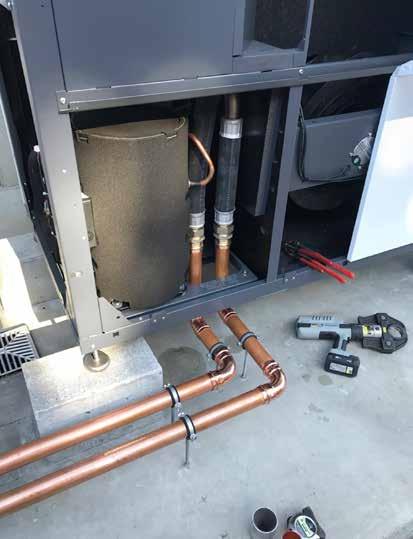
3 minute read
ENERGYEFFICIENT WATER TREATMENT
AUTHOR: LOIS OLDEHAVER
After successfully completing a job at the Te Mana sewage treatment plant, Mount Maunganui-based plumbing, gasfitting, drainage and heating business Pipe Masters were contacted once more by the Tauranga City Council—this time for help with a much larger job.
“Happy with the results we had delivered at Te Mana, we were then asked to come up with a more efficient way to heat their warehouse full of industrial-sized water filtration tanks at the Oropi water treatment plant,” says Pipe Masters director Paul Knight.
The plant runs on Continuous Membrane Filtration (CMF) technology that uses a microfiltration membrane to remove the contaminants in water. Periodically— around every week, depending on town water usage—acidic and caustic solutions held in Clean-in-Place (CIP) tanks are pumped through the pipe network to clean the filters, which are then disposed of and re-batched with new water to start the next round of treatment.
It was taking up to 14 hours for the 36kW elements to heat each new batch from ambient water temperature to the required 36°C for use. This meant, in addition to high running costs, there wasn’t the opportunity to clean the filters as often as the Council would have liked.
They wanted to see if there was a way to reduce the time spent heating and rebatching by coming up with a more energyefficient solution.
Heat exchange methodology
“I’d never been in a water treatment plant before,” says Paul. “My approach was to understand how the current technology worked and then work backwards to find different solutions.”
On his first site visit, seeing the warehouse full of pipes, Paul started asking questions based on his experience with domestic and commercial heating.
“The challenge was to find an energy source to heat both tanks, without crossing water over. I used the same heat exchange methodology we would use for heating a residential pool, with the adaption on a much larger scale in terms of energy resources.”
He first calculated the size of the potential heat pump they would need based on the size of the tanks, the volume of water they would need to heat, and how much energy would be required to reduce the time down significantly to around half the current outputs.

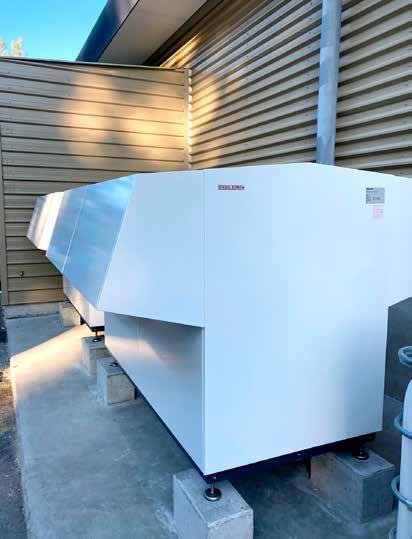
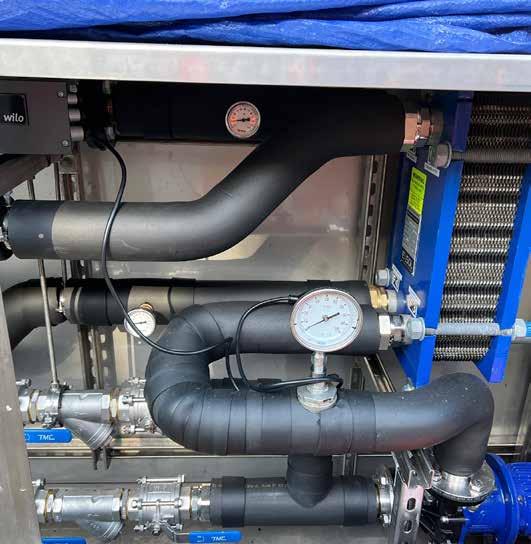
“Heat pumps use a similar amount of energy to the elements that were heating the tanks already, but the conversion rate is much better because they require significantly fewer inputs to get the desired temperature result,” he explains.
Monitoring and control
With many different skill sets needed for the task, Pipe Masters enlisted help from far and wide. German heat pump manufacturer Stiebel Eltron proved to be the linchpin for the project, working with Pipe Masters to recommend a suitable product from their range.
“I basically took my plan to one of the Stiebel Eltron engineers, Bhawesh Singh, based in New Zealand, said what my solution was, and asked if they had a product that could do the job. They’ve been instrumental throughout the project from start to finish.”
Once the size of the heat pump and design methodology was chosen, Tauranga City Council brought in engineering support from 2E Consultancy to map out each part of the process and, importantly, to connect the programme to SCADA—the control system that collects data from equipment and controls the thermostats and pipes.
By working off the controls provided by Stiebel Elton and syncing them to SCADA, the heat pumps could be monitored and controlled 24/7, based on the stage of the water filtration cycle.
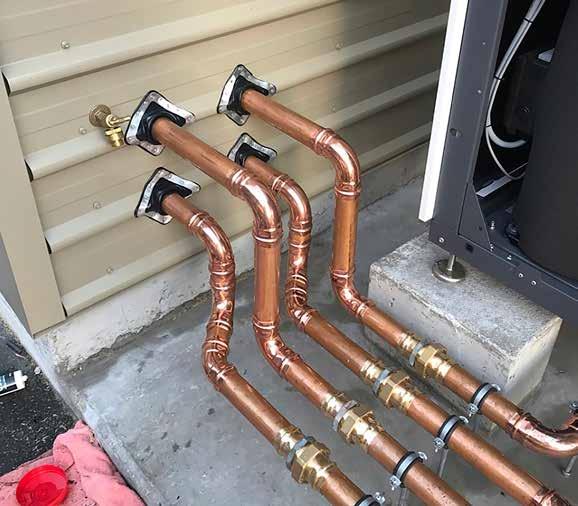
Renewable energy futures
Running both to schedule and budget, the project, taking just over 12 months from design to build, is now in the final testing phase with a go-live date of March 2023.
The new heat pump system can draw on 64kw of renewable energy to heat 24,000 litres of the acidic and caustic solutions for water treatment. This means they are achieving a similar amount of energy as before but with a far better conversion rate of 1:3.5.
The final result? The water can be rebatched in half the time and at less than a third of the cost, using a renewable energy source. For Paul, this is the exact direction he wants his business to head in and sees as an emerging part of the trade.
“In our industry, it’s important to look at ways to reduce energy consumption, and what alternatives there are to fossil fuels,” he says. “To be able to have a team capable of doing projects like this is really great.”