
4 minute read
Decarbonizing Off-Road Vehicles: Putting Electric Powertrains to Work
ABB
Sectors such as marine, mining, harbors, airports and construction sites have an opportunity to accelerate decarbonization.
Collaboration and end user needs should be at the center of plans to reduce carbon dioxide.
by Henrik Nilsson
The current, and probably future, price and supply volatility of fossil fuels and the damaging impact of carbon emissions on our planet are compelling companies to switch to sustainable transportation. To reduce energy consumption and emissions in every sphere of the industry is critical for the environment and company profitability.
Transporting people, goods and raw materials accounts for more than 25% of the world’s total energy consumption and almost 30% of global carbon dioxide (CO2) emissions. Diesel-powered vehicles also emit other harmful gases such as sulfur oxides. The technologies to reduce or eliminate these emissions are available now, and in many cases, they can also improve productivity.
Emission-free technologies have been well-established for many years. Over the past decade electric vehicles have grown in popularity in private, as well as commercial use.
Industrial players have an opportunity to accelerate the shift to sustainable transport in sectors such as in marine, mining, airports and construction sites. Emission-free alternatives are available for these sectors. What the industry does will have a rapid effect on the environment and can make a difference!
Effective Partnerships
While the forces driving the transitioning toward electric powertrains are clear, the path to success is not always straightforward. Operators who want to expand their electric or semi-electric fleet reliably and quickly likely face challenging decisions about the most effective strategy to follow and which partners to work with.
A good place to start is to look at the overall operation to identify specific vehicle use profiles. In doing so, operators can determine which vehicles and machines would be the best fit to operate with an electric powertrain, hybrid solutions, fuel cells, cables or other methods. They can also talk with equipment manufacturers who have partnerships with powertrain OEMs. To identify the right concept for fossil-free operation, everyone must understand key parameters, such as charging
opportunities, drive-cycles (including energy recuperation) and the peak torque demand.
Establishing partnerships with OEMs with strong domain expertise in vehicles, subsystems and systems is a highly effective way to accelerate the electrification journey.
For example, one of Norway’s largest excavator suppliers, Nasta AS, distributes, redesigns and rebuilds construction machinery. The company is collaborating with a powertrain manufacturer to rebuild internal combustion engine (ICE) construction vehicles for electric operation. They used either battery power or a direct cable connection. The conversion procedure included retrofitting the diesel vehicle with new powertrain components using electric motors and drives to replace the combustion engine. This new powertrain included an energy storage system and charging solution in place of the fuel tank.
Users of Nasta’s electric excavator eliminate about 48 tonnes of CO2 emissions each year from the environment and significantly reduce noise pollution. The operators have also expressed satisfaction with the excavators’ responsiveness and performance.
Stakeholders need to speed up their global decarbonization efforts to improve the energy efficiency and productivity of mobile equipment. The path for achieving this is clear and available. When operating in the optimum load range, diesel engines only reach a maximum of 45% energy efficiency, as opposed to the considerably higher 95% efficiency of an emission-free electric driveline.
Key Components
The main components of an electric powertrain are: • The electric motor, which turns electric power into motion • A converter • An energy source Compared to passenger vehicles, components installed and operating in working machines must sustain longer operating lifetimes, handle more challenging drive cycles, withstand tougher environments, and manage shock loads of up to 50 grams. That’s a tough life for a motor. The driveline must be able to deliver high torque and perform effectively across a range of loads at any time. These are not new requirements for electric motors and converters. They have been doing this job for many years in industrial, rail and marine applications.
In a vehicle application, the traction converters and electric motors can play a significant role in capturing energy from regenerative braking and feeding it back to the battery or via catenaries to the network. In a traditional combustion engine vehicle, this energy is lost as heat. Regenerative braking systems (RBSs) are already commonplace in road and rail vehicles, with industrial electric vehicles gradually following suit. |
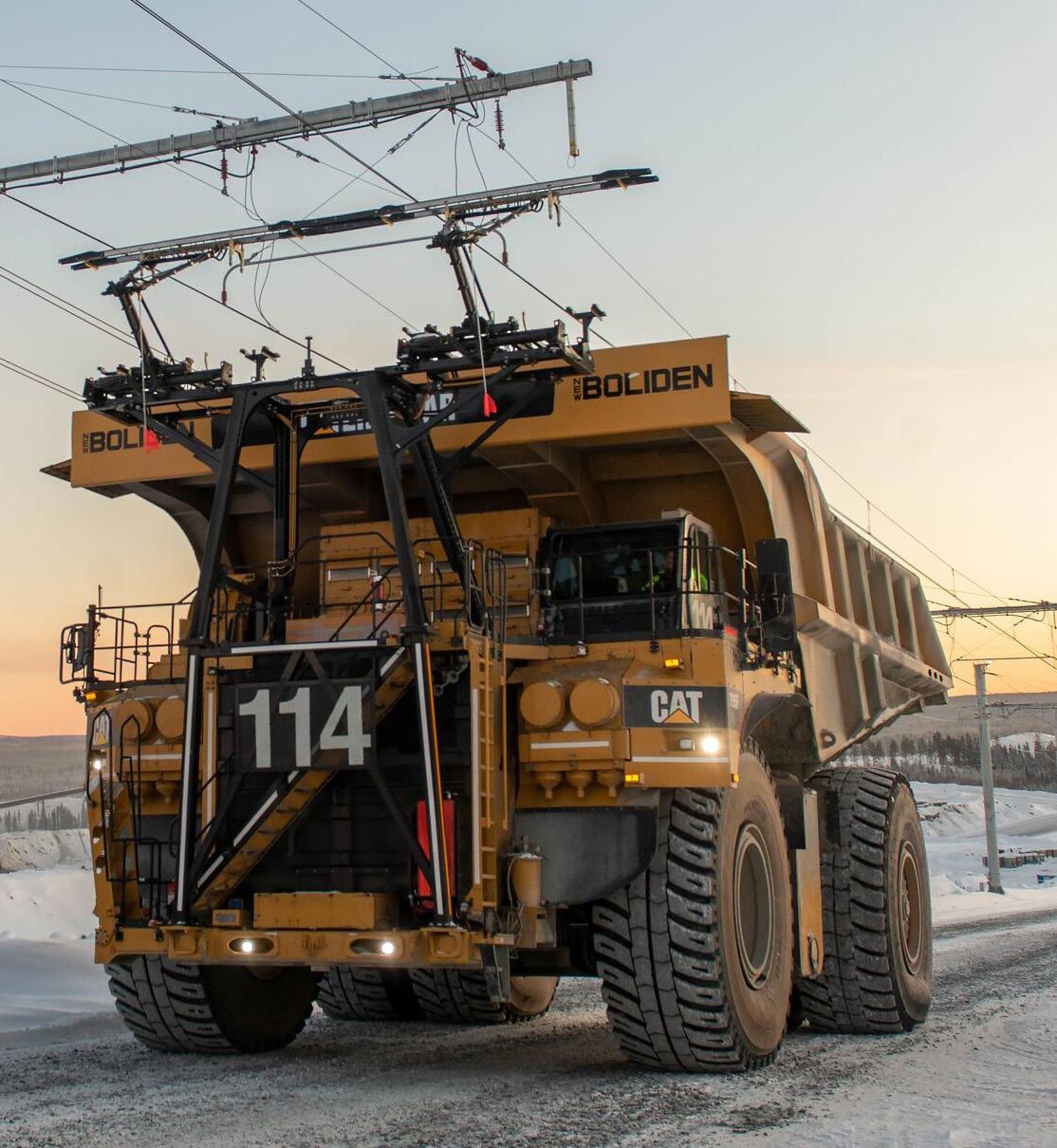
Boliden AB joined forces with an OEM to design and install a 700-meter-long catenary line to power several mining trucks at its Aitik mine.
Henrik Nilsson is sales and market development manager, IEC Low Voltage Motors for ABB.
Read More
https://oemoh.co/h2xr8v
SENSORS FOR MOBILE MACHINES
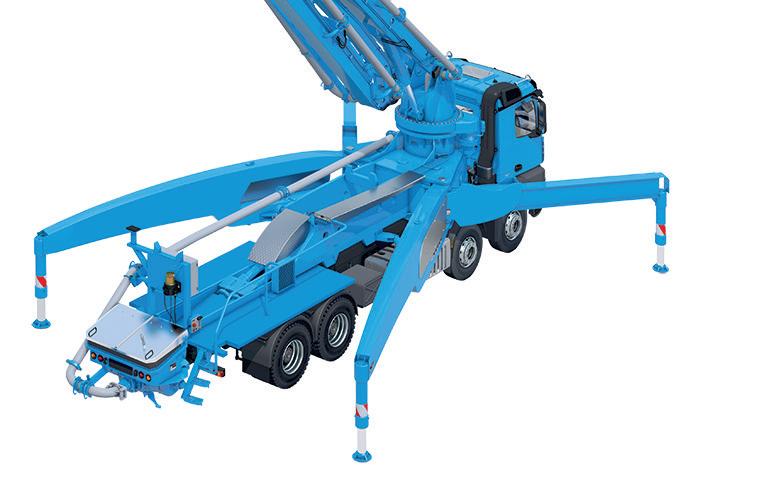
Stroke measurement in hydraulic cylinders – no piston-rod rifl e boring required! Robust rotary encoders for safe angle and speed measurement! Up to PLd! Draw Wire-actuated rotary encoders for position measurement utilizing proven technology! Inclinometers for non-contact measurement of vehicle orientation!