
4 minute read
Austin Western Pilots New Train System
by OneWatco
Watco’s Austin Western Railroad (AWRR) is nearing the completion of a project that is very rare for a short line to undertake: equipping 10 of their locomotives with a distributive power system.
Distributive power (DP) allows the Austin Western to place their locomotives at different points in the train, usually at each end. All the engines communicate with each other and are operated by a single train crew. The system is a significant investment and the installation and conversion of the locomotives are time consuming.
“Distributive power gives our crews better control of their trains,” said Ben Tarran, director of locomotive support and lead on the project. “The Austin Western is a great place to implement this system due to the area’s geography and the commodities the railroad hauls.”
The AWRR regularly hauls heavy rock trains, and the line’s steep grades and curves present a challenge when all the locomotives are located on one end. They can be placed at each end, but without distributive power, it requires a second crew. Now, one crew can control all the locomotives.
“Typically, we might use five locomotives at the front of the train,” Tarran said. “That can make the locomotives bog down on hills and curves. Now, if we put DP locomotives at the front and the back, one engineer can control all the locomotives’ throttles and brakes as they negotiate the track conditions.”
The benefits of DP make the investment worth it. By simultaneously pushing and pulling the train, it lessens the forces on knuckles that couple the cars together as they navigate the slopes and curves of the AWRR.

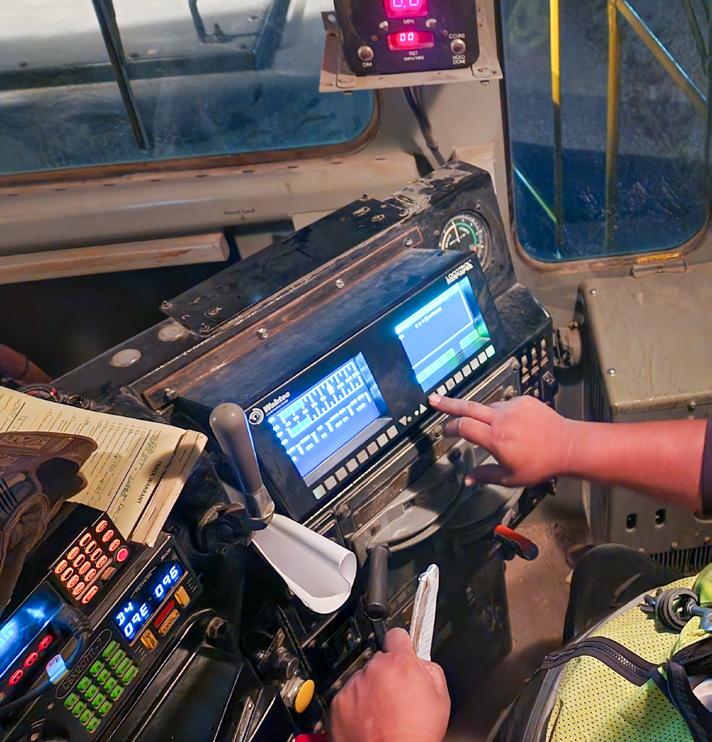
This reduces wear and tear on the railcars. Better control also increases safety. The AWRR passes through many communities and even shares the rail with Austin’s busy commuter line.
DP creates fuel-saving opportunities. It takes fewer locomotives to do the same job, and since the team can push and pull at the same time, they don’t have to rev the engines as high.
“In the past, they might be running five engines at notch 8 to get up some of these hills,” Tarran said. “Now, we might have four locomotives at notch 6. There’s definite fuel savings there.”
Installation was no easy task. Supply chain issues delayed delivery, and when the components arrived, it took extensive work from the AWRR team and their vendor, Precision Train Control Services, to make it all work. It’s not simply plug-and-play. Wiring harnesses and circuit boards had to be built from scratch before the control units could be integrated. Another aspect of DP is the Fast Brake system. This meant the old braking system had to be torn out of the locomotives and completely replaced with an electronic braking system.
Finally, the AWRR crews had to be trained. DP-equipped trains handle differently. The team worked with trainers at the Safe Performance Center (SPC) to create an AWRR program for their locomotive simulators. The SPC’s mobile simulator was set up with the AWRR’s track conditions and new DP capabilities and brought on-site so engineers could gain valuable experience before physically handling the new system.
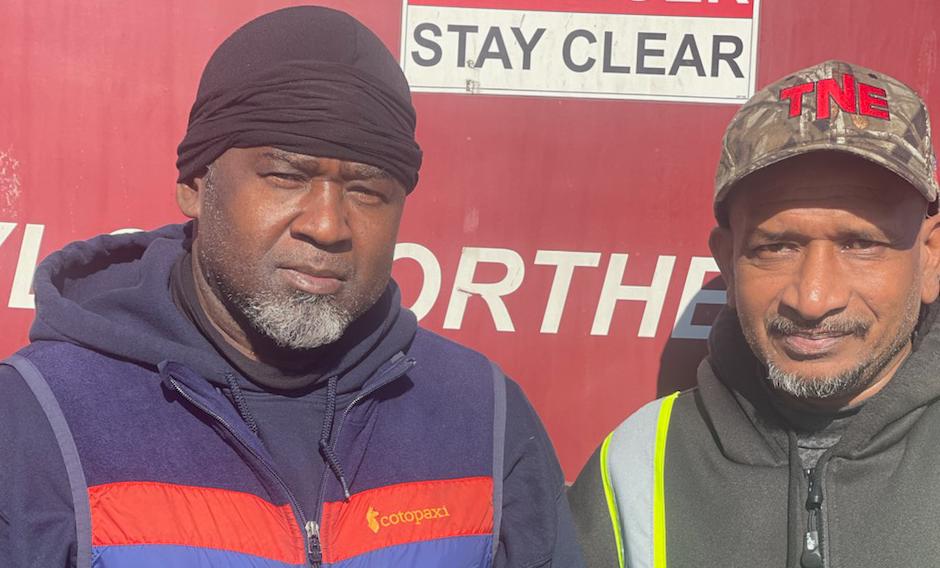
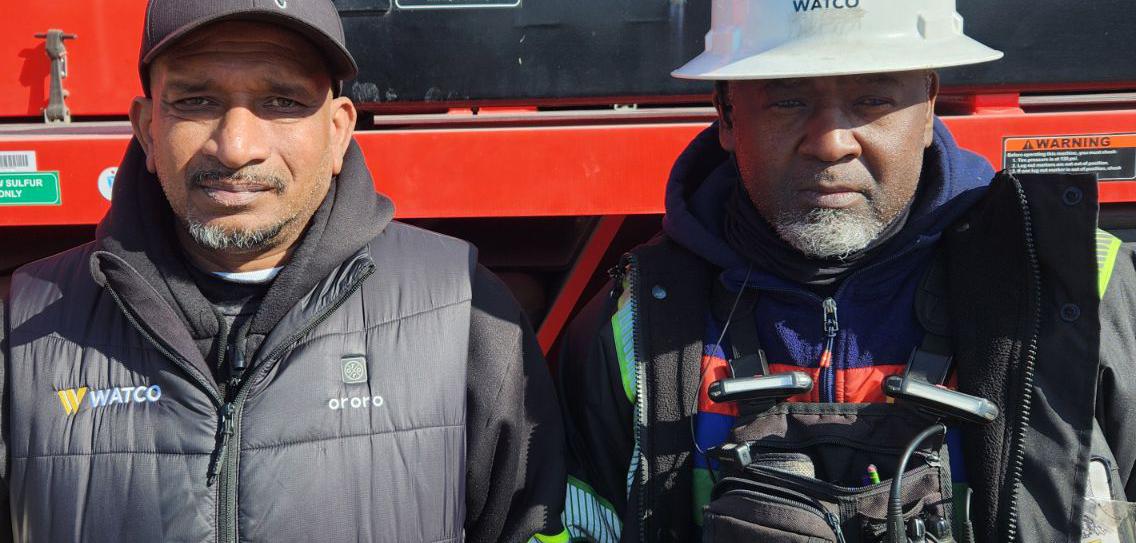
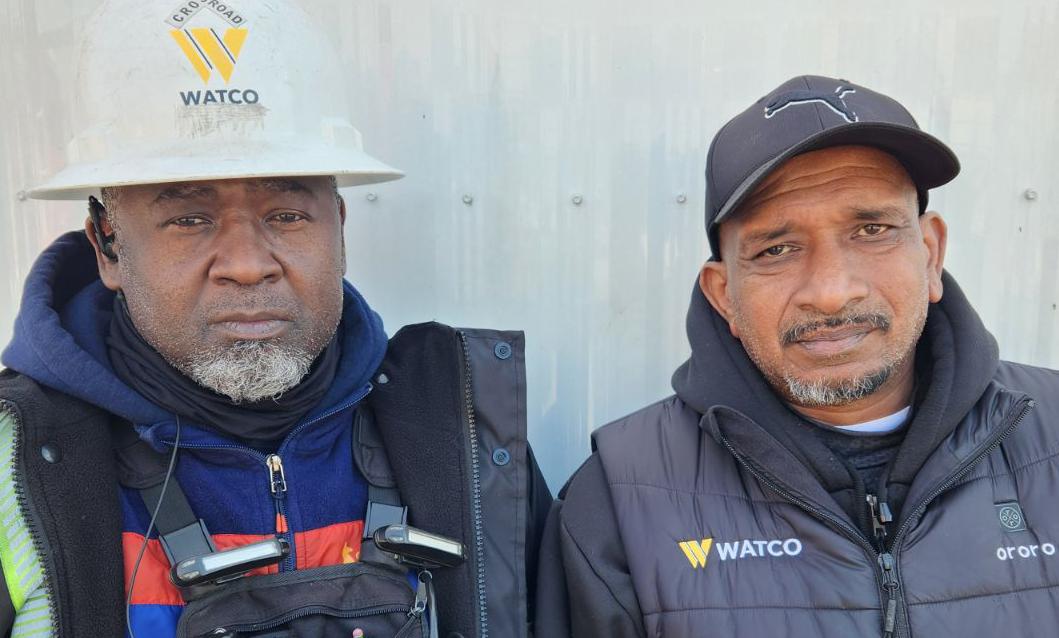
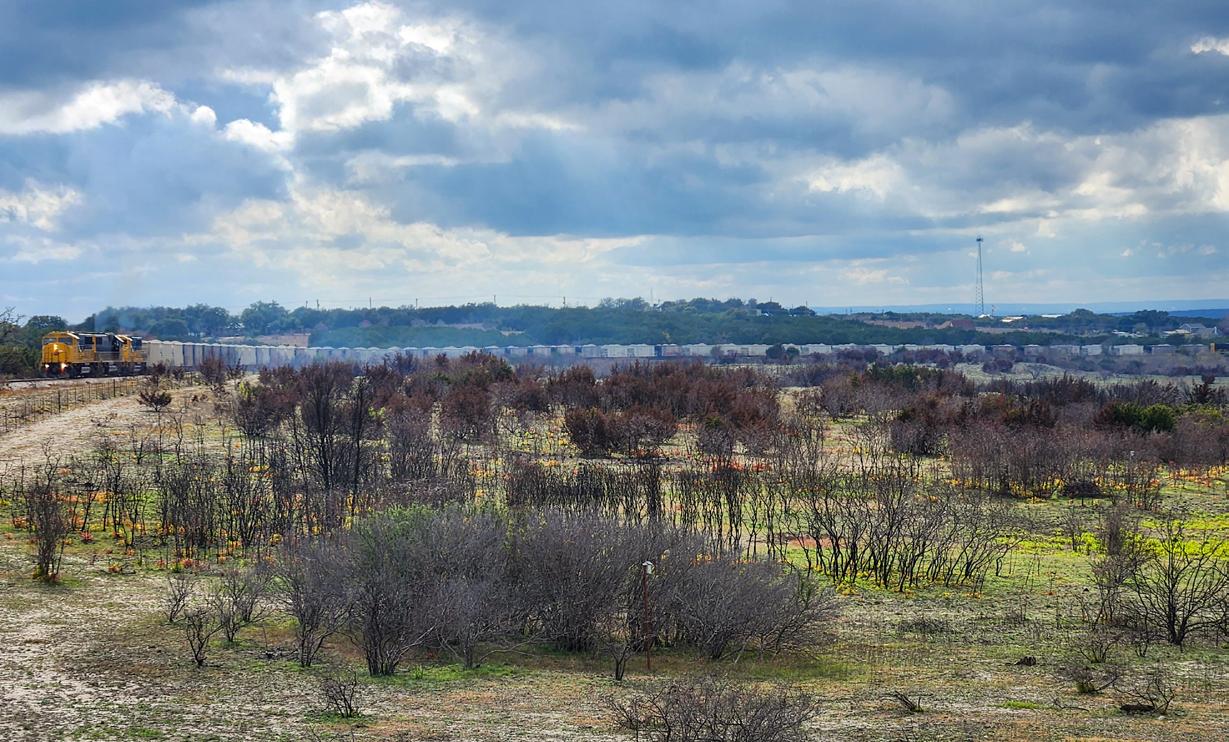
The AWRR regularly hauls heavy rock trains, and the line’s steep grades and curves present a challenge when all the locomotives are located on one end. They can be placed at each end, but without distributive power, it requires a second crew. Now, one crew can control all the locomotives.
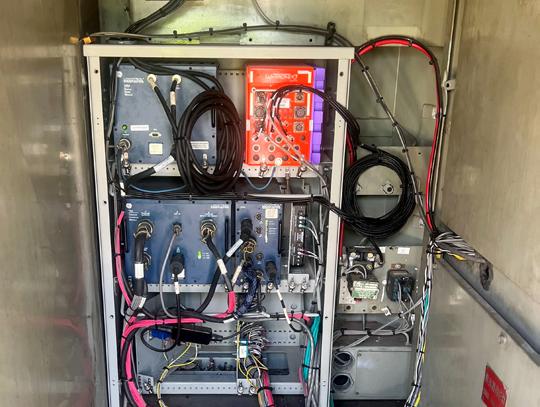