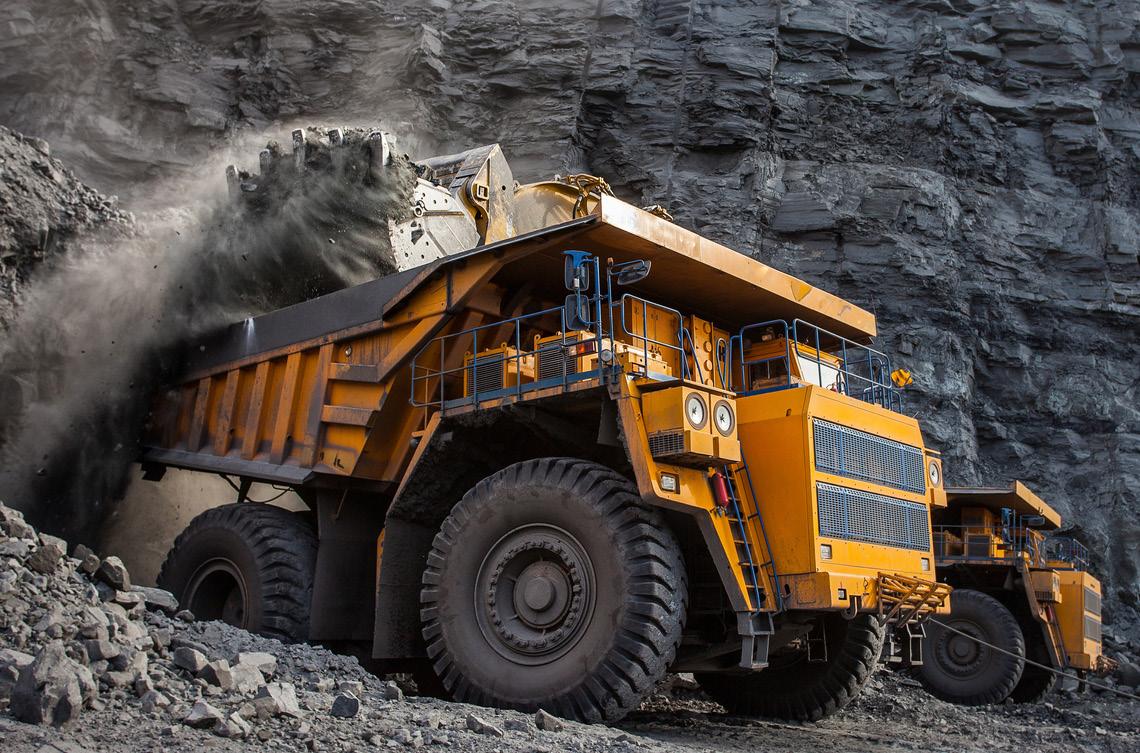
5 minute read
Employing Vehicles with Aftermarket Automation Keeps Existing Fleets on the Road
How COM Express software for small footprints fuels the extended deployment, long life cycle and value of today’s heavy mobile equipment
by Jack London, Kontron | Andrea Thomas, Intel
The trucks and heavy machinery used to build our infrastructure and withstand the rigors of farming, construction excavation and earthmoving, and mining, embody rugged technology. While heavy mobile equipment (HME) has advanced during the last century—continuous improvements to ca-
pabilities, hydraulics and fuel efficiency—more progress is required. Data is in the driver’s seat, sometimes literally, and is the key to smarter, better-connected systems. Today’s telematics and advanced driver assistance systems must capitalize on artificial intelligence (AI), deep learning, GPS, 5G and a range of computer vision applications.
To transform these machines, OEMs must use fleet-specific software and hardware. It should be applicable to a spectrum of automation applications and compatible with existing systems.
Small footprint COM Express modules are an option and demonstrate how aftermarket automation aligns with the extended deployment and long life cycle associated with HME assets. With COM-Express-based systems, developers have an open architecture platform deployable across a vehicle portfolio—a holistic fleet strategy using a single, high-performance system to manage applications.
Automating heavy machinery doesn’t have to mean soaring startup costs or replacing fleet assets. Com Express systems provide customizable, reusable and scalable solutions.
NORDRODEN, ADOBESTOCK
Software HME design needs onboard edge computing platforms based on industry-standard COM Express technologies. COM Express platforms provide two disparate development tracks for data-intensive construction, trucking, mining and agricultural applications.
Driving Flexibility and Longevity
The COM Express standard defines a range of form factors that allow developers to balance flexibility, cost and performance as they consider the needs of their embedded devices. As a result, COM Express is well-suited for small footprint, rugged applications that rely on customization. In system development, modules are paired with a carrier board containing all customization (instead of the COM itself).
This powers system performance across technology generations—for instance, a CPU core can be replaced with a more advanced version when the application requires enhancements or greater performance. It’s an inherent design attribute that adds longevity and flexibility.
Instant Platform or Building Block
COM Express platforms provide two disparate development tracks for data-intensive construction, trucking,
mining, and agriculture applications. One example of an application-ready platform features pre-integrated capabilities for deep learning, in-vehicle AI and high-performance embedded computing HPEC. The platform is optimized for use onboard heavy-duty mobile machinery and features a processor paired with a dual network adapter card and a range of options for graphics, processing units or accelerator cards designed to handle AI and machine learning workloads.
Coupled with built-in AI and machine learning capabilities, the platform’s toolkit helps accelerate the development of high-performance inference and computer vision applications. This allows OEMs to help fleet operators gather and analyze relevant data and quickly develop new processes. OEMs must also consider safety regulations and offer an option to provide functional safety that meets International Organization for Standardization specifications.
Alternatively, developers building their own autonomous applications can use the same platform as a building block. They can access the inherent value of COM Express and customize their carrier boards and solutions.
A crucial advantage provided by these systems is the ability to interpret and analyze data in the vehicle. Almost immediate decisions and actions are enabled near where the data is generated. Outcomes and decision records are transmitted to the control center. Cloud transmission is reserved only for data that is not time-sensitive and is later delivered to datacenters for archive or additional analysis. In this approach, vehicles no longer need nonstop cloud connection. Storage space is also freed in the vehicle-based device, providing real-time or near real-time data as required.
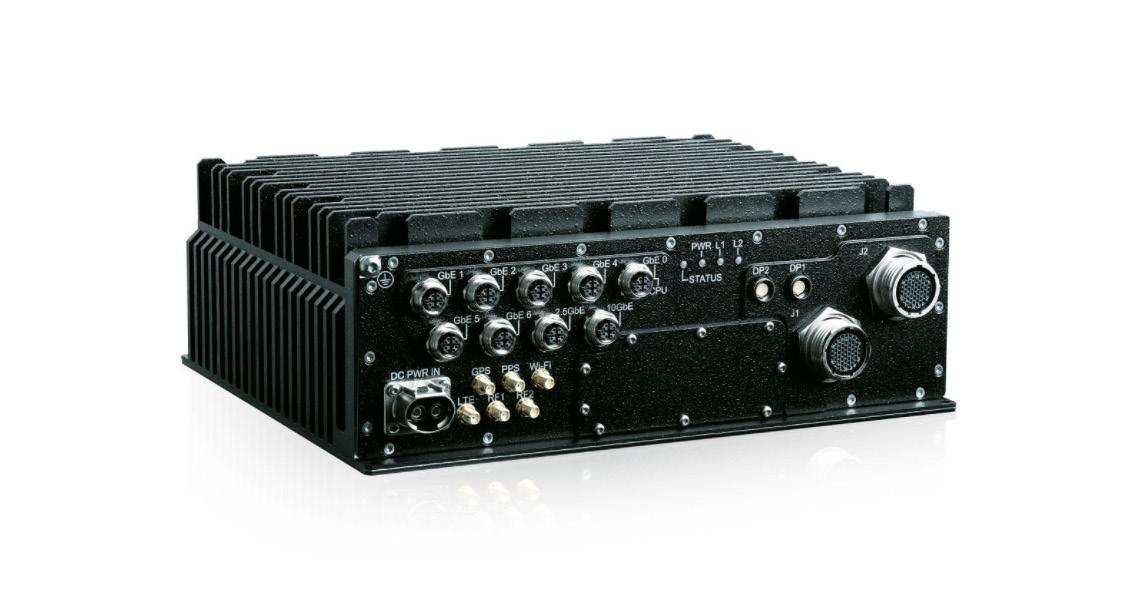
The Impact of Automated HME
The benefits of connected and intelligent heavy machinery include predictive analysis, for example alerting operators to dangerous situations and equipment failures. Predictive maintenance increases uptime and diminishes potential outages. Mechanical data analysis also enables operators to reduce fuel consumption. Predictable costs, such as fuel and insurance, give greater control over expenses and can improve total cost of ownership (TCO). Operating costs are reduced with more precise actions and responses, such as just-in-time analysis of engine parts, low-voltage motors and other mechanical devices. Costs also improve when maintenance crew resources are not wasted on unnecessary rounds. In addition, accidental breakdowns become fewer, and unplanned downtime is minimized or eliminated. Overall productivity increases as payloads are maximized, and bottlenecks are identified.
Aligned with the goal of improved productivity and safety, workers can be removed from hazardous environments. Mining, for example, is inherently dangerous. The industry is moving toward a zero-entry mine landscape in which no humans are physically inside the mine.
Absent humans onboard, heavy mining equipment can go deeper and into more dangerous environments, such as areas with gas buildup. Profitability and mine life can be extended. The mine can be excavated more deeply, and with steeply sloped walls that allow operators to remove more materials, including the lower quality ores often left behind.
With greater efficiency in place, organizations can also free operators to focus on high-value tasks. This is strategic in the face of labor shortages and allows valued personnel to put their insights and judgment to use beyond basic equipment operations. It is also a competitive advantage for emerging economies—their mines can quickly become more viable with automated heavy machinery. Fewer human resources are required to get systems up and operational in the field.
Progress can be made with fewer costly assets, reducing economic and environmental impact. Automation designs with low development and deployment costs, will eventually lower the barrier to market entry for less-developed countries.
Decreased Design Complexity
With retrofit for greater automation, heavy mobile equipment OEMs can equip their components with the technology to secure, observe and use data from other technology-equipped machines for better insight into equipment procedures. Synchronized workflows empower teams and equipment for better, safer productivity.
Effectively and efficiently retrofitting systems is critical. Smart, autonomous solutions are new necessities in HME markets, empowering operators to: • Use machinery safely • Minimize waste • Improve overall production and operations Retrofitting drives new competitive advantages and efficiencies provided by data gathered and processed close to where it is generated. This rapidly evolving environment brings opportunities and hurdles for embedded developers—decreasing complexity is vital, but so is taking intelligent steps to automate for broad competitive value and jobsite safety.
Jack London is vice president, business development, for Kontron North America.
Andrea Thomas is senior product marketing engineer for Intel.
Read More
https://oemoh.co/fjtrkz