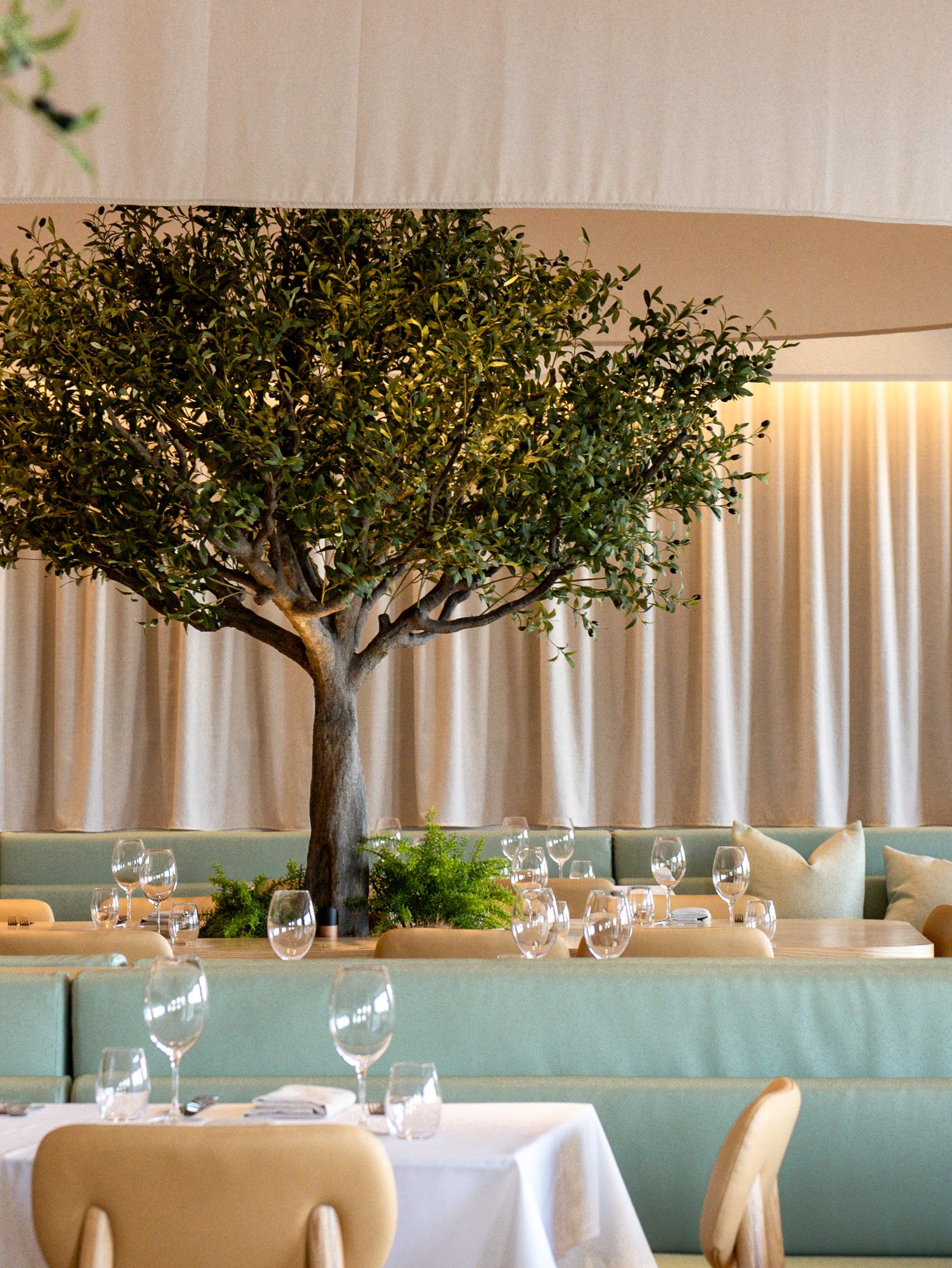
DESIGNED AND REFINED TO PERFECTION
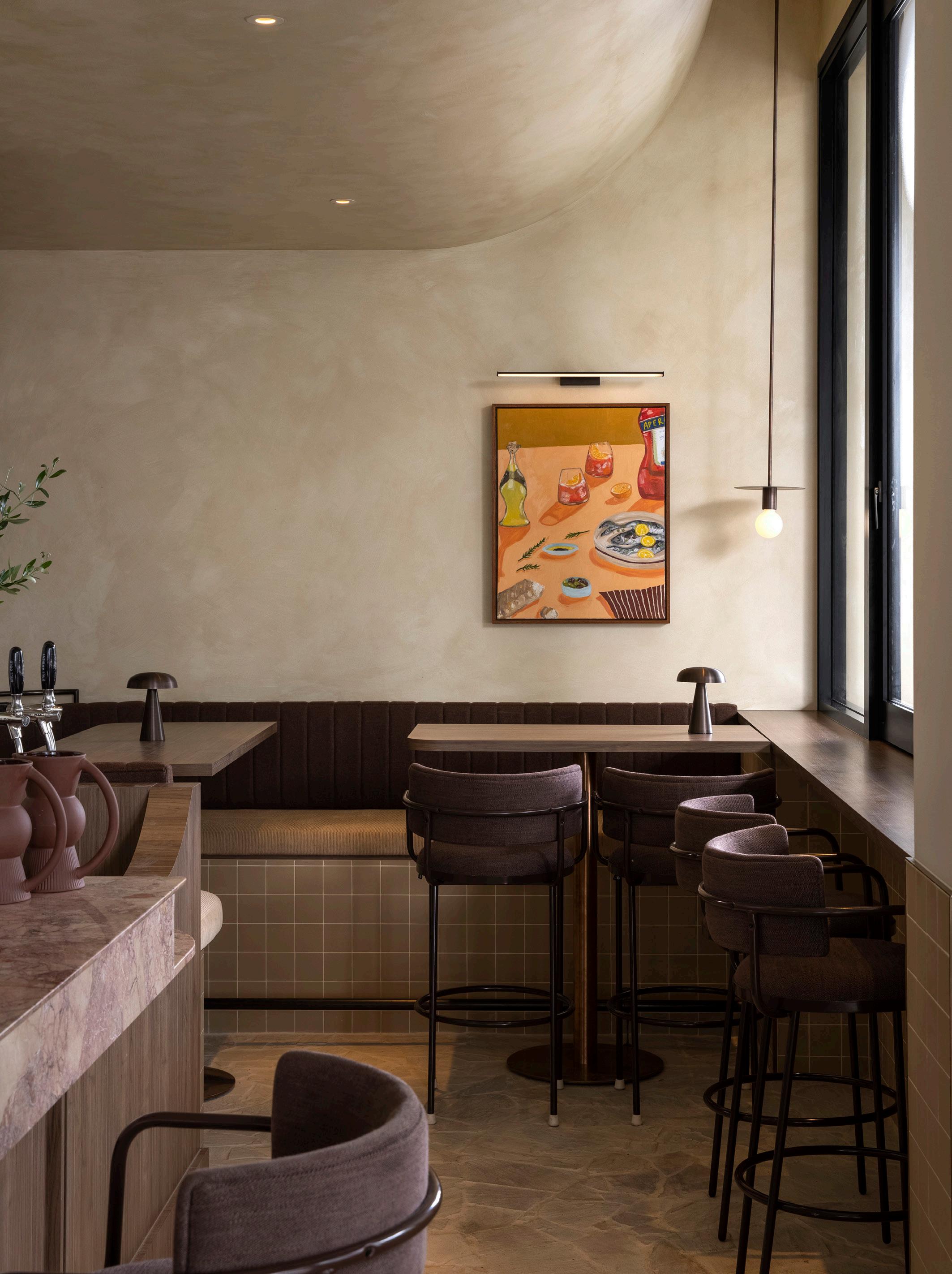
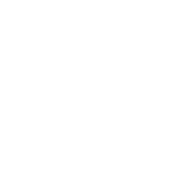
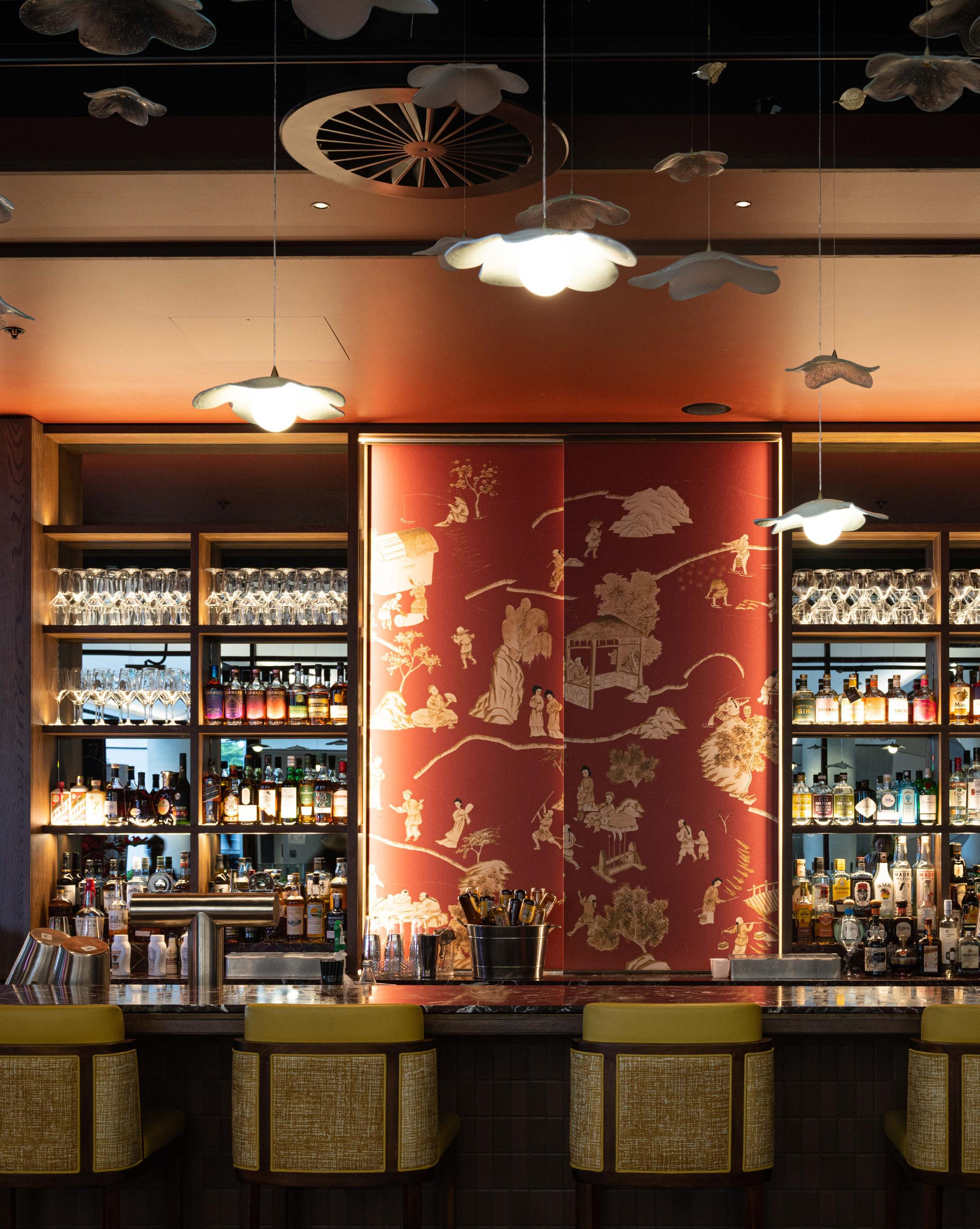

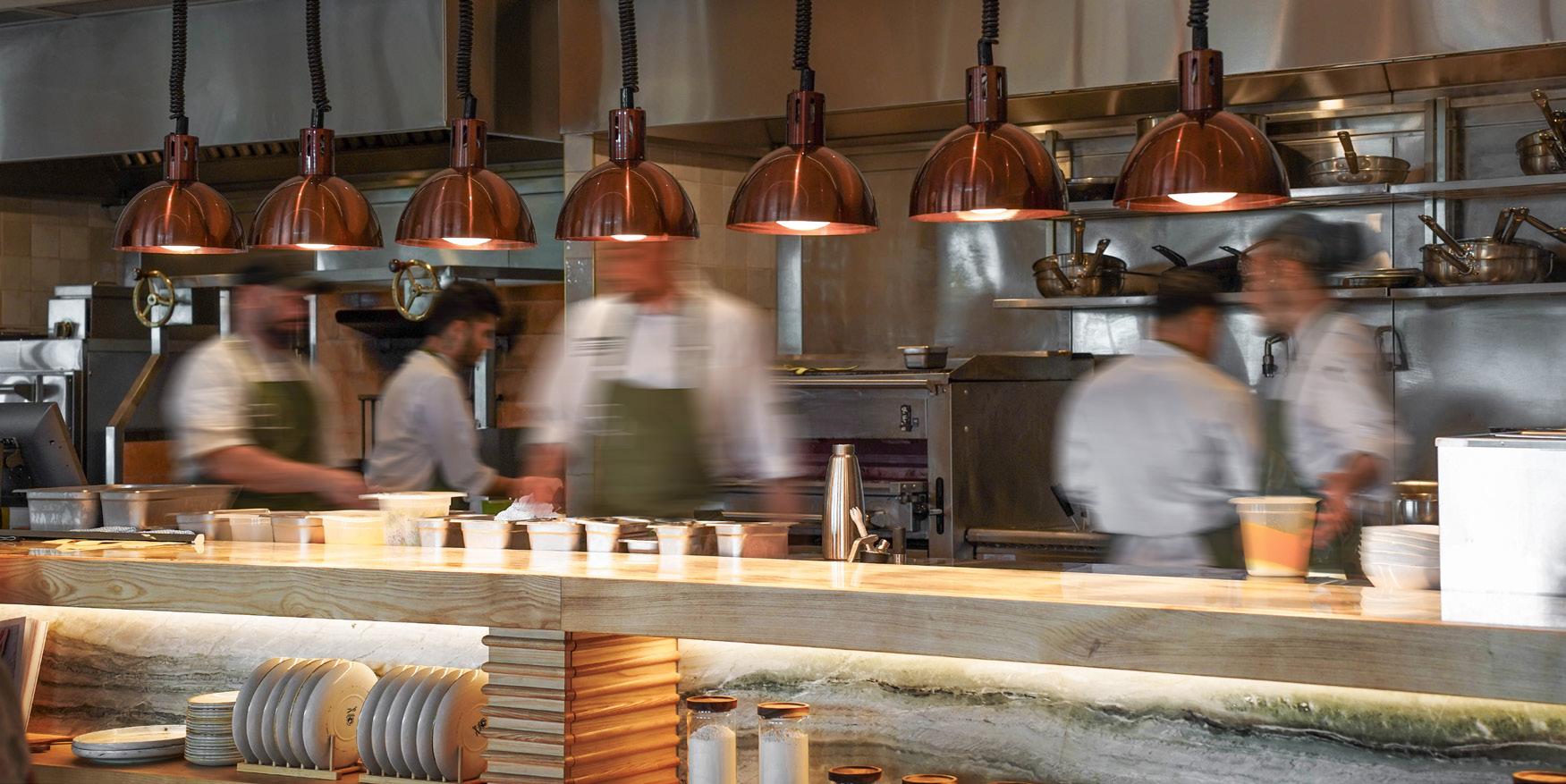
Redefining the possibilities within bespoke construction, Unita specialises in design, fit-outs, and refurbishments for the workplace, retail, hospitality, hotel, fitness, and health sectors. We talk to COO, Matt Lane, about the power of transforming spaces and the company’s burgeoning portfolio of projects
Writer: Ed Budds | Project Manager: Ben Weaver
Since Unita first opened its doors, the company has been driven by its overarching mandate – ‘built better together’.
A respected market leader in the Australian construction industry for over two decades, Unita’s dedicated team of experts work as one across multiple disciplines to build better businesses for its numerous clients.
“It’s an exciting time to be involved in the construction sector, but also a defining one. The industry is evolving fast, expectations are higher, timelines are tighter, and clients want more certainty,” introduces COO, Matt Lane.
“The biggest trend we are currently witnessing is integration. Companies that bring design, manufacturing, and construction under one roof are the ones staying ahead,” he insights.
As such, more businesses now recognise the value of spaces that truly reflect their brand.
Fit-outs, the process of making an interior space ready for occupation, are no longer just about functionality but creating experiences that connect with people, and these undertakings represent a significant portion of Unita’s portfolio of work.
Unita now proudly delivers projects all over Australia and New Zealand and has expanded its team to 150 members.
Alongside, the company has offices in Sydney, Brisbane, Melbourne, and Perth, as well as utilising satellite teams that operate in Tasmania, South Australia, and across New Zealand.
“We craft bespoke spaces that bring brands to life. That means handling everything from design and manufacturing to the build and fit-out process,” Lane sets out.
“Our expertise spans the hospitality, retail, workplace, entertainment, fitness, and health sectors, and we work with brands that want more than just a functional layout – they want a space that reflects their identity, enhances customer experience, and delivers long-term success.”
Uniquely, Unita has developed its own in-house manufacturing facility and global procurement arm.
This now enables the company to produce quality bespoke joinery, furniture, and custom stainless steel locally and with faster turnaround times.
“By controlling the supply chain, including offshore procurement, goods management, logistics, and manufacturing, we’re able to deliver seamless build experiences and save time and money for our clients,” he expands.
It’s all about control and flexibility for Unita, whose newly established in-house manufacturing capabilities ensure quality is never compromised.
“With global procurement, we source the best materials at the best value, which means we’re not waiting on third parties and avoid unnecessary delays and cost blowouts. Clients get a streamlined experience with faster delivery, better pricing, and a higher standard of finish,” explains Lane.
Regularly recognised for the quality of its work, Unita remains committed to a core set of values which promote collaboration, integrity, and, above all else, great service.
In an increasingly saturated market, construction companies such as Unita must work harder than ever to ensure they stand out from the vast swathes of industry competitors.
“BECAUSE WE CONTROL THE ENTIRE PROCESS, FROM GLOBAL PROCUREMENT TO IN-HOUSE MANUFACTURING, WE DELIVER PROJECTS FASTER, MORE EFFICIENTLY, AND WITH AN UNMATCHED LEVEL OF QUALITY”
– MATT LANE, COO, UNITA
Firstly, can you outline Arcular’s experience and expertise as an outsourced joinery supplier?
When we founded Arcular in 2011, we envisioned bringing world-class joinery craftsmanship to clients globally without the typical headaches of overseas manufacturing. That vision has grown into what we are today.
Our journey has led us to establish two state-of-the-art manufacturing facilities in China – a 20,000 square meter factory in Guangzhou and an impressive 100,000 square meter facility in Shandong. What truly sets us apart, though, is our team of over 1,000 master craftspeople who pour their expertise and passion into every piece we create.
We’ve intentionally built local offices and partnerships in multiple countries because we understand clients’ concerns about overseas joinery. This approach allows us to provide a truly end-to-end service, delivering joinery that meets quality expectations and budget requirements. We can source complementary products, so clients receive 80-90 percent of their store needs in a single container, guarantee delivery dates with local support, and, most importantly, take full responsibility when challenges arise. Creating bespoke, oneof-a-kind pieces sometimes means encountering unexpected issues, but our commitment is unwavering – we stand behind our work and resolve any problems promptly.
What extensive range of clients do you work with, and which sectors and countries do you create projects with them in?
We create joinery for the world, supporting clients in all industries.
Some of our recent projects include:
• Retail and Fashion (Fred, Cartier, Adidas, Zegna, David Jones, etc.)
• Medical/Healthcare (Bupa, Health 2000, Lifestyle Nutrition, etc.)
• Hospitality (ST. ALi, Dark Sheppard, Flying Tigress, etc)
• Office/Showrooms (Hoyts, H&R Block,)
• You can find more examples of our work at www.arcular.com.au
How does Arcular combine in-house insights with detailed studies of global shop fitting trends?
We are fortunate to be able to build for clients from all around the world. This enables us to see trends as they emerge from different regions, allowing us to share this knowledge with clients from other parts of the world.
We have found that more brands, builders, and architects are looking to go direct as their confidence in overseas quality increases. By going overseas, they have an increased budget to spend on better materials, including the research and development of new ones.
At Arcular, we love investing in R&D with our partners and working together to develop spaces that have never been done before and wow those who interact with it.
What enables you to deliver joinery and shop fittings of the highest quality whilst ensuring both luxury and financial viability for clients?
We have most of the trades required for an in-house project. This includes metal, wood, stone, painting (powder coat and 2pac), etc. This means that the project isn’t broken up between multiple suppliers, and we are able to give our clients a factory finish on all their joinery.
To ensure quality, we pre-build all orders prior to shipping so that our clients can inspect them before ensuring that all their expectations are met. We welcome all clients and potential clients to visit our factory and see the quality and craftsmanship that goes into every piece.
Whilst we always prioritise quality, we regularly work with customers to value engineer their projects so that they can hit their budgets.
An example would be when we worked with a high-end perfume brand that uses a lot of solid wood carvings. These were heavy and expensive. We helped them develop a new method by combining injection moulding with wood printing to allow them to create a solution that was lightweight, cheaper and hard to discern with the naked eye.
Why else do clients choose Arcular’s comprehensive one-stop service, and what are the advantages of doing so?
In today’s competitive marketplace, our clients choose Arcular for one fundamental reason: we transform complexity into simplicity.
Arcular’s comprehensive approach eliminates these concerns through a single point of accountability. We handle everything: material sourcing, quality control, international shipping, customs clearance, and installation coordination. This integration doesn’t just streamline communication – it fundamentally transforms the client experience.
We believe great partnerships begin with a conversation about your specific challenges and objectives. Whether planning a single flagship location or a multi-store rollout, we invite you to discover how Arcular’s integrated approach can deliver exceptional results while simplifying your process.
Contact us to explore how we can transform your next joinery project into a seamless experience from concept to completion.
“It comes down to understanding, innovation, and execution; we take the time to truly understand our clients, their needs, and their goals–to create tailored spaces that unlock value and amplify success,” Lane tells us.
“Because we control the entire
process, from global procurement to in-house manufacturing, we deliver projects faster, more efficiently, and with an unmatched level of quality,” he prides.
‘Built better together’ is not just Unita’s mantra but the foundation of how it works, as the company firmly
believes that the best spaces come from deep collaboration between its team, clients, and partners.
“Transparency is key. We work closely with clients at every stage, ensuring they’re involved, informed, and confident that their vision is coming to life exactly as planned.”
At present, Unita has some incredible projects in development across its vast and impressive portfolio that showcase the breadth of its capabilities.
“Our work on the Total Fusion Chermside expansion project is a
great example of how we create spaces that enhance both experience and functionality. It’s more than a gym fit-out – it’s a wellness space designed to inspire and support people in their fitness and health journeys,” Lane enthuses.
Elsewhere, at Queen’s Wharf, the company has brought four high-end restaurants to life, helping shape one of Brisbane’s most exciting new precincts.
It was a project that demanded precision, collaboration, and the ability to deliver at scale whilst maintaining the character and individuality of each venue.
“We’re also working with the Australian fashion label Sabo Skirt, rolling out new stores in Sydney that capture their brand’s evolution and provide customers with a seamless, elevated shopping experience,” he follows up.
HOSPITALITY – For two decades, Unita has delivered over 2,500 hospitality fit-outs for top local and global brands. From cafés to sleek restaurant designs and vibrant pubs or clubs, the company handles every detail to create spaces that don’t just look great but feel unforgettable.
RETAIL – Unita brings an exceptional legacy in retail projects, having successfully constructed over 4,000 retail stores. Its expertise in creating remarkable in-store experiences sets the company apart as an industry leader with a comprehensive range of meticulous design and construct services.
WORKPLACE –The company specialises in delivering impressive large-scale office projects. From the initial planning and strategy stages through to completion, the company oversees every aspect.
HOTEL AND LEISURE – With an enviable track record, Unita stands as a trusted leader in delivering long-lasting solutions in the hotel and leisure sector. From creating captivating accommodation and entertainment precincts to crafting vibrant social hubs and leisure destinations, its diverse portfolio showcases a wealth of expertise.
MEDICAL AND WELLNESS – Unita has delivered award-winning results for many of Australia’s most well-respected health brands. This includes projects in medical centres, gyms, dental practices, and aged care facilities.
“Beyond this, we’ve got some very exciting flagship stores in the works across the country that will set new benchmarks for retail design. These projects are pushing boundaries in both aesthetics and functionality.”
Unita cares deeply about the preservation and conservation of the environment and remains passionate about creating a better future for the planet and the community in which it lives and works.
“Through our environmental management system (EMS), we are committed to continually improving our credentials and reducing our impact on the Earth,” Lane elaborates.
“By championing a team culture that values environmental principles and seeks sustainable alternatives, we ensure every project we complete adheres to current legislation and transcends industry best practices,” he adds.
Sustainability is factored into every process at Unita, whose EMS helps minimise waste, reduce energy consumption, and ensure materials are responsibly sourced.
“We create spaces that are
“TRANSPARENCY IS KEY. WE WORK CLOSELY WITH CLIENTS AT EVERY STAGE, ENSURING THEY’RE INVOLVED, INFORMED, AND CONFIDENT THAT THEIR VISION IS COMING TO LIFE EXACTLY AS PLANNED”
– MATT LANE, COO, UNITA
future-proofed, ethical, and environmentally responsible,” Lane ensures.
Working together, Unita believes it can help determine a range of expansion objectives for its clients, identify market opportunities, prepare schedules and timelines, and support its partners in growing their business into a national brand.
“Once the development phase is completed, our team works to ensure every stage of a project runs smoothly and consistently across all sites, from planning through to construction,” Lane excites.
Moving forward, growth is a priority for Unita, but the company resolutely maintains that it must be meaningful.
“We’re expanding to offer even greater capability, investing in innovation, and refining how we
deliver value. Every step we take is about creating high-quality spaces that not only meet client expectations but exceed them,” he qualifies.
In this way, Unita ensures the brand’s uniqueness is reflected and its long-term success is supported in every new project.
“Our creations are experiences that influence people, shape brands, and drive success. That’s what we do at Unita – create environments that work, inspire, and grow with the businesses they house,” Lane concludes proudly.
Ausglobe Logistics is an independently owned Australian company that focuses on tailoring its logistics solutions to its customers needs, through complex practices of managing their import/export processes and their International Freight and Landside Logistic requirements.
Our current in house capabilities include:
1. International freight forwarding, door-door (Air/Sea Import and Export)
2. Project Logistics
3. Licenced customs brokers (Corporate and Individual)
4. Licenced Biosecurity accreditation class 19.1 and class 19.2
5. Biosecurity Approved Arrangement class 1.3
6. HAACP approval
7. In house transport, tail lift, sensitive freight and de-crating
8. Pick / pack / 3pl warehousing and inventory reporting