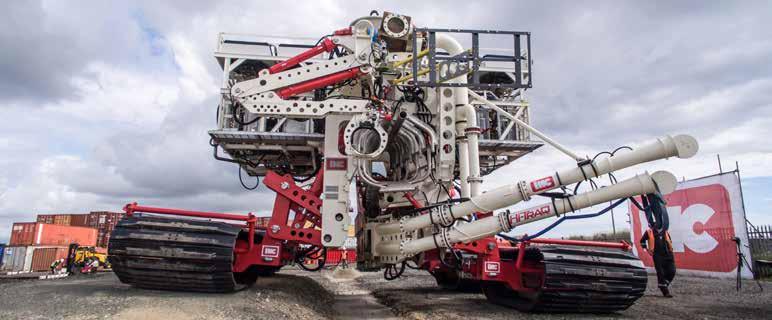
59 minute read
Energy transition
chapeau Disruptive technologies – Pushing the boundaries
Changing Energy Landscape
Advertisement
Energy transition and a drive for reduced reliance on imported energy is further accelerating the already rapid development of the offshore wind industry. As the future power source of choice compared to other established fossil fired and nuclear options, offshore wind is being quoted as being cheaper than nuclear power with much easier public acceptance.
The Biden administration have announced plans which would see 30 gigawatts of offshore wind energy being in place by 2030, equivalent to the current capacity available across Europe. This plan represents approximately 2,000 offshore wind turbines supplying 10 million homes.
Notwithstanding the drive for increasing capacity as quickly as possible, there is a focus on reducing the cost of offshore wind while increasing the quality of the installation. This requires constant innovation as the issues and problems faced by customers are defined. ‘Reduced cost – faster, safer, higher quality operations’ are the key market drivers.
In support of this, industry has stepped up to the challenge, presenting disruptive technologies and processes that enable the work to be done more economically with step changes in performance. This innovation is taking place both in the technology and business models that are being offered to the industry.
Changing status quo
However, introducing new technology is not an easy process with new
techniques and products requiring rigorous testing and proving programmes prior to first use in a commercial application.
Essentially, there is a mismatch between the requirement for technological advancement and the perceived risk profile of the projects which demand proven methods and procedures. The result of which is that new systems only come into play when the cost benefits they offer clearly outweigh their perceived risks.
Cable Conundrums – Trenching
Offshore wind farms feature multiple short runs of cable connecting wind turbines to each other and then to a substation. The approach of the cables to the turbines and especially to the sub stations requires trenching in tight geometrical constraints.
Due to the requirement for relatively tight radius trenching turns on the approach to turbine towers and offshore substations, the trenching vehicle must be very manoeuvrable. However, traditional two track systems experience a number of issues including:
• Skid steer reducing forward cutting pressure • Sudden pitching as the trencher centre of balance moves over the crest of a sand-wave or obstacle • Fixed suspension leading to variability in grading of the trench when passing over boulders or ice scour regions
Royal IHC produced a technology demonstrator to show how these challenges could be overcome. Based on the results delivered by the demonstrator, a production variant was developed and constructed. The Hi-Traq (High Traction) Trencher was purpose built to provide high traction capability and manoeuvrability in difficult seabed topographies and high currents which are common in shallow water. The Hi-Traq incorporates high traction drives ensuring it can climb the subsea slopes and boulders it may encounter while maintaining the product grading within the trench.
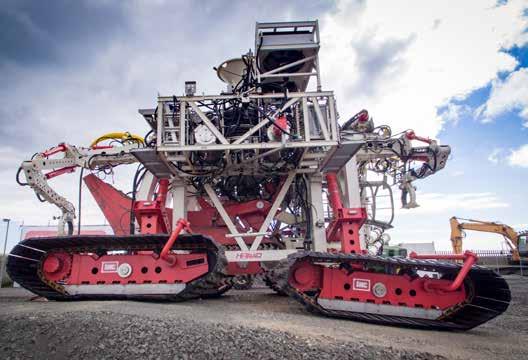
Traction capability is strongly governed by the Mean Maximum Pressure (MMP) of the tracks on the seabed. The Hi-Traq employs several techniques to allow a high ground contact and even ground pressure to provide maximum traction in all conditions:
Pivoting tracks - Each of the four tracks is capable of pivoting, allowing them to follow the contours of the terrain with no reduction in forward cutting pressure Active suspension - As with a pipe line plough’s adjustable skids, each of the pivoting tracks is mounted on active suspension arms to maintain a vertically sided, well graded trench even in the event that the vehicle is manoeuvring over boulders or ice scour regions. No Breakover point - Since the vehicle has four pivoting tracks it does not exhibit the phenomenon of a breakover point which is the sudden pitching of the vehicle as the centre of balance moves over the crest of an obstacle. Grading control - Ability to use the loads the product applies to the vehicle to allow smooth product grading within the trench due to changing bottom topography of the seabed.
Building track record
Even with a comprehensive test and demonstration phase and Royal IHC funding the production of Hi-Traq, the route to market wasn’t quite as planned.
Despite positive signals from the offshore wind installers, no-one was willing to accept a vehicle with no operational track record.
The story may well have ended there, but thanks to the resilience of all involved in the project and a client who was able to see the potential and disruptive advancement that Hi-Traq could bring to their application, it is now in active operation and performing as expected across multiple trenching markets.
A second iteration is now in development which will introduce further step changes in innovation, fully releasing the potential of Hi-Traq to operate across multiple markets and applications.
Understanding and optimisation of bubble screens in offshore wind sector installations
During model tests, MARIN has gained new experiences and insights into the hydrodynamics of bubbles within the Bubbles JIP. Ultimately, the research will lead to improvements in bubble screens deployed offshore.

Figure 2: Hydrodynamic measurement system operating in bubble curtain.
A consortium of research institutes and industry partners involved in the offshore wind sector started the Bubbles JIP in 2019. The aim of the JIP is to achieve more efficient and effective use of bubble curtains deployed for noise mitigation in offshore installation projects by improved engineering of the bubble screen. Within the JIP, MARIN is involved in the laboratory tests and modelling of the hydrodynamics of the bubble curtain.
Improved engineering
Bubble screens are currently used to mitigate noise during the installation of offshore wind turbines. The noise generated by high-energy piling of the turbine foundations could potentially harm marine life. Improved engineering of the bubble screen would lead to better control and therefore, risks with respect to specific noise requirements are reduced. To accomplish these goals, laboratory tests are conducted to investigate parameters influencing the noise attenuation by air bubbles. Additionally, the understanding of bubble generation and bubble growth over the water depth under the influence of waves and currents is also addressed. A more efficient use of the bubble curtains will limit the CO2 footprint due to overcapacity of the compressors used to set up the bubble curtains.
Hydrodynamics
The tests are divided into two separate scopes. The first set of tests was conducted in the Concept Basin
Figure 1: Bubble curtain in the Offshore Basin (photo GROW).

and focused on the bubble generation with different types of delivery hoses and a range of air supply rates. For each of these configurations, the gas fraction and bubble distribution are measured throughout the bubble plume. A new measurement system has been developed to be able to measure the gas fraction, based on conductivity measurement techniques and optical techniques. Combining the optical and conductivity techniques gave a fascinating insight into the hydrodynamics of the bubble screen as a result of a variation of various bubble generation hoses and different mass flow rates.
The second scope is performed in the Offshore Basin, to understand the behaviour of the bubble screen in different environmental conditions. No scaling is applied in these tests, since linear scaling would not deal with the laboratory environment and the size of the bubbles, due to water depth, temperature, salinity and other aspects. Based on previous acoustic tests, the Offshore Basin was suitable to perform acoustic and hydrodynamic tests on a bubble plume with a depth of 10 m in combination with environmental impacts such as currents. The influence of currents and waves is investigated in these tests and the same measurement system is used for these tests in waves and currents in deeper water. A linear bubble curtain over the width of the basin is produced, which is shown in figure 1. The bubble concentration, gas fraction and bubble distribution are investigated over the full depth of the bubble plume. This gives insight into how the bubbles rise and interact on their way up to the surface.
Acoustic tests
To measure the noise mitigation of these bubble screens in a controlled environment, acoustic measurements are performed as well. With the assistance of TNO, the noise transfer of bubbles is investigated for all hose parameters, as well as for the influence of waves and currents. The results of the hydrodynamic, acoustic and measurements on air pressures and flow rates will be used in the numerical modelling of bubble curtains. It turned out that the bubble size distribution is different for different types of hoses and also depends on the environmental conditions and hydrostatic pressure. Within this project the expertise of all the partners contributes to the optimisation of bubble screens in offshore wind applications.
The Bubbles JIP is supported by the Netherlands Enterprise Agency (RVO) and TKI Wind op Zee. The partners in the ‘GROW’ consortium are: Boskalis, IHC, Seaway Heavy Lifting, TNO, TU Delft, Van Oord, Heerema Marine Contractors, Wageningen Marine Research and MARIN.
New modes of fast, reliable and efficient transport for offshore crew and provisions promise to boost operations for offshore energy operations. Vessels that sail at high speed even in the roughest conditions and that are able to provide safe and easy transfers from ship to offshore assets offer improved crew welfare along with increased passenger capacity and a comfortable ride.
Next generation of offshore crew change
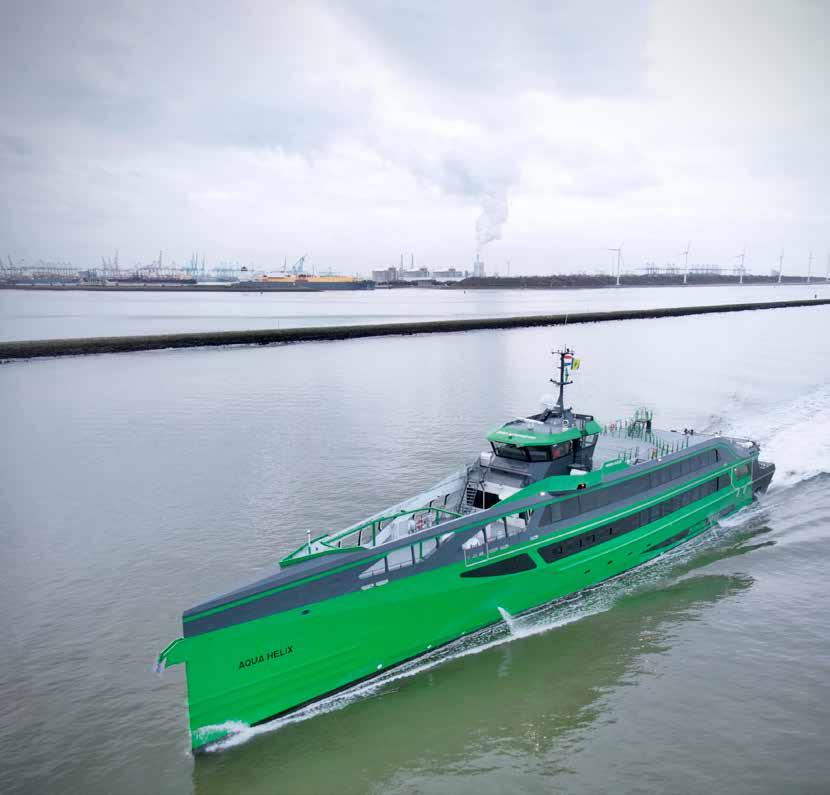
The portfolio of Fast Crew Suppliers (FCS) from Damen Shipyards offers solutions which are able to sail at speeds of up to 40 knots and cut through waves with heights of up to three meters, typical North Sea conditions on its more windy days. It is the Damen Axe Bow that enables its largest crew supply vessel to date, the FCS 7011, to power up the waterjets to reach its impressive speed in such waves. Likewise, the twin axe bow design of the FCS 2710 ensures seaworthiness at speed in rough conditions. Both vessels are purpose-designed to offer very comfortable crew transport along with impressively modest fuel consumption and low emissions.
Proof of concept
At the end of March 2022, the all new FCS 7011 Aqua Helix completed the first actual transfer of crew to an offshore substation in the North Sea. The final testing to demonstrate the proof-of-concept of the 120-passenger vessel followed extensive sea trials and testing of the onboard Ampelmann stabilized gangway. The fast monohull FCS 7011 (with a length overall of 73.6 meters and beam of 11.2 meters) is built in aluminium. The weight reduction achieved by choosing this lightweight material makes it possible to sail at such high speeds.
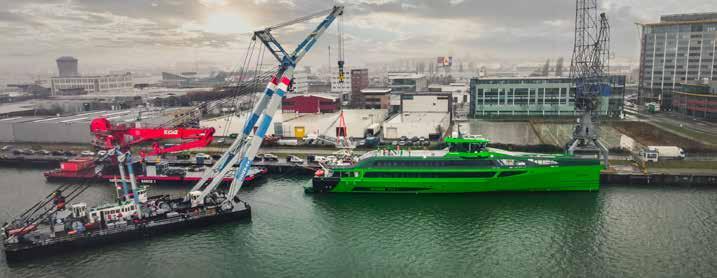
The axe bow greatly reduces slamming end pitching while the biggest gyrostabilizer in the world reduces rolling at zero speed down to 10 per cent of the motion that would otherwise occur without stabilization.
Once the FCS 7011 is positioned alongside a platform or installation at sea to transfer its offshore workers, the Ampelmann gangway can swing out to a maximum of 180 degrees. This allows the vessel to optimally position itself with regard to the incoming wind and waves. The gangway can then extend to a length of 26 meters.
Gyroscope-fed computer technology enables the S-type stabilized gangway to be completely motionless relative to the platform balcony, so the offshore workers can transfer easily and safely in harsh and remote offshore locations. Major offshore energy players like Shell and Exxon provided valuable input that inspired Damen engineers to develop the vessel. Damen Shipyards and Ampelmann joined forces to operate this game changer in offshore crew transport in-house. The passenger capacity of 120 persons is bigger than the typical crew change at North Sea platforms and, thanks to its speed and capacity, Aqua Helix can deliver and retrieve personnel from multiple platforms in a single trip and still offer competitive transfer times and enhanced comfort compared to helicopters. Other areas that require larger numbers of crew to be delivered in a single transfer, for which the FCS 7011 is ideally suited, include offshore West Africa, Australia, Guyana, Brazil and the Gulf of Mexico, where offshore platforms are often further out to sea.
Hybrid
The twin axe bow FCS 2710, is another vessel that has met with an enthusiastic reception from the offshore industry. It is a catamaran design that offers capabilities that fit with the demands of offshore supply but at a smaller scale and is especially popular in the offshore wind sector. As with the FCS 7011, the axe bow design enables fast sailing on rough seas and the catamaran format offers excellent stability.
As part of their commitment towards sustainability, and in line with the objectives of the global offshore wind sector, Damen Shipyards have developed alongside their fuel efficient diesel powered FCS 2710, the FCS 2710 Hybrid. 26.8 meters long and10.5 metres across, the vessel can take up to 26 passengers, has 90 square meters of deck area for assorted cargo and can reach speeds of up to 25 knots. A 232 kWh battery pack allows sailing with zero emissions in port and within offshore wind farms. The generators and main engines are fuel efficient even without electrical support and all comply with IMO tier III emission standards. With a fleet of FCS 2710s already in operation, Damen Shipyards has started c onstruction of three more of the hybrid vessels at the Damen Antalya yard to be built for stock. The shipbuilder is convinced that these vessels offer such superior capabilities for offshore operators that they will be quickly sold. For clients, buying their vessels from stock means extremely short delivery times. Customisation involving the addition of cranes, additional battery packs and other deck equipment to meet specific needs can also be done prior to delivery.
Change
Damen Shipyards Group has set out to revolutionize the offshore crew change market with their fleet of fast vessels offering genuine alternatives to the current helicopter business model. Improvements in safety, costs and fuel efficiency are the pillars that support Damen together with its partners in their drive to change this market. More than any other, the flagship FCS 7011 demonstrates the potential that these vessels have to transform the entire offshore energy market.
Air cooled and dehumidified by POD Cooler
VDL Klima develops and manufactures heat exchangers, coolers and ventilation systems for various industries, such as the maritime industry, on & offshore wind and the oil and gas industry. One example of a product for the maritime industry is the POD Cooler.
Ships, they come in all shapes and sizes. One ship is used to transport goods, while another serves as a luxury cruise vessel. But what remains the same for all ships is that they are powered by an engine with propeller. This is one of the points where VDL Klima is asked for its expertise. It is crucial that this engine, whether fuel or electric, does not overheat.
Podded propulsion system
The VDL Klima POD Cooler is an integral part of the podded propulsion system. The podded propulsion system, also known as the POD drive, is a marine propulsion system. The system consists of an electric motor that is placed in a nacelle which drives the ship’s propeller. The electric motor is subsequently cooled by the VDL Klima POD Cooler. The nacelles mounted on a steerable shaft that is placed completely outside the ship’s hull, below the water surface.
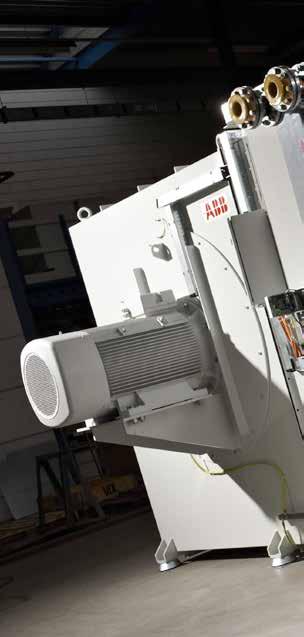
The POD drive is special because of its mobility. The application can rotate completely (360 degrees) and thus generate thrust in all directions, something that is not possible with a conventional system. VDL Klima designs, produces and exports these coolers for a number of major customers. For example, the cruise vessel ‘Oasis of the Seas’, one of the largest cruise vessels in the world, is powered by three Azipods (trademark of ABB) equipped with VDL Klima POD Coolers. Also more and more (ice-going) LNG tankers are being equipped with podded propulsion systems. VDL Klima is specialist in supplying the cooling systems, due to its unique design and many years of experience in this field.
Unique features
Before production actually starts, it is important that the capacity of the cooler is calculated. This involves questions such as ‘What kind of ship is it’, ‘Where is the ship sailing’ and ‘What is the capacity that needs to be cooled’. The dimensions of the cooler are also important, because it has to
fit within the design of the ship. Technical specialists from the sales department, engineering department and the VDL Klima R&D team consult with the customer regarding the criteria the cooler needs to meet. Once everything has been agreed, the final production can begin. The POD Cooler is made entirely in-house. This means that late changes to the design can easily be incorporated into the final product, while retaining the flexibility, agreed price and delivery time. As every POD Cooler is unique, the test phase is very important and this is also done in-house. The lead time for the entire project is around 14 weeks.
How does it work?
Every electric motor generates heat. For an optimal performance of the POD drive, this heat must securely be dissipated. The heated air is extracted from the electromotor by a radial fan and circulates from the nacelle through the casing/shaft of the POD drive. This air is cooled and dehumidified using VDL Klima’s POD Cooler. This is done by means of a KDL (heat exchanger) designed by VDL Klima, especially for the application. With the help of the fan, the heated air is led along a system of tubes and fins. Cold water, originating from the sea, flows through the tube system cooling the heated air that flows through the fins of the heat exchanger. This cooled air will in turn return to the electric motor. This cooling system is a so-called closed system: the cooling air is continuously ‘recycled’ to exclude external influences such as fluctuations in ambient temperature, humidity and pollution.
Related services
VDL Klima currently supplies its products mostly to OEMs or a shipyard that build the ship on behalf of a shipping company. Yet VDL Klima is increasingly involved earlier in the engineering process, also with the shipping companies and the engineering agencies in order to ultimately gain more insight into the customer’s total requirements. As a result, these needs can be anticipated in the design phase of the cooler, what in return will support the customer in the optimum design of his ship.
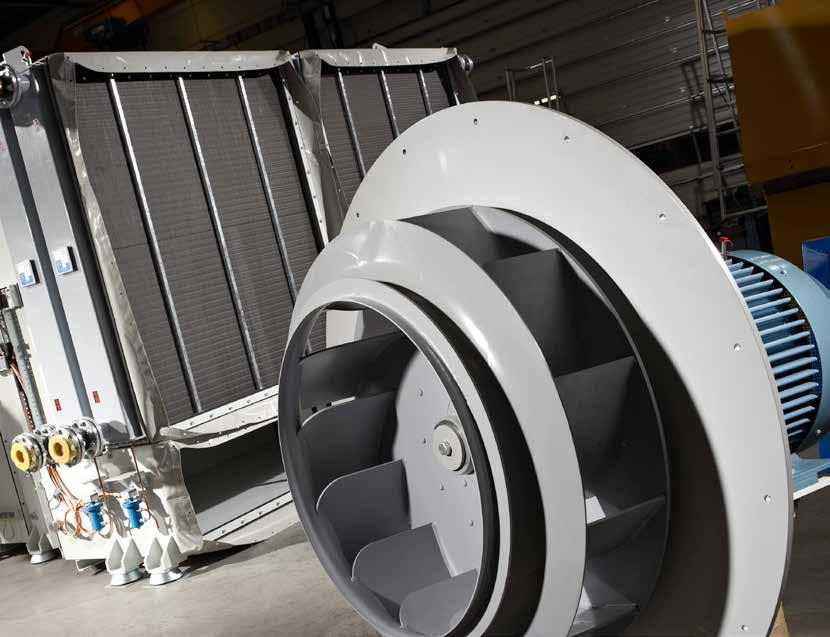
CAPE Holland: redefining the future of (XXL) monopile installation
An incredible amount of development, engineering and manufacturing has taken place in the past years at CAPE Holland and their trusted suppliers to build the next level CAPE Vibro Lifting Tool (CAPE VLT). It is ready for the XXL monopiles the Offshore Wind industry will see in the years to come.
Building on the large track record that has been built up with the CAPE VLT-320 range, which was first deployed in 2015, the CAPE VLT-640 range has been developed over the last 2 years. With the complete unit finished in September 2021, the CAPE VLT-640 has numerous new features in order to operate very large vibro lifting tools and a lot of work has gone into streamlining the design of the hydraulic connections, further reducing the risk of failures during the project. With an enormous power of 640 kgm per unit, the CAPE VLT-640 gearbox is by far the largest single gearbox vibro hammer in the world. Then combining 3 units together to form the CAPE VLT-640 Triple, this monster machine is ready for piles weighing more than 1,000t.
Developments are already underway to increase the maximum line pull per 640 unit to 1,000t, allowing a CAPE CAPE VLT-640 Triple to upend, lift and drive piles to well over 2,000t. It’s bigger brother, the CAPE VLT-640 Quad will then be ready for the largest XXL monopiles weighing up to 3,000t and which are planned for the longer term future for Wind Turbine Generators going towards the 20MW. The control system has also been improved and is now including a highly sophisticated installation monitoring system.
In order to be able to power the large CAPE VLT’s without taking up a lot more deck space, CAPE Holland has further developed the power units that can now also be stacked. As before, the CAPE Power Units are dual prepared which means they can drive both the CAPE VLT and impact hammer
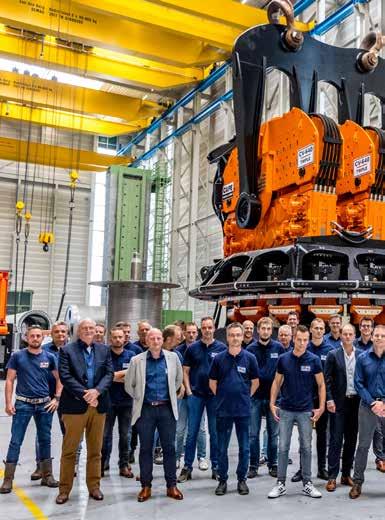
on the same job to save on deck space and rental of double set of power units. The CAPE Holland operators can also operate both the CAPE VLT’s as the impact hammers, so a further saving on personnel helps to keep the costs down. The newly developed Hose Reels can also be stacked and house the smartly bundled hoses in neat umbilical’s for a tidier hose handling.
Vibro technology
With vibro driving, the pile is not forced into the soil by high energy blows, but actually sinks into the soil by gravity due to the temporary reduced soil resistance around the pile caused by the vertical vibrations. This means that the pile deforms less and therefore generates substantial less noise than impact driving. Once the vibro is turned off, the soil is regaining most of its strength immediately. The rest of the setup of the soil will be regained over time. In order to be able to vibrate the pile in a vertical motion, it is paramount that the vibro tool has a fixed connection to the pile. This is normally achieved by hydraulic clamps. This fixed connection brings a number of added advantages to this installation method, like the ability to extract piles, prevent pile run, controlled installation without requiring a gripper system or piling frame.
Noise mitigation
After entering the offshore market with vibro hammers back in 2007, CAPE Holland developed a multiple vibro for the first ever monopile for a wind turbine generator in 2012. Offshore Germany, the monopiles for the Riffgat Offshore Wind Farm were driven to a stable depth, without noise mitigation before they were driven to their final depth with an impact hammer.
The success of driving the 30 monopiles to the desired depth, in about 20 minutes net driving time, on average per pile, convinced the CAPE management that there was a gap in the market for a fast way of driving piles, with very little noise impact.
Combined features
The management realised, however, that the large onshore vibro hammers were not ideal for offshore use and in 2014 they took the plunge and developed a dedicated vibro hammer for the offshore market. It incorporated an upending facility and was designed and built as a lifting tool, certified for lifting offshore. Due to the combination of the lifting tool and vibro driver, the CAPE Vibro Lifting Tool or CAPE VLT in short, was born.

Massive benefits
Having showed its great potential with the CAPE VLT-320 during the pre-piling of jacket piles for a gas platform, CAPE Holland built the first multiple linked CAPE VLT in 2016. This was for the installation of a monopile for the foundation of an unmanned gas platform in the Dutch part of the North Sea. By using the CAPE VLT the pile could be installed, without any form of support frame during driving.
More and more offshore contractors saw the massive benefits of the CAPE VLT, fuelling the demand for a smaller version, which led to the development of the CAPE VLT-80 with a range from 20 to 30 inch with the internal clamp IC-60. This compact unit, which has been flown out to a few projects around the globe already, is mostly used for the installation of pin piles for seabed structures and anchor piles for mooring systems. This has a great potential for anchor piles for floating wind projects.
It has been used successfully in the Caspian Sea to water depths of 170m installing tether piles to final penetration, saving an enormous amount of installation time driving the piles free hanging, as a seabed frame nor tool changes were required, as the full installation from picking up the stored piles, to driving them to final penetration before picking up the next pile happened with the same tool. The whole installation campaign, took less than half the time it would have taken with the traditional installation method.
Most powerful
In April 2020 CAPE Holland was awarded a contract by Seaway 7 to supply a CAPE VLT-640 Triple with a total capacity of 1,920 kgm. This version has multiple vibro hammers linked together, making it the most powerful vibro lifting tool in the world.
In January 2022, the CAPE VLT was successfully load tested to complete the lifting appliance certification process under Lloyd’s Register Code for Lifting Appliances in a Marine Environment (CLAME).
Reaching Net Zero with Green Hydrogen
If you’ve read the news today, you were likely reminded of the dire need for companies to transition to renewable energy. The news is stark - emphasizing the consequences if we stay on the same path of fossil fuels and oils. But the good news is there is hope as key players are choosing to make an investment in green hydrogen, the only form of hydrogen that doesn’t emit carbon.
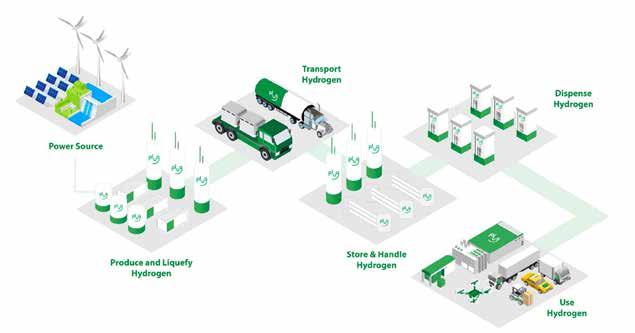
As the first company to believe in the Hydrogen Revolution, Plug has been powering both large and small companies around the world for 25 years. With a commitment to developing effective, economical, and reliable products, Plug has built an end-to-end green hydrogen ecosystem that covers all the steps of operations, including producing, storing, dispensing, and delivering green hydrogen to customers. When it comes to helping the world reach net-zero, Plug takes the responsibility personally, and it is attacking the problem at all angles.
End-to-end
“At Plug, we dream big, and we plan to be a big winner, as our customers in the world turn to green hydrogen to reduce 20% of the world’s global carbon footprint,” Andy Marsh, CEO of Plug, said. “Plug is a company that can provide products and services for the entire green hydrogen ecosystem. This is unique. We can generate hydrogen, like at our plant in Tennessee. We can distribute hydrogen, using our own liquid and gaseous hydrogen trailers. We can operate fueling stations, like at Walmart and Amazon, and can serve a multitude of fuel cell applications in this growing hydrogen space.”
Experts agree green hydrogen is the key to safely powering at least
20% of our world.
With its customers in mind, Plug built an end-to-end ecosystem with more than 100 solutions, 50,000 fuel cell systems, and more than 165 fueling stations for a range of customer applications. Plug’s customers can expect the green hydrogen production plants to produce at least 70 tons of liquid green hydrogen daily by the end of 2022 and 500 tons daily by 2025. However, this is just the beginning of the transition to green hydrogen.
Delivering electrolyzers
With nearly five decades of experience, Plug has developed electrolyzers that have very high current densities, high-pressure output, and seamless load following capabilities. Plug’s electrolyzers will be supplied to customers in Canada, Germany, France, Australia, Brazil, and India, among others. These electrolyzers will support a range of applications, including natural gas pipeline injection, excess renewable energy storage, FCEV fueling, green ammonia and e-methanol production, and decarbonization of refinery operations.

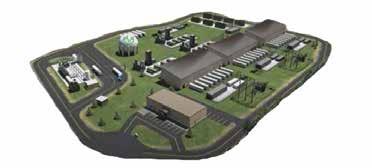
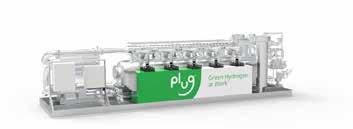
100 MW electrolyzer
Fertiglobe, the strategic partnership between OCI N.V. and Abu Dhabi National Oil Company - recently selected Plug to provide 100 megawatts of electrolyzer to produce green hydrogen as a feedstock for up to 90,000 tons of green ammonia production at EBIC in Ain Sokhna, Egypt. Green ammonia, produced from renewable energy such as solar and wind instead of natural gas, is a versatile product that is an ideal carrier fuel to store and transport hydrogen, and can help decarbonize numerous sectors which represent around 80% of current global greenhouse gas emissions.
1MW Offshore Electrolyzer
Plug’s hydrogen electrolyzer technology will provide 1MW of capacity to the world’s first offshore hydrogen production facility developed by Lhyfe and powered by electricity from a floating wind turbine off the coast of Le Croisic, at SEM-REV, Centrale Nantes’ offshore test site, which will be operational by 2022. Plug and Lhyfe will also pursue other opportunities to develop green hydrogen in Europe.
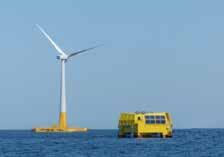
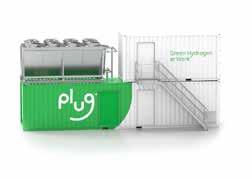
Dutch offshore access specialist Safeway B.V. and Kristiansand-based sister company Techano AS have signed a corporation agreement with Intellilift AS from Norway to equip the ‘SOVs for the future’. Under the agreement, Intellilift will act as preferred supplier of their proprietary technology in the field of power systems, automation and remote control systems.
All-electric gangway to equip ‘SOV for the future’
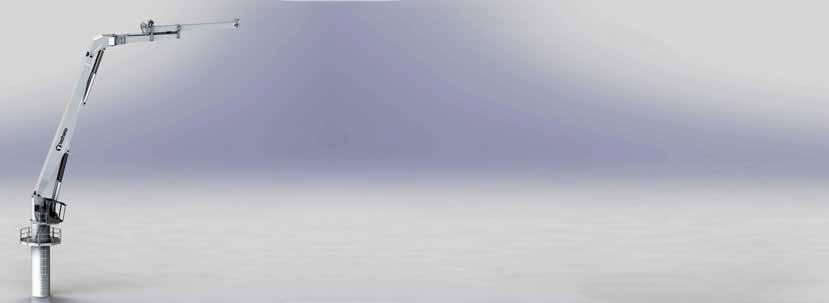
The package system includes an all-electric version of Safeway’s original Gannet 3D motion compensated gangway, elevator and 3D crane. The package may be extended with other products such as davits and winches.
Key features of the autonomous gangway are:
•All electric, incl. hybrid-battery • Remote operation • Bridge control system • Auto docking, hover mode
The collaboration will accelerate the development and supply of a fully electrical and automated system, supporting the industrial green shift.
Presently, the Gannet is Safeway’s most advanced type of access system for SOVs, allowing personnel to move safely between the offshore service vessel and offshore wind turbines. Made with trolley operations in mind, the Safeway Gannet has a stepless transfer and 1.2m transit width.
Designed for installation on newbuild SOV’s, the Gannet gangway combines unique features, such as hover mode, roll compensation and highest workability in the market, with strongly reduced actuator motions.
The shift to full electrification, referred to as IntelliSafe, does not only represent a climate-smart technology, it also reduces the overall environmental impact during the construction phase of an offshore wind farm.
The full electrical and automated solutions offer advantages over hydraulic solutions in terms of power consumption, controllability, and remote operation.
Wijnand van Aalst, CEO of Van Aalst Group, to which Safeway and Techano belong, says: “By combining the outstanding performance of our Gannet gangway as well as the advanced load handling and state-of-the-art lifting equipment of Techano with the smart and innovative electrical drive and controls supplied by Intellilift, the new fully electrical Gannet gangway will be ready for all future SOV requirements. We are committed to driving our industry forward, to a more sustainable future and we are confident that cooperating with a reputed company, such as Intellilift, represents a significant step up. Servicing wind farms will become safer and easier than ever before.”
Dutch Pavilion OTC 2022
2 - 5 May 2022
Huisman
Bakker Sliedrecht
Safeway Strohm
De Graaf EMCE
Navingo Hycom
Breman Machinery
JB Systems DEME Offshore LUC Group
Marin
3127 3227
Ampelmann Bayards Interdam
C-Job
Bolidt
Cape Holland
SDC Varifier Smulders Red Box ELA
IRO Energy Booth 2331 Transition Lounge
3327 Damen
Van Oord
Hatenboer Seatools
3433
Allseas
3115
Company Booth Number
Allseas Group 3115
Ampelmann 3327
Bakker Sliedrecht 3227
Bayards Bolidt 3327 3327
Breman Machinery C-Job Naval Architects CAPE Holland 3127 3327 3327
Damen Shipyards
3433 De Graaf Aandrijvingen 3227 De Haan Special Equipment 3315 DEME Offshore 3227 ELA Container Offshore 3327 EMCE Winches 3227
Lankhorst
De Haan MCS
Mammoet
3315
Company Booth Number
Hatenboer-Water 3315
Huisman Equipment HYCOM 3127 3127
InterDam 3433
JB Systems Lankhorst LUC Group Mammoet
3127 3315 3227 3315 MARIN 3227 Maritime Construction Services 3315 Navingo 3127 Red Box Energy Services 3327 Royal IHC 3415 Safeway 3227
Royal IHC
3415
Company Booth Number
SDC Verifier 3327
Seatools 3315
Smulders Group Strohm Van Oord 3327 3227 3433
Participants in IRO Energy Transition Lounge
Delmar - Vryhof GustoMSC Paradigm Group Plug Power Van Heck VDL Klima 3433 3433 3433 3433 3433 3433
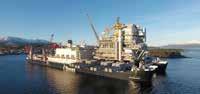
Allseas Group S.A.
Route de Pra de Plan 18 1618 Châtel-Saint-Denis Switzerland phone +41 21 948 3500 mail sales@allseas.com
Ampelmann Operations
Rotterdamseweg 38 2629 HG Delft The Netherlands phone +31 (0)20 2400 121 mail info@ampelmann.nl
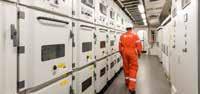
Bakker Sliedrecht
Leeghwaterstraat 55 3364 AE Sliedrecht The Netherlands phone +31 (0)184 436 666 mail info@bakker-sl.nl
Bayards USA LLC
17171 Park Row, Suite 298 TX 77084 Houston USA phone +1 281 717 40510 mail sales@bayardsusa.com Allseas is a leading contractor in the offshore energy market with dynamism, rapid progress and pioneering spirit at its core. Since 1985, we have been at the forefront of offshore innovation, transforming bold ideas into state-of-the-art solutions to meet the market’s ever changing needs.
Our expertise lies in pipelay, transportation, installation and decommissioning of offshore facilities and deep-sea polymetallic nodule collection. Designed and optimised in-house, our record-breaking vessels exceed the limit of what is possible above and below the water surface. Our mission is to remain a frontrunner in current and future offshore energy markets by continuously pushing technical boundaries. As new markets emerge, so do opportunities to apply our engineering expertise to develop new technology that will play a key role in the energy transition. We excel in the design and implementation of large and complex offshore energy infrastructure projects, with a proud history of delivering first-class services, operational excellence and dedicated expertise to clients worldwide. Allseas pioneers the development of groundbreaking offshore technology, driven by creative thinkers who dare to try new things.
www.ampelmann.nl
Ampelmann is an offshore access provider delivering innovative, safe and reliable Walk to Work systems and services to the offshore energy industries globally. With a track record of more than 7 million safe people transfers, over 18.6 million kg cargo transfers and 400 projects worldwide, the company operates in Europe, Africa, Asia Pacific, the Americas and the Middle East. Ampelmann maintains a fleet of 60 operational gangway systems used for transferring crews and cargo to offshore structures. It works with a full-service rental business model, provides clients with trained operators and with data insights into their offshore operations. Ampelmann’s services are tailored to the needs of different market segments, sea states, cargo and crew loads, and are used by key players in the global industry. Stand 3327
www.bakkersliedrecht.com
For more than 100 years, Bakker Sliedrecht has been a leading system integrator in the maritime industry. Our innovative sustainable solutions in alternative energy carriers and fuels, digital monitoring and remote maintenance prepare the current fleet of our customers for the future. Our customers are active in the demanding contexts of dredging, offshore and maritime operations, and the land-based energy transition.
Bakker Sliedrecht specializes in end-to-end system integration. We offer tailored and innovative solutions for power generation, distribution, and consumption and bespoke automation systems when standard products or packages are insufficient to meet the customer’s specific requirements. We provide a flexible process that aligns with the customer’s specific needs and focuses on adding real value. Either by deeply technical dialogues about new concepts to push mission-critical possibilities or on-the-job installation supervision in challenging circumstances.
We take care of it! Stand 3227
www.bayards.com
Our focus on the Offshore Industry can be characterized as a full-service contractor on a turnkey contract basis. We design, engineer, manufacture and install aluminum structures ranging from helicopter landings and parking areas complete with firefighting equipment, support structures, lighting, cage ladders, heat tracing and safety netting to stair towers, living quarters, hand railing, wind and heat shields, safety gates, flex-barriers, swing load protection barriers, antenna towers, telescopic gangways and helicopter hangars. We comply with all international standards such as ISO and OHSAS and product regulations such as CAP437, NORSOK, NORMAM, AVV, ICAO and USCG to ensure premium quality. Stand 3327
Bolidt Synthetic Products & Systems
P.O. Box 131 3340 AC H.I. Ambacht The Netherlands phone +31 (0)78 684 5444 mail info@bolidt.com
Breman Machinery
P.O.Box 135 8280 AC Genemuiden The Netherlands phone +31 (0)88 27 36 200 mail info@breman-machinery.nl
C-Job Naval Architects
Regulusplein 1 2132 JN Hoofddorp The Netherlands phone +31 (0)88 0243 700 mail info@c-job.com
CAPE Holland
Romhof 5 9411 SB Beilen The Netherlands phone +31 (0)593 540 470 mail info@capeholland.com Bolidt is the specialist in lightweight, flexible levelling solutions and deck covering systems for the offshore industry with high focus on a consistent high level of quality and latest HSE standards including requisite certification.
By means of innovative systems, materials and solutions for Offshore Service Vessels, Living Quarters and Offshore platforms Bolidt accommodates the demand of architects, engineers, shipyards, crew and owners for deck covering solutions that perfectly combine expected safety, sustainability and hardwearing characteristics. With a 55-year proven track record in R&D, production, application and refitting of deck covering systems Bolidt knows best how to make the future available today. Bolidt aims at development, production and application followed by worldwide distribution. The versatile range of flooring systems meets all sorts of requirements. From seamless, anti-skid, temperature resistant, hygienic floor finishes to lightweight, fire-insulating, water impermeable and shock-absorbing deck covering systems.
www.breman-machinery.nl
Breman Machinery B.V. has the experience to make your wishes become reality. Our team of 130 wellexperienced employees has the knowledge to create workpieces of extreme sizes with maximum precision. We have a good record of projects for Oil and Gas companies, Mechanical Engineers, Aerospace companies and Industrial firms. We do not turn down any challenge.
The welders of high-quality steel, like S460-S690, Duplex etc., are qualified by Lloyd’s Register or DNV for all welding positions. With 30 milling, boring and turning machines we have the possibility to offer unique services. Our largest boring machine has a range of X=26.500, Y=10.000 and Z=2.500 and the largest turning machine can handle a length of 16.000 mm. Our preservation department can protect your projects with different painting systems. The workshops in Genemuiden have a surface of 21.000 meters with a height of 25 meters. The crane capacity is up to 320T. Our location is beside open water, which means we have a direct connection to the international ports.
High quality is one of our most important standards. We work according ISO9001, ISO3834-2, EN1090-1 and VCA**. Stand 3127
www.c-job.com
As a dedicated naval architect, C-Job is driving change. We are passionate about making it happen: a sustainable maritime industry in one generation.
Architectural innovation is our job. We help our clients to build better ships, become 100% sustainable, and run better because of it.
Our portfolio of services, designs, and programs guarantees better opex and capex for new vessels, as well as existing ones. Stand 3327
www.capeholland.com
Driven by piles We are passionate about piling; we continuously improve the performance of pile installation and removal: faster, easier, smoother and more sustainable. We love to make impact and contribute to good vibrations. Our customers’ offshore oil, gas and wind projects are of the greatest significance. These mighty constructions require solid foundation, and we are there to support them with the smartest piling equipment and all our knowledge, skill and craftmanship. At CAPE Holland we proudly build on six generations of piling experience. We get the job done! Piling outside the box Above all, we are solution providers. We think in possibilities. Whether we need to be creative in sourcing the proper equipment for you, or the situation requires an ‘out-of-the-box’ approach. We are the pioneers in offshore vibro driving. Our work includes research, design, and engineering. We try and test. Both behind a desk, and with our feet on deck. Resourceful as we are, we’ve invented better tools by learning from onshore piling, combining functionality, reducing frills and adopting to the most demanding circumstances. Challenge us, like we challenge ourselves! Stand 3327
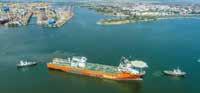
Damen Shipyards
Avelingen – West 20 4202 MS Gorinchem The Netherlands phone +31 (0)183 639 911 mail info@damen.com Family owned Damen Shipyards Group has been in operation for over ninety years and offers maritime solutions worldwide, through design, shipbuilding, ship repair and related services. Damen operates 35 shipyards and 20 other companies in 20 countries, supported by a worldwide sales and service network. We offer direct employment to more than 12,500 people, bringing together a total production value of 2 billion euros and delivering over 140 ships in 2021.
In addition to fellowship, craftsmanship and entrepreneurship, stewardship is a starting point for Damen. We want to be the most sustainable shipbuilder in the world. Digitalisation and standardisation of platforms are important preconditions for this. Our main activities are the design and serial construction of inventive ships by integrating diverse components and subsystems into high-quality platforms. These activities are supported by a worldwide sales and service network. Damen Shipyards Group focuses on niche maritime markets. On workboats for towage, dredging, offshore, fishing, aquaculture and other markets. On high speed craft and maritime public transport. On ships for defence & security and on exclusive yachts. Apart from that we are also active in the repair and conversion of existing ships and the sale and production of components for the maritime industry.
De Haan Special Equipment
Transistorweg 3 9503 GT Stadskanaal The Netherlands phone +31 (0)599 613 300 mail sales@dehaan-se.com

Delmar – Vryhof
Karel Doormanweg 7 3115 JD Schiedam The Netherlands phone +31 (0)10 266 8900 mail info@delmarvryhof.com www.dehaan-se.com
De Haan SE is a prominent global player in the field of lifting blocks and wire rope & chain end terminations. Both standard products and customised products are manufactured entirely by our own hands. This means our customer has one central point of contact and can count on De Haan to provide fast and workable advice based on a superior level of expertise. De Haan SE contributes to the continuity of the working processes of offshore and onshore industries through our knowledge, products and services, which also guarantee the continuous high quality of our products. De Haan SE is familiar with working processes where safety and integrity of the end product are vital. De Haan aims to assist its customers in a manner that is flexible and focused on service.
www.delmarvryhof.com
Delmar Systems and Vryhof are the trusted partners to most offshore energy industry’s leaders, delivering innovative and customer-focused anchoring and mooring solutions.
We are committed to the highest standards of safety, integrity, and respect to the environment. We are proud of our legacy and impeccable track record over our combined 100 years, always delivering value in everything we do.

DEME Offshore NL
Minervum 7442 4817 ZG Breda The Netherlands phone +31 (0)76 520 4140 mail info@deme-group.com www.deme-group.com
DEME Offshore is the leading global solutions provider in the offshore energy industry with a successful track record spanning more than three decades. Our activities started with landfall construction and rock placement. We took our first steps into the renewables sector more than 20 years ago, when 1.5 MW turbines were considered impressive. Today, we are the number one offshore wind contractor in the world, capable of installing the latest generation XL foundations and 15 MW+ wind turbines, as well as offshore substations, inter-array and HVDC export cables. We also have vast expertise in heavy lift, umbilicals, interconnectors, geoscience and decommissioning services. DEME Offshore is part of the DEME Group, a global leader in marine engineering, dredging, infra and environmental works. Benefiting from close synergies between our core activity lines, DEME Group provides a broad range of advanced technology, equipment and vessels, managed by expert teams. Stand 3315
Stand 3433
Stand 3227
ELA Container Offshore
Zeppelinstraße 19 - 21 49733 Haren (Ems) Germany phone +49 5932 7323500 mail info@ela-offshore.com
EMCE Winches
‘s-Gravendamseweg 53 2215 TC Voorhout The Netherlands phone +31 (0)252 214 989 mail sales@EMCE.com
GustoMSC | NOV
Karel Doormanweg 35 3115 JD Schiedam The Netherlands phone +31 (0)10 2883 000 mail info.gustomsc@nov.com
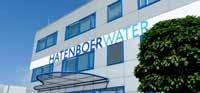
Hatenboer-Water Americas
11424 Spring Cypress Rd., Ste E2 Tomball, TX 77377 USA phone +183 2380 8733 mail info.americas@hatenboer-water.com ELA Container Offshore, established in 2014, provides offshore containers for rent and sale to be used on rigs, transformer platforms and on all kind of seagoing vessels, pontoons and barges.
ELA provides the modules as Temporary Living Quarters, Offices, Mess Rooms, Galleys, Laundry, Recreation or Locker Rooms for your individual demand. Additionally, ELA also offers a wide range of offshore cargo carrying units. Depending on their area of use and purpose, the high-quality containers are certified according to ISO 10855 / EN 12079-1 / DNV2.7-1, DNV 2.7-2, DNV 2.7-3 and/or CSC. ELA’s portable units are completely reusable over multiple decades. Since the products can be refurbished and reused, the product lifecycle is fully sustainable and the negative impact on the environment is minimized.
Depending on customer requirements, ELA Offshore Containers are individually customized, immediately operational and are available on short notice.
www.EMCE.com
EMCÉ Winches designs and manufactures electric-, hydraulic and air operated winches, capstans, hose reels, hoists & BOP systems for the marine, offshore & renewable markets.
In close cooperation with our global dealer network and EMCÉ branch offices in Bahrain & Belgium our mission is to excel in product safety, quality, durability and performance. With our experienced team we tackle every lifting and pulling challenge up to 250 T and ‘tailor’ our modular designs very efficiently to customer specifications.
Fast, cost effective, ISO certified, to any standard and with a strong focus on total cost of ownership, fully summarized in our motto: Every winch a winner!
www.nov.com/gustomsc
Pioneers of Offshore Engineering GustoMSC is recognized for providing advanced design & engineering consultancy for mobile offshore units and equipment supply. In close cooperation with our clients, we translate experience, science, and technical knowledge into realistic & innovative ideas. The performance of new and existing jack-ups, vessels and semi-submersibles is further optimized by our operational support and engineering consultancy. In this way, GustoMSC enables and supports safe and efficient operations at sea, contributing to a sustainable future. ESG, a natural course for offshore pioneers Projects at sea in offshore oil & gas and offshore wind are our most important markets. GustoMSC has been addressing the essential changes in the offshore energy market since years. Technological challenges and pushing boundaries are part of GustoMSC’s DNA. We believe we can help our clients move forward as the global energy transition accelerates. Energy efficiency and sustainability are an essential consideration in all GustoMSC design and equipment solution processes. This is a natural course for us as offshore pioneers.
www.hatenboer-water.com
With many years of experience and our innovative know-how, we are versatile partners in the field of water technology. Providing you with standard or made-to-measure solutions for different applications.
From the supply of simple, products such as a pump or filter, carrying out risk analyses or sampling through to the supply of completely integrated custommade systems. Fully commissioned, if required. Stand 3227
Stand 3433
Stand 3315
Huisman
Admiraal Trompstraat 2 3115 HH Schiedam The Netherlands phone +31 (0)880 702 222 mail info@huisman-nl.com
HYCOM
Antillen 43 7333 PE Apeldoorn The Netherlands phone +31 (0)880 597 200 mail info@hycom.nl
InterDam
Klompenmakerstraat 12 2984 BB Ridderkerk The Netherlands phone +31 (0)180 470 030 mail info@interdam.com
IRO
Boompjes 40 3011 XB Rotterdam The Netherlands phone +31 (0)79 3411981 mail info@iro.nl We are Huisman. We design, manufacture and service heavy construction equipment for the world’s leading companies in the renewable energy, oil and gas, civil, naval and entertainment markets. Our products range from Cranes, Pipelay Equipment, Drilling Equipment and Winches, to Vessel Designs and Specials. The history of Huisman is one of setting new industry standards. Of making impact, since 1929. With step changing technical solutions that vary from stand-alone components to highly engineered integrated systems. From concept to installation and lifetime support.
In these times of transition, our passionate workforce and worldwide production, service & sales facilities make us equipped for impact.
www.hycom.nl
HYCOM, located in The Netherlands and part of the international HYDAC group, specializes in engineering, assembling and installing electric and hydraulic drive and control systems. HYCOM is active internationally in a wide range of areas amongst others offshore, offshore wind and dredging. The company has distinguished itself as a player completely at ease with the demand for bespoke branches where technical challenges are often extremely high. Frequently HYCOM is involved in in-depth discussion with its clients already in the pre-design phase where its professionals prove their ingenuity time and again. For innovative solutions we focus not only on initial costs but life cycle costs and ease of operation as well. Thanks to the HYDAC international network we can provide fast service around the globe.
We as HYCOM are flexible, we focus on results and we will support you to stay one step ahead of your competitor. Stand 3127
www.interdam.com
InterDam is a manufacturer and supplier of fire and blast resistant architectural items, to create the safest area possible for professionals working in high risk environments, applying straightforward and fully certified products and methods.
Products available from InterDam currently include the following standard and heavy duty items fabricated from galvanized or stainless steel: -Blast- and fire resistant doors -Fire resistant walls, welded and bolted types -Blast resistant walls, welded and bolted types -Cladding systems, weather tight and/or blast relief -Spare parts for offshore and onshore fire and blast doors. The company is certified to ISO9001 with all her products extensively tested and approved by DNV, Lloyd’s, ABS and USCG for blast and specific heavy fire ratings A0, A60, H60, H120 and jet fire ratings. All products have relevant type approval certificates from certifying authorities referenced above.
InterDam’s products are custom designed to suit different environments such as Oil and Gas platforms and FPSOs, wind energy transformer installations, refineries, petrochemical plants and laboratories. From a standard fire door up to the most complex specific architectural projects. Stand 3433
www.iro.nl
The Offshore Energy supply industry in the Netherlands belongs to the Top 5 of the world. Established half a century ago, the association IRO is an independent non-profit organisation that supports and promotes the interests of its 400 member companies.
Acting as the gateway to Dutch suppliers in the energy industry, the IRO mission is ultimately aimed at maintaining and strengthening the position of the offshore energy supply industry by creating a level playing field for its members. A sharp focus on cost efficiency, innovation and sustainability amongst the IRO members are instrumental to achieve this goal. The IRO members consist of a wide variety of both multinationals and SMEs. They represent the entire supply chain within the Offshore Energy Industry, with activities covering: Engineering & Consultancy, Construction & Fabrication, Plant & Equipment Supply, Contracting & Installation, Exploration & Production and Personnel & HSE. The range of services that IRO provides to its members varies from maintaining government & NGO relations and facilitating networking opportunities within the IRO community, to participating in international trade missions as well as in exhibitions and providing Business Intelligence and training courses.
Stand 3433
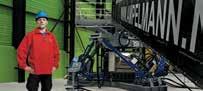
JB Systems
Westlandseweg 190 3131 HX Vlaardingen The Netherlands phone +31 (0)10 460 8060 mail kme@jbsystems.nl
Lankhorst Offshore
Prinsengracht 2 8607 AD Sneek The Netherlands phone +31 (0)515 487654 mail info@lankhorstoffshore.com
LUC Group
Boschstraat 31 6442 PB Brunssum The Netherlands phone +31 (0)45 5270 300 mail sales@lucgroup.com JB Systems supplies industrial automation solutions around the world to clients in machine building, offshore and process industries. With more than twenty years of experience and a permanent core of 70 experienced engineers, our partners profit from an enormous amount of knowledge and experience. Within the offshore industry we are the specialists for the electrical controls of offshore equipment.
www.lankhorstoffshore.com
Lankhorst Offshore is a world leader and innovator in the manufacture of high performance, synthetic fiber ropes for deepwater moorings, single point moorings, floating offshore wind energy moorings as well as heavy lift slings, synthetic tethers and deepwater deployment systems. Our range of Bio Based Dyneema® SK78 fiber rope lifting slings are as strong as steel wire but significantly lighter, easier to handle, and a safer and more efficient way of handling many offshore lifting projects. At Lankhorst Engineered Products we design and manufacture a wide range of pipeline products such as: • The TriVIV and TriVIV2.0 strakes for VIV protection, as well as various types of VIV fairings • UraGUARD, QuickGUARD and SpaceGUARD for crossing and abrasion protection • RiserTec fins and shims for drilling riser protection • Specials like shrouds and piggy-back blocks
We put special focus on sustainability and circular usage of materials with our EcoStrake and EcoGUARD, which are manufactured of 100% recycled plastics.
www.lucgroup.com
Supplying parts for the offshore installation of pipelines since the 1980’s, LUC can be considered as one of the pioneers in developing special PU grades for rollers and tensioner pads used in all kind of pipe handling and laying equipment. Nowadays the activities of LUC for the offshore energy sector cover much more than just pipe laying for the oil & gas industry. Newer areas where LUC’s PU grades are s uccessfully used are in umbilical and cable manufacture and the installation of offshore wind turbines.
There are many applications for polyurethane and rubber parts in the energy industry, for oil & gas as well as wind, both offshore and onshore. The main areas for the products of LUC are: • Handling and laying equipment for rigid pipe, flexibles and cable. Including rollers for stingers, pipe conveyors and spooling equipment and friction pads and spring blocks for tensioners and clamping devices. • Pipe coating equipment • Umbilical and flexible manufacturing sites • Pipe inspection and maintenance • Monopile grippers • Monopile fabrication (welding manipulators) and transport (seafastening) • Offshore access / gangways

Mammoet
Van Deventerlaan 30-40 3528 AE Utrecht The Netherlands phone +31 (010 204 2424 mail sales@mammoet.com www.mammoet.com
Mammoet is the world’s largest heavy lifting and transport company. It is playing a key role in many oil & gas and offshore wind projects, using the biggest global fleet of equipment, multiple engineering nerve centers across the globe and commitment to innovation to drive both markets forward.
It has engineered some of the largest movements in offshore energy. These include lifting the world-record 42,780t Exxon Neftegaz Arkutun Dagi topside, raising the Shell Malikai topside over 40m high and loading-in both decommissioned Brent Alpha and Bravo structures. In offshore wind, it is involved in many major projects all over the world, in a wide range of scopes. It has transported and loaded-out massive foundations for many pilot and now commercial floating wind farms. On land, its PTC and SK cranes – the world’s biggest – are now helping to integrate and load-out giant jacket foundations.
Its upcoming SK6000 crane will allow both FPSO and wind installations to be built more efficiently than ever before, enabling both markets to enjoy significant cost-efficiency benefits. Stand 3315
Stand 3227
Stand 3315

Maritime Research Institute Netherlands (MARIN)
The Netherlands phone +31 (0) 317 493 911 mail MARIN | offshore@marin.nl mail MARIN USA | usa@marin.nl
Maritime Construction Services
Parnassusweg 805(B) 1082 LZ Amsterdam The Netherlands phone +31 (0)20 505 1000 mail e.dehaas@mcs.nl
Navingo
Jan van Galenstraat 56 3115 JG Schiedam The Netherlands phone +31 (0)10 209 2600 mail info@navingo.com
Paradigm Group
Rotterdam The Netherlands phone +31 (0)184 609 419 mail info@paradigm.eu MARIN is a globally recognised top institute for hydrodynamic and nautical research. Our mission is ‘Better Ships, Blue Oceans’: we stand for clean, smart and safe shipping and sustainable use of the sea.
We do this as an independent knowledge partner for the maritime sector, government and society. We offer integrated solutions, from concept development and design to operation, making optimal use of our test facilities, computer simulations, simulators and full-scale measurements. In developing, applying and sharing our knowledge, we stimulate innovation and global collaboration.
The knowledge and involvement of our people are our strength. MARIN is based in the Netherlands.
To provide our USA clients with advice in an easy and fast way, we have offices in Houston, Phone +1 832 533 8036 (including a simulator facility) and Chesapeake.
www.mcs.nl
Maritime Construction Services (MCS) is an emerging, independent offshore contracting and vessel management company. MCS provides high quality project management and engineering services to the oil & gas majors and main contractors worldwide. The services of MCS range from pipelay, heavy lift and SURF to SAT diving. In addition, MCS services its clients in the construction of ports & terminals and vessel management.
MCS has been established in 2015 as an independent Dutch entity to execute international projects and deliver project management, tendering, business development and commercial support. The exclusive partnership with various stakeholders assures direct access to owned assets and unique experience in reference to turnkey construction of oil and gas subsea facilities, pipelay and port and terminal constructions. In addition, MCS has access to local offices worldwide, to service its clients on site.
For the delivery of projects, MCS has an extensive fleet of (construction) vessels. This includes dredgers, tugs, pipelay/derrick barges, but also DSV’s. A unique asset to the fleet is the DP3 Multi-Purpose Vessel EVEREST. Stand 3315
www.navingo.com
Offshore Energy Exhibition & Conference 2022
brings together buyers and suppliers for two days in RAI Amsterdam. Think of buyers from the marine and offshore energy industry at this year’s events, including ship owners, commercial shipyards, offshore wind operators, energy companies and many more. Offshore Energy Exhibition & Conference 2022 is an ideal place to showcase sustainable solutions to a diverse audience. The mix of decision makers from different sectors that are present on Offshore Energy Exhibition & Conference 2022 will bring business opportunities for your company. Offshore-Energy.biz connects communities to tell the story of the energy transition and sustainable solutions in the maritime and offshore world. Expect daily news from markets of interest, in-depth articles and videos, insights from industry leaders, an overview of the important players in the business landscape and job boards. With 336.000 monthly users and 75.000 newsletter subscribers OE.biz reaches the entire offshore energy industry. Use our reach to get the attention your company deserves. Stand 3127
www.paradigm.eu
Paradigm Group was established in The Netherlands in 2009, to develop and commercialize new technologies and innovations for the upstream Oil & Gas Industry, which now covers four specialisms; Drilling Optimization, Production Efficiency, Well Intervention and Fire Protection.
With a broad range of products and solutions across the market, Paradigm delivers technologies that offer game changing operational value alongside lower carbon intensity. Each specialism boasts unique technologies supported by strong intellectual property, and collaboration with oil and gas operators to drive down the overall cost of operations.
Drilling Optimization | Production Efficiency | Well Intervention | Fire Protection. Stand 3433
Be Amazed | Visit Paradigm | Stand 3433
Plug Power
Eikenlaan 237 2404 BP Alphen aan de Rijn The Netherlands phone +31 (0)172 46 16 00 mail www.plugpower.com/contact-us/ Plug is building an end-to-end green hydrogen ecosystem, from production, storage and delivery to energy generation, to help its customers meet their business goals and decarbonize the economy.
In creating the first commercially viable market for hydrogen fuel cell technology, the company has deployed more than 50,000 fuel cell systems and over 165 fueling stations, more than anyone else in the world, and is the largest buyer of liquid hydrogen. With plans to build and operate a green hydrogen highway across North America and Europe, Plug is building a state-of-the-art Gigafactory to produce electrolyzers and fuel cells and multiple green hydrogen production plants that will yield 500 tons of liquid green hydrogen daily by 2025.
Plug will deliver its green hydrogen solutions directly to its customers and through joint venture partners into multiple environments, including material handling, e-mobility, power generation, and industrial applications.
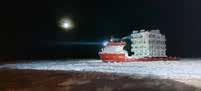
RBES
Hofplein 20, 14th floor 3032 AC Rotterdam The Netherlands phone +31 65208 7411 mail judith.lalau@redboxgroup.com
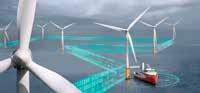
Royal IHC
P.O. Box 3 2960 AA Kinderdijk The Netherlands phone +31 (0)88 015 2535 mail info@royalihc.com www.redboxgroup.com
RED BOX ENERGY SERVICES (RBES) is a leading provider of module transportation services for a wide range of energy infrastructure projects.
The Polar Class (PC3) Heavy Transport Sister Ships, AUDAX and PUGNAX are the only vessels in the world today that can not only navigate unescorted, year-round above the Arctic Circle; they have been designed and constructed to safely transport module cargoes weighing as much as 20,000 tonnes anywhere in the world today and have transited the Suez and Panama Canals as well as the Northern Sea Route. The Vessels have an ice-free deck area capable of receiving both side and stern loadout and discharge of modules as long as 174 meters with a beam of 45 meters.
The AUDAX and PUGNAX have firmly established their credentials as safe and reliable vessels able to serve the needs of our clients in the most challenging marine environments, capable of transporting some of the most valuable cargoes for the world’s largest energy infrastructure projects.
www.royalihc.com
Anchored in a rich Dutch maritime history, Royal IHC is a leading supplier of maritime technology and expert craftsmanship.
With the right people and skills on board, and driven by innovation, we provide a competitive edge to our worldwide customers in the dredging, offshore, mining and defence industries. However, Royal IHC is much more than vessels, equipment and services. We deliver reliable, integrated solutions that improve operational efficiency and allow for a more sustainable performance. All over the world, our people are deeply committed to technological innovation, supported by our long-standing experience in our core markets. Our experts work in close collaboration with multiple stakeholders to meet the specific needs of each customer.
As we navigate new waters in an ever-changing world, our aim remains unchanged: to discover the smartest and safest way forward for both our customers and our people. Together, we create the maritime future.
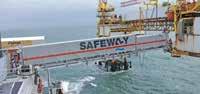
Safeway
Baanhoekweg 16 3313 LA Dordrecht The Netherlands phone +31 (0)78 622 1304 mail info@vanaalstgroup.com www.safewaygangway.com
Safeway is part of global operating Van Aalst Group B.V. and defines the next generation in offshore access solutions.
Highly innovative, based on proven technology and extensively tested, this motion compensated gangway system allows year round access to a broad range of offshore installations. Safeway offers efficient and reliable solutions for the renewable, oil, gas and offshore wind industry. Stand 3327
Stand 3415
Stand 3227
SDC Verifier
Zijlvest 25 2011VB Haarlem The Netherlands phone +31 (0)153 010 310 mail support@sdcverifier.com
Seatools
Edisonstraat 67 3281 NC Numansdorp The Netherlands phone +31 (0)186 680 00 mail sales@seatools.com SDC Verifier is an engineering company on a mechanical and structural design that provides engineering consultancy services and tailor-made code checking software. Since 1998, we have built the trust of top global companies in Offshore and Wind Energy industries, like Allseas, SBM Offshore, Technip FMC, Perenco, Chantiers de l’Atlantique, Boskalis, Bluewater. The SDC Verifier software is a powerful standard checking tool that works within ANSYS, Femap, Simcenter 3D. It automatically verifies your FEA results according to multiple industry standards as DIN, EN, Eurocode, FEM, AISC, Norsok, ISO, DNV, ABS, FKM Fatigue, DVS code, and others. With SDC Verifier, engineers can analyze load combinations according to the Standards listed above. The software automatically detects and recognizes structural members in finite elements models. Optimization tool allows taking the best design decision based on code checking results. Automatic reporting for Ansys, Femap, and Simcenter 3D saves time on repetitive documentation and reduces the deadline pressure.
Contact SDC Verifier when in need of consultancy on FEA, design review according to standards or user-friendly code-checking software.
www.seatools.com
Seatools is a subsea technology company that provides technology solutions for a wide range of subsea challenges. The majority of the solutions we provide are custom-made.
Our scope includes: • Subsea vehicles and other mission critical equipment: ROVs, trenchers, cleaning vehicles, excavators, saws • Subsea production equipment • Subsea, offshore, and dredging monitoring and control systems • Subsea and offshore installation tools • Subsea hydraulic and electronic components • Subsea sensors
We serve any subsea-related market: this ranges from aquaculture through to offshore oil and gas.
We support our clients throughout the entire lifecycle: from feasibility studies to disassembly. Stand 3315
Smulders
Hoge Mauw 200 2370 Arendonk Belgium phone +32 14 672 281 mail info@smulders.com
Strohm
Monnickendamkade 1 1976 EC IJmuiden The Netherlands phone +31 (0)255 763 500 mail info@strohm.eu www.smulders.com
Smulders is an international steel construction company with a proven track record in the engineering, production, delivery and assembly of heavy, technically complex steel constructions. With over 50 years of experience in its field, Smulders was the logical choice for offshore wind structures back in the pioneering days of wind energy 20 years ago. Today, Smulders is an established market leader and can boast delivery of 35 substations, more than 2,000 transition pieces and 150 jackets spread over wind farms in Europe, Asia and soon also the United States. Smulders has more than 1,000 employees working across 5 locations in Belgium, the United Kingdom and Poland. The power of cooperation is a motto that applies unconditionally in all the facilities of Smulders – and to all of its employees. The combination of individual specialisms and internally shared experience forms a source of expertise for any application of steel. It is because of the unique cooperation partnership between our five international branch offices that we can master all the aspects in the field of steel constructions.
Stand 3327
www.strohm.eu
Strohm is the world leader in thermoplastic composite pipes (TCP). TCP reduces total installed and life cycle cost for subsea flowlines, jumpers and risers and has proven to reduce the CO2 footprint of pipeline infrastructures by more than 50%.
The company is committed to driving sustainability with its range of TCP solutions which enable clients towards their net-zero carbon emissions targets and supports the renewables sector. Since 2020, Strohm is certified climate neutral as organization. TCP is a strong, non-corrosive, spoolable, lightweight technology which is delivered in long lengths, resulting in a significant reduction of transportation and installation costs. TCP is installed using small vessels or subsea pallets, significantly reducing CO2 emissions. It is also 100% recyclable.
Strohm’s shareholders are Aker Solutions, Chevron Technology Ventures, Evonik Venture Capital, Saudi Aramco Energy Ventures, Shell Ventures, Subsea 7, Sumitomo Corporation and the private equity investor, HPE Growth. The firm’s manufacturing facility is located at its headquarters in IJmuiden in The Netherlands. Strohm also has offices in Houston (US), Rio de Janeiro (Brazil) and Kuala Lumpur (Malaysia).
Stand 3227
Van Heck
P.O. Box 14 8390 AA Noordwolde The Netherlands phone +31 (0)561 431739 mail info@vanheckgroup.com
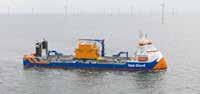
Van Oord
P.O. Box 8574 3009 AN Rotterdam The Netherlands phone +31 (0)88 8260 000 mail info@vanoord.com
VDL Klima
Meerenakkerweg 30 5652 AV Eindhoven The Netherlands phone +31 (0)40 298 1818 mail info@vdlklima.com Van Heck is an internationally operating company with over 50 years’ experience in the field of water control and management. Van Heck’s speciality is often called upon to manage floods.
Van Heck’s expertise includes providing tailormade solutions for dredging, civil and industrial projects, government and water boards. Van Heck is also active in the offshore industry with ballast equipment. This is specifically designed for load-outs and float-overs, and ideally suited for salvage operations. The completely autonomous ballast and deballast system can be entirely controlled from a central point and has a total capacity of over 40,000 tons per hour.
www.vanoord.com
Van Oord is a leading global marine contractor specialising in dredging, energy infrastructure and offshore wind projects. Our purpose is to create a better world for future generations by delivering Marine ingenuity.
The growth of the global economy and the expanding world population are generating an increasing demand for energy worldwide. To meet this global demand for energy Van Oord Offshore provides integrated solutions with a focus on the installation, stabilisation and protection of offshore oil, gas and wind infrastructure. We are a market leader in the seabed intervention technique Subsea Rock Installation (SRI). Our fleet of flexible fallpipe vessels enables us to stabilise and protect pipelines, cables and other installations. Besides, we provide integrated solutions for the installation of nearshore pipelines, cables and offshore constructions. In the energy transition, Van Oord is leading the way towards renewable energy by constructing offshore wind projects. We furnish all-round solutions, often as turnkey projects including engineering, procurement, and construction to assume full responsibility for entire projects for our clients.
www.vdlklima.com
VDL Klima is specialised in the design, engineering and production of industrial heat exchangers and cooling systems for OEMs in a wide range of industries, including oil & gas, shipping, energy, food and the high-tech semiconductor industry.
Besides one-off engineer-to-order projects, we also produce in smaller to larger series. Because we handle the entire process in-house (from design to processing and assembly), we remain extremely flexible throughout the entire project, allowing us to directly incorporate the customer’s wishes into the execution while also maintaining excellent control over the lead-time. VDL Klima has 115 years of experience and supplies systems for various applications, such as coolers for (electric) motors and appendages on various vessels (amongst others cruise ships, LNG and Cargo vessels, Tugboats), generator cooling for wind turbines, (marine)transformer and generator coolers and shell-in-tube heat exchangers for various applications.
VDL Klima is part of the VDL Groep, with its head office in Eindhoven, the Netherlands. VDL Groep is an international industrial family business with 105 companies, spread over 19 countries and with more than 15,000 employees. Stand 3433
Stand 3433
READ THE LATEST NEWS ON OUR DIGITAL NEWSLETTER
CLICK HERE FOR FREE SUBSCRIPTION

OFFSHORE VIBRO TECHNOLOGY
01 UPENDING, LIFTING, DRIVING IN SINGLE OPERATION
02 IN COMBINATION WITH DP OPERATED VESSEL THE FASTEST WAY OF INSTALLING MONOPILES
03 NO NEED FOR GRIPPER OR INSTALLATION FRAME
04 VERTICALITY MONITORING DURING DRIVING
05 CONTROLLED INSTALLATION
06 MODULAR DESIGN
07 ELIMINATE PILE RUN/DROP FALL
08 NO DIAMETER LIMITATION
THIS IS WHY WE LOVE THE CAPE VLT
DISCOVER HOW ITS UNIQUE FEATURES WILL UPLIFT YOUR NEXT PROJECT
GET THE OFFSHORE VIBRO TECHNOLOGY GUIDE
