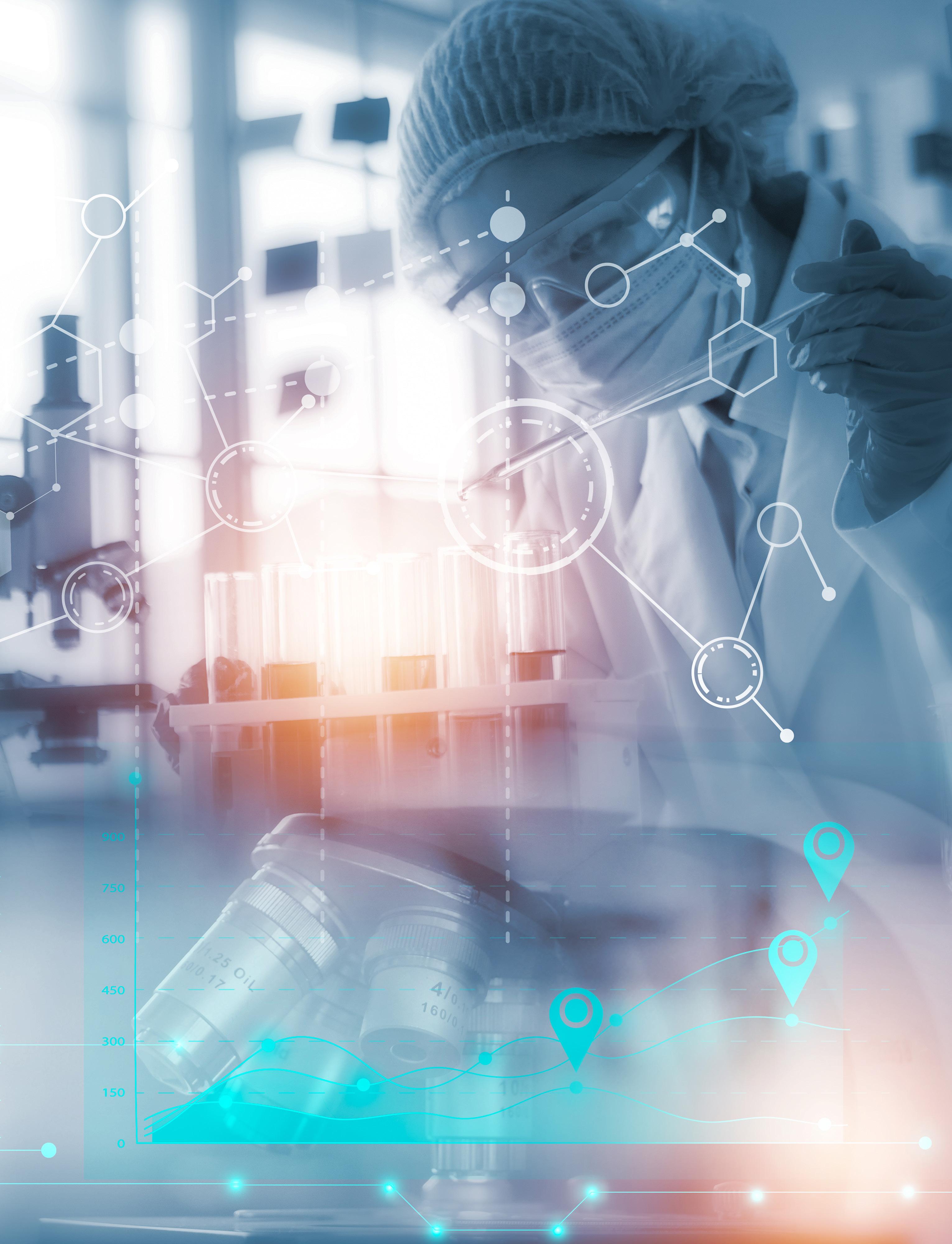
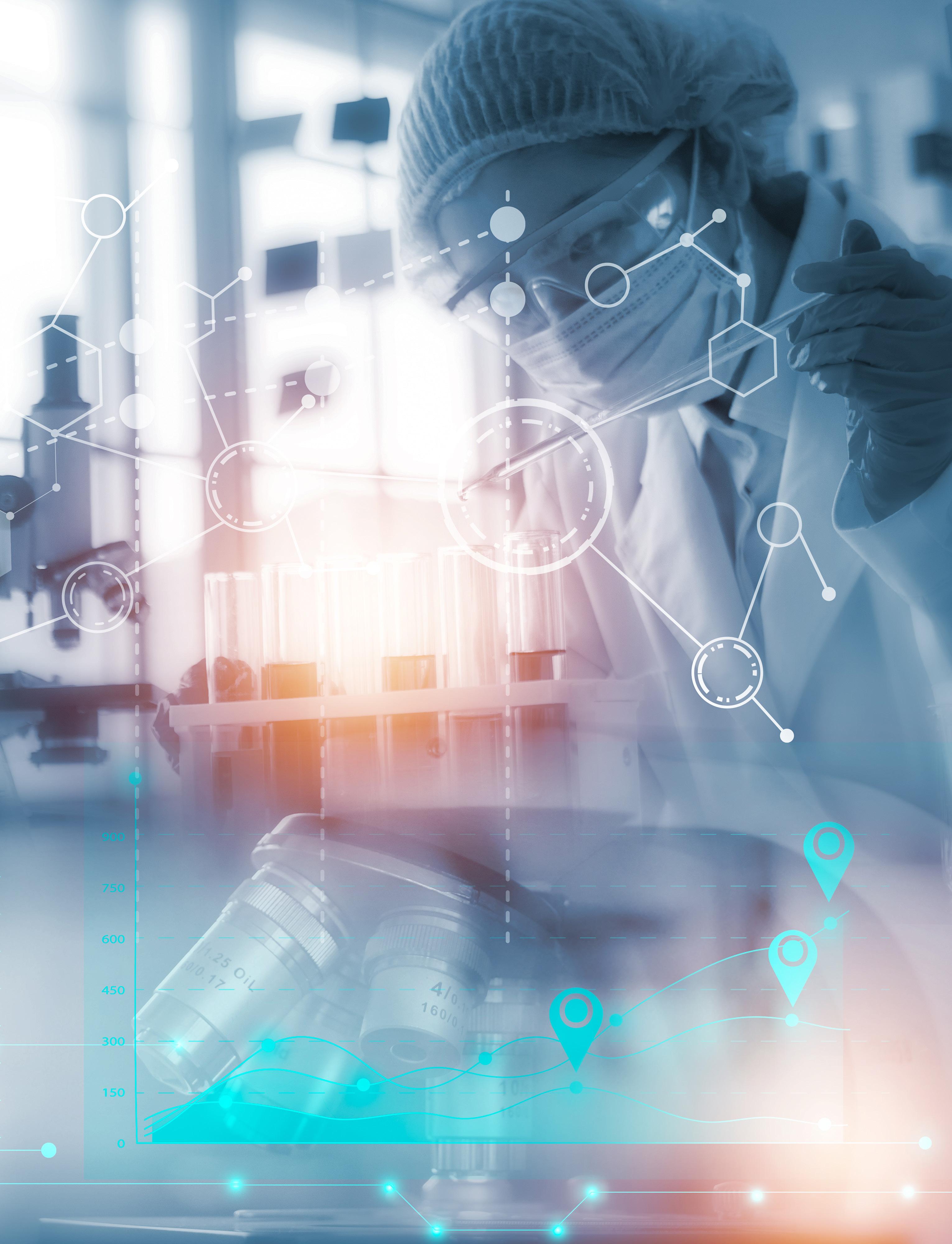
Founded in 2005, Sypharma has grown to become a trusted contract, development, and manufacturing organisation (CDMO), intelligently connecting cutting-edge insights, technology, and expertise to bring extraordinary solutions to healthcare.
“Our mission is to be an innovative and leading Australian company respected for continually creating outcomes that make a difference and enhance lives,” introduces Ganeshan Varnakulasingham, CEO.
Indeed, the company holds a longstanding reputation in the nation’s animal health arena for delivering unparalleled products.
“Given our strong position in the milk fever space, with prevalence in Australia ranging from 10 to 15 percent in any given year, the impact of not having Sypharma’s support would have a direct effect on the dairy industry,” he highlights.
The company’s many reputable solutions have a considerable
Emerging at the forefront of Australian animal healthcare, Sypharma’s unmatched industry knowledge and state-of-theart manufacturing solutions help address critical supply chain gaps. CEO, Ganeshan Varnakulasingham, tells us more
Writer: Lucy Pilgrim Project Manager: Cameron Lawrence
economic impact, including the manufacturing of critical care intravenous fluid (IV) for animal hydration therapy, of which Sypharma is estimated to have an 80 percent market share, positioning it as a key sterile IV partner.
The company’s other business operating units include sterile human health and custom-made buffers as well as Clean In Place (CIP) solutions.
Regarding the former, it manufactures, under contract, investigational medical products (IMPs) for the clinical supply chain, including treatments for rare conditions and vaccines in humans.
Sypharma’s human healthcare products are a key differentiator within the Australian market, as it utilises a molecule incubator model to develop products throughout their lifecycle without retaining the products’ intellectual property (IP). Any subsequent IP generated is given directly to clients, which include startups and primary investigators.
The company additionally produces
good manufacturing practice (GMP)grade excipients, cleaning solutions, and buffers for the manufacturing of pharmaceutical products.
“This is the fastest-growing business segment for Sypharma, and we have a huge value proposition as the only manufacturer of these products in Australia that holds a Therapeutic Goods Administration (TGA) license,” Mr. Varnakulasingham proudly informs.
The Australian healthcare industry is currently experiencing a shortage of IV fluids, namely sodium chloride 0.9 percent and sodium lactate solutions. This challenge is being attributed to global supply limitations, unexpected demand increases, and manufacturing issues, with the TGA anticipating that these shortages will persist in 2025.
In response to the disruption, the government has approved the importation of overseas registered
IV fluids and is coordinating efficient distribution to manage the situation.
As it stands, the only manufacturer of critical care fluids in Australia is Baxter Healthcare, who produces approximately 75 percent of the Australian market’s saline products
that permeate the animal healthcare space.
“Due to quality and manufacturing issues, Baxter Healthcare stopped supply into the animal health market, affecting veterinary clinics nationally,” Mr. Varnakulasingham reveals.
By choosing to work at the company, employees have a chance to do something good, work for a purpose, experience personal growth through professional integrity, and be part of a community.
Boasting a senior team with over 150 years of combined experience in GMP manufacturing, Sypharma is dedicated to being a smart, ethical company that clients can trust and respect.
Sypharma is also committed to transparent communication between the senior leadership team, line managers, and operators, ensuring the whole workforce has a clear understanding of the business direction.
On top of this, the company promotes work-life balance through hybrid working arrangements where suitable and conducts regular employee surveys to understand areas for improvement.
How to streamline small batch production and commercialization with adaptiQ®.
Ready-to-use pharmaceutical glass vials for injectables
That is why SCHOTT Pharma designs solutions grounded in science to ensure that medications are safe and easy to use for people around the world. The portfolio comprises drug containment solutions and delivery systems for injectable drugs ranging from prefillable glass and polymer syringes to cartridges, vials, and ampoules.
Further information at: www.schott-pharma.com/small-batch-packaging-solutions
As a result, Sypharma has been able to increase its operational capacity tenfold as the only other manufacturer of animal health products, resulting in its recent flurry of IV production.
Meeting the new demands of veterinary health clinics, the company now anticipates holding 70 percent of the animal health market and has signed long-term distribution agreements to maintain its increased market share for years to come.
“The industry has been supportive of Sypharma proactively marketing the products to veterinary clinics,” he states.
The company’s ability to meet this demand is supported by its recent AUD$10 million investment in the upgrade of its IV manufacturing plant.
This will completely automate the production of IV fluids, and the company is expecting to sell the line’s first commercial products by the end of Q1 2025.
In the next 12 months, Sypharma is looking to technology transfer two platform technologies specifically related to the manufacturing of investigational medical products, including mRNA manufacturing platforms.
“Sypharma has a business partner that has developed its own end-toend manufacturing platform, which will be transferred to the company in 2025,” details Mr. Varnakulasingham.
Sypharma recently decided to transfer its manufacturing supply chain back to Australia, a decision that was made based on eight key principles:
INCREASED GDP – Local manufacturing contributes to the national economy.
SUPPLY CHAIN RESILIENCE – Domestic production reduces reliance on international suppliers, mitigating risks from global disruptions.
DIRECT EMPLOYMENT – Onshoring creates jobs in manufacturing facilities.
INDIRECT EMPLOYMENT – Stimulates jobs in supporting industries.
UPSKILLING THE WORKFORCE – Onshoring encourages investment in local training programmes and apprenticeships.
STEM OPPORTUNITIES – High-tech manufacturing industries often require expertise in STEM, driving innovation and education.
BOOSTING REGIONAL ECONOMIES – Establishing manufacturing plants in less-developed or rural areas reduces urban migration and promotes regional economic growth.
INFRASTRUCTURE DEVELOPMENT – Local manufacturing projects often lead to improved infrastructure.
5. ENHANCED INNOVATION
COLLABORATION WITH LOCAL R&D – Proximity to Australian universities and research institutes can foster innovation.
TECHNOLOGY ADOPTION – Onshoring encourages the adoption of advanced manufacturing technologies.
6. SOCIETAL BENEFITS
COMMUNITY EMPOWERMENT – Manufacturing jobs are often the source of a stable income, bettering employees’ quality of life.
SOCIAL EQUITY – Onshoring provides opportunities for underrepresented groups to participate in the workforce.
7. ENVIRONMENTAL AND ETHICAL BENEFITS
SUSTAINABILITY – Local production adheres to stricter Australian environmental regulations.
ETHICAL STANDARDS – Manufacturing in Australia ensures compliance with fair labour practices and safety standards.
8. STRATEGIC ADVANTAGES
NATIONAL SECURITY – Domestic manufacturing reduces dependency on foreign resources for critical goods.
EXPORT POTENTIAL – Strengthened manufacturing capabilities can position the country as an exporter of high-quality, locally-made goods.
“This will make Sypharma one of two GMP manufacturers able to manufacture mRNA therapeutics.”
Meanwhile, the company is also technology transferring a synthetic artificial pharmaceutical ingredient (API) manufacturing required for anti-infectives against bacteria and viruses, which is being specifically designed to work against antibioticresistant bacteria.
The platform is a proprietary product whose integrated kanban system (IKS) is owned by another of the company’s business partners.
The total technology transfer of the two platforms is expected to reach completion by the end of Q1/Q2 2025.
Elsewhere, Sypharma is also working to reduce supply time for IV bags, which are currently one of the company’s biggest expenditures as they must be imported from Asia and Europe.
This represents a high-risk component for the business as the IV bags are used in the manufacture of critical care products but take up to 12 weeks to procure.
Sypharma is therefore currently in discussions with local manufacturers that it could partner with to reduce the risk of stock shortages.
Sypharma foresees a bright future with four key areas of therapeutic focus.
Firstly, the company will utilise its facility expansion to increase the supply of electrolytes to the Australian animal market.
Indeed, the AUD$10 million upgrade to its IV facility has increased its manufacturing facility by 40 percent, allowing the company to overcome previous capacity challenges and positively address supply issues.
Additionally, Sypharma is also placing greater focus on injectable excipients, which is the company’s fastest growing business unit.
“There is a need within the
“SYPHARMA IS IN A UNIQUE POSITION AS WE HAVE REGULATORY APPROVALS FOR BOTH HUMAN AND ANIMAL HEALTH, MAKING OUR REACH TO VARIOUS RESEARCHERS WIDE”
– GANESHAN VARNAKULASINGHAM, CEO, SYPHARMA
Australian market for local manufacturers who can make these types of products to the grade required to be used as excipients in the manufacturing of drug products,” notes Mr. Varnakulasingham.
There are currently no manufacturers in the country catering to this demand, with the majority of supply being imported from Europe or North America.
Thus, by leveraging the advantages of its TGA license, the company can produce these products according to the custom needs of pharmaceutical manufacturers.
Elsewhere, Sypharma also endeavours to implement further downstream processing capabilities in liquid nanoparticle (LNP) encapsulation for RNA products.
This is the company’s key innovation project, which will contribute towards the creation of an end-to-end contract manufacturing organisation (CMO) hub for RNA therapies with its business partners.
“Sypharma is in a unique position as we have regulatory approvals for both human and animal health, making our reach to various researchers wide,” he concludes.
Finally, the company’s focus remains on maintaining the continuous supply of its milk fever products, whilst innovating for the market with new solutions.
Tel: +61 39706 4914 info@sypharma.com.au www.sypharma.com.au