
8 minute read
Ingrijpende automatisatie bij Witzenmann
from Lastechniek 2 - 2022
by online-mbm
THEMA
Ingrijpende automatisering bij Witzenmann
Inspelen op toekomstige uitdaging op de arbeidsmarkt
Door de krapte op de arbeidsmarkt heeft lasspecialist Witzenmann uit het Belgische Ranst besloten om de productie vergaand te automatisering. Omdat er veel stukgoed en kleine series gelast worden, is dat een hele puzzel. Een lasrobot, een orbitale lascel en twee cobots vormen belangrijke stukjes in deze puzzel. Voor het automatiseringproces werd een speciaal team opgericht met lasingenieur Tom Vandenwijngaert aan het hoofd. door Jerom Rozendaal Er is bewust voor gekozen om deze inspanningen nu onder verantwoordelijkheid van een team te brengen
Witzenmann is een lasbedrijf met hoofdkantoor in Pforzheim, Duitsland en vestigingen over de hele wereld dat allerhanden leidingstukken produceert. De helft van de omzet wereldwijd wordt gegenereerd in de automotive waar het maakbedrijf vooral bekend staat om haar ontkoppelingselementen, het onderdeel tussen uitlaat en motor dat de trillingen van de motor dempt. ‘In België doen we echter niets voor de automotive’, vertelt Tom Vandenwijngaert, lasingenieur en hoofd van de nieuwe divisie automatisering van het bedrijf. ‘We doen op uitlaatvlak wel wat voor bus- en landmachinebouwers, maar het gros van onze klanten zijn industriële klanten die een product van A naar Z willen vervoeren. We maken de leidingen en bijbehorende flenzen en socketten die nodig zijn voor de aansluiting.’
Stukgoed en kleine serie
De producten die uit de werkplaats van Witzenmann in België vertrekken, zijn op maat van de klant gemaakt. ‘De meeste producten worden in een range van 0 tot 40 exemplaren gemaakt’, vervolgt Vandenwijngaert volgens wie deze pluriformiteit een automatisering niet in de weg staat. ‘We maken wel duizenden verschillende items, maar producten liggen in bepaalde productfamilies waardoor automatisering mogelijk is.’ De opdeling van de fabriek is in lijn met de drie hoofactiviteiten die uitgevoerd worden. Een afdeling legt zich toe op het buigen van leidingen, de andere divisie verlast de starre buizen leidingsystemenen in een derde afdeling worden metalen slangen voorbereid en afgelast. De lasvoorbereiding van de flexibele metalen slangen gaat volgens een uniek recept waarvan Witzenmann alleen de ingrediënten kent. De lasspecialist heeft 160 mensen om de loonlijst staan in België, waarvan 120 productiemedewerkers en zo’n 40 lassers. De lassers doen hun werk in afgeschermde lascellen waarvan het bedrijf er ongeveer 20 heeft. Lichtstraten in het dak zorgen voor veel natuurlijk licht en creëren een optimale werkomstandigheden. ‘Dankzij een combinatie van een goede puntafzuiging en een algemene afzuiging blijven er ook geen lasdampen in de werkplaats hangen’, vult Vandenwijngaert aan.
Automatiseringsteam opgezet
Vandenwijngaert (38) voerde jarenlang de divisie kwaliteitscontrole en lastoezicht aan. Sinds dit jaar prijkt er ‘projectleider automatisatie’ op zijn visitekaartje. ‘Voorheen werden er door het hele bedrijf verschillende automatiseringsprojecten uitgevoerd, maar er is bewust voor gekozen om deze
Onderdeel in de lasrobot
komt juist van de orbitale lascel waar het schroef-
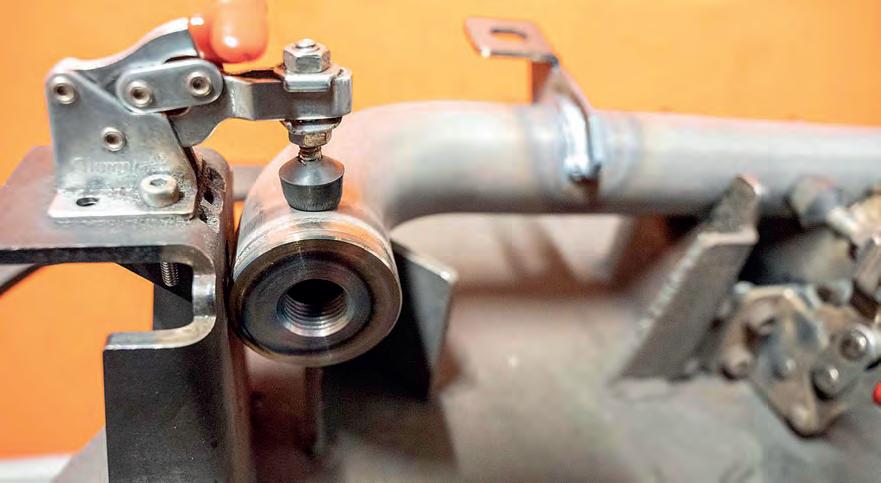
THEMA
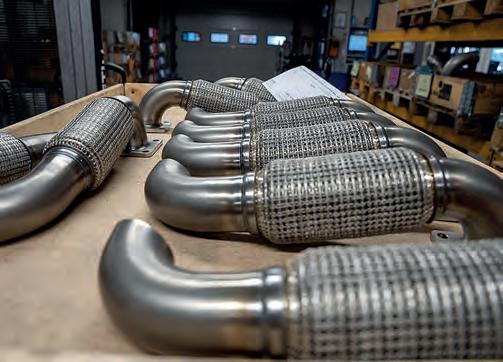
Combinatie flexibele en starre buis. Flexibele buizen worden door de hoofdvestiging van Witzenmann in Duitsland geproduceerd.
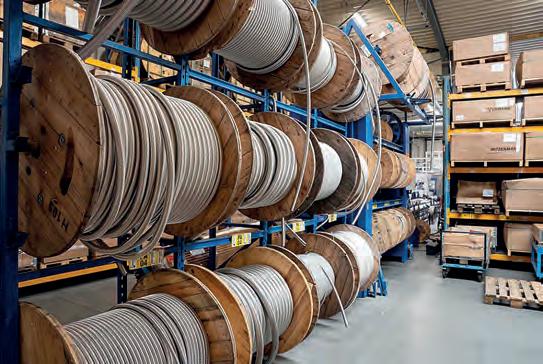
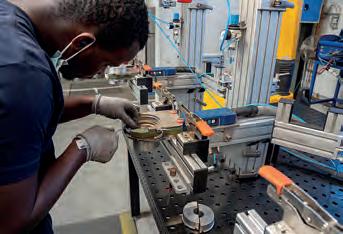
Medewerker prepareert de orbitale laskop.
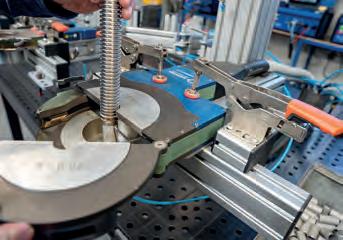
Orbitale lasinstallatie als onderdeel automatisatie
lasproces. inspanningen nu onder verantwoordelijkheid van een team te brengen. Zo is onze divisie dit jaar opgericht.’ Met het nieuwe team wil Witzenmann de automatisering binnen het bedrijf opvoeren. Binnen vijf jaar moeten 90 procent van de lasnaden automatisch gelegd worden. Nu ligt dat rond de 50 procent voor flexibele buizen en 20 procent voor de starre buizen. De automatiseringsnoodzaak kwam 2018 voor het eerst ter sprake toen het bedrijf zeer goed draaide maar in de groei geremd werd door het gebrek aan geschikte lassers. ‘Ook andere metaalspecialisten zijn lastig te vinden, maar deze kunnen makkelijker opgeleid worden waardoor het iets makkelijker werven is’, vertelt de projectleider. Hij noemt het voorbeeld van een iemand die een carrièreswitch maakt. ‘Een werkzoekende, bijvoorbeeld een bakker met het nodige boerenverstand, feeling met de sector en vooral een sterke motivatie, kan intern opgeleid worden tot metaalbewerker. Als een bakker zich bij ons aandient om zich tot lasser om te vormen, dan zullen we hem niet aannemen. Lassen vergt veel meer voorkennis. Om deze zelf op te leiden is niet haalbaar.’
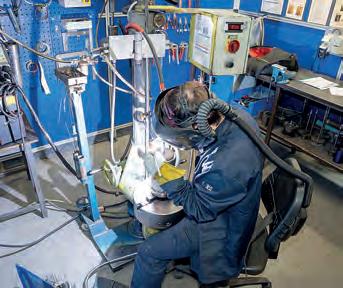
Opschaling door automatisering
Alhoewel het nijpende personeelstekort sinds de coronacrisis wat verminderd is, omdat het bedrijf een kleine terugval van 12 procent in het werk kende, verwacht men in de nabije toekomst weer tegen hetzelfde probleem aan te lopen. Automatisering moet dan het antwoord bieden. ‘Maar automatisering betekent niet dat wij streven naar minder lassers, het betekent vooral dat wij zo kunnen opschalen.’ Het automatiseringsproces valt in een aantal elementen uiteen. Als eerste wordt de lasrobot, die al in 2018 werd aangeschaft, vaker ingezet. Waar deze eerst een shift per dag draaide, doet hij er nu drie. Het tweede instrument dat in de strijd werd gegooid, was de orbitale lasinstallaties. ‘Dit is echter een vorm van semi-automatisering, maar beter geschikt voor ons kleine seriewerk’, vertelt Vandenwijngaert die vorig jaar zeven toestellen in gebruik nam. Zes van de zeven nieuwkomers staan in een productiecel en worden door één operator bediend, terwijl de zevende wordt gebruikt voor enginering en onderzoek. Volgens de planning komen er dit jaar één of twee koppen bij waarmee de productiecel zijn maximum van acht bereikt heeft. Vandenwijngaert geeft aan dat de orbitale lasinstallatie de lassnelheid een enorme boost heeft gegeven. ‘De efficiëntieverbetering is duidelijk aanwezig en noodzakelijk om onze concurrentie positie te verstevigen, maar een deel van deze winst bij het lassen moet geïnvesteerd worden in een nauwkeurigere voorbereiding.’
Langere voorbereidingstijd nodig
Deze langere voorbereidingstijd bestaat onder andere uit een nauwkeurige voorbewerking van het te lassen materiaal. ‘Manueel kunnen afwijkingen makkelijk gecorrigeerd worden van enkele millimeters, maar bij de orbitale lasinstallaties is dit beperkt tot tienden van millimeters.’ Dit vergt volgens hem ook een mentaliteitsverandering bij de voorbereiders. ‘Zij moeten niet langer materiaal afleveren met in het achterhoofd dat de lasser zijn plan wel trekt.’ Deze mentaliteitsaanpassing is binnen het hele bedrijf vereist en vergt maatwerk. Sommige handlassers weigeren zich met een (semi) automatische installatie te werken.
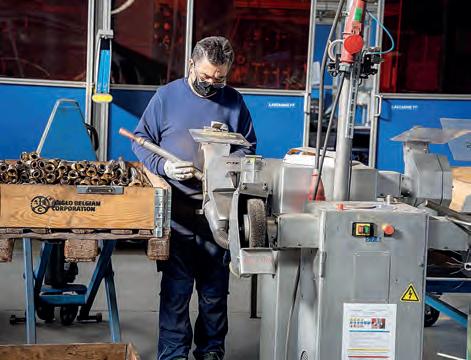
Bewerking gelaste flexibele buizen. Lasmallen in automatische lean lift waarvan er twee geïnstalleerd zijn sinds kort.
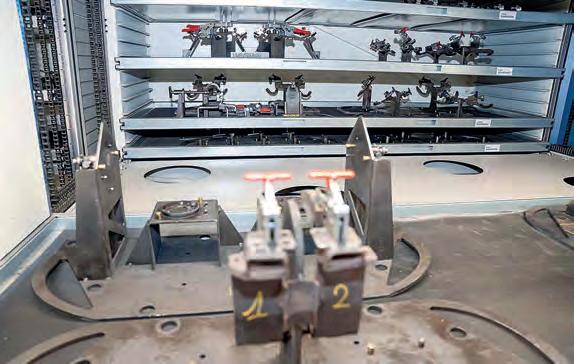
‘Ook prima. Dat is geen enkel probleem. Er zal altijd genoeg handlasarbeid blijven’, benadrukt de teamleider die aangeeft dat andere lassers juist weer graag meewerken aan automatisering. Leeftijd is hierbij niet leidend. Hij vervolgt: ‘Ons laswerk vindt veelal plaats op één en dezelfde locatie waarbij er weinig beweging is en de lasser vaak lange tijd dezelfde houding aanneemt. Dat is niet altijd even ergonomisch. Zo hebben we een medewerker met rugklachten overgeheveld naar de cobot en daarmee zijn rugklachten opgelost.’
Betere kwaliteit en arbeidsomstandigheden
Een verbetering van de ergonomie is een andere uitvloeisel van automatisering. Dat geldt ook voor de efficiëntieverbetering. ‘Dat zijn aangename bijkomstigheden, maar het was aanvankelijk echt te doen om het arbeidsprobleem op te vangen’, herhaalt Vandenwijngaert die eraan toevoegt dat ook de kwaliteit van het laswerk is toegenomen. ‘Er is vooral meer uniformiteit ontstaan.’ Vlakbij de orbitale productiecel staat een cobot opgesteld die bestemd is voor half automatisch laswerk. Dit is het derde instrument in automatiseringsproces van Witzenmann. ‘Hier worden de flexibele buizen met grote diameters onder andere gelast’, vertelt de lasingenieur. De cobotarm is van Universal Robots en de bijbehorende draaitafel werd ontwikkeld door een machinebouwer in Duitsland. Nog dit jaar staat de levering van een twee cobot op de planning.
Aanpassing productieproces
Terwijl de instrumenten voor automatisering aanwezig zijn, moet er nu naast de mentaliteitsverandering vooral gewerkt worden aan een aanpassing van het productieproces. De automatiseringsengineers onderzoeken hoe bestaande ontwerpen aangepast kunnen worden zodat automatisch lassen mogelijk wordt. Bestaande stukken gaan met andere woorden opnieuw op de tekentafel. Het team van Vandenwijngaert bekijkt hoe productfamilies te groeperen zijn, zodat automatisering überhaupt mogelijk is. ‘De meeste stukken hebben een unieke geometrie, maar de lasnaad voor sommige productgroepen is wel identiek is. Deze stukken kunnen allemaal in hetzelfde lasprogramma gelast worden’, legt hij uit om vervolgens enkele voorbeelden te geven. ‘Sommige stukken hebben bijvoorbeeld een langer flexibel gedeelte, of de geplooide, starre buis is iets langer, of de socket zit op een andere plaats.’ Parallel aan het automatiseringsklaar maken van bestaande stukken, zullen de customer engineers, die verzoeken van klanten binnenkrijgen, ontwerpen zo vorm geven dat deze met de nieuwe productietechnieken vervaardigd kunnen worden. Door de complexiteit en pluriformiteit van de stukken is het automatiseringsproces bij Witzenmann niet voor vandaag of morgen, maar een project van de lange adem.
Volledige automatisering op termijn
Daarbij staat ook niet alleen een automatisering van het lasproces op het programma. ‘Dat heeft aanvankelijk wel prioriteit omdat dit onze belangrijkste activiteit is. Maar op termijn willen we ook andere activiteiten en afdelingen verder automatiseren’, vertelt het hoofd automatisering. Zo werd recent ook de interne logistiek door een externe firma aan een analyse onderworpen met het oog op automatisering. Mogelijk dat er over enkele jaren AGV’s rondrijden of Lean Lifts mallen, onderdelen en halffabricaten uit het magazijn halen. ‘Maar misschien gaan we de logistiek ook uitbesteden zodat we meer ruimte krijgen voor productie’, zegt Vandenwijngaert. De 38-jarige Vlaming geeft aan dat het automatiseringproces bij Witzenmann in België niet op zich staat. ‘We zijn het laboratorium voor de hele groep. We onderzoeken hoe sommige productie-eenheden, die bijvoorbeeld in ons Italiaanse filiaal gemaakt worden, automatisch gelast kunnen worden.’