www.mining-outlook.com •
COLLAHUASI

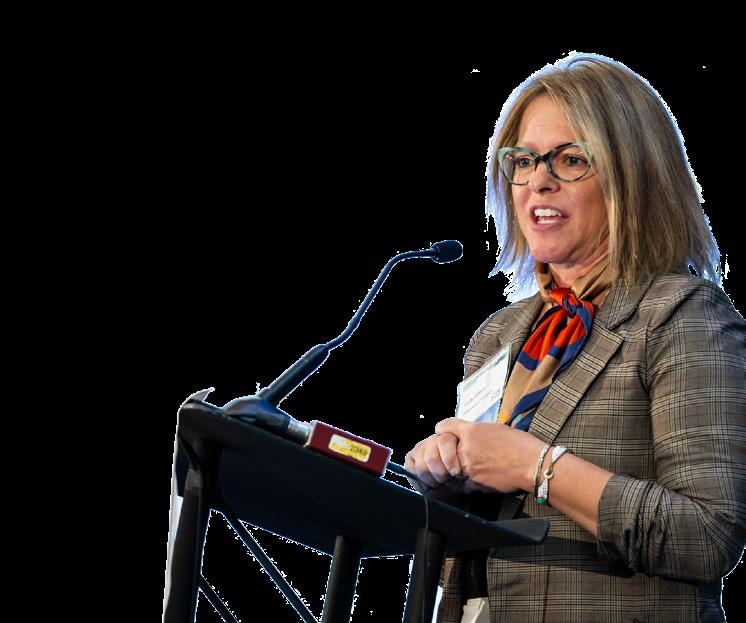
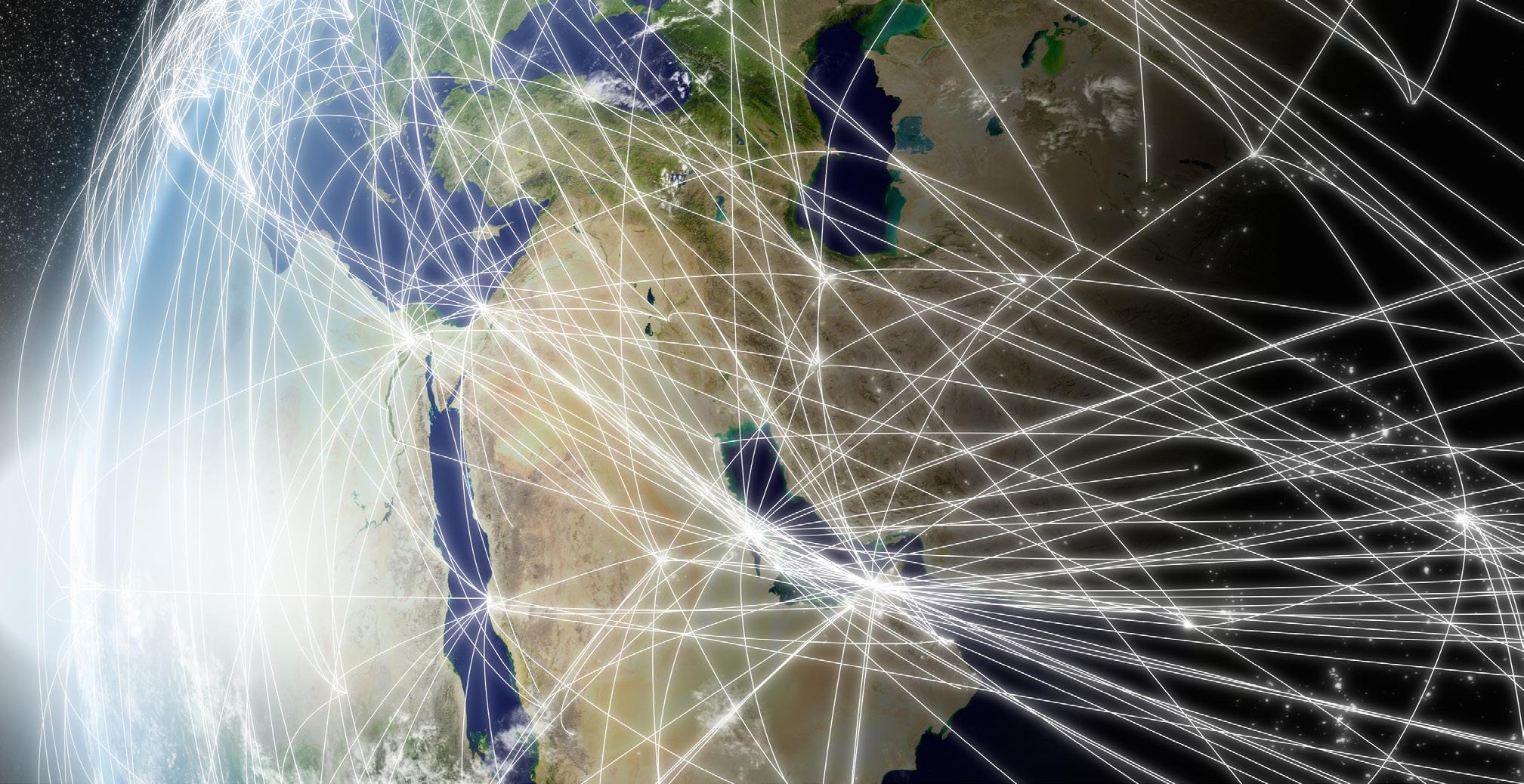
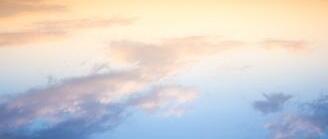


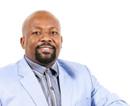
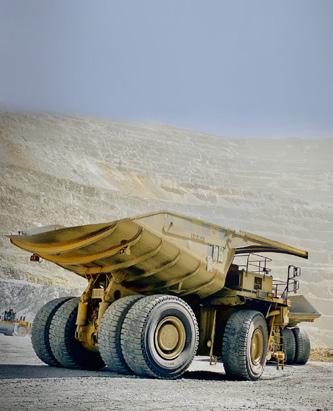
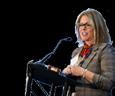
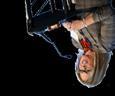

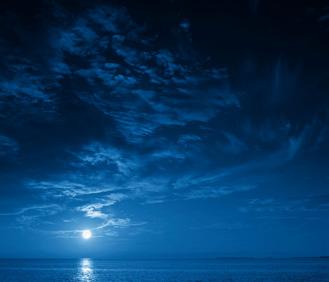
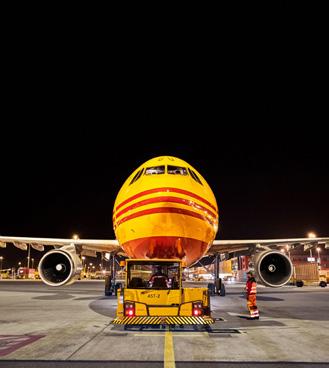
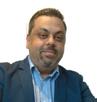
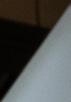



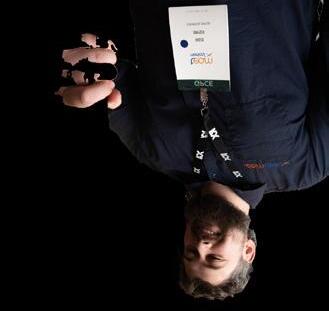
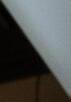
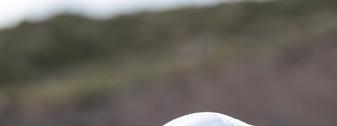

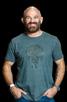
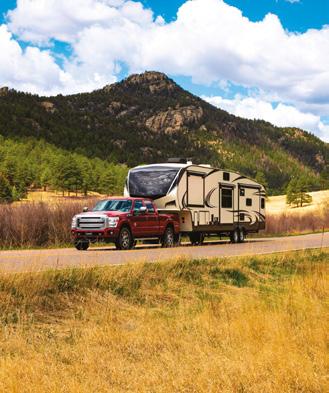



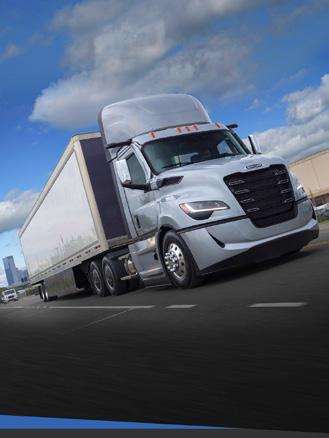
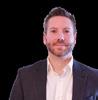
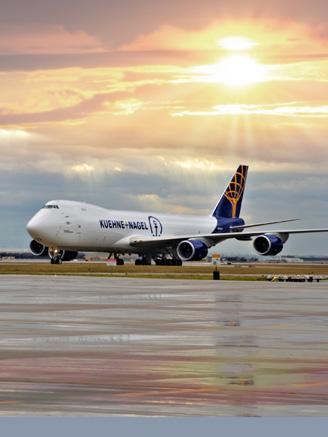

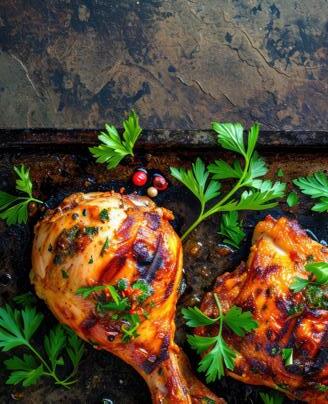
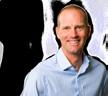
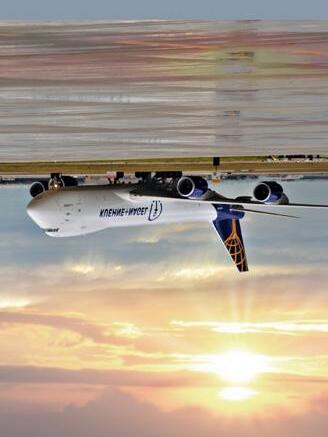

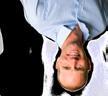
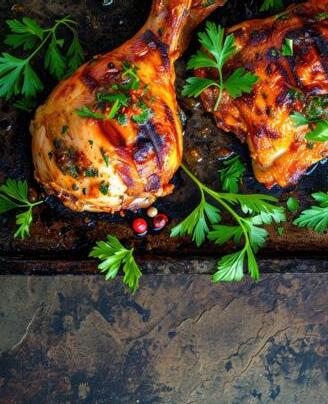
Africa Outlook, APAC Outlook, EME Outlook, North America Outlook, Mining Outlook, Healthcare Outlook, Manufacturing Outlook, Supply Chain Outlook, and Food & Beverage Outlook are digital publications aimed at boardroom and hands-on decision-makers, reaching an audience of more than 800,000 people around the world.
With original and exclusive content compiled by our experienced editorial team, we look to promote the latest in engaging news, industry trends and success stories from across the globe.
Your company can join the leading industry heavyweights enjoying the free exposure we provide across our platforms with a free marketing brochure, extensive social media saturation, enhanced B2B networking opportunities, and a readymade forum to attract new investment and to help you grow your business.
Visit www.outpb.com/work-with-us for details on how your company can feature for free in one of our upcoming editions.
EDITORIAL
Head of Editorial: Jack Salter jack.salter@outpb.com
Deputy Head of Editorial: Lucy Pilgrim lucy.pilgrim@outpb.com
Senior Editor: Lily Sawyer lily.sawyer@outpb.com
Editor: Ed Budds ed.budds@outpb.com
Editor: Rachel Carr rachel.carr@outpb.com
Editor: Lauren Kania lauren.kania@outpb.com
PRODUCTION
Art Director: Stephen Giles steve.giles@outpb.com
Senior Designer: Devon Collins devon.collins@outpb.com
Designer: Louisa Martin louisa.martin@outpb.com
Production Manager: Alex James alex.james@outpb.com
Digital Marketing Director: Fox Tucker fox.tucker@outpb.com
Web Content Manager: Oliver Shrouder oliver.shrouder@outpb.com
Social Media Executive: Jake Crickmore jake.crickmore@outpb.com
BUSINESS
CEO: Ben Weaver ben.weaver@outpb.com
Managing Director: James Mitchell james.mitchell@outpb.com
Chief Technology Officer: Nick Norris nick.norris@outpb.com
ADMINISTRATION
Finance Director: Suzanne Welsh suzanne.welsh@outpb.com
Finance Assistant: Victoria McAllister victoria.mcallister@outpb.com
CONTACT
Mining Outlook
Norvic House, 29-33 Chapelfield Road Norwich, NR2 1RP, United Kingdom. Sales: +44 (0) 1603 804 445
Editorial: +44 (0) 1603 804 431
SUBSCRIPTIONS
Tel: +44 (0) 1603 804 431 jack.salter@outpb.com www.mining-outlook.com
Like us on Facebook: facebook.com/miningoutlook
Follow us on X: outlookpublish

FUTURE-FACING COMMODITIES
Welcome to our ninth edition of Mining Outlook.
Chile, the distinctive ribbon of land that runs along the west coast of South America, is a curiously shaped country abundant with vast natural landscapes.
It is also the world’s largest producer of copper, which has become increasingly critical within the green energy transition. South America, and Chile in particular, therefore remain key for the global supply of the resource.
An industry stalwart, and this issue’s cover star, Collahuasi is one of the world’s primary copper producers and the second largest in Chile, boasting an extensive operation in Tarapacá.
“Today, we stand out as one of the safest, most efficient, productive, and sustainable mining operations worldwide,” shares CEO, Jorge Gómez.
With the energy transition gaining momentum, demand for future-facing commodities remains strong and sustainability continues to be a core focus of the industry as organisations work to decarbonise their operations and supply chains.
It is also a key strategic component of Orica and integral to the company’s operations in Europe, the Middle East, and Africa (EMEA) as well as globally.
Orica, whose purpose is to sustainably mobilise the earth’s resources, is unwaveringly committed to excellence in the EMEA mining sector and has ambitions to achieve net zero emissions by 2050.
“My interest in mining grew as I recognised its critical role in supporting global sustainability, providing essential raw materials for the energy transition and critical minerals that are vital for modern society,” reflects Victor Morales, Vice President of EMEA Mining at Orica.
Grydale, a renowned dust management solutions provider and equipment manufacturer, likewise incorporates sustainability into its operations.
The company tackles significant dust emissions in the mining industry, whilst its protected intellectual property meets stringent air quality standards mandated within major projects.
“Thanks to our proprietary technology, Grydale’s dust collectors have gained a reputation worldwide,” acclaims CEO, Alex de Andrade.
Elsewhere, we collect the latest developments from Cooper Fluid Systems, Campbell Transport, and G4 Mining and Civils (Pty) Ltd.
We hope that you enjoy your read.
Jack Salter Head of Editorial, Outlook Publishing
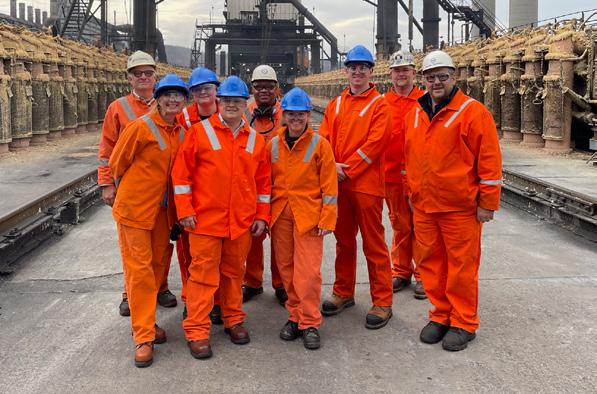
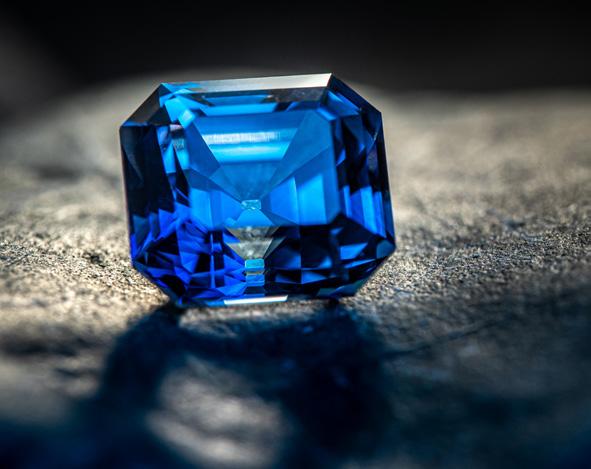
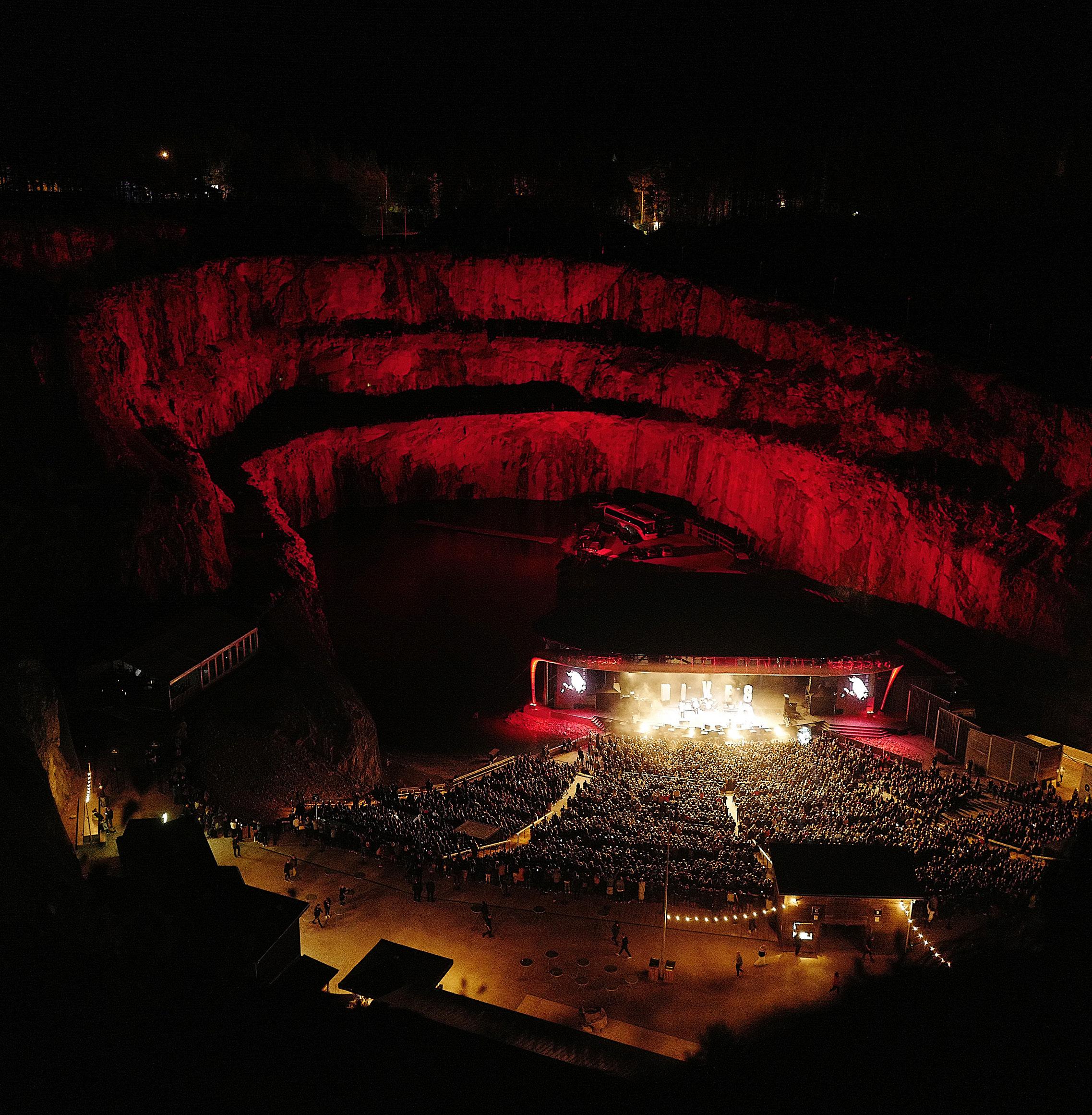
NORTH AMERICA
32 Collahuasi
The House of the Miner
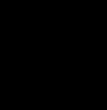
An extensive presence in Chilean mining
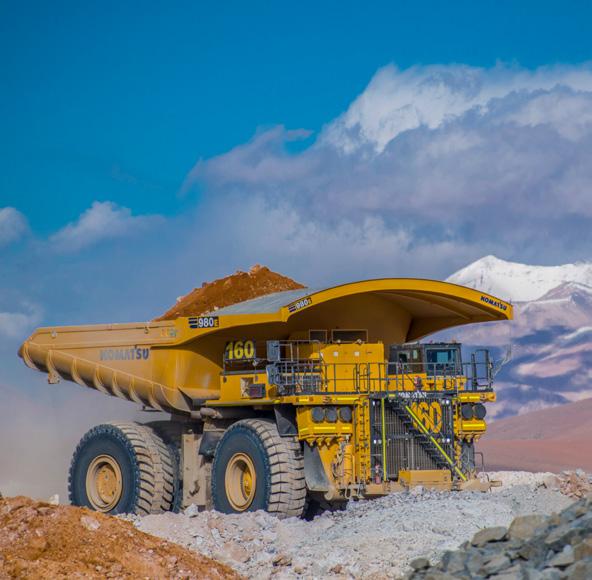
AFRICA
52 Bokoni Platinum Mines
Mining for the Future
Committed to innovative mining and community development
86 G4 Mining and Civils (Pty) Ltd
Building South Africa’s Future
A solid track record for success
EUROPE & MIDDLE EAST
94 Orica EMEA
Sustainably Mobilising the Earth’s Resources
Innovative and sustainable solutions across Europe, the Middle East, and Africa ASIA PACIFIC
Grydale
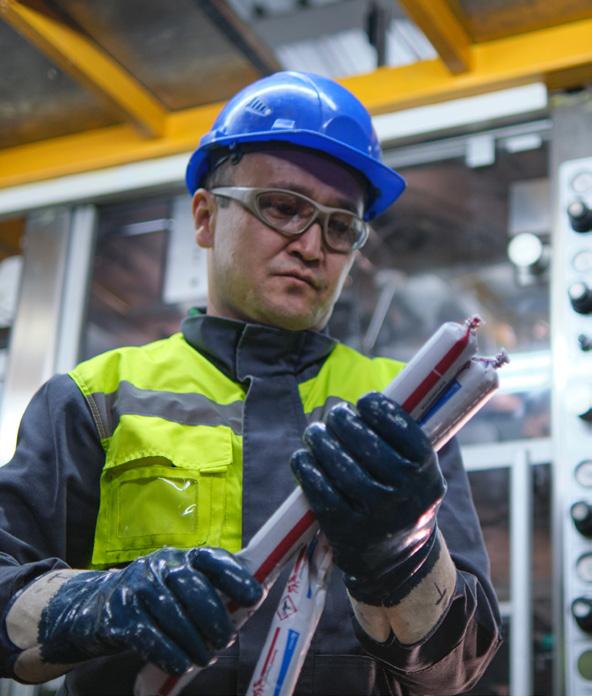
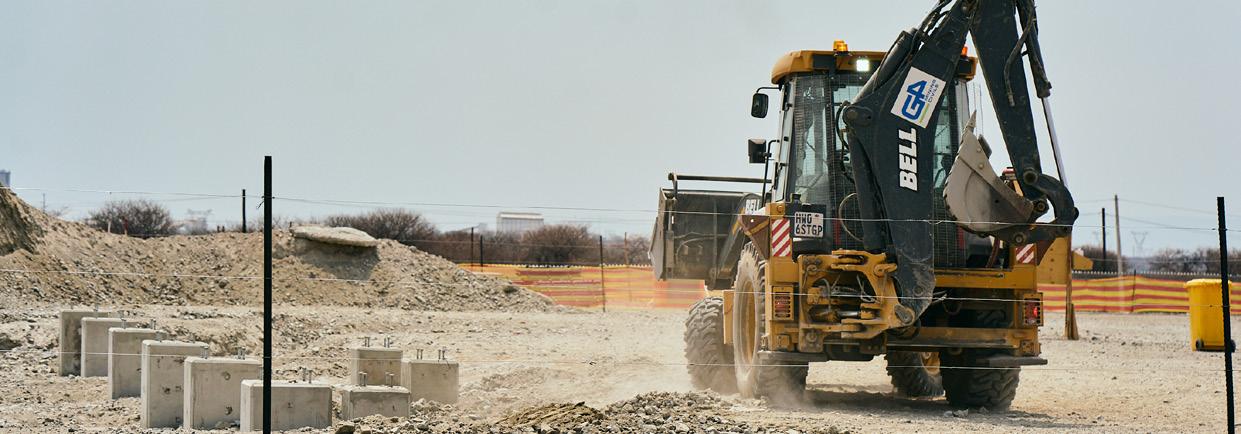
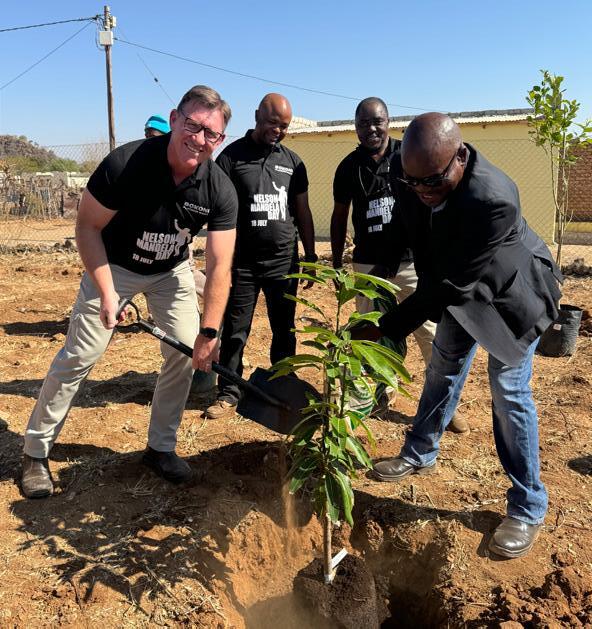

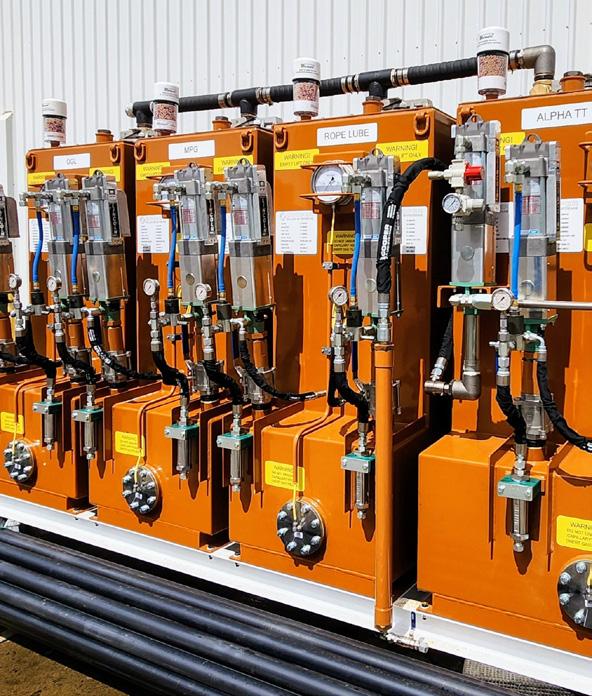


CHINA-PAKISTAN
PARTNERSHIP
FOLLOWING PAKISTAN PRESIDENT Asif Ali Zardari’s recent visit to China, it has been revealed that Chinese-funded enterprises are to carry out mining activities in Pakistan, including the exploration of terrestrial and marine geological resources.
China already has thousands of its nationals working on projects grouped under the China-Pakistan Economic Corridor (CPEC), and Pakistan welcomes further development of its offshore oil and gas resources.
A long-term ally of Pakistan, China’s notable financial support began in 2013. The two countries have historically collaborated closely due to their long-standing competition with neighbouring India and a general desire to resist homogenising US influences.
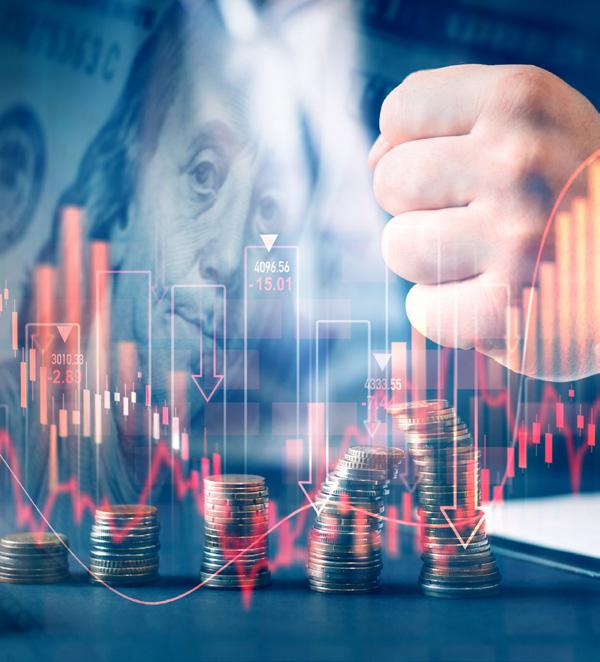
OUTCRY AMIDST FAILED COMMUNITY REINVESTMENT
THE COAL INDUSTRY Social Welfare Organisation (CISWO) has come under fire as mining communities claim that up to £12.2 million raised by the sale of former social welfare sites has failed to be reinvested locally.
The Maltby Miners Welfare
US EUROPE & MIDDLE EAST
GREENLAND’S MINERALS COVETED BY
TO FUND ITS two preproduction mining assets in Europe, the Tanbreez Rare Earths Project in Greenland and the Wolfsberg Lithium Project in Austria, Critical Metals Corp has recently entered into a securities purchase agreement for private investment in public equity (PIPE) financing that is expected to raise approximately USD$22.5 million.
The former, in particular, has made headlines of late following President Trump’s interest in bringing Greenland’s significant rare earth mineral deposits under US control.
The announcement follows restrictions placed on China’s export of rare earth minerals, with the funds raised intended to deliver long-term value for Critical Metals Corp’s stakeholders.
As such, the burgeoning company is building a portfolio designed to address the increasing global demand for critical minerals, distinguishing itself as a key industry player.
Institute site in South Yorkshire, for example, which was part-funded over the years by payments from miners’ own wage packets, was recently sold and demolished to make way for private housing. 27 such sites have been sold between 2010 and 2024 across the UK.
As such, a group of Labour MPs have now sent a letter to CISWO expressing their view that the profits from the sale of such buildings should be refocused and ringfenced within local communities.
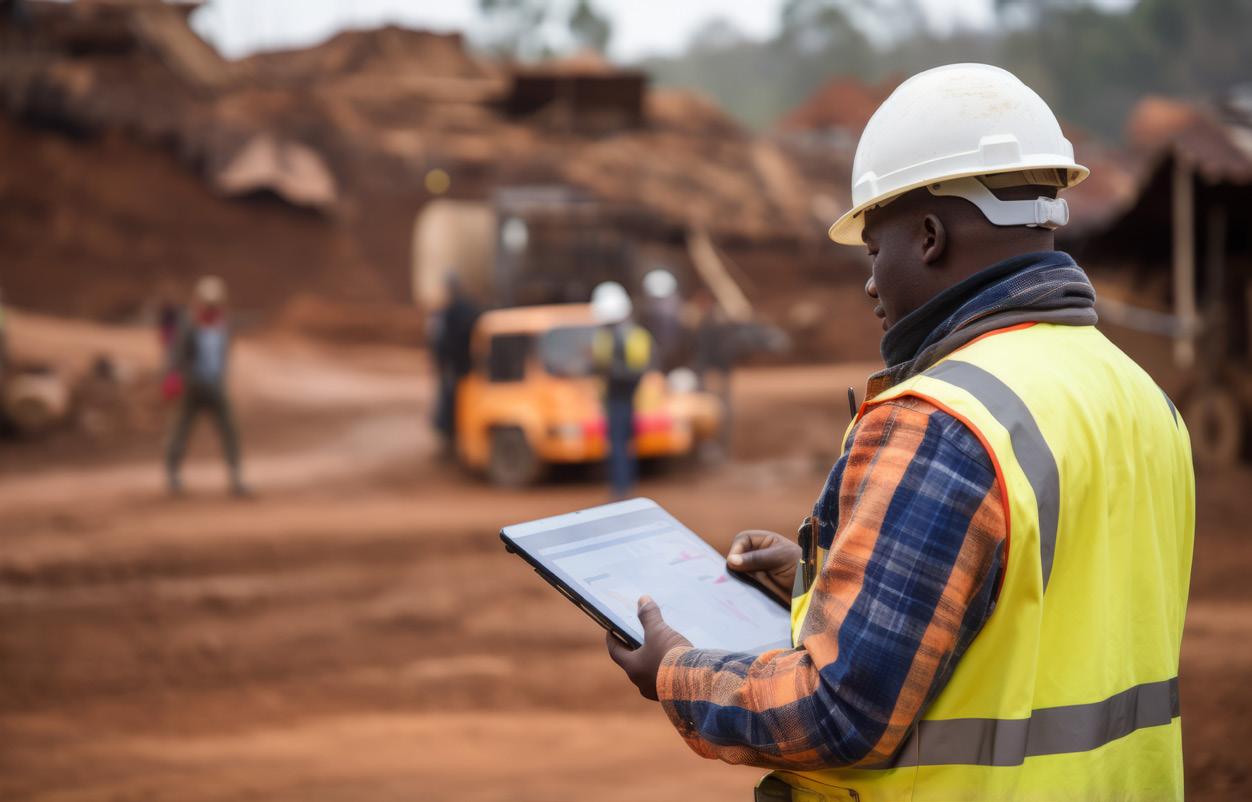
US TO DEVELOP AFRICAN MINING
THIS YEAR’S MINING Indaba conference, hosted in Cape Town, South Africa from 3rd – 6th February, witnessed a major declaration from the US revealing President Trump’s interest in developing the African mining sector.
Scott Woodard, the Acting Deputy Assistant Secretary for Energy Transformation in the US State Department’s Bureau
LOCKING IN AN ENVIRONMENTAL PLEA
ENVIRONMENTAL GROUP, LOCK the Gate, has called for Pembroke Resources’ Olive Downs Coal Mine in Central Queensland, Australia, to increase its ecological protections for endangered species native to the area.
The plea comes after recent thermal drone footage revealed endangered koalas and greater gliders breeding in the path of the project’s intended AUD$875 million expansion.
of Energy Resources, spoke of Trump’s intention to focus on mineral exploration, extraction, and processing.
Director of the Africa Programme at the Carnegie Endowment for International Peace, Zainab Usman, emphasised how, in addition to mineral extraction, US investment must also support African industrialisation.
Meanwhile, Zambia’s Minister of Transport and Logistics, Frank Tayali, thanked the US for its investment.
The group is appealing to the Australian Minister for the Environment and Water, Tanya Plibersek, to update conditions to better protect endangered species in light of the drone footage.
As part of its plea, Lock the Gate also noted how Australia’s centre-left Albanese government should be in
CANADA CONFIRMS CONTINUED AIR LOGISTICS SUPPORT
JB AVIATION SERVICES (JBAS) has reaffirmed its commitment to Canada’s mining sector amidst economic uncertainty and anticipated industry constraints and tariffs posed by the US.
JBAS has assured partners across Canada that its strategic air logistics solutions will remain in place to support them. These include fly-in, fly-out (FIFO) services, exploring potential synergies amongst industry players to consolidate flight routes, and a flexible approach towards air logistics which allows mining companies to adjust to potential economic or operational fluctuations.
As such, JBAS continues to offer its services to sustain the strength and profitability of Canadian mining.
A GREEN REGENERATION
GOVERNMENT SUPPORT FOR former coalfield communities across the UK has recently been debated in Parliament, with a call for excoalfields to become green energy hubs amongst the suggestions put forwards.
Grahame Morris, Labour MP for Easington, discussed how latent geothermal energy from former mines could be used to heat homes and, in turn, create new green-collar jobs.
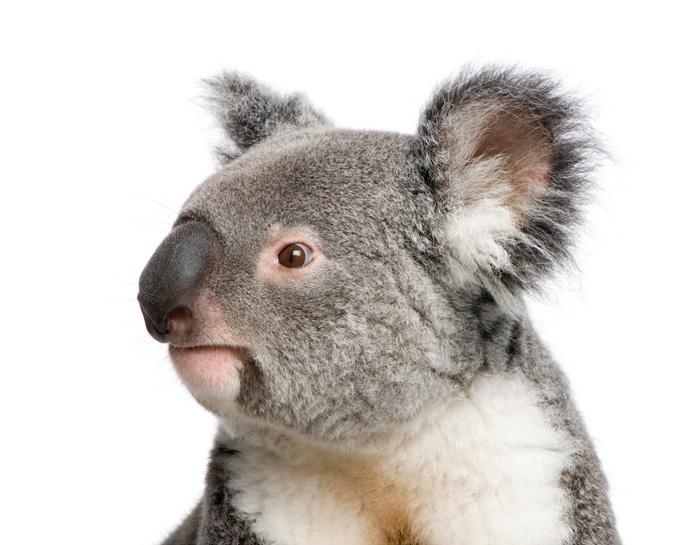
Jim McMahon, Minister of State for Housing, Communities, and Local Government, proposed a package of up to £20 million in funding and support for such communities, citing devolution as an important contributing factor to sharing wealth and opportunity across the UK.

THE KEY TO UK ENERGY TRANSITION
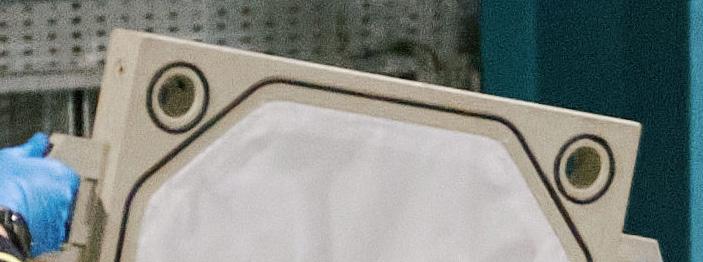
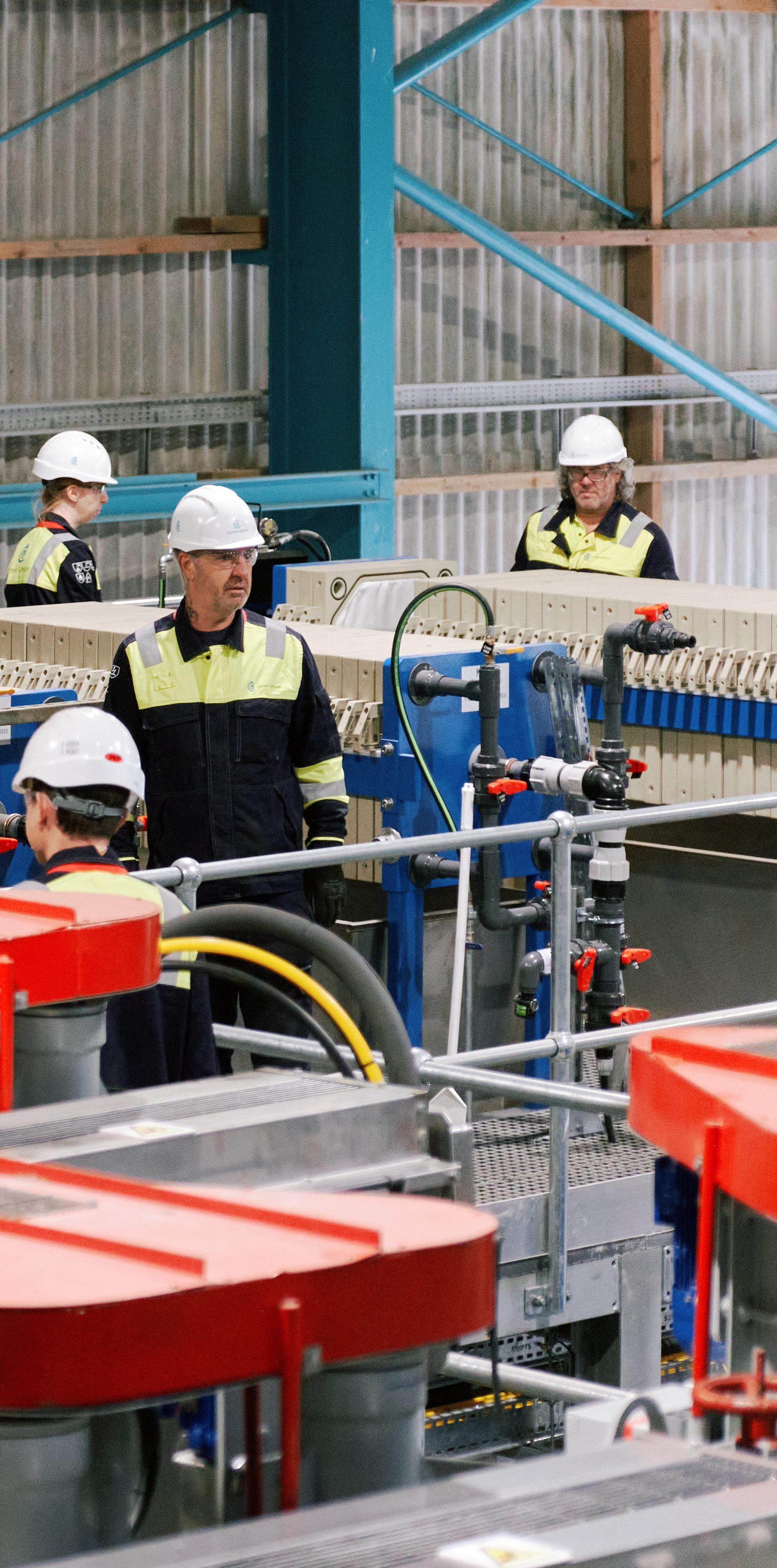
Jeremy Wrathall, the Founder and CEO of Cornish Lithium, discusses how pioneering and innovative mineral exploration and development can supply the raw materials needed for the green industrial revolution and advance a sustainable economy
Writer: Jeremy Wrathall, Founder and CEO, Cornish Lithium
The UK government has acknowledged that lithium will be vital to our automotive sector’s electric vehicle (EV) transition and will drive the green industries of the future. As such, Cornwall’s critical minerals resources - lithium, tin, and tungsten - are essential components of a commercially and environmentally sustainable net zero UK economy, positioning the region as a linchpin in the future of the UK’s energy transition.
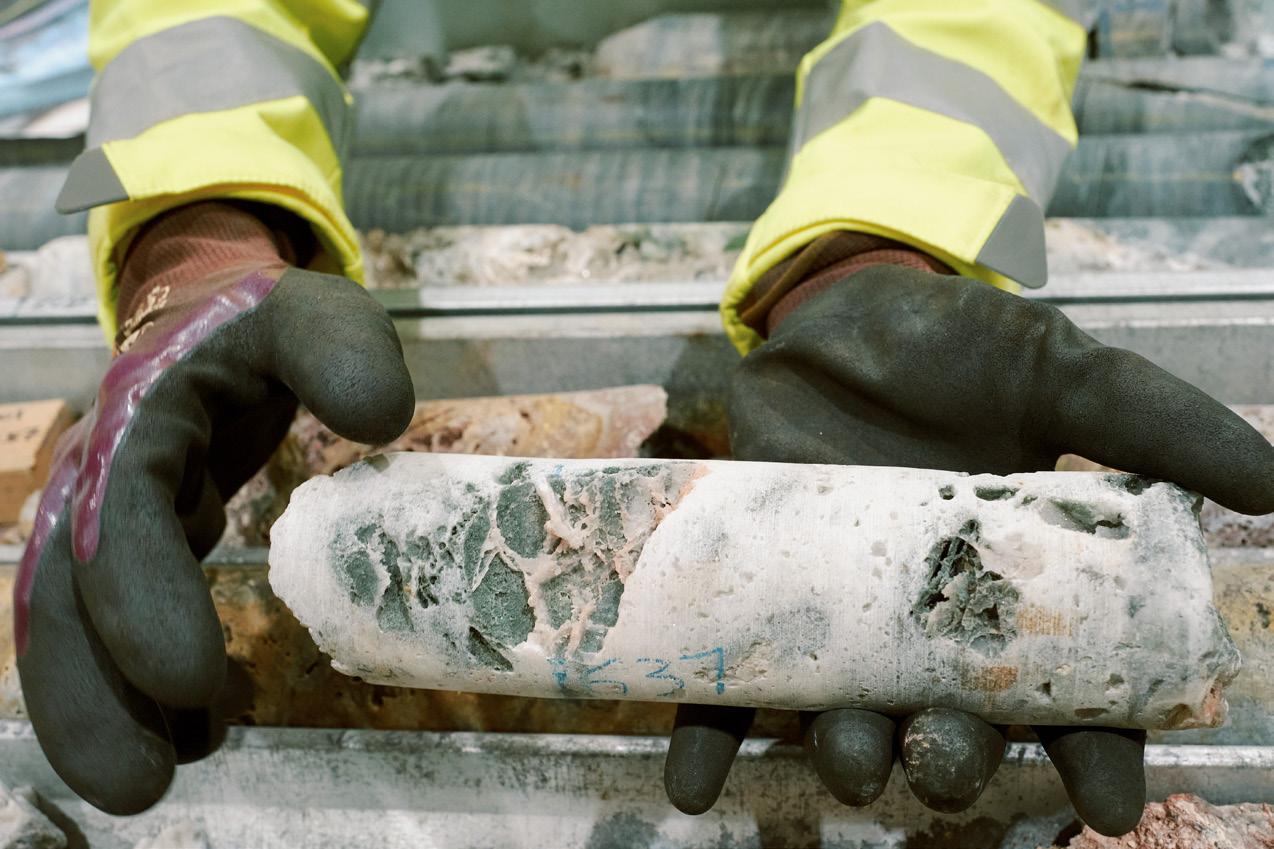
Cornwall has the largest lithium deposit in Europe, with enough beneath our feet to extract 50,000 tonnes per year for over 20 years – over half of what the EV industry needs, presenting a significant opportunity to ethically produce lithium for the UK. Yet, the UK currently imports all of its lithium from overseas.
We’re on a mission to change that. Cornish Lithium aims to sustainably provide around 20,000 tonnes per year of battery-grade lithium hydroxide - around 20 percent of the UK’s annual needs by 2030.
Every tonne supplied domestically by Cornish Lithium is one tonne less than the UK needs to import from overseas. Accelerating the development of Cornwall’s critical minerals resources would deliver, de-risk, and decarbonise critical minerals supply chains vital to the future of UK manufacturing-based sectors and generate much-needed economic growth for Cornwall and the UK.
We are advancing lithium production from two sources - hard rock lithium
extraction and geothermal waters lithium extraction.
THE UK’S FIRST LITHIUM HYDROXIDE DEMONSTRATION PLANT
Our Trelavour Hard Rock Project is testing and refining the extraction of battery-grade lithium from granite rock. Several processing steps are required after mining, so to perfect our technology on a larger scale before building a full-sized commercial plant, we’ve built a demonstration facility at our site near St Dennis.
This new demonstration plant marks a major step forwards in supporting the UK’s shift to net zero. This stateof-the-art facility uses a new and innovative processing technology developed by Lepidico that is less energy-intensive than conventional processing technology used to extract lithium from hard rock.
Located just one kilometre from the Trelavour Pit, the plant can produce battery-grade lithium hydroxide all in one place without needing extra shipping or processing.
By 2028, the demonstration plant

will evolve into a fully operational production plant. In addition to lithium, the demonstration plant could create valuable by-products, reducing waste and benefitting various industries. Examples include amorphous silica for green cement, sulphate of potash for fertiliser, and gypsum for plasterboard.

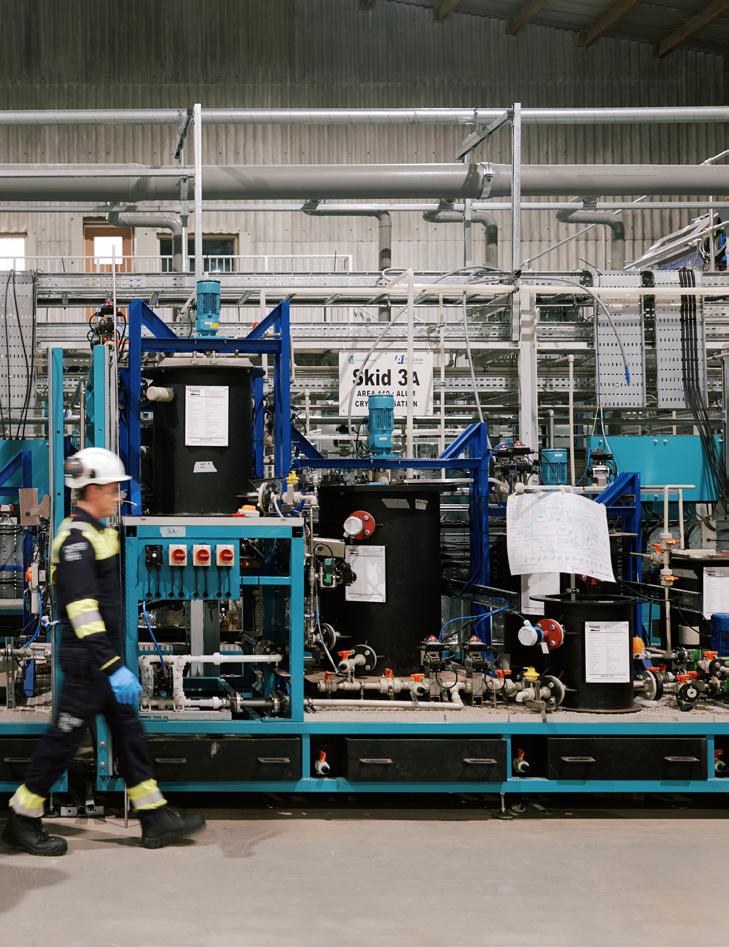
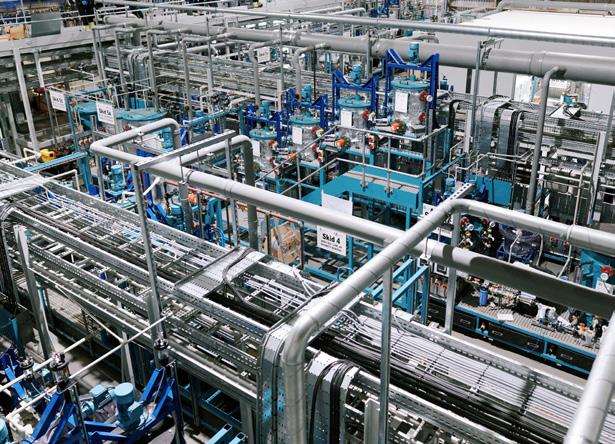
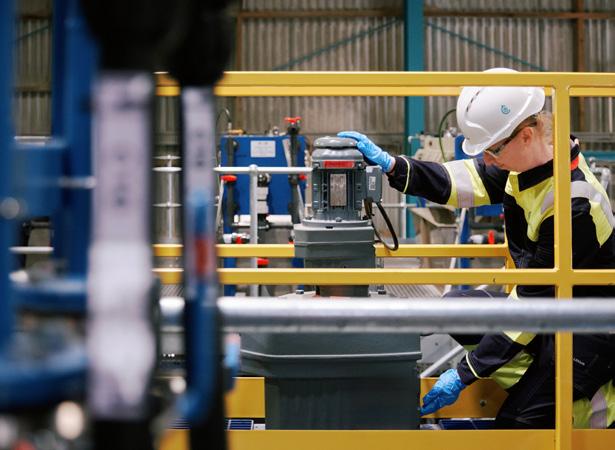
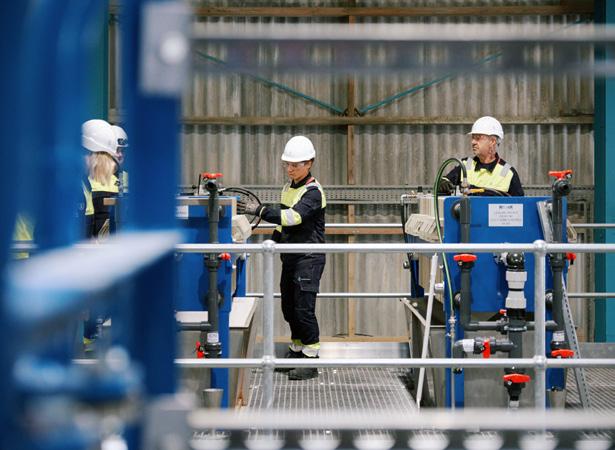
LITHIUM IN GEOTHERMAL WATERS
In addition to hard rock sources, lithium can dissolve in the geothermal waters beneath Cornwall. These mineral-rich waters offer a unique opportunity for sustainable lithium extraction.
We’re using direct lithium extraction (DLE) technology to produce lithium from geothermal water pumped from deep below the surface. This process not only produces lithium but also taps into significant amounts of low-carbon heat energy, which could potentially be used to benefit local industries and communities.
The process used in our geothermal lithium extraction plants can be likened to a water purification system. Mineral-rich water is pumped from approximately 2,000 metres below the surface via a borehole and passed through columns where the lithium is extracted from the water. The water is returned to the ground via a second borehole, and the lithium is removed.
‘MINES TO WHEELS’ SUPPLY CHAIN
In addition, the UK has started building the components of a ‘mines to wheels’ supply chain. Mining battery-grade lithium in Cornwall will support the production of EV batteries to help the UK become a powerhouse for green technologies and much more.
The potential of Cornwall’s critical mineral resources will have a significant positive impact. A secure, responsible domestic supply will reduce carbon emissions, bolster the UK’s economic resilience, strengthen energy security, and create muchneeded high-quality, high-productivity careers in the region and across the UK through supply chain development. Development of critical minerals in Cornwall has already attracted significant UK and foreign direct investment, complemented by UK government equity investment through the National Wealth Fund and
grant funding from sources including the Automotive Transformation Fund. This private and public co-investment should be sustained to enable Cornwall to realise the full potential of its critical minerals.
By extending its support for critical growth sectors, including critical minerals, the government will unlock long-term economic growth, generate thousands of high-quality, highproductivity jobs, support UK-wide supply chain development, and, in doing so, secure the UK’s cleaner, greener energy future.
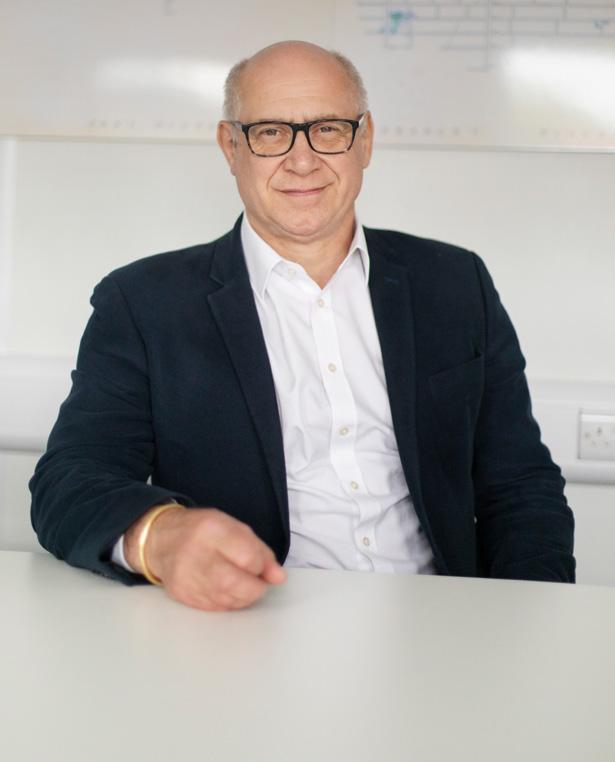
ABOUT THE EXPERT
Jeremy Wrathall is the Founder and CEO of Cornish Lithium and has over 30 years of experience in the mining finance industry, where he has advised companies on global transactions.
After graduating with a degree in mining engineering from the Camborne School of Mines in Cornwall, he worked for three years as a mining engineer in the South African gold mining industry.
In 2016, Wrathall founded Cornish Lithium, a company focused on exploring lithium deposits found in the naturally occurring hot springs beneath the surface in and around Cornish granites.
SOLUTIONS FOR THE JOURNEY
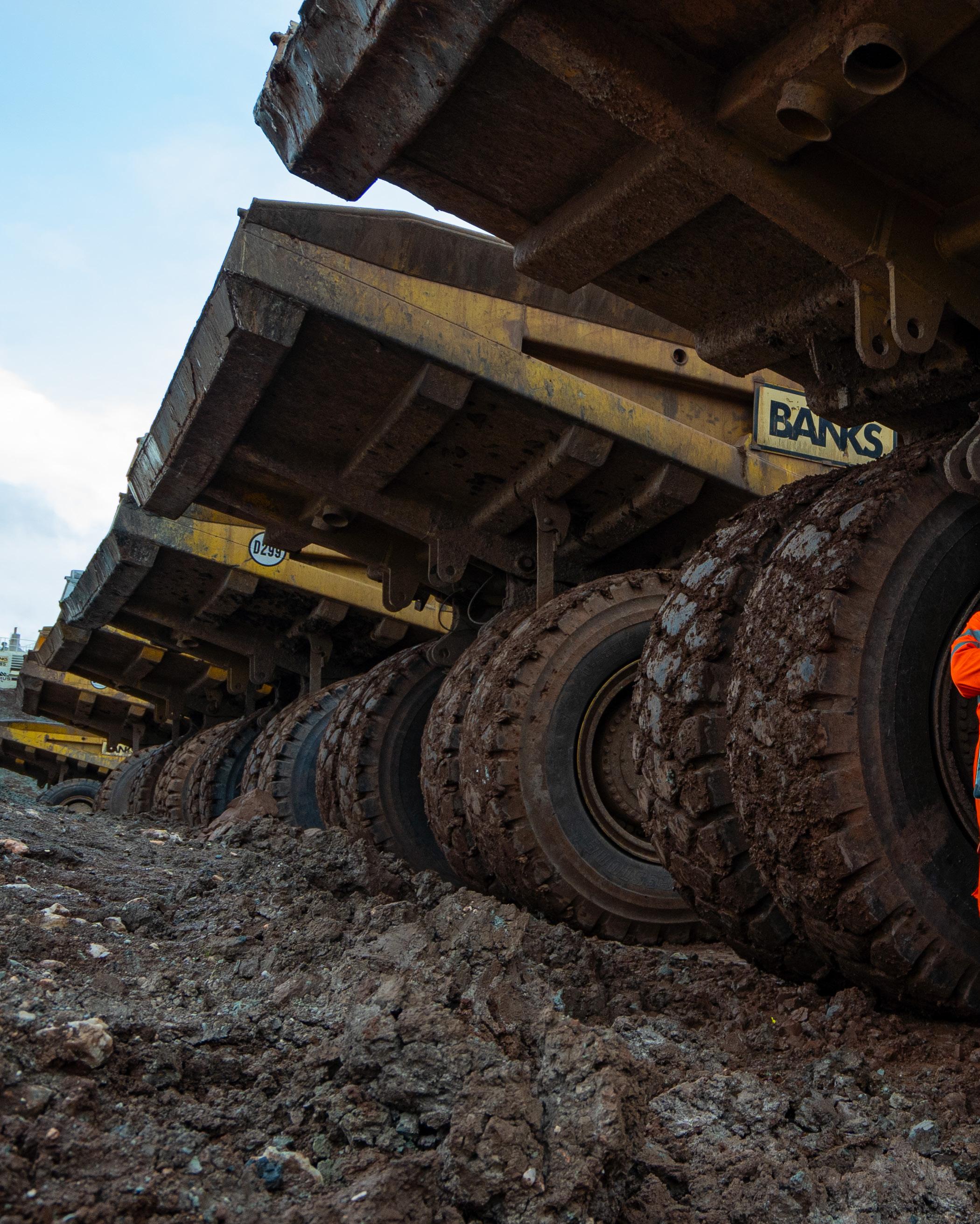
In ever-changing social and economic environments, Bridgestone precisely recognises the dynamism of social and customer values and continues to provide tailored solutions to support mining operations. We find out more from Rob Cole, Key Account Manager – Off Road Tyres, UK and Ireland
Writer: Ed Budds
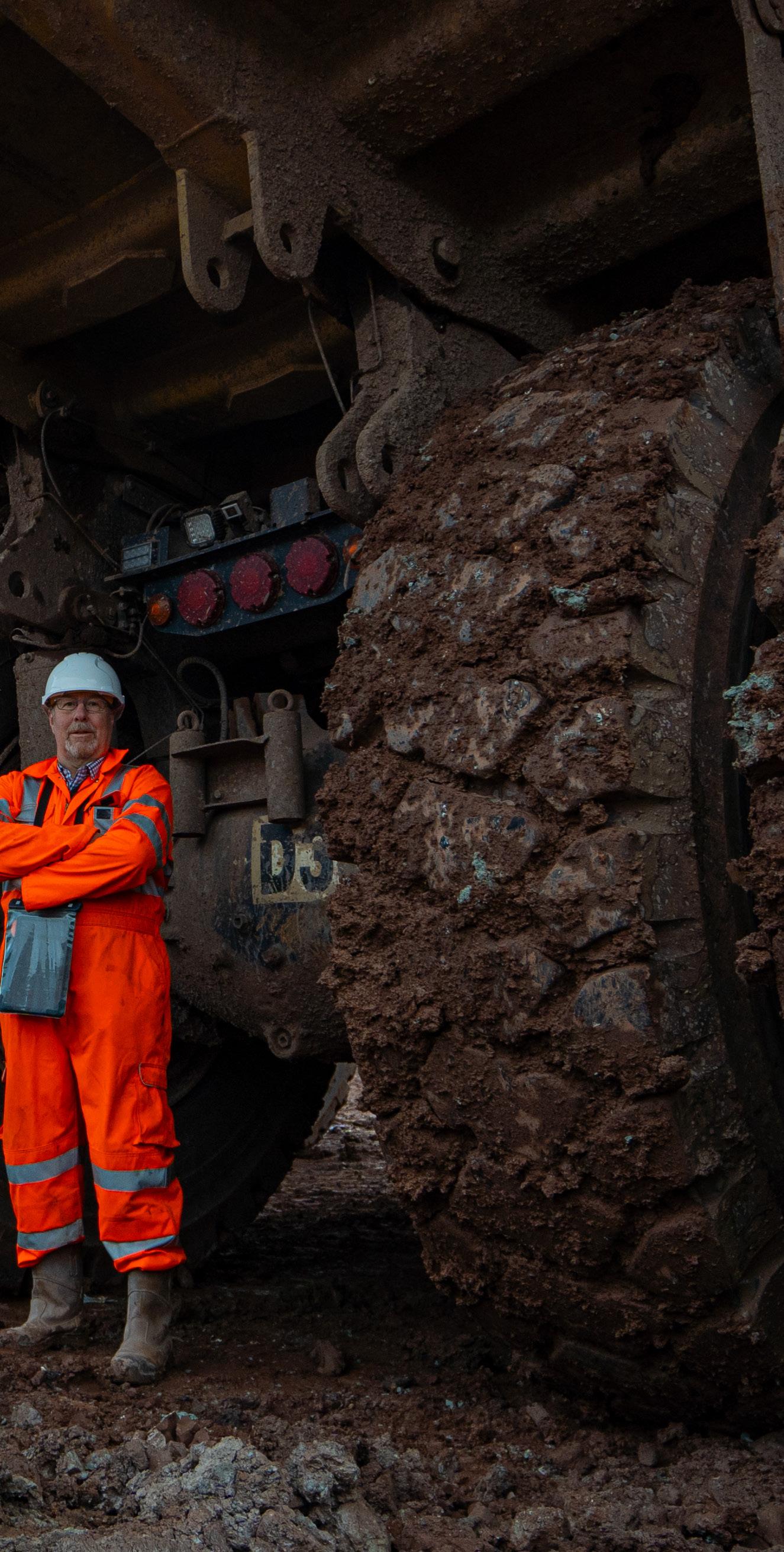
Bridgestone is a world leader in tyres for the mining sector, offering a comprehensive range of sizes, patterns, and compounds to suit all applications.
Across an expansive range of ever-changing social and economic environments, the role of Bridgestone today is to improve productivity and optimise costs for each mining customer in accordance with changes in this vast industry.
“We produce high-quality, premium tyres that provide reliability, durability, and longevity, and are a trusted brand in the mining sector,” introduces Rob Cole, Key Account Manager – Off Road Tyres, UK and Ireland.
“Our mining solutions are all built on a foundation and global heritage of off-the-road tyre performance and innovation.”
By maximising its usage of a wide range of products, services, and digital tools, Bridgestone collaborates with customers as a partner and provides customised, innovative solutions.
“Working directly with end users and service agents, we’re able to tailor tyre solutions to each individual mine site,” he adds.
DURABILITY AND LONGEVITY
Today, tyres are one of the top three costs involved in running mining equipment.
As such, product reliability, durability, and longevity are vitally important factors for Bridgestone to reduce the amount of machine downtime caused by tyres.
“We’re constantly developing new technologies in the giant sizes of our tyres, such as our MasterCore product,” states Cole.
JOURNEY
This product includes a new casing design that enables the tyre to host a greater load at a higher speed, which are both key factors in making a mine site more efficient.
“Elsewhere, for underground mining operations, we have
developed new casings that also carry higher loads but at the same pressures as before, in order to cope with the extra weight of the batteries in electric mining equipment,” he expands.
“We also offer a range of systems such as iTrack that monitor tyre pressures and vehicle tracking. This is to ensure tyres aren’t lost due to heat build-up.”
GLOBAL HERITAGE
Undoubtedly, site visits are the most important part of Bridgestone’s efforts to collaborate effectively with its partners and clients.
“Every mine site is different in some respect, so to see and understand the challenges of an individual site enables a more tailored solution to be presented,” Cole explains.
Similarly, the company also has very
strong relationships with the original equipment manufacturers (OEMs) of premium mining equipment.
“In terms of what makes Bridgestone a trusted supplier of solutions for the mining sector, our reputation for producing reliable products and solutions through direct engagement with mine sites and service agents is growing,” he acclaims.
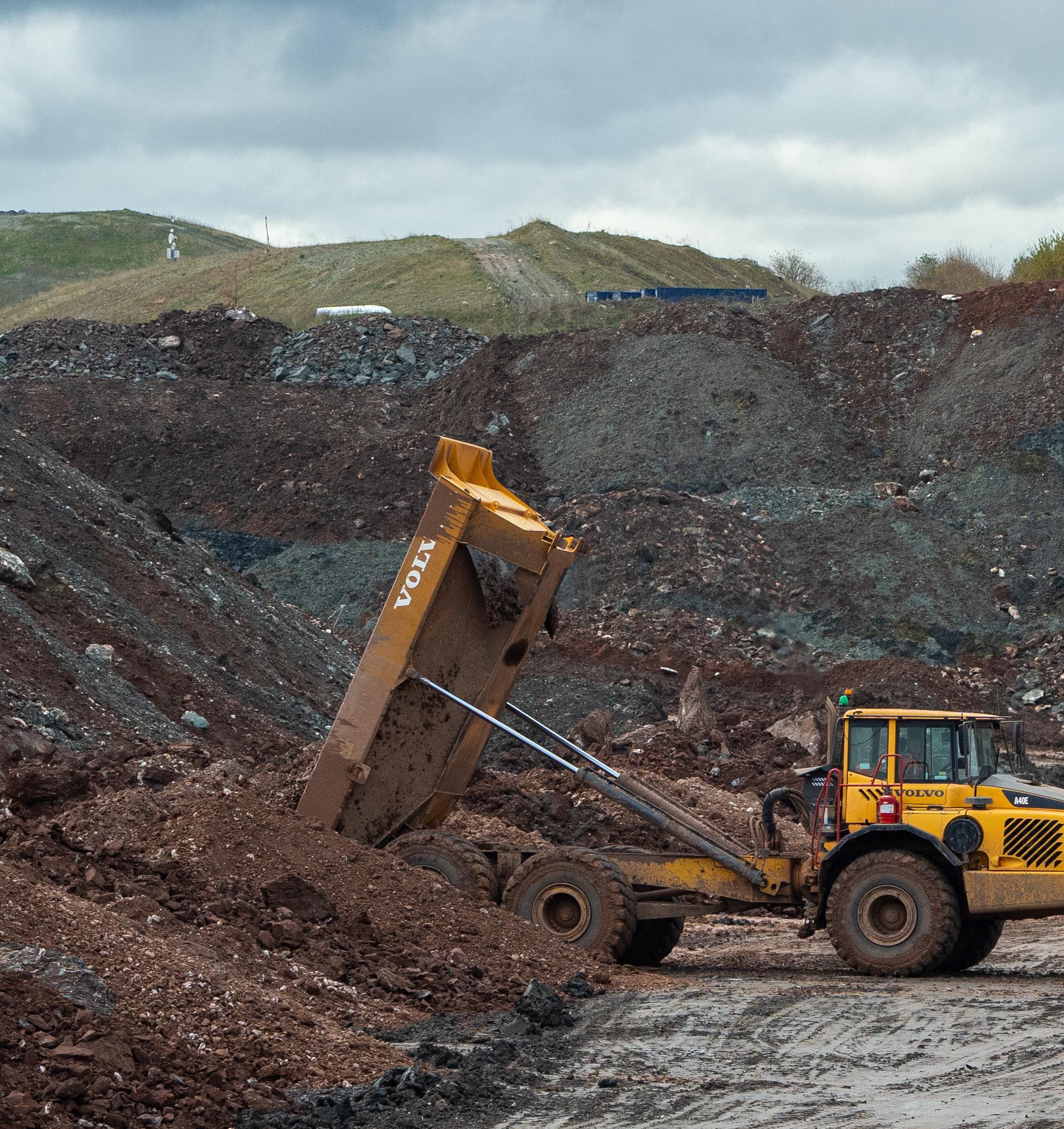
Looking ahead, Bridgestone recognises that competition is increasing in the mining sector, with more Tier 2 brands entering the market.
“We continue to develop products, such as our MasterCore technology, that keep pushing innovation for the benefit of our long-standing client base.”
OFF-ROAD TESTING
Bridgestone’s tyre manufacturing and testing facilities are located in both Japan and the US, with R&D operations also being carried out in the former at its dedicated technical centre.
The comprehensive testing of new products is done in real world environments with customers in the field, whereby dedicated engineers
monitor and report findings.
Bridgestone’s Off the Road Tire Test Centre (ORTC), located in the city of Hōfu in Yamaguchi Prefecture, was first established in 1982 with the goal of performing multifaceted tests and analysis of off-the-road radial tyres, and has continued to grow and develop to meet the market’s needs ever since.
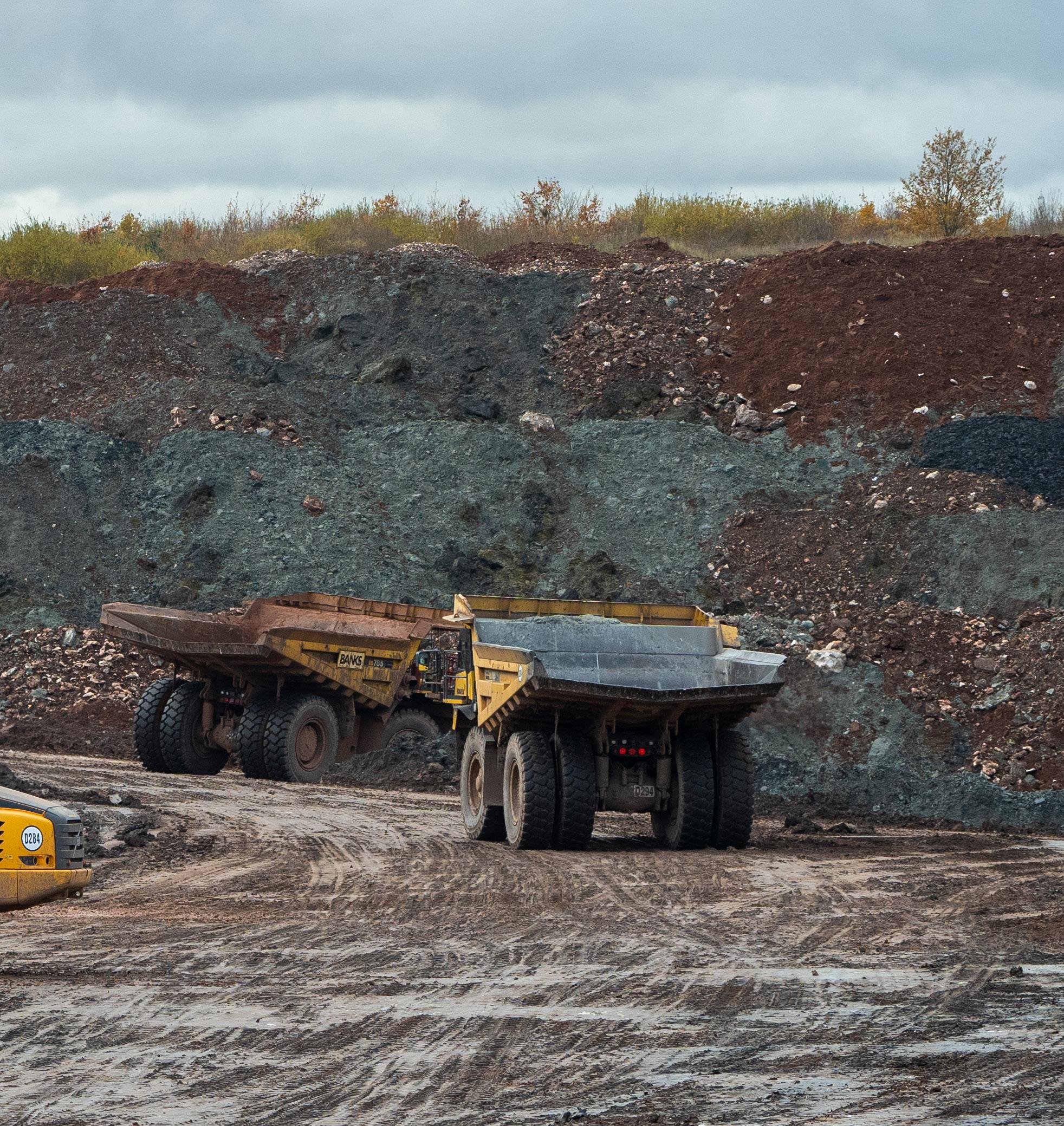
“WE PRODUCE HIGH-QUALITY, PREMIUM TYRES THAT PROVIDE RELIABILITY, DURABILITY, AND LONGEVITY, AND ARE A TRUSTED BRAND IN THE MINING SECTOR”
– ROB COLE, KEY ACCOUNT MANAGER – OFF ROAD TYRES, UK AND IRELAND, BRIDGESTONE
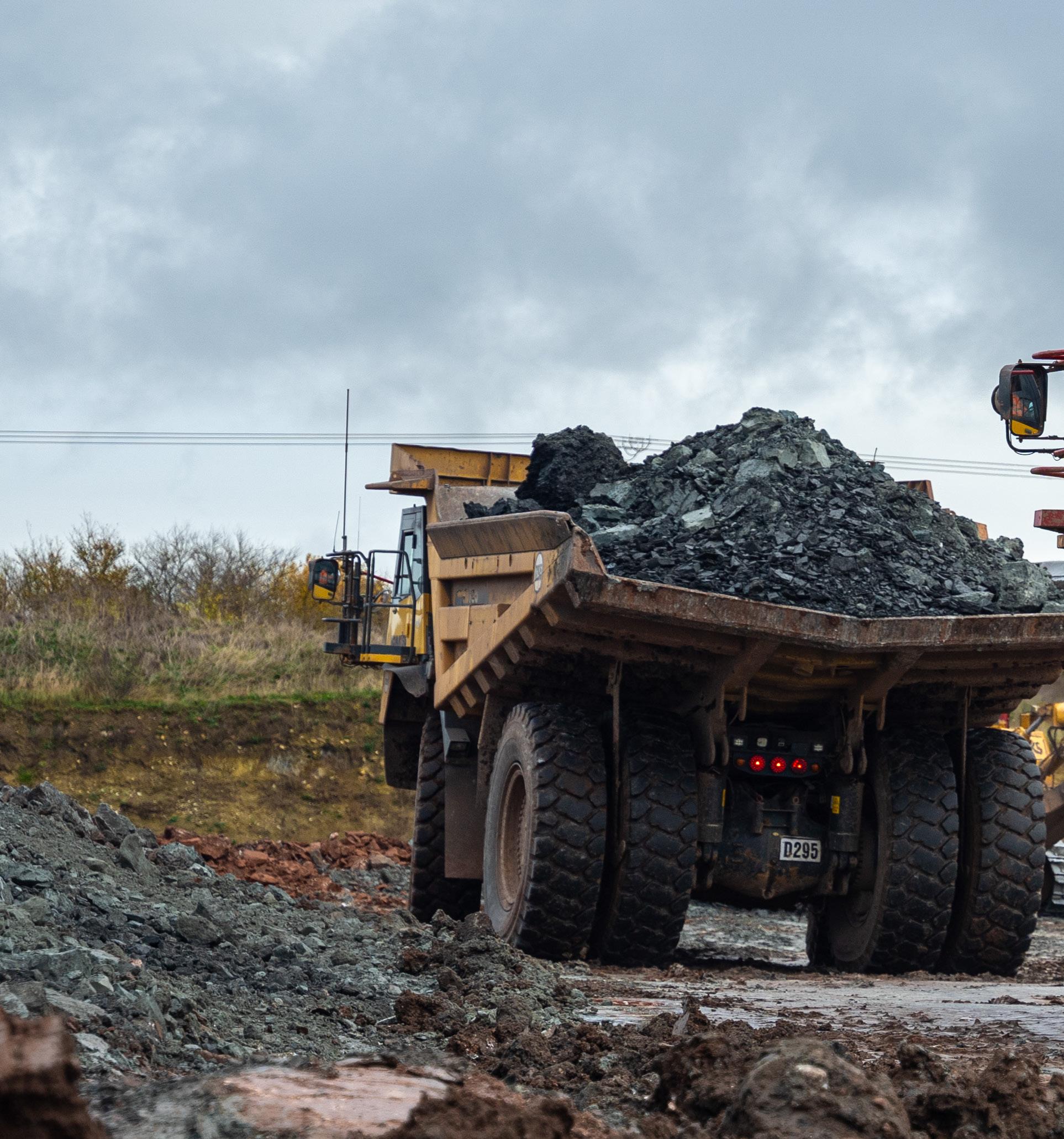
ORTC plays an essential role in the development of off-the-road tyres by performing laboratory tests to ensure the quality and performance of Bridgestone’s portfolio of products before the tyres are sent for final validation at customer operating sites.
Furthermore, at ORTC, multifaceted tests and analyses are performed, such as the static test, dynamic test, and cut analysis. These can monitor a wide variety of off-the-road tyres, including ultra-large products with diameters of more than four metres.
ORTC also supports Bridgestone’s development platform for off-theroad radial tyres, with various tests based on customer usage conditions and performance requirements, to deliver safe and reliable products to mining sites across the world.
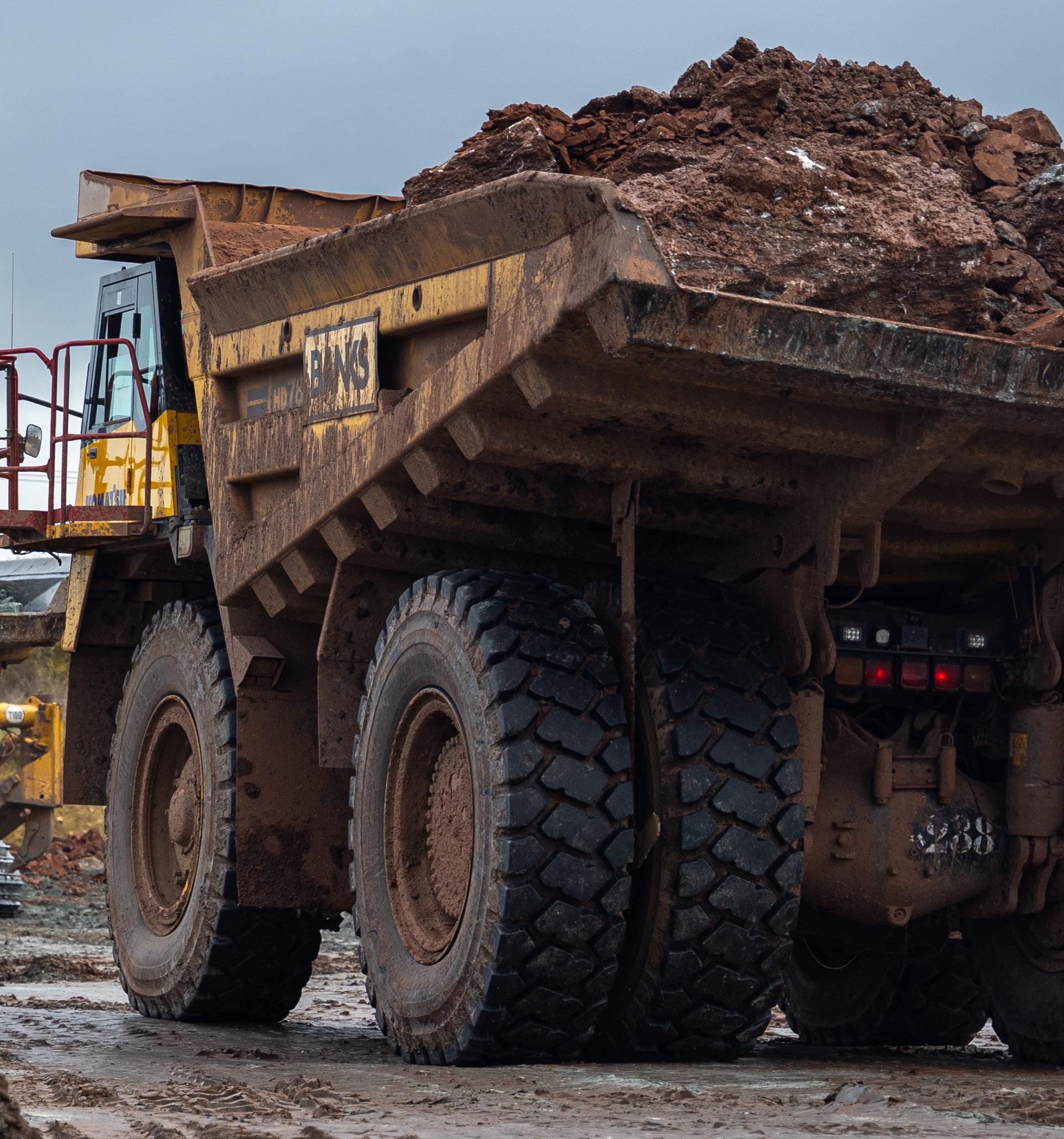
“Bridgestone, together with ORTC, remains committed to continuing to support off-the-road sites around the world, including mines, by supplying customers with high-quality tyres long into the future,” Cole concludes proudly.
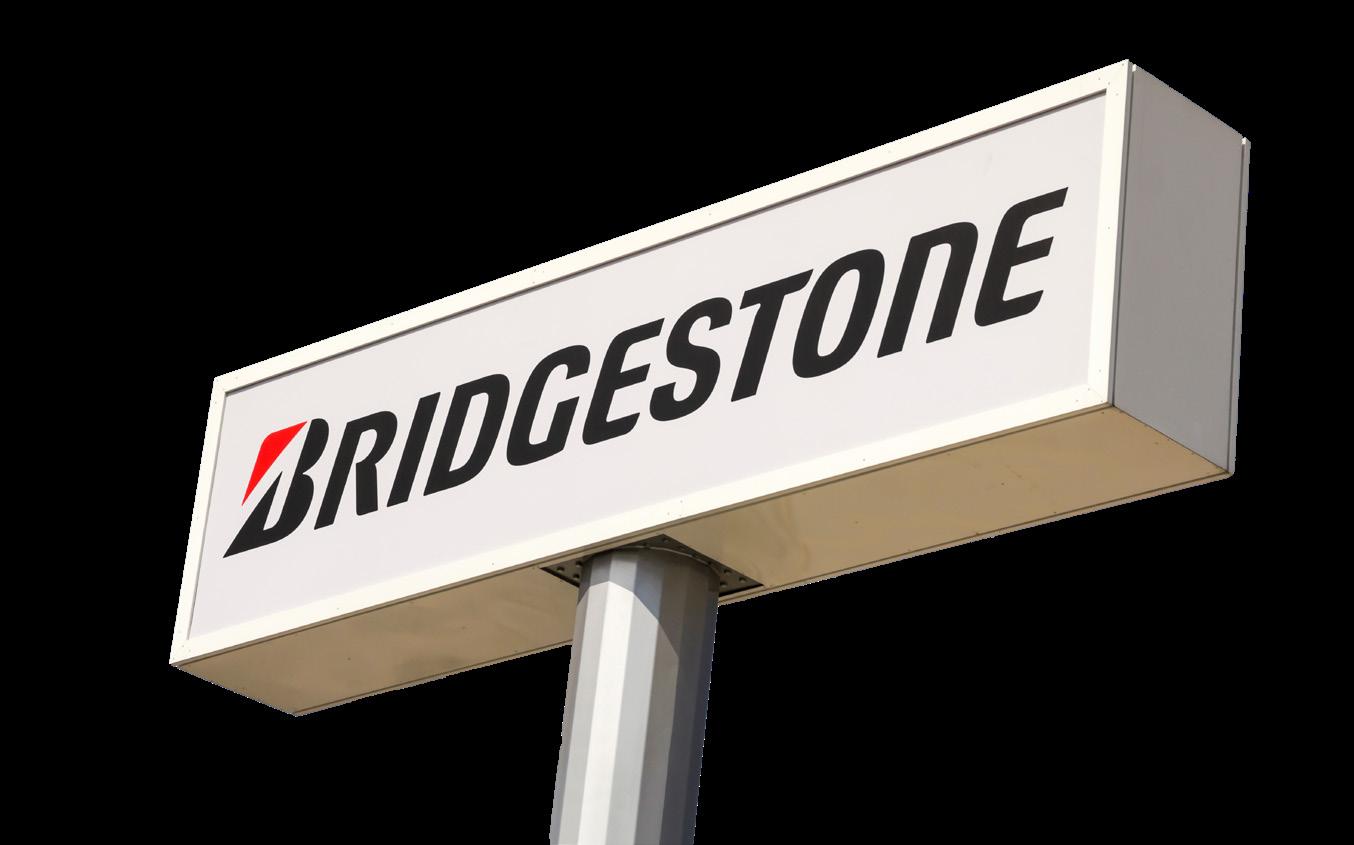

CONCERTS IN A QUARRY
An internationally renowned events venue, Dalhalla is one of the most impressive and beautiful outdoor arenas in Europe – located in a former limestone quarry
Writer: Jack Salter
Every summer, a wide range of events take place at Dalhalla, an eye-catching Swedish open air concert arena that attracts and captivates more than 100,000 visitors a year.
It hosts artists from both Sweden and around the world, spanning various music genres, with the singlenight attendance record of 6,156 set in 2023 by US rock band, Kiss.
This striking destination, seven kilometres (km) north of Lake Siljan
and the municipality of Rättvik in Dalarna, Central Sweden, is uniquely located in the former Draggängarna limestone quarry, where mining ceased in 1990.
Dalarna was struck by a meteor that fell from space over 360 million years ago during the Late Devonian period, creating the Siljan Ring and the surrounding Siljan area.
The impact left quite a mark, with the scar still recognisable even after hundreds of millions of years of erosion
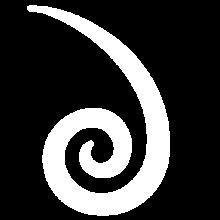

and especially apparent when viewed from above.
With a diameter of more than 50km, the Siljan Ring is the largestknown impact structure in Europe and amongst the 20 biggest on Earth.
The entire bedrock of the Dalarna region was affected by the meteor, forming an intriguing composition of colourful vertical stripes representing various layers of earth and rock, amongst which limestone became easily accessible.
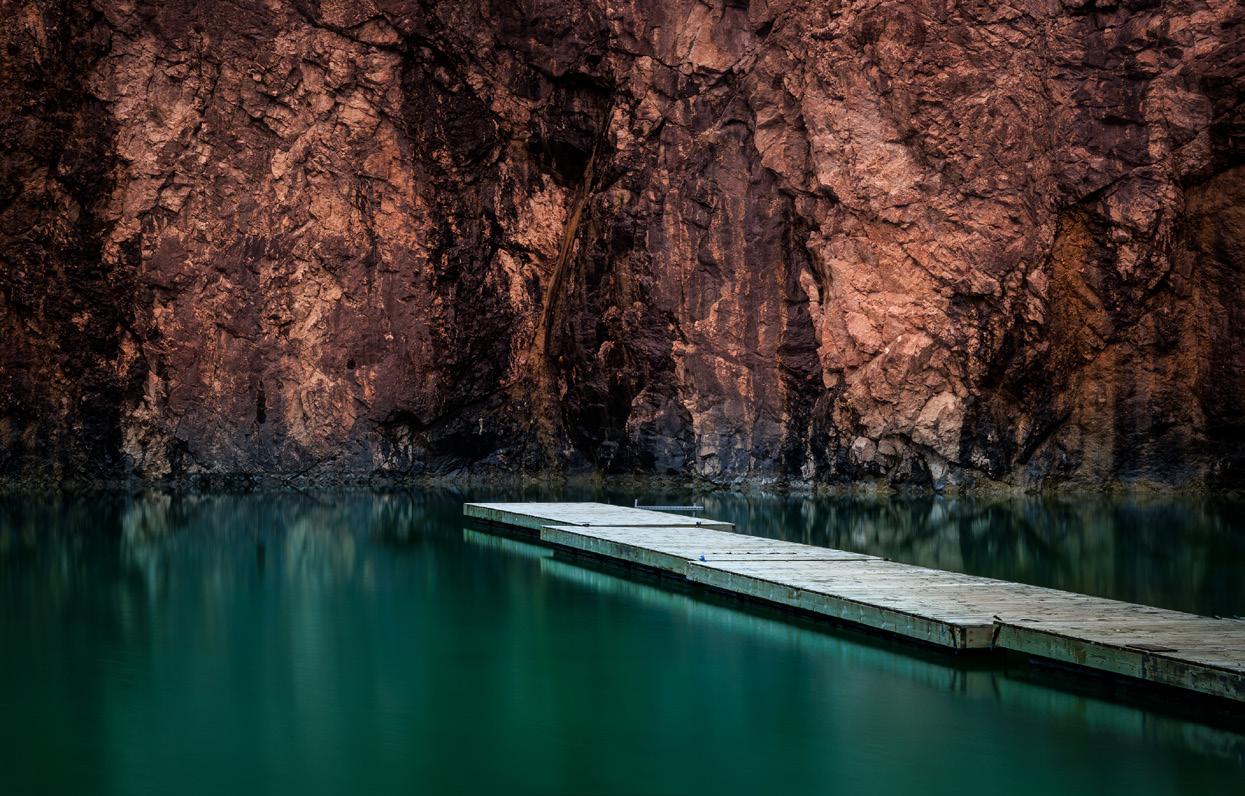
FROM LIMESTONE QUARRY TO ARENA
Over half a century of excavation and blasting at Draggängarna revealed what has now become the foundation for Dalhalla, an acoustically designed arena shaped in measurements that form an idealised golden ratio but in three dimensions.
This stroke of luck places the venue on par with renowned stages from ancient Greece and Italy, as Dalhalla’s dimensions provide excellent resonance and a balanced length of reverberation.
The founder of Dalhalla, Margareta Dellefors, first visited the Draggängarna limestone quarry in 1991 during the Christian holiday, Pentecost.
An ex-opera singer and radio producer, Dellefors had long been searching for a summer festival venue until Åsa Nyman, former Cultural Director of Rättvik, “discovered” the abandoned quarry.
The site was ideally situated far from any settlements, well shielded from disruptive noise, and truly an experience for the eyes and ears.
Astonished by the incredible
acoustics, Dellefors immediately saw the potential to create a music arena on an international level, described as truly exceptional by artists who have performed there.
Its rugged limestone walls prevent sound from becoming too harsh or creating echoes, whilst the design of the audience sections ensures a quality sound experience from any seat, although wind and rain – common in the Swedish summer – can sometimes affect the acoustics.
To take part in Dalhalla’s rich history and geology, from the meteor impact through to today’s concert arena, visitors can embark on a guided tour.
HIGHLIGHT EVENTS
This year marks the 30th anniversary of Dalhalla’s official inauguration on 21st June 1995 in which a grand opera concert was broadcast on Swedish television, making it known throughout the country, with foreign press also covering the event.
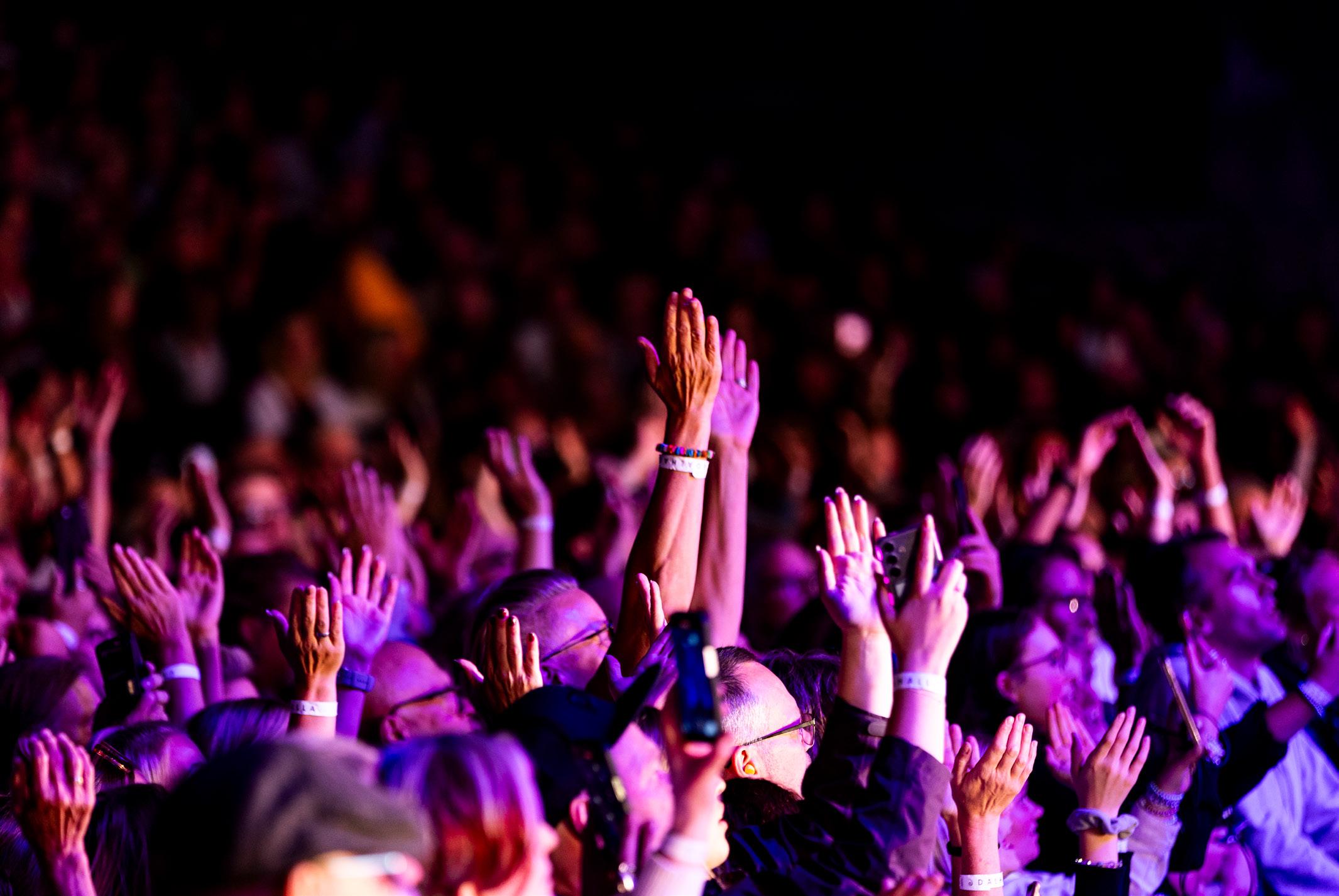
28 concerts were held last year during the summer season, with an impressive average attendance of 3,862 visitors per event.
Highlights in 2024 included a soldout premiere from rock legends ZZ Top to kick off the summer, a first-ever “EPA dunk” performance as Northern

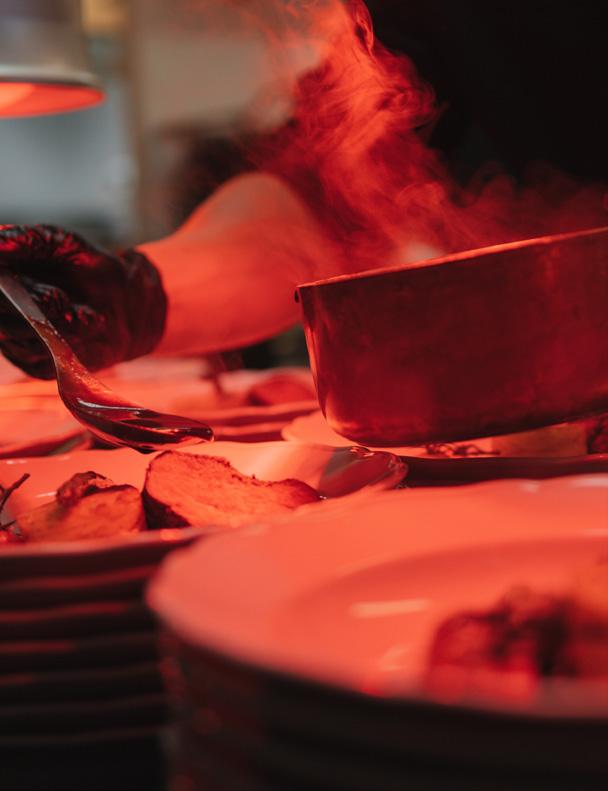
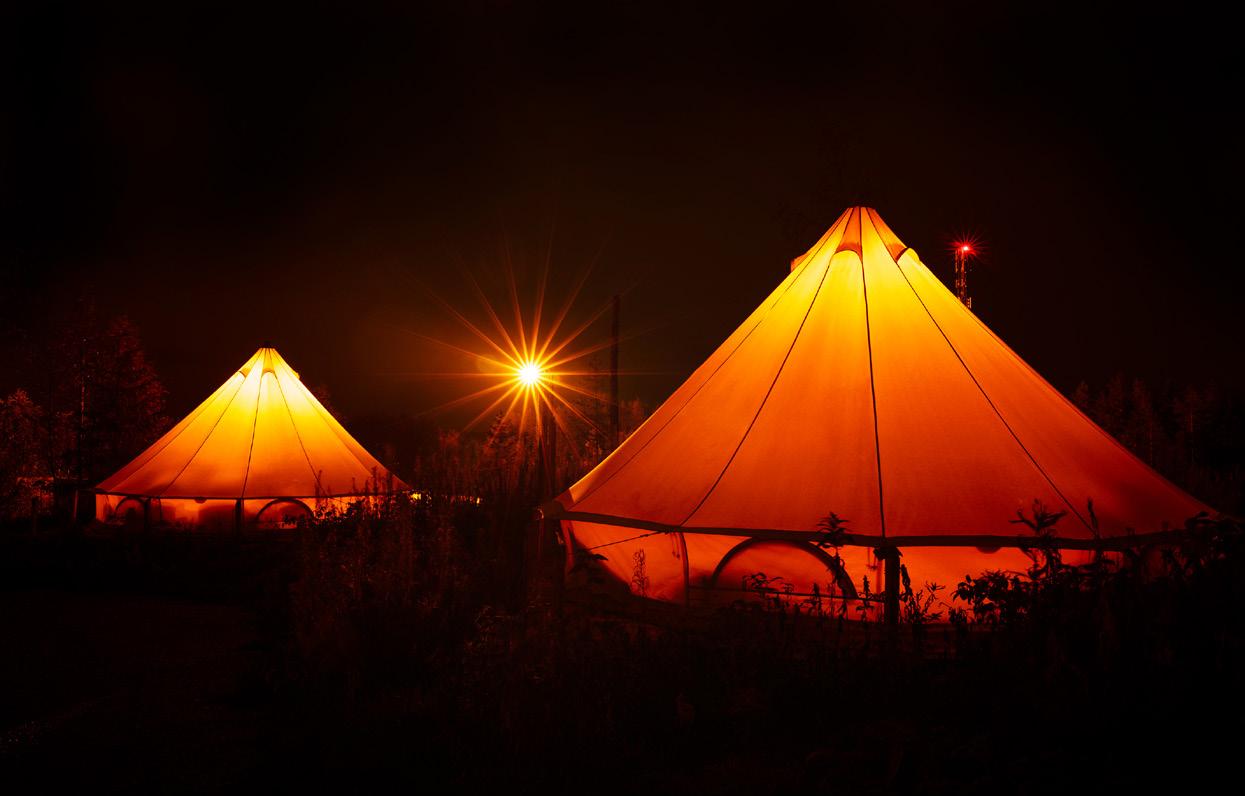
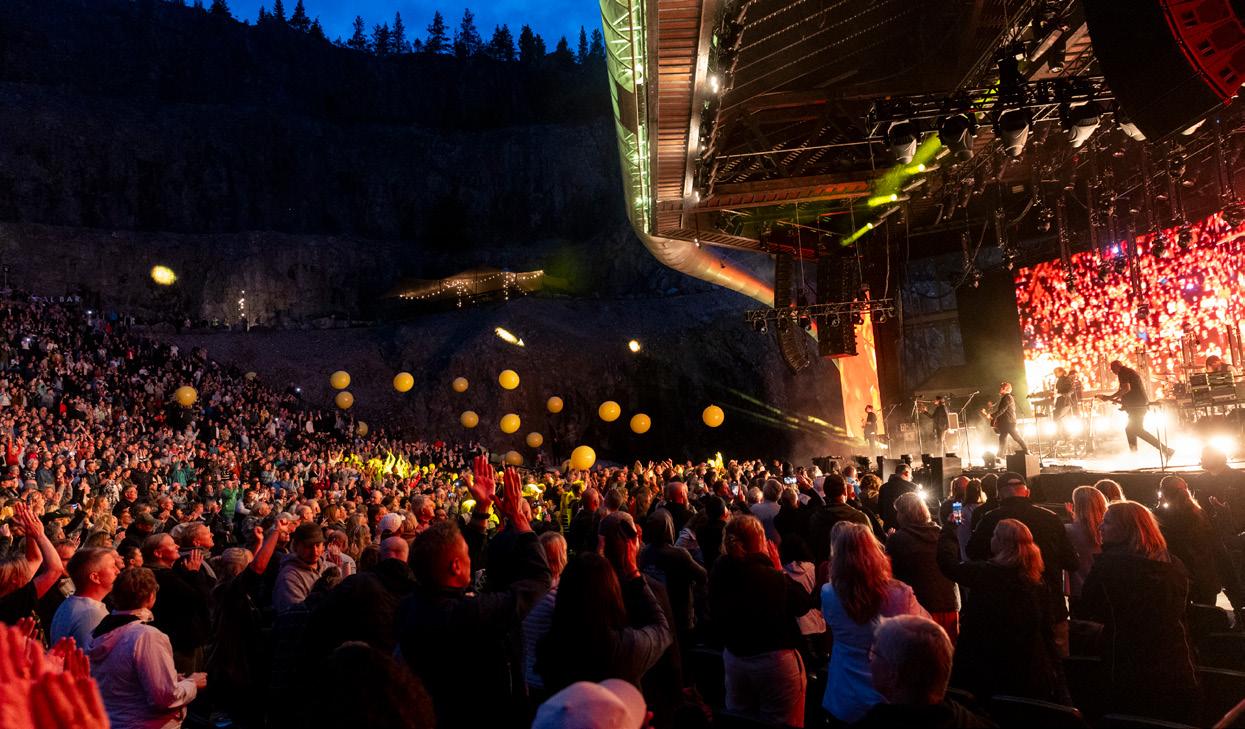
Swedish act Hooja took to the stage, and the return of Gene Simmons with his own band a year after the massive success of Kiss’ performance, reuniting him with many fans.
This summer, there is another extensive range of events on offer from the likes of Daniel Norgren, Avenged Sevenfold, Bryan Adams, Judas Priest, Laleh, Miriam Byrant, Sting, and many more.
Seats towards the front offer closeups of the stage and performers, whereas further back, attendees can experience a view of the unique arena and the surrounding mountain walls. As well as enjoying the surroundings
of Dalhalla and a variety of performing artists, attendees can find fantastic food experiences that cater to everyone’s tastes at the venue, with the Dalhalla Restaurant’s carefully selected menu prepared using the best local and seasonal ingredients.
Alternatively, there is a wide selection of street food available, including pizzas, tacos, burgers, and sandwiches, as well as numerous bars serving a well-crafted selection of beers, wines, spirits, cocktails, and nonalcoholic beverages.
SUSTAINABLE VENUE
As a former limestone quarry
transformed into a spectacular concert venue, Dalhalla is fundamentally a large-scale reuse project.
Today, the arena is tasked with conducting sustainability efforts that allow it to continue to develop whilst also preserving it from both a local and global perspective.
Sustainability is therefore an ongoing effort for Dalhalla, as it works to make improvements for every season.
2024, for example, marked the first year in which no food or drinks were served in single-use plastic as part of active efforts by the arena to reduce plastic usage.
Beverages available for purchase at the arena’s sales outlets also come in polyethylene terephthalate (PET) bottles rather than glass as the material has a lower carbon footprint and is easier to handle and recycle.
Since 2022, only electric vehicles (EVs) have been used at Dalhalla to reduce emissions and contribute to a better work environment, whilst the electricity used is 100 percent green. Such careful and conscious choices are required in order to leave as little impact on the environment and climate as possible whilst making a big impression on visitors.
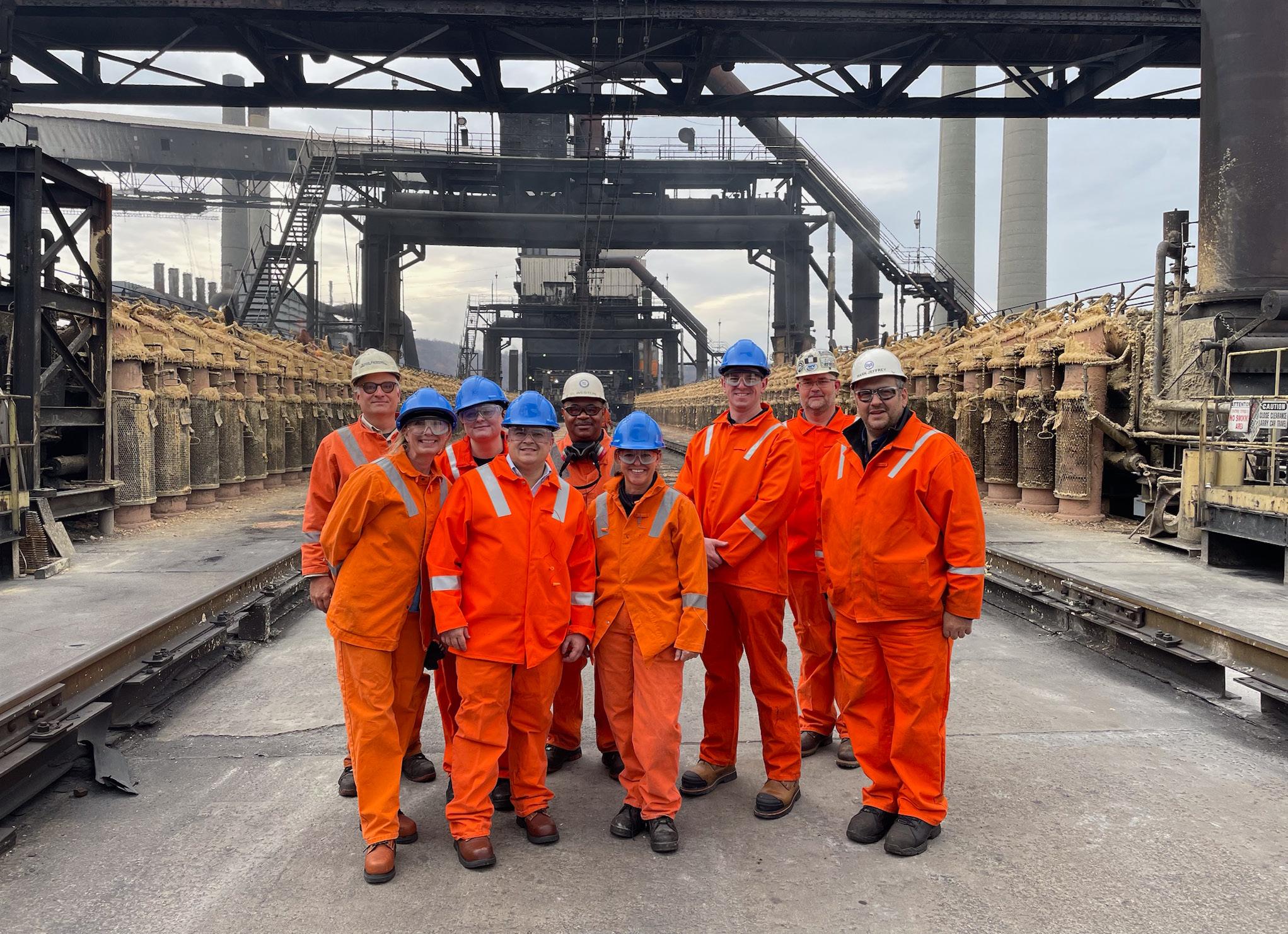
POWER, PROMISE, AND PRIDE
Emily Arthun, CEO of the American Coal Council, highlights the importance of the resource to the US economy and the coal industry’s exciting potential in 2025
Writer: Lucy Pilgrim
Mining Outlook (MO): Firstly, please could you introduce us to the American Coal Council?
Emily Arthun, CEO (EA): The American Coal Council (ACC) was founded in 1982 as a private industry trade group to promote the exports of Western US coal to the Pacific Rim, previously known as the Western Coal Export Council.
The ACC exclusively represents the collective and mutual interests
of the entire coal industry. Its membership includes coal suppliers and consumers, energy traders, coal transportation companies, and support service firms.
We rebranded in 2024 with the establishment of the council’s five pillars, which are the building blocks required for the organization to solidify coal’s stake in an evolving global market. They include:
• Serving our members, stakeholders, and communities
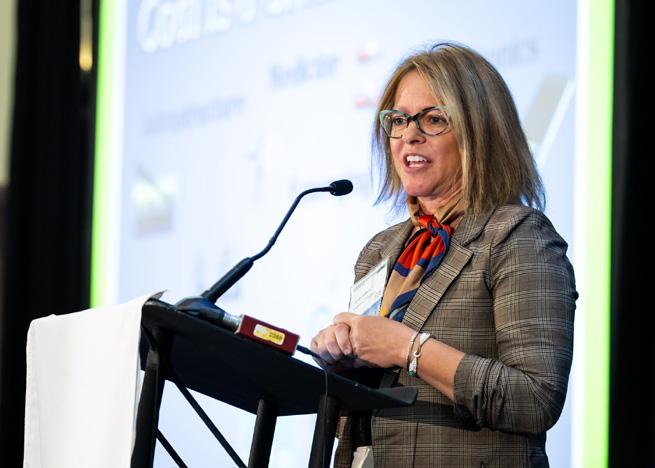
– Support the supply chain with relevant educational options to promote viability and engage with all constituents to build a prosperous future for the industry.
• Championing rigorous, full value chain support – Ensure sustainability along the entire ecosystem to encourage and guarantee progress in coal communities as they fight for sustainable, family-supportive employment.
• Promoting ongoing viability and sustainability – Foster responsible business methods via innovation while preserving the industry’s heritage by working in harmony with viable energy supply chains and local governments, achieving the industry’s potential.
• Advocating awareness, education, and policy – Advocate for the industry and build the supply chain via facts and data in the face of inaccuracies, while also collaborating to educate, promote, and preserve its place as a cornerstone of our nation’s economy and for the industry’s various stakeholders.
• Encouraging advancements, innovation, and cooperation –Build a future where coal maintains its integral role in a broad global economy, facilitate data-based solutions to issues, and invest in modern methods of production while inspiring continued innovation.
MO: What is your current take on the US coal industry? Is it particularly exciting or challenging to work in?
EA: Coal is a critical resource as it provides fuel for the electrification of our lives, resulting in everyday comforts.
Coal also provides coke that allows for the manufacturing of steel, and with it, the building of cities, automobiles, ships, and planes. It additionally facilitates many of the materials used in our high-technology products, from carbon foam to graphene and beyond.
Coal is additionally used in the manufacturing of rockets that take our astronauts into space, and it is a basic component of everything from bowling balls to modern medicine.
In the US, the dismissal of this resource by the Obama and Biden administrations has been a tragedy, jeopardizing the well-being of
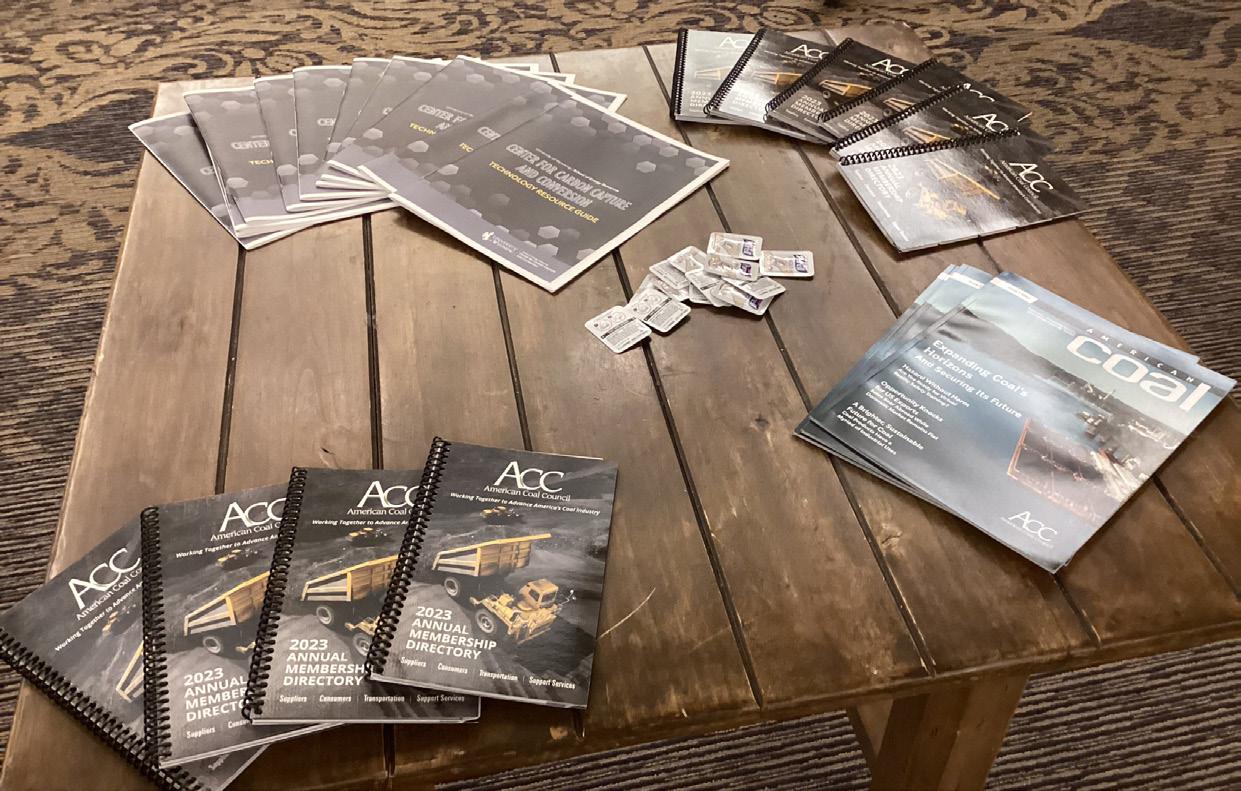
“THE REALITY IS THAT MANY STILL DO NOT FULLY UNDERSTAND THE ESSENTIAL ROLE COAL PLAYS IN PROVIDING MORE THAN JUST ENERGY. IT IS INTEGRAL TO MEETING SOME OF OUR MOST BASIC NEEDS AND IT IS TIME TO ENSURE THIS MESSAGE IS HEARD”
–
EMILY ARTHUN, CEO, AMERICAN COAL COUNCIL
US citizens and the economy. As we move on from the Biden administration to a new Trump administration, we have a unique opportunity to reset natural resource policy to one grounded in common sense.
The results of the election show that people across the country are calling for a shift in how we approach energy and industry. There is a growing recognition that affordable, reliable energy is critical for the well-being of our communities and nation.
For those of us in the coal industry, this presents a tremendous opportunity to emphasize the resource’s vital role in not only powering our homes and businesses but supporting our daily lives.
The reality is that many still do not fully understand the essential role coal plays in providing more than just energy. It is integral to meeting some
of our most basic needs and it is time to ensure this message is heard.
Looking ahead, it is exciting to know that we have a favorable federal government that we will be able to work with. The challenge will be to reverse the war on coal narrative and show US citizens that coal is critical to their well-being.
MO: Can you tell us more about how the ACC advances the commercial and professional development interests of members?
EA: The ACC hosts several conferences each year that include in-depth discussions and analysis about coal production, governmental policies, regulations, transportation, generation, and emerging markets, as well as facilitating concentrated networking and business building opportunities with industry leaders.
The second annual Miami Coal Forum, taking place from February 11th-13th 2025, is a partnership with McCloskey by OPIS, a Dow Jones Industrial Average company. This event will focus on all aspects of the coal industry, highlighting North America’s pivotal role in supplying both established and emerging markets.
The Coal Innovation and Market Strategies Conference, happening from August 19th-21st 2025 in Park City, Utah focuses on industry innovations and domestic and international markets, including coal, natural gas, and minerals.
The ACC recognized the importance of federal interactions and has hosted two Day on the Hill events, giving members an opportunity to talk about all things coal with Congress. The third event will be held in the spring of 2025.
MO: Likewise, how does the ACC represent the collective interests of the US coal industry in advocating for coal as an economic, abundant, and environmentally sound critical resource?
EA: The ACC is very cognizant of the diversity of our business members. Therefore, we advocate for coal and find common ground.
To ensure that coal can continue to be a critical resource, there are four key issues:
1. Protecting the nation’s coal supply chain.
2. Ensuring safe and accessible transportation for coal production.
3. Focusing on the affordability and reliability of the electric grid.
4. Promoting and developing the coal workforce.
Protecting the nation’s coal supply chain is crucial, and key to that is permitting reform. It is essential to
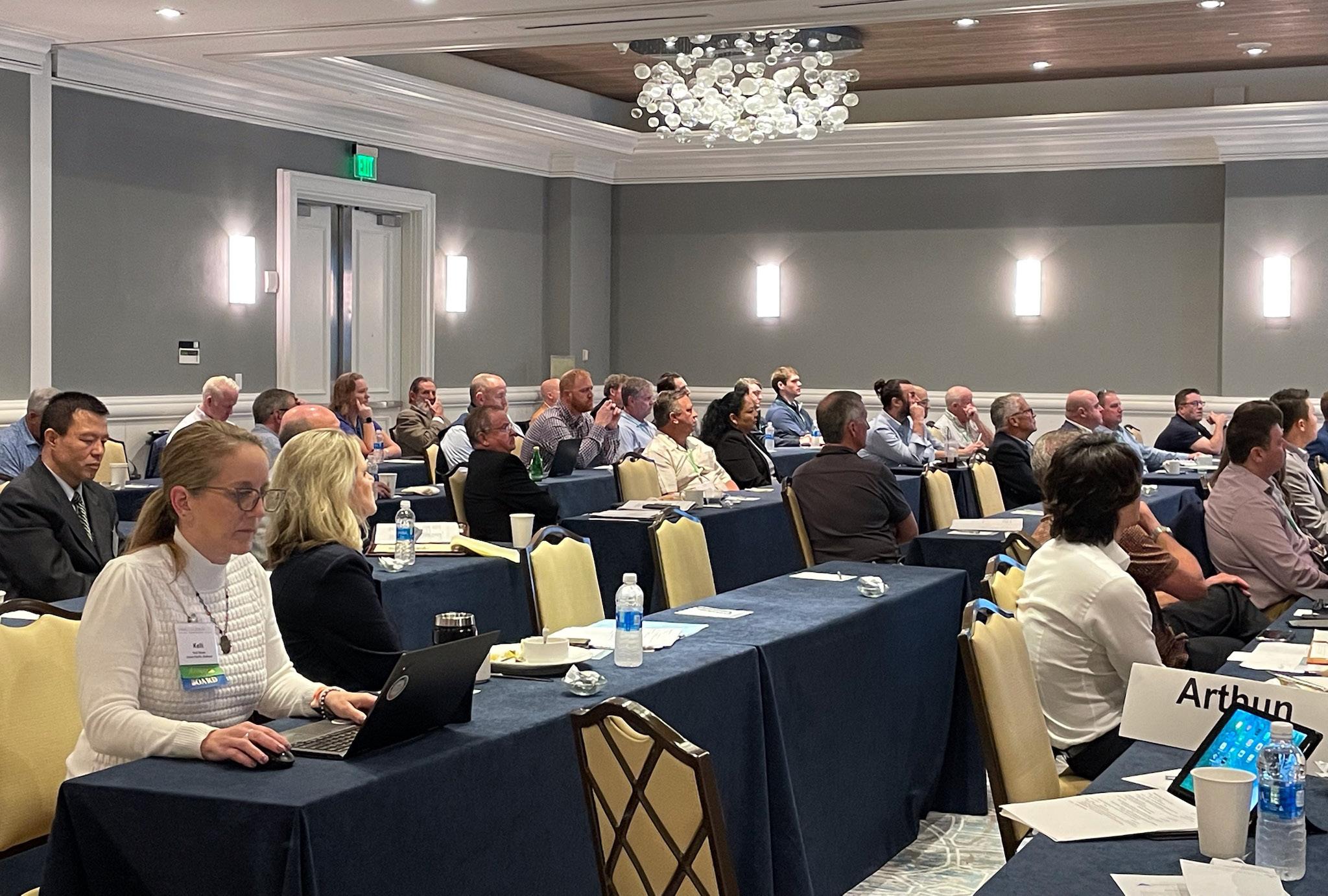
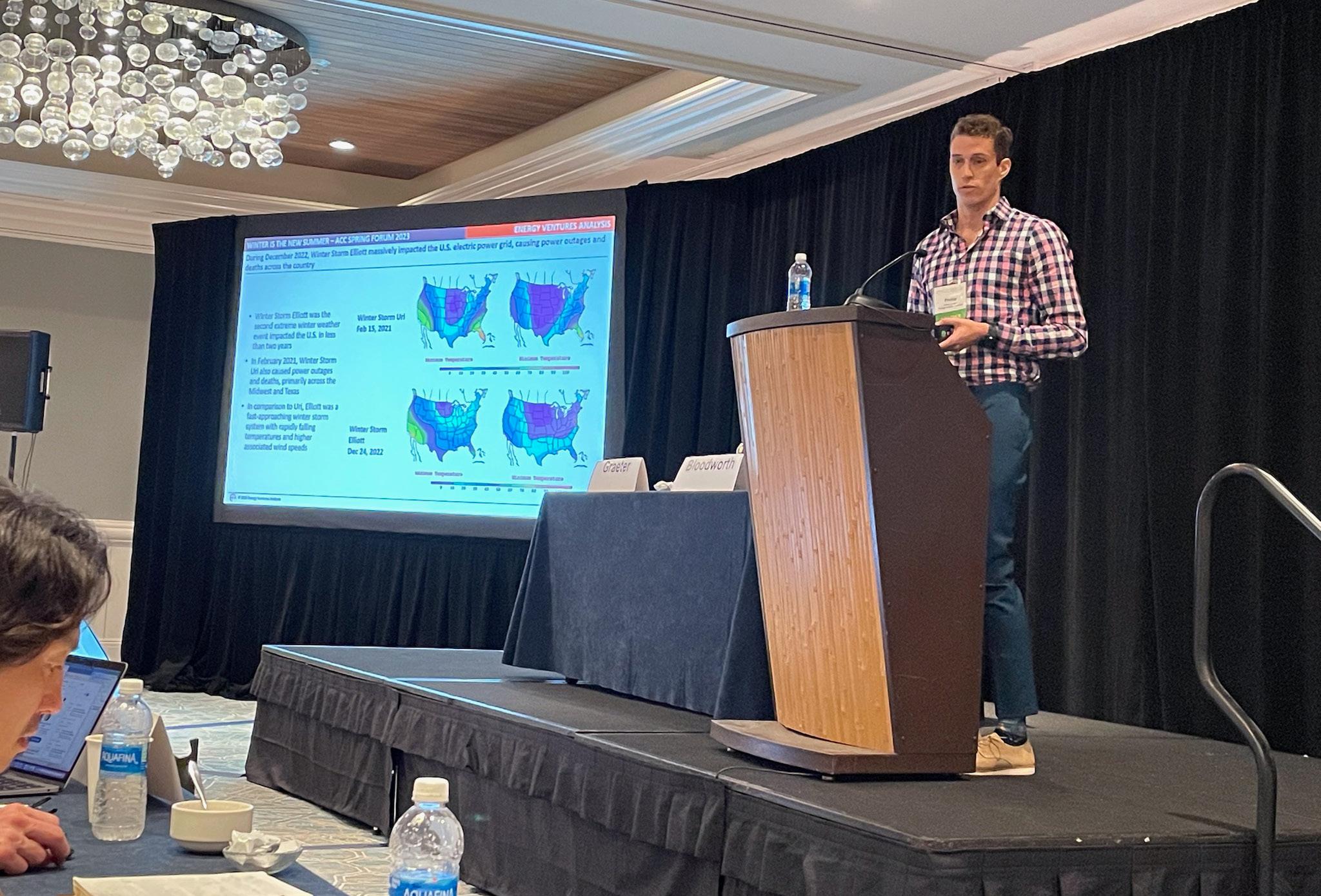
“THERE IS A GROWING RECOGNITION THAT AFFORDABLE, RELIABLE ENERGY IS CRITICAL FOR THE WELL-BEING OF OUR COMMUNITIES AND NATION”
– EMILY ARTHUN, CEO, AMERICAN COAL COUNCIL
streamline the process of obtaining permits and prevent the federal government from revoking existing permits.
Safeguarding and enhancing the transportation infrastructure for coal, encompassing rail access, port and river transport facilities, and roadways, is another key component
in our nation’s energy policy moving forward.
This effort plays a pivotal role in boosting our economic competitiveness by cutting down the expenses associated with coal delivery, thus maintaining the competitiveness of US coal in both domestic and international markets.
The enhancement of transport systems, including railways, ports, and inland waterways, facilitates the efficient and cost-effective access of coal to international markets. Furthermore, the improvement and expansion of transportation systems leads to job creation in various sectors such as construction, engineering, and operations, ultimately benefiting local economies.
Coal plays a crucial role in ensuring electric grid reliability by providing a constant supply of energy that is needed to meet demand.
Unlike some renewable sources, coal-fired plants operate continuously, contributing significantly to the grid even during high electricity demand periods such as extreme weather events.
Moreover, the ability of coal plants to maintain large fuel stockpiles on-site enhances their resilience to supply chain disruptions, ensuring price stability in the electricity market. This reliability instills confidence in the energy system’s capacity to meet future demands, benefiting industries and consumers alike.
The US workforce is essential for addressing the shortage of trade skills in fields like welding, mechanics, and electricians.
MO: What makes the ACC an essential resource for industry, policymakers, and public interest groups?
EA: I see an organization that over the last two and a half years has taken
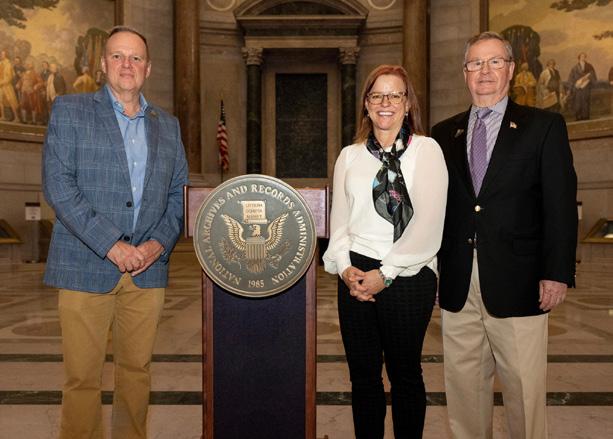

significant steps to shape the future of coal.
The ACC has become more active on social media, published op-eds, launched a grassroots election video campaign supporting coal, and witnessed a resurgence in attendance at our conferences.
Personally, I’ve spent time traveling, discussing coal, attending meetings in Washington, D.C., engaging with members at conferences, and touring our exceptional supply chain.
Now more than ever, it is crucial for the ACC to be bold in its commitment to the coal industry as we have laid a strong foundation to become the leading advocate for the resource.
2024 began with a fresh look and a renewed dedication to our industry. Our rebranding was met with enthusiasm as we embraced the past, present, and future of coal, boldly proclaiming that we’re “Proud To Be American | Proud To Be Coal” with a clear vision to champion our industry, product, and people.

MO: Finally, what are the AAC’s key priorities in order to continue representing the interests of the nation’s coal industry?
EA: Our country is fortunate to have some of the world’s greatest natural resources, which if properly managed can contribute to both energy and economic security worldwide.
Coal is, and must remain, one of those resources. The natural resource community must work together for the best outcome for our nation’s citizens. Whether you drill, mine, harvest, or grow a natural resource, the time to be bold and find a common message that all natural resources will need for a vibrant, strong world is now.
We must clearly communicate the importance of coal and its role in securing our nation’s future. Celebrate this amazing industry by telling everyone how proud you are to be part of coal.
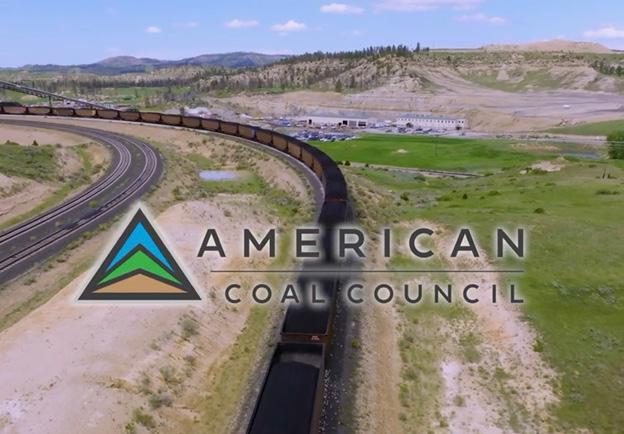
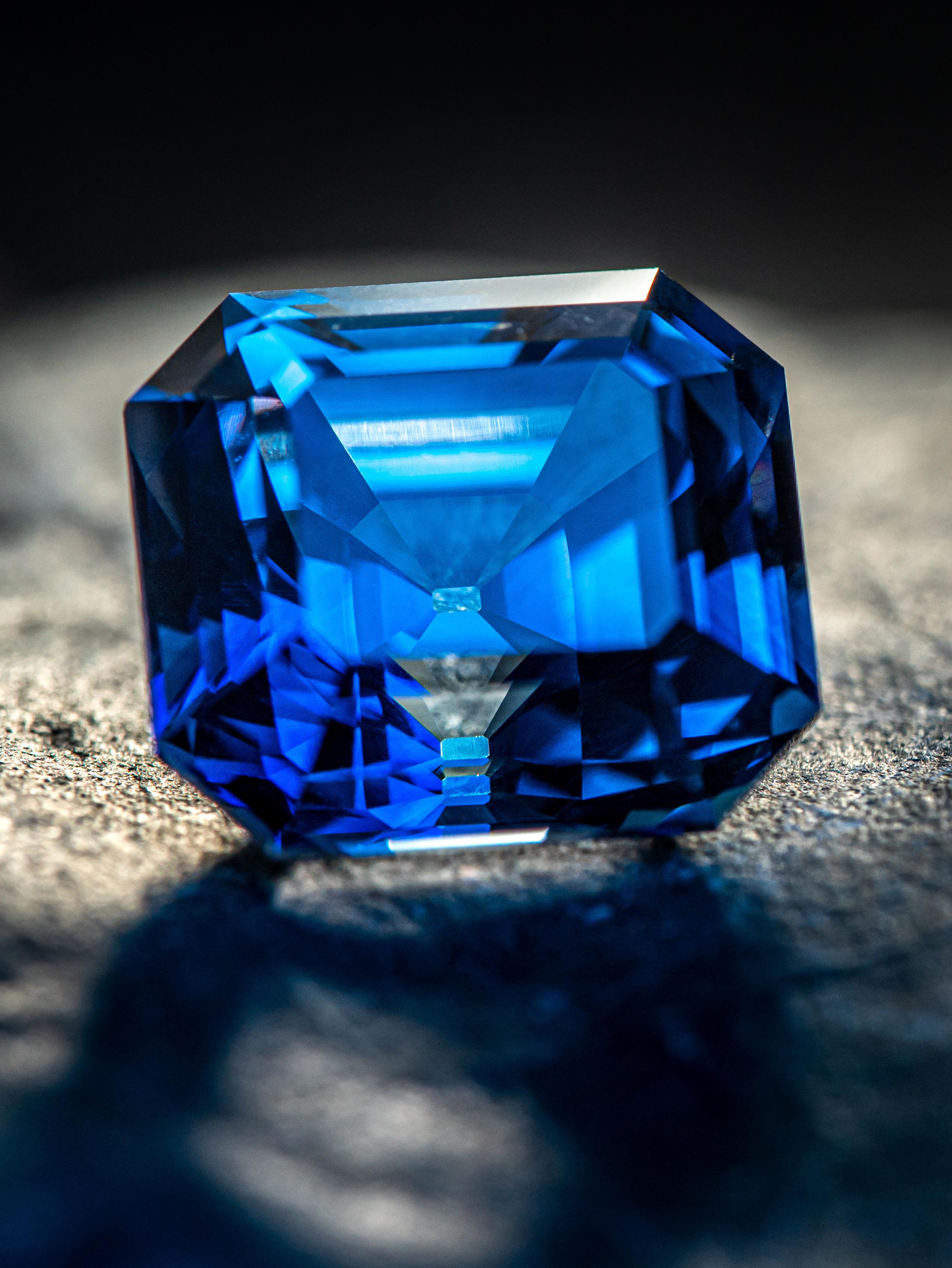
CELESTIAL SAPPHIRES
As one of the many ores recovered by mining, the sapphire gemstone is traditionally connected to the sky, but its roots began firmly in the ground in Kashmir, India
Writer: Rachel Carr
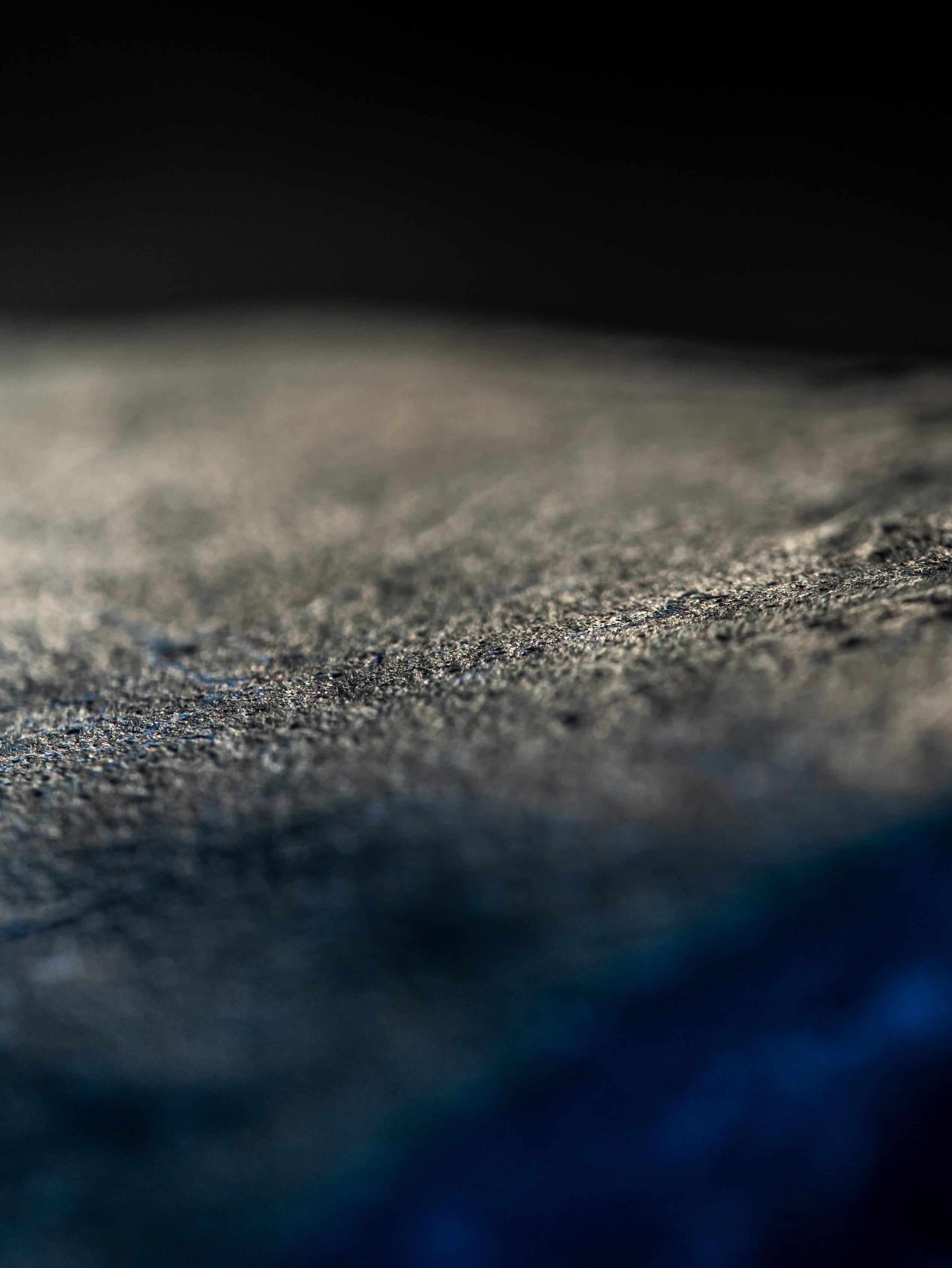
Sapphires have been mined for centuries, but occasionally new deposits are discovered that capture the attention of the mining world and gemstone market. Traditionally, mines in Kashmir, Myanmar, and Sri Lanka produced the world’s highest-quality sapphires. Whilst two of the three locations remain, the last sapphire was mined in Kashmir in 1927. The gems are now mined in myriad places across the globe, and fascinatingly enough, they are not all blue; two of the rarest colours, padparadscha and cornflower blue,
were found high in the Zanskar Range of the Himalayas, although some of the most interesting colours hail from Africa.
MINING MAP
Along with its notoriety for diamond mines, Africa has emerged as having a wealth of sapphire supplies. Rwanda, Malawi, Laos, Cambodia, Cameroon, Kenya, Ethiopia, and Mozambique all harbour the precious gemstones. Nigeria, however, is the most important West African producer of sapphires, which have been mined in the central part of the country for around 30 years.
In 2014, Nigerian sapphires caused waves in the industry after the discovery of a substantial number of high-quality sapphires, which were recognised for their attractive size, high clarity, good colour, and strong crystal habit.
Southern Madagascar joined the sapphire mining map in the late 1990s when an unusually large deposit was discovered in the small town of Ilakaka.
Australia, Thailand, Myanmar, China, Vietnam, Afghanistan, and Columbia are also part of the mining map, alongside Tanzania which acquires
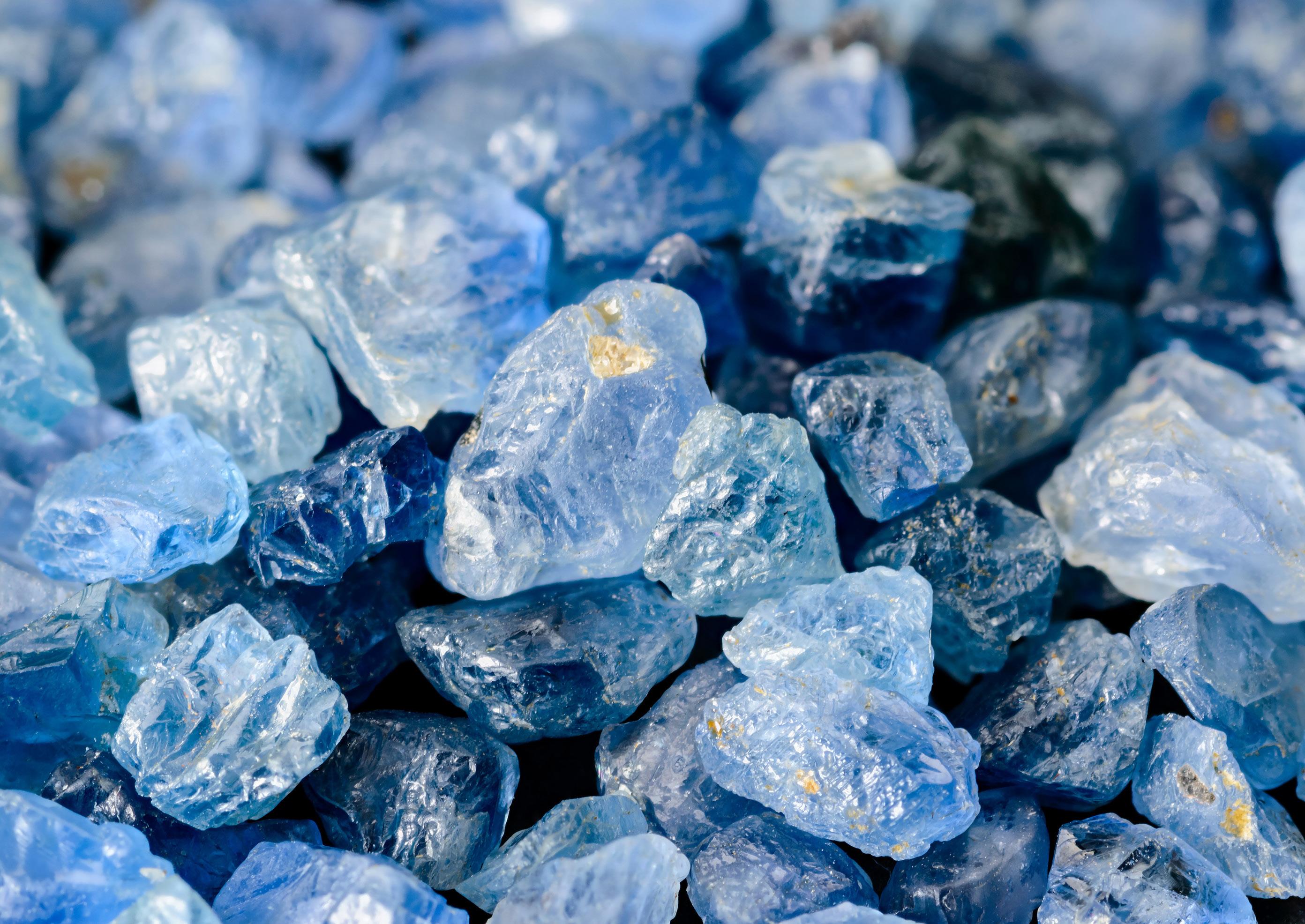
many of its rarer gems from the Umba River Valley.
The gravel area has yielded sapphires of all shades including the highly valued padparadscha colour. Although Songea is the most productive sapphire mining region in Tanzania, recent discoveries near Kibuko have produced pink sapphires of up to 100 carats.
MONTANA ROCKS
Montana is the only source of sapphire mining in the US, and its nickname ‘The Treasure State’ is for good reason due to its abundant natural and mineral resources.
The sapphires were initially a by-product of the gold rush of the 1860s, but recently, the deposits throughout Montana have surrendered high-clarity sapphires, which are extremely unique as they have no cavities.
SAPPHIRE SECRETS
• Sapphires score nine out of 10 on the Mohs scale for durability, third behind diamonds and moissanite, respectively.
• Besides jewellery, sapphires are used to create Swiss timepieces, Apple watches, scientific instruments, and high-durability windows.
• Yellow sapphires are caused by the presence of iron without titanium.
• The largest cut and polished sapphire is the Millennium Sapphire, with a weight of 61,500 carats.
The most precious sapphires are the ones found in the Yogo Gulch area, located in the Little Belt Mountains of Montana, which unlike many other sapphires are igneous rather than metamorphic.
These unique gems are considered some of the finest in the world. Visual properties include an even colour of cornflower blue, as a result of trace amounts of iron, but they are also found in shades of violet and purple. Other distinguishable features lie in the trace element concentrations with elevated levels of magnesium and titanium content.
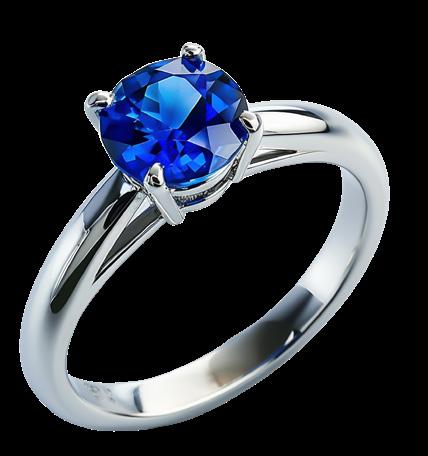
ROMANCING THE STONE
In 1865, a prospector named Ed R Collins discovered Montana sapphires had value when he sent samples to Tiffany & Co.
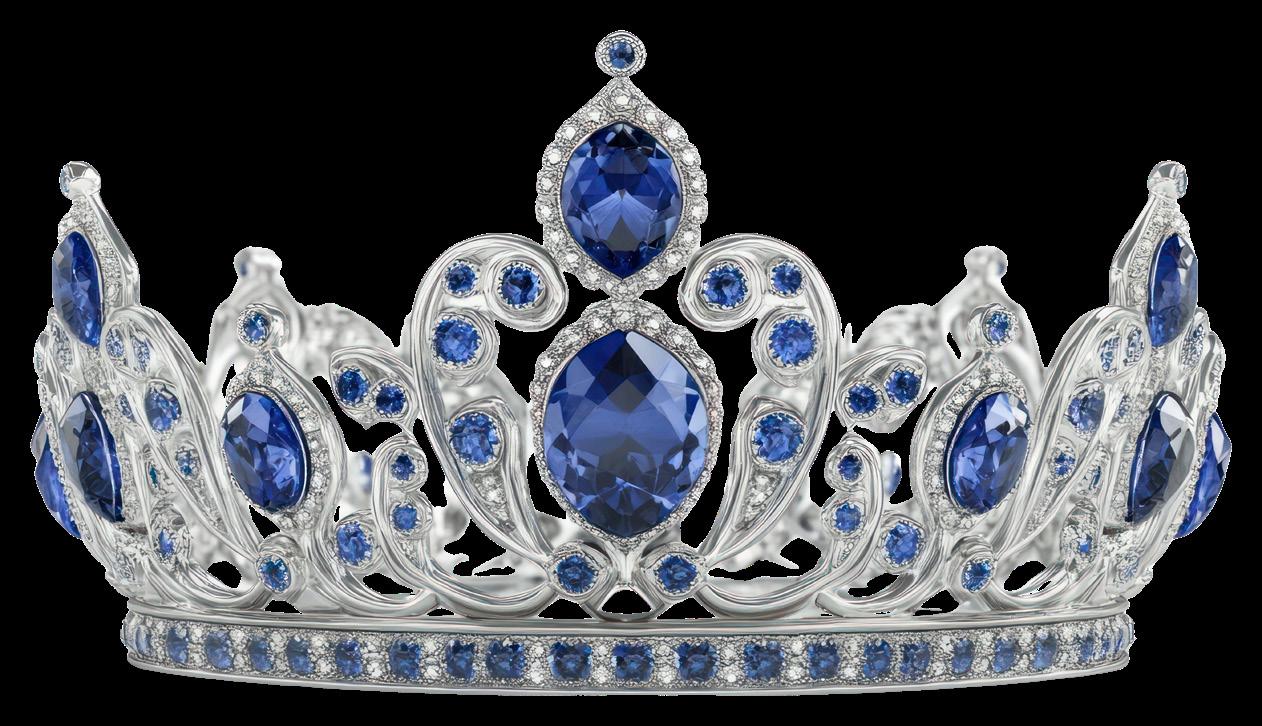
The jewellery company declared that the gems were “sapphires of unusual quality”, and a small sapphire rush began.
Famed for their clarity and brilliance, many Montana sapphires are used for engagement rings. In fact, the gems enjoyed a renaissance from the Princess Diana effect when she received a stunning 12-carat sapphire engagement ring, worth almost USD$400,000 today. It is now known
that the oval sapphire is of Sri Lankan origin.
Other famous sapphires include The Star of Adam, worth a staggering USD$300 million, and the Stuart Sapphire, which is set into the Imperial State Crown of England. However, the world’s biggest star sapphire cluster was uncovered in Ratnapura, Sri Lanka. Weighing in at 2.5 million carats, it is known as the Serendipity Sapphire.
ETHEREAL AND ETHICAL
Sri Lanka has been mining sapphires for almost 2,000 years with little change to its mining operations or construction.
Mined in primarily alluvial deposits using the tunnel mining method, the operations are small scale and the gems ethically sourced.
Larger projects are restricted to minimise the environmental impact and ensure the longevity of the supply, and open pit operations are permitted providing that the area is revegetated.
The Sri Lankan government does not allow environmentally or economically unstable mining activities. Sapphires are generally mined from less troubled communities across the mining map and therefore more ethical and ecofriendly than other gemstones, with traceable beginnings.
Coupled with their vivid colours, these details make them one of the most sought-after gems around the world.
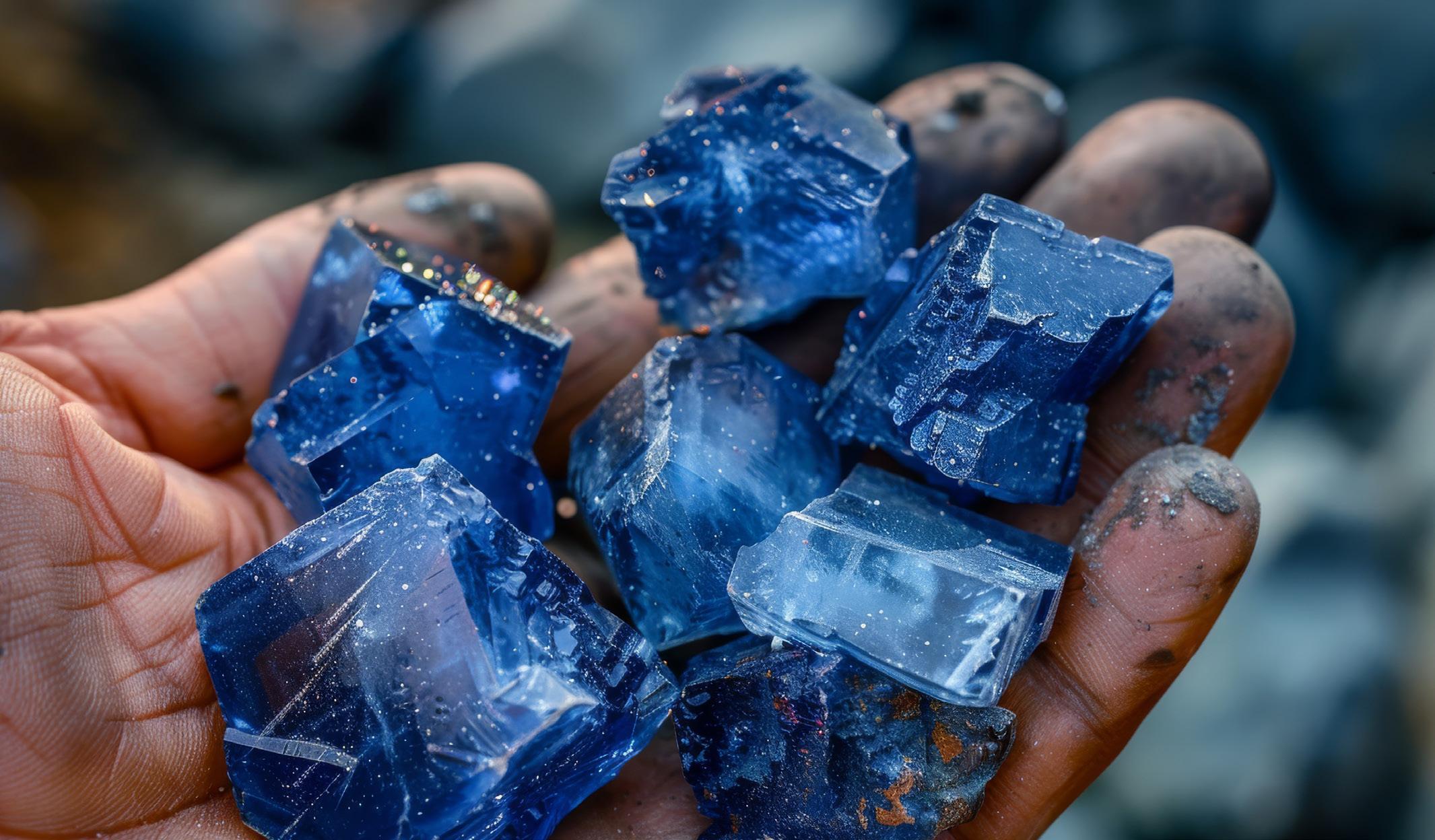
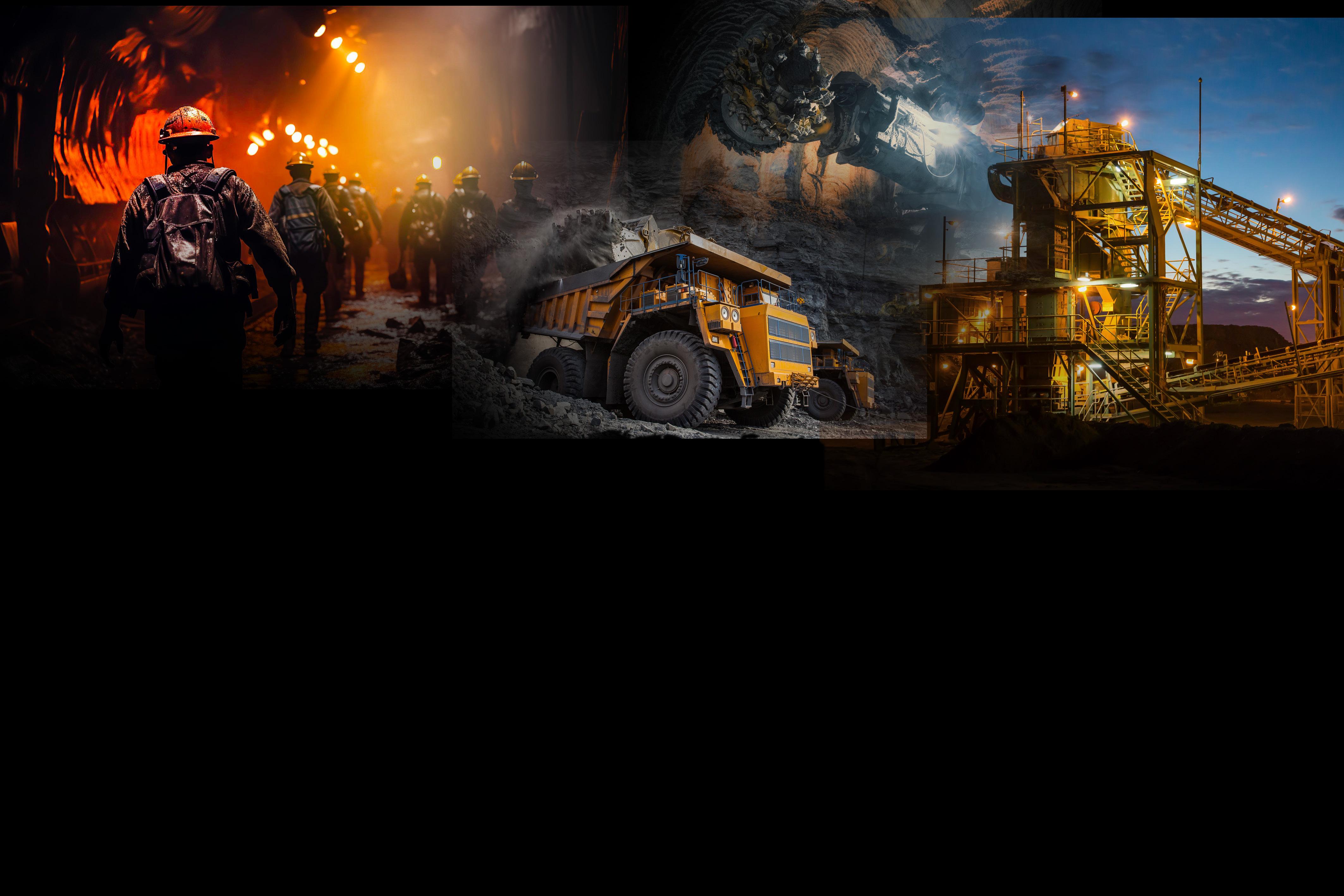
Discover our exclusive content, delivered straight to your inbox
As mining organisations worldwide confront unprecedented change, embracing technological innovations and incorporating critical environmental sustainability agendas, now more than ever is the time to showcase the strides being taken in this dynamic sector.
A multi-channel brand, Mining Outlook brings you the positive developments driven by organisations across the global mining industry through its various platforms.
Discover exclusive content distributed through its website, online magazine, social media campaigns and digital dispatches, delivered straight to your inbox with a bi-weekly newsletter.
Through these compelling media channels, Mining Outlook continues to foreground the movers and shakers of the industry.
To participate as a featured company and join us in this exciting endeavour, contact one of our Project Managers today.
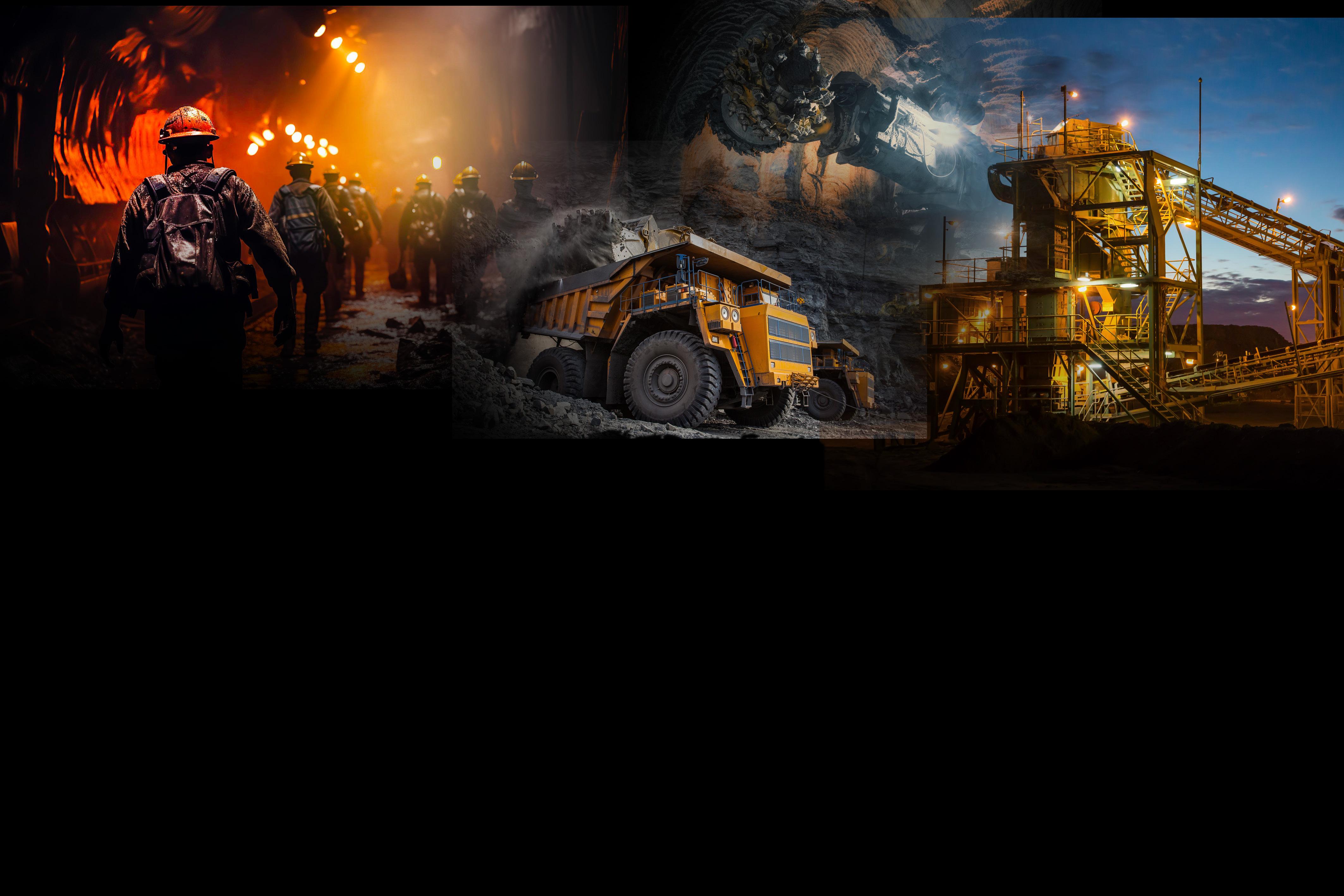
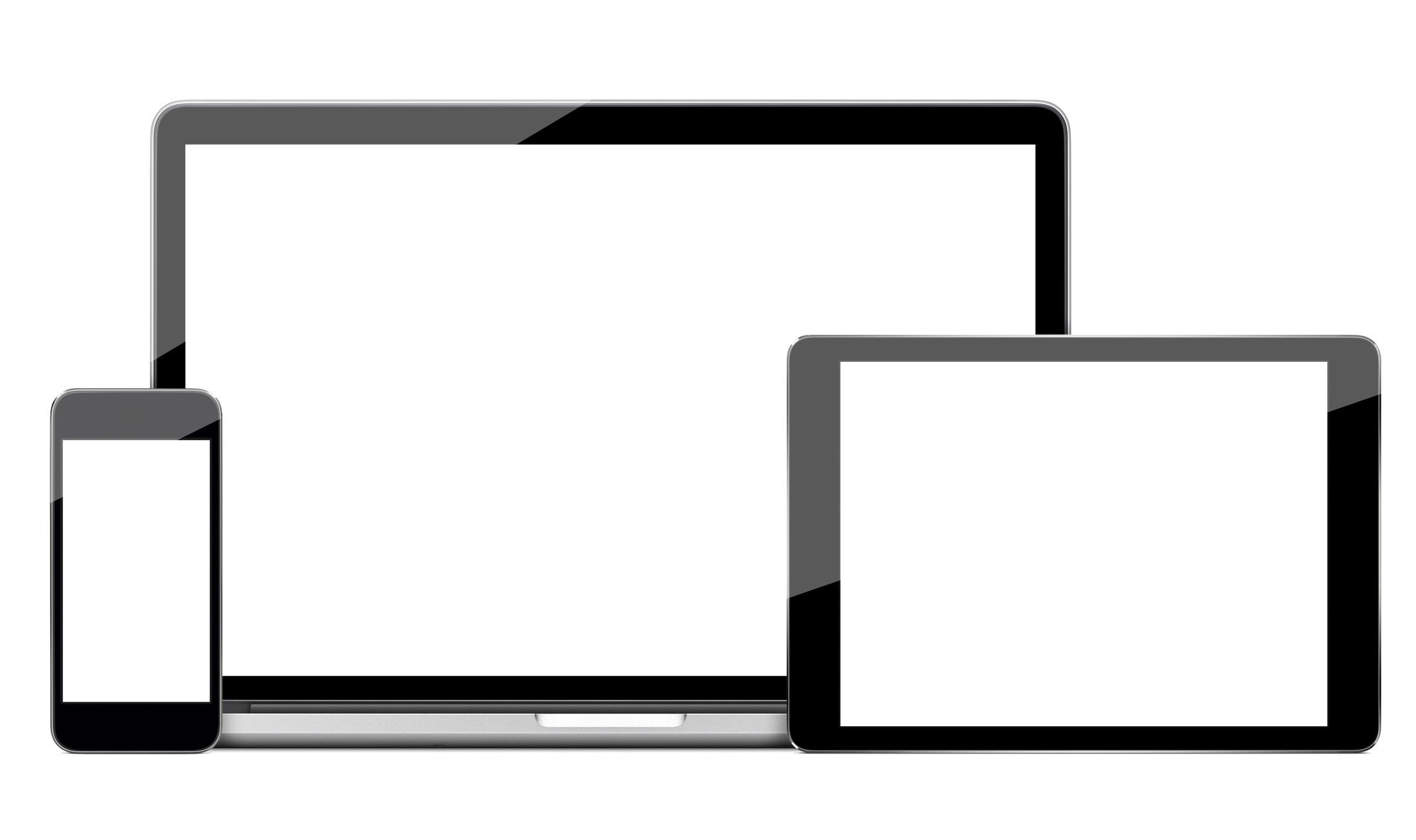
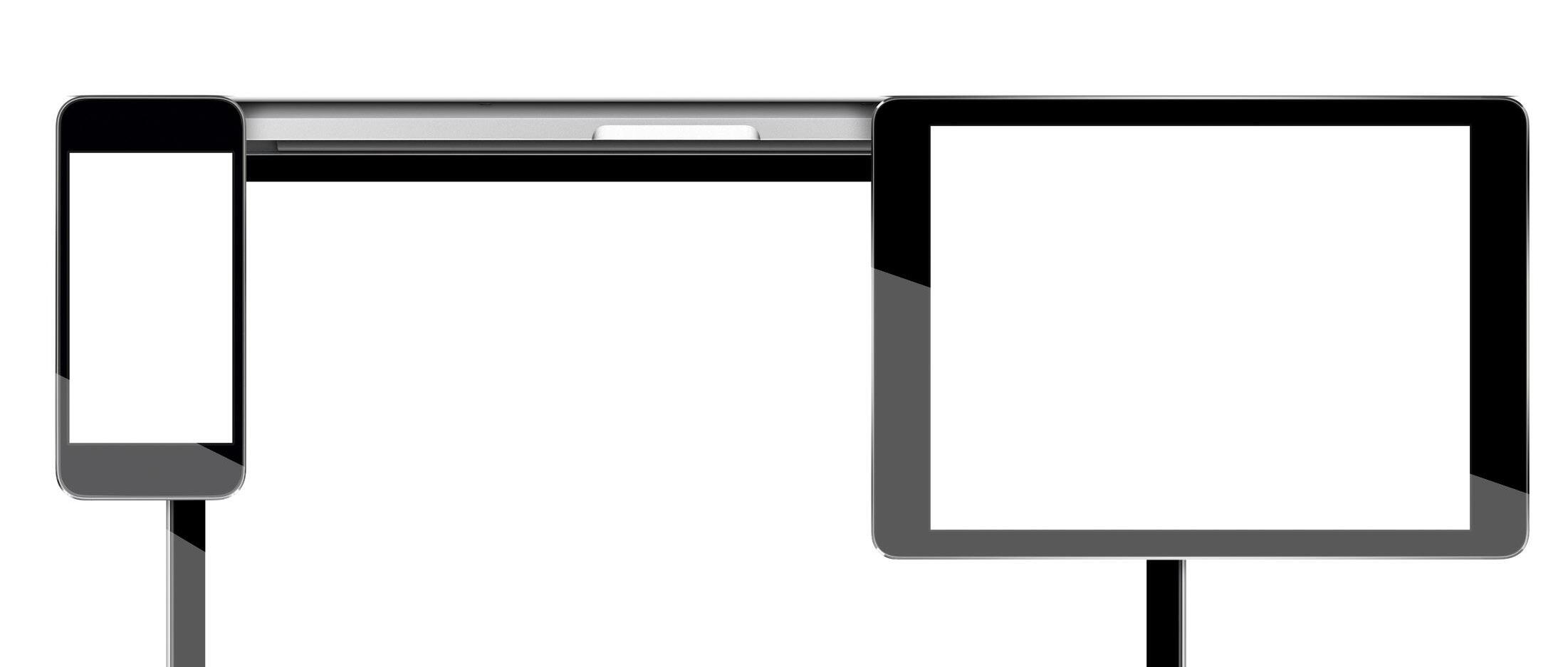
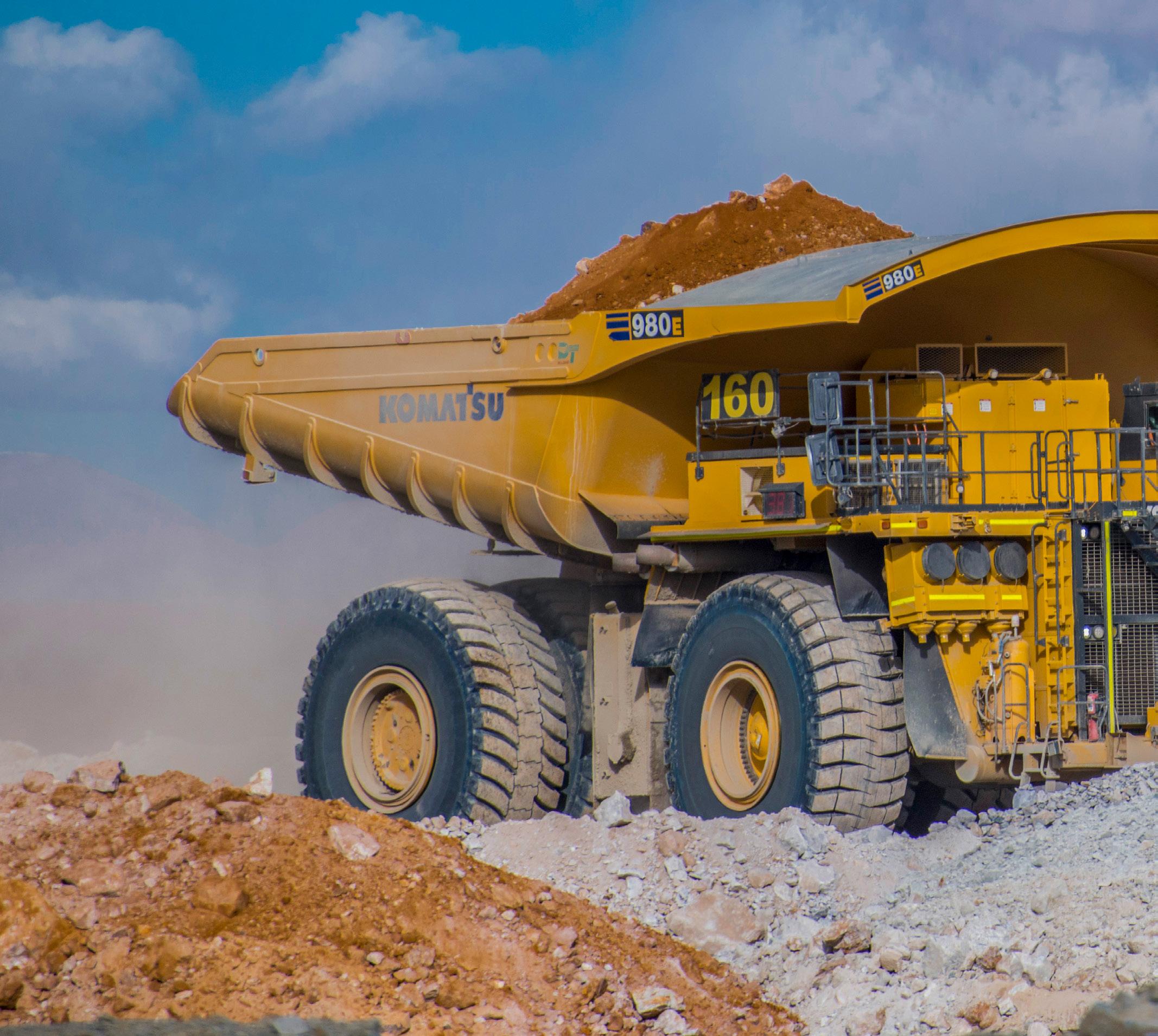
THE HOUSE OF THE
MINER
Collahuasi’s executive team comes together to discuss the company’s extensive contribution to Chilean mining and mineral production –particularly as resources such as copper become increasingly critical within the global energy transition – while emphasizing its role in supporting local communities and economies
Writer: Lily Sawyer | Project Manager: Lauren Robinson

Chile, the distinctive ribbon of land that runs along the west coast of South America, is a curiously shaped country abundant with vast natural landscapes – from the rolling sands of the Atacama Desert, the driest non-polar desert in the world, to the peaks of the Torres del Paine National Park.
The vibrant capital of Santiago, meanwhile, is a bustling urban metropolis that perfectly juxtaposes against this tranquility.
Among its beautiful landscapes,
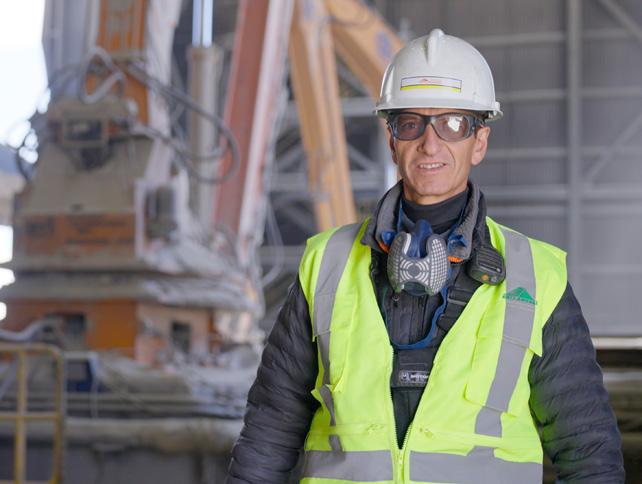
Chile is also the world’s largest producer of copper, responsible for around a quarter of global production.
Bordering Peru and Bolivia, the Tarapacá region in the north of the country demonstrates Chile’s longstanding tradition as an epicenter for mining and mineral production.
In fact, many abandoned mining towns can still be found in the area, offering an insight into the region’s historical economic significance and the ways in which vital mineral resources were fought over in the War of the Pacific.
Today, Tarapacá remains home to numerous significant mining operations and some of the world’s most desired resources, including copper and naturally occurring sources of sodium and potassium nitrate.
Chilean mining company, Collahuasi, meaning ‘the house of the miner’ in the local Aymara language, boasts an extensive operation located in Tarapacá.
As one of the world’s primary copper producers and the second largest in Chile, Collahuasi is renowned for the extraction and production of copper and molybdenum concentrate.
Diligently mining its two major deposits, Rosario and Ujina, the company contributes significantly to the country’s gross domestic product (GDP) each year.
A BRIEF HISTORY
Collahuasi’s origins date back to the second half of the 19th century, when commercial exploitation of highgrade copper-silver veins began in Tarapacá.
However, mining activities in the area were interrupted in 1930 with the arrival of the Great Depression, only recommencing in Collahuasi’s current area of operation in 1978 after key features of the Rosario deposit’s exceptional copper grades were identified.
13 years later, the adjacent Ujina deposit was discovered, with the feasibility and environmental impact studies for its exploitation approved in 1995 and commercial operation commencing in 1999.
“In 2003, we more than doubled our sulfide ore treatment capacity, increasing our output from the initial project’s 60 thousand tons per day (ktpd) to around 130ktpd,” introduces Jorge Gómez, CEO.
Since then, various process optimizations have delivered an
increase in capacity, equating to around 155ktpd in 2023.
Two years prior, the company also obtained the environmental permits required to extend the operation for 20 years and increase its ore treatment capacity up to 210ktpd.
Today, Collahuasi has an installed capacity of 170ktpd, with other debottlenecking projects in the process of implementation or under review to increase this capacity further in the coming years.
In terms of production and distribution, a 203-kilometer (km)long system of slurry pipelines transports copper concentrate from the company’s concentration plant in Ujina to the Collahuasi Maritime Terminal in Punta Patache, 65km south of the city of Iquique.
From this facility, where the

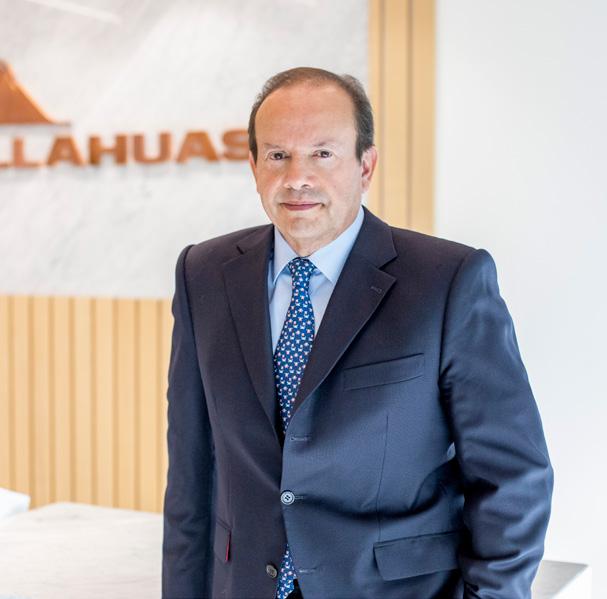
company’s molybdenum and concentrate filtering plants are also located, products are shipped to international markets – primarily China and other parts of Asia.
2023 saw Collahuasi record C1 costs of $1.27 per pound of copper, positioning the company in the first
“COLLAHUASI’S FOUNDING PRINCIPLES ARE FOCUSED ON THE RESPONSIBLE AND EFFICIENT DEVELOPMENT OF RESOURCES –FIRST AND FOREMOST, THE SAFETY OF OUR WORKERS, RESPECT FOR THE ENVIRONMENT, AND THE SUPPORT OF OUR LOCAL COMMUNITIES”
–
JORGE GÓMEZ, CEO, COLLAHUASI
quartile of the industry.
Its direct and indirect economic contribution to the Chilean economy during the same year was equivalent to 1.34 percent of national GDP and 56.31 percent of GDP in the Tarapacá region.
In addition, Collahuasi generated a significant contribution to the country
through tax payments of $809 million.
“Collahuasi’s founding principles are focused on the responsible and efficient development of resources – first and foremost, the safety of our workers, respect for the environment, and the support of our local communities,” Gómez prides.

Over 40 years of excellence
United Pipeline Systems is a global specialty contractor, providing solutions to pipeline integrity challenges through high-performance thermoplastic internal pipeline lining systems for the oil and gas, industrial, mining, and municipal industries.
United works worldwide to safeguard mining companies’ pipelines by extending their life and helping to meet regulatory requirements. Our Tite Liner® solution prevents internal corrosion and erosion to help ensure the integrity of these critical pipelines.
High Performance Lining Systems across all Major Sectors
Our long-standing partnerships with leading mining companies, along with thousands of miles of Tite Liner being in service for over two decades, attest to the effectiveness and durability of our Tite Liner solution.

Providing tangible evidence of its ability to extend pipeline durability and meet stringent regulatory requirements across all aspects of mining pipeline infrastructure, including: • Tailings • Concentrate • Acid lines • PLS • Water lines

United’s Tite Liner® system protects your critical pipeline system around the clock.
The Tite Liner® system can often rehabilitate pipelines at half the cost and time of dig-and-replace solutions. The transportation of corrosive or abrasive materials in the oil & gas, mining, industrial and municipal markets can wreak havoc on your pipelines. Internal corrosion and abrasion can lead to leaks, pipeline failure, environmental damage and lost production.
Complete replacement of these pipelines is costly and time-consuming. Internal abrasion and corrosion can be avoided by utilizing the pipeline construction capabilities of United Pipeline Systems.
The Tite Liner® System United developed the Tite Liner® system, a technology that enables a thermoplastic liner to fit tightly inside a host pipe.
The Tite Liner® system is manufactured with a larger outside diameter (OD) than inside diameter (ID) of the host pipe.
The Tite Liner® system temporarily reduces the thermoplastic liner’s diameter for insertion. The liner then expands tight following installation. The tight-fitting liner acts as a continuous barrier between the host pipe and the corrosive or abrasive material.
The corrosion and abrasion resistance properties of thermoplastic allow the Tite Liner® system to protect pipelines from a variety of chemicals
and abrasives through a broad range of temperatures and pressures. It is an efficient and cost-effective way to protect new or existing pipelines and its use can often extend the life of a pipeline far beyond the expected life of an asset. The Tite Liner® system comes in sizes from 50 mm to 1,300 mm (2 inches to 52 inches) in diameter, with larger diameters possible in certain situations.
The Tite Liner® system offers many benefits:
• Long pull lengths: Average pull lengths are approximately 600 meters to 800 meters (1,900 feet to 2,600 feet) and longer. Pull lengths of 2.5 km (8,000 feet) have been achieved (individual section length depends on the diameter, bends, terrain and condition of the host pipe).
• Low cost and time: The Tite Liner® system can often rehabilitate your pipelines for less than one half the cost and time of dig-and-replace solutions.
• No maintenance: The Tite Liner® system is a “fit and forget” solution, unlike chemical injection alternatives that require ongoing maintenance and operating costs.
• Temperature limitation: The polyethylene pipe utilized in the Tite Liner® system exhibits superior mechanical properties
in temperatures up to 90ºC (194º) for water and oil emulsion service. For higher temperatures or more aggressive fluids, United can recommend alternative lining materials.
• Chemical resistance: Thermoplastic is very resistant to chemicals and other media such as acids, alkalis and salts, which makes it suitable in almost every process application.
• Field bends: The lining system can easily negotiate field bends of 50D or greater. Bends as low as 20D have been achieved and tighter bends may be possible.
• No pressure limitation: The Tite Liner® system has no pressure limitation since the pressure is contained by the host pipe.
• Leak-free connections: Tite Liner® system flange fittings have been successfully used in projects with pressures up to 340 bar (5,000 psi). The connection has been tested and independently verified up to 500 bar (7,500 psi).
• Increased operating efficiencies: A Tite Liner®- protected pipeline often experiences increased operating efficiencies because the smooth thermoplastic liner improves hydraulic properties over and above a slight reduction of the inside diameter.
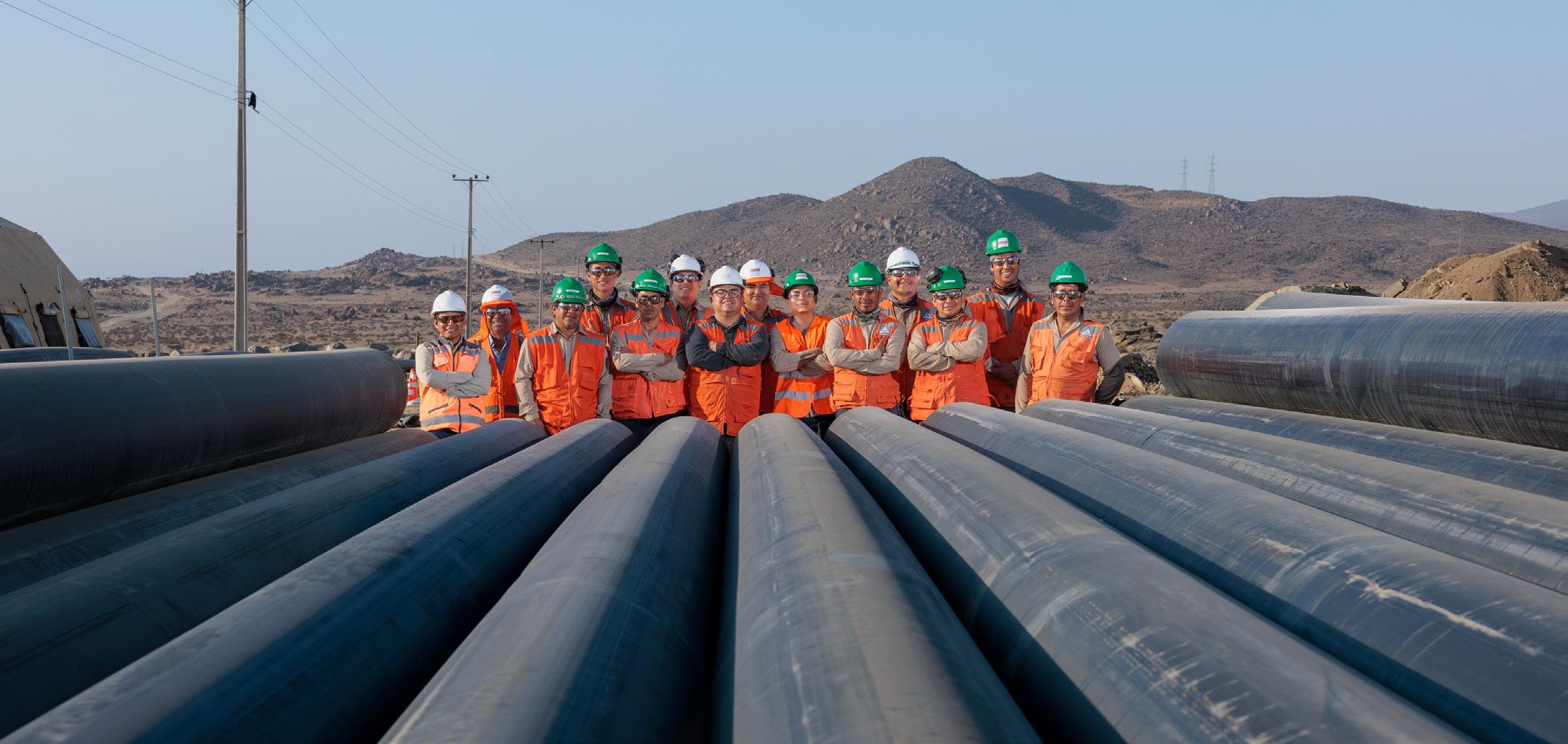
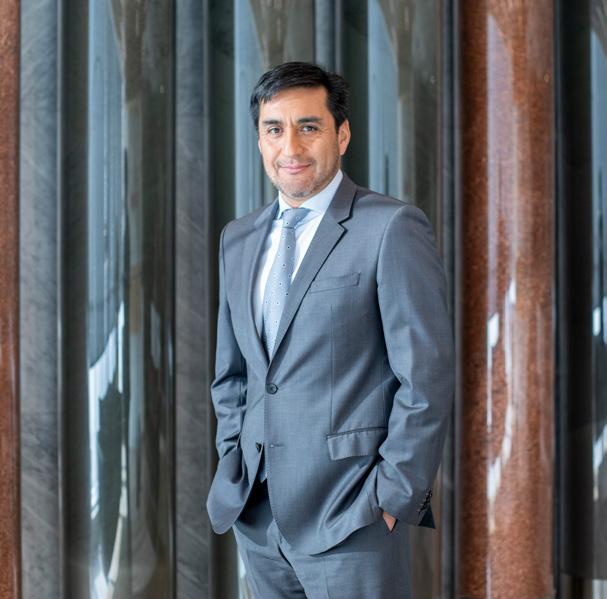
AN EVOLVING INDUSTRY
An industry stalwart, Collahuasi has noted major transformation in South America’s copper mining industry since its inception.
“Not only has the scale of the industry grown in line with global demand, but we have also seen dramatic changes in the landscape in terms of innovation and automation, while the sector has embraced and
“WE HAVE A SUSTAINABILITY POLICY APPLICABLE TO ALL OUR ACTIVITIES, WHICH SEEKS TO HARMONIZE FOUR KEY DIMENSIONS – BUSINESS, ENVIRONMENT, COMMUNITIES, AND PEOPLE”
– MARIO QUIÑONES, VICE PRESIDENT OF DEVELOPMENT AND SUSTAINABILITY, COLLAHUASI
made significant progress toward sustainability alongside inclusion and diversity goals,” Gómez surmises.
Globally, demand for copper has grown due to the emergence of the resource as a critical mineral within the green energy transition – a trend that will continue to have a great impact on the future of the planet.
South America, and Chile in particular, therefore remain key for the
global supply of copper.
However, the sector also faces challenges such as access to water and increasing regulatory pressures, while fluctuating commodity prices are expected to remain a feature of a rapidly changing world.
“While accessing and developing the human capital needed for the future is a challenge, it is also an opportunity to accelerate the
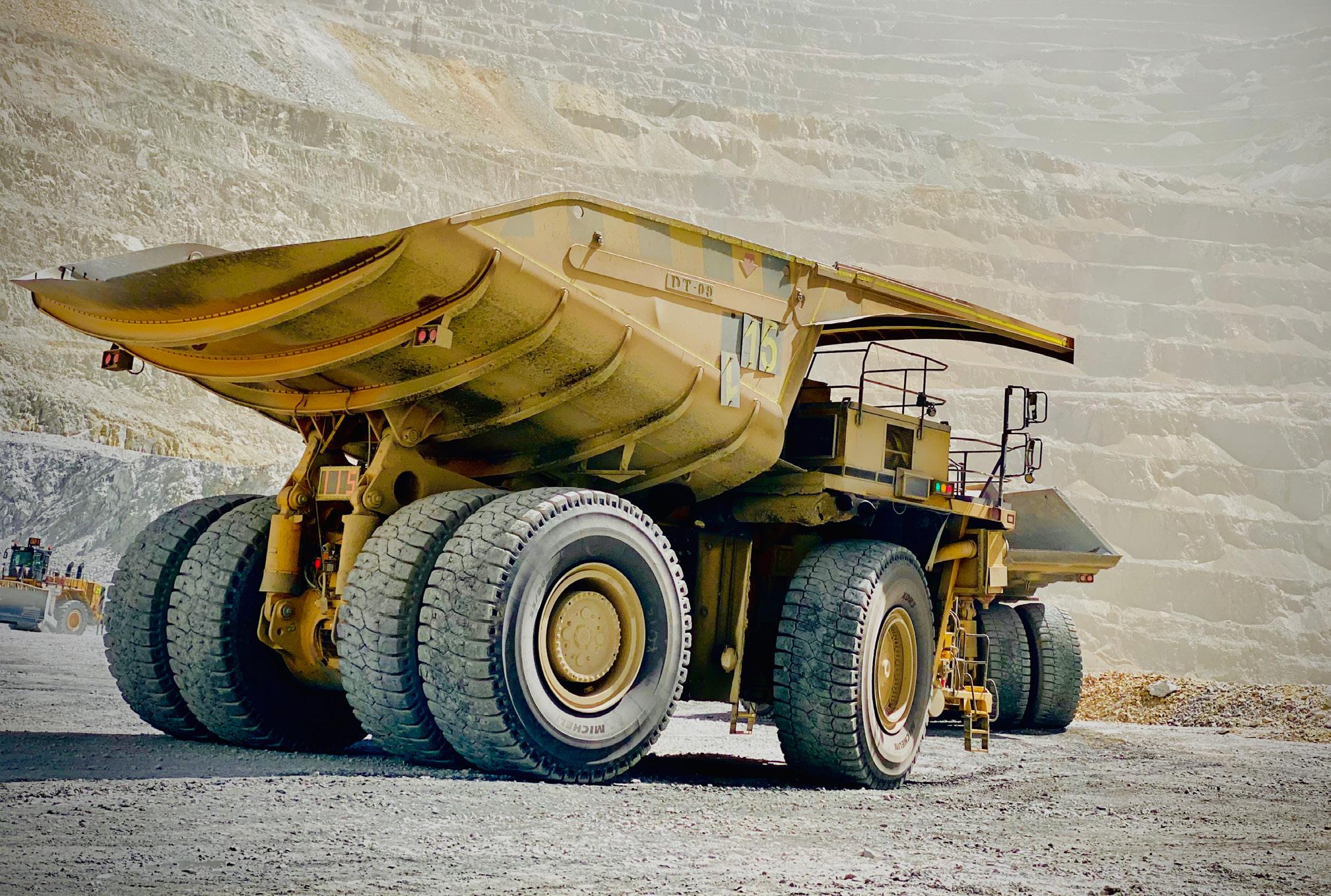
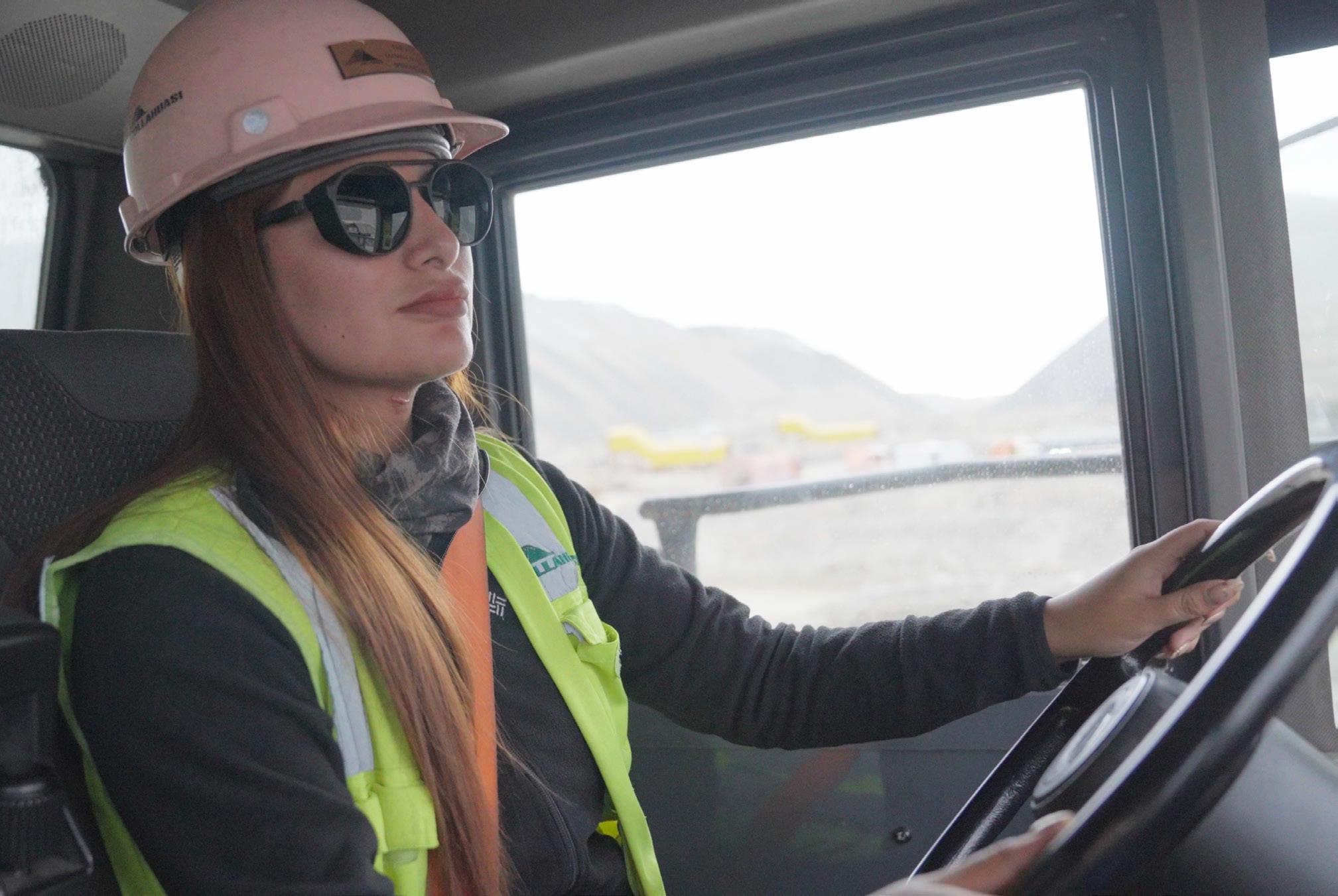
transformation of our workforce to be more inclusive and diverse,” he notes.
Mining, particularly copper mining, is a key pillar of development for Chile and plays a key role in attracting investment, driving economic growth, and contributing significant fiscal resources to the nation.
Chile and Peru dominate copper production in South America, accounting for more than 35 percent of global production combined, while other countries in the region such as Argentina, Brazil, and Ecuador play a smaller but steadily increasing role.
South America as a whole, meanwhile, has a significant 40 to 45 percent share of world copper production as it is home to some of the world’s largest and highestyielding copper mines.
CONTRIBUTING TO LOCAL DEVELOPMENT
In 2023, Chile’s mining sector accounted for 11.9 percent of the
country’s GDP, while its exports accounted for 56 percent, with a total value of $53 billion.
In the same year, Collahuasi was the third-largest copper producer in the world, responsible for the direct employment of around 2,000 workers and 3,000 contractors, with a strong focus on the development of local suppliers.
“We are committed to regional growth and being a positive contributor to neighboring local communities,” informs Trevor Dyer, CFO.
“Our focus is on generating shared value, ensuring that Collahuasi’s economic progress also translates into tangible benefits for our local communities.”
Indeed, Collahuasi has implemented various initiatives through the Collahuasi Foundation which is focused on entrepreneurship, socioeconomic development, capacity building, and education.
COLLAHUASI SHAREHOLDERS
ANGLO AMERICAN (44 PERCENT) – The largest producer of platinum on the planet, Anglo American’s portfolio also comprises copper, diamonds, iron ore, and steelmaking coal. Based primarily in the UK, the organization also has operations in North America, Africa, Asia, and Australia.
GLENCORE (44 PERCENT) –
A world leader in diversified natural resources, Glencore produces and markets more than 60 assets internationally across 35 countries.
JAPAN COLLAHUASI RESOURCES (12 PERCENT) –
A subsidiary of Mitsui & Co., the consortium of companies is involved in a variety of mining operations across Chile and is one of the largest trading and investment companies in Japan.
Innomotics
and Collahuasi:
Achieving Mining Excellence Through Collaboration
In the ever-changing landscape of the mining industry, the enduring partnership between Innomotics and Minera Collahuasi stands as a prime example of how technological innovation can drive operational excellence. By working together, the two companies have implemented cutting-edge technologies that not only optimize efficiency and productivity at the giant Collahuasi copper mine but have also improved safety conditions for personnel and contractors and increased the sustainability of the business.
“Innomotics is proud to be at the forefront of mining innovation with Collahuasi. We are not just solving today’s problems; we are laying the groundwork for tomorrow’s opportunities,” said Hector Andrade, Country Business Unit Manager for Innomotics Solutions.
Drive Systems: Enhancing Operational Efficiency
Central to the collaboration is the integration of advanced drive systems tailored to meet the unique needs of Minera Collahuasi’s operations.
The mining industry demands robust, reliable, and efficient equipment, and Innomotics’ drive technology is designed to handle these challenges seamlessly. These drives are crucial in enhancing the efficiency of
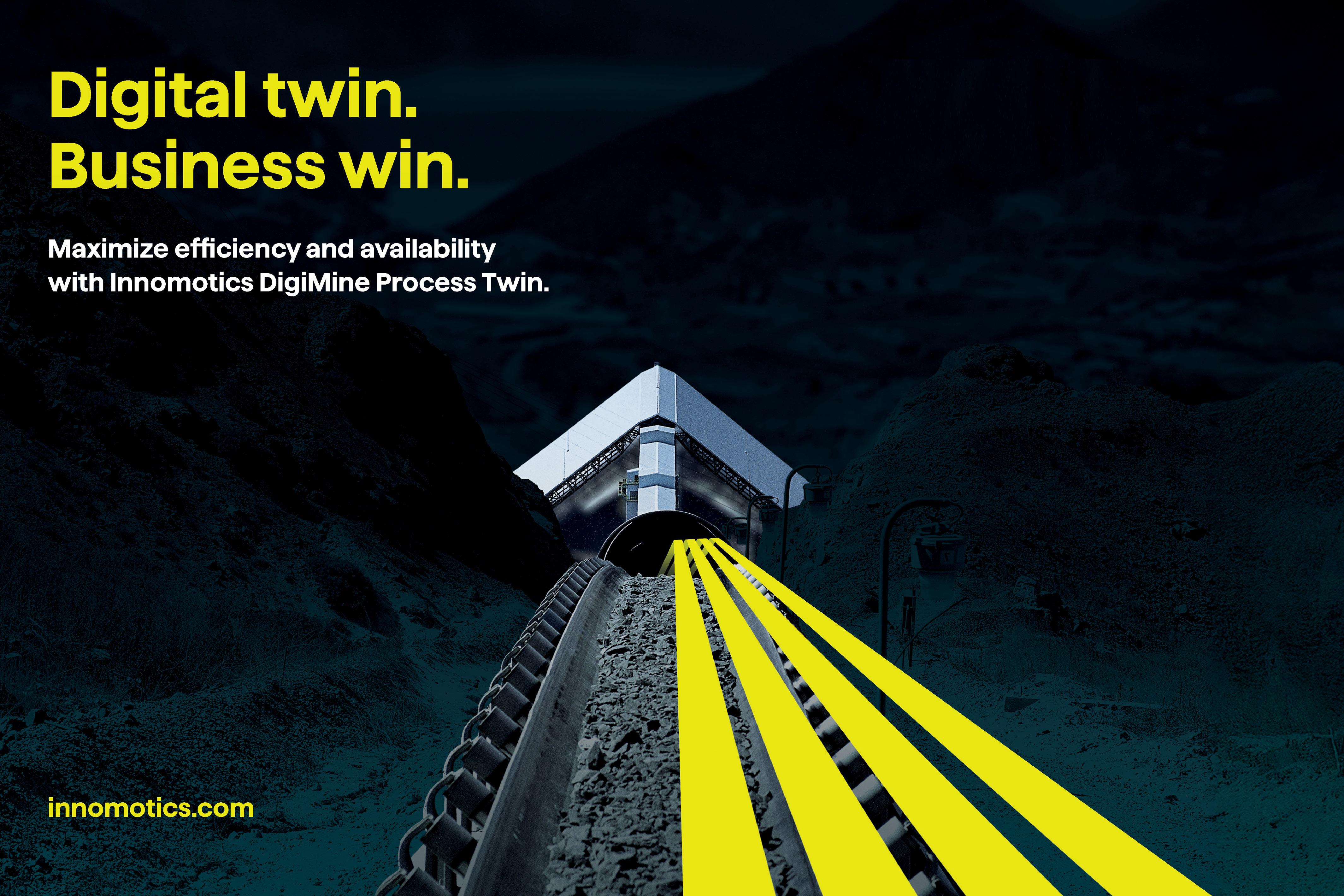
Collahuasi’s operations, especially in critical areas like the grinding process.
In 2016, Innomotics carried out the modernization of the Dual Pinion drive systems for four mills in Collahuasi’s Ujina concentrator plant.
This involved the installation of four 4.85MW motors for the two ball mills and four 4MW for the two SAG mils, plus four E-houses equipped with SL150 converters and auxiliary systems, and an automation system based on cutting edge technologies.
As well as providing the equipment, the company was also responsible for transporting the hardware to the plant site, located at more than 4,400 meters above sea level, as well as installation supervision, commissioning, start-up services and training.
The modernization process also complied with the customer’s requirement of just 10 days of downtime for the SAG and then the Ball mills.
“Our goal is to ensure that Collahuasi’s machinery not only meets but exceeds performance expectations. By implementing state-of-the-art drive systems, we are contributing to a more sustainable and productive mining process,” said Andrade.
Integral Plant Maintenance
Innomotics’ partnership with Minera Collahuasi has continued through
the provision of Integral Plant Maintenance service to its plants for the last ten years. One of the largest maintenance contracts in the global mining industry, the contract today covers the crushing operations at the mine, the Ujina concentrator and the port facility at Puerto Patache.
Through its IPM service, Innomotics aims to provide optimal maintenance of the equipment, minimizing costs and downtime while achieving the highest levels of safety for its personnel. Sensors embedded in drive systems, conveyors, and crushers continuously collect data on equipment performance. Innomotics is developing methodologies to analyze this data to identify early warning signs of wear and tear, enabling timely interventions and reducing unplanned shutdowns
The emphasis on integral maintenance not only extends the lifespan of critical equipment but also improves overall safety and reliability. Furthermore, it aligns with Collahuasi’s commitment to operational excellence and sustainability by reducing resource waste and enhancing equipment utilization.
“Integral Plant Maintenance is about moving from a reactive to a proactive mindset. By using data to forecast potential failures, we are moving forward together with Collahuasi reshaping how we face the mining of the future,” says Andrade.
Digitalization: Leveraging Data for Smarter Operations
One of the most transformative elements of the InnomoticsCollahuasi partnership is the focus on digitalization. In line with Collahuasi’s

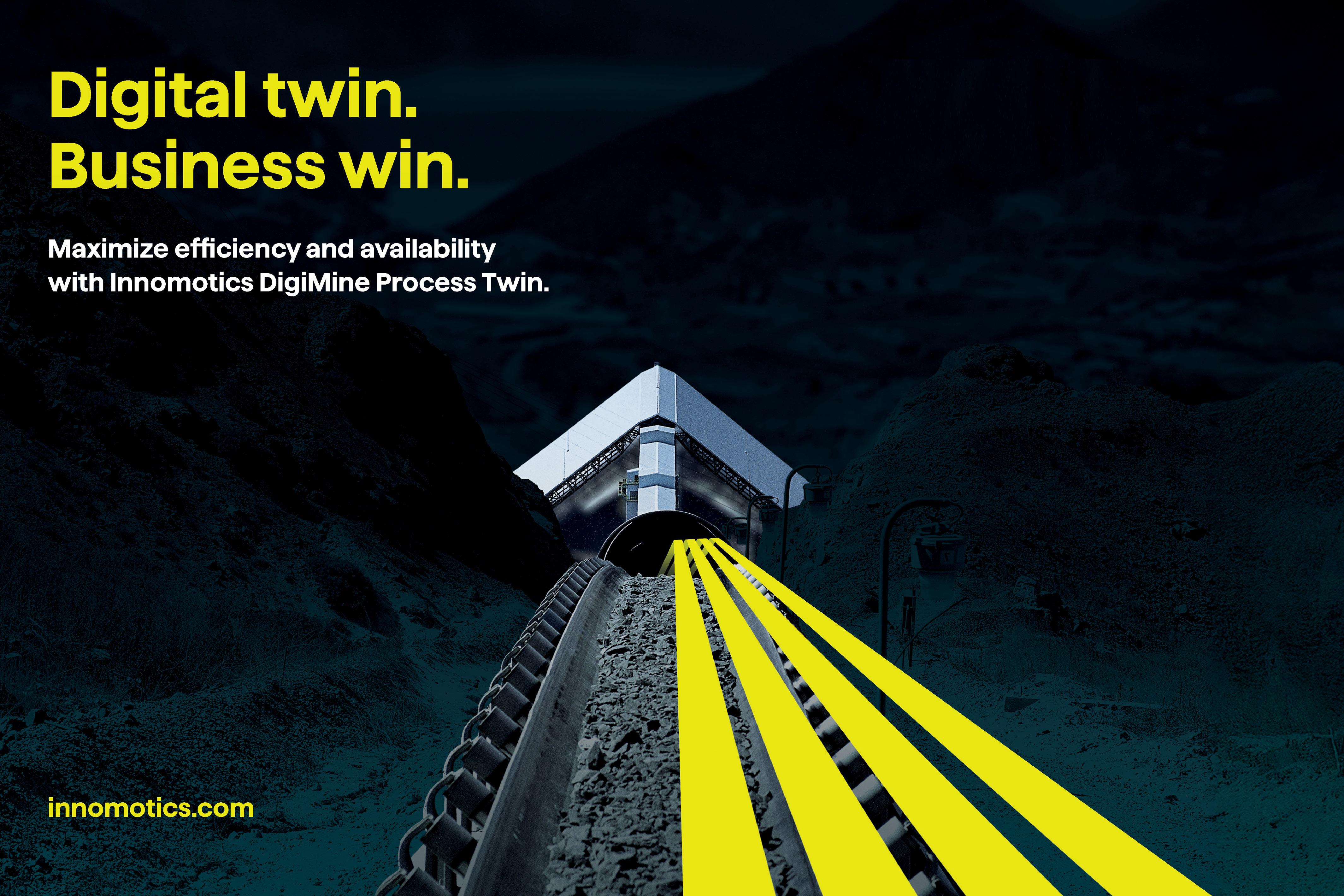
strategy to achieve the algorithmization of its business, Innomotics has worked with its team to implement a Digital Twin, that is a virtual replica of its physical assets and operation which operators can use to test out new operating criteria without affecting the productivity of the operation.
At Collahuasi, the Digital Twin simulates the crushing process at the Rosario sector of the mine. By analyzing information such as hopper levels, ore reduction, and conveyor belt speed, the team has been able to optimize a traffic-light system based on Artificial Intelligence that indicates to operators exactly when they should unload to keep the volume of ore in the crusher chamber at optimal levels avoiding bottlenecks.
“We are excited about the promising results of the digital twin in optimizing the crushing process. The data-driven insights have shown us how much more value we can extract from our current systems helping us to define future expansions more precisely,” explains Andrade.
Conclusion: A New Era of Mining Excellence
The collaboration between Innomotics and Minera Collahuasi is a testament to the transformative power of technology in mining. By focusing on advanced drive systems, digitalization, and innovative forms of maintenance, the partnership is setting new standards for efficiency, sustainability, and operational excellence.
“This is more than a technological upgrade; it’s a shift in how we approach mining. Together with Collahuasi, we are proving that the future of mining is intelligent, sustainable, and resilient,” comments Andrade.
Through the Collahuasi Foundation, high-quality educational establishments are co-managed and teach technical careers related to mining.
The foundation is critical in this regard, as the company actively invests in the education and co-management of two municipal technical high schools, raising the overall quality of education in the Tarapacá region.
Currently, more than 300 graduates from these schools work at Collahuasi or its contractor companies.
The contribution of mining in terms of direct employment in Chile last year reached 278,000 workers, a figure that rises to 986,000 if indirect employment is included –equivalent to 10.9 percent of national employment.
SUSTAINABILITY POLICY
Collahuasi’s sustainability policy drives productivity, permeates every area of the company, and is based on a number of international sustainability standards, including:
UNITED NATIONS (UN) GLOBAL
COMPACT – Revolves around a set of 10 principles, including human rights, labor, environment, and anti-corruption.
UNIVERSAL DECLARATION OF HUMAN RIGHTS (UDHR) –
Developed by the UN Human Rights Commission in 1948, the UDHR seeks to ensure global freedom, equality, and dignity.
TRANSPARENCY
INTERNATIONAL – The Chilean chapter of the association promotes accountability, integrity, and transparency.
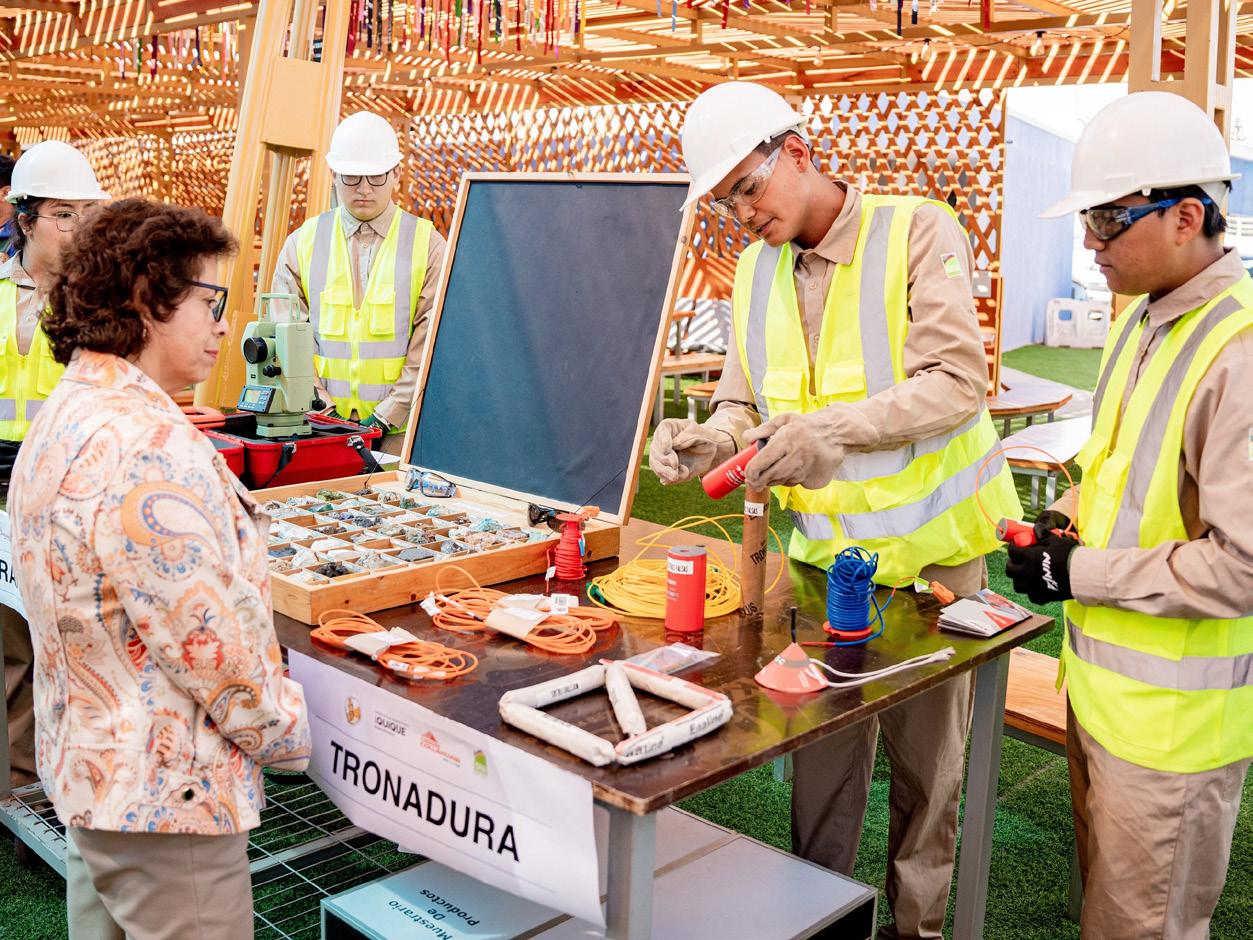
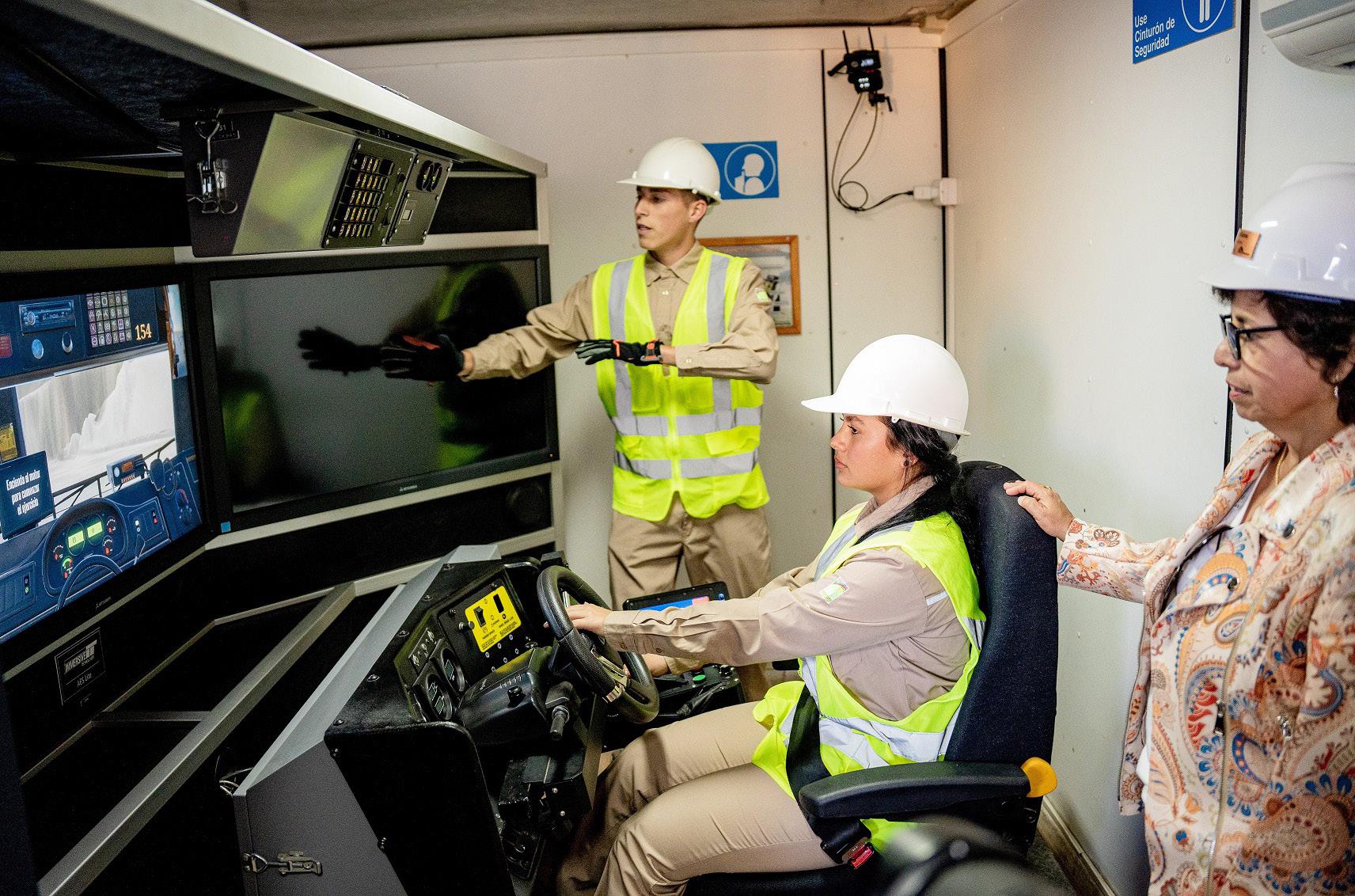
Policies implemented in Chile also ensure that mining royalties paid by companies in the sector are distributed to regional governments and municipalities throughout the country to fund community-centered initiatives.
“For example, some of these resources are allocated to national funds. These include the Territorial Equity Fund, which seeks to reduce the gaps that exist between
municipalities’ incomes, the Mining Communities Fund, which focuses on the impacts of mining activity, and a fund for citizen security,” Dyer explains.
A STAND-OUT OPERATION
Differentiated by its management model, Collahuasi applies a risk management cycle framework throughout the entire value chain.
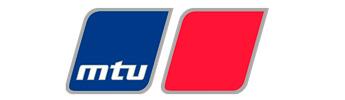
A Rolls-Royce solution
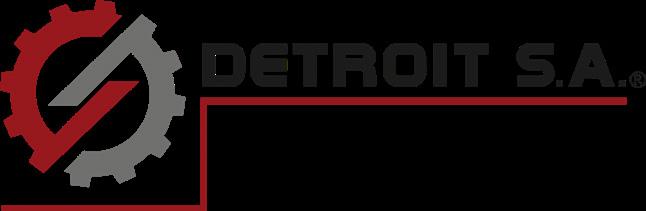
Power for your business
It fills us with pride and happiness to be able to accompany Collahuasi for more than 30 years of uninterrupted cooperation in its operations, reiterating our commitment to continue developing and implementing technologies that enhance mineral transportation aligned with shared values, visions and objectives of safety, energy efficiency, productivity and respect for the environment.
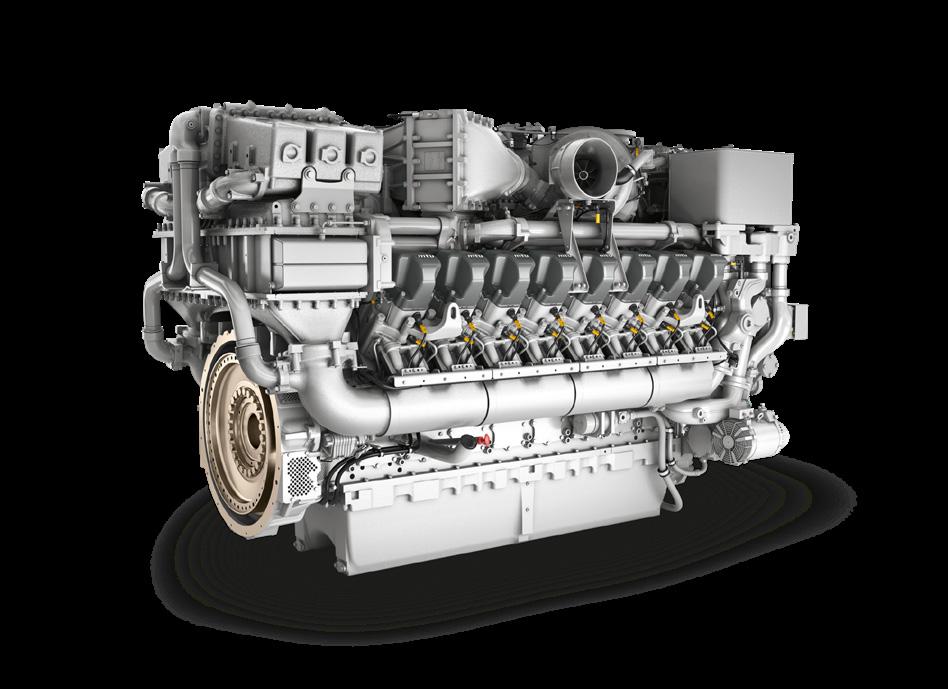
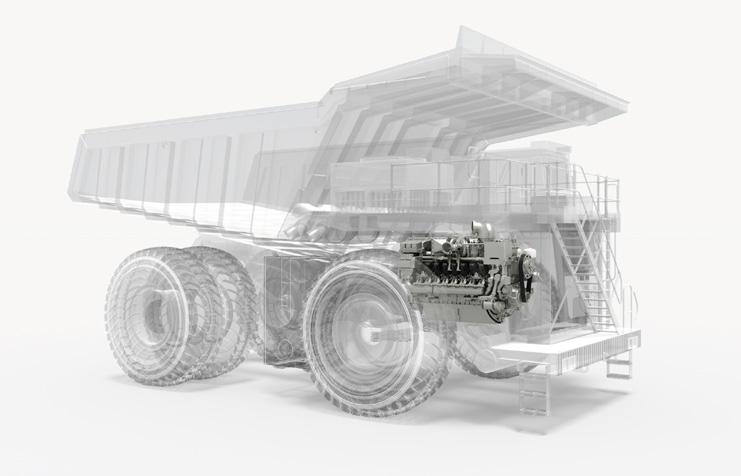
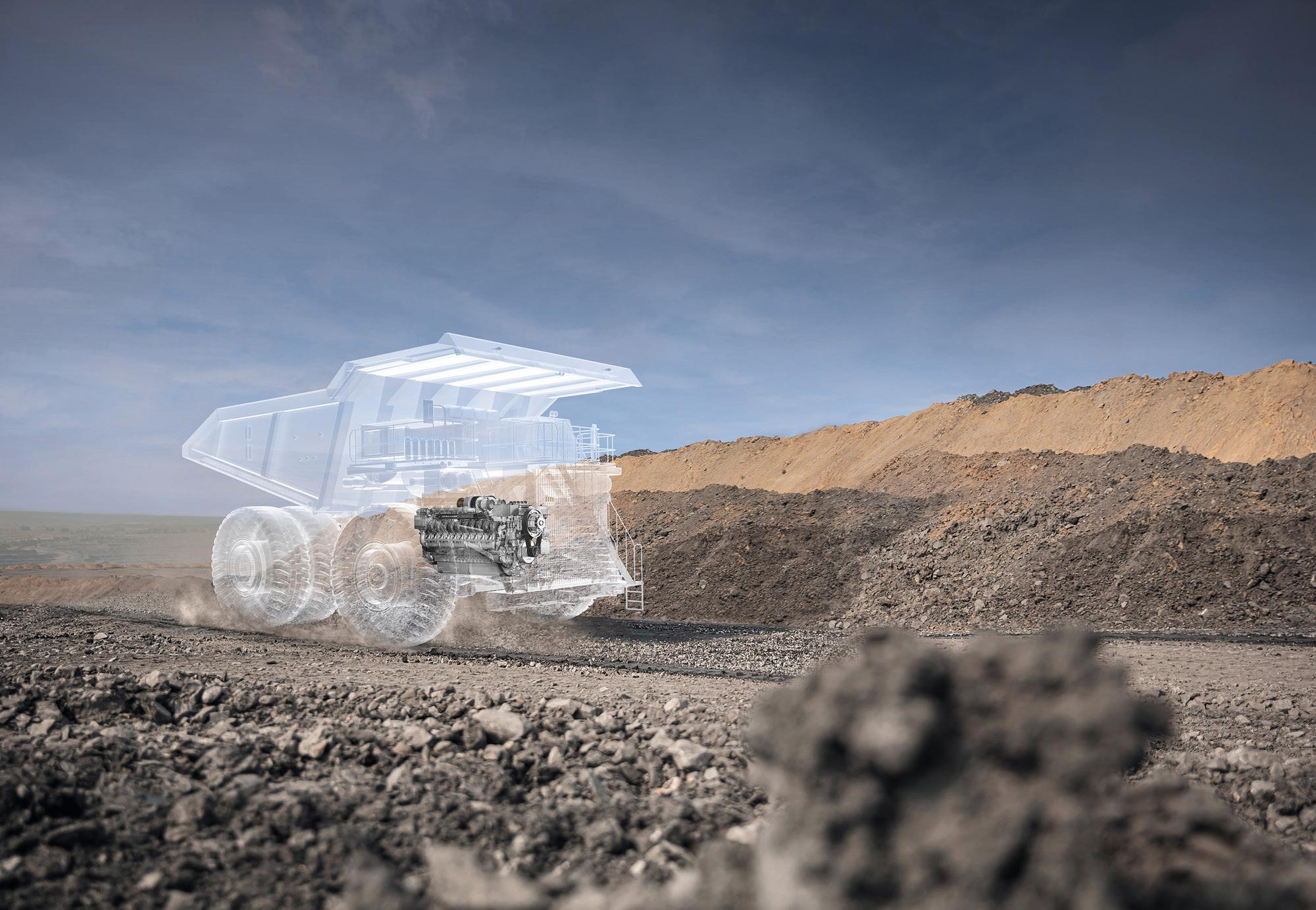
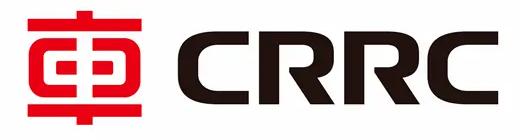
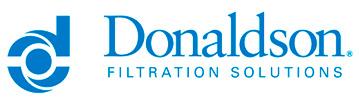
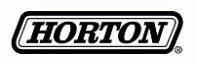

This has been the foundation for the company’s ongoing history of operational excellence, ensuring that learnings and opportunities are captured in a way that generate value for the business and the environment.
“Today, we stand out as one of the safest, most efficient, productive, and sustainable mining operations worldwide,” Gómez shares.
This is despite the fact Collahuasi’s main mine is located in the highlands of the Atacama Desert at an altitude of over 4,400 meters above sea level, close to the border between Chile and Bolivia, which has historically presented unique challenges in terms of operations and logistics.
As a result, the mine faces climatic conditions that vary widely from other mining operations in the country.
“For this reason, we have implemented advanced technologies to both protect the health and safety of our employees while ensuring operational continuity and productivity,” he outlines.
Collahuasi is one of the world’s true

Tier 1 copper resources, both in terms of its absolute size but also because of its exceptional quality.
The asset’s copper reserves alone stand at over four billion tons with an average grade of 0.8 percent – a key factor that will help to maintain the exceptionally strong competitive
COLLAHUASI’S ACTIONS TO PROTECT BIODIVERSITY
• Environmental management and compliance through the company’s sustainability policy.
• Efficiently using water resources through the C20+ project.
• Adhering to the principles of a circular economy.
• Exclusively using renewable energy since 2020 in order to achieve its net zero goal by 2040.
• Enacting measures to reduce Scope 1, 2, and 3 emissions.
• Adhering to UN Sustainable Development Goal (SDG) 15 by protecting nearby ecosystems.
• Implementing a forest management plan for 20+ years.
• Introducing a program in 2019 to restore and revitalize 15.4 hectares (ha) of the bofedales in the local area.
• Reforestation of native queñoa trees over a 22-year period, covering a total of 102ha.
position of Collahuasi in the long term.
“To realize the full potential of our asset, there are a number of projects that are either in the execution or development stages,” Gómez asserts.
A PLETHORA OF PROJECTS
One key focus is the growth project at the Ujina plant, which incorporates a number of initiatives required to increase the treatment capacity of the concentrator to the environmentally approved maximum capacity of 210ktpd.
“The various elements of this project will allow us to reach a production of over 600kt of copper per year, positioning Collahuasi as one of the leading copper producers in the world,” he adds.
At the same time, the company is also executing the construction of the C20+ project, which will provide the operation with a desalinated water supply.
The project, which will have an initial capacity of 1,050 liters per second, includes the construction of the desalination plant and water impulsion system, which will see water transported 194km from sea to mine.
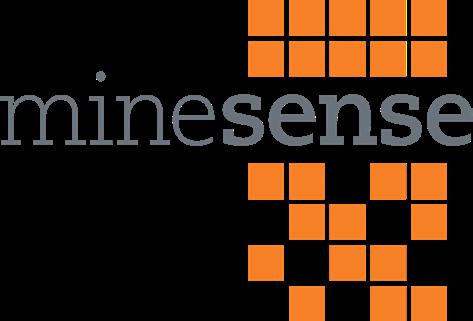
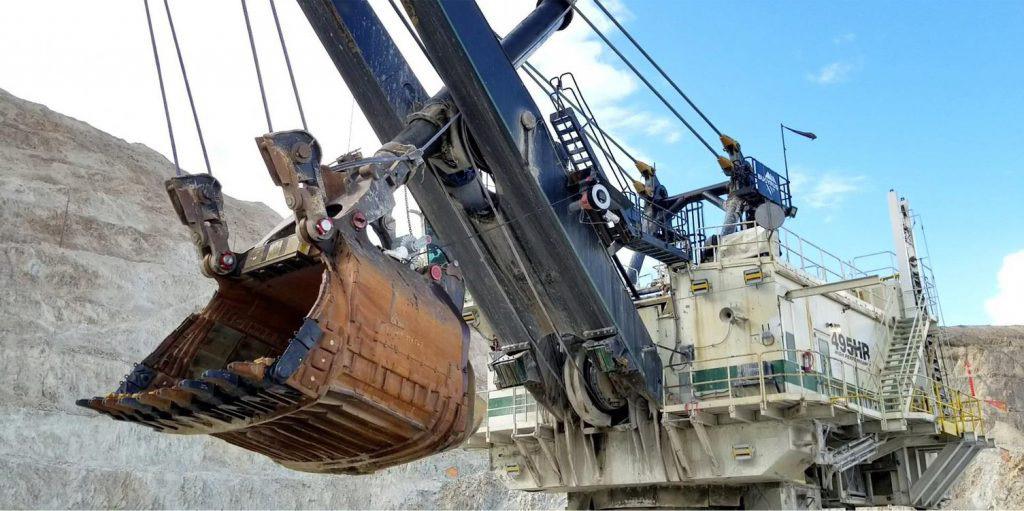
The world needs more metals to thrive. At Collahuasi, the integration of ShovelSense® and BeltSense® delivers complete ore stream coverage, enabling actionable decisions that drive downstream optimization and maximize recovery. Across the globe, millions of tons of valuable ore are lost each year due to material misclassification as a result of limited orebody knowledge, blast movement and mixing, and allocation errors – factors that lead to dilution entering the ore stream and loss of potentially valuable resources.
MineSense’s mine-to-mill digital solutions deliver real-time data to optimize mining operations, starting at the beginning of the mining process – extraction. At the mine face, ShovelSense uniquely delivers real-time ore characterization by the bucket, using innovative X-Ray Fluorescence (XRF) sensors custom installed in the shovel of existing excavators, creating powerful datasets that drive more informed operational decisions. By integrating with a mine’s Fleet Management System (FMS), ShovelSense also enables automated truck routing, ensuring that assessed payloads are routed to the mill, stockpiles,
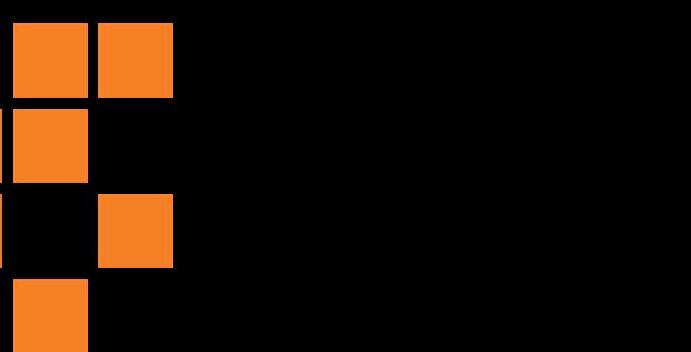

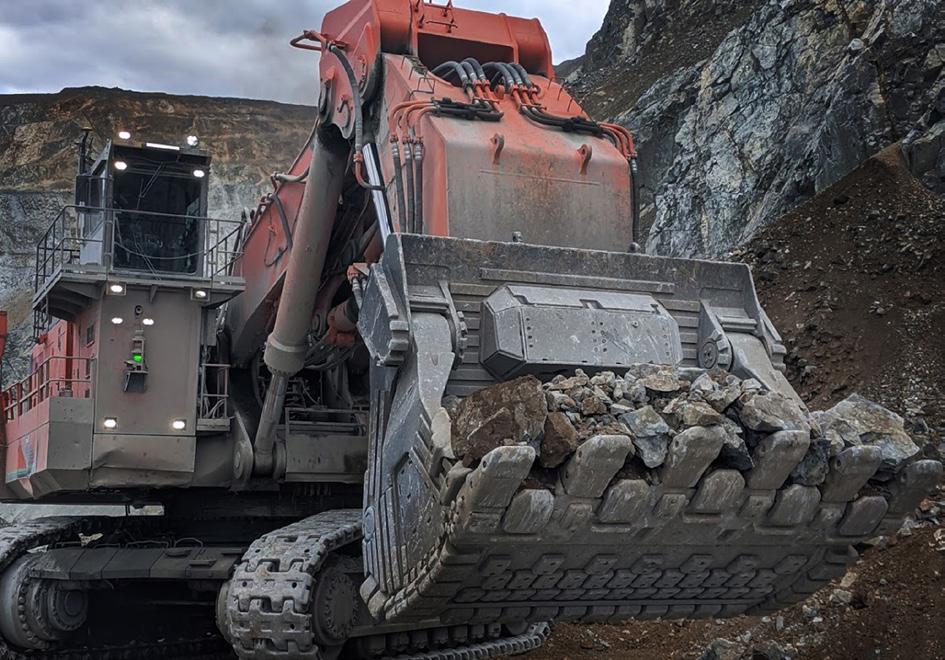
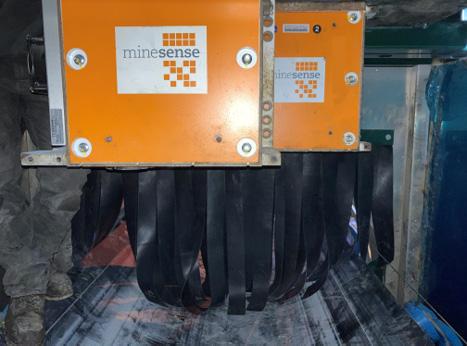
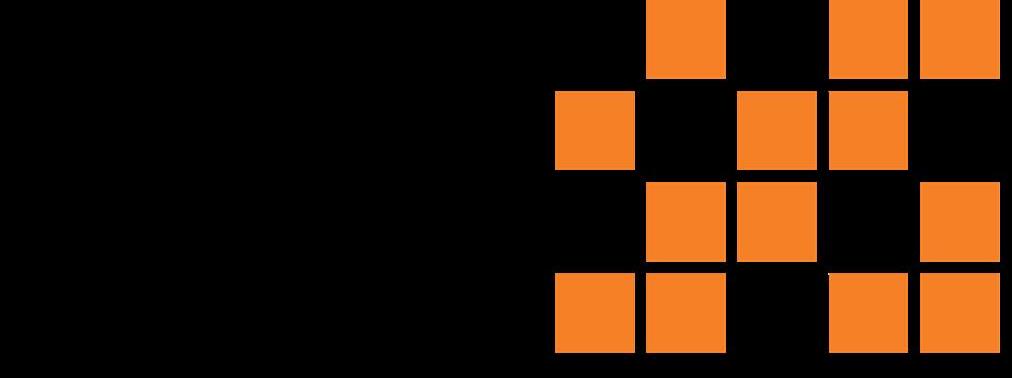

or waste dumps based on their economic viability. This stepchange in efficiency, driven by advanced material classification and ore sorting, improves the mill head grade and reduces grade variability, resulting in a more efficient mill process.
BeltSense is equipped with the same XRF technology as ShovelSense and installed on top of conveyor belts at key control points along the grinding circuit to complement ShovelSense’s at-face readings, resulting in continuous, end-to-end material tracking. The combined measurements of both technologies deliver actionable data that reduce grade variability, refine process control, and optimize the entire mining operation.
MineSense’s mine-to-mill optimization begins at the mine face and continues seamlessly across the entire production process. By leveraging high-resolution datasets and real-time actionable insights, the company helps mines improve efficiency, boost productivity, and enhance sustainability. Trusted by the world’s largest mining operations, MineSense’s proven digital solutions increase the recovery of payable metals, delivering significant data-driven gains in profitability and sustainability.
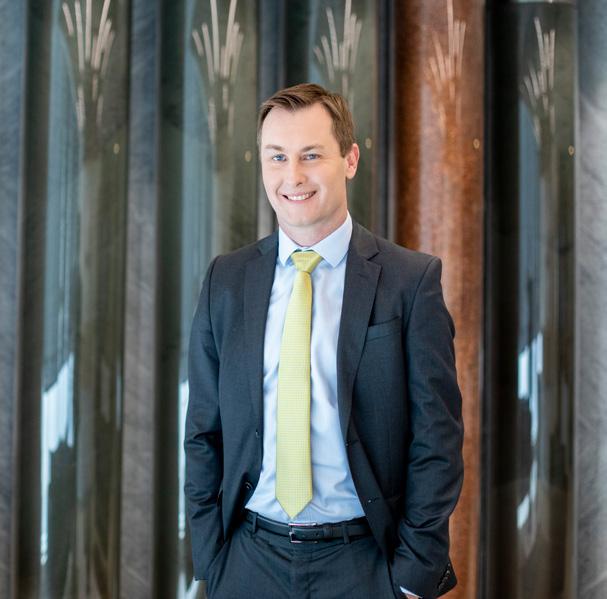
This will ensure the supply of desalinated water for current operations and future growth projects, reducing pressure on local water resources, thus achieving a very significant milestone in line with enhancing the sustainability of Collahuasi’s processes.
“This is a crucial step to ensure operational continuity in an environment where water is a limited resource,” Gómez outlines.
While the project is still in its construction phase, it is expected to
“WE SEEK TO BE MUCH MORE THAN JUST A COPPER MINING COMPANY –OUR PURPOSE IS TO CONTRIBUTE TO A BETTER SOCIETY”
– TREVOR DYER, CFO, COLLAHUASI
lower emissions.
These include the operation of autonomous trucks, the use of a trolley system for its trucks in dumps, and the robotization of maintenance activities at the Ujina plant.
“All our projects are key to achieving Collahuasi’s objective to realize the full potential of our asset in the context of a growing global demand for copper.
be fully operational during the first half of 2026.
Collahuasi is also moving forward at pace with studies to prepare for the future growth of the company, with the intention of significantly increasing its ore processing capacity.
Finally, the company is investing in the modernization of its mining facilities and processes by incorporating automation technology in mineral transport and processing, which will allow it to operate more efficiently and with
“Further, these projects will enable the delivery of a more resilient, competitive, and sustainable operation, which will benefit all our stakeholders,” he asserts.
SUSTAINING PEOPLE AND PLANET
The Chilean mining industry has adopted more sustainable practices, such as the use of renewable energy sources and desalinated water and the optimization of processes through digitalization and automation, promoting the longevity of the country’s copper mining industry and long-term employment.
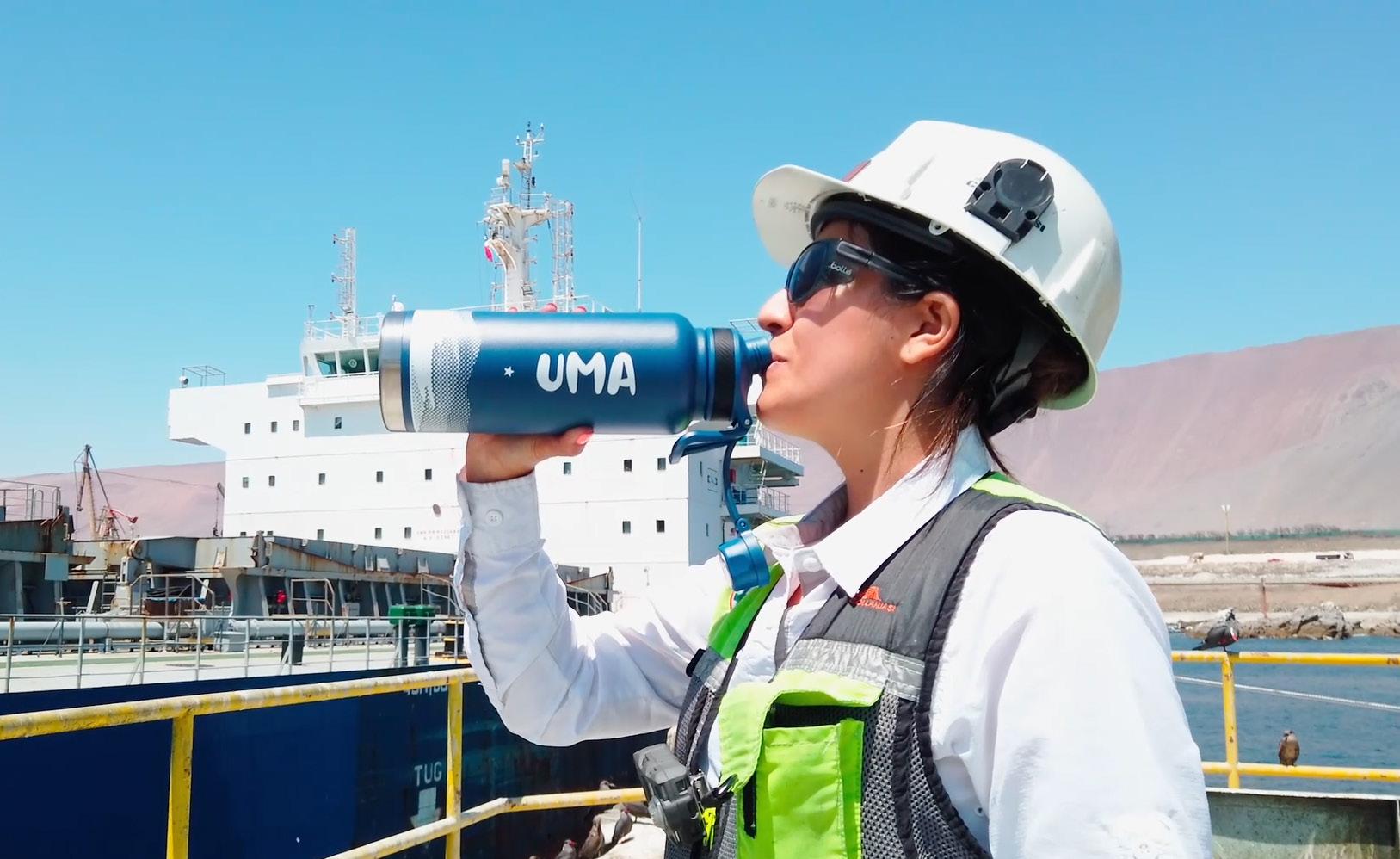

Delivering the mining industry’s rst Integrity Management System

Find a better way.

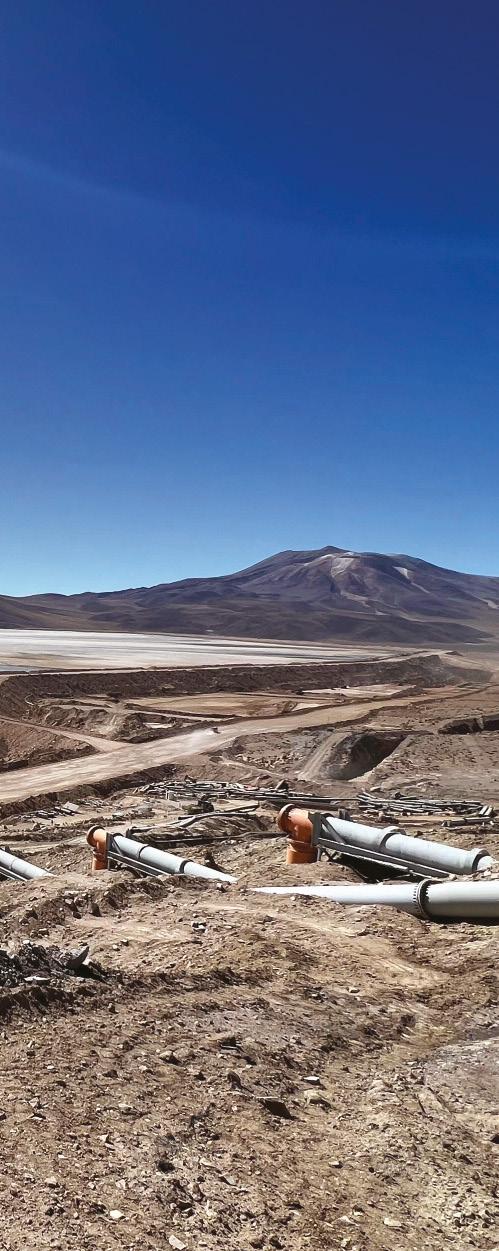
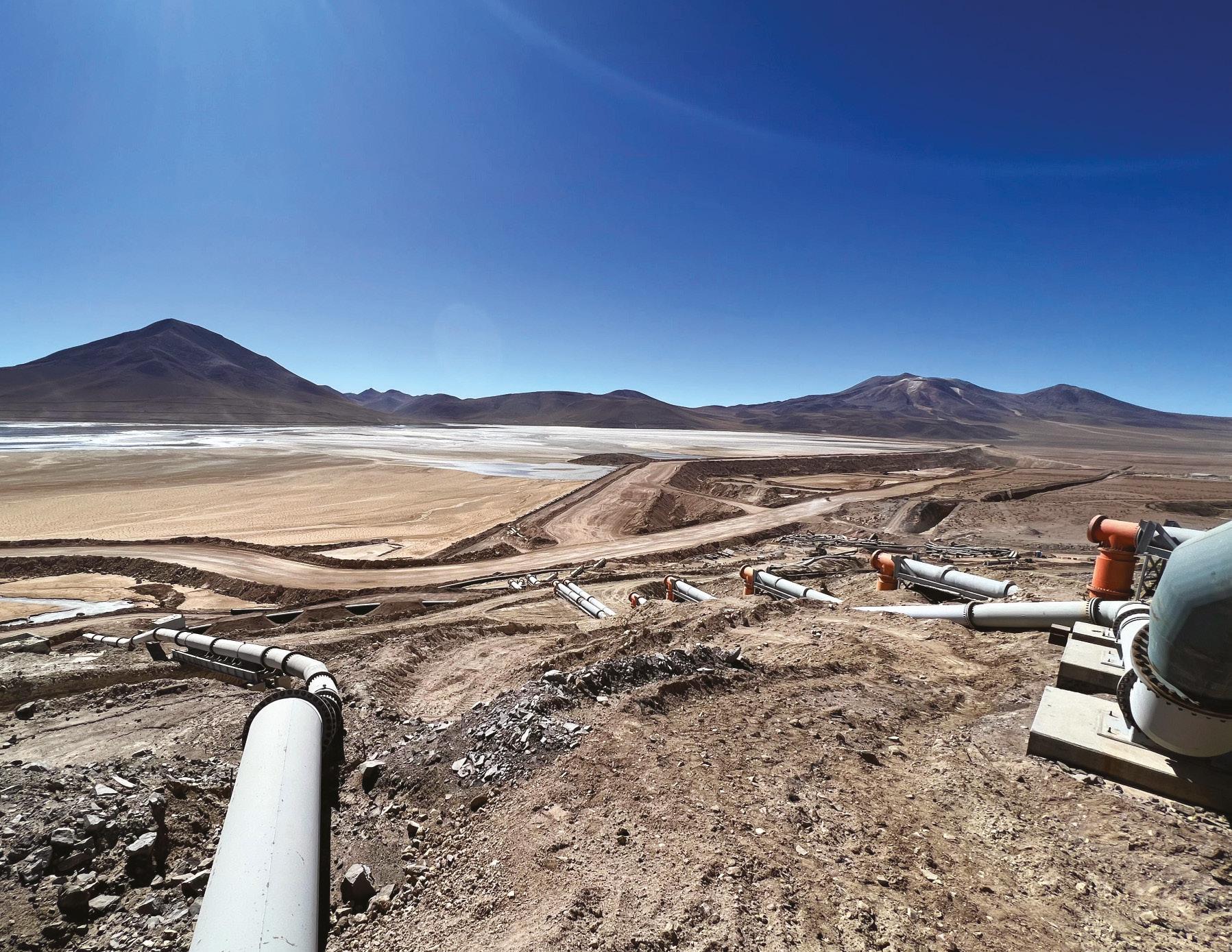
Safeguarding assets and operations for one of the largest copper mines in the world.
Together with Collahuasi, a global leader in mining operational efficiency, Ausenco delivered an Integrity Management System for their mine’s concentrate pipelines, tailings management facilities, and water management system. We provided an overarching framework to guide the management of critical non-processing infrastructure that resulted in increased productivity, reduced downtime and minimised environmental and safety risks.
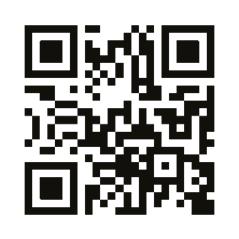
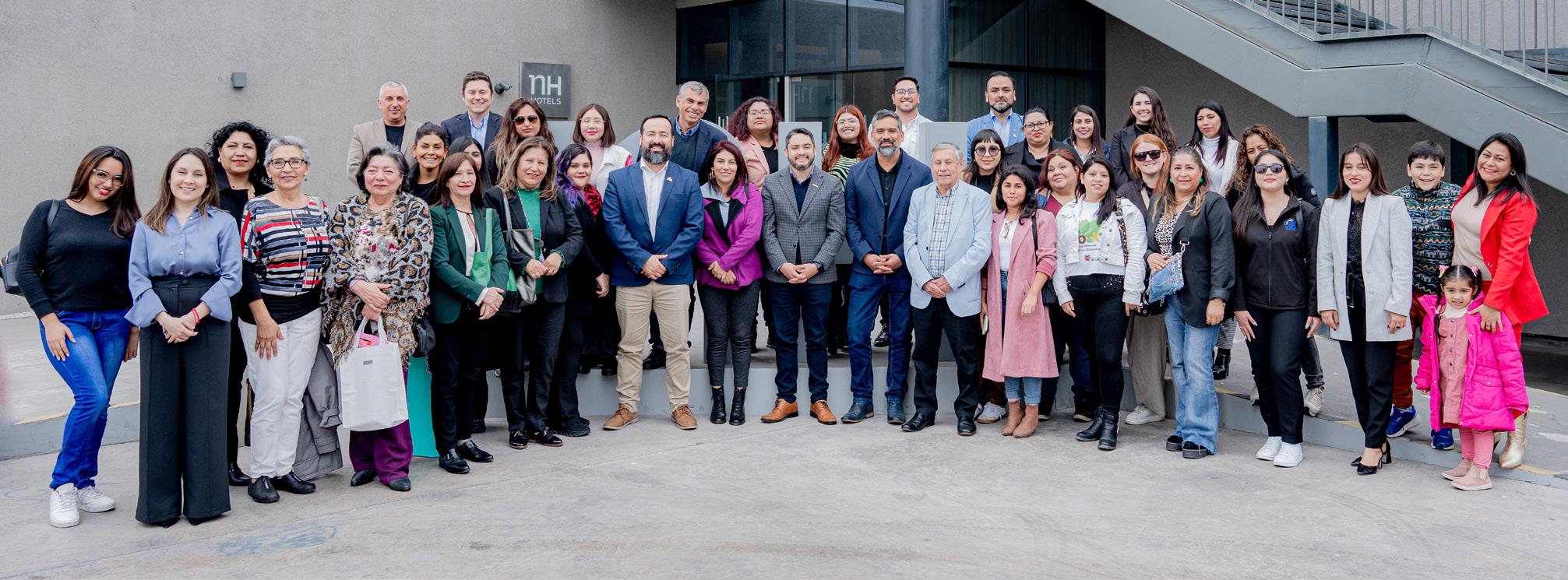
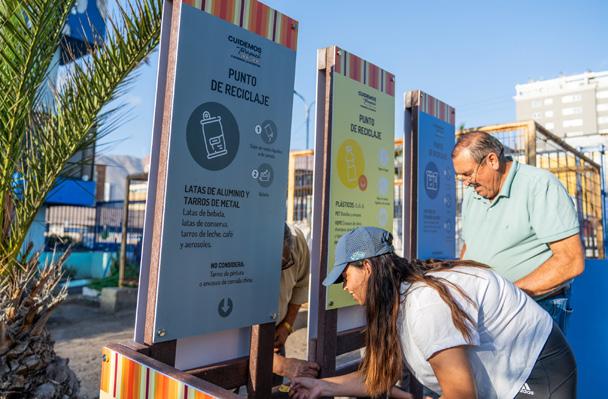
Collahuasi is a pioneer of sustainability in the country due to its use of renewable energy, with 100 percent of the company’s energy coming from clean sources such as solar and wind power.
Sustainability is therefore a core guiding framework for Collahuasi and applies to all levels of the organization, spanning people, projects, operations, facilities, and products.
“For this reason, we have a sustainability policy applicable to all our activities, which seeks to harmonize four key dimensions –business, environment, communities, and people,” clarifies Mario Quiñones, Vice President of Development and Sustainability.
Since 2021, the company has been implementing an environmental, social, and governance (ESG) management strategy, which includes specific medium and long-term commitments.
LET’S TAKE CARE OF TARAPACÁ
Another example of Collahuasi’s support for local communities, Cuidemos Tarapacá – which translates as ‘let’s take care of Tarapacá’ – directly benefits residents in the region.
In the spirit of collaboration and through alliances with public and private partners, the program seeks to deepen Collahuasi’s contribution to the socioeconomic development of Tarapacá and respond to the needs of its inhabitants.
ITS ACTION LINES INCLUDE: TARAPACÁ SONRÍE – Improving the dental health of more than 300 women in the area.
IQUIQUE SE CUIDA – Related to the care and recovery of the historic center of Iquique so that the city remains a safe and attractive meeting place for residents and visitors.
MUJER AVANZA – Supports the work of 300 female entrepreneurs from the Tarapacá region through financing, training, and the formalization of their ventures.
IQUIQUE CIRCULAR – Strengthening Collahuasi’s commitment to caring for the environment by promoting circular economy initiatives to reduce waste generated in the city, making the current refuse problem an opportunity for local development.
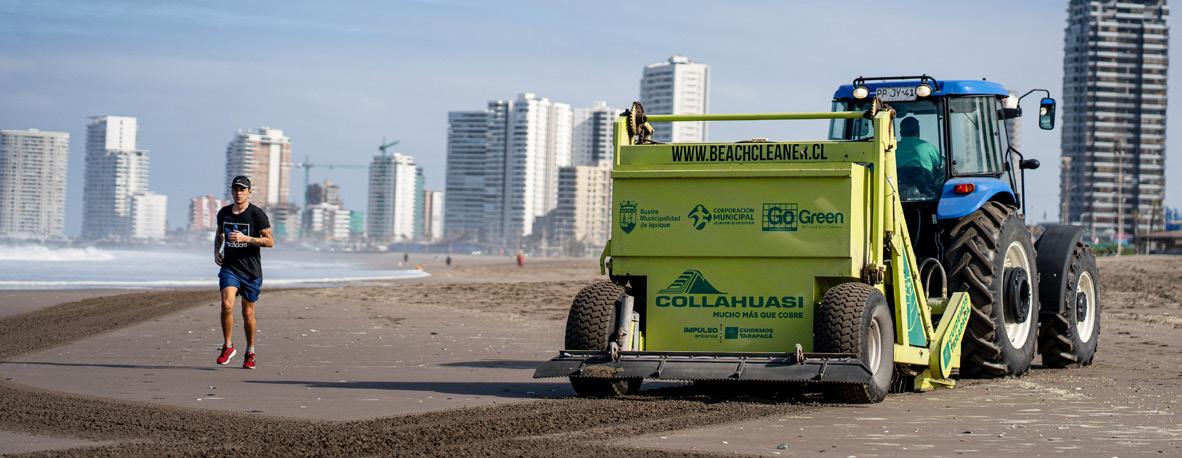
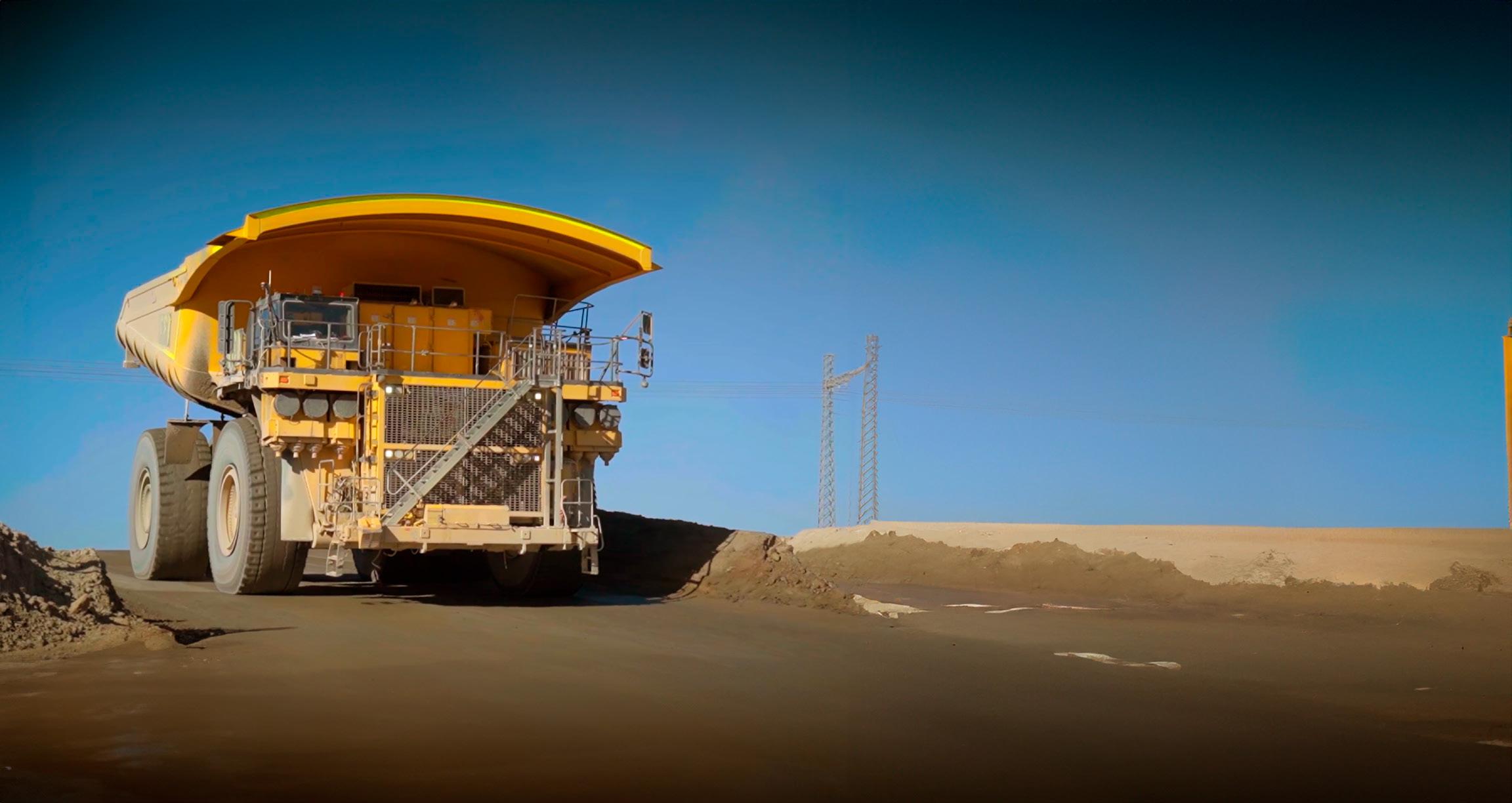

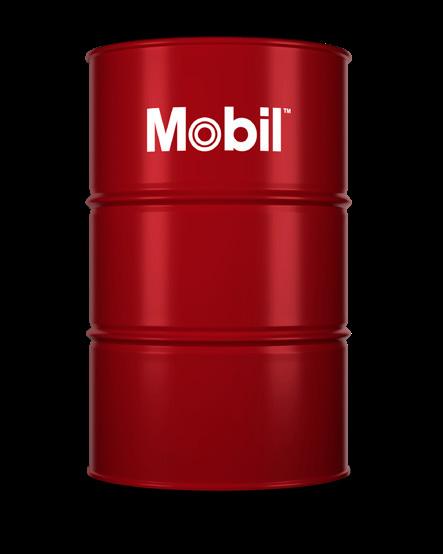
A Worldwide Company with Strong Expertise in the Energy & Resources Segment.
At Sodexo, we understand that the well-being and motivation of your workers are crucial to your success. That’s why we work to ensure operational continuity, predictable cost management, and adherence to environmental and social standards.
We Are Remote Living. To achieve this, Sodexo incorporates top-level innovations, such as our Culinary Base Plant and a Command Center that standardizes processes, increases e ciency, and tracks everything, analyzing information in real-time.
Together, let's create a thriving community where remote living is not just a necessity, but a choice.
At Copec, official distributor of MobilTM in Chile, we highlight the successful tests carried out in collaboration with the mining company Doña Ines de Collahuasi, who committed to their sustainability vision, relied on Mobil Delvac Modern™ 15W-40 Advanced Protection Mine for their haul truck fleet.
This test, conducted in collaboration with ExxonMobil and equipment manufacturers, reduced the environmental impact by doubling oil change intervals resulting in less waste generation and reducing the carbon footprint, while simultaneously increasing productivity.
We would like to thank the Mining Vice Presidency and its entire team for their trust and leadership in pioneering this initiative, which promotes a more efficient, safer, and environmentally respectful mining industry.
Scan the QR code and discover more about the complete line of Mobil™ lubricants for the mining industry
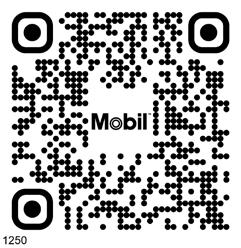
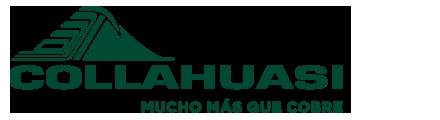
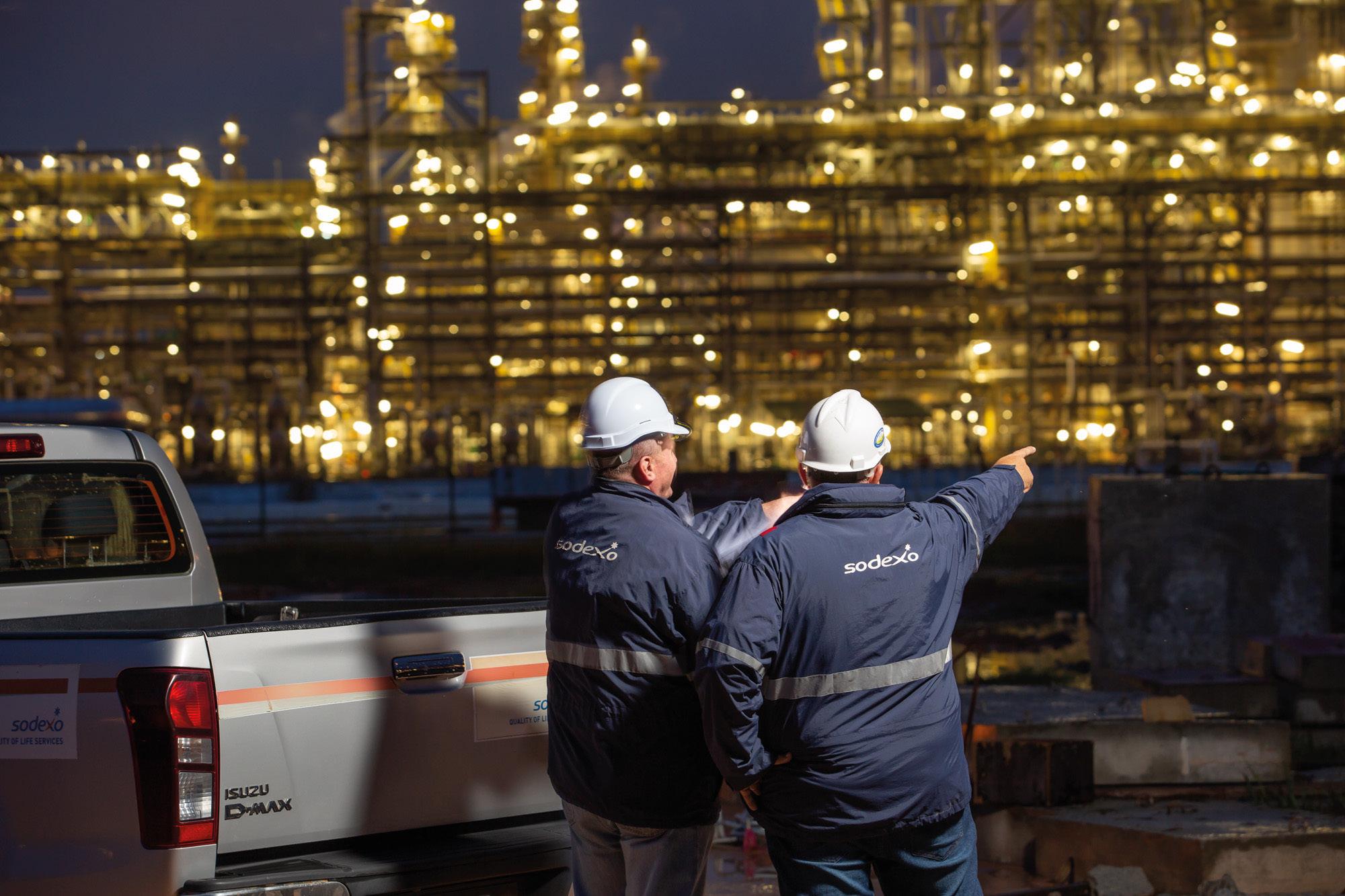
This entire policy is framed within the ambition to deliver sustainable development – harmonizing the company’s economic growth with the construction of a transparent and ethical relationship with stakeholders, alongside the consideration of the ESG needs and expectations of communities.
“Sustainability considerations are an integral part of our business planning and decision-making processes.
“They contribute to responsible resource management and allow us to better manage risks while achieving improved outcomes for all,” Quiñones explains.
Alongside the environment, Collahuasi recognizes the importance of sustaining people as its most valuable asset. Therefore, it promotes a company-wide culture of safety, inclusion, and personal development.
“Our continuous training programs ensure that employees and contractor partners can improve their skills and grow within the organization,” Gómez tells us.
The company also fosters an inclusive environment where diversity is seen as a strength and recognizes talent through incentive and recognition programs that value both individual and team contributions.
“The goal is not only to offer employment but create opportunities for professional growth,” he adds.
DEVELOPMENT PROGRAMS
In line with the aforementioned,
PARTNERSHIP WITH MINESENSE
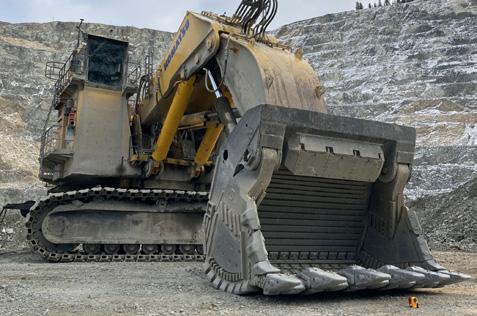
Collahuasi’s partnership with MineSense is transforming North America operations, leveraging the power of data through technologies such as ShovelSense® and BeltSense® to revolutionize ore stream management. Through MineSense’s solutions, companies can achieve complete ore stream coverage, enabling real-time, actionable insights that drive downstream optimization, maximize metal recovery, and improve sustainability.
MineSense’s revolutionary ShovelSense technology powers mine-to-mill optimization, beginning at the point of extraction. ShovelSense delivers several advantages at the mine face, beginning with accurate ore characterizations and grading with each bucket. Equally, ShovelSense seamlessly integrates with Fleet Management Systems to enable automated truck routing to the mill, stockpiles, or waste dump based on the payload grade to greatly increase recovery and reduce dilution.
Deployed in strategic areas along the grinding circuit, BeltSense provides continuous material tracking to further optimize and improve ore control and enhance downstream performance at the mill.
Collahuasi exemplifies the success of MineSense’s innovative technologies, achieving significant improvements in efficiency, productivity, and profitability while setting new benchmarks for operational excellence.
Collahuasi has developed a range of employee development programs.
Among them, the Professionals in Training initiative seeks to strengthen and diversify its portfolio of emerging professionals, encouraging their participation in and contribution to various strategic and functional areas of the company.
Alongside its employee development
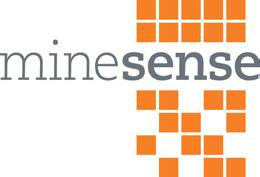
www.minesense.com
programs, Collahuasi’s local supplier development programs encourage the hiring of regional companies, generating employment and economic growth in the Tarapacá region.
During 2023, 47 percent of supplier spending was made with local or mixed companies, reaching $1.398 million across 853 companies.
“We seek to be much more than
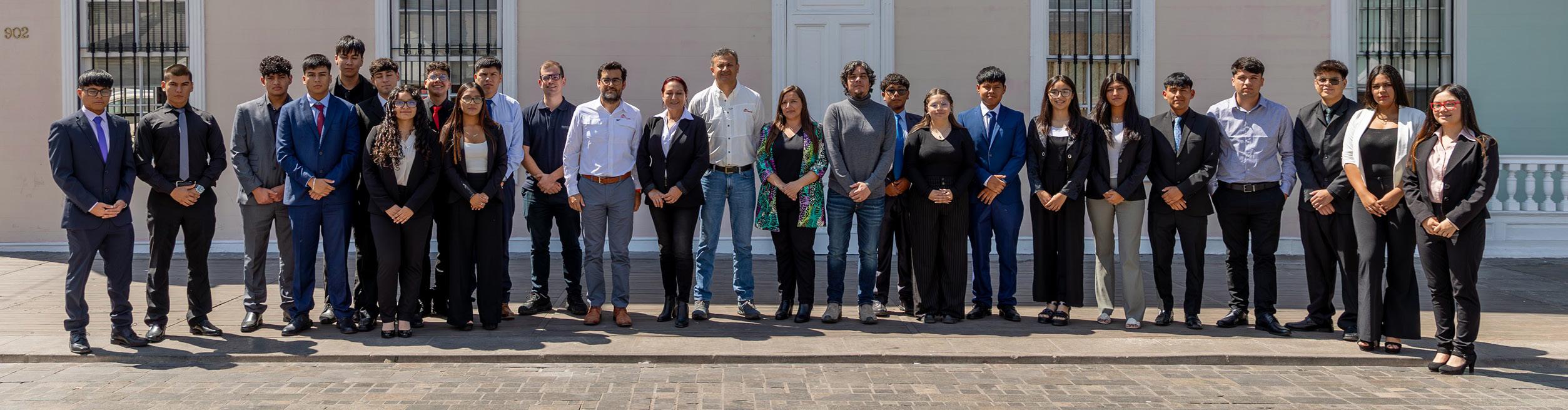
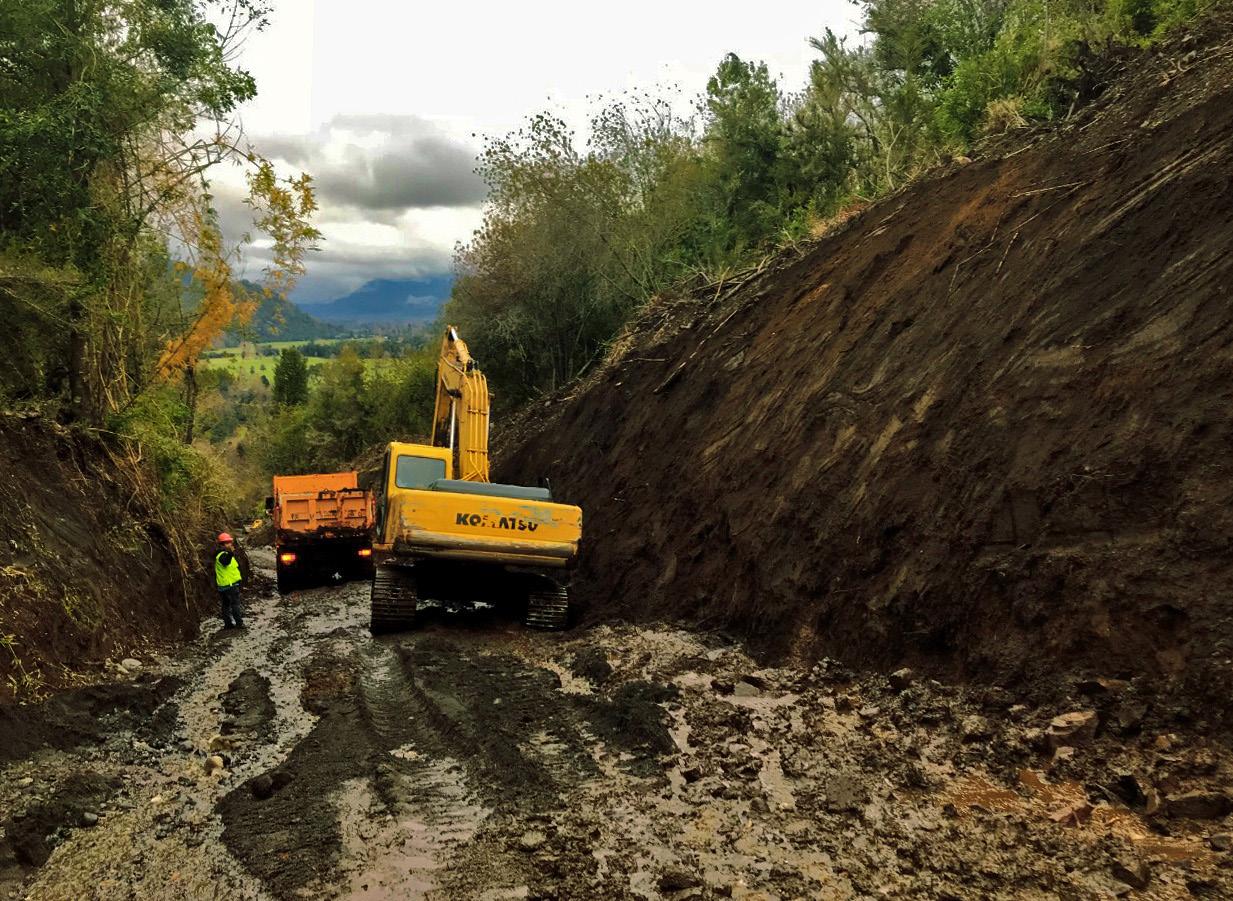
WE BUILD quality of life
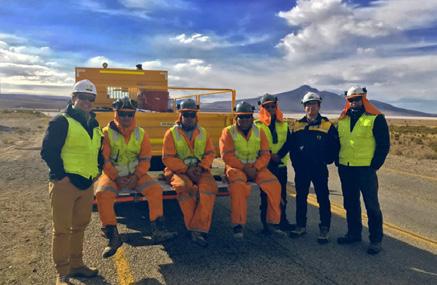
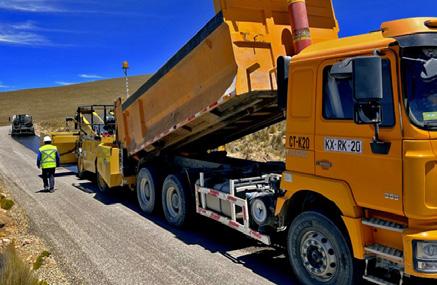
Management: maedo@eltoqui.cl | jhernandez@eltoqui.cl | chernandez@eltoqui.cl Compliance Director: vsandoval@eltoqui.cl | +56979690098
just a copper mining company – our purpose is to contribute to a better society,” asserts Dyer.
Collahuasi’s local supplier development programs are part a series of initiatives and measures that go beyond the business.
“We also maintain commitments with different indigenous and local organizations which, among other things, consist of carrying out participatory environmental monitoring that considers flora, fauna, and water resources,” adds Quiñones.
By joining community organizations in this work, the company ensures complete traceability regarding its work methodologies, measurements, and reporting.
“In this way, we have made progress in achieving greater transparency and strengthening trust in our management,” he points out.
LOOKING AHEAD
Going forward, in the short term, Collahuasi’s priorities include expanding production capacity in a sustainable manner, implementing new technologies to optimize operations, and completing the construction of the C20+ project.
“We are also advancing our strategy of reducing carbon emissions and the digitalization of our processes,” Quiñones divulges.
In addition, the company is deepening its commitment to local communities by expanding regional development programs.
Collahuasi is also working to deliver its medium and long-term growth agenda through the implementation of various ongoing projects.
“Given the aforementioned potential of Collahuasi´s resources, this includes the advancement of studies, which will allow us to continue on the pathway of growth for our

Founded and led by engineers with over 25 years of experience,
itself as a
in
Focused on exceeding client expectations, El Toqui stands out for its adaptability to industry challenges. Through an innovative vision and personalized service, it strives not only to meet standards but also to create a positive and responsible impact on the environment. Its leadership team is firmly committed to excellence, ensuring that every project meets the highest standards of quality and sustainability.
www.eltoqui.cl

company,” he adds.
As Collahuasi’s purpose and values state, it seeks to challenge the present to contribute to a better society for the future.
“Through this goal, we seek to create a positive legacy for our employees and local communities, as well as for the country,” prides Gómez.
Equally, it seeks to be a facilitator of development – socially, economically, and environmentally.
“All of this aligns with our commitment to develop a more sustainable mining company,” he passionately concludes.
www.collahuasi.cl/en/

MINING FOR THE FUTURE
Amongst a major revival in the global platinum group metals industry, JJ Joubert, Senior General Manager of Bokoni Platinum Mines, delves deeper into the company’s proud heritage, innovative mining technology, and commitments to community development
Writer: Lucy Pilgrim | Project Manager: Thomas Arnold
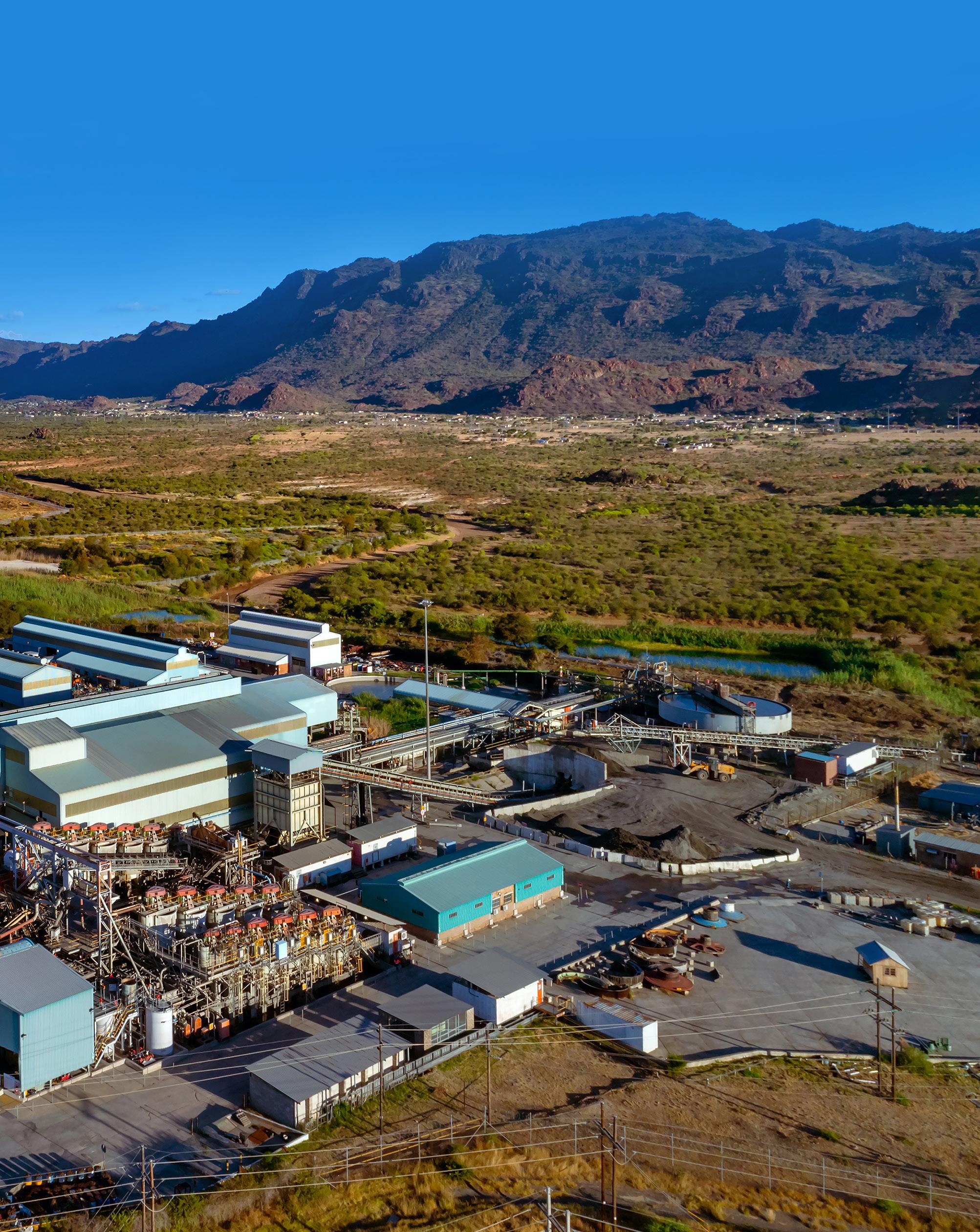
As the northernmost province of South Africa (SA), the never-ending horizon of Limpopo holds a microcosmic collection of Earth’s most outstanding views, histories, creatures, and natural resources.
Indeed, jutting out into the vast, iridescent skies of the province is an eclectic topography of mountain ranges and passes, building a unique landscape that acts as the stepping stones of giants.
Surrounded by these sky-splitting wonders, humans and animals alike gaze upon the rudimentary drawings of those who walked the land thousands of years ago, stamped across many of the mountains’ caves.
A particularly exquisite example is the Makgabeng Plateau which has been pulled and pushed into a convoluted shape, creating iconic rock formations. This site acts as a natural canvas for primitive paintings of hunter-gatherers with bows and arrows as well as large, elementary animals, providing an insight into the stories of ancient Limpopo.
These magnificent but looming mountains gently transform into the rolling hills of the province’s many rural areas and world-renowned nature reserves.
In fact, Limpopo is home to Kruger National Park, the largest wildlife sanctuary in SA. This two million hectare (ha) nature reserve is a particularly special patch of land as it is home to some of the world’s most majestic creatures, including the ‘Big Five’.
The province has for centuries been the stomping ground of African lions,
THE BIC AT A GLANCE
• The large igneous complex was formed in the Paleoproterozoic era over two billion years ago.
• The complex is so abundant with PGM resources that even after a century of mining, 192,000 tonnes of platinum remain.
• At the current rate of mining, the BIC will not be depleted of resources for another 700 years.
• The BIC consists of underground and open pit mining.
• There are currently 30 active organisations in the complex.
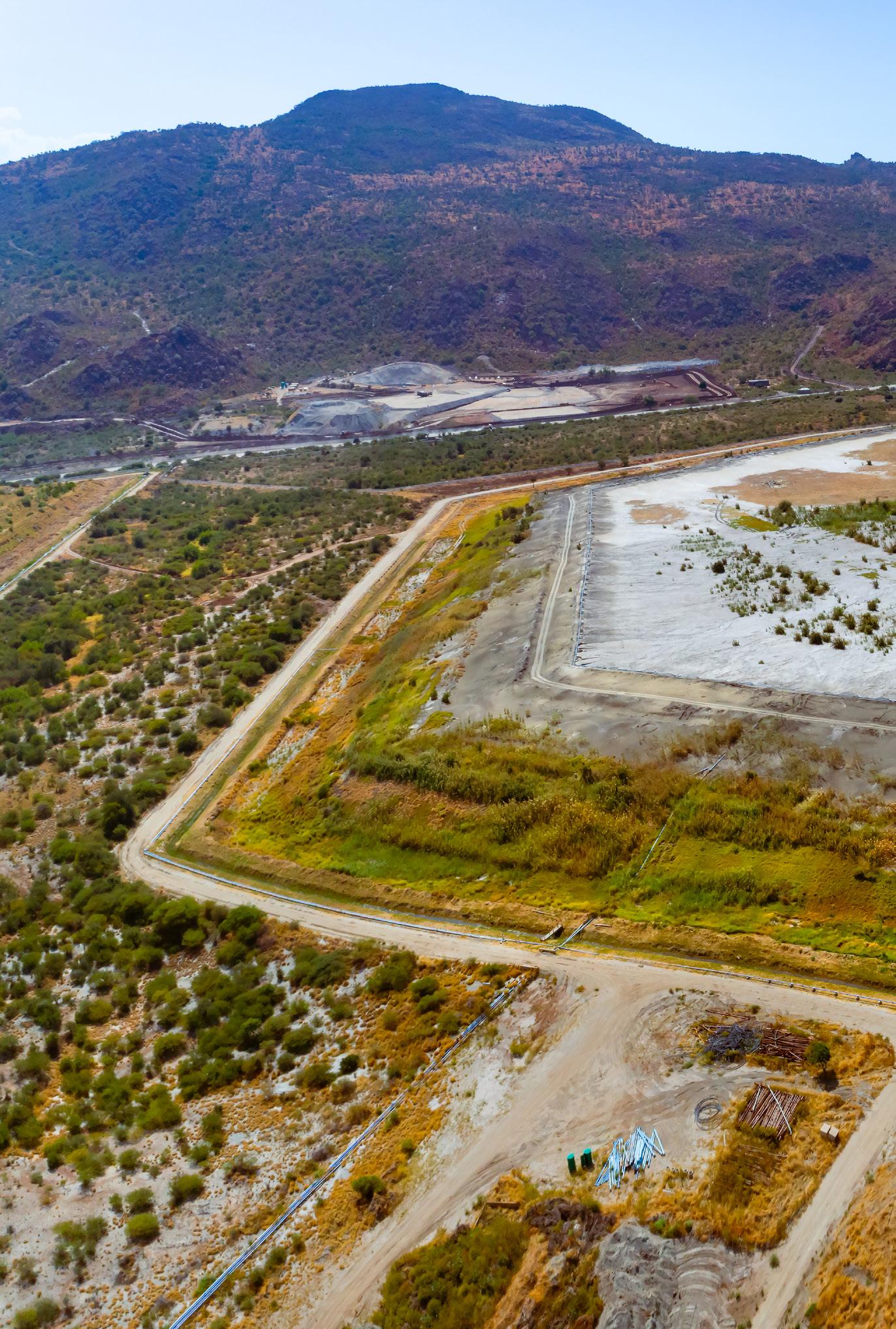
leopards, rhinoceroses, elephants, and cape buffaloes who serenely graze upon the emerald pastures of the area’s undisturbed bushvelds.
Yet, unbeknown to Limpopo’s range of magisterial beasts and roaming creatures, a complex flurry of activity occurs beneath the Earth’s crust. Indeed, nestled under the surface are some of Africa’s most bountiful natural resources and globally desired minerals.
Specifically, the Bokoni mine, one
of the continent’s largest open pit mines, heralds some of Africa’s most expansive mining discoveries and is headed by world-renowned Bokoni Platinum Mines (BPM).
PLATINUM GROUP METALS’ RESURGENCE
Located on the eastern limb of the Bushveld Igneous Complex (BIC), BPM’s platinum mine sprawls across an impressive 15,000ha. The pear-shaped complex covers
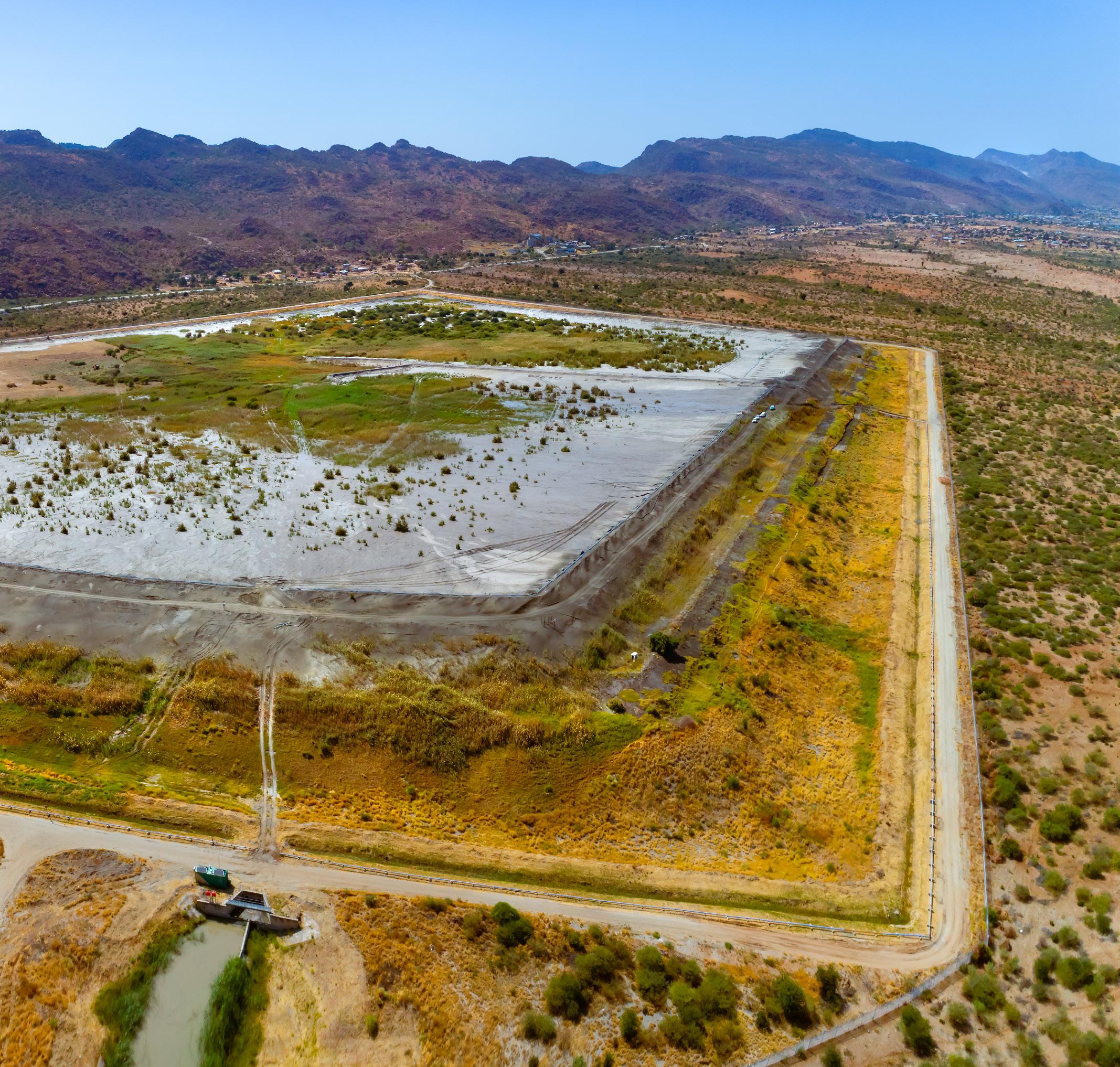
an astonishing 66,000 square kilometres, reaching across several South African provinces including Mpumalanga, North West, and Gauteng, as well as Limpopo. Contributing 75 percent of the world’s platinum and around 50 percent of total palladium, the BIC possesses an enviable collection of platinum group metals (PGMs), including platinum, palladium, osmium, iridium, rhodium, ruthenium, and much more. The abundance of PGM resources
across the complex has a long and storied history spanning over a century. Specifically, the BIC contains the largest ultramafic igneous rock formation on the planet, holding over one million cubic metres of igneous rocks formed over two million years ago.
Initial discoveries of the metal group occurred in 1924 when a collection of platinum nuggets was uncovered in a riverbed north of Pretoria. A further two platinum deposits were brought
to light soon after, each at 100 metres in length. Due to the abundance of resources found, the area was named and crowned as one of Africa’s greatest PGM sites.
However, the South African PGM sector has faced substantial challenges in recent years, experiencing pressures caused by rising operating costs and falling market prices, making some of the country’s largest platinum mines increasingly difficult to operate.
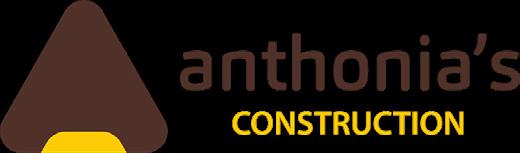
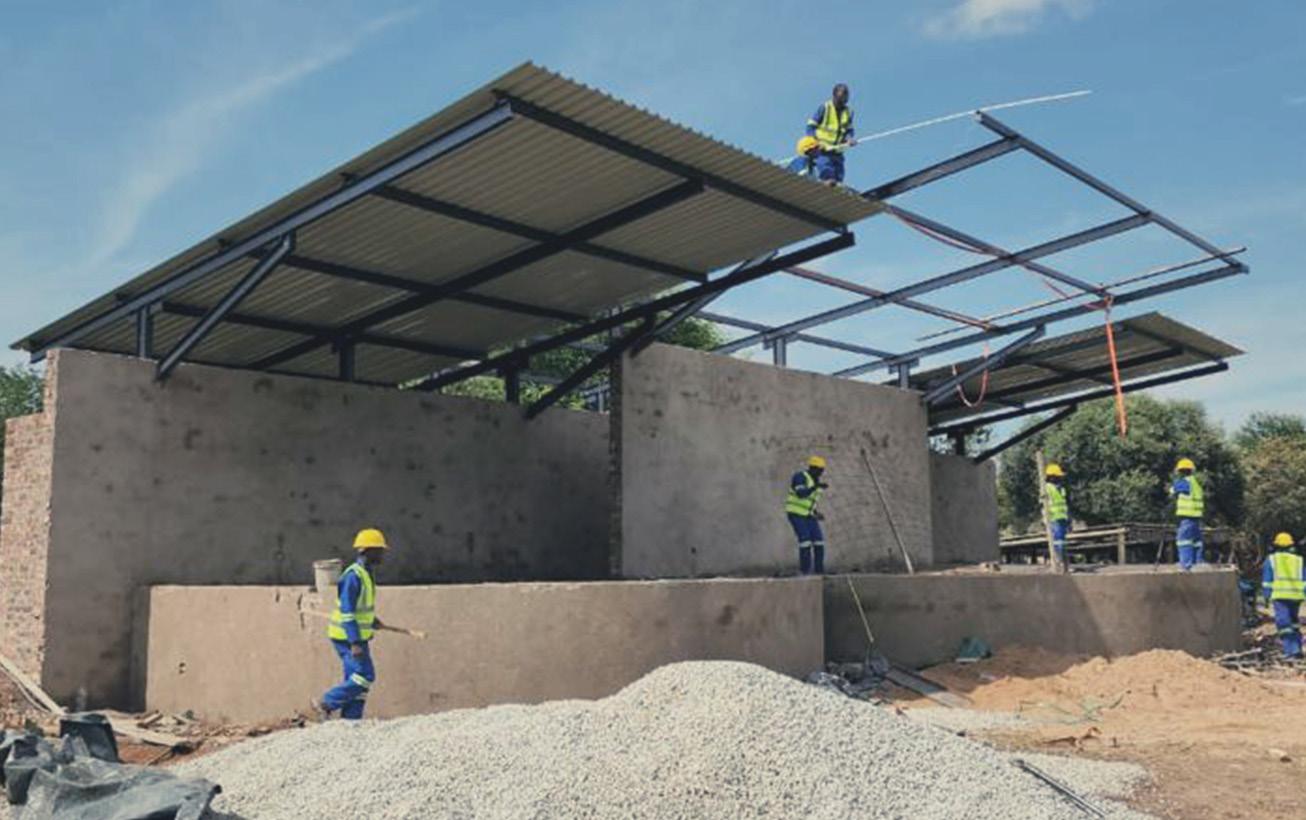
Build your next project with professionals
ABOUT US
Construction building and renovation experts
Anthonia’s Construction is a 100% black female-owned and controlled organisation that is registered with the NHBRC. The company was established in 2018 and consists of a consortium of experienced businesses that specialise in the construction and manufacturing industries. We have the commitment, skills and resources to meet the requirements of our customers. We are a hands-on, start-to-finish group of experts taking on the challenge of rebuilding South Africa and beyond.
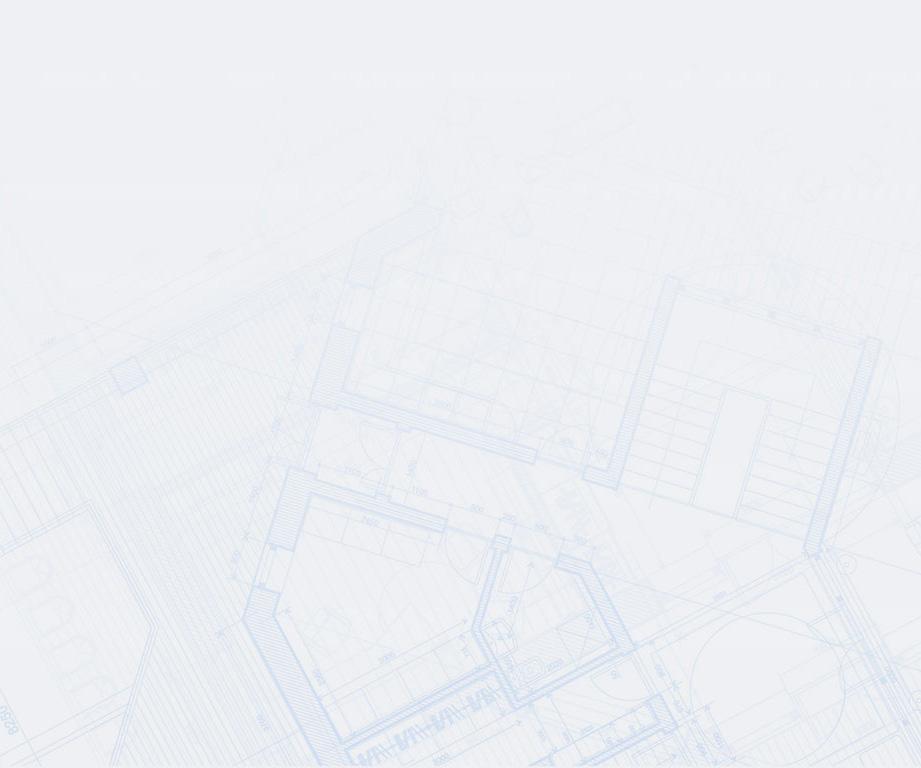
Core Values
• Honesty
• Integrity
• Reliability
• Professionalism and Quality
• Confidentiality and Integrity
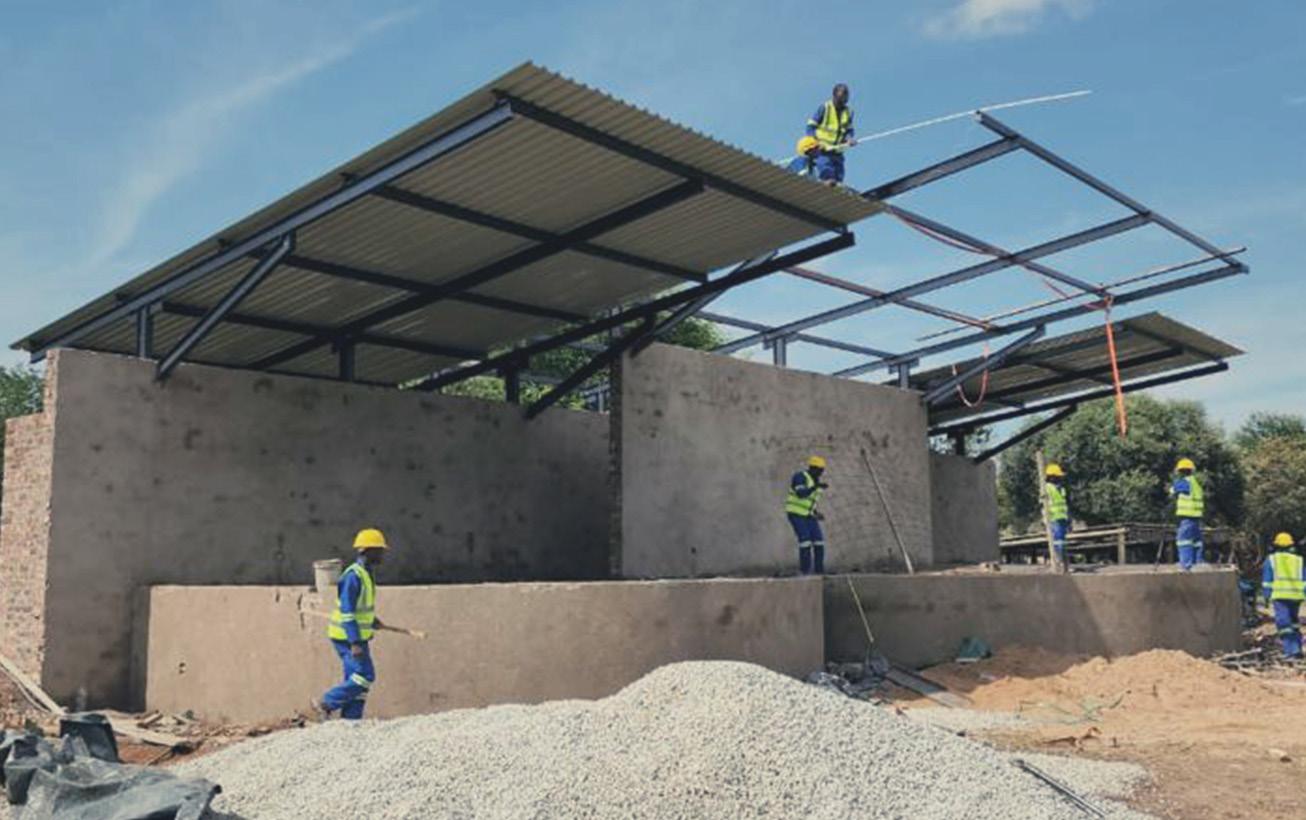
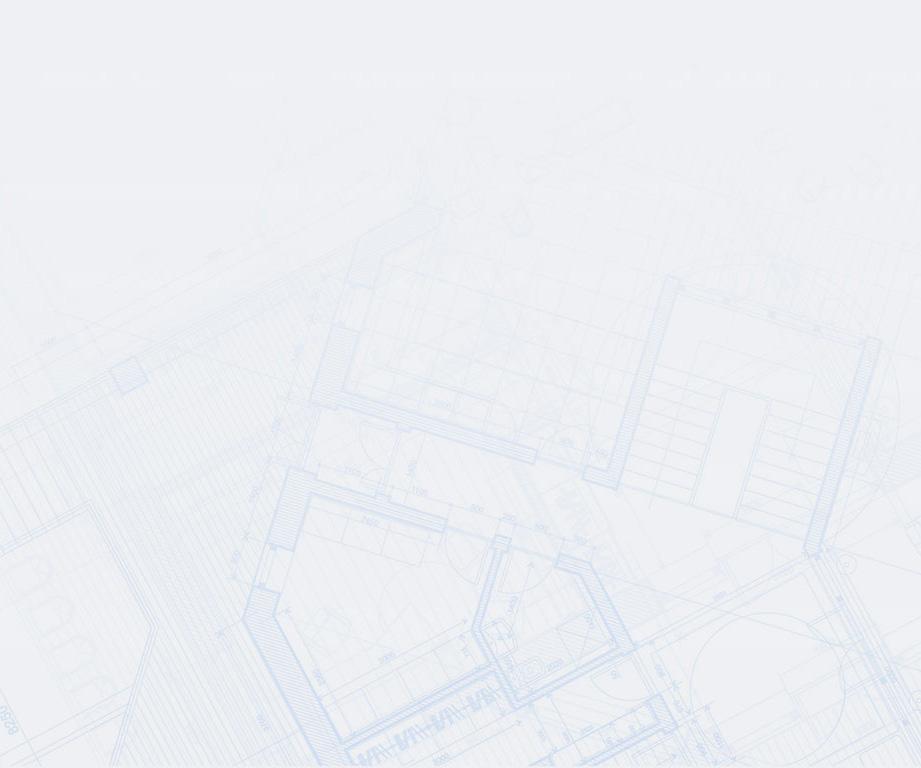
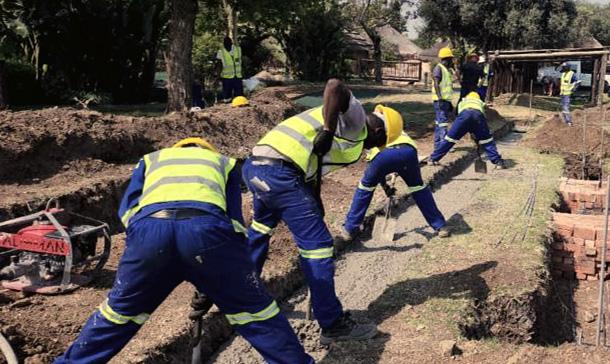
Eco‐Friendly Solutions
We follow stringent guidelines and methodologies to deliver the finest graded structures and products which are friendly to our environment.
Quality Guarantee
Using industry management tools and techniques, we are able to guarantee our customers exceptional products and services.
Industry Experts
We invest in expertise to reaffirm our customers’ peace of mind. It is our utmost responsibility to ensure satisfactory results in everything we touch.
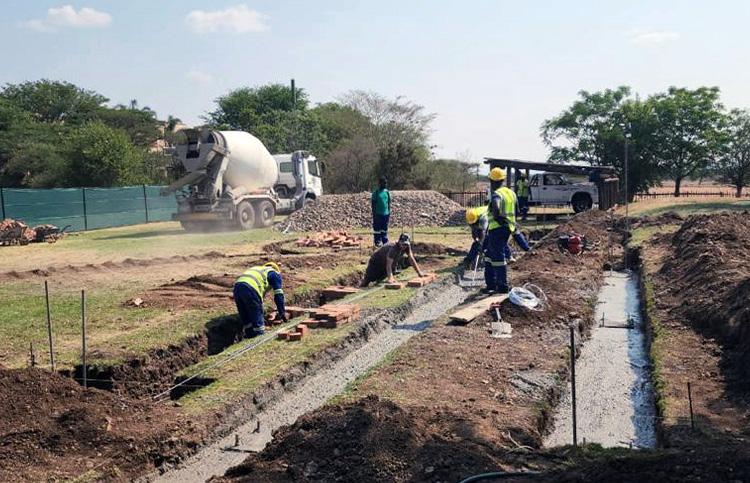
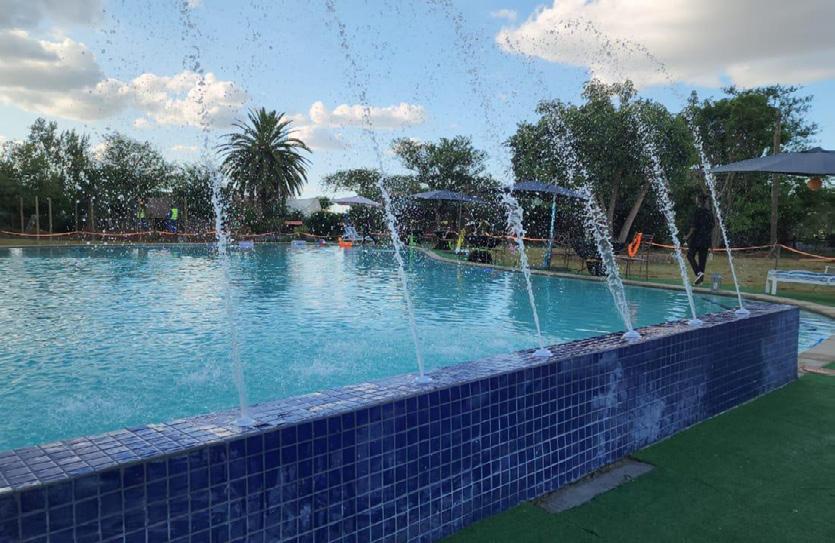
Mining Services
From site preparation, excavation, and blasting to mineral testing, tailings management, and environmental compliance, the company provides extensive support for mining operations, including the delivery of mine mechanical equipment, geotechnical services, and safety inspections.
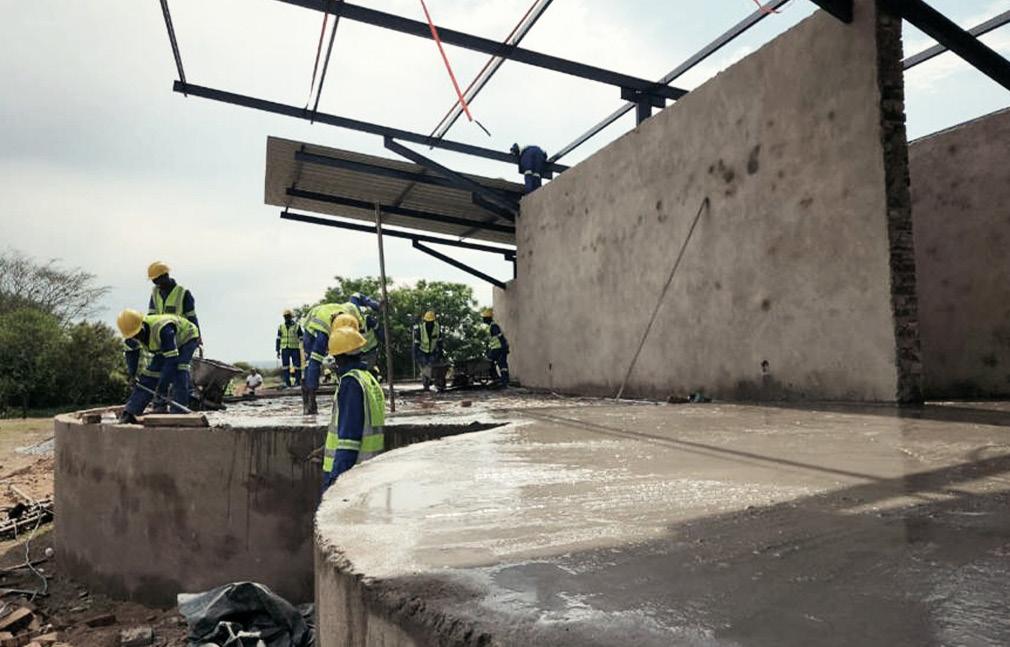
WHAT WE DO
Bringing new thinking to the ways of old
We specialise in delivering high-quality results, timely project completions, and exceptional customer satisfaction. Let us bring your projects to life with our expertise and dedication.
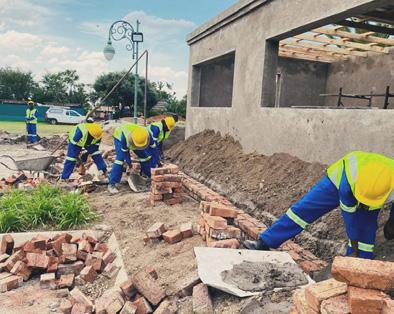

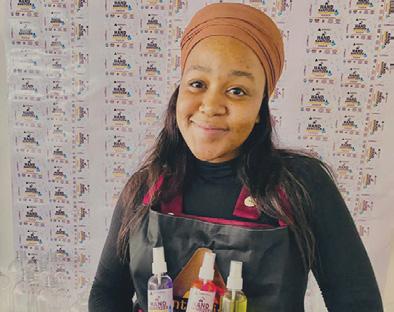
General Construction
We manage infrastructure, treating it as a developmental production.

Property Maintenance
We offer professional home renovation, home remodeling, office renovation and office remodeling services.
Sanitisers
We manufacture bulk hand sanitisers, locally produced in South Africa.
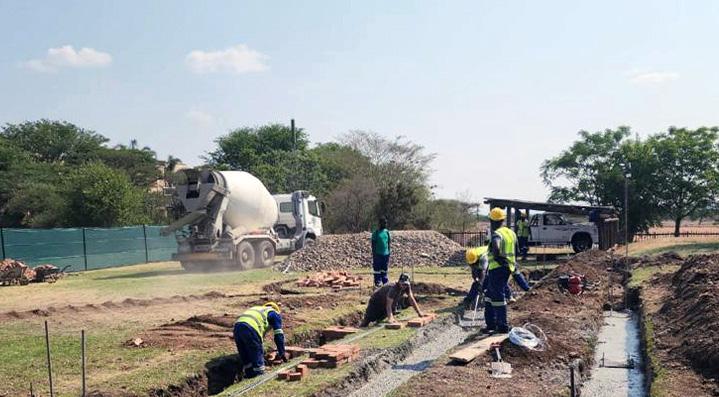
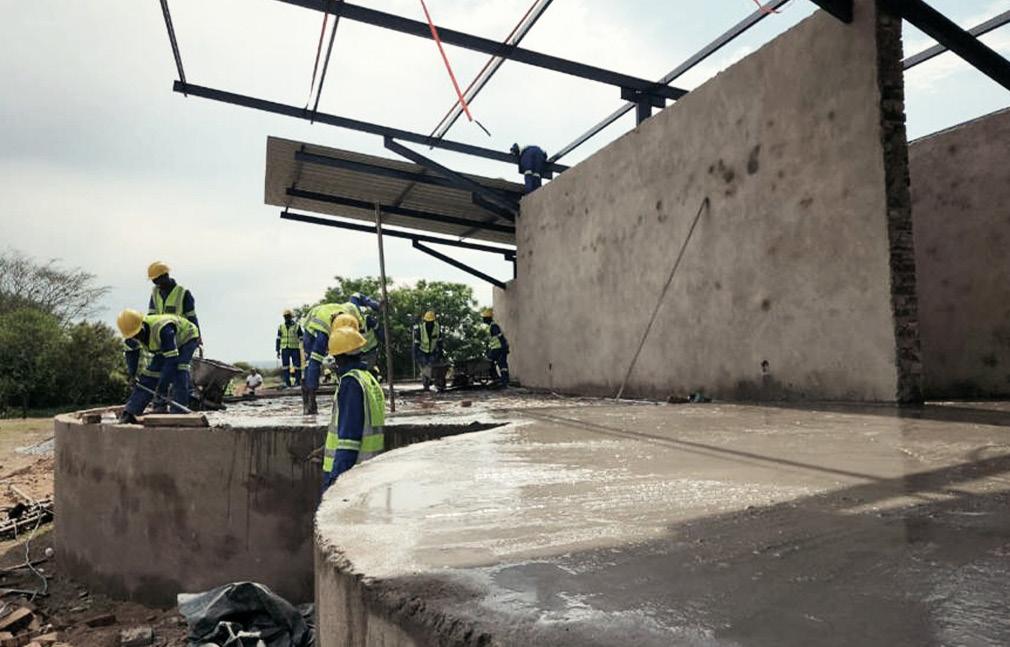
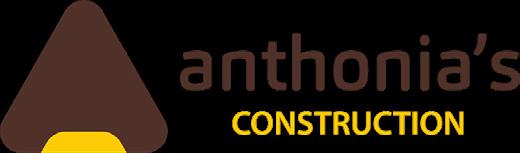
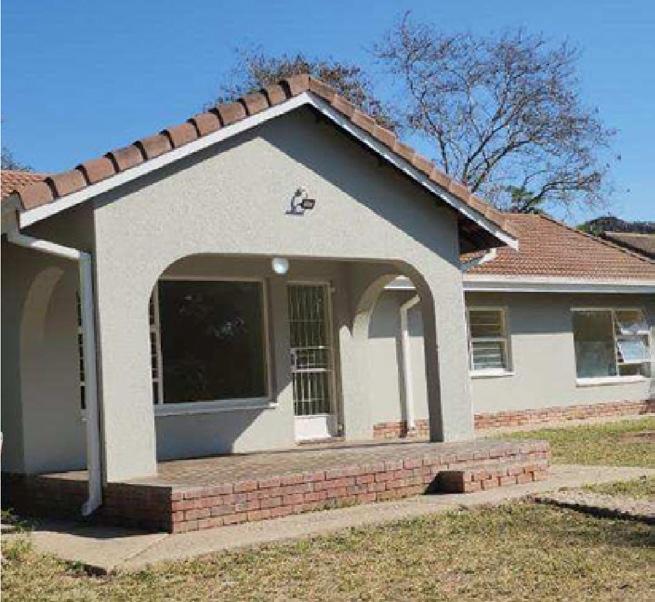

Our reach extends beyond the borders of South Africa.
We are a company that prides itself on 'family' culture. We seek high calibre people and set even higher standards. We are a company that has, at its core, a team philosophy that is tightly integrated in our day-to-day operation – there is a real sense of responsibility among our staff. We believe in nurturing the skills of our team members and providing growing levels of responsibility and opportunity. CONTACT
44 Dorp Street, Polokwane (LP), South Africa (+27)61 586 1506 (+27)68 069 6491 admin@anthoniasconstruction.co.za anthoniasconstruction.co.za
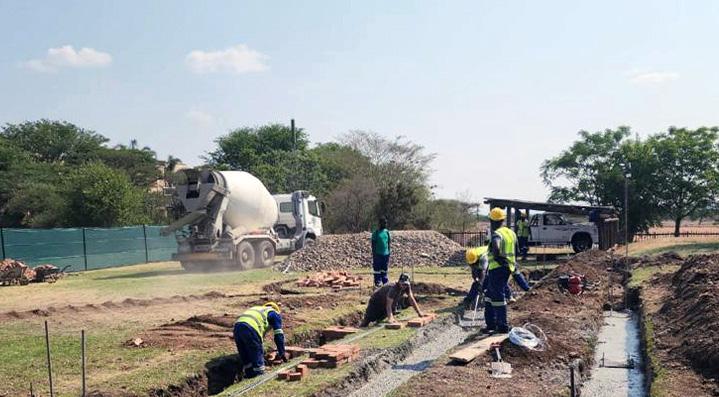

However, the industry is currently experiencing a major turning point, leading to a resurgence in PGM demand. After decades of growth in the international electric vehicles (EVs) market, manufacturers are looking at other, more reliable options.
As a result, hybrid electric vehicles (HEVs) are an increasingly popular alternative as they provide greater range and power and are becoming a more cost-effective option, whilst still allowing motorists to reduce their environmental impact. As a result, the amount of HEVs sold in 2023 increased by 18 percent compared to the corresponding quarter the year before.
Likewise dissimilar to EVs, the catalytic converter technology used in HEVs requires a substantial level of PGMs – an even greater amount than is typically used in conventional internal combustion engines (ICEs) found in motor vehicles, once again contributing to the uptick in demand. Consequently, with reports indicating that the rise in the use of HEVs could last until 2030 or even longer, the recent resurgence in the global PGM market could be set
ARM GUIDING VALUES
• Aim for operational excellence.
• Provide a safe and healthy work environment.
• Maintain a non-discriminatory workplace.
• Improve the lives of those living in communities neighbouring its operations.
• Work responsibly to achieve a balance between the economic, societal, and environmental aspects of the business.
• Maintain the highest standard of corporate governance.
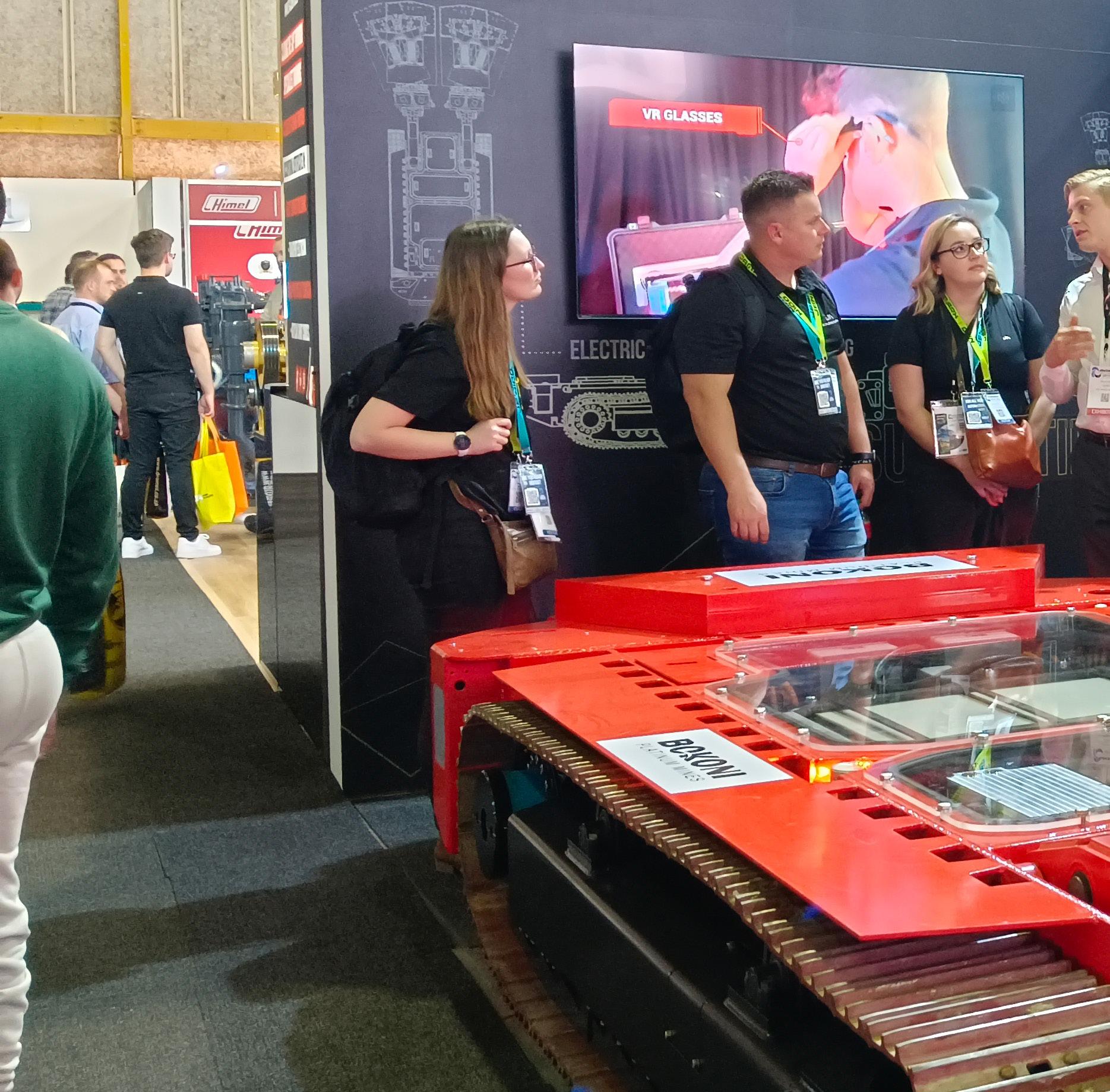
to last, which bodes well for many mining entities that are currently witnessing a major revival in prices and mine site longevity.
Even though BPM has been no stranger to the industry’s previous stagnation, the company has planned accordingly to ensure that it sustains its ongoing success and capitalises on growing hybrid technology, maintaining its position as SA’s second-largest PGM resource and firmly establishing its presence in the diverse sector.
“Although we believe it will recover, the PGM market is under extreme pressure. Therefore, we have slowed down our ramp-up and expansion but have also positioned ourselves well on the cost curve to exploit improvement in the prices,” introduces JJ Joubert, Senior General Manager.
As such, BPM is well-positioned to capitalise on the market’s recovery in the face of changing global demands and contribute to the long-term sustainability of the industry in SA.
A NEW CHAPTER
BPM’s journey to its present enviable success and reputation is marked by transformation and innovation.
Despite previously facing financial challenges that resulted in a six-year period of care and maintenance, the company’s future took a positive turn in September 2022 when Africa Rainbow Minerals (ARM) acquired the mines from Anglo American Platinum and Atlatsa Resources, marking a new chapter for BPM.
Today, ARM is the sole owner of the company, granting it a vast network of resources and market opportunities, particularly given the fact ARM stands as the leading South African mining and minerals business with operations across the country as well as in Malaysia.
Established 30 years ago, ARM has experienced a unique journey, leveraging both joint ventures and stakeholders to facilitate enhanced mining projects. Through four divisions, the organisation extracts

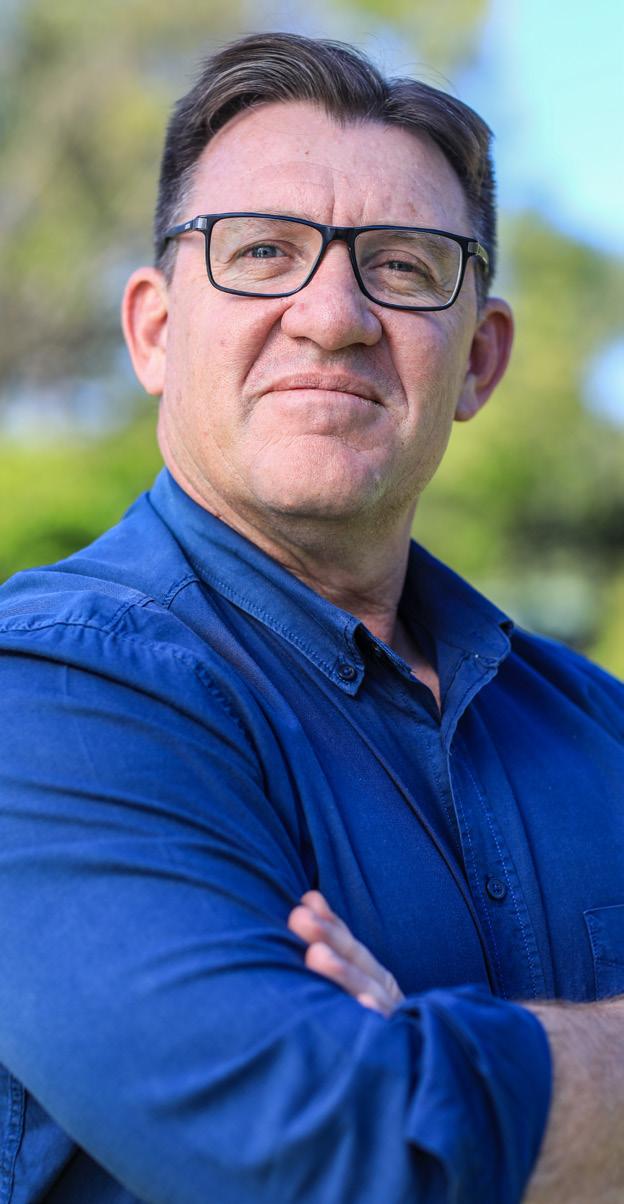
“THE SUCCESSFUL IMPLEMENTATION OF NRE ACROSS OUR MINES WILL SEE HUGE BENEFITS IN THE SAFETY IN PRODUCTION FACILITIES FOR THE MINING INDUSTRY AT LARGE”
– JJ JOUBERT, SENIOR GENERAL
MANAGER, BOKONI PLATINUM MINES
and beneficiates iron ore, manganese ore, nickel, coal, and PGMs in SA, making it a major player in the country’s mining landscape.
Despite a significant decrease in PGM prices over the past five to 10 years – causing many other platinum organisations to suffer unprofitable production – ARM strongly believes in the prosperity of BPM and its investment attractiveness in an industry that is experiencing an upward trajectory.
Since becoming a part of ARM’s extensive and diversified portfolio over two years ago, BPM has, in turn, become a valuable asset for the organisation and its platinum
discovery and mining activities.
“BPM enhances ARM’s position in the global mining sector, particularly in the platinum market,” Joubert insights.
“It strengthens the organisation’s competitive edge and market presence, attracting potential investors and partners.”
The PGM orebodies mined by BPM complement ARM’s platinum division in particular by reducing reliance on a single commodity and balancing the company’s exposure to any market fluctuations, which is particularly critical given the historical turbulence of the African PGM sector.
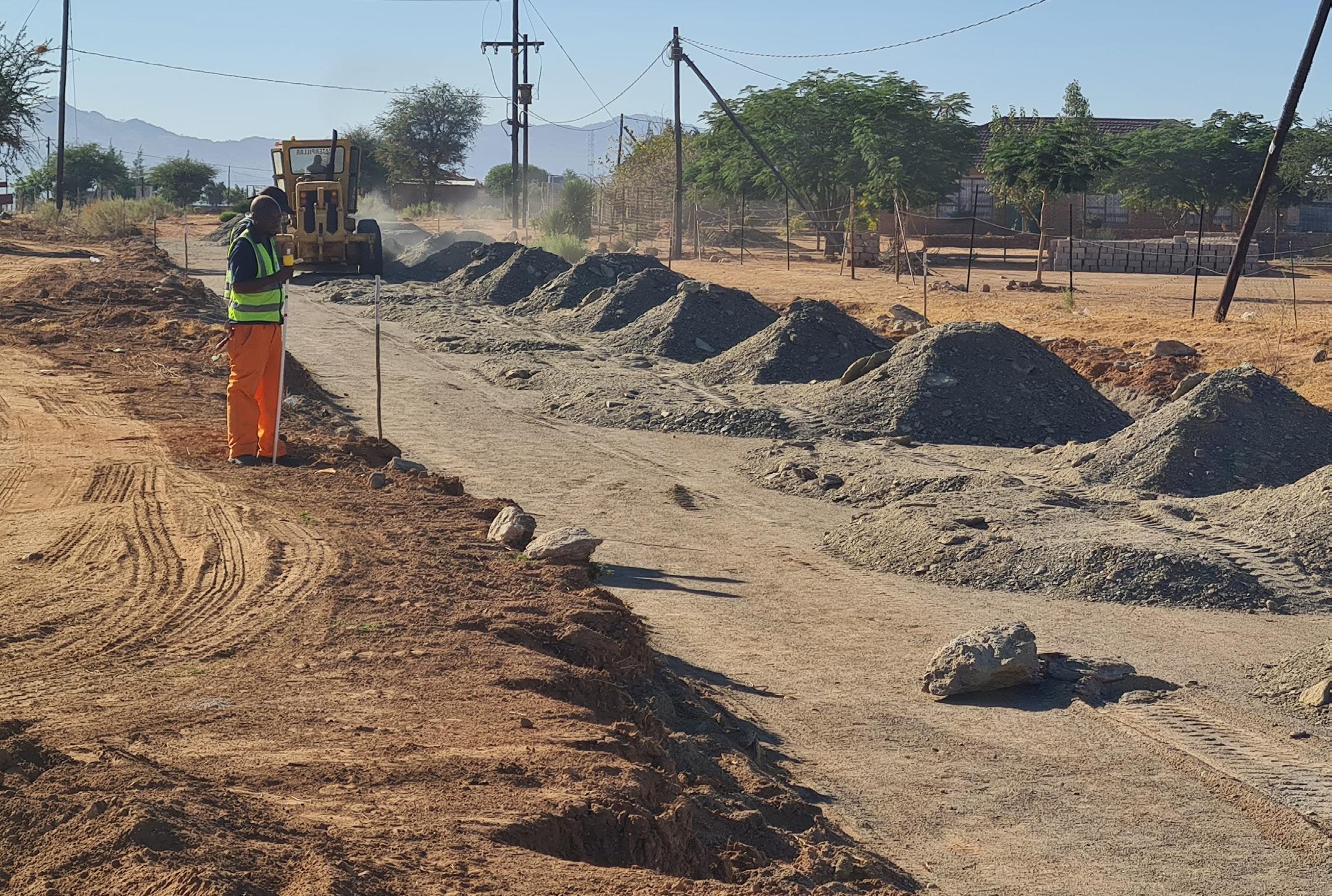
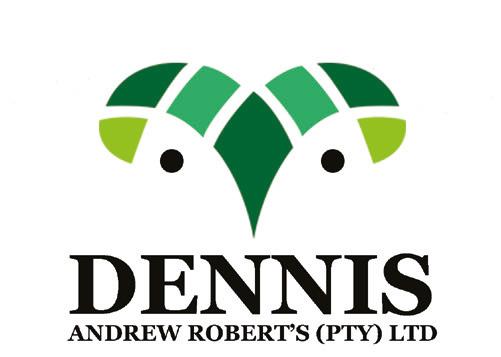
Quality First
Dennis Andrew Roberts (Pty) Ltd is a leading African construction company with a proven track record of success. Offering a wide range of construction and add-on services that ensure the highest possible quality, the company promises client satisfaction in every project
Presenting a comprehensive range of civil construction, water sanitation, and reticulation services, alongside fibre projects and add-on services, Dennis Andrew Roberts (Pty) Ltd (DAR) is a visionary construction partner for the industry.
Driven by a mission to provide world-class services to its clients, the company enables organisations to achieve their goals and objectives through its effective and efficient use of resources.
Under the expert guidance of Managing Director, Thulani Mashele, principles of safety, health, environment, risk, and quality (SHERQ) are closely followed, resulting in excellence across every aspect of DAR’s operations.
A strong advocate of a hands-on management approach, Mashele ensures the highest standards of quality and safety are met through his active on-site engagement with projects, underscoring the entire company’s commitment to delivering top-notch services.
DAR’s adherence to SHERQ principles highlights its dedication to maintaining a safe and healthy work environment, minimising environmental impact, and effectively managing risk.
As such, the company’s core values are centred around professionalism, high-quality products and services, and empowering the communities in which it operates.
QUALITY MANAGEMENT
DAR’s implementation of a robust quality management system (QMS) helps it to consistently deliver high-quality outcomes, comply with regulatory requirements, and enhance client satisfaction.
Why choose DAR As a leading construction company with a well-established history, DAR ensures the highest quality, safety, and client satisfaction in each and every one of its projects.
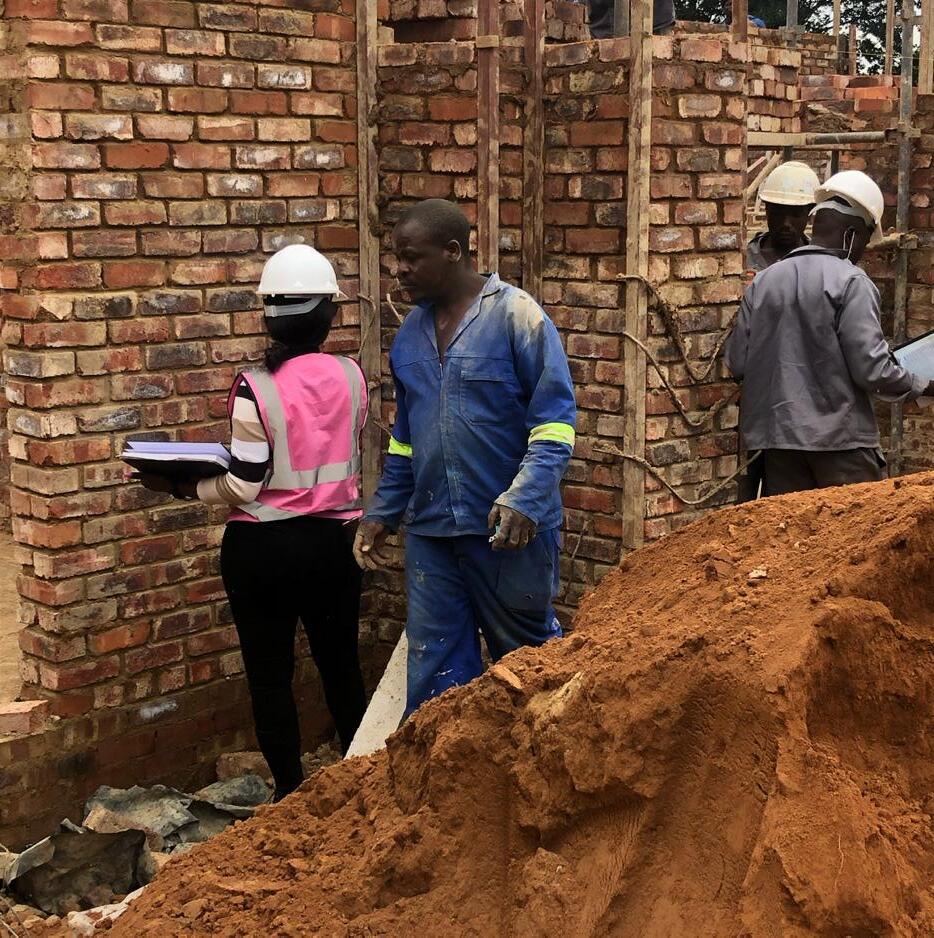
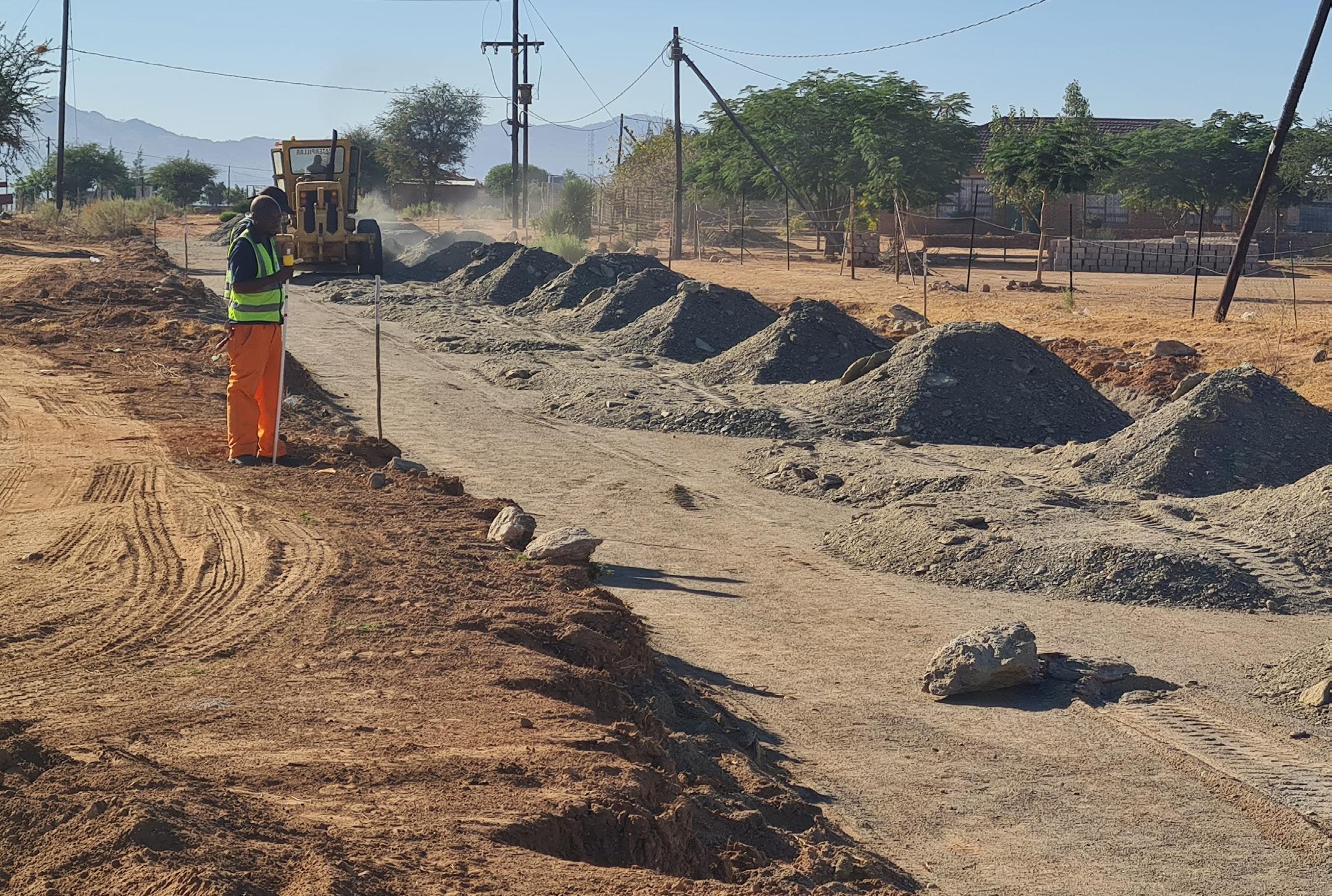
The company understands how a QMS is important in enhancing project quality, operational efficiency, and risk management. By consistently delivering exceptional projects, the company has built and maintains a strong market reputation.
Closely following the key components of a construction QMS such as quality planning, assurance, and control, as well as continuous improvement, DAR seeks to implement corrective and pre-emptive actions to improve processes and prevent issues recurring.
Furthermore, a QMS is promoted deeply within the company through comprehensive training, which includes outlining key principles and procedures. DAR also cultivates comprehensive documentation and record-keeping, maintaining stakeholder engagement through transparent quality expectations.
By following international QMS standards, such as ISO 9001:2015, ISO 14001:2015, and ISO 45001:2018, the company has a robust framework for quality assurance and continuous improvement.
HEALTH AND SAFETY
Alongside its high QMS standards, DAR recognises the importance of occupational health and safety (OHS) management, and its integral role in minimising risk, preventing workplace incidents, and promoting a culture of safety.
The company’s own OHS system ensures the safety and well-being of employees, legal compliance, risk management, and operational efficiency, all of which contribute to its strong reputation. This is due to the effectiveness of OHS management that helps improve client trust, employee morale, and the ability to attract new business opportunities.
Key components of OHS management include policy and objectives, hazard identification and risk management, training, incident reporting, and emergency preparedness and response.
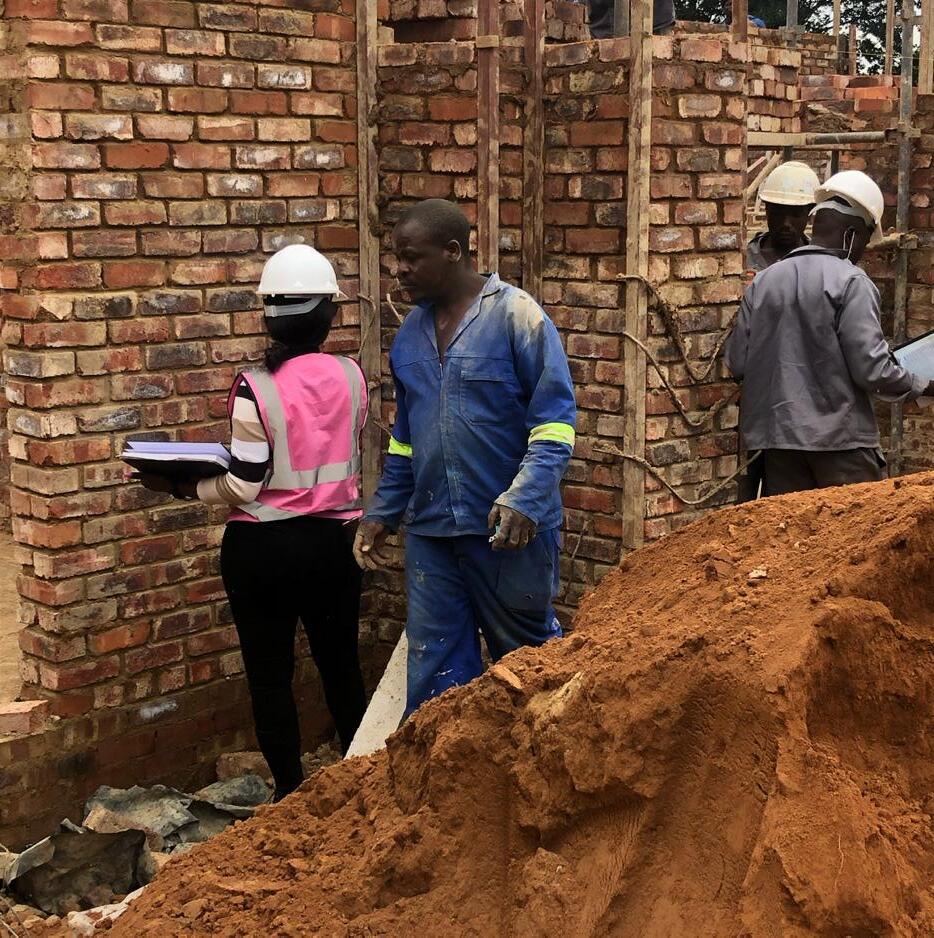
Alongside its other certifications and standards, DAR also holds ISO 45001:2018 and occupational health and safety assessment series (OHSAS) 18001, which combine to provide a framework to improve employee safety and reduce workplace risks for an optimal working environment.
By implementing a wellthought-out approach to OHS management, the
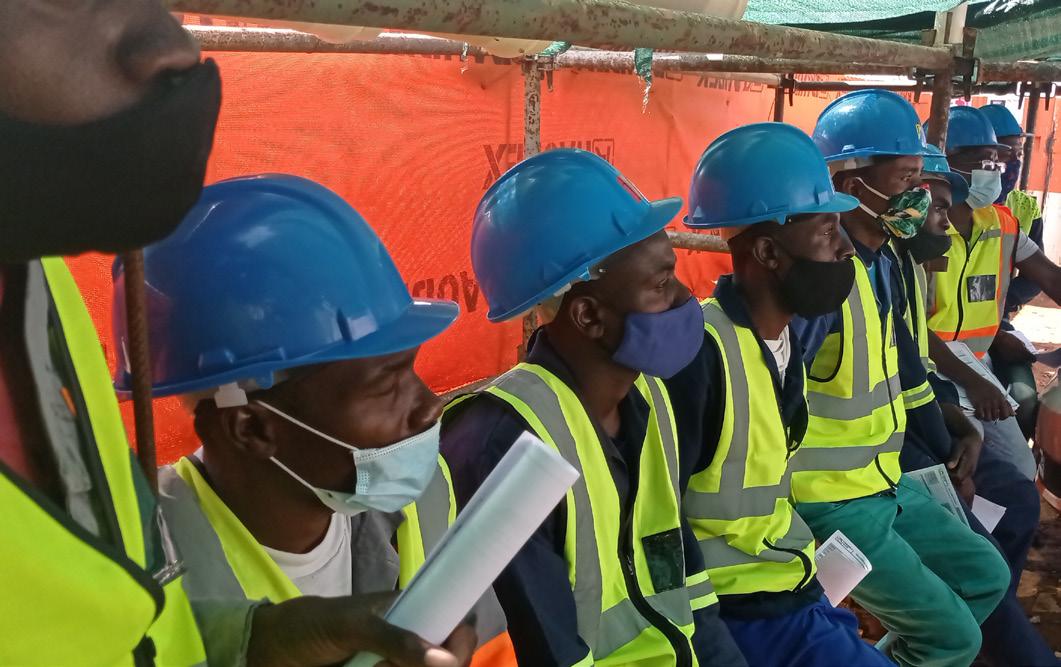
company has seen a significant reduction in workplace accidents, enhanced compliance with regulatory requirements and industry standards, and increased operational excellence.
SKILLS TRANSFER
Placing strong emphasis on skills transfer to the communities in which it operates, DAR seeks to empower society through sustainable business practices.
For example, it creates value for its labourers and subcontractors by prioritising upskilling and training, ensuring they gain tangible skills to enhance their capabilities when working on company projects. Its training programme goes beyond technical skills transfer by recognising the importance of a wellrounded skillset in its workforce.
DAR’s ongoing collaboration with Nkuhlwana Trainers & Projects demonstrates its strategic approach to skills development and its dedication to providing accredited programmes and competency certificates to its staffbase, adding depth to its commitment to comprehensive skills transfer.
DAR’S PRODUCTS AND SERVICES – AT A GLANCE
Project Management
A dedicated project management team oversees all aspects of construction projects, from planning and design to construction and completion. Working closely with clients to understand their needs and goals, whilst developing a project plan that meets these requirements, the team ensures that projects stay on track and within budget.
Civil construction works
• Road
• Bridge
• Storm drainage
• Water and sewer line
• Earthworks
• Site preparation
Building construction works
• Residential
• Commercial
• Industrial
• Institutional
Water sanitation and reticulation works
• Water treatment
• Wastewater treatment
• Water distribution
• Wastewater collection and disposal
Fibre projects
• Installation
• Repair and maintenance
• Network design and engineering
Add-on services
• Fibre installation, repairs, and maintenance
• OHS
• Environmental management
This makes ARM’s position even more lucrative, as BPM’s operations will contribute a significant revenue stream through the production and sale of other PGMs, thus helping to support the financial health of ARM and allowing it to invest in other projects and strategic initiatives.
SUPPORTING ARM’S CORPORATE GOVERNANCE
On top of the projected market prosperity, the successful management of BPM positively impacts ARM’s reputation and relationships with local communities, regulatory bodies, and other stakeholders.
“ARM is fully dedicated to BPM’s revival in a way that collaborates with local communities,” expands Joubert.
Given ARM’s extensive presence across SA, permeating into many provinces alongside Limpopo including Northern Cape, North West, Mpumalanga, KwaZulu-Natal, as well
as Sarawak in Malaysia, successful community engagement and environmentally conscious operations are increasingly important to the organisation.
So much so, ARM’s economic, social, and governance (ESG) practices infiltrate every aspect of the company’s operations as it is guided by ethical leadership that paves the way for integrity and respect across all mining activities.
Indeed, as an industry-leading business, ARM has a deep understanding of the impacts it has on the world around it and therefore strives to embrace opportunities to make a positive contribution to the growth and development surrounding societies.
“Positive community engagement and responsible mining practices bolster ARM’s social license to operate and contribute to its overall sustainability,” enlightens Joubert.
As a continuation of this, the
BPM’S PROCUREMENT PROCESS
The company deploys a procure-to-pay strategy at the beginning of each mine site’s production, which includes a number of purposeful and engaging steps:
1) Identifying a resource or material need: The mine site team identifies that a specific product needs to be supplied or a service delivered.
2) Appointing a supplier: The procurement team goes through the process of searching for a supplier that will meet their particular business needs. Significantly, BPM follows a competitive process in which all submissions must follow market-related pricing.
3) Contracting the successful bidder: The company negotiates and signs a contract with the successful bidder. BPM then dictates the terms and conditions of the contract to make sure that all the necessary requirements are met, including pricing, delivery, and warranties.
4) Verifying that the work is completed to the required standard: The company ensures that goods or services have been provided to a high standard as set in the contract whilst also checking for any defects or issues.
5) Payment: Once the work is completed to an adequate standard and appropriately verified, BPM ensures that it pays suppliers on time and according to agreed terms and conditions.
company invested ZAR124 million in corporate social responsibility (CSR) in the 2022 financial year, and a further ZAR371 million in skills development and training.
This financial input is a testament to ARM’s dedication to fostering positive relationships across its local communities and amongst staff.
Meanwhile, through a highly comprehensive sustainable development model, the company explicitly acknowledges that good corporate governance and ample environmental stewardship are also conducive to creating strong relationships with shareholders and in turn generating greater socioeconomic value for the community.
ARM’s commitment to transformation and recognition of the role it plays in socioeconomic and people development is demonstrated by the company’s dedication to facilitating equal access to business opportunities.
Accordingly, ARM and the many organisations under its ownership, such as BPM, are acting in accordance with the Mineral and Petroleum Resources Development Act 28 of 2002, which guarantees equitable access to and the sustainable development of SA’s mineral and petroleum resources.
The organisation’s primary activities – which include mining, crushing, milling, processing, and beneficiating metals and minerals – present highly adverse working conditions.
Therefore, in recognition of industry legislation, ARM implements stringent hazard identification and risk assessment criteria. As a result, the company and its various acquisitions can ensure that its operations do not harm the planet or its people.
By adopting a more holistic view of success, ARM, and BPM by extension, are ensuring a long road ahead for corporate sustainability in South African PGM mining.
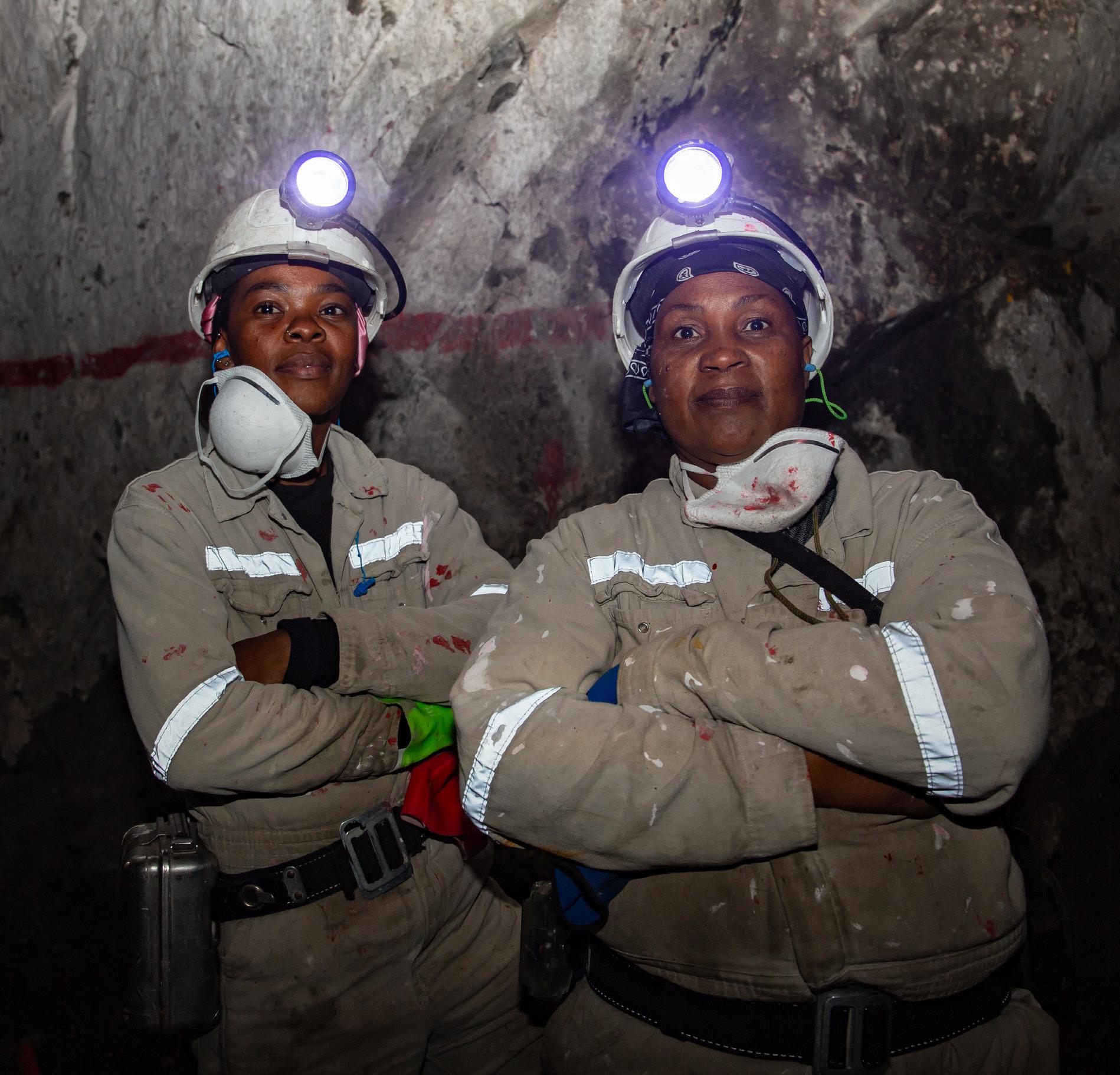
INTRODUCING INNOVATIVE EQUIPMENT
BPM’s success and long-lasting perseverance in the South African mining industry are marked by a willingness to adapt and become a catalyst for progression.
Since its change of ownership over two years ago, the company has revitalised its operations. This has proven to be an immense challenge, requiring highly specialised work and significant levels of investment.
Yet, instead of diminishing its activities, such upheaval has made
BPM more determined to succeed and pioneer innovative strategies.
For instance, the company’s recently appointed management team is currently in the process of implementing a new design layout for its mine sites. This will eventually enable the efficient underground extraction of platinum orebodies in a way that aligns with the ore’s unique characteristics and ARM’s forwardthinking mining strategy.
BPM’s platinum orebody is one of the largest and richest in SA and grades between six grams per tonne
(g/t) and 9 g/t which, according to the World Gold Council, makes it an incredibly high-quality resource.
The company’s orebody is further characterised by its complex geology, narrow and dipping at an average of 14 and 23 degrees. Due to this diverse formation, the required concentrations of platinum orebody to make it economically viable are harder to obtain. Therefore, BPM must employ specialised technology to ensure its PGM products are sufficient for the market.
THROUGH INNOVATION IN ROBOTICS, WE STRIVE TO SAVE HUMAN LIVES
Established in 1991, DOK-ING is an engineering powerhouse of heavy-duty robotics & autonomous systems, serving high-risk industries worldwide. With a presence in over 40+ countries, the company has earned a reputation for delivering safety, efficiency, and reliability in some of the world’s most hazardous environments.
DOK-ING’s innovative robotic solutions are designed to address a range of critical operations, including Underground Mining, Military and Humanitarian Demining, Military Engineering, CBRNe, Emergency Response and Counter-terrorism.
The company’s commitment to innovation is embodied in their motto, “Don’t send a man to do a machine’s job,” reflecting the company’s dedication to developing cutting-edge technologies that protect lives, the environment, and critical assets in dangerous conditions.
With over 30 years of experience, DOK-ING has garnered international recognition for its industry-leading advancements, earning more than 100 awards for revolutionising standards across multiple sectors. From safe exploitation of narrow reef layers and clearing minefields to responding to natural disasters and industrial hazards, DOK-ING’s mission remains focused on safeguarding people and improving operational safety with groundbreaking technologies.
The headquarter is in the Croatian capital, Zagreb, and, besides the European office, DOK-ING is incorporated on the following continents: North America, Africa and Asia.
Contact DOK-ING Mining:
Mr. Luka Petro, Managing Director
Mobile: +385 (95) 903 06 14 | Email: luka.petro@dok-ing.hr
Address: Slavonska avenija 22 G, 10000 Zagreb, Croatia
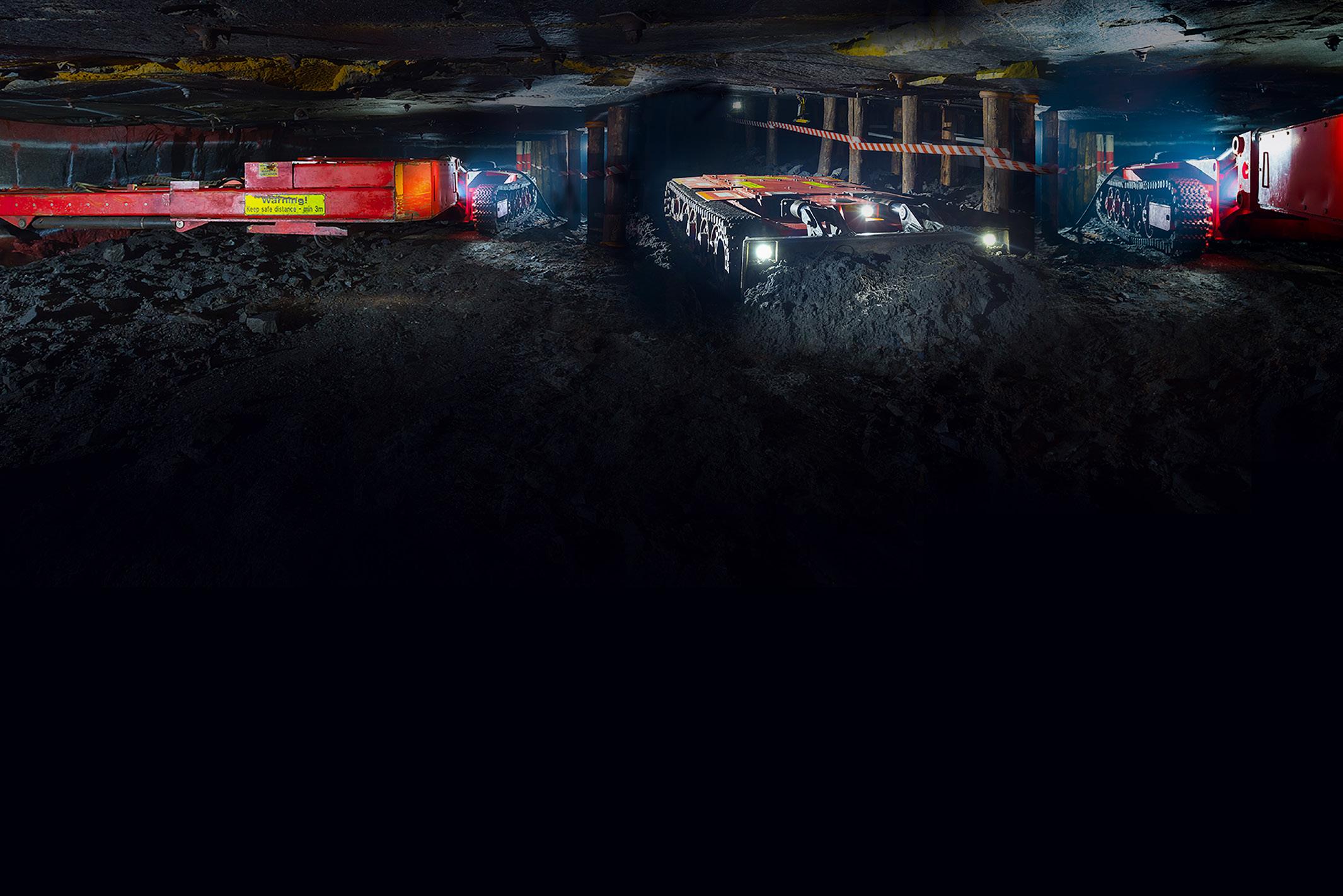
MINING PORTFOLIO
The DOK-ING portfolio of cutting-edge robotic systems for Underground Mining includes: NRE Fleet and XLPD Groundhog dozer to enhance safety and efficiency. The NRE fleet consists of three robotic systems: NRE dozer, NRE Support Rig and NRE Drill Rig that seamlessly complete the drilling, cleaning, and supporting processes. These groundbreaking innovations were specially designed for platinum, chrome and gold extraction. DOK-ING’s innovative product is a VR training simulator designed to train operators on the NRE Dozer for underground mines, allowing them to train control of these systems effectively before entering the mines.
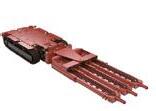
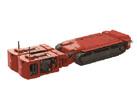

Contact DOK-ING Africa:
Mr. Tom Sertić, Managing Director, DOK-ING Africa
Phone: +27 82 5530 674 I E-mail: tom@doking.co.za
Address: DOK-ING House & Workshop, 237 Joseph Street, CNR Nyewerheid, Gemiston 1401, Johannesburg, SA
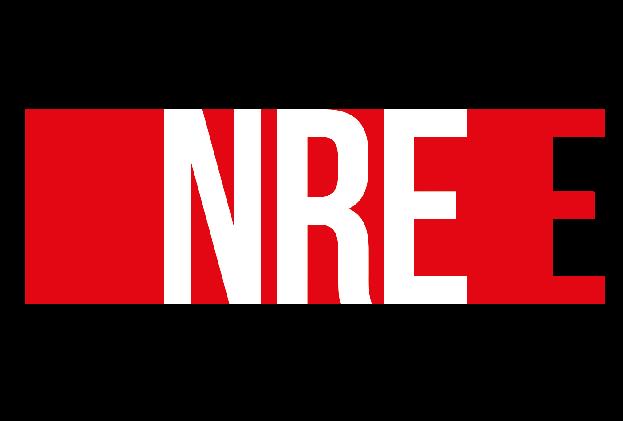
MECHANISING MINING:
NRE Technology: Advancing Mechanised Mining in Ultra-Low Profiles
DOK-ING underground mining equipment and remote-controlled systems are built to tackle the challenges of deep excavation and hazardous materials, revolutionising how mining operations are conducted. The NRE technology enables mechanised exploitation in ultra-low profiles (0.9 m to 1.7 m), increasing safety, productivity, and ore concentration, leading to less waste and more selective extraction whilst reducing capital investment, less rock is excavated, which can reduce costs. With the development and production of NRE, DOK-ING is expanding its product range, bringing innovation to the mining industry and pushing the boundaries of the efficiency of mining methods.
Redefining Underground Mining
DOK-ING’s NRE fleet can handle slopes of up to 22°, surpassing the 10° limit of wheeled machines and providing the underground mining industry with new opportunities.
The ability to operate on higher slopes opens up access to deposits that conventional machines can’t reach or would make unprofitable. This flexibility not only enhances mine design but also leads to significant cost savings.
Ultra-low Profile and Remote-Controlled Efficiency
The NRE fleet is remote ly controlled, eliminating the need for personnel in unsecured areas. The fully automated roof drill ing and supporting oper ations further enhance operator safety, ensuring a safer and more efficient mining process.

Market Competitiveness and Safety
DOK-ING’s unique innovative NRE, measuring just 65 cm tall, is designed to navigate the world’s most challenging mines. The electric drive eliminates the noise and impact of exhaust gases in confined spaces and reduces the carbon footprint of the overall exploitation process. Mechanisation of the production process increases production efficiency, improves occupational conditions, and drastically reduces risks for workers.
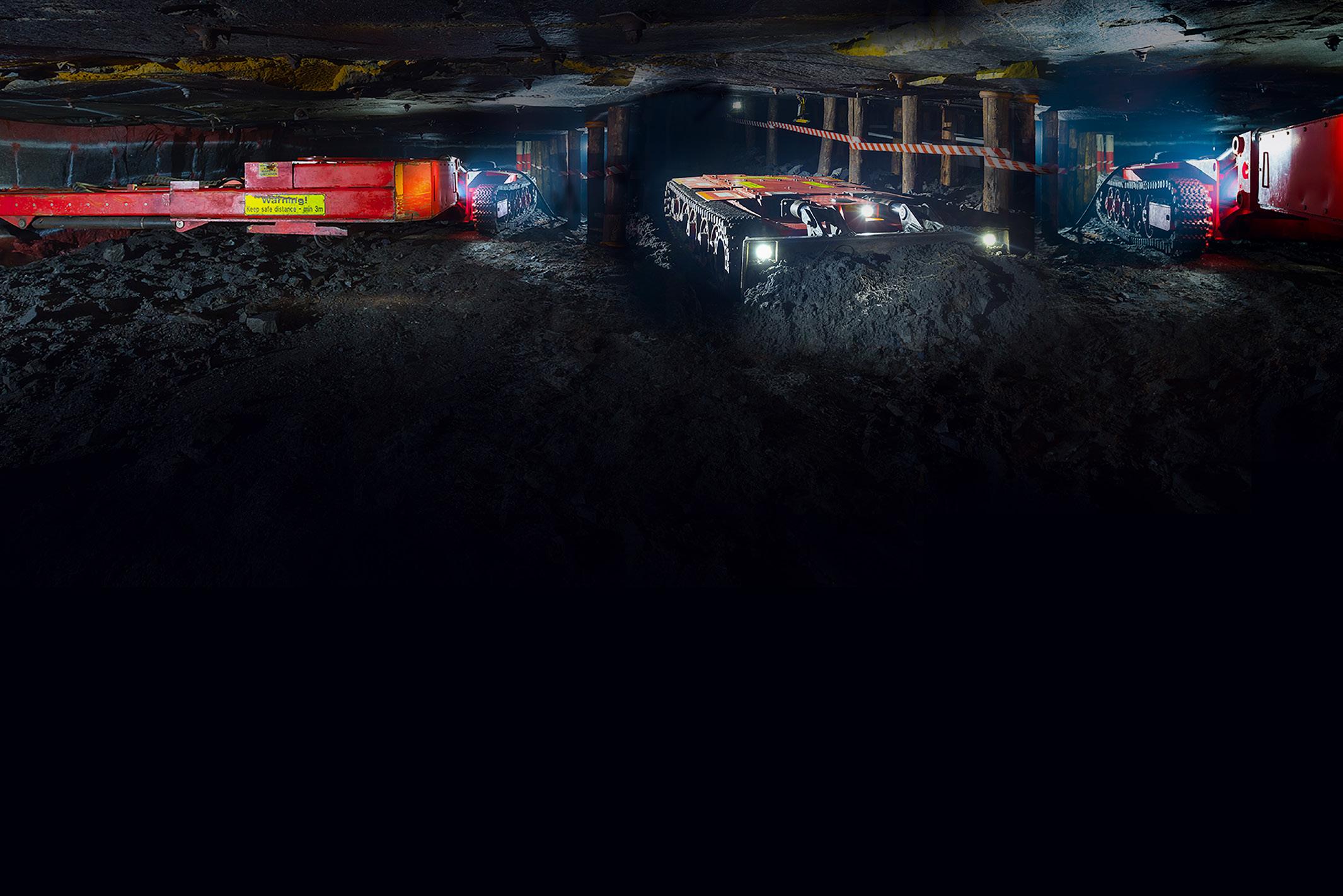
This technology comes in the form of narrow reef equipment (NRE), which vastly improves mining efficiencies beyond conventional recovery methods.
Although NRE has been utilised across many South African mining operations, it is best deployed across a homogenous orebody, making it ideally suited for BPM’s platinum operations. This also means the technology can be used across the company’s many mining areas.
“By purchasing the equipment, BPM has made a generous capital commitment. The successful implementation of NRE across our mines will see huge benefits in the safety of production facilities for the mining industry at large,” Joubert informs.
Set to be commissioned and handed over by December 2024, the company must strategically deploy the equipment in order to
make the most of the PGMs forming underground.
Firstly, BPM will carry out trackless development methods, using mobile equipment to establish the footprint of the mine reef. This will advance the initial evolutions of the mine by contributing to the early extraction of resources, thus reducing capital pressure at the first stages of the mine.
Once the initial footprint has been established, the NRE suite will be used to establish a stope that will maximise the ore grade output.
The stoping methods will provide direct access to the orebody, reducing the creation of waste in the underground mine and ensuring the careful management of tunnels, equipment, and infrastructure.
Such efficiencies are vital for ensuring improved worker safety, and NRE will facilitate optimum environments for recovering
GETTING A BOOST FROM BCM
As part of its vast range of corporate commitments, the company strongly advocates for and supports local women in becoming business owners and prosperous entrepreneurs.
In May 2024, Kenneth Mbewe, Head of Social Performance at the time, held a communal meeting in the village of Sefateng to allow the community’s voice to be heard regarding women’s skills training and empowerment.
Many of those at the meeting shared their concerns about the lack of female empowerment as well as their dreams to own a business. The gathering also facilitated the opportunity to learn more about the important skills needed to run a company and significant supply chain procedures.
The key goals of the meeting included:
- Empowering women through entrepreneurship opportunities.
- Sharing potential business ideas.
- Assisting aspiring female company owners.
- Motivating and educating attendees on prosperous business sectors.
- Identifying potential business ideas that fit with BPM’s objectives.
The meeting allowed attendees to voice their opinions and take control of their futures.
orebodies in a way that maximises safety and minimises potential hazards.
Moreover, using NRE means that even the most inclined reefs and narrow tubular orebodies can be effectively extracted, enhancing the overall productivity of the mine.
As such, by utilising this exceptional infrastructure, the company can remain up-to-date with the latest industry evolutions and ensure burgeoning success under the ARM umbrella.
“The NRE stoping method will revolutionise the mining techniques employed in narrow reef mining across SA,” Joubert affirms.
OPTIMISING PRODUCTIVITY AND PROFITS
As the critical next step to the strategic extraction of required resources, BPM is currently working
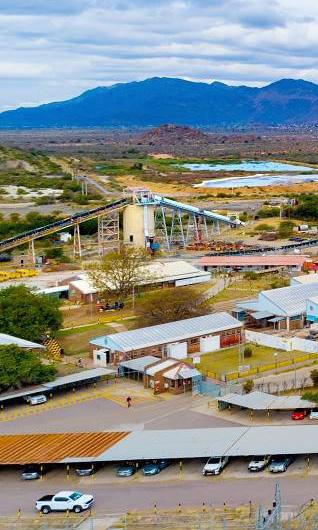
on a further open pit mine to help increase the amount of ore processed in its plants.
As a result, the company is hoping to enhance early ounce production across the Bokoni area.
The new open pit mine will bring a plethora of benefits to the fore. For example, the project will help increase the ore tonnage delivered to the plant, subsequently enabling the optimum extraction of PGMs.
Additionally, the open pit mine will have a specially designated stockpile in front of its plant to improve production efficiency and speed and prove the viability of opencast material.
Towards the end of 2025, BPM will also commission a chrome recovery plant, which will be used to remove chrome from ore to become a marketable and profitable by-product.
This process will increase the number of plant recoveries that can be sold off as chrome, which will not only fully optimise the minerals but also increase the company’s eventual profits.
The commissioning of the chrome recovery plant will arrive at a fortunate time, given that the market is comparatively robust and bullish, allowing many mining entities to find more ways to generate profit from what was once considered a waste product of PGM mining.
Moreover, the increasing prominence of the chrome market will help offset the original costs of the mine and support the growing demand for the material in China, which is showing a growing investment interest in the mineral.
Elsewhere, BPM is keenly expanding its underground operations at its Klipgat site, where the surface box cut
has now been completed.
The company is also currently in the process of developing three main site declines to intersect with its existing underground workings. This will prove highly advantageous for the productivity of the Klipgat mine as it will increase the site’s ore handling capacity and allow enough room for larger equipment to be deployed across the project’s underground operations.
In the last year, the Klipgat mine has already facilitated numerous opportunities for BPM and the local community, as the project was purposefully designed with advanced safety measures and constructed with operative staff in mind.
This has proven particularly important given the project was completed by a dedicated group of local labourers and tradespeople that comprised 60 percent of the workforce.
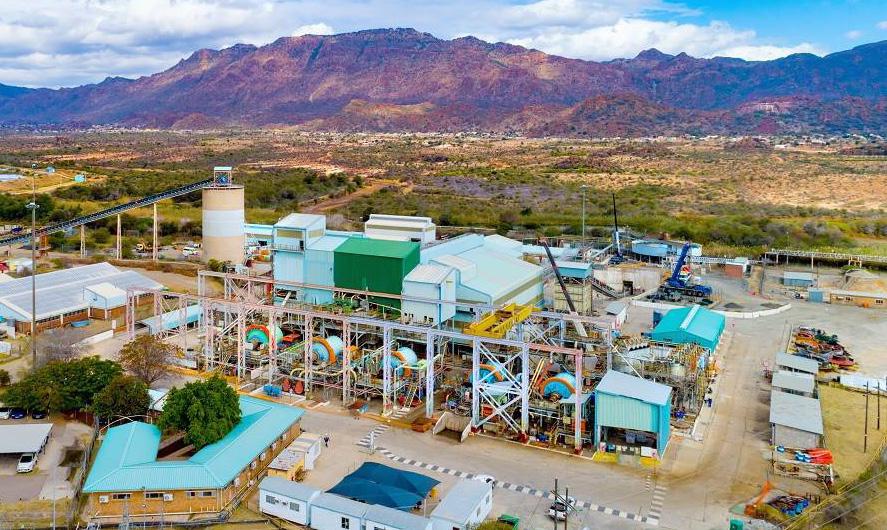


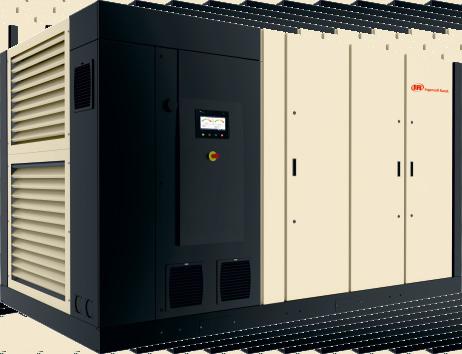
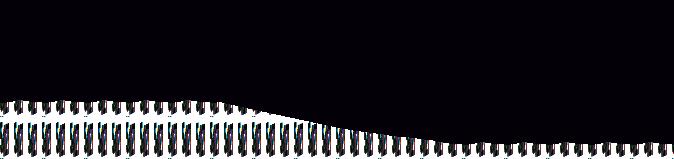

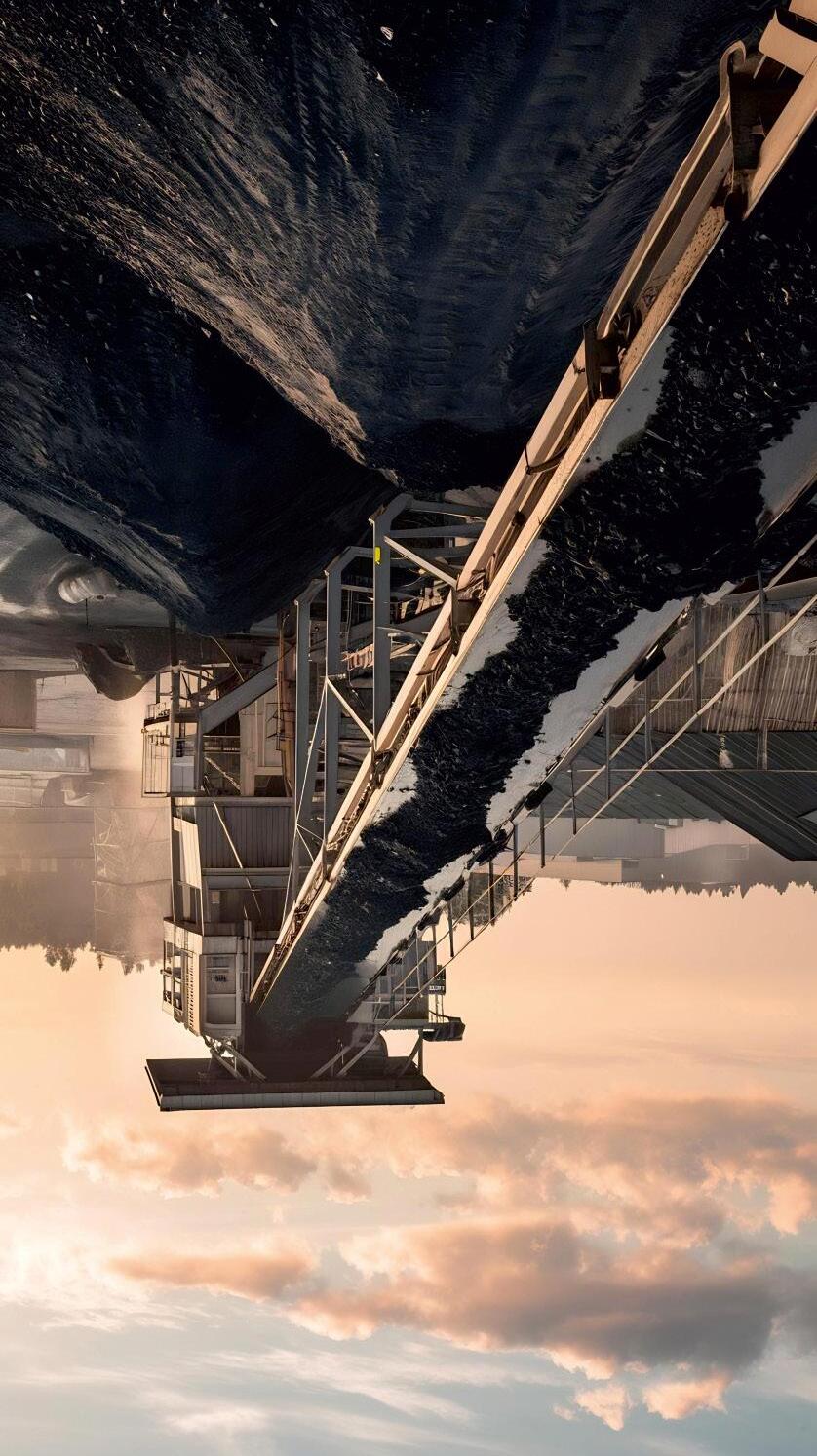
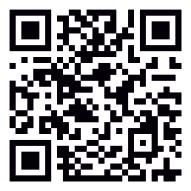
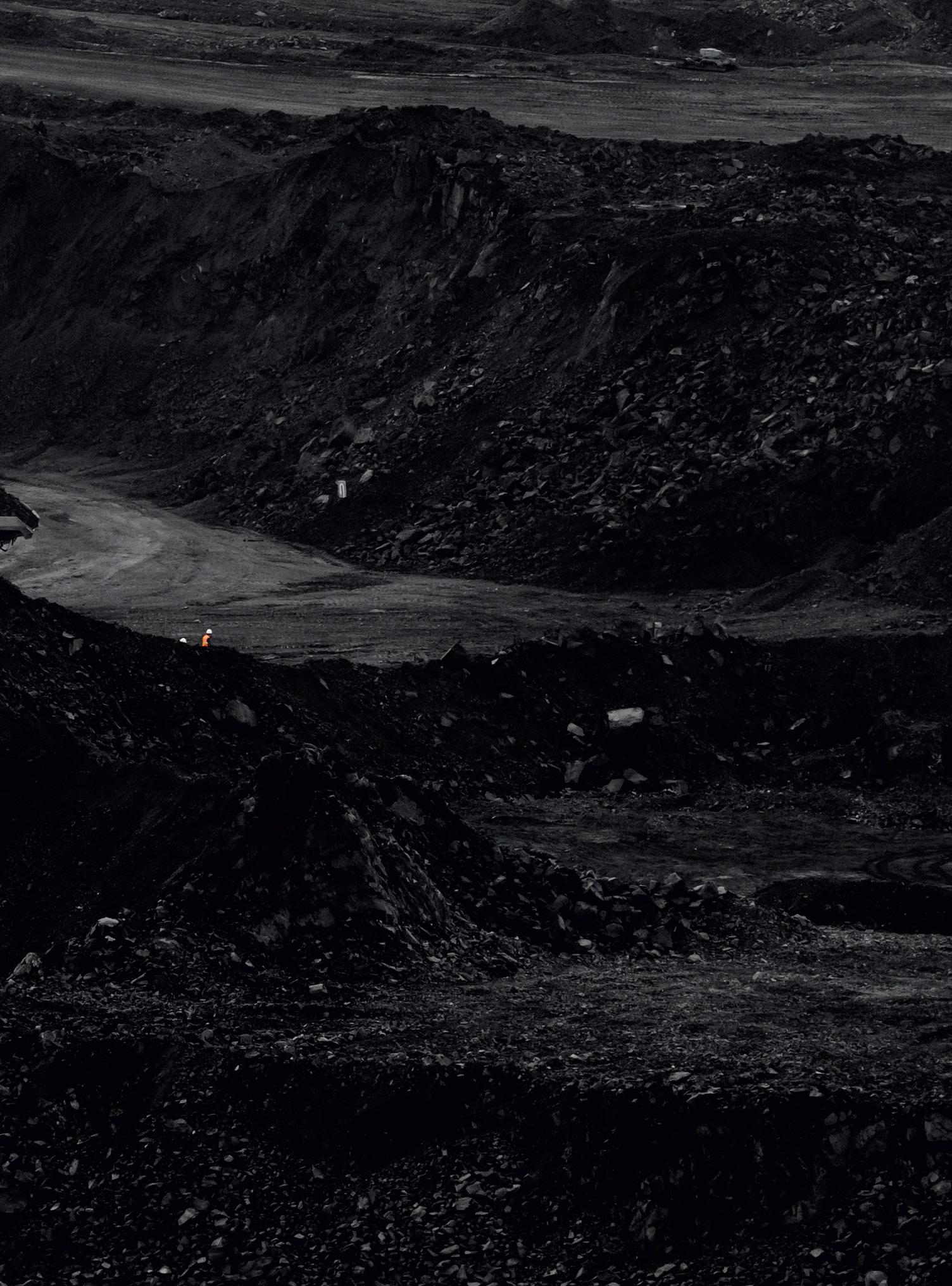

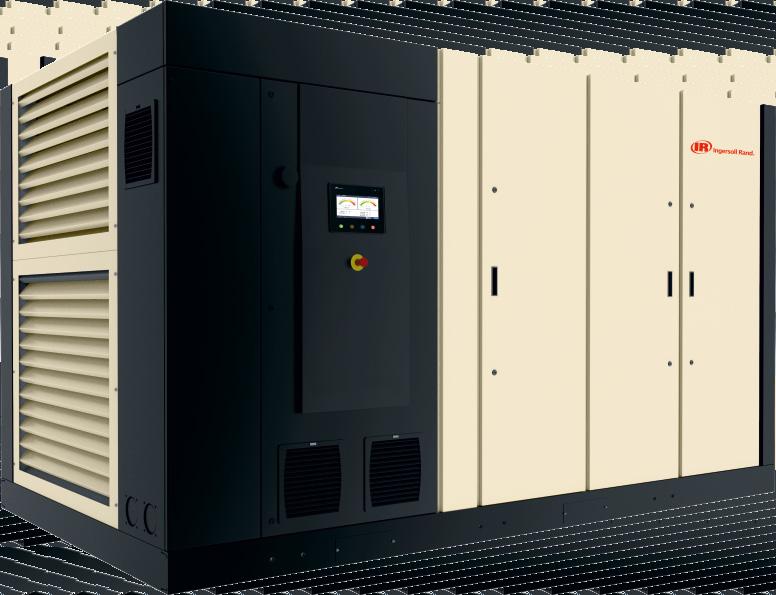
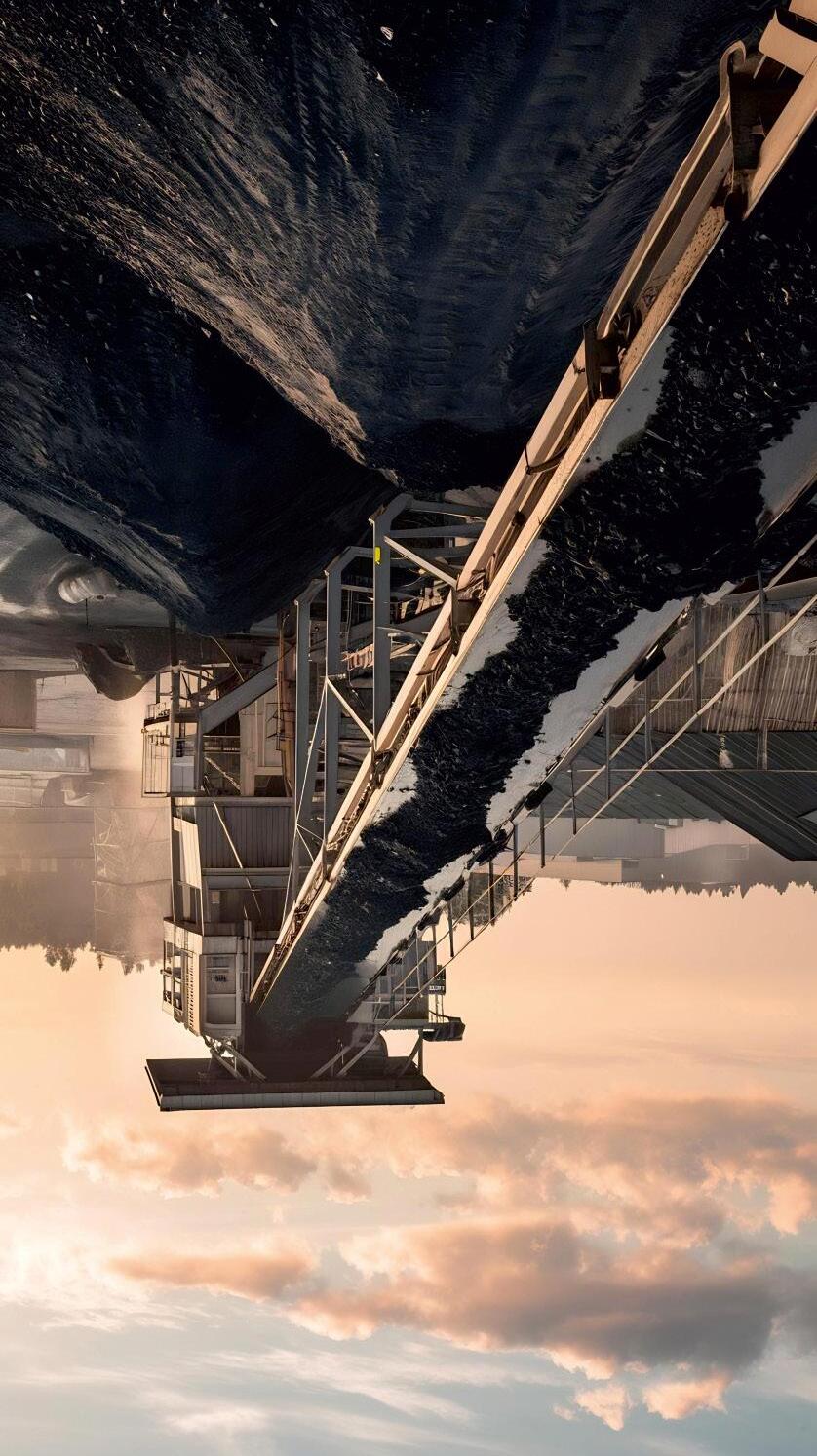
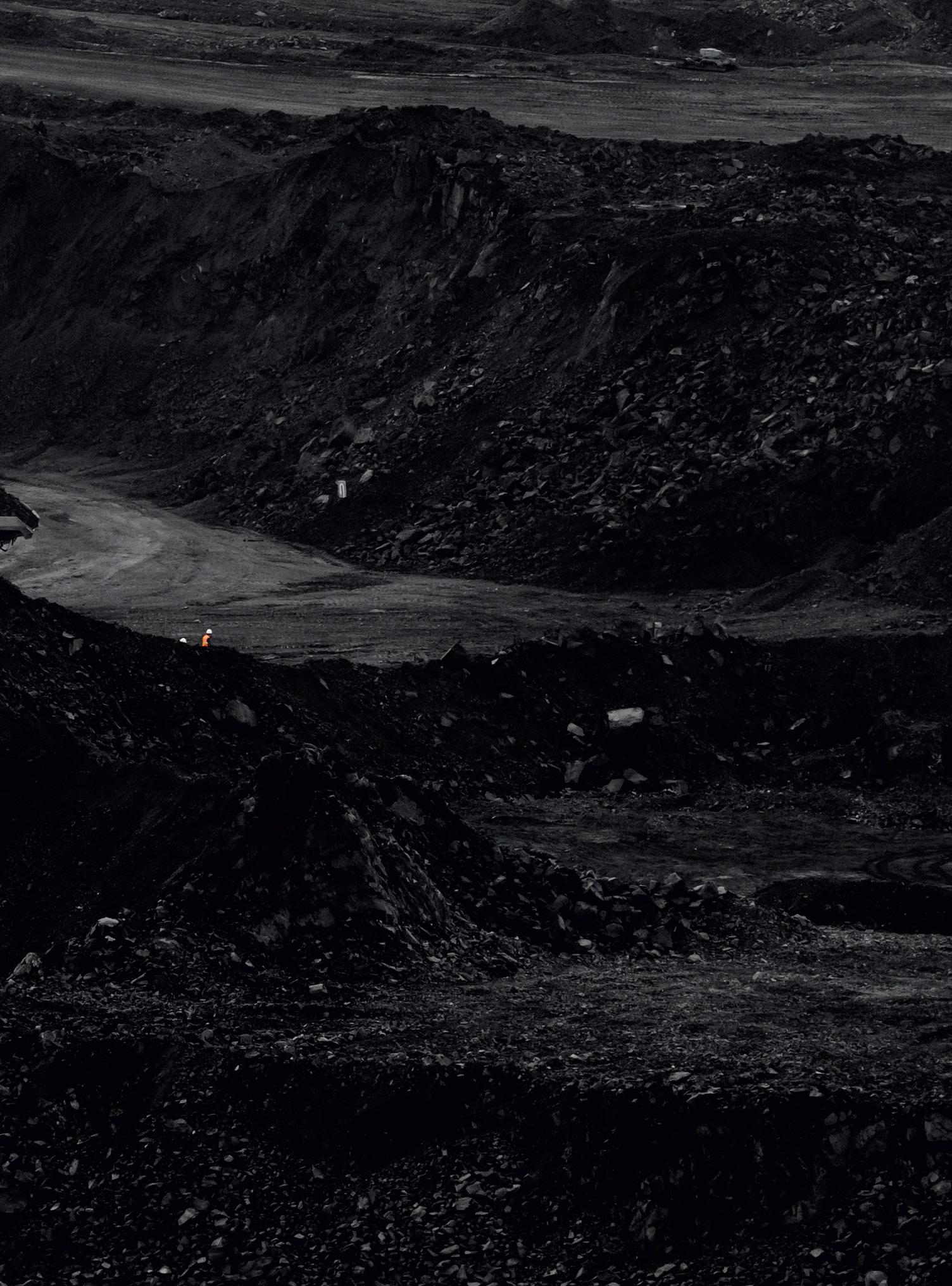
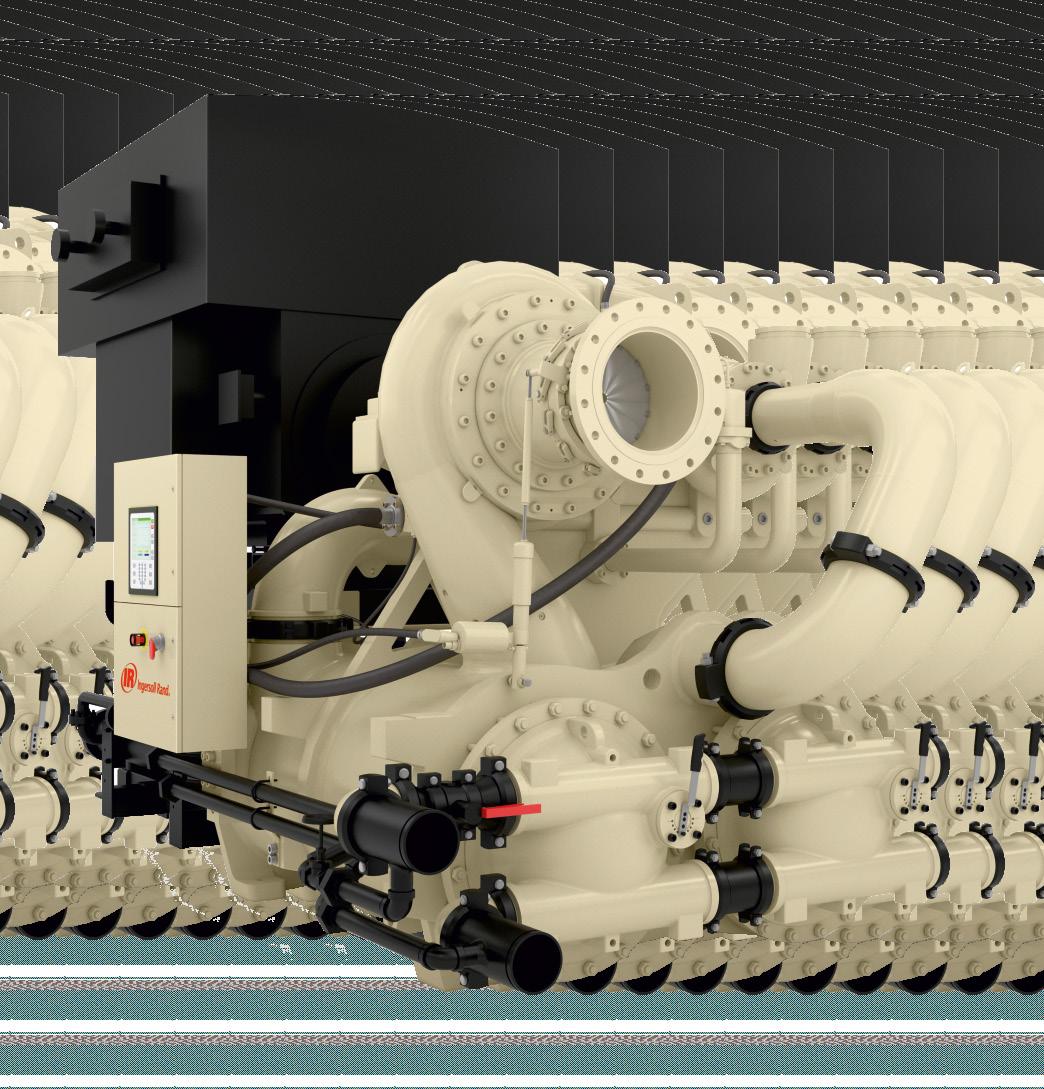
As such, the Klipgat project is proving advantageous for both BPM and the local community as it is contributing to SA’s growing minerals and metals industry whilst bolstering job opportunities in nearby communities.
PREFERENTIAL PROCUREMENT
To ensure a sustainable and successful mine site that also benefits nearby communities, BPM has a purposeful procurement strategy that entails consistency and success across every mining endeavour.
ACCESS BRIDGE CONSTRUCTION
As a key part of BPM’s SLP, the company recently constructed a significant access bridge, demonstrating its commitment to improving local infrastructure and making a positive impact by increasing accessibility.
IMPROVING ACCESS: The project created greater transport routes for both vehicles and pedestrians to churches, clinics, schools, and workplaces. As such, the infrastructure benefits a vast amount of the local population.
FUNDING: In order to ensure that the project reached completion, BPM fully funded the ZAR5 million bridge in collaboration with the local municipality.
IMPROVING DAILY LIFE: By constructing the bridge, BPM addressed a critical need as it facilitates a safe mode of travel across difficult terrain, especially during the rainy season when roads become difficult to navigate. As such, the project made a huge improvement to daily life.
“Our local procurement strategy is designed to support and uplift surrounding communities by promoting entrepreneurship and fostering the development of small, medium, and micro enterprises (SMMEs),” Joubert explains.
Indeed, the dedicated process for acquiring a team of local talent and suppliers cultivates many benefits for nearby businesses and those potentially impacted by mining operations.
For example, in line with corporate SA’s commitment to broad-based Black economic empowerment (B-BBEE), the company strives to maximise purchases from Blackowned (BO), Black women-owned (BWO), and Black youth-owned (BYO) entities, known as its preferential procurement strategy.
“This approach helps promote entrepreneurship and supplier development in local communities by providing access to mainstream procurement opportunities,” elaborates Joubert.
In a similar vein, the company also supports historically disadvantaged South Africans (HDSAs), including those who were unfairly treated prior to the Constitution of the Republic of South Africa.
As such, BPM’s procurement strategy actively promotes entrepreneurship in unfairly disadvantaged communities, giving HDSA-owned enterprises in host and local communities access to conduct business in the nation’s mainstream economy.
This includes proactively supporting procurement from BO-exempt micro enterprises and qualifying small enterprises to reduce unemployment amongst these groups.
An additional component of the company’s preferential procurement process is the education of stakeholders and spreading the importance and meaningful impact of the strategy.
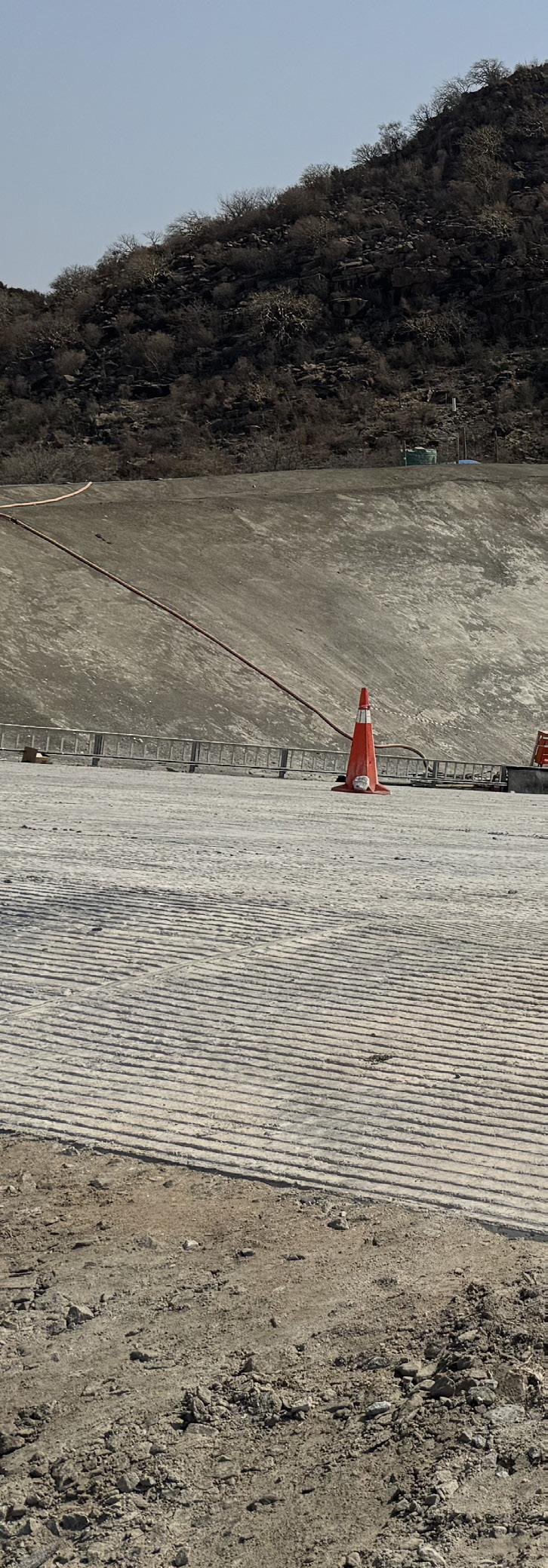
“Spreading awareness about preferential procurement and its potential positive impact on the community is crucial as it helps create an enabling environment for sustainable Black businesses,” impassions Joubert.
Akin to spreading awareness of Black empowerment, BPM follows through on its beliefs by strategically awarding tenders and contracts to community development projects, as well as BO, BWO, and BYO enterprises
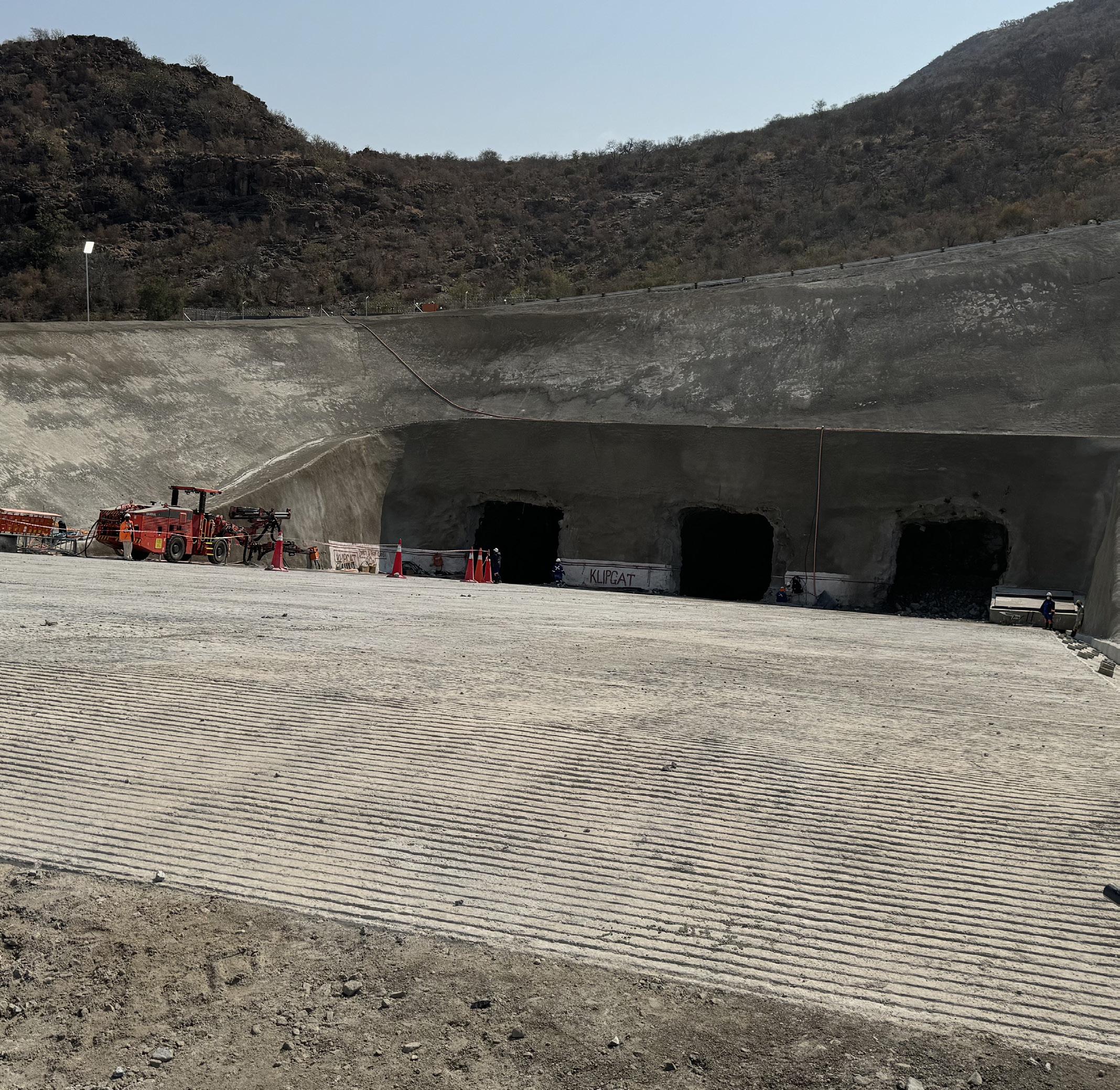
and suppliers.
In collaboration with BPM, these businesses, as well as other local entities, have the opportunity to be part of Enterprise and Supplier Development (ESD) programmes.
The company’s procurement strategy aligns ESD with preferential procurement by actively managing the growth and development of HDSA enterprises within host communities. This involves educating end users
– including heads of departments, contract managers, engineers, and budget holders – on the importance of their participating role in the procurement process.
By creating such a comprehensive and steadfast strategy for sourcing suppliers and employment, BPM is creating long-term sustainable value by positively contributing to those who are disadvantaged in neighbouring communities.
“The local procurement strategy not only supports the national agenda for SMME development but also contributes to poverty alleviation, employment creation, and shared economic growth in local communities,” informs Joubert.
In turn, this ensures that these businesses continue to prosper beyond the life of the mine whilst also contributing to the company’s corporate citizenship.
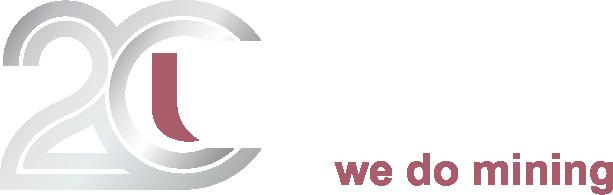
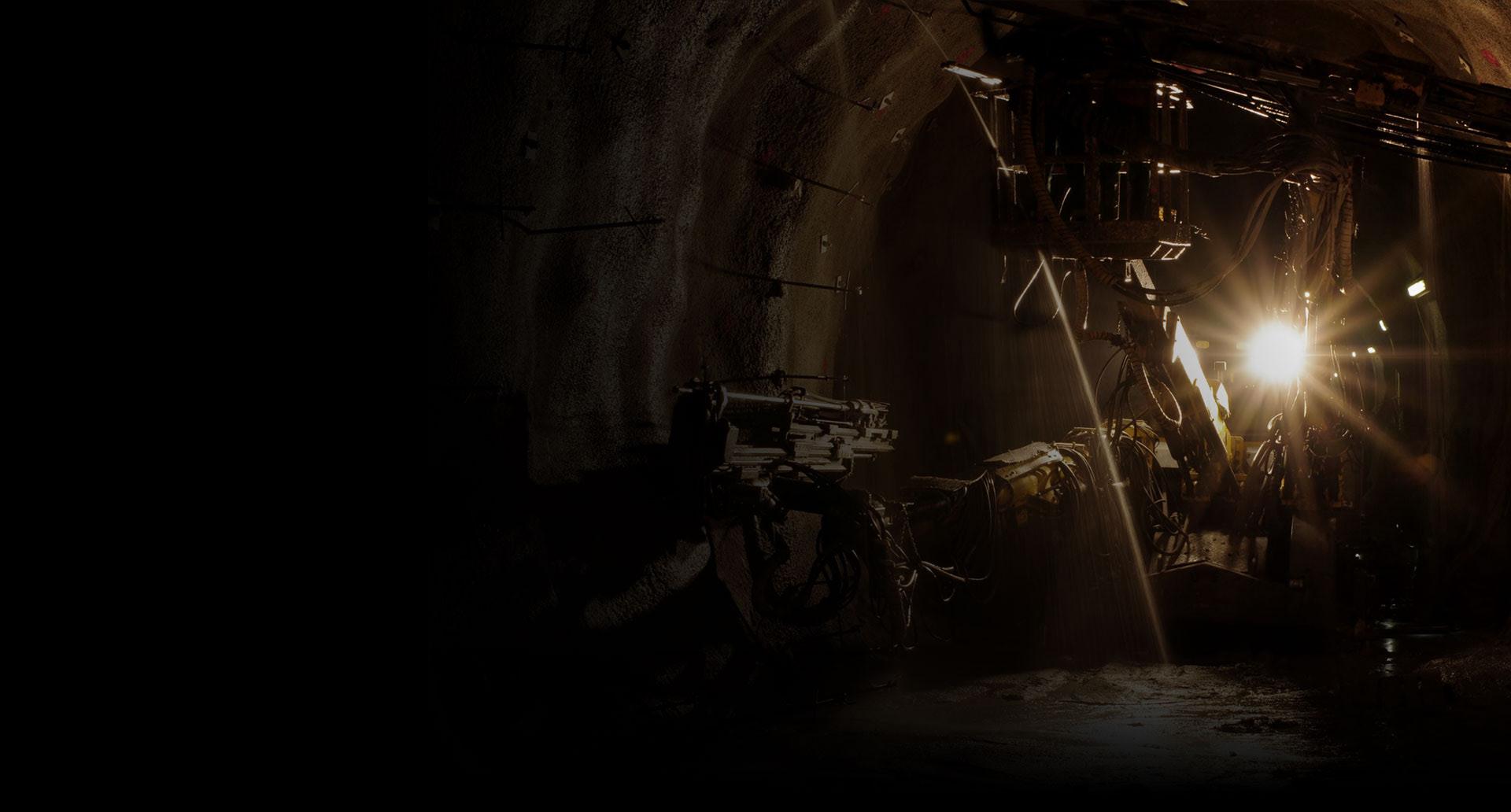
Unmatched Mining Solutions
Written by Jaco Lotheringen, Managing Director and Spencer Eckstein, Chief Operating Officer, Ukwazi
Briefly introduce us to Ukwazi, including a short overview of your main products and services, locations, client base, number of employees, etc.
Ukwazi celebrates 20 years in operation this year. We are a niched, mining advisory company that specialises in providing critical services like integrated mining studies, mine engineering and planning, engineering infrastructure design, environmental, social, and governance (ESG), project valuations, public reporting, on-site technical services, and transaction advisory services to mining clients in the sub-Saharan Africa and the Middle East regions. We have also recently concluded an exclusive distribution agreement with the Canadian yellow equipment supplier, K-Tec, for its pull scrapers. The application thereof is diverse and focuses on the mining of typical materials associated with tailings facilities and residue deposits. As part of mine rehabilitation activities, the equipment removes soft overburden material as part of the conventional mining cycle and general earthmoving as part of large civil projects.
We are based in Pretoria, South Africa (SA), and have offices in the coal fields of Mpumalanga and the iron and manganese fields of the Northern Cape. More recently, we opened an office in Dubai.
We are a mid-sized business with more than 50 fulltime employees and another 50 associates, whom we collaborate with on a project-by-project basis. We provide services to most of the major mining companies, as well as mid-sized and junior miners across Africa.
What, for you, differentiates Ukwazi from the competition?
In general, our competitive advantage comes from being based in Africa, which is home to some of the world’s most important bulk metals and minerals, precious metals, energy minerals, rare earths, and battery metal deposits. More specifically our competitive advantage comes from three main sources:
Firstly, how we are organised – our organisational DNA focuses on collaboration with our clients and our Superteams. These Superteams work together with the client to respond with agility and deliver on the demand for innovative solutions, which are provided according to
project specification, on time, and on budget. This way, clients have direct easy access to disciplined expertise for better collaboration and well-designed projects.
Secondly, our unique skill combination within each Superteam is based on permanent groupings of individuals with in-depth industry knowledge, creating a collective of experienced engineers and technical experts. This way, each client or project gets the A-team for their specific requirements so we can provide solutions that are sustainable and practical to implement and are safe and cost effective.
Thirdly, our service delivery methodology is based on integration within and between different disciplines, to deliver a bottom-up approach to projects that ensures seamless integration from pit to port or mine to market, delivering cohesive operations.
Could you elaborate on your partnership with Bokoni Platinum Mines? How long have you worked together and what is the nature of your interaction with the company?
Ukwazi has been involved with Bokoni Platinum Mines (BPM), owned by African Rainbow Minerals, since the inception of the project almost three years ago. Our brief was to focus on mine planning and engineering for the open pit, the related infrastructure engineering, and a review of the permitting solutions. This included elements of closure, civil engineering for storm water management and pollution control dams, haul road development, project controls and assistance with survey, mining geotechnical, and contract mining appointments.
We have over the course of the operation provided important technical insights to improve the cost profile of the project, improving its valuation despite a sustained reduction in international commodity prices of the 6E, platinum group metals (PGM) basket.
How do the two companies mutually benefit each other and what complementary strengths do you bring?
BPM has assembled a highly talented ownership team, with support from various mining advisors, including Ukwazi. Whilst other companies have worked on the underground portion of the project, we have focused on the open pit.
Our collaboration with the BPM team has been professional
and beneficial in terms of our ability to provide technical support and strategic advice in aid of the ownership team. Our strength and contributions have been particularly focused on providing scenario planning, engineering design, and ESG solutions.
Are there any recent or upcoming projects that you would like to highlight?
Given the shifts in commodity prices and geopolitical tensions globally, mining companies are looking to augment their existing operations by switching out certain commodities (e.g. coal) with other materials, most notably copper, and have focused on acquisitions rather than exploration. Certain companies with large open pit operations have looked to transition into underground and others have focused on reprocessing tailings and mine residue deposits.
Therefore, Ukwazi has focused on K-Tec scraper applications to be used in appropriate cases as a potential alternative to wet re-mining of historic deposits. We are seeing a decline in PGM projects and an increased interest in gold and uranium sites both in the southern and central Africa regions.
Please could you tell us more about how Ukwazi contributes to the economic growth of South Africa? How important is this to the company’s mission?
Ukwazi believes we have a role to play in the development of SA, particularly the mining industry, as we believe it can contribute to job creation and GDP growth in the right policy environment. We contribute by helping our clients to create a mineral exploitation strategy that is safe, cost effective, and sustainable. In particular, Ukwazi has been
involved in providing small, medium, and micro enterprise (SMME) support and has also created Tsebokgadi, which us our women in mining initiative.
Similarly, how does the business contribute to local employment?
Ukwazi has helped mining companies with their mining rights applications, which require a Mine Works Program (MWP), Social and Labour Plans (SLP), and Environmental Management Plan (EMP). Although these are statutory requirements, we are able to provide technical input to these processes, which ultimately result in job creation in some cases but also align with local economic development initiatives in communities where the mine is located.
How do you try to empower your staff and recognise the contributions that they make?
Ukwazi has a Level 2 Black economic empowerment (BEE) rating and we contribute to the empowerment of our staff via skills development, mentoring and coaching, as well as corporate social investment. We also have a programme of long service awards and performance bonuses to reward our staff.
Looking ahead, what are Ukwazi’s key priorities?
Our key priorities are to grow our Africa and Middle Eastern footprint, manage our growth, and retain our staff who are our most important asset. We want to ensure that we maintain high brand recognition for our technical competence and service excellence within the industry locally and, increasingly we hope, globally.
Multi-disciplinary mining advisors
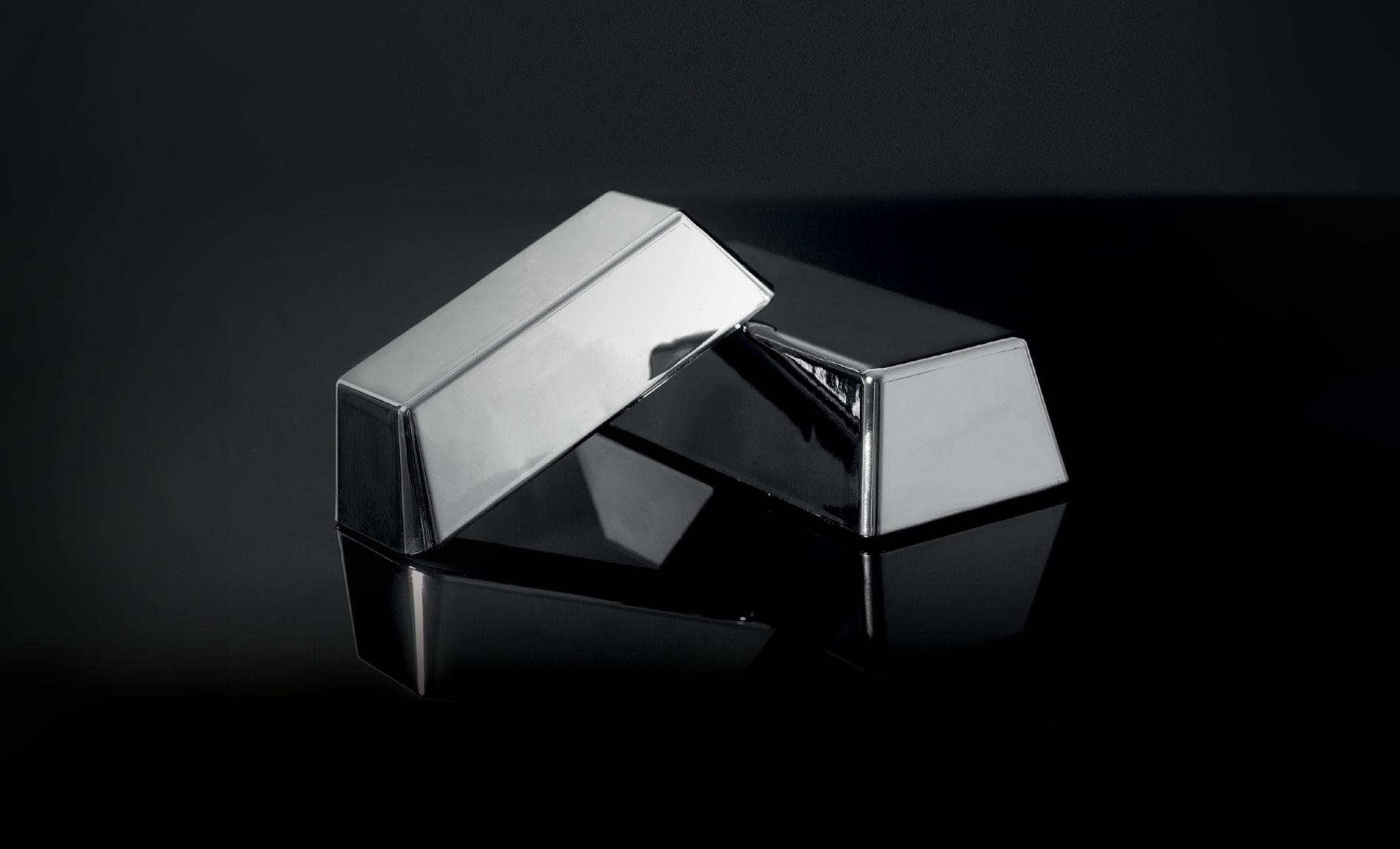
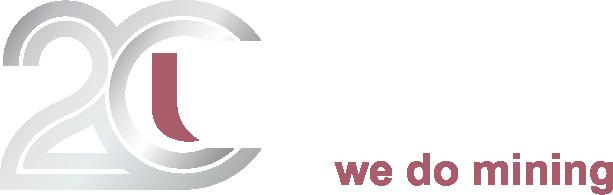
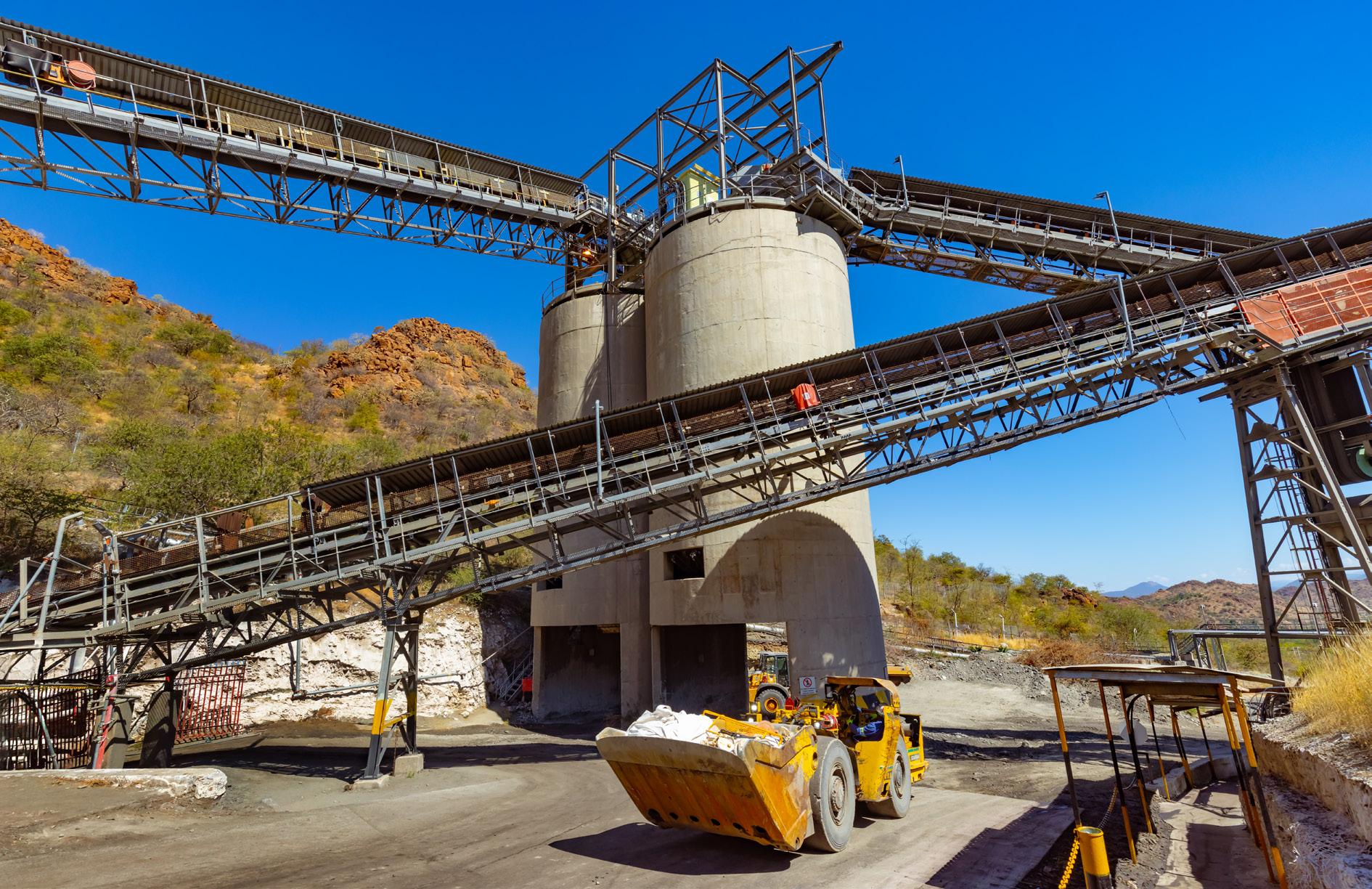
CENTRALISED SUPPLY CHAIN SUCCESS
The South African mining and metals industry accounts for a highly substantial level of the world’s platinum supply per year and is the vital first link in the long chain of processes that eventually lead to the final product, whether in aircraft manufacturing, stateof-the-art technology, or precious jewellery.
Consequently, the PGM sector is an integral part of the international supply of metals and minerals for a vast range of industrial, medical, and electronic applications, generating considerable opportunities for suppliers.
SA’s place in the global PGM supply chain draws significant value for the country’s economic growth, especially given the fact that the sector is currently one of the highest earners in the domestic mineral
“THE GOAL IS TO ENSURE THAT THE RIGHT PRODUCTS ARE DELIVERED TO THE RIGHT PLACE AT THE RIGHT TIME WHILST MINIMISING COSTS AND MAXIMISING EFFICIENCY”
– JJ JOUBERT, SENIOR GENERAL MANAGER, BOKONI PLATINUM MINES
industry and is seeing an increase in worldwide demand.
Taking into account the critical role that BPM plays in the world’s PGM industry, the company’s supply chain operations are carefully considered and thought out to maximise overall output and productivity.
Indeed, BPM implements a comprehensive strategy to manage and optimise the flow of goods, services, and information from suppliers to customers.
“The goal is to ensure that the right products are delivered to the
right place at the right time whilst minimising costs and maximising efficiency,” Joubert states.
Unlike other mining entities in SA, BPM utilises top-of-the-range central supply chain management practices that afford the company a multitude of benefits.
For starters, centralising its supply chain management results in significantly improved efficiency as this particular method allows for better coordination and integration of activities, leading to a refined flow of goods at minimal cost.
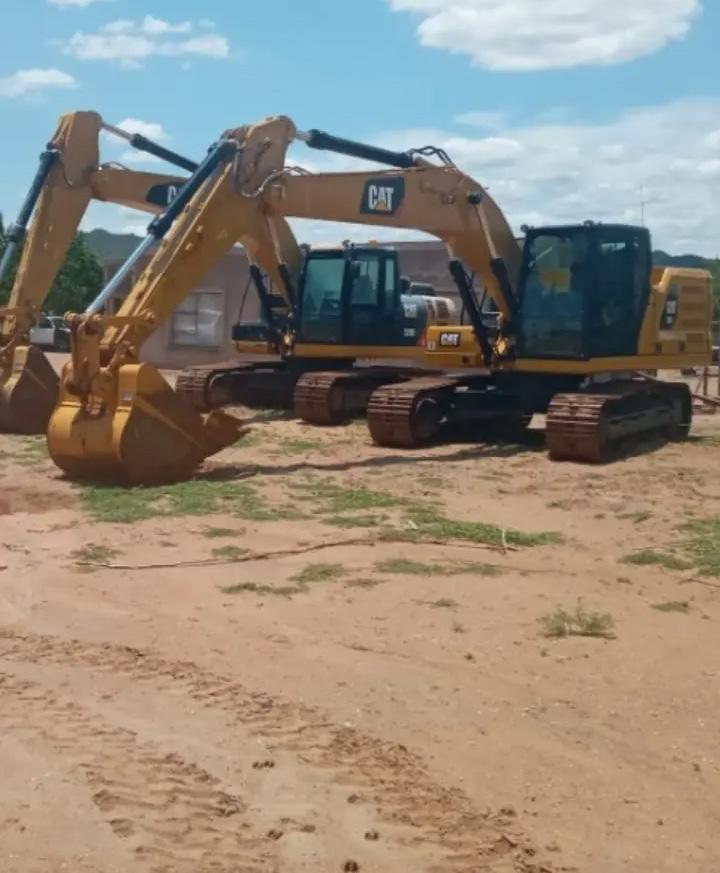
SERVICES:
• All products are either manufactured or repaired
• Strict adherence to all OEM standards and specifications
• Consignment stock and various service exchange units
• 24/7 field service
• Civil and Building Construction
• Renovations and Maintenance
• Fencing
• Yellow Plant Hire
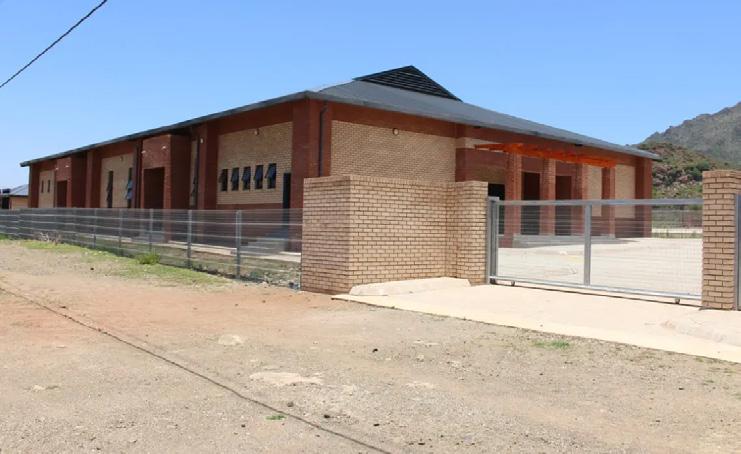
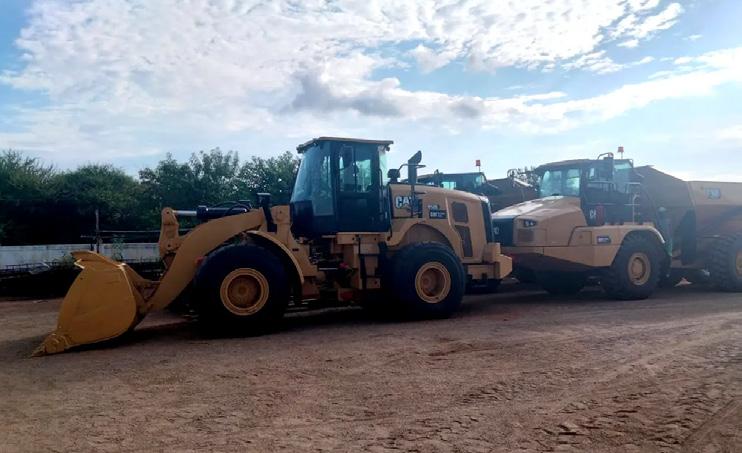
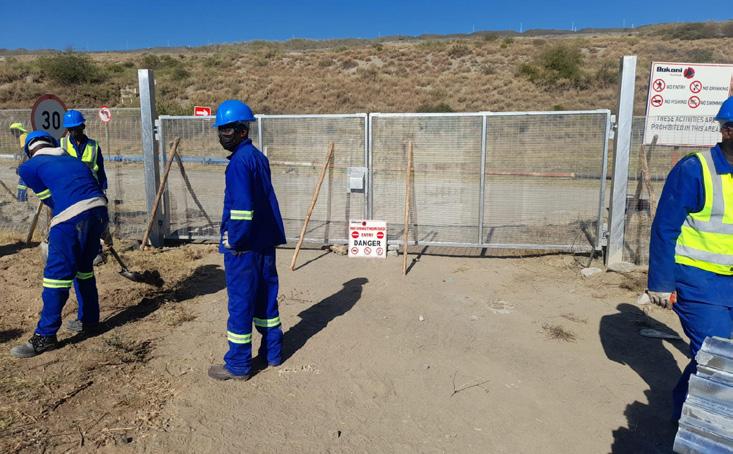
A PROFESSIONAL SERVICE
WITH FULL ACCOUNTABILITY, TRANSPARENCY, HONESTY AND INTEGRITY
We are a service orientated company that specialises in construction and civil works as well as yellow plant hire, supply of hydraulic cylinders, pumps, motors, and control valves.
VISION
It is our vision to establish a sustainable, progressive, gender sensitive, proactive empowered business that will consistently provide unparalleled service with the highest possible quality at competitive rates, whilst building and maintaining long-term mutually beneficial business relationships with our customers that grow from strength to strength as well as assuring our customers of the shortest possible collection, repair and delivery turnaround times in the industry.
MISSION
It is our mission to ensure that our level of quality and service will exceed all our customers’ expectations at all times.
OBJECTIVE
It is our objective to contribute in alleviating poverty by creating jobs where possible to uplift and improve the economy of the local community as well as empowering women and the disabled youth.
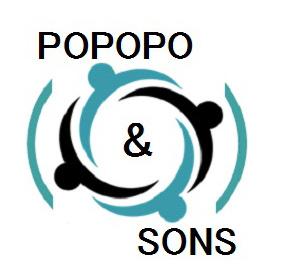

Additionally, a centralised supply chain grants the company greater visibility and control across the entire global logistics network, which consequently enables better tracking and monitoring of inventory levels, order statuses, and delivery schedules.
The key to this advanced level of insight is the abundance of generated data and analytics, allowing BPM’s team to make informed and timely decisions that facilitate improved logistical performance.
A centralised supply chain ultimately benefits the end user; by ensuring the timely and accurate delivery of resources and products, the company’s supply chain strategy enhances customer satisfaction and loyalty.
STATE-OF-THE-ART TECHNOLOGY
In order to streamline and optimise its supply chain management and procurement processes, BPM has introduced Coupa, a leading digital e-procurement platform that helps connect the company to its diverse breadth of suppliers.
Coupa is capable of accommodating a vast range of systems to help identify suitable suppliers, make smarter buying decisions, and optimise any purchases.
The supplier portal is used by BPM to request specialist materials and services as well as create and communicate purchase orders and invoices.
Additionally, Coupa equips the company with a deep understanding of any supplier disruptions, which
helps to build the integrity of the entire procurement system and provides artificial intelligence (AI)driven insights to help BPM identify and unlock efficiencies that ensure supply chain continuity.
Coupa also reduces third-party risk, streamlines onboarding, and monitors the ongoing performance of products and materials, making the software a valuable asset to BPM’s procurement team.
Moreover, the company’s dedicated ESG commitments extend to its supply chain operations, as it monitors and reports on its environment, health, and safety (EHS) performance following the recent introduction of IsoMetrix EHS software.
This software digitalises BPM’s EHS processes by integrating modules such as incident and risk
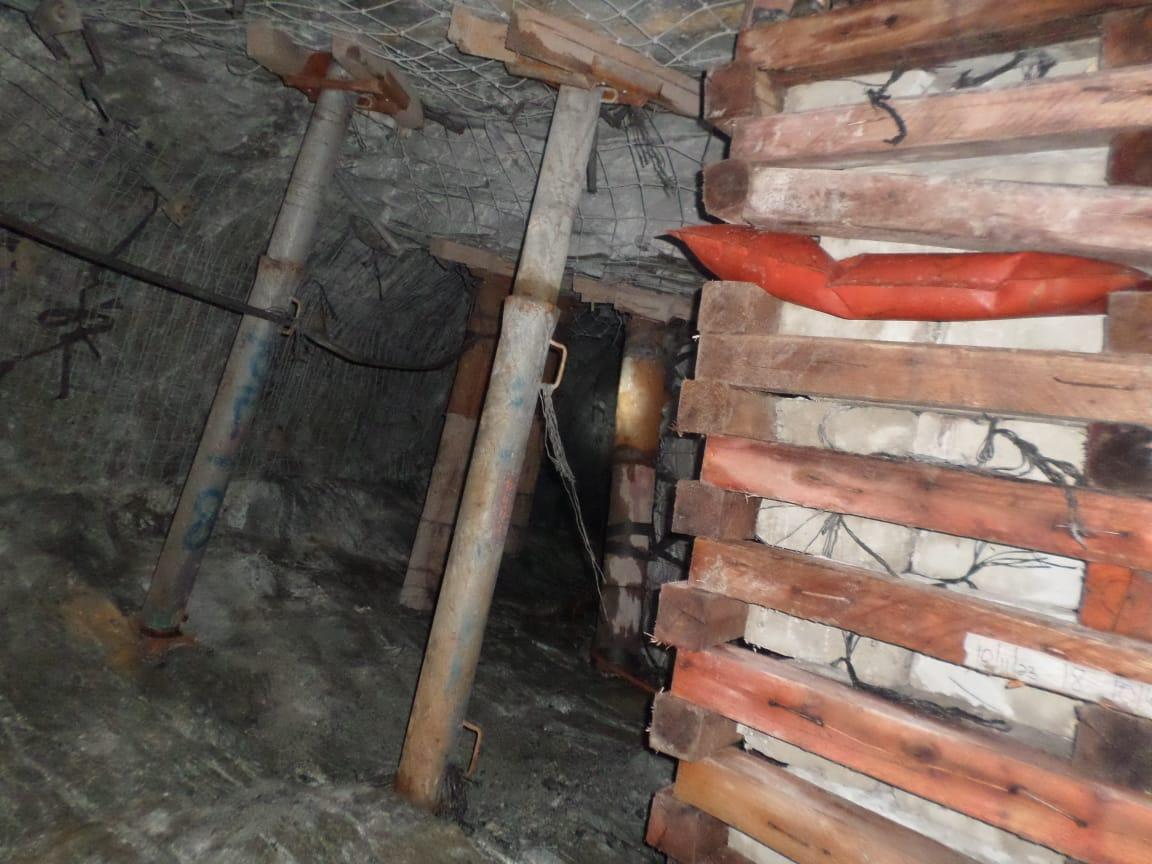
Rainbow Mining Support: Pioneering Innovation in
Underground Mine Safety and Efficiency
Rainbow Mining Support stands as a leading authority in providing specialised, cutting-edge solutions for the mining sector, with an unwavering commitment to enhancing both safety and operational efficiency in underground environments. Recognising the complex and hazardous nature of subterranean mining, we are dedicated to delivering highquality, resilient products that not only safeguard the workforce but also uphold productivity and sustainability.
Our ethos revolves around a meticulous understanding of the mining landscape, allowing us to craft innovative support systems that respond to the evolving demands of the industry. This strategic focus has established Rainbow Mining Support as a trusted partner within South Africa’s mining community, where our bespoke solutions have consistently ensured smooth operations across a multitude of sites.
Our Core Expertise at Rainbow Mining Support, lies in the development of versatile and dependable support systems that are both simple to install and integral to enhancing operational uptime. Our products, designed with the rigours of underground mining in mind, undergo rigorous testing to ensure they meet the most stringent safety standards, setting new benchmarks for operational safety and efficiency.
Our key offerings include:
Cementitious Solutions: We manufacture high-strength cementitious products and bulk bag systems, purpose-built for enduring the extreme conditions of underground mining. With an annual production capacity of 32,000+ tonnes of cement, cementitious grouts and pumpable grouts, we serve both largescale and mining operations, offering solutions that provide lasting support in subterranean environments.
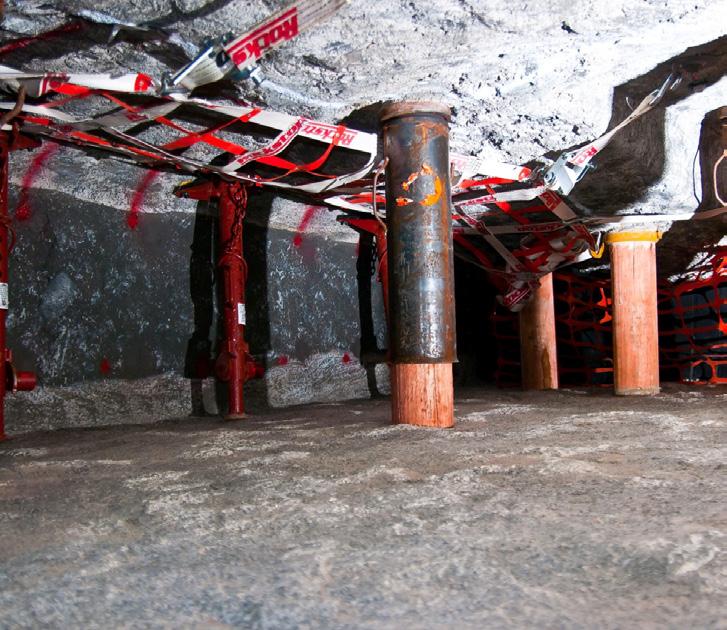
Stand-Up Support Systems:
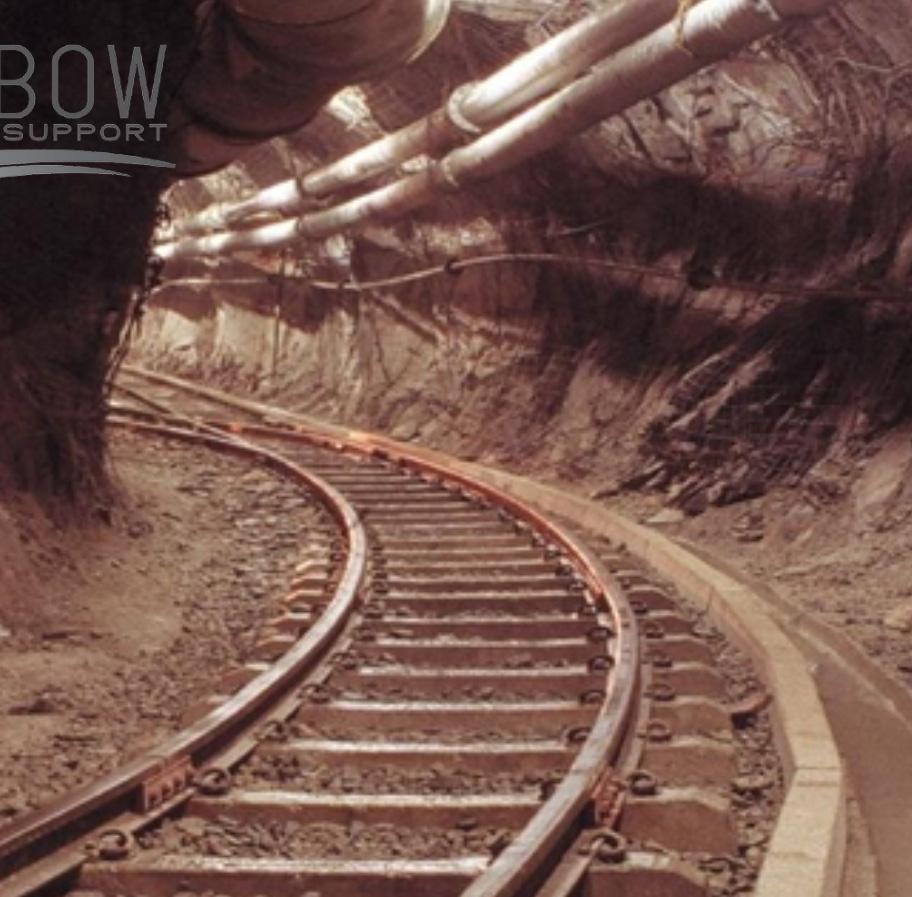

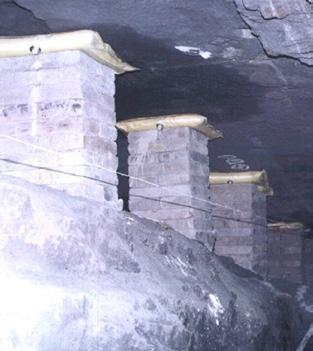
Our pioneering product, the BossProp, exemplifies our commitment to innovation in mine safety. Renowned for its robust design, ease of installation, and exceptional durability, the BossProp significantly enhances underground support, reducing downtime and improving operational outcomes.
Complementing this, our Durapak and Grinpak systems are engineered to withstand the severe pressures of deeplevel mining, ensuring comprehensive support across various applications.
Customised Solutions:
Recognising that each mining operation presents its own distinct challenges, we offer tailored solutions that address specific project requirements. This ensures that every mine is equipped with the most effective tools, thereby optimising safety and operational efficiency.
Durapak, Grinpak, Endgrain and Timber: Comprehensive underground support systems that cater to a wide array of mining environments, ensuring robustness and adaptability across operations.
Sleepers and Flolok Solutions: Essential for reinforcing underground mine infrastructure, these products ensure that even the most challenging operational demands are met with uncompromising safety and reliability.
Website URL: www.rainbowms.co.za
Email Addresses: sales@rainbowms.co.za salesmanager@rainbowms.co.za
Contact Number: 010 448 4746
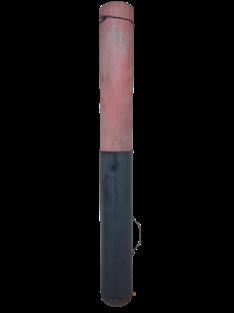
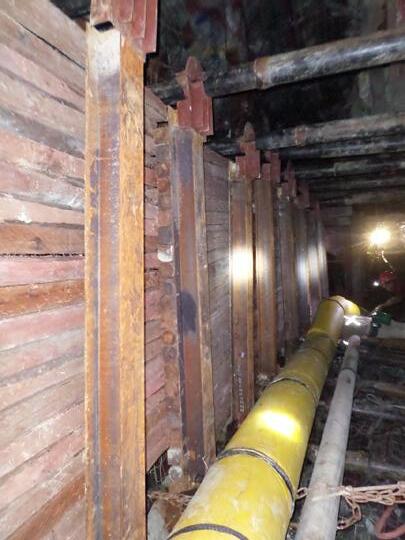
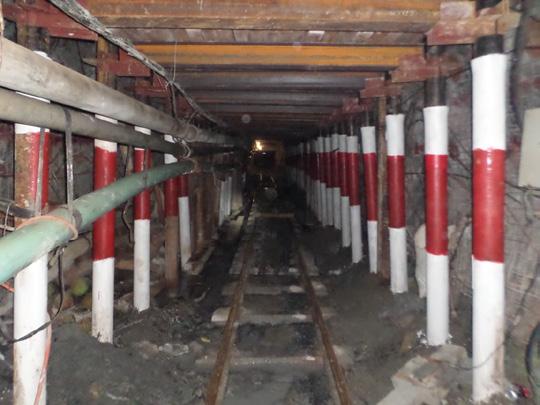
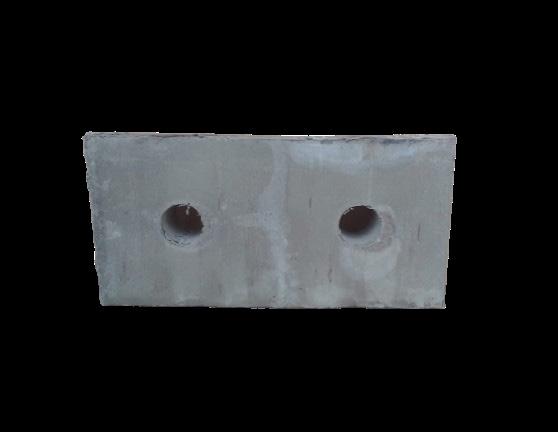

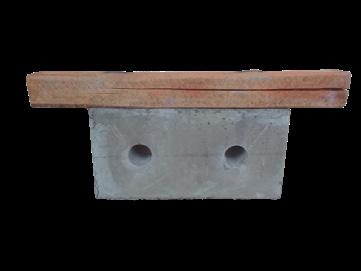
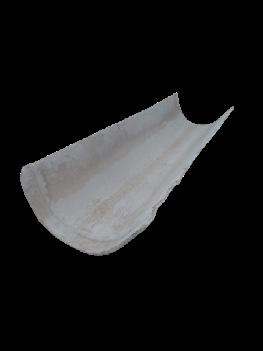
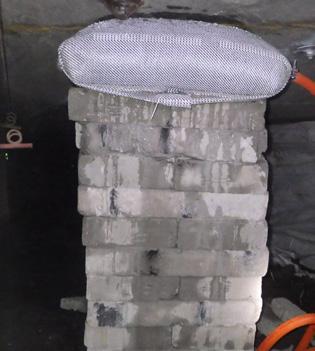
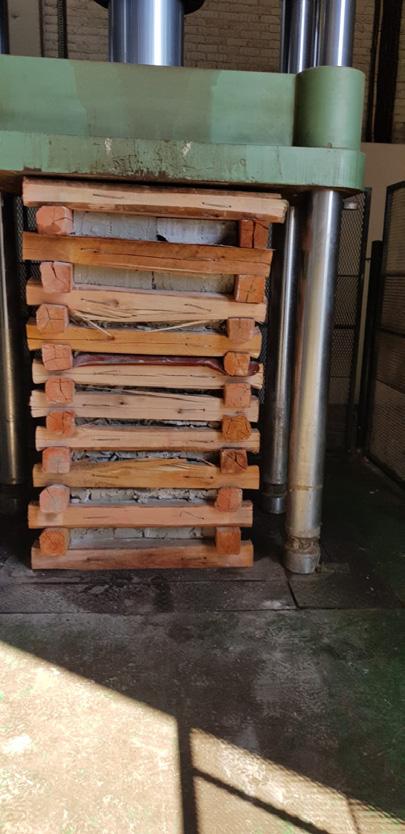
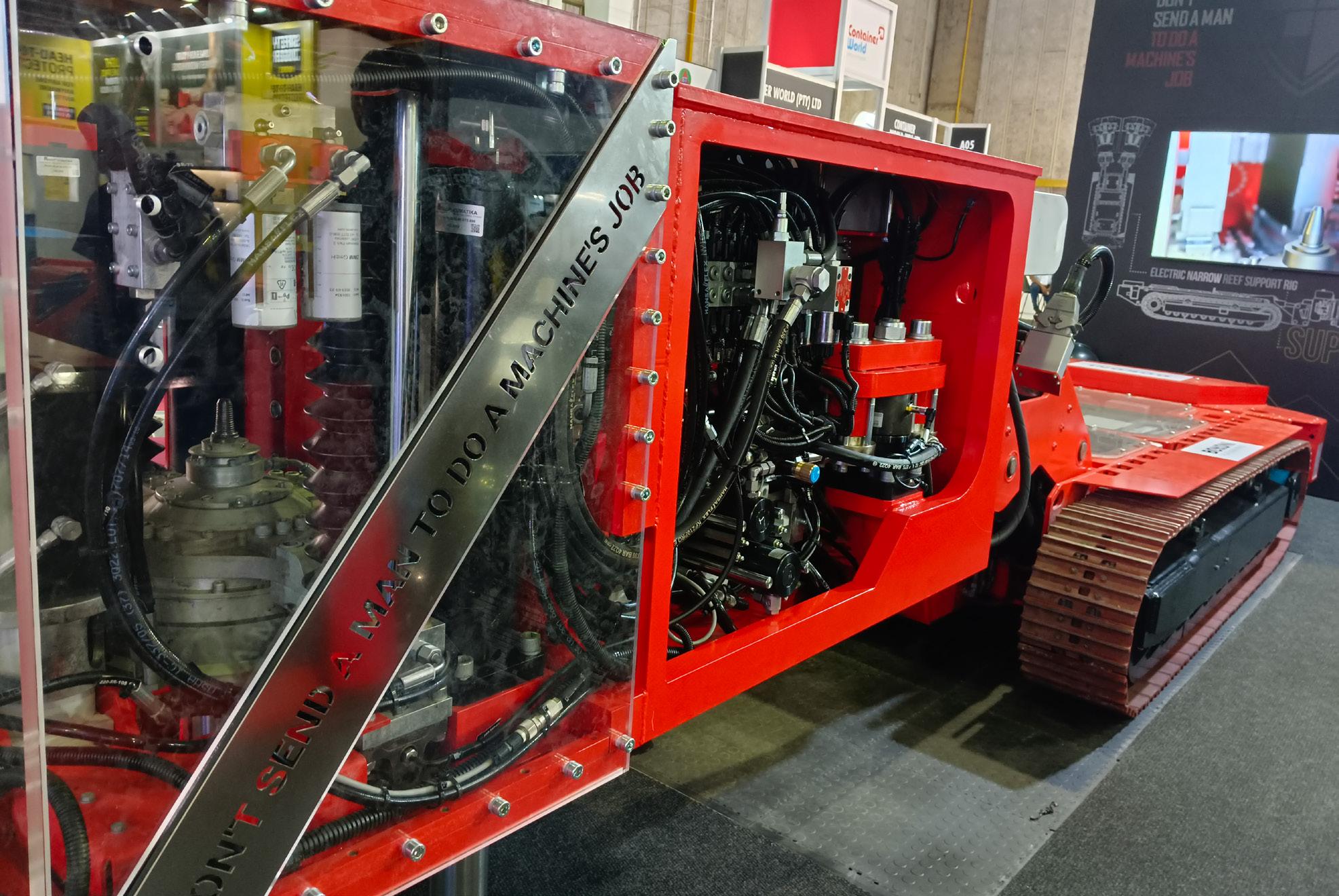
management, compliance auditing, and environmental monitoring and reporting to ensure compliance with regulations, minimised risk, and most importantly, a safe and sustainable working environment.
COMMITTED TO ENVIRONMENTAL EXCELLENCE
In line with BPM’s dedication to shaping a brighter future in mining, the company leverages a robust and impactful environmental strategy, keeping a close eye on its carbon contributions.
“We report both monthly and quarterly on sustainability data that indicates BPM’s contributions towards environmental stewardship, which is one of the key pillars of ARM’s sustainable strategy,” Joubert points out.
In line with this commitment, the business has embarked on the ambitious mission of modernising its mining activities to ensure long-term sustainability.
At the heart of this vision, BPM is upgrading several core processes, which it hopes will filter out into the
“SPREADING AWARENESS ABOUT PREFERENTIAL PROCUREMENT AND ITS POTENTIAL POSITIVE IMPACT ON THE COMMUNITY IS CRUCIAL AS IT HELPS CREATE AN ENABLING ENVIRONMENT FOR SUSTAINABLE BLACK BUSINESSES”
– JJ JOUBERT, SENIOR GENERAL MANAGER, BOKONI PLATINUM MINES
rest of the company’s operations.
At the same time, BPM also deploys innovative methods to ensure the mine’s longevity as the industry pivots more towards environmental stewardship.
The company has implemented many sustainable practices that are having a substantial and meaningful impact, minimising BPM’s ecological footprint as well as safeguarding and preserving the environment for future generations.
For instance, the company has begun tracking its water consumption across the entire business, looking at both the quantity and quality of
the water it is using, and proactively participating in a number of watersaving initiatives.
BPM also has a comprehensive water and wastewater management system that carefully oversees disposal.
On top of this, the company regularly monitors its emissions through the regulation of dust, electricity usage, as well as diesel and petrol consumption.
Moreover, BPM has installed lowenergy lights at its plant and the Middlepunt Hill UG2 shaft section. In addition, it has replaced major energy-consuming air conditioning
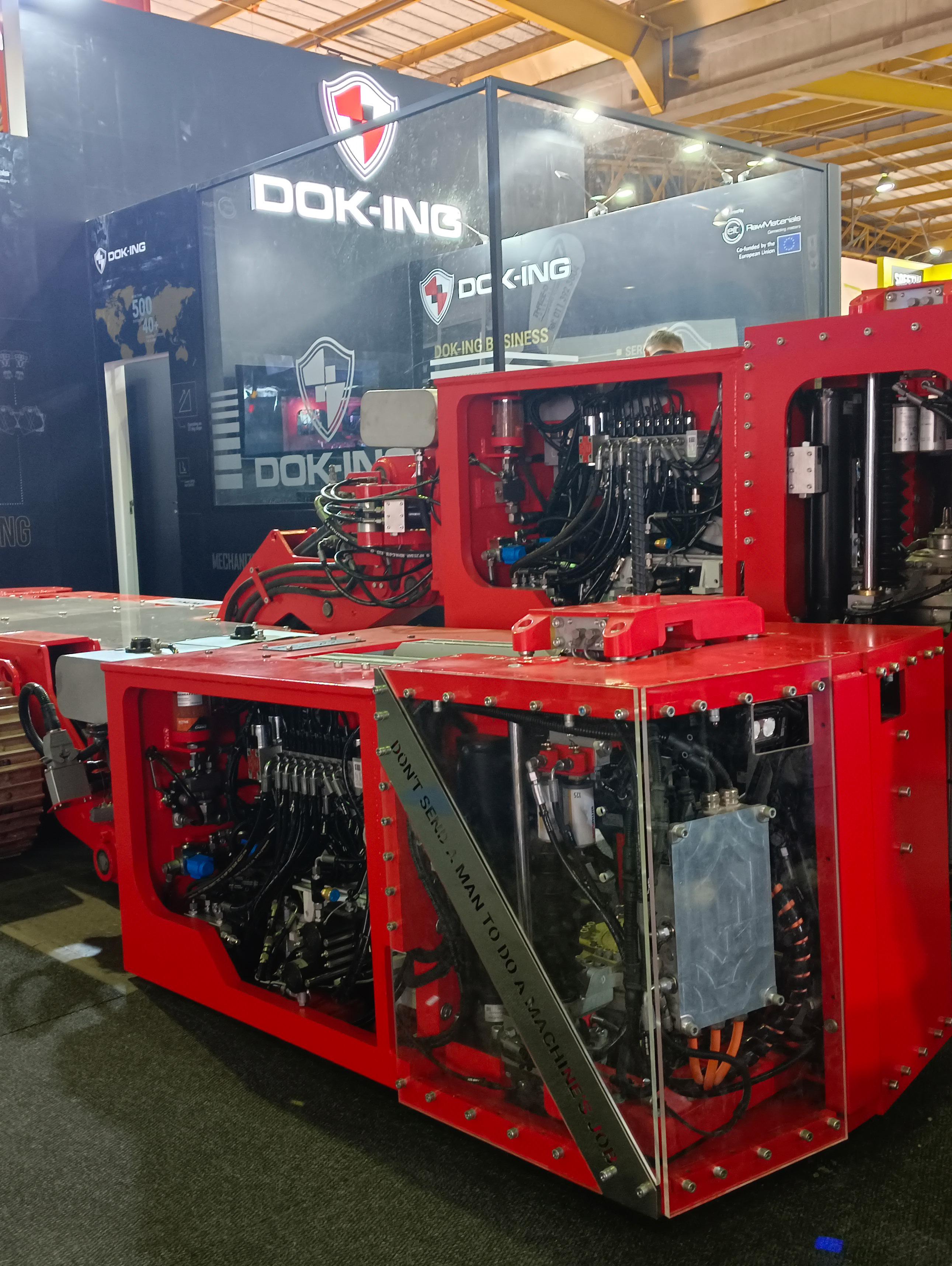
to low-consumption systems whilst also installing heat pumps at its vertical shaft at Middlepunt Hill.
Regarding the company’s trackless mobile machinery (TMM), it has refurbished the equipment to include Tier 3 engines across all its machines and introduced hydraulic-operated handheld drills, which ultimately use less power.
“We hold the highest standard of tailing storage facilities management, disturbed land rehabilitation, and biodiversity management,” Joubert surmises.
SHAPING A BRIGHTER FUTURE
As community lies at the heart of BPM’s mining activities, robust corporate governance therefore shines as a leading light throughout the company.
Indeed, BPM believes that mining doesn’t just revolve around extracting precious metals but building sustainable partnerships and generating shared value.
In line with ARM’s CSR commitments, the company proactively embraces the needs of its surrounding areas, working with nearby tribal leaders and collaborating with government agencies to ensure that the voices of local communities are always heard.
Regarding state administration, the company works with government agencies to navigate regulatory frameworks and contribute to regional development.
For example, BPM recently facilitated state-of-the-art water purification capabilities for a local community in the form of a water treatment plant. As a continuation of the company’s recent open pit mine operations, the water treatment plant was acquired to provide potable drinking water to the entire company and its surrounding areas.
Set for completion by the end of 2024, the plant will streamline the area’s water provision by negating
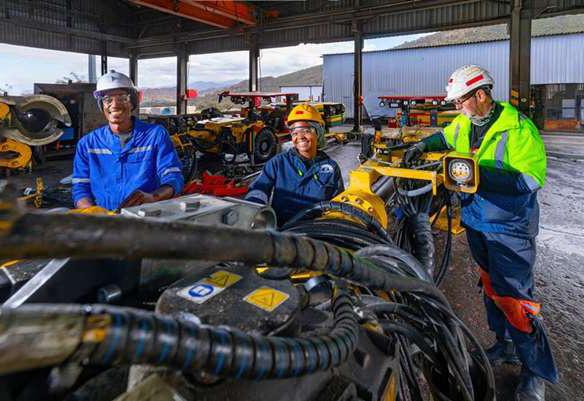
“WE HOLD THE HIGHEST STANDARD OF TAILING STORAGE FACILITIES MANAGEMENT, DISTURBED LAND REHABILITATION, AND BIODIVERSITY MANAGEMENT”
– JJ JOUBERT, SENIOR GENERAL MANAGER, BOKONI PLATINUM MINES
the need for a number of smaller water plants that require substantial maintenance, whilst also enabling an influx of water for the planned growth of the open pit mine.
BPM will likewise bring the company in line with the latest Department of Mineral Resources and Energy (DMRE) requirements by going through a stringent dam realignment process in the near future.
“This will save on water and protect our underground water supply for generations to come,” Joubert points out.
The mandatory legislature dictates that all mining dams must be lined to prevent underwater contamination for future generations, increasing the company’s credible standing in the industry.
Therefore, this project will not only benefit BPM’s ability to provide potable water, but by doing so, it will have a major impact on many institutions across the surrounding area.
“For example, we received a request from two of our neighbouring schools - Potlake Secondary School and Motsepe Primary School - to assist with the provision of safe drinking water.
“This required us to assess the situation and ensure that the water was purified and made safe for consumption,” he adds.
Additionally, the company recently completed a landmark community project through the construction of Mogabane Mobile Clinic, a pillar of BPM’s social and labour plan (SLP) initiative.
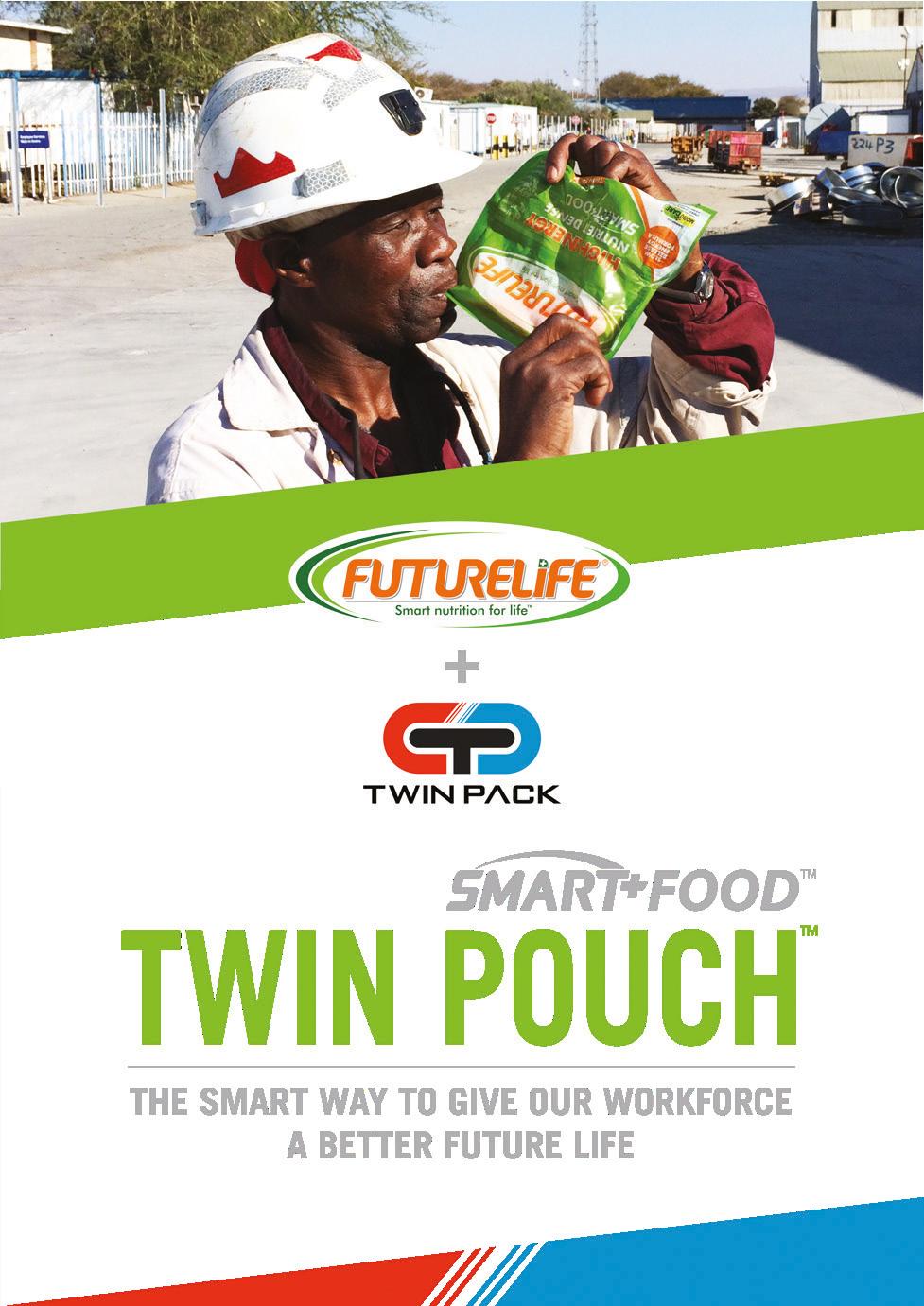
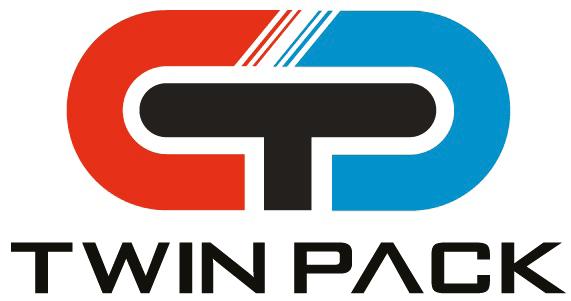
THE SMART WAY TO GIVE YOUR WORKFORCE A BETTER FUTURE LIFE
What is FUTURELIFE®?
FUTURELIFE® is Smart because it is the first and only scientifically LOW GI food, to combine 25 VITAMINS and MINERALS, 19 AMINO ACIDS, OMEGA-3, SELENIUM and MODUCARE®.
It is also high in ENERGY, PROTEIN and DIETARY FIBRE and can be enjoyed as a complete meal or snack anytime of the day. It can be MIXED INSTANTLY WITH JUST WATER AND REQUIRES NO COOKING.
The TWIN POUCH concept combines an excellent FUTURELIFE® nutritional powder with purified water separated by a temporary seal in a twin pouch. Keeping the nutrtional powder and the purified water separate, with a shelf life of six months, is what makes it very practical to use in any situation.
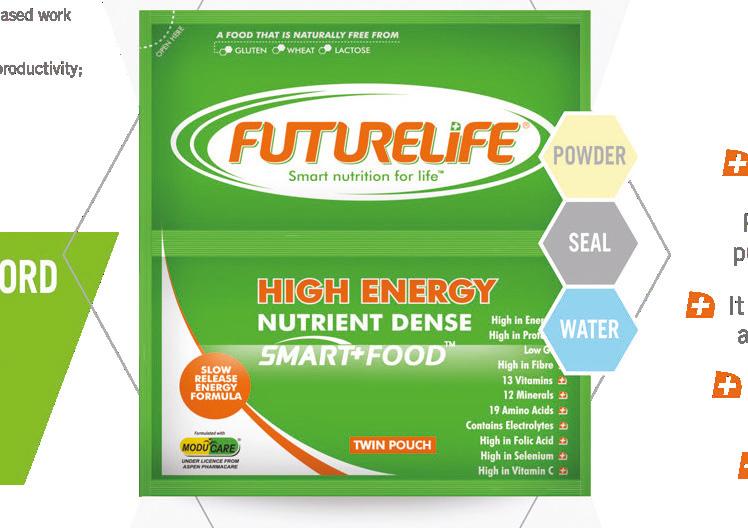
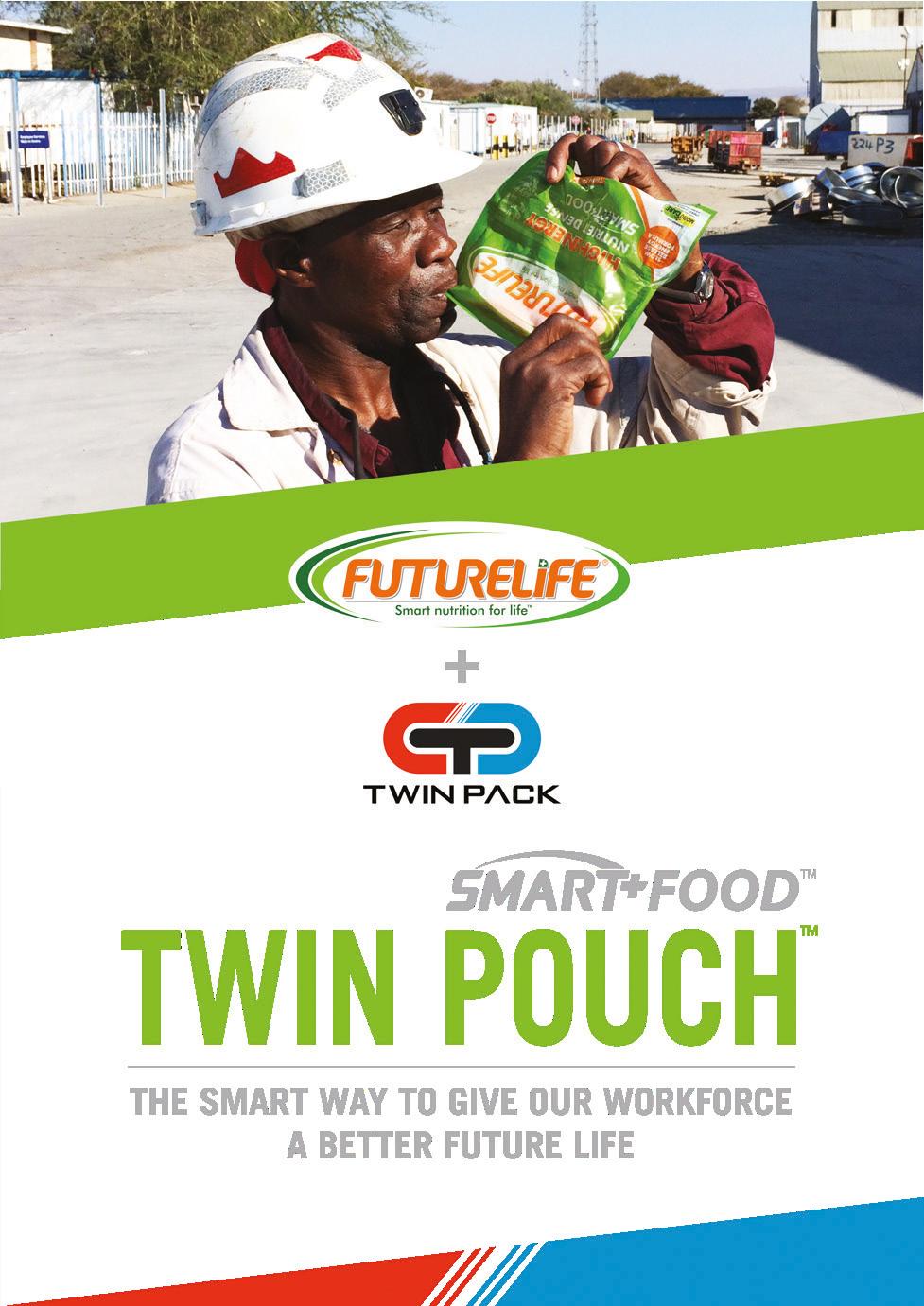
By squeezing the water pouch, the seal is broken and the powder and water combine. The result is a delicious and nutritious meal in a pouch! 260ml (60g / 200ml) 275ml (75g / 200ml) available in For enquiries please

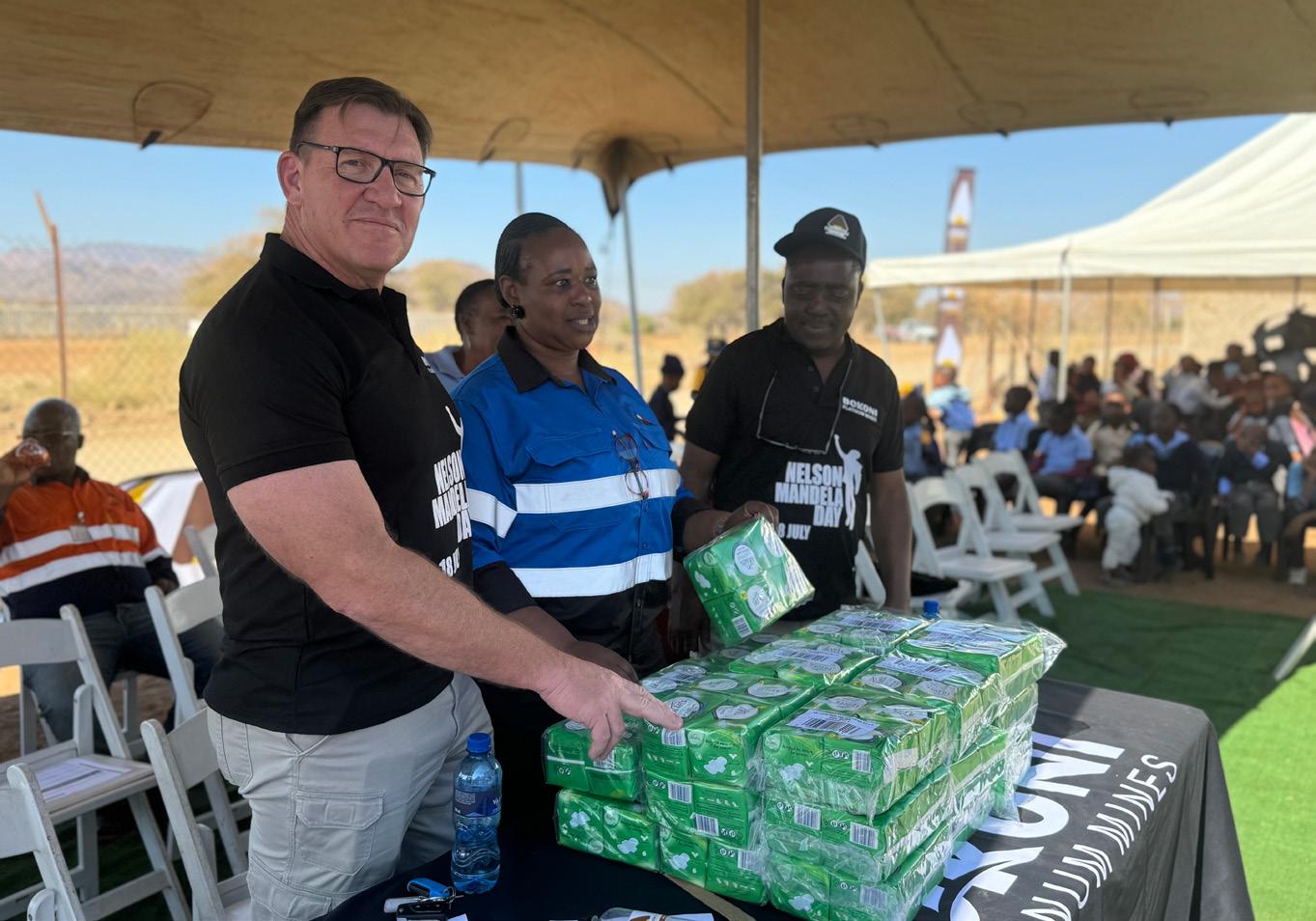
Correlating with the company’s overarching mission, the clinic has addressed the critical need for healthcare access across all areas of the local community.
The mobile clinic will help bring urgent patient care closer to home in underserved areas and meet the needs of those who may not be able to travel far due to limited transport infrastructure in certain areas.
The Mogabane Mobile Clinic was constructed and opened in close collaboration with the Department of Health, as the company helped fund the ZAR6 million project.
With the aim of restoring dignity by ensuring accessible and appropriate healthcare, the clinic supports caregivers from food security programmes and social development organisations, reflecting BPM’s commitment to the advancement and well-being of the community.
EMPLOYEE EXCELLENCE
BPM’s commitments go beyond that of mineral extraction, as the company consistently endeavours to positively impact the lives of its team, as well as their families and local communities.
In recognition of this aim, BPM has implemented strategic measures to ensure that its workforce is effectively upskilled and reskilled to align with the future needs of the PGM sector and African mining landscape.
Firstly, the company regularly conducts a skills audit to assess the
“ARM IS FULLY DEDICATED TO BPM’S REVIVAL IN A WAY THAT COLLABORATES WITH LOCAL COMMUNITIES”
– JJ JOUBERT, SENIOR GENERAL MANAGER, BOKONI PLATINUM MINES
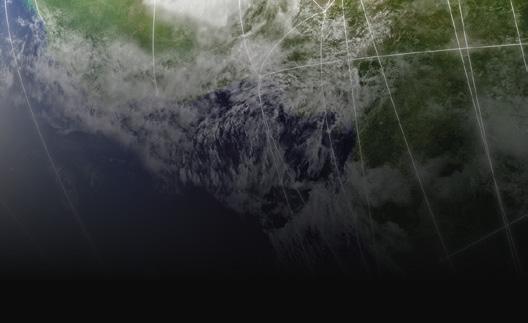
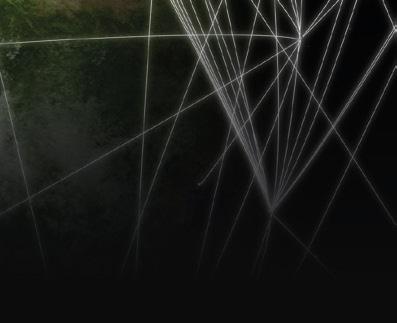

UNLOCKING VALUE TO DRIVE RESULTS
Value is elusive. You know it exists, but bringing it to the fore is never easy when it is shrouded by the complexities of your day-to-day.
We’re a wholly owned black management consultancy focused on unlocking value. Our expertise spans across diverse industries, allowing us to bring unique insights and methods to your supply chain challenges.
Our approach transforms challenges into clear, actionable solutions, stripping out complexity and undue pressure on people, processes and systems. Reach out to us to produce clear, practical, and repeatable results.
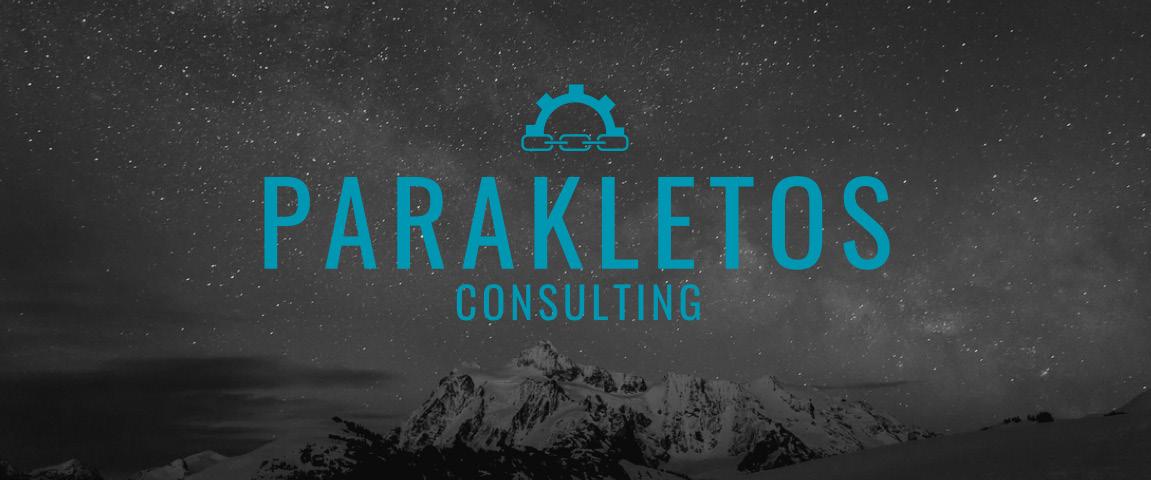
ability of its staff and identify gaps to improve efficiencies with various training initiatives.
For instance, BPM offers a plethora of training programmes across the organisation. These include digital literacy, training for the use of specialised equipment such as NRE, and online learning courses such as Artisan 4.0™, ultimately ensuring operator and automation excellence.
Additionally, the company actively encourages and supports the higher education of its staff, as demonstrated by its many educational partnerships in which it collaborates with regional further education and training colleges to facilitate specialist upskilling.
BPM alternatively offers an on-thejob training initiative in which team members are assigned a mentor that offers guidance and continuous feedback on learnerships, internships, and cadetships, which are also offered
to those in the local community.
Through online and flexible courses, the company has introduced simulators, virtual reality (VR) for practical learning, and gamification in order to transform learning.
“With a strong emphasis on training, we encourage continuous learning through incentives and recognition programmes, such as our General Manager’s Quarterly Update and awards sessions,” Joubert shares.
In constant pursuit of efficiency, BPM gathers employee feedback, regularly assesses its training effectiveness, and subsequently updates its programmes accordingly.
BPM’s future holds great potential as the company anticipates 2025, marked by investing in the modernisation of operations and preparing its mine for the next generation.
“We are ensuring that our
operations are globally competitive and profitable whilst maintaining a robust balance sheet. We align production capacity to logistical and infrastructure constraints while exploring value-enhancing growth opportunities,” Joubert closes.
Therefore, at the core of its mission, BPM is continuously introducing innovative methods and maintaining successful operating standards across its mine sites, whilst also fostering community development and ensuring longevity in an evolving PGM industry.
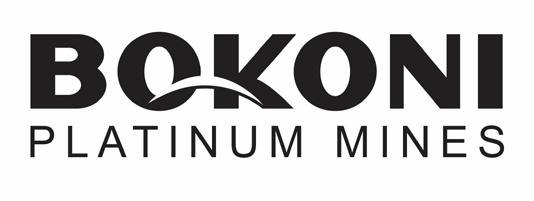
BUILDING SOUTH AFRICA’S FUTURE TOGETHER

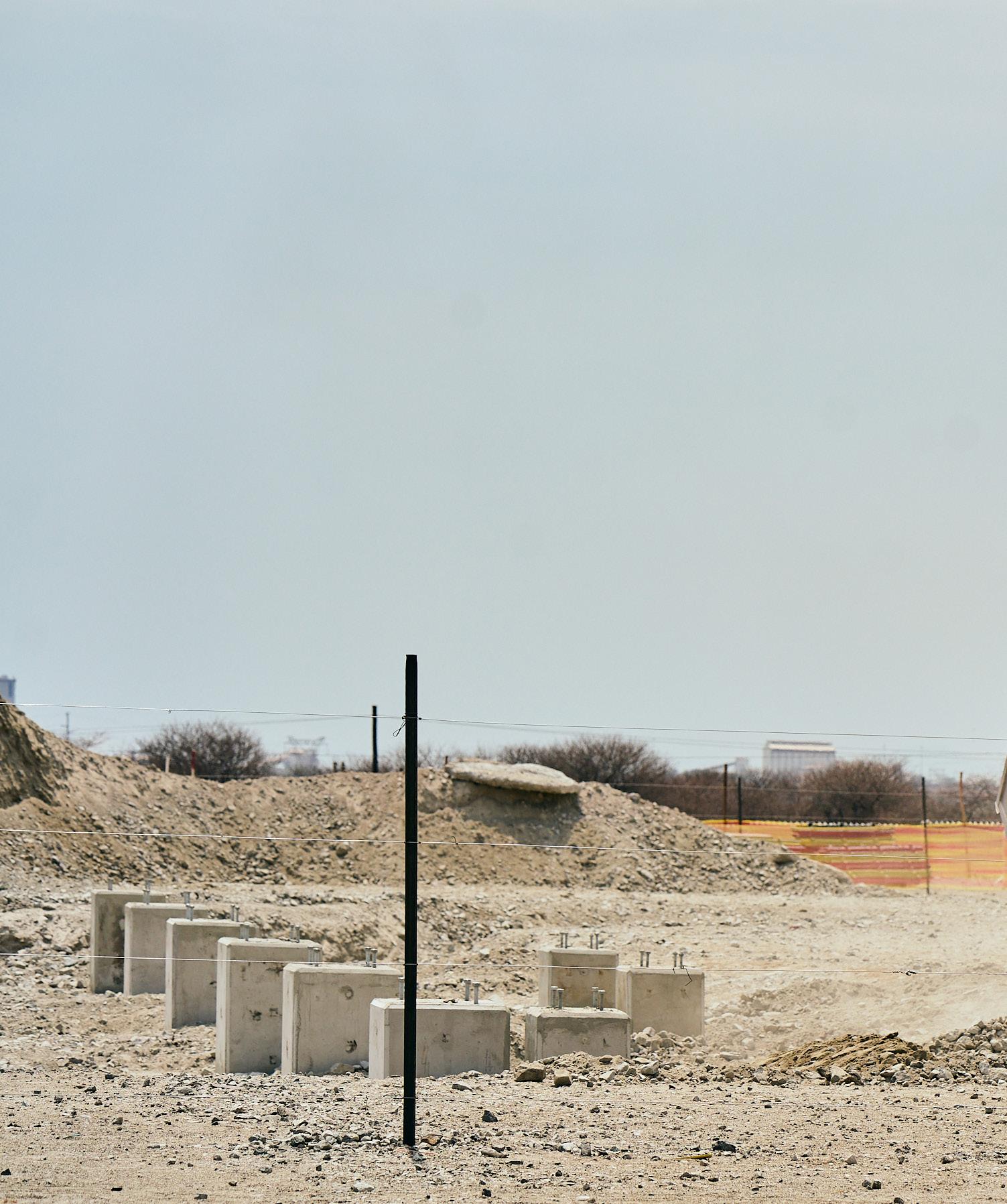
Proudly providing specialist mining infrastructure services across South Africa for over a decade, G4 Mining and Civils (Pty) Ltd boasts a solid track record for success. Quintin Badenhorst, Managing Director, tells us more about the company’s resilience, competency, and wide-ranging capabilities
Writer: Lily Sawyer | Project Manager: Andrew Marjoram
Having faced ongoing fluctuation in recent years, today’s South African construction industry, although still unpredictable, is optimistic – with imminent government investment forecast to give rise to an average annual growth rate (AAGR) of more than two percent between 2025 and 2028.
Leading provider of specialised
mining infrastructure and civil engineering solutions, G4 Mining and Civils (Pty) Ltd (G4MC), is poised to benefit from this uplift.
“The market has been under pressure, so a downward cycle is understandable – however, this has started to pick up, which is very positive for us,” introduces Quintin Badenhorst, Managing Director.
G4MC’s expertise in reinforced
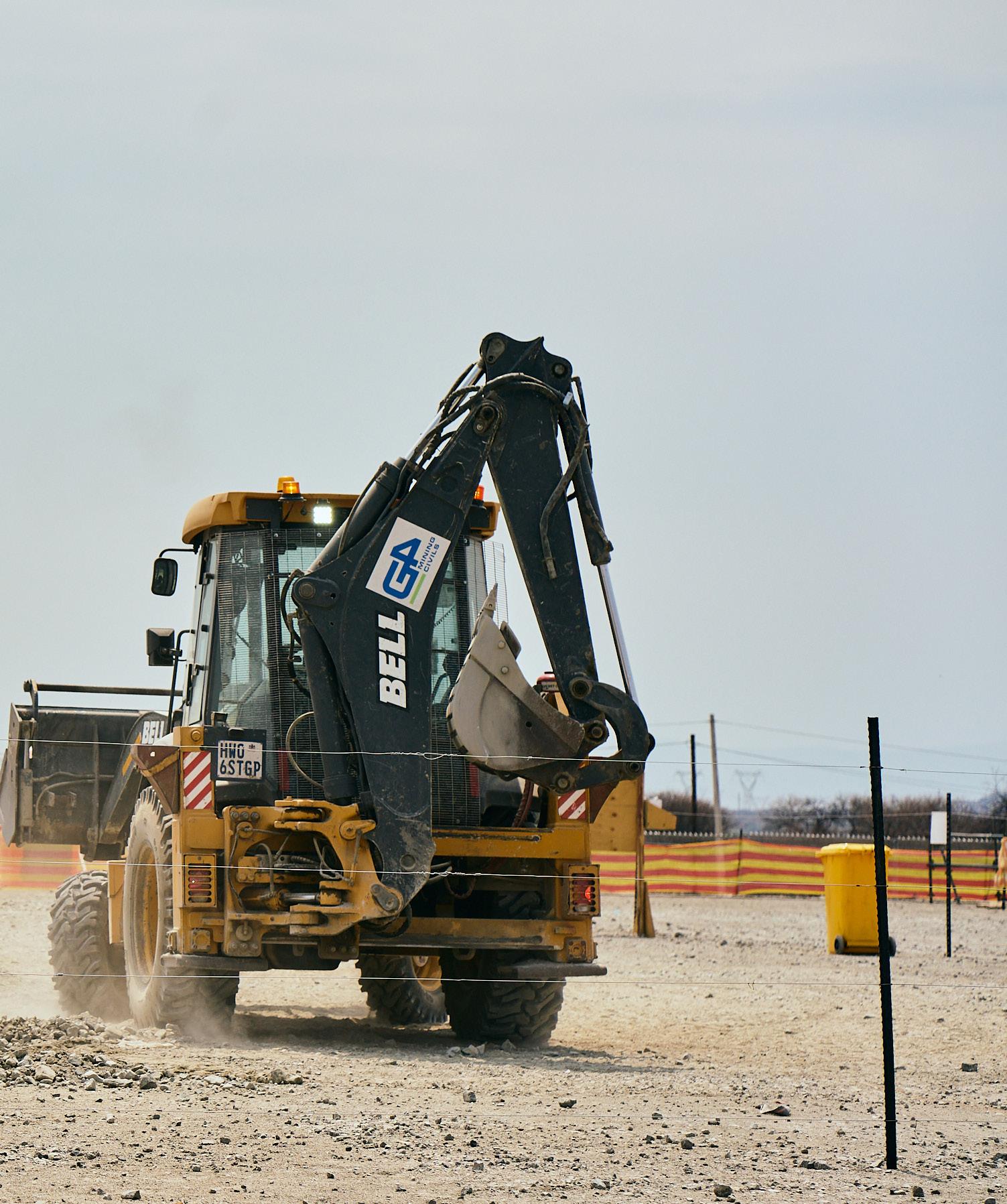
concrete, geotechnical engineering, bulk earthworks, water infrastructure, and water reticulation services has made it a leader in the South African construction market.
Primarily focusing on local operations, the company remains close to its core market, with the majority of its work taking place in the mining infrastructure sector, where it has built a solid reputation.
“We thrive on the complex and rewarding projects we encounter in this space and have a thorough understanding of the unique needs of the industry,” he elaborates.
GOING THE EXTRA MILE
Setting G4MC apart is its dedicated team of 175 knowledgeable and enthusiastic employees.
“We are privileged to have a team who really go the extra mile to ensure that our projects are executed effectively.”
“Our company structure is reasonably flat, so we find that senior management is personally involved in projects and consequently remain close to the workforce,” Badenhorst informs.
In addition to its staff, an extensive and diverse fleet of in-house plant and equipment adds to G4MC’s impressive arsenal.
With a wide range of machinery at its disposal, including tractor-loaderbackhoes (TLBs), excavators, tippers, 14,000 litre (l) water carts, walkbehind and ride-on rollers, complete with a comprehensive inventory of small tools, the company’s capabilities are extensive.
An on-site workshop enables it to maintain and efficiently service equipment, ensuring it is always ready to meet high workload demands.
Moreover, a carefully managed vendor application process helps G4MC to source additional construction equipment when needed, ensuring that selected partners align with company values and meet its high standards.
“Furthermore, we are wellconnected with key service providers, enabling us to quickly address any operational shortfalls,” he adds.
These key capabilities allow G4MC to confidently take on new contracts and consistently deliver timely projects of the highest standard.
A VAST PORTFOLIO
Of course, G4MC’s competency and expertise are reflected most clearly in its vast portfolio of ongoing projects.
“The successful completion of the Two Rivers Platinum (TRP) Merensky Project this May was a significant milestone for our team,” Badenhorst reveals.
This project involved carrying out extensive civil and earthworks for the crusher facility in Steelport, Limpopo province. The company cast 3,605 cubic metres (cbm) of concrete, used 222 tonnes (t) of reinforcement, and moved 153,000 cbm of earthworks –requiring a total of 457,455 man-hours.
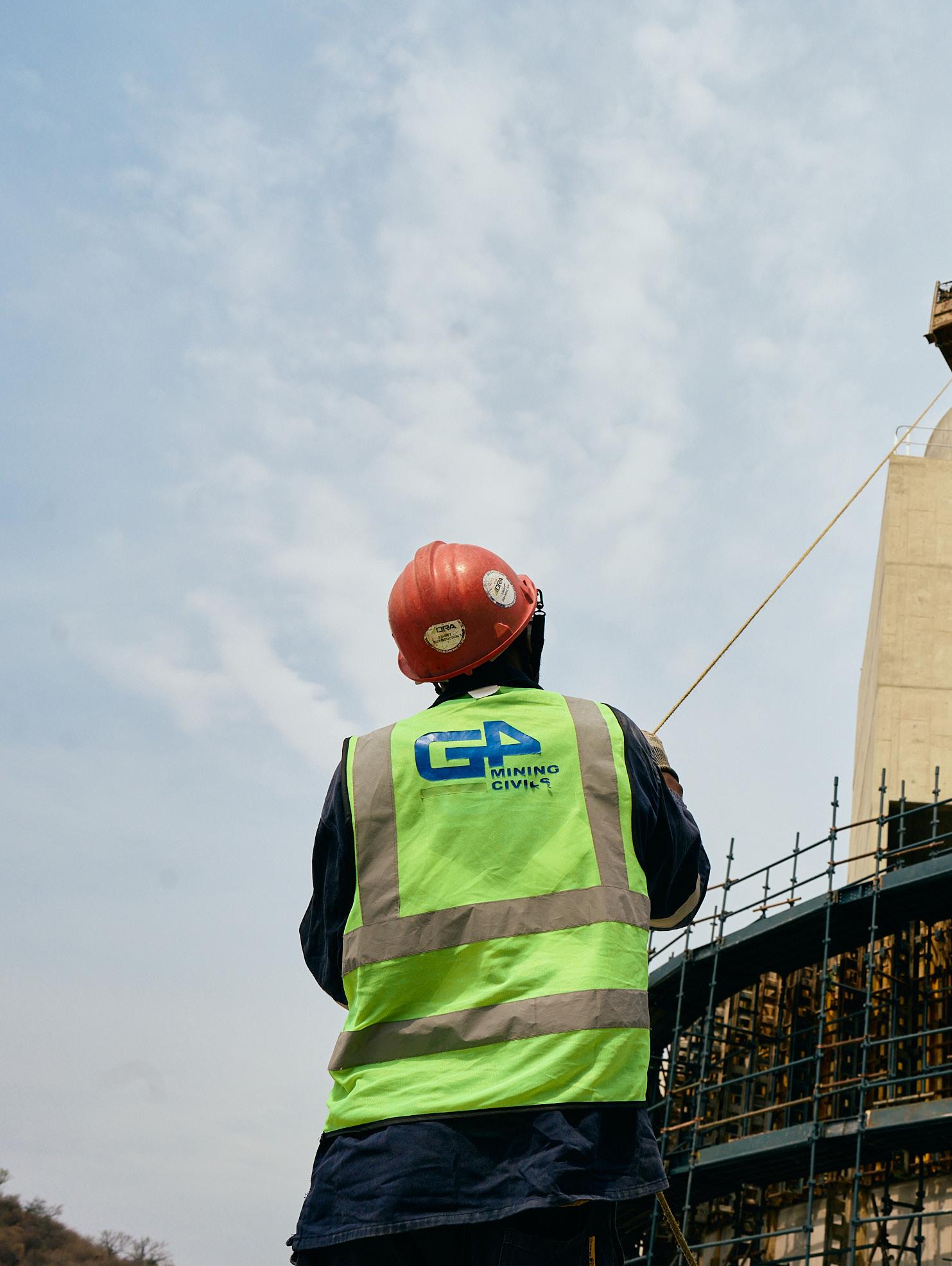
“This project was a strong showcase of our ability to manage complex projects and deliver top-quality outcomes for our clients,” he adds.
G4MC is currently constructing a triple-cell cooling tower and two double-cell pre-cooler structures at Zondereinde, also in Limpopo province.
As the structures are in excess of 20 metres (m) high, this project will require 1,300 cbm of concrete to be cast, 41t of steel reinforcement bars (rebar), and 1,100 square metres (sqm) of formwork.
“At such a height, these structures pose a challenge.
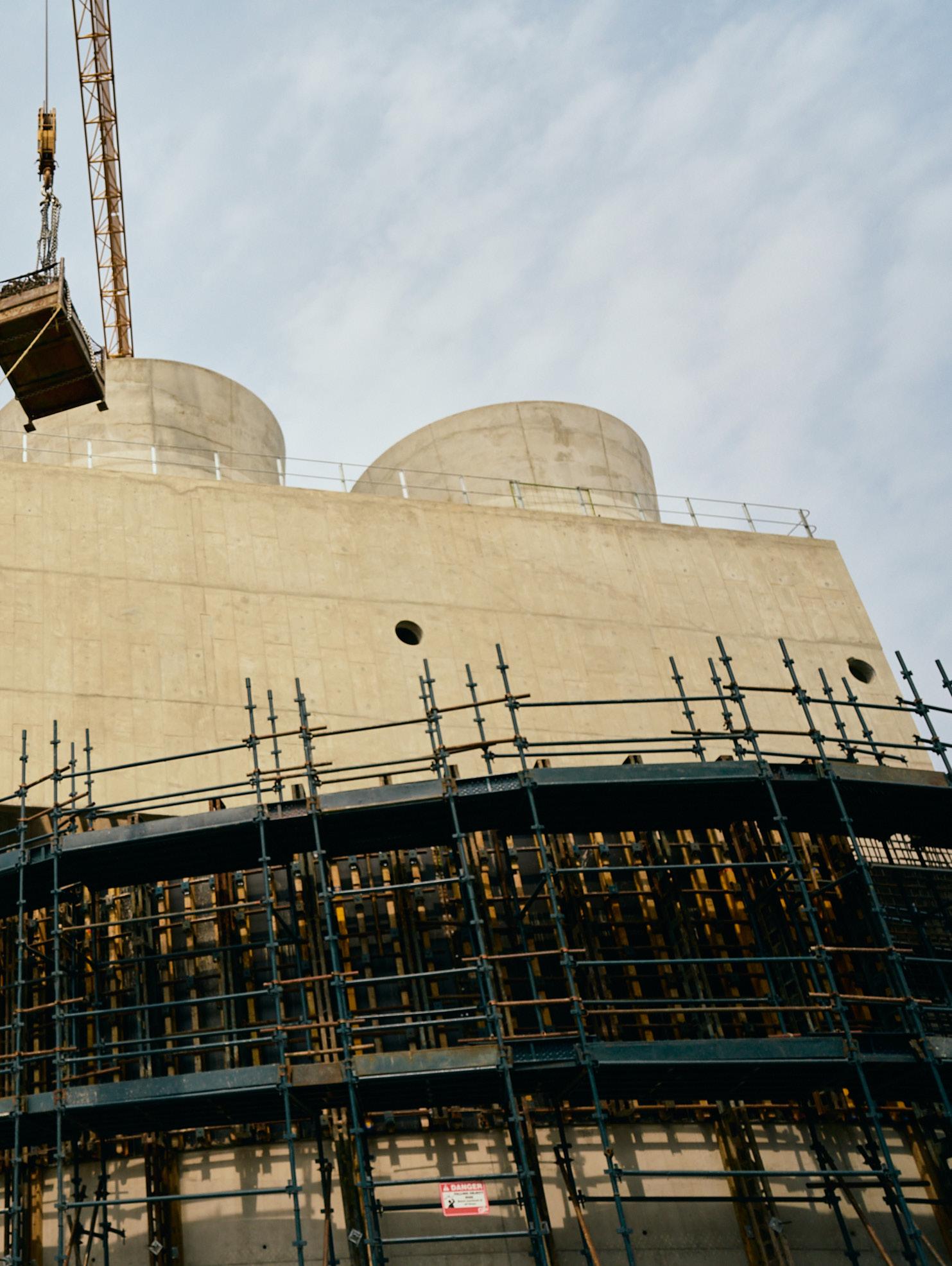
“IT IS IMPORTANT FOR US TO INCREASE THE EFFICIENCY AND SUSTAINABILITY OF OUR OPERATIONS, BENEFITTING BOTH OUR COMPANY AND THE ENVIRONMENT ”
– QUINTIN BADENHORST, MANAGING DIRECTOR, G4 MINING AND CIVILS (PTY) LTD
“Attention to detail and strict safety procedures are therefore integral to the project’s success, which we expect to be completed in the first quarter of 2025,” he states.
EXTENSIVE EXPERIENCE
G4MC’s extensive experience in reinforced concrete, particularly within the mining infrastructure sector, is a key differentiator for the company.
“Our capabilities include completing projects ranging from the construction of cooling towers to foundations for steel structures to motor control centres (MCC), mine stores, winder houses, and winder foundations,” Badenhorst informs.
The company has also worked on both shaft collars and chrome mine reflux classifiers, concretising its broad range of expertise.
SUPPORTING COMMUNITIES
G4MC believes that engaging with local communities is a top priority and essential not only in supporting the growth of the area, but also enhancing the broader purpose of its work. The company’s recent projects include:
· LERUTLE PRIMARY SCHOOL, BENONI – G4MC is proud of its ongoing partnership with Lerutle Primary School, where it has donated science kits and books to aid in the education of students. Supporting education in this way helps foster a future generation equipped with the tools for success.
· BARUAKGOMO AGRICULTURAL COOPERATIVE – During its time at the Waterval Smelter, Rustenburg, G4MC donated a SHORTi Husky MT50 fodder mixer to Baruakgomo Agricultural Cooperative, a small local business. Established in 2011, the cooperative comprises 11 farmers who primarily focus on cattle farming. G4MC’s donation supports these farmers in their efforts to improve productivity and sustainability.
“Community work is vital to our business because it builds strong local relationships and gives our work a purpose beyond financial success. By investing in the future of our community, we aim to create a lasting and positive impact,” enthuses Badenhorst.
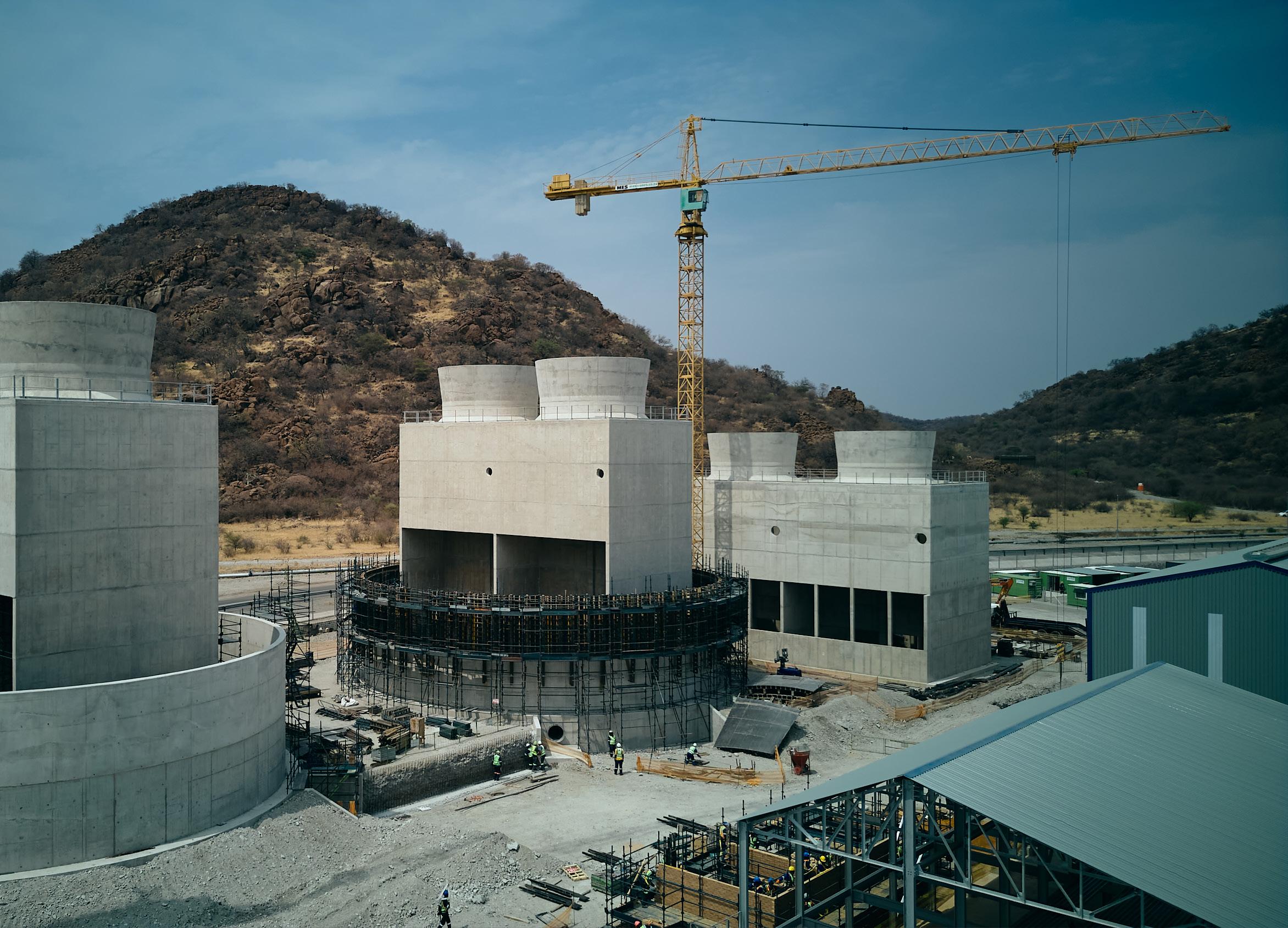
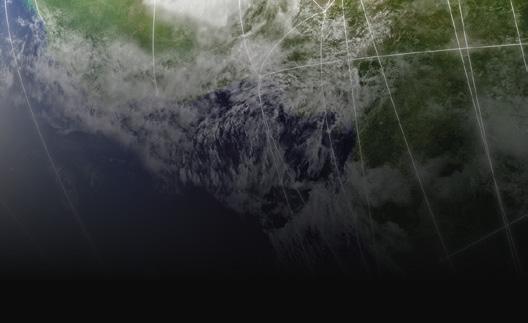
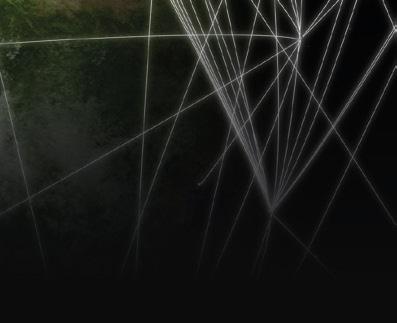

www.mining-outlook.com/subscribe
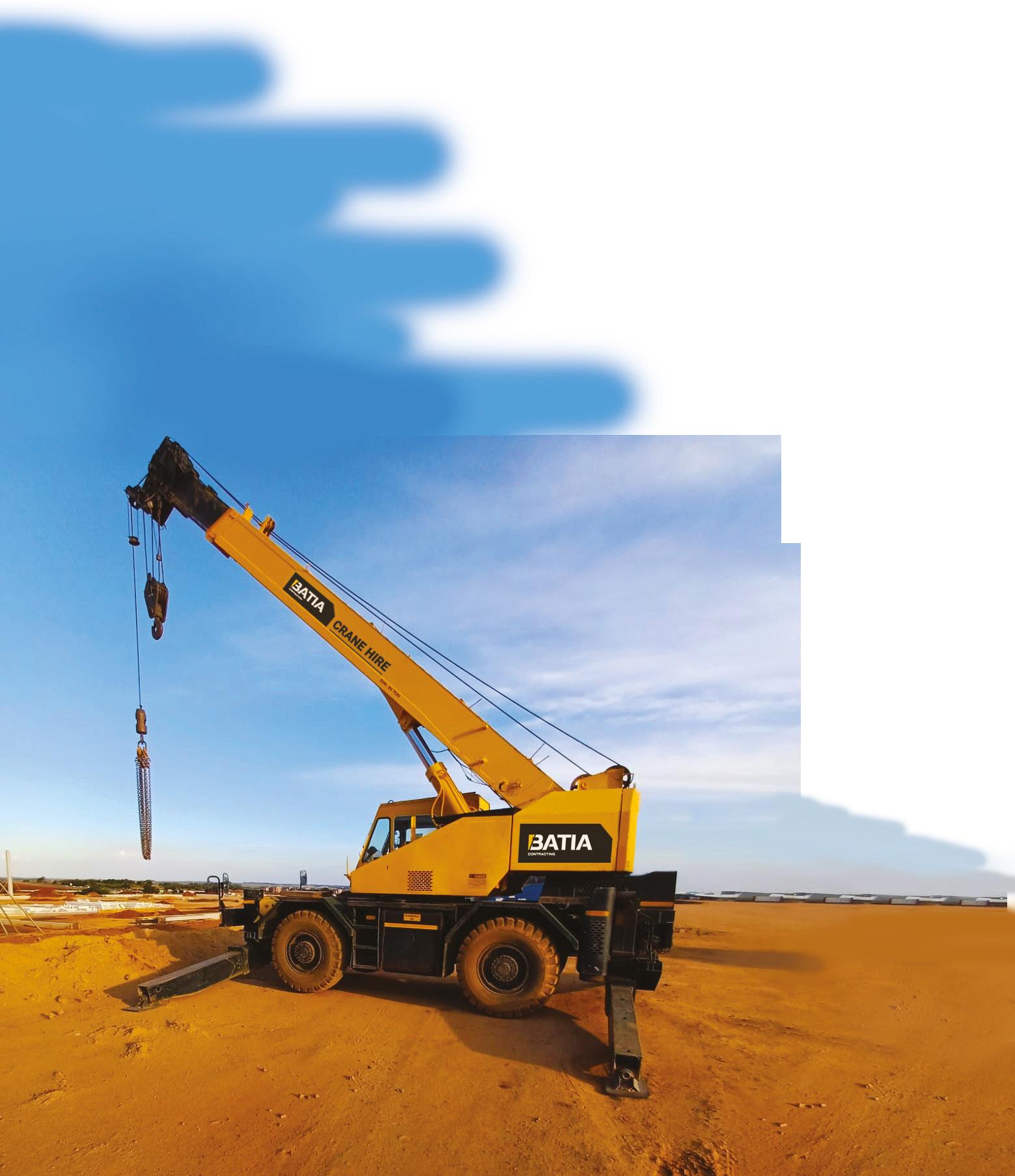
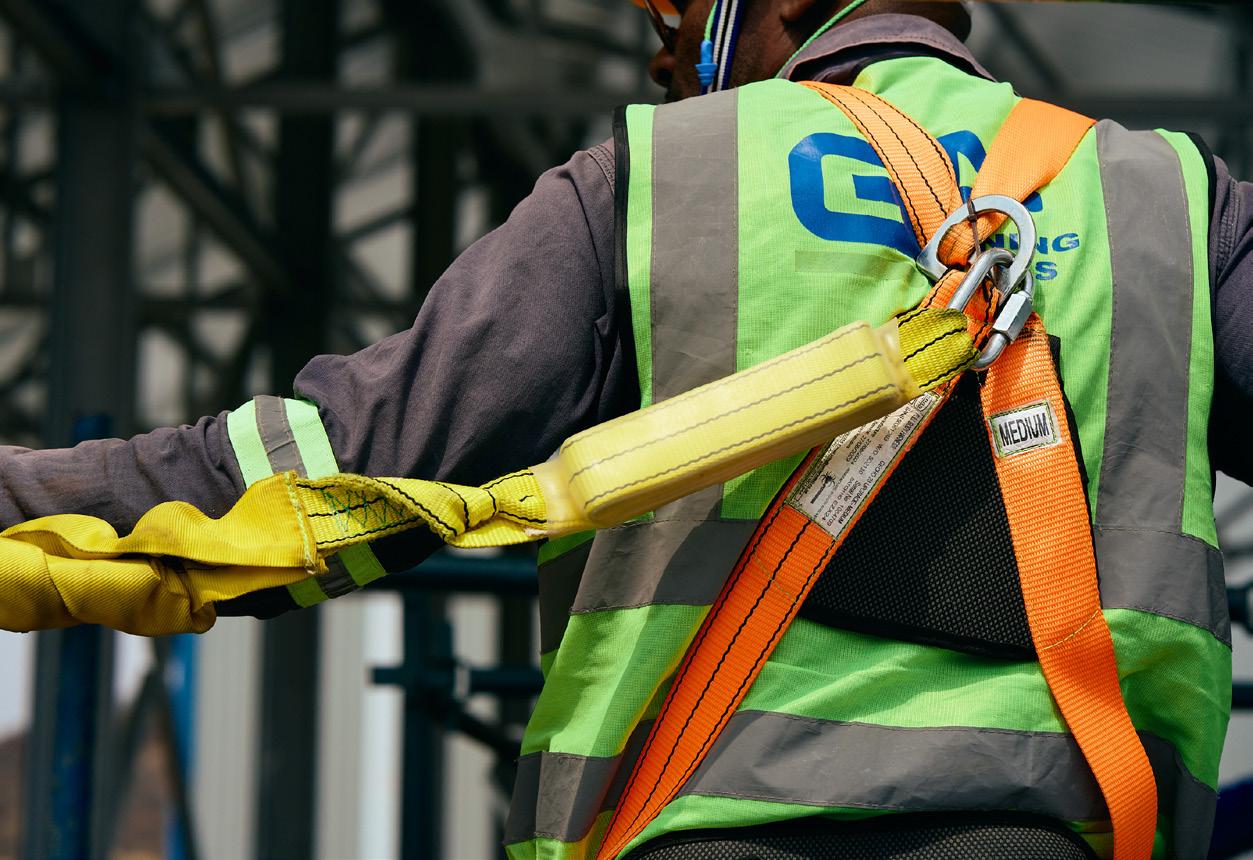
In addition, having successfully completed projects involving thickener foundations, surge bins, dense media separation (DMS) plants, filter presses, and overland conveyor support foundations, G4MC
CRANE HIRE
has a strong track record in material building.
Meanwhile, having an internal quality management system (QMS) helps the company to define risks clearly.
“An effective QMS is vital in our industry and has become an important part of the tendering process,” he details.
This is because recent industry requirements now compel construction companies to consider their environmental impact.
“We understand our role in the mining industry and its effect on the planet. It is important for us to increase the efficiency and sustainability of our operations, benefitting both our company and the environment.”
As the business works to determine how it might reduce its environmental impact in a highly carbon-dependant industry, it looks to its colleagues for guidance as it continues to learn and grow.
A TEAM EFFORT
G4MC recognises that a company’s success does not rely on the sole efforts of an individual but on collective effort.
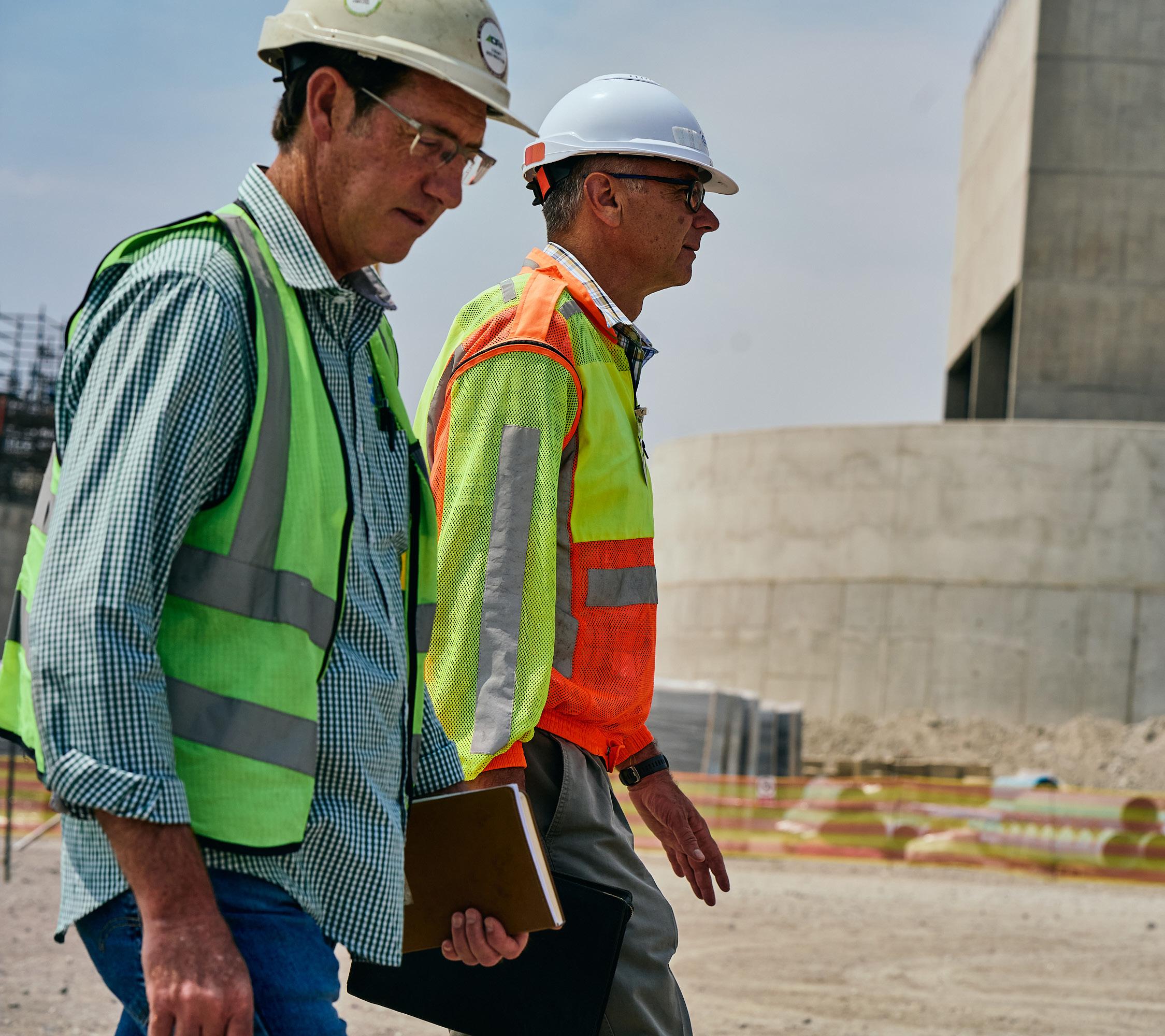
MINING OUTLOOK: COULD YOU PROVIDE SOME INSIGHT INTO YOUR CAREER TO DATE AND EXPLAIN HOW YOU BECAME INTERESTED IN THE CONSTRUCTION INDUSTRY?
QUINTIN BADENHORST, MANAGING DIRECTOR:
“I graduated from Technicon Witwatersrand with a B-Tech degree in Civil Engineering (Structural) and have over 30 years of experience in the construction industry.
“I joined G4 Civils in 2005, before taking on the role as Managing Director of G4MC
“I became interested in the industry as I had been exposed to construction my whole life – my father had his own company. I used to go to the site with him during the school holidays and always enjoyed the practical aspects of the industry combined with seeing how things were constructed.
“Initially, I was a bursary student with Basil Read Mining, working on both surface and underground projects, so I was exposed to the mining industry and environment from inception.”
The company’s staff have played an integral role in its growth over the last 10 years, demonstrating the adaptability and willingness to tackle new challenges – even beyond their assigned roles.
“We deeply appreciate our workforce, who ensure we continuously learn and push ourselves to new heights,” Badenhorst reflects.
Moreover, G4MC is proud that many of its current staff have remained with the company for several years, with engineering students who joined 15 years ago still playing an integral role today.
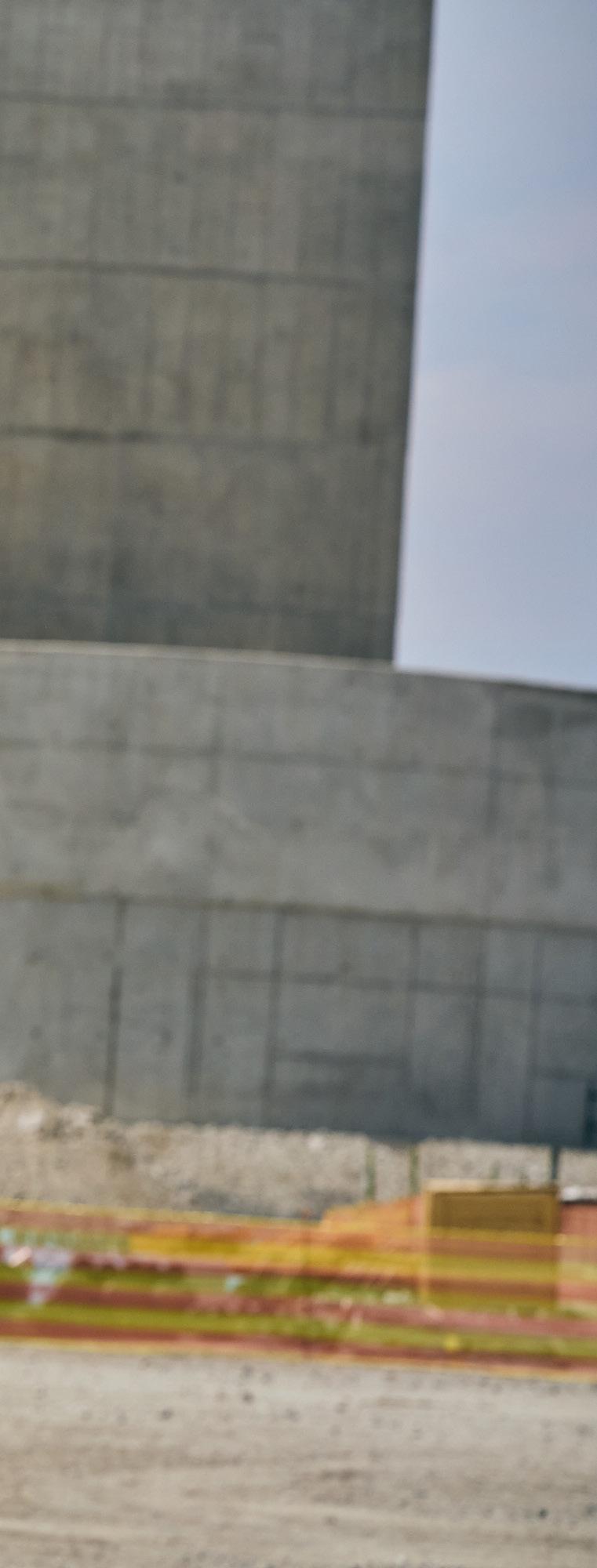
“Several of these individuals are even shareholders now, helping us to meet our broad-based black economic empowerment (B-BBEE) targets and compliance initiatives,” he prides.
As Managing Director, Badenhorst’s role is to set the tone and lead by example. By conducting fair and ethical business practices, he seeks to ensure these principles are deeply ingrained within the company’s culture.
“I truly enjoy what I do, so putting in the hours and working alongside the various teams is something I value.”

“WE ARE PRIVILEGED TO HAVE A TEAM WHO REALLY GO THE EXTRA MILE TO ENSURE THAT OUR PROJECTS ARE EXECUTED EFFECTIVELY”
– QUINTIN BADENHORST, MANAGING DIRECTOR, G4 MINING AND CIVILS (PTY) LTD
Going forwards, G4MC is working to better align its in-house system with occupational health and safety certification ISO 45001.
It also seeks to have at least six operating sites in 2025, which will require an additional plant, equipment, and a site manager, each of which is currently being procured.
Elsewhere, workforce skills development and internal knowledge training are currently underway, whilst an updated website and increased social media presence are hoped to optimise the company’s visibility.
“We are excited to see what new
opportunities and exposure the coming year may bring,” Badenhorst concludes.
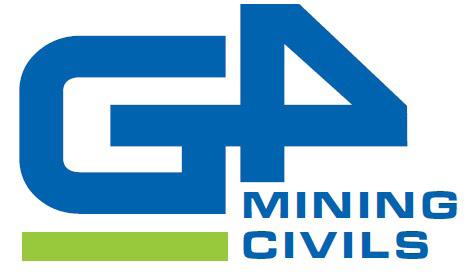
Tel: +27 (0)11 100 7126
info@g4miningandcivils.co.za
Home - G4 Mining & Civils
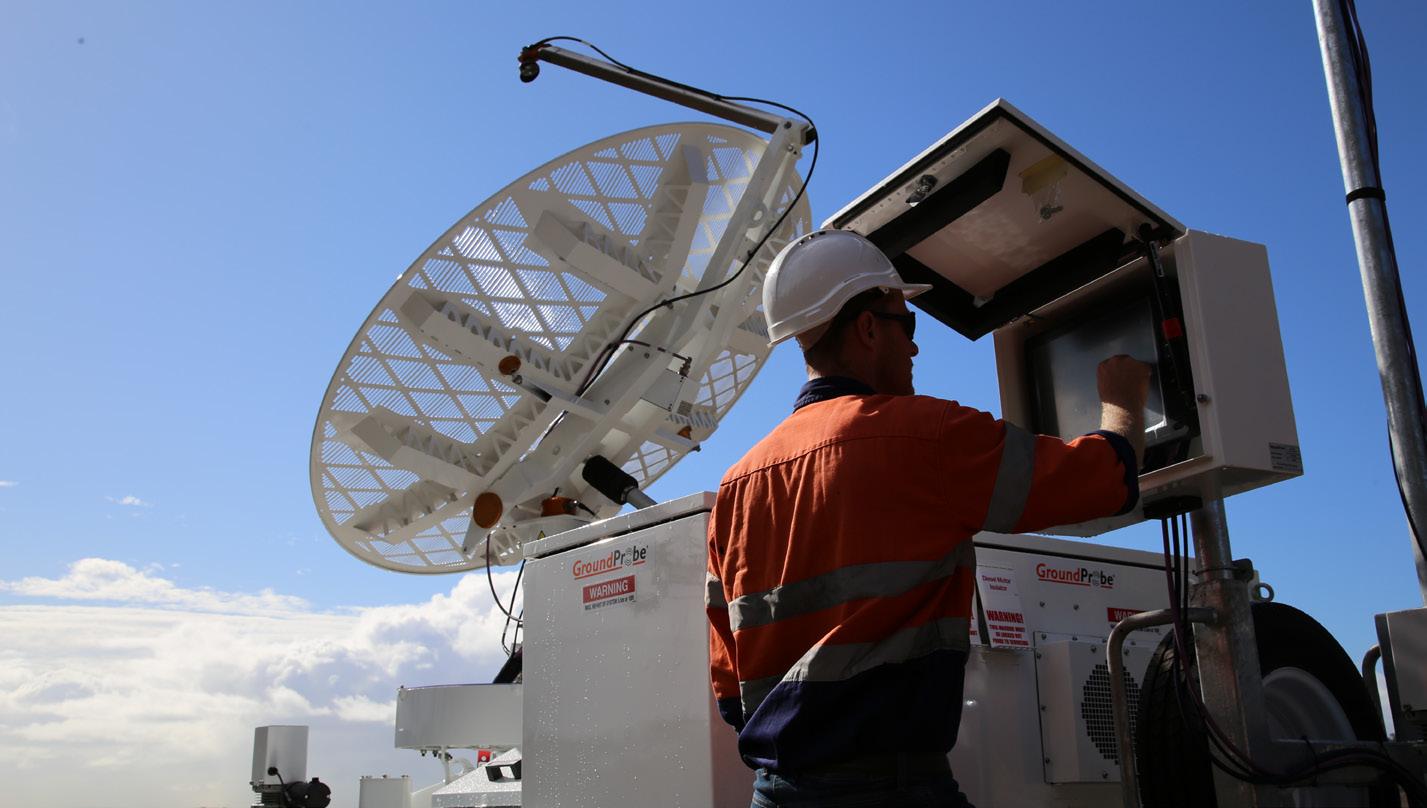
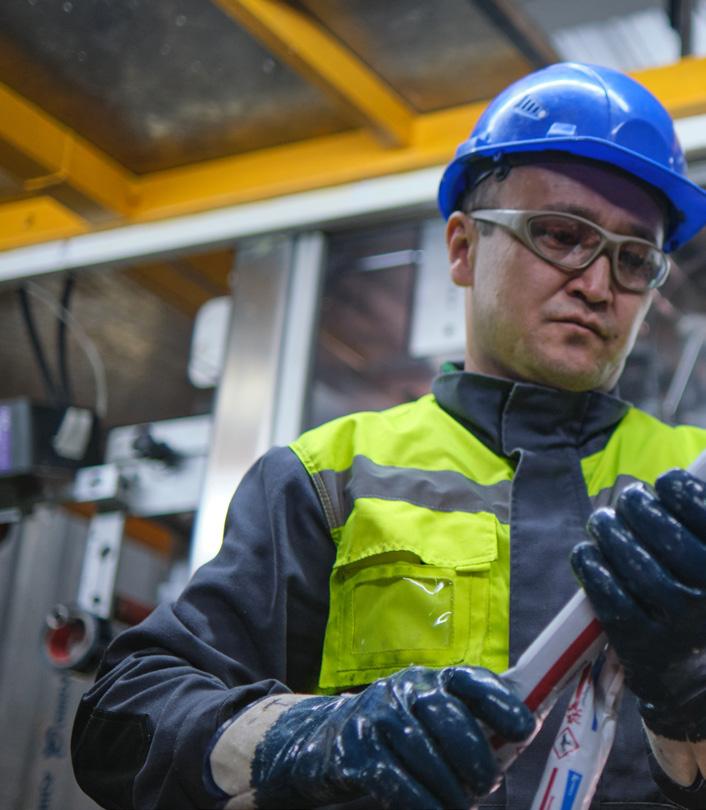
SUSTAINABLY MOBILISING THE EARTH’S RESOURCES
Across Europe, the Middle East, and Africa (EMEA), Orica is at the forefront of innovation, technology, and sustainability in the mining and infrastructure sectors. Victor Morales, Vice President of EMEA Mining, digs deep into developments across the region
Writer: Jack Salter | Project Manager: Eddie Clinton
The story of one of the world’s leading mining and infrastructure solutions providers began more than 150 years ago.
Founded in June 1874 as a supplier of explosives to the Victorian goldfields in Australia, Orica proudly
celebrated its sesquicentenary last year, an exciting milestone for the company.
This extensive heritage is a testament to Orica’s resilience, adaptability, and ability to thrive in a constantly evolving business landscape.
Its 150-year journey has also been one of transformation, as the company originally started out as Jones, Scott and Co. before it was bought by Nobel.
The organisation then went on to merge with Brunner Mond and Co., the United Alkali Company, and the British
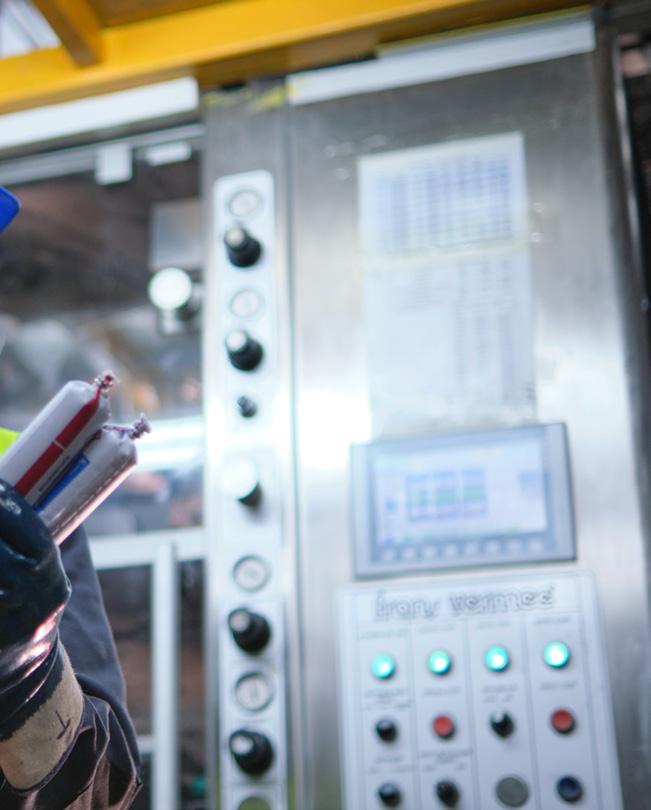
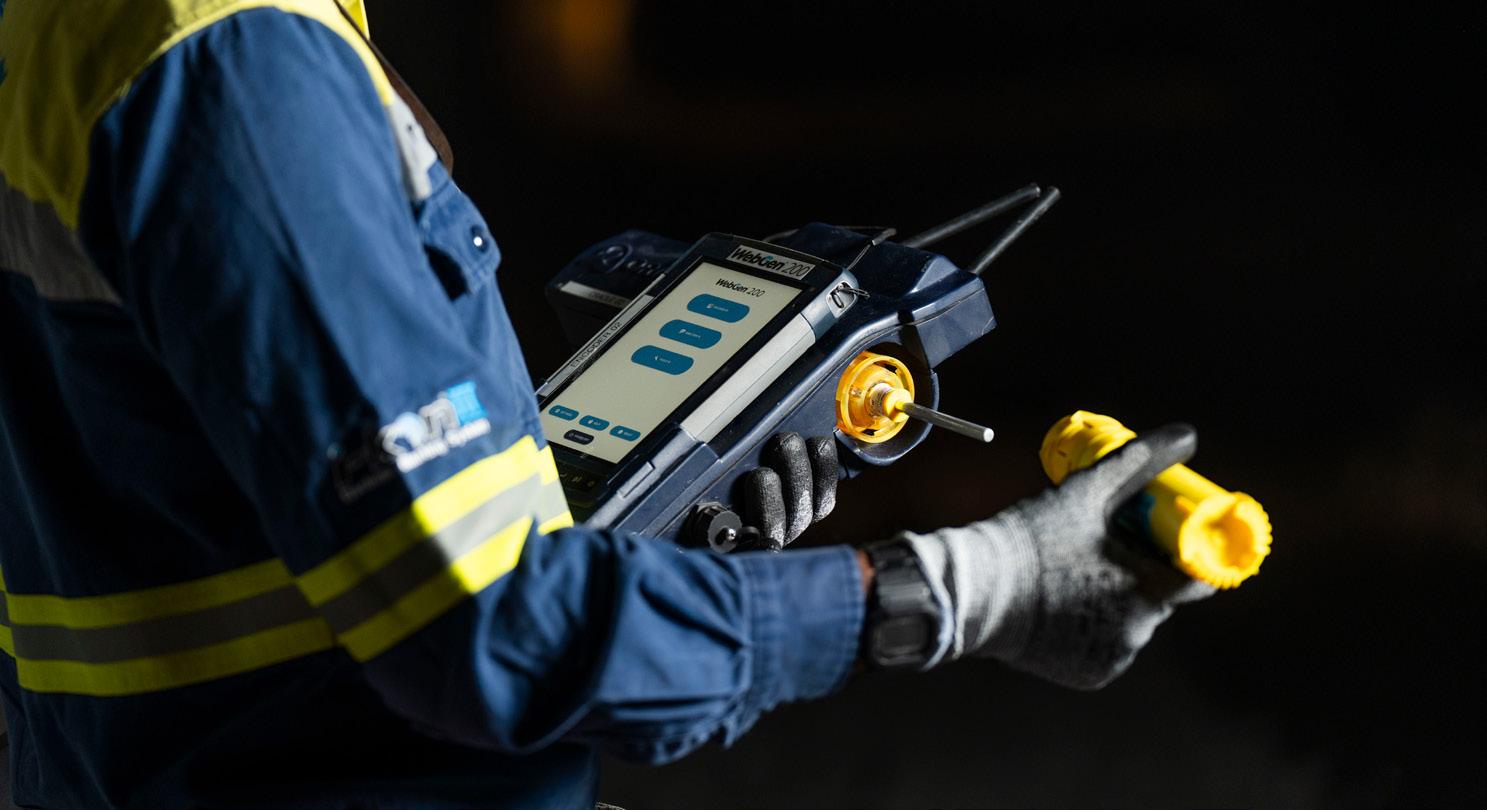
RESOURCES
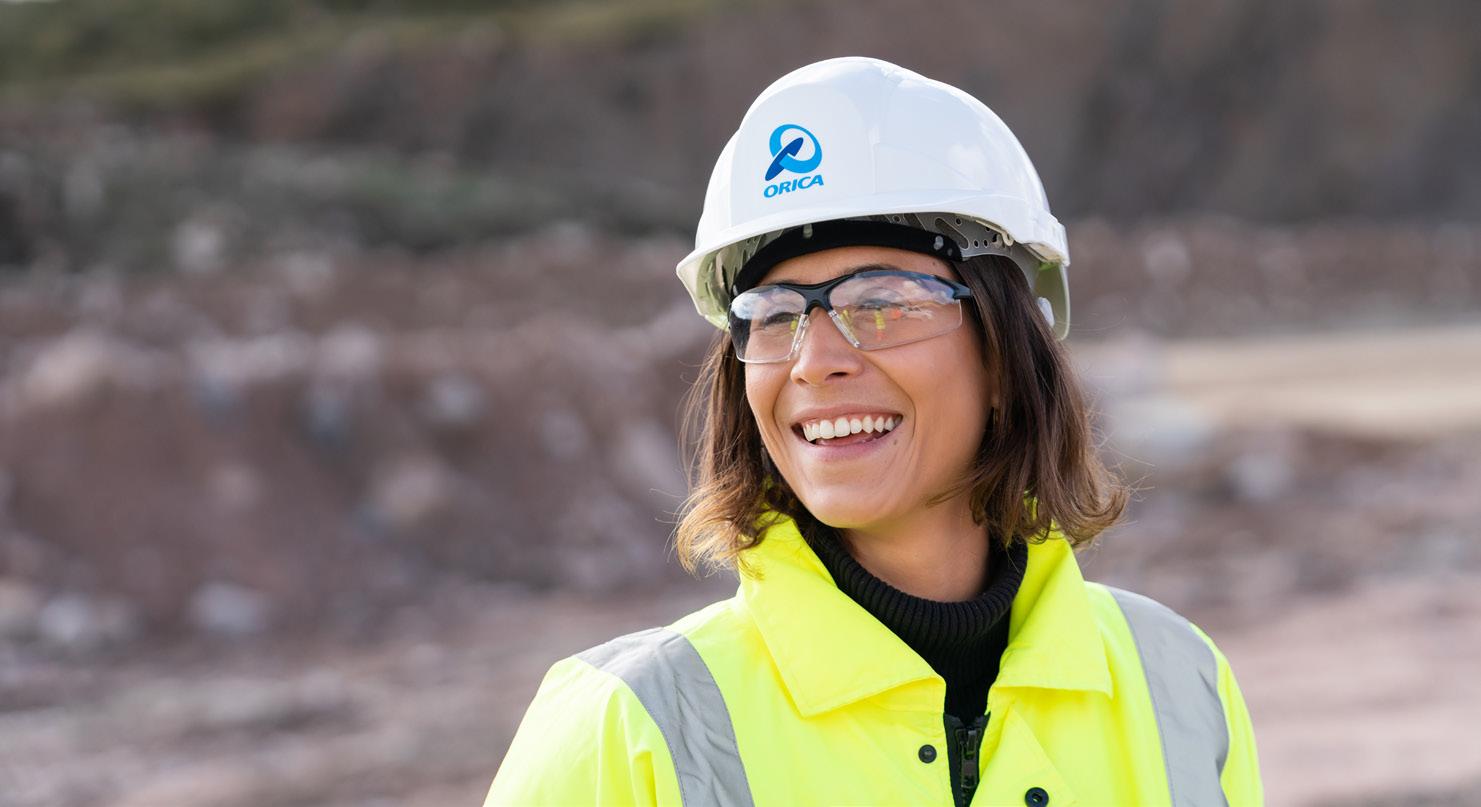
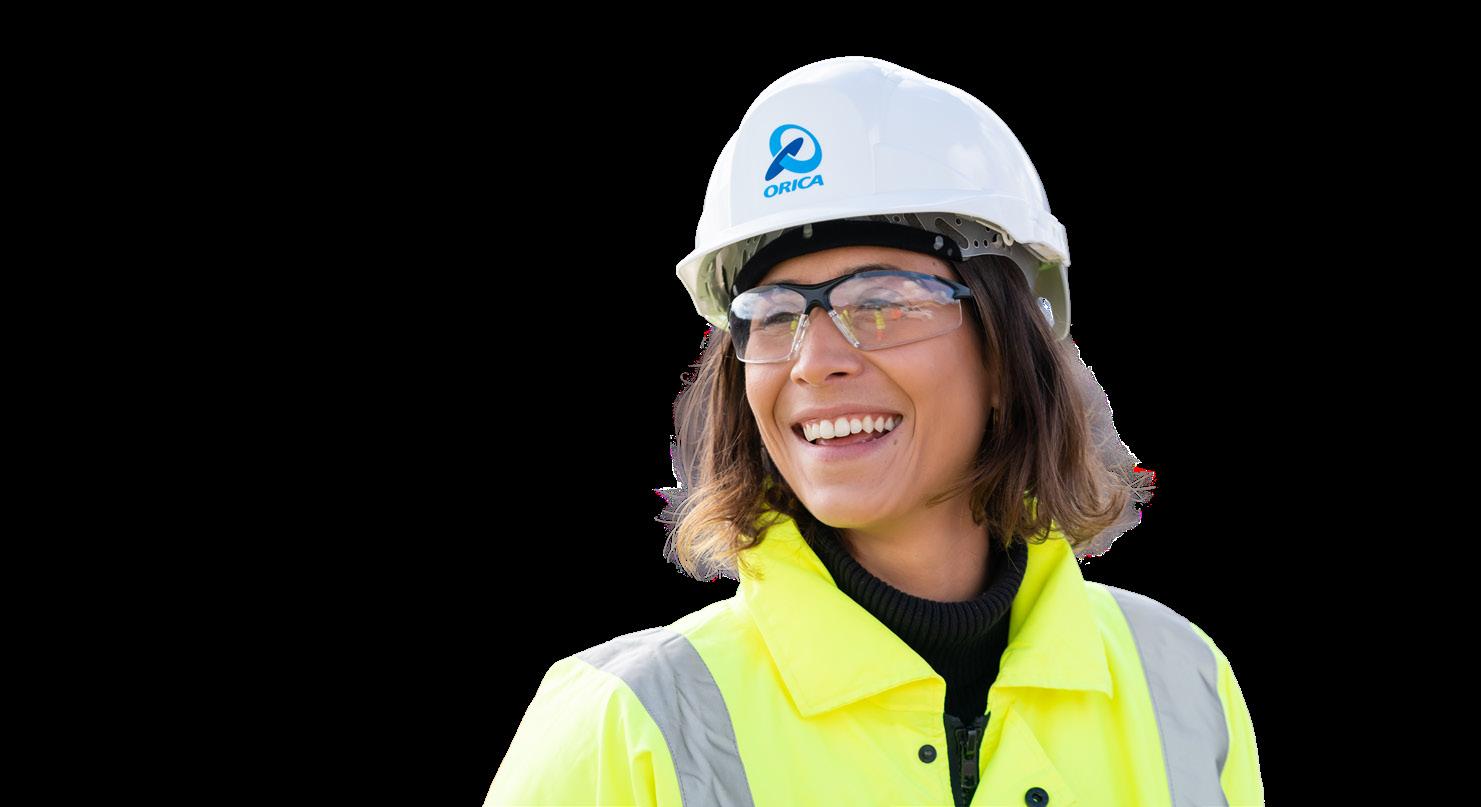
Dyestuffs Corporation to form Imperial Chemical Industries Plc (ICI Plc).
In 1928, Imperial Chemical Industries of Australia and New Zealand (ICI ANZ) was incorporated to acquire and coordinate the Australasian interests of ICI Plc, later becoming ICI Australia in 1971.
When ICI Plc divested its major shareholding in ICI Australia in 1997, a new independent Australasian company was formed, known since February 1998 as Orica.
The acquisition of ICI Plc’s global explosives interests began Orica’s transformation into a global business,
one that has maintained its proud traditions of leadership, innovation, quality, and safety.
Orica has also grown to become one of the leading publicly-owned companies listed on the Australian Stock Exchange (ASX) over the course of 150 years.
Throughout 2024, the business recognised its landmark anniversary together with its people, partners, customers, and communities globally whilst taking the opportunity to reflect on its proud history and look towards the bright future of this iconic organisation.
A DYNAMIC AND DIVERSE REGION
Today, Orica employs a community of more than 12,500 engineers, scientists, technologists, operators, business specialists, and on-site crew around the world, supporting customers in surface and underground mines, quarries, construction, and oil and gas operations.
The business operates in over 100 countries worldwide, including numerous sites across the EMEA region, an extensive area that is incredibly dynamic and diverse with
unique cultures and a wide range of mining commodities and segments.
The company’s commitment to excellence in the EMEA mining sector is unwavering as it is a key region within Orica’s global operations, with a diverse talent pool of approximately 2,000 staff members dedicated to delivering value and the best customer experience.
“We serve around 1,500 customers, ranging from large mining corporations to small and mediumsized enterprises (SMEs) in quarrying, construction, and infrastructure,” outlines Victor Morales, Vice President of EMEA Mining at Orica.
“What makes EMEA particularly inspiring is the opportunity to collaborate with talented individuals from across this vast and multicultural region, combining diversity, innovation, and meaningful contributions to the mining industry’s future.”
Orica’s solutions extend beyond
blasting and integrate seamlessly into the entire value chain, from geological exploration and blast design to ore processing and addressing geotechnical challenges.
This comprehensive approach enables the company to support mining and infrastructure projects with innovative technologies and tailored services that drive efficiency and sustainability.
“Our talented teams thrive in challenging environments, developing and implementing unique solutions that address the entire value chain,” Morales acclaims.
Equally important is Orica’s dedication to creating value not only for customers, but also for the communities where it operates.
This holistic approach, powered by local expertise and cuttingedge technologies, reinforces the company’s position in EMEA as a global leader in mining and infrastructure solutions.
SUSTAINABLE OPERATIONS
Sustainability continues to be a core focus of the industry as organisations work to decarbonise their operations and supply chains.
Areas such as Africa, Central Asia, the Middle East, and Southern and Eastern Europe are growing fast and rapidly evolving to play a pivotal role in supporting the global energy transition.
Demand for copper, nickel, and other future-facing commodities remains strong as the energy transition gains momentum. However, with the push towards a lower-carbon economy, there is expected to be a decline in thermal coal, which is crucial for meeting the energy needs of developing countries.
Sustainability is a key strategic component and integral to operations in EMEA and globally at Orica, whose purpose is to sustainably mobilise the earth’s resources and ambition is to achieve net zero emissions by 2050.
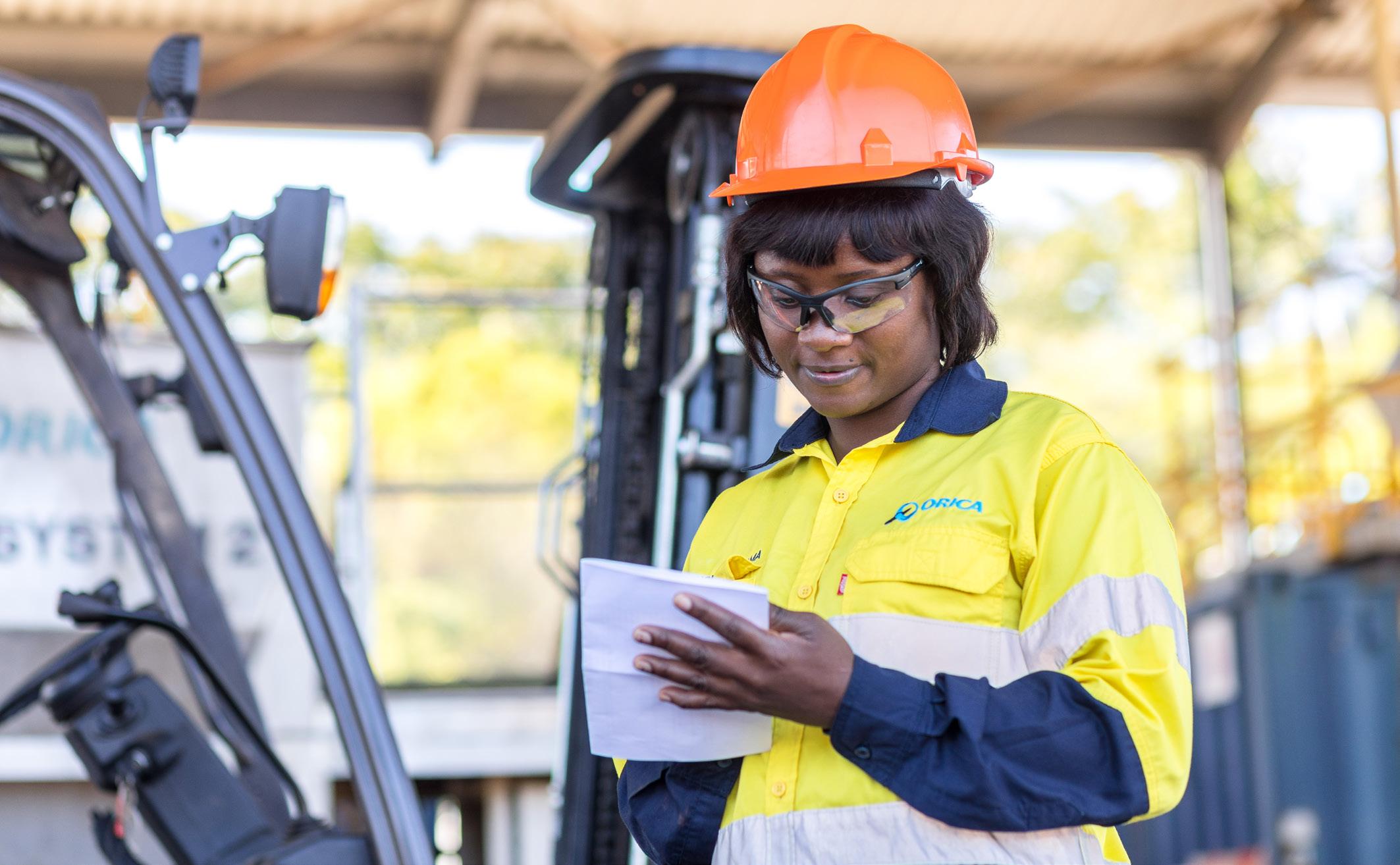

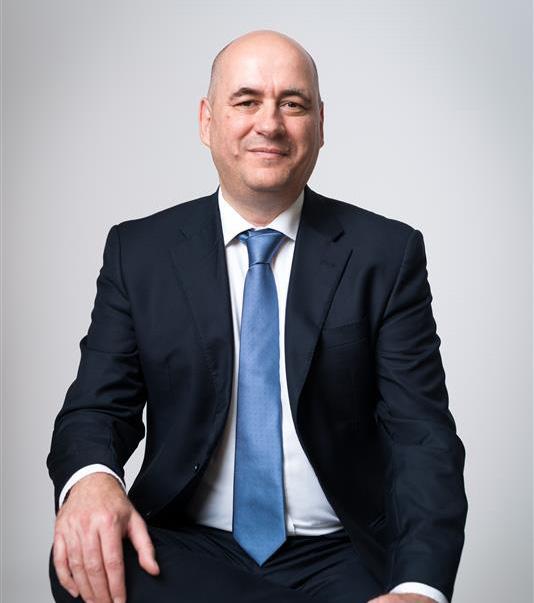
“My interest in mining grew as I recognised its critical role in supporting global sustainability, providing essential raw materials for the energy transition and critical minerals that are vital for modern society,” reflects Morales.
The company delivers smart, safe, and sustainable solutions for customers working in complex operating environments, playing its part in addressing climate challenges and supporting local communities.
Championing a more environmentally-friendly industry, responsibly managing its impact on society, and supporting the fair transition to a net zero economy is fundamental to Orica’s decisionmaking and the way it runs the business.
Indeed, sustainability is embedded in the company’s policies, business strategy, and practices as it pursues new opportunities, delivers on its commitments, and improves its performance.
MINING OUTLOOK: HOW HAVE ORICA’S LONG-STANDING SUPPLIER RELATIONSHIPS HELPED TO NAVIGATE INDUSTRY DISRUPTION?
Victor Morales, Vice President of EMEA Mining:
“In response to recent global geopolitical challenges, Orica has focused on building robust and resilient supply chains to remain a reliable partner for our customers.
“We have successfully navigated disruptions in the supply of critical raw materials, ensuring our operations continue seamlessly across EMEA and globally. Our strong relationships with key suppliers, freight forwarders, and logistics partners play a crucial role in maintaining the reliability of our services.
“This resilience, combined with our strategic partnerships, is a key differentiator that allows us to deliver consistent value to our customers, even in challenging environments.”
“ORICA IS SET APART BY ITS PEOPLE, COMMITMENT TO INNOVATION, AND ADVANCED TECHNOLOGIES, ALL FOCUSED ON DELIVERING EXCEPTIONAL VALUE TO CUSTOMERS AND STAKEHOLDERS”
– VICTOR MORALES, VICE PRESIDENT OF EMEA MINING, ORICA
Guided by its sustainability strategy, which is informed by the UN’s Sustainable Development Goals (SDGs), Orica collaborates with customers and other stakeholders to find solutions to the industry’s biggest challenges and move together towards a lower-carbon future.
Along with proactively engaging with a diverse range of stakeholders in EMEA and around the world, Orica undertakes periodic materiality assessments to understand the topics that matter most to them and inform its strategy, public sustainability targets, and external reporting.
The company is focused on mobilising the materials, metals, and minerals required to help the global economy grow and transition to net zero emissions, advancing technology and innovation across the value chain and accelerating its decarbonisation commitments.
ESSENTIAL MATERIALS
Orica is committed to securing the supply of critical raw materials for the mining industry, with the safe and reliable supply of ammonium nitrate (AN) another key component of its offering.
ORICA EMEA EUROPE & MIDDLE EAST
“As one of the world’s leading producers of AN for technical use, we operate five production facilities worldwide,” confirms Morales.
“We are also one of the main buyers of AN for technical use, especially for our operations in EMEA and Latin America, where we have long-term agreements to secure steady supply to our operations.”
In EMEA, Orica recently partnered with Fertiberia to execute the first blast using low-carbon technical ammonium nitrate (TAN) in June 2024 at the Canteras de Santullán quarry in Spain.
This innovative product, made with renewable hydrogen, marks a milestone in reducing the carbon footprint of blasting and mining operations, providing a more sustainable solution compared to conventional TAN.
The blast signifies a further step
towards the decarbonisation of mining, a crucial sector for the energy transition due to its role in extracting copper and other essential industrial minerals, as it marked the first industrial-scale use of a sustainable, low-carbon explosive product.
Alongside AN, Orica also invests in the production of various essential materials such as sodium cyanide and other critical resources.
“This ongoing investment strategy ensures we can meet the growing demands of our customers whilst supporting the industry’s long-term sustainability,” Morales emphasises.
INNOVATIVE TECHNOLOGIES
The new mining and infrastructure projects driving the EMEA region evidently have a great focus on sustainability and efficiency, supported by the introduction of forward-thinking technologies.

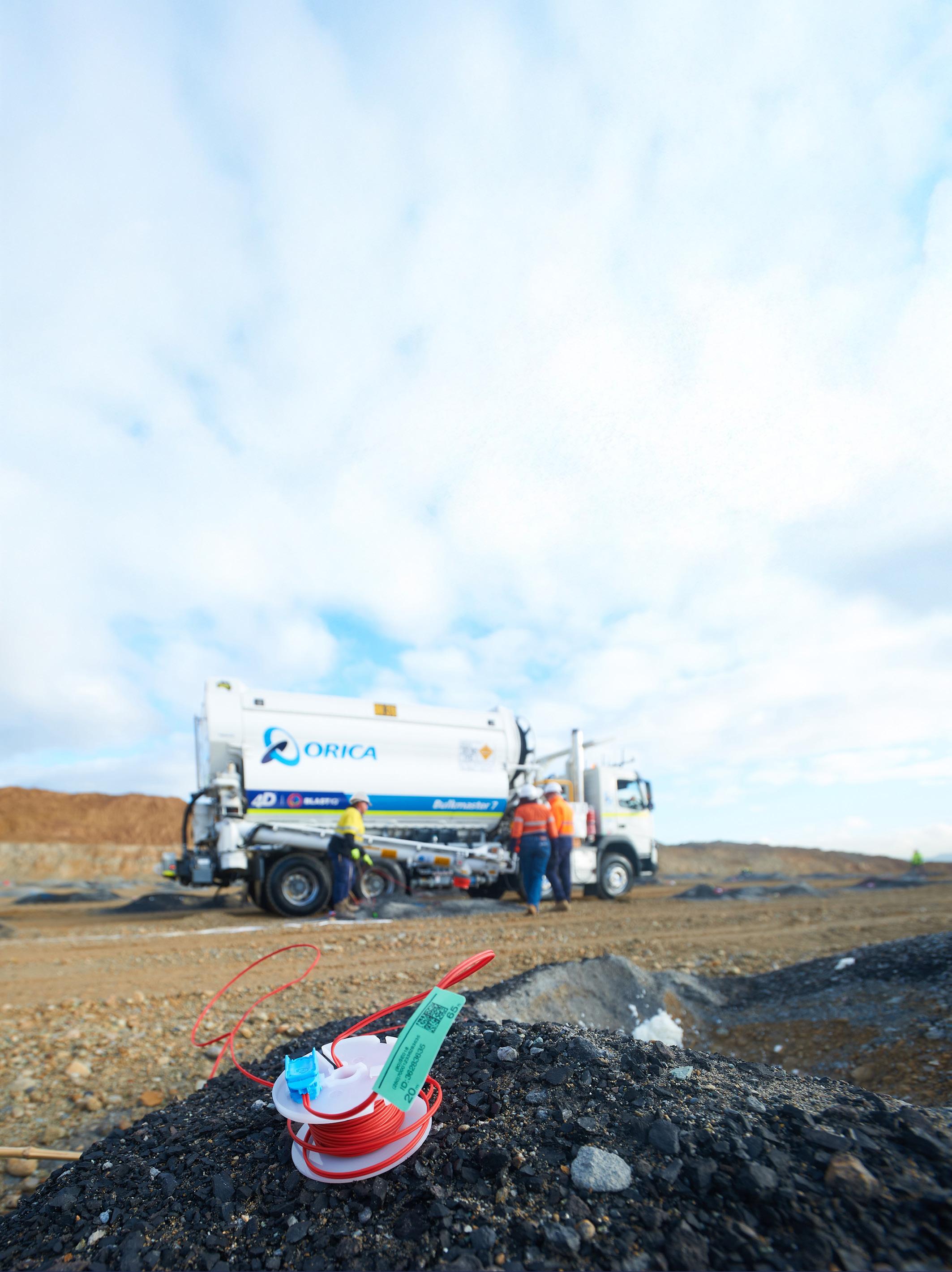
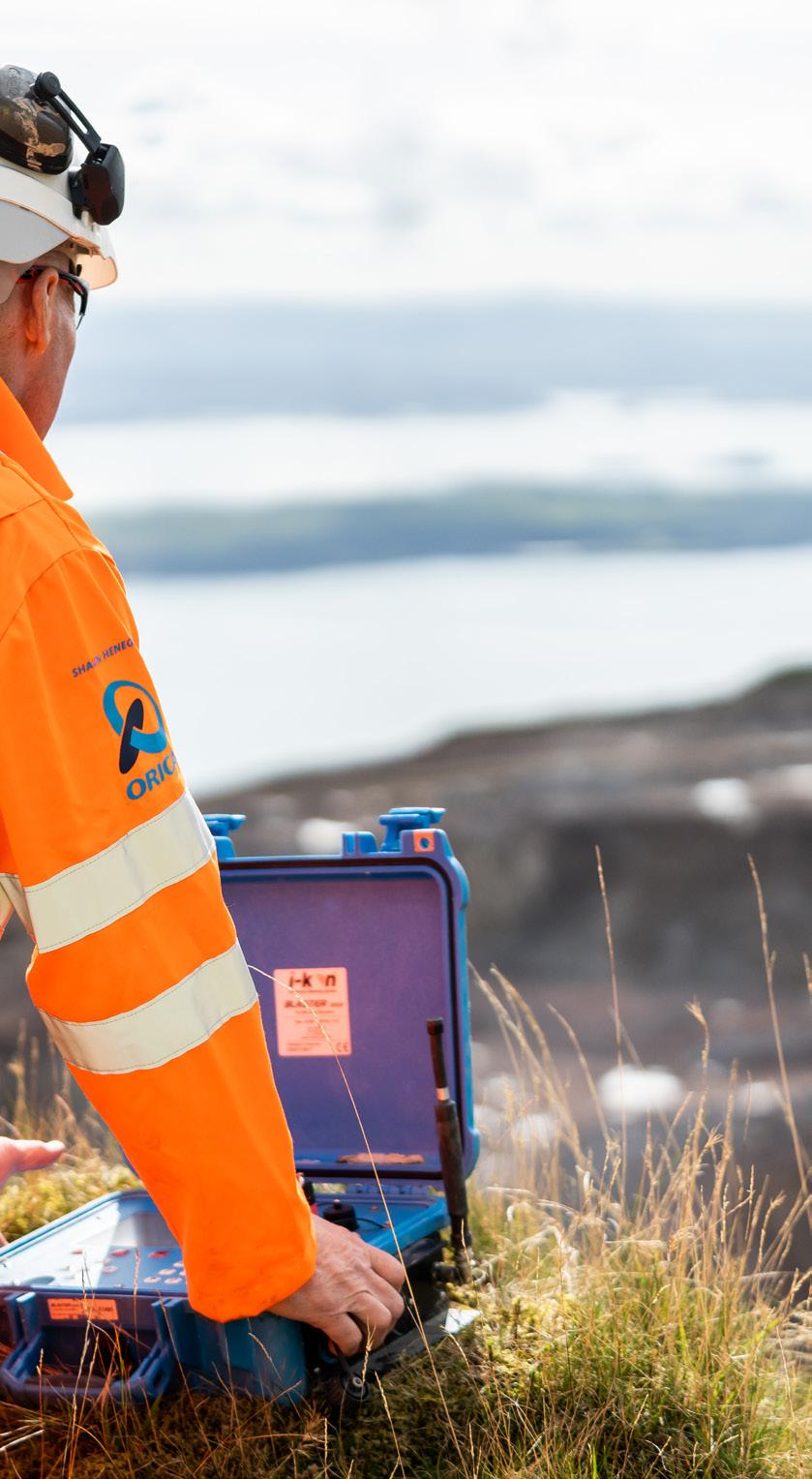
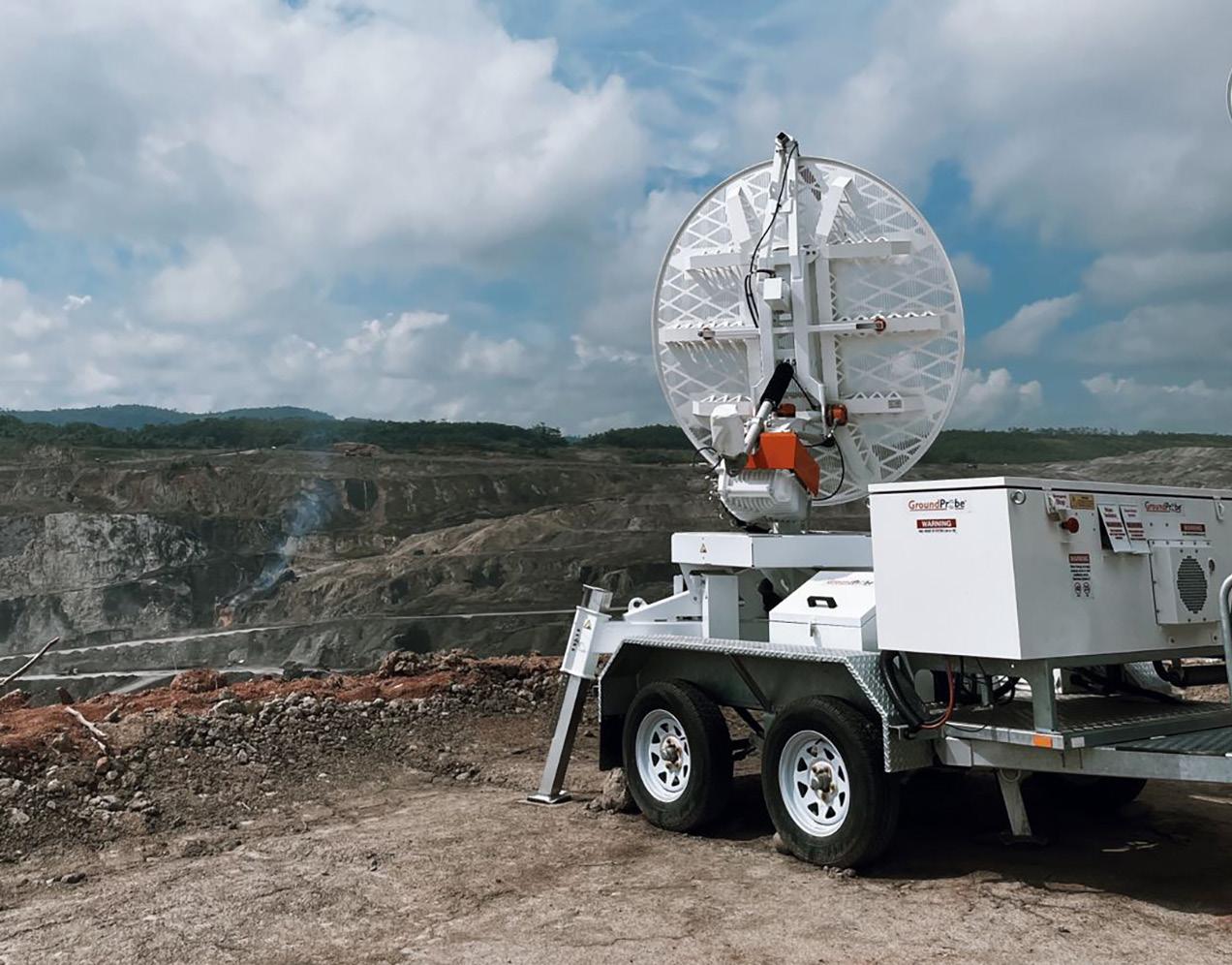
“We continue to innovate with groundbreaking solutions designed to enhance efficiency, safety, and sustainability in mining operations,” Morales states.
Orica has long been at the forefront of innovation in mining and infrastructure, helping to shape the industry through leading digital and automated technologies to create safer and more productive outcomes for customers.
Continuous innovation led by talented people and fuelled by collaboration with customers and industry and research partners to solve shared challenges has been at the heart of the company’s success over the past 150 years.
Innovation at Orica is defined by its pioneering spirit and key to addressing the significant
“WHAT MAKES EMEA PARTICULARLY INSPIRING IS THE OPPORTUNITY TO COLLABORATE WITH TALENTED INDIVIDUALS FROM ACROSS THIS VAST AND MULTICULTURAL REGION, COMBINING DIVERSITY, INNOVATION, AND MEANINGFUL CONTRIBUTIONS TO THE MINING INDUSTRY’S FUTURE”
– VICTOR MORALES, VICE PRESIDENT OF EMEA MINING, ORICA
global challenges faced by the mining industry, including sustainability, safety, efficiency, resource depletion, and social responsibility.
Finding ways to address these is therefore essential for the sustainable growth and development of the industry.
Committed to continuous
technological investment, the company’s vision is to transform how drilling and blasting are used to unlock mining value.
“Our innovations reflect Orica’s dedication to providing cutting-edge, value-driven solutions for the evolving needs of the mining industry,” prides Morales.
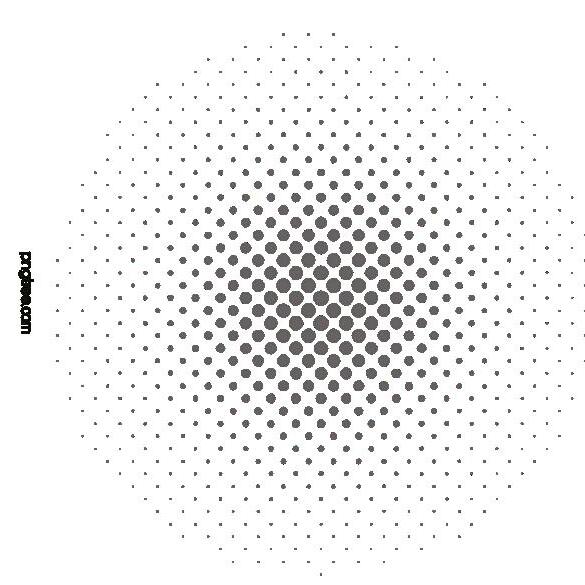
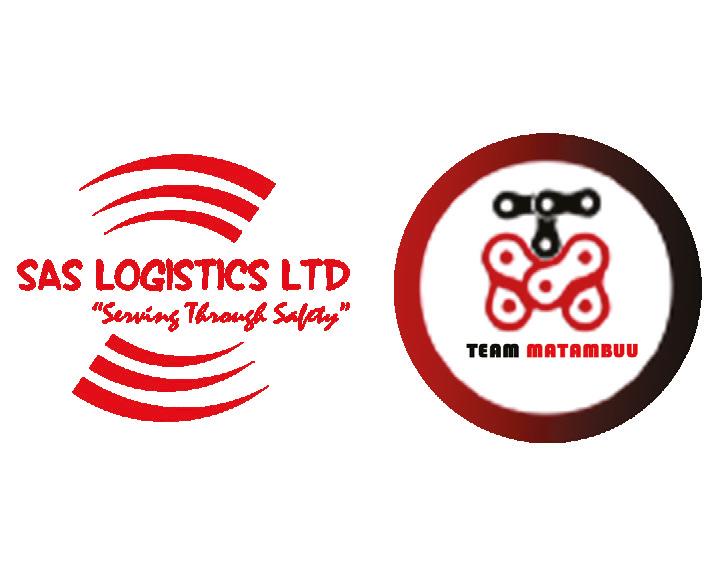
SAS LOGISTICS SERVING THROUGH SAFETY
Founded in 2006, SAS Logistics has become one of Tanzania’s leading logistics and transport companies, o ering innovative and reliable solutions. Initially, the company started with only 9 trucks, branching out from parent company, S.A. Said & Co. Ltd, which was established in the 1970s by the late Seif Abdallah Said. The company’s name, SAS Logistics, honours his legacy in the transport industry.
SAS Logistics’ success story is rooted in the vision of its CEO, Mr. Salim Seif Elbusaidy, the eldest son of Seif Abdallah Said. With wisdom and a brilliant strategy, Mr. Elbusaidy saw the opportunity to build a sustainable company that would o er top-tier logistics and transport services. Under his leadership, SAS Logistics has grown from a small operation to one of the most respected logistics providers in the country, now owning a eet of 250 trucks with capacities ranging from 3 to 30 tonnes.
At the core of SAS Logistics is its guiding principle, ‘Serving Through Safety ’ The company prioritises safety in all aspects of its operations, from the transportation of goods to the maintenance of its eet. Whether transporting dangerous goods such as ammonium nitrate or providing general cargo transport, SAS Logistics ensures that all operations are executed with the highest safety standards. This commitment is also re ected in the continuous training of its drivers and technicians to adhere to safety protocols.
To meet the country’s growing
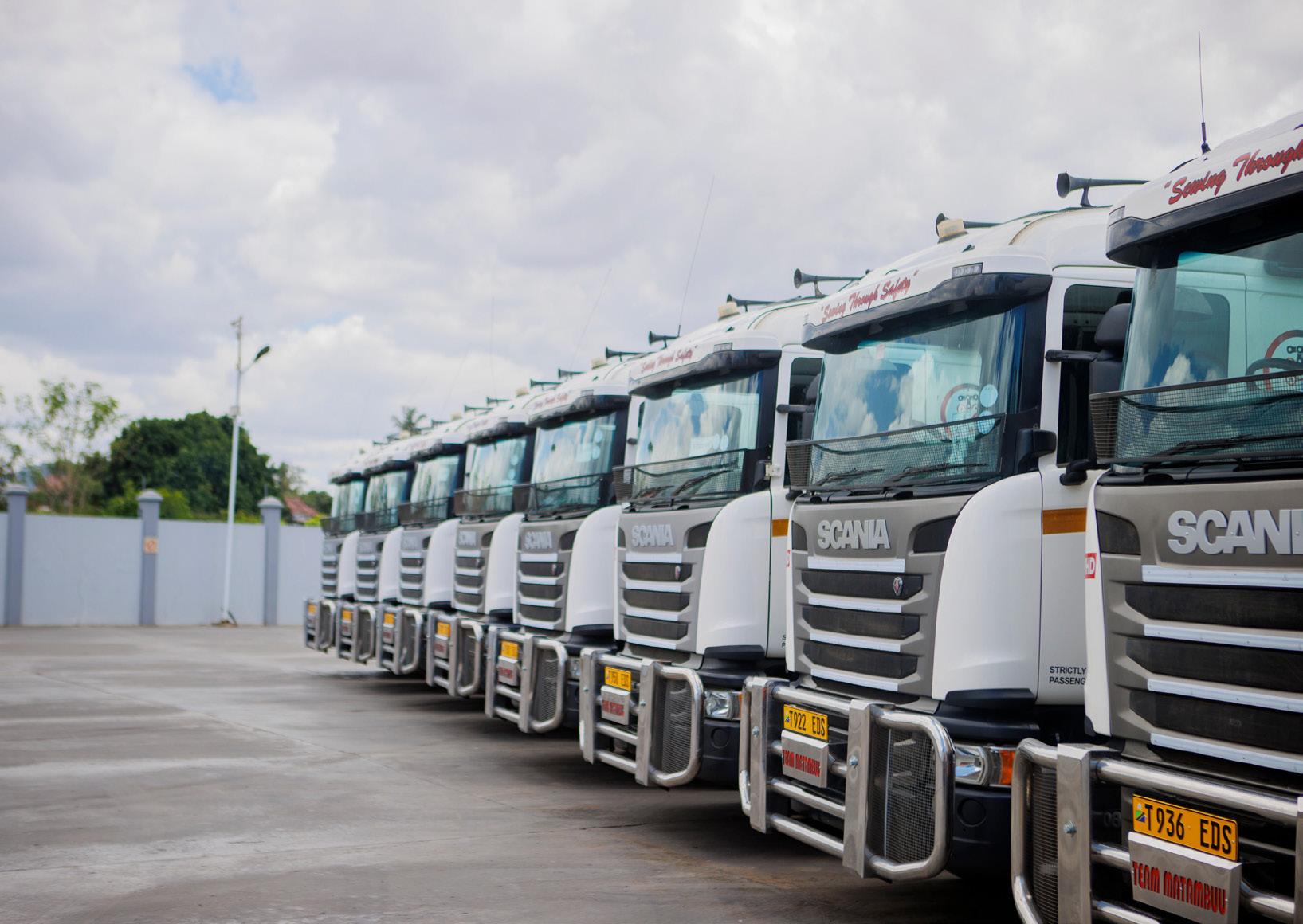
demand for logistics services, SAS Logistics has strategically positioned its warehouse facilities in key locations across Tanzania. In Kahama, located near some of the country’s richest mining areas, the warehouse serves as a critical hub for materials and equipment used in the mining sector. This location allows the company to efficiently support the mining industry by providing timely and secure storage and transportation solutions.
Tanga, another key port city, is home to a second SAS Logistics warehouse. Situated close to important trade routes, the Tanga warehouse supports both import and export activities, further enhancing the company’s ability to
o er exible logistics solutions for various industries, including mining and manufacturing.
These strategically located warehouses allow SAS Logistics to o er comprehensive logistics solutions tailored to the needs of its clients. Whether it’s transporting goods to and from the mining regions or facilitating the smooth ow of trade through the ports, the company’s logistics network plays a crucial role in supporting Tanzania’s economy. Over the years, SAS Logistics has expanded its operations beyond transport to o er a range of services, including customs clearance, freight forwarding, and the specialised handling of dangerous goods. The company’s growth has been driven by its
customer satisfaction and its ability to adapt to the changing needs of the logistics industry. SAS Logistics continues to invest in modern technology and eet management systems to enhance e ciency and maintain the highest safety standards.
SAS Logistics is also committed to sustainability. The company imple ments green logistics practices to reduce its environmental impact, such as optimising routes to reduce fuel consumption and adopting eco-friendly packaging materials. These e orts align with global sustainability goals whilst maintaining operational e ciency.
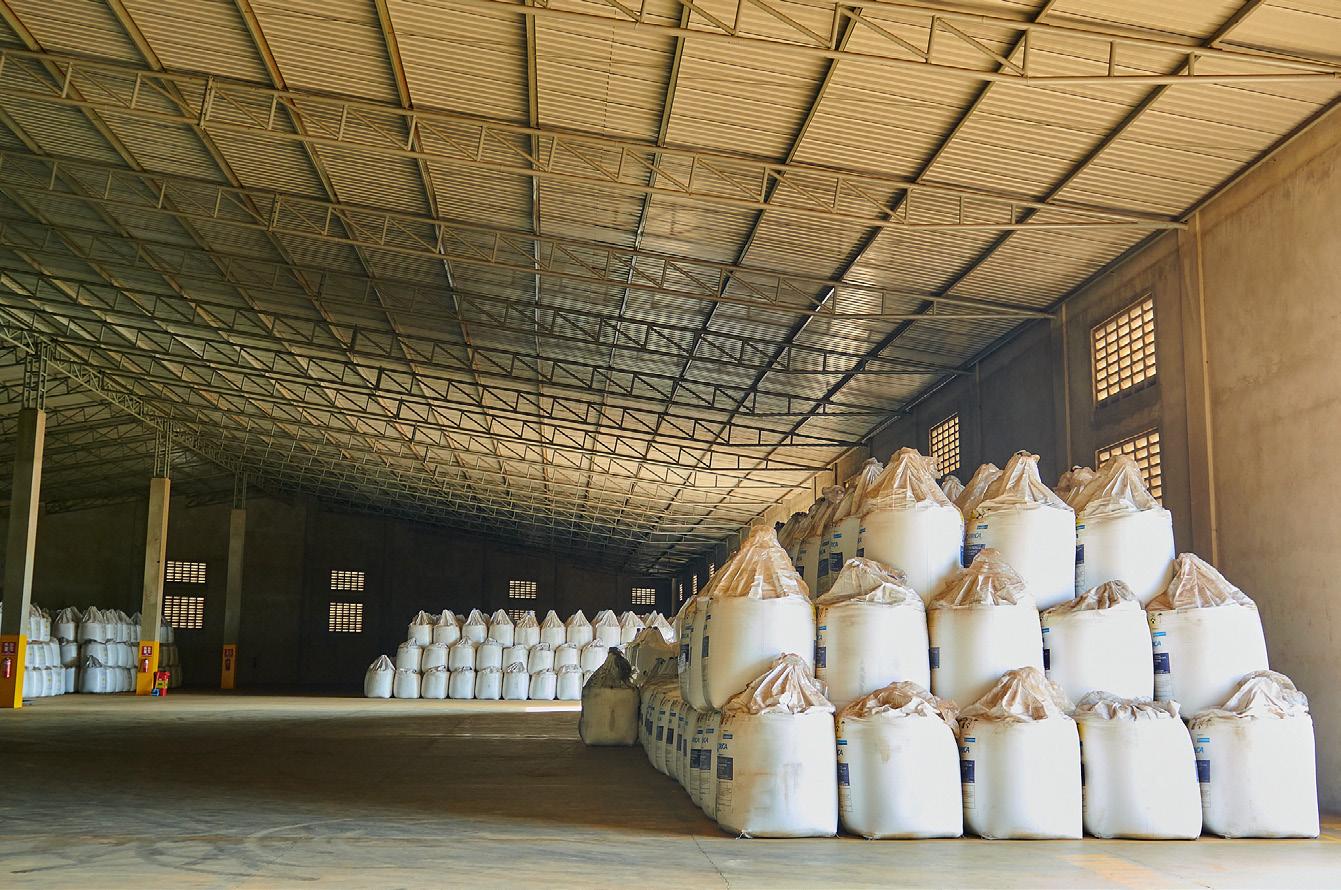
In addition to its environmental initiatives, SAS Logistics embraces innovation by integrating advanced eet management technologies and real-time tracking systems. This enables the company to provide clients with up-to-date information about their shipments, ensuring transparency and improving the overall customer experience.
The company’s dedication to safety extends to its handling of hazardous materials, such as ammonium nitrate, where stringent safety protocols and industry regulations are strictly followed. SAS Logistics’ fleet is equipped with the latest safety features, and its drivers are welltrained to manage hazardous goods safely.
From industry, a veteranled specialize transport,
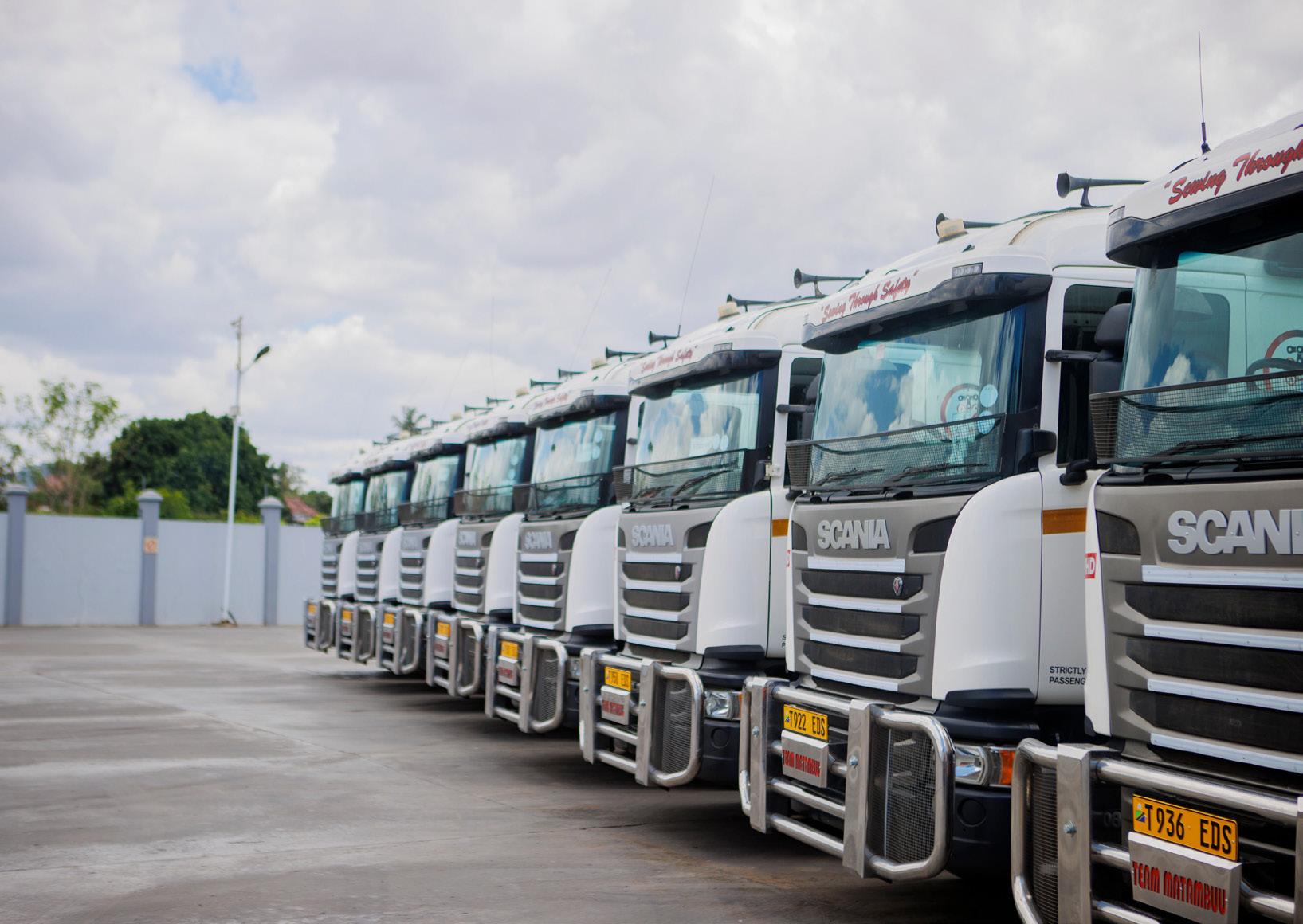
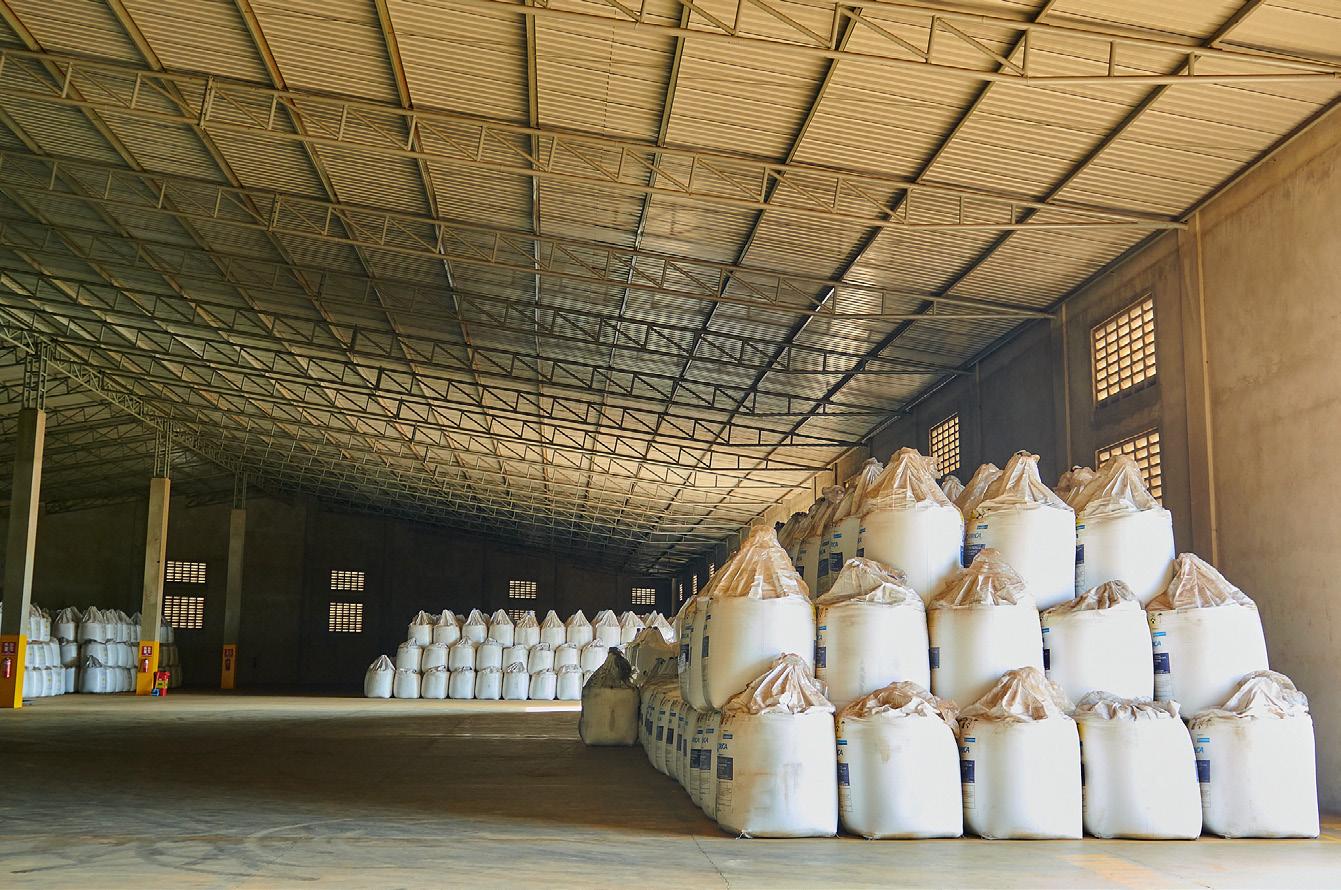
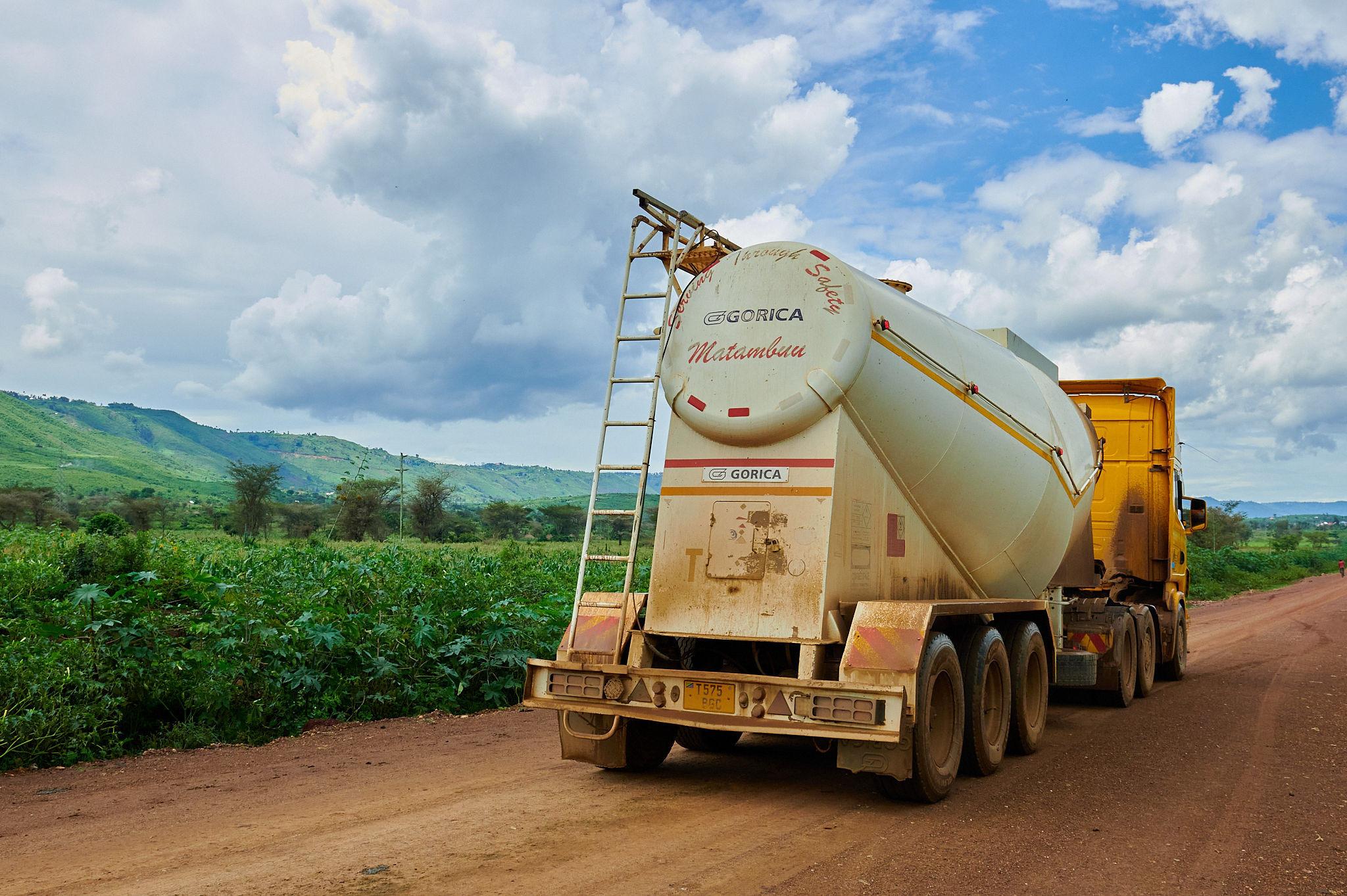

Your Trusted Partner for Safe and Reliable Transport Solutions
its roots in 2006, SAS Logistics has become a leader in Tanzania’s logistics industry, setting the standard for safe, efficient, and customer-centric services. With veteranled team boasting over 65 years of combined experience, we specialize in handling complex logistics needs, including dangerous goods transport, freight forwarding, and customized warehousing solutions. Why Partner SAS Logistics?
Industry Expertise: Decades of experience across diverse industries, including mining and energy, to meet unique logistical needs with precision. End-to-End Services: Comprehensive solutions from road, air, and sea freight to specialized warehousing and customs clearance, o ering seamless support every step of the way.
Safety Commitment: Certi ed to handle hazardous materials with rigorous safety protocols, ensuring secure and compliant transportation.
Strategic Locations: Facilities in Dar es Salaam, Kahama, and Tanga for optimal regional market access, streamlining logistics throughout East Africa.
Competitive Pricing: Delivering high-quality service at competitive rates to maximize value for your logistics investment.
Timely Delivery: Committed to on-time delivery, keeping your supply chain moving e ciently and reliably.
heart of everything we do. The company has built a strong reputation for reliability and exibility, o ering customised logistics solutions for businesses of all sizes. Whether working with multinational corporations or smaller local enterprises, SAS Logistics takes the time to understand the unique needs of each client and tailors its services to exceed their expectations. With a strong presence at key border points in Tanzania and neighbouring countries like Zambia, SAS Logistics facilitates smooth cross-border transportation and ensures compliance with international shipping regulations. This expertise in customs procedures and regulations helps eliminate delays and ensures e cient delivery across borders. SAS Logistics’ commitment to safety, sustainability, and customer service has earned it a reputation as a reliable partner for businesses across Tanzania. As the company continues to grow, it remains focused on providing innovative, cost-e ective logistics solutions that meet the evolving needs of the industry. Guided by the legacy of Seif Abdallah Said and the leadership of Mr. Salim Seif Elbusaidy, SAS Logistics is wellpositioned for a future of continued success. With a eet of modern vehicles, cutting-edge technology, and strategically located facilities, SAS Logistics is ready to tackle the logistics challenges of tomorrow whilst staying true to its commitment to serving through safety.
Join the many satisfied clients who rely on us for secure and timely delivery. Discover the SAS Logistics advantage—where your business goals drive our commitment to excellence.
Contact Us: +255 767 841 840 Email: info@sas-logistics.co.tz Visit Our Website: sas-logistics.co.tz
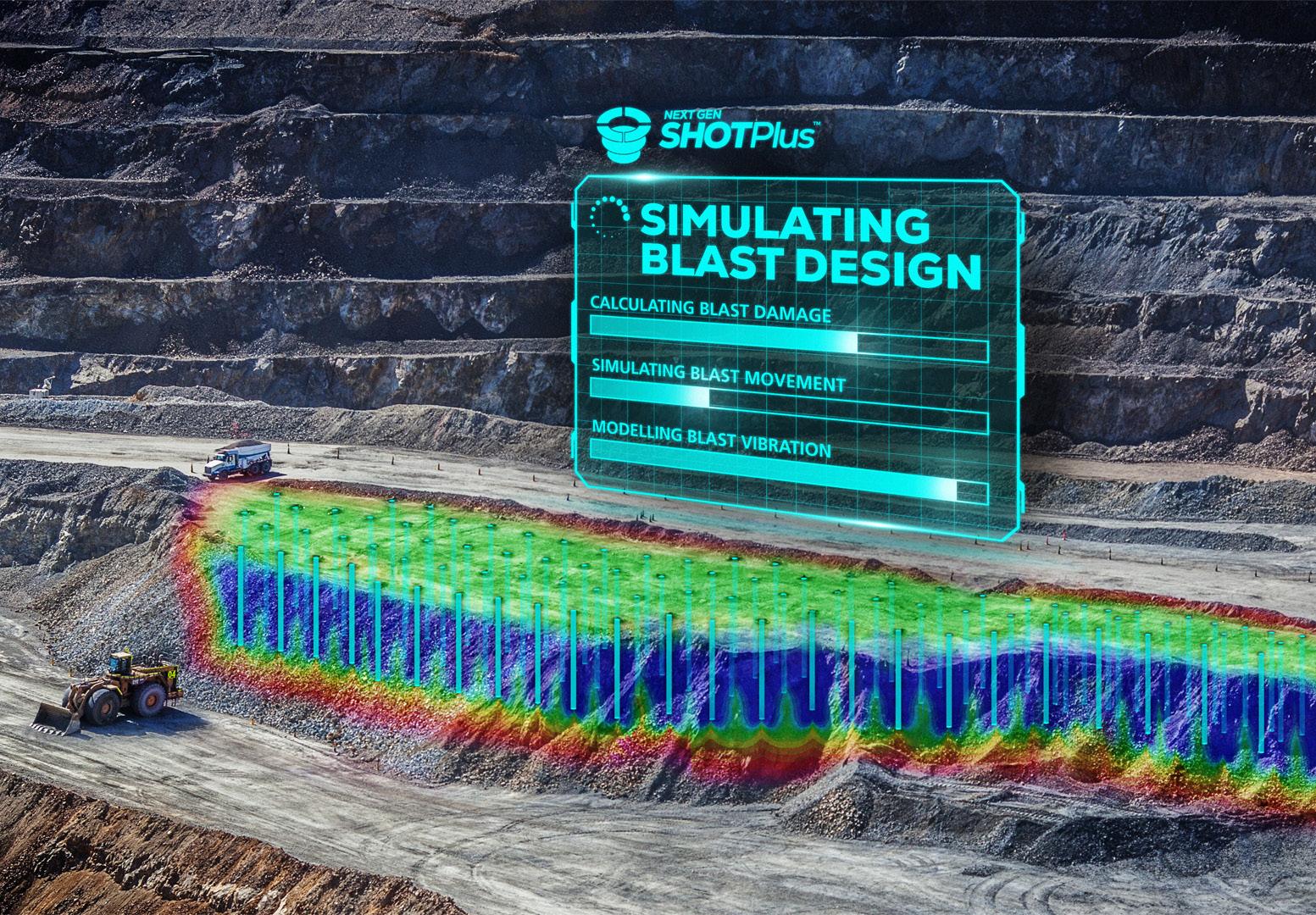
In EMEA, the company has technology centres located in Gyttorp, Sweden and Troisdorf, Germany that specialise in nonelectric (NE) initiation and electronic blasting systems (EBS), respectively.
These two regional sites complement Orica’s global technology centres in Australia, the US, Canada, and Singapore, as well as its Centre for Innovation and Collaboration in Chile.
CIRCULAR SOLUTIONS
Orica is in a unique position to leverage its expertise in technology to create solutions that deliver positive socioeconomic and environmental contributions to customers and
ORICA EMEA LOCATIONS
EUROPE – Belgium, Bulgaria, Estonia, Finland, Germany, Norway, Portugal, Spain, Sweden, UK
MIDDLE EAST – United Arab Emirates (UAE)
AFRICA – Democratic Republic of the Congo (DRC), Ghana, Mozambique, Namibia, Senegal, South Africa, Tanzania, Zambia
communities around the world through its business activities.
For example, the company is reducing environmental footprints by offering more sustainable solutions such as Exel™ Neo, which was launched in September 2023 and represents another step towards the company’s purpose.
The world’s first series of leadfree NE detonators, Exel™ Neo uses unique, proven non-primary explosives detonator (NPED) technology for the safe and reliable initiation of explosives.
“Exel™ Neo offers reliable and robust lead-free detonators for operations in challenging conditions,” Morales tells us.
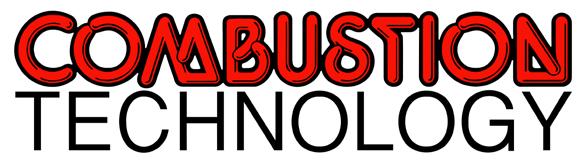
The Preferred Partner for Containerised Hot Water Boiler Systems in Africa’s Mining Sector
For over a decade, Combustion Technology has been the trusted supplier for Orica Africa, delivering cutting-edge mobile Steam and Water Heating Systems designed specifically for the manufacturing of explosives and blasting systems. This long-standing partnership highlights Combustion Technology’s expertise in providing reliable, energy-efficient, and innovative solutions tailored to meet the unique demands of Africa’s dynamic mining sector.
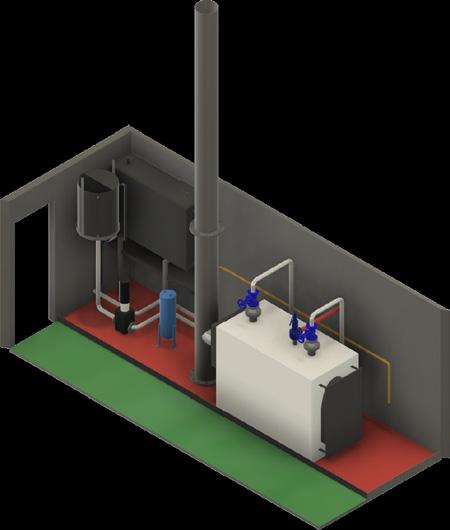
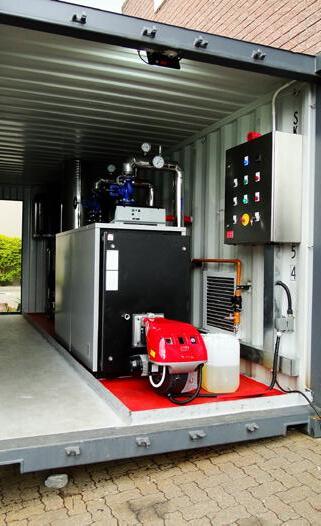
Geographical Reach and Legacy
With offices in Cape Town and Johannesburg, as well as an extensive dealer network, Combustion Technology services clients across Africa and the Indian Ocean islands. With over 38 years of experience, the company’s world-class products and technical expertise have driven its consistent growth and leadership in the mining sector.
Partnering for a Sustainable Future
The partnership with Orica Africa exemplifies Combustion Technology’s commitment to sustainability and innovation. By providing state-of-theart systems that enable efficient on-site manufacturing of explosives, the company helps mining clients mobilise the earth’s resources responsibly.
Why Choose Combustion Technology?
• Proven Expertise: Decades of experience in the heating and combustion industry.
• Custom Solutions: Tailored systems designed for rugged mining environments.
• Comprehensive Support: A dedicated team offering 24/7 service.
• Global Brands: Exclusive partnerships with world-class manufacturers.
Energy-Efficient Solutions for Challenging Environments

Combustion Technology takes pride in producing containerised hot water boiler systems that are not only reliable but also optimised for quick and seamless on-site deployment. Every system is designed to be “plug and play” and pre-tested for hassle-free commissioning. These features are critical for mining operations, where efficiency and uptime are paramount.
The ability to overcome harsh environmental conditions and operate in abrasive site settings has been central to Combustion Technology’s success. Through continuous innovation and customization, the company ensures its systems meet the highest standards of performance, durability, and sustainability.
Each containerised unit includes:
• A boiler and burner
• Fuel and water tanks
• Electrical panel
• Pump and pipework
This user-friendly Water Treatment System design takes approximately one month to complete and is fully transportable for easy shipment to site locations.
Expert Support and 24/7 Service
A critical factor in Combustion Technology’s success is its dedicated team of engineers and project experts who provide 24/7 support to mining sites across Africa. This hands-on approach guarantees smooth operations and builds long-term client trust.
World-Class Products and Exclusive Partnerships
Combustion Technology proudly represents leading global brands, including:
• Autoflame Combustion Management Systems
• Limpsfield Burners
• Riello Burners
• Unical Boilers
• I.VAR Industry Boilers
• Cannon Bono Energia Industrial Boilers
These premium products form the foundation of Combustion Technology’s solutions, enabling the company to deliver professional service. From pre-sales energy analysis and installations to after-sales service and spare parts support, the company ensures clients receive a professional and seamless experience.
• Geographical Reach: Operations spanning Africa and beyond.
• Effortless Setup: Plug-and-play systems for minimal disruption.
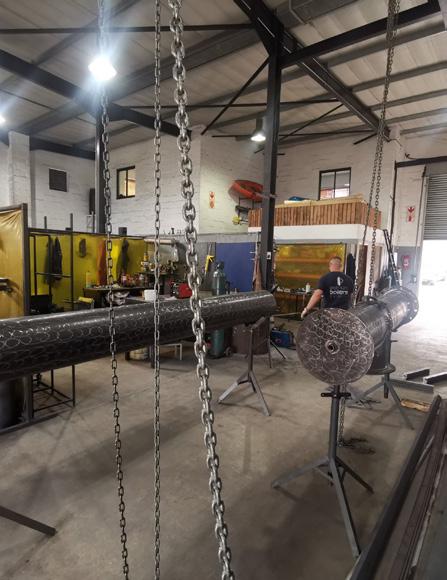
Looking Ahead
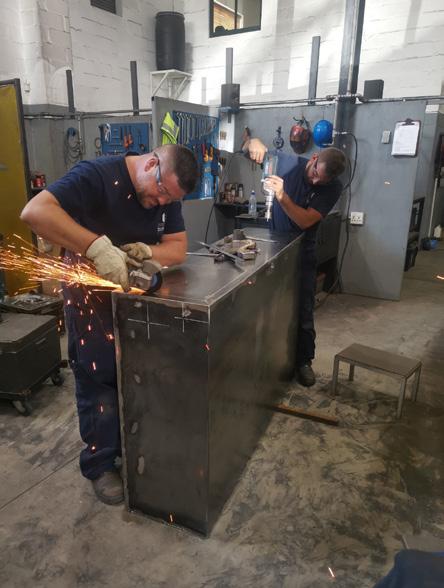
Combustion Technology remains committed to its partnership with Orica Africa, supporting the mining sector with innovative and sustainable solutions. With its proven track record and dedication to client satisfaction, Combustion Technology continues to set the standard for containerised hot water boiler systems across Africa.

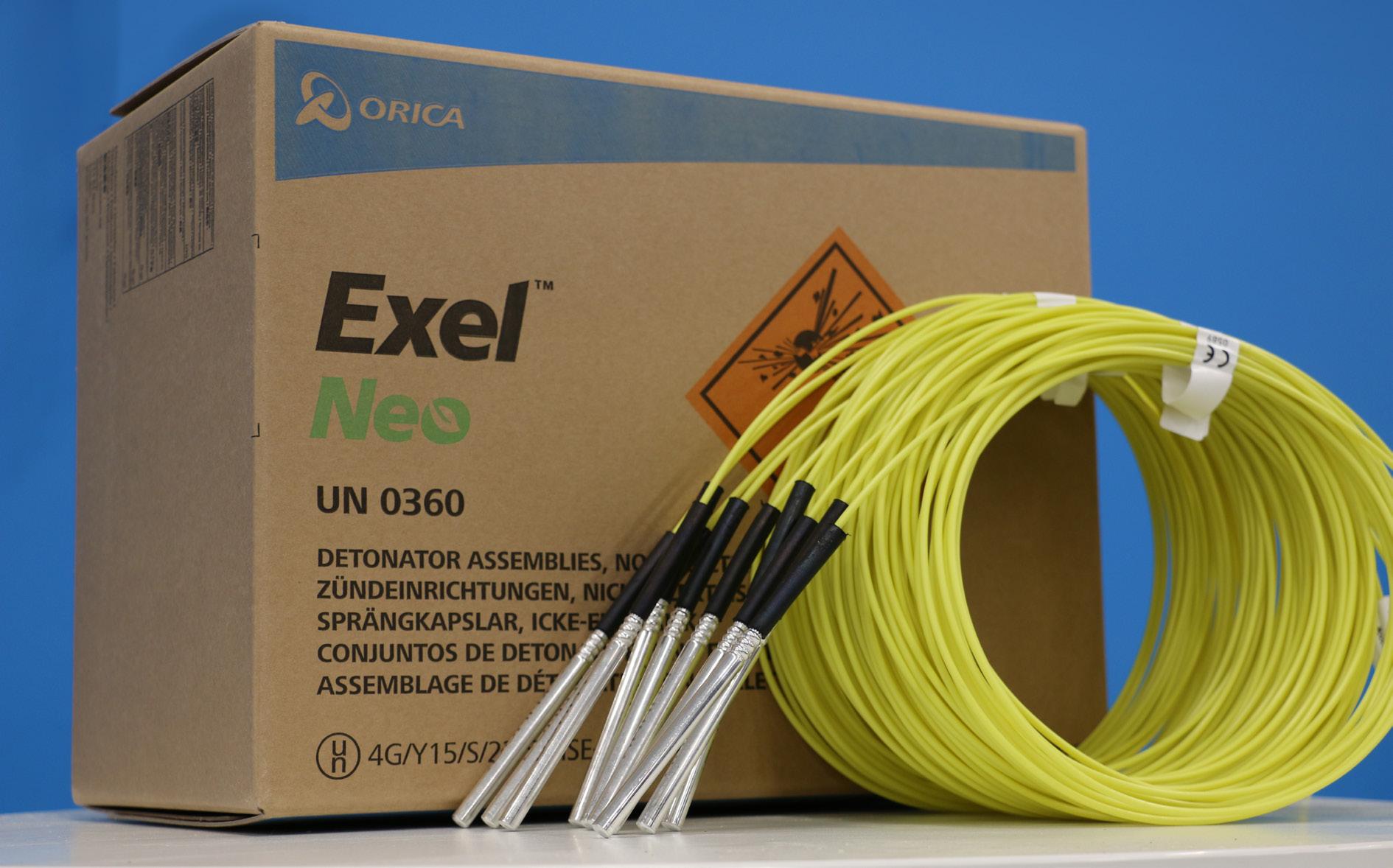
Orica does not use lead or lead components in the manufacturing or production of Exel™ Neo detonators, but rather a safer and more sustainable lead-free formulation in Gyttorp, creating more eco-friendly products whilst maintaining the performance of its premium Exel™ range.
Exel™ Neo detonators are designed for use in civil infrastructure, as well as surface and underground mining operations.
The technology is manufactured close to Orica’s customer base in Europe and is currently available in the EMEA region.
The first Exel™ Neo detonators were shipped from its state-of-theart Swedish production facility in November 2023 to address the need for more sustainable initiation systems in the market.
Orica’s NE manufacturing and
supply network is expanding, with capability and capacity uplifts at a number of sites.
New equipment and processes have solidified multiple export hubs, improving the safety, efficiency, reliability, and security of shipping components to the company’s assembly plants.
AUTOMATED PROCESSING
Along with Exel™ Neo, Orica is also lowering environmental footprints through solutions such as Cyclo™, an automated processing system that enables used oil from heavy machinery to be recycled directly on-site and transformed into raw materials.
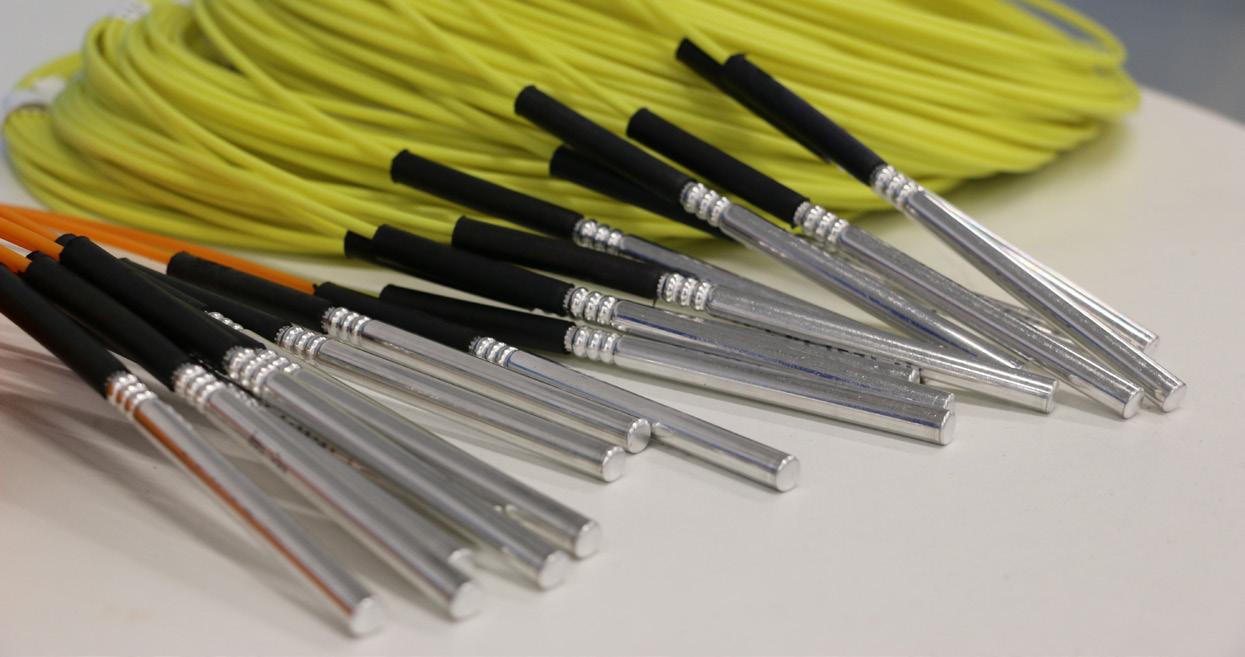
Tailoring Your Travel
At Malabar Business Travel, we specialise in crafting exceptional travel experiences across the Democratic Republic of the Congo (DRC).
Our commitment to customising seamless international and domestic journeys reflects our unwavering dedication to quality and professionalism.
Since our establishment in 2003, we have offered comprehensive travel solutions that prioritise high-quality customer care and meticulous attention to detail. As a leading travel management company, we guarantee a top-notch journey filled with unparalleled services.
Begin your adventure in our VIP lounge at Luano International Airport, where our friendly professionals handle all your administrative tasks, allowing you to relax and enjoy the journey ahead.
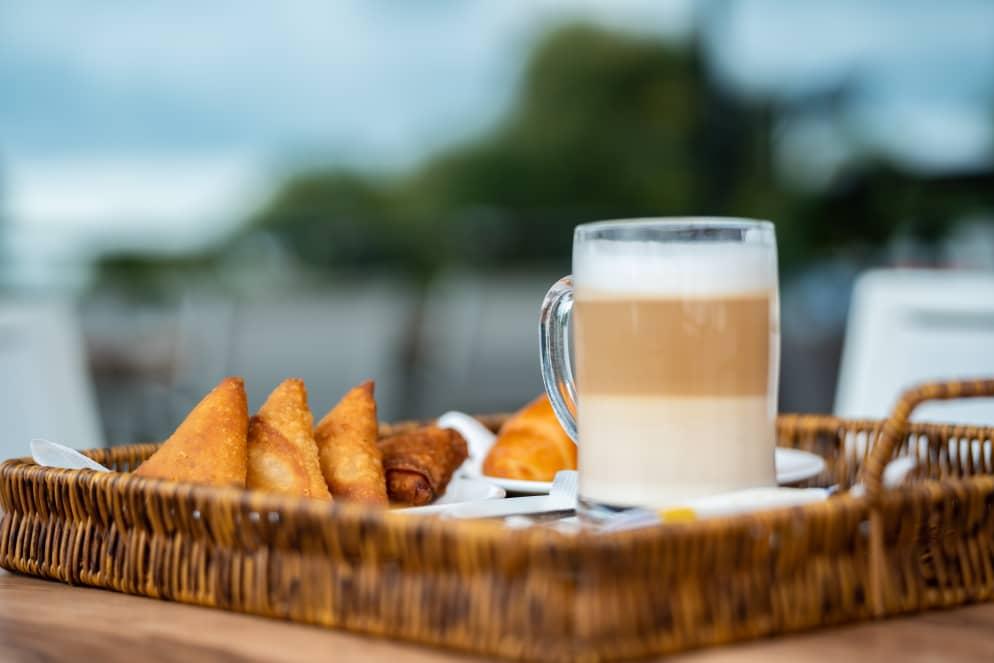
EVERY STEP OF THE WAY
We believe in the power of personalised travel. No matter your preferences, we strive to make each moment unforgettable. As your trusted travel partner, we prioritise environmental sustainability and provide guidance throughout your journey. Join us at Malabar Business Travel as we redefine travel experiences that leave a lasting impression. We aim to unlock possibilities and create remarkable memories whilst ensuring your travel plans align perfectly with your desires. Our commitment goes beyond traditional travel services; we focus on building strong relationships with our clients and partners.
AN ENVIRONMENTAL ENDEAVOUR
Traveling with Malabar Business Travel means exploring the extraordinary while embracing our mission of ethical practices. Guided by transparency and sustainability, we are dedicated to responsible travel that benefits both communities and ecosystems.
Let’s explore the wonders of the world together while leaving a positive impact on the destinations we visit. We believe sustainable travel enriches our experiences and fosters a deeper connection with the places we discover.
Malabar Business Travel: +243 815 995 588 info@malabar-group.com www.malabar-group.com
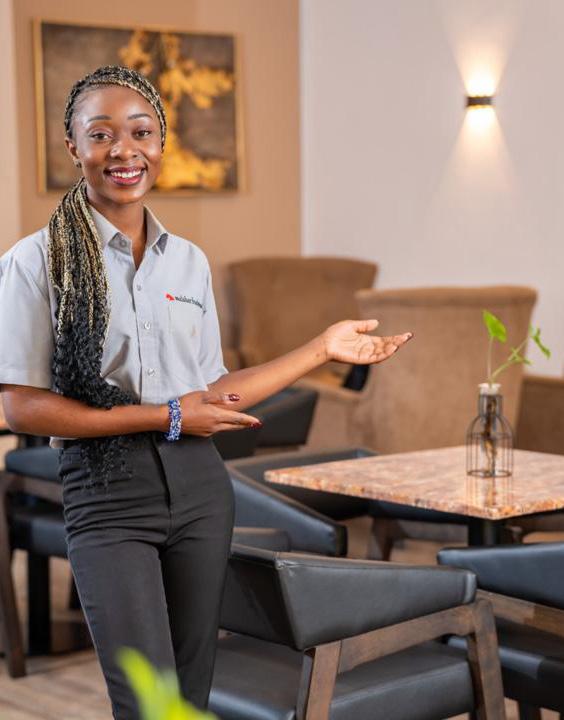
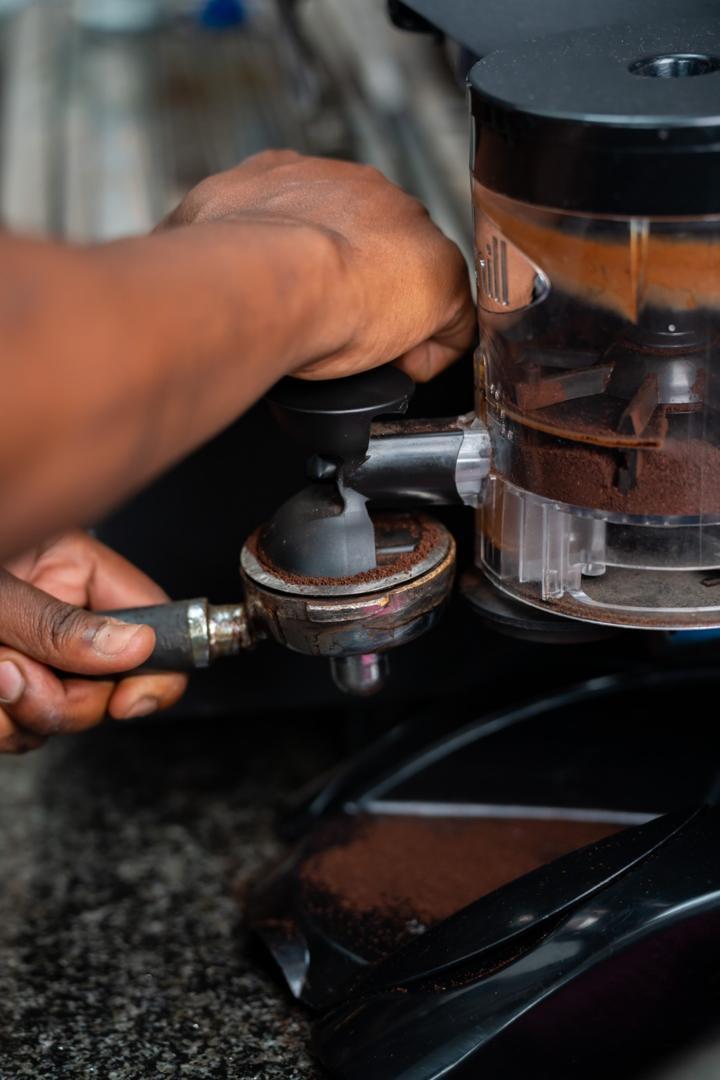
Seamless Service
Our dedication to excellence is reflected in the seamless services we offer, designed to ease your travel experience:
• Car Rentals: Enjoy the freedom of exploring your destination comfortably and conveniently.
• Airport Protocol Service: Experience hassle-free travel with fast-track immigration and customs clearance.
• Flight Bookings: Access seamless connections, competitive fares, and personalised itineraries.
• Hotel Reservations: Secure faultless accommodation, both nationally and internationally.
• Administration Handling Benefit: Seamless operations, from logistics coordination to administrative support.
• Visa Assistance: Receive expert guidance for all your visa needs.
• 24/7 Customer Support: Our team is committed to exceptional service, providing round-the-clock assistance for your convenience.
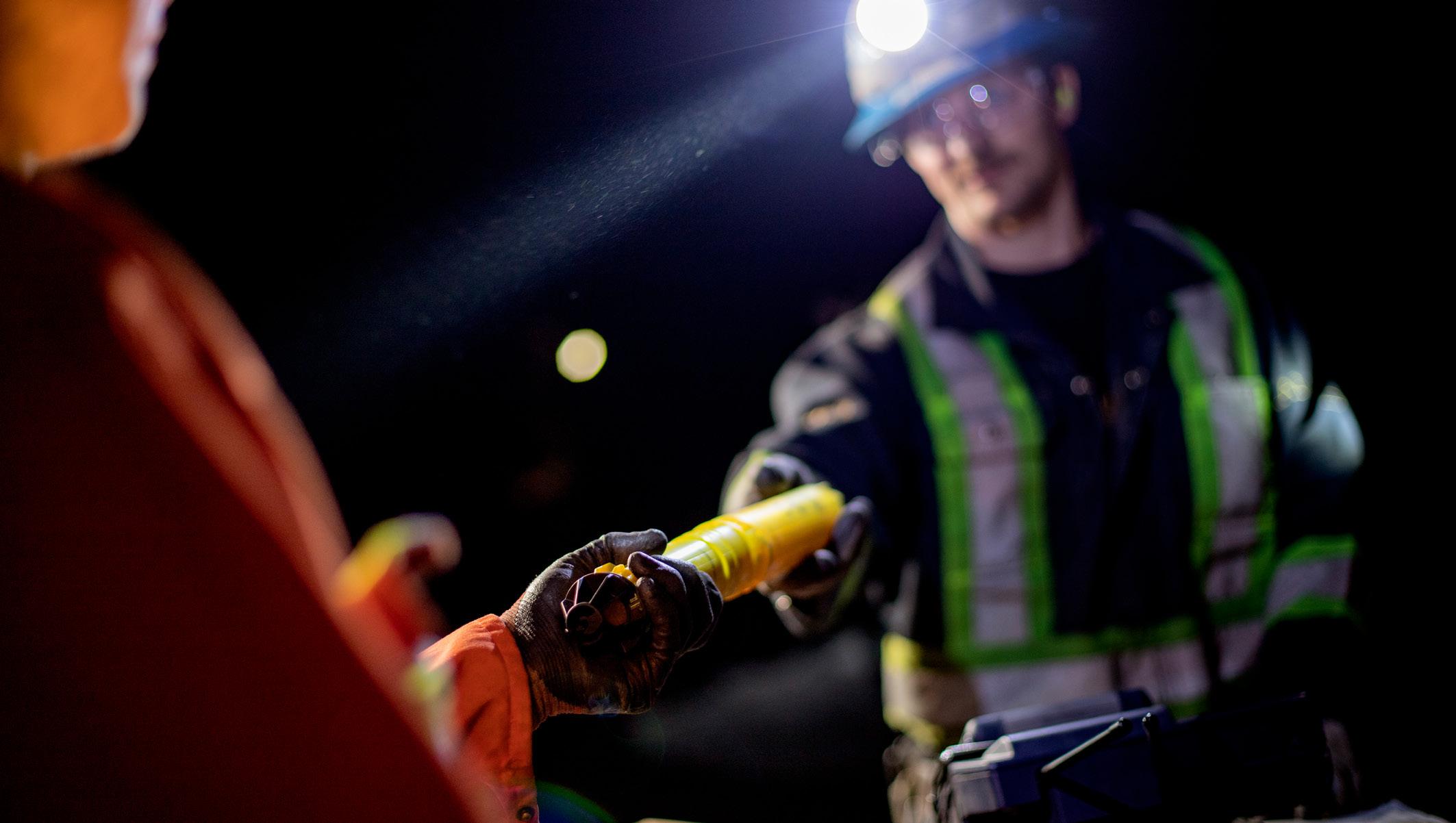
ORICA VALUES –AT A GLANCE
The company works as one team and is always guided by its values. As a purpose-led, responsible business, how value is delivered for customers, communities, and other stakeholders is as important as what is delivered.
SAFETY – The most important thing is that everyone at Orica returns home safely every day.
RESPECT – Care for each other, customers, communities, and the environment builds trusted relationships.
TOGETHER – Collaboration makes Orica better, individually and collectively.
INTEGRITY – The company is open, honest, and does what is right.
EXCELLENCE – Orica takes accountability for its business and delivers outstanding results.
“TOGETHER, ORICA’S INNOVATIONS IMPROVE SAFETY, EFFICIENCY, SUSTAINABILITY, AND OPERATIONAL FLEXIBILITY IN MINING ENVIRONMENTS”
– VICTOR MORALES, VICE PRESIDENT OF EMEA MINING, ORICA
The proven technology offers efficient processing and quality output that matches the standard required for the manufacturing of emulsion explosives.
Designed to support remote operations where Orica’s site-based emulsion plants are available, Cyclo™ delivers several environmental and commercial benefits for surface metal and coal mining.
For example, up to 1,000 litres (L) of used oil can be processed per hour by the fully containerised and automated system, associated used oil disposal costs and risks can be lowered, whilst annual diesel consumption in the production of bulk explosives can be reduced by up to an estimated 800,000L per site.
Cyclo™ additionally reduces logistical risks as it removes the need for off-site disposal and
truck movements through local communities and ensures finished product quality is maintained to the standard required for bulk emulsion explosives manufacturing.
Other environmental benefits are delivered by reducing heavy vehicle movements through local communities and thereby minimising the carbon emissions they cause.
In the EMEA region, Cyclo™ units are currently installed across several customer sites in Africa. Elsewhere, there are installations in Asia, Oceania, and Latin America, with a version to suit arctic conditions also being developed for Canada, China, and Mongolia.
Thus, Cyclo™ is an example of how the company is constantly looking for ways to reduce the carbon footprint of its customers whilst creating value for stakeholders.
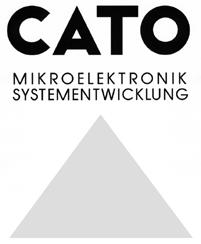
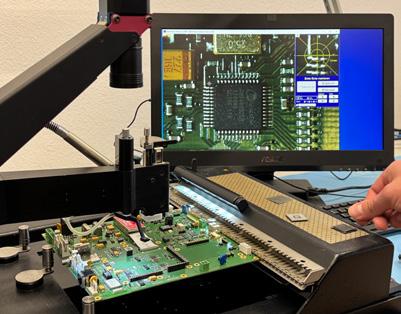
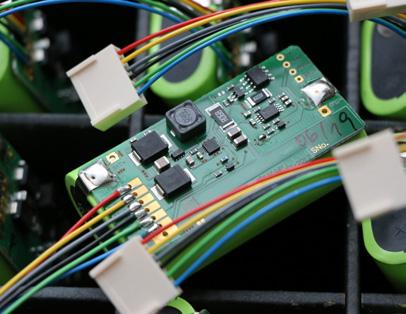
We. Give Electronics a Shape.
For over three decades, we have been designing and manufacturing custom electronic systems for industrial clients worldwide, thriving in the Ruhr region’s industrial hub. Our team focuses on developing solutions precisely tailored to our customers’ requirements.
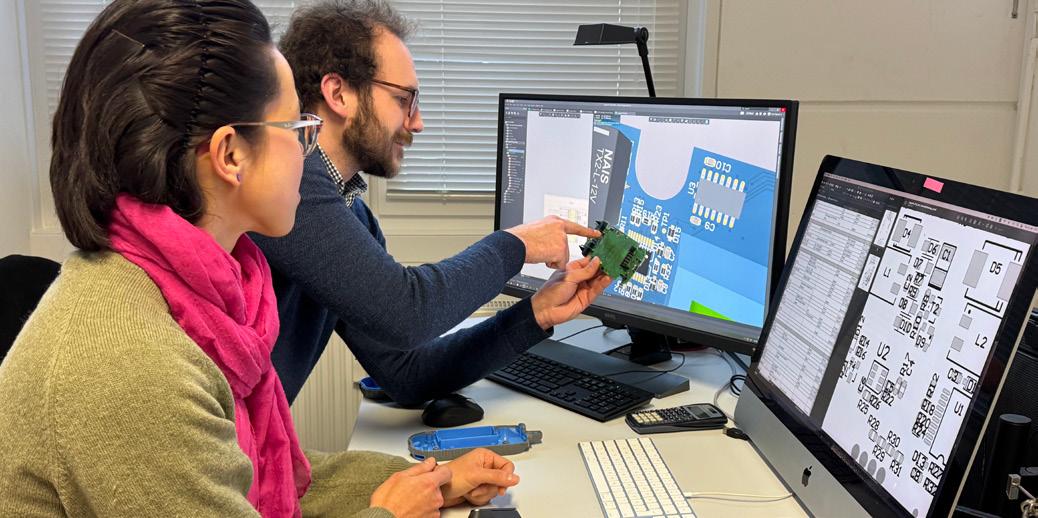
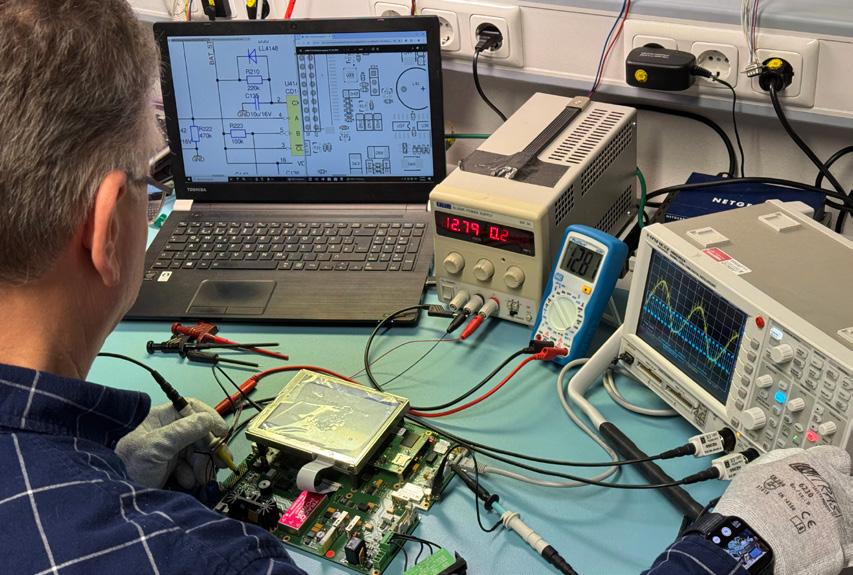
As a service-driven organisation, our sole focus is on delivering quality and reliability. From concept creation to production, we cover the entire electronics life cycle, integrating external specialists for advanced mechanical components, certifications, and high-volume manufacturing.
Whether prototyping or crafting small-series systems, our expertise ensures solutions that withstand demanding conditions such as high temperatures, vibrations, and electromagnetic interference, whilst meeting thermal management, high precision, and performance requirements.
From initial design to ongoing product support, we remain a steadfast partner, delivering comprehensive development and manufacturing services with cost optimisation at every stage.
Let’s shape the future together - delivering complete electronics solutions, from design to product life cycle support, tailored to meet tomorrow’s challenges.
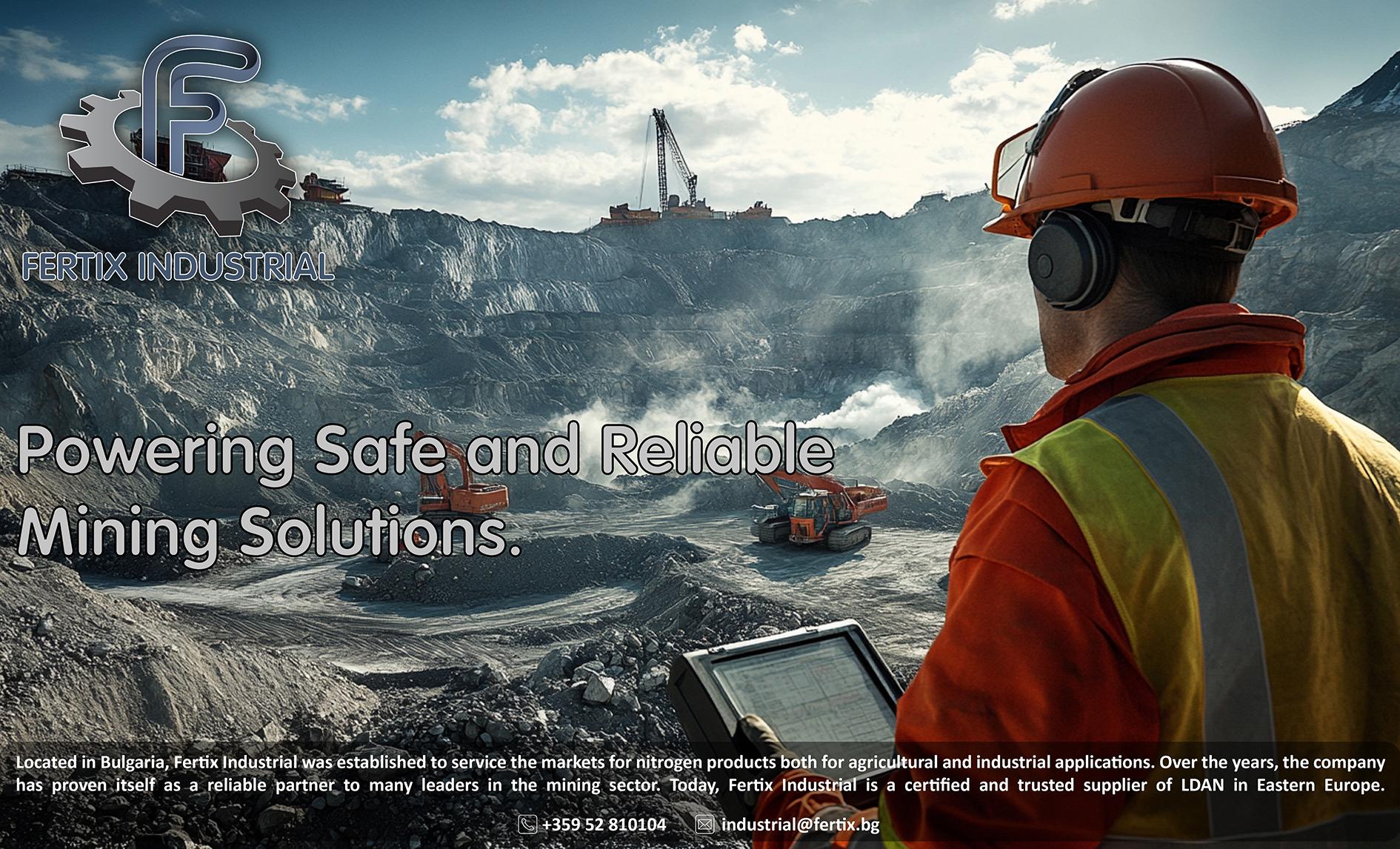
“Orica’s premium emulsifier technology enhances the quality and stability of bulk explosives whilst significantly reducing the carbon footprint of production processes, showcasing our commitment to sustainability,” Morales affirms.
ADVANCING SAFETY
Rapid technological advancements that are reshaping the mining and infrastructure landscape are also propelling the industry towards safer practices.
New technologies are transforming safety in the mining industry by reducing human exposure to hazardous conditions, monitoring geotechnical challenges, and enhancing precision in operations.
Orica, whose approach begins with ensuring it conducts business responsibly and prioritising the safety of people, customers, and communities, helps to improve safety and productivity with smart technologies such as WebGen™ and Avatel™.
The world’s first truly wireless initiating system, WebGen™ was launched by Orica in early 2017 and
completely eliminates the need for downlines and connecting wires in surface mining.
Underground, the system communicates through rocks, air, and water to initiate blasts safely and reliably, removing people from harm’s way, and enables new mining methods and blasting techniques to increase productivity and reduce blasting costs.
“WebGen™ allows for remote blasting, eliminating the need for workers to enter dangerous zones,” notes Morales.
Avatel™, meanwhile, is a semiautomated charging solution that eliminates the need to handle initiating systems or manually load blast holes.
The first-of-its-kind innovation enables a single operator to prepare the development face and complete the entire charging cycle from within the safety of an enclosed roll-over protective structure (ROPS) and falling object protective structure (FOPS) cabin.
Thus, Avatel™ represents a step change in safe and productive development charging through
advanced mechanisation, automation, and digitalisation.
As well as improving accuracy in blast execution, the technology reduces the exposure of workers to hazardous environments.
“Avatel™ enhances underground mining safety by combining precision with automation, minimising human involvement in high-risk areas,” Morales elaborates.
SHAPING THE FUTURE
Other Orica technologies improving safety and productivity include 4D™, a revolutionary bulk explosives system that supports surface and underground blasting operations and can be tailored instantaneously to suit varying geologies and hole conditions for the desired blast outcomes.
Enabled by Orica’s proprietary emulsion chemistry and smart technologies, operations using 4D™ can achieve accurate, automated, and efficient energy control.
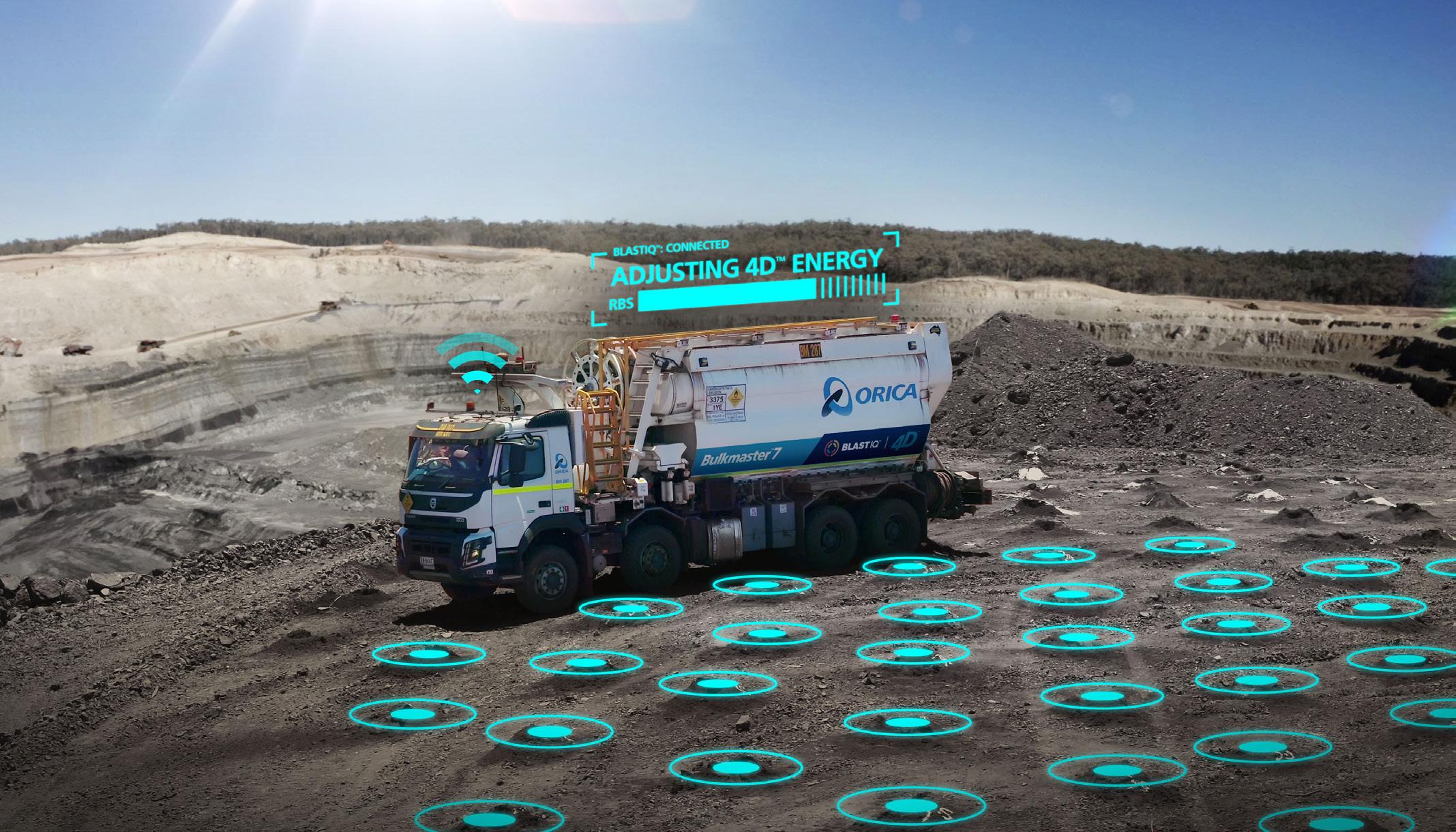
On the surface, one of the key benefits of 4D™ is the technology’s augered and pumped loading methods for improved efficiency in explosives delivery.

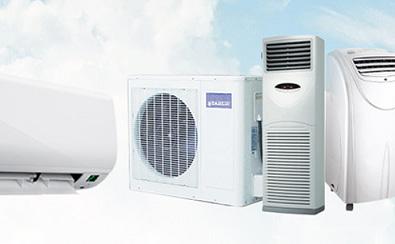

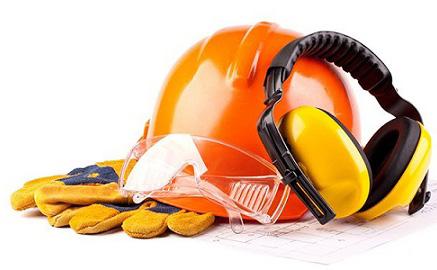
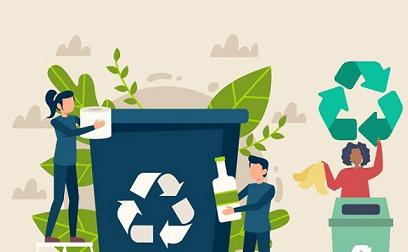
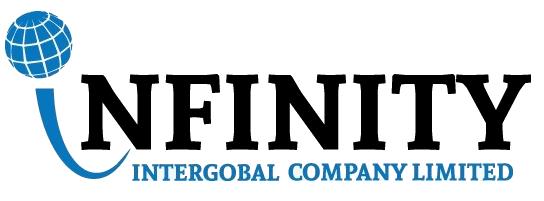
Best-provider in general mining services
Infinity Interglobal Company Limited, is the Company Incorporated in Tanzania on 25th October 2011 and issued certificate of incorparation number 86739. It has been registered with the Tanzania Revenue Authority and assigned Taxpayer Identification Number 117-077-543, Also it has been registered for Value Added Tax (VAT) and assigned VAT registrartion number 40-017177-B.
The company is dealing with general supplies of mining equipment, hardware stores, recruitment agency, stationeries, alluminium glass, timber and its products and other agricultural products.
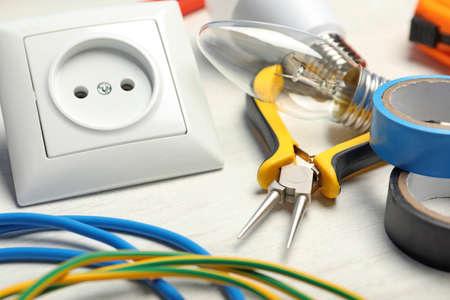
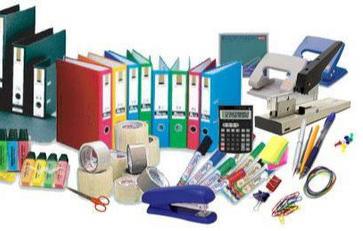
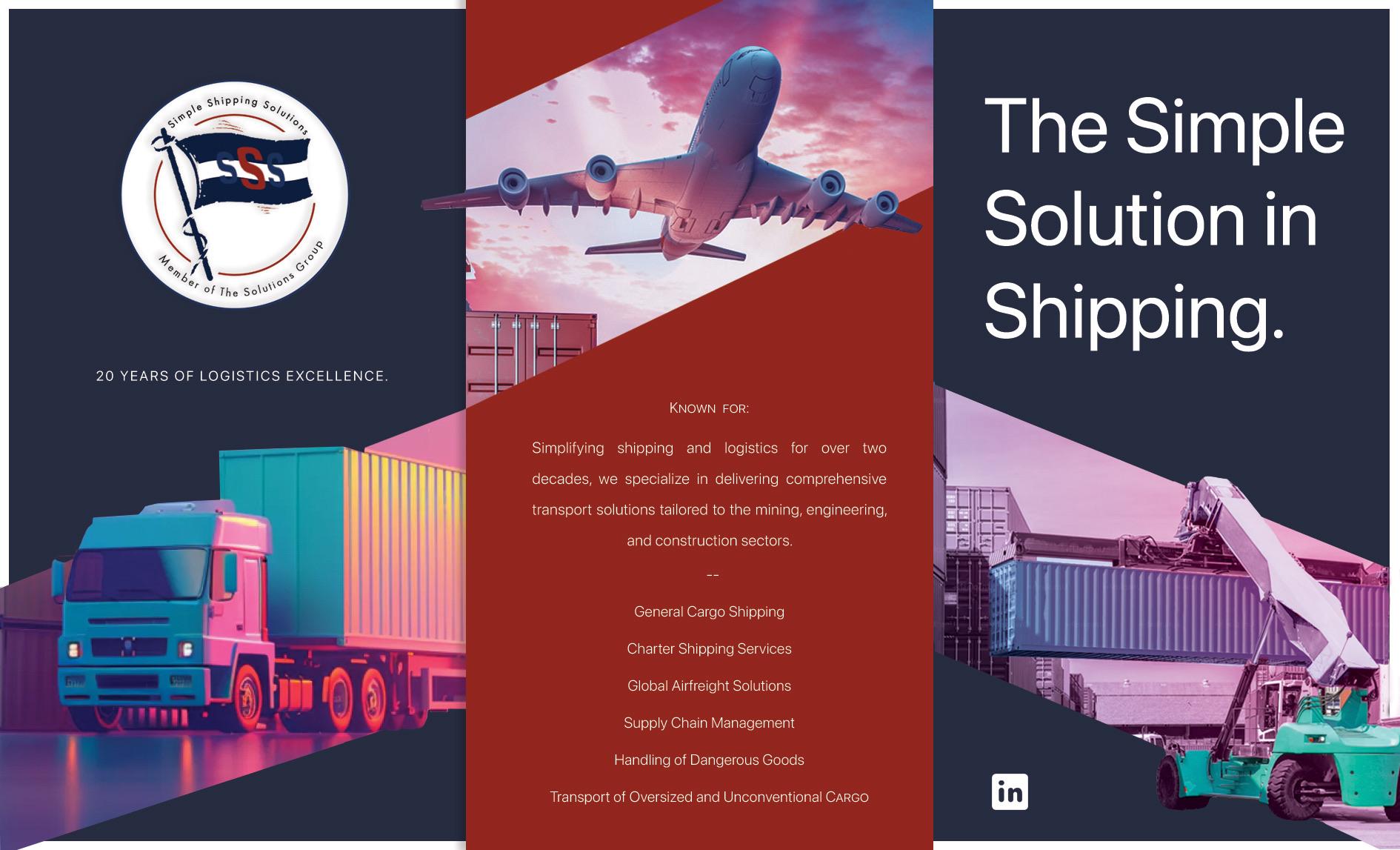
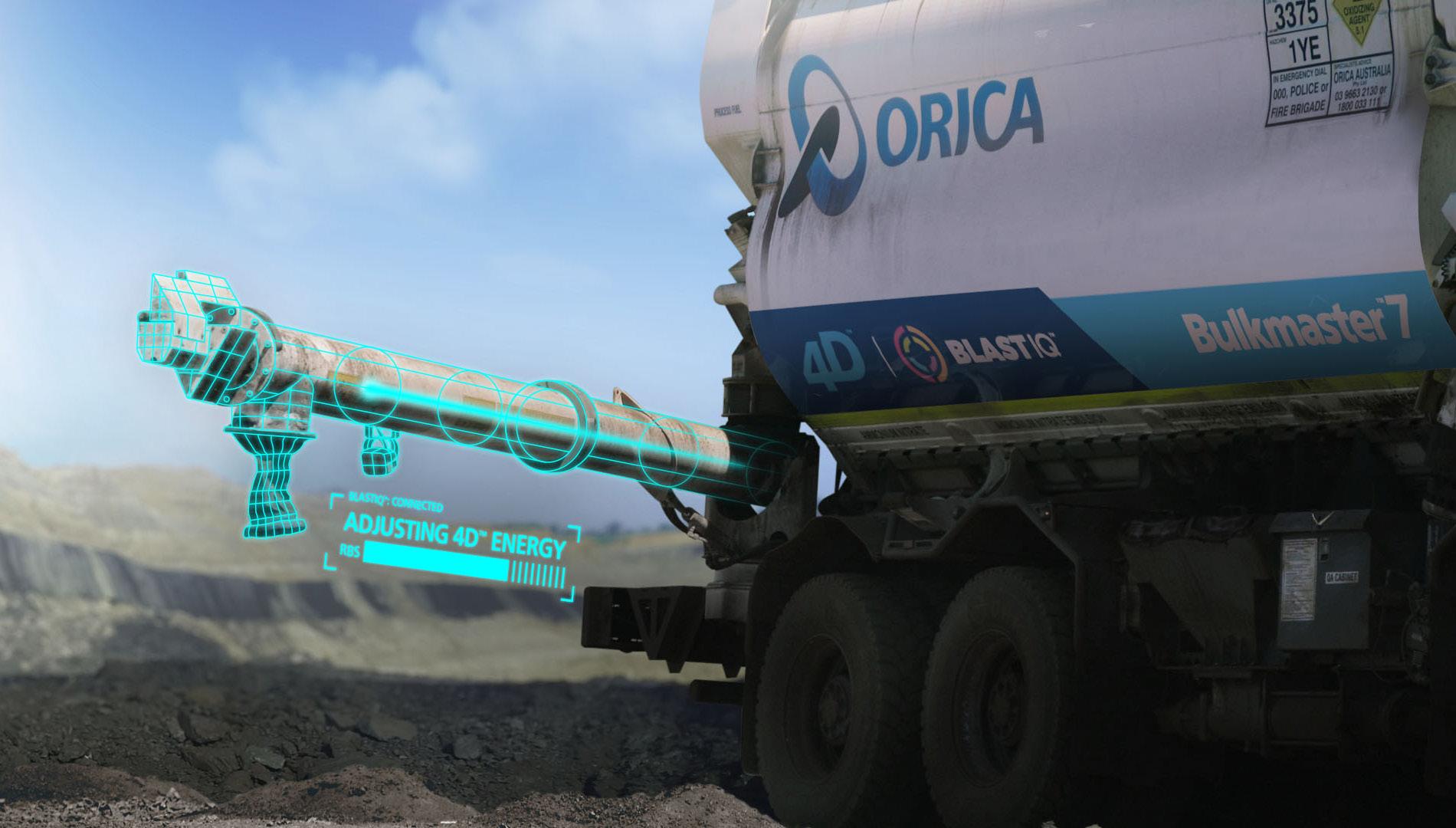
Surface operations also enjoy reduced drill and blast costs through the application of greater energy, optimised fragmentation, improved productivity and wall control, lowered fume risks, and much more.
Underground, 4D™ enables instantaneous energy control, automation and repeatability, maximised orebody recovery, and sustainable blasting practices.
“4D™ is a revolutionary bulk explosives technology that allows the real-time customisation of blast energy, optimising safety, productivity, and resource efficiency whilst minimising environmental impact,” Morales details.
Next Gen ShotPlus™, meanwhile, is shaping the future of drill and blast by enabling users to assess the impact of engineering decisions and design the highest-value blast for any situation.
This groundbreaking innovation combines high-performance visualisation, best-in-class design tools, and modelling capabilities to
predict blast movement, damage, and vibration, leading drill and blast into a new era.
Engineers can also share the outcomes of these predictive models with multiple stakeholders, allowing for collaborative assessment of the
ORICA’S PURPOSE, VISION, AND STRATEGY
PURPOSE – To sustainably mobilise the earth’s resources.
VISION – To be the world’s leading mining and infrastructure solutions company.
STRATEGY – To deliver solutions and technologies that drive productivity for customers across the globe. Orica’s strategy is centred on three key pillars – optimising its operations, delivering smarter solutions, and partnering for progress.
highest-value blast designs in the context of the entire mining value chain.
Launched in September 2024, Next Gen ShotPlus™ therefore empowers drill and blast engineers to move beyond descriptive designs.
“NextGen ShotPlus™ redefines blast design and visualisation, offering advanced 3D modelling and simulation capabilities,” highlights Morales.
“It allows customers to optimise blast outcomes, streamline planning, and enhance operational efficiency.”
EBS EXPANSION
Then there’s Orica’s market-leading GroundProbe radars, which support the control of wall movements across mining operations worldwide, and i-kon™ III, the most sophisticated EBS on the market.
Reliable even in harsh conditions, i-kon™ III helps customers to achieve their blasting goals and enhances productivity through faster
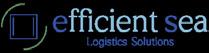

Our integrated teams deliver creative solutions and tailored support for customers around the world, placing Efficient Sea at the forefront of the shipbroking industry. We operate in Mauritania, Senegal, and Spain.
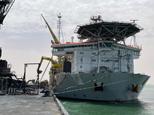

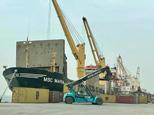
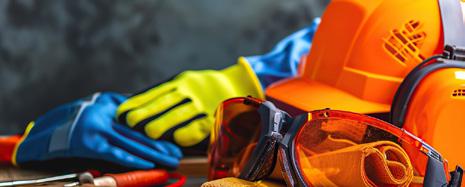
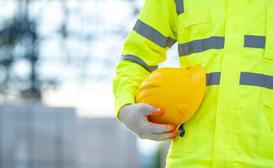
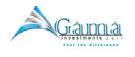


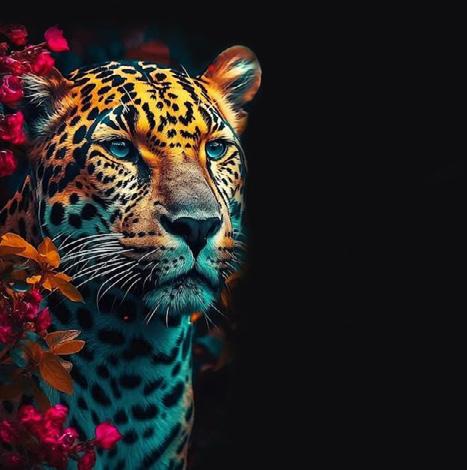
Freightworx: Excellence in Logistics Since 1999 Since 1999, Freightworx has been at the forefront of logistics in Africa as a proud family-owned enterprise. With a century of combined experience, we provide exceptional service and peace of mind through state-of-the-art warehousing, expert crating, and seamless air, road, and sea transportation, all backed by comprehensive insurance. As an IATA-affiliated company, we maintain international standards and competitive rates for all imports and exports. Being 100% female-owned, we champion diversity and inclusivity. Choose Freightworx for a reliable and innovative logistics experience tailored to your needs.
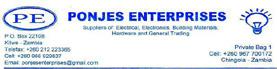
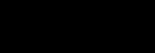
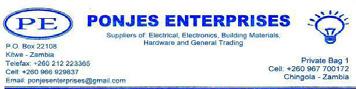
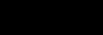
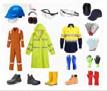
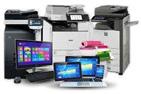
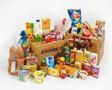

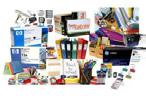

deployment and setup for both small and large-scale blasting.
“Our i-kon™ III EBS provides unparalleled accuracy and control, reducing the risks associated with misfires,” adds Morales.
Orica’s EBS manufacturing and supply network has been actively expanding worldwide, with new plants and equipment strategically deployed in all major regions, including EMEA, to enhance the company’s proximity to customers.
As a result, Orica has grown from two EBS manufacturing sites globally to six, significantly bolstering its EBS capacity and subsequently enhancing the company’s responsiveness to customer demands, ensuring a more robust supply chain.
Following the successful introduction of the Exel™ Neo range, with early adopters reaping the benefits, Orica is expanding its leadfree NPED technology to manufacture EBS Neo, its first lead-free EBS at its Gyttorp plant.
This is the first time Orica’s EBS are being manufactured at its state-ofthe-art facility in Sweden, bolstering supply security and optimisation.
The Gyttorp plant will initially be used to assemble Orica’s standard EBS detonators and will subsequently be used to assemble the lead-free EBS range based on NPED technology.
Like the Exel™ Neo range, EBS Neo is free of any Substances of Very High Concern (SVHCs) according to the EU’s regulation on the registration, evaluation, authorisation, and restriction of chemicals (REACH).
Both product lines also comply with the EU’s Restriction of Hazardous Substances (RoHS) Directive beyond the current deadline of April 2025 and will help customers meet their own environmental, social, and governance (ESG) compliance targets.
Customer trials of EBS Neo got underway in 2024 ahead of market launch, as the company continues to explore how it can use innovative
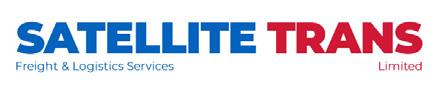
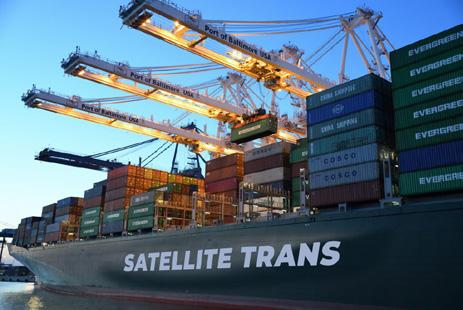
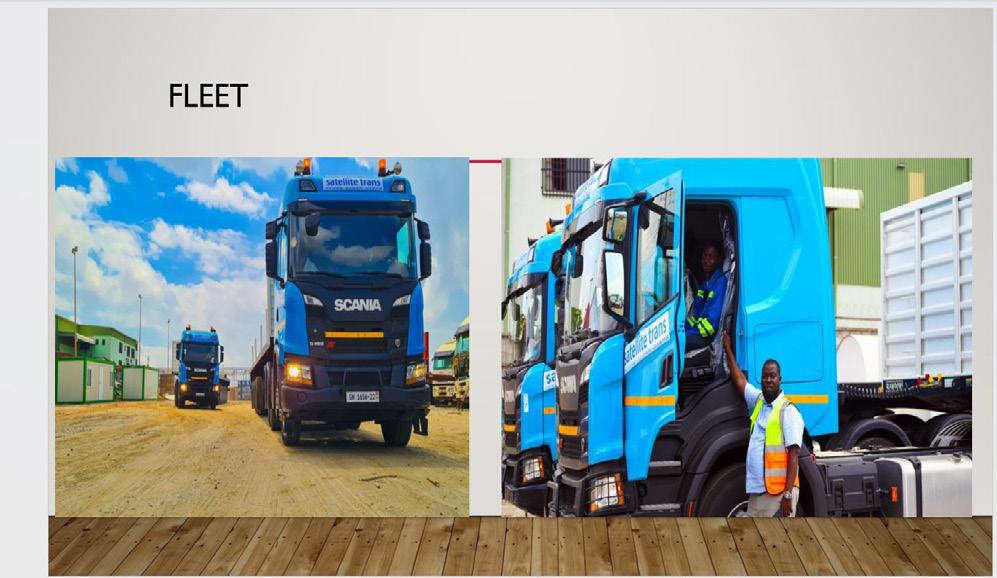
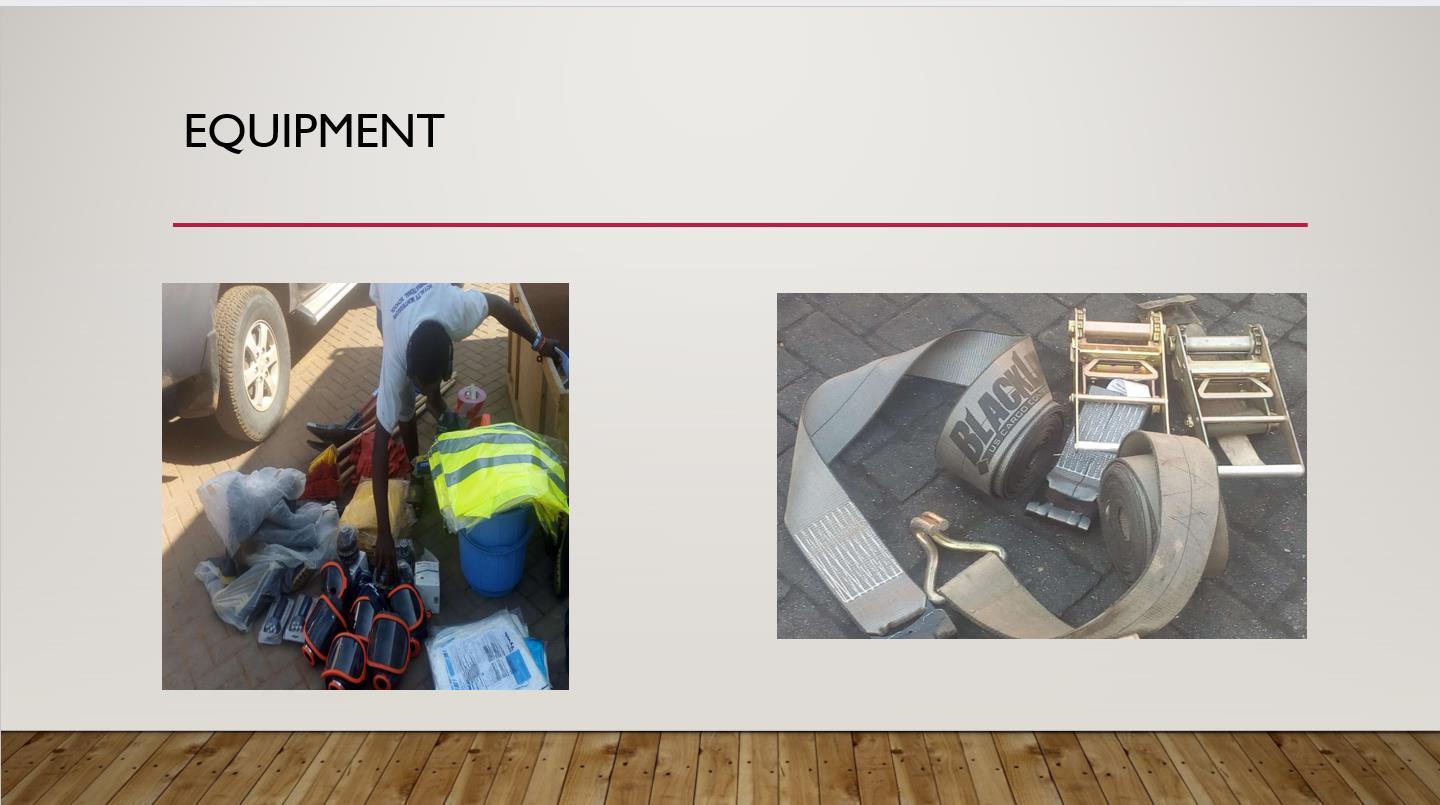

www.satellitetransghana.com
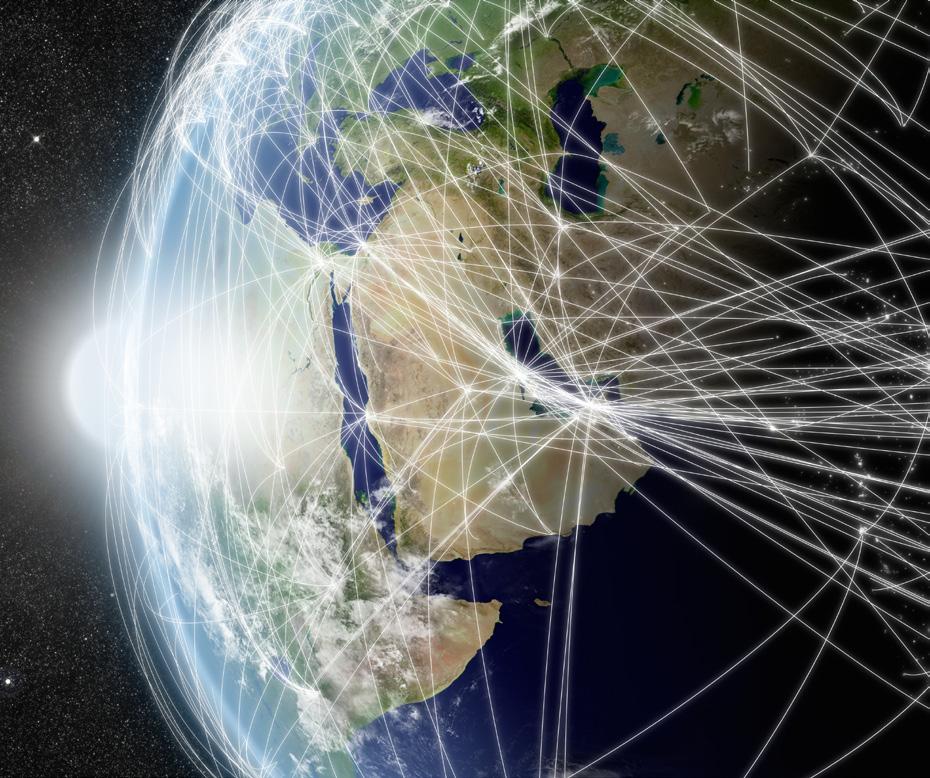

With more than 30 years of experience TEUP provides tailored solutions to optimize and automate production processes.
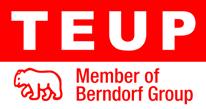


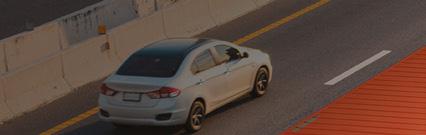
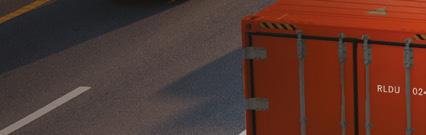
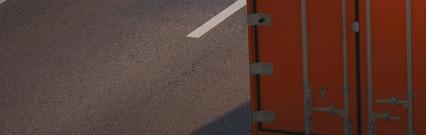
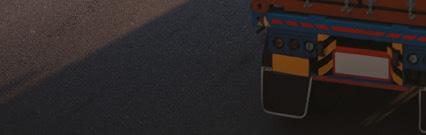
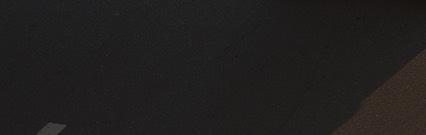
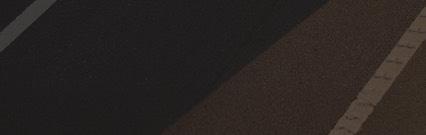

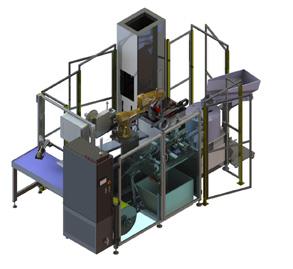
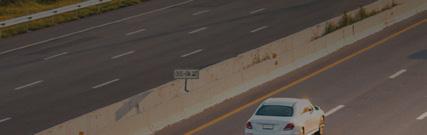
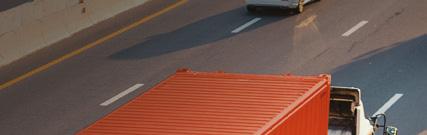
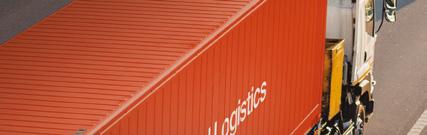
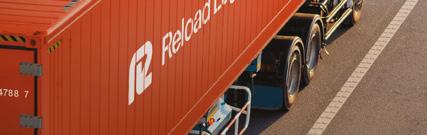

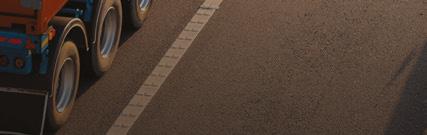

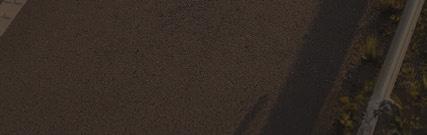
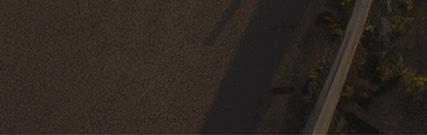
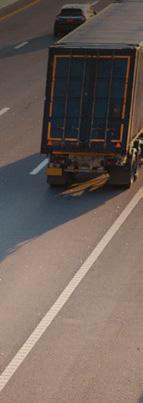
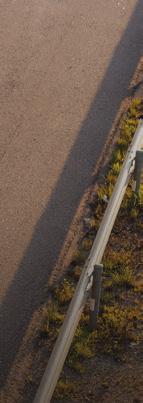
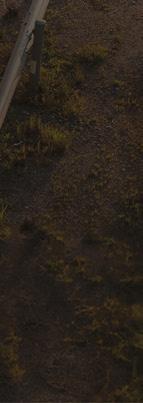
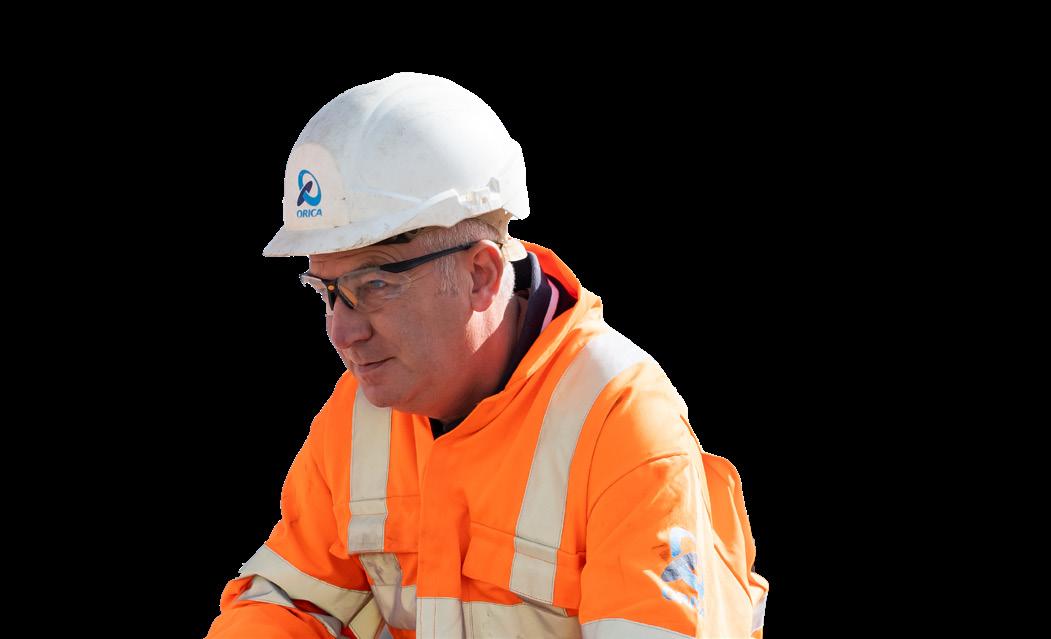

technologies to help achieve their ESG goals.
INVESTMENT IN COMMUNITIES
Alongside ESG, Orica is deeply committed to corporate social responsibility (CSR) with a strong focus on community engagement.
Indeed, in 2024, the company invested USD$4 million into communities globally, which puts Orica on track to exceed its corporate community investment goal of USD$15 million by the end of FY25. CSR projects across EMEA include promoting diversity and providing local talent opportunities, such as supporting women in technical roles in Africa and aiding social equality efforts.
Vulnerable African communities are also assisted by Orica through efforts such as combatting human trafficking in Tanzania, developing schools for
children in Zambia, providing medical support in Ghana, and ensuring access to clean water in remote areas of the continent.
“These efforts reflect our ongoing dedication to creating meaningful social impact,” Morales informs us.
As well as investing in communities, Orica’s success is equally built on continuous investment in developing its people.
“We are an innovative, technologydriven company, so having the best talent is crucial – not only for driving innovation, but also fostering resilience, commitment, and a focus on generating value for all stakeholders,” he enthuses.
This dedication to continuous improvement and ability to adapt in challenging environments are key attributes of Orica’s team, which ultimately enables it to deliver exceptional and lasting value to
customers and communities.
STRATEGIC ACQUISITIONS
Likewise, the company continues to invest in strategic acquisitions to enhance its offerings and expand its global footprint.
These acquisitions also further broaden Orica’s business and create global opportunities amongst new customers and industries in diverse locations.
For example, in February 2024, the company acquired Cyanco, a US-based leader in manufacturing and distributing sodium cyanide, primarily serving the gold mining industries in the US, Canada, Mexico, Latin America, and Africa.
The acquisition has enhanced the safety and reliability of Orica’s systems and processes, improved security of supply through global supply optimisation, and
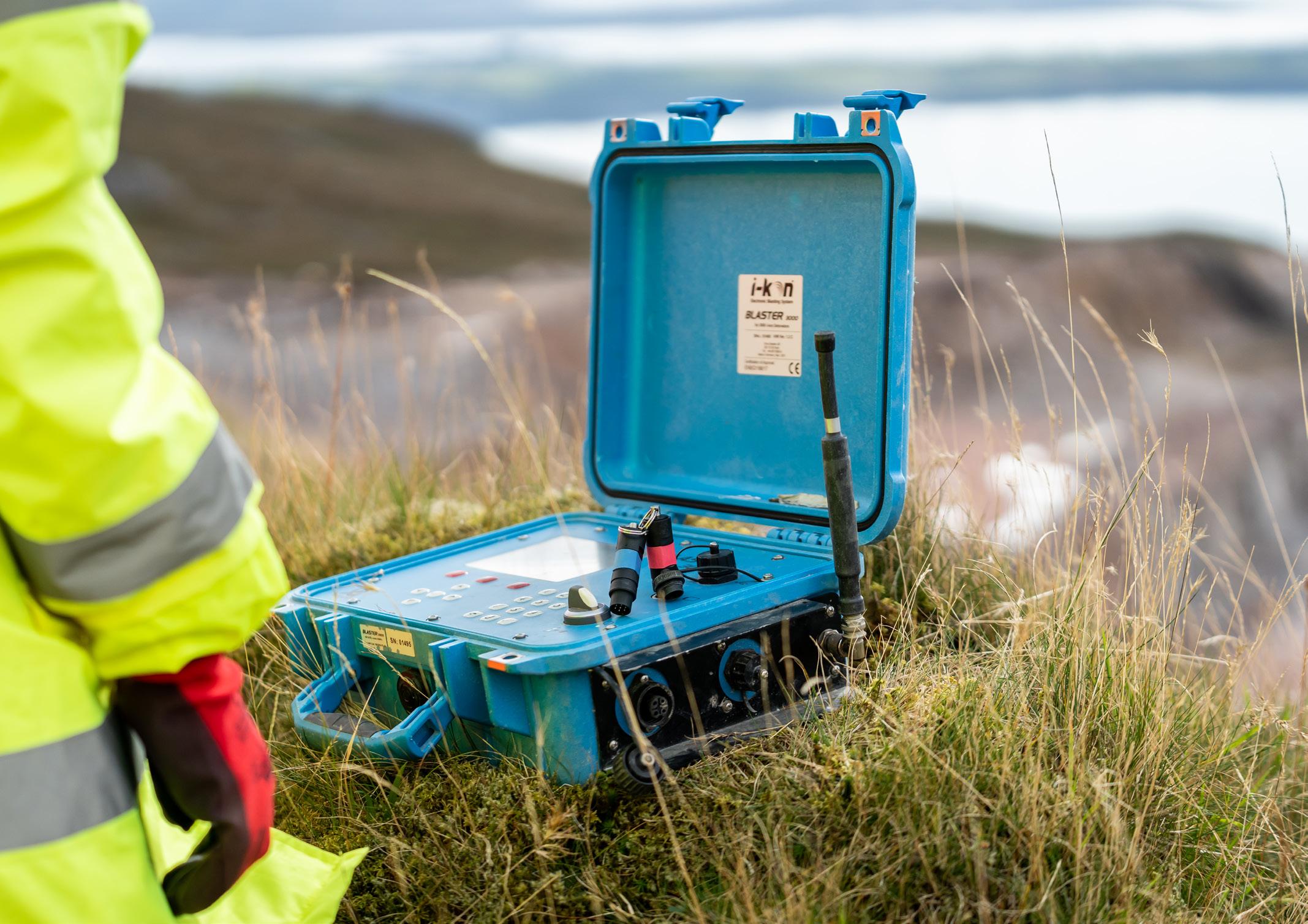
expanded the company’s portfolio of technologies and services to differentiate its speciality mining chemicals offering.
It has also more than doubled Orica’s existing sodium cyanide production capacity to approximately 240 kilotonnes per annum (ktpa) courtesy of Cyanco’s two manufacturing plants in Nevada and Texas.
A couple of months prior, the company expanded its digital solutions portfolio by acquiring Terra Insights, a leading provider of innovative sensors and data delivery technology for geotechnical, structural, and geospatial monitoring in mining and infrastructure.
Terra Insights adds additional products and capabilities across these two value chains, allowing Orica to provide a more complete offering.
“The acquisition of Terra Insights
strengthens our capabilities in geotechnical monitoring and geological solutions, creating opportunities in the civil infrastructure environment and energy industries,” Morales acknowledges.
These acquisitions reflect Orica’s commitment to expanding beyond traditional blasting services and developing integrated, added-value technologies.
“We remain focused on identifying and investing in new technologies that drive efficiency and sustainability in mining and infrastructure operations.”
Other priorities for the year ahead include delivering greater value for customers, communities, and stakeholders.
Orica aims to support customers in achieving their sustainability goals in 2025, particularly reducing greenhouse gas (GHG) emissions, advancing the energy transition
through future-facing commodities or critical minerals, and enhancing operational reliability and productivity.
“We are excited by the growth of key markets such as the copper belts in Africa and Central Asia, gold belts across Africa, mining growth in the Middle East, and major infrastructure projects in Southern Europe and the Middle East,” shares Morales.
“Our focus remains on being the preferred partner in these regions, driving sustainable growth for our customers,” he concludes.

Tel: +351 213 571 311 orica.portugal@orica.com orica.com
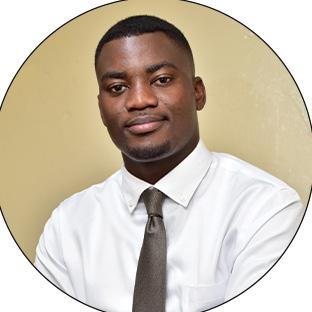
Henri Cheko General ManagerMuche Graphique
Supplying the Best Products at even Better Prices
With a proud history of supplying spare parts, printing services to various sectors for over a is a company driven by customer satisfaction
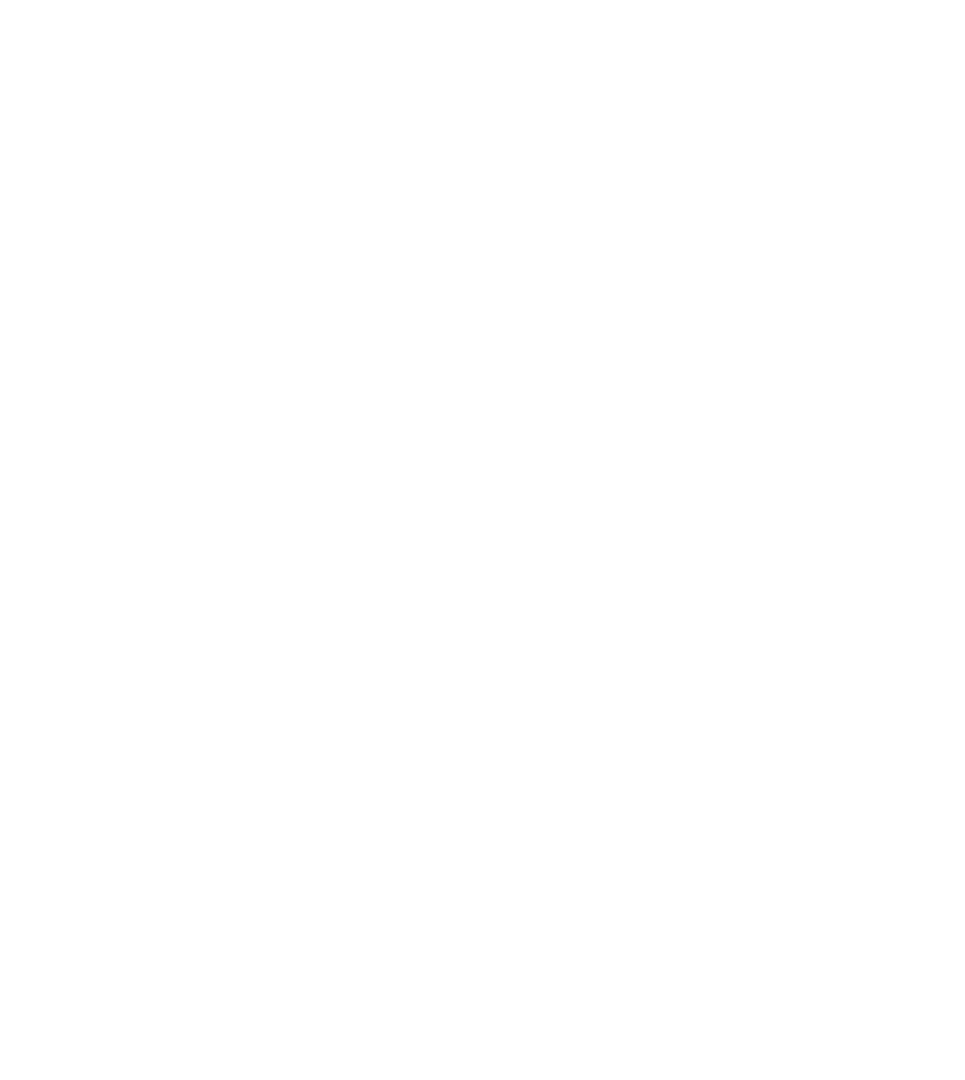
Headquartered in Lubumbashi, Haut-Katanga, in the Democratic Republic of Congo (DRC), Muche Graphique’s offerings are wideranging.
The company supplies spare parts to original equipment manufacturers (OEMs), alongside safety equipment, printing services, chemical products, and laboratory equipment to other clients.
Founded on innovation and an entrepreneurial spirit, Muche Graphique has recruited a dynamic and qualified team that is experienced in their respective fields and able to meet the market’s evolving needs. Underpinned by over ten years of industry experience, the company has gained the trust of several large companies in Grand Katanga, consistently meeting their supply and equipment needs. On leader intends relationships vision service fair FIRST-CLASS Muche its all services, throughout project and Offering quality way, and company satisfaction reputation
Products Prices
parts, safety equipment, and decade, Muche Graphique
satisfaction and service excellence
On a mission to be a progressive leader in its field, Muche Graphique intends to build strong, lasting relationships with its clients, with a vision to offer exceptional customer service and top-quality products at a fair price.
FIRST-CLASS SERVICES
Muche Graphique prides itself on ability to provide customers with the requisite information on its services, remaining in communication throughout the execution of each project due to its diligent monitoring and communication department.
Offering each of its customers quality assurance every step of the way, deeply personalised service, and a results-oriented attitude, the company ensures total customer satisfaction – a key factor of its reputation for excellence.
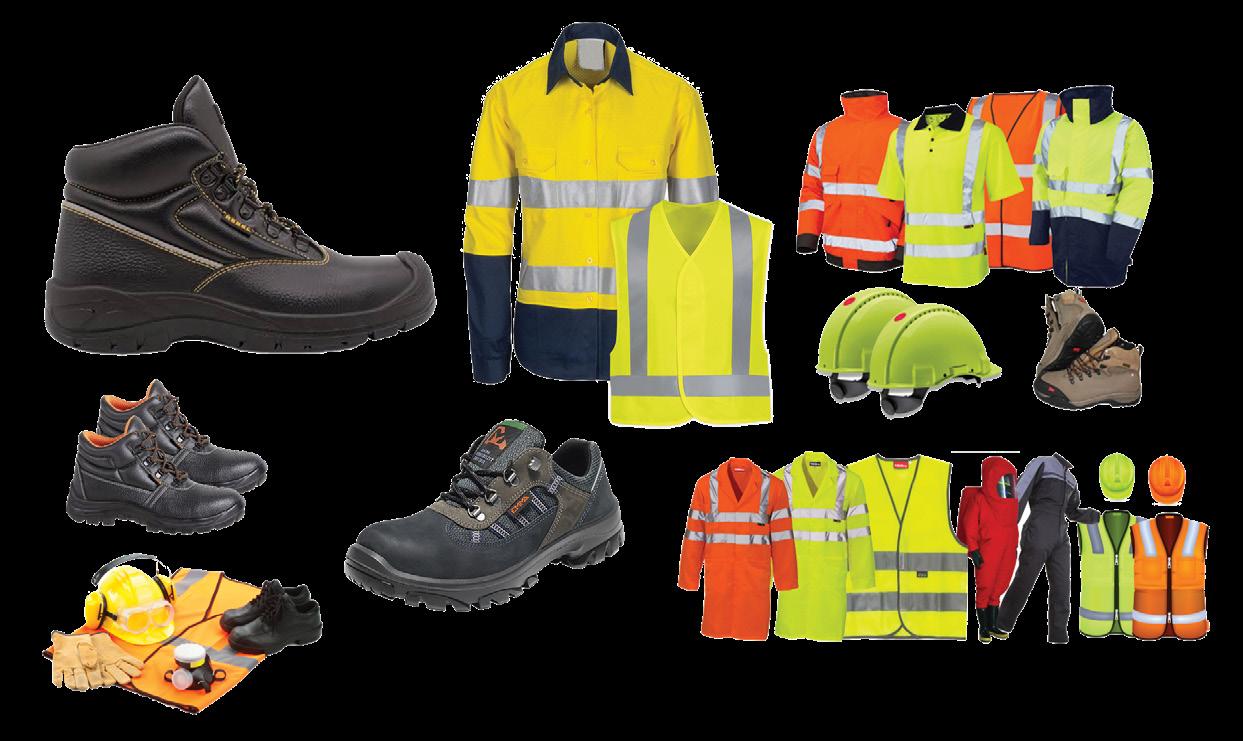
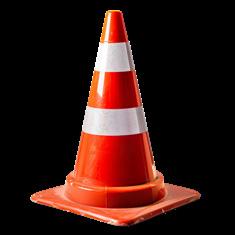
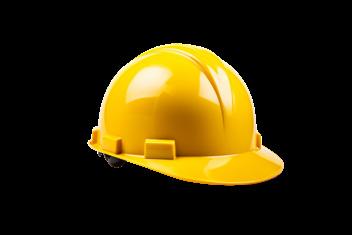
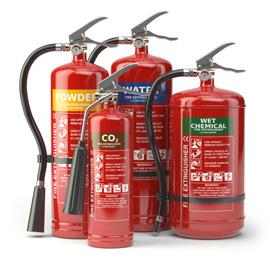
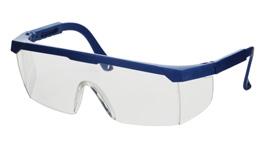
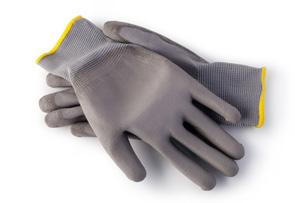
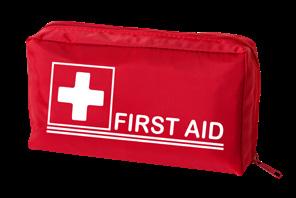
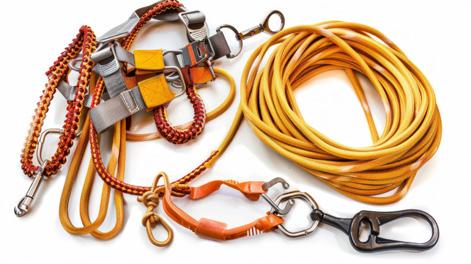
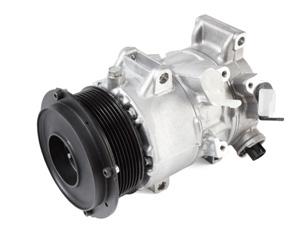
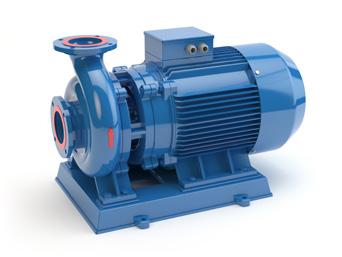
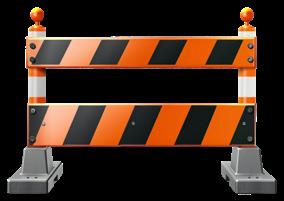

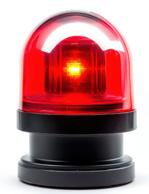


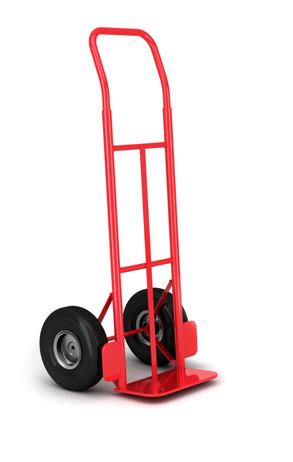
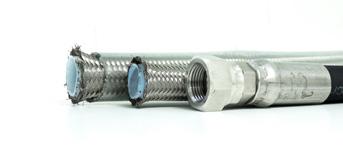



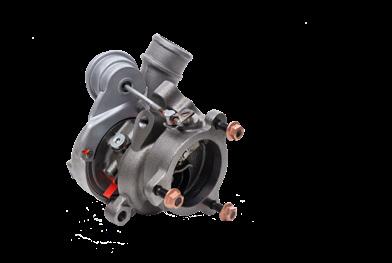
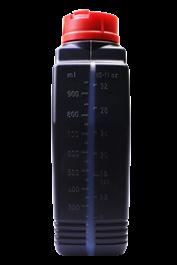
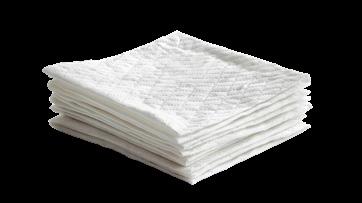
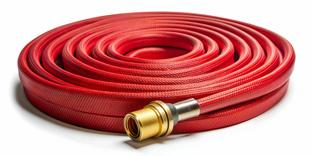
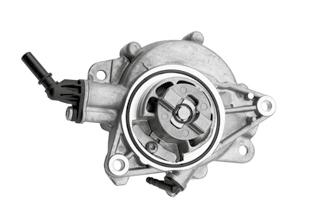
MUCHE GRAPHIQUE’S SERVICES
SPARE PARTS
Genuine lubricants spare parts for trucks and machines: Volvo, Caterpillar, Sinotruck Howo, Shacman, Foton, Auman, Isuzu, and Faw, Man. For compressors and pumps: Atlas Copco, Balma, Abca, Almig, Alup, Airman, Vaccumpump, Bosch, Bowie, Napco, Wilden, Becker, etc.
SAFETY EQUIPMENT
Offering long-term safety solutions, Muche Graphique’s safety equipment and engineering experts are on hand to guide customers.
To ensure consistently high health, safety, and environmental (HSE) standards, the company has established strong partnerships with some of the best manufacturers.
As always, Muche Graphique offers the best products at even better prices. This includes safety equipment supplies and signage for both residential and commercial use.
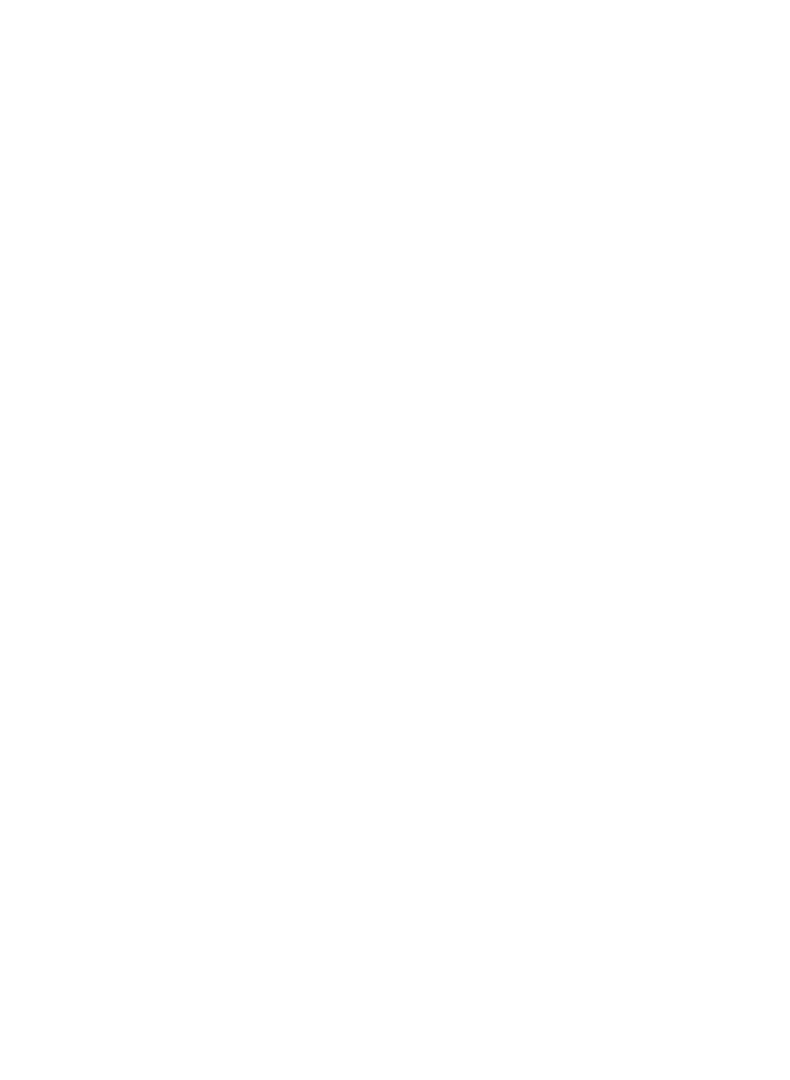
Deep-rooted trust and reliability between Muche Graphique, its customers, and its partners are also of the utmost importance. By prioritising long-term satisfaction over immediate success, the company proudly centres everything it does around customer fulfilment.
Innovating to stay ahead of the curve, Muche Graphique seeks to continuously improve its services. It encourages the creativity of its employees, utilising progressive technical innovations to think outside the box, benefitting its customers.
AN
Proud Muche its This financial over to Seeking across ambition and success To regularly production
Spare Parts
PRINTING
With over a decade of experience in printing and utilising various professional machines, Muche Graphique is an ideal partner for companies to work with.
Its clients range from small and medium enterprises (SMEs) to large groups throughout the Greater Katanga region, demonstrating its wide-reaching capabilities.
Regardless of volume, size, or quantity, the company prints on all types of media, offering a complete suite of services – from design to printing and delivery.
Muche Graphique even goes as far as to provide manuscripts of digital files provided by clients upon request.
RELATED SERVICES
Chemicals and laboratory equipment –
Comprising various lab materials, chemical products, and mining blasting materials such as installation of argon gas lines, acetylene, and nitrous.
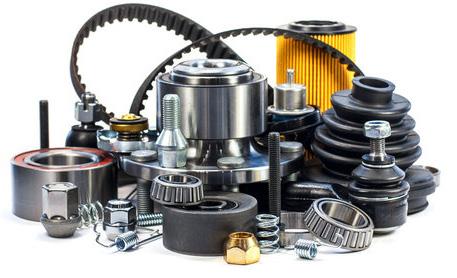
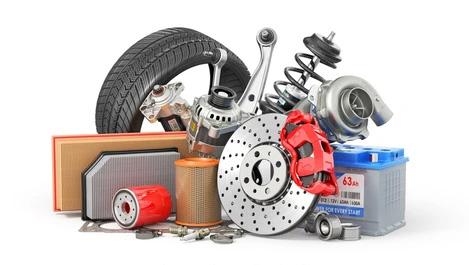
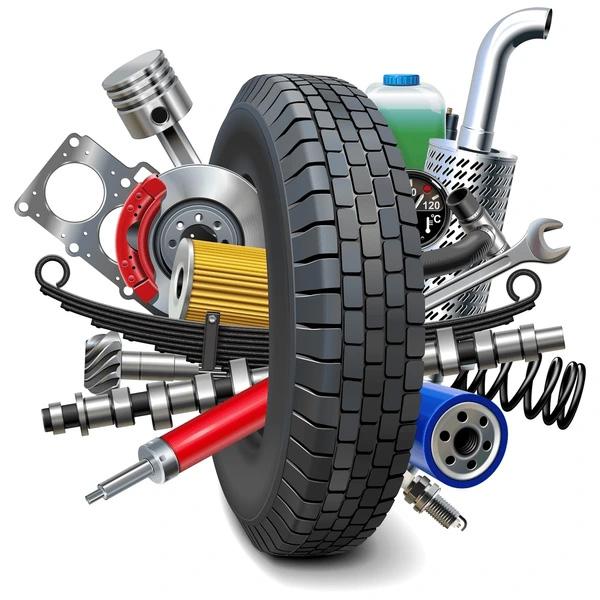
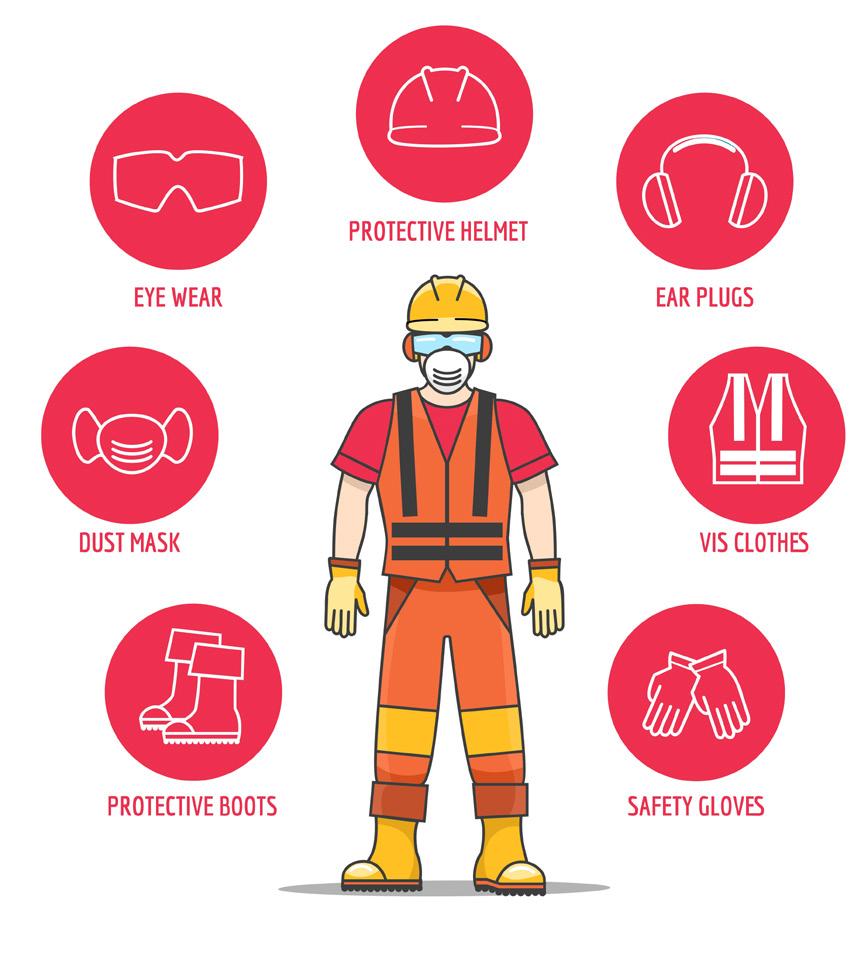
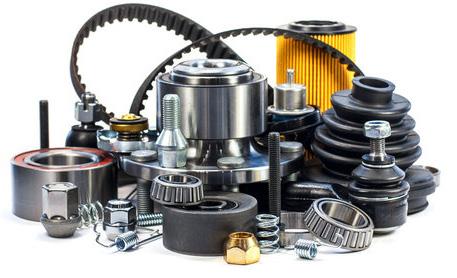
AN INDEPENDENT SUPPLIER
Proud to be an independent supplier, Muche Graphique enjoys freedom in decision-making. This freedom is largely based on its financial independence, acquired over many years of operation thanks good management.
Seeking to obtain maximum quality across all its activities, the company’s ambition is to always keep its promises and continue to contribute to the success of its customers.
achieve this, Muche Graphique regularly invests in modernising its production tools.
Personal Protective Equipment
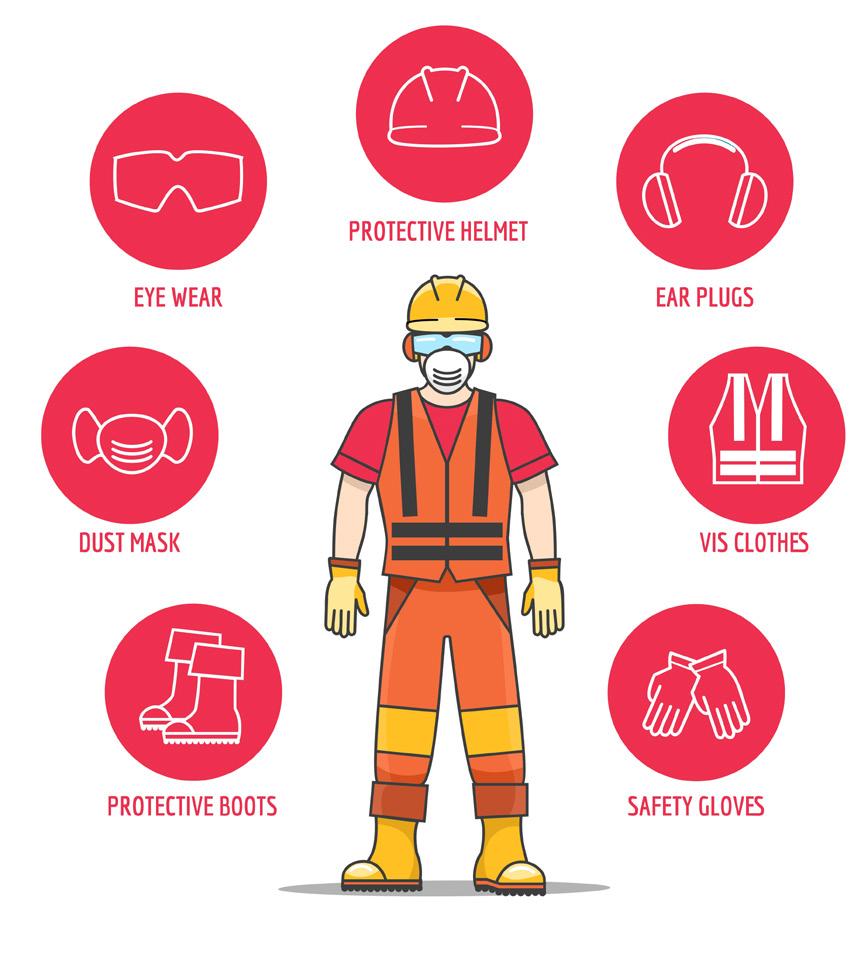
CONTACT:
DR Congo
128, Avenue Kasa”i, Quartier Makutano, Commune et ville de Lubumbashi
Information Line: +243 899 363 067
Zambia
567/3b Pelican Road makeni, Lusaka Zambia
Information Line: +260 971152 243
South Africa
129 Walton Rd, No. 2A Carlswald Estate Midrand, Johannesburg
Information Line: +27 66 314 6742
info@muchegraphique.com graphiquemuche@gmail.com www.muchegraphique.com
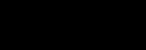
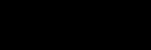
@muchegraphique
Printing Services
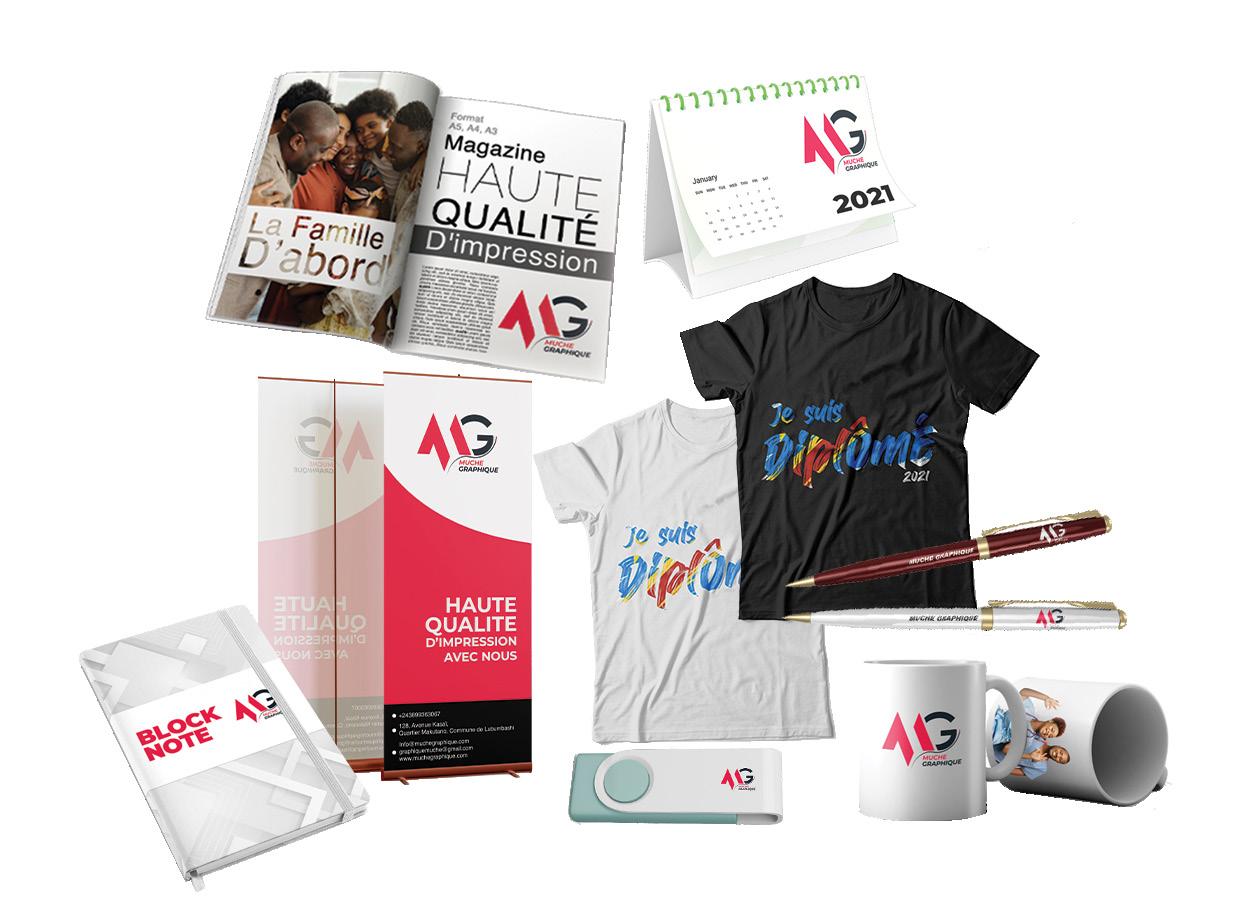
THE MUST COLLECTION
We speak to executive members of renowned dust management solutions provider and equipment manufacturer, Grydale, about the company’s innovative equipment, sustainable operations, and continuous improvement
Writer: Rachel Carr | Project Manager: Eddie Clinton
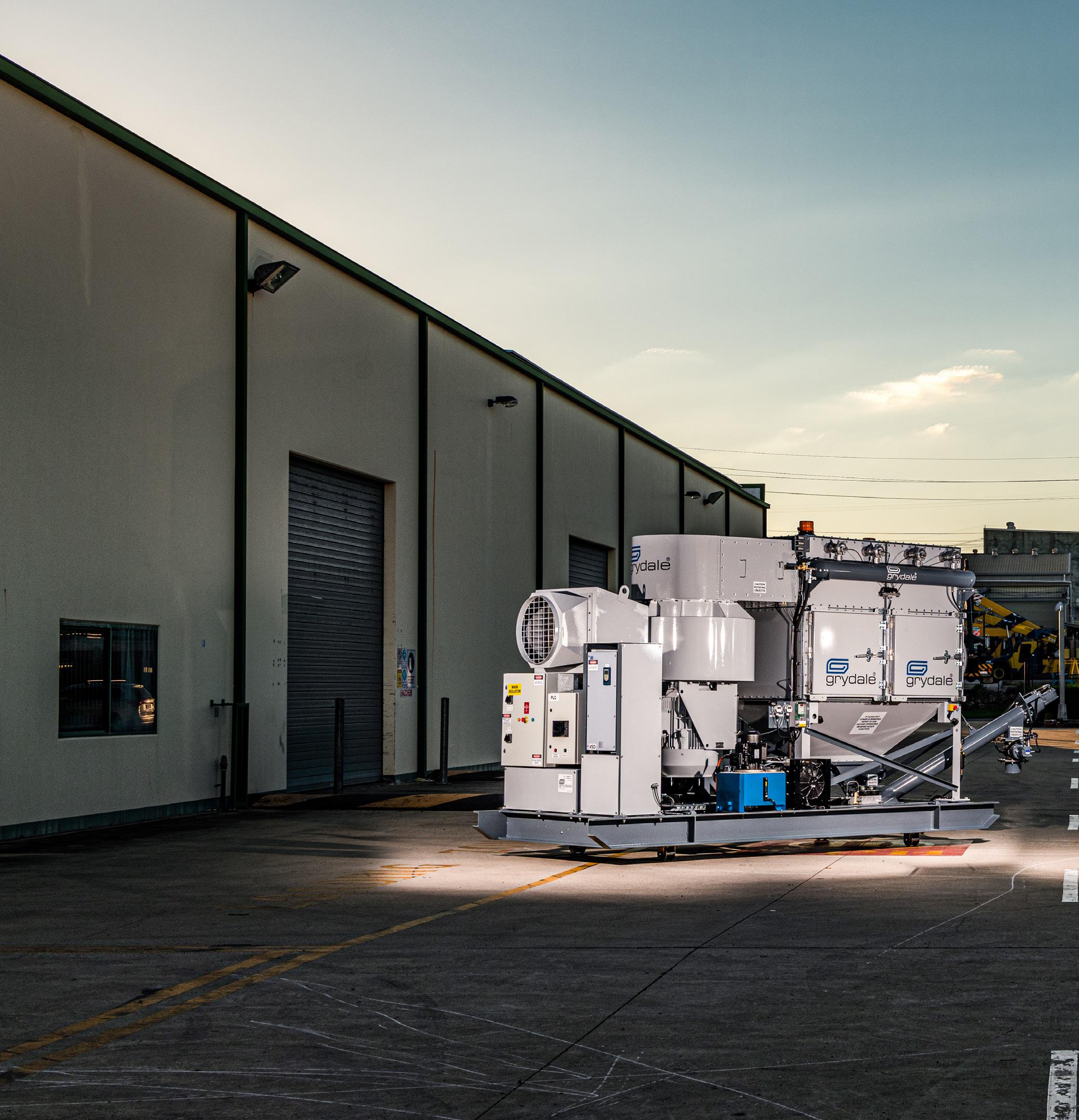
Mines are busy environments that use heavy industrial equipment, often creating dust clouds.
As health and safety experts focus on protecting workers, the demand for dust control solutions is subsequently increasing. Many industries face harmful dust
caused by dangerous minerals such as asbestos and crystalline silica, which can be inhaled during activities like grinding, drilling, cutting, or sanding –this is where Grydale excels.
Established in 2011, the company specialises in engineering, manufacturing, and servicing a range of fixed, mobile, and onboard
industrial dust collection equipment.
Grydale’s patented technologies effectively control dust and airborne contaminants in a range of industrial applications, including tunnelling, mining, quarrying, and air quality management in factories.
“Thanks to our proprietary technology, Grydale’s dust collectors
FOR DUST COLLECTION
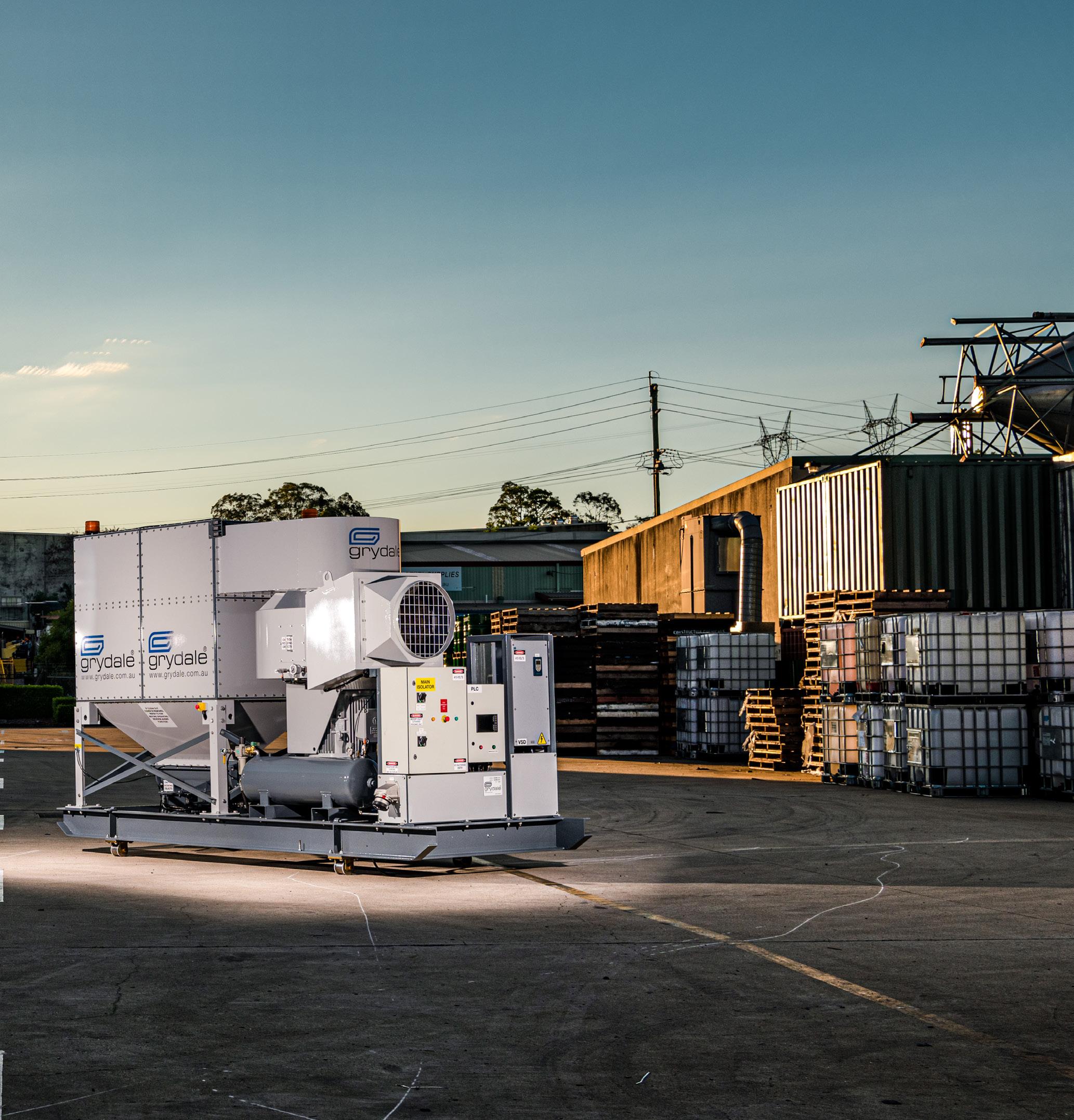
have gained a reputation worldwide. They are transforming how dust extraction processes and ventilation design are approached across various industries and projects,” opens Alex de Andrade, CEO of Grydale.
The company distinguishes itself in the market with protected intellectual property that meets the
most stringent air quality standards mandated within major projects and has built a strong portfolio for fixed, mobile, and onboard dust solutions.
“This provides a significant and sustainable competitive advantage within the global dust control market,” adds General Manager of Sales, Adam Wallace.
The company is further looking to invest in independent air quality monitoring technology, providing certified evidence of air quality and filtration efficiencies as it maintains an unwavering commitment to continuous improvement and innovation to keep ahead of global air quality regulations.
“Our patented technology has allowed us to deliver solutions to dust challenges that were previously not possible. This, combined with our passionate team, supplier parts selection, and manufacturing and quality processes, are the attributes that truly set us apart in the market.
“We select and test the best available parts for our machines to have maximum uptime and this attests to the support we get from our longstanding suppliers on a 24-hour basis,” de Andrade prides.
STRINGENT SAFETY STANDARDS
The risk of dust-related diseases increases with exposure levels, therefore, workplace health and safety legislation now requires strict dust management and diesel particulate matter (DPM) control through permissible exposure limits (PEL) and workplace exposure limits (WEL).
Regulations are periodically reviewed and updated to reflect current scientific evidence linking exposure to disease.
“Our dedicated engineers and artisans are committed to continuous improvement, with a strong focus on eliminating waste and minimising safety risks,” urges de Andrade.
Silicosis is the most common occupational lung disease worldwide and is often referred to as the modern-day asbestos.
“By adopting Grydale’s advanced dust control methods, companies can protect their workers, comply with regulations, and enhance overall operational efficiency,” de Andrade suggests.
Grydale is rapidly building a robust reputation for driving up industry standards with its safe and efficient dust extractors as accountability and compliance regulations relating to health and safety within the
construction industry are continually tightened.
The extremely high safety standards set by the company extend to its own team, who are willing to enact the exact level of caution for co-workers, family, and friends, as well as the next generation.
“With our dedication to ISO 14001 compliance, we handle the washing of our machines and returned rental units with the utmost care. The same way we protect the operators servicing our machines from any exposure, we do likewise for the environment and neighbours,” de Andrade assures.
Grydale believes there is always a safer and cleaner way of doing any task, accordingly, it retains all washed water and slurry in contained bunded areas and recycling tanks, disposing of the contents through certified waste handling companies.
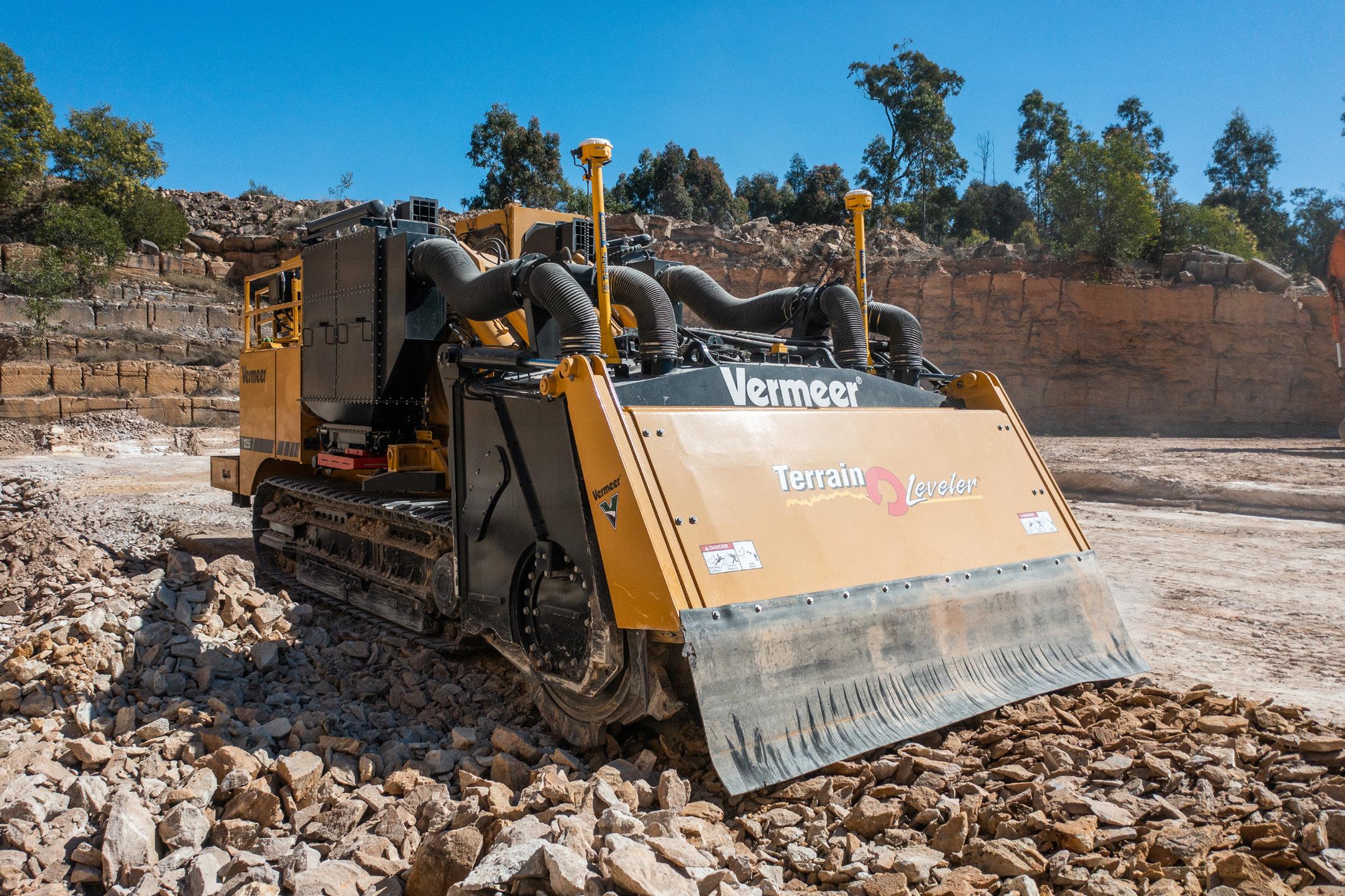
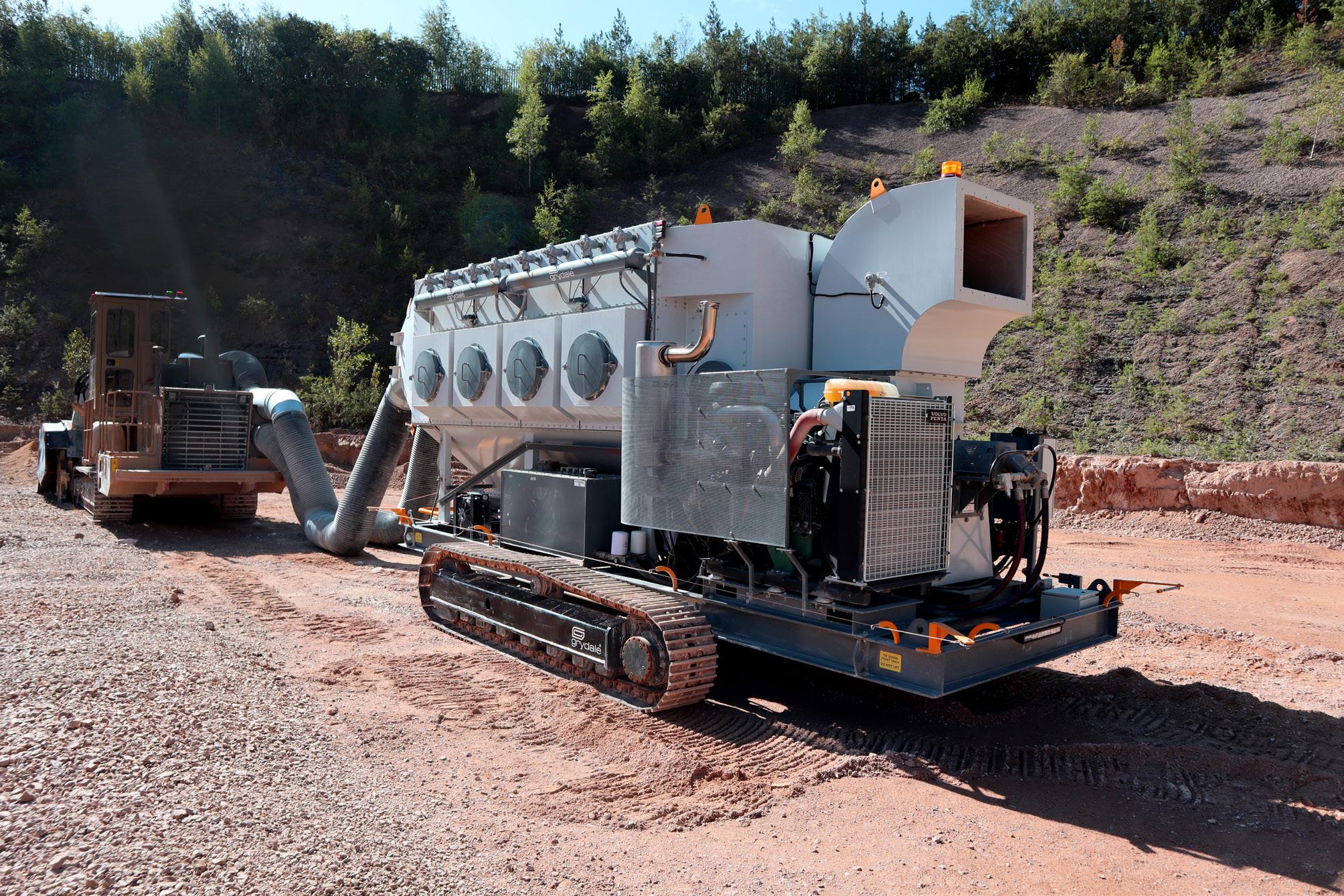
“OUR INTELLECTUAL PROPERTY IS PATENTPROTECTED AND MANUFACTURED WITH THE HIGHEST QUALITY CONTROL STANDARDS AND THE BEST COMPONENTRY FOR EACH APPLICATION”
– ALEX DE ANDRADE, CEO, GRYDALE
“There is no compromise for protecting the most amazing part of the country around us in the Moreton Bay region,” de Andrade affirms.
A TEAM UNITED BY DEDICATION
Employees are drawn to Grydale’s strong culture and ethical principles, which prioritise safety by eliminating risks and providing a safe working environment.
The company currently has staff across Australia, the US, and Canada, with service contractors and spare parts also in the UK, New Zealand, and Saudi Arabia. It also has plans
to expand its consignment and field support within the UAE, Hong Kong, and Europe.
“Our dedicated field service technicians work closely with clients to provide routine and preventative maintenance schedules, ensuring maximum machine uptime and optimising our solutions’ operational efficiency,” shares Jamie Baskett, General Manager of Field Service.
“We understand that dust control solutions are often critical parts of operations, so our service team works closely with our warehouse and procurement teams to ensure stock of
essential spare parts and service items is available to our customer base when required as part of our worldclass customer and service support.”
To enable efficient and timely operations, Grydale’s team utilises advanced, state-of-the-art equipment.
“Our in-house team of engineers and designers use advanced 5D building information modelling (BIM) and computer-aided design (CAD) with material property metadata, integrated into our enterprise resource planning (ERP) procurement system, to create bills of materials and drawings for production,” de Andrade expands.
As Grydale transitions from a 15-year-old family-owned business to a shareholder-owned entity with an investment for steady longterm growth, some manufacturing workflow changes have been necessary to meet customer demands and lift the service deliverables in full and on time.

A.T. Hydraulics:
The preferred hydraulics supplier to leading equipment manufacturers Australia wide

A.T. Hydraulics Pty Ltd is an Australian owned company established in 1990 to service the Australian fluid power market. With branches located in Sydney, Perth and South of Brisbane the company is well situated to offer servicing and support for the entire Australian market on its range of exclusive products.
All our factories are well equipped with full machining and service facilities backed by our highly qualifed sales, workshop and engineering staff. Whether you need components, repairs, service or an entire hydraulic system, we can deliver. We are dedicated in providing complete customer satisfaction. With our exclusive product ranges and distribution of some of the world’s leading brands we can offer our customers a single source of hydraulics.
Complete Hydraulic Solutions: Power Pack Design, Fabrication, Installation & Commissioning: Your Trusted Partner for Precision Hydraulic Systems
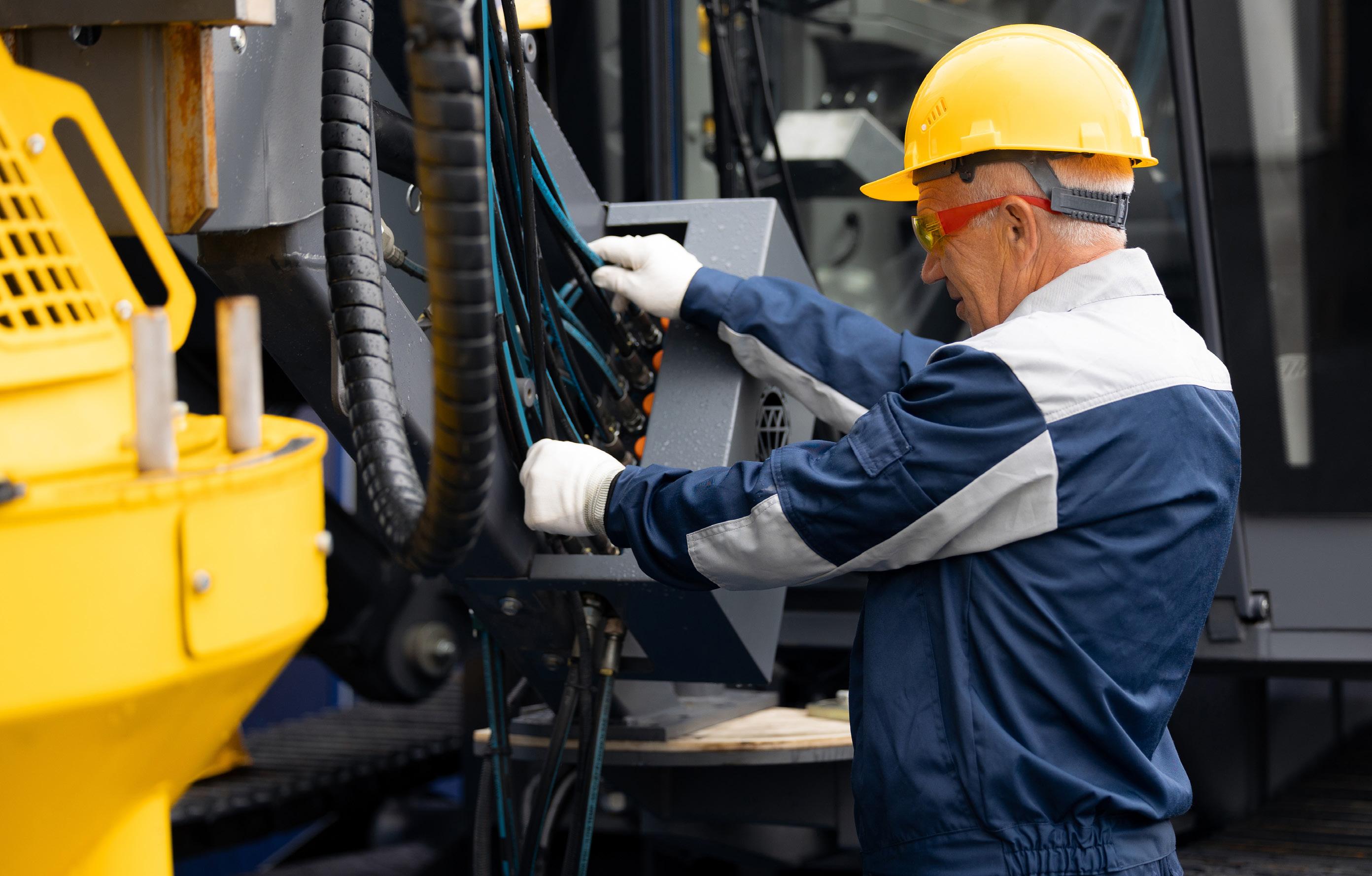
At A.T. Hydraulics, we specialise in delivering complete hydraulic solutions tailored to your project’s unique needs. From initial design through to fabrication, installation, and commissioning, we ensure your hydraulic systems are powered, optimized, and ready for peak performance. With years of expertise across a broad range of industries, we are proud to provide high-quality hydraulic power packs designed to meet the demands of the most diverse sectors.
Our Expertise in Hydraulic Power Packs
Whether you need a simple,
compact unit for a small-scale application or a complex, heavy-duty system for industrial use, A.T. Hydraulics offers comprehensive hydraulic power packs for a wide range of sectors. Our custom-designed systems ensure efficiency, reliability, and flexibility, no matter the scope of your project.
Industries We Serve: Manufacturing & Industrial Automation
Hydraulic power packs are essential for industries relying on automation and heavy machinery. We design systems that integrate seamlessly with manufacturing processes to
improve productivity, precision, and consistency. Whether it’s for assembly lines, presses, or conveyors, our solutions deliver the power you need for highdemand operations.
Mining & Heavy Equipment
The mining industry requires robust, high-performance hydraulic systems for demanding environments. Our power packs are built to withstand extreme conditions, offering reliable operation in mobile equipment, drilling rigs, excavators, and more. A.T. Hydraulics ensures your mining equipment operates smoothly under even the most challenging circumstances.
Design, Systems
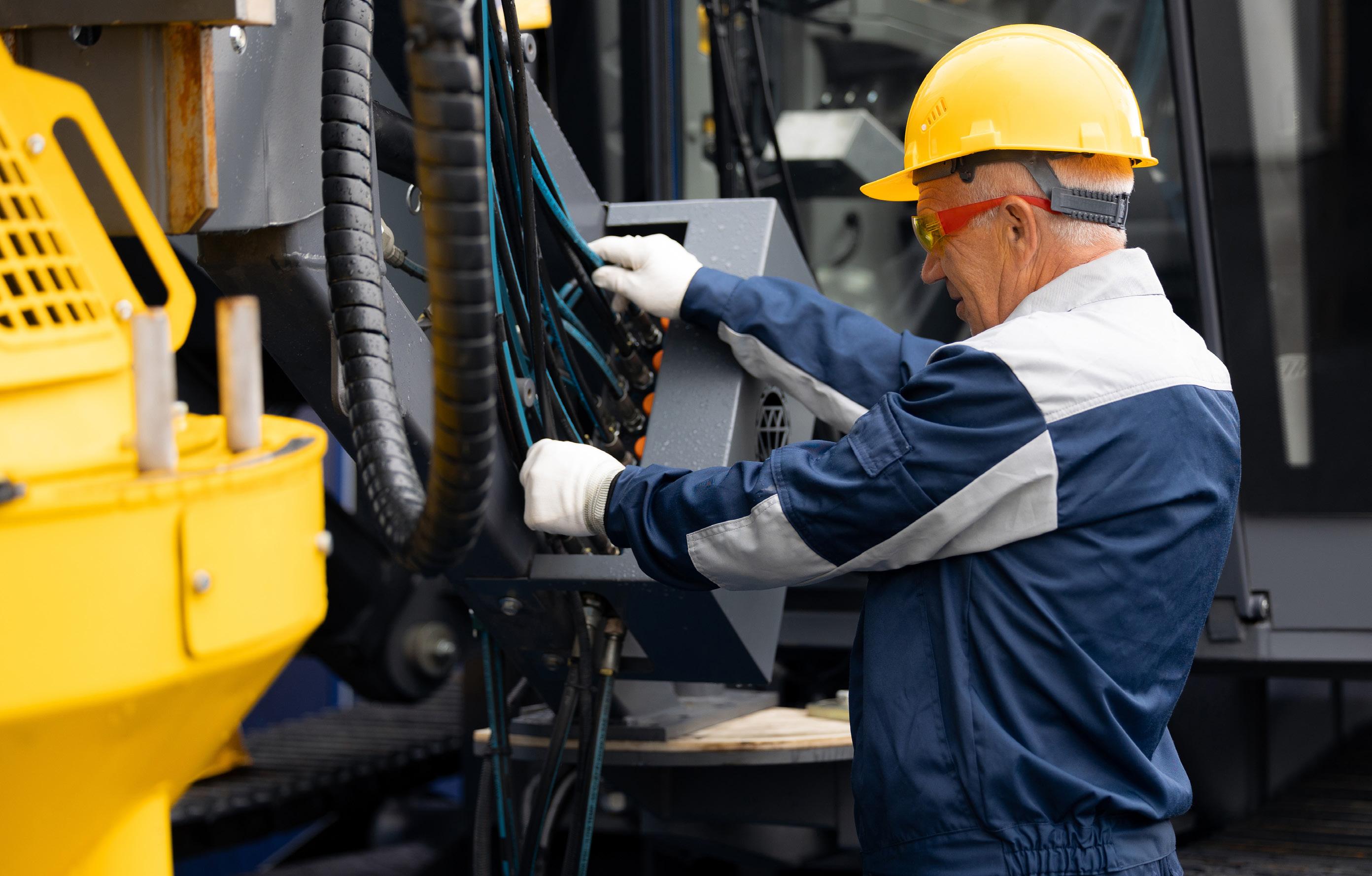
Construction & Civil Engineering
Hydraulic systems are crucial in the construction industry, driving cranes, excavators, and pile drivers. A.T. Hydraulics designs durable, efficient power packs tailored for the construction sector, ensuring that your equipment is reliable and ready for use at any project site, from small builds to largescale infrastructure projects.
Oil & Gas
In the oil and gas sector, hydraulic power packs are pivotal for offshore platforms, drilling operations, and refining equipment. We design high-performance,
corrosion-resistant systems that meet the industry’s strict standards for safety, reliability, and efficiency, ensuring that critical operations can continue uninterrupted.
Agriculture & Farming Equipment
Hydraulic power packs play a vital role in modern farming, powering machinery such as harvesters, planters, and irrigation systems. Our designs are focused on providing reliable, cost-effective systems to support efficient farming practices and maximize productivity.
Marine & Offshore
From vessel deck machinery to offshore rigs, hydraulic systems are indispensable in the marine industry. A.T. Hydraulics engineers power packs designed for extreme marine environments, offering exceptional durability and performance for ship lifts, winches, and other essential systems.
Automotive & Transport
Hydraulic systems are widely used in the automotive industry for tasks such as testing equipment, jacking systems, and vehicle lifts. We provide power packs that ensure smooth, efficient operation for both production lines and repair facilities, optimizing workflows across automotive operations.
Power Generation & Utilities
Our hydraulic power packs are also designed for use in power plants, utility services, and renewable energy projects. Whether it’s for turbine maintenance, energy storage systems, or hydraulic dampers, we supply high-efficiency solutions that support the stable operation of critical infrastructure.
Why Choose A.T. Hydraulics?
Tailored Design: We work closely with you to understand your specific requirements, ensuring each hydraulic power pack is custom-designed to meet your unique needs.
Precision Engineering: Our systems are designed for optimal performance, energy efficiency, and long-term durability.
End-to-End Service: From consultation to design, fabrication, and final commissioning, A.T. Hydraulics provides a comprehensive service to ensure smooth project execution.
Expert Installation & Commissioning: Our experienced technicians handle every aspect of installation and commissioning, ensuring that your hydraulic power pack functions at its best from day one.
Quality Assurance: We only use premium materials and components, and all our systems undergo rigorous testing to guarantee reliability and performance.
Get in Touch Today
Whether you’re working on a large-scale industrial project or need a compact solution for specialized equipment, A.T. Hydraulics is here to provide the hydraulic power packs you need. Contact us today to discuss your requirements and how we can help streamline your hydraulic operations.
Sydney 1300 760 531
Brisbane 1300 760 531
Perth 1300 760 531

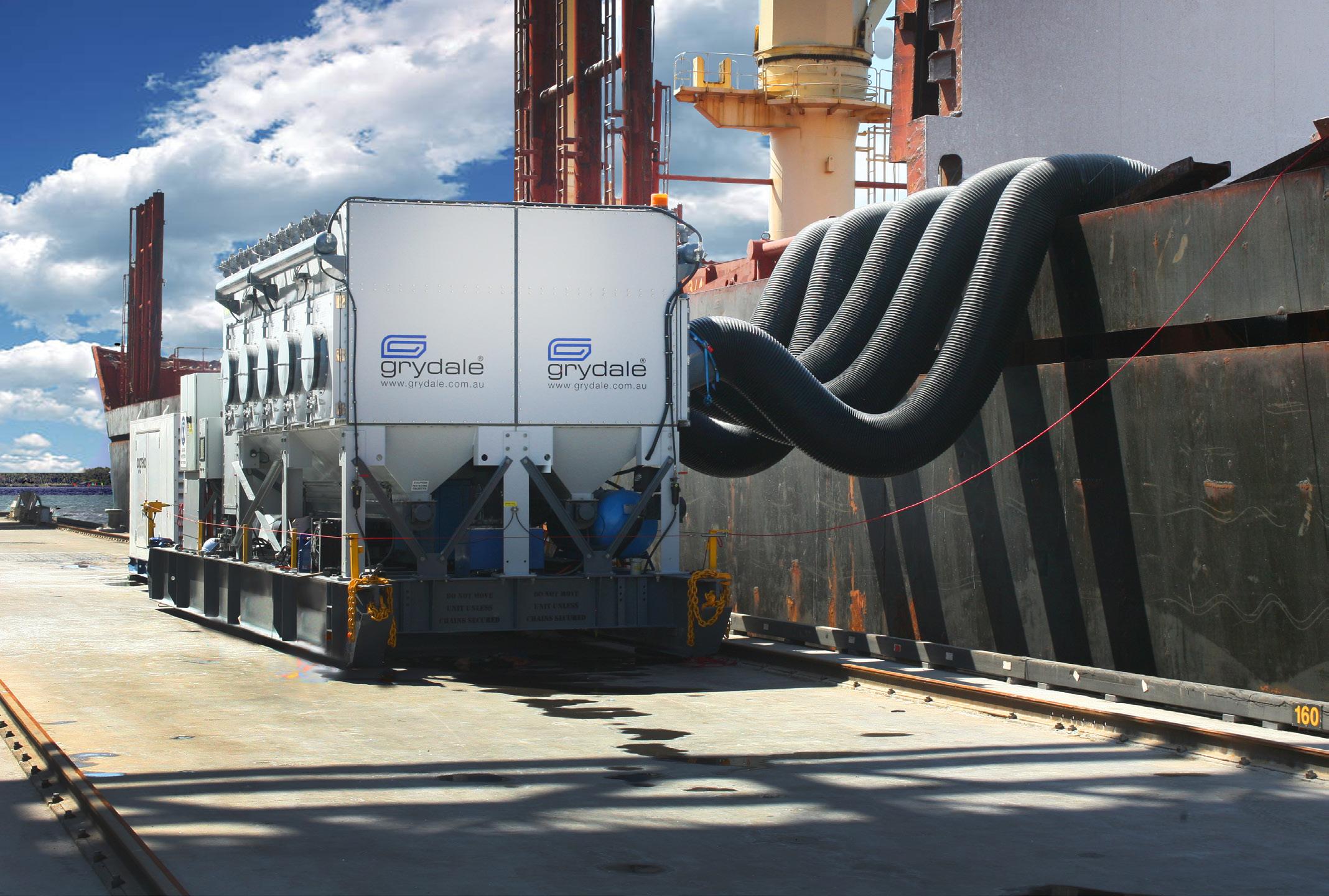
Under challenging product specifications, the founding team and owner moved the company forward to a formidable original equipment manufacturer (OEM) brand that has proven itself in the market.
“Our shift to a multi-national structure aims to build a foundation for scalable growth whilst retaining agility. As a result, the focus moves from completing individual projects on schedule to a global model prioritising quality, consistency, and delivery on time,” acknowledges de Andrade.
Each machine must fundamentally be a replica of the one before it so that simultaneous, consistent technical support is possible on all machines worldwide.
“When customers request spare parts or performance support, we must ensure the as-built status and accuracy of the parts book, manuals, maintenance procedures, and troubleshooting guides cater for
MINING OUTLOOK: HOW DOES GRYDALE INCORPORATE SUSTAINABILITY INTO ITS OPERATIONS?
Andy Greenslade, COO: “In an era prioritising environmental responsibility, Grydale has earned ISO 14001 environmental standard accreditation, showcasing its commitment to sustainability. ISO 14001 is a globally recognised environmental management system that enables organisations to enhance their environmental performance through efficient resource use and waste reduction.
“Our dust extraction equipment tackles significant dust emissions in construction, mining, and manufacturing industries. Dust is managed at the source, improving air quality and ensuring safety compliance.
“We focus on energy efficiency and recyclable materials, helping clients meet sustainability goals whilst reducing their carbon footprint. Partnering with us enables clients to navigate environmental regulations and enhance their reputation and business opportunities.
“The company recognises aligning operations with global environmental standards is vital for fostering a sustainable future. Grydale’s focus on continuous improvement, staff training, and stakeholder engagement ensures that ecological considerations are integral to its business strategy. As organisations seek to meet carbon reduction commitments, our ISO 14001 certification reflects our dedication to environmental stewardship and contributes to a cleaner, safer planet for future generations.”
global supply equivalent parts but sourced locally.
“Our business model ensures that field service teams or local contractors are available in-country, maintaining strong face-to-face interactions and relationships, with routine monthly inspections of our rental fleet,” de Andrade notes.
Grydale is committed to developing people skills and succession as it grows, creating more opportunities for its employees.
In addition to apprenticeship and graduate programmes, Grydale offers advanced leadership training and sponsored tertiary education support for key roles like technical degrees and Master of Business Administration (MBA) programmes to improve service quality through training and retention.
“We are testing productivity and efficiency for four-day roster work
weeks in certain divisions, empowering a culture of completing the job correctly the first time and enabling us to try new rosters and lifestyle approaches,” de Andrade delights.
DESIGNED TO LEAVE COMPETITORS IN THE DUST
Grydale’s team ensures complete control over the design and manufacturing of dust control solutions, exceeding performance, safety, and environmental standards to create leading products in the market.
“Our approach involves customers in the process, which is beneficial. Engaging a multi-disciplined team in the design has often led to new ideas and allowed us to push the boundaries of what is possible,” Wallace insights.
The team aims to understand the holistic dust control challenge by
communicating with customers, visiting sites, exchanging documents, and evaluating key factors such as dust type, particle size, air volume, and industrial processes.
“Input from stakeholders, including project, plant, and operations managers, health and safety officers, and procurement teams, is essential. Their insights help us define project goals and find effective solutions, making every team member a vital part of the process,” Wallace emphasises.
Production begins when designs are finalised, with the company using a triple ISO certification platform, namely ISO 9001 Quality, 14001 Environment and 45001 Safety accredited quality control process.
Utilising LEAN principles and semiautomation, the company produces both standard and customised equipment, achieving a 94 percent on-time delivery rate.
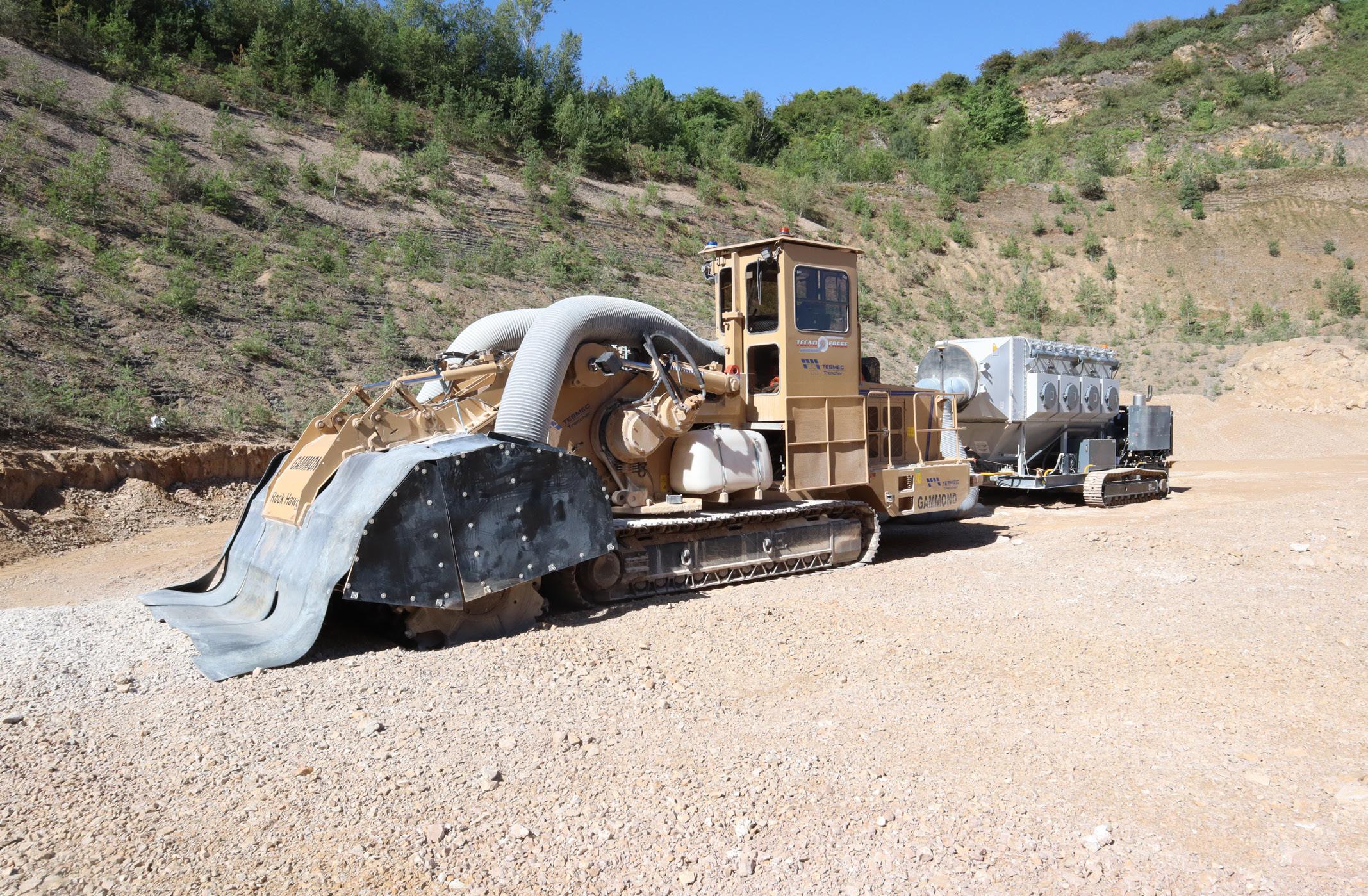
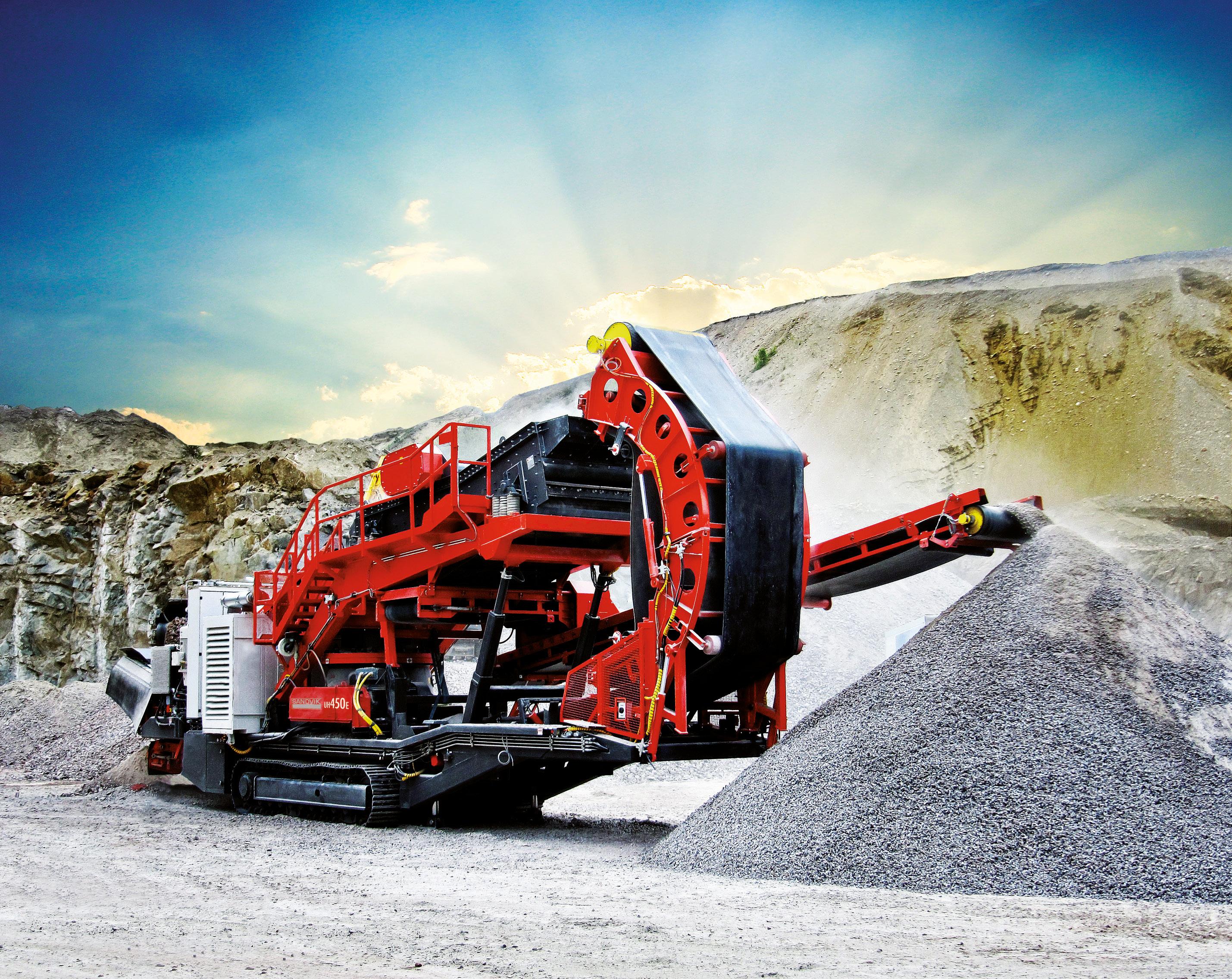
POWER AND PARTNERSHIP YOU CAN DEPEND ON
At Volvo Penta, powerful industrial solutions and strong partnerships drive success. From optimising your application to providing global dealer support, we are committed to assisting you. With cutting-edge technology shared across the entire Volvo Group, our innovations are shaping the future of industrial power systems.
Industrial and Power Generation Engines
Volvo Penta’s engines deliver high
performance, are powerful and reliable, and are fuel efficient. Designed for versatility, they feature a low-weight, compact design for easy installation, and optional equipment packages make them ideal for a wide range of machine and equipment applications and industries.
Our engines power applications in construction, agriculture, underground mining, dewatering, port handling, drilling, crushing, and power generation, ensuring dependable performance in demanding environments.
Volvo Penta’s off-road diesel engines can be configured as either stand-alone units or mounted on robust base frames in a power pack configuration, featuring our renowned heavy-duty cooling packs and high-dust intake systems, complemented with an extensive offering of accessories including power take-offs, air-conditioning, and air compressors. Our impressive complement of engine models range from 105 to 585 kW / 140 to 785 hp - this makes our engines the perfect fit for your industrial power application.
Commitment to Sustainability
Volvo Penta is dedicated to meeting and exceeding global emissions standards, ensuring you a power solution which is compliant with global emissions regulations. Our engines share a common base platform and are certified for hydrotreated vegetable oil (HVO) fuel. Volvo Penta also offers dualfuel engines capable of running on a mix of 80% Hydrogen / 20% Diesel and we continue to explore renewable fuel options, including natural gas and 100% Hydrogen.
Beyond traditional combustion engines, Volvo Penta is pioneering with innovative electric driveline technology for the diverse and evolving needs of industries. Leveraging Volvo Groups proven expertise, we have successfully integrated electric solutions into a variety of industrial applications.
Our Battery Energy Storage System (BESS) leads the market - enhancing energy reliability and sustainability by storing surplus electricity, often from renewable sources of wind and solar, providing a solution for backup power or cost optimisation.
Total Cost of Ownership and Unmatched Support
Volvo Penta diesel engines are designed to maximise uptime and productivity, safeguarding operations the world over. Our reliability and performance ensure your operation can deliver. Paired with our extensive aftermarket support, we keep your business running day in, day out.
In Australia, our global parts distribution network and over 65 dedicated Service
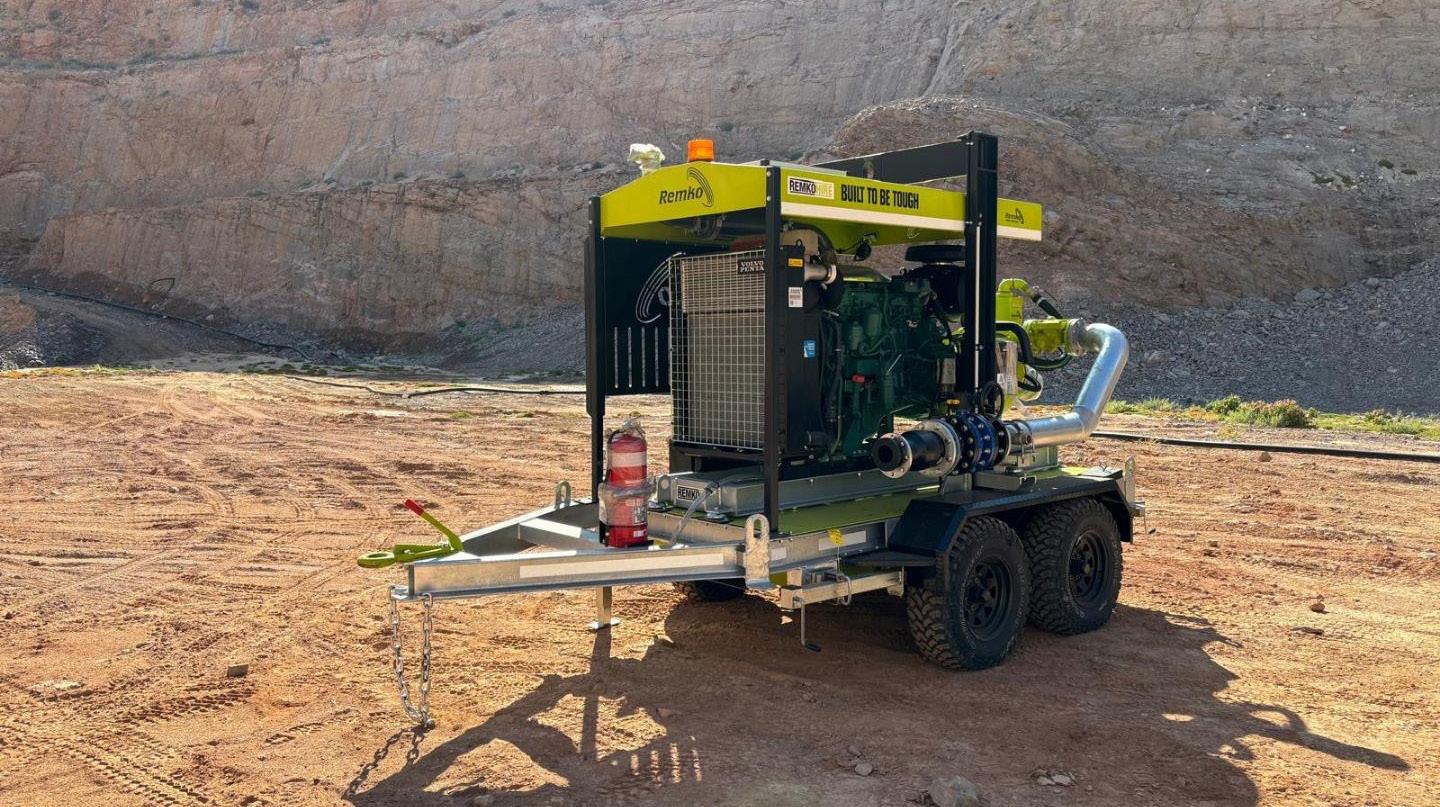
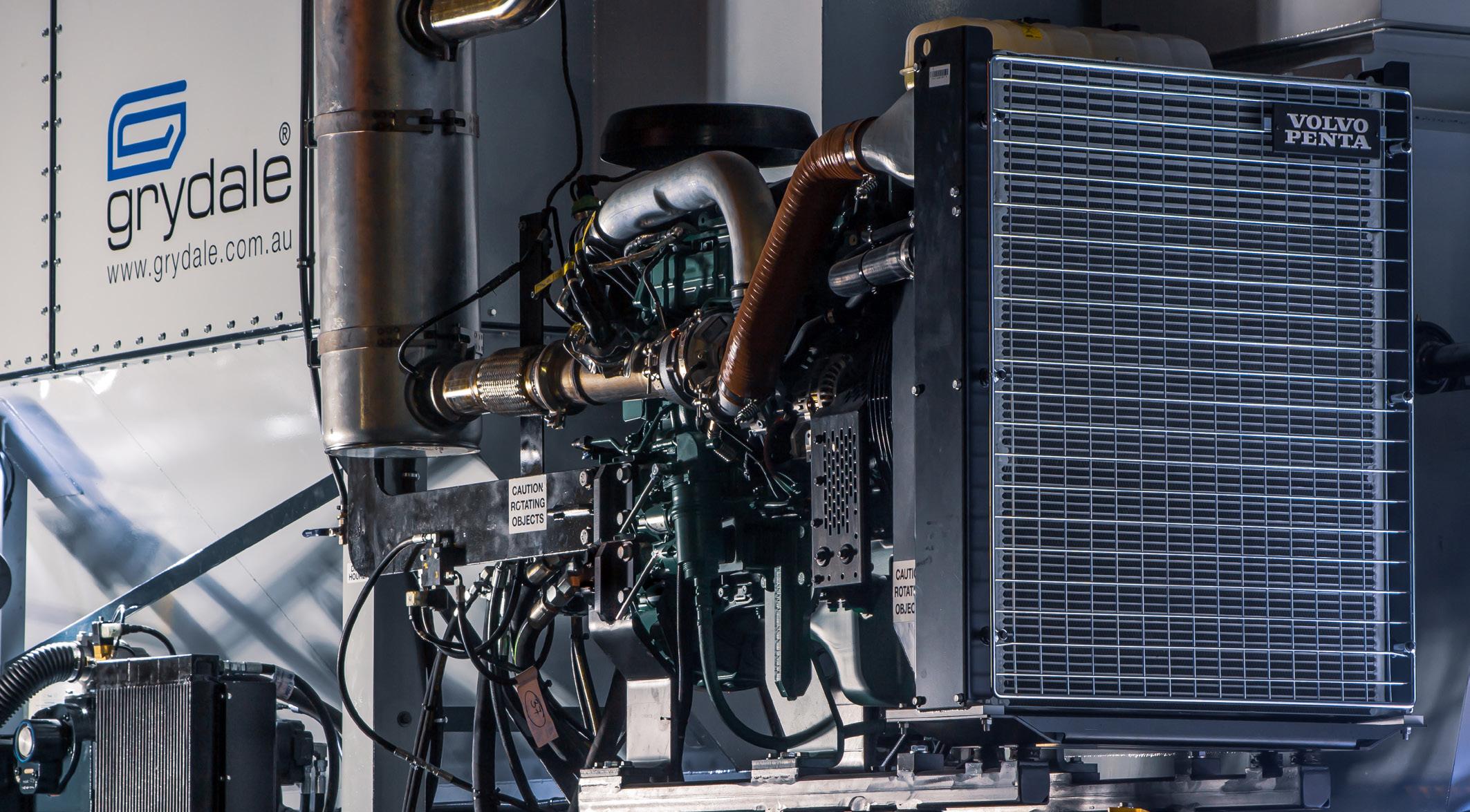
Dealers ensure around-the-clock service. Operators benefit from extended service intervals of up to 1,000 hours and are backed by Volvo Penta’s comprehensive engine and parts warranties.
Supporting Australian OEMs with Cutting-Edge Solutions
Volvo Penta’s Australian distributors are trusted sales, service, and support partners.
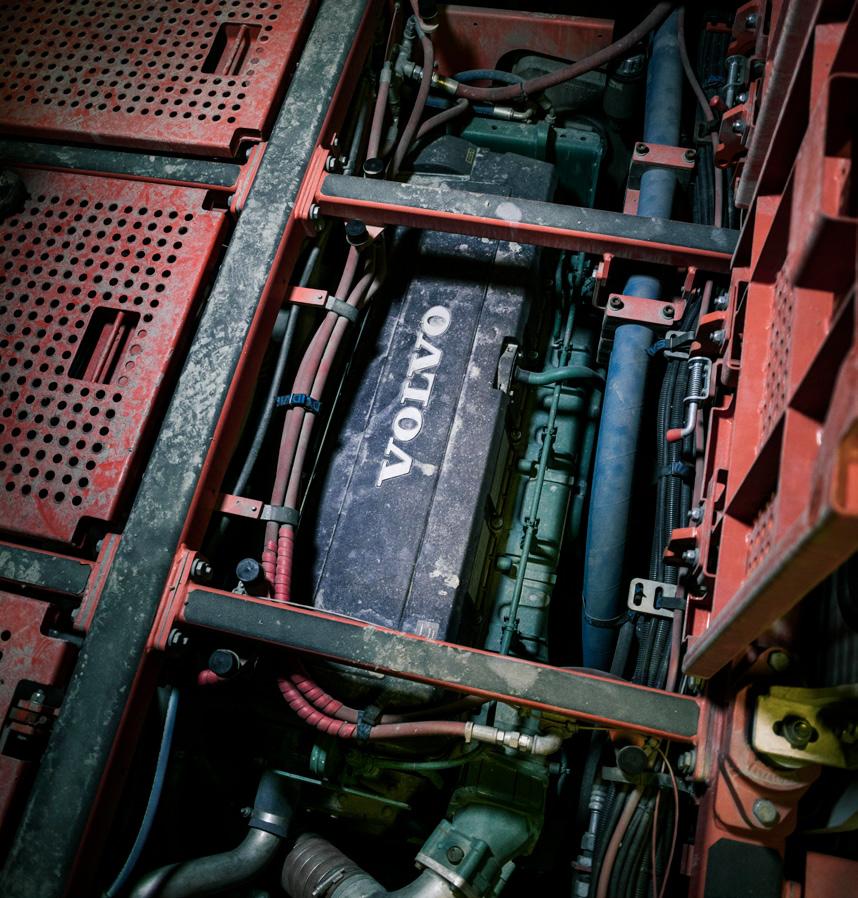
In Queensland, the Distributor Seamech has partnered with Grydale, Australia’s leading manufacturer of dust collectors and ventilation systems. Grydale required a heavy-duty engine that met stringent Tier 4 Final emissions standards. Through the collaboration with Seamech, Grydale became the first Australian machinery manufacturer to integrate Volvo Penta’s Tier 4 emission-reducing engines in local machinery production.
This successful partnership between Grydale and Seamech has resulted in nearly 100 locally produced machines equipped with Volvo Penta engines. Seamech continues to support Grydale’s operations with access to diagnostic tooling, extensive parts inventory, and 24/7 support.
In neighbouring New South Wales, the Distributor Fenquin has partnered with Jacon Equipment, a leading manufacturer of underground mining and construction equipment. Jacon now offers Volvo Penta’s 8-litre 235kw Tier 4 final engines in its MaxiJet, WaterJet, and JSV3 vehicles.
As a leading global supplier of
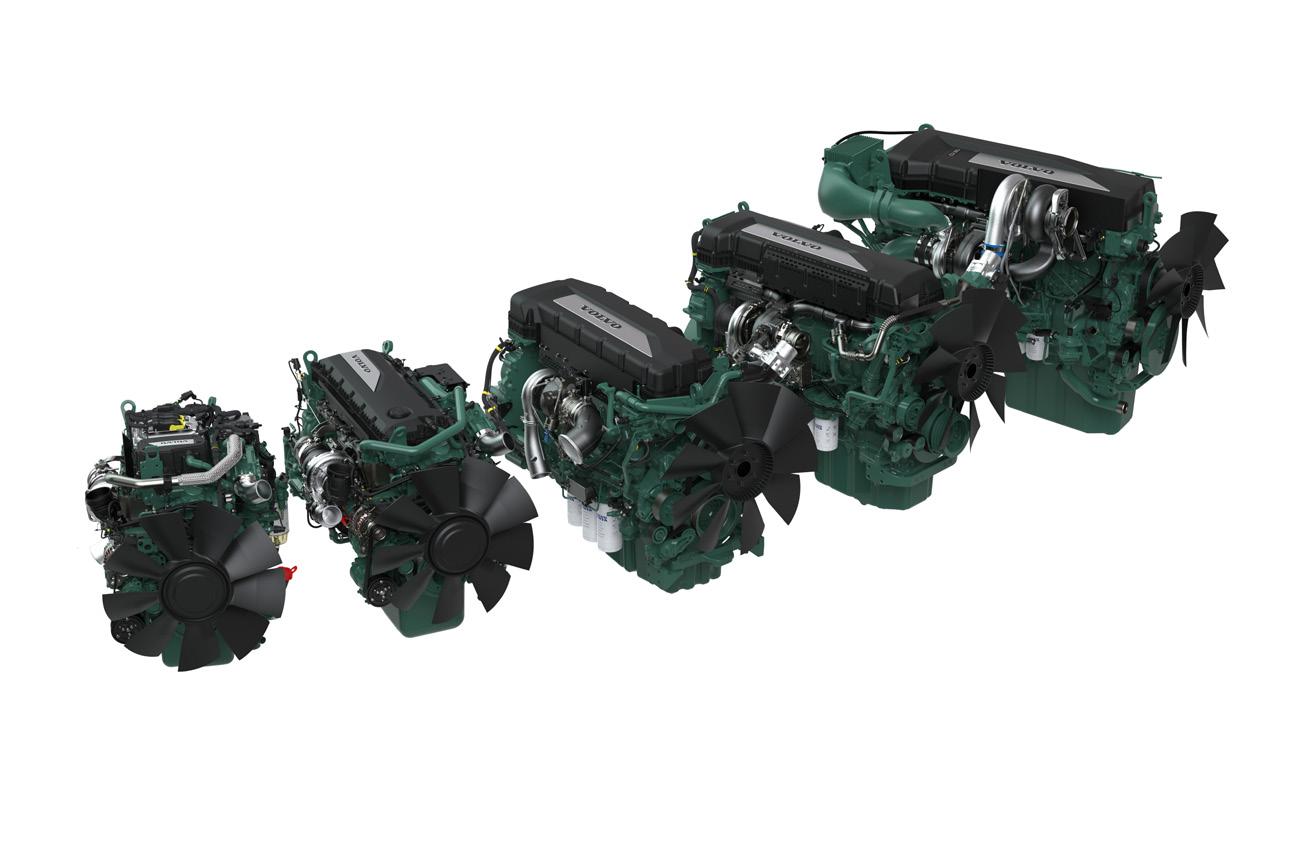
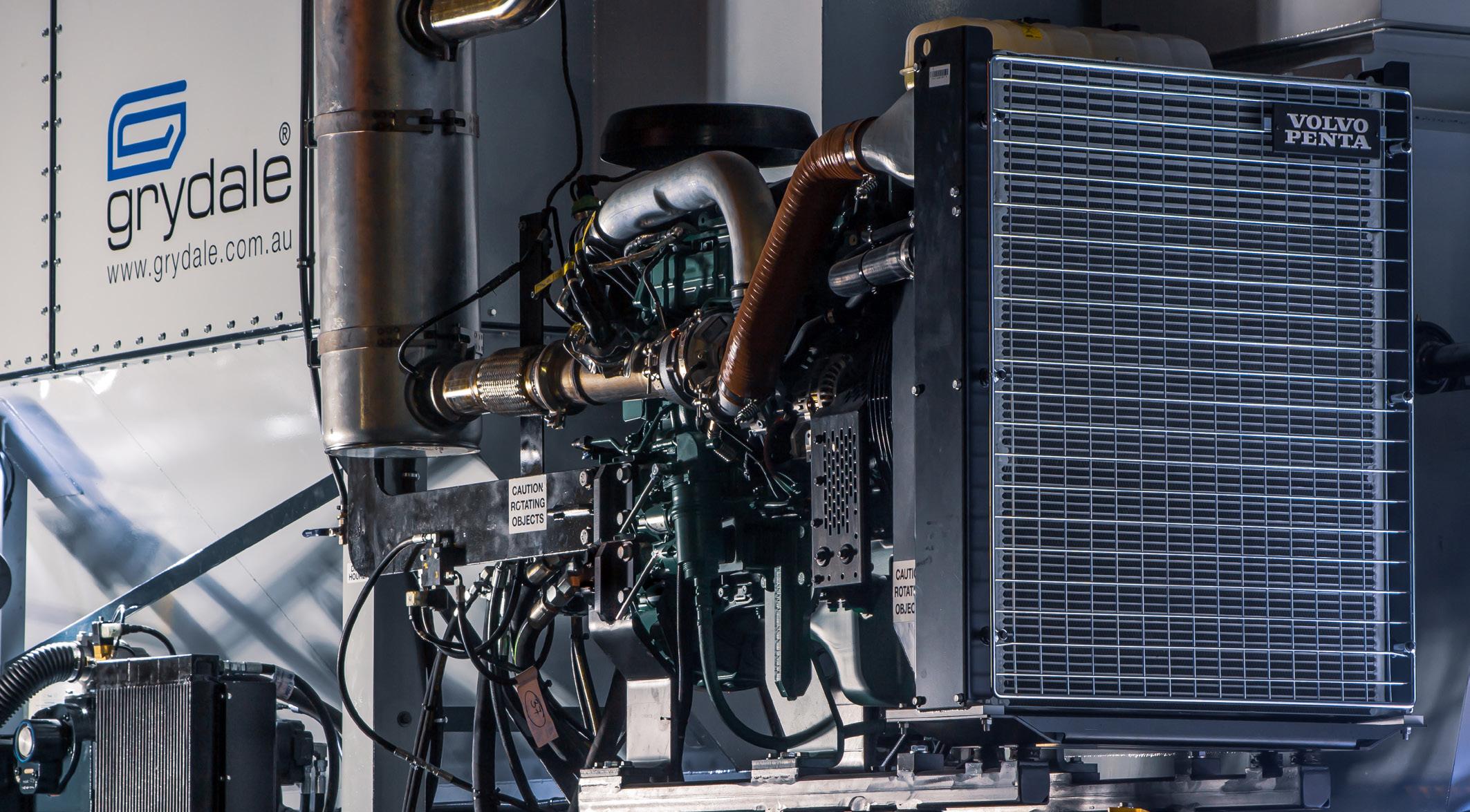

underground mining engines, Volvo Penta’s strong presence and experience with global OEMs in these harsh environments provided Grydale and Jacon with confidence in their chosen engine solution. This was particularly important considering the extreme conditions, with high dust, heat, and difficult access often endured by their machinery. Volvo Penta’s heavy-duty engines proved the perfect match.
Powerful Partnerships
Volvo Penta’s Australian distributors are committed to partnering with you to power your business. From project inception to operation, our in-house application support, technical expertise and industry experience ensure the right engine for your needs, backed by unparalleled, dependable local
support for you, your business, and your customer.
For more information or to find your nearest dealer, visit volvopenta.com.
Queensland: Seamech (07) 3890 7615 www.seamech.com.au
New South Wales: Fenquin (02) 9605 5522 www.fenquin.com.au
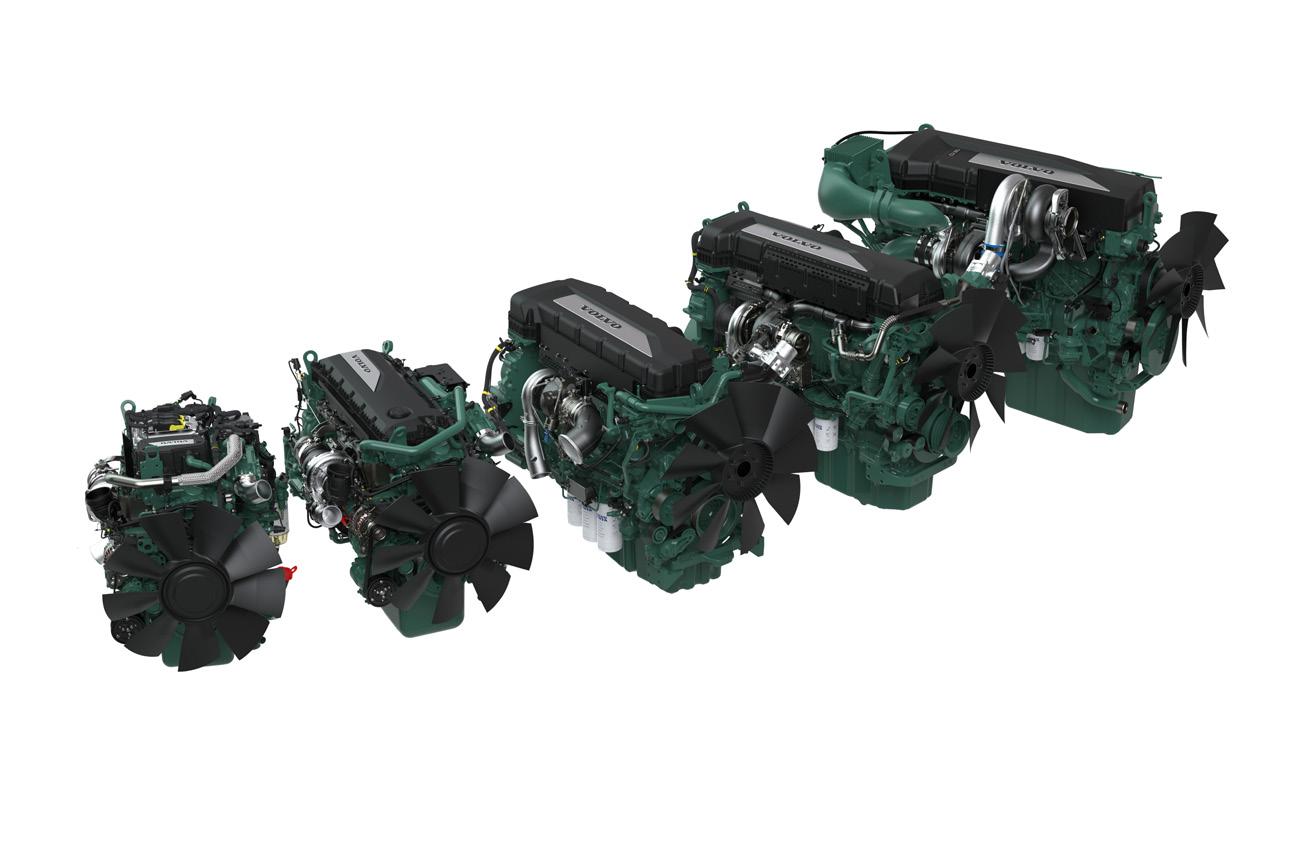
Victoria: Industrial Power Systems (03) 8353 0400 www.industrialpowersystems.com.au
South Australia: Don Morton (08) 8347 0011 www.donmorton.com.au
Western Australia: Ches Power Group (08) 6144 3111
www.chespower.com.au
“Our fabrication facility has its own world-class laser cutting, bending, and pressing machines, which allow us to be in control of quality and reduce manufacturing lead times,” de Andrade elaborates.
In-process inspections and tests are performed at each stage of the manufacturing cycle, ensuring adherence to specifications and reliable final designs.
“After installation, performance is monitored when equipment is operating and feedback is sought from site personnel to optimise the solution further and inform future improvements, fostering a cycle of continuous innovation,” outlines Andy Greenslade, COO.
Grydale also has a fleet of rental equipment, which has opened up new market opportunities where there are short-term or temporary dust control requirements. Rental equipment has also supported major infrastructure projects with out-of-sequence and subcontracted temporary works.
“There should be no reason why an employer isn’t trying out our gear for a one-to-three-month rental trial and obtaining feedback from their work crew as to how much safer they felt the air quality was when they
were alongside a Grydale machine,” acclaims de Andrade.
TUNNELLING TO TRIUMPH
Grydale developed a patented, trackmounted mobile dust collector initially for underground use, enhancing efficiency in tunnel construction and transforming ventilation and excavation methods.
Dust collector supply contracts in Australia quickly followed, with major contracts for Melbourne Metro, WestConnex Stage 3A and 3B.
In 2021, over 100 units operated underground for ventilation and dust control during tunnel excavation. Recently, they have also been used in major projects such as City Rail Link (CRL) in Auckland, Sydney Metro Central Station, HS2 in the UK, Neom in Saudi Arabia, the Western Sydney Airport Tunnel, M6 in Sydney, and Northeast Link in Melbourne.
Grydale has additionally worked on significant projects within the mining, quarrying, abrasive blasting, and ship loading industries.
The Melbourne Metro Tunnel project posed significant challenges for the ventilation design, such as space and noise constraints. However, Grydale overcame these by using
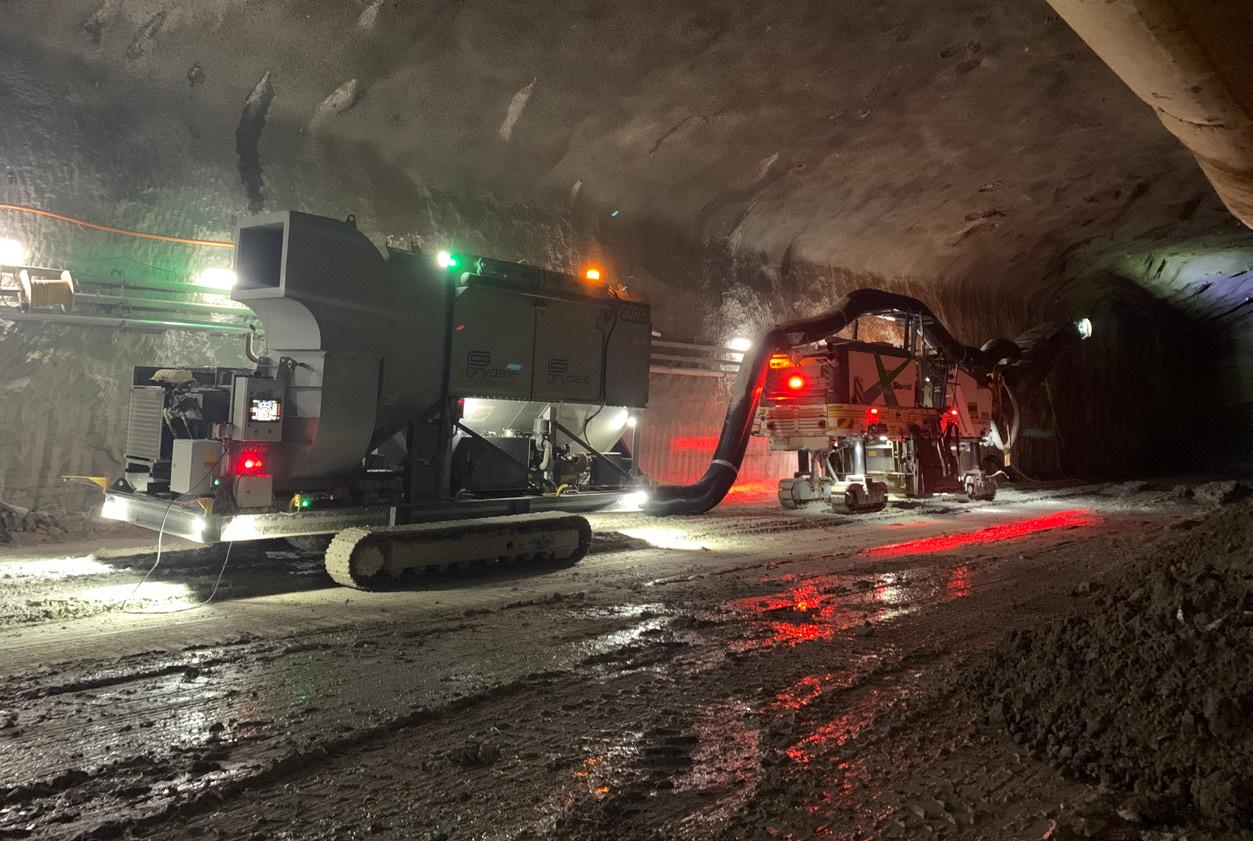

Ventsim Design 5.0 to simulate ventilation, airflows, pressures, heat, gases, radon, fire, and other critical factors.
The company’s approach was to implement an alternative ventilation design, using a full extract ventilation model, with dust collectors operating on the surface during the excavation of underground stations. This led to the design and manufacture of the largest airflow mobile dust collector available on the market – 60m3/s, 125,000 cubic feet per minute (CFM).
Elsewhere, Australia’s largest public transport project Sydney Metro, in the country’s most populous city, is expanding its network and increasing the frequency of trains. The upgrade of Central Station incorporated Grydale’s JMS-50-MES dust collector for ventilation and dust control during excavation works.
CRL, meanwhile, is New Zealand’s first underground rail line and largest transport infrastructure project.

GRYDALE’S STATE-OF-THE-ART EQUIPMENT
FIXED UNIT DUST COLLECTORS – JMS F-SERIES: This cost-effective solution controls dust, efficiently handling high-volume dust loads. Its modular design allows for flexible sizing based on airflow requirements. The engineering team uses site drawings to determine airflow needs and design the ducting for an effective dust control solution.
CUSTOM ONBOARD UNITS – Using the company’s expertise in dust control, Grydale has developed and patented a range of onboard dust control solutions for excavation equipment, including surface miners, large track trenchers, skid steers, and posi-track loaders.
The onboard dust control solutions are effective for dealing with residual dust and debris and offer a fuel, emissions, and labour-efficient solution when space constraints prevent using a trail-behind dust system.
Skid-mounted dust collection units are ideal for static dust generation scenarios. In contrast, internationally patented track-mounted units offer mobility, allowing them to move with dust generation processes or be used temporarily.
These track-mounted dust collectors are easy to transport and operate with minimal setup, eliminating the need for costly ducting. Powered by a diesel motor, they don’t require an external power supply, making it easy to relocate them during operation alongside dust-generating equipment. In addition, hybrid-powered track units support environmental and sustainability agendas.
Grydale designed a ventilation system for Karangahape Road, one of the main streets in the central business district (CBD) of Auckland, that uses negative pressure to draw air through the tunnel and expel it via ducting to the JMS-60-MES dust collector.
“We are also supplying units for the North-East Link tunnelling project in Victoria, including the JMS-60-MES with 1,000-volt harmonics and the JMS-30-MHT dust collectors. These solutions offer significant advantages for our customers and enhance our market position,” Wallace adds.
Grydale dust collectors have also provided effective dust control during major mine shutdown works, including demolition and relining of calciners and furnaces.
The use of dust collectors has helped to provide a clean and safe working environment for contractors and generate operational efficiencies. This approach is now being cited as industry best practice.

A STEP-BY-STEP GUIDE TO MOBILE DUST COLLECTORS
Grydale’s JMS M-Series of mobile dust collectors range in airflow from 12,000 CFM to 125,000 CFM and are available as diesel, electric, or hybrid solutions.
1. Air is pulled through the dirty air intake by the centrifugal fan.
2. Larger dust particles are separated from the air stream.
3. Dust is trapped on the filters, forming a cake on the surface as air passes through the filter house.
4. Reverse pulse filter cleaning system cleans the filters.
5. Dust particles are discharged from the machine via the augers and rotary valves.
6. The velocity probe monitors air speed and turns the centrifugal fan up or down to maintain air volume.
7. Clean air exhausts from the machine with a filtration efficiency compliant with international regulations.
NEW OPPORTUNITIES
Currently, Grydale has 16 units working in the Neom Tunnels in Saudi Arabia and is finalising a distributor agreement to provide additional local support for existing units operating and future sales into the UAE.
“This partnership will provide us with local sales, service, and support staff in a key growth region, where dust control regulations are rising in response to growing health, safety, and environmental concerns,” de Andrade assures.
The global tunnel construction market will continue to be a major focus for Grydale, complemented by its work in the mining sector in Australia and North America.
“To support our expanding customer base in Western Australia, we are selecting a location for a field service centre in the region. Facilities will hold consignment stock and inventory to provide spare parts and
rental equipment to better service the region,” de Andrade continues.
A SOLID STRATEGY FOR SUCCESS
In 2023, Grydale focused on diversifying its equipment for deeper mining applications by upgrading its CAD system and design database.
This allows machinery, such as laser cutting and bending equipment, to operate directly from CAD files, improving change management efficiency.
Grydale has also introduced a Remote Monitoring Service that provides access to key data on machines worldwide. This service helps customers and our team to ensure equipment is operating efficiently and optimised to maximise dust collection efficiency and machine up-time.
“At the same time, customers can use these parameters and reports for predictive maintenance, finding

“PARTNERING WITH GRYDALE OFFERS CLIENTS ADVANTAGES IN NAVIGATING STRINGENT ENVIRONMENTAL REGULATIONS AND ENHANCES THEIR REPUTATION AND BUSINESS OPPORTUNITIES
– ANDY GREENSLADE, COO, GRYDALE
faults, and keeping machines at optimal performance. In mid-2025, we will offer hands-on onboarding for operators using our equipment for the first time,” de Andrade reveals.
The second area of innovation is onboard dust control systems, where a kit is designed, manufactured, and tested by Grydale in collaboration with the customer or the OEM.
“The on-board systems reduce the need for an additional dust control unit to operate onsite,” de Andrade sets out.
The company is working with four partners on repeat business for skid
steers, and surface miners and large track trenchers.
“The onboard dust control solution for skid steers to manage dust when sweeping areas with silica sands is a game-changer,” declares de Andrade.
Alongside a two-year strategy to build a solid foundation for future growth, Grydale’s long-term plan is to expand and support loyal customers in North America and Western Australia.
“We have successfully increased production throughput capacity at world-class quality standards and have been acknowledged with our
triple ISO accreditation for those efforts.
“Our goal is to raise awareness of health and safety concerning dust and harmful respirable levels. By working with key industry sectors, we aim to create safer work environments, to allow people to return home safely and enjoy their jobs.


www.grydale.com.au
A FLUID OPERATION
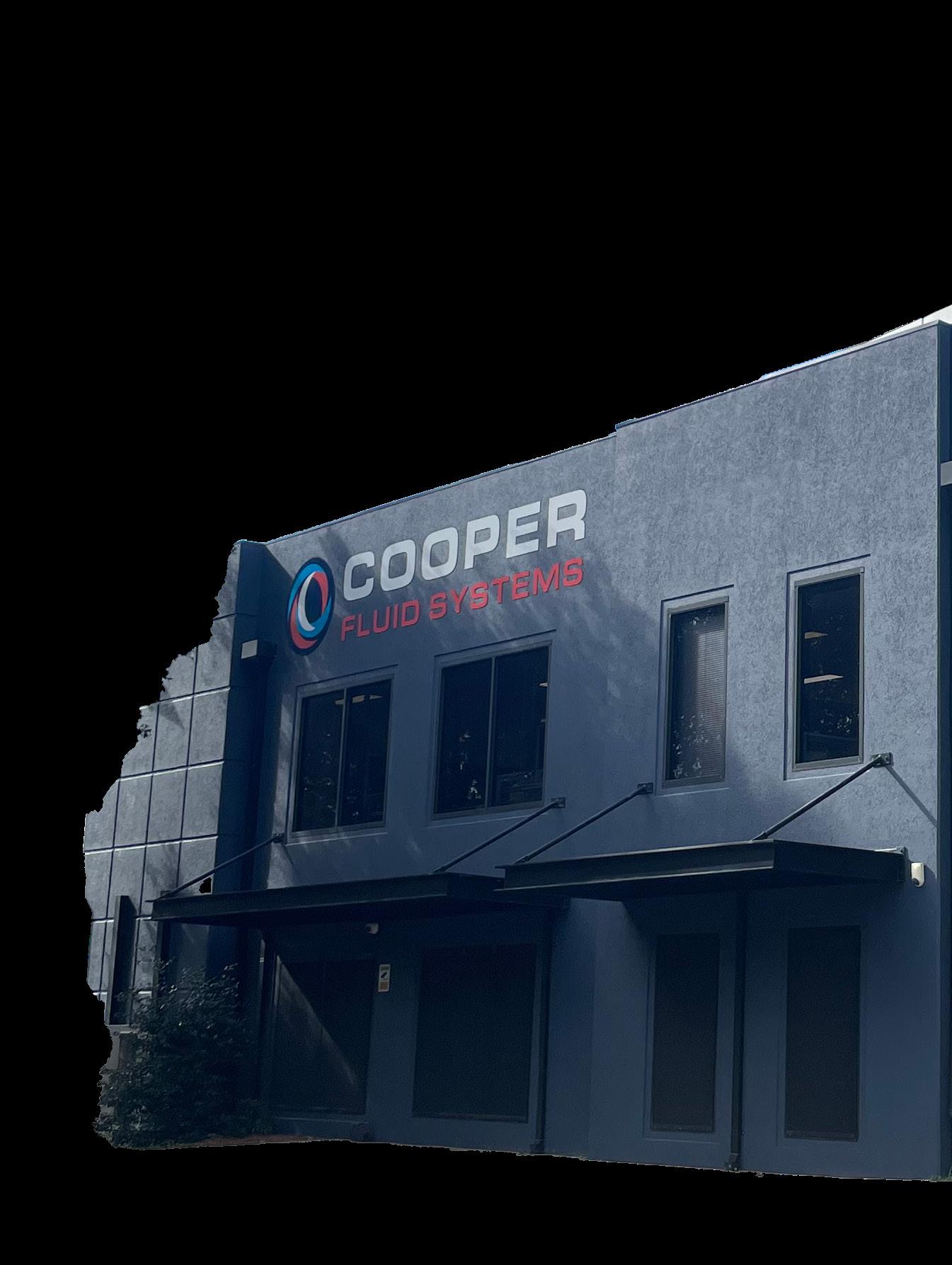
On a mission to be the leading supply and services group for Australia’s hydraulic, lubrication, fluid dispensing, and refuelling markets, Cooper Fluid Systems sets itself apart through its innovative solutions and people-centric approach. Brody Sewell, General Manager, and Robert Bulluss, CEO of Coventry Group Ltd, parent company since 1997, come together to tell us more
Writer: Lily Sawyer | Project Manager: Eddie Clinton
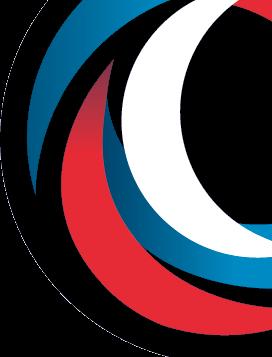
As a primary contributor to the global supply of coal, gold, copper, nickel, lithium, and iron and aluminium ore, today’s Australian mining industry thrives.
Continuing to attract major global investment due to its stability, highgrade resources, and continuous refinement of technologies, Cooper Fluid Systems (Coopers) emerges as a trusted partner to companies within this burgeoning sector.
Working with major Australian

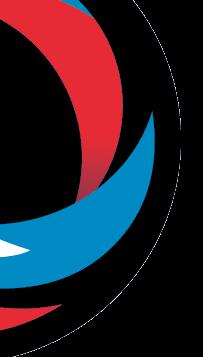

mining firms and assisting them with reducing costs by increasing efficiencies, improving reliability, and minimising environmental impacts, the company supports its clients’ efforts to remain competitive whilst enhancing productivity on a global scale.
“Following a recent uptick in Australian mining organisations’ interest in adopting new technologies, especially those which foster a safe and efficient work culture, Coopers
has continued to prioritise these same initiatives,” introduces Brody Sewell, General Manager.
Providing a ‘cradle to grave’ approach for its clients, Coopers’ historical focus has been on hydraulics, lubrication, refuelling, fluid dispensing, pneumatics, and fire suppression systems.
More recently, technological advancement has led to the company expanding its offerings to include automation, electrification, and
Industry 4.0 products, which integrate well with the company’s legacy offerings.
Dealing with clients that value premium products and solutions and have a long-term focus on total cost of ownership, safety, and reliability is a core component of Coopers’ offerings.
“We understand that safety and reliability for our clients is paramount, and this remains our unwavering priority,” he confirms.
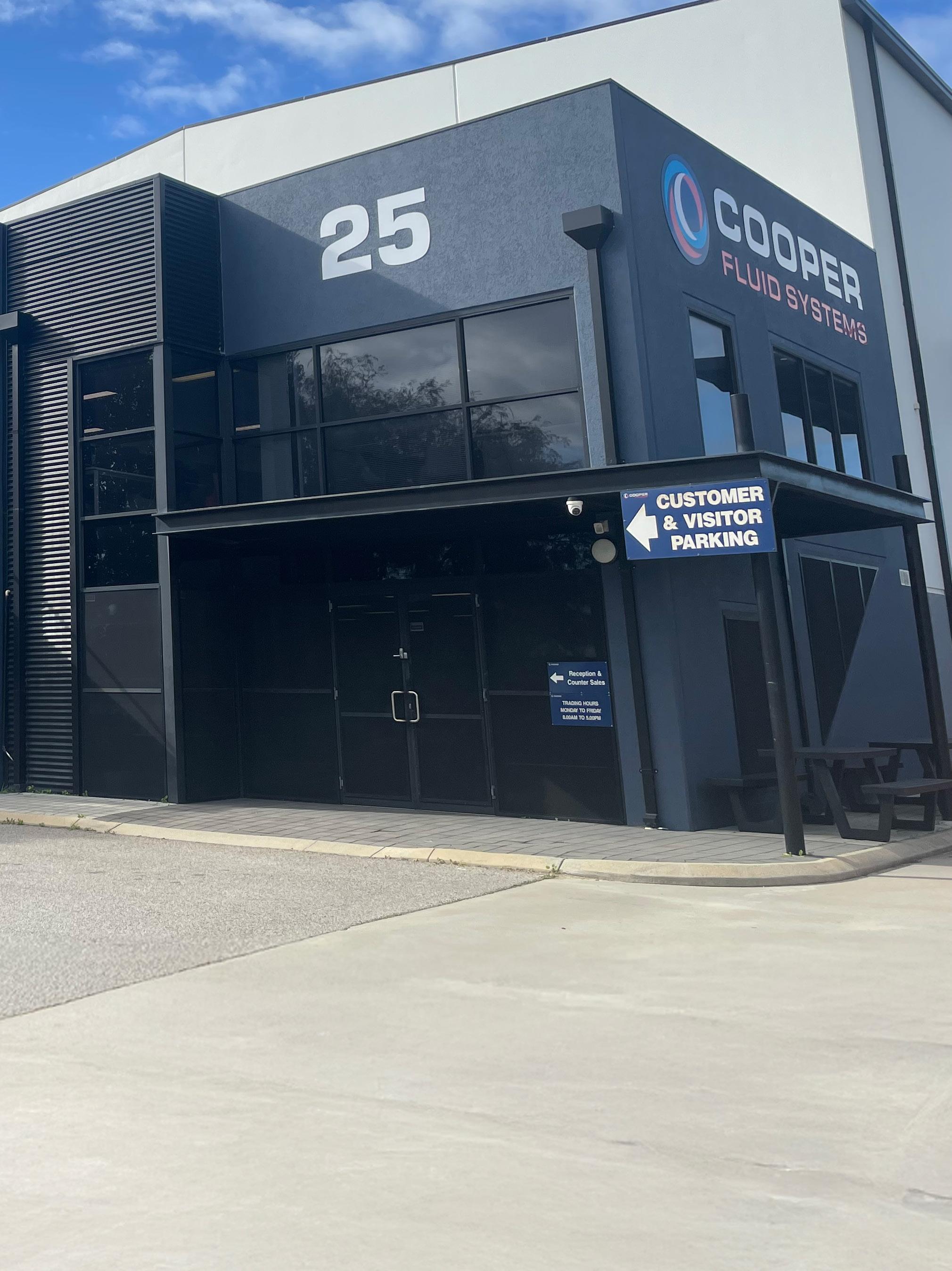
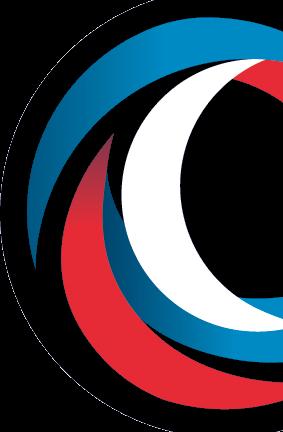
LOCAL SOLUTIONS, NATIONAL STRENGTH
With 15 branches located close to its core customer bases across the country, each complete with fully equipped workshops and warehouse operations, Coopers offers comprehensive support to customers across Australia.
These branches are backed up by strong nationwide capabilities within engineering, technical sales, and procurement, providing access to best-in-class products and cuttingedge solutions.
“Our tagline – ‘Local Solutions, National Strength’ – really distils the power of our value proposition,” Sewell shares.
Alongside its national presence, Coopers seeks to guarantee consistently prompt and accurate delivery alongside quality customer service and technical assistance.
“Our success in this area is a result of an internal focus on our customer promise, which is to deliver highquality products, services, and solutions,” he adds.
As such, the company recently upgraded to Microsoft Dynamics 365 Finance and Operations, a modern enterprise resource planning (ERP) system that has helped to streamline its services and allowed the company to focus on exceeding customer expectations.
Coopers also maintains industryleading inventory levels, ensuring that it has adequate supply coverage across all its locations.
Meanwhile, each of the company’s branches boasts highly skilled employees, further complemented by a national support network of specialists.
In addition, Coopers’ team of almost 20 hydraulic mechanical and automation engineers are on hand to ensure it is always ready and able to tackle any customer problems, no matter the size or complexity.
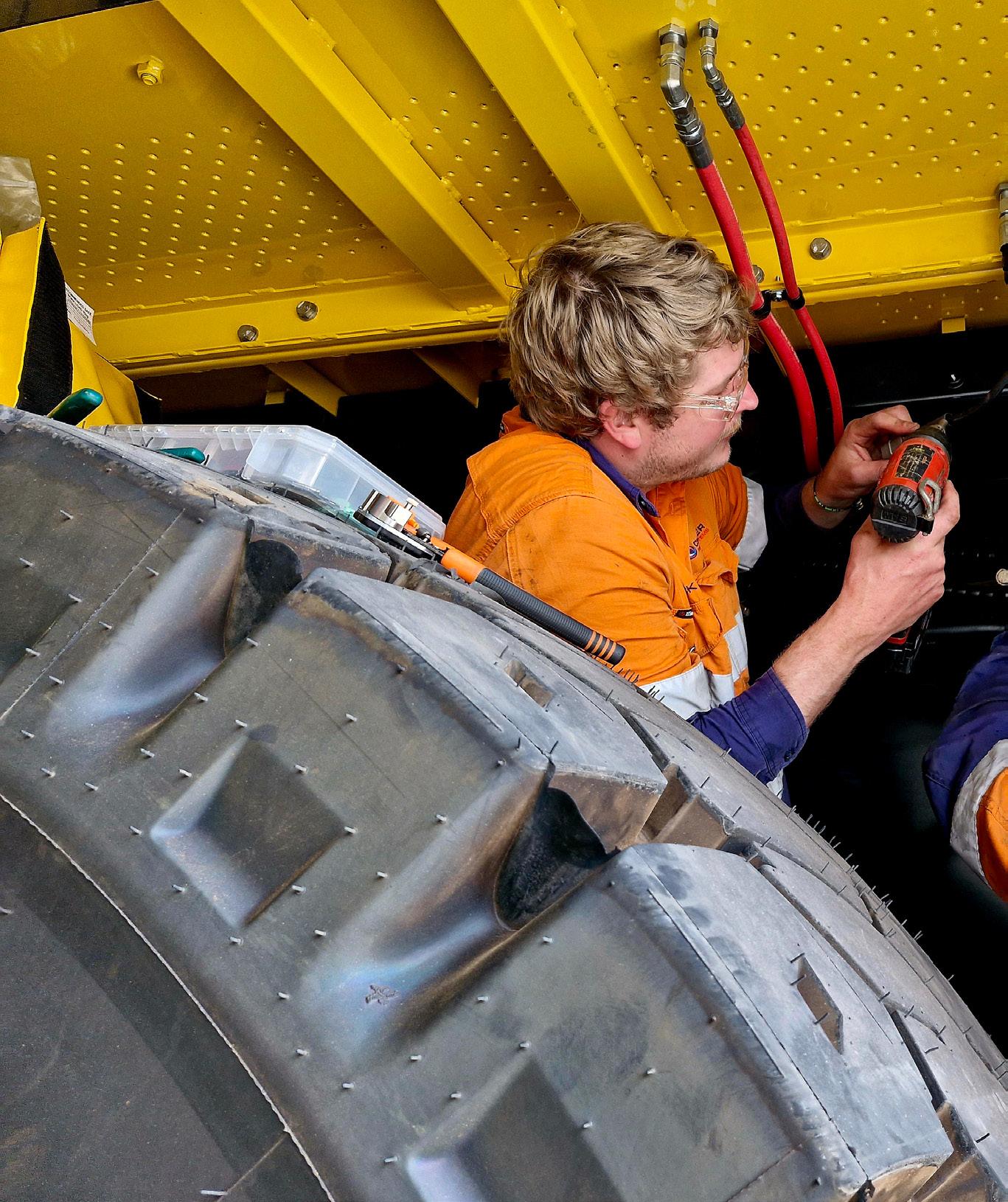
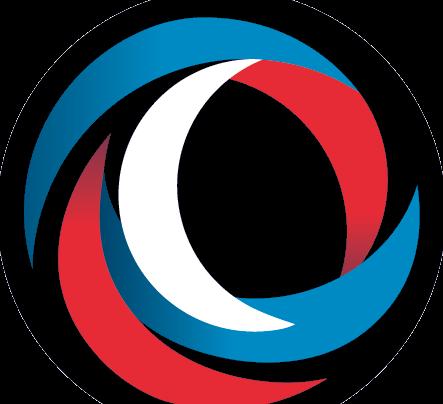
“WE UNDERSTAND THAT SAFETY AND RELIABILITY FOR OUR CLIENTS IS PARAMOUNT, AND THIS REMAINS OUR UNWAVERING PRIORITY”
–BRODY SEWELL, GENERAL MANAGER, COOPER FLUID SYSTEMS
ENDLESS INNOVATION
Amongst Coopers’ ongoing activities is an exciting plethora of projects that demonstrate the company’s continuous commitment to innovation.
For example, in Mackay, Queensland, it recently devised an automated hydraulic solutions project for eliminating live works (ELW).
Coopers was approached by a major mining company who sought to fulfil a safety initiative to drive ELW and required a solution to perform maintenance works on a major piece of equipment during a shutdown.
As a result, the team designed and manufactured a trailer mounted hydraulic power unit (HPU) with full automation and remote control capabilities, which allowed for the safe operation of specific components such as hydraulic cylinders, pumps, lubrication circuits, and air conditioning.
“As this solution was going to
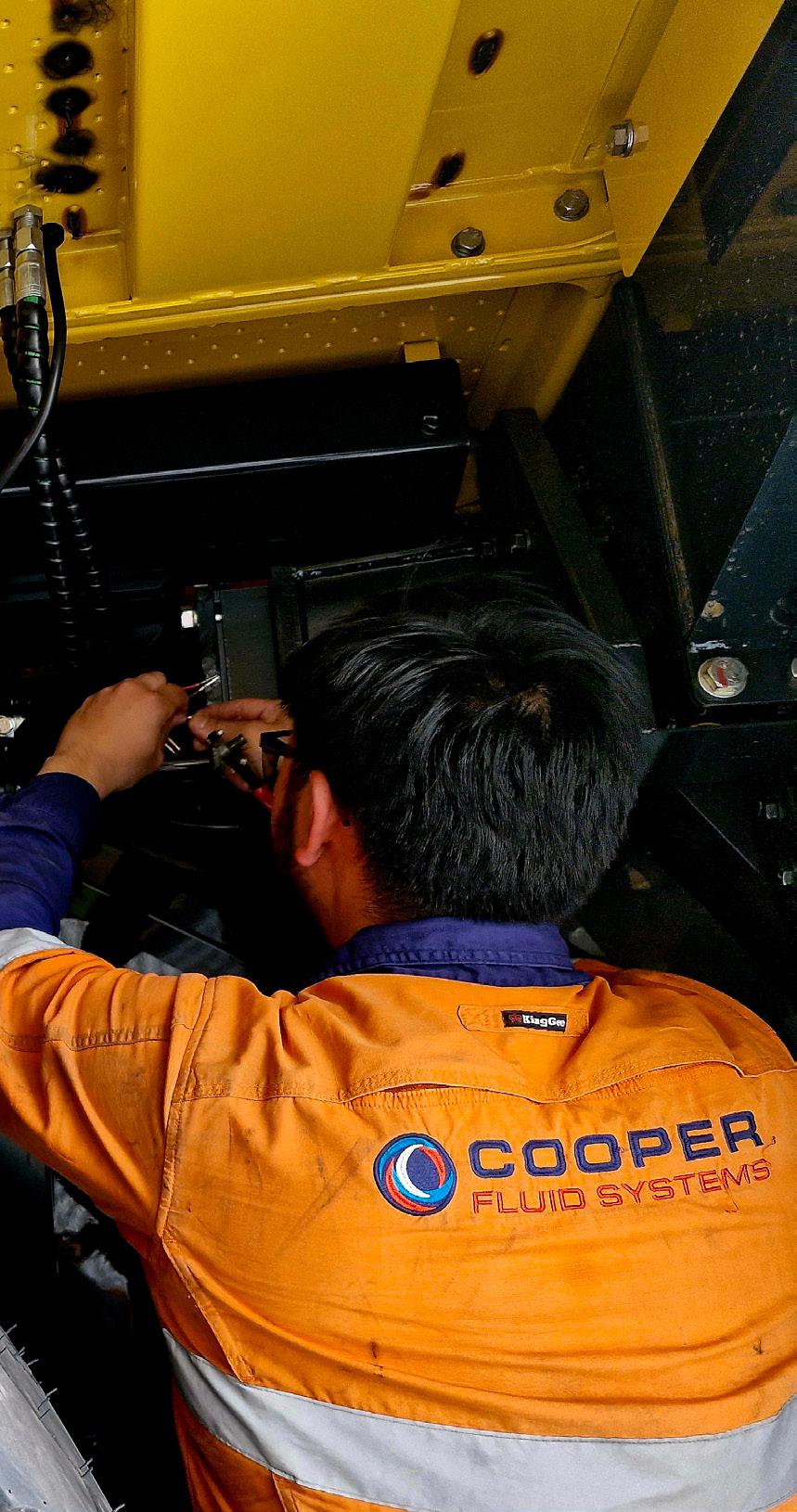
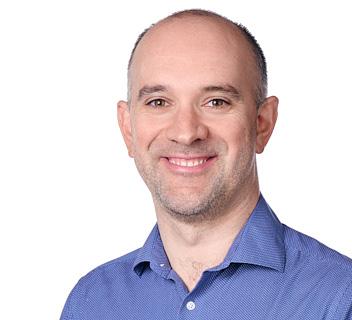
be utilised in the Australian mining industry, we ensured that it was built to last with independent, off-road suspension and our own marketleading CooperBuilt hydraulic hose reels,” Sewell informs.
The unit also features a fully programmable logic controller (PLC), pre-programmed to the different circuit requirements of each piece of equipment being serviced.
Another interesting project completed by the company towards
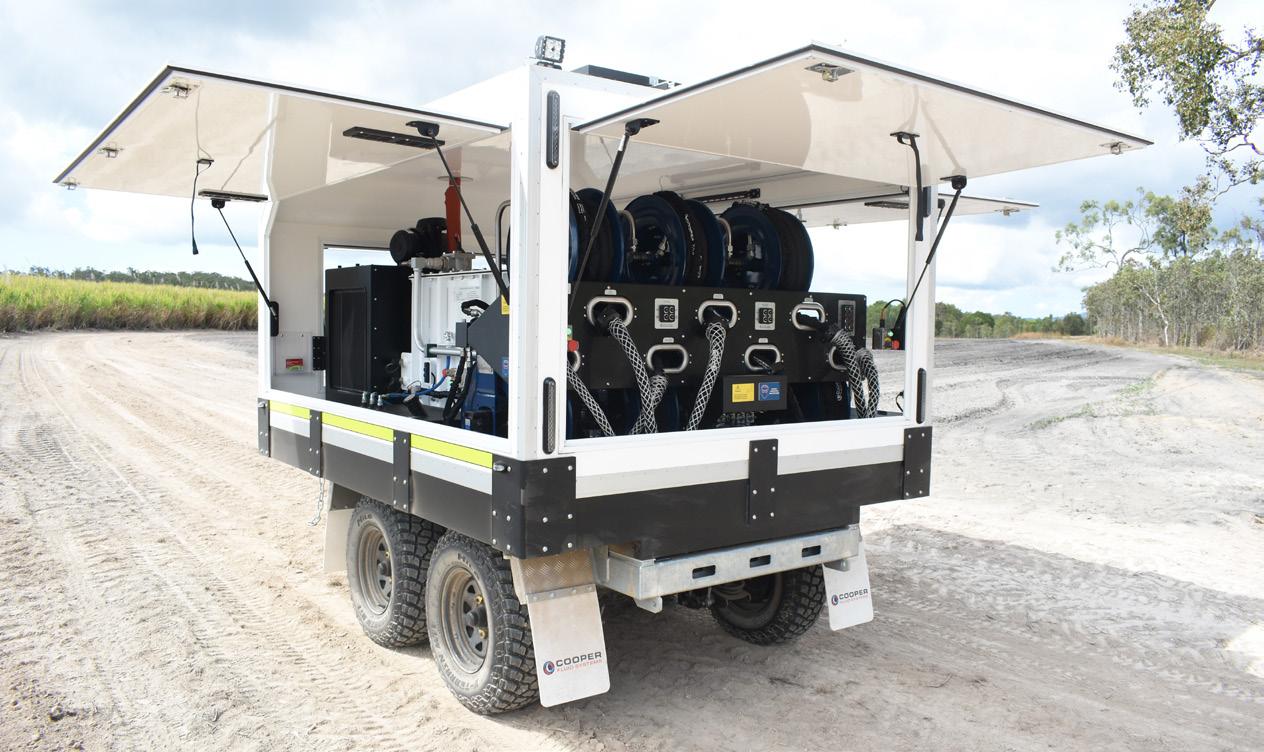
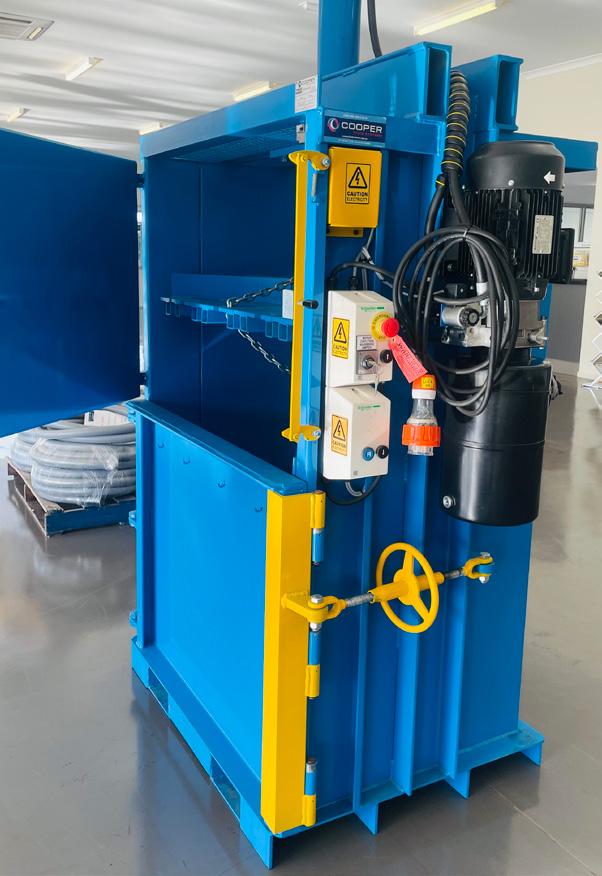
the end of 2024 was its solar-powered degreaser dispensing system for use in remote mining applications.
“This really tied together our capabilities in fluid dispensing as well as automation and electrification engineering,” he explains.
“We designed and manufactured a complete solution which included solar panels, battery back-up, and a dispensing circuit that allowed for the connection of degreaser pods in remote locations with no access to power.”
WIDE-RANGING SERVICES
Having worked closely with Australia’s major hay exporters and significantly improved their cycle times, Coopers has demonstrated its diversity.
“Our work with Australia’s hay industry has improved its ability to
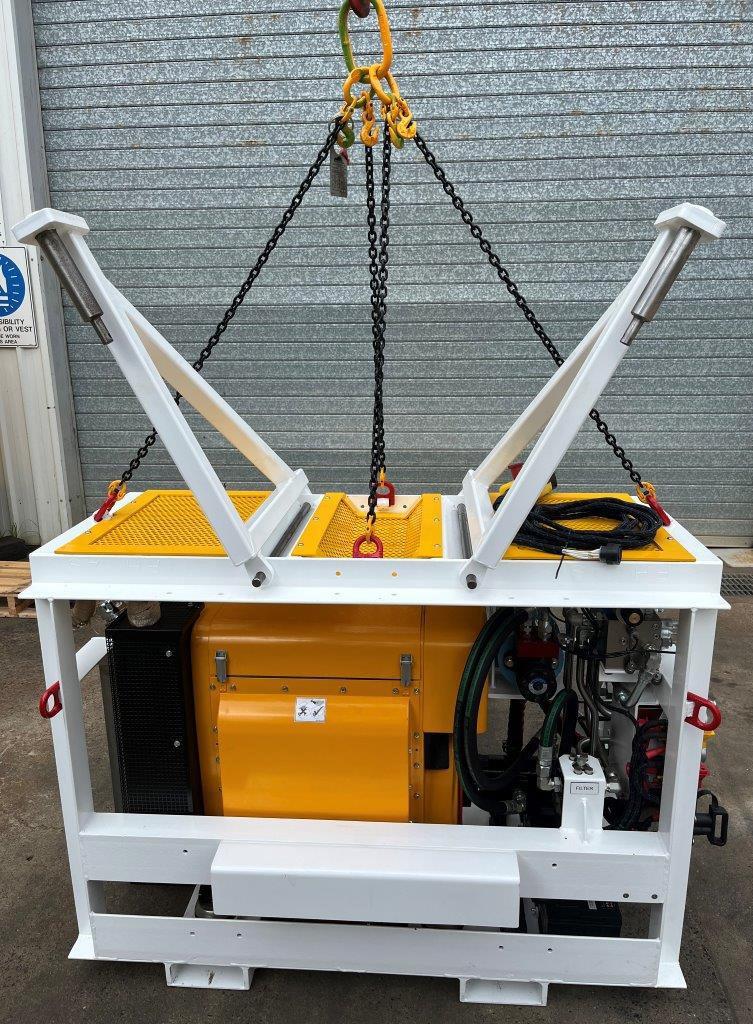
COOPERS’ KEY STRENGTHS
• A safety-first culture
• 50+ years of industry experience
• A national network of 15 branches
• ISO 9001:2015 certified across all locations
• Engineering and technical support
• Qualified service staff
• Premium brands
• Specially manufactured products
• Bespoke engineered solutions
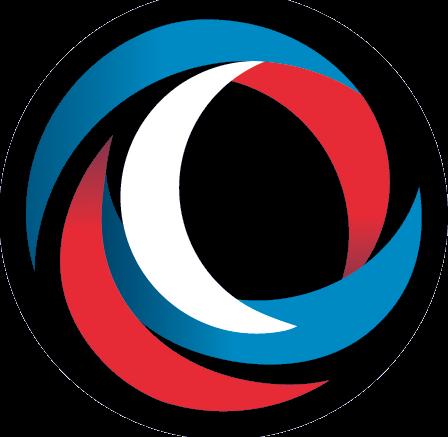
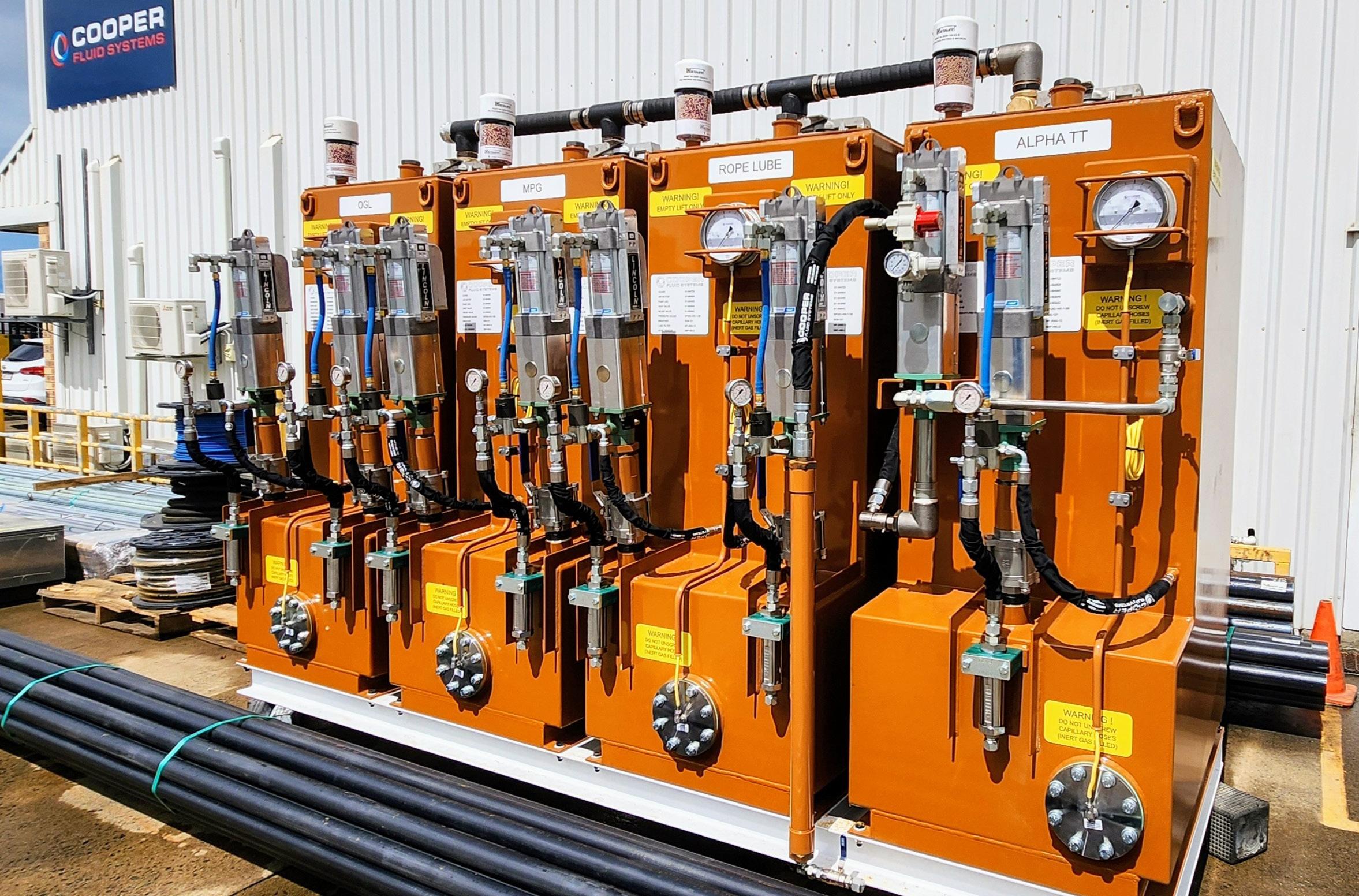
compete in the global market,” Sewell prides.
With some of the projects it has undertaken in this industry worth several million dollars and featuring incredibly complex hydraulic and automation solutions, thousands of engineering and manufacturing hours are often required.
“We’re currently working on an incredibly exciting hay plant. Whilst not specific to the mining industry, the solutions we employ can have many uses, especially in fixed-plant applications,” he outlines.
The company’s flexible, multisector approach feeds into to its vast supplier base, which ranges from local to international brands, as it must account for a wide array of needs and requirements.
“We find that local suppliers generally understand the requirements of our domestic customers and businesses, whilst we
A BRIEF HISTORY OF COOPERS

Since its inception in 1972 as John Cooper Hydraulics and Pneumatics, the company has grown significantly.
Purchased by industrial products and services distributor, Coventry Group Ltd, in 1997, it has since acquired six additional businesses, enabling it to provide local knowledge and solutions tailored to customers’ needs.
Today, Coopers is as a national leader in Australia’s hydraulic, lubrication, fluid dispensing, and refuelling market, with over 45 years of industry experience and an extensive network of 15 branches.
also embrace premium brands from across the globe, particularly where products are highly technical in nature or we need to leverage international manufacturing networks,” Sewell reveals.
“One thing that remains consistent is our commitment to partnering with vendors who share our strong focus on quality.”
CENTRED AROUND PEOPLE
With people at the heart of the business, Coopers tries to bring in the best talent and provide them with the tools and guidance to do their job.
“It is vitally important in an organisation to make sure people know it’s okay to view mistakes as opportunities to learn and develop,” Sewell divulges.
As such, the company has numerous initiatives to help develop its people, including graduate, apprentice, trainee, and technical
55 YEARS OF SERVICE AND INNOVATION IN THE AUSTRALIAN MARKET ALEMLUBE
Alemlube, a family-owned business with 55 years of industry leadership, continues to stand out as a proactive, dynamic force in the Australian market. Known for its commitment to quality, design, and innovation, Alemlube has set the bar high across multiple sectors, including automotive, industrial, commercial and mining.
A TRUSTED NATIONAL PRESENCE
With branches strategically located across Australia and New Zealand, Alemlube has built a solid foundation in providing tailored solutions to its customers. Its focus on mining is particularly noteworthy, where the company boasts a team of design engineers capable of creating bespoke outcomes for its diverse client base in the ANZ region. Alemlube’s expert team collaborates with its Business Development Managers (BDMs) to ensure that each customer’s needs are met with a complete, end-to-end solution.
CUSTOMER SERVICE EXCELLENCE
Alemlube’s exceptional customer service is bolstered by its network of six branch locations, giving the company a genuine national platform. This strategic positioning allows for prompt order fulfillment, sales support, design assistance, and on-site after-sales service. Whether it’s providing a tailored design solutions for OEM dealership workshops or installing lube systems for stacker reclaimers in the Pilbara, Alemlube consistently goes above and beyond to exceed customer expectations.
A MISSION TO LEAD
Alemlube’s mission is clear: to be the most consistent, reliable, and valuable supplier of products and services in the mining sector. The company prides itself on its deep expertise, gained both from within the organisation and through overseas partnerships. Alemlube’s experienced teams understand the critical role their products and services play in maximising the efficiency and longevity of fixed plant, mobile equipment, machinery, and power generation facilities.
A WIDE RANGE OF PRODUCTS
Specialising in the mining sector, Alemlube offers an extensive range of products from the humble grease nipple to large-capacity vehicle hoists. Each product is designed to enhance productivity and safety at mine site workshops. Alemlube has made significant contributions to Australasian industry, particularly through the design, fit out, and commissioning of workshops, as well as the design, supply, and installation of lube systems for mobile and fixed plant.
COMPREHENSIVE DIVISIONS FOR DIVERSE NEEDS
Alemlube operates across several key divisions, each focused on providing high-quality solutions to various industries:
· Refuelling Equipment: Alemlube offers a range of refuelling products designed to cater to a variety of sectors, including mining, manufacturing, food & beverage, agriculture, and transport. Their box-in-box-out options and branded products ensure that clients receive top-tier equipment and consistent after-sales service.
· Capital Workshop Equipment & Workshop Fitout Design: Alemlube specialises in the design, installation, commissioning, and after-sales service of workshops for mine sites. With advanced 3D graphics and animations, Alemlube helps customers plan and optimise their workshop operations, ensuring higher efficiency and profitability.
· Lubrication Systems and Solutions: Alemlube’s expert team offers design, installation, and maintenance services for lubrication systems across mobile and fixed plant applications. Their services include the supply of single and multi-point grease and oil lubricators, fluid flow and level management solutions, and advanced oil and fuel management systems. The company’s flexible, programmable lubricators help businesses optimie maintenance schedules and enhance equipment lifespan.
LEADING
THE WAY FORWARD
Alemlube’s success over the past 55 years is a testament to its unwavering dedication to quality, service, and innovation. As the market continues to evolve, Alemlube remains at the forefront, ensuring that its products and services meet the ever-changing needs of the mining industry and beyond. With its extensive experience and commitment to excellence, Alemlube is poised to continue leading the way for years to come.
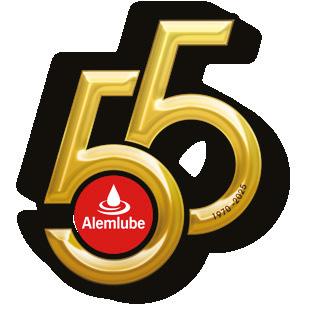
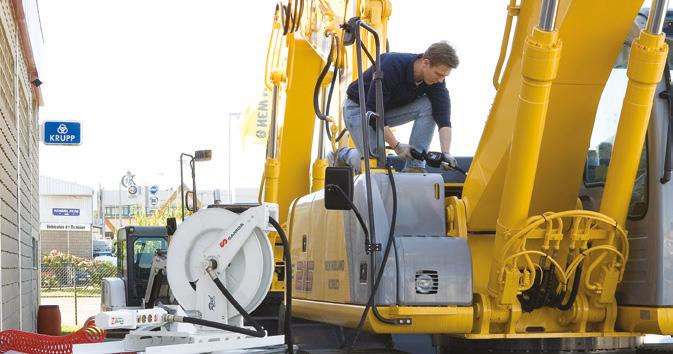
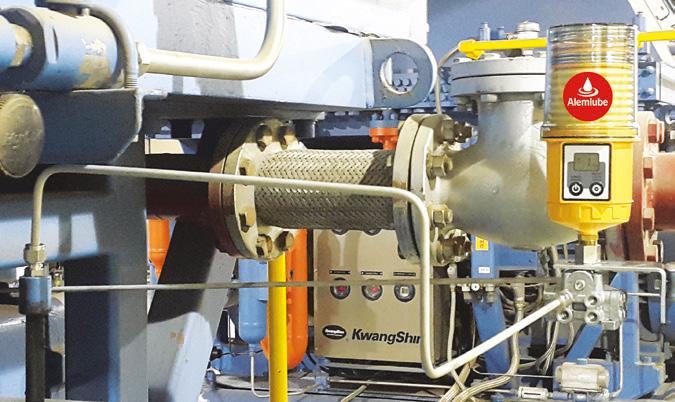
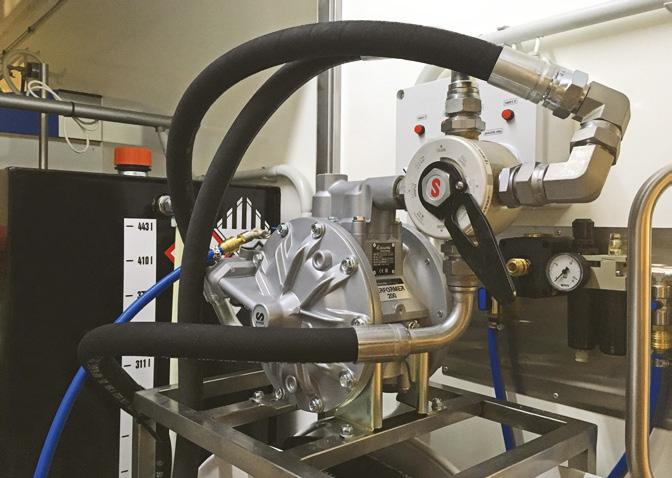
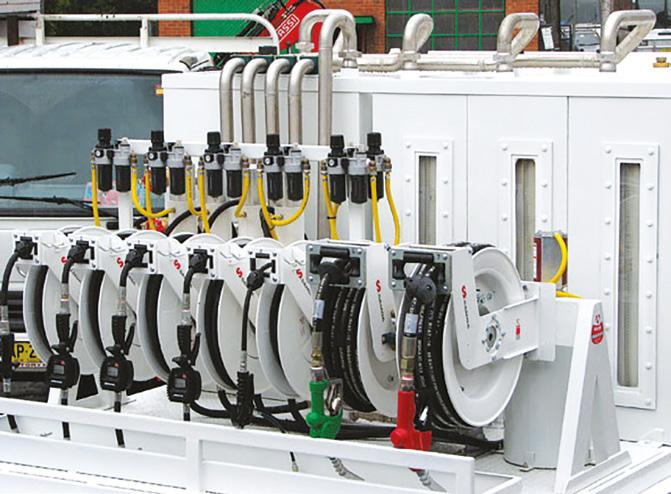
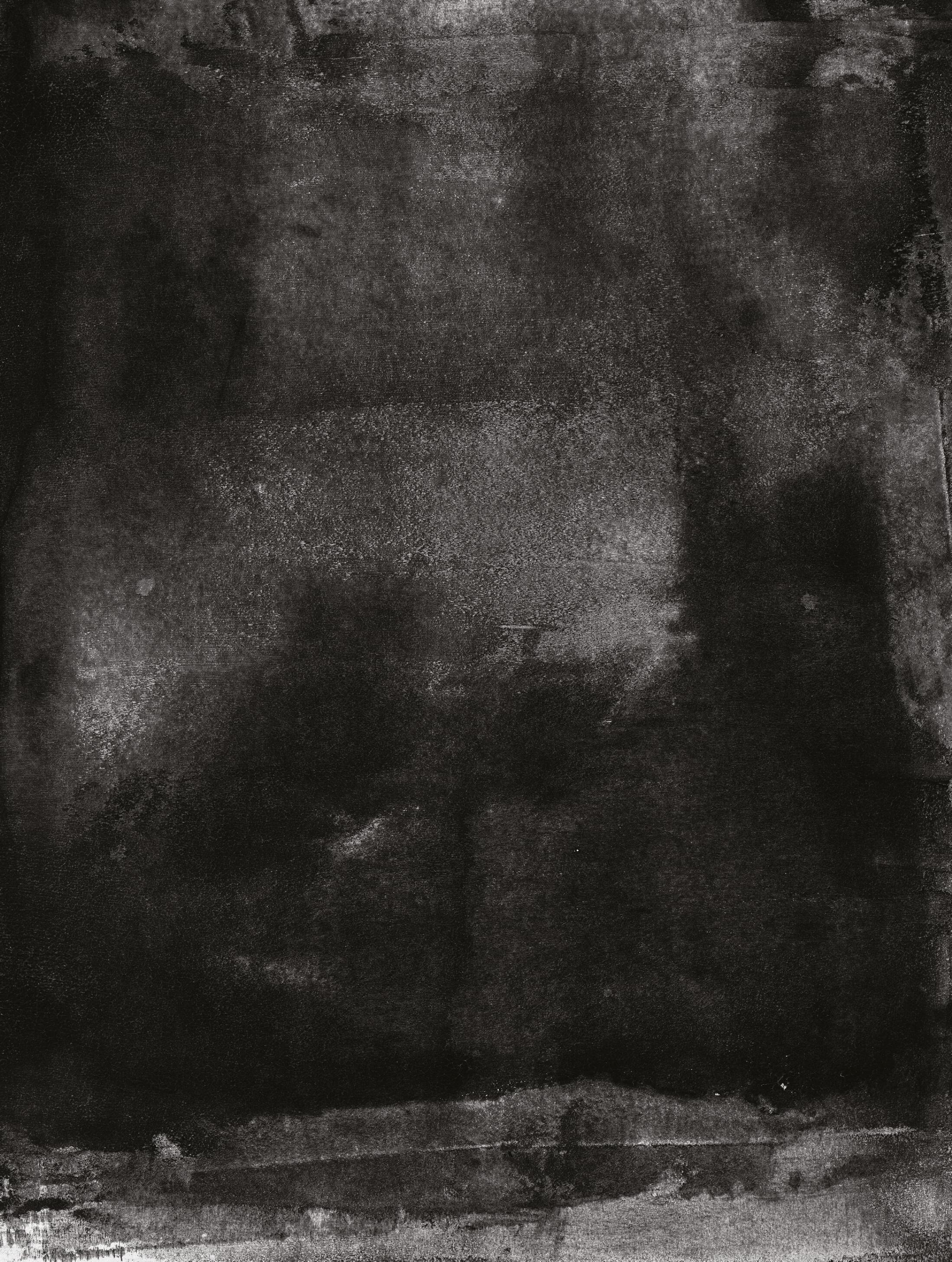
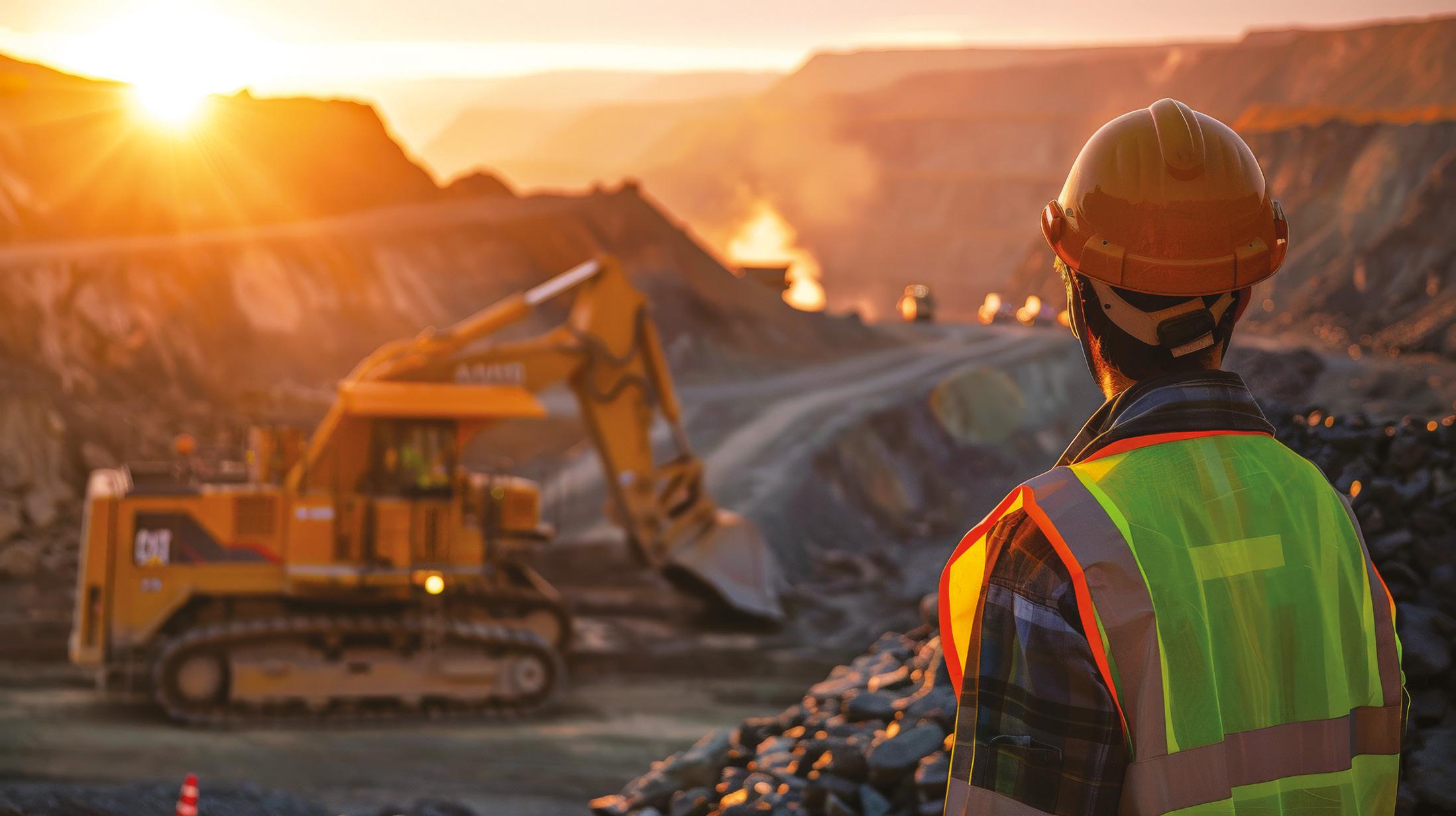

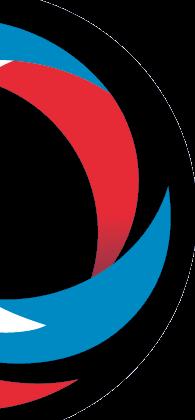
training programmes, and engages third-party organisations to provide both commercial and specialised technical training.
It also encourages willing employees to undertake university studies, with Sewell himself having earned a degree with the support of Coopers.
“My view is that there’s no point in recruiting and developing people if you can’t retain them,” he comments.
“We also ensure that our people are properly and fairly renumerated for the good work they do and have an organisation-wide incentive plan that applies to all employees.”
Therefore, whilst the company is a corporate organisation, it still maintains a personal touch and views each of its 1,000+ staff members as part of its extended family, celebrating them accordingly.
“WE PRIDE OURSELVES ON LIVING OUT OUR VALUES EVERY DAY AND USING THEM TO GUIDE OUR DECISION MAKING”
–ROBERT BULLUSS, CEO, COVENTRY GROUP LTD
To mark each employee’s birthday, for example, they receive a personalised email from Coventry Group Ltd CEO, Robert Bulluss, and a birthday card from their General Manager.
The company also has weekly staff ‘shout-outs’, monthly ‘values champions’, and quarterly CEO awards.
With people critical to the success of the company, they are viewed as more than mere assets – they are the beating heart.
“I often hear people being described as a company’s assets – I
don’t agree, as assets are things you own,” reflects Bulluss.
“People can choose to leave an organisation and only stay when they feel they resonate with its values and have opportunities to grow. Therefore, we need to work on multiple fronts to build a culture that people want to work in,” he adds.
A BRIGHT FUTURE
On a continuous mission to establish innovative ways to better serve its customers, Coopers is constantly opening new avenues to market.
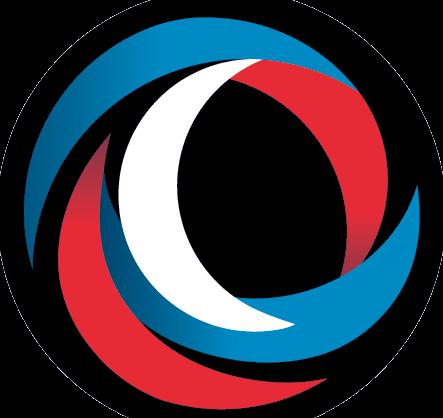


Meanwhile, it is staying ahead of the technological curve with advancements in electrification, battery technology, and electrohydraulic components.
“These all offer great opportunities for us to improve our customers’ operations,” Sewell shares.
The company is also investing in its expanding legacy capabilities due to its core belief in the value of continuous improvement.
“We understand that there’s always room to improve the equipment we have, further train and educate our
people, and ensure we facilitate knowledge sharing across the market,” he adds.
With people at the heart of its success, a key priority for Coopers’ leadership team going forwards remains building a culture that attracts and retains the right people to grow the business.
“We pride ourselves on living out our values every day and using them to guide our decision making,” Bulluss reflects.
In this way, the company is well placed for future success as it continues to provide full turn-key solutions for its customers.
“One thing I can guarantee is that whatever we do, it will be in line with our purpose of providing specialist solutions that our customers can trust,” Sewell confidently concludes.
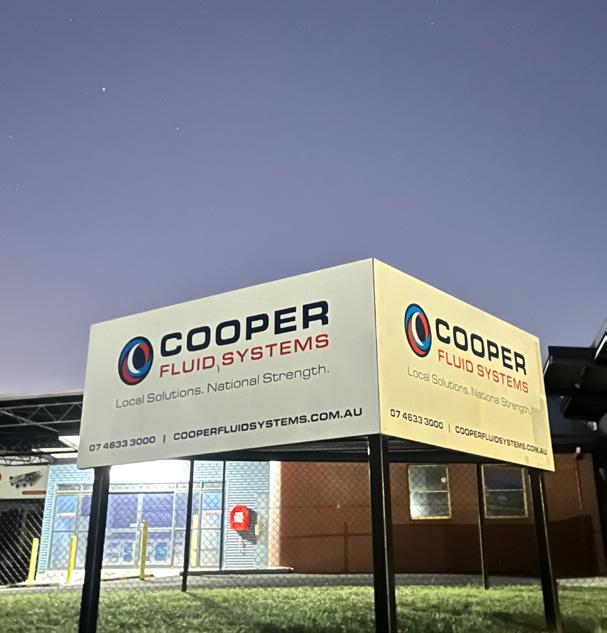
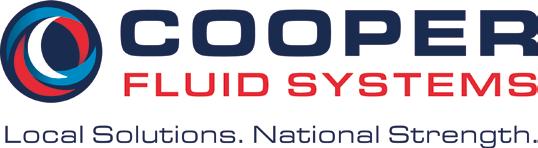
Tel: 1300 026 673
cfsadmin@cfs.cgl.com.au
www.cooperfluidsystems.com.au
Home to vast plains and diverse environments, moving goods across Western Australia (WA), the largest state in the country, requires precision and thorough efficiency. As such, WA’s heavy transport sector plays an integral role in the progression of numerous core industries, from mining to agriculture.
Providing cutting-edge logistics services since 1997, Campbell Transport has a history of innovating the bulk haulage industry and has grown to manage the biggest road-legal trucks in the world.
The company expertly oversees more than 200 top-of-the-range vehicles equipped with quad and
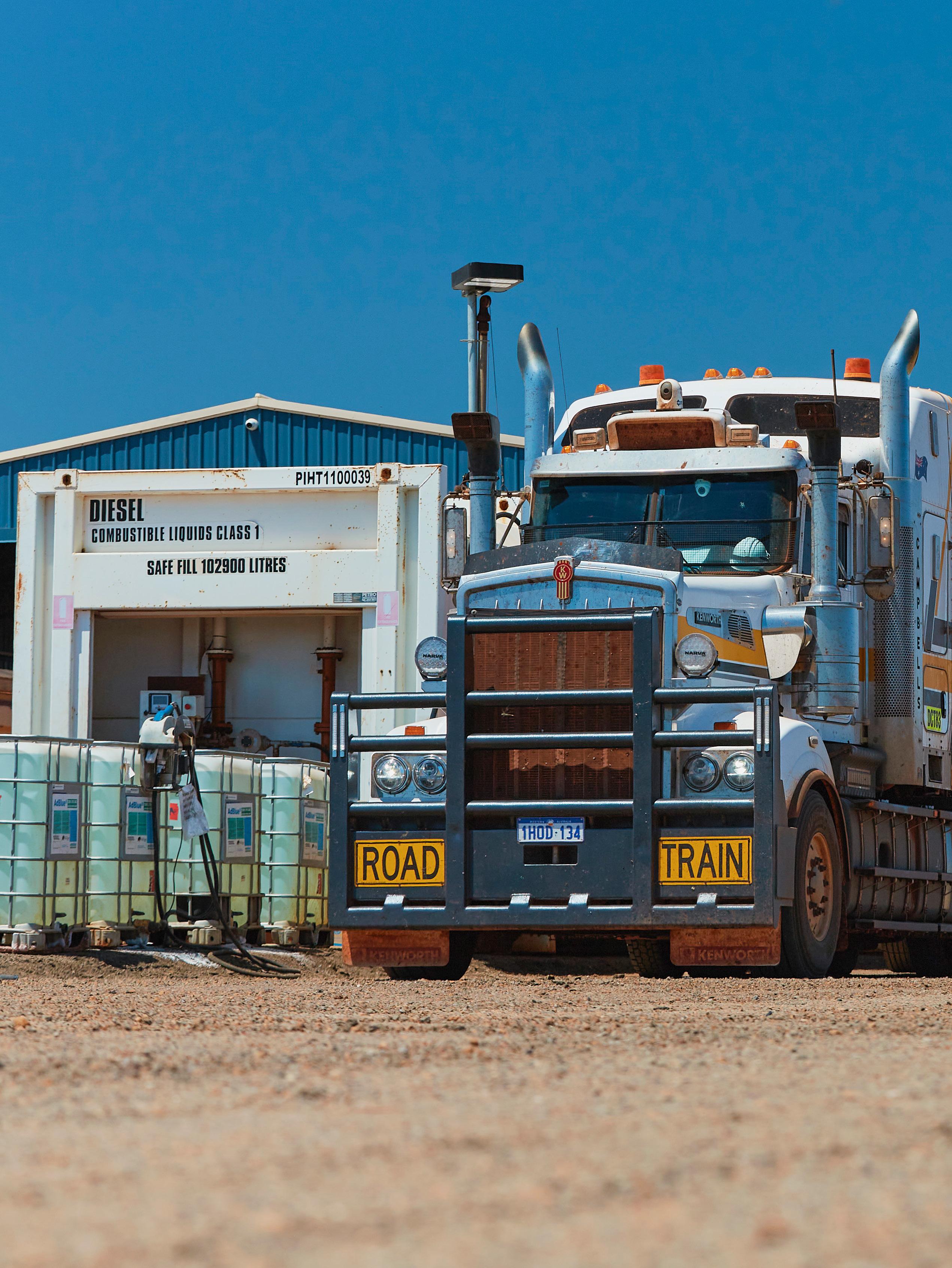
triple road trains, making it the largest performance-based standards (PBS) fleet, combined with a supporting plant, and specialist machinery for any load, haul, and maintenance requirements.
The WA PBS Scheme offers improved efficiency by allowing higher productivity vehicle combinations,
THE GO-TO LOGISTICS PROVIDER
We explore the ways in which Campbell Transport has evolved to provide comprehensive logistics services across the breadth of Western Australia, serving multiple industries and guaranteeing truck drivers’ safety
Writer: Lucy Pilgrim | Project Manager: Andrew Lewis
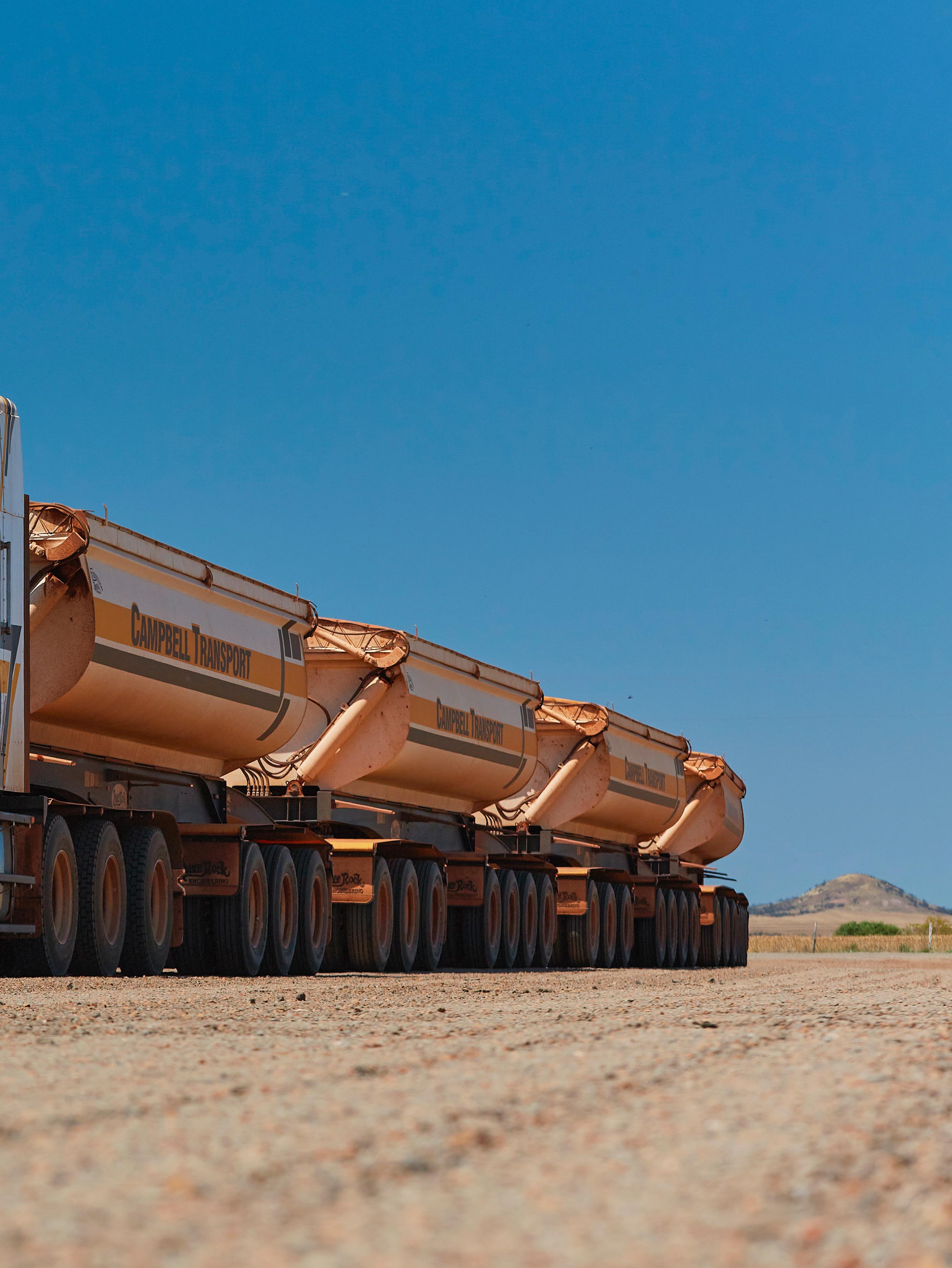
which have been assessed against stringent safety standards to operate on routes that would not typically be approved for prescriptive vehicles with the same mass and dimensions.
Thus, with an unmatched fleet, Campbell Transport is able to cover over 47,531 kilometres across WA, delivering its clients’ goods safely and
efficiently across some of the state’s most remote areas.
MEETING THE NEEDS OF MANY
Since its inception, Campbell Transport has achieved a stronghold in WA’s agricultural sector. For decades, the company has been known for its unmatched grain haulage capabilities
and its capacity to meet the needs of local farmers.
In the last 25 years, Campbell Transport has evolved to meet the changing needs of agribusinesses, initially ensuring the orderly delivery of crops before incorporating fertiliser and chemical transportation into its repertoire.
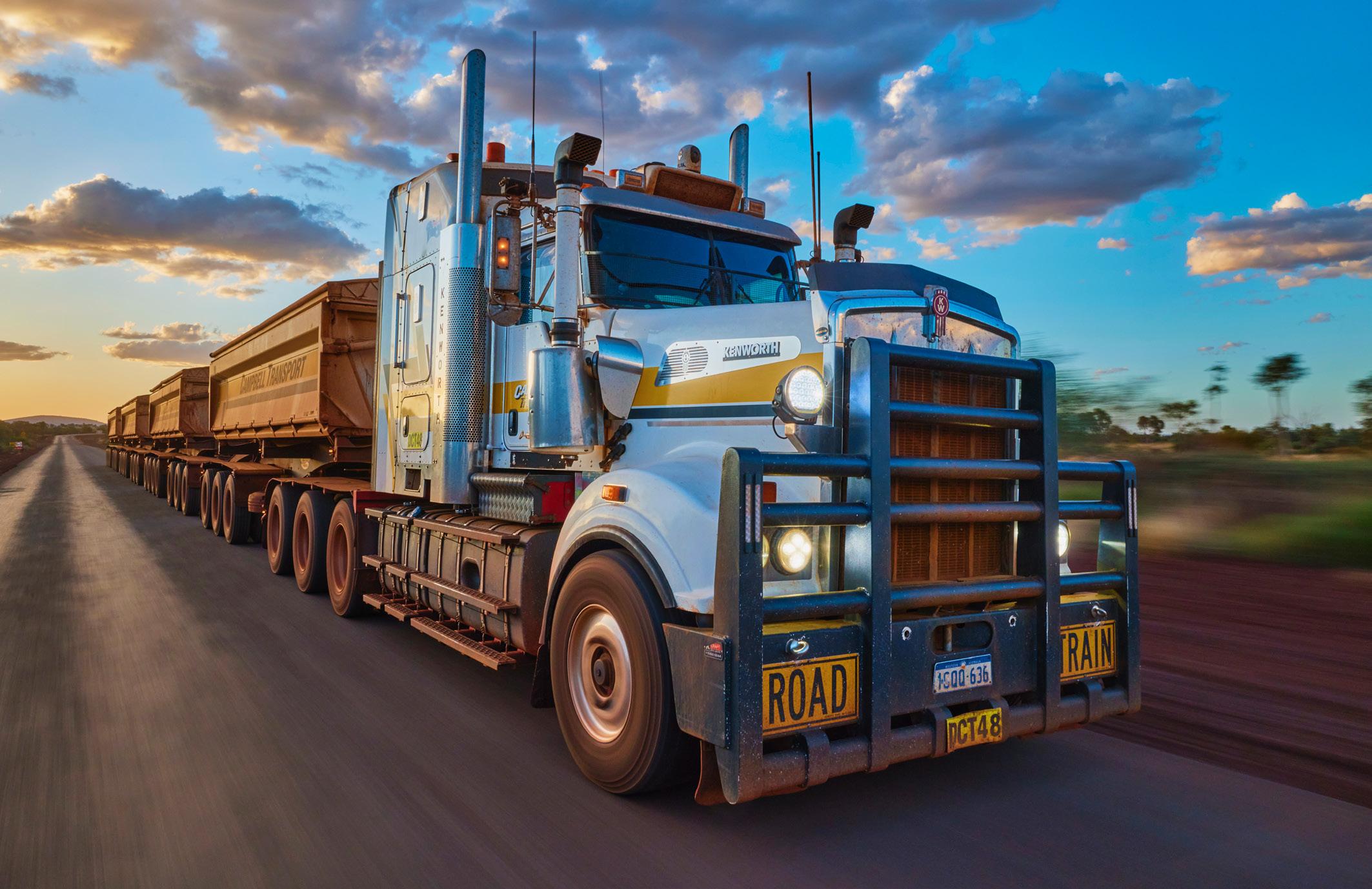
Nowadays, the company also supports the set-up and movement of sizeable agricultural machinery and complex equipment, becoming a vital aid for WA’s largest agrarian organisations.
Seven years ago, Cambell Transport entered the bulk haulage to mining market, providing both on-road and off-road services.
Subsequently, the company took the decision to accelerate its growth by branching out into more general freight operations, offering clients state-wide delivery services across a vast network of highly developed warehousing and depot facilities.
Today, Campbell Transport’s general freight division holds an admirable reputation for the seamless and safe delivery of goods. Leveraging more than 20 years of experience, the company handles a diverse range of freight, including oversized loads, using 24/7 GPS tracking. Therefore, all clients’ logistical needs are met, offering robust and dependable freight management services.
Customers can also rest assured that their products are safely stored in one of the company’s many strategically located warehouses and depots, where goods distribution is managed in an efficient and transparent manner.
Campbell Transport’s depots span WA, including Port Hedland, Perth, Geraldton, Broome, Esperance, Kalgoorlie, Bunbury, and Jerramungup, each with comprehensive warehousing and bulk solutions.
As such, the company’s allencompassing and world-class freight services expertly address business’ most complex storage and warehousing challenges.
FROM PIT TO PORT
Campbell Transport’s cutting-edge general freight and warehousing divisions are accompanied by its trusted mining services, which include drilling and blasting operations, crushing and screening, loading and hauling, and maintenance, making it front
THUNDERBIRD MINERAL SANDS PROJECT
Campbell Transport is proud to be the main carrier for the Thunderbird Mineral Sands Project (Thunderbird) in the Dampier Peninsula in the Kimberley region, WA.
Thunderbird is one of the world’s largest and highest-grade zircon mineral sand deposits, containing valuable minerals, including ilmenite, zircon, leucoxene, and rutile, extracted and exported via the Port of Broome to global markets.

and centre of Campbell Transport’s activities.
Campbell Transport’s mining division is renowned for its adaptability and proactiveness, offering tailor-made and multifaceted approaches to customers’ needs. It also utilises top-of-the-range mining equipment and knowledge of the main roads’ PBS to issue its team with the necessary techniques to ensure maximum operational efficiency.
The WA PBS Scheme is also significant as it means the company can run heavier loads with specially engineered truck combinations.
For each workforce, Campbell Transport also offers on-site accommodation with comfortable facilities and amenities, ensuring that team members have a good standard of living with high-quality camp solutions.
The company’s enviable mining services lend themselves well to its turnkey pit-to-port capabilities for mining activities across WA.
To address the diverse demands of clients, Campbell Transport leverages the combined strength of state-wide bulk storage facilities, purposefully situated close to ports to maximise material transportation.
A highly knowledgeable and experienced team is also available
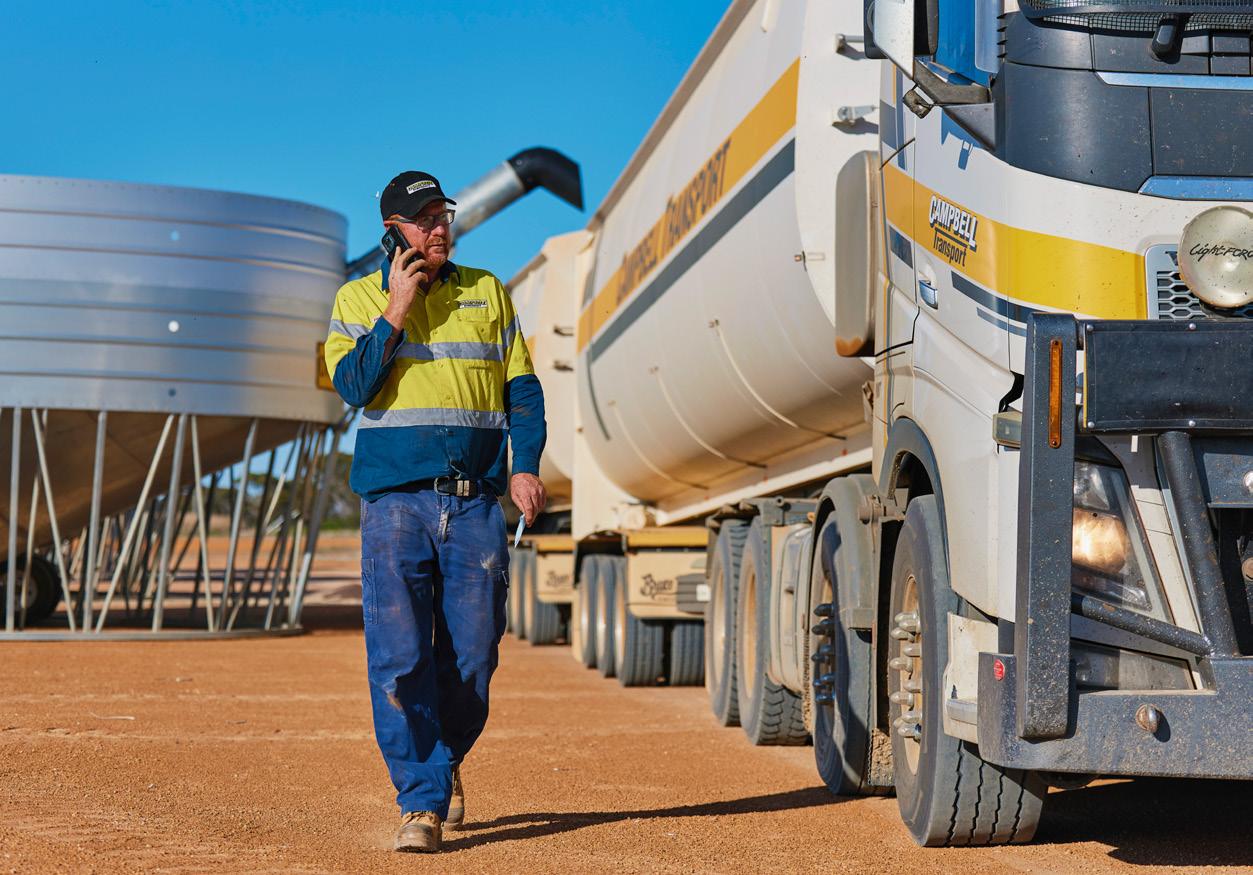
to clients for pre and bankable feasibility studies to maximise project capabilities and ensure specific supply chain targets are met, whilst also cementing the possibility of future projects.
On top of this, Campbell Transport also boasts a tailormade pit-toport rotating container system that centres around the loading of ore and concentrates into eco-conscious sealed containers for transportation.
The system includes a purposebuilt integrated lid that only
opens and releases a product once the material is within the ships holds.
Regarding the bulk haulage of ores, mineral sands, and other mining products, the company is capable of providing enclosed storage or directto-port deliveries for ship loading.

Leveraging the unparalleled capabilities of industry-leading equipment and a highly professional team, the safe and timely delivery of materials is a Campbell Transport guarantee, allowing clients to focus on their core mining activities.
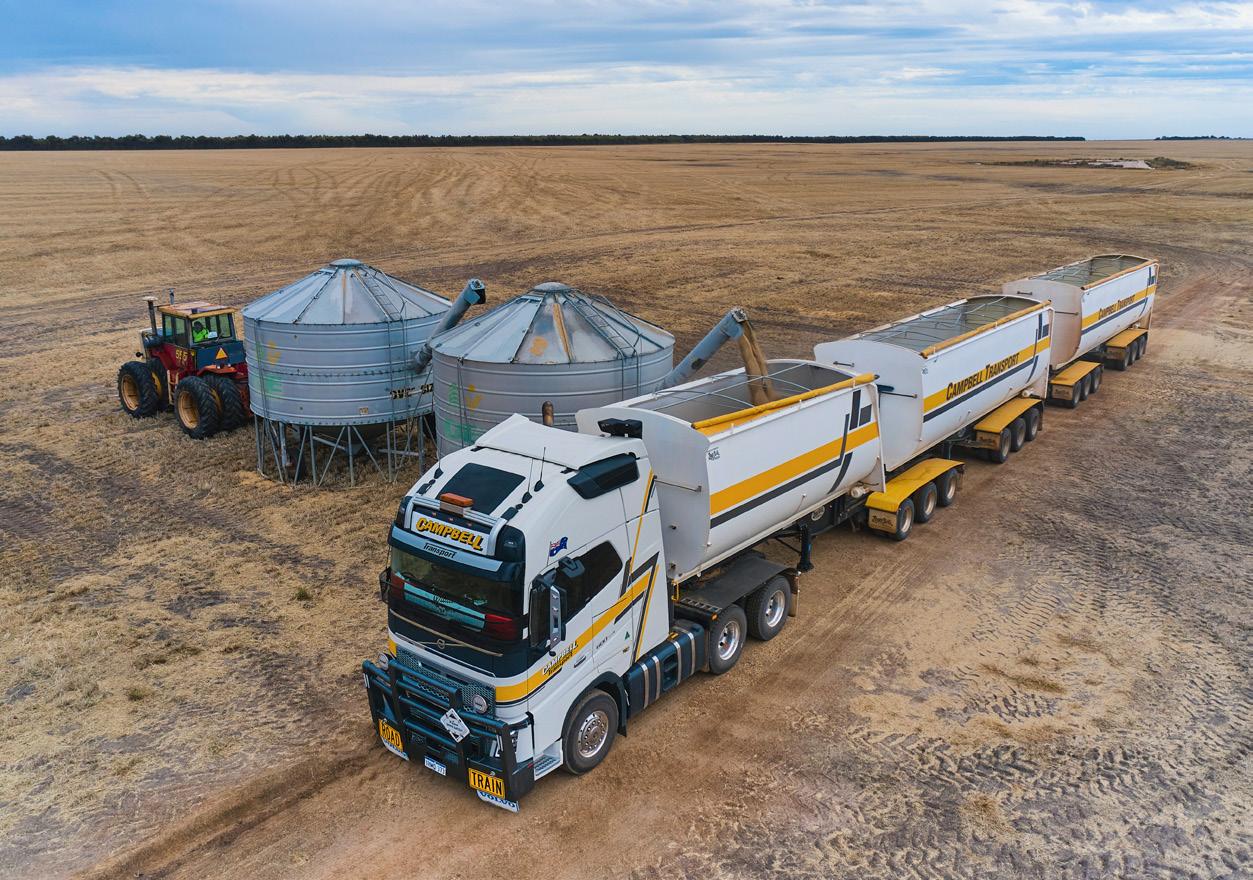
As such, the company is proud to offer end-to-end pit-to-port capabilities for mining operations in WA.
As a trusted industry partner, Campbell Transport understands the complexities involved in drill and blast, mining load and haul, crushing, haulage to port, shed storage, and ship loading. Indeed, the company’s
comprehensive solution ensures seamless coordination and efficient transportation of valuable materials from the mine site to the port.
Campbell Transport has several on-port and nearby bulk storage facilities around WA to cater for any of its current and future clients’ requirements.
COMMITTED TO SAFETY
The high supply and demand of Campbell Transport’s operations mean that its trucks are on the road 24 hours a day, leveraged by a multitude of industries.
With such an extensive and complex operative network, the company has a highly stringent set of safety protocols that have been refined to create a robust and faultless safety system, monitoring the wellbeing of drivers whilst also delivering clients’ needs.
The system comprises a range of equipment that minimises risk for truck operators, including Seeing Machines, who uses cutting-edge software such as proprietary face and eye-tracking algorithms to detect fatigue in drivers working 12 to 14-hour shifts.
This is one of the many instances of real-time in-cab intervention where the driver is told to re-focus their attention. In these cases, Campbell Transport’s 24/7 Fleet Controller Services team are notified and subsequently contact the driver to discuss their fatigue levels and provide adequate advice.
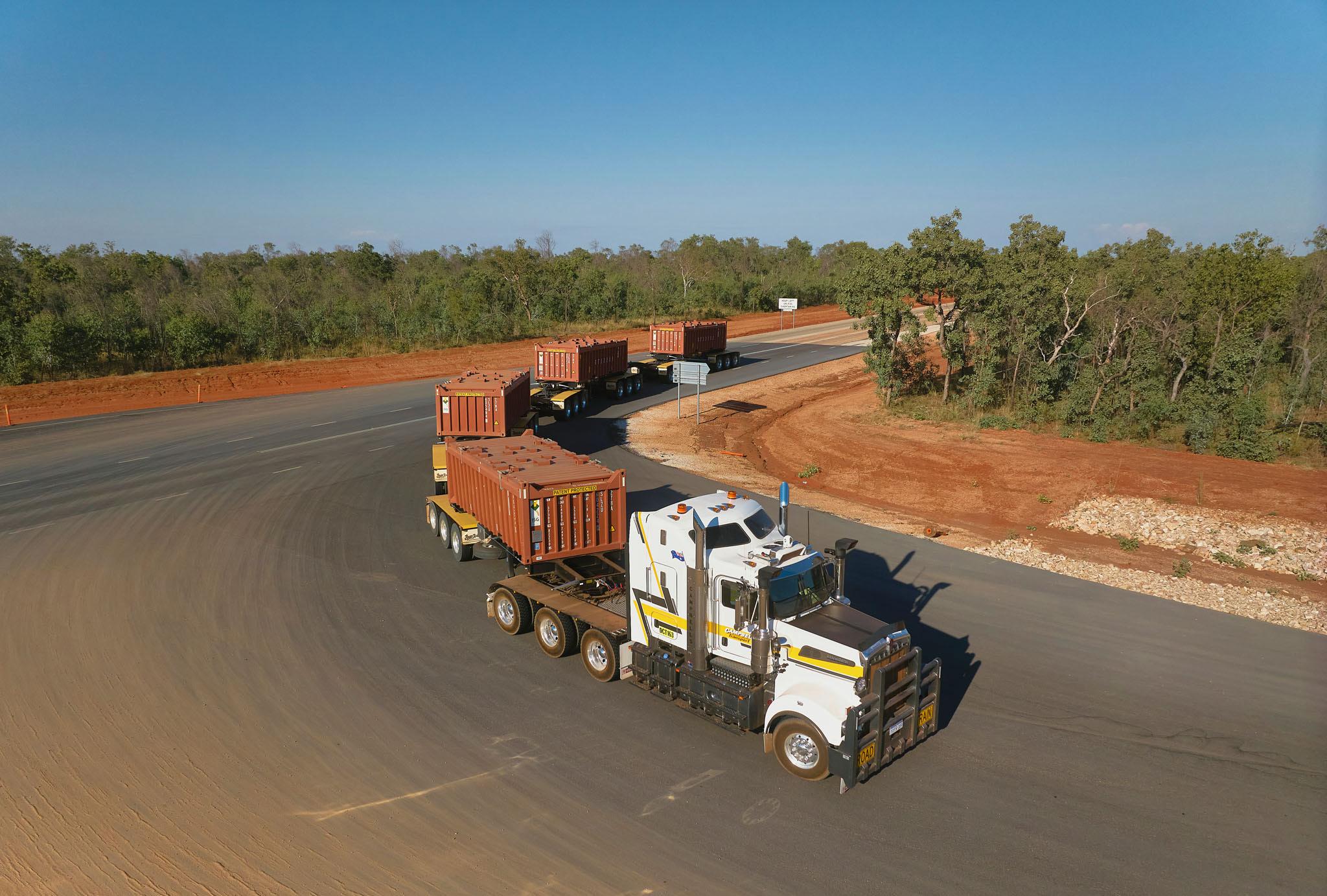
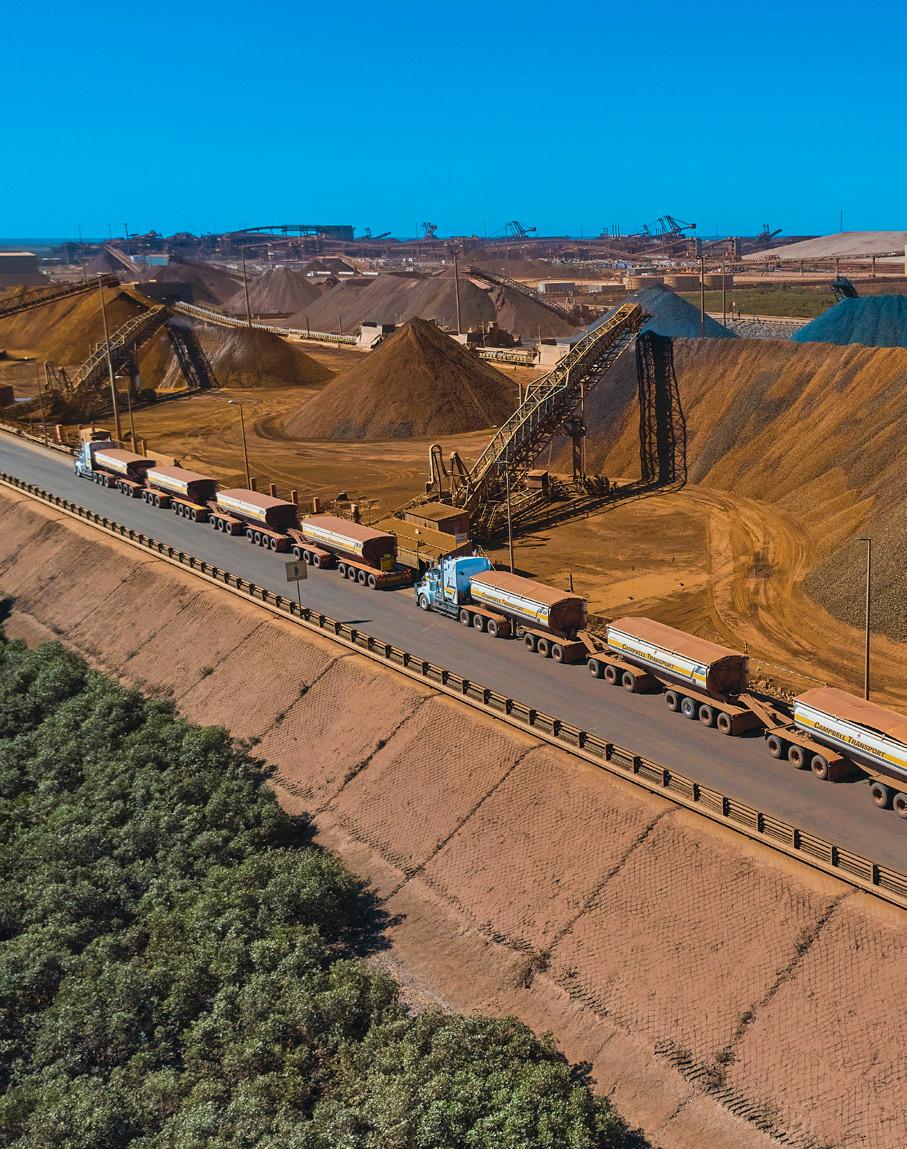
This unobtrusive process prioritises staff welfare and provides a last-ofline defence for drivers, resulting in a significant reduction in driving incidents caused by fatigue.
Drivers’ safety is also monitored by an In Vehicle Monitoring System that gathers critical information and enables around-the-clock observations. The system comprises live GPS and fatigue tracking, truck diagnostics, and the continuous recording of several footage streams.
Regarding the latter, every truck has at least five cameras, each running through an independent system. As a result, in the rare event of an incident, the company knows exactly how and where it occurred. On top of this, a thorough investigation can also be conducted on how best to prevent a reoccurrence.
Given the transportation of goods across many landscapes in WA, the company also recognises the

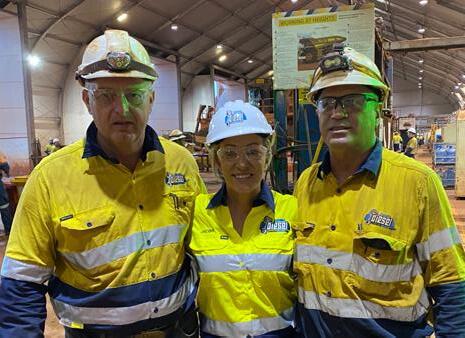
importance of the flora and fauna surrounding its operations. As such, each truck is equipped with ForwardLooking Infrared (FLIR) Thermal Imaging cameras, providing drivers with the visibility to detect heatproducing hazards such as cows, kangaroos, and camels present on the WA’s roads.
This highly-advanced software means drivers can react effectively to any potential incidents, allowing time for greater decision-making when faced with a potential hazard.
Alongside a comprehensive set of safety equipment, Campbell Transport generates regular road reports that create specialist haulage routes that are then examined by a professional safety team, who subsequently publish a detailed report for Main Roads Western Australia – a government body responsible for road access policies across the state.
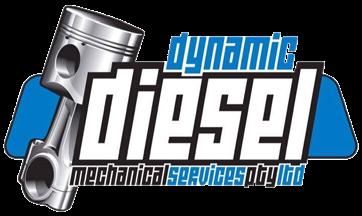
Dynamic Diesel Mechanical Services is your trusted specialist business partner for the provision of highly skilled personnel to the mining, bulk haulage, civil and rail sectors. Established in 2001, Dynamic Diesel has been immensely successful in helping our clients achieve their mission-critical projects and goals. We provide flexible services Australia-wide – whatever you need, wherever you need, we can find the workforce and the solution.
Dynamic Diesel has safety and compliance at the core of everything we do, and our competent personnel always strive for excellence in everything they do.
www.dynamic-diesel.com.au


This detailed and precise report reduces potential incidents, informing the maintenance and repair of many of WA’s arterial roads, including the Great Northern Highway, the Geraldton to Mount Magnet Road, as well as the Coolgardie-Esperance Highway.
Ultimately, Campbell Transport’s trusted and cost-effective transportation and warehousing solutions maximise the operational efficiency and profitability of clients’ projects across multiple industries, whilst also guaranteeing the safety of truck drivers and WA’s flora and fauna.

Tel: (08) 9393 9240
perth@campbelltransport.net.au
www.campbelltransport.net.au
MINE DEWATERING EXPERTS
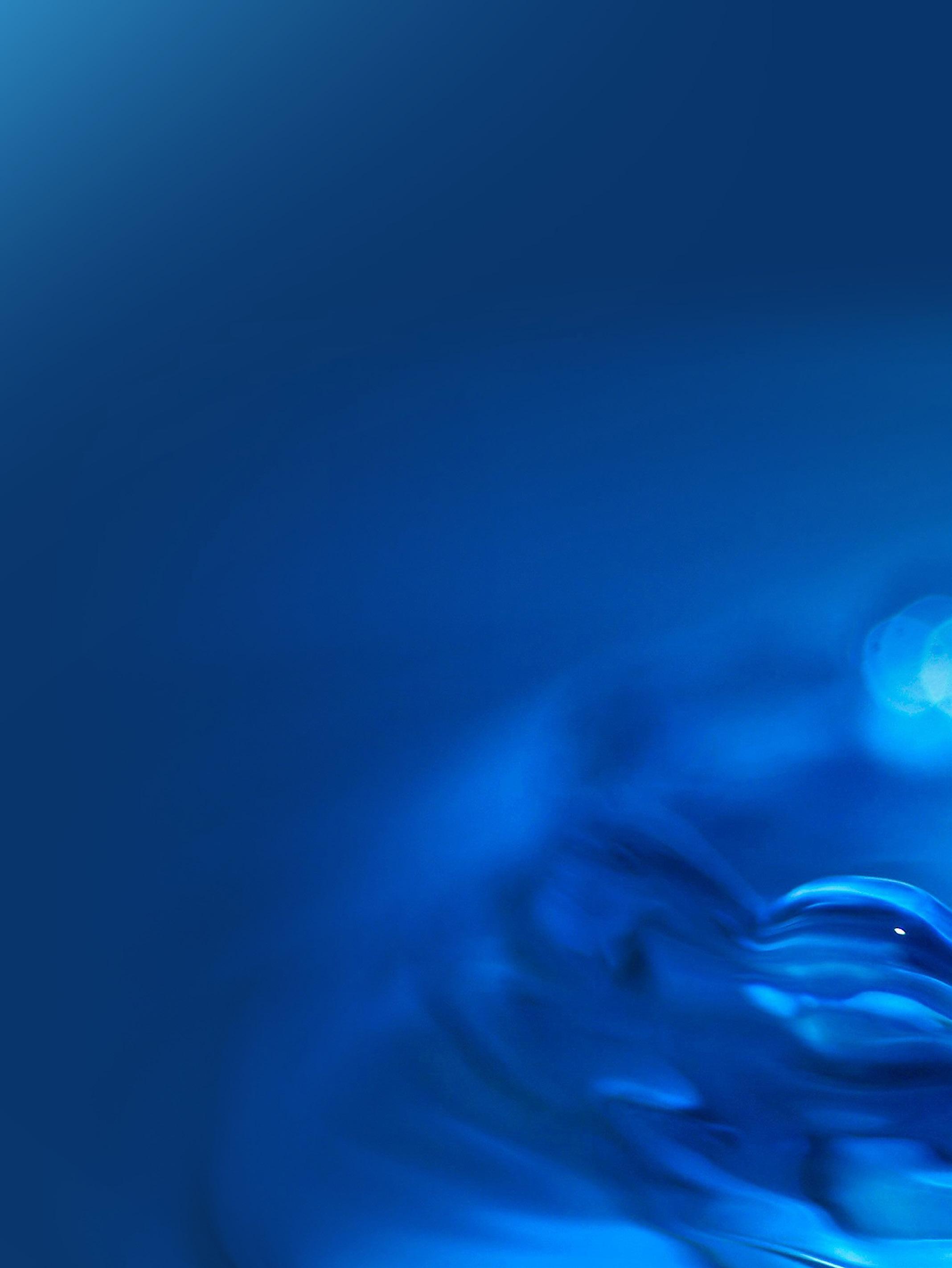
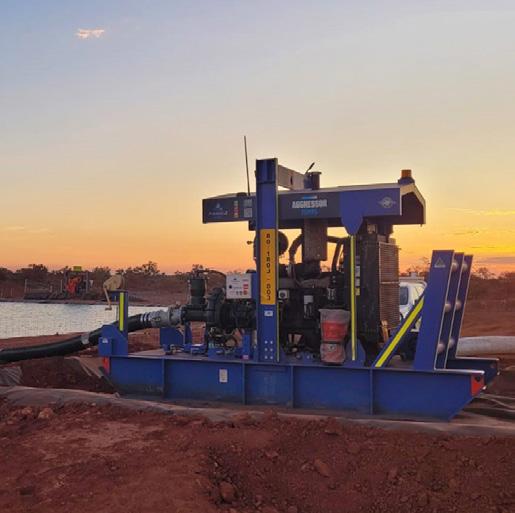
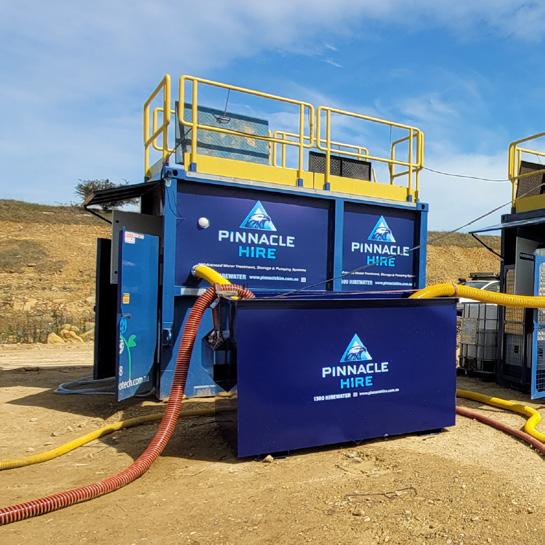
