Cultivating innovation, entrepreneurship, and care
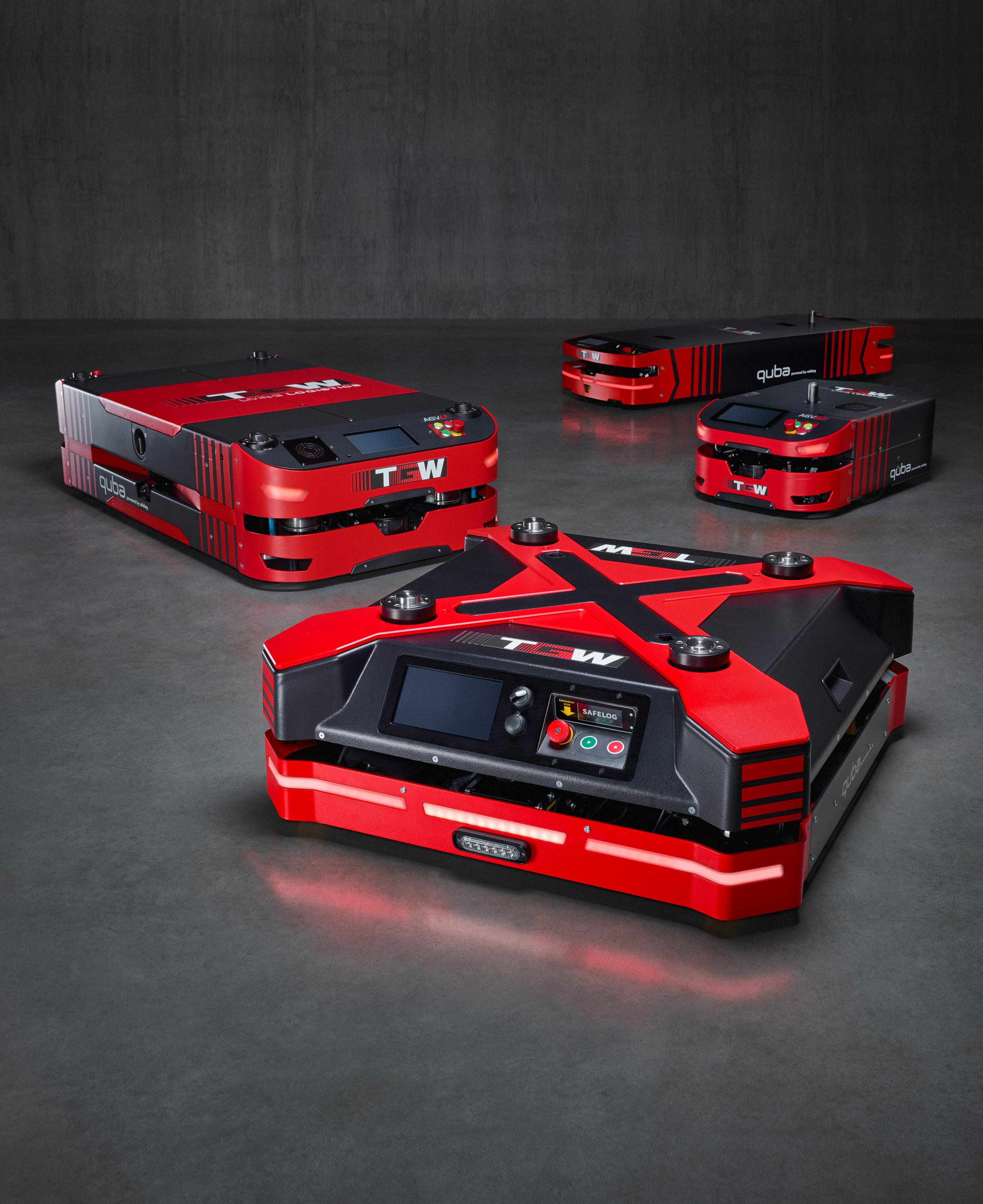
Unrivaled boatbuilding brilliance
Cultivating innovation, entrepreneurship, and care
Unrivaled boatbuilding brilliance
One of the world’s most renowned and trusted names in warehouse automation and logistics
Bill Mazzetti, Senior Vice President of Rosendin Electric, provides a unique insight into the
Africa Outlook, APAC Outlook, EME Outlook, North America Outlook, Mining Outlook, Healthcare Outlook, Manufacturing Outlook, Supply Chain Outlook, and Food & Beverage Outlook are digital publications aimed at boardroom and hands-on decision-makers, reaching an audience of more than 800,000 people around the world.
With original and exclusive content compiled by our experienced editorial team, we look to promote the latest in engaging news, industry trends and success stories from across the globe.
Your company can join the leading industry heavyweights enjoying the free exposure we provide across our platforms with a free marketing brochure, extensive social media saturation, enhanced B2B networking opportunities, and a readymade forum to attract new investment and to help you grow your business.
Visit www.outpb.com/work-with-us for details on how your company can feature for free in one of our upcoming editions.
EDITORIAL
Head of Editorial: Jack Salter jack.salter@outpb.com
Deputy Head of Editorial: Lucy Pilgrim lucy.pilgrim@outpb.com
Senior Editor: Lily Sawyer lily.sawyer@outpb.com
Editor: Ed Budds ed.budds@outpb.com
Editor: Rachel Carr rachel.carr@outpb.com
Editor: Lauren Kania lauren.kania@outpb.com
PRODUCTION
Art Director: Stephen Giles steve.giles@outpb.com
Senior Designer: Devon Collins devon.collins@outpb.com
Designer: Louisa Martin louisa.martin@outpb.com
Production Manager: Alex James alex.james@outpb.com
Digital Marketing Director: Fox Tucker fox.tucker@outpb.com
Website Content Manager: Oliver Shrouder oliver.shrouder@outpb.com
Social Media Executive: Jake Crickmore jake.crickmore@outpb.com
BUSINESS
CEO: Ben Weaver ben.weaver@outpb.com
Managing Director: James Mitchell james.mitchell@outpb.com
Chief Technology Officer: Nick Norris nick.norris@outpb.com
ADMINISTRATION
Finance Director: Suzanne Welsh suzanne.welsh@outpb.com
Finance Assistant: Victoria McAllister victoria.mcallister@outpb.com
CONTACT
North America Outlook
Norvic House, 29-33 Chapelfield Road
Norwich, NR2 1RP, United Kingdom
Sales: +44 (0) 1603 804 445
Editorial: +44 (0) 1603 804 431
SUBSCRIPTIONS
Tel: +44 (0) 1603 804 431 jack.salter@outpb.com
www.northamericaoutlookmag.com
Like us on Facebook: @northamericaoutlook
Follow us on X: @OutlookPublish
Welcome to our 28th edition of North America Outlook.
The eye-catching autonomous mobile robots (AMRs) that appear on this issue’s front cover are those of TGW Logistics.
As one of the world’s most renowned and trusted names in warehouse automation and logistics, the company offers a comprehensive suite of end-to-end automated systems and modular technologies.
These are designed to overhaul fulfillment operations from the ground up and solve a variety of workflow challenges.
Today, TGW Logistics is widely considered a global leader in manufacturing, designing, implementing, and maintaining highly automated, future-proof fulfillment centers for a multitude of industries.
“Our comprehensive approach ensures that we deliver solutions to enhance performance, tackle complex supply chain challenges, and transform distribution centers into strategic assets that support and drive our customers’ growth in an increasingly unpredictable future,” outlines Vice President of Business Development, Stipe Galic.
Cruisers Yachts likewise provides unparalleled performance and comfort for clients through its mid-size luxury vessels.
Possessing a rich boat-building heritage that dates back over 70 years, the company crafts each model with industry-leading design, manufacturing, and amenities.
To further improve its products and offer more boats at a lower price, Cruisers Yachts is constantly looking at new materials, suppliers, building processes, and equipment.
“Additionally, in the near future, we predict that technology will grow to the point where we start seeing more electric and hybrid solutions in larger production yachts. Today, we only see this in small pockets, but we are getting closer each day,” explains Josh Delforge, Vice President of Engineering and Operations.
In the water meter manufacturing industry, metering as a service (MaaS) delivers unmatched benefits with assured performance.
This innovative model is disrupting the traditional approach to advanced metering infrastructure (AMI) deployment, and to date, over 200,000 Kamstrup water meters are under contract with MaaS – a number it expects to double in the next 18 months.
“MaaS includes hassle-free service and performance guarantees that deliver accountability – if a meter is defective or malfunctioning, monthly payments stop for the service and payments don’t start again until it’s verified to be successfully functioning once again,” details Bruce Bharat, Country Manager and Vice President of North America at Kamstrup.
Other top industry performers featured in this latest issue include Paloma Pressure Control, Zgemi, and Morris-Shea.
We hope that you enjoy your read.
Jack Salter Head of Editorial, Outlook Publishing
SUPPLY CHAIN
48 TGW Logistics
Driving Performance and Growth
Creating a smoother automation journey
82 Paloma Pressure Control
Culture at the Core
Cultivating innovation, entrepreneurship, and care
ENERGY & UTILITIES
90 QM Environmental
Building Capacity Together
Committed to safety and Indigenous partnerships
102 Zgemi
Building Beyond Buildings
60 Cruisers Yachts
Handcrafted American Legacy
Unrivaled boat-building brilliance
72 Kamstrup
Water Meter Masters
Smart solutions that buck the trend
96 Morris-Shea
Advanced Deep Foundation Team and Equipment
Laying deep foundations for a brighter tomorrow
Constructing more than just buildingscreating lasting legacies
110 ADCO Electrical Corporation
Energizing the Industry with Impact An illuminating legacy
FOR THE 23RD year in a row, Los Angeles-based marketing company, Distinctive Assets, offered the top 2025 Oscar nominees its exclusive “Everybody Wins” gift bag.
Valued at almost $200,000, the extravagant collection of goodies included cannabis products such as pre-rolls and THC-infused drinks, a four-night stay at a resort in the Maldives, a $5,200 stay at a Barcelona hotel, as well as AncestryDNA’s VIP Family History
Experience in which a genealogist builds the nominee’s family tree.
This year, the gift bags also included skincare products from Swiss brand INSTYTUTUM and luxury pocket squares from Daniel Ashley.
Disaster recovery company Bright Harbor is also offering nominees help with providing personalized disaster recovery support for over 300 families who have been affected by the recent California wildfires.
THE ELECTRIC VEHICLE (EV) revolution of Japanese automotive giant Honda has begun with a $1 billion investment in a new, state-ofthe-art production plant in Ohio. ECONOMY
AMERICANS WERE WARNED to brace for higher prices within days of US President Donald Trump pulling the trigger on his new tariff mandate, imposing tariffs on goods imported from Canada and Mexico.
As numerous US retailers rely heavily on imports from Mexico and Canada to stock their shelves, the tariffs would have resulted in price increases across the board.
However, Trump has since said he would temporarily spare carmakers from a new 25 percent import tax imposed on Canada and Mexico just a day after the tariff came into effect.
The tariff exemption applies to cars made in North America that comply with the continent’s existing free trade agreement.
Further orders have now been signed, significantly expanding the goods exempted from the new tariffs on Canada and Mexico.
The company’s latest facility includes a separate $3.5 billion battery plant, which will serve as the flagship for its global manufacturing operations including its Marysville Auto Plant, a facility that will be capable of producing traditional vehicles, hybrids, and EVs on the same assembly line.
Once completed, Honda will be able to produce roughly 220,000 vehicles annually.
THE US NAVY has terminated its partnership with global security and aerospace company Lockheed Martin for its next-generation wave of stealth fighter jets.
The forecasted new jets are planned to replace the current Super Hornet fleet, which has been in
service since the 1990s.
Instead, the US Navy move forward in collaboration with manufacturers Boeing and Northrop Grumman.
A contract for engineering and manufacturing development will be awarded to the two selected competitors. After the Pentagon has evaluated their designs, a single contractor will then be chosen to produce the jets, which are expected to enter service in the next decade.
Starbucks has made the audacious move to poach CFO, Cathy Smith, from luxury department store brand Nordstrom as its ongoing executive shake-up continues at pace.
across North America.
Smith, 61, joins Starbucks after two years at Nordstrom, replacing veteran Rachel Ruggeri in the role. STARBUCKS MAKES
The change of personnel is the latest for Starbucks after Brian Niccol joined the company as CEO in September, tasked with the goal of turning around slumping coffee sales
REDDIT CO-FOUNDER ALEXIS
Ohanian has joined a substantial bid to acquire TikTok’s US operations in an ambitious move led by billionaire Frank McCourt, who plans to integrate blockchain technology into the popular social media platform.
Ohanian confirmed his involvement in the bid on X, announcing he is joining as a strategic adviser, leveraging his wealth of experience in social media and digital innovation.
The prospective acquisition, branded as the “People’s Bid”, aims to integrate distributed ledger technology into TikTok, meaning the platform’s synchronized digital data would be geographically spread across many sites, countries, or institutions.
AEROSPACE TECHNOLOGY
PRIVATE SPACECRAFT BLUE Ghost has successfully landed on the Moon, joining esteemed historical company as it becomes only the second commercial vehicle ever to reach the lunar surface.
The Blue Ghost mission left on 15th January earlier this year, having been launched by US firm Firefly Aerospace (Firefly) with the intention of exploring the Sea of Crises, a huge lunar basin visible from Earth.
The exciting project is the latest in a series of collaborations by US space agency NASA and a growing list of private companies.
The proud staff at Firefly’s headquarters in Texas broke out into cheering and applause when they were told the landing was successful.
Nathan Pyne-Carter, CEO of award-winning aquaculture technology company Ace Aquatec, discusses how innovation can deliver greater sustainability for the North American aquaculture industry
Writer: Nathan Pyne-Carter, CEO, Ace Aquatec
We’re consuming more seafood than ever, but with growing consumer demand for higher welfare produce, is the aquaculture industry doing enough to address this demand as it treads the line between quality and quantity?
The aquaculture sector is reliably providing 130.9 million tons of produce globally, and we are seeing a trend toward improving welfare practices across several markets
– from Japan to Canada.
This trend is driven, in part, by consumer demand – with some willing to spend around 9.7 percent more for sustainably sourced goods –and, in part, by the desire to improve conditions for workers producing the food and greater operational efficiency in a competitive landscape.
Similarly, restauranteurs are beginning to see the reputational and quality benefits of serving
responsibly sourced, high welfare seafood in their restaurants.
In the US, sushi chefs, for example, are sourcing fish locally, reducing the footprint of imports from Japan while supporting local economies. We’re also seeing this mirrored on grocery store shelves across North America, despite the growing cost of living.
A notable example is Canadian food and pharmacy retailer, Loblaw,
who in 2015 met its commitment to sourcing all seafood from fisheries certified by the Marine Stewardship Council (MSC), farms certified by the Aquaculture Stewardship Council (ASC), or products certified by an equivalent standard – though there is still some way to go for its competitors.
In the UK, meanwhile, recent pledges from leading food retailer, Waitrose, will see the supermarket brand work with suppliers to trial electrical stunning for warm water prawns in partnership with the Shrimp Welfare Project – a project Ace Aquatec is proud to support.
From chefs to local grocery stores, the traceability and accountability of seafood is becoming more and more important in meeting demand.
Of course, the consumer relationship is important, but what about quality? There is a direct relationship between the quality of life of the fish and the quality of the produce on our plates.
We are seeing the emergence of groundbreaking technologies, from hatchery to harvest, that are working to reduce mortality, stress, and disease, and ultimately improve yield.
We know that stressed fish can lead to a drop in quality and shelf life, which is why Ace Aquatec has created an in-water, humane stunning system that keeps fish in water, stunning them insensible in less than a second.
Legislation and regulatory changes have played a part in driving up welfare standards, too. Ahead of new legislation coming into play in Canada, Ace Aquatec’s team recently launched a new skid-based version of its in-water stunner to the North American market.
This system was designed with Canadian producers in mind so they could process trout lakeside in sub-zero temperatures and meet stringent new regulations from The National Farm Animal Care Council (NFACC) under the Code of Practice
for the Care and Handling of Farmed Salmonids, approved by the Ontario Ministry of Agriculture, Food, and Agribusiness (OMAFA).
A phenomenon that touches all aspects of our lives is the advent of artificial intelligence (AI). Rapid advancements in this area present both opportunities and challenges for the aquaculture industry. In response, Ace Aquatec launched its A-BIOMASS® camera in 2024.
This small, highly accurate piece of equipment enables farmers to effectively monitor fish length, height, and weight which, in turn, allows for more efficient feed conversion and reduced wastage.
Similarly, the technology can effectively monitor individual fish through spot pattern markings and identify disease and wounds that may otherwise be missed, further reducing mortality and improving the overall health of the fish.
Data from the camera is fed into Ace Aquatec’s intelligent portal, which also connects third-party application programming interfaces (APIs) on weather, water quality, temperature, and farm operating systems to provide smart insights that help farmers grow their fish intelligently and make real-time, datadriven decisions.
Despite global uncertainty surrounding import tariffs in North America and Europe, with the right technology in place, we can support these markets in meeting the growing demand for high welfare seafood while streamlining business processes to ensure efficient and cost-effective seafood production – taking some of the risk out of farming.
We at Ace Aquatec remain positive and see a path forward for aquaculture and related industries through a program of innovation and
best practice.
From the outset, our vision has been to support the aquaculture industry to become the most sustainable source of food production, with innovation and adaptability at its heart.
I’m heartened to see so many producers working across a range of species putting animal and employee welfare at the core of their business.
I call on industry leaders, producers, and innovators to continue along this path, despite global trading pressures and environmental challenges. In doing so, a blue economy that meets global demands while striving for the highest welfare standards is firmly in our sights.
Nathan Pyne-Carter, CEO of Ace Aquatec, took over the running of the family business in 2012. He grew the company through two investment rounds, with a central office in Dundee, Scotland and regional offices across the globe.
He has been a prominent keynote speaker at industry events including Seafood Expo North America and was named Director of the Year for Tayside and Fife by the Institute of Directors (IOD). He also won the IOD award for National Director of the Year for Innovation in 2019.
Qualified with over 40 years in the data center industry, Bill Mazzetti, Senior Vice President of US electrical contractor, Rosendin Electric, provides a unique insight into the sector’s current and future developments, and its confluence with artificial intelligence
Writer: Lucy Pilgrim
North America Outlook (NA): Firstly, what is your take on the current uptick in data center development and how long do you think this will continue?
Bill Mazzetti, Senior Vice President (BM): That’s what everyone is asking us these days! When you look at both the backlog and recent quarterly calls from hyperscale data centers, everyone is showing robust expenditure for the next three years. All reports indicate that there will be no break in capital expenditure (CapEx) for the foreseeable.
The recent DeepSeek announcement, for instance, really set everything off as many industry players see the company as an artificial intelligence (AI) platform that is not only useful but represents an improvement to Rev.ai, a speech recognition AI platform, and a new look for the large language model (LLM) stack.
However, it doesn’t break the dynamic shift that the computer industry is experiencing from central processing units (CPU) to graphics processing units (GPU).
The announcement also caused a lot of turmoil, but we believe this enables a greater commoditization of AI services. Historically, when commoditization in the technology sector arrives, it actually drives greater demand and further growth, contrary to most industries.
Our clients are certainly voting with their feet and checkbooks right now. We anticipate them doing so for the next several quarters, so we’re optimistic through to 2029.
We don’t see the “crazy busy forever” trend as indefinite, but we feel that this robust build cycle will continue for the next six years, or two complete leasing, procurement, and development cycles. This will allow hardware and facility deployments to catch up with application usage and
the resulting revenue.
Time will tell whether we’ve overbuilt in the short term, hit the sweet spot between data center megawatt (MW) needs and AI demand, or if we’re still short. If you listen to recent interviews from leadership at social media conglomerate Meta and US AI organization OpenAI, it reinforces this opinion.
Some of us at Rosendin Electric are contrarians as we feel there’s a confluence of several factors that could affect facility deployments.
First, the industry can’t keep going at this pace indefinitely; we have all been caught up in the “get it at all costs” AI arms race for the past two years.
Eventually, tech does what tech firms do – it makes things more efficient, drive their customization to a commoditized level, set reference designs and procurement pipelines for their particular business, and drive both adoption and lower costs.
Evidently, none of our clients’ medium to long-term development forecasts have changed after the announcement.
When you look back at the history of the cloud business, there is a precedent. We’re seeing how the next generation of technology is going and how it advances organically, as evidenced by the fact the growth of cloud environments in the past decade has not been linear.
AI is a hardware-centric world where the hardware, operating systems, network, and applications are more homogeneous and similar to the mainframe technology seen in the 1990s.
This is contrary to the heterogeneous cloud reality of blended best-in-class and vertically integrated hardware, software, applications, and networks defined by the end user. It’s basically a major change to known design form factors, or at worst, massive revisions to existing facilities.
“POWER AVAILABILITY IS BOTH THE GREATEST ENABLER AND DISABLER IN DATA CENTER DEVELOPMENT TODAY AND FOR THE FORESEEABLE”
– BILL MAZZETTI, SENIOR VICE PRESIDENT, ROSENDIN ELECTRIC
DeepSeek might require lower MW and time needs, but it does not decrease the overall need for AI computing in the short, medium, or longterm. It may prove to be a good platform for certain AI workloads, but we’ll see what happens to DeepSeek adoption for large organizations and governments over security and data custody concerns.
There is no doubt that the software is thought-provoking, but we have some concerns about its assertion and whether it will displace other LLMs, and existing AI systems.
We also feel that Bloomberg’s coverage on DeepSeek was not entirely forthcoming for the company’s total cost.
Time will tell how truthful its reporting was, and to be honest, we’re doubtful that Bloomberg stated all the costs on an apples-toapples basis from what we’ve seen in North America, the European Union, and the UK.
Several industry thought leaders are sceptical of the cost to complete the DeepSeek model but not the code and application itself.
The software is head-turning, open-source work, but it won’t be the only AI system to be employed by our clients. We also don’t believe that it will slow data center development in the next several years.
NA: Will end users or developers be the driving force behind data center facility development? If so, what will their roles be?
BM: The short answer is that everyone’s busy, and we feel this pace will continue for the next three to five years.
The building of facilities and this demand starts with the end user. We’ve seen some swings in the split between end user and developer-delivered facilities. This has been the reality of data center development for the past two decades.
We take a more macro view of the market. For us, it’s about the MWs delivered per year in a given market or region.
The capital plans of our end users are arranged years in advance, so all of us who work in the space – designers, builders, manufacturers – have pretty good visibility.
That said, it’s been the busiest time for facility delivery that we’ve seen in the past 15 years, which is driving an
all-hands-on-deck approach where both end users and developers are working through the former’s facility needs.
It also drives a matrixed and nuanced approach to the location of facility developments, which is based around where power is available, permits and entitlements are not particularly onerous, the end user or developer has a footprint to execute, and how relevant historical markets are to the needs of the facility being presented. These conditions will drive developers or end users to deliver facilities depending on the market.
Today’s reality is that all the usual suspects are aligned with a stable of developers and end users, which tends to focus firms on specific regions or clients.
We have seen a strong trend over the past two years for many newer, larger developments in the 1+ gigawatt (GW) range to become developerdelivered, which we expect to continue for a number of reasons.
Firstly, end users can’t scale their
staff to face builds of this magnitude as quickly as developers can.
Second, the campuses used, and likely the power plants that may accompany them, are very capitalintensive. While our end users are successful, we feel that they are allocating their capital to technology, building up their GPU base and AI-specific applications.
NA: What is the greatest enabler and biggest concern in data center development?
BM: Power availability is both the greatest enabler and disabler in data center development today and for the foreseeable.
Sites and areas that have power will attract the lion’s share of these major developments. We’re also seeing power developers entering and partnering in key data center markets and energy development taking place in the utilities service areas that support these large data center advancements.
We’ve also seen alternative energy being embraced by end users in developed areas short of power. This has been an issue we’ve been promoting for a while; I guess it just took time for folks to catch on. When you’re starving, your palate is forced to expand!
Some of our other biggest concerns also include project enablers or killers, such as regulation, entitlement difficulties, NIMBYism, and a rising tide of negative outlooks toward data center development in some markets.
Indeed, AI data centers aren’t truly different from their generational predecessors, they’re just bigger projects.
Without getting into specifics, overcoming this starts with ground-up education across all project constituents, including state, county, city, and town officials, regulatory agencies, and most importantly, the people that live in
“THERE IS A STRONG TREND TOWARD RETROFITTING
AND
SIMPLY
TOO MUCH FIBER AND INVESTMENT GOING INTO THESE OLDER FACILITIES TO IGNORE THEM, BUT THEY REQUIRE MASSIVE COOLING SYSTEM UPGRADES IN THE MIGRATION FROM AIR-BASED TO WATERBASED COOLING”
– BILL MAZZETTI, SENIOR VICE PRESIDENT, ROSENDIN ELECTRIC
and around the job site.
We’ve seen several instances where developers have tried to ride roughshod over a town to push a development through without diplomacy and sensitivity to any of these parties.
On the other side of the coin, some areas have become negative and obstructive toward data center development. In that situation, and over the next few years, those areas will need a time-out.
NA: What are the hottest markets for data center development?
BM: AI markets have been the hottest in the US based on export restrictions on Nvidia’s top-of-the-line systems, but we’re not seeing the same demand outside the US.
Development follows power availability these days. This falls into three categories – the interconnection queue at regional utilities, available power that resides in a utility’s service
area, and the ability to develop co-located or near-located power plants with a data center campus.
Right now, the hottest markets are a mix of some historic places in Western and Central Texas, including Houston, Amarillo, Midland and Odessa, as well as Oklahoma and the Phoenix-Tucson corridor. In the Southeast US, other markets include Memphis, Nashville, Montgomery, and Atlanta. There’s also a bunch of legitimate activity in Northern Ohio, Illinois, and Western Pennsylvania.
NA: Stakeholders are weighing up the benefits of the increased speed of upgraded facilities and cooling systems versus the longer lead times for greenfield developments using the latest technology. What is your view on this?
BM: What an insightful question. Firstly, CloudTech is not going away, nor is storage. All that data has to virtually live somewhere!
There is a strong trend toward retrofitting and simply too much fiber and investment going into these older facilities to ignore them, but they require massive cooling system upgrades in the migration from airbased to water-based cooling.
The rest of the improvements are system churns that we typically see with any technology update, with everything still working on a three megavolt-ampere (MVA) main switchboard (MSB) basis.
Greenfield developments are the core driver in today’s markets and we are seeing them get a lot bigger. 10 years ago, a big data center was 30MW, now they have grown to 100MW, with multiple buildings being delivered in 300MW tranches. This not only speaks to our point about deal and project flow, but also refers to the deep backlogs on the fulfillment side of the industry. It also means that there’s not enough MWs on a mature campus
to accommodate these larger AI facilities.
NA: Finally, do you believe that data centers can be future-proofed, and if so, how?
BM: Great question. I’m not sure there’s a way to futureproof facilities between a CPU versus a GPU environment.
It’s an easier question to answer electrically versus mechanically. As mentioned, AI requires water for direct cooling to the cabinet, a technique that harks back to the 1990s when continuous cooling and thermal storage were required and is a hard pivot away from the air-based cooling of cloud facilities.
While this is a tactical change, by adding an uninterruptible power
supply for cooling systems in an electrical MSB line-up, AI requires a pivot from air-based to water-based cooling.
Due to the amount of evaporative cooling required, this pretty much kills off any open-circuit cooling system. Likewise, cooling system tonnage serves the whole data center load and can be delivered via air-side coils, direct connection to an AI system, or a mixture of both.
This forces a tough balance if one has a strong mix of CPUs and GPUs in the same facility, as the last-mile heating, ventilation, and air conditioning (HVAC) or cooling solutions are diametrically opposed.
Thankfully, there are some recently released HVAC systems that provide air and water-based cooling, and that’s a brilliant start.
Tech behemoth, Apple, recently revealed plans to invest $500 billion into the US over the next four years. We explore how this will advance the corporation’s manufacturing footprint and boost opportunities in communities nationwide
Writer: Lucy Pilgrim
Atech giant that needs no introduction, Apple has had a tight grip on the global market for decades, thanks to forward-thinking technological solutions and innovative devices that have continued to revolutionize the international landscape.
In its latest development, the company has announced its largest ever spending commitment of $500 million into the US domestic market over the next four years, helping to cement its world-class position.
This marks a new chapter in Apple’s ongoing investment in the nation’s manufacturing capabilities, paving the way for team and facility expansion across the US, including Michigan, California, Arizona, Nevada, Iowa, Oregon, North Carolina, Washington, and Texas.
Apple currently supports more than 2.9 million jobs across the country, alongside working with predominantly US-based suppliers and manufacturers.
As such, the significant financing will also support the development of crucial initiatives around artificial intelligence (AI), silicon engineering, and skills development in local communities across the US, making this an investment in not only the company’s future but the US domestic tech market.
Alongside the expansion of Apple’s existing factory in Texas, the state will also welcome a brand-new server manufacturing facility, with production scheduled to begin in Houston later this year.
The 250,000 square foot (sqft) factory is expected to create thousands of local jobs once it opens its doors in 2026 and foster a greater level of domestic manufacturing, as the servers will no longer be manufactured overseas.
This technology will play an integral role in the developmental infrastructure for Apple Intelligence, a personal intelligence system that helps iOS users write, express themselves, and get things done.
The server’s primary function, however, revolves around Private Cloud Compute, the amalgamation of high-power AI software with the most advanced security architecture ever deployed in the tech sector. As such, the server represents years of unmatched R&D by Apple engineers, which is to be combined with industry-leading silicon system capabilities.
Once developed, the servers will lessen the recently heightened demand for Apple’s data centers.
Thanks to its development of Apple Intelligence, the company also has ambitious plans to expand its data center capacity in North Carolina, Iowa, Oregon, Arizona, and Nevada.
The $500 billion investment will also be allocated to doubling Apple’s US Advanced Manufacturing Fund, created eight years ago to support international innovation and highly-skilled manufacturing job opportunities across the country.
The company’s recent contributions will boost the fund from five to $10 billion, which will also be put toward the Taiwan Semiconductor Manufacturing Company’s (TSMC) Fab 21 facility in Arizona, which Apple utilizes to produce advanced silicon and mass manufacture chips used in its devices.
The silicon produced enhances the company’s products by unlocking unparalleled features, power efficiency, and high performance in its devices.
As it stands, Apple’s vast supplier network already manufactures chips across 24 factories in 12 states, with the corporation’s multi-billion-dollar commitment helping create highpaying jobs across the country.
More broadly, the US Advanced Manufacturing Fund has helped support local businesses and
train workers across 13 states, accelerating community growth while simultaneously bringing forwardthinking manufacturing processes and materials for Apple devices to the fore.
Apple’s projected investment in R&D follows a pattern of increased spending in this area, having nearly doubled its domestic advanced R&D investments over the last five years.
The fruits of this labor are showcased in the corporation’s latest release, the iPhone 16e, which enhances users’ experience with smooth performance and the longest battery life yet, all thanks to the worldclass efficiency of the A18 chip and Apple C1.
The latter marks a new era in Apple’s silicon chip development and is a representation of how far the company’s capabilities have evolved in a modern market and the technical prowess of its engineering team.
Apple C1 is a key part of the corporation’s long-term strategy that will allow it to further innovate and optimize its systems for future Apple devices.
On top of this, the company plans to recruit over 20,000 employees to join its R&D department, as well as its silicon engineering, software development, AI, and machine learning (ML) operation, which will be channeled through the investment in R&D hubs across the US.
Apple’s multi-billion-dollar investment and the drive for increased manufacturing capabilities will have a substantial impact on the company’s manufacturing supplier network.
Therefore, the corporation has created the Apple Manufacturing Academy to support small to mediumsized enterprises (SMEs) in the transition to advanced manufacturing and the implementation of AI and smart manufacturing techniques.
Situated in Detroit, the academy will offer both in-person and online courses with Apple engineers and industry experts from the country’s top institutions, such as Michigan State University.
The curriculum will center around vital skills development in various areas, including project management and manufacturing process optimization, helping to enhance productivity, efficiency, and quality in small businesses’ supply chains.
The Apple Manufacturing Academy is part of the company’s wider commitment to education and skills development for students and workers across the US.
This is characterized by the increasing number of grant programs awarded to a vast range of charitable youth organizations, including 4-H, Boys & Girls Clubs of America, and Youth First, which works closely with Apple in local communities to create free programs that facilitate the education of the nation’s young people in vital skills such as coding.
Apple’s commitment to future generations is also demonstrated by its New Silicon Initiative (NSI), which prepares students for future job opportunities in hardware engineering and silicon chip design.
Established at the Georgia Institute of Technology in 2024, the NSI now extends to eight universities across the country with exciting future plans, including a collaboration with UCLA’s Center for Education for Microchip Designs (CEMiD), which began earlier in the year.
Overall, Apple’s multi-billiondollar investment will not only boost the company’s manufacturing presence and eventual nationwide product roll-out but also foster skills development among local communities and education institutions across the US.
Ahead of the grand opening in May, we explore SUPER NINTENDO WORLD™, where guests can jump into the universe of beloved Nintendo characters such as Mario, Luigi, Princess Peach, Toad, and for the first time in the US, Donkey Kong
Writer: Jack Salter
From the fun of Mario Kart™ to careening through Donkey Kong Country™, visitors will soon be able to experience all the interactive excitement on offer at SUPER NINTENDO WORLD™, opening on 22nd May 2025.
It is one of five amazing worlds that will comprise Universal Epic Universe, a transformational theme park currently under construction in Orlando, Florida that will immerse guests in beloved cross-generational stories, empowering them to be the epic heroes of their own adventures.
Developed in partnership between the visionaries of Nintendo and Universal Creative, SUPER NINTENDO
WORLD™ combines the former’s iconic characters with the latter’s renowned craft of creating innovative theme park experiences.
As such, the vibrant land delivers a multisensory environment where guests will experience the fun and adventure of Nintendo games in a whole new way.
The Orlando site will be the third installment of SUPER NINTENDO WORLD™, which can also be enjoyed in Los Angeles, California and Osaka, Japan.
It all begins the moment visitors
enter the portal to this immersive world, which will transport them through the infamous green pipe synonymous with Super Mario to the second level of Princess Peach’s Castle.
Emerging from the pipe, they will be surrounded by the vibrant scenery of the Mushroom Kingdom and greeted by familiar sights and sounds from the Nintendo franchise, including swaying Piranha Plants, pacing Goombas, spinning coins, ‘?’ Blocks, and more.
SUPER NINTENDO WORLD™ will be divided into two areas – Super Mario
Land™ and Donkey Kong Country™.
In Super Mario Land™, visitors will put on their goggles and steer through iconic courses alongside Mario, Luigi, and Princess Peach on Mario Kart™: Bowser’s Challenge.
An interactive ride with multiple different outcomes every time, the challenge is to try and defeat Team Bowser and win the Golden Cup by collecting digital coins, throwing shells, dodging obstacles, and more.
Those up for the challenge will enter through the winding corridors of Bowser’s Castle before boarding their kart, heading to the start line, and competing to help Team Mario to victory.
THROUGHOUT SUPER MARIO LAND™ and Donkey Kong Country™, guests will be able to level-up their fun by purchasing a Power-Up Band.
This enables wearers to collect digital coins by punching ‘?’ Blocks and playing interactive activities, accumulate digital stamps on attractions, earn digital keys to unlock an exclusive showdown against Bowser Jr., and discover other hidden surprises.
Those with a Power-Up Band will also get to access leaderboard screens in SUPER NINTENDO WORLD™ to see where they rank among their fellow guests.
The ground-breaking attraction fuses augmented reality, projection mapping technology, and elaborate environments to bring the Mario Kart™ video game series to life in a compelling ride-through experience.
Elsewhere in Super Mario Land™, the little ones will love Yoshi’s Adventure™, an enchanting, familyfriendly attraction making its US debut.
This colorful adventure weaves through iconic Mushroom Kingdom landscapes, with glowing eggs to search for and familiar characters to encounter along the way.
At the edge of Super Mario Land™, there will also be plenty of action and fun on offer in Donkey Kong Country™, a lush, tropical landscape complete with towering trees, waterfalls, and landmarks such as the majestic Golden Temple.
Here, guests will help Donkey Kong and Diddy Kong protect the coveted golden banana in Mine-Cart Madness™ and more.
Entering the Golden Temple, this thrilling first-of-its-kind family coaster appears to jump across gaps in the track and perform other eye-popping feats and maneuvers from the video game series.
Mine-Cart Madness™ utilizes an unprecedented ride system, innovative technology, and a unique coaster design.
Play won’t be paused for long when looking for great food at SUPER NINTENDO WORLD™, as there will be plenty of restaurant and dining options available.
At Toadstool Cafe™, while watching the playful scenery of the Mushroom Kingdom through the windows, visitors
MARIO AND LUIGI – There’s no mistaking the brothers’ famous caps and mustaches!
PRINCESS PEACH – Enjoy an audience with Princess Peach in her gazebo.
TOAD – He may be small, but Toad has a big smile and a big heart.
DONKEY KONG – Go bananas over the most famous resident at Donkey Kong Country™.
will power up with Chef Toad’s tasty creations, including the Mario Burger, Luigi Burger, and Bowser’s Fireball Challenge.
Inspired by his favorite food, Yoshi’s Snack Island™, a cozy burrow tunneled into the base of Mount Beanpole, provides a variety of juices and fruit-based specialty beverages.
For some Mario Kart™ race day snacks, a pit stop at Turbo-Boost Treats will refuel guests with whatever their appetite is revved up for.
The Bubbly Barrel, meanwhile, offers tropical drinks in the heart of Donkey Kong Country™, the perfect place for refreshments on a jungle adventure.
Once refueled, guests will be ready to resume play at SUPER NINTENDO WORLD™.
SUPER NINTENDO WORLD™ Tel: (407) 363-8000
www.universalorlando.com
With an economy supported by strong legislative and regulatory frameworks, a robust foreign investment program, and political stability, Grenada’s investment climate is thriving
Writer: Lily Sawyer | Project Manager: Krisha Canlas
An increasingly attractive investment destination, Grenada has certainly recovered from the prior impacts of the COVID-19 pandemic, which saw the country’s tourism-driven economy decline.
Bouncing back, 2022 saw Grenada’s GDP grow by a robust 7.3 percent, followed by a healthy 4.8 increase the following year. This is due, in part, to the strong performance of the tourism, manufacturing, and construction sectors during this period.
Today, one of the fundamental objectives of Grenada’s government is to promote private sector and foreign direct investment (FDI) activity on the island to facilitate continued economic growth.
Specifically, Grenada continues to experience a wave of FDI through its highly successful Citizens by Investment (CBI) program, which was introduced in 2014 as an investment migration scheme offering participants a second citizenship through investment. It was subsequently rebranded to the Investment Migration Agency (IMA) in 2024 to emphasize due diligence and attract local support.
The program has seen unprecedented applications and continues to provide support for stakeholders looking to navigate the island’s business landscape.
In addition to IMA, Grenada offers a comprehensive range of investment incentives, including investment allowances, deductible expenditures, and customs duty exemptions.
Ronald Theodore, CEO of the Grenada Investment Development Corporation, outlines the organization’s critical role in facilitating investment on the island, alongside plans to continue its targeted investment model, infrastructure development, and policy advocacy going forward
North America Outlook (NA): Firstly, could you introduce us to the Grenada Investment Development Corporation, including your three strategic business units? How do they nurture and promote Grenada as a prime investment and business development location?
Ronald Theodore, CEO (RT): The Grenada Investment Development Corporation (GIDC) was established in 1985, and on 1st March this year, we’ll be celebrating our 40th anniversary. I strongly believe that, over these 40 years, we have made a solid impact on Grenada’s economy.
As an organization, GIDC has three strategy-based business units – the Investment Promotion Agency (IPA), the Business Development Center (BDC), and the Facilities Business Unit (FBU).
Through our business units, we see ourselves doing more than just promoting investment. While most
Caribbean countries have an active IPA, we have other units that comprise GIDC; thus, we see ourselves as more of an economic development agency. First and foremost, the IPA promotes and facilitates investment on the island, assesses investors, advises on the do’s and don’ts, and provides information on Grenada’s legal and regulatory framework.
We also facilitate the grant of incentives to qualifying investments. The IPA is additionally involved in aftercare, providing post-investment support.
Elsewhere, we are heavily involved in policy advocacy. By meeting with investors and businesspeople alike, we have a clear understanding of what they would like to see happening in Grenada’s business environment, and we make policy recommendations to the government on potential changes inclusive of investment incentives and tax reforms.
The BDC, meanwhile, works with micro, small, and medium-sized enterprises (MSMEs).
GIDC has a suite of packages and services on offer to allow MSMEs to grow from strength to strength, not only assisting with business name registration and company incorporation, but playing an instrumental role in providing training to MSMEs through its two training centers, where individuals are trained in several areas such as QuickBooks, record-keeping, business plan development, and customer services. Training is carried out either by GIDC or external facilitators. Most of our training is demand-driven and based on the requirements of our MSMEs.
We carry out diagnostic studies and advise on pricing and costing for MSMEs in addition to a suite of packages. Then, there is grant assistance, through which we help entrepreneurs complete the sometimes cumbersome grant forms.
Meanwhile, the FBU has three business parks –Frequente, St. Patrick’s, and Seamoon – and we remain the largest landlord on the island with approximately 60 tenants.
The FBU occupies 285,000 square feet (sqft) of commercial space on 38 acres of land across the three parks. Various operations take place, including agroprocessing, manufacturing, and business process
outsourcing (BPO), and our role is to ensure tenants are satisfied while continuing to make new space available for emerging businesses.
GIDC’s shared services provide support to strategic business units, namely financial, human resource management, legal, research, and monitoring and evaluation.
NA: What did GIDC initially set out to achieve when it was established as the Grenada Industrial Development Corporation back in 1985? How have you evolved since?
RT: GIDC was established to assist investors doing business on the island and play a critical role in facilitating investment incentives.
When we were first established, there were pieces of legislation which allowed investors to benefit from incentive support, both within the manufacturing and hotel sectors, which at that time were the two main areas investments facilitated.
Back then, GIDC’s approach was very reactive –investors would decide to invest on the island, and we would assist them with incentive support and in securing necessary consents and licenses.
Its strategic goal is to promote local and foreign investment, facilitate and strengthen entrepreneurial development within the growth sectors of Grenada’s economy, which comprise:
1. Tourism and hospitality services – Focusing on niche areas such as boutique hotels and the marina sector.
2. Agribusiness – With a focus on adding value to local produce such as fishing and fresh produce and developing farming through methods such as hydroponics and vertical farming.
3. Health and wellness – Targeting investments in retirement homes and wellness and rejuvenation centers.
4. Information and communication technology (ICT) –With a focus on further expanding our BPO sector.
5. Energy development – With a focus on renewable energy opportunities such as solar, wind, and geothermal, as well as assembling solar panels and water heaters.
GIDC’s BDC was established in 2005 to provide muchneeded business support to MSMEs.
Our industrial park facilities in Frequente, Seamoon, and St. Patrick’s continue to be prime locations for entrepreneurs, as demonstrated by a steady increase in occupancy rates.
We are currently constructing a 40,000 sqft building to provide additional commercial space for businesses to operate. Construction commenced in September 2024 and is expected to be completed in June 2025.
We are also seeking further land that can be developed to expand our park facilities and constantly looking at opportunities and creative ways to grow the stock of buildings within our parks.
From the promotional side of things, we’ve become
increasingly involved in marketing Grenada as an investment destination. We are cognizant of the benefits of FDI, so our approach toward investment is now more targeted, utilizing investment opportunity profiles.
As we target investors for our priority sectors based on their specific investment interests, we will be developing bankable specific opportunity profiles with clear details on investments, return on investment (ROI), and payback periods.
VISION – To be globally recognized as a highly-rated, innovative economic development corporation.
MISSION – GIDC strives to continue contributing to Grenada’s socio-economic development by:
• Adopting a targeted approach to promoting investment opportunities
• Providing superior investor facilitation and entrepreneurial development services
• Advocating for a supportive enabling environment for investors to develop and grow business, trade, and industries.
GOAL – To promote local and foreign investment and facilitate and strengthen entrepreneurial development within the growth sectors of Grenada’s economy.
We’ll continue our work in this area throughout 2025 and beyond as we realize that a targeted approach to investment is definitely necessary.
In short, our role has certainly evolved since 1985. This is reflected not only in changes to our name but also in the impact we’ve had on the economy in terms of job creation and attracting FDI.
NA: What is your current take on Grenada’s economy? What recent challenges or opportunities have you faced?
RT: I’d say Grenada’s economy is diverse, and this has contributed to its growth over the years.
While tourism is a major contributor, the agriculture sector plays an instrumental role in economic growth. We continue to be a major exporter of spices such as nutmeg, cinnamon, and more – Grenada is known as the ‘Spice Isle’. Meanwhile, the export potential of our fish is also notable.
When it comes to education, our accredited medical school, St. George’s University (SGU), has continued to contribute tremendously to the economy since its establishment in July 1976. One statistic I am particularly proud of is that approximately one out of every 100 doctors currently practicing in the US is an SGU graduate.
We also have our IMA, which promotes our robust CBI program and assists investors to obtain enhanced global mobility and other benefits of being a Grenadian citizen. Overall, our economy is diverse and doesn’t solely rely on a single aspect, but it also has challenges. From an investment perspective, Grenada’s population of just 110,000 is considerably small. However, investors must also consider external markets – we are part of the Caribbean, so you’re actually looking at a combined population of over 44 million.
There is also the issue of the cost of electricity, however this presents an opportunity for alternative and renewable energies to augment these costs.
Natural disasters also have the potential to negatively impact our investment landscape. Although the island lies on the outskirts of the hurricane belt, last year Hurricane Beryl caused some devastation to our tourism and agriculture sectors. This presented the opportunity to rebuild – and rebuild better.
We are aware of these challenges as we continue to promote investments, cognizant that Grenada is, indeed, a preferred location for investment.
There are several things that make us an attractive investment destination, from the stability of our government to our excellent quality of life. It’s also very easy to do business on the island, repatriate profits, and move currencies. The abundance of investment opportunities to be explored is also of great importance.
In life, there are always challenges, but we constantly strive to improve, enabling a conducive business environment.
“THROUGH OUR ACTIONS, WE HOPE TO REMAIN DYNAMIC, RELEVANT, AND AN EFFECTIVE CONTRIBUTOR TO GRENADA’S ECONOMY”
– RONALD THEODORE, CEO, GRENADA INVESTMENT DEVELOPMENT CORPORATION
NA: How do you represent the collective interests of your members?
INVESTMENT FACILITATION – Through the IPA, GIDC offers robust solutions for stakeholders looking to navigate the island’s business landscape.
BUSINESS DEVELOPMENT – The BDC acts as a gateway for entrepreneurs to thrive in Grenada, providing technical assistance, training, and support for start-ups.
FBU - Accommodates both local and foreign investors, providing best-in-class mixed-use facilities to ensure sustainable business growth.
We recently revised our incentives framework to be performance-based and compliant with the World Trade Organization (WTO) rules and obligations. So yes, we have done a lot of work in terms of creating and fostering an environment that facilitates doing business on the island.
RT: There are several players within Grenada’s investment generation system and we try to work closely with each player.
The Inland Revenue Division, National Insurance Scheme, Physical Planning Unit, Department of Labor, and Grenada Bureau of Standards, among others, are all involved in investment generation on the island, so GIDC must establish a strong network and collaborate effectively with each player for the common good.
To ensure that the interests of all our clients and investors (existing and potential) are met, we disseminate relevant information via various mechanisms including social media.
In addition, through our targeted approach to investment, we reach out to existing and potential investors within our priority sectors who may be looking to expand, diversify, or obtain investment, compile said information, and approach investors looking for equity, a joint venture (JV), or shares opportunities.
NA: How do your best-in-class mixed-use facilities, such as your business parks, facilitate the development of sustainable business in Grenada?
RT: I say this with a smile on my face – GIDC facilities are deemed a preferred location to establish operations. In
addition to the location and aesthetics, our rental rates are more competitive.
We’re currently looking for opportunities to expand the parks, including creative methods to build out additional space, inclusive of JV arrangements between the private sector and GIDC. We also have some vacant land available which could be ideal for investors to build out themselves.
I am always pleased when considering the multiplier effect that our business parks have on our economy.
NA: Finally, how do you see Grenada’s economic climate developing in the next five years, and how do you plan to action GIDC’s key priorities going forward?
RT: I believe Grenada’s economy will continue on a positive growth trajectory. The current numbers in terms of investment inquiries are strong, which is a clear indication of investors’ confidence.
Over the last five years, I’ve only seen these numbers increase, both from domestic and foreign sources.
Grenada’s CBI program continues to attract investment, and we anticipate additional investment in other sectors apart from hotel and real estate.
There is definitely a need to enhance Grenada’s food security, and this presents investment opportunities within the agriculture and agribusiness sectors. There are opportunities to diversify from traditional methods of farming to alternatives such as vertical farming and hydroponics.
Our government is committed to the development of a state-of-the-art hospital. Land has already been secured for construction, which is set to commence in 2026. This development will transform Grenada’s health and wellness sector and attract investment in other niche opportunities such as retirement homes and rejuvenation centers.
From GIDC’s perspective, we will continue a targeted approach to investment during 2025 and beyond. Our outreach must be accompanied by developed opportunity
“OUR ECONOMY IS DIVERSE AND DOESN’T SOLELY RELY ON A SINGLE ASPECT”
– RONALD THEODORE, CEO, GRENADA INVESTMENT DEVELOPMENT CORPORATION
profiles that clearly outline each project investment cost, ROI, and payback periods.
In terms of the enabling environment for investors, efforts will be made to continue to enhance and streamline the existing incentive regime to ensure it is dynamic and meets the needs of investors as well as the processes and procedures to obtain consents and licenses.
There are several events in 2025 where we will ensure our presence, including the World Expo 2025 in Osaka, Japan and the AfriCaribbean Trade and Investment Forum that will be held in Grenada this July.
As it relates to entrepreneurial development, we will continue to promote entrepreneurship, especially among young people, and actively have outreach programs at our schools.
AUSTRALIAN ENERGY PRODUCERS
We will also continue to enhance the infrastructure within our parks to ensure we remain a preferred location for businesses to establish and grow.
Tel: 0000000000 xxxxxxxxxx@xxxxxxxxxxxx www.xxxxxxxxxxxxxxx.com.au
1st March marked 40 years of GIDC’s existence, and we look forward to the next 40. Through our actions, we hope to remain dynamic, relevant, and an effective contributor to Grenada’s economy.
Tel: 1 (473) 444-1033 to 35 contactus@gidc.gd www.gidc.gd
Known as the “Spice Isle” of the Caribbean, Grenada presents a unique blend of business opportunities and challenges
Writer: Jack Salter
Grenada’s strategic location, stable political environment, and attractive investment incentives make it a promising destination for entrepreneurs and investors.
However, understanding the local business landscape is crucial for success.
We explore key aspects of doing business in Grenada, including the economic environment, legal framework, investment opportunities, cultural considerations, and practical tips for navigating the business climate.
Grenada’s economy is primarily driven by tourism, agriculture, and services.
The country has experienced consistent economic growth in recent years, supported by government-led infrastructure projects and a robust tourism sector.
The International Monetary Fund (IMF) projects continued growth, making Grenada an attractive option for investors.
Key economic sectors include:
• TOURISM – The largest contributor to Grenada’s GDP, tourism is a cornerstone of the economy. The island’s natural beauty, including white sandy beaches, waterfalls, and lush rainforests, attracts visitors from around the world.
• AGRICULTURE – Grenada is famous for its spices, particularly nutmeg
and cocoa. The agricultural sector provides employment and export revenue, with opportunities for investment in organic farming and agribusiness.
• REAL ESTATE AND CONSTRUCTION – The government’s Citizens by Investment (CBI) program has spurred growth in the real estate sector, with numerous luxury resorts and residential developments underway.
• RENEWABLE ENERGY – Grenada is committed to reducing its dependence on fossil fuels, creating opportunities for investment in solar, wind, and geothermal energy projects.
GREETINGS – A friendly handshake and polite conversation are customary.
PUNCTUALITY – While business meetings may start slightly late, punctuality is generally appreciated.
–
Grenadians value courteous and respectful communication. Avoid aggressive negotiation tactics.
The legal and regulatory framework is another key aspect of doing business in Grenada, whose legal system is based on English common law, offering a transparent and predictable business environment.
The government has implemented several reforms to streamline business registration and promote investment. For business registration and investment facilitation, meanwhile, the Grenada Investment Development Corporation (GIDC) serves as a one-stop shop.
The process typically involves reserving a business name, registering the company with the Corporate Affairs and Intellectual Property Office (CAIPO), obtaining a Taxpayer Identification Number (TIN), and applying for business licenses and permits.
Grenada also offers a range of incentives to attract foreign investment, including:
• Tax holidays of up to 15 years.
• Duty-free importation of equipment and materials.
• Exemptions from VAT on certain investments.
• Special incentives for tourism, manufacturing, and renewable energy projects.
Understanding Grenadian culture is essential for building strong business relationships, with the island’s culture reflecting a blend of African, French, and British influences.
Building relationships is likewise crucial in Grenada as business is often conducted through personal connections, while attending
establish trust and rapport.
–
Understand the demand for your product or service and identify potential competitors.
SEEK LOCAL PARTNERSHIPS – Partnering with local businesses can provide valuable market insights and facilitate smoother operations.
–
Professional advice can help navigate regulatory requirements and optimize tax benefits.
– The GIDC and other government agencies offer support for business development and investment.
PRIORITIZE CORPORATE SOCIAL RESPONSIBILITY
– Community involvement and sustainability initiatives can enhance your business’s reputation.
However, despite its many advantages, doing business in Grenada also comes with certain challenges, such as:
• SMALL MARKET SIZE – Grenada’s population of approximately 112,000 limits domestic market potential.
• BUREAUCRACY – While the government has made progress in streamlining processes, bureaucratic delays can still occur.
• NATURAL DISASTERS – The island is vulnerable to hurricanes, which can disrupt business operations.
• ACCESS TO FINANCING – Small and medium-sized enterprises (SMEs) may find it difficult to access affordable financing.
Despite the challenges, Grenada offers a welcoming environment for business, with numerous investment opportunities across various sectors.
However, success requires a thorough understanding of the local market, regulatory framework, and cultural nuances.
By leveraging the available incentives, building strong relationships, and adopting a strategic approach, businesses can thrive in Grenada’s dynamic and growing economy.
With its combination of natural beauty, political stability, and investorfriendly policies, Grenada stands out as a promising destination for entrepreneurs and investors in the Caribbean.
Having grown in recent decades to become a key player in South America’s mining landscape, Colombia’s extensive exploration potential and commitment to sustainable mining practices make it ripe for substantial international and domestic investment
Writer: Lucy Pilgrim | Project Manager: Krisha Canlas
South America, home to some of the world’s most extensive mining investment regions, boasts an abundance of mineral resources.
Indeed, many countries across the continent hold substantial growth potential, brimming with copper, lithium, iron ore, nickel, and gold deposits.
Colombia, in particular, is a leading mining nation in South America, and with good reason. The country possesses one of the world’s largest coal deposits alongside a substantial level of nickel and gold, not to mention its huge investment prospects, with vast areas
of ground yet to be explored.
In the last 30 years, in preparation for significant levels of foreign direct investment (FDI), the Colombian government has implemented a regulatory framework that has primed the industry for future development. The 1991 Constitution of Colombia, for instance, set out a vast range of socioeconomic and cultural rights, establishing the parameters for the country’s exploration and extraction activities.
As a result, the state became the executive owner of Colombia’s non-renewable natural resources,
managing its mineral commodities and regulating extractive projects. Today, such activities are funneled through the Ministry of Mines and Energy, established in 2001.
In the same year, the Colombian Mining Code was introduced, which set the foundations for what the industry has now grown to become. The code maintains clear regulations for the exploration, mining, and production of minerals across the country, establishing a 30-year mineral rights concession agreement.
More recently, the government announced plans to double the country’s gold production by 2030 in the face of many regulatory and socioeconomic obstacles that have delayed major mining operations.
However, with new draft reforms to the mining code on the horizon and a continuously stabilizing economy, Colombia’s mining industry is set to turn a corner.
A key component of this uptick is the government’s commitment to sustainable mining, cultivating Colombia to become a key mining player in the ongoing energy transition.
With more than 150 years of experience, Orica stands as a global leader in advanced solutions and technology for the mining and construction industries. Manuelangel Aldana, the new General Manager Colombia & Caribbean, and Patricio Rivera, Manager Colombia, share a unified vision: “At Orica, we’re shaping the future with digital innovation, expanding into Specialty Mining Chemicals, and driving sustainability to provide superior solutions that enhance efficiency and create greater value for our clients.” Together, they are committed to leading continued growth and impact in the region.
1. How is Orica leveraging digital technologies to drive innovation within the company, and how do these advancements position Orica for growth in the mining industry? – MA
At Orica, we are fully committed to leveraging cuttingedge digital technologies to drive innovation across the mining sector for our clients. By integrating end-to-end digital workflows, we optimize every step of the mining process from exploration to processing, while enhancing safety, productivity, and sustainability. Our solutions help clients by using advanced data analytics to analyse rock properties, adjust explosive energy, simulate outcomes, and assess the broader impacts on both mines and surrounding communities. These innovations not only enable us to make more precise, data-driven decisions but also position Orica for sustainable growth, allowing us to meet the evolving challenges of the mining industry, reduce costs, and minimize environmental impact.
2. Can you share more about Orica’s new focus on Specialty Chemicals? How does this strategic move align with Orica’s long-term goals in Colombia? – PR
Orica’s acquisition of Cyanco underscores our strategic focus on specialty chemicals and our commitment to supporting the growth of Colombia’s gold industry. Cyanide is a critical reagent in gold extraction. With the combined expertise of Orica and Cyanco, we can deliver safer, more reliable, and more sustainable solutions to our customers.
This decision aligns with Orica’s long-term objectives of driving innovation, enhancing customer value, and strengthening our role as a key partner in Colombia’s expanding gold mining sector and the broader commodities market of the future.
3. How is Orica integrating sustainability into its business operations, and what impact do you expect this to have on both the company and the communities involved? – PR
At Orica, sustainability is not just a commitment it’s a strategic priority embedded in every aspect of our operations. We are actively reducing our carbon footprint, investing in clean technologies, and promoting responsible practices across our entire value chain. From utilizing more environmentally friendly products to optimizing resources and implementing systems that minimize environmental impact, our approach is both comprehensive and forward-thinking.
These initiatives are designed to deliver meaningful contributions in the fight against climate change, strengthen the resilience of the communities where we operate, and enhance our reputation as a sustainability leader. For the communities involved, this translates into greater access to sustainable employment opportunities and long-term economic benefits.
Beyond our operational efforts, Orica also runs a social investment program focused on creating lasting positive impacts. We carefully assess community needs and strategically allocate resources to maximize their potential. By fostering economic development and social well-being, we aim to build stronger, more sustainable communities while driving shared value for all stakeholders.
4. How do you see the adoption of new digital technologies shaping the future of the mining industry in Colombia? – MA
In Colombia, our clients leverage our technologies to tackle diverse challenges. We provide vibration monitoring to safeguard installations and communities, while optimizing explosive design and consumption to enhance operational efficiency and minimize environmental impact. Our solutions also help improve mineral recovery by reducing dilution and enabling continuous fragmentation measurement across different stages. Additionally, we support slope stability monitoring and the efficient use of specialized chemicals. While technology adoption varies by mining type, our Colombian clients remain committed to long-term sustainability and responsible resource management.
At Orica, we are fully committed to driving growth and delivering lasting impact. By leveraging advanced digital technologies and placing sustainability at the core of our operations, we are transforming how we partner with our clients in Colombia and beyond. Our focus on innovation and responsible practices ensures we are wellpositioned to lead the mining sector forward, creating value and driving long-term success for all involved.
At Orica, we are fully committed to driving growth and delivering lasting impact. By leveraging advanced digital technologies and placing sustainability at the core of our operations, we are transforming how we partner with our clients in Colombia and beyond.
Our focus on innovation and responsible practices ensures we are well-positioned to lead the mining sector forward, creating value and driving long-term success for all involved.
To learn more about Orica and how we can support your operations, reach out to your local Orica representative or visit orica.com
Representing a mining industry flourishing with potential, we learn about the work of the Colombian Mining Association (ACM) and its efforts toward promoting the sector as a pillar of the country’s socioeconomic development. President, Juan Camilo Nariño Alcocer, delves deeper into the dynamic industry
stablished in 2014, ACM is a unique union of Colombian mining entities that seeks to reengineer the country, bring together the business mining sector, and purposefully facilitate projects that contribute to positive economic growth across local communities.
In addition, ACM operates as a regulatory framework and reference point for constructing policy and public opinion around mining. This helps promote a forum to attract FDI, which in turn fosters innovation, technological development, and a growing international presence for the industry.
With the founding goal to have the Colombian mining sector recognized as a contributor to the country’s development, ACM is poised to propel the industry into a sustainable future and be a key contributor to the nation’s energy transition.
North America Outlook (NA): Firstly, could you tell us about the origins of ACM and your initial vision?
Juan Camilo Nariño Alcocer, President (JCNA): ACM was created with a clear purpose – to represent and strengthen the formal mining industry in Colombia, ensuring that it operates according to standards of sustainability, responsibility, and global competitiveness.
Since its inception, the association has worked to make mining a pillar of the country’s development, boosting
employment, investment, and growth across the nation. Our work goes beyond union representation; we have become a key player in the development of public policies through dialogue with the government and articulating with international actors.
Today, ACM is the voice of a mining industry committed to innovation, environmental protection, and creating opportunities for thousands of Colombians. We believe in mining that not only extracts resources but also positively impacts communities and the national economy.
NA: What is your take on the mining industry in Colombia at the moment? Would you say it’s a particularly exciting or challenging environment to work in?
JCNA: Mining in Colombia is facing a complex moment but also one of opportunity. We are a country with enormous geological potential and minerals that will be key to the global energy transition, such as copper, nickel, and gold.
There are also obvious challenges, such as regulatory uncertainty, deteriorating security in some regions, and limited incentives to attract FDI.
The truth is that Colombia cannot afford to turn its back on mining. It is a sector that accounts for more than 30 percent of national exports, purchases COP14 billion in goods and services each year, and generates formal employment in regions where few industries can.
“WE BELIEVE THAT WITH CLEAR RULES, LEGAL CERTAINTY, AND POLICIES THAT REFLECT GLOBAL REALITIES, MINING WILL CONTINUE TO BE A SOCIOECONOMIC PILLAR FOR THE COUNTRY”
– JUAN CAMILO NARIÑO ALCOCER, PRESIDENT, COLOMBIAN MINING ASSOCIATION
“COLOMBIA HAS THE POTENTIAL TO BE A STRATEGIC PLAYER IN THE PRODUCTION OF ESSENTIAL MINERALS FOR THE ENERGY TRANSITION, AND OUR ROLE AT ACM IS TO ENSURE THE INDUSTRY IS PREPARED FOR THIS CHALLENGE WITH WORLDCLASS STANDARDS”
– JUAN CAMILO NARIÑO ALCOCER, PRESIDENT, COLOMBIAN MINING ASSOCIATION
At ACM, we are working to ensure that mining continues to be an engine for development. We believe that with clear rules, legal certainty, and policies that reflect global realities, mining will continue to be a socioeconomic pillar for the country.
NA: How do you represent the collective interests of your members and assist them in the generation of responsible and sustainable mining, alongside establishing linkages with global entities?
JCNA: ACM represents responsible mining that operates to the highest standards and understands that its license to operate depends on its commitment to community development and sustainability.
At ACM, we have led the implementation of the Towards Sustainable Mining (TSM) standard in Colombia, an internationally recognized self-regulatory model that allows companies to measure and improve their performance in environmental, social, and governance practices (ESG).
TSM has been adopted by leading mining jurisdictions such as Canada and Australia, ensuring that Colombia is at the forefront of the global industry.
We are now in the third year of implementing TSM, and ACM member companies have progressed in selfassessing the standard’s nine protocols, which address key issues such as tailings management, respect for Indigenous rights, community relations, energy efficiency, and water conservation.
This process not only reflects the industry’s commitment to sustainability but also allows society and government to monitor progress with full transparency.
We also maintain an ongoing dialogue with multilateral organizations, mining associations in other countries, and global bodies that promote sustainable development. Colombia has the potential to be a strategic player in the production of essential minerals for the energy transition, and our role at ACM is to ensure the industry is prepared for this challenge with world-class standards.
NA: In what ways does the association position the mining industry as a pillar of Colombia’s socioeconomic development?
JCNA: Mining in Colombia is not just an extractive activity; it is a strategic industry that drives economic development, strengthens production chains, and generates regional wealth. Its impact on the economy is undeniable, and its role in the productive transformation of the country is increasingly evident.
Each year, the mining sector invests more than COP14 billion in the purchase of national goods and services, boosting key sectors such as manufacturing, metalworking, transport, infrastructure, technology, industrial inputs, and agribusiness.
This productive link not only strengthens thousands of companies in the country but also contributes to the reindustrialization of Colombia and the creation of formal and quality jobs.
However, mining is not only an economic engine – it is also a key ally in regional development and nationbuilding. In many areas of the country, the sector’s presence has made it possible to provide infrastructure for education, health, roads, and public services, fostering development that goes beyond mining.
Globally, countries that have been able to take advantage of their mineral resources have built stronger, more diversified economies.
Therefore, Colombia has the opportunity to consolidate a modern, responsible, and sustainable mining model that guarantees not only the exploitation of its natural wealth but also transformation into progress, well-being, and competitiveness for all Colombians.
At ACM, we continue to work to ensure the industry is recognized for what it truly is – a strategic pillar for the country’s growth and an engine of community
development. The challenge is great, but the sector’s commitment is even greater.
NA: Finally, how do you see the nation’s mining industry developing in the next five years? Are you optimistic about the future?
JCNA: The future of Colombian mining depends on the decisions we make today. The world is in a race to secure critical minerals for the energy transition, and the country has a unique opportunity to position itself as a strategic supplier of these resources.
Currently, 70 percent of clean energy technologies rely on minerals such as copper, nickel, and lithium, and global demand continues to grow.
If the nation can make progress in the exploration and development of new projects, we could be on the verge of a major economic transformation, driving new investment, creating formal jobs, and strengthening public finances.
However, this will only be possible if there is a stable regulatory framework, clear rules of the game, and legal certainty for investment.
Regulatory stability and business confidence will be crucial if Colombia is to keep up with the global competition for these resources.
Currently, countries such as Canada, Australia, and Chile have made significant progress in attracting sustainable
mining investment, recognizing that the sector is not only essential for the energy transition but also for socioeconomic development.
At ACM, we are optimistic about the future of the sector. We believe in a mining industry that not only contributes to the national economy but also drives regional development, generates formal employment, and operates with the highest standards of sustainability.
Mining companies in Colombia have demonstrated their commitment to global best practices, and the country has all the ingredients to consolidate itself as a benchmark for sustainable mining.
However, time is short. If Colombia does not make strategic decisions now, we risk losing key investments and seeing other countries take advantage of the boom in demand for minerals.
It is time to develop a long-term vision that recognizes mining as an essential sector for the country’s development and a key player in the global energy transition.
Tel: (57) 601 466 0214 contacto@acmineria.com.co acmineria.com.co
Mining Outlook is a dedicated digital publication reaching key decision makers across the mining sector worldwide. With an audience of over 500,000 industry professionals, we specialise in sharing the latest innovations, success stories, and trends shaping the mining landscape. Our experienced editorial team works closely with companies to showcase their achievements, spotlighting the leaders driving the industry forward. As a featured company, you’ll benefit from:
• FREE EXPOSURE: A professionally crafted marketing feature in our widely-read magazine.
• GLOBAL REACH: Amplified visibility through our extensive social media channels and global distribution.
• B2B BUSINESS OPPORTUNITIES: Build connections with industry heavyweights and potential investors.
• BUSINESS GROWTH: Position your brand as a trusted leader in the mining sector. Join the mining companies already leveraging Mining Outlook to share their stories and inspire the industry. Visit www.mining-outlook.com/work-with-us to
Building on the global success of our regional titles – EME Outlook, Africa Outlook, APAC Outlook, and North America Outlook – Outlook Publishing is proud to introduce a digital magazine and web platform, dedicated to the supply chain sector.
As supply chain organizations worldwide confront unprecedented change, embracing technological innovations and incorporating critical environmental sustainability agendas, now more than ever is the time to showcase the strides being taken in this dynamic sector.
A multi-channel brand, Supply Chain Outlook brings you the positive developments driven by organizations across the global supply chain industry through its various platforms. Discover exclusive content distributed through its website, online magazine, social media channels, and dispatches delivered straight to your inbox with a bi-weekly newsletter.
Through this compelling new venture, we foreground the movers and shakers of the industry. To participate as a featured company and join us in this exciting endeavor, contact one of our Project Managers today.
TGW Logistics offers a comprehensive suite of end-to-end automated systems and modular technologies designed to overhaul fulfillment operations from the ground up and solve a variety of workflow challenges. Vice President of Business Development, Stipe Galic, tells us more
Writer: Ed Budds | Project Manager: Poppi Burke
Automation can be quantified as the use of machines or technology to perform tasks with a reduced need for human intervention, an innovative approach that looks to streamline processes, enhance efficiency, and reduce human error.
As a result, the use of automation is becoming increasingly prevalent across a plethora of different realms and domains.
Within this burgeoning landscape, TGW Logistics was created in 1969 when Ludwig Szinicz and his friend Heinz König transformed a small metalworking shop in Wels, Austria into what would become one of the world’s most renowned and trusted names in warehouse automation and logistics.
“Today, we’re widely considered a global leader in manufacturing, designing, implementing, and maintaining highly automated, futureproof fulfillment centers for a multitude of industries, including fashion and
apparel, grocery, and industrial and consumer goods,” opens Stipe Galic, Vice President of Business Development.
“Our comprehensive approach ensures that we deliver solutions designed to enhance performance, tackle complex supply chain challenges, and transform distribution centers into strategic assets that support and drive our customers’ growth in an increasingly unpredictable future,” he follows up.
The rise of e-commerce has transformed warehousing and distribution (W&D) operations. Previously focused on bulk orders for retail, these facilities now handle complex sortations for online consumers who often order just one or two items.
The shift to goods-to-person (GtP) presents challenges, especially for sortation facilities that now manage tasks previously handled by retailers, like sorting item sizes and colors for B2C orders. Managing returns has become more complex, with e-commerce return rates reaching up to 60 percent. This reverse logistics process involves quality checks, relabeling, and repacking, increasing operational complexity and cost.
A basic GtP system can serve as an inventory buffer or picking system but requires additional configuration for post-picking processes like consolidation, sequencing and shipping. This is where a pouch system comes in, acting as a complementary consolidation buffer to the existing GtP setup without needing complicated reconfiguration.
A pouch sorter is a conveyance system with hanging pouches that transport items like garments, shoes, and books along a rail. It is flexible and scalable and utilizes overhead space for sorting, buffering, and automating order handling and returns. Pouch systems optimize throughput and order consolidation, manage returns efficiently, and handle sequencing challenges by sorting fragile items last, improving overall efficiency in the returns process.
Creating a business case for a new materials handling system varies with each GtP operation. It involves considerations of building type, product sizes, return levels, labor needs, capital expenditure (CAPEX), and operating expense (OPEX).
Pouch systems offer strong advantages, as they can be easily integrated into existing GtP setups, providing midto short-term storage and acting as a shipping buffer with automated sortation. They enhance reverse logistics and
can scale with the growing e-commerce market while supporting digitization for improved data insights and productivity.
Pouch as an enhancement to the existing GtP setup can add value by serving as a pick order consolidation buffer. It also provides the ability to sort and sequence the picked ship orders. Additionally, a pouch system can function as a temporary ship order buffer until ready for shipment.
Pouch technology has existed for decades but is now crucial in modern warehousing and fulfillment operations.
Pouch systems use overhead sortation to transport and sort products in bags or pouches, effectively managing the complexities of e-commerce. They excel in reverse logistics by reducing the costs and challenges of relabeling and repacking returned items for outbound shipment, often without storage.
also leverage AI, ML, and analytics to optimize warehouse operations, predict issues, and support proactive decisionmaking.
BEUMER Group has launched the AutoDrop feature for its pouch system, enabling flexible and reliable automatic packing lines. This innovative design uses a shape-memory nickel-titanium alloy for automatic pouch unloading, reducing manual handling and processing by around 10,000 pieces per hour. Adjustable drop point positions optimize flexibility while minimizing space usage in distribution facilities, streamlining pouch handling, and saving time.
Integrating physical equipment with software and analytics in modern fulfillment operations is crucial. Software provides visibility, accurate forecasting, and better decision-making, helping manage complex logistics. A key goal is to minimize latency between fulfillment planning and real-life events.
A WMS is essential for digital transformation, streamlining goods flow and resource use. It integrates physical systems like pouch sorters and AMRs with technologies such as auto-ID and voice solutions, enhancing productivity. A WMS uses IoT sensors to track assets, monitor stock levels, and locate lost items. It can
Integrating equipment and software in a WMS can transform the W&D industry, driving full digitization and significant improvements in efficiency and performance. Central to this is the pouch warehouse management system (WMS), which digitizes inventory management and order consolidation. This digital approach enhances tracking, traceability, and control, enabling process optimization for improved fulfillment efficiency.
An existing GtP setup might not efficiently tackle post pick processes like order consolidation, pick order sortation or sequencing. Additionally, it may require the pick orders to be stored back into the inventory. This would lead to inefficient use of the storage buffer. A pouch system essentially solves these challenges my acting as an enhancement to the existing GtP setup.
Additionally, A pouch system can function as an excellent addition to automation capabilities to handle the returns shipment.
BEUMER Group can help identify the best opportunities for enhancing your existing setup to address improvement in fulfillment accuracy, reliability, and productivity.
DO YOU FIND THE AUTOMATION INDUSTRY AN EXCITING LANDSCAPE TO BE INVOLVED IN?
STIPE GALIC, VICE PRESIDENT OF BUSINESS DEVELOPMENT:
“Yes, I find it a super exciting sector to work in, and the reason why I fell in love with the automation industry is because I get to be involved with lots of big, exciting projects and work alongside some of the best brands in the world.
“Our work at TGW Logistics puts us in the room with executive teams of global retailers and brands, driving the future of supply chain innovation. Shaping what’s next alongside industry leaders? Now that’s the kind of game I love to play.
“At the same time, another exciting aspect of being involved in the industry is that when I walk into a store or go to order an item from somewhere like Amazon, I can fully understand the entire distribution process and what is going on behind the scenes across the whole value chain.”
TGW Logistics is a foundationowned company, still headquartered in Austria, and a trusted systems integrator with more than 50 years of experience.
Now boasting over 4,500 employees spanning Europe, Asia, and North America, TGW Logistics combines its wealth of expertise, innovation, and customer-centric dedication to help keep its clients growing and transform their warehouse logistics into a smooth and efficient operation.
“We are a one-stop solutions provider, offering not only cuttingedge technology for distribution centers but also the essential software to ensure seamless operations. Our focus extends beyond simply implementing technology – we strive to make life easier for operations teams by creating smooth, efficient, and user-friendly solutions.
“With our extensive global presence, we are able to provide this full range of technologies, services, and expertise in all our locations worldwide,” Galic prides.
TGW Logistic’s impressive array of solutions are delivered through three key business areas – Integration Business, Distributor Business, and Lifetime Services.
“As a systems integrator, we design, implement, and maintain fully integrated and highly automated warehouse systems, as well as modernize warehouses to make them future-ready – this is the biggest portion of our revenue streams,” says Galic.
“From concept and detailed planning to execution, we ensure a seamless experience from design to implementation and beyond. By analyzing our customers’ current and future needs, we match them with the right designs and solutions to drive efficiency.
“Our goal is to deliver best-in-class process flows that optimize cost per piece handled, because it’s not just about selling technology - it’s about creating smarter, more effective operations,” he furthers.
TGW Logistics expertly empowers businesses to move, store, and pick goods reliably, transforming operations with smarter, faster, and more adaptable processes that are prepared and ready for anything the future brings.
The second key portion of its operational umbrella is represented through its Distributor Business, which provides mechatronic technologies to other systems integrators.
“We partner with intralogistics system integrators to provide high-performance subsystems and leverage our deep industry expertise to navigate market opportunities together.
“By providing best-in-class technology, we empower integrators to deliver exceptional results for their clients,” Galic affirms.
The third key portion is Lifetime Services. TGW Logistics’ service packages ensure maximum warehouse availability, protecting investment with tailored support options – from essential spare parts to 24/7 virtual support to full-service on-site maintenance and more.
With guaranteed 98 percent system availability, real-time visibility, optimized operations, and reduced ramp-up times, businesses can focus on meeting service level agreements (SLAs) and growing their operations with confidence.
The best automation in the world is worthless if it isn’t reliable and doesn’t achieve the committed availability rates needed to meet SLAs,” Galic affirms.
One sector in which TGW Logistics
continues to play a pivotal role is the broader retail industry, a dynamic and rapidly evolving market shaped by shifting consumer expectations, technological advancements, and increasing pressure for operational efficiency.
Consumer behavior is changing at an unprecedented pace, influenced by digitalization, e-commerce growth, and the need for seamless omnichannel experiences. Retailers must continuously adapt their supply chain strategies to keep up with demand fluctuations, shorter delivery windows, and the rising preference for sustainable practices.
The industry also faces ongoing challenges in attracting and retaining skilled labor, further compounded by shifting workforce demographics and evolving job expectations. At the same time, rapid technological innovation requires businesses to stay agile, integrating new solutions that enhance efficiency and scalability.
Historically, many retailers primarily focused on product development and brand positioning. However, in today’s landscape, an optimized supply chain is no longer just a support function – it has become a key driver of strategic success. Efficient logistics and distribution networks are essential to navigating increasing complexity, meeting customer demands, and maintaining a competitive edge.
“THE BEST AUTOMATION IN THE WORLD IS WORTHLESS IF IT ISN’T RELIABLE AND DOESN’T ACHIEVE THE COMMITTED AVAILABILITY RATES NEEDED TO MEET SLAS”
– STIPE GALIC, VICE PRESIDENT OF BUSINESS DEVELOPMENT, TGW LOGISTICS
Recognizing this, TGW Logistics takes a holistic approach to understanding its customers’ supply chains, ensuring they remain agile and resilient in an ever-changing business environment.
“It is not enough to focus solely on warehouse automation – we must also consider the unique challenges of modern retail logistics and stay ahead of emerging trends,” explains Galic.
Beyond offering a diverse portfolio of automation solutions, TGW Logistics supports its customers with a dedicated team of industry experts who assist in identifying and implementing the right technologies to build adaptable and future-ready distribution strategies.
“Our commitment lies in helping businesses address these challenges by continuously researching industry trends and developing solutions that enable retailers to optimize their logistics operations,” he adds.
Automating a distribution center
involves the seamless integration of various systems and technologies, connecting operations from inbound processing to outbound fulfillment.
“We analyze the entire end-toend process to design the optimal combination of technologies that meet both current and future business needs. Our tailored automation solutions cover all critical processes within the distribution center, ensuring that software and systems work together to coordinate and manage operations efficiently.”
In 2004, TGW Logistics’ co-Founder, Ludwig Szinicz, set out to transform his company into a foundation-owned organization with a bold mission.
“He believed that the company is not just a purely economic partnership of convenience, but a community of shared values driven by a purpose and follows the mission of its foundation,” Galic tells us.
Since its establishment, SINTEC US LIMITED provides a range of installation services of commercial and industrial equipment.
Each Client has their unique meaning of quality. We work closely with everyone to identify specific requirements and to accommodate each project’s needs on a very personal basis.
We are particularly knowledgeable of how international business is structured nowadays. With that in mind, and considering our experience in organizing international projects, we strive to support our Customers on a global scale.
Our offices in UK, US, Latvia and OAE provide more flexibility in fulfilling such standards.
“Each Client has their unique meaning of quality. We work closely with everyone to identify specific needs and to accommodate each project’s individual requirements. Once again, SINTEC has delivered quality workmanship, showed good technical expertise along with flexibility of working to ensure a successful delivery of the project.”
Paul Roman, Director of Controls and Operations Strategy TGW Limited
Our offered services are focused on thorough provision and impeccable implementation of any scale of the projects for our customers, with the aim of making the whole experience straightforward, consistent, and time/cost-efficient.
• Electrical Installation
• Electrical Design
• Procurement of Materials
• Estimation
• Inspection and Testing
• Commissioning Support
150+ 146
• Mechanical Installation
• IT and Fibre Optic
• Manufacturing of CP
• Internal / External / Process Lighting
• Project Management
• H&S Documentation
4
projects completed industry professionals offices in 4 countries
“This community enables personal and technical growth as well as entrepreneurial success. We believe our values-based culture will carry us into the future and foster continued growth – not just for our business but also those who drive our success,” he expands.
For TGW Logistics, this unwavering commitment to both employees and customers, paired with cutting-edge innovation in warehouse automation and logistics, makes anything possible.
Elsewhere, as the owner of TGW Logistics, the TGW Future Private Foundation safeguards the company’s long-term vision.
By reinvesting two-thirds of its profits into employees and the technologies of tomorrow, the foundation fuels innovation and creativity in the fields of warehouse automation and logistics.
TGW Logistics cannot be sold and cannot be bought, making it a reliable employer, financial partner, and pioneer in automated warehouse solutions.
In addition, 10 percent of its profits are dedicated to charitable projects, reflecting the company’s belief that thriving in this industry can and should make a meaningful impact on society.
HOW TO TREAT EACH OTHER –Show respect and appreciation for all colleagues, promote freedom from fear, and always exude friendliness and trust.
HOW TO LEAD – Promote passion and empowerment, set a good example for all, and win as a team.
HOW TO WORK – Be responsible, results-driven, proactive, and open-minded.
FASHION AND APPAREL – Changing trends and fluctuating demand in the ever-evolving world of fashion requires fast, efficient, and flexible supply chains.
GROCERY – Food storage, material handling, and distribution must be seamless and adhere to safety and compliance regulations. For over half a century, TGW Logistics has been helping grocery companies automate their supply chains with state-of-the-art technology and innovative thinking.
INDUSTRIAL GOODS – The industrial sector demands high quality, exceptional service, and the fastest possible deliveries. To overcome supply chain challenges, companies need agile warehouse solutions that speed up distribution and support omnichannel environments.
CONSUMER GOODS – TGW Logistics’ solutions optimize efficiency and minimize downtime, ensuring seamless operations and complete transparency in all aspects of consumer goods logistics. Additionally, automated workflows help wholesale, retail, and e-commerce businesses reach their fulfillment goals.
“At TGW Logistics, success isn’t measured solely in numbers – it’s reflected in how we interact with one another, what our customers think about us, and profits through principles. We are here to make things possible and create strong supply chain backbones which allow businesses to navigate ever-evolving industry demands. Our core values form the foundation of our corporate culture, shaping our relationships, decisions, and approach to harnessing innovation,” outlines Galic.
“They empower us to create fulfillment solutions that push boundaries and inspire progress in warehouse logistics.”
Today, through a unique combination of business success and social responsibility, the company remains a leader in warehouse automation and a model of exemplary entrepreneurship.
“It’s how we ensure sustainable growth together – today, and for generations to come,” Galic finishes.
us.info@tgw-group.com tgw-group.com
Automation is transforming the way industries operate, and reliable packaging plays a key role in making these systems work. At Utz, we design reusable plastic totes, trays, and containers that work perfectly with robotic solutions and conveyors.
Whether you’re upgrading an existing system or starting fresh, our packaging is tailored to optimize your processes and increase productivity.
At Georg Utz, Inc., we help businesses work more efficiently with innovative, reusable packaging solutions. For over 77 years, we’ve been creating durable, custom-engineered products that integrate seamlessly with automated systems.
With eight locations across three continents and a team of 36 specialized product design engineers, we’re here to support your automation needs.
Reusable packaging benefits both your business and the planet. By reducing waste and replacing single-use materials, our solutions help lower disposal costs while offering better durability and reducing product damage. This combination of savings and sustainability helps businesses meet their operational and environmental goals.
Every business has different challenges, and we specialize in creating solutions to meet them. Our team works closely with you to design, prototype, and produce packaging that fits your operations perfectly. With decades of expertise and advanced manufacturing tools, we ensure your packaging is as efficient as your systems.
We believe great outcomes come from working together. Our partnerships with system integrators and end-users have shown how collaboration leads to reliable, efficient systems. By combining your automation expertise with our packaging knowledge, we create solutions that drive success.
When you choose Georg Utz, Inc., you choose an experienced partner committed to your success. Our global expertise, technical innovation, and focus on sustainability make us the right choice for businesses looking to improve their automation with reusable packaging.
As manufacturing organizations worldwide confront unprecedented change, embracing technological innovations and incorporating critical environmental sustainability agendas, now more than ever is the time to showcase the strides being taken in this dynamic sector.
A multi-channel brand, Manufacturing Outlook brings you the positive developments driven by organizations across the global manufacturing industry through its various platforms.
Discover exclusive content distributed through its website, online magazine, social media campaigns and digital dispatches, delivered straight to your inbox with a bi-weekly newsletter.
Through these compelling media channels, Manufacturing Outlook will continue to foreground the movers and shakers of the industry.
To participate as a featured company and join us in this exciting endeavor, contact one of our Project Managers today.
With a rich history and unrivaled passion, Cruisers Yachts creates American-made boats for the world. We speak to Josh Delforge, Vice President of Engineering and Operations, about the company’s first-class fleet and commitment to innovation
Writer: Ed Budds | Project Manager: Michael Sommerfield
The global yacht building industry presents a unique blend of adventure, luxury, and freedom.
It is a vast and diverse sector that attracts designers, engineers, and builders from across the world but has the feel of a much smaller community, and for many, it exists as a lifelong passion.
At present, the US continues to be the main focus of yacht builders worldwide.
Within this expanding market, some builders may only produce one or two bespoke boats a year, whereas others are producing that same quota every hour.
“With the US being a key market, we see a continuous flow of new products introduced which fuels new design
trends. As a designer and builder, we’re excited by the challenge of creating unique solutions for clients with each of our vessels,” introduces Josh Delforge, Vice President of Engineering and Operations at Cruisers Yachts.
“The main market trends we are seeing today focus on increasing the ease of water interaction and giving our customers more flexibility with how they can utilize our yachts,” he continues.
After graduating from the University of Wisconsin-Madison in 2003 with a degree in engineering mechanics, Delforge was hired as a design engineer at Carver Yachts, where he was first introduced to the nautical world.
“OUR RICH BOAT-BUILDING HERITAGE DATES BACK TO 1953 AND WE HAVE SINCE BECOME ONE OF THE WORLD’S PREMIER PROVIDERS OF MID-SIZE LUXURY PLEASURE YACHTS”
– JOSH DELFORGE, VICE PRESIDENT OF ENGINEERING AND OPERATIONS, CRUISERS YACHTS
this in small pockets, but we are getting closer each day,” Delforge explains.
Cruisers Yachts has been building boats for over 70 years in Northeast Wisconsin and today boasts production plants located in both Oconto and Pulaski, with a total of just under 400 employees.
“As a young engineer, I was drawn to the combination of creativity and technical skills needed to be successful.”
Today, time is such a valuable commodity, and with families having less free time, Cruisers Yachts wants to give its customers the ability to cruise, anchor, entertain, overnight, and everything in between on its state-of-the-art vessels.
As such, one of the company’s goals is to find avenues to open
up boating to new customers and audiences.
To do this, Cruisers Yachts is constantly looking at new materials, suppliers, building processes, and equipment to improve its products and allow it to offer more boats at a lower price.
“Additionally, in the near future, we predict that technology will grow to the point where we start seeing more electric and hybrid solutions in larger production yachts. Today, we only see
What started as a production base for small wooden vessels has now evolved into the home of multi-milliondollar luxury yachts.
“Our rich boat-building heritage dates back to 1953 and we have since become one of the world’s premier providers of mid-size luxury pleasure yachts.
“Each model is crafted with industryleading design, manufacturing, and amenities. Every part, texture, and element has been hand-picked to
JOSH DELFORGE, VICE PRESIDENT OF ENGINEERING AND OPERATIONS: “As a major employer in both cities where we operate, we are always looking for ways to expand our reach within the community. We sponsor local events, donate to local charities, and connect with local schools.
“Additionally, as a boat builder, we are a member of the National Marine Manufacturers Association (NMMA), in which we strive to educate and promote safety on the water.
“At a local level, we are members of the North Coast Marine Manufacturing Alliance (NCMMA) and the Northeast Wisconsin Manufacturing Alliance (NEWMA). These groups focus on promoting manufacturing through connections with local schools, universities, workforce development boards, chambers of commerce, and state organizations. To date, NEWMA has sponsored over $500,000 in college scholarships over the past 20 years.
“Elsewhere, at corporate level, MarineMax has been such a positive influence with their focus on employee and community outreach. A great example is their newly-created Crew Care Relief Fund, an amazing program to help team members who need financial assistance following an unforeseen disaster or personal hardship. Their commitment to employees has been evident since day one and goes a long way in building trust with the entire team and community.”
provide our clients with unparalleled comfort and performance,” Delforge prides.
In 2021, the company was purchased by MarineMax, the world’s largest retailer of recreational boats and yachts.
Through this key partnership, and ongoing relationships with independent dealers, Cruisers Yachts distributes its products and interfaces with customers.
“While distribution of our yachts is mainly focused across the US, we ship products all over the globe,” he confirms.
Over the past three years, the company has invested close to $15 million in new equipment, facility upgrades, and expansion, with a focus on employee safety, plant cleanliness, product quality, internal capabilities, and output capacity.
In addition, Cruisers Yachts has recently implemented new systems and processes that are designed to
foster a culture that understands the importance of receiving feedback.
This valuable feedback loop allows the company to make changes to improve its end products and increase efficiency.
Cruisers Yachts currently has three key product lines of vessels ranging from 34 to 60 feet (ft) in size.
“Our Grand Luxury Sport (GLS) line-up ranges from 34 to 50ft and is categorised in the bow rider segment. These models have a focus on exterior entertainment with spacious interiors,” Delforge sets out.
Meanwhile, the company’s Cantius models are cabin cruisers that range from 42 to 60ft. These vessels feature a larger enclosed interior volume but maintain a focus on exterior entertainment.
General Hydraulics (GHS) is a marine manufacturer specializing in swim platform lifts and side door hinge assemblies.
“Our swim lifts and side doors are manufactured and assembled here in the US at our plant in Clearwater, Florida. We have thousands of products out in the field, proving our experience and understanding in what this industry demands.”
GHS also manufactures all its lift and hinge components inhouse, including its stainless hydraulic cylinders which are manufactured and assembled at its primary facility.
“This process allows us to maintain the highest quality standards, enhancing GHS’s ability to quality control (QC) every aspect of lift and side door operation prior to delivery. Each component is comprehensively tested with its hydraulic pump package to its fullest capacity ensuring trouble free installation and operation.
“We are known in the industry for our innovative yet simple designs with reliability at the forefront of each concept.”
Over the last 25 years, GHS has developed proven QC and testing procedures.
The company’s QC processes are derived from the experience of over 15,000 swim lifts and more than 4,000 side doors installed in operation on vessels around the world.
“We are proud of our resolute zero-defect policy from the factory, and we are constantly adapting to ensure this industry leading standard is maintained.”
GHS has earned its place as the world’s largest original equipment manufacturer
(OEM) supplier of hydraulic platform lifts by delivering the best selection, proven quality, and unmatched customer service.
Family owned and operated for 35 years, the company has, to date, built, shipped, and installed over 19,000 hydraulic swim platform lifts for happy boaters and boat manufacturers around the world.
“Because our personal guarantee and professional reputation rides with each swim platform lift that we build, all mechanical parts are created in-house at our state-of-the-art manufacturing facilities. These parts are never outsourced.
“Additionally, our huge product line of multi-purpose platform lifts means we have the perfect lift for every boat and for every boater. Furthermore, GHS’s extensive warranty and responsive customer service professionals ensure your complete and total satisfaction.”
GHS was created in 1998 to design and build reliable, durable, and multi-function hydraulic platform lifts for boaters and boat manufacturers.
“Our company got its start by filling a need for sea ray boats for a transom mounted hydraulic swim platform lift. The product sea ray used at the time was a telescoping lift that proved to be unreliable and needed to be replaced and upgraded.”
Through extensive research and firsthand feedback from OEMs and customers of the existing style lift, GHS engineered and developed a panographic lift. This design eliminated the complexity of a telescoping lift and over time has proved to be the reliable, flexible platform swim lift demanded by boaters around the world.
The GHS Mission: Lift and Inspire joy in recreational boating through innovative design, unwavering reliability and exceptional support. We are committed to exceeding all expectations.
GHS manufactures a large array of hydraulic platform lifts and platform lift packages for boats 36 feet and larger.
“All of our current model lifts are built using our original, proven designs and advanced technology. Years of experience and utilizing skilled craftsmen have allowed us to become very efficient and successful at adapting our technology to fit most of the various and complex transoms of today’s boat market without a drastic increase in price to the consumer.”
Regardless of boat manufacturer, GHS can build the Right Swim Lift or Side Door for your application.
Since its beginning, GHS has built and released more than 19,000 units worldwide, firmly establishing the company as the world’s largest OEM supplier of hydraulic platform lifts and side-door assemblies. GHS’s design capabilities and manufacturing expertise has earned it a growing customer list featuring the most recognized boat manufacturers in the business.
“Our customers include Sea Ray Boats, Marquis Yachts, Carver, Four Winns, Cruisers, Regal, Chapparral, Scout, Tiara, Aquila, Intrepid, Formula, Pursuit, Mastercraft, and many other premier boat builders around the world.”
GHS is a subsidiary of Southcoast Marine Products, one of the nation’s largest manufacturers of custom, production-type marine hardware. The company’s state-of-the-art facilities house the latest in manufacturing and machining technology and tools including:
• Over 65,000 square feet of manufacturing space
• 6000 and 10,000 watt Bystronics & BLM Plate and Tube Laser cutting Systems
• Bystonic 150-ton and Strippit 120-ton 5 axis press brakes
• 350-ton press
• Computer numerical control (CNC) robotic welding and polishing
• BLM CNC Tube Bender Elect 80B
• Hand benders, hand polishing, and CNC machining capabilities
“Our combination of tooling capabilities and experienced craftsmen allows GHS to be the
only platform lift manufacturer to manufacture all mechanical aspects of its lifts in-house. This provides an unmatched level of quality control throughout the building process.”
Each GHS platform lift includes:
• Complete mechanical lift assembly
• Adapter bracket assembly (if needed)
• Bulkhead fittings
• Hydraulic pump assembly with anti-float (as needed) backup alarms, backup hand pump
• All required interior hoses
• All required exterior hoses
• All required installation fasteners, fittings, and backup washers
• Detailed owner’s manual
• Hard-wired handheld control with required harness
• Rocker switch with switch panel and required harness
• One gallon of hydraulic oil
“AS A DESIGNER AND BUILDER, WE’RE EXCITED BY THE CHALLENGE OF CREATING UNIQUE SOLUTIONS FOR CLIENTS WITH EACH OF OUR VESSELS”
– JOSH DELFORGE, VICE PRESIDENT OF ENGINEERING AND OPERATIONS, CRUISERS YACHTS
“This gives us control and visibility of the build process from start to finish, ensuring the highest levels of quality.”
This also gives the company the required flexibility to react to customer requests, changes in market trends, or interruptions in the supply chain without disrupting production.
Another vital differentiator is Cruiser Yachts’ commitment to its customers and their boating experience, which is overseen by a service team at both dealer and corporate level.
“We often talk about how the yachting world is small, yet we have many customers who have owned multiple boats and built a relationship with the service team over time,” Delforge reveals.
“The newest addition to the fleet is our 57 FLY, which debuted in November 2024. The new FLY series redefines on-water luxury with a bold design, unmatched flybridge entertainment, seamless water access, and an interior created in collaboration with superyacht
designer, Luiz De Basto,” he excites.
Elsewhere, one critical element that defines Cruisers Yachts’ portfolio of boats is vertical integration.
“We design and fabricate 99 percent of our own tooling, fiberglass, cabinetry, metal components, electrical wiring, and upholstery.
With a majority of its customers located in the US, a simple phone call to the factory in Wisconsin provides clients with the answers or parts needed to keep them happy and on the water.
As a yacht builder, the company’s goal is to provide its customers with
BOMON Marine is a trusted, family-owned company based in Montreal, Canada, with a rich history that spans over four decades. Founded in 1982, BOMON Marine has been a leader in the production of high-quality, custom-made windows, doors, and hatches for a wide range of applications, including pleasure crafts, commercial, and industrial sectors. Now run by the second generation of the founding family, BOMON Marine continues its legacy of craftsmanship, innovation, and commitment to meeting the diverse needs of boat owners, builders, and businesses alike.
The company’s focus is on providing versatile and tailored solutions for marine and industrial applications. BOMON Marine specializes in crafting bespoke products that meet both the aesthetic and functional demands of its customers. Whether you need an individual replacement door, window, or hatch for your boat or are a major boat builder looking for high-volume custom solutions, BOMON Marine offers products designed with precision and durability in mind.
Over the years, BOMON Marine has expanded its offerings and expertise to include a variety of custom doors, windows, and hatches. These products are built to stand the test of time, engineered with advanced materials and cutting-edge techniques that ensure they perform under the toughest conditions. The company’s extensive experience in manufacturing bespoke products allows it to meet a wide array of requirements for both small vessels and large commercial projects, ensuring quality and reliability across the board.
A key feature of BOMON Marine’s product line is its madeto-measure approach. No matter the boat’s make, model, or year, BOMON Marine has the expertise and extensive database to find the perfect solution. Clients simply need to provide details about their boat, and BOMON Marine will take care of the rest, ensuring that the custom windows, doors, or hatches fit perfectly and function flawlessly.
BOMON Marine offers a variety of window types, including fixed, sliding, porthole, and hinged designs, each crafted to provide ease of use, optimal visibility, and enhanced durability. The windows are designed for easy installation, requiring no screws or holes to be drilled through the hull of your boat, which minimizes the risk of leaks and preserves the integrity of your vessel.
Whether you are looking for a single replacement window or outfitting an entire fleet of boats, BOMON Marine’s ability to deliver high-quality, custom products tailored to your specific needs sets them apart. Their dedication to craftsmanship, innovation, and customer satisfaction has earned them a loyal following and a reputation as one of the most reliable providers of custom marine windows and doors in the industry.
From its humble beginnings in Montreal to its continued success as a second-generation family-run business, BOMON Marine has stayed true to its roots of delivering exceptional products and service. With a rich history of producing custom, high-performance solutions for the marine industry and beyond, BOMON Marine remains committed to maintaining its leadership in the field of custom windows, doors, and hatches for years to come.
In a world where quality and precision matter, BOMON Marine stands as a beacon of trust, providing customers with reliable, made-tomeasure solutions that ensure their vessels are equipped with the best products available.
a wonderful boating experience at all times.
“To do that, we rely on having strong partners when we source parts, many of which we have done business with for decades,” Delforge expresses.
As such, Cruisers Yachts is always striving to find creative solutions and the best possible materials for its vessels.
“It is very easy to find someone to sell you materials, but we value a partner that is focused on getting us the right materials for the applications. We also take into account the technical support services that many of our
partners offer,” he tells us.
Across the entire sector, there has been an explosion in the use of new outboard drives, with the technology becoming more accessible and integrated throughout the wider yachting industry.
As Cruisers Yachts develops new features, the ultimate goal is to find partners willing to think outside the box and get creative in finding the best possible solutions.
“For our fold-down beach doors, we partnered with the team at General Hydraulic Solutions (GHS). They have always been great to work with and
they embraced this new challenge.
“Their system is extremely robust, which gives our doors a solid feel; at the same time, we achieve a very clean look because of the internal pin mechanism. As a builder, any supplier as open and willing to take on new projects as GHS would be considered a win,” Delforge gushes.
The primary focus for Cruisers Yachts in 2025 is on new product development and continuous improvement throughout its operations.
“Keeping our product line current and staying on top of trends is a key priority. With a five-year plan to spend over $25 million on new product development, much of our focus is on design and engineering,” Delforge elaborates.
As of today, the company remains in the build phase of three new models with a further two in the concept stage. These new yachts will play a big role in continuing to diversify Cruisers Yachts’ product line
going forward.
Furthermore, continued investment into design and engineering shows the company’s resolute commitment to long-term growth.
“Our teams understand the business and have suggested many improvements, implemented methods to enhance and develop our products, found efficiencies in the building process, and curated a culture of pride,” he concludes.
Since we last spoke to Kamstrup in early 2024, the water meter manufacturing industry has continued to progress towards digitalization and connected technologies.
Along the way, Kamstrup, a worldleading manufacturer of advanced solid-state metering solutions for smart energy and water utilities, has seen its competitors struggle to maintain product quality and overcome supply chain issues.
While component availability is being resolved, the next macro level supply chain challenges for the water metering industry in North America concern trade policy and the increasing costs of metals.
As the sector moves towards integrated digital networks and smart solutions, meter manufacturers appear to have overlooked quality, reliability, and durability.
However, Kamstrup bucks this trend. Headquartered in Denmark with employees in more than 20 countries, the company has been trusted by utilities around the world to deliver reliable metering solutions for over 75 years.
In North America, the company has almost 120 employees and is focused on supporting water utilities
We revisit smart metering solutions provider, Kamstrup, whose Country Manager and Vice President of North America, Bruce Bharat, updates us on the company’s latest investments, developments, and achievements from the past 12 months
Writer: Jack Salter | Project Manager: David Knott
with ultrasonic meters, network communications, and software applications, as well as heating and cooling in Canada.
It boasts an impressive North American return rate of just 0.25 percent and a high customer satisfaction rating, while competitor manufacturers continue to lag behind in terms of delivery and lead times.
“With US-based manufacturing, we are able to deliver meters in a fraction of the time that our competition requires,” elaborates Bruce Bharat, Country Manager and Vice President of North America.
“For example, a customer in Alabama recently noted that availability was a deciding factor in their decision to choose Kamstrup. To that end, their Kamstrup system would be completely installed before the incumbent manufacturer estimated their first meter could be delivered.”
As Kamstrup continues to invest heavily in supply chain localization and source more components in the US, the company is well-positioned in the face of impending trade regulations that would negatively impact metering products made by
In June 2024, Kamstrup was honored to announce its inclusion in the prestigious Georgia Fast 40 list for the second year in a row.
The list recognizes companies across various industries that have demonstrated significant revenue growth and job creation.
It serves as a showcase for GA’s most dynamic and successful businesses, underscoring their positive impact on the local economy.
competitors in other countries.
“We want our utility customers to know that we are navigating ongoing trade regulations and doing everything within our control to make sure we deliver on our promises,” emphasizes Bharat.
“Additionally, our flagship residential metering products feature our robust polyphenylene sulfide (PPS) composite material, which helps minimize risk from inflationary metal pricing-based supply and demand or future tariffs,” he adds.
In March 2024, Kamstrup celebrated the grand opening of its new US headquarters and manufacturing facility in Cumming, Georgia (GA), which was attended by the GA Governor, Brian Kemp, along with the
Ambassador of Denmark to the US, Jesper Møller Sørensen.
A testament to Kamstrup’s commitment to the North American market, the facility includes over 150,000 square feet (sqft) of operations and manufacturing space – enough to support the production of over three million meters annually.
“In keeping with Kamstrup’s globally recognized reputation
for outstanding quality, the facility features robotic automation, technologically advanced flow bench equipment, and robust internal quality checks and processes,” Bharat informs us.
Alongside the opening of Kamstrup’s new US headquarters and manufacturing facility, metering as a service (MaaS) is expanding and gaining exposure.
“WITH US-BASED MANUFACTURING, WE ARE ABLE TO DELIVER METERS IN A FRACTION OF THE TIME THAT OUR COMPETITION REQUIRES”
– BRUCE BHARAT, COUNTRY MANAGER AND VICE PRESIDENT OF NORTH AMERICA, KAMSTRUP
Offered by public-benefit corporation, Sustainability Partners, in collaboration with Kamstrup, MaaS is disrupting the traditional approach to advanced metering infrastructure (AMI) deployment, delivering unmatched benefits with assured performance.
To date, over 200,000 Kamstrup water meters are under contract with MaaS and Kamstrup expects this number to double in the next 18 months.
The innovative model delivers a turnkey AMI project with no upfront costs and immediate cash flow.
Instead of buying, installing, and maintaining a solution, utilities pay a monthly fee per meter in exchange for a new AMI system.
“MaaS includes hassle-free service and performance guarantees that deliver accountability – if a meter is defective or malfunctioning, monthly payments stop for the service and payments don’t start again until it’s verified to be successfully functioning once again,” explains Bharat.
Last year, the City of Shreveport in Louisiana (LA) entered into a MaaS agreement with Kamstrup and Sustainability Partners, through
which it will transition approximately 80,000 drive-by automatic meter reading (AMR) devices to Kamstrup’s AMI with embedded acoustic leak detection (ALD).
This is a huge achievement for the City of Shreveport and Kamstrup and one of the company’s largest MaaS projects to date.
“The residential meters for the city will be manufactured in our Cumming facility and, as of today, over 47,000 meters have already been delivered,” Bharat acclaims.
Elsewhere, in Las Vegas, where water is a precious resource, Kamstrup recently signed a seven-year agreement with the Las Vegas Valley Water District (LVVWD).
As a careful water steward, Kamstrup’s focus on sustainability and the environment resonated with the utility.
Delivering robust and innovative water and wastewater solutions across Louisiana, Mississippi, Arkansas, and Western Tennessee, ETEC’s services are designed to optimize its clients’ operations, enhance productivity, and elevate overall system performance, driving measurable improvements in efficiency and customer satisfaction
s an organization with expertise in equipment applications for water meters, water treatment, solids handling, and air emissions, ETEC emerges as a leading provider of municipal and industrial water and wastewater services across the southern states.
Capitalizing on its unique areas of expertise, ETEC offers an extensive collection of products and equipment, which allows the company to present optimum solutions for its clients’ particular water and wastewater problems.
Through its wide variety of professional services, ETEC partners with local water utilities to achieve sustainable, long-term growth and success, collaborating with a range of manufacturers to offer the highest quality solutions for its clients’ projects.
As such, the company actively partners with manufacturers that not only produce stellar equipment but are also technological leaders in their respective fields.
With this range of comprehensive resources and unique industry knowledge at their fingertips, ETEC’s clients can feel confident they will be consistently provided with exceptional service and guidance that they can trust.
As an elite distributor of Kamstrup products, ETEC plays an integral role in every stage of the deployment and implementation of Kamstrup solutions.
From initial planning through to full deployment and optimization, ETEC’s sales and project management teams collaborate seamlessly to ensure a smooth and efficient transition.
With extensive experience in deploying Kamstrup solutions across Louisiana and Mississippi, ETEC has established itself as a trusted provider of Kamstrup’s advanced metering technologies.
ETEC’s project management team is extensively trained and certified in Kamstrup’s software, infrastructure, and water meters, equipping the team with the expertise to deliver tailored and optimized Kamstrup solutions to its customers.
Furthermore, ETEC’s proven track record ensures that each solution is seamlessly integrated into the utility’s operations, delivering sustained improvements in performance and efficiency.
ETEC has deployed and implemented Kamstrup water meter systems across Louisiana and Mississippi including:
Lake Charles, LA
- ALD Solution
- 36,000 metering points
Shreveport, LA (In Progress)
- ALD Solution
- 77,000 metering points
City of Jackson, MS
- ALD Solution
- 70,000 metering points
ETEC’s comprehensive project management offering oversees every phase of the deployment process to ensure first-class execution.
The company collaborates closely with manufacturers, installation contractors, utility personnel, and consultants to maintain efficiency and alignment throughout the project lifecycle.
Additionally, it monitors progress, manages change orders, and implements rigorous quality control measures to uphold the highest standards.
With deep industry expertise and a proven track record, ETEC’s project management team delivers the strategic guidance and robust support necessary for a successful project. Its full suite of project management services include:
• Procurement
• Project Controls
• Inventory Management
• Quality Control
• IT Support/Troubleshooting
• Training
• Software Integration and Testing
ETEC also provides leak monitoring services and support to its customers, utilizing Kamstrup’s innovative Acoustic Leak Detection (ALD) solution, which provides permanent, round-the-clock monitoring of clients’ water distribution networks.
With faster and more efficient leak detection capabilities, ALD enables less cost per identified leak, reduces non-revenue water, and, in turn, increases overall revenue.
ETEC’s support team provides services and support our AMR, AMI, and ALD customers, enabling them to utilize Kamstrup solutions to their fullest potential and maximize ROI. Its comprehensive suite of customer support includes:
• IT support – A dedicated technical support team troubleshoots software related issues, manages software updates, and provides additional technical support and troubleshooting services to customers.
• Online help desk – ETEC’s Help Desk is an online platform for enhanced customer service and support. It includes services such as ticketing management, remote desktop support, and access to a diverse knowledge-base for product information and user guides.
• Return merchandise authorization (RMA) – The company’s support team will manage the warranty process for every customer. It files potential warranty claims with the manufacturer, manages all correspondence throughout the warranty process, and coordinates the delivery and installation of any new replacement meters.
• Training – ETEC provides training on all Kamstrup software, infrastructure, devices, and field procedures to ensure the utility’s staff operates efficiently. It offers both remote and onsite training options in the following:
• Software
• READy Manager
• READy App
• Leak Detector
• Field Procedures
• READy Mobile App
• Field Troubleshooting
• Leak Investigation
By allowing utilities to efficiently identify, locate, and repair leaks on service lines and distribution mains, ETEC’s comprehensive ALD monitoring services offer clients peace of mind. Meanwhile, advanced analytics and reporting enables the company to prioritize maintenance and repair efforts.
ETEC’s full suite of acoustic leak detection and monitoring services include:
• Monitor acoustic noise data throughout the distribution network
• Analyze and interpret acoustic noise data
• Localize potential leaks on service lines and distribution mains
• Prioritize and coordinate maintenance and repair efforts
• Work order management
• Advanced Reporting
Beyond deployment, ETEC offers a comprehensive range of post-deployment services and support, empowering utilities to maximize the value of their Kamstrup solutions.
Through ongoing professional services and support, ETEC’s dedicated team enables utilities to unlock the full potential of their investment, enhancing performance and maximizing return on investment (ROI). By providing proactive and reliable services throughout the lifecycle of each project, ETEC enables its clients to achieve operational excellence and sustainable growth, building a strong foundation for long-term success supplemented by Kamstrup’s industry-leading solutions.
In short, ETEC’s comprehensive postdeployment service and maintenance solutions ensure long-term reliability and efficiency of its clients’ advanced metering infrastructure (AMI) network infrastructure and devices, whilst its proactive approach helps utilities to reduce operating costs and optimize system performance.
ETEC provides services and support throughout all phases of its clients’ projects:
• Pre-Deployment
• Full Deployment
• Post-Deployment
Its full suite of service and maintenance offerings include:
• AMI Network monitoring – Continuous oversight to ensure system stability and performance
• IT support and troubleshooting –Resolving technical issues to maintain seamless operations
• ALD monitoring – Monitoring acoustic noise levels throughout the utility’s distribution network to efficiently identify and address potential distribution side leaks.
• Analytics and reporting – Providing data-driven insights for informed decisionmaking
• Customer service – Offering responsive support to address utility and end-user concerns
• RMA process management – Streamlining the return and replacement process for defective equipment
• Field service and maintenance – Onsite support for system upkeep and issue resolution
• Training – Equipping utility personnel with the knowledge to maximize system capabilities
“MAAS INCLUDES HASSLE-FREE SERVICE AND PERFORMANCE GUARANTEES THAT DELIVER ACCOUNTABILITY – IF A METER IS DEFECTIVE
OR MALFUNCTIONING, MONTHLY PAYMENTS STOP FOR THE SERVICE AND PAYMENTS DON’T START AGAIN UNTIL IT’S VERIFIED TO BE SUCCESSFULLY FUNCTIONING ONCE AGAIN”
–
BRUCE BHARAT, COUNTRY MANAGER AND VICE PRESIDENT OF NORTH AMERICA, KAMSTRUP
“LVVWD looks forward to seeing how a more accurate meter will help them with their progressive conservation and non-revenue water programs in a true urban desert environment,” outlines Bharat.
“They will be evaluating our claims of meter reliability and accuracy over the next few months and using the agreement to enable expansion into integrated ALD and other solutions.”
Excited to work with Kamstrup, LVVWD is going before its management board to authorize up to 400,000 residential meters as well as the new flowIQ® 4200 for casinos and
other large water users.
“Our ability and willingness to flex our production capabilities to win Las Vegas shows Kamstrup’s dedication to innovation,” Bharat observes.
Alongside its LVVWD agreement, Kamstrup announced the extension and expansion of its exclusive partnership with Everett J. Prescott, Inc. (Team EJP) in April 2024.
This partnership is a significant display of confidence in Kamstrup by Team EJP, a premier provider of water, wastewater, stormwater, and erosion control products.
“Team EJP officially ended a 70+
year relationship with a competitive meter manufacturer in order to represent Kamstrup,” reveals Bharat.
Through this relationship, Kamstrup has been able to expand its distribution network in Canada through an agreement with Team EJP and ICONIX Waterworks, a leading distributor of water, wastewater, and civil construction products.
The team at Kamstrup, meanwhile, continues to drive the company’s success in North America. 2024 was a year of significant
growth for its sales team, including several internal promotions, while staff reported a 90 percent loyalty rate in a recent employee survey.
“This is not only a key metric for our cultural and business success, but it also translates to consistent service and sales relationships with our customers,” Bharat notes.
Looking ahead, a big focus for Kamstrup in 2025 is to maintain its manufacturing efficiency and quality while growing into newer, larger segments of the North American water utility industry.
The company therefore recently completed a major overhaul of its internal sales processes in an effort to streamline the connection between sales and production.
“As a result, we are seeing our short lead times shrink even further while our production team is breaking efficiency records,” he prides.
Momentum is also expected to increase for MaaS this year, with
• Comprehensive Product Range: From 60” diameter pipes to ½” diameter pipes, and ¾” hose bibs to 48” valves, we offer everything you need for your water and wastewater, utility construction projects.
• Trusted Manufacturers: We represent hundreds of utility construction material manufacturing companies, ensuring that only the best products make it to your project.
• Superb Customer Service: We pride ourselves on exceptional customer service, offering guidance and support before, during, and after your purchase.
• Personalized Services: Receive one-on-one attention from our dedicated sales team to choose the perfect product tailored to your construction needs.
Kamstrup increasing its promotion of the model and increasing interest from water utilities.
From a product standpoint, the company anticipates increasing its market share in 2025 with the help of its groundbreaking flowIQ® 2200 residential meter, which has two significant differentiators that are revolutionary for utilities.
First, the flowIQ® 2200 features built-in ALD, which utilizes ultrasonic technology first introduced by Kamstrup in 2020 to listen out for leaks within the water column.
With an increasing number of Kamstrup ALD meters in the ground across the US, the real-world impact of this technology is revealing itself through impressive customer stories and testimonials.
The flowIQ® 2200 is also earning accolades for its ability to measure ultra-low flow consumption.
As hyper-efficient customer appliances become ubiquitous in US
households, utilities have been falling behind – until now.
“With Kamstrup’s ultra-low flow meters in place, utilities are able to capture an additional six gallons per minute (GPM), per household, per day on average.
“When this additional flow capture is multiplied over time and across communities, the results are astounding as just six gallons a day can help shave many years off the business case for a meter changeout project. With Kamstrup, water utilities are able to increase their return on investment (ROI), become more productive and efficient through AMI, and reduce non-revenue water,” Bharat concludes.
+1 (404) 835-6716
info-us@kamstrup.com www.kamstrup.com
Bryan Wilborn, Founder and CEO of Paloma Pressure Control, discusses the company’s key role in the provision of best-inclass oilfield services for North America’s oil and gas industry and how it has cultivated a culture of entrepreneurship, innovation, and most importantly, care
Writer: Lily Sawyer | Project Manager: Lauren Robinson
Following years of volatility caused by a fluctuating economy and cyclical price points, the North American oil and gas industry has begun to stabilize.
Having spent his entire career working in the sector, Bryan Wilborn, Founder and CEO of leading oilfield equipment supplier Paloma Pressure Control (Paloma), reflects on current market conditions.
“Today’s atmosphere is different to what we’ve experienced in the
past; I would describe it as stable,” he introduces.
Thanks to the advent of new technologies across the industry, Wilborn has witnessed evolution occur at breakneck speed, with the upstream sector, which has historically been slower in adopting and implementing new innovations, keeping pace. All these advancements have led to improved operational efficiency.
“At Paloma, we’re thrilled to
play a small role as the industry continues to gain momentum – it’s an incredibly exciting time to work in our space,” he adds.
Delivering specialized pressure control products and services to oilfield operators throughout the US and Canada, Paloma understands that operational efficiency is key to rapid production, and its flagship products support customers in this effort.
Headquartered in the Permian Basin, the US’ highest-producing oilfield, and with a large and expanding presence across Alberta, one of the richest oil provinces in Canada, the company is well-placed for continued success.
As a long-standing company that specializes in providing premium oilfield services for a wide range of exploration and production companies, Paloma has maintained
an acute awareness of both market conditions and the needs of its customers.
Prior to the COVID-19 pandemic, a mandate was brought forward by the company’s investors and its customers outlining how oil and gas companies should focus on free cash flow and responsible, sustainable growth – as opposed to the boomand-bust mentality of the past.
“While sustainable expansion has always been a key focus of Paloma’s managerial team, we stayed
disciplined during the pandemic and made two strategic acquisitions in 2021, increasing our asset base by approximately 35 percent,” Wilborn prides.
The successful completion of these acquisitions has allowed the company to continue growing within the Permian and Canadian markets, as well as expanding geographically into the Midcontinent (MidCon), Eagle Ford, and Haynesville Shale Basins.
“Since the pandemic, we’ve been much more strategic in terms of our
Paloma’s expertise was first established in the Permian Basin in late 2016. The company began as a team of pressure control experts working under the wellknown brand, Butch’s Rat Hole & Anchor Service (Butch’s).
Commencing service in early 2017 with an acute focus on exceptional quality, the team quickly earned a reputation for success in the field that initiated an unparalleled level of growth year-on-year.
However, just as the oil and gas industry reached a peak of rapid expansion, it was faced with economic difficulties caused by the COVID-19 pandemic.
In the face of such adversity and with a sense of devotion to the partnerships it had cultivated, the company endured this period of turbulence and emerged from it stronger than ever. As such, Paloma earned widespread respect for its most defining characteristic – its culture.
Considering the opportunities ahead and with a new-found appreciation for the industry, Paloma was brought to life as a new company with the same brand of quality and service that Butch’s was originally built upon.
Today, the company operates primarily in North America’s Permian Basin, with substantial excess capacity in place to secure continued growth.
growth and where we’re allocating capital,” he explains.
Today, Paloma’s core products include its MF frac valve line and Rapid Run frac line for remote and extended fracking applications, weldless missiles such as the Paloma Single Barrel (PSB), a semi-automatic disconnect system, and Birdseye View (BEV) automation system.
“In all applications, our field services team is available to support with rig-up and rig-down, torque and test requirements, and field maintenance and operations,” Wilborn assures.
Born out of three guiding principles, Paloma differentiates itself from the rest by seeking to take care of and develop its employees and customers while working harder and smarter than its competitors.
This has allowed the company to develop a dedicated, knowledgeable, and skilled workforce with an unrivaled culture of customer focus.
“Fostering a ‘make it happen’ culture and taking care of people both inside and outside of Paloma is incredibly important to us,” Wilborn acknowledges.
Much more than just words, the company’s three guiding principles set standards for its workforce to live by.
In line with its culture, Paloma is always seeking opportunities to improve the efficiency of its processes, develop its people, and enhance its product offering to solve challenges, alongside advancing customer operations as a top priority.
As such, corporate social responsibility (CSR) is extremely important to the company as it strongly believes it should support and care for the communities in which it operates.
Paloma therefore sponsors various educational and family-focused events throughout the year, including a ‘toys for tots’ donation drive in which
“FOSTERING A ‘MAKE IT HAPPEN’ CULTURE AND TAKING CARE OF PEOPLE BOTH INSIDE AND OUTSIDE OF PALOMA IS INCREDIBLY IMPORTANT TO US”
– BRYAN WILBORN,
FOUNDER
AND CEO, PALOMA PRESSURE CONTROL
Paloma matches the number of gifts and toys brought in by employees for local children.
“We also host a back-to-school drive where we collect backpacks and supplies for students in the area, hosted at a local park. It’s a familyfriendly day with hot dog stands,
One of Paloma’s key priorities is to listen to its customers’ challenges from the field and provide value-added solutions.
“With so much new technology being deployed, we’re working to intertwine our innovative products and
For example, the Rapid Run frac line helps maximize efficiencies to achieve first production faster. With a reach of 5,000 feet (ft) and counting Paloma’s Rapid Run extended flowline system enables complex remote, multi-pad, or simultaneous frac rig-ups without the bird’s nest of iron and hoses
Certified Labs specializes in delivering advanced lubrication solutions that are specifically engineered to meet the rigorous demands of the oil and gas industry.
Our products are designed to withstand extreme temperatures, pressures, contamination, and corrosive substances encountered in drilling, extraction, transportation, fracking, and refining operations. No matter if it’s protecting drilling equipment from wear and corrosion or ensuring the smooth operation of pumps, compressors, power ends, and turbines, our lubricants are formulated to deliver exceptional performance and reliability in the most challenging environments.
• Industry Expertise: With years of experience serving the oil and gas industry, Certified Labs understands the unique lubrication needs and challenges faced by our customers.
• Advanced Formulations: Our lubricants are formulated using the latest technology and highest quality base oils and additives to deliver superior performance, reliability, and protection in even the most demanding applications.
• Customized Solutions: We offer a comprehensive range of lubrication solutions tailored to meet the specific requirements of different equipment types, operating conditions, and industry standards.
• Technical Support: Our team of lubrication specialists provide expert advice and support to help you optimize your lubrication practices and achieve maximum efficiency, productivity, and reliability.
Certified is the largest independent lubricant manufacturer in North America
· Certified has 500 full-time local representatives providing expert on-site service
Certified provides the industry expertise customers need Certified delivers rapid innovation and technical support
· Certified provides industry-leading value-added services
· Certified generates savings and productivity improvements supported with measurable results
Whether you’re operating in upstream exploration and production, midstream transportation and storage, or downstream refining and processing, Certified Labs is your trusted partner for peak performance in the oil and gas industry.
Contact us today to learn more about how our advanced lubrication solutions can help you increase uptime, improve equipment life, and maximize the efficiency and reliability of your operations.
“AT PALOMA, WE’RE THRILLED TO PLAY A SMALL ROLE AS THE INDUSTRY CONTINUES TO GAIN MOMENTUM – IT’S AN INCREDIBLY EXCITING TIME TO WORK IN OUR SPACE”
–
BRYAN
WILBORN, FOUNDER AND CEO,
PALOMA
Elsewhere, Paloma is focused on improving its real-time pressure monitoring, predictive maintenance, and automation processes to optimize operations.
“Specifically, we’ve been working on expanding our BEV system to
provide enhanced visibility into wellsite operations while integrating additional pressure monitoring capabilities for better data-driven decision-making,” he reveals.
The advanced BEV system provides a real-time view of critical
pressure control equipment and systems for optimal wellsite performance and management. With such advancements, larger projects are now more feasible for Paloma.
“While artificial intelligence (AI) could play a role in the future, our current focus is on refining and deploying proven automation technologies that align with our operational needs,” Wilborn confirms.
As it continues to cultivate strong relationships with suppliers, Paloma
· MF FRAC VALVE™ is an innovative grease-less, service-less valve that eliminates traditional maintenance requirements and lasts longer on the job than conventional valves. The MF Frac Valve™ is redefining performance expectations to deliver unprecedented operating efficiency and cost savings.
· RAPID RUN FRAC LINE™ is a scalable, large bore frac line system that reduces iron and inefficiency to help smart operators get to first oil faster. With a reach of 5,000 ft, Paloma’s extended flowline system enables complex remote pad, multi-pad, or simultaneous frac rig-ups.
· WELDLESS MISSILE™ is a patent-pending missile system that delivers advanced pressure control capabilities from the pump to the wellbore. Built for precision performance and durability, the Weldless Missile™ offers stronger, seamless connections to improve functionality while minimizing the need for infield maintenance and the risk of pinhole leaks.
· SEMI AUTO PUMP DISCONNECT™ system allows for the quick, efficient, and safe exchange of surface fracking equipment with minimal disruption. With its smart, simple design, the Semi Auto Pump Disconnect™ has fewer potential points of failure or malfunction, so it minimizes operational disruptions and eliminates the need for complete shutdowns for repairs.
· BEV AUTOMATION™ is an advanced automation system that provides a real-time view of critical pressure control equipment and systems for optimal wellsite performance and management. BEV’s adaptable dashboard allows operators to monitor current pressures, verify valve positioning and operational modes, and set alerts to prevent and automatically troubleshoot problems.
feels a deep sense of loyalty toward those who have helped it grow over the years.
“Our suppliers are our partners in every sense of the word. We’re proud of our supplier relationships and have benefited from their exceptional quality, service, and commitment to doing what’s right and never taking shortcuts,” Wilborn pronounces.
Given its growth since the two acquisitions made in 2021, Paloma has a distinct idea of what it seeks to achieve going forward.
As such, employee development is a key priority for the business, having worked hard to maintain a culture of integrity.
“As companies grow, it’s hard to maintain the type of culture we’ve developed, and we’re very protective of it. We always want to be a company that our customers can rely upon when trying to solve a problem,” he shares.
Celebrating its entrepreneurial and innovative thinkers, problemsolvers, and solution-minded team members, Paloma is a proudly people-centric organization.
“We’re on a constant mission to improve our operations – that starts with the folks we hire and the culture within,” Wilborn passionately concludes.
Agnes Wietrzynski, President and CEO of QM Environmental, outlines the company’s ongoing projects while emphasizing its deep-rooted commitment to safety and Indigenous inclusion
Writer: Lily Sawyer | Project Manager: Kierron Rose
Characterized by continuous development as new technologies and advancements emerge, Canada’s environmental and industrial services industry is poised for growth.
Meanwhile, companies operating in this space have seen their environmental priorities evolve as new contaminants and associated remediation needs materialize.
“The industry is currently an exciting yet challenging space,” introduces Agnes Wietrzynski, President and CEO of leading Canadian environmental and industrial services company, QM Environmental (QM).
Wietrzynski points out how, to be successful, companies such as QM must remain agile to keep pace with constant industry changes, continually innovating with new technologies and approaches to address ongoing challenges.
“It’s a rewarding sector to work in as
we collaborate with others to build climate resilience,” she reflects.
With locations spanning across Canada, QM’s vast suite of services include environmental remediation, demolition and decommissioning, hazardous materials abatement, and emergency response and management, among others.
The company’s varied and diverse clientele includes general contractors, government, transportation authorities, manufacturers, mining companies, agricultural companies, and private businesses.
At the core of QM’s identity and success are its corporate values, which include a company-wide commitment to safety, excellence, diversity, and resilience, summarized in its tagline – ‘Done Safely, Without Compromise’.
“OUR STEADFAST DEVOTION TO DIVERSITY ENSURES THAT WE FOSTER A CULTURE WHERE EVERYONE IS VALUED FOR THEIR UNIQUE PERSPECTIVES”
– AGNES WIETRZYNSKI, PRESIDENT AND CEO, QM ENVIRONMENTAL
In recognition of QM’s successful, people-centric safety strategies, Wietrzynski herself was recently awarded the Workplace Safety and Prevention Services (WSPS) award for ‘CEO of the Year’ at the 2024 Canada’s Safest Employers event.
Some of the competitive criteria used to determine the winner included identifying skills in each CEO which inspire, engage, and excite the workforce about safety.
Meanwhile, Melissa Clarke, the company’s Vice President of Environment, Health, and Safety (EHS), has been recognized multiple times by Canadian Occupational Safety (COS) as a ‘Top Woman in Safety’, further solidifying QM’s commitment to welfare.
In addition, the company was awarded COS’ 5-Star Safety Cultures award in 2023, the adjudication process of which saw employees complete an anonymous survey to outline how they felt about QM’s safety culture, demonstrating the company’s positive view on safety from within.
“Our EHS policies, systems, procedures, and results consistently meet the stringent requirements of Canada’s most safety-conscious clients and industries,” Wietrzynski prides.
QM’s award-winning commitment to safety helps it to attract talent who share the company’s commitment to excellence, providing it with a competitive advantage.
Since its inception, QM’s Indigenous Partnerships and Capacity Building program has formed an integral part of its core values, cultivating a policy of active engagement of Indigenous peoples on its projects.
“The program is a proven methodology of integrating with and contributing to local Indigenous communities, businesses, and peoples through training, employment, sub-contracting, and other business ventures,” Wietrzynski outlines.
QM’s Indigenous initiatives have succeeded so far because of the
• Gunnar mine and mill site demolition and remediation – The project has undertaken many crucial work scopes including extensive asbestos abatement, the demolition of more than 80 buildings and structures, and the remediation of physical, chemical, radiological, and biological hazards.
• Portlands flood protection and enabling infrastructure – Involves the transformation of a blighted industrial lake fill area into a new river channel for the Don River in Southern Ontario. QM’s role in this project includes the excavation of river valleys, reuse backfilling, soil tracking, geomatics, soil treatment, horizontal reactive barrier construction, river finishes, and marine construction.
• Diamond mine demolition and remediation - The scope for this project includes the complete demolition of all above-ground mine infrastructure at a former diamond mine located in the Northwest Territories. This project strongly emphasizes local northern and Indigenous employment and relations.
• Large North American automotive manufacturer – Includes interior selective removals, asbestos abatement, and demolitions at multiple automotive facilities to pave the way for electric vehicle (EV) manufacturing and assembly.
• Large power generation station environmental decommissioning
– Comprises the restoration of large power generation sites, returning them to their original, natural condition. For example, the construction of passive surface water management systems is used to properly manage stormwater from becoming impacted and reduce potential issues associated with erosion and flood conditions.
Powering Ontario’s infrastructure with reliable trucking solutions, AM Haulage specializes in material transportation and disposal services for large-scale infrastructure projects. A proud transportation partner of QM Environmental, our hauling capabilities are second to none.
Operating one of Ontario’s most dependable and efficient trucking fleets, complete with over 90 tri-axle dump trucks and live-bottom units, AM Haulage has built a reputation for reliability, safety, and efficiency.
Whether moving aggregates, soil or construction materials, our fleet is ready to meet the demands of the most challenging projects.
Having played a crucial role in several high-profile projects in the region, AM Haulage ensures seamless material transportation solutions while maintaining the highest standards of safety and environmental compliance. We play a significant role in trucking for QM Environmental, working closely with them to support large-scale environmental projects, ensuring safe and responsible material haulage.
One of the largest construction undertakings in Canada, the Toronto Port Lands Flood Protection (Toronto Port Lands) project is transforming the city’s waterfront. QM Environmental was awarded the request for proposal (RFP) 33.6 subcontract in 2021.
Successfully providing tri-axle dump truck haulage solutions on the project for the past three years, AM Haulage has secured its status as a trusted partner on this complex initiative. Handling large volumes of soil and aggregate, we ensure efficient transportation solutions while navigating strict safety regulations.
The Toronto Port Lands project is known for its intricacies, presenting various challenges, however our expertise has continued to ensure success.
AM Haulage’s role in this project showcases our ability to meet stringent timelines, adhere to environmental compliance, and operate efficiently within a high-demand urban setting, and its success is a testament to our commitment to quality and reliability in major infrastructure works.
AM Haulage has also provided material haulage solutions for the Toronto Transit Commission’s Russell Carhouse Upgrades, efficiently transporting soil and aggregates off-site.
Our ability to coordinate logistics for high-traffic urban projects makes us the preferred choice for municipal and transit-related construction.
Further to this, experienced and efficient AM Haulage drivers bring a wealth of experience and efficiency to every project, making us a reliable choice, whilst our dedication to everything we undertake results in clients that are deeply satisfied with our services.
In addition to construction, AM Haulage also manages winter operations for the City of Hamilton’s snow removal program.
Our fleet operates across multiple sites, ensuring roadways remain safe and functional during heavy snowfall.
This large-scale, time-sensitive operation underscores the company’s adaptability and reliability in diverse project settings.
AM Haulage stands out as the best in the industry, and this is why.
• Safety first – With one of the strongest safety track records in the industry, AM Haulage has experience in handling highrisk and complex projects. Our drivers are highly trained and our fleet is equipped with the latest safety technologies.
• Reliable fleet and experienced operators
– With over 90 trucks, we provide scalable solutions that meet all types of project demands, from small-scale municipal work to large infrastructure projects.
• Efficiency and compliance – AM Haulage’s operations meet all regulatory standards, ensuring environmentally responsible and legally compliant material transport.
• Proven track record – Partnerships with major contractors, government agencies, and municipalities demonstrate our expertise and commitment to excellence.
Let’s connect and discuss how AM Haulage can support your next project with cost-effective and dependable trucking solutions.
For more information, visit www.amhaulage.ca.
diversity of its approach, commitment to its people, and corporate support at all levels of the organization.
“Our steadfast devotion to diversity ensures that we foster a culture where everyone is valued for their unique perspectives,” she notes.
Having trained over 500 Indigenous people and carried out project contracts with Indigenous partners amounting to more than $250 million and counting, QM is a leading Indigenous training provider to both the public and private sectors.
The company also works with staff and students at local high schools in remote communities to identify, train, coach, and motivate young people to work on-site while gaining credits toward their high school graduation.
“Many of those that we train have subsequently been hired by QM or other employers across a variety of industries,” Wietrzynski informs.
This approach has brought new ideas to the organization that have allowed it to continue to evolve its services offerings and enhance the way it does business.
Committed to Indigenous partnership, capacity building, and long-term sustainability in the Athabasca Basin of Saskatchewan, QM Points (QMP) is a QM company that operates in partnership with Points Athabasca, a progressive and fast-growing Indigenous-owned general contractor.
Recently awarded to QMP by the Saskatchewan Research Council (SRC), the demolition of asbestosladen buildings at the Gunnar mine and mill site is a standout project for the company due to both its operational success and the majority involvement of Indigenous people from the Athabasca Basin region, exceeding the target set by SRC.
The project scope, which is centered around a former uranium mine in Northern Saskatchewan, includes the development of approximately 400,000 square meters (sqm) of local borrow areas, alongside the innovative construction of an engineered cover system over waste rock piles using 230,000 cubic meters (cbm) of backfill material. Meanwhile, construction of
“WE ARE ALWAYS OPEN TO PARTNERING WITH ORGANIZATIONS WHO SHARE OUR COMMITMENT TO SOLVING ENVIRONMENTAL CHALLENGES”
– AGNES WIETRZYNSKI, PRESIDENT AND CEO, QM ENVIRONMENTAL
two landfills – non-hazardous and hazardous – and their demolition and legacy waste clean-up included excess concrete removal and the excavation of soil.
In addition, the development saw the construction and installation of three stainless steel-engineered mine opening caps.
“The cooperation and partnership of neighboring communities has been critical to this project,” Wietrzynski shares.
QMP’s overall goal for the Gunnar mine and mill site remediation project is to properly engage, include, and support the people of the Athabasca Basin region throughout the project lifecycle in a manner that serves communities in the years after the project ends.
Looking to the future, the company’s priorities remain rooted in revitalizing its local environment and
building climate resilience for future generations.
“Our diverse services will continue to evolve based on the changing needs of our customers. We are always open to partnering with organizations who share our commitment to solving environmental challenges,” she passionately concludes.
Tel: 1.800.251.7773
info@qmenv.com
www.qmenv.com
As one of the most experienced deep foundation specialty contractors in North America, we catch up with Bill Shea, COO, about Morris-Shea’s recent developments
Writer: Lucy Pilgrim | Project Manager: Kierron Rose
The US construction industry has evolved to meet the demand for greater manufacturing capabilities and renewable energy applications.
This is realized in new construction starts for significant transportation and manufacturing infrastructure projects, including liquefied natural gas (LNG) terminals, electric vehicle (EV) plants, and rolled aluminum mills.
It is in these sectors that MorrisShea shines, having completed deep foundation operations for six LNG projects in the Gulf Coast, as well as a Ford electric vehicle (EV) plant and a massive aluminum manufacturing facility.
Bill Shea, COO, believes its recent successes are a direct result of the company’s ambitious evolution from
a regional player to the fourth largest deep foundation contractor in North America.
“We’ve propelled our whole
operation into the future with an ongoing employee training program, innovative project engineering, and state-of-the-art construction equipment. MorrisShea has searched worldwide for the most advanced specialty deep foundation equipment,” offers Shea.
The contractor has more than doubled its operational capacity over the last decade, enabling it to reach new heights in the installation of deep foundation systems across the energy, manufacturing, commercial, and industrial markets.
“Our successes are not only about the projects we complete, but they are also about the people behind them. As we grow, so do the opportunities for personal and professional achievements among our team,” Shea says.
For generations, the MorrisShea team has helped to build the backbone of the US’s infrastructure. Today, the company continues to strengthen this foundation with innovation and engineering prowess. Nationwide, communities depend on the contractor’s expertise as a leader in deep foundation construction.
Great structures, whether they are buildings or factories, begin with a vision and solid foundation. Therefore, Morris-Shea’s focus is on developing foundation solutions and maintaining the highest quality standards.
In addition, the country’s top companies across various industries trust Morris-Shea to provide a crucial foundation that supports their dreams.
Morris-Shea has the necessary manpower, equipment, and experience to
“WE ARE PROUD TO SUPPORT THIS GENERATION OF MORRIS-SHEA TEAM MEMBERS, LAYING DEEP FOUNDATIONS FOR A BRIGHTER TOMORROW”
– BILL SHEA, COO, MORRIS-SHEA
maintain the engineering integrity and construction processes necessary for multiple projects.
The concurrent installation of nearly 66,000 DeWaal piles at new LNG terminals in Corpus Christi, Texas and Plaquemines Parish (Plaquemines), Louisiana, required numerous highlyskilled crews of deep foundation professionals.
Operations in Plaquemines comprised 12 rigs drilling around the clock, involving 300 on-site employees installing approximately 33,000 piles to depths of more than
120 feet (ft).
The experience needed for the project grew from years of DeWaal pile installation at LNG liquefaction facilities near Freeport, Texas; Sabine Pass, Gulf of Mexico; and Cameron Parish and Calcasieu Pass, Louisiana.
Today, the Morris-Shea DeWaal Pile System provides critical foundations for advanced LNG terminals operating throughout the southern US.
At the Plaquemines LNG terminal project, the company amassed over one million man-hours without a single reported safety incident.
At Tractor & Equipment Company (TEC), we believe in building lasting relationships with our partners. Our longstanding collaboration with Morris-Shea is a testament to the trust and confidence they have placed in our products and services. Together, we have achieved remarkable milestones in the construction industry. We applaud Morris-Shea for all its success and are proud to assist the company as it continues to grow and thrive.
The cornerstone of our partnership lies in the utilization of advanced Komatsu equipment. Known for its unparalleled reliability, cutting-edge technology, and exceptional performance, Komatsu machines have become a key part of Morris-Shea’s projects. These machines enable them to tackle complex challenges with ease, ensuring projects are completed on time and to the highest standards.
TEC takes great pride in our commitment to minimizing downtime and maximizing efficiency. We understand that even the slightest delay can have a significant impact on project timelines and costs. That is why we have implemented robust
measures to keep downtime to a minimum. Our proactive maintenance practices, comprehensive spare parts inventory, and expert technical support are tailored to meet the unique needs of Morris-Shea and to keep their operations running smoothly.
We are grateful for the trust and confidence that Morris-Shea has placed in TEC as its longstanding partner. Our continued collaboration is a testament to our unwavering commitment to its success and to providing industry-leading equipment and service.
If you have any questions or would like to learn more about our partnership with Morris-Shea, or the range of Komatsu equipment we offer, please do not hesitate to reach out to us. Our dedicated team is here to support you and help you achieve your construction goals.
Thank you for your continued support and trust in TEC. We look forward to serving you and exceeding your expectations in the years to come.
Visit us at tec1943.com
In 2024, Morris-Shea completed the installation of DeWaal piles, rigid inclusions, and foundation shoring at Ford’s expansive new production facility near Stanton, Tennessee.
Nearly 10,000 DeWaal piles were drilled in sites throughout Ford’s EV manufacturing complex. Three major pits were excavated and the bases were fitted with mud slabs, followed by the installation of concrete slabs. Two of the pits began as sheet pile cofferdams and the third utilized wood lagging for earth retention shoring.
Morris-Shea collaborated with the facility’s engineers to optimize an alternate design to the original specification for drilled shafts. DeWaal piles provided a value-engineered solution that improved production performance while maintaining load capacity.
Morris-Shea is nearing the completion of deep foundation continuous flight auger (CFA) piles, soil mix walls, sheet pile cofferdams, and drilled shafts at a massive aluminum manufacturing plant under construction in Bay Minette, Alabama.
The contractor utilized a rigmounted vibro hammer, Kemsolid KSI soil mixer, Fundex F5600 and F3500, Liebherr, and Bauer BG 45 drill rigs for the project.
Morris-Shea installed drilled shafts in the caster pit, setting four 103-inch diameter steel casings in pre-drilled shafts to a depth of 106ft. Internal casings were added and reinforced with rebar and concrete between the two steel pipes to accommodate a piston-like action.
Going forward, large hydraulic cylinders will be mounted inside the inner casings for the purpose of pushing the castings out of the caster pits.
Morris-Shea’s Fundex F5600 is the largest sole-purpose foundation drill rig in use in North America. The contractor maintains two of these purpose-built, fixed-mast rigs in its extensive fleet of advanced deep
foundation installation equipment.
The Fundex F5600, for example, can be purposed to perform multiple foundation techniques but is primarily used by the company to install the DeWaal Pile System. The drill rig was also recently employed for critical energy facility construction and major residential high-rise projects.
Additionally, Morris-Shea has purchased six portable, compact, track-mounted drill rigs designed for the installation of geothermal closedloop heating and cooling systems.
All of the company’s heavy equipment is linked to its Automated Monitoring System, which records all parameters during drilling operations and then produces a comprehensive log for each borehole.
Morris-Shea achieved the Associated Builders and Contractors’ (ABC) STEP Diamond Award for a second consecutive year in recognition of its outstanding safety performance.
“This award demonstrates how strongly we believe in our culture of safety,” Shea says.
“Our company is committed to safeguarding the well-being of every Morris-Shea team member. Workplace safety is our ongoing priority; it’s an initiative that strives to deliver us home
safely at the end of each workday.”
Meanwhile, Morris-Shea’s geotechnical team constructs foundations for many of the world’s largest energy, manufacturing, industrial, and commercial projects. The contractor is currently installing deep foundations under some of North America’s most exciting construction operations.
“We are proud to support this generation of Morris-Shea team members, laying deep foundations for a brighter tomorrow. The work we do today builds a strong future for both the company and our families, driving health and prosperity for our whole team,” Shea concludes.
Since 1992, Morris-Shea has installed hundreds of thousands of deep foundation piles throughout the US, Caribbean, and South America, and will continue to excel into the future.
Tel: Tel: +1-205-956-9518
info@morrisshea.com
www.morrisshea.com
Possessing two decades of industry-leading construction expertise, Zgemi has built a reputation as one of Canada’s elite general contractors and construction management firms. We speak with Yusuf Yenilmez, coFounder and Managing Partner, and Stelios Hiotakis, Executive Vice President, to learn more about their journey and the company’s unwavering commitment to excellence
Writer: Lauren Kania | Project Manager: Kierron Rose
At Zgemi, construction is about more than just bricks and mortar – it’s about vision, relationships, and making a lasting impact.”
With a presence in major cities across Canada, Zgemi is a full-service general contractor and construction management firm headquartered in Brampton, Ontario.
Over the past 20 years, the company has successfully completed more than 5,000 projects, solidifying its reputation for delivering unparalleled quality, safety, and efficiency in institutional, commercial, multi-unit residential, and industrial developments.
The firm stands out for its meticulous planning, client-first mentality, and ability to handle complex, large-scale projects. Whether it is pre-construction advisory, value engineering, cost estimation, or full-scale design-build solutions, Zgemi approaches each project with the same philosophychallenges are opportunities.
“One of our differentiators is that we don’t see problems as roadblocks; we see them as opportunities,” continues Stelios Hiotakis, Executive Vice President.
Just as important as execution is the company’s deep-rooted commitment to client relationships.
“Trust and transparency are the foundation of everything we do,” adds Hiotakis.
“Our clients are our top priority, and that mindset is ingrained across our company. We build lasting partnerships by always putting their interests first.”
With a team made up of highly skilled professionals, the company takes pride in a work culture that values collaboration, innovation, and customer-first thinking.
“We have built long-term relationships with a diverse client base, healthcare providers, developers, and private corporations,” insights Yusuf Yenilmez, co-Founder and Managing Partner.
Zgemi’s leadership reflects its core values – both Yenilmez and Hiotakis bring decades of industry expertise, each with a unique path into construction.
Hiotakis, originally from Greece, began his career in the national military, earning his civil engineering degree through the armed forces. After moving to Canada, he completed a Master of Applied Science in Engineering at Carleton University before working in project
management, advocating for clients as an owner’s representative.
“My background allowed me to see construction from the owner’s perspective, which is invaluable in building relationships and delivering successful projects,” he shares.
Yenilmez, on the other hand, took a more unconventional route. He studied fashion design before arriving in Canada, only to find himself drawn to construction.
“For me, construction is like designing a piece of art – each project presents unique challenges that require creative problem-solving.
Whether it’s infrastructure, commercial developments, or institutional projects, the common thread has always been a commitment to innovation and excellence,” he explains.
Zgemi’s guiding principle is simple yet powerful – “see the customer’s point of view first, and then create a win-win deal.”
This philosophy drives every decision, from contract negotiations to project execution. The company
“ONE OF OUR DIFFERENTIATORS IS THAT WE DON’T SEE PROBLEMS AS ROADBLOCKS; WE SEE THEM AS OPPORTUNITIES”
– STELIOS HIOTAKIS, EXECUTIVE VICE PRESIDENT, ZGEMI
prides itself on fostering strong client relationships by understanding their unique challenges and working toward mutually beneficial solutions.
“Construction isn’t just about contracts and deadlines – it’s about people”, says Yenilmez.
Whether collaborating with clients, suppliers, or subcontractors, Zgemi’s approach centers around trust, transparency, and fairness.
“We want our partners and trades to feel valued. If they trust us, they’ll want to work with us again and again. That’s the foundation of long-term success,” adds Hiotakis.
This people-first mindset extends beyond clients and stakeholders – it directly impacts entire communities. Zgemi understands that every project affects multiple layers of society, from developers and investors to local businesses and residents.
“To achieve true success, you need open communication, no surprises, and a shared vision,” says Hiotakis.
YUSUF YENILMEZ, CO-FOUNDER AND MANAGING PARTNER: “In construction, delays or quality issues can derail an entire project, so we only work with trusted suppliers who share our commitment to excellence. Long-term partnerships ensure cost efficiency, reliability, and seamless execution. We also prioritize working with local suppliers to support the communities we operate in.”
STELIOS HIOTAKIS, EXECUTIVE VICE PRESIDENT:
“We don’t succeed alone – we succeed as a team. Trades are constantly pulled in different directions, so we strive to be the partner they trust most. That means paying on time, treating them fairly, and showing appreciation. When you create an environment of respect and reliability, your entire supply chain thrives.”
Despite the current economic challenges, looming tariffs, and a fluctuating condo market, Zgemi has continued to thrive and expand by strategically targeting stable, highdemand sectors.
Rather than pulling back, the company has diversified its portfolio, focusing on social infrastructure projects that drive long-term impact.
“If you have the right team and the right plan, you can turn challenges into opportunities,” Hiotakis states.
By staying adaptable and forwardthinking, Zgemi has successfully navigated the industry’s uncertainties
alongside maintaining operational resilience.
“While the market may be shifting, our ability to pivot, innovate, and remain client-focused ensures we continue to grow despite challenges,” says Yenilmez.
One of Zgemi’s strongest competitive advantages lies in its expertise in healthcare construction – a field that demands precision, regulatory compliance, and an unwavering commitment to excellence.
The company has been instrumental in delivering state-of-the-art
long-term care facilities, addressing Canada’s urgent need for more accessible and sustainable healthcare solutions.
“One of our most exciting projects is a cutting-edge healthcare facility that will redefine patient care with advanced technology, sustainable design, and a patient-first approach,” reveals Yenilmez.
Zgemi is currently engaged in
delivering four long-term care facilities across Ontario, a critical step toward improving healthcare accessibility and employment stability in the sector.
“It’s incredibly rewarding to know that our work directly improves lives – not just for residents, but also for healthcare workers and families who need peace of mind knowing their loved ones are in good hands,” adds Hiotakis.
• Development planning
• Pre-construction advisory
• Value engineering
• Cost estimation
• Constructability review
• Construction management
• General contracting
• Design-build
Sustainability has been woven into Zgemi’s DNA since its inception. The company integrates eco-friendly materials, energy-efficient designs, and waste reduction strategies into every project.
Beyond construction, Zgemi is deeply involved in community initiatives, supporting local charities, education programs, and
environmental sustainability efforts.
“We don’t just build for today –we build for future generations,” emphasizes Yenilmez.
To further its commitment to sustainability, Zgemi has developed a renovation program that salvages furniture, doors, and materials from project sites to be repurposed or donated instead of discarded.
“CONSTRUCTION ISN’T JUST ABOUT CONTRACTS AND DEADLINES – IT’S ABOUT PEOPLE”
– YUSUF YENILMEZ, CO-FOUNDER AND MANAGING PARTNER, ZGEMI
“When we renovated our Ottawa office, we didn’t buy a single new piece of furniture – we reused everything from previous projects. That’s something I’m really proud of,” shares Hiotakis.
Looking ahead, Zgemi is focused on expansion, innovation, and smart construction technologies. The company is exploring new
opportunities in the US and Europe while integrating artificial intelligence (AI) and data analytics to enhance project efficiency, progress, and safety monitoring.
“We want to grow for the right reasons – by representing owners, fostering strong relationships, and making a meaningful impact in our communities,” says Hiotakis.
With an exceptional leadership team, strong company culture, and innovative approach to construction, Zgemi is poised to continue leading the industry in building not just structures, but a better future.
“We’re incredibly proud of what we’ve built so far – but even more excited about what’s ahead,” concludes Yenilmez.
Tel: 905-454-0111 info@zgemi.com www.zgemi.com
ADCO Electrical Corporation is recognized for promoting diversity and inclusion within the construction industry, powered by its clientcentric approach and ability to address various technical challenges. We illuminate how the current leadership is upholding a legacy of excellence
Writer: Rachel Carr | Project Manager: Kierron Rose
The history of women in construction reveals a gradual evolution, shaped by a series of pivotal events, such as during World War II when the iconic Rosie the Riveter recruitment campaign symbolized women stepping into roles traditionally held by men.
As societal norms and stereotypes continue to shift, the narrative surrounding women in construction is also beginning to change.
An increasing number of women are opting to pursue careers in traditionally male-dominated fields as opportunities in industries such as construction and engineering continue to grow. According to the U.S.
Department of Commerce, today, one in seven jobs is held by women – a female workforce percentage of just over 14 percent.
A prominent company that plays a significant role in impacting gender disparity in construction is ADCO Electrical Corporation (ADCO).
Established in 1977, ADCO is continuing the legacy of its founder, Richard Addeo, a well-respected leader in the industry. His mission was to create a standard of excellence in the New York electrical contracting market.
Today, Addeo’s daughter, Gina, who has served on the executive leadership team since 2011, has taken the reins as President and CEO, with her sister, Lisa, as Executive Vice President.
Since its inception, this family-run organization has been inspired by its clients’ vision, aligning with the founder’s objective of addressing technical challenges in the constantly evolving fields of lighting and low voltage design. As the complexities of the construction environment have changed, ADCO has continued to adapt.
Under Richard Addeo’s leadership, the company became a client-centric entity, maintaining its reputation
in shaping the electrical and telecommunications industry in New York City’s metropolitan area. Furthermore, ADCO’s emphasis on logistics, planning, and production capabilities are core differentiators defining its value to customers as a commercial partner.
Gina Addeo is a strong advocate for diversity in the industry and has made significant investments in talent at all levels. Notably, she was the first woman to be appointed President of the New York Electrical Contractors Association (NYECA) and obtain a New York City Master Electrician License.
She serves on the Board of Directors for charitable organization, Friends of St. Dominic’s, the Joint Industry Board of the Electrical Industry, and various committees within NYECA. Additionally, she is part of the Negotiating Committee for contracts for the Local Union No.3 International Brotherhood of Electrical Workers (IBEW).
• Today, over 1.3 million women are employed in the construction sector nationwide in the US, compared to more than 10 million men.
• Since 2016, this figure has increased every year thanks to targeted training programs and grants aimed at improving diversity.
• The overall numbers reveal not only gender disparity but also the types of roles occupied by men and women, with men dominating field roles and women in more administrative positions.
• Alaska has the highest share of women in the construction sector, with Hawaii coming a close second. The city with the most female workers in the industry is Jacksonville, Florida.
• The gender pay gap is lower in construction – women tend to command higher wages than female workers in other industries.
Elsewhere, she is a member of the zenith group of the Women Presidents Organization (WPO), advocates for Nontraditional Employment for Women (NEW), and is a recipient of the Distinguished Alumni Award in Business and Finance from the Stevens Institute of Technology.
ADCO is a certified woman-owned business enterprise recognized by the Women’s Business Enterprise National Council (WBENC), the City of New York, the Port Authority of New York and New Jersey, and the School Construction Authority (SCA). The two sisters own 51 percent, selling 49 percent to an employee stock ownership plan.
The company is dedicated to empowering its employees to create and maintain a diverse and ethical workplace. It is committed to continuously improving its business practices, which is central to its culture and informs its partnerships and operations.
ADCO collaborates closely with NEW to recruit, train, and place women in careers within the unionized
construction industry, providing them access to the middle class.
The company’s leadership has been actively represented on the board of NEW for over two decades.
Local Union No.3 IBEW has achieved remarkable success in helping women enter the preapprenticeship training program at NEW, boasting the highest placement success rate for long-term employment among NEW graduates.
The program’s success is evident in the tradeswomen from NEW who have become highly skilled union electricians and are now working for ADCO.
ADCO’s approach to innovation focuses on leveraging big data analytics to improve the outcomes of the construction process.
The valuable insights gained can help identify when a project is at risk of exceeding its budget or experiencing delays. This allows project managers to address potential issues before they escalate into larger problems.
In addition to financial aspects, these analytics programs can evaluate data related to performance and safety. As a powerful digital tool, analytics can support every phase of a project, making it essential for effective planning in the construction process.
At ADCO, transitioning into a data-driven company through a multi-year initiative has fostered a safer and smarter work environment. Collaborating closely with the executive committee, the team – which includes data analysts and scientists – has developed a roadmap, architectural framework, operating model, and governance structure for the advanced technology landscape.
Focused on the intersection of people, processes, and technology, the Business Use Case virtualization platform continues to span the entire project lifecycle.
AIRPORTS AND AVIATION – TWA Hotel and Delta Terminal 4 Headhouse at John F Kennedy (JFK) Airport, Delta Sky Club, and Delta Airlines Headhouse at LaGuardia Airport (LGA).
BASE BUILDING – New York University Mercer Street campus, Alexandria Real Estate Tower, the David H. Koch Center for Cancer Care at Memorial Sloan Kettering, and the Staten Island Mall expansion and solar power project.
COMMERCIAL INTERIORS – Deutsche Bank, LBrands Headquarters Space, NASDAQ MarketSite, and 21st Century Fox.
HEALTHCARE – Staten Island University Hospital, Mount Sinai Health System, New York University Langone Ambulatory Care Center East 53rd Street, and Richmond University Medical Center.
STADIUMS, ARENAS, AND VENUES – Yankee Stadium, Madison Square Garden, David Geffen Hall at the Lincoln Center, and the United States Tennis Association (USTA).
WAREHOUSING AND LOGISTICS – Confidential Project One – a one million square foot (sqft) distribution facility, and Confidential Project Two – a 770,000 sqft premier logistics and last mile distribution center.
•
A new communication strategy has successfully increased stakeholder buy-in in an industry where big data adoption has been slow. This ongoing process has led to a steady stream of business use case requests from project teams aimed at enhancing relationships and deliverables among stakeholders.
As a result, there has been improved real-time visibility, proactive risk mitigation, and a sustained focus on client-centric objectives.
Since its establishment in 2007, Addeo House, founded in a collaborative effort with various other people and organizations, grants and community donations soon poured in with Gina and Lisa as the primary supporters.
The residential project is dedicated to supporting the residents of Staten Island by offering a compassionate,
homelike hospice residence for individuals facing terminal illnesses who can no longer return to their homes.
The facility is designed to provide comfort and dignity, allowing patients
to spend their final days in a nurturing environment surrounded by caring staff and volunteers.
Under the stewardship of Lisa, the company continues to uphold ADCO’s deep-rooted commitment to
ABLE Rigging Contractors provide complete rigging solutions. From planning to coordination with construction management and general contractors, and logistics to implementation, our extensive experience means your next job will be a complete success.
We provide various lifting solutions for a wide variety of industrial and construction applications. Now set to grow even bigger with the addition of Transcope and Farren International.
SPECIALIZING IN:
• Rigging Services
• Mission Critical Systems
• Power Generation
• Substations/Transformers
• Mechanical/HVAC
• Boom Trucks/Cranes/Derricks
• Storage & Warehousing
• Transport & Trucking
1-888-541-0044 | info@ablerigging.com www.ablerigging.com
community service. This encompasses not only the operation of the hospice but also various philanthropic initiatives, including employee giving programs and volunteer opportunities primarily focused on helping children.
• Fifth generation lightning protection specialist
• Established in 1895
• North America’s leader in design, consulting, manufacturing, and new lightning protection technologies
• Dealing in both Faraday and ESE systems
Visit our website: lightningpreventor.com Or call toll free: 1-800-420-6141
VISA/ MASTERCARD ACCEPTED
The company aims to foster a sense of community and responsibility among its employees while making a tangible difference in the lives of those it serves.
Through corporate philanthropy,
ADCO has supported numerous nonprofit leaders and initiatives across various organizations.
These include the March of Dimes, Mercy Home for Children, Jewish Community Centre (JCC), Staten Island Yankees, St. George Theatre, Staten Island University Hospital, Eggers Nursing Home, Catholic Charities, Snug Harbor Cultural Fund, and many local Little League teams.
In addition to an unwavering commitment to philanthropy, ADCO’s ongoing success will leave a lasting legacy in multiple ways, ensuring that it continues to give back to communities, advocate for women in construction, and align with its clients’ vision to maintain the standard of excellence it is known for.
To round off each issue, we ask our contributing business leaders for their views on the same question
What is your favorite thing about your workplace and why?
Josh Delforge
Vice President of Engineering and Operations, Cruisers Yachts
“My favorite thing is the daily challenge to compete in a global industry with such a talented team. With my background in engineering, the design and build process is something that I absolutely love. Each new boat is unique with a new set of design hurdles.”
Bruce Bharat
Country Manager and Vice President of North America, Kamstrup
“The amazing people I get to work with everyday to do something transformative, something
that hasn’t been done in our industry in a very long time, if ever.
“We are working to disrupt and modernize our industry and show utilities that just because it’s always been done ‘one way’, doesn’t mean it has to continue or that it’s better. We are working to show that we truly care about our water utility customers and how they experience Kamstrup end-to-end.
“I am grateful every day for our team members that have decided to join us on this journey. Like most organizations focused on growth, we experience every emotion in our business on our journey.
“It requires resilience, grit, faith, and
determination, and we go through it together. They could choose to be anywhere, but they choose to be at Kamstrup.”
Yusuf Yenilmez
Co-Founder and Managing Partner, Zgemi
“It’s the people. Every day, we work alongside passionate, driven individuals who inspire us. There’s a sense of camaraderie and shared purpose that makes coming to work exciting. And at the heart of it all is the satisfaction of knowing that we’re building something meaningful.”
Stelios Hiotakis
Executive Vice President, Zgemi
“One of the things I like the most is helping others grow professionally, and our team allows me that opportunity. I always say that I believe I’m successful when I render myself useless – what I mean by that is when I know I’ve built someone else to do what I do so I can focus on something different. You motivate people when you’re part of a motivated team.”
Bill Shea
COO, Morris-Shea
“I love the people and the relationships I have with my fellow employees and co-workers, which stems across the company as everyone is treated with the same care.
“You also never know what tomorrow is going to bring, because if you can dream it, we can do it. We bite the bullet and don’t let good ideas pass us by, otherwise you’re never going to have innovation.”
Are you a CEO/Director with a company story to tell? Contact North America Outlook now!
reading
Reaching
To