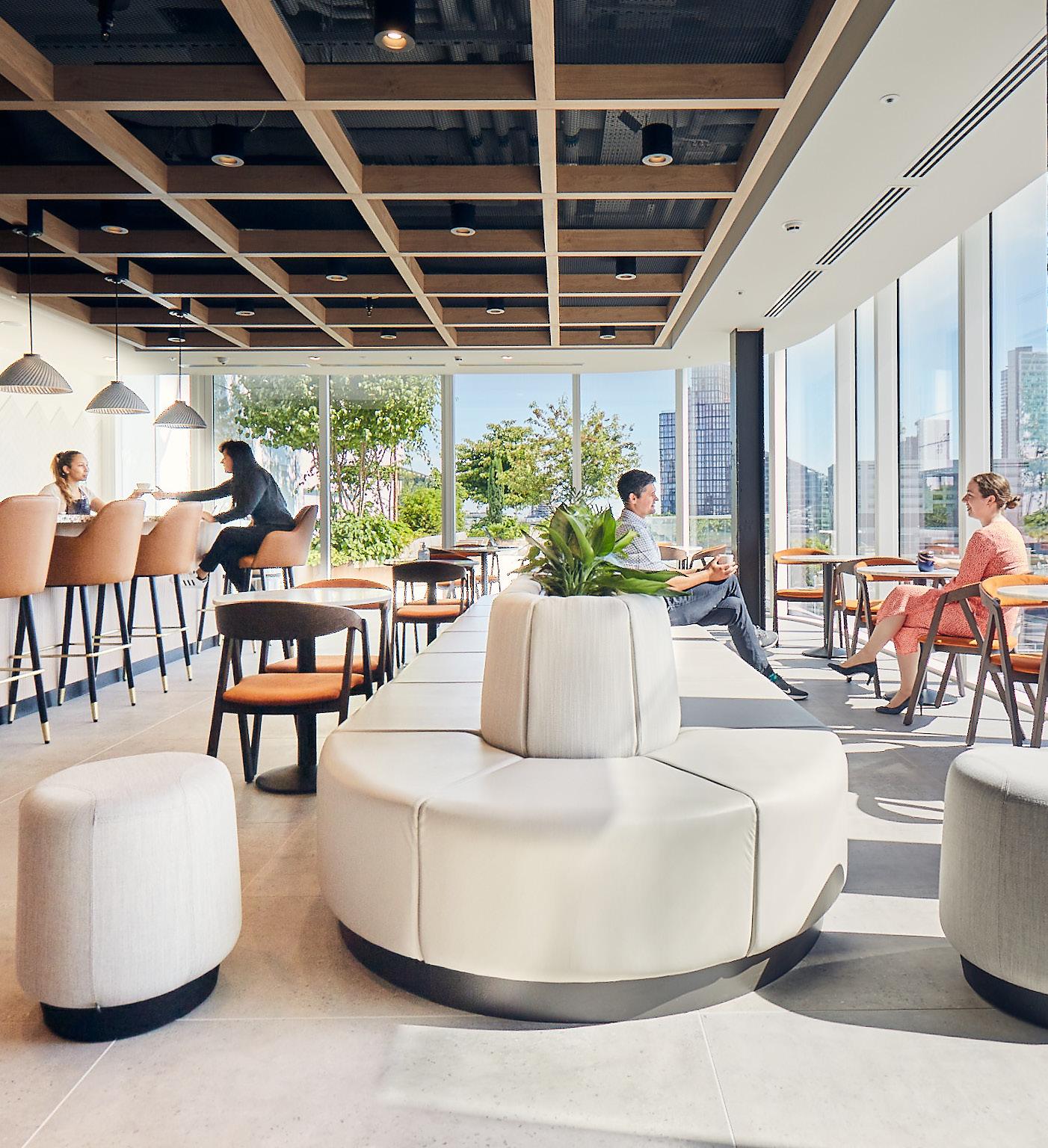
WESTERN BAINOONA GROUP
Staying up to date with the evolutions and demands of the aggregates market Transforming
Staying up to date with the evolutions and demands of the aggregates market Transforming
Africa Outlook, APAC Outlook, EME Outlook, North America Outlook, Mining Outlook, Healthcare Outlook, Manufacturing Outlook, Supply Chain Outlook, and Food & Beverage Outlook are digital publications aimed at boardroom and hands-on decision-makers, reaching an audience of more than 800,000 people around the world.
With original and exclusive content compiled by our experienced editorial team, we look to promote the latest in engaging news, industry trends and success stories from across the globe.
Your company can join the leading industry heavyweights enjoying the free exposure we provide across our platforms with a free marketing brochure, extensive social media saturation, enhanced B2B networking opportunities, and a readymade forum to attract new investment and to help you grow your business.
Visit www.outpb.com/work-with-us for details on how your company can feature for free in one of our upcoming editions.
EDITORIAL
Head of Editorial: Jack Salter jack.salter@outpb.com
Deputy Head of Editorial: Lucy Pilgrim lucy.pilgrim@outpb.com
Senior Editor: Lily Sawyer lily.sawyer@outpb.com
Editor: Ed Budds ed.budds@outpb.com
Editor: Rachel Carr rachel.carr@outpb.com
Editor: Lauren Kania lauren.kania@outpb.com
PRODUCTION
Art Director: Stephen Giles steve.giles@outpb.com
Senior Designer: Devon Collins devon.collins@outpb.com
Designer: Louisa Martin louisa.martin@outpb.com
Production Manager: Alex James alex.james@outpb.com
Digital Marketing Director: Fox Tucker fox.tucker@outpb.com
Website Content Manager: Oliver Shrouder oliver.shrouder@outpb.com
Social Media Executive: Jake Crickmore jake.crickmore@outpb.com
BUSINESS
Chief Executive Officer: Ben Weaver ben.weaver@outpb.com
Managing Director: James Mitchell james.mitchell@outpb.com
Chief Technology Officer: Nick Norris nick.norris@outpb.com
TRAINING & DEVELOPMENT DIRECTOR
Joshua Mann joshua.mann@outpb.com
DIVISIONAL DIRECTOR
Deane Anderton deane.anderton@outpb.com
BUSINESS DEVELOPMENT DIRECTOR Thomas Arnold thomas.arnold@outpb.com
HEADS OF PROJECTS
Alfie Wilson alfie.wilson@outpb.com
Eddie Clinton eddie.clinton@outpb.com Josh Rayfield josh.rayfield@outpb.com Nicholas Kernan nicholas.kernan@outpb.com
SALES & PARTNERSHIPS MANAGER Donovan Smith donovan.smith@outpb.com
PROJECTS DIRECTOR Ryan Gray ryan.gray@outpb.com
PROJECT MANAGERS Cameron Lawrence cameron.lawrence@outpb.com Kierron Rose kierron.rose@outpb.com
ADMINISTRATION
Finance Director: Suzanne Welsh suzanne.welsh@outpb.com
Finance Assistant: Suzie Kittle suzie.kittle@outpb.com
Finance Assistant: Victoria McAllister victoria.mcallister@outpb.com
EME OUTLOOK
Norvic House, 29-33 Chapelfield Road Norwich, NR2 1RP, United Kingdom
Sales: +44 (0) 1603 804 445 Editorial: +44 (0) 1603 804 431
SUBSCRIPTIONS Tel: +44 (0) 1603 804 431 jack.salter@outpb.com www.emeoutlookmag.com
Like us on Facebook: facebook.com/emeoutlook Follow us on X: @OutlookPublish
Welcome to our 62nd edition of EME Outlook magazine.
Blooming on the front cover of this issue is Peldon Rose, the leading office design and build firm transforming workplaces throughout London and beyond.
There has recently been considerable evolution when it comes to commercial offices in the UK, with the COVID-19 pandemic in particular drastically increasing freedom for employees through hybrid and remote work models.
Amid this accelerating rate of change, Peldon Rose lends its expertise to companies looking to navigate this fluctuating landscape and optimise their productivity, offering strategic insights, innovative solutions, and considerately designed spaces suited to any needs.
“Today, it’s all about cultivating experiential spaces. Businesses are interested in how we can unlock potential and bring people together to collaborate and innovate,” shares CEO, Jitesh Patel.
“Take a company experiencing a massive growth spurt and looking to recruit, for example. This is where we come in to design best-in-class spaces that enhance the employer’s profile and brand, helping it to stand out as a preferred option for potential employees.”
Elsewhere, Moravia Cans has rose to the occasion to become a leading European producer of aluminium aerosol cans.
The Czech company, based in Bojkovice, supplies almost every major aerosol brand owner and is now also diversifying into containers for adjacent markets and portfolios, such as drinking water as well as alcoholic and non-alcoholic beverages.
Martin Boaler, Managing Director, lifts the lid on how Moravia Cans is prioritising lightweight and sustainable products, investing to increase its production capacity, and revolutionising its manufacturing footprint.
Western Bainoona Group (WBG), meanwhile, has blossomed into an industryleading provider in the construction, land transportation, and crusher markets.
Having been awarded a multitude of private and public infrastructure projects, WBG has seen increased demand for the production and delivery of aggregates.
“To keep up with increased demand, WBG has invested in new quarries, production plants, and distribution centres,” informs CEO, Martin McGinty.
Complete with the latest developments from Spacemaker KSA, a regional leader in manufacturing and erecting modular buildings, we hope that you enjoy your read.
Jack Salter Head of Editorial, Outlook Publishing
Peldon Rose
Moravia Cans
A Can-Do Attitude to Aerosols
Innovative, lightweight, and sustainable aluminium aerosol cans
Western Bainoona Group
Pushing Aggregate Boundaries
Staying up to date with the evolutions and demands of the aggregates market
A BAN ON ADVERTISEMENTS for junk food in the UK will come into force in October next year under the country’s new Labour government, which will mean such content cannot air on television before the 9pm watershed.
The restrictions are intended to protect children from media exposure to unhealthy food and drinks, which have been proven to influence dietary preference from a young age.
The ban is part of a government-wide push to improve children’s overall health, which also includes a crack-down on selling high-caffeine energy drinks to under-16’s.
UK ENERGY REGULATOR, Ofgem, has recently approved three subsea power lines, known as interconnectors, between Britain, Ireland, and parts of Europe, granting the UK greater flexibility when it comes to exporting more of its surplus clean power overseas.
One interconnector will run from East Anglia to Germany, a second
DEVELOPMENT OF RAIL Baltica, an 870-kilometer high-speed, trans-Baltic railway line, continues across Estonia, Latvia, and Lithuania, connecting the countries with Poland and beyond.
Historically, passengers from the Baltics have had to change trains as they reach the Polish border due to an outdated width of railway track from the Soviet era. The new network’s use of standardised European track width will enable a seamless connection.
Meanwhile, the railway is set to significantly reduce travel times and provide countless economic and environmental benefits.
However, the costs of the ambitious project are piling up, with recent estimates at around €24 billion.
between Wales and Ireland, and a third between Scotland and Northern Ireland. Meanwhile, two additional offshore hybrid assets are set to connect the UK’s power grids with Dutch and Belgian offshore windfarms.
Whilst the country’s current interconnectors can carry around 11.7 gigawatts (GW) of electricity, the upgrade is set to incrementally increase this capacity to 12GW in 2030 and 18GW in 2032.
JUST MONTHS AFTER its UK debut, Revolut X, a crypto exchange platform aimed at professional digital currency traders, is now officially available across all 30 European Economic Area (EEA) countries, including Belgium, Cyprus, and Denmark.
In a bid to promote increased access to ‘banking without borders’, the expansion of Revolut’s crypto platform seeks to present an alternative to others across Europe, offering more than 200 cryptocurrencies and tokens for those who already hold a Revolut
BRAZILIAN PLANE MANUFACTURER, Embraer, anticipates opening a defence office in Europe following an uptick in sales of its C-390 Millennium military cargo aircraft on the continent.
In 2019, Portugal was the first European nation to purchase the C-390
bank account.
The company’s confident launch into the European crypto market builds on the success of Revolut Ramp, an in-app feature that allows users to purchase cryptocurrencies through partnerships with platforms such as MetaMask and Ledger.
Millenium, closely followed by Hungary. The most recent country to fulfill orders for the aircraft is Sweden, following the lead of its European counterparts in the Czech Republic, Austria, and the Netherlands, who opted for the model due to its notable speed and cargo capacity.
Currently, Europe represents 14 percent of global C-390 Millenium sales, whilst Embraer intends to build on this statistic as it strives to secure more orders from NATO nations.
SVEN FUHRMANN, HEAD of Group Investments at major German automotive brand, Volkswagen (VW), has reportedly resigned from the board of Northvolt, a Swedish electric vehicle and battery manufacturer.
VW’s Swedish truck brand, Scania, is known to be one of the primary buyers of Northvolt’s battery cells, whilst VW remains Northvolt’s biggest shareholder with a stake of 21 percent, according to its annual report.
Fuhrmann’s decision coincides with Northvolt scaling back and cutting jobs as the company faces ongoing funding and production issues.
Both VW and Northvolt refuse to elaborate on the impact of Fuhrmann’s resignation and are already in conversation about a possible successor.
SHELL ENERGY (SHELL), recently won a landmark court case in the Netherlands, overturning a previous ruling which required the company to reduce its carbon emissions in line with the Paris Agreement.
In 2021, Friends of the Earth, an environmental group, won its case against Shell at the District Court of the Hague, claiming the energy company had a ‘social standard of care’ to reduce its emissions by 45 percent.
Shell recently appealed this ruling and, although the Hague agreed the company had an obligation to citizens to limit emissions, it found no current recognised agreement in climate science legislating a required amount.
CEO and co-Founder of FarmERP, Sanjay Borkar, discusses the integration of innovative new technology that is driving the transformation of agriculture into a more efficient and sustainable entity
Writer:
Sanjay Borkar, CEO and co-Founder, FarmERP
The integration of technology has reshaped the agricultural value chain from seeding and harvesting to transportation and logistics, transforming the agribusiness sector. Today, artificial intelligence (AI) and machine learning (ML) are driving this transformation, empowering agribusinesses to enhance productivity, profitability, and predictability, streamline operations, and promote sustainability. From fieldwork to food safety, AI and ML optimise every stage of the agricultural process, fostering a more efficient, transparent, and environmentally responsible value chain.
One of the most impactful uses of AI and ML in agriculture is precision farming, which involves using datadriven insights to improve crop management. With AI-powered tools, farmers can monitor soil conditions, weather patterns, and crop health in real time. ML algorithms process vast datasets to predict optimal planting times, irrigation schedules, and fertilisation needs for specific crops based on factors such as climate, soil type, and crop variety.
For example, AI systems can determine precise irrigation requirements by analysing soil moisture
data collected from Internet of Things (IoT) sensors. This approach reduces water waste and ensures crops receive adequate nutrients, resulting in higher yields. Similarly, AI-powered tools can identify early signs of disease or pest infestations through image analysis from drones or cameras, enabling farmers to take preventive measures, reducing pesticide use, and minimising crop loss.
Beyond the field, these new technologies are revolutionising agricultural transportation and logistics. The efficient movement of goods from farms to processing plants or retail outlets is crucial, as inefficiencies can lead to waste, increased costs, and delays. AI optimises logistics by providing realtime data on transportation routes, vehicle conditions, and delivery schedules. ML models analyse historical data and current conditions, such as traffic and weather patterns,
to recommend the most efficient routes, reducing fuel consumption and transport costs.
AI also optimises load management, ensuring vehicles operate at full capacity, reducing empty trips, and enhancing supply chain efficiency. AI-driven predictive analytics additionally supports demand forecasting, allowing producers to adjust production and inventory levels. This helps mitigate risks of overproduction or stockouts, ensuring product availability without surplus waste.
Equally, IoT devices play a key role in automating agricultural tasks. Autonomous tractors, drones, and harvesters are deployed in fields to reduce manual labour and expedite operations. These machines can be remotely controlled and continuously monitored using IoT technology, ensuring optimal performance.
Another significant development in agriculture is the use of QR codes for food safety and traceability. By adding QR codes to packaging, agribusinesses offer consumers detailed information about a product’s origin, farming practices,
and supply chain journey. This transparency is increasingly valued as consumers demand safer and more traceable food.
Software as a service (SaaS)based enterprise resource planning (ERP) platforms are also emerging as comprehensive solutions for modern agribusinesses. These platforms incorporate AI, ML, IoT, and QR code technology, integrating every aspect of farming operations, from planting to logistics and food safety. With a single software solution,
agribusinesses manage operations more efficiently, track crop cycles, optimise inventory, streamline supply chains, and ensure regulatory compliance, all while leveraging AI to make data-driven decisions.
As agriculture continues its digital transformation, advanced technologies will play an increasingly crucial role, helping the sector meet the needs of a growing global population while minimising environmental impact.
Sanjay Borkar, CEO and co-Founder, has championed FarmERP’s mission to contribute to the UN’s Sustainable Development Goals (SDGs) of Zero Hunger and Climate Change for nearly three decades. Equipped with an Engineering degree in Computer Science from the University of Pune (India), Borkar directs his focus towards sustainability, climate resilience, traceability, and food safety.
Founded in 2019, ecofleet began as one of the UK’s few cargo bike companies with a mission to transform the logistics industry. Felipe Murua, CFO and Chief Sustainability Officer, reflects on the organisation’s commitment to providing fast, efficient, and carbon-neutral delivery services
Writer: Lily Sawyer
Dedicated to meeting the needs of businesses while contributing to a cleaner, greener future, ecofleet specialises in last-mile delivery using electric cargo bikes. Based in Chiswick, West London, it covers the majority of the city’s Zones 1 and 2.
“We offer three main solutions to our clients: same-day delivery,
next-day delivery, and dedicated rider services,” opens Felipe Murua, CFO and Chief Sustainability Officer.
The company’s diverse customer base ranges from grocery stores, e-commerce businesses, and pharmacies to wine cellars, cheese shops, florists, and more.
With new advancements in technology and artificial intelligence
(AI) coming to the fore, ecofleet is able to operate with a small but highly motivated fleet of just eight dedicated individuals.
“In this way, we are able to ensure we deliver efficient, personalised, and sustainable services to our clients,” Murua confirms.
The last-mile delivery industry in London has become highly competitive of late, with major players such as DPD, Royal Mail, and Amazon dominating the market.
However, due to a shift in customer preferences and priorities, many businesses and individuals are increasingly seeking greener and more personalised delivery solutions.
“This evolving demand has created opportunities for smaller companies like ecofleet to step in and provide tailored services that address these new expectations,” Murua points out.
The public perception of cargo bikes has also evolved significantly over time. Initially, the company’s clients were primarily e-commerce businesses and local shops, but today, it increasingly serves the health industry that has embraced this mode of logistics due to its efficiency and sustainability.
“Cargo bikes offer key advantages over traditional delivery methods, particularly in healthcare, where reliability and eco-friendliness are essential,” he elaborates.
This makes ecofleet’s bikes an ideal choice for industries that prioritise sustainability without compromising on service standards.
As the last-mile delivery industry continues to rapidly evolve, it presents an exciting space to be working in.
“The growing recognition of the value that smaller, agile companies like ecofleet bring to urban logistics is driving innovation, particularly
in green logistics solutions,” Murua excites.
As ecofleet has grown and evolved over the years, it has faced various challenges.
“When we first started, a key challenge was introducing cargo bikes as a viable logistics solution,” Murua reveals.
As many were unfamiliar with ecofleet’s concept, it invested significant efforts in educating customers on how its electric cargo bikes could meet their logistics needs in a more efficient and eco-friendly way. Five years on, customers now understand and appreciate the value of the company’s fleet.
Today, ecofleet’s challenges have shifted. Its primary concern is optimising the utilisation of its bikes to minimise downtime for riders, particularly the time spent commuting between jobs.
“To address this, we are leveraging technology to optimise routes and improve scheduling efficiencies,” he informs.
The company’s second challenge concerns fleet maintenance. As ecofleet’s service reliability hinges on the performance of its cargo bikes, regular maintenance is critical.
As such, the company has implemented a rigorous maintenance schedule and invested in training each of its team members on bike maintenance to keep the fleet running smoothly.
“By prioritising upkeep, we ensure the safety of our riders and the satisfaction of our clients,” Murua details.
A key, ongoing project of ecofleet’s involves expanding its partnerships with general practitioners (GPs)
Felipe Murua, CFO and Chief Sustainability Officer:
“Over the next 12 months, our primary goal is to solidify our position as a key player in the sustainable supply chain within the medical industry.
“We plan to strengthen our partnerships with healthcare providers, including GPs, pharmacies, and hospitals, to continue demonstrating the value of cargo bikes for efficient and eco-friendly medical deliveries.
“By focusing on this area, we aim to reinforce our role as a leader in green logistics, particularly within healthcare, and drive further adoption of sustainable delivery solutions across the sector.”
pharmacies, and hospitals. This initiative is part of the company’s broader mission to decarbonise the supply chain within the healthcare sector.
“Healthcare has unique logistical needs, and by integrating cargo bikes into the delivery process, we provide a sustainable, efficient, and reliable solution for medical deliveries,” he affirms.
Being able to provide this service is especially important to ecofleet as it enables the company to contribute to patient care whilst making a significant environmental impact.
By utilising electric cargo bikes in this way, it is able to reduce carbon emissions and improve delivery efficiency to ensure that patients receive medications and essential supplies faster and more reliably.
“This initiative underscores our commitment to innovation and sustainability, and highlights our dedication to making a positive
impact within the community,” Murua explains.
Sustainability is not just a pillar for ecofleet – it’s the very reason the company exists.
From the outset, its mission has been to provide a greener solution to the last-mile delivery industry, reducing environmental impacts through the use of electric cargo bikes and other sustainable practices.
In fact, the company sees sustainability as more than just an environmental concern but a holistic approach to doing business, which includes treating employees with respect and ensuring it has the best possible working conditions.
“Sustainability also means consistently putting our client’s needs first, delivering exceptional customer service alongside efficient, green logistics solutions,” Murua insights.
For ecofleet, sustainability is about
Dedicated rider service:
• Customers are partnered with a dedicated rider to handle their business deliveries, ensuring personalised attention and timely performance.
• Businesses are able to build strong relationships with the ecofleet’s skilled and experienced full-time employees.
• Committed to paying employees the London Living Wage, the company provides a dependable and motivated workforce.
• Clients are able to enhance their corporate image by collaborating with a B Corp-certified, eco-friendly delivery provider.
Same-day service:
• ecofleet provides the advantage of same-day delivery.
• The company provides rapid and efficient logistics with its dependable fleet of eco-friendly vehicles.
• It can boost client satisfaction by meeting increasing demands for fast delivery services.
• ecofleet offers a competitive advantage with its seamless and environmentally responsible solutions.
Planned multiple drops:
• ecofleet optimises clients’ delivery routes with its cutting-edge route planning technology.
• It minimises delivery services’ carbon footprint through effective route optimisation and eco-friendly vehicles.
• The company saves its client’s time and resources by consolidating multiple deliveries in a single trip.
• ecofleet enhances operational efficiency and reduces expenses with its well-coordinated delivery services.
making a positive impact on all fronts – environmentally, socially, and economically.
“It’s about running a business that benefits the planet, our people, and our clients, creating long-term value for all stakeholders,” he adds.
ecofleet’s unwavering commitment to social and environmental responsibility across every aspect of its operations clearly defines the business as a delivery service with a difference.
“Unlike companies that might prioritise financial success alone, we take pride in our triple bottom line approach: people, planet, and profit,” Murua sets out.
In this way, ecofleet is able to ensure that not only its own business practices benefit from its sustainable output, but so do society and the environment.
Another key differentiator is that it is the first cargo bike organisation in London to achieve EcoVadis’ Gold Medal, alongside recently becoming B Corp-certified – a milestone outlined in the company’s initial vision.
“These prestigious certifications reflect our dedication to the highest standards of social and environmental performance, accountability, and transparency,” Murua concludes. By adhering to these principles, ecofleet demonstrates how sustainability and ethical business practices are at the core of its operations, setting it apart in what has evolved to become a highly competitive industry.
ECOFLEET
Tel: +44 203 982 3266
hello@ecofleet.co.uk
ecofleet.co.uk
With the epic historical blockbuster, Gladiator 2, hitting big screens across the globe, we examine the film’s breathtaking shooting locations in Malta and analyse how its production helped boost the local construction sector
Writer: Ed Budds
As Gladiator 2 gears up for its much-anticipated European premiere on the 14th of November, the spotlight isn’t just on the star-studded cast or legendary story – it’s on the nation of Malta, and the crucial role that construction plays in making a cinematic masterpiece.
This tiny Mediterranean island, renowned for its ancient architecture and rich history, served as a central filming location for the movie, a sequel to the classic blockbuster from 2000, providing Gladiator 2 with its iconic backdrop and stunning array of breathtaking landscapes.
As such, Malta has become a primary filming location for many of Hollywood’s biggest movies over the course of the last 20 years.
The film stars a dazzling new cast,
including lead actor Paul Mescal, complemented by swashbuckling support from Pedro Pascal, Joseph Quinn, Connie Nielsen, and Hollywood royalty, Denzel Washington.
Meanwhile, director, Ridley Scott, returns once again to the aweinspiring world of Gladiator battles and Roman politics that he created a quarter of a century ago.
Gladiator 2 is another feather in Malta’s distinguished set-jetting cap, taking its place alongside other blockbuster hits that have filmed on location in the country, like Napoleon, Troy, Game of Thrones, the original Gladiator, and Jurassic World Dominion.
It is a destination that auteur director and cinematic creator of the Gladiator
franchise, Scott, has returned to several times during his storied career.
One of the landmark filming locations chosen for the shoot was the iconic and stunning Fort Ricasoli. This impressive structure is the largest fort in Malta and has been on the tentative list of UNESCO World Heritage Sites since 1998.
Most of the fort is leased to the Malta Film Commission and has been used extensively as a location for various films and TV series. In recent years, huge sets have been meticulously built within its towering walls.
Whilst a Roman amphitheatre and ancient buildings were constructed for Gladiator 2 near the shore at Fort Ricasoli, the castle itself will also play as prominent a role as it did in the original film.
Numerous enormous sets were built during production, including a one-third size Colosseum complete with complementary CGI technology.
In a world of green screens and artificial intelligence (AI), this “might be the last great build in movies”, according to co-producer, Lucy Fisher.
The star-studded cast has also praised Malta and its impressive filming locations.
“Malta is a character. You can feel the history here and it was the perfect place to shoot,” said lead actor, Denzel Washington, on the recent worldwide press tour.
“Location is everything when it comes to telling a story, and Malta is one of the best places in the world to make movies,” added co-star, Pedro Pascal.
Amongst the many jobs and roles that are required and created during the process of making a blockbuster movie, none represent such vital importance as the task that construction fulfils, from set design to stunt work.
Furthermore, large-scale film productions such as Gladiator 2 provide numerous high-profile job roles within the sector and help to
invigorate the local industry – in this case, across Malta.
As such, a construction manager is responsible for the building of sets and studios, including hiring the workforce, ensuring the safety of the crew, and interpreting the production designer’s drawings. They also manage the dismantling of sets, known as ‘striking’.
Elsewhere, a set builder creates artificial environments or scenes for the film using materials like wood, metal,
or paper. Movie sets can, of course, be built either in studios using sound stages or on location. Historical epics such as Gladiator 2 usually favour using real-world locations to enhance the sense of place and period accuracy.
Additionally, an array of standby roles are required on a movie set, including a painter, carpenter, rigger, and stagehand, who remain present on set at all times, representing their department and making modifications as needed during filming.
One final role under the diverse umbrella of construction is that of the bookings coordinator, who may be tasked with ordering and collecting art department materials, helping to build scale models, and assisting with last-minute set changes.
These many constructionrelated roles and responsibilities form the vital building blocks of production on films of such scale as Gladiator 2.
VERSATILE LOCATIONS – The island nation can easily double-up on screen as anything from Southern France to the Middle East – and everything in between.
PROVEN WORKFORCE – Malta’s English-speaking crews have worked with the biggest names in the industry and have what it takes to turn any story into a reality.
UNIQUE WATER TANK FACILITIES - Malta Film Studios offers unique infinite-horizon water tanks, suitable for large-scale special effects (SFX) and underwater shooting.
LONG HOURS OF FILM LIGHT - Malta’s climate is known as one of the best in the world and guarantees over 15 hours of film light during summer months.
England’s rugby union autumn campaign continued to capitulate in dismal despair, as Australia stunned the hosts by landing the decisive blow in a tightly contested thriller
Writer: Ed Budds
The world-class, iconic giants of southern hemisphere rugby – South Africa, New Zealand, Argentina, and Australia – are descending on the northern hemisphere this November.
The Autumn Internationals, a month-long rugby extravaganza, sees these great sides battle against the home nations of England, Ireland, Scotland, and Wales.
This festival of rugby forms an
exciting calendar highlight for the sport and gives adoring fans the chance to witness many of the world’s hottest talents live in the flesh and at the pinnacle of competition.
After a narrow loss to New Zealand in their opening fixture a week earlier, England continued their autumn run of fixtures with an agonising last-minute defeat to Australia at the home of English rugby, Twickenham.
At the end of a ferocious, gruelling match, Australia emerged as 42-37 winners against England in a thrilling battle that remained in the balance until the dying seconds.
A lively, positive start from England saw Chandler Cunningham-South secure a pair of excellent tries in the opening exchanges.
However, the Wallabies gradually clawed their way back into the first half with well-worked tries from Tom Wright and Harry Wilson. Next, a second penalty kick from Noah Lolesio propelled the Aussies into a tight 20-18 lead at the halfway point.
Responding strongly in the second period, Jeremy Williams touched down in the 50th minute to reward
Australia with a well-deserved third try and extend their lead.
Finally, the ominous Aussie momentum was extinguished when Ollie Sleightholme scored twice to get England back on the front foot and in the lead once more as the game again fluctuated in a chaotic battle of wills.
With just five minutes remaining, Andrew Kellaway collected a loose ball and powered his way to the try line for Australia’s fourth maximum score after Ben Donaldson’s successful conversion placed the visitors back into a five-point lead.
Refusing to give up the game, Maro Itoje seemingly rescued England in the 78th minute to bring the scores level, and after Smith
calmly converted, the hosts sprung into a dramatic lead with just seconds remaining on the clock.
Then, unthinkably, in the final sequence of the game, Len Ikitau silkily offloaded to Max Jorgensen who sprinted clear to score the match-winning try for a jubilant Australia.
On a Saturday evening that saw people up and down the country celebrating bonfire night, there was unfortunately a distinct lack of fireworks in the England performance, with the Twickenham crowd instead forced to once again endure a frustrating display of reoccurring frailties.
DATE: Saturday 9th November 2024
VENUE: Allianz Stadium, Twickenham
REFEREE: Ben O’Keeffe (New Zealand)
ATTENDANCE: 81,329
ENGLAND 37
TRIES: Cunningham-South (2), Sleightholme (2), Itoje
CONVERSIONS: Smith (3)
PENALTIES: Smith (2)
AUSTRALIA 42
TRIES: Wright, Wilson, Williams, Kellaway, Jorgensen
CONVERSIONS: Lolesio (2), Donaldson (2)
PENALTIES: Lolesio (3)
MAN OF THE MATCH: JosephAukuso Suaalii (Australia)
The last time England conceded more than 40 points at Twickenham was during their record home defeat, 53-10 by France, during last year’s Six Nations tournament.
The Red Roses bravely engineered opportunities to win the game on multiple occasions, but with the match clock deep in the red zone, they lost control once again on a fatal final play from the Aussies, who displayed a ruthlessly clinical edge throughout, ultimately proving to be the difference between the two teams.
Despite building a promising lead of 12 points in the first quarter and finding themselves ahead with two minutes to play, the game squirmed free of England’s fragile grasp as Ikitau got away from Sleightholme, and Australia’s replacement winger, Jorgensen, gleefully charged through a wall of bodies to triumphantly score in the corner.
Harrowingly, England have now lost their last four international fixtures by excruciating points margins of five, two, seven, and one.
In the immediate fallout, England captain, Jamie George, has resisted the broad prognosis from many pundits that his team’s inability to see out matches is proof of a severe psychological glitch that must be overcome and conquered.
However, until this squad can grind through adversity and hold on to a much-needed victory, it will struggle to dispel this disturbing diagnosis.
Unfortunately, there is no respite for Steve Borthwick’s England side as South Africa are up next and present an ominous test for a team that finds itself badly out of form and lacking belief.
England will now turn their focus to the daunting prospect of taking on the current world champions, who defeated Scotland comfortably in their opening Autumn International.
Transforming workplaces throughout London and beyond, leading office design and build firm, Peldon Rose, offers strategic insights and innovative solutions to businesses looking to optimise their productivity. Jitesh Patel, CEO, discusses the company’s position within an evolving sector, its wealth of industry knowledge, and aspirations for the future
Writer: Lily Sawyer | Project Manager: Keely Story
In recent years, the UK’s design and construction industry has witnessed considerable evolution, particularly when it comes to commercial office design.
From the office cubicles popularised in the late 1990s and open-plan layouts of the mid-2000s, to hot desking and the resimercial designs seen today, the sector has never been static.
Heralding the birth of work from home and the hybrid-remote model, the COVID-19 pandemic drastically increased freedom of choice amongst workforces and accelerated the industry’s rate of change.
Leading London office design and construction company, Peldon Rose, is on hand to lend its expertise to companies looking to navigate this fluctuating landscape.
Offering considerately designed spaces tailored to suit any need, the company prides itself on providing full lifecycle real estate solutions for commercial businesses.
“As a company, we provide a response to what the market is asking for,” opens Jitesh Patel, CEO.
“Today, it’s all about cultivating experiential spaces. Businesses are interested in how we can unlock potential and bring people together to collaborate and innovate.”
In this way, Peldon Rose works with companies and corporations across London to pinpoint their business goals and develop innovative, bespoke solutions to achieve these within their office space.
“If we do our job well, we give businesses a competitive advantage,” he adds.
In a world where travelling to the office is now more of a rarity, Peldon Rose recognises the importance of providing employees with a reason to make the journey in.
“Going to work was once a chore whereas now it should be an exciting privilege,” Patel notes.
As such, the company pays heed to placemaking, which includes the integration of leisure and well-being facilities within and in proximity to the workplace alongside optimising factors such as an office’s location, acoustics, and even air quality.
“Placemaking is about providing a holistic experience for all aspects of life. We need to make sure spaces are designed to promote physical and mental health and well-being, and optimise the work-life balance,” he reflects.
“No longer is the office a place siloed for ‘work’ or ‘stress’. It can be a location for exercise, socialising, and leisure activities. That’s what placemaking is about – creating a
destination workplace with a total greater than the sum of its parts.”
To action this, Peldon Rose’s dedicated Workplace Strategy Team is on hand to help shape clients’ business narratives.
Derived from data such as demographics, growth charts, travel patterns, and time-utilisation studies, each client’s strategy is geared towards innovatively addressing their own unique business challenges through workplace design.
For example, because attracting and retaining talent can pose difficulties for growing businesses, the team devises case-by-case strategies to deliver solutions.
“Take a company experiencing a massive growth spurt and looking to recruit, for instance. This is where we come in to design best-in-class spaces that enhance the employer’s profile and brand, helping it to stand out as a preferred option for potential employees,” Patel explains.
In addition, Peldon Rose’s Landlord Business Unit (BU) works with
landlords, developers, and asset managers to reshape and reimagine their real estate to meet the needs of businesses.
“Because of our wealth of knowledge in this sector, we’re able to assist landlords in effectively repositioning their assets to make them more attractive in a modern-day environment,” he divulges.
Underpinning the Workplace Strategy Team and Landlord BU is a Furniture Consultancy BU, which delivers specialised commercial furniture solutions to each project, and a Client Focus Team that responds to the constantly changing needs of businesses.
Therefore, Peldon Rose seeks to offer a full lifecycle of services, even providing aftercare for each of its design and fitouts in the form of planned preventive maintenance (PPM).
“We don’t just want to be there if something’s gone wrong – we want to ensure that in five years’ time, the space is operating as effectively as it was on day one,” Patel clarifies.
Within a saturated industry, Peldon Rose is a consultancy-led design and construction company that sets itself apart by heavily investing in its people, processes, and products.
• Workplace strategy – The Workplace Strategy Team carries out keystone data reviews, surveys, and staff interviews to inform a feasibility report that provides clients with a clear project vision and design brief. This is followed by a test fit-out in which pros and cons of the design can be discussed, whilst a change management process manages the ‘people side’ of proposed changes.
• Design – This includes architectural, interior, and furniture design alongside visualisation of the space through innovative technology. A cost planning and programming stage allows clients to make budget decisions with complete peace of mind. Towards the end of the design process, Peldon Rose’s Engineering and Technical Teams can pass the design over to the preconstruction stage.
• Build – A streamlined, seamless, single team approach to the fit-out construction stage ensures all design, technical, and construction parameters are met, including mechanical and electrical installation.
• Everyday services – Peldon Rose’s services do not cease as soon as the project is complete. Rather, it remains a key partner, helping businesses to evolve and change over time.
“If you compare us to our top-tier competitors here in London, we are the only business that continues to actively invest in people,” he tells us.
Peldon Rose prioritises investment in its staff so that it can remain ahead of the curve and be ready for future opportunities, cultivating a distinct advantage.
As an organisation that strives towards continuous improvement, Peldon Rose also pays attention to both successes and challenges in the marketplace to inform its approach.
“When approaching new projects, we seek to add value based on our years of industry experience and knowledge of what works,” Patel informs.
This is exemplified through each recent project the company has undertaken, all of which are focused on delivering industry change through innovative solutions.
Ongoing projects in the gaming, private equity, and financial sectors, for example, include exciting, changefocused plans that will see Peldon Rose impart its expertise to major brands.
For each of these designs, clients have access to a suite of state-of-theart technologies such as 3D modelling, computer-generated imagery (CGI), and even virtual reality (VR).
“Our 3D modelling is photorealistic, so we can demonstrate project change without impacting any visual modification,” Patel excites.
Furthermore, the company’s innovative use of Matterport’s spatial mapping technology streamlines the design and planning process, enabling it to survey real estate within two weeks or less – a vast improvement on the two months this process would otherwise take.
VR, meanwhile, helps clients to understand how a space might work for them by allowing them to physically walk around it whilst being shown visuals in real-time, which often results in faster decision-making,
Securing the safety of businesses and homes since 2011, Fusion Security provide state-of the-art security products from our on-premises designs to full cloud solutions specially designed to meet any customers needs in safeguarding their workplaces or homes.
Thus, with such innovative products, Fusion Security Integration brings both integrity and experience to the industry, building an enviable legacy of excellence over the last decade. Indeed, the company continues to elevate its reputation through unmatched customer support, unparalleled product reliability and highly innovate portfolio.
0333 123 7990 sales@fusionsi.co.uk www.fusionsi.co.uk
0333 123 7989 sales@fusionlocks.co.uk www.fusionlocks.co.uk
At Fusionlocks, we align our thinking with yours
We understand that every industry has unique storage and security requirements. That’s why we offer Digilock products— designed to be compatible, flexible, and customizable to meet your specific needs. Whether you’re looking for wireless, cloud-based management systems or simple keyless retrofit solutions, Digilock is committed to safeguarding your workspace. Our mission is to provide security that stands the test of time—today, tomorrow, and long into the future. We don’t just make promises; we demonstrate our reliability every day.
With over four decades of expertise, Digilock, has built a legacy of excellence. We continue to uphold our reputation through exceptional customer support, unwavering product reliability, and a portfolio of innovative patents. Trust Digilock not only as your provider, but as a true partner in protecting what matters to you.
especially if business leaders are based in overseas headquarters.
“In short, cutting-edge technologies help us not just to improve the client experience, but speed up the process,” he surmises.
Evidently, Peldon Rose is deeply committed to its mantra of delivering exceptional everyday experiences.
Doing more than just promoting a holistic, solution-oriented approach towards real estate optimisation amongst its clients, the company seeks to do the same amongst its own workforce.
“You can have the best ideas in the business, but if you don’t have the right people or culture to deliver them, you’ve failed. Therefore, we put a lot of effort into operating our own healthy company culture,” Patel reveals.
Peldon Rose is London’s leading office design and build expert. Its team of workplace strategists and specialists create workplaces that deliver business value, while providing exceptional everyday experiences for the people who use them.
Through a bespoke end-to-end service, Peldon Rose rapidly gains an understanding of business needs then designs and delivers industry-leading solutions. Throughout the process, the team provides a consistently uplifting experience for clients and their people.
They achieve this by sparking joy, enabling purpose, inspiring belief, and building connections through the spaces and relationships created every day.
Echoing the advice and solutions it offers clients, Peldon Rose’s company culture naturally begins with its real estate, offering employees premium spaces to carry out their best work whilst also creating a sense of community and well-being.
Mental health and well-being initiatives in the office include regular puppy therapy and office massages, helping instil moments of comfort and joy throughout the working day.
“Culture is rich when people want to share experiences together, and the spaces we design allow us to do that,” he prides.
To further develop a sense of community within its own workforce, the company has introduced ‘Bring Your Passion to Peldon Rose’, a programme through which employees have organised ski trips, book clubs, marathons, and bike rides.
The company also participates in an employee engagement survey
“PLACEMAKING IS ABOUT PROVIDING A HOLISTIC EXPERIENCE FOR ALL ASPECTS OF LIFE. WE NEED TO MAKE SURE SPACES ARE DESIGNED TO PROMOTE PHYSICAL AND MENTAL HEALTH AND WELL-BEING”
– JITESH PATEL, CEO, PELDON ROSE
each year in collaboration with Great Place to Work® and has recently been voted one of the leading design and construction businesses in this category.
“Ultimately, the fabric that holds us together as a business is engagement – whether it’s the space we provide or the activities we do, it’s all about maximising our people’s well-being and collaboration.”
Looking to the future, Peldon Rose’s priority is to continue providing exceptional everyday experiences for
clients through its work in real estate, despite being faced with ongoing industry fluctuations.
“The nature of our work is always changing, as is the industry. We therefore need to ensure we are fluid and constantly evolving to continue to meet our clients’ needs,” Patel affirms.
Thus, the company seeks to recruit more young people who can learn from experienced staff, cultivating a cyclical, versatile workforce able to serve a multitude of client requirements.
“My vision is that we continue providing innovative office and real estate solutions in which a more
experienced workforce mentors and develops those that are only just entering the market,” he shares.
“Today’s young talent is tomorrow’s new horizon.”
In pursuit of innovation and education amongst its staff, Peldon Rose implements a culture of continuous learning, with a robust mentorship scheme and a physical working environment which encourages opportunities for learning and growth.
Collaboration is a cornerstone of successful learning, so its office includes communal workplaces and breakout areas dedicated to collective use. An open layout and much-loved common areas, such as the large kitchen table in the office tea point, promote learning by osmosis, as colleagues overhear each other or catch up informally.
These areas are also great levellers – having lunch and bumping elbows with the COO over a bowl of soup means that junior and senior members feel equally comfortable, valued, and approachable.
Meanwhile, working with organisations to help them integrate their own unique culture and identity to motivate their workforces remains
of utmost importance.
Reflecting on today’s business landscape, Patel notes how a closely monitored, surveillance-oriented approach to hybrid working can only result from a loss of culture, identity, and therefore motivation within a business.
“Without culture or identity, every business would be the same – just working from a different postcode,” he points out.
With a belief in upholding the highest standards of environmental, social, and governance (ESG), the company constantly strives for learning, excellence, and progress in its sustainability practices.
• Aligning with clients, Peldon Rose reduces its environmental impact by recycling and upcycling as part of its supply chain, whilst much of its projects are carbon neutral and SKA Gold accredited.
• In partnership with international sustainability certification expert, Planet Mark, Peldon Rose has pledged to reduce its annual carbon footprint by a minimum of five percent as it seeks to achieve formal carbon and social value certification.
• Supporting diversity, equity, and inclusion amongst the workforce, the company participates in initiatives such as Black History Month, Mental Health Awareness Week, International Women’s Day, and Pride Month.
Therefore, Peldon Rose’s goal is more than just developing and delivering real estate solutions – it’s cultivating a unique sense of identity for businesses.
“For us, the future is about making sure we collaborate with organisations to deliver both culture and identity through workplace design, because that’s what ultimately leads to differentiation,” he concludes.
Tel: 020 8971 7777
hello@peldonrose.com
https://www.peldonrose.com
With more than 15 years of experience, Spacemaker KSA is a leader in modular solutions across Saudi Arabia and beyond. We speak to Mohammed Amro, General Manager, to learn more about the company’s illustrious history and innovative plans for the future
Writer: Lauren Kania | Project Manager: Keely Story
Providing the highest quality solutions, ultimate customer satisfaction, and timely execution, Spacemaker KSA is a market leader in the construction industry whose vast portfolio of innovative products caters to every building demand.
Founded in 2009 as a small operation in the Kingdom of Saudi Arabia (KSA), Spacemaker KSA is proud to have grown into a leading manufacturer and erector of steel frames, modular buildings, and knock down structures in the Middle East and North Africa (MENA) region.
In the company’s early years, it operated out of a modest factory with a small team dedicated to producing prefabricated buildings.
Despite the challenges of operating in a competitive market, Spacemaker KSA’s focus on quality, attention to detail, and a customercentric approach allowed it to carve a lucrative niche in the highly fragmented KSA construction market.
The real turning point was when the company made a strategic decision to expand beyond traditional prefabricated buildings, recognising a growing demand for modular construction solutions across the wider region and investing in state-ofthe-art manufacturing technologies.
“With an eye on the future, we adopted advanced modular building manufacturing techniques, streamlining the production process, reducing waste, and improving efficiency,” opens Mohammed Amro, General Manager.
“These adaptations also allowed us to become a pioneer in sustainability, implementing green building practices and eco-friendly materials in our modular solutions.”
The company’s ability to deliver high-quality, energy-efficient buildings in record time has been a key factor in its continued success and ability to handle more complex projects whilst maintaining the high-quality standards that serve to differentiate it.
“Today, Spacemaker KSA is not just another construction company – it’s a regional leader in the manufacturing and erection of modular buildings, known for its ability to deliver fast, customised, and sustainable solutions,” prides Amro.
By embracing innovation, personalising projects, and focusing on long-term relationships, the company has consistently outperformed its competitors in terms of both client satisfaction and project delivery.
Having initially focused on prefabricated modular manufacturing servicing needs for temporary facilities within the oil and gas sector, Spacemaker KSA has worked through the combined efforts of its team to shift to a wider range of off-site construction solutions.
Today, the company boasts over 1,000 team members who offer wider solutions through four verticals – prefabricated modular, modular
buildings, pods, and mechanical, electrical, and plumbing (MEP) modular systems.
“Our commitment to speed, customisation, sustainability, and technology-driven efficiency has allowed us to carve out a niche in an otherwise crowded marketplace,” details Amro.
“Clients trust us to not only meet their construction needs but go above and beyond expectations, creating lasting value and building strong partnerships along the way.”
Having been excited by the construction industry from a young age, Amro finds that the current trends, innovations, and evolving challenges make the field both stimulating and impactful.
“I was drawn to construction techniques and knew I was destined for a career in the industry. The daily challenges keep me energised, and my passion for this field has only grown stronger as we’ve built Spacemaker KSA into what it is today,” he expands.
Having joined the company in 2011 as a founding team member bringing off-site construction technology into the region, Amro has progressed to lead a dedicated team with a vision to make Spacemaker KSA the region’s premier provider of all-inclusive offsite solutions.
“Together, we are close to reaching SAR1 billion in revenue whilst remaining committed to setting new industry standards, driving progress, and meeting the evolving needs of our clients,” he asserts.
Amro’s journey has offered him unique insights into market needs and how Spacemaker KSA can evolve to meet them, resulting in the company successfully developing innovations that have been key to its growing portfolio.
With a vision of becoming the leading supplier of modular construction solutions in the Middle East, Spacemaker KSA sets the standard for innovation, sustainability, and
excellence within the industry.
The company sees modular construction as the future of the built environment, offering unmatched flexibility, efficiency, and sustainability in the design and delivery of buildings across diverse sectors.
In such a competitive industry, Spacemaker KSA believes the best way to differentiate itself is by thinking differently, investing in
innovation, and prioritising the needs of its clients.
“It’s not just about building structures; it’s about building trust, relationships, and a legacy of excellence,” declares Amro.
The company is furthering this dedication and reputation for success through its various projects, such as NEOM and the construction of a new factory.
Mohammed Amro, General Manager: “We understand that our supply chain operations are not just a logistical function – they are the backbone of our ability to deliver high-quality modular solutions on time, within budget, and to the exact specifications of our clients.
“Our supply chain is the essential link between our design and manufacturing processes and the final product that reaches our customers. Given the scale of our modular construction operations, we rely on a global network of suppliers, manufacturers, and logistics partners who help us source high-quality materials, deliver products efficiently, and meet the stringent requirements of our construction projects.
“From steel framing to modular components and finishing materials, every part of our supply chain must work in harmony to ensure the seamless execution of our projects.”
Both of these endeavours are pivotal to the growth trajectory of Spacemaker KSA, with the former representing a rare opportunity for the company to be involved in a transformative megaproject and contribute its expertise in modular construction and steel frame solutions to help build a futuristic, sustainable city.
The new factory, meanwhile, serves as a crucial investment in the company’s manufacturing capabilities, enabling it to meet increasing demand, drive innovation, and position itself as a pioneer in the regional modular construction market.
“Together, these projects align with our vision of becoming a leader in modular solutions, enhancing our ability to deliver high-quality, sustainable buildings quickly and efficiently whilst reinforcing our commitment to supporting Saudi Vision 2030 and contributing to the economic diversification of the KSA,” expands Amro.
“TODAY, SPACEMAKER KSA IS NOT JUST ANOTHER CONSTRUCTION COMPANY – IT’S A REGIONAL LEADER IN THE MANUFACTURING AND ERECTION OF MODULAR BUILDINGS, KNOWN FOR ITS ABILITY TO DELIVER FAST, CUSTOMISED, AND SUSTAINABLE SOLUTIONS”
– MOHAMMED AMRO, GENERAL MANAGER, SPACEMAKER KSA
• 100+ satisfied clients
• 1,000+ completed projects
• 95 percent on-time delivery
Additionally, the company’s strategic geographic facility in Dammam provides a distinct advantage, as the city offers accessibility in terms of logistics that allows Spacemaker KSA to better service its project needs around the region.
Spacemaker KSA has prioritised utilising eco-friendly products since its inception, recognising the importance of implementing environmentally-friendly practices for both the longevity of the company and the people who enable it to continue to progress.
“We are dedicated to being more than just a business – we are committed to making a lasting, positive impact on the environment, society, and our workforce,” explains Amro.
“WE ARE DEDICATED TO BEING MORE THAN JUST A BUSINESS – WE ARE COMMITTED TO MAKING A LASTING, POSITIVE IMPACT ON THE ENVIRONMENT, SOCIETY, AND OUR WORKFORCE”
– MOHAMMED AMRO, GENERAL MANAGER, SPACEMAKER KSA
The company’s corporate social responsibility (CSR) initiatives reflect its values of sustainability, innovation, and integrity, which guide the company as it builds a better future for the communities it serves. Through its ongoing efforts, Spacemaker KSA aims to create longterm social value, ensure its business practices benefit future generations, and remain a responsible corporate citizen in the MENA region and beyond.
“By continuing to invest in sustainable practices, empowering people, and giving back to our neighbourhoods, we will maintain our position as a leader not just in the construction industry but in CSR,” enthuses Amro.
As the company looks ahead to a prosperous future, it is focused on expanding its market reach, continuing its innovation efforts, and strengthening its commitment to sustainability and client satisfaction.
Through strategic growth, operational excellence, and an emphasis on employee development and strong partnerships, Spacemaker KSA aims to solidify its position as a regional leader in modular construction.
“Our ultimate goal is to meet the growing demand for flexible, sustainable, and cost-effective building solutions whilst also creating value for our clients, employees, and communities,” he concludes.
As manufacturing organisations worldwide confront unprecedented change, embracing technological innovations and incorporating critical environmental sustainability agendas, now more than ever is the time to showcase the strides being taken in this dynamic sector.
A multi-channel brand, Manufacturing Outlook brings you the positive developments driven by organisations across the global manufacturing industry through its various platforms.
Discover exclusive content distributed through its website, online magazine, social media campaigns and digital dispatches, delivered straight to your inbox with a bi-weekly newsletter.
Through these compelling media channels, Manufacturing Outlook will continue to foreground the movers and shakers of the industry.
To participate as a featured company and join us in this exciting endeavour, contact one of our Project Managers today.
Moravia Cans is committed to designing and producing the most innovative, lightweight, and sustainable aluminium aerosol cans in the market. Managing Director, Martin Boaler, updates us on recent developments
Writer: Jack Salter | Project Manager: Nicholas Kernan
Since featuring Moravia Cans (Moravia) at the beginning of 2021, many significant events have impacted the development of all business environments.
The packaging and containers sector is no exception, as it has been affected by the COVID-19 pandemic and ongoing conflicts in Ukraine and the Middle East.
However, the resilience and continuity of metal packaging as a leading and increasingly sustainable solution has been remarkable, whilst Moravia’s focus on the highest specification of aluminium monobloc aerosol cans, principally for personal and home care markets, has also remained unwavering.
“We supply almost every major aerosol brand owner, plus many more local market players,” states Managing Director, Martin Boaler.
“The company is now also diversifying into containers for adjacent markets, such as drinking water, alcoholic, and non-alcoholic beverages.”
LIGHTWEIGHT PRODUCTS
Based at a single world-class manufacturing facility in Bojkovice in the southeast of the Czech Republic, Moravia has operated in its current guise for over 30 years.
The company has always been focused on the design and production of the most sustainable products in its market segment.
Lightweighting in particular has been the number one priority in Moravia’s drive to increase the sustainability of its monobloc aerosols and bottles.
“On a product-by-product basis, Moravia’s offerings have always been lighter than the competition,” acclaims Boaler.
“This has been achieved by investing in the highest capability production machinery and then further optimising this machinery through leading R&D to enable the production of complex-shaped products at the same weight and speed as standard products from our competitors.”
Wall ironing has long been adopted as part of the company’s standard impact extrusion process, enabling lower wall thickness with improved surface quality and reduced weight.
This lightweighting was further enabled by moving to proprietary
patented alloys that maintain the highest strength after required curing processes.
A significant proportion of Moravia’s production has recently been moved to the coil-fed drawn and wall-ironed (DWI) process that is usually more associated with beverage cans.
“The greater consistency of the coil input material, together with the faster and more controllable DWI production process, enables long-run specifications to be produced with increased speed and quality,” Boaler informs.
Moravia has undergone significant industrial development and increased its output volumes since we last featured the company just under four years ago.
Indeed, it has grown its production capacity by almost 20 percent in that time, which has improved efficiency by a similar amount across the whole operation.
“We will now make further changes to increase capacity and efficiency by similar additional percentages over the next two years,” outlines Boaler.
The broadening of Moravia’s
VISION – To be the most innovative and trusted aerosol can supplier to the world’s leading brands. Moravia achieves this by empowering its people to deliver product innovation at the highest level, creating sustainable value for customers and the business.
MISSION – To supply marketleading, sustainable products reliably and at the highest quality to the delight of its customers.
VALUES – Moravia’s values of openness, transparency, and trust are shared with customers and suppliers through its people. The company pursues business with integrity and honesty, as detailed in its code of business principles.
“ON A PRODUCT-BY-PRODUCT BASIS, MORAVIA’S OFFERINGS HAVE ALWAYS BEEN LIGHTER THAN THE COMPETITION” ”
– MARTIN BOALER, MANAGING DIRECTOR, MORAVIA CANS
product range to include more top consumer brands has likewise contributed to its recent growth.
“We have grown in all respects, with 30 percent being organic with existing customers across their product portfolios,” he reveals.
“The remaining 70 percent of our recent growth has come from new customers and through the development and implementation of our new products and processes.”
The company also plans to heavily invest in its production lines over the next two years, prioritising front and back-end automation.
It has already added an 11th production line, which is now running at full capacity, whilst a 12th is currently being implemented. Both of these lines are state-of-the-art
and based on Moravia’s marketleading DWI product technology. This will be a logical continuation of Moravia’s long-term capital investment strategy and revolutionise its manufacturing footprint.
“We will densify our production and concentrate this over two fewer production halls,” Boaler tells us.
“This will enable increased harmonisation of end-of-line processes between lines with improved integration into warehousing and upstream and downstream logistics.”
Additionally, the company will be retiring some outdated lines and sections of lines to enable 100 percent of its production capacity to run Moravia’s market-leading product standing in both DWI and impact
“WE BELIEVE OUR INCREASED FOCUS ON MANUFACTURING EXCELLENCE, ALLIED TO OUR CONTINUING LEADERSHIP IN R&D, CAN MOVE MONOBLOC PRODUCTS TO NEW LEVELS OF PERFORMANCE”
– MARTIN BOALER, MANAGING DIRECTOR, MORAVIA CANS
extrusion with ironing (IEI).
“Maintaining this load balancing flexibility between the two formats has been a priority to ensure the best continued alignment with the customers and market that we serve,” notes Boaler.
Moravia’s status as an industry leader is demonstrated by its EcoVadis Silver rating and long-standing ISO 9001/14001/45001 and BRC accreditations.
Complemented by other local
environmental, health, and safety (EHS) accreditations, including the company’s own ‘Vision Zero’ approach, these ‘license to operate’ necessities have focused Moravia on continuous improvement and maintaining the most exacting standards.
“We are now also fully focused on the most relevant accreditations in sustainability and have a clear action plan to move to EcoVadis Gold and beyond,” discloses Boaler.
The company has also identified the Aluminium Stewardship Initiative (ASI), CyberVadis, and Sedex as focus areas for accreditation and continuous improvement.
This is in addition to much more active participation in relevant industry-wide initiatives through Metal Packaging Europe (MPE) and the Metal Packaging Manufacturers Association (MPMA).
Operating in a highly competitive market, Moravia recognises the
need to prioritise promoting and enhancing the position and perception of metal packaging against less sustainable and capable alternatives.
The focus has always been on bringing product excellence, which has included full body shaping, to the market, with others then following suit.
“We believe our increased focus on manufacturing excellence, allied to our continuing leadership in R&D, can move monobloc products to new levels of performance,” Boaler concludes.
“Moravia has always had an exclusive focus on the aerosol market, and we are now adding other relevant adjacent portfolios to this approach.”
The next few years will see some interesting developments in aluminium monoblocs at customer, product, and consumer level, and Moravia aims to remain at the forefront of these exciting times.
Aproduct is only as good as its performance in the field. The ATMOS system, designed and manufactured by Core Systems, has been rigorously tested and deployed in some of the most challenging environments. This article explores how ATMOS is being used in real-world military and industrial applications, demonstrating its reliability and effectiveness in critical situations.
Real-World Deployment: ATMOS has been successfully deployed in various military operations, where its rugged design and reliable performance have proven indispensable. From remote field operations to highstakes missions, ATMOS has been a key component in ensuring mission success.
ATMOS has been successfully deployed in military field operations, where its rugged design has proven essential. One example is its use in remote command units, where its onboard UPS battery backup has ensured uninterrupted command and control during critical missions.
Additionally, ATMOS has been used in mobile data centers, providing reliable highperformance computing in rapidly changing environments. Feedback from users has highlighted the system’s durability and reliability under pressure.
Field Performance: The true test of any product is how it performs under pressure. ATMOS has consistently met the demands of military and industrial users, delivering reliable performance even in the most extreme conditions. Its advanced features, such as secure communication systems and enhanced durability, have made it a trusted tool in the field.
ATMOS has consistently delivered 100% uptime in some of the world’s harshest environments. Users in the military have noted that the system remained operational even during power outages and extreme temperature changes.
In industrial settings, ATMOS has performed flawlessly in conditions involving high dust levels and vibrations, such as those found in mining operations.
Case Studies: To illustrate the impact of ATMOS, we present two cases where the system has been critical to the success of military or industrial operations. These examples showcase the system’s robustness, reliability, and the strategic advantage it provides to our clients.
One case study involved the deployment of ATMOS in a remote military base, where it was used to process real-time data for battlefield decision-making. Its modular design allowed the system to scale from a single node to a full stack of five nodes, enabling real-time analytics with increased computational power.
32 Intel® Xeon® Gold Cores, 64 Total Threads per node
• 512GB DDR4 ECC RAM
• Dual 1.92TB NVME Hot-Swap
SSD Drives (OS Drives)
Dual 15.36TB NVME Hot-Swap
SSD Drives (Storage)
• NVIDIA L4 Tensor Core GPU Card
Another example is from the oil and gas sector, where ATMOS was used to control critical equipment in offshore operations, withstanding extreme weather conditions without issue.
Future Applications: As military and industrial needs evolve, so too does ATMOS. Core Systems is continuously refining and adapting the system to meet the emerging challenges of the defence sector. Whether it’s in the battlefield or in industrial environments, ATMOS is ready for the next generation of challenges.
Looking ahead, Core Systems is exploring how ATMOS can be integrated with AI-driven analytics for faster and more accurate decision-making in the field.
Enhanced cybersecurity features are also being developed to protect sensitive data during highrisk operations.
The scalability of ATMOS will also support its use in emerging fields such as space exploration and cyber defence.
It
is the long-lasting mission of Western Bainoona Group
to stay up to date with the
evolutions and demands of
the
aggregates market. We catch up with CEO, Martin McGinty, about the company’s latest projects and focus on sustainability
Writer: Lucy Pilgrim | Project Manager: Eddie Clinton
Over the past 18 months, the Middle Eastern construction industry has continued to implement greener practices.
The aggregates sector in particular has felt a pressure to provide more sustainable options across its operations, such as recycled aggregate materials.
“Many countries are investing in infrastructure, and there is also a greater demand for aggregates, especially for large-scale construction projects including roads, bridges, and housing,” introduces Martin McGinty, CEO of Western Bainoona Group (WBG), an industry-leading provider in the construction, land transportation, and crusher markets.
Since last speaking to the company in mid-2023, supply chain issues have also continued to affect the availability of machinery, transportation, and other logistics technicalities.
However, WBG has worked hard to increase and improve logistical construction efficiencies to mitigate these disruptions.
Over the past 16 months, WBG has been awarded a multitude of private and public infrastructure projects, which has resulted in increased demand for the production and delivery of aggregates, ultimately leading to a significant spike in the company’s revenue.
“To keep up with increased demand, WBG has invested in new
quarries, production plants, and distribution centres.
“Expanding our production capacity through new facilities and modernising existing ones with advanced equipment has helped our operational and production capacity,” McGinty highlights.
Indeed, the company’s investment in cutting-edge machinery and equipment has significantly improved the efficiency, safety, and environmental performance of its aggregates and infrastructure works. By adopting automation, digital technologies, and sustainable practices, WBG has been able to boost production, reduce operational costs, and meet the growing demands of large-scale infrastructure projects whilst staying competitive in a dynamic marketplace.
“These innovations not only contribute to operational excellence but also ensure long-term sustainability and growth for the company,” he adds.
WBG’s continued evolution is also granted by its vast network of supply chain operations that form the backbone of the company’s ability to deliver high-quality materials and services for infrastructure projects.
Therefore, by maintaining strong relationships with both international and local vendors, WBG ensures that it has access to the best equipment, materials, and technology, whilst mitigating potential risks from supply chain disruptions.
“These partnerships are crucial to the company’s long-term success, enabling it to remain competitive, innovative, and responsive to the demands of a dynamic and rapidly evolving industry,” McGinty affirms.
One of WBG’s long-term goals is to integrate electric vehicles (EVs) into its fleet for transporting aggregates, corresponding with the aims of the wider construction industry.
However, the implementation of this sustainable technology offers both substantial advantages and challenges for the company, as well as the aggregates sector at large.
Regarding the former, EVs have considerably lower operation costs thanks to the fact electricity is far cheaper than diesel, and electric-powered trucks require less maintenance due to having fewer moving parts.
Additionally, EV trucks use regenerative braking that not only recharges the battery but also extends brake durability in the long run.
“These vehicles are also powerful enough to tackle steep inclines and heavy loads, making them suitable for demanding construction tasks,” McGinty points out.
On the other hand, electric trucks also present certain limitations. The shorter driving range, for example, makes the vehicles less suitable for long-distance journeys.
They also require extra time for charging, leading to extended potential downtimes, whilst the need for specialised charging infrastructure and high upfront costs require significant initial investment.
Moreover, the warm weather often found in the United Arab Emirates (UAE) can impact the fleet’s battery performance, which can be affected by high temperatures and lead to overheating.
From a supplier perspective, the industry-wide adoption of electric trucks is still in its early stages.
“Establishing standardised practices with suppliers and dealers through in-depth discussions is therefore crucial for a smoother and more reliable integration process,” McGinty insights.
Although thorough trials of electric trucks have been conducted previously, additional real-world testing on construction sites is essential to fully assess their capability and effectiveness in challenging environments such as the UAE.
Throughout WBG’s history, it has been committed to empowering its employees and recognising their contributions, which has evolved to become a key factor in maintaining a motivated, engaged, and highperforming workforce.
“By investing in training, fostering a collaborative and inclusive culture, and offering opportunities for career growth and recognition, the company ensures that its staff feel valued and empowered to contribute to our success,” McGinty prides.
This strategy not only improves employee retention and satisfaction but also drives innovation and operational excellence, positioning WBG for long-term growth. The company has likewise made significant strides in its corporate social responsibility (CSR) and ESG practices over the past 12 months, focusing on carbon reduction, sustainable sourcing, community engagement, and workforce diversity.
“By embedding sustainability and social responsibility into our core business operations, WBG not only strengthens relations with stakeholders but also positions itself as a leader in driving positive and environmental change in the aggregates and infrastructure sectors,” he states.
“ELECTRIC TRUCKS CAN BE A VALUABLE INVESTMENT FOR COMPANIES AIMING FOR ECO-FRIENDLY OPERATIONS AND LONGTERM COST SAVINGS”
– MARTIN MCGINTY, CEO, WESTERN BAINOONA GROUP
“In summary, electric trucks can be a valuable investment for companies aiming for eco-friendly operations and long-term cost savings.
“However, it is important to carefully consider these sustainability benefits alongside the practical limitations to determine if they align well with the specific requirements of construction projects,” McGinty reflects.
WBG’s most recent projects include the Northern Runway Rehabilitation
at Abu Dhabi Airport, which delivered a series of significant advancements. Beyond the reinforcement and resurfacing of the runway with 210,000 tonnes of asphalt to ensure durability and resilience, the project also saw major technological advancements. These included a new redundant ground visibility monitoring system for enhanced safety, a cutting-edge instrument landing system (ILS) for improved operational precision, and the replacement of over 1,200 energyintensive halogen airfield lights with environmentally-friendly LED technology.
On top of this, the company is currently completing the design and construction of the Ras Ghumais Road Project on the Saudi Arabia border.
“This has been a key project for WBG in 2024, and the aggregates industry has played a major role in the operation due to the scope of work.”
The project consists of a number of construction works, including 30 kilometres (km) of carriageway, comprising three lanes with a width of 3.65 metres (m), an outer shoulder of 1.2m, and a median width of 5m.
It also includes a highway interchange with the E11 – the longest road in the UAE – designed to cater for a dual carriageway with a maximum speed of 80km per hour.
The company has recently been awarded a design and build cycle track project from Aldar, a prominent real estate organisation in the UAE. The project will span the Abu Dhabi mainland to Yas Island and consists of:
• 38km of cycle track
• 14 bridges
• One underpass
• Three culverts
The partnership between Western Bainoona Group (WBG) and Emirates Motor Company-Commercial Vehicles (EMC), showcases the benefits of effective collaboration in the transportation and construction sectors. Since 2011, WBG is operating a fleet of over than 300 Mercedes Benz trucks with different applications such as tractor heads , rigid tippers, mining tippers and Mixers.
With the innovative aftersales solutions from EMC, WBG has achieved a significant savings in total cost of ownership. EMC Service contracts & custom made solutions enhanced the performance, increased vehicles uptime and maximized operation efficiency.
This partnership highlights the importance of innovation in fleet management and sets a benchmark for efficiency and excellence. As WBG continues to integrate advanced technologies, the collaboration with EMC paves the way for future growth and operational success in both transportation and construction sectors.
trucks.mercedesbenzmena.com/ abudhabi/en/
Mercedes-Benz Trucks you can trust
Emirates Motor Company (Commercial Vehicles), Authorised General Distributer of Daimler Trucks in Abu Dhabi, U.A.E. M-12, Mussafah, 02 403 4755, emc.cv@emiratesmotorco.ae, trucks.mercedesbenzmena.com/abudhabi
“THOSE THAT PRIORITISE SUSTAINABILITY, DIGITALISATION, AND LOCAL SOURCING WILL BE WELL POSITIONED TO SUCCEED IN THIS EVOLVING LANDSCAPE”
– MARTIN MCGINTY, CEO, WESTERN BAINOONA GROUP
WBG is additionally constructing a bridge with a roundabout and local connecting roads, as well as an additional truck lane from the E11 to the new bridge.
“To benefit this project, WBG has installed a dedicated asphalt plant, which consumes vast amounts of aggregates,” McGinty informs.
The Middle Eastern aggregates sector is set for continued growth, driven by infrastructure megaprojects, an increased focus on sustainability, and the adoption of cutting-edge technologies.
As a result, the next 12 months
will see more regional collaboration, greener construction practices, and enhanced supply chain resilience.
“Companies will face competition and pricing pressures that will require them to innovate and optimise their operations,” comments McGinty.
“Those that prioritise sustainability, digitalisation, and local sourcing will be well positioned to succeed in this evolving landscape.”
Accordingly, WBG’s key priorities for the next year centre around sustainability, technology implementation, operational efficiency, and growth through market expansion and diversification.
The company’s environmental
strategy will be guided by specific targets such as carbon emissions reduction, improving environmental, social, and governance (ESG) reporting, increasing the use of recycled materials, and enhancing employee development.
“By focusing on these areas, WBG aims to position itself as a leader in the aggregates and infrastructure construction sectors, capitalising on growth opportunities while staying ahead of the market and environmental trends,” McGinty concludes.
Tel: +97125513222 info@wbg.ae wbg.ae
To round off each issue, we ask our contributing business leaders for their views on the same question
IF YOU COULD WORK IN ANOTHER INDUSTRY, WHAT WOULD IT BE AND WHY?
Jitesh Patel CEO, Peldon Rose
“If I was to pick one, it would probably be aeronautics. Why would I pick aeronautics? Because the challenges are huge. First of all, how do you make
a plane fly? This was something that, years ago, no one could ever imagine, but now it happens every day and just look at the transformation in the world.
“When we talk about making everybody’s lives better, that’s what I love about what we do at Peldon Rose. We make everybody’s lives better in the workplace, and look how it’s impacted our leisure time.
“So, I’d choose aeronautics from that perspective because it has a massive impact on people, but it’s also full of challenges – we’ve now
got to come up with a plane that’s environmentally friendly, for example. That’s going to be interesting!
“Ultimately, I’d pick an industry with challenges. That is what I love about ours, which has its own challenges – how do we unlock real estate in Central London? How do we make people’s lives better?”
Are you a CEO or Director with a company story to tell? Contact EME Outlook now!
Our expertise lies in customizing zeolites for various applications, offering our customers unparalleled flexibility and the ability to optimize processes for maximum success. From catalysts in refining and petrochemical processes to sustainable applications like renewable fuels and plastic circularity, our versatile zeolite products cater to diverse industries.
An exceptional line of zeolite products curated to drive progress in the renewable fuels industry and revolutionize catalytic technologies, leaving a considerable mark on Renewable Fuels production.
A portfolio of zeolites for advanced plastic recycling applications, delivering substantial value by enabling precise control of the end products and lowering energy requirements of pyrolysis processes.
At the forefront of developing customized zeolite products across various industries. Our expertise extends to tailoring zeolite materials and catalysts to meet the specific requirements of customer processes.
Zeolyst International offers a large selection of zeolites and Catalysts tailored to Refining and Aromatics processing, Emission Control, Clean Water and Adsorption, and many more applications.