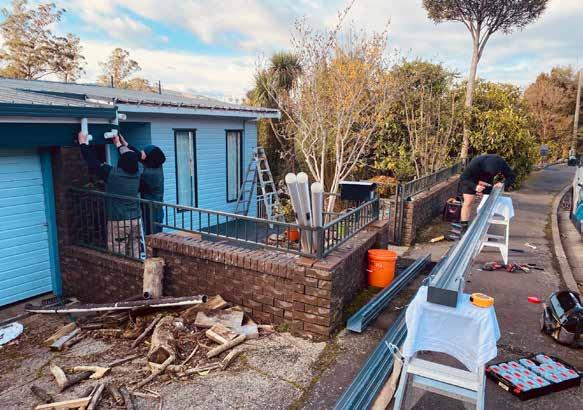
5 minute read
Understanding work as done
HEALTH & SAFETY
UNDERSTANDING ‘WORK AS DONE’
Before businesses can try and resolve workplace health and safety issues, everyone needs to understand—and discuss—how the actual work is done. Learning teams are a valuable tool to get the conversation started.
AUTHOR: GREG DEARSLY, FIRST 4 SAFETY
It’s fair to say that most PCBUs are committed to ensuring the health and safety of all those exposed to the work done as part of the organisation’s activities—but what knowledge do they have about how work happens?
We all look at work through a different lens. If you’re in a management role, you’re viewing work from the perspective of business success, contractual obligations and logistics. If you’re a frontline worker, the business is the place where you perform your duties to enable you to make a living. And if you’re, say, an industry association or territorial authority—you will see work in the context of representing the interests of your community or members.
These different perspectives change what you look at in the actual work environment and what you do to make problems go away.
Learning teams: facilitated conversations
As part of the development of its approach to health and safety, the Masterlink group apprentice training company was keen to know more about health and safety issues experienced by its apprentices and by the host companies who manage the apprentice’s day-to-day.
The organisation undertook a series of ‘learning teams’ during the early part of 2022. A learning team is a facilitated conversation between those who do the work and those who design the work, to enable the
Business smarts
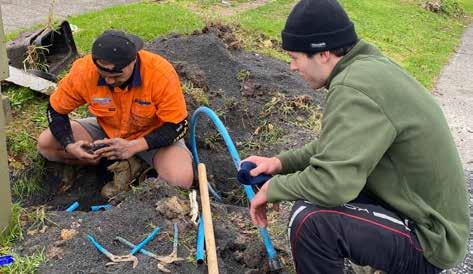
sharing of operational intelligence between the two groups and improve system design.
The learning team process recognises that team-based learning is the best way to understand a particular problem—and that a significant contributor to such a team must include the workers who are involved in the actual work.
For learning teams to deliver the best results, the process should be unstructured and organic. It is also important to understand the following:
‘Work as done’ is a dynamic activity, not a linear process, and the best way to understand the complexities of work is to have open discussions about those complexities
Before we try and resolve issues, we first need to understand work as done.
How work is actually done
While learning teams achieve best outcomes when they are unstructured, there are some key components to consider, starting with having a clear understanding and agreement about the goals for the process.
The most beneficial phase of a learning team is when the group is in discovery mode—when the focus is solely on learning. It is not an environment to edit or argue about what is right or wrong; the group is simply in a situation of discovery. If the group jumps from learning mode to problem solving mode, learning stops.
The intent of this process is to help the organisation get wiser. Not knowing about aspects of how work happens is a powerful position to be in. It means the business has the potential to find out more and knowledge is powerful—making learning a deliberate improvement strategy.
Masterlink’s learning team sessions identified a number of areas where there was more to learn about the role and experiences of apprentice plumbers and their host companies. The knowledge gained from the process was through the power of asking better questions.
There were learnings about conditions across the diverse range of workplaces that apprentices experience. The groups learnt about mistakes that new and experienced apprentices might make, and attendees were asked to discuss situations where they had to be extra vigilant or where they had to innovate or improvise. These types of questions are designed to generate discussion about how work is done.
Developing ideas for improvement
Several themes emerged in relation to the jobs apprentices carry out in their various work environments. These themes were expanded on during learning team sessions, with attendees developing a range of opportunities that could improve the apprentice’s work experience in relation to health and safety.
Thirteen opportunities were discussed, ranging from different approaches to training outside the normal training environment; new ways to distribute health and safety information for apprentices, such as QR codes on tools; targeted areas for apprentices’ development, such as job planning and train the trainer courses; and improved approaches to risk management in what can be dynamic environments.
The learning team project equated to 20 hours of organisational learning by Masterlink and all those who participated.
If you are interested in finding out more about how a learning teams approach can enhance your organisation’s knowledge about how work is done, contact greg@first4safety.co.nz
TIPS FOR A SUCCESSFUL LEARNING TEAM
To make sure your learning team is a success:
Conduct the sessions in a way that all contributions are valued, without judgement
Sessions need to be safe environments, where everyone is free to communicate their context without fear of repercussion
Learning has value—it is a corrective measure that makes us smarter and more informed
When you get better at learning, you gain more knowledge, which leads to making better decisions.
Learning is vital and primary to fixing problems. Many businesses say they are a learning organisation, which is a great aspirational goal—but what is actively being done to achieve this? You need to be prepared to hear good and bad news, or that change is required. Only by deliberately engaging in learning will you understand what you don’t already know.
About the author: Greg Dearsly owns First 4 Safety, a generalist health and safety consultancy. Greg holds a Masters in Advanced Leadership Practices and is a Professional member and former President of the NZ Institute of Safety Management (NZISM). He represents NZISM as President of the International Network of Health and Safety Practitioner Organisations (INSHPO).
First 4 Safety offers Master Plumbers tailored health and safety support and advice at competitive rates. Order through the Master Plumbers member website (Health and Safety).