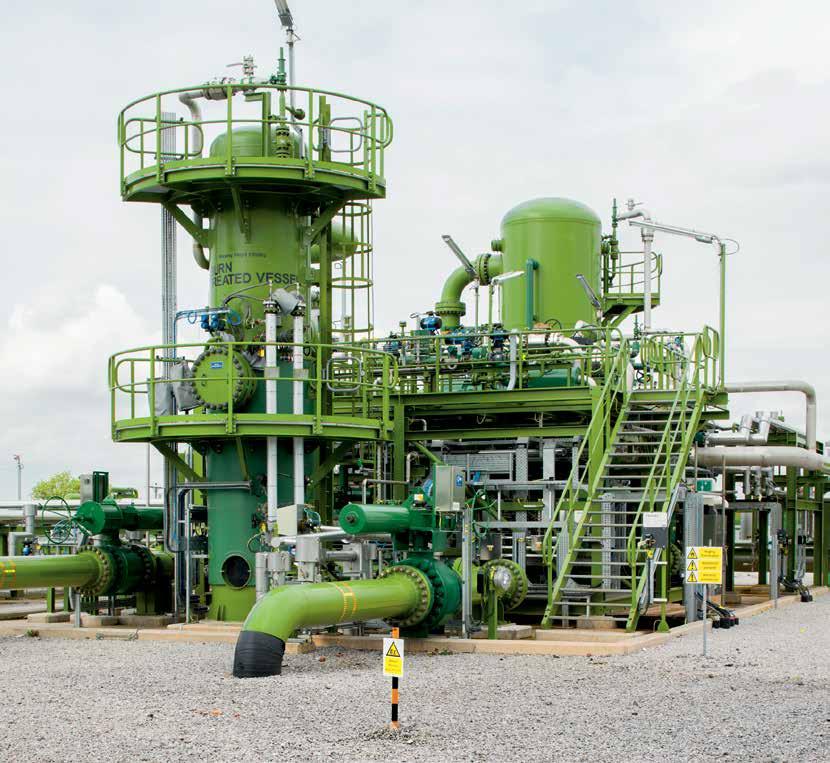
8 minute read
Gas treatment packages
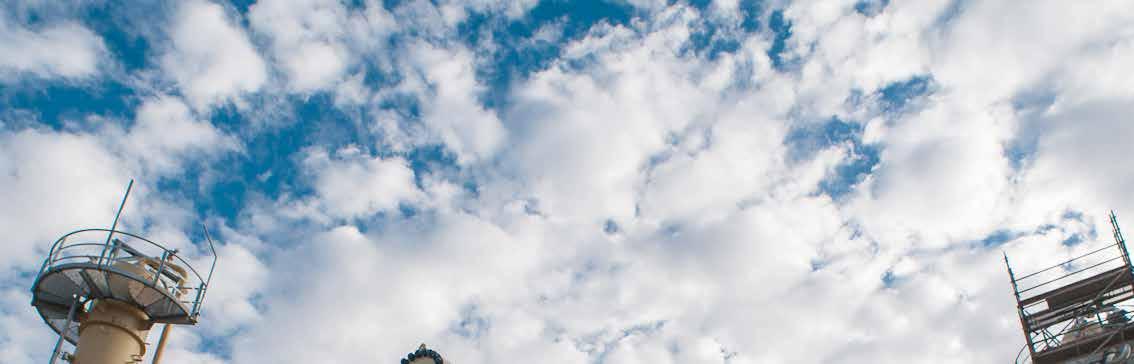
Advertisement
Allwyn Rodrigues, project manager Frames.
Supply contract for Frames
Gas treatment packages for South Ghawar LNG processing
Leading energy equipment supplier Frames has been awarded a contract to supply engineering contractor, JGC Gulf International Co., with dehydration and water treatment packages for production of natural gas by Aramco Unconventional Gas Program in South Ghawar.
Aramco is developing infrastructure for processing unconventional gas to meet in-Kingdom energy demand and to reduce liquid burning at power generation facilities.
The Unconventional Gas Program is a series of projects to be undertaken for Jafurah and South Ghawar. The South Ghawar basin is a key unconventional tight sand gas asset in the Eastern Province of the Kingdom of Saudi Arabia. JGC Gulf International Co. is building the main gas separation plant in which the Frames triethylene glycolbased (TEG) dehydration and Produced Water Treatment (PWT) packages will operate. The TEG dehydration package is a liquid desiccant technology for the removal of both water and CO2 from natural gas, thus preventing corrosion problems in downstream processes and equipment. Frames standardized produced water treatment packages reduce the oil-in-water content, typically from 2000 ppmv to 20 ppmv. The separated water is then pumped back into the reservoir to maintain the pressure in the well.
“Frames TEG and PWT packages are compact, skid-mounted systems that can be readily integrated with other plant processes,” says Allwyn Rodrigues, Frames project manager. “We are working closely with JGC engineers to enable their optimum performance for the Unconventional Gas Program in South Ghawar.”
Ready for new offshore industries
Engineered initially for the wind turbine industry, over the past few years the VPI Cable Hang-off system (HOS) has been further engineered and developed by a dedicated innovation team, which has resulted in the VPI Cable Hang-off system evolving into a multifunctional offshore solution. In addition, the Cable Protection System (CPS), also known as cast-iron pipes, is a bespoke and tailor-made solution for various industries, including submarine telecom cabling, high-voltage subsea power cables, and from this decade the oil and gas electrification. From every project that is successfully delivered, Vos Prodect innovations (VPI) learns and adapts from its experience to ensure that they are servicing the electrification of the offshore industry in the most effective manner.
Within the industry, VPI has gained a reputation of quality and has been trusted with over 150 projects, supplying VPI’s cable protection system across the globe. In recent years, VPI has been established as the market leader in the engineering and supply of cable hang-off systems. Over the last 60 years, the company has constantly reinvented itself in the face of shifting market demands and industry trends. Three generations of cable protection systems have already been established for various industries and are now ready for the next step: the electrification of oil and gas platforms.
Changing markets
Becoming increasingly prominent in both the professional and personal lives, sustainability and the fight against global warming needs to be addressed imminently.

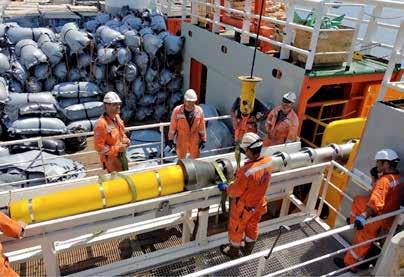

Marc Derks , CEO VPI.
One major factor to combat climate change is the production of renewable energy, a field in which VPI is heavily embedded and has a vested interest. In conjunction with these notions, VPI has focused within the other offshore industries to see whether any further sustainable innovation can be applied, as many of these industries are being supplied with fossil fuel power. VPI is exploring the various options into providing renewable electricity sources for these platforms, to further address sustainability and reduce greenhouse gas emissions.
The main transition that VPI actively promotes is to attain electricity that is provided by a subsea cable from the mainland facility instead of using an offshore power generator. VPI can deliver both protection systems to accommodate submarine electricity cables from the mainland facility to the offshore facility, as the VPI Hang-off System is designed for securing medium and high voltage power cables to the top of a cable deck of a monopile, jacket, or rig. VPI’s Cable Protection System (CPS) serves to protect and stabilize the subsea power cable and VPI’s Hang Off-System secures the electricity cable during the installation on an offshore platform and securely locks the cable after final installation. Both systems have been tested extensively, it is a proven solution for offshore projects which has been delivered successfully across a wide range of projects.
Hybrid protection system
VPI’s CPS consists of two primary products, including VPI CIS (Cast Iron Shell) and VPI HPS (Hybrid Protection Shell). The VPI CIS is utilized for the cable in contact with the seabed and the VPI HPS is utilized for the free span areas leading into the offshore platform. The VPI CIS, also known as articulated pipes, is cast from cast iron half-shells whereas the VPI HPS is formed using the cast iron half-shells along with an outer polyurethane shell, to provide extra corrosion protection around the free span areas.
Precious time
The multitude of benefits the revolutionary system offers ensures that the cable is fully protected and will remain intact being situated at the bottom of oceans for decades but also due to being an innovated hybrid system, this significantly reduces installation time by 50%, offering potential cost savings across the life of the project.
VPI’s CEO Marc Derks stated: “Out of personal experience, I recognize that our offshore systems need to be fast and easy to install, saving precious offshore time. Our universal system is fast to install as we offer a self-locking system, so no bolts are needed. The combination of the polyurethane surface and the cast iron insert, provide all the protection required when your cable lay upon the bottom of the ocean. The VPI CPS also offers additional benefits of bend restriction and impact protection.’’
Offshore collaborations
VPI’s collaborative and open approach enables them to work closely with their partners, to further promote sustainability processes, and to understand how they can further enhance custom-engineered products to suit. Another innovative product that has been engineered as a result of this collaborative approach, is the J-Tube cable protection system along with other subsea cable accessories. VPI’s J-tube cable protection system is a hybrid product withstanding against drag and the accompanying effects such as VIV and fatigue. The system has been successfully tested and deployed across numerous projects.
The combination of both their own experience along with those views of their partners who install and work with VPI’s offshore products enables VPI to learn, engineer, and innovate their products further, whilst focusing on sustainability throughout the entire process. An example of this can be demonstrated when VPI successfully installed the first onshore landing clamps this year, including on the beach of Ameland. This ‘Beach Clamp’ is now being used for securing a power cable of the NAM, which is currently electrifying three offshore platforms for the production of natural gas.
Emerging business in challenging times
Maritime Construction Services (MCS) provides high quality project management and engineering services to the oil & gas majors and main contractors worldwide. The services of the company range from pipelay, heavy lift and SURF to SAT diving. In addition, MCS services its clients in the construction of ports & terminals and vessel management.
MCS has been established in 2015 as an independent Dutch entity to execute international projects and deliver project management, tendering, business development and commercial support. The exclusive partnership with various stakeholders assures direct access to owned assets and unique experience in reference to turnkey construction of oil and gas subsea facilities, pipelay and port and terminal constructions. In addition, MCS has access to local offices worldwide, to service its clients on site.
Fleet
For the delivery of projects, MCS has an extensive fleet of (construction) vessels. This includes dredgers, tugs, pipelay/derrick barges, but also DSV’s. A unique asset to the fleet is the DP3 Multi-Purpose Vessel Everest.

Due to its characteristics, the MPV Everest can continue operations safely, in remote areas and in the harshest weather. With 1,400m2 of deck space a large quantity of project equipment or subsea structures/ parts can be brought on board or lowered. The MPV Everest is equipped with a 250MT Active Heave Compensated crane, three state-of-the-art ROV’s and a twin bell 18 person saturation dive system, making the vessel particularly suited for subsea construction and other specialized projects.
In 2019 the Everest was deployed in Indonesia. MCS, together with its partner DCN-Diving was contracted for the execution of an extensive campaign to connect the subsea infrastructure to the subsea gas transport pipelines. The MPV was deployed for installation and diving support operations.
During this project the Everest, equipped with two dive bells, ensured a 25% reduction of dive operations time. Finally, when the monsoon started and all other vessels in the field were waiting on weather, the MPV Everest continued to work tirelessly. Another noteworthy project performed with the MPV Everest is the project performed for the Australian Antarctic Division (AAD) early 2021. With the Everest, MCS executed supply services in the Arctic. The project included resupplying several AAD bases in Antarctica, where research is carried out into climate change in the Arctic. Despite a major challenge, the project was delivered successfully. During project execution a fire started onboard the vessel, which led to serious damage to the vessel. Fortunately nobody was injured and due to the DP3 capabilities of the vessel it could safely return to Australia. After full investigations into the cause of the fire, the Everest has been fully repaired and all recommendations following the investigation have been implemented.
Russia
Today, the MPV Everest is back in business and working in the east of Russia on a project which includes the installation of subsea infrastructures with divers and ROV’s. The first part of this project was executed in 2020 already. MCS is also supplying technical support to several port installation projects in Russia. To follow up on the growing demand and the ambitions for the future, expansion of the MCS team is part of the agenda.
