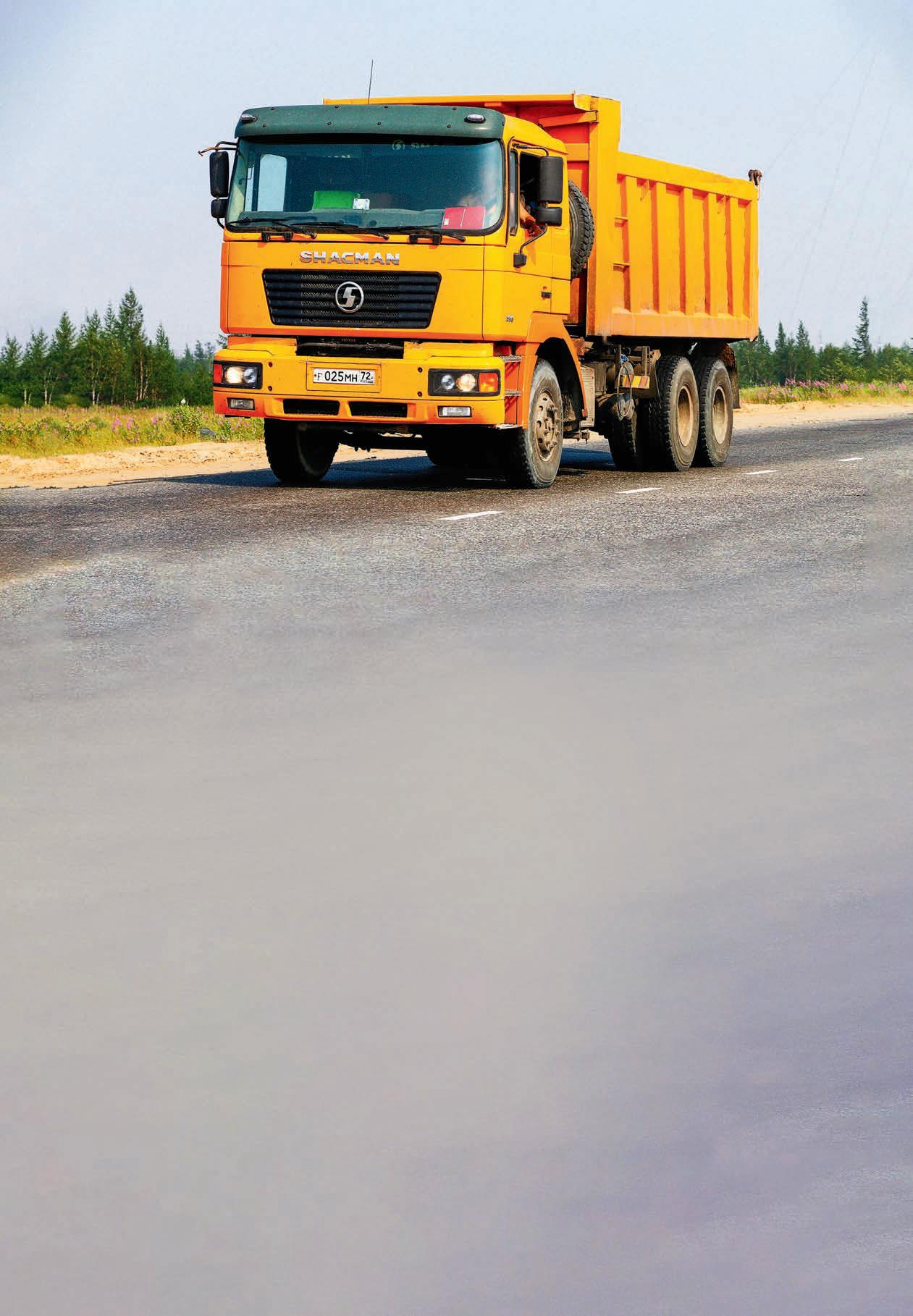
12 minute read
International Truck Stop – China on the up
Chinese trucks have come a long way...
CHINESE TRUCK PRODUCTION
ON THE UP DESPITE GLOBAL PANDEMIC
In the past year, China’s truck-makers managed to sell more than 1.6 million heavy vehicles. Compared with 2019, this represented a growth of more than 38%.
The results are quite an achievement as 2020 will be remembered as a period of great hardship due to the Covid-19 pandemic and resulting economic downturn. So what made the Chinese heavytruck market so attractive?
There were two main factors – an influx of new models matching European standards in design and operation, and the government came up with new measures to reduce the environmental footstep of heavy vehicles.
Furthermore, the monthby month-increase in
Story by Niels Jansen Photos by Vladimir Chekhuta

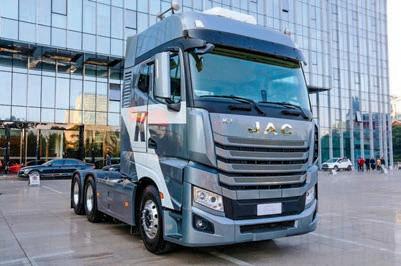

The interior of the recently launched Foton Auman Auhawk R medium-duty truck (bottom left photo).
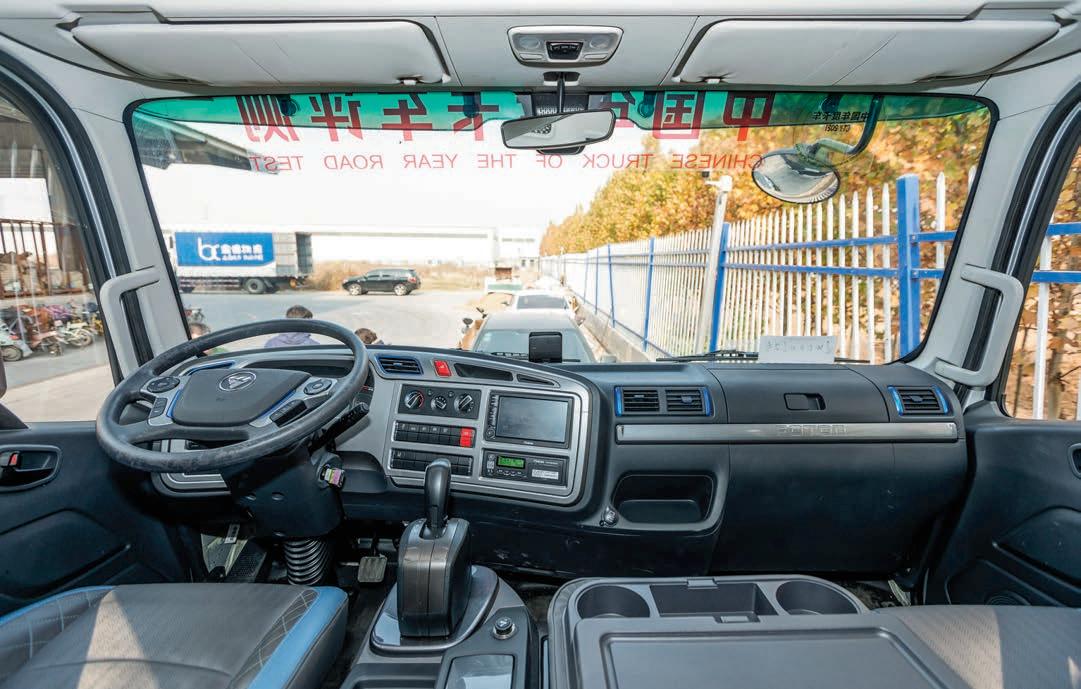
commercial-vehicle sales was helped by the resumption of work and production after the pandemic eased off in China in 2020. The change of people’s lifestyle after the Covid-19 period – for example, the rapid development of e-commerce – also brought a sharp increase in the demand for logistic services and a consequent need for better and more economical commercial vehicles. And the Chinese road authorities introduced a new tax-collection policy based on the number of axles and permissible axle weights.
Since 2020, the manual weighing of trucks has been abolished and a new electronic toll road system set up, becoming active in January 2021. This led to an increase in two-axle tractors and trucks. As a consequence, sales of rigid 18-tonne GVW trucks made a big leap forward. Compared with the previous year, companies sold no less than 40% more medium-weight trucks in 2020. And significant investments in infrastructure by the government have also contributed to increased sales of dump trucks, mixer chassis and other construction vehicles.
In line with rapid growth in the commercial-vehicle market, Chinese truck manufacturers have continuously launched various new medium- and heavy-duty models. Some completely new names entered the field, keeping up with the latest trends in road transportation and the more stringent government regulations. The mechanical quality of vehicles has improved as a result, and so has the operational applicability in the modern logistic market.
It is interesting to see which brands gained the most in the recent developments. Looking at the top 10 rankings for 2020, FAW Jiefang led the list with total sales of 377,000 trucks and a market share of 23.2%. The company’s flagship truck/tractor is the J7 Eagle, which not only looks good but is built to the highest standards. With 311,000 units, the Dongfeng Corporation comes second. The top model in the Dongfeng line up is the KX Tianlong. Although it was developed a few years ago, it is now available with a six-cylinder diesel engine of 447kW (600hp), which produces a peak torque of 2750Nm.
The third spot goes to Sinotruk Corporation, which

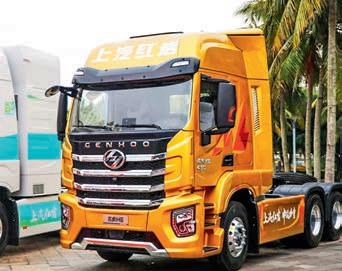
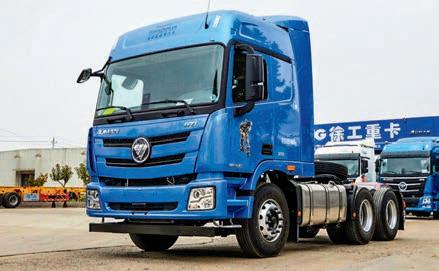
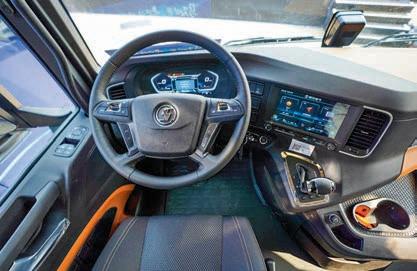
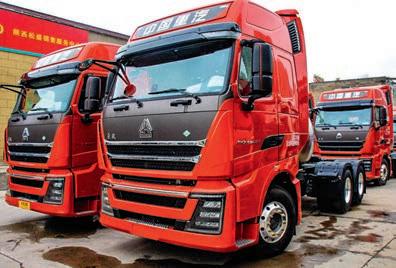
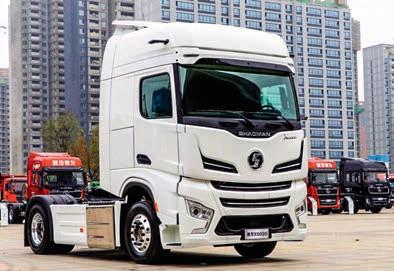
The sleek Shacman Delong X6000 must help the Shaanxi HD Automobile Group gain more market share this year. The European-style cockpit of the new Shacman X6000 heavy truck. Sinotruck’s Howo TH7, with its old Volvo FH cab, got a makeover.

Know these logos? These are the top 10 Chinese truck manufacturers.
saw a growth of 57% in 2020. For this year, its topof-the-range Howo TH7 received a facelift of the old Volvo FH-based cab. Together, these three large manufacturers form the main core of the Chinese truck market.
Shaanxi Co saw sales of the Shaanxi and Shacman heavy trucks increase by 28%. The latter company’s products are exported to many countries worldwide, including New Zealand. The Delong X6000 is the company’s top model. Power comes from Weichai Euro-6 diesel engines with up to 447kW (600hp), with a ZF automated manual transmission. For some markets, Cummins engines and Eaton AMT transmissions are also fitted.
Foton Motor increased sales by no less than 75% last year, making it the fastestgrowing truck maker in the top 10 ranking. Its all-new Auhawk R medium-duty truck, recently voted Chinese Truck of the Year 2021, should help increase sales even more. The 18-tonne GVW truck is equipped with a six-cylinder diesel engine of 162kW (217hp)/820Nm, combined with a ZF AMT transmission. Its good-looking design integrates European standards with China’s new regulations and market needs.
During the ceremony in April to celebrate the production of its 10,000,000th vehicle, Foton Motor also launched the new top-of-the-range Auman Galaxy. The heavy tractor has a modern Euro-style cab but you have to get used to the front-end styling.
Selling 80,000 units in 2020 makes SAIC Hongyan CV Co the sixth-largest truck maker. The company, established in 2003 as a joint venture with Iveco, markets its vehicles under the Hongyan, Genhoo and Genlyon brands. The allnew H6 range was presented late last year. Contrary to most Chinese offerings in the heavy-duty field, the new SAIC products are also available in a flamboyant colour scheme.
JAC Motors, one of the oldest truck manufacturers in the country, saw its sales share increase by 41%. JAC is one of several manufacturers that also offers heavycommercial vehicles that can run on alternative fuels such as LNG. The last three truckmakers in the top 10 rankings, CAMC, Dayun and XCMG, each had a share of just 1% to 2% of annual truck production in 2020.
It will be interesting to see what the new year brings. The big names are expected to do good business again because of the growing demand for cleaner and leaner road transport. But do not be surprised to see also some new entrants appearing on the local market.
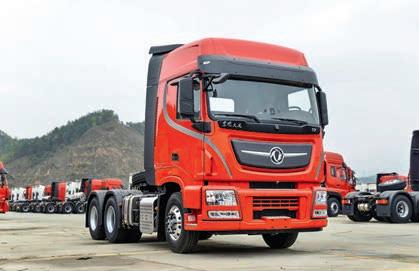
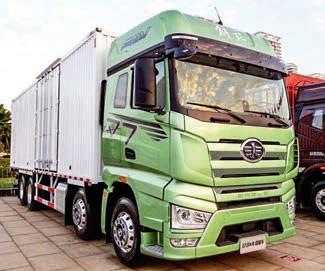
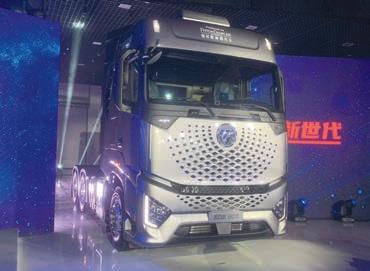
The concept drawings Howard took to the initial meeting with Mack. They were going to supply the prime mover to tow the B-double as well.

PART I THE MACK TITAN
RACE TRUCK
Even by today’s standards, it would be considered ambitious to bolt a 2500hp V8 Mack engine to a truck chassis with visions of running it down the quarter-mile in 11 seconds or less. Nevertheless, back in the mid1990s, that’s what we set out to do. The following is a recount of a project we called Thunderbolt.
Incongruously, my wife does not share the same passion I have for trucks nor the industry.
Consequently, it is with some irony that if it weren’t for her insistence that I clean out the storeroom as I’d been promising for the past few years, I would not have stumbled across the two-andbit-decade-old files on Project
Thunderbolt.
Back in the early 1990s, I worked for Truckin’ Life as the technical editor and editor at large. One of my tasks involved covering the truckracing circuit, and I’d become friends with well-known truck racers, Frank and Charlie
Gaffiero. You might remember their famous Kenworth T400
Bandag Bullet with the two 92-Series Detroit Diesel V8
1

2

4 5
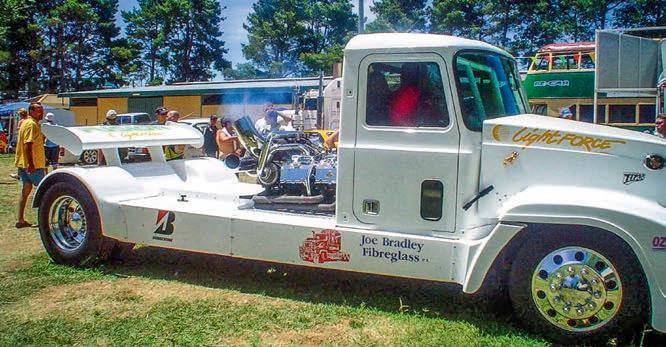
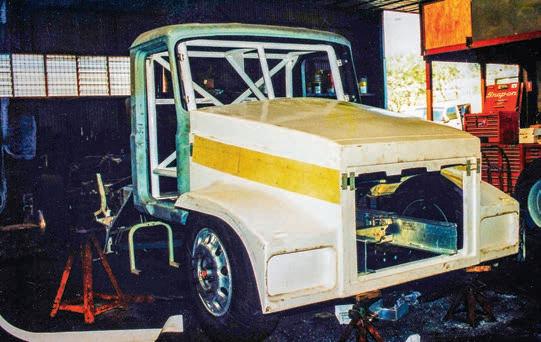
1) Project Thunderbolt and the famous Bandag Bullet. 2) In the pits shortly after completion. 3-5) Snapshots of the mock-up as the Mack was being hand-built. The team would make something then sit the cab and bonnet back on to make sure it would fit.

engines.
One night, after a drag meeting in Townsville, I suggested to Frank that if the Bandag Bullet had a challenger – something to race down the quarter-mile – it would make for a bigger drag show and ultimately more publicity. Our concept drew on the rivalry of Ford versus Holden, which had thrilled touring-car fans for years. If you’re into trucks, then you either love your Kenworth or Mack. There is no in-between.
We had the idea; we knew what truck we wanted. Now, it was a matter of putting it all into motion, and that was the start of the late nights.
By early 1996, we had a sound strategy. Discussions with promotors and potential sponsors and suppliers were proving promising. Furthermore, the positive feedback we received from Mack during preliminary discussions encouraged us to proceed with a formal proposal. By the time we’d submitted it to Mack at a meeting with Gary Richards, the then-marketing manager of Mack Trucks Australia, Project Thunderbolt had evolved into more than just a drag truck.
The subject line on the MTA internal memorandum dated 20 December 1996 read: ‘Unique Promotional Opportunity.’ It went on to read, “the basis of the proposal is to develop and exhibit a special display/ demonstration truck…”
Time for a quick bit of Aussie trucking history. Mack introduced the Super Liner in the early 1980s, powered by its E9 V8, with power output from 400hp (298kW) to 500hp (373kW). These trucks and their engines quickly developed a reputation for producing inexorable power and steadfast reliability. The Mack E9 engine became king in the heavy-haulage market segment. By the mid1990s, electronics had found their way into Mack’s V8 as the drive to produce more power persisted. With the introduction of electronics and horsepower boost, the V8 received new nomenclature, now known as the EA9. (Incidentally, the ‘A’ in the designation indicated an Australian engine.)
At the time, most truck manufactures could only supply engines up to 550hp (410kW) and 1850lb/ ft (2598Nm) torque. Even Caterpillar’s big C16 just made (575hp) 428kW.
Mack Trucks Australia had propelled its new EA9 beyond the 600-plus horsepower (447kW) frontier. It even boasted what, for the time, was a mind-blowing 2050lb/ ft (2780Nm) torque. This new tenacious V8 engine aimed squarely at heavy haulage and road-train applications indeed turned heads. When those 610hp (455kW) EA9 engines were cracking, they cracked. And operators that had the good ones loved them. But sadly, not all of them enjoyed the longevity of their predecessors.
As a result, the idea of

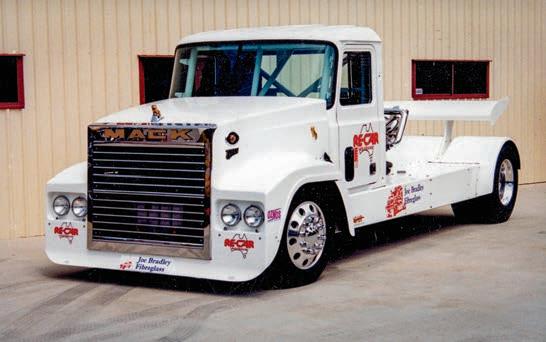
The business end of a 2000hp+ drag truck. A vague resemblance to the Mack Titan of the day.
reliably squeezing high horsepower out of the Mack V8 excited Gary Richards. He was keen to get involved and believed the primary objective should promote Mack’s engine power and reliability.
By April 1997, we’d received written confirmation of MTA’s sponsorship. The chassis build commenced in Frank and Charlie’s Archerfield workshop. By late September, we’d secured a cabin that went to Gold Coast bullbar manufacturer Bocar, which offered to construct a roll cage to meet the ANDRA specifications.
Meantime, the race was now on to get an EA9 engine to thump out some serious horsepower. However, thanks to Gary’s enthusiasm and a couple of strategically placed phone calls he made to the USA, a few chaps from Mack Trucks International (MTI) agreed to assist with the project, and the engine solution arrived. Between Gary and his contacts at MTI, we made contact with USA National Tractor Puller Champion Ray Collins, who ran an E9-V8-powered 1984 Mack Super Liner called the Buckeye Bulldog, which reportedly reliably produced more than 2500hp (1864kW).
The team at Mack’s Hagerstown engine factory, which built the engines for Ray Collins, agreed to construct an engine for us similar to the champion winning model in Ray’s Super Liner. According to a facsimile dated 1 September 1997, for an investment of US$40,000 the team would deliver an engine capable of 2000hp+ (1491kW). A month later, I received confirmation that MTA transferred the deposit to MTI for the engine build’s commencement.
Over the next few months, our fax machine received an extensive workout as correspondence went back and forth between ourselves and the United States regarding engine specs. One facsimile from MTI in late October 1997 worth noting suggested the engine colour of the block should be Mack grey while the exhaust manifold was to be treated in ‘jet hot black’ and the intake manifold ‘jet hot silver’, a proprietary baked hightemperature finish.
Engineer Steve Trevitz was responsible for the final engine configuration. He planned to run a two-stage turbocharging system with two primary turbos feeding two secondary turbos, which fed the engine. Keeping the turbos cool is critical to reliability, especially in an engine producing this amount of horsepower. It was necessary to inject water both before and after the secondary turbo to achieve the required cooling. The addition of this water-injection system meant an additional chassis-mounted water tank.
The engine design necessitated a staged/ progressive nitrous oxide injection to achieve more than 2500hp. In theory, the nitrous would be introduced into the engine once it left the starting line to avoid unnecessary wheel spin and provide more top-end speed. Nevertheless, Steve Trevitz indicated that without nitrous use, the engine output would exceed 2000hp. Exciting news. Gary Richards suggested the engine serial number reflect the horsepower output; subsequently, the Hagerstown team stamped EA9-20000001 into the block.
We decided to use an auxiliary drive-belt arrangement to power the air compressor because of the high engine rpm. We used standard EA9610 components with the installation of the alternator and power-steering pump. An external high-flow water pump was the preferred option to cool the engine adequately.
On 3 April 1998, we received a facsimile from Jerry confirming the engine had left Mack’s Hagerstown factory bound for MTA, Brisbane headquarters.
Now, much like part two of this article, it was just a matter of waiting...

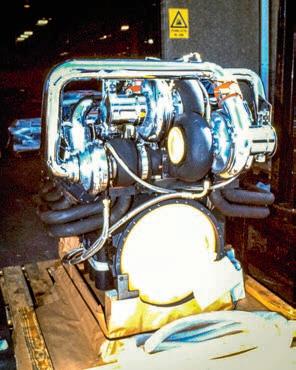