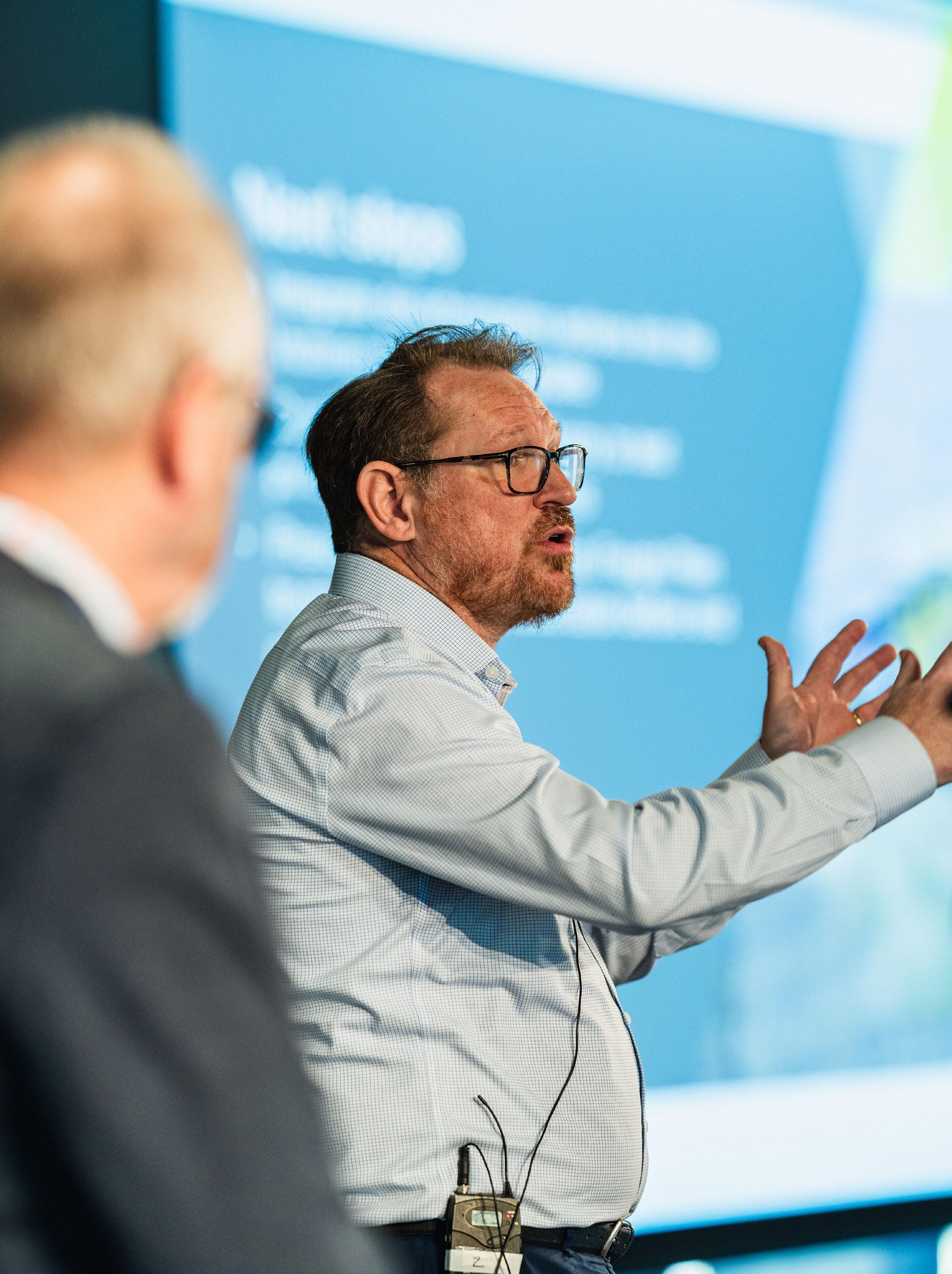
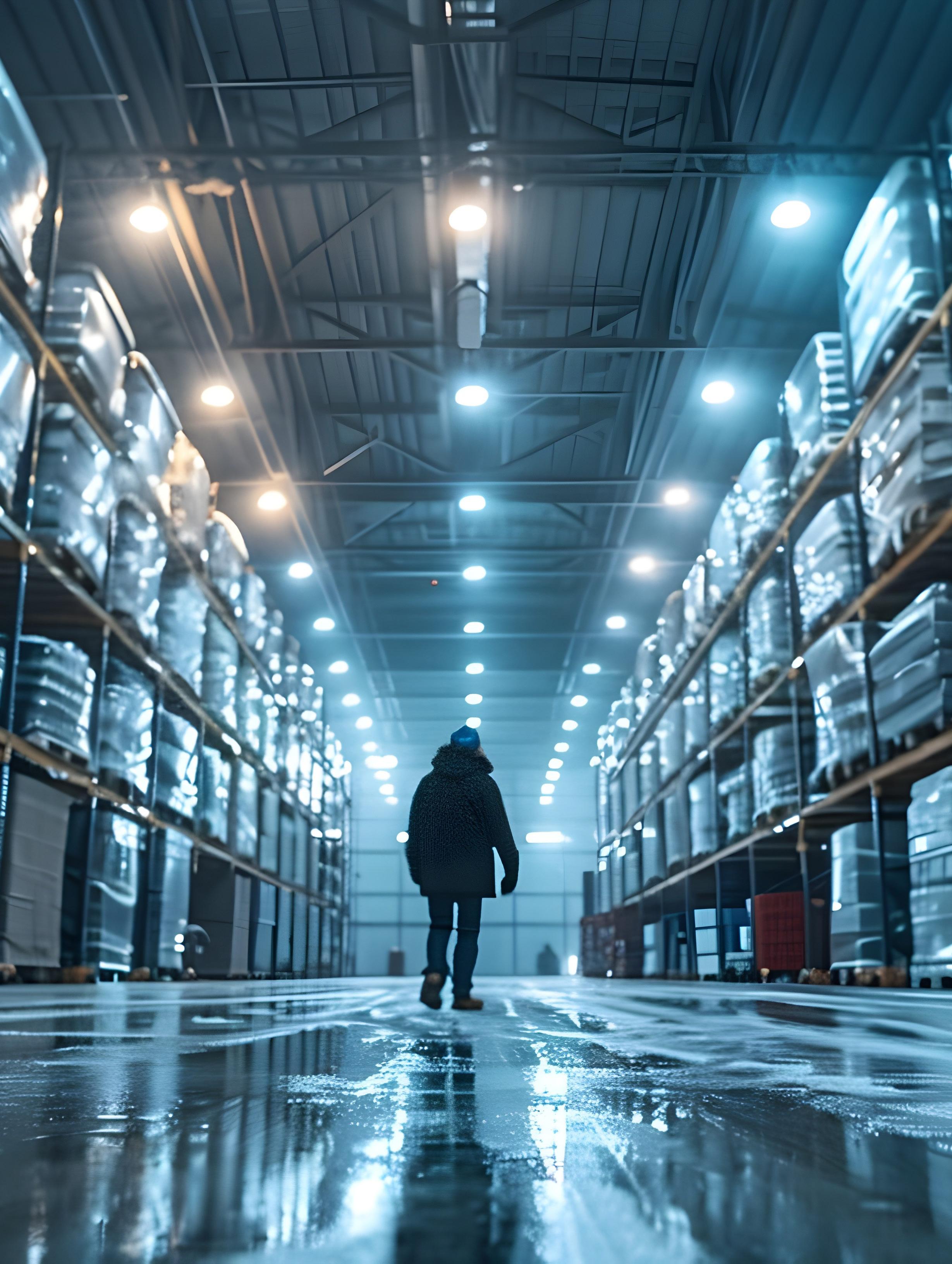
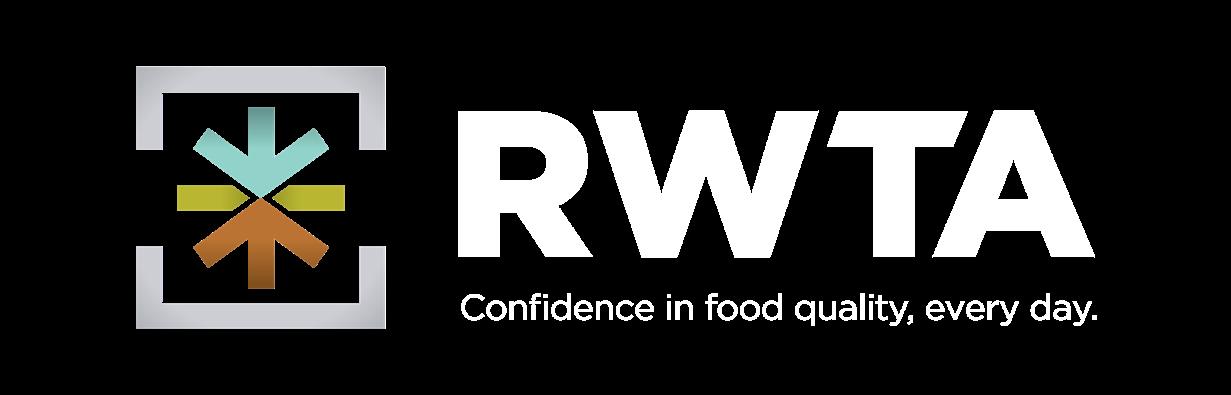


Essential for preserving integrity from point of origin to consumption, the cold chain plays a crucial role in maintaining the quality, safety, and freshness of perishable products throughout Australia
Writer: Jack Salter | Project Manager: Deane Anderton
The Australian cold chain is integral to ensuring that perishable goods are delivered in optimal condition to consumers, fulfilling demands for quality and safety while supporting economic and public health objectives.
A complex system that requires ongoing innovation, strict regulatory compliance, and effective management to
adapt to the challenges of a global market, the cold chain provides controlled temperature environments necessary for preserving these products.
By maintaining specific temperatures, the cold chain ensures that food items such as meat, dairy, fruits, and vegetables remain fresh, retaining their nutritional value and safety until they reach the consumer.
Effective cold chain management also significantly reduces the likelihood of spoilage by inhibiting the growth of pathogenic microbes and slowing the enzymatic breakdown of food products.
This not only helps in reducing food waste, but also ensures economic efficiency by minimising the loss of valuable goods.
By extending the life of perishable products, the cold chain enables producers to reach markets that may have previously been inaccessible due to distance or transit times, opening up new opportunities for growth and expansion for Australian businesses both domestically and internationally.
Products that are well-preserved and maintained through effective cold chain management also often command a higher market value, meaning consumers and businesses are willing to pay a premium for goods that guarantee freshness and safety.
Consistent and reliable cold chain management likewise leads to higher consumer satisfaction, as it ensures products maintain their desired state and quality from the
point of production to the point of sale.
To prevent foodborne illnesses, meanwhile, it is crucial that proper cold chain practices are maintained as many perishable foods can harbour bacteria and other pathogens if they are not stored and transported at correct temperatures.
The Australian cold chain helps to mitigate such risks, contributing to public health and safety in the country.
It equally ensures compliance with strict regulatory standards regarding the transportation and storage of perishable items, particularly food and pharmaceuticals, which are designed to protect consumers and ensure businesses operate within legal requirements.
To futureproof its critical role, the cold chain in Australia is continually evolving with technological advancements such as real-time temperature monitoring, Internet of Things (IoT)-based logistics, and improved refrigeration equipment.
These technologies further enhance the efficiency and reliability of the cold chain, reducing energy consumption and improving environmental sustainability.
Marianne Kintzel, Executive Officer, outlines the vital role of the Refrigerated Warehouse and Transport Association of Australia (RWTA) amid the latest industry developments, such as setpoint temperature changes and booming demand for cold storage facilities
Our purpose is to strengthen and invigorate the Australian cold chain by providing insightful and ethical leadership for our members.
AO: What is your current take on the Australian cold chain? Is it particularly exciting or challenging to work in?
MK: It is a dynamic and exciting industry to be involved in, but not without its challenges. Where there are people, there needs to be effective cold chain processes in place.
APAC Outlook (AO): Firstly, please could you introduce us to RWTA and explain your purpose?
Marianne Kintzel, Executive Officer (MK): RWTA represents the industry sectors involved in the Australian cold chain and looks to meet the increasing demands of Australia through the provision of temperature-controlled warehousing, refrigerated transport, and related essential services.
The cost of energy is forever increasing, sustainability processes need to be implemented, and a skilled labour force requires attention. For instance, Australia is tens of thousands short of skilled truck drivers, and with an average age of 58, it is set to get worse rather than better.
Throughout the COVID-19 pandemic years, the cold chain continued to ensure there was fresh and available food for all. During this time, there was considerable consolidation in the industry to create additional disruption to our sector.
Insurance costs are skyrocketing, so we are investigating
a Discretionary Mutual Fund (DMF) on behalf of the cold chain in Australia and New Zealand (ANZ). RWTA is working to explore if a DMF can reduce property insurance premiums for the cold chain in ANZ.
If adopted, will help to mitigate the problem of increasing premiums for Industrial Special Risk (ISR) policies, which provide cover for physical loss or damage to property and the financial losses incurred.
The cold chain in Australia has its own unique issues but continues to grow and develop, with automation and safety processes a constant focus.
AO: In what ways does RWTA represent both the warehousing and transport sectors involved in the Australian cold chain?
MK: RWTA plays a vital role in representing both the warehousing and transport sectors that are integral to the Australian cold chain.
• Advocacy and policy influence – RWTA acts as a powerful advocate for the interests of the cold storage and transport industries at various levels of government and industry. It engages in lobbying efforts to influence policy decisions that impact the cold chain sector, aiming to shape regulations that support the industry’s growth and operational efficiency.
• Standards and best practices – We promote high standards and best practices within the cold chain industry. It helps develop and disseminate guidelines and protocols that ensure safety, efficiency, and compliance across both the warehousing and transport segments. These standards are crucial for maintaining product integrity and consumer safety.
• Education and training – RWTA provides educational programmes and training resources to enhance the
professional skills of those working within the cold storage and transport sectors. This includes workshops, seminars, and courses on the latest technologies, regulatory requirements, and operational best practices in cold chain management.
• Industry networking and events – The association holds an annual conference, multiple networking events, and a golf day in most states annually that bring together professionals from both the warehousing and transport sectors and provide opportunities to network and do business. These events facilitate knowledge sharing, networking, and collaboration among members, offering opportunities for business development and industry advancement. We’re very excited to be offering access to over 15 functions in 2025, including our annual RWTA Conference, which next year is being held at The Langham, Gold Coast.
• Information dissemination – RWTA plays a key role in gathering and distributing information relevant to the cold chain industry, including market trends, technologies, regulatory changes, and research findings. This information is crucial for businesses to stay competitive and compliant.
• Representation and membership services – RWTA represents a wide range of members, from small operators to large corporations within the cold storage and transport sectors. It offers various membership benefits, including access to industry insights, advocacy on behalf of members, and discounts for services and products.
• Crisis management and support – We provide support and guidance to members during crises that affect the cold chain, such as natural disasters, economic downturns, or regulatory changes. The association
helps coordinate response efforts and communicates with governmental bodies to mitigate impacts on the industry.
• Public relations and awareness – By promoting the critical role of the cold chain in food safety and public health, RWTA helps to raise awareness amongst the public and stakeholders about the importance of refrigerated warehousing and transport. This enhances the sector’s profile and underscores its importance in the global supply chain.
• Innovation and technology adoption – RWTA encourages innovation and the adoption of new technologies to improve the efficiency and sustainability of the cold chain. It supports initiatives and partnerships that explore innovative solutions, such as automated systems, advanced refrigeration technologies, and energy-efficient practices.
Through these activities, RWTA ensures that the warehousing and transport sectors of the Australian cold chain are well supported, professionally managed, and adequately represented, enabling them to effectively meet the demands of a dynamic global market whilst maintaining the highest standards of quality and safety.
AO: Can you tell us more about the change in cold chain set-point temperature from -18°C to -15°C and how this is impacting energy efficiency?
MK: The move to -15°C is a global campaign to change the standard temperature for frozen food from -18°C to -15°C. The campaign aims to reduce greenhouse gas emissions, lower supply chain costs, and secure global food resources. The campaign was launched in 2023 and found that the change in temperature would:
• Save 17.7 million metric tonnes of carbon dioxide (CO2) per year.
• Create energy savings of around 25 terawatt hours (TWh).
• Cut costs in the supply chain by at least five percent and in some areas by up to 12 percent.
AO: What about the development of cold storage facilities and infrastructure across Australia?
MK: There is a booming demand and record rents for Australia’s cold storage facilities. Australia’s cold storage capacity per person is lagging behind the Netherlands, Canada, the UK, and the US, with at least 400,000 square metres (sqm) of new temperature-controlled space required by 2028.
“RWTA PLAYS A VITAL ROLE IN REPRESENTING BOTH THE WAREHOUSING AND TRANSPORT SECTORS THAT ARE INTEGRAL TO THE AUSTRALIAN COLD CHAIN”
–
MARIANNE KINTZEL, EXECUTIVE OFFICER, REFRIGERATED WAREHOUSE AND TRANSPORT ASSOCIATION OF AUSTRALIA
Australia currently has 0.4 cubic metres (cbm) of refrigerated warehouse capacity per urban resident, behind the US at 0.6 cbm and the Netherlands at 0.9 cbm.
To reach US levels would require approximately an additional 400,000 sqm of new warehouse space to be developed in Australia, stretching up to 1.3 million sqm to be in line with the Netherlands.
AO: What was the theme, focus, and aim of the 82nd RWTA Conference that took place in August?
MK: The theme of this year’s RWTA Conference was ‘On Thin Ice, Navigating Australia’s Cold Chain Viability’.
As we confront challenges such as geopolitical unrest, food insecurity and food wastage, environmental changes, regulatory updates, and technological innovations, this theme emphasised the importance of maintaining a robust, strong, and sustainable cold chain operations in our country.
Our aim is to foster dialogue amongst industry leaders, policymakers, and stakeholders to share insights and best
practices. The conference will focus on strategies to ensure we bolster overall supply chain sustainability.
We invited attendees to join us in identifying and addressing the key challenges facing our industry, with a focus on collaborative solutions and innovative approaches.
Together, we can strengthen Australia’s cold chain and ensure its long-term viability.
AO: How successful was the conference in strengthening the Australian cold chain and ensuring its long-term viability?
MK: There were multiple speakers, panels, and tech talks to debate what solutions we can integrate into companies to make the year ahead a success.
These include diversity and inclusion, energy consumption, sustainability, usage of land and space to extend the industry, changing the standard temperature for frozen food to -15°C to save on costs without risking quality and confidence in food quality, maximising labour where there are shortages, and much more!
“WE AIM TO STRENGTHEN THE AUSTRALIAN COLD CHAIN INDUSTRY, ENSURING IT REMAINS ROBUST, COMPLIANT, AND COMPETITIVE IN A RAPIDLY EVOLVING GLOBAL MARKET”
– MARIANNE KINTZEL, EXECUTIVE OFFICER, REFRIGERATED WAREHOUSE AND
ASSOCIATION OF AUSTRALIA
AO: Finally, what are RWTA’s key priorities in order to continue representing the warehousing and transport sectors involved in the Australian cold chain?
MK: RWTA focuses on several key priorities to effectively represent and support the warehousing and transport sectors within the Australian cold chain. These are designed to address the challenges and opportunities in the industry, ensuring sustainability, compliance, and growth. RWTA’s key priorities involve:
• ADVOCACY AND LEGISLATIVE INFLUENCE
Regulatory advocacy – RWTA actively engages with government bodies to influence policies and regulations that affect the cold chain industry. This includes lobbying for favourable legislative changes and ensuring that the industry’s needs are considered in policymaking.
~ Compliance support – Providing members with guidance and resources to navigate complex
TRANSPORT
regulatory landscapes, helping ensure that they remain compliant with current laws and regulations.
• INDUSTRY STANDARDS AND BEST PRACTICES
~ Promoting best practices – RWTA is dedicated to promoting and developing industry standards that ensure safety, efficiency, and sustainability in cold chain operations.
Quality assurance – Encouraging adherence to highquality standards helps maintain product integrity and consumer safety, which are critical for the reputation and reliability of the cold chain industry.
• EDUCATION AND TRAINING
Professional development – Providing ongoing education and training opportunities for industry professionals to help them stay updated with the latest technologies, practices, and regulatory changes.
~ Workforce development – Initiatives to attract, develop, and retain skilled professionals in the cold chain industry, addressing potential skill shortages, and enhancing the workforce capability.
• TECHNOLOGICAL INNOVATION
~ Adoption of new technologies – Supporting the adoption of innovative technologies that improve the efficiency and sustainability of cold chain operations, such as IoT, artificial intelligence (AI), and automation.
R&D – Encouraging research into new methods and technologies that can solve existing challenges in the cold chain sector.
• SUSTAINABILITY AND ENVIRONMENTAL RESPONSIBILITY
Sustainable practices – Promoting environmental sustainability in warehousing and transport operations, including energy efficiency, waste reduction, and the use of eco-friendly materials and processes.
~ Advocacy for green policies – Engaging with policymakers to support the development of green logistics policies that align with global sustainability goals.
• MEMBER SERVICES AND SUPPORT
Network and community building – Facilitating networking opportunities for members to share knowledge, collaborate on common challenges, and foster business relationships.
~ Member benefits – Offering a range of services tailored to the needs of the cold chain industry, such as legal advice, insurance options, and financial services.
• CRISIS MANAGEMENT AND INDUSTRY SUPPORT
~ Emergency response – Developing and coordinating response strategies for industry-wide crises, such as pandemics or natural disasters.
Advocacy for industry support – Working to secure government and financial support for the industry during challenging times.
• PUBLIC AWARENESS AND INDUSTRY IMAGE
~ Promoting industry value – Enhancing public and stakeholder awareness of the vital role that the cold chain plays in the food supply and health sectors.
Positive industry representation – Actively working to improve the public image of the warehousing and transport sectors through outreach and education.
By focusing on these priorities, we aim to strengthen the Australian cold chain industry, ensuring it remains robust, compliant, and competitive in a rapidly evolving global market.
Tel: 0490 799 777 mariannek@rwta.com.au www.rwta.com.au
Somerville Road, Tottenham - cornerstone of Melbourne’s industrial landscape
ABOUT ALIRO GROUP
Aliro Group, established in 2017, is a leading property development, investment, and funds management firm, delivering enduring value across a diverse range of real estate projects. In just a few years, the Group has grown its assets under management to over A$3.31 billion (A$4.41 billion on completion of developments), a clear testament to its capacity to identify and deliver quality, strategic developments. The Group’s impressive track record spans core, core-plus, value-add, and opportunistic strategies, demonstrating their ability to meet the complex needs of large-scale tenants, particularly in the industrial sector.
As businesses strive to adapt to an increasingly complex supply chain environment, the need for intelligent, sustainable, and flexible warehouse spaces has become a pressing issue. While demand for industrial real estate in Melbourne has traditionally been driven by location and capacity, the evolution of business needs calls for a more nuanced approach. Warehousing today is about more than just size and location—it’s about creating spaces that are future-ready, adaptable to technological advancements, and aligned with Occupiers’ sustainability goals.
Jason Blake, Development Director of Victoria at Aliro Group, notes that the key to creating spaces for tomorrow’s supply chains is the ability to anticipate future demands. “What we’re seeing now is a shift towards more flexible, high-tech warehouses that can evolve as businesses grow. It’s not just about providing space; it’s about enabling businesses to adapt quickly to change, whether it’s new technology, changing customer expectations, or evolving as market demand shifts.”
Aliro’s Somerville Road development in Melbourne’s Inner-West Tottenham area stands as an example of how these new demands are shaping the future of logistics, blending strategic location, cutting-edge design, and forwardthinking features.
The industrial real estate sector faces challenges in meeting modern logistics needs while maintaining efficiency, affordability, resilience and environmental concerns. . Traditional warehouse designs, built to meet the needs of a more conventional supply chain model, often struggle to keep pace with the speed of technological and environmental, social and governance changes. Today’s warehouses need to incorporate flexibility, sustainability, and connectivity. These factors must be considered from the ground up.
“Somerville Road is an embodiment of this shift, featuring a range of innovative and sustainable design principles that not only improve operational efficiency but also position the development as a key player in the future of industrial spaces. From advanced logistics facilities to green technologies, Somerville Road is pushing the envelope in modern warehousing,” added Blake.
REDEFINING OPERATIONAL EFFICIENCY
One of the key priorities at Somerville Road was integrating sustainable solutions that meet the operational needs today and anticipate future demands. With features like solar PV systems, electric vehicle (EV) charging stations, and rainwater harvesting systems, the development not only supports current operational requirements but also positions tenants to be at the forefront of eco-conscious logistics practices.
Blake explains, “Sustainability isn’t just a buzzword—it’s an essential aspect of how we need to think about the long-term viability of any development. At Somerville Road, we’ve prioritised green technologies and energy-
ESG is a cornerstone of Aliro’s vision Aliro’s ESG Strategy is to build resilient assets, create places where people can connect and thrive, and operate the business in a responsible and ethical manner. Aliro Group’s core plus industrial vehicle, AGIV (Aliro Group Industrial Vehicle) recently received a Sector Leadership prize and been ranked #1 in its peer group by the Global Real Estate Sustainability Benchmark (GRESB) for 2024. This achievement solidifies AGIV’s position as a leader in sustainable industrial real estate and reflects Aliro’s commitment to embedding ESG excellence in everything they do.
efficient solutions that help reduce environmental impact while improving the bottom line for businesses.”
This integration of eco-friendly features is not just about meeting the growing demand for environmentally responsible real estate but also about making these properties attractive to businesses that see sustainability as a key part of their long-term strategy.
STRATEGIC LOCATION MEETS FUTURE-READY LOGISTICS
Somerville Road’s location, strategically positioned within 10 kilometres from Melbourne’s Central Business District and a major transportation hub, the Port of Melbourne, highlights the growing importance of accessibility in industrial real estate development. The site also provides direct access to major thoroughfares such as the Princes Highway, West Gate Freeway, and Western Ring Road. This prime location makes it an ideal hub for logistics and distribution. In today’s fast-paced supply chains, proximity to key transportation links, infrastructure, and urban centres is crucial for ensuring smooth and efficient operations.
Beyond location, the design of Somerville Road caters to the evolving needs of logistics companies
by incorporating scalable spaces that can adjust to a range of business activities - from last-mile delivery hubs to large-scale distribution centres. THE ROLE OF SUSTAINABILITY IN FUTURE WAREHOUSING
Aliro’s commitment to sustainability is evident in its leadership in ESG practices. The Somerville Road facility exemplifies the company’s dedication to reducing emissions, implementing solar energy systems, and integrating rainwater harvesting. These technologies are becoming essential to future-proof industrial real estate, which is increasingly expected to meet strict sustainability standards.
The importance of sustainable real estate development is growing as businesses face increasing pressure from consumers, regulators, and investors to meet environmental goals.
According to a recent industry report, industrial real estate that incorporates green building certifications and sustainability measures has seen higher occupancy rates and greater tenant retention. As companies seek to meet their own environmental targets, spaces like Somerville Road, with its eco-friendly design and operational capabilities, will become even more valuable.
SHAPING THE FUTURE OF INDUSTRIAL WAREHOUSING: A NEW ERA OF LOGISTICS
As the logistics sector evolves, businesses need spaces that meet both current and future demands. Sustainability, adaptability, and innovation are no longer optional, as illustrated by the Somerville Road development in Melbourne. By integrating green technologies, scalable designs, and future-proof features, this project sets the standard for the future of industrial warehousing.
Daniel Wise, Managing Director & Chief Executive Officer of Aliro Group added, “As we move into 2025, our commitment to Environmental, Social, and Governance (ESG) principles will continue to drive everything we do at Aliro Group. We understand that to create lasting value for our clients and partners, we must go beyond simply meeting market demand. It’s about building sustainable,
Somerville Road Development: Key Facts
Location: 10km from Melbourne’s CBD and 9km to the of Melbourne
of Warehouse 2: 51,230 sqm of Warehouse 3: 22,141 sqm
Clearance: 14.6m ridge height in Warehouse 2
Floor Load: 8-tonne post load floors
Solar Power: 500kW solar system in Warehouse 3
Storage Temperature Range: -25°C to 4°C (Warehouse 3)
Pallet Capacity (Warehouse 3): Up to 30,000 pallets
Truck Access: B-Double access with heavy-duty hardstand
Canopies: 34.5m wide super canopies on Warehouse 2
Aliro Group’s Track Record of high-profile developments
Aliro Group has made significant strides in Australia’s real estate sector. Its progress and development expertise can be seen via the completion of a series of high-profile projects.
MOCO Food Services Facility
As the trusted development partner of ISPT, Aliro recently completed a state-of-the-art facility for MOCO Food Services at the Barracks in Metroplex Estate, Wacol, Queensland. This 18,000 sqm facility, pre-leased for 15 years, features 19 loading docks, a 5,000 sqm freezer, a 2,300 sqm chiller, 4,000 sqm of ambient space, and specialised refrigerated meat processing areas, showcasing Aliro’s ability to deliver tailored solutions for clients.
Elevations at Greystanes
In New South Wales, Aliro celebrated the official opening of Elevations at Greystanes on September 20, 2024. This project has provided over 80,000 sqm of premium industrial space across multiple warehouses since 2021, featuring state-of-the-art facilities, an onsite café, a professional-grade basketball court, and a BBQ area. The development of Warehouse 7, the final warehouse in the estate, is currently underway and is set for completion in March 2025.
Estate
Aliro’s commitment to excellence was further seen with the practical completion of Stage One at Ellison Estate in Geebung, Queensland. This stage encompasses 23,600 sqm across six tenancies within two prime industrial facilities. With tenants like JS Hayes and Applied Medical already secured, Aliro is well-positioned to forge strong partnerships with future tenants. Stage Two, slated for completion in December 2024, will introduce 12 high-exposure showroom units spanning 11,200 sqm.
Chobani Australia Facility
The Chobani Australia facility at 8-22 Quality Drive, Dandenong South, has garnered external attention by being shortlisted for the Best Business or Industrial Park at the 2024 Innovation & Excellence People’s Choice Award. In partnership with Qanstruct, Aliro transformed a former vehicle parts warehouse into Chobani’s national head office, featuring a fully refurbished 10,986 sqm storage warehouse and a newly constructed 9,500 sqm temperature-controlled facility.
TripleTwoNine Project
The TripleTwoNine project in Caringbah, NSW, underscores Aliro’s ability to refurbish and reposition existing properties. The 27,000sqm warehouse, originally built in the 1980s, was transformed into a prime grade industrial facility with sustainability upgrades, including a 300KW solar array and comprehensive EV charging provisions. This project achieved a 5 Star Green Star Design & As-Built rating and secured major tenants like Australia Post and Woolworths, showcasing Aliro’s commitment to delivering high-quality, sustainable real estate solutions.
adaptable developments like Somerville Road, which not only deliver operational efficiency but also ensure long-term, responsible growth.”
The shift in industrial real estate extends beyond Somerville Road. As digitalisation and environmental goals reshape the sector, businesses must invest in spaces that evolve with these changes. The Somerville Road
development exemplifies Aliro’s expertise in meeting the evolving demands for flexible, highquality industrial spaces.
To explore how Aliro Group can help your business find future-ready spaces or to learn more about our innovative projects, contact us today. Together, we can shape the logistics solutions of tomorrow.
Industrial & Logistics | For Lease
CBRE Asia Pacific, on behalf of Aliro, is excited to exclusively present for lease Warehouse 2, 427-451 Somerville Road, Tottenham. Available from Q2 2025.
Warehouse 2A
+ Total Building Area: 9,455sqm*
+ Warehouse Area: 9,015sqm*
+ Office Area: 440sqm*
+ 10,500* Pallet Capacity
Warehouse 2B
+ Total Building Area: 16,480sqm*
+ Warehouse Area: 15,940sqm*
+ Office Area: 540sqm*
+ 23,320* Pallet Capacity
Key Property Features Include:
+14.6m* high warehouse clearance
+34.5m* super canopies
+Multiple on-grade roller shutters and recessed docks
+8 tonne post load floors
Warehouse 2C
+ Total Building Area: 11,410sqm*
+ Warehouse Area: 10,870sqm*
+ Office Area: 540sqm*
+ 16,150* Pallet Capacity
Warehouse 2D
+ Total Building Area: 13,885sqm*
+ Warehouse Area: 13,345sqm*
+ Office Area: 540sqm*
+ 19,450* Pallet Capacity
+Targeting 5-star Green Star accreditation
+Significant solar array
+Heavy duty hardstand
+Flexibility to combine tenancies into larger sizes
&
CBRE Asia Pacific, on behalf of Aliro, is excited to exclusively present for lease Cold Store, 427-451 Somerville Road, Tottenham. Available from Q4 2025.
Key Property Features Include:
+Total Building Area: 22,040sqm*
+Warehouse Area: 21,295sqm*
+Office & Staff Amenities Area: 745sqm*
+Cold Store Area: 20,315sqm*
+Four (4) cold storage chambers (-25°C to 4°C), each averaging 3,800sqm*
+12.3m* high clearance warehouse/office facility
+Flexibility to accommodate single or dual users
+Designated separate entry and exit points for cars and trucks
+Targeting 5-star Green Star accreditation
+500kw solar array
+30,000* pallet capacity
+10m* cantilever awning for all-weather loading
+40m* hardstand and 22 recessed docks
Tom Hayes
Industrial & Logistics
Senior Director
+61 413 997 703
tom.hayes@cbre.com.au
Harry Kalaitzis Industrial & Logistics Senior Director
+61 409 994 419
harry.kalaitzis@cbre.com.au
Tom Murphy
& Logistics State Director
+61 434 414 901
tom.murphy@cbre.com.au