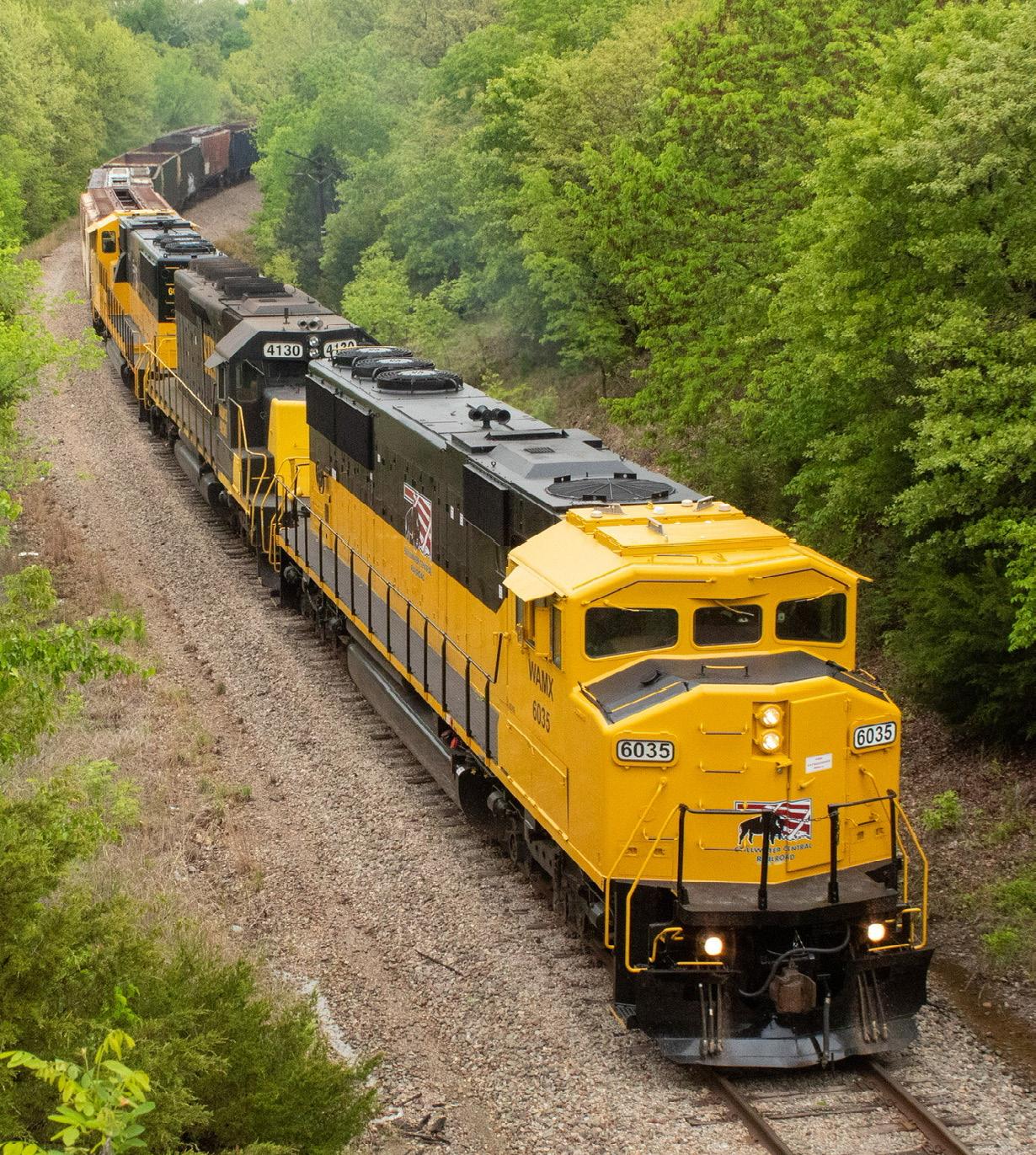

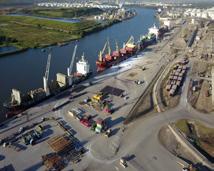
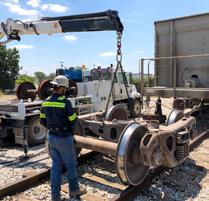
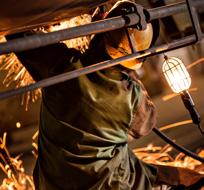
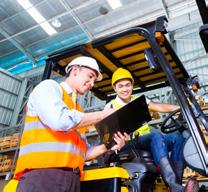
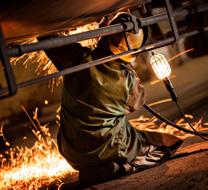
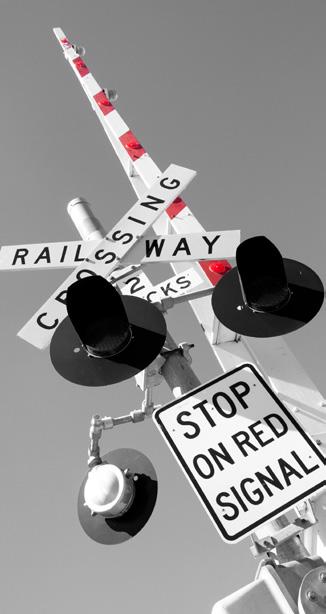
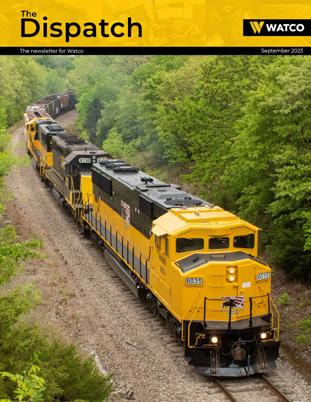
Congratulations to the following locations who celebrated August Safety Anniversaries:
August 8 – Cherokee Switching (AL) – 7 years
August 8 – Freeport Industrial Rail (TX) – 1 year
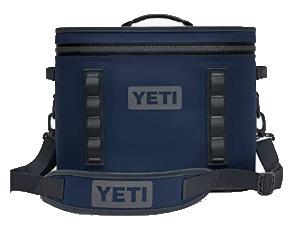
August 8 – Oklahoma City Transload Terminal (OK) – 4 years
August 10 – Willis Transload Terminal (TBT) (MI) – 13 years
August 10 – Mission Mountain Railroad (MT) – 7 years
August 14 – Sauget Cahokia Marine Terminal (IL) – 1 year
August 17 – DeRidder Ingevity (LA) – 2 years
August 17 – Pennsylvania Southwestern Railroad (PA) – 12 years
August 19 – Burley Transload Terminal (ID) – 1 year
August 20 – Baton Rouge Southern Railroad (LA) – 1 year
August 21 – Fryburg Dedicated Terminal (ND) – 1 year
August 26 – McIntosh Switching (AL) – 3 years
August 30 – Savannah & Old Fort Railroad (GA) – 4 years
August 31 – Hawesville Marine Terminal (KY) – 4 years
Moo-ving Liquid Cattle Feed By Rail
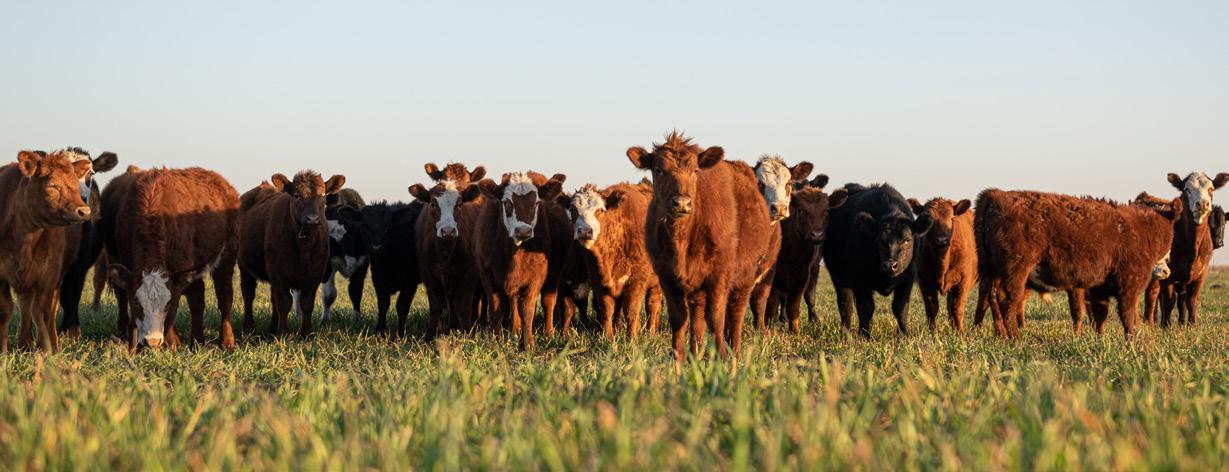
With Watco as a logistics partner, moving freight by rail can be as easy and reliable as trucking.
Take a Wisconsin-based agriculture manufacturer, for example. After exclusively moving their product over the road, they decided last year to shift their transportation strategy to rail in order to enter new markets as far away as Washington, California, and Texas.
The customer sought a third-party logistics provider to help them make this shift. And that’s just what our team did, thanks to the efforts of many like Logistics Director Sabin Reynolds, Oshkosh Transload Terminal Manager Solomon Watkins, and Wisconsin & Southern Railroad (WSOR) Sales Manager Mike Sullivan.
There’s always a learning curve when trying something new. But with Watco as their partner, the customer quickly got up to speed and benefited from having our team serve as a trusted advocate.
Reynolds said, “We were glued to the hip of the customer throughout the setup and implementation process. Our team covered everything from how a railcar is configured, the cost of leasing railcars, to physically showing them how to safely transload product from truck to rail.”
For rail to be a success for this customer, it was essential to lease a fleet of tank cars to support this business. That’s not the easiest task given the nation’s current railcar shortage. But that didn’t deter Watco. Team members served as liaisons between the customer and railcar brokers, located the appropriate tank cars, and aided in pricing conversations.
After procuring the fleet, Watco tackled the next obstacle: demurrage. To avoid congesting Class I railroads or serving yards before rail operations started, Watco metered tank cars into the OshKosh Transload Terminal.
Today, all tank cars are in use. Watco’s logistics team uses freight technology to monitor tank cars every step of the way — from starting at the Oshkosh Transload Terminal, and the WSOR track and interchange points where tank cars get picked up by Class I partners, and final delivery. And at any time a tank car stays parked for too long or is misrouted, our logistics experts help resolve the issue quickly.
“To say the customer is pleased is an understatement,” said Sullivan. “Watco is excited to grow alongside this customer. We could potentially have double the railcars dedicated to this customer by this time next year.”
“He’s assembled the best track team I’ve ever seen in all my years of railroading.”
That’s what Mississippi Southern Railroad (MSR) General Manager Michael Goss said about Roadmaster Devin Jurs. Goss would know. He’s been in the rail industry for 20 years.
Jurs came to the MSR from the Boise Valley Railroad in 2020 as a track foreman. His initiative and knowledge quickly led to his promotion to roadmaster, overseeing maintenance on all 156 track miles in eastern Mississippi.

Jurs went all-in, familiarizing himself with the track and location. His efforts have reduced track team turnover and track-caused derailments. He also helped organize visits for the government officials who ultimately awarded the MSR state-funded short line railroad grants.
need and stepped up. They took time to help repair bad rail and educate them on what to look for to avoid issues in the future.
“Devin went above and beyond to help our customer make sure they could ship their products safely,” Goss said. “It’s a classic example of Watco’s customer-first focus and doing more than is asked of him and his team.”
That’s where Jurs exceeds the requirements of his regular duties. Recently, a customer doubled the amount of railcars shipped on the MSR. As a result, the customer began having track issues. Since the customer owns the track inside their facility, the MSR isn’t responsible for maintaining it. However, Jurs and his team saw the customer’s
“He basically started from scratch,” said Goss. “Today, he has a finely tuned team that looks for issues and fixes them before they become problems. Because he knows the track so well, he was able to easily show the state officials where we needed help and why.”
Southern Idaho Successes
If you want to see the full range of Watco’s customer service capabilities in action, look no further than southern Idaho.
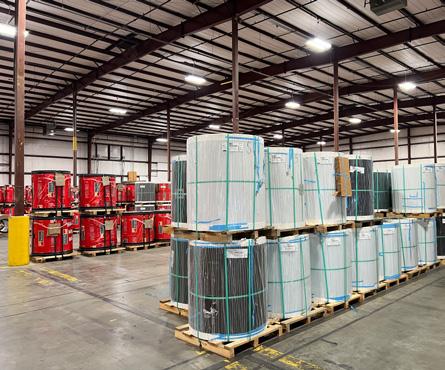
In early 2020, an ethanol plant on the Eastern Idaho Railroad (EIRR) was forced to shut down. Ethanol is made from corn, but the thriving Idaho dairy industry also runs on corn. Liberty Basin, a cattle feed provider, saw potential at the site.
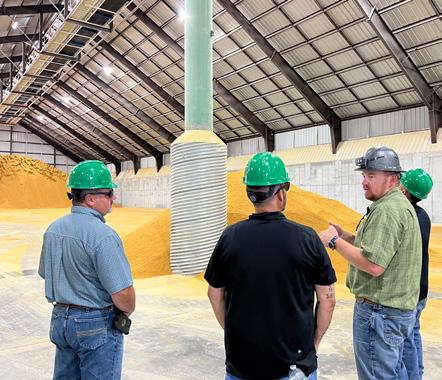
They purchased a majority of the facility, developed plans for a high-tech feed processing facility, and turned to the Watco team for support. The EIRR team created a service plan to support their vision for a new 300-railcar capacity storage barn and expanded rail infrastructure to accommodate unit trains and manifest cars simultaneously. Watco’s Design & Development team was brought in to help with planning and construction oversight.
“Liberty Basin came in and breathed fresh life into the complex,” said Sales Director Kurtis Lindsey. “We came in at the 10-yard line and helped get it into the end zone. What they’ve done is very impressive, especially considering it was completely idle two years ago.”
Liberty Basin’s investment also helped the ethanol plant get running again. Today, the EIRR is providing rail service to both customers with the help of a rail yard expansion made possible by a Federal Railroad Administration Consolidated Rail Infrastructure and Safety Improvement grant.
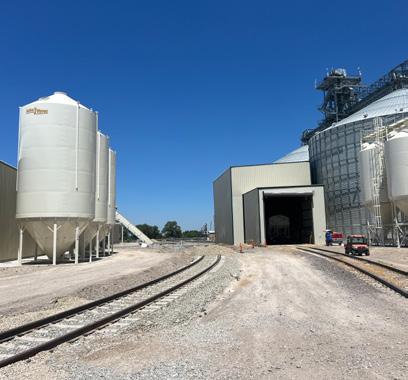
Just over a mile down the line, the Burley Transload Terminal is also getting in on the action. Formerly a primarily perishable, food-grade warehouse, the terminal has expanded to support the dairy industry from start to finish. The team created a new dedicated laydown space to accommodate rebar and other steel products used to build barns and equipment for the large dairy farms in the area. They also store and transload powdered milk and cheese, and components for consumer dairy product packaging, like bags and containers. They also cross-dock frozen butter, moving it directly from inbound trucks to outbound railcars.
“It all kind of ties into and centers around the cow,” Lindsey said. “What’s changed is that it’s less a perishable warehouse and more of a total Watco warehouse. We can handle almost anything. The entire team in Southern Idaho has done a great job adapting and serving the changing needs of our customers.”
click to play video to learn more about rail safety
Make Plans for Rail Safety Week
At Watco, nothing is more important than safety. Each fall in the United States, we have a significant reminder of this: Rail Safety Week.
The observance is sponsored by Operation Lifesaver, Inc. (OLI), a national nonprofit dedicated to rail safety. Rail Safety Week this year starts September 18. Watco leaders encourage all locations to plan events as reminders to stop and think when around the tracks.
“Rail safety isn’t just about the people working at a railroad,” said Vice President of Safety Brad Walker. “It’s about all of us. We want everyone to use Rail Safety Week as a time to think about safe practices. The week is for our railroads, but it’s also for our switching teams, terminal teams, office teams – everybody at Watco and their families.”
OLI provides themes for each day of Rail Safety Week that Watco teams can use to spark ideas. The overall 2023 theme is “Stop Track Tragedies.”
A suggested topic for September 22 is “Wear Red for Rail Safety.” That’s what’s planned at the office in Overland Park, Kansas. Team members there will gather with team members from the Kaw River Railroad, based in nearby Kansas City, Kansas. The event will feature safety discussions, with an emphasis on grade crossing safety.
Other ideas for rail safety awareness:
• Host a law enforcement officer on board your train. Railroads often have “Officer on a Train” events during Safety Week to give officers a view from the cab. It’s an opportunity for information exchange and for state troopers or local police to potentially see safety violations, especially at grade crossings, in real time.
• Go to the OLI site to complete rail safety pledges, and then download and print certificates of completion. “There’s a certificate for kids, so it’s a good exercise for families,” Walker said.
• Adult Pledge
• Kid Pledge
What is your site doing for Rail Safety Week? Will you have an officer on a train? Send your information and photos to marketing@watco.com so we can share them in Watco communications channels.

Help for Tobacco Users

So, you or someone in your family is ready to call it quits and abandon a tobacco habit.
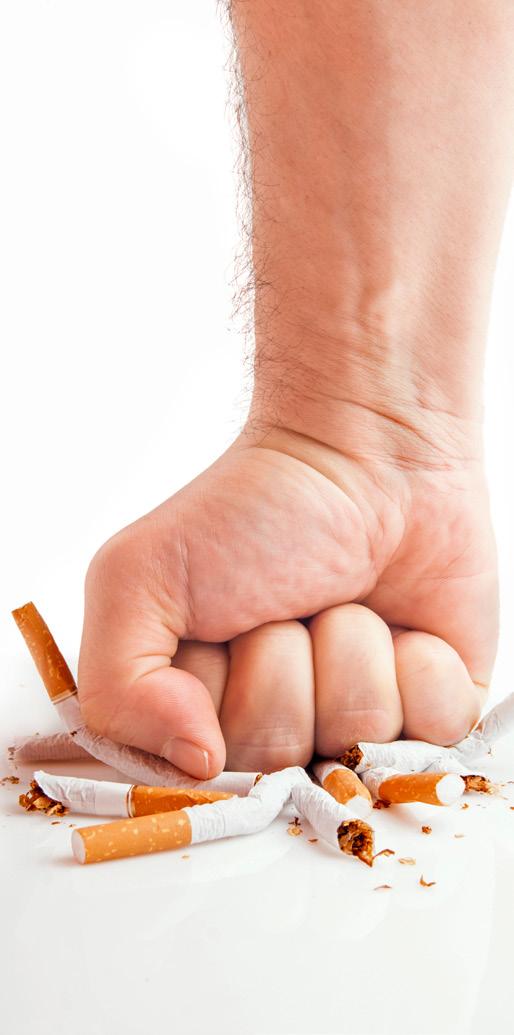
Well, Watco provides a free tobacco cessation program through Quit for Life® (QFL). It’s available to team members and their family members 18 or older who are covered under either of Watco’s medical plans.
QFL is for anyone who smokes, chews, or vapes tobacco products. QFL resources include phone coaching sessions to map out a plan for quitting, medications to help reduce nicotine cravings, and a website for tracking progress and connecting with others who are trying to quit.
Team members who are tobacco users but wish to pay the non-tobacco premiums in 2024 will need to enroll in QFL before December 31, 2023. Failure to do so could result in your premiums increasing by as much as $5 to $25 per paycheck
If you’ve ever tried unsuccessfully, don’t give up. Try QFL. According to QFL, your chances of quitting successfully – “for life” – are eight times better following the program than going it alone.
Anyone who’s ready to break up with tobacco can reach out to Quit for Life at (866) 784-8454 or quitnow.net.