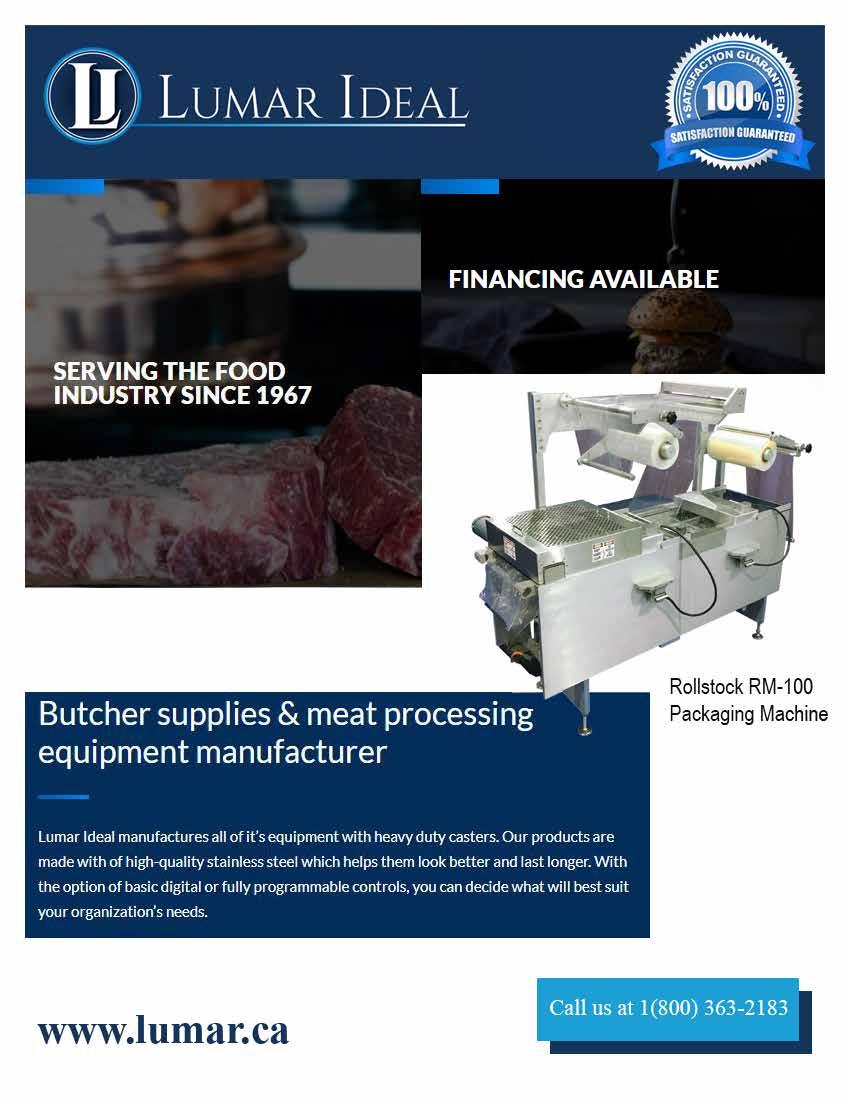
6 minute read
How Traceability is Modernizing Abattoirs
By Joe O’Keefe, Account Manager, Carlisle Technology
Everyone loves meat, but very few people understand what goes into the food manufacturing process. To accommodate and adapt to the never-ending demand for meat and poultry products, the industry has had to adjust rapidly. This article will provide a glimpse into the production processes and food safety measures of abattoirs in the past versus how modern-day abattoirs operate today. We will also focus on the importance of traceability, the usefulness of data collection, and operational efficiencies in the modern-day food plant.
The Historical Abattoir The abattoir emerged as a revolutionized institution in the nineteenth century. A combination of health and safety concerns, exacerbated by the rapid urbanization experienced during the Industrial Revolution, led social reformers to call for the isolation, sequester, and regulation of animal slaughter. Concerns were also raised about the lack of sanitization and the foodborne disease coming from abattoirs. Abattoirs previously had been lacking in critical elements that are imperative in today’s supply chain such as traceability, real-time production visibility, and sanitation standards for their plant floors. Processors were more focused on production volume and speed, to accommodate an ever-increasing demand for animal products.
Current Abattoir’s Adoption of Traceability Today’s meat and poultry processing industry is much different and has evolved from 30-40 years ago. Population growth, globalization, and an ever-growing demand for products such as beef, poultry, chicken, fish, continue to drive growth and expansion for the era of the mega-plant in North America.
Present-day abattoirs are becoming increasingly better equipped to incorporate cutting, processing and packing departments, deep freeze units, and warehousing. One of the main reasons for this shift is government-mandated action. Due to a long history of recalls, food safety issues, public health concerns, and no viable way of preventing them, traceability has become the solution.
Since the passage of the 2011 Food Safety Modernization Act, the FDA has shifted its food safety and food traceability approach. The new proposed set of regulations is part of the FDA’s New Era Blueprint. This blueprint emphasizes the importance of food traceability, and a processor’s responsibility to collect and pass along relevant information that can be used in the event of a food recall. For a comprehensive look at the new proposed rules, check out the FDA’s website https://www.fda.gov/food/ food-safety-modernization-act-fsma/fsma-proposed-rule-foodtraceability. Why is Traceability Needed? Traceability is needed for recall management, investigation into plant and animal disease, efficiency and productivity improvements, cost and waste reduction, better supply chain management, and ability and access to new markets. Traceability has become the cornerstone of a modern-day food plant.
Benefits of Traceability include: • Improved accuracy and access of information when responding to quality and food safety issues or incidents. • Quality Recall Management • Enhanced reporting and response to disease outbreaks which causes and reduced impact upon markets and operation. • Increased efficiencies with record-keeping and tracking of costs related to labour, productivity, and waste. • Tighter inventory control and improved logistics for achieving a competitive edge. • Access new and retain existing markets by meeting expectations for product tracking and verifications of claims. • Real-time data collection and the availability of historical data. • Access to accurate and timely data for better decision-making.
Traceability Provides Abattoirs with Actionable Data In the era of big data, data collection is one of the prime benefits of a traceability system. Food plants can run leaner, more efficient plant-floor operations. Having accurate carcass yield data is the key to providing producers with valuable insight. Even a small amount of waste can result in large product loss. Therefore, yield reporting and analysis are a huge part of the production manager’s daily function. Thus, collecting data at key production points and making sense of the data for yield management can improve plant performance. This information can be arranged into visual data dashboards to allow managers to make more informed decisions.
How Technology Strengthens Traceability With the implementation of a fully integrated traceability system, the food plants have streamlined their plant-floor operations by implementing modernized, high-accuracy solutions. These include: • Static/In-Motion Conveyor Lines • Mobile Handheld Computers • Print and Apply Systems • ERP System • Warehouse Management System • Manufacturing Execution System
While strides have been made within the food industry, many abattoirs have still not implemented and utilized modernized technology to optimize their plant floor.
A typical traceability solution designed to capture slaughter and animal/carcass information on the kill floor will integrate multiple components. Plant floor MES, WMS, ERP software, live animal scales, carcass rail scales, RFID tag readers, barcode scanners, label printers, and weighing/labeling software all need to be integrated to make one complete solution.
It’s easy to see the value in adopting a modern integrated solutions that can help capture Kill Floor data and track carcasses through slaughter and further processing. The data collected provides valuable information back to the abattoir or processor, and it gives them full visibility into the history of each carcass or receiving lot.
The Future for Abattoirs is in Automated Traceability The future for Abattoirs is the adoption of technology and the implementation of efficient processes in manufacturing. Transparency and visibility on a Kill Floor are vital to helping abattoirs survive. They regularly face an obstacle course of government auditors, producer demands, religious ceremonial requirements, and political activists. Therefore, a fully integrated traceability system that does data capture as well as streamline operations can be a real lifeline to an abattoir facility. By implementing an integrated traceability system, abattoirs can have real-time information about every animal or animal lot that has been processed through its facility. This is imperative for Abattoirs looking to aggressively, expand from their market, supply their products to larger distributors, and maintain operational efficiency. Plant traceability solutions give the processor or abattoir complete product traceability from animal receiving to the sale of the final product.
A fully integrated traceability solution is a long-term investment. While it may seem costly at first sight, the long-standing benefits outweigh the initial concern. This type of system elicits improved efficiency, clear ROI, streamlined operations, and 360-degree traceability and vision into the plant floor operations.
Simply put, a traceability system modernizes your plant and empowers your decision making by providing actionable data. Abattoirs are the backbone of the food industry. The evolution and modernization of their plant-floor operations are not only critical to achieving success, but they are also critical to the industry.
FoodTraceabilitySolu�ons
DesignedfortheMeatIndustry
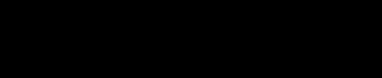

ScheduleaDemoToday!
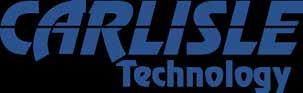
www.carlisletechnology.com (800)806-2000

AWorldofSolutions forallofyourCasing andPackagingNeeds
THERMOFORMING FILMS
• Atopqualityrangeofcrystalcleartopandbottom thermoformingmediumandhighbarrierflexiblefilms. • Suitableforallfoodapplications,thermoformingfilmsare9layer crystalclearcoextrudedfilmsproducedwithstateoftheartnew technologyextruders. • Thickercornersafterthermoforming • Widethicknessrangeavailability
SHRINK BAGS
• Wedeliveranextensiveshrinkbagproductlinewithstrong mechanicalpropertiesandagreatopticalattributes. • Superioroxygen-barrierthatensuresprotectionthroughout distribution,storageandretail. • Regularand“Boneguard”protectionprovidingasolutiontoall yourproductrequirements. • AwiderangeofShrinkBagsizesavailableforallapplications.
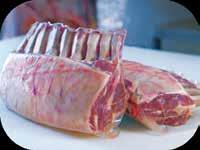
EDIBLECOLLAGEN
• Reducescookingcycles,improvesyieldsandoptimizes production. • Excellentsmokingpropertiesforoptimalandattractivefinal products. • ExpandyourrangeofslicedproductswithCOFFINETTCN.
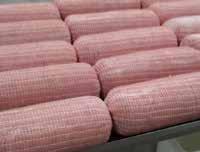
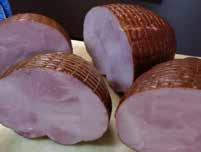
Formoreinformationcontact: TimSylander
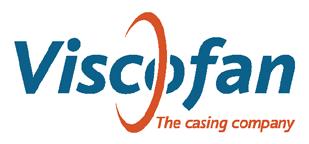