
21 minute read
SHAW’S WIRE ROPES SPECIAL FEATURE: MACHINE OVERHAUL
from NZ Logger April 22
by nzlogger
Unique Cat Story & photos: John Ellegard swing yarder cheats death
YES, YOU READ THAT HEADLINE RIGHT – this is a story about a Caterpillar swing yarder.
Not many people know there was a Caterpillar-branded swing yarder on the market back in the day – I certainly didn’t, until I came across this particular machine now working in Northland. And then discovered that it’s actually been hiding in plain sight here in New Zealand for the past 40 years.
Well, we think this Caterpillar SY235 has been here that long, but the actual date of its arrival is not clear. It has passed through a few hands over the years after being imported brand new sometime in the 1980s by Canadian logger Brent Hewlett, who established a harvesting operation in the North Island.
It has gone through a few more hands since then, before being purchased by Palmerston North-based forestry manager, Forest360, three years ago to work with one of its Northland crews.
It was in need of some serious TLC and the next stop may well have been the graveyard. But Forest360 has a history of breathing life into old machines, especially yarders (swing and pole) and after keeping it going for a couple of years, it decided the SY235 was worth hanging onto and commissioned a 12 month-long complete overhaul.
At the end of February NZ Logger travelled north to see the end result. The reason for our special interest? This may well be the last Caterpillar SY235 still working anywhere
BANNER 1BANNER 1BANNER 1
EST 1909EST 1909EST 1909 THE SUPPLIER TO NEW ZEALAND HEAVY INDUSTRY THE SUPPLIER TO NEW ZEALAND HEAVY INDUSTRY THE SUPPLIER TO NEW ZEALAND HEAVY INDUSTRY

Fresh from the workshop, the fully rebuilt Caterpillar SY235 swing yarder is making wood recovery easier for the ACL Logging crew.
BANNER 2BANNER 1BANNER 1
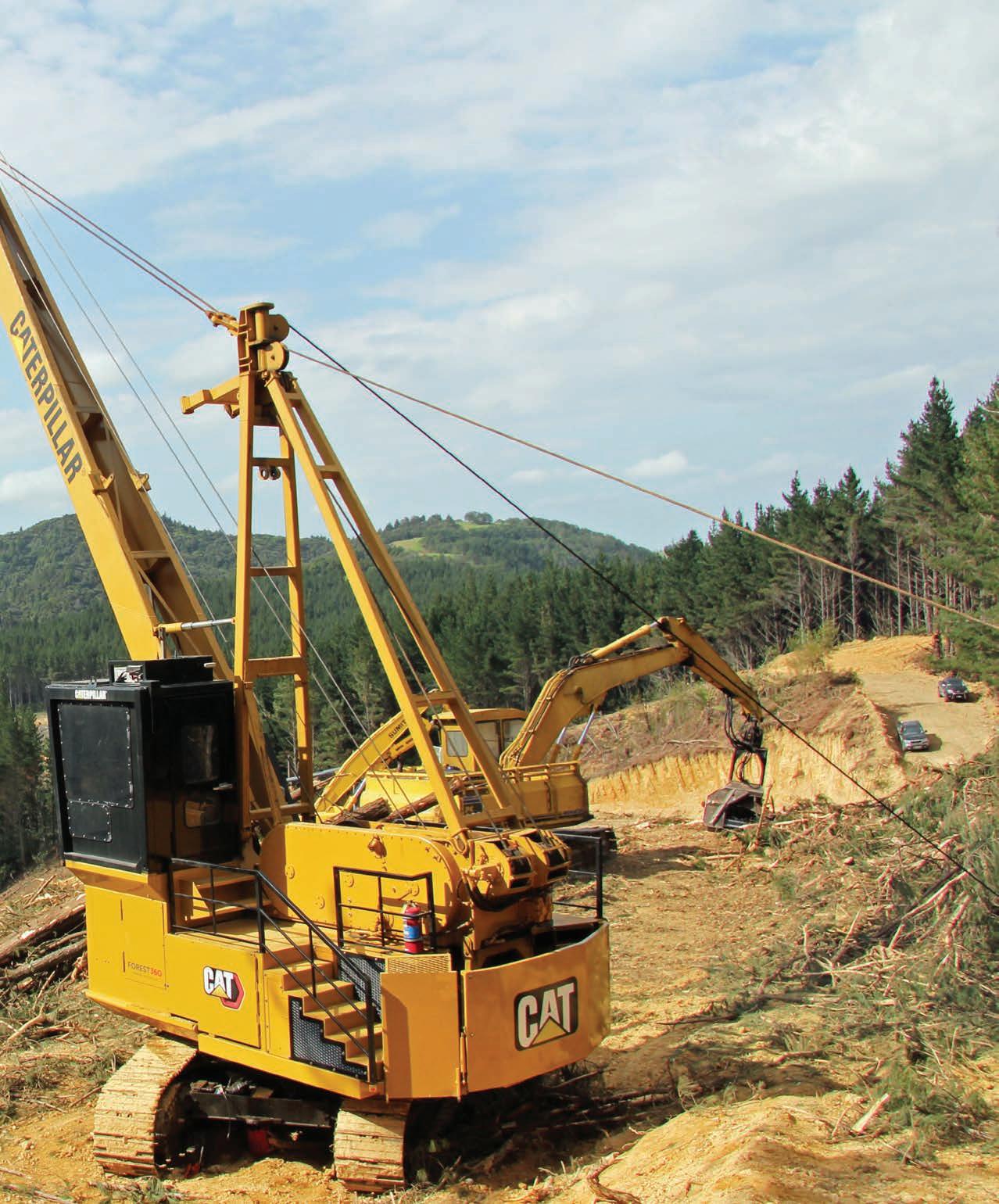

The rebuilt Caterpillar SY235 currently uses a mechanical grapple that is due to be fitted with a high-definition Falcon camera system to help the operator spot trees on the ground.
in the world, making it a rare beast.
Only seven were put into production, following the development and testing of a prototype in Canada in the early 1980s. Some 40 years later there is no record of whether any of the other six are still working. Caterpillar never made any more after that first batch, so the Kiwi SY235 is likely now one-of-a-kind.
There is precious little information on the web and what we do know has been gathered from local knowledge, plus a technical study carried out on the prototype by the Forest
Engineering Research Institute of Canada,
FERIC, (the forerunner of Canada’s current forestry R&D organisation, FPInnovations).
According to the FERIC report, the SY235 was the result of a 1979 collaboration between
Caterpillar, the Finning Tractor & Equipment
Company and Lantec Industries. The aim was to build a lightweight, all-hydraulic, high production swing yarder to work on compact and environmentally sensitive sites, similar to the PeeWee yarder that the USDA Forest
Service and Lantec had developed for thinning coastal stands.
Caterpillar supplied its 235 excavator undercarriage, the hydrostatic drive and associated hydraulic pumps, Lantec provided the PeeWee winch set, boom and gantry, while Finning assembled the whole thing and BANNER 4BANNER 1BANNER 1 provided technical assistance.
Interesting technical innovations built into the SY235 included the fully interlocking three-drum winch set, which was considered a unique feature at the time. Also, the walking guy line sheaves on the gantry that swivel independently for quicker direction changes.
Up in the cab, the controls were laid out to mimic those of an excavator, with all movements worked from the two joysticks. It was a cool machine in its day, but the SY235 did have some quirks that hampered the operation – we’ll get to those shortly.
Battered and bruised
Dan Gaddum, Managing Director of Forest360, explains what drew his company’s attention to the Caterpillar SY235: “It just looked like a useful piece of kit. We bought the 235 along with a Halla Harvestline from Shane McGuire of Mana Logging in Gisborne.
“Prior to that it was owned by Gus Thompson who, we understand, purchased it after it had been sitting in Rotorua for a while, where it had been working in the GSL Eucalypt.
“We’ve always had this philosophy of trying to support contractors into good kit to be able to do the job, so we invest in the machine then lease it out. We’ve done a lot of haulers this way because of the size of the investment required.
“When we bought this one, we could see that in the right situation it could be very useful. In an effort to keep our costs down, like a lot of our gear, it has to be a reasonably low capital outlay and that’s great on the one hand, but bad on the other because there are challenges around reliability, and even things like safety start to become an issue due to the age/design.”
The SY235 was purchased with an eye to using it on the broken hill country of Northland, to assist Forest360’s local contractor, ACL Logging, overcome the challenges of recovering wood from steep, hard-to-log sites.
Although it was battered and bruised, the SY235 was still in working order and was pressed into service with one of three logging crews run by ACL.
The owner of ACL, Lance Aukett, also doubles as the regional manager of Forest360 operations in Northland. Formerly a civil contractor, who got into forestry 15 years ago when the Global Financial Collapse severely impacted his business, Lance has made a habit of getting the most out of whatever equipment he has to hand. But he admits that the SY235 did test his fortitude.
“It arrived as an old beaten-up, end-of-life machine,” he says.
Apart from being “bent and buckled”, there was a major issue with getting the SY235 onto and off the transporter, says Lance.
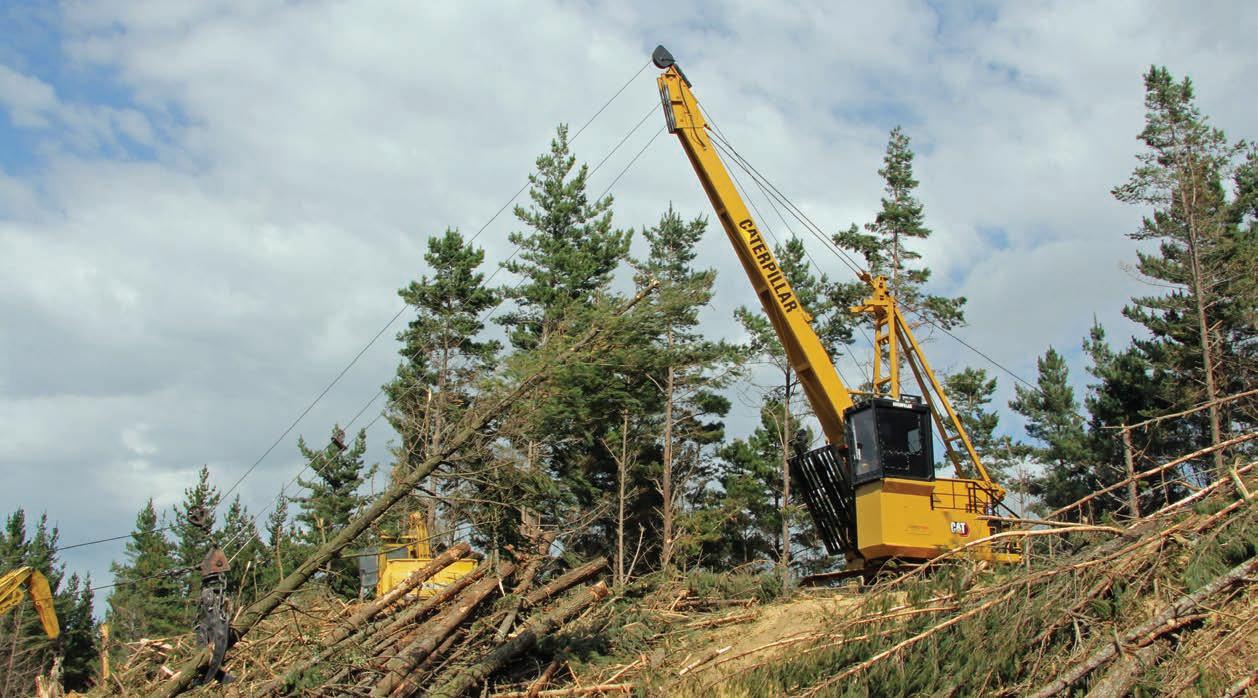
SERIOUS POWER FOR BIG TIME LOGGERS
ALWAYS SWING A BIG STICK
“There was no way to walk the machine when we got it up here, we couldn’t even get it off the transporter without a lot of drama. With the boom and gantry lowered you literally put the cab over and somehow had to sit in the cab to push the pedals to get it onto the transporter. You ended up standing on the inside of the roof, pushing the pedals. There was not a lot of control. I don’t know how they shifted it in the past. It was bloody dangerous.
“We ended up putting in five metres of hydraulic lines that connected to a hand-held unit – I wouldn’t even describe it as a remote control as it was pretty primitive – just to be able to walk it from outside the cab. All to get it off the transporter.
“Using that primitive hand-held was interesting because things on the machine would start working by themselves, like guy ropes or whatever, because there was stuff touching other controls.
“Then you had to get a digger in to lift the cab, which rocked over with a real thud because of all the weight on it. That just added to the drama.”
Compounding the situation was the effort needed to raise the boom and gantry using chains with grapples, requiring one of the crew to climb up the precarious structure and secure them with locking pins. “The potential for someone to get seriously hurt was very high,” reckons Dan.
“When you start looking at things in regard to working at height, with everything being so manual, essentially we should have had guys fitted with harnesses or set up scaffolding around it to assemble this kit and we decided that we can’t do that anymore,” he adds.
Better access
The decision was made to decommission the SY235, send it to the workshop and rebuild it into a more user-friendly, up-to-date yarder.
“The work was done by Nick Hill in his yard and our mechanic Kevin Griffiths, who also happens to be my stepfather who has worked for us for around 13 years – and 12 months later it came out looking like new,” says Lance.
“It’s very original in terms of the base machine. The gantry is obviously original. The cab is original but we pulled all the guarding bars off and replaced them with Marguard so you’ve got great vision from the operator’s seat now.
“The track motors, slew gear, pumps, winches, they’re all original but they have been refurbished or rebuilt. It’s got a new Cat 3306 engine, basically replacing like-for-like and it’s a Tier 2. Hydrostatic transmission is the same. Even the interlocking mechanism for the winches is the same as before.
“The bodywork was bent and buckled through years of use and misuse, so we had to straighten out a lot of the metal. And we made some changes, such as fully re-guarding and fitting a rear drop-down plate that opens up to the engine. Like, we couldn’t get the engine out, so we had to cut parts of the framework at the back that had the gantry on. Now we’ve got much better access and that rear plate can be lowered and raised with hydraulic rams, so there’s good access to the engine now.”
Hydraulic rams were also fitted to the boom and gantry so that these can be raised and lowered at the push of a button. Same with the tilting cab.
There’s also much better access to the rear of the cab through stairs built into the bodywork, along with a set of hydraulically folding steps that make it so much easier to climb up from ground level. For safety, the yarder will not operate until those steps are raised.
The cab itself remains fairly basic, with felt covering some of the inside metal surfaces and rubber matting on the floor. But it is very roomy, with space for two people to stand behind the operator’s seat.
BANNER 3BANNER 1BANNER 1
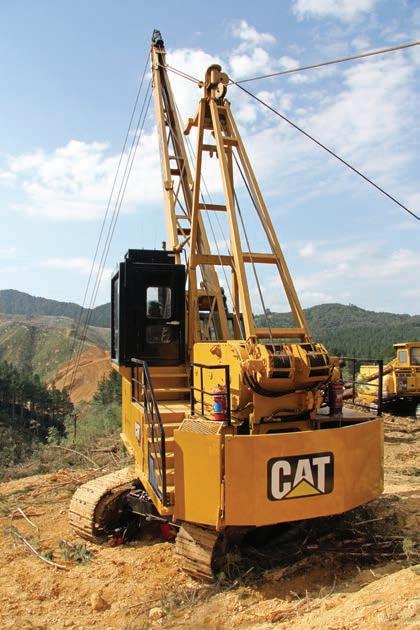
Above: One of just seven built by a Caterpillar-led consortium, this SY235 swing yarder may be the last survivor. Below left: The battered bodywork has been totally reconstructed and now features stairs up to the rear of the cab and hydraulically folding steps for easy access from the ground. Below right: Operator, Carl Sadgrove, demonstrates the fully remote control unit that controls the walking and assembly of the cab, boom and crane from the ground.

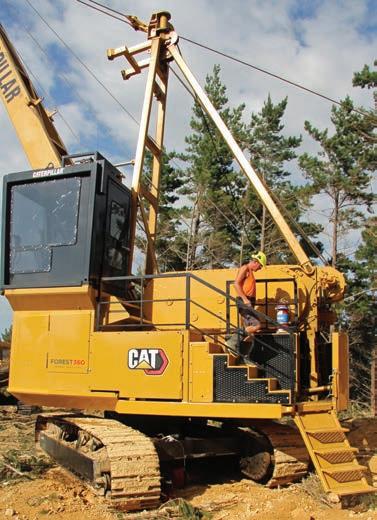
SERIOUS POWER BIG TIME LOGGERS
The controls haven’t changed. They’re all still hydraulic, working off the four-way joysticks as before, with a foot pedal on the extreme left for controlling the speed of the ropes. The operator has a panel of switches on the front-left pillar to control the winches. On the front-right pillar is a cluster of gauges to provide information on items such as engine oil pressure, water temperature, a voltmeter, etc.
In a nod to the crew’s initial answer to the challenge of walking the machine on and off the transporter, they’ve now fitted a sophisticated fully-wireless remote-control system to operate the machine from the ground in place of the rudimentary hydraulic hose handset.
Lance says: “You can stand beside the machine, push the button on the remote and it will start up, put the cab down because it now has hydraulic rams, then you can walk it off the transporter and put the boom up using the remote. No one hops on until the mast is up and the gantry slides out and all you do is put two pins in and pull the guy ropes out and start pulling wood. It’s a one-person set-up.”
Dan concurs, adding: “It’s a lot easier and a lot safer. Guys climbing around that thing, dealing with chains and bits of steel swinging around, that’s all history. Fiona Ewing (of the Forest Industry Safety Council) talks about ‘safety by design’ and that’s the sort of thing we were looking to do and we’ve achieved it here.
“And we’ve also turned it back into a reliable and productive piece of equipment. Just about every hydraulic hose has been pulled off and
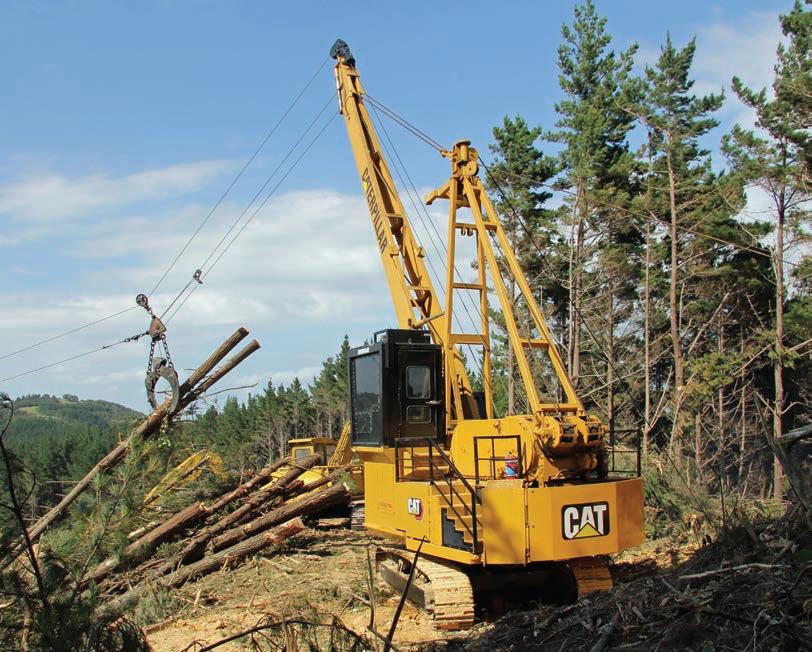
Designed as a compact swing yarder to work in compact, environmentally fragile areas, the Caterpillar SY235 was said to be quite advanced for its time. Having survived around 40 years in the bush, the 12-month long rebuild will ensure it goes on working for many more years.
NEW NEW $2,839* $2,839*
*Price includes 24inch Bar and Chain *Price includes 24inch Bar and Chain

HUSQVARNA 592 XP HUSQVARNA 592 XP ® ®
90cc worth of unparalleled power in an easily manoeuvred and lightweight package. An X-Torq® engine with outstanding torque and acceleration and, to top it off, a razor-sharp X-CUT® chain perfectly in tune with your saw. The end result is best in class 90cc worth of unparalleled power in an easily manoeuvred and lightweight package. An X-Torq® engine with outstanding torque cutting capacity, making you better, faster, providing you with unparalleled levels of productivity. In short, a better cutting and acceleration and, to top it off, a razor-sharp X-CUT® chain perfectly in tune with your saw. The end result is best in class experience. Scan the QR code to read more about new Husqvarna 592 XP®, cutting capacity tests.husqvarna.com / 90cc cutting capacity, making you better, faster, providing you with unparalleled levels of productivity. In short, a better cutting experience. Scan the QR code to read more about new Husqvarna 592 XP®, cutting capacity tests.husqvarna.com / 90cc

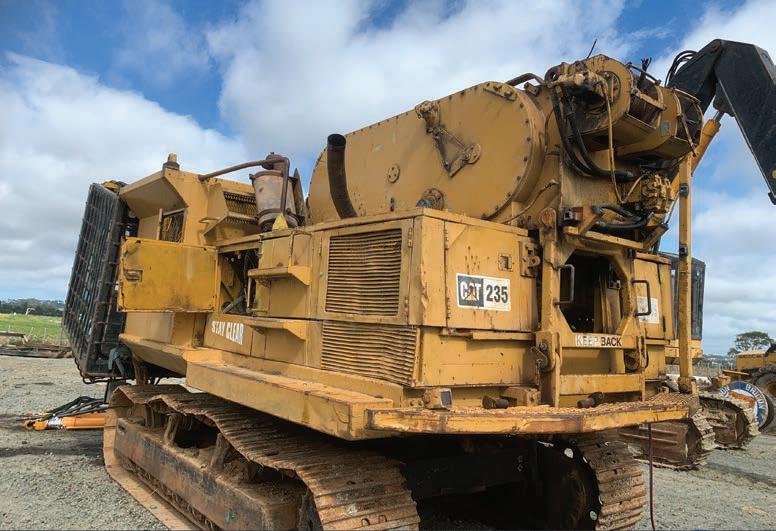
Above left: The battered and beaten-up Caterpillar SY235 prior to its full rebuild – there was no way to remove the engine from either the sides or the rear. Above right: Most of the original structure of the Caterpillar SY235 has been retained in the rebuild.
replaced, the pumps have been reconditioned. Still fully hydraulic, not air over hydraulic, even the controls in the cab – no electronics. The same unlagged PeeWee drum set. Running ¾” swaged ropes on the big drums. It’s the same, but better.”
Lance chips in: “As the boys say, it’s not a Madill 123 or whatever, but it’s probably more current now than a lot of machines out there. With all that integrated gear for walking and all that stuff, it’s right up-to-date.”
Weighing in at around 55 tonnes, the rejuvenated Caterpillar SY235 is just the right piece of kit for tackling the current harvesting job on the Brynderwyn Hills, just south of Whangarei.
Reaching this site was another first for me; the first time I’ve ever had to access a forest directly through a working quarry, manoeuvring in between massive dump trucks running up and down the roads. It’s part of the Atlas Concrete quarry complex situated on the southern side of the Brynderwyns.
Lance explains that Atlas owns two quarries up here and two forests, comprising a total of 230 hectares of pines. The site his crew is harvesting is the steeper of the two forestry blocks and it’s very broken, with gullies and ridges criss-crossing at all sorts of angles.
Best forestry roads
In terms of roading challenges, working in a quarry is woodlot utopia, says Dan. This forest has some of the best forestry roads to be found anywhere in New Zealand, all built by Atlas. When the harvesting crew wants a new track created, they just get on the radio to the Atlas team and their equipment arrives in minutes to take charge.
The trees were planted 23 years ago, tightly stocked and then pretty much left to fend for themselves. They are over-crowded and the piece size is very small compared to trees found in other forests around Northland.
The crew started logging it 18 months ago when prices were very high to maximise the returns and even though there was a dip towards the end of last year, prices have rebounded and it’s still paying off, although the skyrocketing fuel prices are eating into the budget.
“We looked at whether we could hold out and let it grow more but it wasn’t really worth it because it’s so tightly stocked,” says Lance.
“So it was about coming up with the right systems to get it done properly and having the SY235 working in here now is going to help make a difference.” BANNER 5BANNER 1BANNER 1
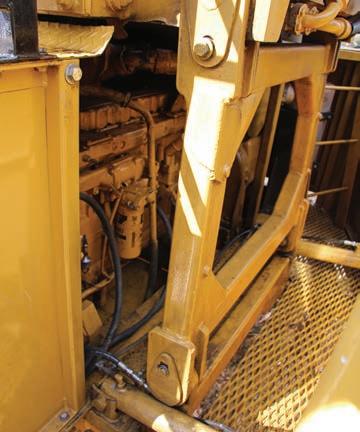
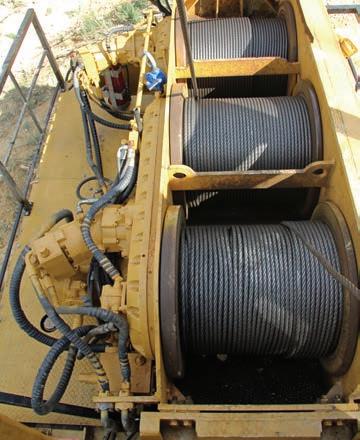
Above left: The new Cat 3306 engine can now be easily accessed from the opened-up rear of the body. Above right: The original PeeWee winch set, complete with interlocking feature, was regarded as an innovation back in the early 1980s.
MADE IN CANADA FOR NZ CONDITIONS
The setting where it is currently working is the first since the SY235 arrived, apart from a trial carried out in another part of the forest to check everything was running correctly.
The main line is stretching out over a deep gully where it connects to a backline machine on the opposite hill, more than 300 metres away.
Currently, it is running a mechanical grapple without the benefit of a motorised carriage or even a camera system to help spot the trees on the gully floor.
“We’ve got some camera gear for it (a Falcon HD system) but haven’t quite got around to putting it on yet, so we do use a spotter when needed,” says Lance.
Members of the crew are being rotated through the SY235 cab so that there is always someone available with experience to operate it through holidays, sickness and COVID isolation requirements. 30-year forestry veteran, Carl Sadgrove, is at the controls today and after a little over a week he admits he is still getting used to how the SY235 works. He’s operated a range of machines in his time, including tower haulers, swing yarders and also Harvestlines (there’s one working up here with ACL Logging).
“It’s like a Harvestline incorporated into a swing yarder – with a bit more height and swing,” says Carl.
“It’s all mechanical, all hydraulic. But in saying that it’s quite a nice machine, it is smooth. In a machine fitted with air lines you can get a lot of fluctuation and the controls can feel very touchy.”
He’s enjoying the simplified joystick controls – moving the right lever forward and backward lowers and raises interlock (haulback) tension, while left-to-right controls the slackpulling function, along with a grapple opening and closing switch; moving the left lever forward and backward controls the speed and direction of the yarder primary drive and moving it left-toright works the swing and line direction.
“The remote control for walking is really good,” he adds. “Being outside the cab you can see everything going on around the machine, which is much better.”
One of the things that makes this yarder work so well is the interlock system on the drums. When the interlock is set, it allows the operator to take up one drum and pay cable out of another drum and provide a predictable tension between the two. The line pulls and speeds might be a bit lower as a result, but it has the advantage of reducing wear and tear. A lower line pull also reduces the chance of pulling over the tail-hold machine.
The hydraulic interlock on the SY235 is said to have inspired others to use the same technology on their yarder designs over the years.
The ACL Logging team is looking forward to seeing what they can wrangle out of their newly upgraded swing yarder, although Lance admits: “It’s still very early days and in this setting it’s not easy, especially in this broken country, which makes it hard with having to move it around so much.
“We’re probably sitting at around 130 tonnes a day right now and the wood is nothing flash - mind you this is probably the best wood that we’ve come into in the whole block. It would be good to get into a really nice forest and see how it goes.”
For Forest360, the cost of the overhaul has already proved the value of the exercise, with Dan Gaddum noting: “The cost of the upgraded machine is about one-third of the cost of a new Harvestline.
“No one is saying the productivity is the same, but it would be a lot better than one-third!” NZL
Forest360’s Dan Gaddum (left), with Lance Aukett of ACL Logging.
1: Operator, Carl Sadgrove, now has a great view from the cab following the replacement of the guarding bars with Marguard protective glass. 2: The SY235 is controlled through the pair of joysticks. 3: Switches for the different winches are easily accessed from this panel on the front-left pillar. 4: Key information on the swing yarder’s systems are displayed on these gauges on the front-right pillar.
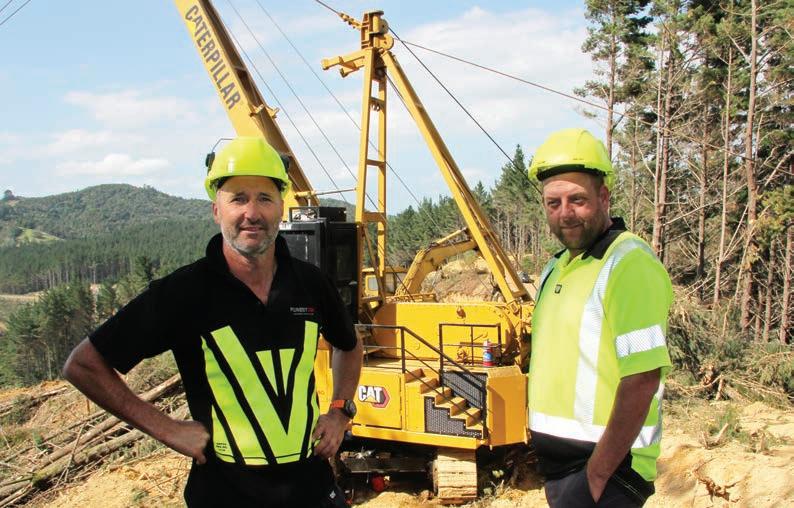
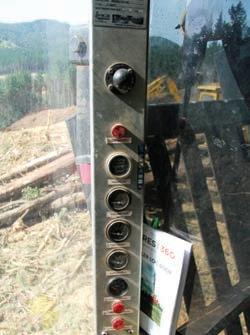
1
BANNER 1BANNER 1BANNER 1
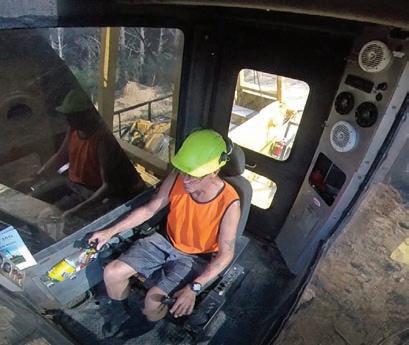
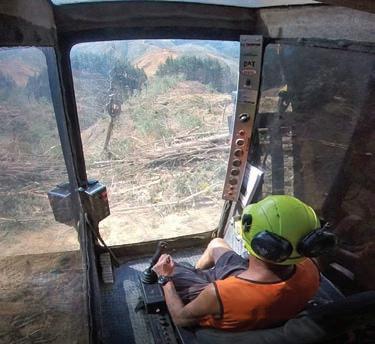
2 3 4
EST 1909EST 1909EST 1909 THE SUPPLIER TO NEW ZEALAND HEAVY INDUSTRY THE SUPPLIER TO NEW ZEALAND HEAVY INDUSTRY THE SUPPLIER TO NEW ZEALAND HEAVY INDUSTRY

SPEC IFICATION S SPECIFICATIONS – CATERPILLAR SY235 SWING YARDER
ENGINE
6-cylinder, 10.5-litre, Caterpillar 3306, Tier II Bore / stroke Power Max torque Max travel speed
HYDRAULICS 121mm x 152mm 145kW (195hp) @ 2,000rpm N/A 3.8km/h
Travel Swing Main pump flow Swing pump flow Swing speed
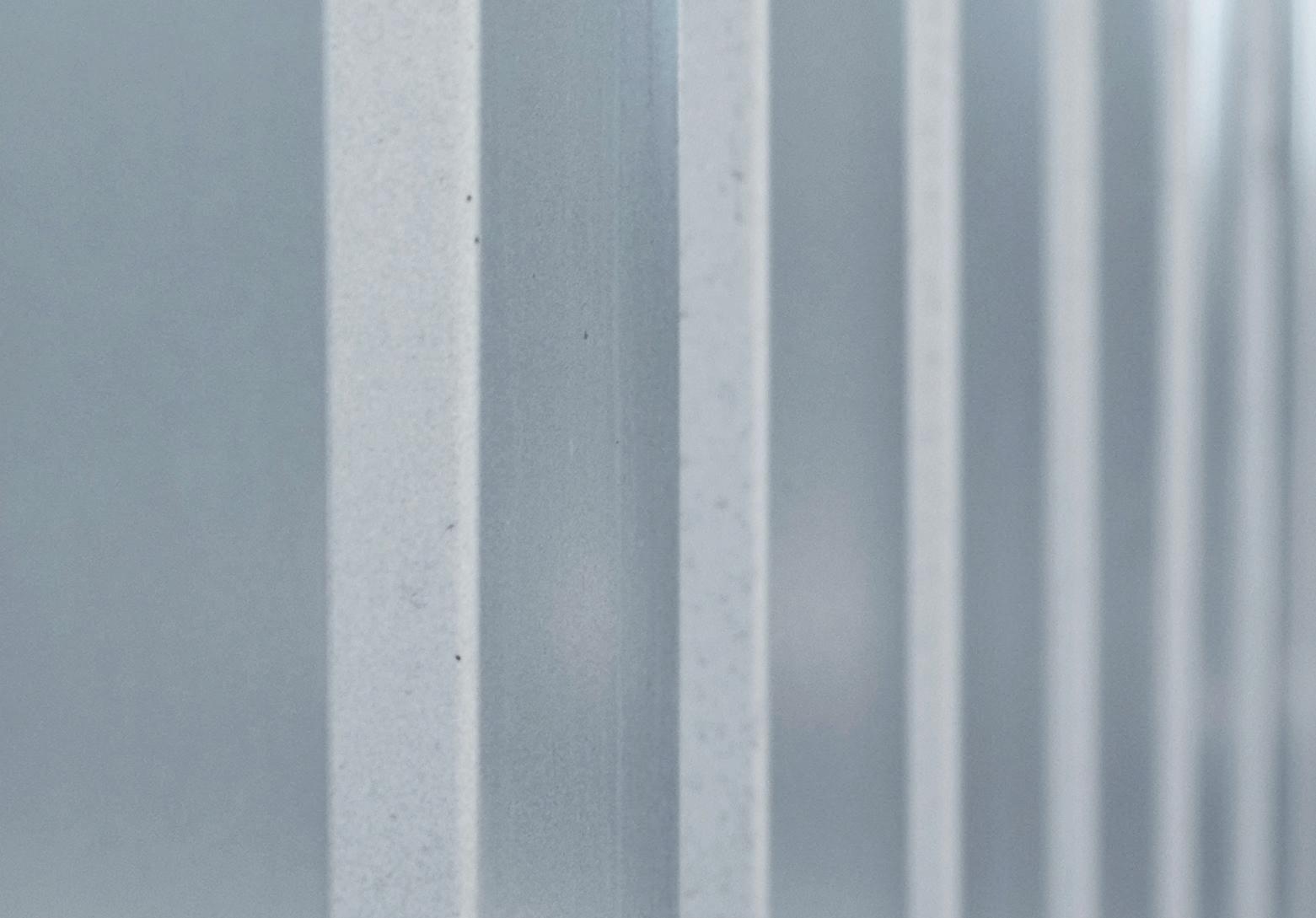
MAST & BOOM
Height Reach 2 variable displacement axial piston motors 1 double section gear pump 365Lpm x 2 223Lpm 5.5 (rpm)
13.716 metres 5.740 metres
WINCH SET
Main Drum: • Drum Capacity 400 metres (unlagged) • 19mm (3/4-inch) swage rope.
Slackpulling Drum: • Drum Capacity 400 metres (unlagged) • 19mm (3/4-inch) swage rope. Haulback Drum: • Drum Capacity 800 metres (unlagged) • 19mm (3/4-inch) swage rope.
Strawline Winch: • Drum Capacity 1,097 metres • 8mm (5/16-inch) swage rope
GRAPPLE
Unknown design and size
REFILL CAPACITIES (LITRES)
Fuel tank Engine coolant Engine oil Hydraulic system
DIMENSIONS (MM)
Shipping height Shipping width Ground clearance Tail swing radius Track length Operating weight 397 43.5 27.4 720
3,760 3,327 700 3,500mm 5,033 55,000kg (approx.)
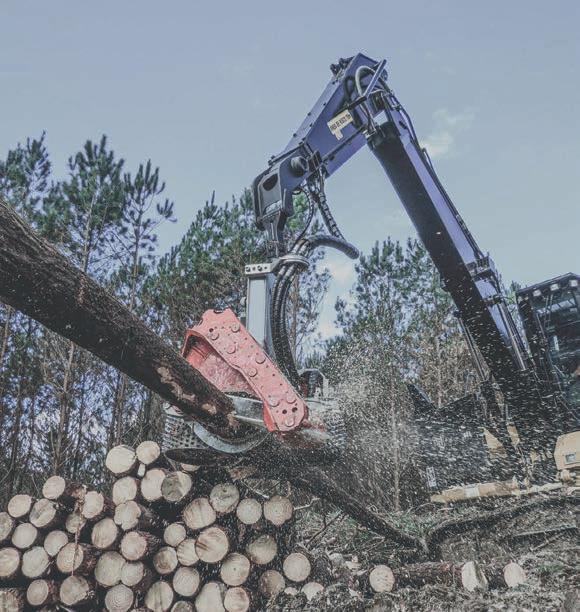
NZ Premium Wear-Part Dealer
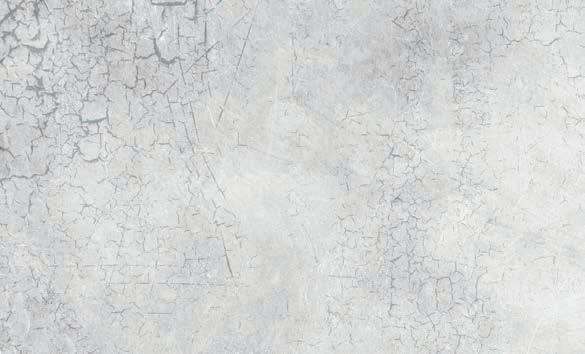
With Our Award-Winning Superseal® Chains, Expect...
Zero Seizing & Reduced Internal Wear Reduced External Bush & Sprocket Wear 30% Extended Chain Life
FREE BOLTUPS
That’s right! We’re offering FREE bolt-ups on all track group orders before 30 April 2022! Just mention NZ Logger Magazine.
0800 551 201 mainlinetrack.co.nz
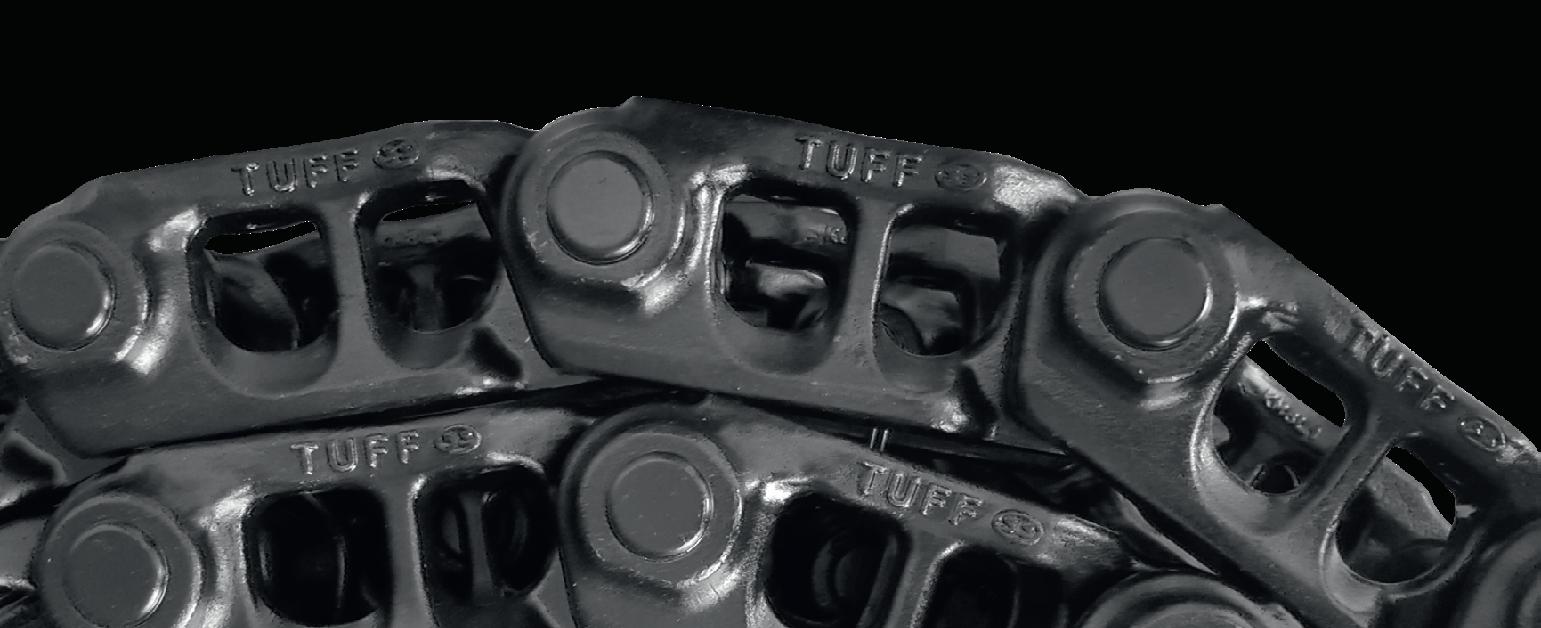
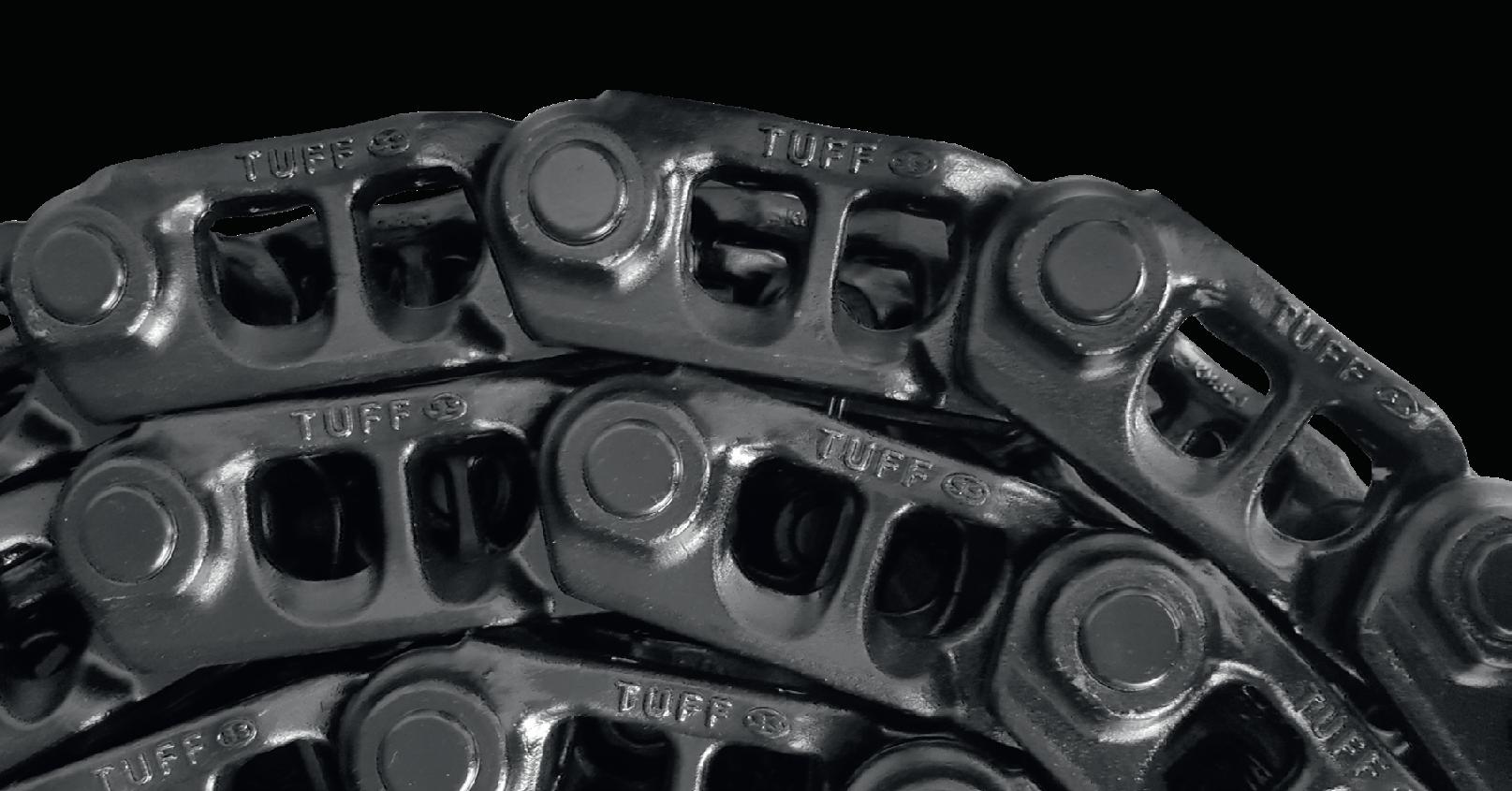
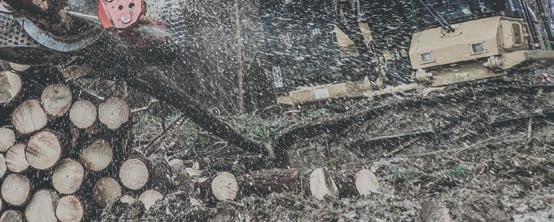
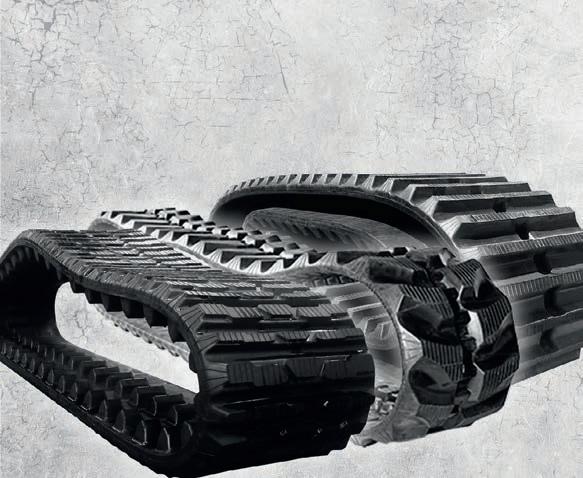
ALWAYS SWING A BIG STICK ALWAYS SWING A BIG STICK
CONTACT JONNY EDWARDS FOR MORE DETAILS WOODCUTTER@SHAWS.CO.NZ CONTACT JONNY EDWARDS FOR MORE DETAILS WOODCUTTER@SHAWS.CO.NZ | | 021 944 894 021 944 894

CUSTOMISE YOUR KAIWAKA GEAR CUSTOMISE YOUR KAIWAKA GEAR
RANGE OF WET WEATHER GEAR WILL KEEP YOU DRY AS RANGE OF WET WEATHER GEAR WILL KEEP YOU DRY AS
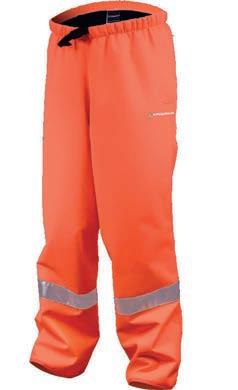
FLEXIBLE FLEXIBLE LIGHTWEIGHT LIGHTWEIGHT TEAR RESISTANCE TEAR RESISTANCE PERFECT FOR FORESTRY USE PERFECT FOR FORESTRY USE HEAVY DUTY TWO WAY ZIPPERS HEAVY DUTY TWO WAY ZIPPERS INTERNAL WATERPROOF POCKETS INTERNAL WATERPROOF POCKETS NO SPLIT SEAM LIFETIME GUARANTEE NO SPLIT SEAM LIFETIME GUARANTEE WATERPROOF OIL/CHEMICAL RESISTANT WATERPROOF OIL/CHEMICAL RESISTANT REFLECTIVE TAPE ON EACH GARMENT REFLECTIVE TAPE ON EACH GARMENT
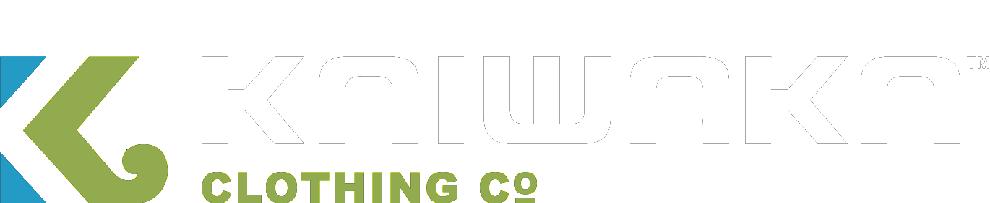
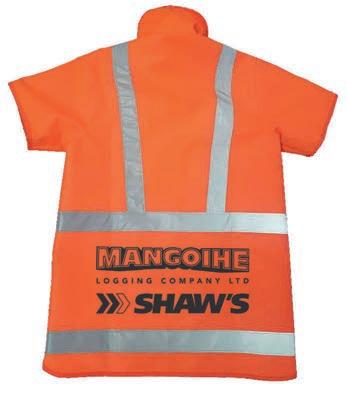
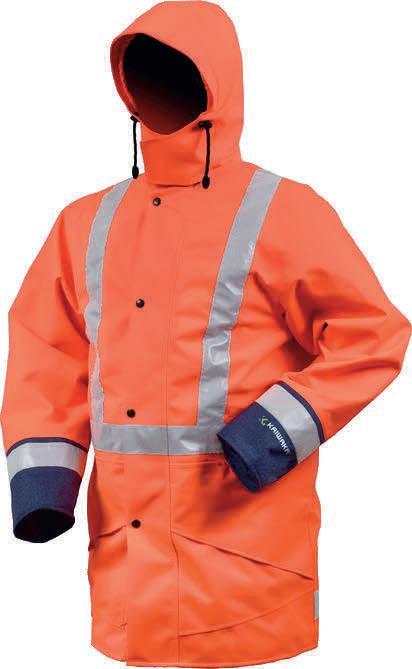