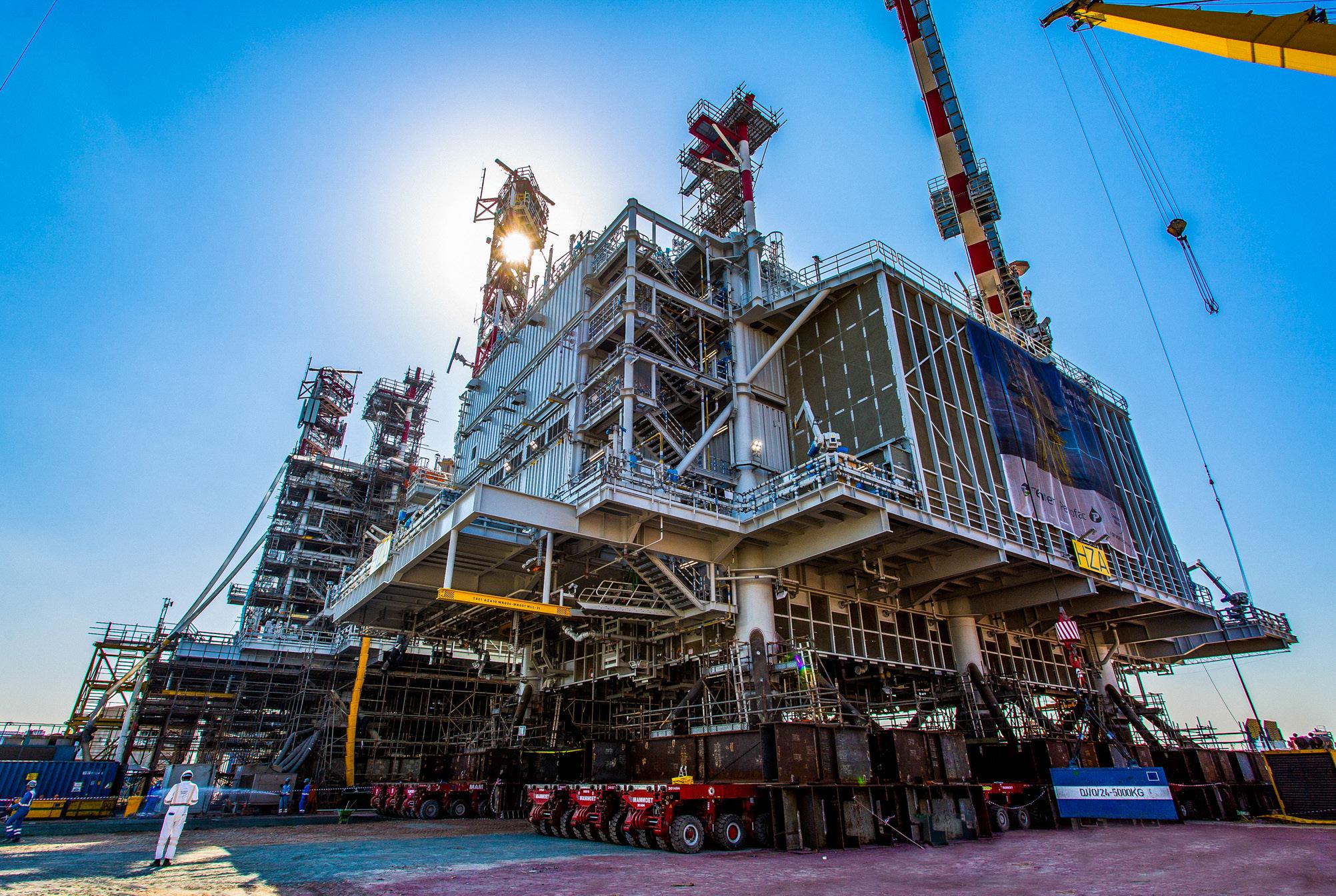
4 minute read
Introduction way of working environmentally
Floating wind can play a major role in the world reaching carbon neutrality in the coming decades, but how will this emerging technology develop so it is deployable at commercial scale?
Ensuring floating wind realizes its potential
Advertisement
A complete floating wind farm turbine consists of a floating foundation, manufactured by specialist fabricators, and the turbine tower, nacelle and blades, manufactured by a wind industry OEM. While the manufacturing process remains similar for everything above water, the sheer size of each floating foundation will mean huge changes to its supply chain, logistics and launch.
Load-out substation in Dubai.
Facilities that fabricate floating foundations will face demand to increase production rates as the sector grows. What’s more, given the broad similarity between floating foundations and petrochemical modules, competition for facilities will be high as they will require the same facilities, equipment and personnel to build.
Space needed for the storage of these giant foundations will challenge even
the largest facilities, ultimately opening the market up to new entrants. Clearly, storing foundations that can measure 100m square on land will not be a viable long-term option, and will mean that manufacture and logistics must go hand-inhand.
Then there is the task of managing the load-out of these huge structures, akin to the demands seen during
Load-out in Ferrol, Spain, for Kincardine project.
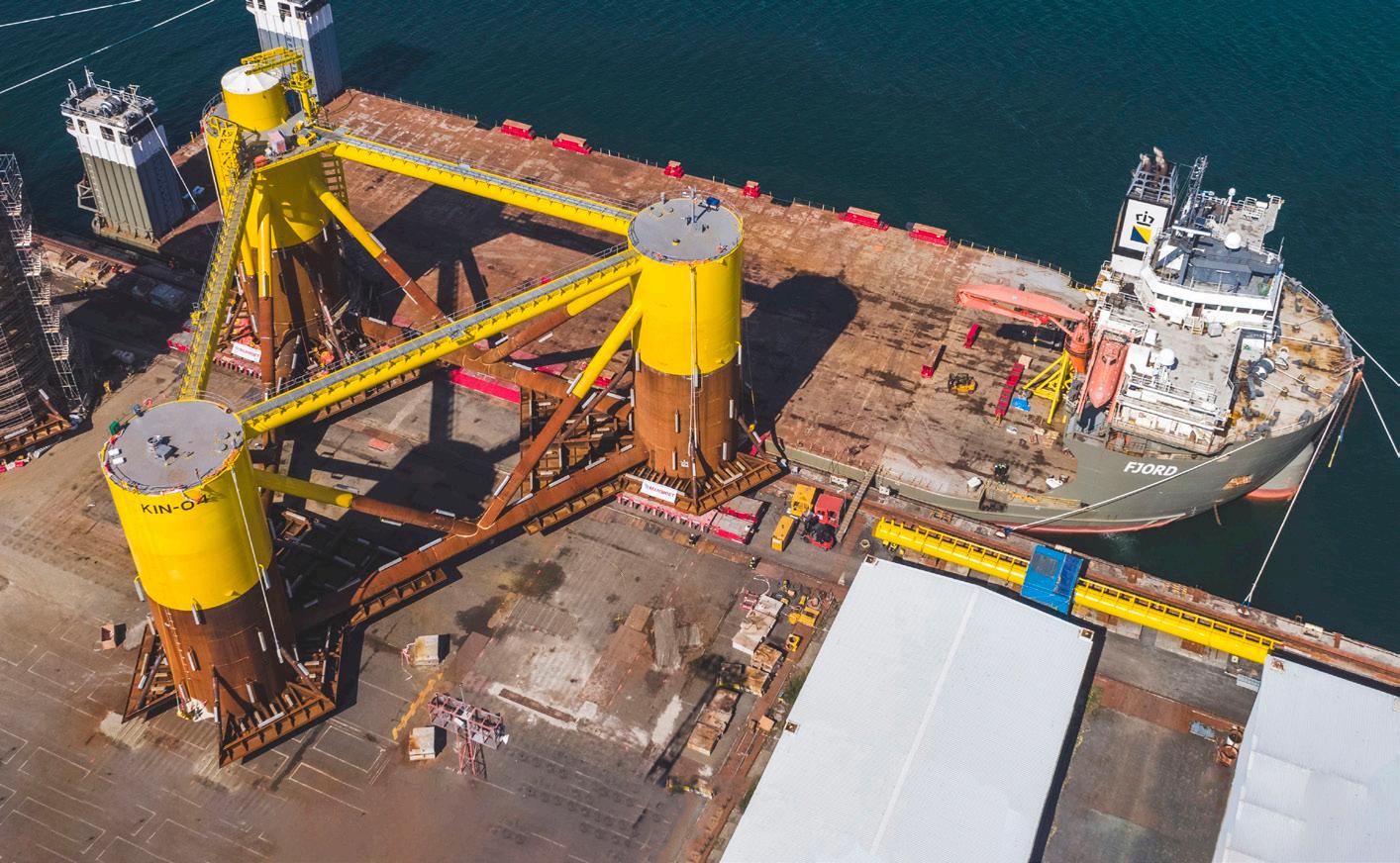
modularized projects for the petrochemical sector. The industry will need to look beyond Europe to locations such as Southeast Asia, China and the Middle East to make best use of the facilities available.
Using multiple fabricators in several locations will allow more of each project to be undertaken in parallel, and by specialist facilities - shortening the schedule of projects and therefore increasing cost-effectiveness. This, in turn, will increase the viability of projects and allow more of them to move forward.
When fabrication of foundation is complete and it’s time to get them in the water, there are further challenges. For one, this must be achieved for the most part without the use of dry docks, as the majority of these will be unsuitable for objects of this size. Ports of a suitable draft are also needed, typically around 12m or more.
Choosing the right partner to handle lifting and load-out operations will be crucial if developers are to best manage risk and increase the cost-effectiveness of projects without being tied to one particular region. Luckily, the expertise that has been used in the past to load-out modules of over 40,000t can be re-deployed to match the needs of floating wind, as foundations grow ever-larger.
Launching 16,000t components
With weights of anything between 3,000t and 16,000t, the launch of floating foundations is far from simple – the key challenge being to find a safe, cost-efficient and scalable method for placing large units in the water.
To date, a range of different solutions have been used to perform launching and one common approach has been the use of semi-submersible vessels. But there are questions over whether enough vessels will be available to meet demand, and whether they will be cost-effective when hired over a long period of time, during which they will be stood idle for long periods. So, what are the solutions for projects where this is not a suitable - or available - option?
Mammoet has found that moving foundations directly into the water is the most effective method of launching, as opposed to the use of transition equipment such as a floating platforms. A promising methodology is to use a hybrid approach, whereby the floater is lifted from both land and sea and lowered onto the water directly at the quayside.
As components are placed directly into the water right next to the quay, the process takes less time, is therefore less costly and requires less auxiliary equipment – generally needing only commonly available grades of barges.
Super crane capacity
With water depths at sea ruling out assembly solutions such as jack-up vessels, the most efficient way to integrate turbines onto floating foundations is to position the floater in the water directly alongside the quay, and piece it together using a large crane. But crane assembly presents its own challenges.
As already mentioned, the largest floating foundations can be 100 meters square. If the turbine lies close to the center of the foundation, the lifting radius required could be as much as 55m – that is, half of the foundation’s width plus the space between quay edge and crane.
At the same time, nacelle weights are expected to reach 1,000t in the near future, and hub heights a staggering 170m. This means that even the largest of crawler cranes are no longer sufficient, and that far fewer suitable cranes are suitable than the market may realize.
Given that a large capital expenditure investment to purchase a suitable crane is unlikely to be an appealing option for many, Mammoet is able to provide a large ring crane that lifts some floating foundation types directly into the water and also assemble wind turbines - all from a single position – turning the quayside into a highly efficient production line.