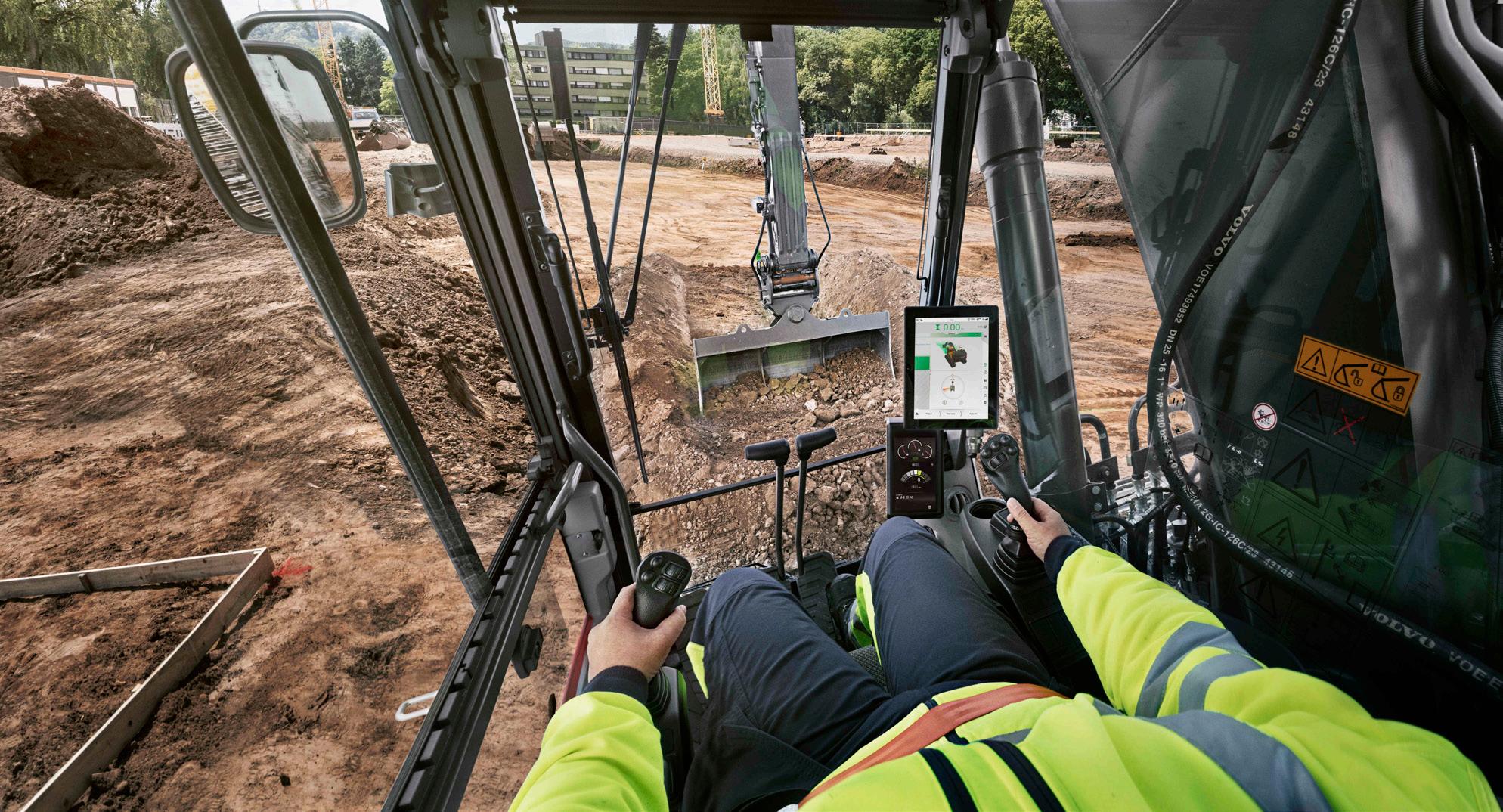
7 minute read
Trends in Lawn, Landscape and Construction Work
Battery power, digitalization and efficiency drive these industries.
by Lori Ditoro
The construction and lawn and landscape industries have been experiencing disruptions. The need for energy efficiency, noise reduction and operator safety are drivers of ongoing innovation. Reduced emissions in these sectors is paramount.
Green Industry Insight
OEM Off-Highway recently spoke to Sara Webb, editor, Green Industry Pros, about lawn and landscape, commonly called the “green industry,” trends.
“Most green industry professionals I speak to are looking for ways to up their efficiency—labor efficiency, equipment efficiency, energy efficiency, water efficiency,” Webb said. “You name it; they’re striving for it. To that aim, some landscapers are taking a fresh look at robotic equipment and software to streamline and automate tedious processes they already had in place. It will be interesting to see how manufacturers answer the calls for new efficient products, particularly at this year’s Equip Expo in Louisville, Kentucky.”
Webb said other trends include: • Battery-powered equipment—It is becoming more mainstream with longer runtimes. Prices are coming down, so it’s worth the upfront investment with high fuel prices. • Smart irrigation controllers that help save on water—These are popular in the West and in municipalities— while most OEMs’ equipment does not directly affect water use, landscapers’ goals may influence them.
Electrification
One popular buzzword in the green industries and construction is electrification, and with good reason. Both industries are in a transformation in power sources. The electrification of passenger and smaller mobile commercial vehicles is occurring rapidly.
“While landscapers and turf managers have had electric options ... for years, fully electric, battery-powered construction equipment like compact wheel loaders and excavators are new,” said Lars Arnold, electromobility product manager, Volvo Construction Equipment.
According to Nick Moore, director of sales—electrification, at Briggs & Stratton, green industry professionals realize how important battery-powered equipment is.
Image 1. An operator takes advantage of digital technology on a construction site.
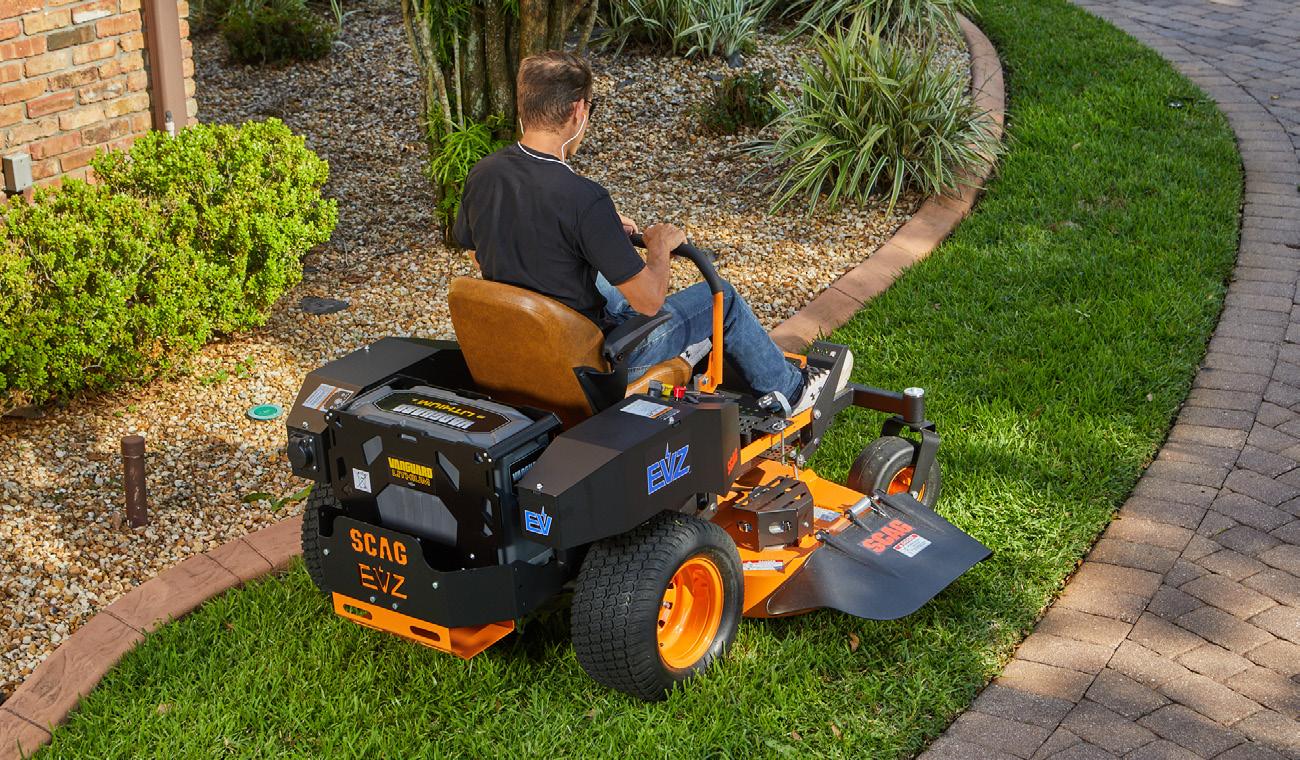
“When it comes to the benefits of battery power, the output of zero emissions is a huge regulatory driver for OEMs and end users,” Moore said. “However, battery-powered equipment can also offer a better user experience because of its quieter operation and minimal required maintenance. Another big driver is mitigating the cost of fuel. For professional cutters who must fuel up an entire trailer full of equipment every day, battery power can really benefit the bottom line of their business given current gas prices.”
End-users demand for quieter, lower emission equipment. OEMS must meet these needs. Arnold discussed a case study in which Volvo provided quieter operation and lower emissions.
“One of the first U.S. projects our ECR25 electric compact excavator and L25 electric compact wheel loader were used on was building a trail at a national wildlife refuge,” Arnold said. “The quiet operation was less of a disturbance to the animals living in the area, and the lack of emissions was safer for the environment.”
Vanguard also helped customers with electrification. “Earlier this year, Scag Power Equipment (Scag) introduced its EVZ electric zero turn riding mower (see Image 2), which is powered by the Vanguard 5 kWh commercial lithium-ion battery pack,” said Moore. “The EVZ is the first fully-electric unit in Scag’s lawn mower lineup. We were excited to work alongside Scag to bring a new battery-powered option to the turf market.”
Efficiency
Increased efficiency includes decreased maintenance intervals, better time management, and automating redundant or tedious tasks
According to Moore, “Another big trend we’ve seen is that many manufacturers, including Vanguard, are turning ... to developing and designing engine (or power-source) features that help enhance productivity and reduce maintenance requirements.
“With labor shortages and a pent-up demand of lawn and landscape work, the industry is being asked to do more with less. Professionals are relying on their equipment ... to deliver a powerful performance and maximize productivity.”
Decreased wait time to get started is also an increase in efficiency. “Electric machines provide instant torque, so there is no delay like you might feel on a diesel machine,” said Arnold. “In addition, the maintenance is much easier (and less expensive) because you don’t have an internal combustion engine to take care of.”
To add to the efficiency of using battery power, Vanguard developed a swappable battery, borrowing from smaller batteries used in power tools and small outdoor power products.
According to Moore. “The battery features an exchangeable design, allowing customers to easily remove and replace the battery with minimal downtime. The Swappable Battery also enables [scalable] power, so you can use [multiple battery packs] to meet larger power needs.”
Digitalization
Often, digital enhancements, including Internet of Things (IoT) technologies, go hand in hand with efficiency. Other benefits include transparency and minimized risk, according to Wilfried Aulbur, senior partner, Roland Berger.
“Digitization is expected to grow significantly, driven by evolving technologies and industry/segment-specific advancements—for example, building information modeling (BIM),” Aulbur said. “On the construction site, IoT provides transparency, helps optimize planning, minimize risk and improve efficiency. Being clear on the purpose of IoT applications is critical for the successful use of IoT.”
4 Disruptive Construction Trends
The construction industry will face disruption in the upcoming decades that will be driven by 4 highly disruptive trends: • Automation, robotics and artificial intelligence—The use of digital tools to complement traditional processes will increase. • Changing to active/intelligent buildings—Intelligent technologies (sensors, for example) will be required in new constructions. • A shift to off-site manufacturing—Project speed will increase with prefabricated or modular • BIM and digital twin—These initiatives will increase cooperation and transparency
Contributed by Wilfried Aulbur, senior partner, and Giovanni Schelfi, principal, Roland Berger
Supporting OEMs on the Journey
Component suppliers are eager to help OEMs meet their customers’ needs.
“We are closely working with OEMs, ... to help them be successful in a world with changing demands,” Moore said. “Wherever the industry takes us, we’ll be there to support OEMs and their customers in navigating these changes.”|
Read More
https://oemoh.co/59ojyp
How GPS and Other Tech Boost Productivity and Safety by Matthew McLean, Jenny Olsen
Onboard weighing is a popular feature for many operators and is recommended to OEMs.
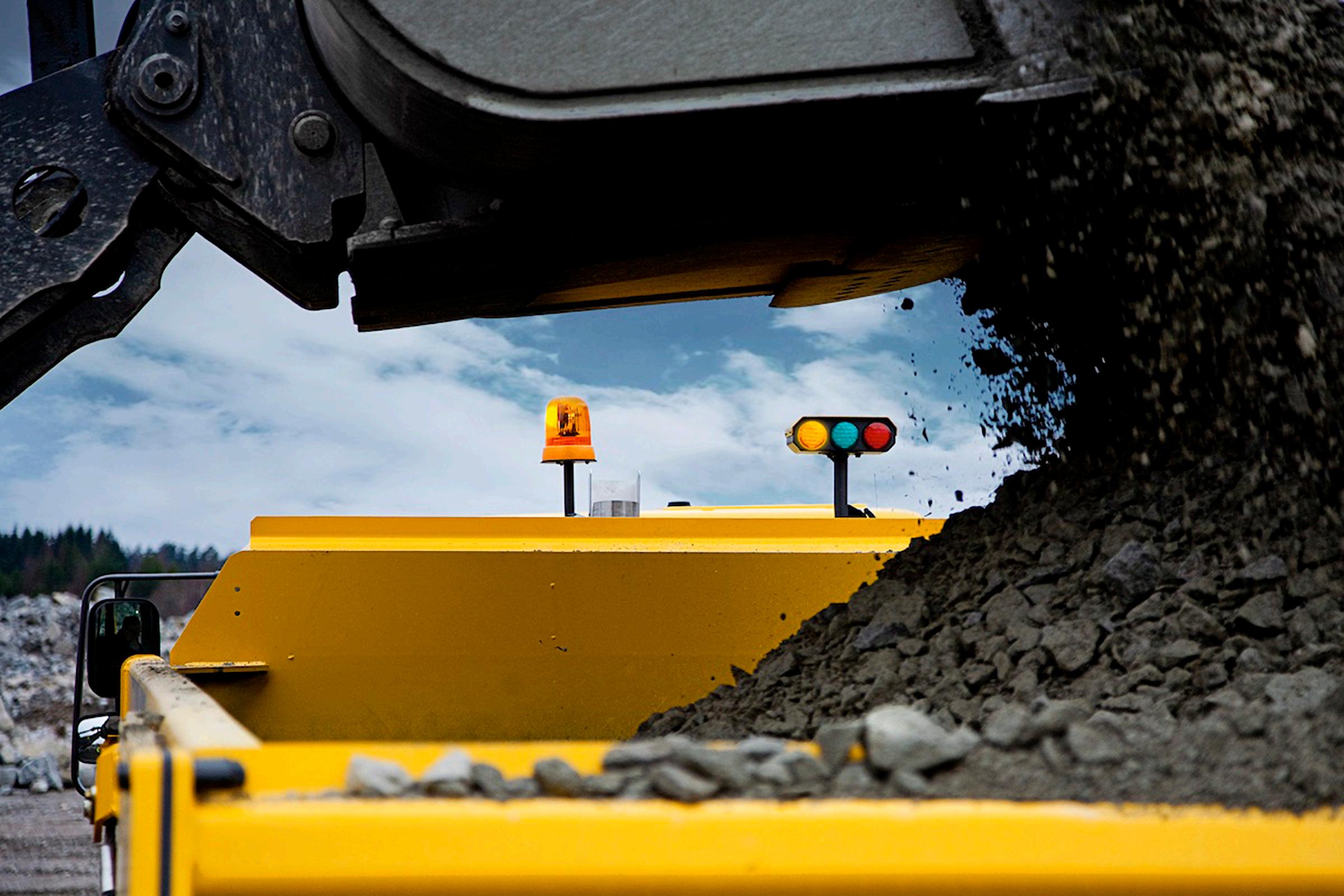
Using GPS functionality on construction equipment to automate tasks is becoming more common, and some OEMs have made these features standard on new equipment. Though many owners and operators are getting more comfortable with—and even dependent upon—technology to help them be more productive, some may still need a little help making sense of it all.
How GPS Can Help

Machine control is now widely used on excavators and dozers, but systems that support GPS can take things to another level for digging accuracy and more complicated shapes. Typically, inertial measurement unit (IMU) sensors are mounted to certain parts of a machine and can tell the operator where the bucket tooth is and therefore, how close they are to a target depth or grade. Upgrades can include satellite antennas and smart receivers, which make up GPS functionality and allow the machine to “know” where it is.
For example, on an excavator, the operator can use an in-cab interface (like a tablet) to draw the shape he or she wants to dig. Let’s say it’s a basement. Then he or she can put the bucket on the ground where one corner of the basement will be, move the bucket to a second spot and that tells the machine to “draw” a wall between the two. Depth and slope can be factored in, as well. Thanks to sensors and satellite receivers, the machine will remember where every point is as it moves.
Upgrading to 3D software like Trimble or Topcon takes GPS support one step further. These programs can import a computer-aided-design (CAD) file for an entire jobsite, such as the roads, water and sewer lines for a housing subdivision. All GPS-equipped machines will know how far to dig no matter where they are located on that site.
Some GPS software allows operators to create layers, as well. Suppose you’re putting in a water line that involves multiple material layers with specific requirements for each. Let’s say you want 6 inches of sand as your base, 3.5 feet of gravel, 2 feet of fill soil and then 1 foot of topsoil. Having a screen show exactly where you