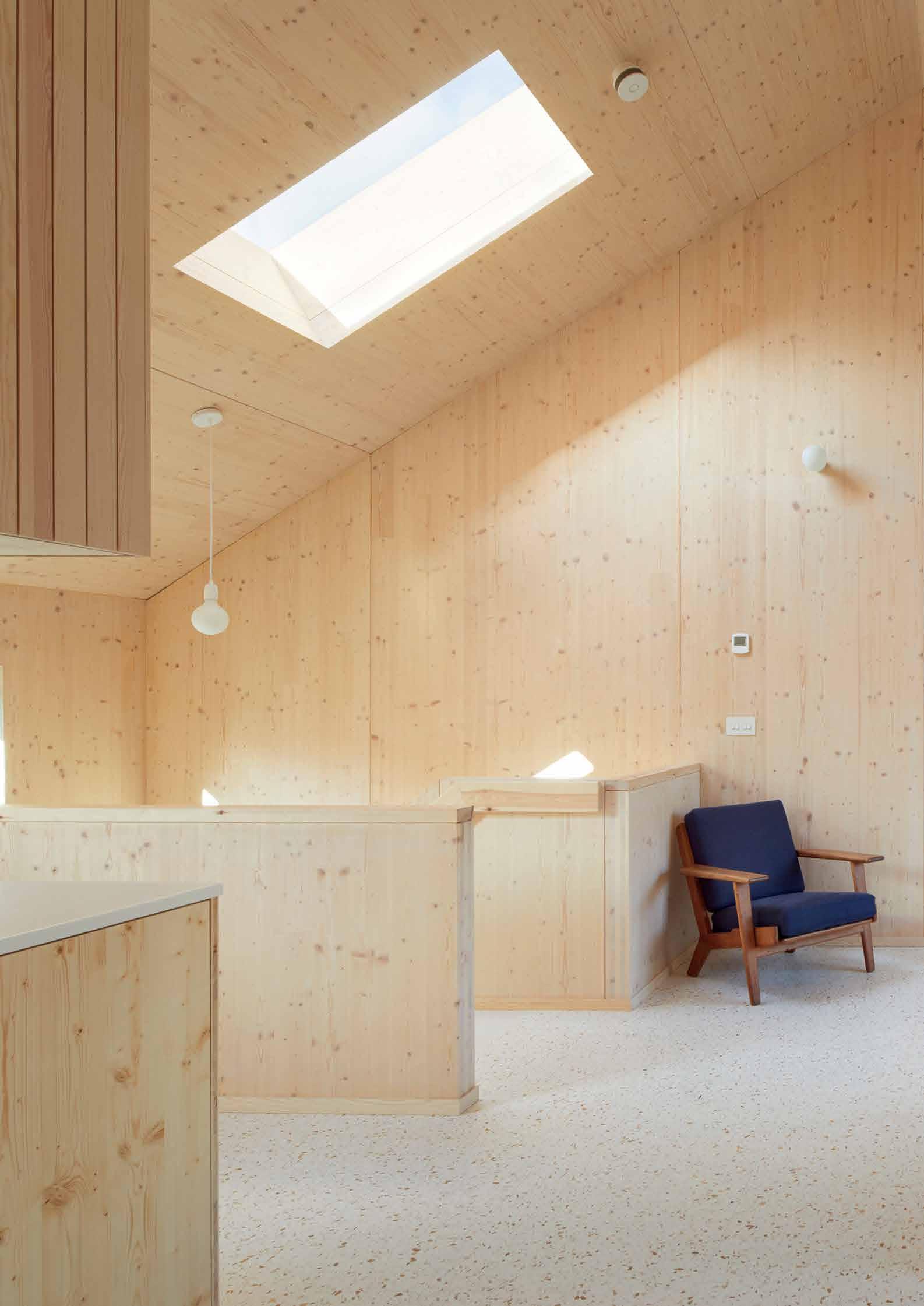
6 minute read
Wood Awards winner: The Rye Apartments
Outstanding and sustainable new homes
Winning both the Gold Award and the Private Award in the 2020 Wood Awards, The Rye Apartments showcase how timber can be used to create efficient, high-quality and low-carbon buildings.
Facing Peckham Rye Park in South London is a new development of ten apartments which demonstrate how the use of timber can create homes that are sustainable, efficient to build and with interior spaces of exceptional quality. The apartments have a structure of cross-laminated timber (CLT) which is exposed on the internal walls of the apartments, creating warm and tactile interiors filled with light from generous windows.
Tikari Works acted as architect and – unusually – as both client and main contractor for the project. Practice partners Ty and Nicola Tikari had previously acted as client, developer and main contractor for their own home, the award-winning Pocket House, subject of a TRADA Case Study in July 2020.
The project
The practice acquired the prominent corner site, containing a dilapidated two-storey building and four garages, with the intention to create, as the architect explains: ‘exciting, sustainable homes full of detail, craft and delight. The project was driven by two key considerations – how to design spaces which resisted standardised or default positions within housing design, and how to create an efficient building with the minimum amount of material, embodied carbon and cost. To this end, the choice of timber as a primary material within the project was key to achieving these objectives.’
The ten apartments are set in two blocks, one of three storeys and one of four storeys, which face each other on a corner site opposite the popular park. Red brick Victorian houses and larger apartment buildings lie alongside, and the two blocks relate to this neighbouring context in form and scale. They are clad with red clay shingles that reflect the colour and texture of adjoining brickwork yet, because they extend seamlessly over both walls and roof, the shingles create an urban composition that appears both new and familiar. A concrete plinth at the base resolves changes in level and encloses bin and bike stores. >>
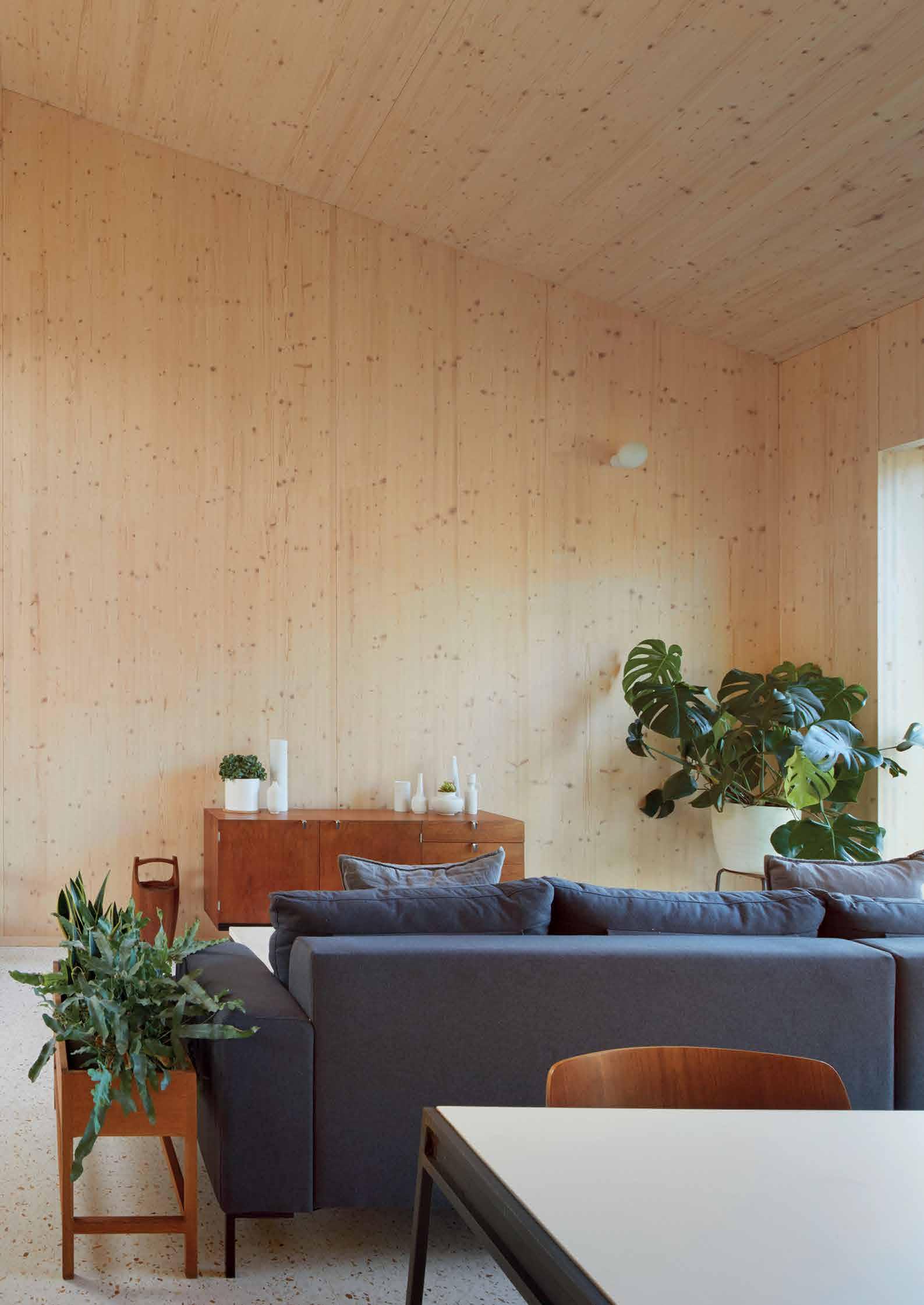
2020 Wood Awards winner The Rye Apartments
Completion date: March 2020
Building type: Apartments Location: Peckham Rye, South London Architect and client: Tikari Works Structural engineer: Webb Yates Engineers Main contractor: Tikari Works CLT subcontractor: Eurban Timber supplier: Stora Enso, Binderholz Timber elements: Structure, walls and roof, staircases and lift shafts, floors and interior fittings Timber species: PEFC-certified Austrian spruce
Photo: Jack Hobhouse
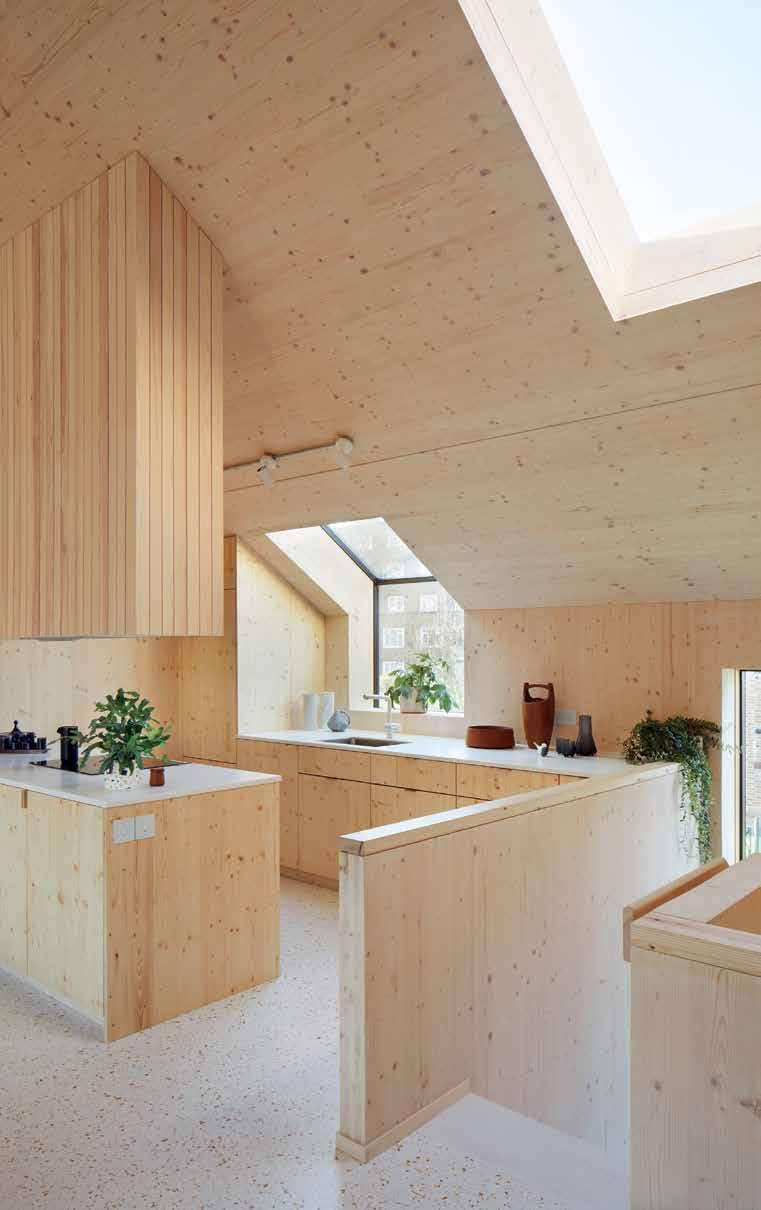
The accommodation ranges from one-bedroom apartments with garden plots in the space between the blocks, twobedroom apartments with terraces facing the park and three-bedroom two-storey apartments on the upper floors and within the pitched roof spaces; the rooms open out to terraces on both sides.
The timber structure
Richard Mayo, structural engineer and associate at Webb Yates Engineers, describes the structure: ‘The use of CLT as the primary superstructure material had a number of benefits for the scheme. It enabled us to take advantage of its lightweight nature and provide a reduced foundation scheme which wouldn’t have been achievable with a heavier structure. The construction programme of the superstructure was also very short, with each block being built in a couple of weeks using a mobile crane positioned between the blocks to lift all the panels into place.
With the sloping topography of the site, the concept design was to use a concrete substructure to provide a ground slab and external retaining walls. These walls were then used as a plinth for the superstructure to launch the perimeter CLT walls above ground, with internal CLT walls extending down to ground floor. The concrete faces have been left exposed which provide an aesthetic contrast with the also exposed CLT walls and soffits.
The internal layouts and geometry of the two apartment blocks enabled the CLT to be used in an efficient way with a clear primary span between the perimeter walls and the spine/party wall, while the internal walls within the apartments were also used as loadbearing and provided additional support to the floor panels. This resulted in 200mmthick floor panels and 100mm-thick wall panels throughout both blocks. The apartment layouts also gave an opportunity to show how CLT can be used effectively with changing floor plans either by utilising the walls as deep beams, or with light transfer framing. Where transfer structures were required, the use of glulam beams and columns was prioritised, and working with Tikari Works we developed a design solution to suit each apartment
which incorporated these elements into the internal walls to avoid compromising the spaces with additional structure.
As a result of the use of CLT, the primary structure has a net negative embodied carbon with the sequestered carbon in the timber offsetting the amount of carbon produced for the materials used in the substructure and superstructure.’
The design of the interior spaces
The apartments’ interiors are designed to be clean and simple, using a limited palette of natural materials to minimise visual clutter and create spaces that act as a backdrop to furniture and daily life. Internal walls, ceilings and staircases are all of visual quality spruce CLT. The internal walls and ceiling surfaces were treated with a site-applied coating that achieves Class 1 and Class 0 fire resistance and spread of flame; it has a 10% white tint to prevent the timber yellowing over time due to UV light.
The CLT floor panels – which are exposed on the underside as the ceiling of the apartment below – are overlaid with underfloor heating and floating floors for acoustic deadening between apartments. The floors are finished with white-lacquered ash boards and terrazzo tiles. Bathrooms and halls are floored with red quarry tiles and services are housed in dropped ceilings lined with delicate spruce timber strips. Other services were co-ordinated into pre-routed channels in the prefabricated CLT structure or routed within the floor space.

Within the timber-lined living spaces are cupboards, shelves, cooker hoods and kitchen units made of CNC grooved 18mm three-layer spruce ply boards and worktops made from recycled paper.
The apartments on ground and first floors are divided by the staircase/lift core and by a central CLT party wall comprising twin 100mm CLT wall panels; the air gap between them is filled with a mineral wool acoustic barrier.
Sustainability
The extensive use of timber as a renewable resource and carbon store was a key consideration in minimising the embodied carbon of the development, allowing the building to satisfy cradle-to-cradle principles of sustainability. A total of 227 tonnes of carbon dioxide has been removed from the atmosphere and stored in the timber structure over its lifetime. The length of time required to grow the same timber again in the Austrian forest is less than two minutes.
The thermally efficient ‘fabric first’ CLT superstructure is close to Passive House standards of airtightness; this was achieved by careful detailing and rigorous management on site by the in-house design and construction team. The CLT frame is wrapped with 150mm of non-toxic and non-combustible mineral wool insulation overclad with the rainscreen of red masonry shingles. The use of CLT prefabricated components reduced construction time, minimised waste and enabled dry construction techniques to be used extensively.
In addition to the use of timber, energy-saving features include photovoltaic panels, whole-house heat recovery mechanical ventilation and high-performance solar control glazing, all set within a highly airtight envelope. n
Awards
RIBA London Regional Award 2020 – Shortlist Wood Awards 2020 – Gold Award and Private Winner
New London Architecture Environmental Prize 2020
– Highly commended Structural Timber Awards 2020 – Private Housing Project of the Year Shortlist
Further information
For further information and to download the complete case study, go to www.trada.co.uk/casestudies