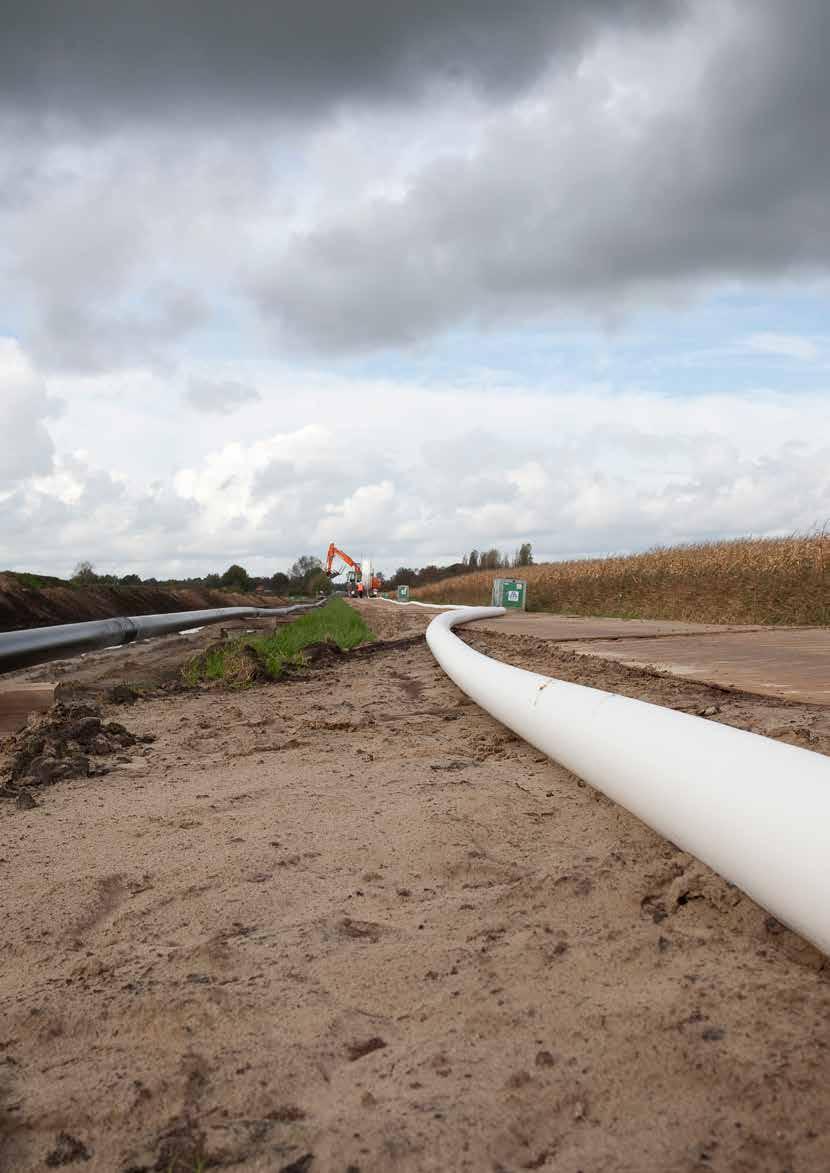
5 minute read
CO2-free energy
Energy efficient infrastructure for CO2-free energy
Since the EU set the goals under Green Deal in order to become climate-neutral by 2050, all sectors have been motivated to integrate renewable energy solutions. Green hydrogen is seen as one of the solutions to integrate more renewable energy acting as an energy-storing medium. However, before it can be fully utilized as such, there are still some challenges to overcome.
Advertisement
“If Europe wants to reach its target of climate neutrality, there is no way around hydrogen. By 2050, it must be firmly anchored in the European energy landscape. I think that by then, half of the energy mix will be electricity, mainly from solar and wind power, and the other half will be hydrogen,” says Ad van Wijk, Delft University of Technology.
So, why isn’t green hydrogen already supporting our lives with sustainable energy? The issue lies in the framework – the production of green hydrogen, the construction of hydrogen infrastructure as well adaptations of appliances. While some of the necessary technologies have reached maturity, others, such as networks for high-pressure hydrogen, still need to be improved in terms of reliability, cost-effectiveness, and sustainability. To facilitate/improve the distribution of high-pressure (green) hydrogen, it is needed to first implement a suitable, viable, and sustainable infrastructure. So, how can we effectively implement the promising solution?
Long-lasting solution
Sometimes, we need to leave the known in the past to enable change for the better. Especially, when it comes to innovative solutions. To facilitate the transportation of green hydrogen, we need to reconsider its infrastructure. The steel pipes that are traditionally used for conveying hydrogen are considerably heavy and inflexible, making their transportation and installation process costly and time-, and energy-consuming. Apart from this, metal pipes commonly suffer from hydrogen embrittlement and thus have a limited lifecycle. To solve these issues, SoluForce (a brand of Pipelife) has developed an innovative piping technology, based on extensively proven technology. Marking a milestone that plays a part in accelerating the feasibility of green hydrogen infrastructure.
The SoluForce pipe system, on which the hydrogen certified pipe is based, has been on the market since the year 2000 with over 3.500km installed around the world in various applications such as oil and gas, water and mining. RTP (Reinforced Thermoplastic Pipes) consist of HDPE and synthetic fibers making them more sustainable in production than traditional pipes. The pipes score with their flexibility and availability in long lengths up to 400 meters, simplifying the construction process considerably. Their most prominent advantage is, however, their perseverance. Other than steel pipes, RTP do not suffer from hydrogen embrittlement or corrosion and so can be utilized for an extended period without maintenance. The ease of installation due to the flexible nature of SoluForce hydrogen-certified pipe systems saves on time and resources while ensuring the longevity and endurance of the pipe infrastructure. In addition, the production, transportation, and installation of RTP require significantly less energy, reducing the carbon footprint by 4 times.
Hydrogen
Currently, SoluForce is taking part in a project in Eemshaven to distribute hydrogen with its high-pressure pipeline. For the near future, the Netherlands is actively working on a model project in the Province of Groningen, where they are constructing a massive offshore wind park. The park will be built to produce clean electricity which then will be converted into green hydrogen with the process of electrolysis, supplying Groningen Seaports (a port operator in the north of the Netherland) with green power via a complete hydrogen piping system.

Seal For Life Industries Group boasts a wide range of brands offering coating and sealing solutions to infrastructure markets. With a history of more than 60 years, over 700 employees, more than 250 patents and formulations and customers in over 90 countries Seal For Life is has a wealth of experience to offer its customers.
Combating corrosion with traditional and new methods
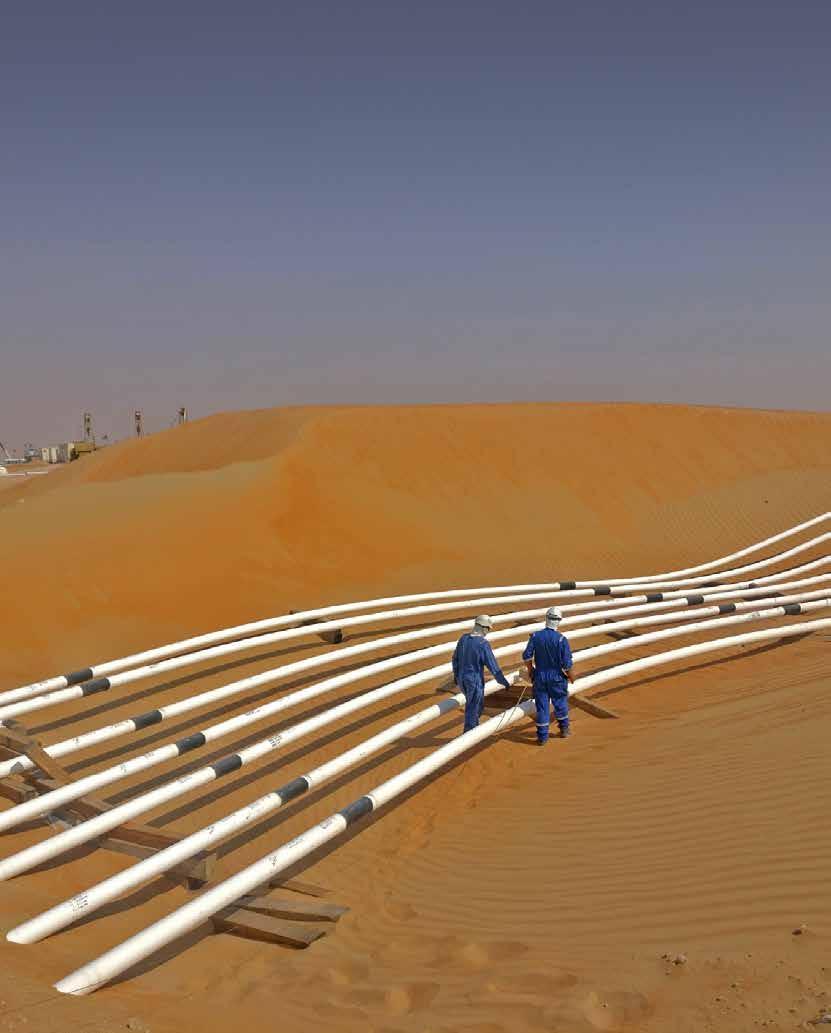
Polyken application in Abu Dhabi, UAE.
Heat shrink sleeve protection by Covalence in UAE.

Our coating technologies are approved, specified and deployed globally with a focus on corrosion prevention, fire and temperature protection and cathodic protection for pipeline, oil, gas, water, infrastructure and industrial applications.
Projects
Powercrete QC, R&D and Technical Service Teams in India completed an HDD project with Powercrete DD for Mahangar Gas Limited. Protection was provided to 850m of 8” Pipe in extremely rocky soil and difficult conditions.
An extensive gas pipeline project has been completed in Croatia including field joints, bends, flanges and risers throughout. Apart from the basic system, Stopaq Wrappingband and Outerwrap, due to the rocky areas Outerglass Shield was added at the field joints and SFL RockShield for the main pipeline running underground, subsea and above the ground. In addition, the casings were filled with Stopaq Casing Filler.
China Petroleum & Pipeline Bureau Indonesia awarded Seal For Life the supply contract for a 14km offshore and 7km onshore Balikpapan Project using Covalence 2 Layer series to protect the field joint areas on the large 52” OD 3LPE coated pipeline transporting crude oil.
After successfully supplying SHWE Phase I in 2015, Seal For Life Industries were awarded the complete supply contract from McDermott Malaysia (EPCIC) for the SHWE Phase II Project. Supply scope consists of Covalence heat shrink sleeves (WPC100M) for field joint coating (FJC) of all subsea flowlines, risers and umbilicals for in total 75 km 6”, 12” and 14”.
A flange connector on a Gas scrubber/ coalescer V1109 on the G17 A-Platform for Neptune Energy was recently protected with Oxifree TM198 by their Global Services Team. The 1650mm diameter flange was suffering from corrosion due to the offshore environment. The Oxifree Technician completed the project coating over 3 days and TM198 will now provide long term protection.
Polyken 1600HT is being applied to flowlines in Abu Dhabi for ADNOC. Polyken has been selected as a reliable cold applied corrosion protection solution for both below ground and above ground applications. Polyken offers corrosion protection, mechanical protection, withstanding high temperatures and UV protection being suitable for existing and new lines.
Over 8,500 field joints are being protected with Covalence Heat Shrink Sleeves in the UAE.
We are delighted to be working with two EPC contractors on this project, who are first time customers of Covalence for water pipelines in UAE.