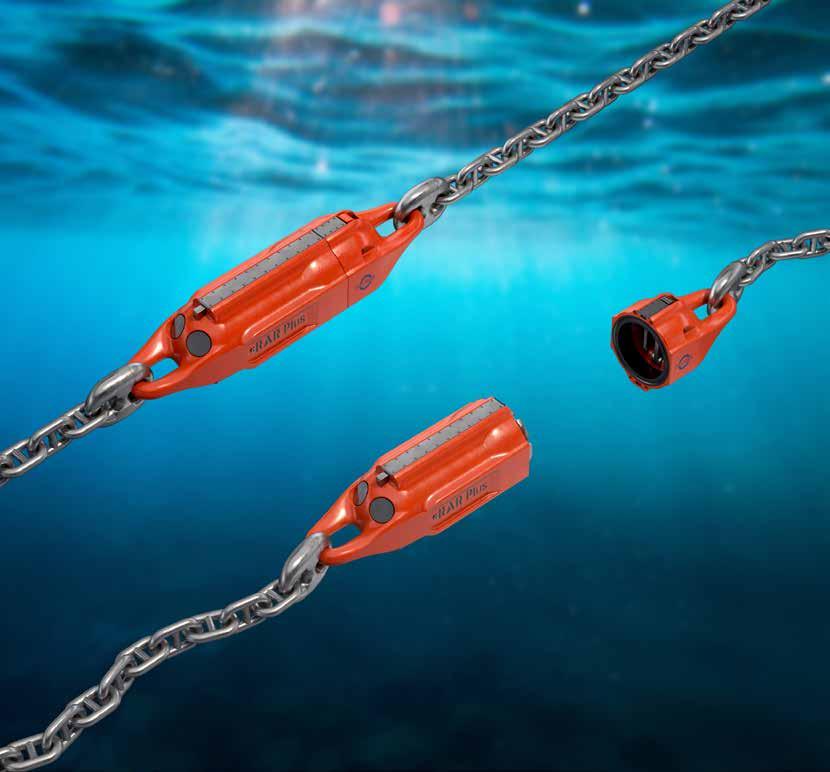
8 minute read
Success with RAR Plus™
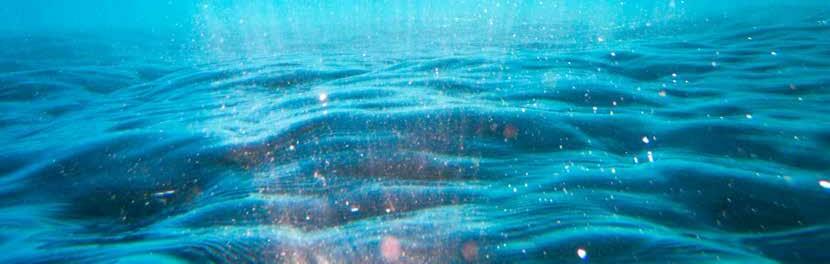
Since 2018, the RAR Plus has been deployed to release over 530 mooring lines on 64 different MODUs for efficient rig move operations, storm evasion, and ice avoidance.
Advertisement
Unmooring MODU Deepsea Stavanger
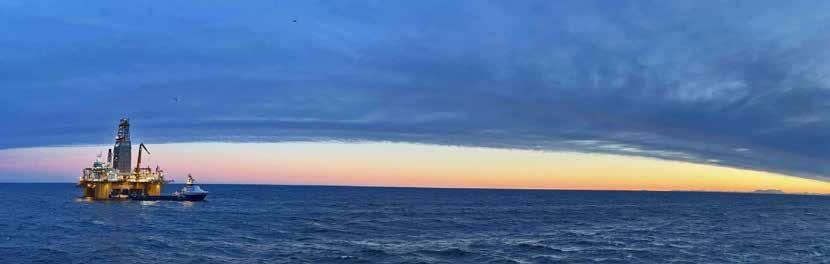
Lundin Energy and Delmar & Vryhof have success with RAR Plus™
Unmooring a Mobile Offshore Drilling Unit (MODU) from eight mooring lines in less than two hours is quite an achievement; especially, when comparing conventional unmooring times that take up to twelve to eighteen hours in ideal weather. In January 2022, this is what Lundin Energy Norway AS experienced using the Delmar & Vryhof RAR Plus™ Releasable Mooring System on the Deepsea Stavanger.
This semisubmersible offshore drilling unit is one of the largest active MODU in the North Sea, and Lundin’s actual drilling location was fairly close to the Norwegian coast with area characterised by bad weather conditions. In the words of Sigmund Andre Hertzberg, Senior Marine Supervisor at Lundin Energy Norway AS: “In close consultation with Odfjell, we therefore decided to deploy an anchor system consisting of anchors, chain and fibre rope, in combination with the RAR Plus™ Releasable Mooring System (RMS).”
Lundin was already convinced of the exceptional features of the RAR Plus™ System as they saw its advantages during a drilling campaign in the Barents Sea. Nonetheless, the quick release with a ‘single touch of a button’ to unmoor the Deepsea Stavanger in marginal weather conditions exceeded the operator’s wildest expectations. The operational efficiencies of the RAR Plus™ Releasable Mooring System allowed Lundin to save substantial time, money, and reduce their NOx and CO2 footprint by having no vessels onsite when unmooring. Sigmund Andre Hertzberg has nothing but praise when talking about the fast and successful unmooring of the semi-submersible Deepsea Stavanger.
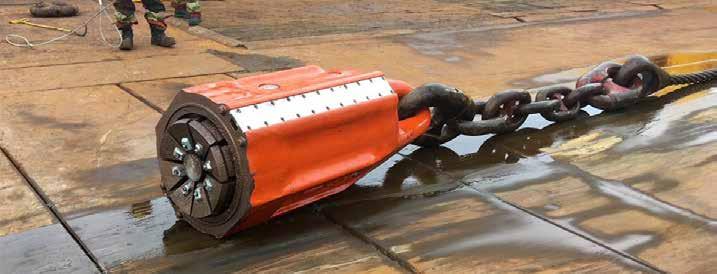
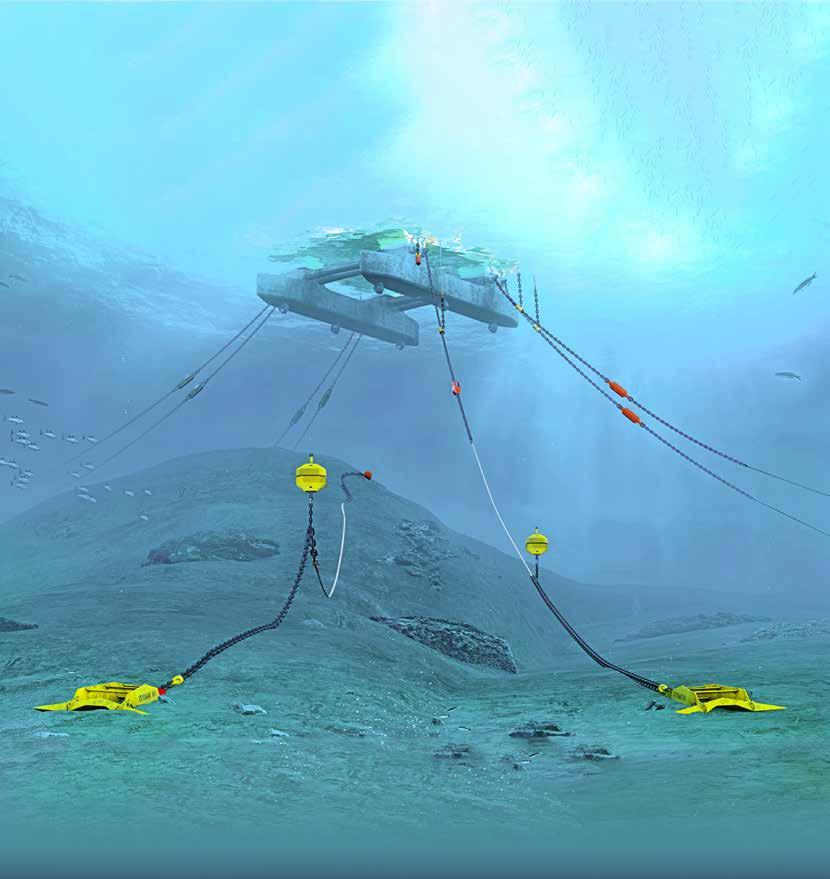
Sigmund Andre Hertzberg, Senior Marine Supervisor at Lundin Energy Norway AS.
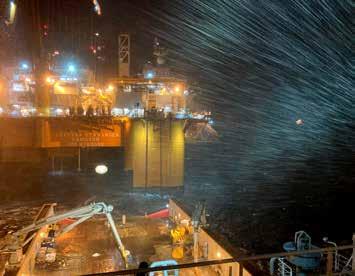
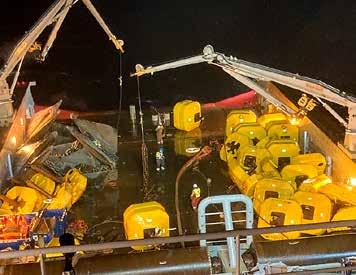
Pictures: Lundin Energy.
Cost reductions
One of the primary advantages of deploying the efficient RAR Plus™ is that it removes the need for traditional anchor handling vessels during unmooring operations. Once a rig has completed drilling and is ready to move on, it is simply a matter of releasing the rig from the mooring lines at the ‘touch of a button’. In the case of the Deepsea Stavanger drilling project, Lundin Energy had anticipated that deploying anchor handling vessels to disconnect all the mooring lines would require a 12-hour operation, which in turn would result in the company requiring an 18-hour weather window. Moreover, the maximum permitted wave height would have been 3.5 metres HS, or the operation would have to be postponed. Sigmund Andre Hertzberg continued: “All-in all, we predicted a 12 to 18-hour disconnection operation for all the mooring lines with three vessels. Given the weather probability plot at the chosen disconnection time and our decision to deploy RAR Plus™, the result was a time saving of at least fourteen days. In precisely 1 hour and 50 minutes, the Deepsea Stavanger was ready for immediate departure from the well location, without assistance from a single anchor handling vessel. Incredible, but true. For Lundin Energy, the time-saving achieved also meant no further rig hire, an overall reduction of the environmental footprint of the operation and on top of that, no need to pay daily rates for the anchor handling vessels. All we needed were a couple of boats to recover the mooring system, consisting of between 1000 and 1500 metres of round chain, 800 to 1200 metres of fibre rope and an 18t STEVPRIS MK6 anchor for each mooring line.”
Acoustic and mechanical release
So what exactly is the nature of the RAR Plus™ Releasable Mooring System (RMS) of Jørund Havnerås, Managing Director at Delmar Systems AS, explained: “The RAR Plus™ is unique in that it allows immediate MODU transit following release of the mooring line using the RAR Plus™, from their secured position in the trigger sleeves against the rig’s fairlead. Delmar Systems introduced this new generation technology to the market in 2018. The RAR Plus™ is an enhanced version of the original RAR which had acquired more than 35 years’ documented use in MODU ice avoidance operations. The most important new development is the addition of an independent mechanical backup release feature, which ensures the ability to still release the moorings in the unlikely event that the remote acoustic transmission fails to actuate the RAR. The backup mechanical release bypasses the acoustic, electronic and hydraulic systems in the RAR Plus™, and can be actuated from the trigger sleeve, thereby guaranteeing 100% redundancy within the system.”
The innovative RAR Plus™ also has a significantly increased minimum break load (MBL) of 907 tonnes, certified by DNVGL and ABS. As a result, with its robust shell and locking mechanism, the device is not the limiting MBL component, even in systems that include modern R5 high-strength components in their mooring line.
High-quality project
Lundin’s senior marine supervisor looked back with satisfaction, on a high-quality project off the Norwegian
coast and the successful deployment of RAR Plus™. He was also delighted with the cooperation with the people from Delmar Systems. In Hertzberg’s own words: “Lundin Energy and Delmar Systems have already been working together for a number of years. Disconnecting the Deepsea Stavanger was the perfect opportunity to consider all the benefits of Delmar’s releasable mooring system, from a range of different perspectives, and to deepen our understanding of various components of the RAR Plus™ system. Although we faced a number of challenges during the preparation and execution phases of the project, we still maintained very open and honest dialogue, throughout. Lundin Energy and Delmar Systems have no secrets from each other, and that in itself is an essential precondition for successfully completing a complex project of this kind.”
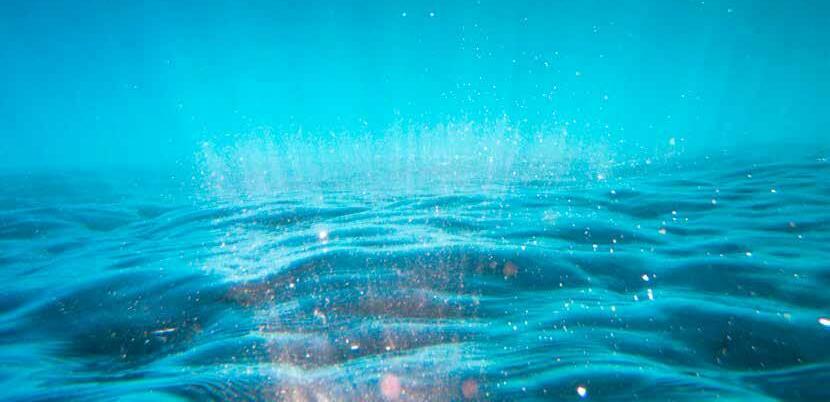
Integrity builds Trust
“Achieving this significant milestone without a safety incident or failure to release highlights the talented nature of our workforce and the unique dependability of the RAR Plus™,” concluded Jørund Havnerås.
“Completing an operation involving an eight-line mooring spread in under two hours represents substantial cost savings in rig and vessel time, for Lundin. We appreciate Lundin’s trust in deploying the RAR Plus™ on this valuable operation.”
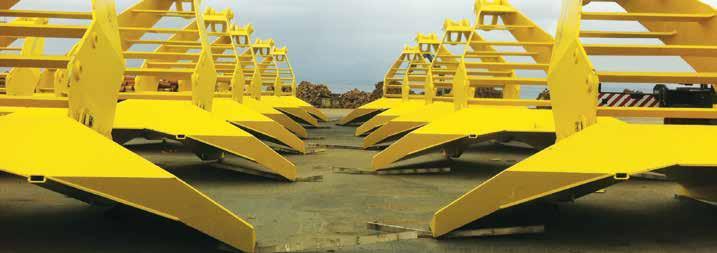
The mooring system used during this particular drilling campaign in the North Sea, consisted of between 1000 and 1500 metres of round chain, 800 to 1200 metres of fibre rope and an 18t STEVPRIS®MK6 anchor for each mooring line. This anchor has been developed by Vryhof, the Dutch world leaders in the market for innovative and customer-focused anchoring and mooring solutions, which was acquired by Delmar Systems in May, 2021.
Due to their versatility STEVPRIS®MK6 anchors serve a wide range of mooring applications. Although the large majority serves the mooring of offshore units such as drilling rigs, FPSO’s and SPM buoys they are also widely used for various dredging, crane and pipelay vessels.
The anchor’s geometry provides an extreme high weight/strength ratio. The fluke shape minimizes soil disturbance and its large surface provides the huge holding power that is well in excess of 30% more than that of any other drag anchor today.
STEVPRIS®MK6 has superior uplift capability. On a case to case basis uplift is allowed of 5 degrees in intact condition and 10 degrees in damaged condition. API rules suggest an uplift of 20 degrees, proven in tests to be possible without losing holding power. The uplift capability significantly increases the range of water depths in which rigs can operate on the same anchor spread.
Important focus area will be energy transition
Breman Machinery has a track record of supplying mission critical offshore equipment. A project for Breman Machinery starts with an engineering package either in digital form or on paper. This is transformed in steel components of extremeproportions and precise dimensions. These are assembled - together with purchased items such as hydraulic and electric parts - so that ready-to-use equipment is supplied to clients.
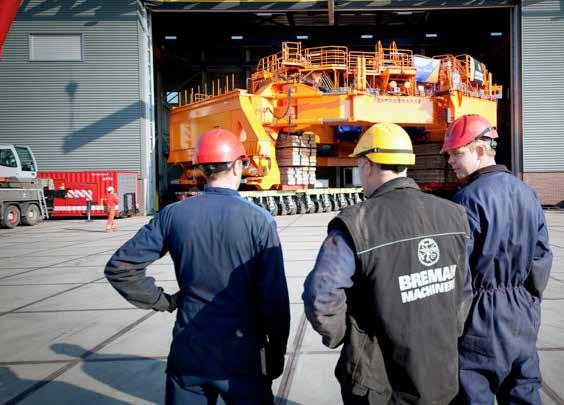
For these clients however, the development of new offshore equipment starts much earlier with conceptual development and engineering phases. Sometimes even the installation method still needs to be developed in the early days.
New initiative
In order to also assist clients in those first phases Breman Machinery has decided to create a new initiative called Breman Innovation. This new company will be managed by Arjan Boezeman. Arjan has previously worked for The Ocean Cleanup and for Norwegian shipbuilding group Ulstein. Before that he was one of two founders of an engineering company that built a track record of developing tools from a blank sheet of paper into convincing equipment proposals.
With this addition in service, Breman Machinery is able to provide clients a wider scope of supply.
Important focus
An important focus area of Breman Innovation will be energy transition, electrification and the reduction of the CO2 footprint of offshore operations. In addition Breman Innovation aims to be engaged in waste handling equipment and smart lifting tools.
With this step Breman Machinery acts on the ambition to further strengthen its leading position in the supply of extreme offshore energy equipment.