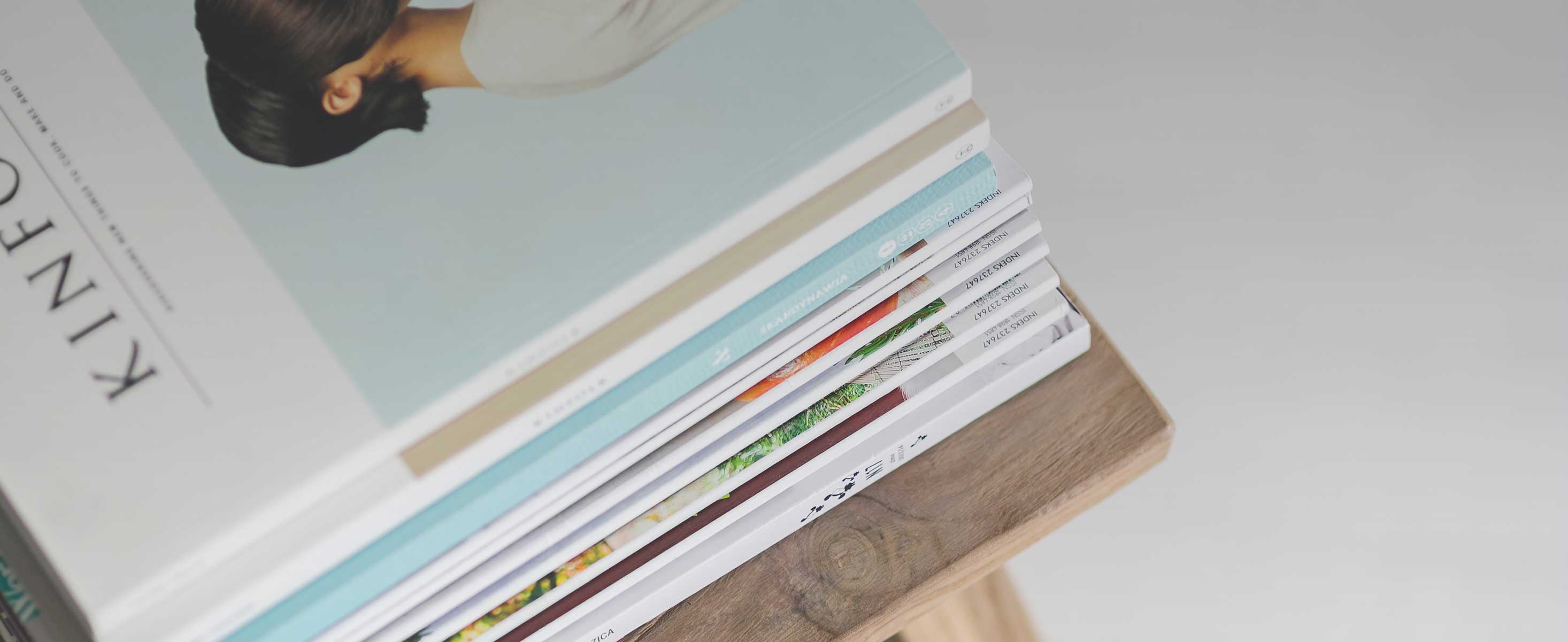
3 minute read
Measuring for Food Safety
By Daphne Nuys-Hall, Technical Director, Meat & Poultry Ontario
The concept of Key Performance Indicators (KPI) has been around for a long time in business and manufacturing. Specifically, KPI stands for key performance indicator, a quantifiable measure of performance over time for a specific objective. KPIs provide targets for teams to shoot for, milestones to gauge progress, and insights that help people across the organization make better decisions. KPIs have been used in sales, production, and even human resources. But what about food safety? What KPIs does your company have in place to measure the success of your food safety programs? And what influence do these have on your food safety culture?
The first step in establishing KPIs is to determine what your food safety objectives are. What is it that your company is trying to achieve? It is important to clearly state the objective. Let’s look a quick example that can be used in a meat processing facility today – the objective would be to reduce customer complaints by 5%. Once the objective has been determined, the activities that need to occur (what measurements need to be taken) to support reaching that objective must be defined - these are the key performance indicators. Therefore, in this case a company would need to collect data to first determine the number of customer complaints and then evaluate that data on an on-going basis to measure their success at achieving the objective – in this case a reduction of 5%. But where would the company find this data?
For this example of customer complaints, it is a requirement of Ontario Meat Regulation 31/05 to have a documented Recall Program that must include “methods to investigate and respond to consumer complaints”. Often this means recording customer complaints when they are received. However, what happens to those customer complaints once they are resolved? Is it just filed away in binder on a shelf never to be looked at again? Take the time to log the complaint into a database – it doesn’t have to be complicated, just a simple spreadsheet will do. Every time a complaint is recorded, review the previous complaints for any trends, such as multiple complaints about the same issue, the same customer having repeat complaints, etc. Once KPIs are measured and the results are shared, then informed decisions can be made about where resources and efforts need to be spent. The process of investigating and resolving customer complaints should been seen an opportunity for continuous improvement in your business.
In the meat industry we are collecting data all the time. Often meat companies are collecting data as evidence that they are in compliance with regulations, that products are manufactured in accordance with the recipe or specifications, or that products are meeting customer’s expectations. However, it is what we do with that data that is important. Do the people who need to see the information actually see it? Do they review the information collected and look for trends or opportunities for improvement?
No matter what your food safety objectives and KPI’s are, the most important element to their success is the support of top management. This means that top management is communicating the importance of the food safety objectives, top down, and are investing time and other resources to make sure that accurate measurements can be taken, and corrective actions are taken when they trend off target.
KPIs are invaluable tools for your business as it gives you insight into your operation. Informed decisions maximize resources and ensure that focus remains on top issues, namely food safety and quality.