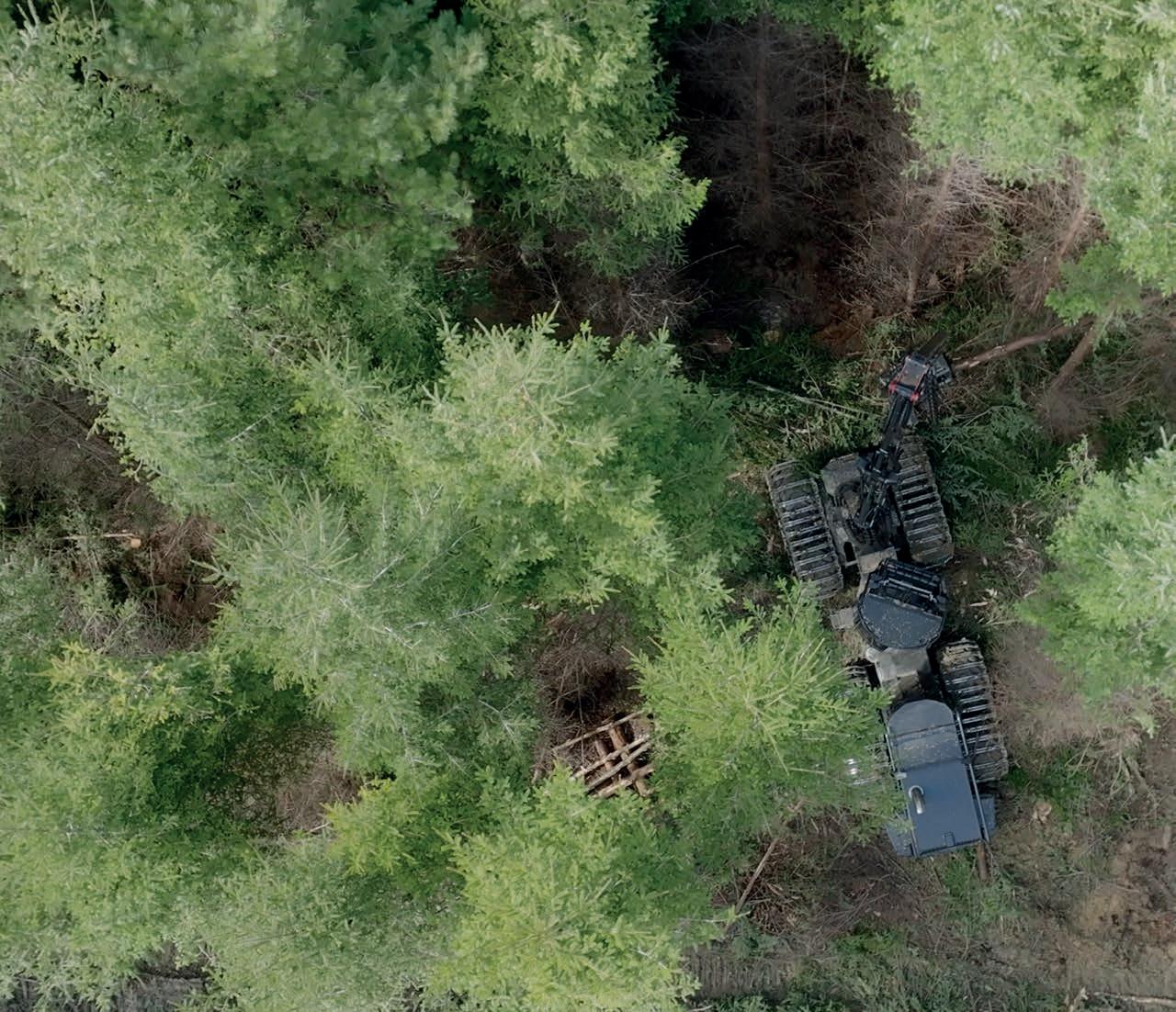
7 minute read
SPECIAL FEATURE
by nzlogger
Hybrid harvesting HIGHLIGHTS
Story: Richard Stringfellow, Toroawhi/Worker Champion, Safetree
THE PAINTWORK ON NEW ZEALAND’S
first diesel-electric harvester is still shiny after nearly a year of hard work from this machine that’s been in the country since December. (NZ Logger first took a look at this Logset 8H GTE diesel-electric hybrid wheeled harvester from Finland when we took it for a run on an Iron Test earlier this year.) Josh Hurring, from Mike Hurring Logging & Contracting in Balclutha says that good looks aren’t the only attractive feature of this new hybrid.
“On the whole, we’ve found it’s a lot more economic to run. It’s a lot better for the environment and it has features that add to the safety of the operator,” Josh says.
There’s a battery in the back and when the machine travels along, that charges the battery. When the machine is harvesting it uses electricity from the battery to power the hydraulics that run the feed rollers and saws. The diesel can kick in when needed, but it’s majority electric while harvesting.
Josh says the company has discovered that being a hybrid makes the machine far more economical to run: “The hybrid feature saves a lot of fuel. The machine burns about 10 litres of diesel an hour, compared with the normal diesel machines that are running about 18 litres to 20 litres sometimes.”
With diesel prices where they are today, that saving is very helpful, he adds.
Another environmental benefit is that the machine is eight-wheel drive, compared to Hurring’s other wheeled-harvesters, which are six-wheeled.
“Being eight-wheeled gives it more traction, so it’s more stable. It allows the machine to go further and cause less ground disturbance. It’s a lot less messy and a lot tidier,” says Josh.
The company has put the machine into a production thinning crew, paired up with another harvester and two forwarders.
“These production thinning machines allow us to recover all the wood felled during thinning, compared with thinning to waste manually where the trees sit on the floor and rot away.
“They go through the blocks, pick out the trees, fell them and then cut them into log grades. Then the forwarders come through and sort them and offload them at the skid where they’re sorted again and put onto the truck. So, essentially, they go through three lots of quality control before they get to the port or sawmill.”
As a result, wood that would have been left to waste on the ground (and possibly cause environmental issues later on) brings in a financial return.
“We had one customer, a farmer, who was quoted about $10,000-$20,000 to
Above: The Logset 8H GTE dieselelectric hybrid wheeled harvester. Top right: Machine operator, Logan Bennett, using the retractable steps into the cab of the Logset 8H GTE and shown in the cab (below). Middle: View from the cab of the machine.
Bottom: The machine is operating in a production thinning crew.
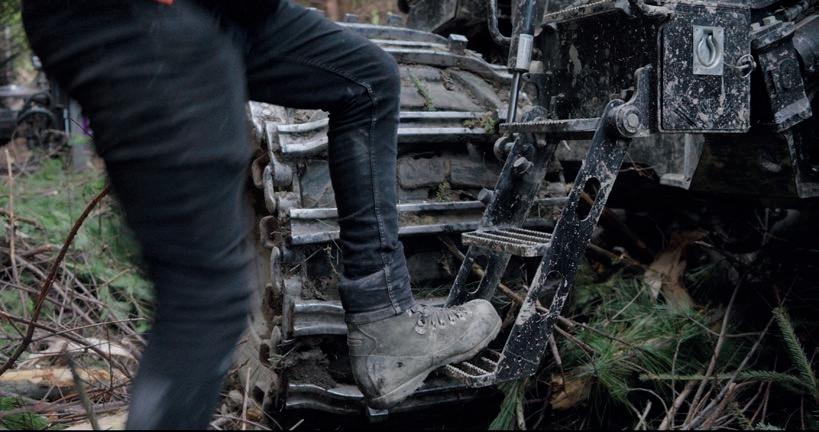


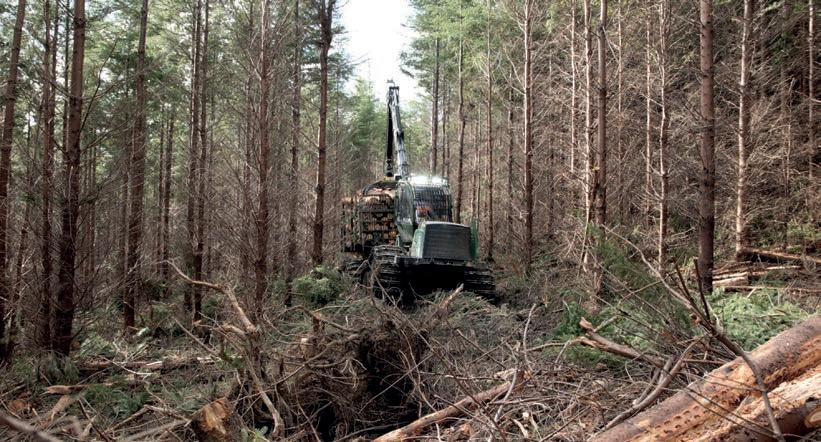

Above: The Logset 8H GTE in action. Right: Josh Hurring, Health and Safety Manager at Mike Hurring Logging & Contracting. Bottom: Workshop apprentice, Zak Phillips, tries out using real machines under Josh's guidance.
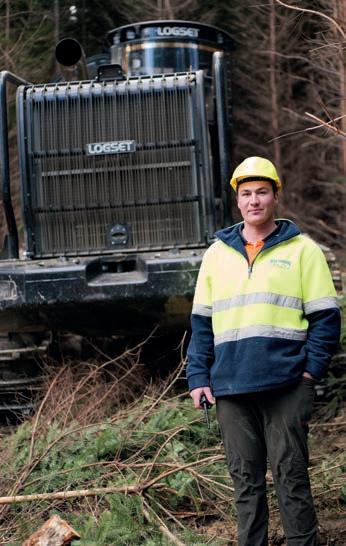
get his block thinned to waste. We went in with our machines and extracted the wood and got a return of about the same amount. The other big benefit of thinning with machines, rather than manually, is safety,” Josh says.
“If a stem falls on the boom, it scratches the paint. Whereas if a tree comes down and hits someone, it could be very serious.”
The machine’s thinning head has a few differences to other heads commonly seen in New Zealand. The feed rollers are a set of discs so they can be more easily changed out. There is also no topping saw.
Josh says the hybrid has other features that help look after the operators: “There are doors on both sides, rather than an escape hatch. So, in the event of an emergency, the operator can get out either side of the machine.”
As soon as the operator gets in the machine, the steps automatically fold back up. Then when the machine shuts down, they come straight back out again.
“So, there’s always easy access and three points of contact when the operator is getting in and out of the machine.”
This feature is important because industry statistics show that injuries from falling or jumping off machines are relatively common in forestry.
“All these features add up to make the machines safer for operators,” Josh says. “As a whole, we’ve found this machine a lot more economical to run, a lot better for the environment and better for the operator.”
Future forward
Of course, it’s no good having great machinery without the skills to put it to good use. Mike Hurring Training School was established to try to increase the pool of skilled workers.
“We’ve always had quite a heavily trained workforce and there was a bit of a tendency for other companies to cherrypick our guys. So we decided to offer to train people outside our company as well, to increase the number of skilled workers and to hopefully reduce the poaching.”
A stand-out feature of the school is its two forestry machinery simulators. The simulators are a good way to fast-track people’s learning in a safe environment, Josh says.
“We start students off doing the basics, learning to drive forward and back and then we move them on to felling trees, and processing to certain grades.
“We normally start them on the forwarder, in the John Deere simulator, to learn the basic controls. Then they’ll move on to a harvester, and through the wheeled machine and the tracked machine.
“The other simulator is for a tracked machine. It has sure grips, which are common in all the different brands of machine. It’s handy for guys, regardless of the brand they’re driving, to learn the controls and how the machine works.”
The simulators are good for weeding out bad habits too, Josh says: “It’ll tell us if they’re too rough, or too slow, or just not doing it right.”
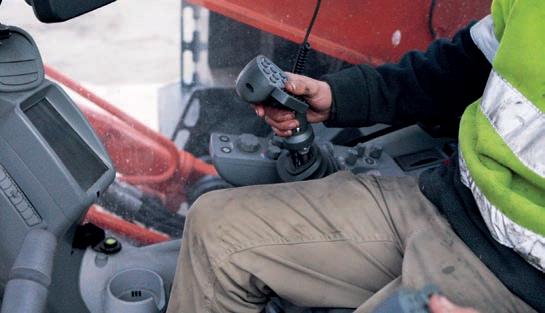


The school works in partnership with industry training organisation, Competenz, which gathers cohorts of students. The training is led by Neville Muir, a trainer with 30 years’ experience. Neville also does follow-up training with the students when they go back to their own worksites while Josh looks after the training on the simulators.
About eight students join at a time, for one week five times a year, says Josh: “The course covers their bookwork and their national certificate stuff, as well as training on the machines. They also visit other crews, just to see how other people do things. And they visit places like ports and sawmills. That shows them the whole cycle of forestry and helps them understand how what they do can have an impact further along the supply chain.”
Once students have trained on the simulators, there are real machines in the yard for them to have a go on, including log trucks, harvesters, and bulldozers.
“The simulators are good but once they jump in the real machine, it’s a wee bit different. If you are rough in the simulator, you don’t feel it. If you are rough in the real machine, it’ll shake you around and give you quite a fright.”
Josh says one of the main benefits of coming to the school is being taught by an experienced trainer like Neville, as well as being able to practice on the simulators and machines in the yard.
“When they go back to their crews, they know how to do things the correct way. They’re a lot safer, and they know ways they can improve how they work environmentally and production-wise.” NZL Top left: Workshop apprentice, Zak Phillips, gets help using the simulator from Josh Hurring. Top and middle: The John Deere simulator in action. Bottom: The simulator for learning to use tracked machines.
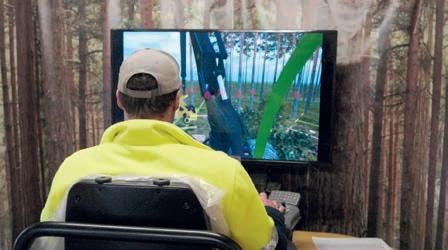
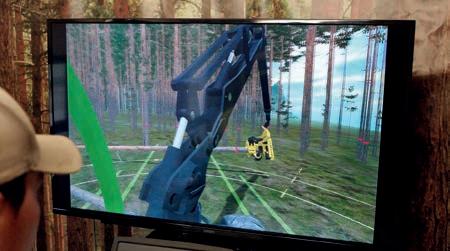
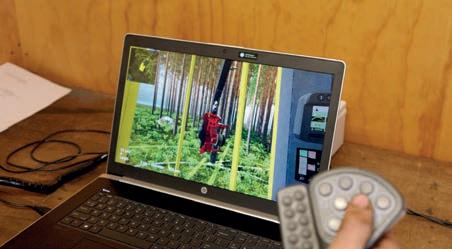
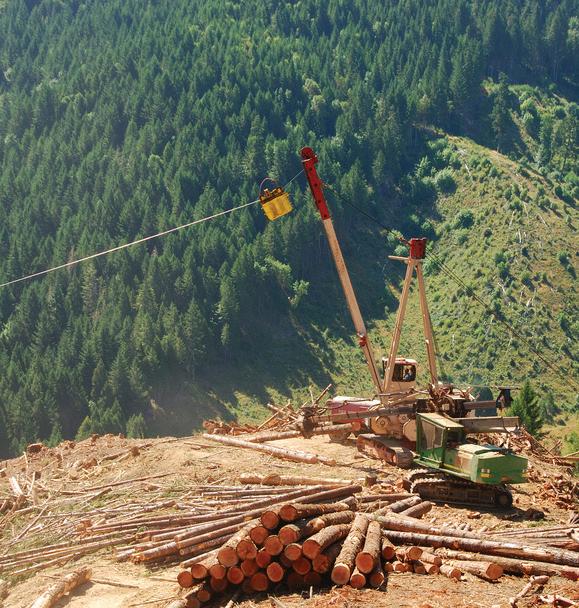
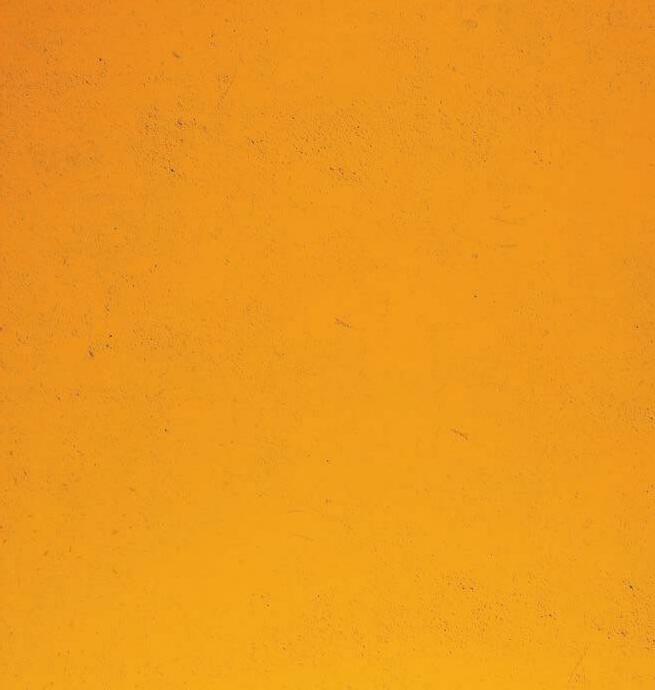