
5 minute read
Harnessing power of organic waste
Andrew Keaney, left, managing director of T&G Fresh, and Andrew Fisher, director of Ecogas, mark the start of work at the Reporoa site.
PROJECT SPOTLIGHT
A $30 million facility being built in Waikato to turn food waste into bioenergy is being described as a “plumber’s dream”. NZ Plumber finds out what it’s all about.
HARNESSING POWER OF ORGANIC WASTE
AUTHOR: MATTHEW LOWE

A plan of the Ecogas Reporoa plant that is due to be completed in 2022.
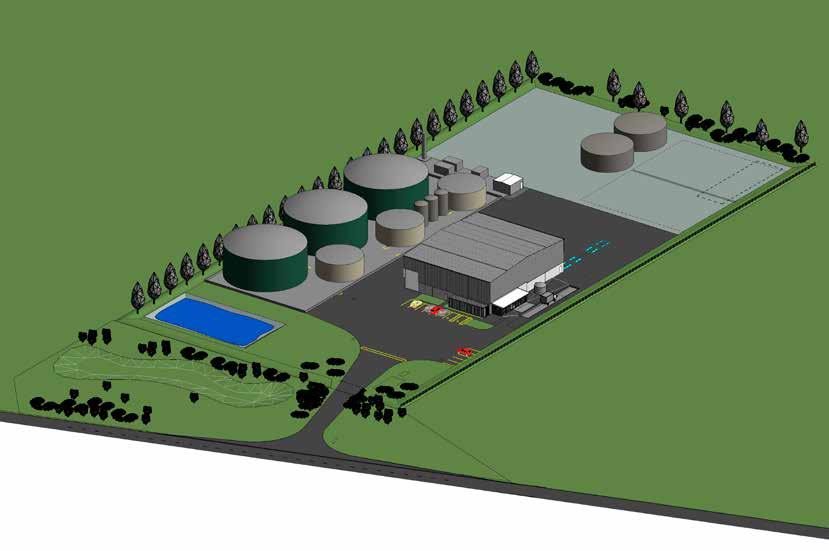
ANDREW FISHER Business Development & Director, Ecogas
Ecogas is building a plant in Reporoa that aims to process 75,000 tonnes of organic waste annually from businesses and kerbside collections into renewable clean energy. Earthworks at the site are already complete and the company plans to be operational in 2022. It will create enough energy annually to power about 2,500 households and produce clean bio-fertiliser for about 2,000 hectares of farmland.
Director Andrew Fisher has been working on the project for nine years and believes there is ultimately scope for more than 20 similar facilities across the country. “It’s an opportunity to utilise science and technology to generate renewable energy and recover significant volumes of water that would otherwise be lost to landfill,” he says.
“For me, it’s just the application of science and using our heads. The whole facility is plumbing centric because the system is all about moving liquids and capturing gases—the process is totally enclosed and it’s a plumber’s dream.”
“Much like a septic tank” Ecogas, a partnership between Pioneer Energy and EcoStock Supplies, will operate New Zealand’s first commercial scale anaerobic digestion facility recovering biogas and manufacturing nutrient rich bio-fertiliser. The world-class Ecogas Reporoa facility will help New Zealand value and sustain multiple beneficial outcomes from biomass recovery already seen globally with this technology. The UK alone has more than 142 of these facilities and its population is only 12 times the size of New Zealand.
Fisher explains that organic waste (biomass), which will be collected from across the North Island, will first go through a depacking process to get rid of decontaminants. “After that it comes out of the machines like a thick spirulina,” he says. “Everything has to be resized to less than 12mm in the depacking process.”
The substance next goes into a huge hydrolysis tank, which has a pH level of two to four, and spends four to five days there. After that it is subject to a pasteurisation process and treated for one hour at 72 degrees. Eventually, the “thick spirulina” goes into biogas reactors. While in the reactors, micro-organisms feed from the substance for between 30 and 70 days. Biogas is generated from the top and liquid fertiliser comes out “like a weak tea” from the bottom of the tanks. This is all done in an enclosed tank without air, hence the term anaerobic digestion.
“It operates very much like a septic tank, except the bugs we have in there are designed to produce biogas,” he notes. “We have various options with the biogas. It can go directly to the boiler and replace natural gas usage on site, but in time we’re looking at doing as they do in the UK and getting green gas injected directly to the grid, or power combined heat power generators, to create electricity.”
Proven technology overseas Future options for the system may include putting in membrane technologies to separate out carbon dioxide for industrial applications and creating biomethane for truck fuel. Anaerobic digestion technology is well proven overseas—similar plants operate in Europe and the United States—but the Reporoa’s plant is the first commercial-scale facility in New Zealand.
“This approach to dealing with food waste has been around for 2,000 years,” says Fisher. “It’s essentially how we’ve dealt with waste historically to maintain a level of hygiene, and circularity of resource. We’re not reinventing the wheel with this development; it’s more a case of putting a new set of tyres on it.
“Most food is between 50 and 70 per cent water and recovering this water reduces demand on our nature resources and is improving productivity. It’s only been in the last five to six years that New Zealand
has really looked at sustainability solutions at a scale such as this. There’s a lot of people who really want this to happen and support from small and medium-sized New Zealand businesses has been fantastic. We’re also starting to get movement from directors of large business who are making direct contact to learn more. This has been a massive change and been extremely positive for both parties.”
Fisher adds the biggest challenge of the project, and his long-term ambitions for more facilities, is persuading large industry of the value of what Ecogas is doing, and that any business that needs energy or produces biomass will benefit. He enjoys introducing his existing clients and new businesses to comparable businesses in the UK, Australia and Europe that already access similar anaerobic digestor facilities. The standard response has been, “This is fantastic”.
“Historically, people have made what we’re doing sound difficult and complicated but big things like this need to be kept simple.
For high-volume hot water
The Jandakot Bioenergy Plant in Perth, Australia, was built by Biogass Renewables and will be a ‘sister site’ to Ecogas Reporoa.

Plumbers will be key More than 70 people will be involved in building the Ecogas Reporoa plant and plumbers will be key for the ongoing maintenance and servicing of the site. There is a lot of pipework and a significant number of tanks. Fisher says besides utilising the skills of existing plumbers, he hopes the facility and any future ones can be used to help apprentices.
“What we’re creating is a manufacturing facility using modern technology, bio-technology and agri-tech, dependant on the skills and support of plumbers and general, hands-on engineers, who will run diagnostics and be able to monitor the work remotely. It will be a great environment to bring on apprentices and we will be working with local plumbers and won’t keep all the work just for people on site. We want a circulatory market and are keen to work with local tradespeople.
“Because the facility runs 24/7, it would be difficult for us to operate in isolation long term. As a result, there’s an opportunity at this site and future ones to be working with local trades, and Pioneer Energy Limited has been doing this at its sites across New Zealand for a long time.”

Check out the most extensive truly commercial range of energy-efficient hot water systems available in New Zealand.
Contact Paul Watson on 021 437 611
NZ
YOUR HOME CENTRAL HEATING & DOMESTIC HOT WATER PROVIDER
