ewers.
“We operate 15 crews around the country, sometimes in very difficult locations and we’re able to use mechanisation in up to 98% of those situations in all but one of our crews – and that crew still does around 80-to-90%,” he says.
The challenges of keeping people safe prompted Dale to start up his company, DC Equipment, which has developed a number of solutions to mechanising steep slope harvesting, including the Falcon Winch-Assist system and the Falcon Claw grapple carriage.
It was the safety of his people that led Dale to come up with a workable grapple carriage ten years ago. In spite of being told by many in the industry that it would never work, the Falcon Claw has gone on to become a key piece of equipment for many crews in New Zealand and overseas.
The Falcon Claw has also spurred a number of others to design and build their own grapple carriages and release them to the market.
“That’s good,” says Dale of the increased competition. “It shows that we’ve been on the right track and, quite frankly, I’m not bothered what colour grapple carriage people buy, so long as they adopt the technology. It means that we are putting fewer people into dangerous places.”
But the adoption rate is not growing anywhere near as fast as it could, for a variety of reasons: some older towers either don’t have water cooled brakes or just don’t have enough power to lift a skyline with a carriage; contractors are not in a position financially to adopt the new technology; and, of course, there’s always challenging terrain and other obstacles.
Yet Dale says there are ways around those roadblocks: “I struggle with the theory that tower haulers cannot run grapple carriages because I don’t agree with that,” he says. “You can run grapple carriages on all those machines, some better than others, of course. Any machine with a water-cooled skyline can run them and that’s most machines being used here in New Zealand forests.”
For those that are not capable of running a grapple carriage, Dale says that the cost of a set of water-cooled brakes is around $10,000-to$15,000.
“It’s not a major job to adapt most towers – I’m talking about those built from the early eighties onwards,” he adds.
Like any old machine, there’s always a need for ongoing maintenance, so upgrading with water-cooled brakes and even a new engine to increase power can be built into the schedule.
Dale goes on to say: “Breaking out and manual tree falling are the most dangerous jobs in the forest and there is always the potential for something to go wrong and for someone to get hurt… or worse.
“That’s why I decided to look at mechanising those tasks. To protect my people. It’s not about putting them out of work – no jobs have been lost since we started introducing these technologies. Those guys are being deployed in much safer jobs elsewhere in the company.”
Asked why he thinks the rate of mechanisation is slower than expected, he says: “It’s a mindset and the willingness to make a difference.
“There needs to be a change from saying ‘we can’t make it work’ to ‘how can we make it work’. While they are saying they can’t make it work, they won’t ever make it work. There has to be an action, otherwise there’s not going to be a result.
“They are going to have to adopt that technology otherwise we are not going to be able to get people to go on the hills.”
That last point is a reflection of the situation already facing the industry where it’s becoming harder to attract new blood to fill vacancies in forestry, partly driven by the perceived poor safety record. It’s a struggle to convince parents to recommend their children take a job in forestry, he says.
Safety was a key concern when Gareth White decided to put a grapple carriage onto his Skagit 739 100ft tower hauler.
“Getting people off the ground is most definitely a major reason for introducing the grapple carriage,” says Gareth.
“When you’ve got breaker-outs down the hill, at the back of your mind is the thought that something could go wrong.”
It’s been more than a year since he put the grapple carriage to work and he says it is going even better than he first imagined, staying on the skyline in all but the most exceptional circumstances.
And, contrary to what some may think, productivity has improved, not gone backwards. It can pay back in other ways, such as in reduced maintenance, because there is less stress and shock to the ropes and running gear, so they last longer.
It does take time to learn how to use a grapple carriage effectively on a tower, utilising a mobile tail hold to shift the skyline around or using a Live Dutchman setting to create lateral movement, but the more familiar the crews become with how it works, the better it works for them.
In the ten years since grapple carriages first came to market, the technology and reliability has improved substantially. Hauler and swing yarder operators can see the wood on the ground much better thanks to the introduction of high-definition (HD) cameras and there’s now a move to fit multiple cameras on the carriage to give a much broader view of the cut-over.
Nelson logger, Jason Moir, is now on his third Falcon Claw and has used them on a tower and swing yarder over the past nine years. He says: “I honestly don’t know how we used to do it (before the Falcon) and these days to get a man to go down a hill to hook up a tree, they don’t exist – so you move with the times or get left behind.
“And this thing doesn’t complain, it just turns up every day and does the job. The last claw we had, before our latest one, we just tipped diesel into it and it did not let us down for one day.”
In spite of the slow progress, Dale says he can foresee a time when all manual breaking out is consigned to history.
“It’s not too far away for us. We are currently working on a project that will eliminate all manual tree falling and manual breaking out.” NZL
Durable debarking
WARATAH FORESTRY EQUIPMENT HAS
launched the H225E – a new generation of its H215E head. Designed for use on large, wheeled harvesters and excavators, the H225E is a powerful, high-capacity debarking head for harsh applications.
“The H225E redefines what it means to be a workhorse, with improved features that facilitate enhanced debarking productivity and durability,” says Product Marketing Manager for Waratah, Brent Fisher.
Weighting in at 1690 kg (3,720 lb.), this new 200 Series head features a higher performance valve that allows for better oil flow and greater hydraulic working pressure capabilities (35 MPa or 5,076 psi) for more feed power. It also boasts reduced frame friction for straight or curvy trees. Improved measuring wheel log contact enables more accurate measuring while a new find-end laser sensor reduces the need to saw.
The H225E also includes patented variable angle feed rollers for better bark separation cutting as well as debarking initialisation and efficiency, improving debarking for varying diameters. Redesigned swept cast arms improve delimbing in harvesting or processing applications with lower knife improvements for reverse delimbing. The H225E features Waratah’s TimberRite H-16 measuring and control system for increased efficiency, accuracy and productivity.
Built to master debarking, the H225E also features new delimb arm profiles, which improve delimbing and durability in plantation stands of consistent diameter or variable diameters of big timber. The length measuring system has been improved for more durability and placement on the log – or with optional measuring from the feed motors.
The new valve includes anti-cavitation protection for feed motors, and additional guarding protects the main frame and roller arm cylinders. Additionally, a new hose bulkhead bracket reduces hose wear and interference on tracked carriers. Extra protective elements have been added to the rear knife hose routing and tilt cylinder baseend bearing for increased part durability.
With more efficient hydraulic operation, the H225E valve design allows for higher working pressure to reduce oil flow needs and provide more torque with reduced fuel consumption. This also decreases the need for hydraulic oil cooling. Additionally, an improved hose layout promotes uptime by minimising potential hose failures.
The Waratah H225E head is currently available to customers in New Zealand, Australia, Asia Pacific, the United States, Canada, Brazil and Latin America. NZL
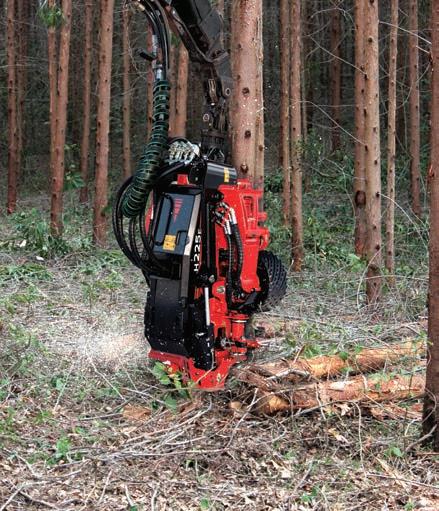
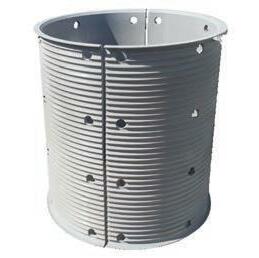

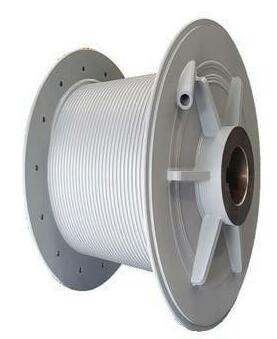
Grooved Drums and Sleeves
Put through its paces
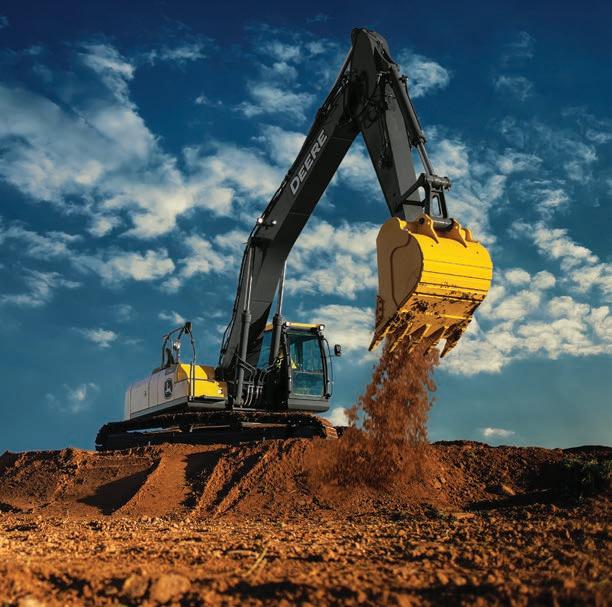
THE JOHN DEERE SERIES-II EXCAVATOR MADE ITS ENTRANCE
into New Zealand six months ago after being introduced to the Australian market over a year ago.
The line-up includes eight models to take on Australian and New Zealand conditions.
Through John Deere Customer Advocate Groups (CAGs), engineers and developers engage closely with customers, and respond to their feedback at key points in the design of John Deere machines, so that features and specifications deliver what is needed. Customers also help evaluate John Deere designs by putting equipment through its paces in a series of in-dirt evaluations.
“By understanding real-world application, our engineers have the information and insights they need to create a differential edge on John Deere products, and this critical input is the driver behind every comfort, function, and performance feature we produce,” says Kel Davison, Director for Marketing and Sales, Construction and Forestry Equipment.
The result is a machine with a number of useful features. The spacious cab of the Series-II was designed with convenience in mind, with plenty of storage and easily-accessible controls. The Sealed Switch Module (SSM) is intuitive, conveniently placed, water and dust proof and eliminates unsealed connections and moving parts associated with traditional rocker switches. The 7-inch touch screen monitor is easy to navigate, providing quick access to machine features and functions. Multiple machine readings and Diagnostic Trouble Codes (DTC’s) are available for the operator to read via the touch screen.
Grouped service points, single position swing greasing, 4,000-hour hydraulic oil and filter and 500-hour engine oil and filter changes, as well as the oil-sealed and lubricated undercarriage, ensure daily servicing is simple and efficient.
John Deere excavators are built tough to deliver more uptime by harnessing the power of heavy-duty booms and arms, a robust electrical system and optimised hydraulic routing. A sealed and lubricated undercarriage and heavy-duty welded X-frame provide a solid, stable platform, while the sloped track frame resists material build-up to decrease cleaning time.
Full-length track guides and double-grouser track shoes are optional for rocky terrain and a heavy-duty cooling system keeps the engine and hydraulic system running efficiently, even in tough environments. Four power modes and three work modes deliver the right power and response for maximum productivity and strong digging force. Other strategic features include a durable and thick boom, arm and buckets to withstand tougher digging conditions, and Auto Pressure Boost to anticipate and deliver power when it’s needed. The John Deere PowerTech Plus engine with variable-geometry turbocharger (VGT) delivers strong fuel efficiency, to move more material on less fuel. Full integration with the Intelligent Hydraulic (JD-IHC) system combines performance with smooth, low-effort control. Generous flow, arm force, and swing torque help keep things moving, while the 90/180-deg function (available on the E300’s) increases the boom-up speed for faster truck loading. In addition, the JDLink Telematics system enables dealers to respond to customer needs and diagnose and even correct many issues, without leaving the dealership. This also means software updates can be made quickly and simply, by pushing downloads over the air to equipment. NZL For additional quality auditing, a UV sensitive dye is added to the factory fluids, the equipment is run through a thermal cycle then thoroughly inspected under a black light to detect even the smallest of leaks.
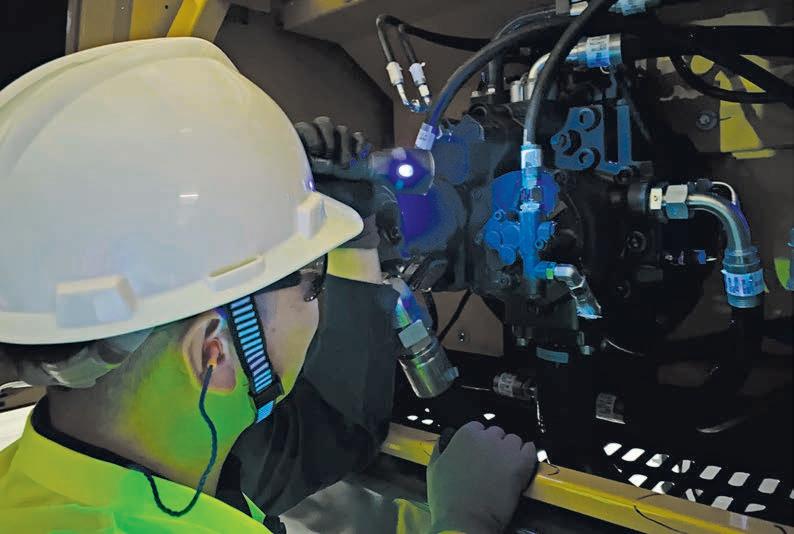
CASTROL’S NEW SUSTAINABILITY STRATEGY
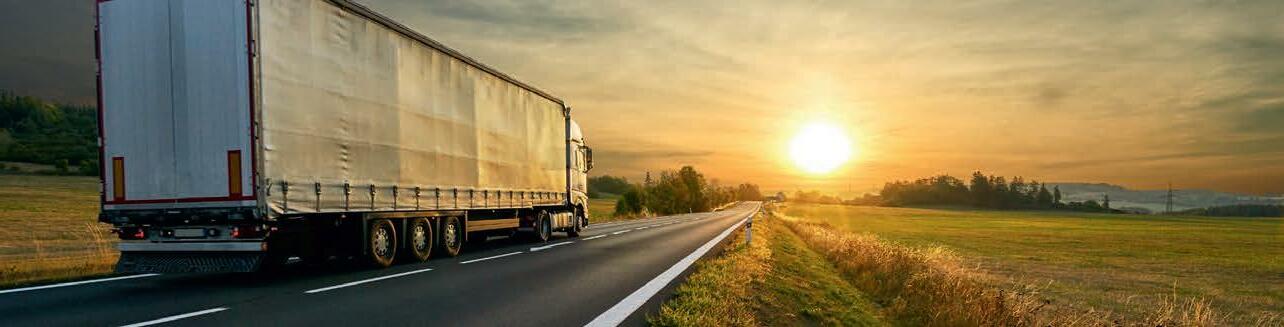
CARBON NEUTRAL PROJECTS To help fulfil its carbon neutral programme, Castrol works with bp Target Neutral who purchase carbon carbon credits that support a portfolio of carbon reduction, avoidance, and removal projects around the world. These include support for projects such as the Zhaoyuan Zhangxing wind energy scheme in China, which mitigates more than 180,000 tonnes of carbon dioxide are each year by replacing fossil fuel power. Another such project has supported investment in solar energy in India, through a large-scale project that helps provide reliable and cost-effective off-grid electricity for families and business. To date, 60,000 solar units have been distributed. BUILDING ON ACHIEVEMENTS Castrol’s Senior Vice President, Mandhir Singh, said: “PATH360
builds upon work we’ve been doing for years, pulling it all together into one integrated sustainability programme. We know that many of our customers are looking for more sustainable offers and help with their sustainability goals, and this is what this programme is designed to deliver.”
Castrol is helping to drive a more sustainable future with its recently announced PATH360 strategy
The strategy sets out aims for 2030 to save waste, reduce carbon and improve lives, not just in Australia and New Zealand, but on a global basis. Castrol became Australia’s pioneer in carbon neutral lubricants in 2016, when the premium Castrol VECTON range of diesel engine oils became the first to be certified as carbon neutral. In 2021, all Castrol products we sell in Australia and New Zealand will be committed to carbon neutrality in accordance with PAS 2060. CASTROL’S 120 YEAR FIGHT AGAINST FRICTION, CORROSION AND WEAR Close to a quarter of the world’s energy is believed to be lost to friction, corrosion, and wear as per study by Kenneth Holmberg and Ali Erdemir.
“From Castrol’s earliest days, we have delivered products that help save energy by fighting exactly these
problems,” says Jotika Prasad, Castrol Marketing Director, Australia and New Zealand. Castrol is also supporting new and growing sectors, like renewable energy and e-mobility with products and services. For example, Castrol is the first lubricant supplier in the world to offer PAS 2060-certified carbon neutral lubricants for the wind turbine industry. REDUCING PRODUCT LIFE-CYCLE CARBON EMISSIONS As well as significantly increasing its carbon neutral offers to Australian customers, Castrol is aiming to halve its own global use of virgin plastic packaging from its 2019 baseline. The PATH360 strategy is based on circular thinking, which means the company is looking at the life-cycle of its existing and new products, to see how they can be improved, extended, reused, or recycled.
said Jane Carland, General Manager Castrol Australia and New Zealand, “and we plan
to be an important partner in helping them achieve their goals and our target is to halve the net carbon intensity of our products by 2030.”
For example, three of Castrol’s plants globally moved to renewable electricity in 2020. At the same time, the company has developed new light-weight bottle designs which use less plastic, saving on a global basis 7,000 tonnes per year by 2023.
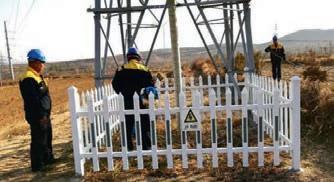
The upgraded Ponsse H8 harvester head.
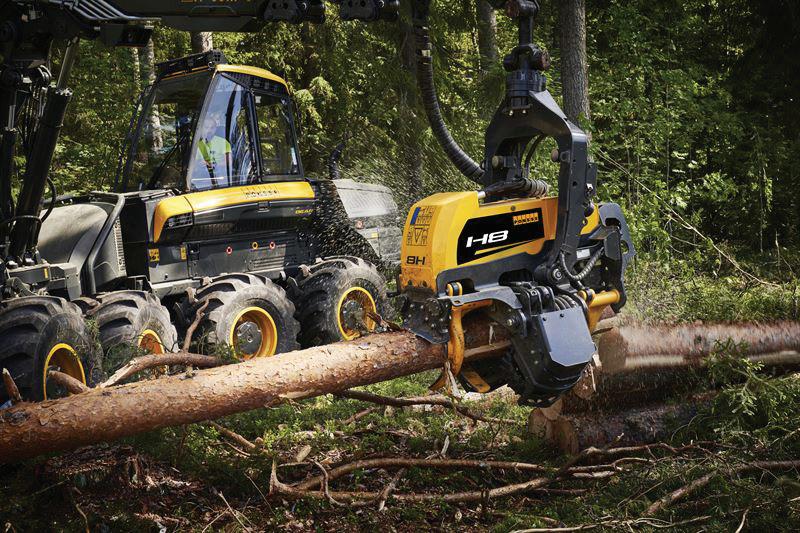
Tackling big wood
THE UPGRADED PONSSE H8 HARVESTER HEAD FEATURES
powerful feed, firm grip and a solid, agile frame.
The Active Speed feature means the operating speed can be adjusted based on tree species and stem diameter. Equipped with this new function, working with the H8 harvester head is smooth and productive, no matter what the tree diameter is.
“We have developed our product range of harvester heads actively with our customers. Many of our customers work in challenging conditions, which is why their ideas give us the best possible feedback for product development. With its completely new structure, the H8 harvester head is ideal for processing large trees,” says Product Manager for Harvester Heads, Janne Loponen.
The new head can be mounted on Ponsse Ergo and Bear, the strongest harvesters in the product range. The wide saw box area makes the head a good choice for trees with a high butt diameter. The harvester head’s structure has been designed for easy maintenance, and the frame has been built for durability.
A powerful feed, combined with a geometry that firmly supports larger stems on feed rollers, results in high productivity and fuel economy.
The automatic features of the Opti control system, developed and built by Ponsse, control the feed speed and saw movement according to the tree diameter, and ensure fast and precise sawing.
MORE WOOD IN ONE GO
The Ponsse Elephant King forwarder is the most powerful machine in Ponsse’s forwarder range. It is particularly economical and efficient when transport distances are long or transported trees are large.
“Elephant King’s technology, tested in extreme conditions in the Russian cold and the Brazilian heat, improves productivity and helps the operator keep going. The forwarder’s cabin is comfortable and safe. The powerful engine and the 20-tonne load carrying capacity guarantee that trees are transported efficiently,” says Product Manager, Forwarders, Juha Haverinen.
When the Elephant King is equipped with Ponsse Active Crane, a loader control system for forwarders, productivity in demanding conditions further improves. The system allows the operator to control grapple movements instead of individual functions, thereby lightening the operator’s workload. One lever controls the grapple height from the ground and the other controls the direction of movement.
The Elephant King forwarder with the K121 loader is the most powerful combination at worksites where load handling takes up a large part of working hours, says Mr Haverinen. The K121 loader also makes working easier at sites where large trees are handled and on steep slopes. The high slewing and lifting power, longer reach, new loader geometry and good controllability, speed up loading and unloading. NZL
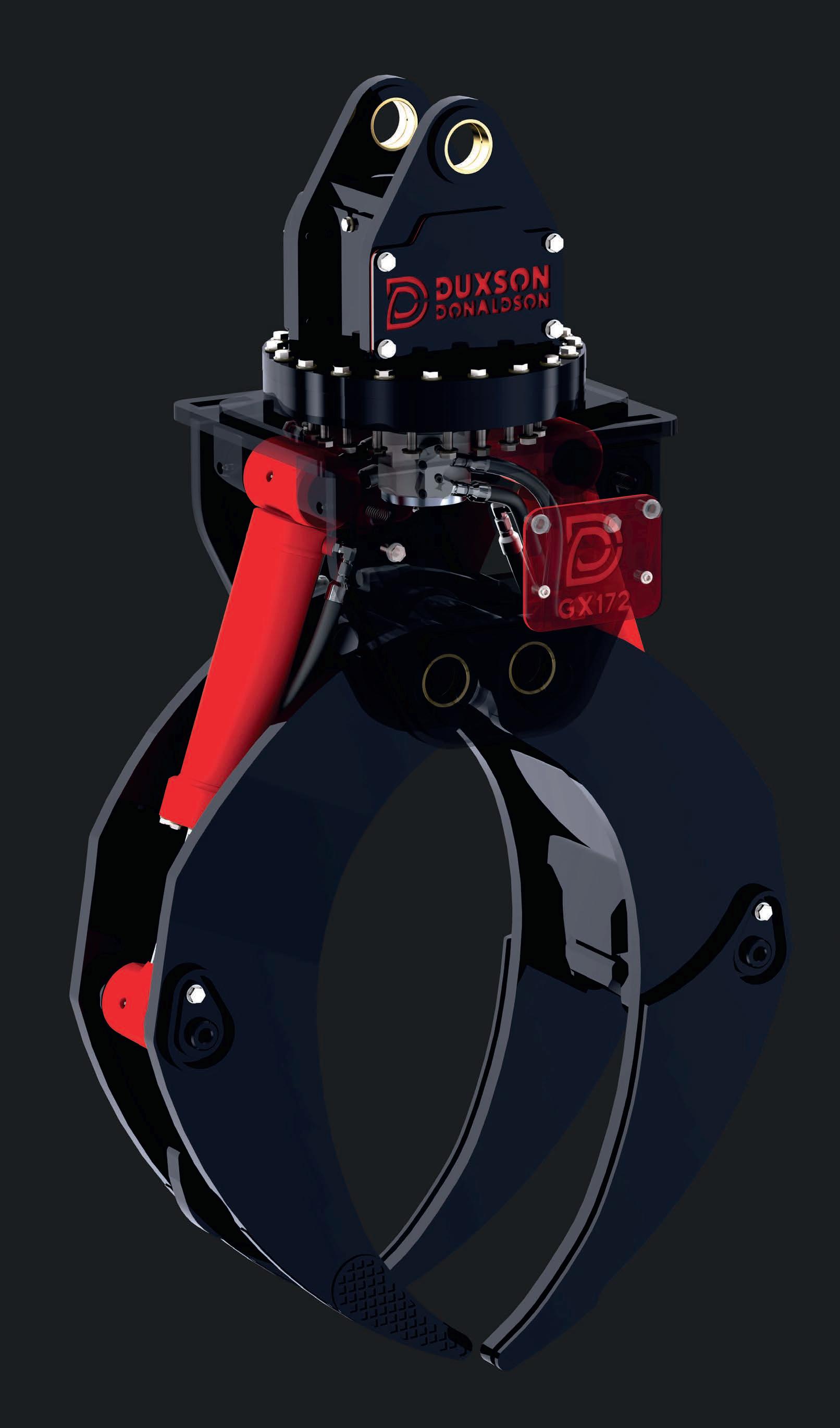
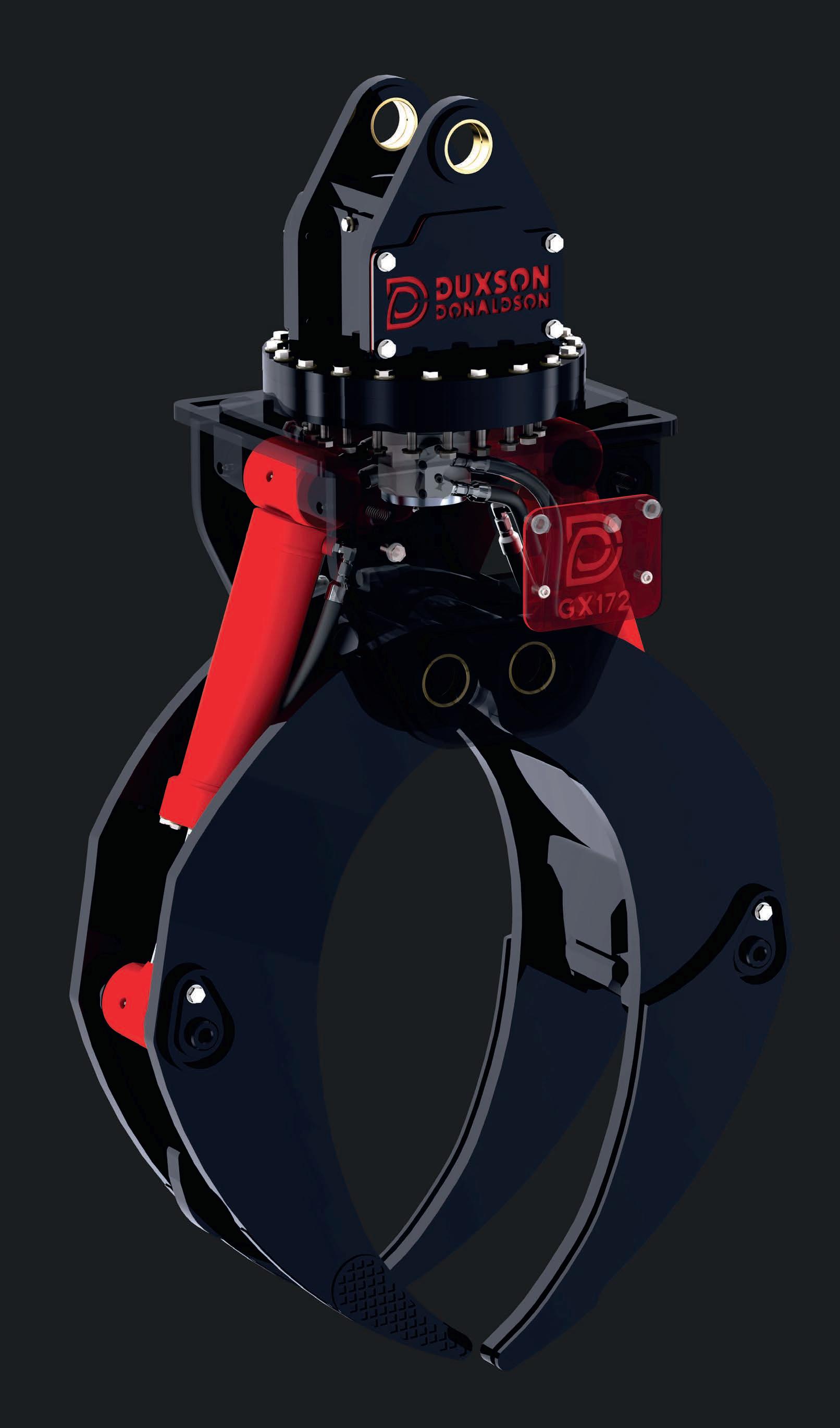
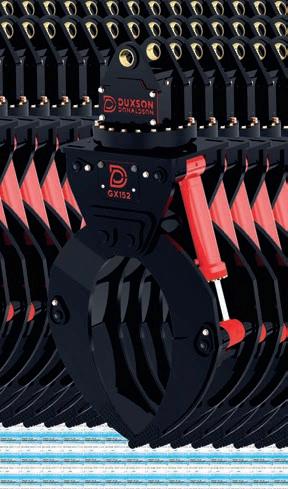
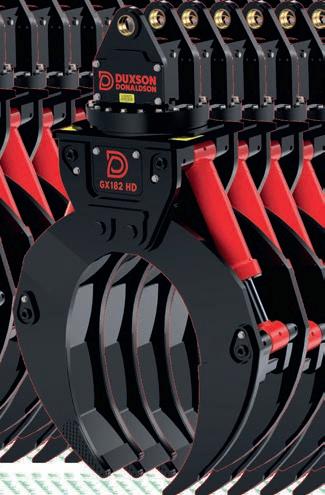
