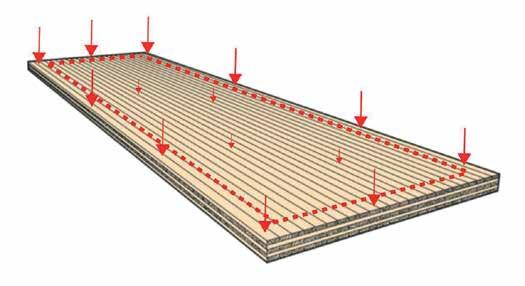
8 minute read
Moisture management
Nick Clifford and Lewis Taylor reflect on lessons learned through consultancy work on the importance of accounting for timber’s hygroscopic properties when building with engineered timber.
Modular timber building products such as crosslaminated timber (CLT), structural insulated panels (SIPs) and closed panel timber frame cassettes offer significant time savings during construction. Compared to steel, masonry or concrete buildings, the primary structure can be erected quickly using prefabricated or modular timber systems. However, these non-timber forms of construction are largely unaffected when exposed to the prevailing weather unlike prefabricated timber building systems that can absorb and retain rainwater due to timber’s hygroscopic properties.
Once the building is complete, timber components will dry out due to these same hygroscopic properties, but if they are enclosed at a very high moisture content, drying can take a sufficiently long period of time that fungal decay becomes a risk. A greater consideration of moisture management is therefore needed for prefabricated timber building systems, starting at the design and project scheduling phase, following through to the construction site.
Through BM TRADA’s consultancy work, we have been involved in several projects where ineffective planning and moisture management has led to time-consuming and expensive drying works during construction and defects in newly completed buildings. These types of defects can undermine confidence in timber building systems.
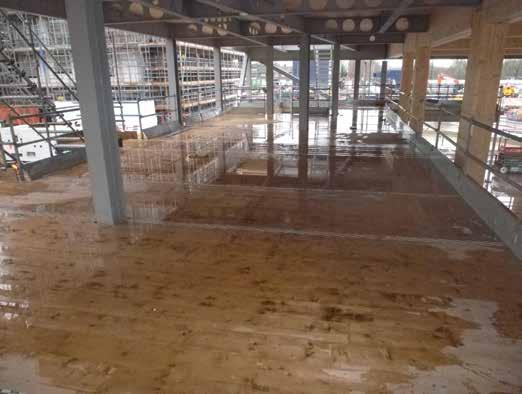
Moisture uptake is much greater at panel perimeters than across the surface. Moisture assessments should focus on the higher risk zones.
Considerations
Trapped water within pre-insulated closed panel walls and standing water on flat roofs are particularly concerning; avoiding these issues should be considered in the design, construction and phasing of timber buildings. Small buildings with short build programmes are typically low risk, but large multi-storey residential buildings and extensive commercial and education buildings are at a higher risk due to the extended nature of the build programme.
Despite closed panel timber frame walls being factory wrapped with breather membrane and vapour control membranes, there is a risk of water penetration into the panel around window openings or at the top. Traditional open-panel timber frame will also be exposed to wetting during construction, but the open nature of panels allows water to quickly drain away, drying the timbers when conditions allow. However, factory-fitted insulation and vapour control layers to closed panel kits can hold or trap moisture within the panels resulting in a greater risk of elevated timber moisture content.
Reducing risks
The risks of trapping water within wall panels can be reduced by ensuring that windows and roof coverings are installed as soon as is practicably possible once the timber structure has been erected. Robust lapping of membranes around window openings and at the top of panels can also help to reduce risks along with consideration of vertical phasing and timely engagement of follow-on trades. >>
Flat roofs can be subject to standing water during construction that can lead to excess water uptake, particularly at the edges of panels. If designing a timber building with a flat roof, it is beneficial to include a fall within the timber elements to encourage drainage during construction, rather than creating falls with insulation. Although creating falls with insulation is reasonable, the difficulty lies in the time between installing horizontal panels and installing insulation and waterproofing. Depending on the size of the building and handover procedure, this period can extend for weeks and in some cases months, resulting in prolonged exposure to standing water. Improved project scheduling can reduce this time, but it may be difficult to achieve a scenario where flat roofs are insulated and waterproofed in rapid succession after panels are installed and it is therefore important to ensure on-site moisture management. Most timber panel manufacturers and suppliers increasingly recognise the need to highlight the importance of moisture management to architects, project managers and contractors.
Best practice
Ideally, timber panels should always be protected from prolonged exposure to the prevailing weather and kept free of standing water, but given the maritime climate in the UK, complete avoidance of wetting during construction is not realistic and it is likely that moisture management planning will be needed. For example, correct lapping of membranes to walls and regular removal of standing water from flat roofs.
Moisture content readings
Water trapped within closed panel timber walls is often hidden by vapour control layers and other factory-applied finishes and is not easily detectable without taking moisture content readings within the panel. Standing water on flat roofs will eventually dry from the wind and sun but it would be a mistake to assume that roof panels are then dry; using incorrect equipment can lead to the mistaken conclusion that no residual moisture remains.
Plywood and oriented strand board (OSB) roof decks and sheathing boards are relatively thin and can be checked for moisture using the 12mm to 15mm prongs in-built to most electrical-resistance moisture meters; fully embedding the prongs will measure moisture through much of the panel thickness. However, this method is not suitable for thicker timbers such as sole plates or solid wood panels such as CLT, where residual moisture can be much deeper. Deep readings are needed to ensure that high moisture levels are not missed; proprietary hammer probes and insulated deep probes are available with measurement depths ranging from 35mm for hammer probes to insulated deep probes up to 250mm long.
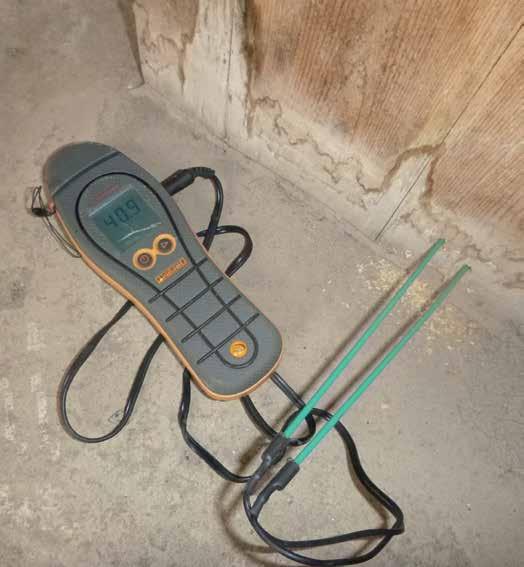
The base of vertical CLT panels can be vulnerable to moisture uptake during construction.
Metallised membranes such as reflective vapour control layers can short out the electrical resistance moisture meter pins giving artificially high readings and so insulated deep probes are normally required to ensure measurements are only taken from the timber behind.
BM TRADA consultants have seen several cases where moisture content readings taken using insufficient probe lengths and from the wrong areas have incorrectly been used as evidence that panels are dry throughout. To gather meaningful data, moisture must be measured not only with the right equipment, but also where the risk of wetting is highest. Although moisture uptake through panel faces does occur, for CLT, plywood and OSB, moisture uptake is greatest at panel edges, so the 300mm or so at horizontal panel perimeters should always be a focus in moisture checks. Sole plates and the lower 300mm of vertical or pitched panels are also higher risk zones.
Variations
Inevitably there will be times when prefabricated timber panels are exposed to prolonged wetting during construction. The effect of wetting on panel performance is dependent on panel type and grade, as well as the panel orientation and the period of exposure. BS EN 636-2 and BS EN 636-3 grade plywood should be able to withstand exposure to moisture during the construction phase and, once dry, should perform as normal. >>
OSB3, a common grade for SIPS panels and closed panel cassettes, has a reasonable resistance to construction moisture and, if swelling in thickness has been avoided (for example after short term exposure), OSB3 should perform as normal once dry. However, if swelling in thickness has occurred, the panel manufacturer should be consulted
Moisture can be held deep within CLT panels so and/or testing surface readings are insufficient and the correct equipment is required. undertaken as panel strength may be reduced. This may be of particular concern for SIPs where structural loads are taken solely by the OSB panels.

With good ventilation, relatively thin plywood, OSB or chipboard panels typically dry quickly, unless they are in contact with wet mineral wool insulation or where drying is restricted by vapour control membranes. Experience shows that CLT can take considerably longer to dry fully after exposure to construction moisture, and this drying rate may not be fast enough to avoid a decay risk by woodrotting fungi. This highlights the importance of using the right equipment to monitor moisture in CLT, which may be held deep within panels.
Drying
Where high moisture levels are identified, active in-situ drying is often the only option and this must be carried out before enclosing the panels with insulation and vapour control membranes which severely restrict drying pathways. Where factory-insulated closed panels become wet during construction, it may be necessary to remove internal vapour control layers and wet insulation to aid the drying process.
Passive ventilation with ambient air is of some benefit in warm, dry conditions, but is of little benefit in colder months – colder temperatures reduce the rate of water evaporation from the surface of the panels. Active ventilation with warm air is usually required, and drying periods of many weeks or even months are often needed to dry deeply embedded moisture in thicker timber components. Such prolonged drying periods delay project scheduling, which reinforces the importance of moisture management at all stages of design, scheduling and construction.
Conclusion
Prefabricated timber building systems, such as closed panel timber frame, SIPs and CLT, can offer considerable advantages in speed of build, cost, environmental impact, in-use energy performance and aesthetics when compared to other forms of construction. However, as higher levels of factory prefabrication occur, moisture management and care of panels during construction becomes of greater importance in ensuring contractors, clients and building users can realise these benefits.
BM TRADA encourages all parties involved with the design and construction of prefabricated timber buildings systems to take time to consider moisture management not just as an afterthought if problems arise, but as an important and beneficial exercise. If the industry is to embrace more advanced methods of off-site construction (including non-timber based off-site systems), thinking about moisture management should become a normal part of the building process. n
About the authors
Nick Clifford Senior Technical Consultant BM TRADA
Lewis Taylor Timber Frame Consultant BM TRADA
Further reading
• WIS 4-14 Moisture in timber, BM TRADA, 2019
• Cross-laminated timber: Design and performance, Revised reprint, ISBN 978-1-909594-63-0, BM TRADA, 2019
• Off-site and industrialised timber construction, 2nd edition,
ISBN 978-1-909594-81-4, BM TRADA, 2019
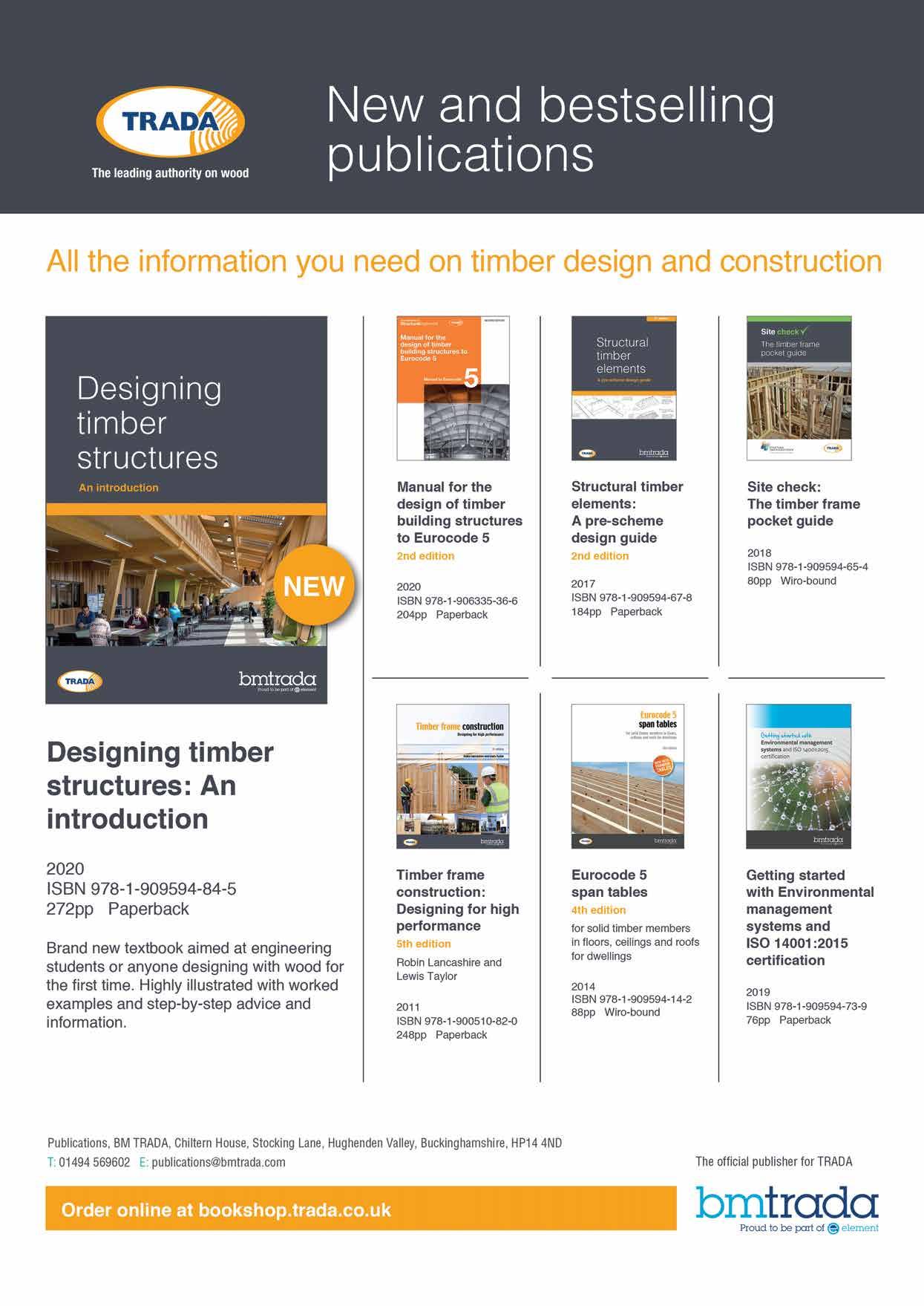