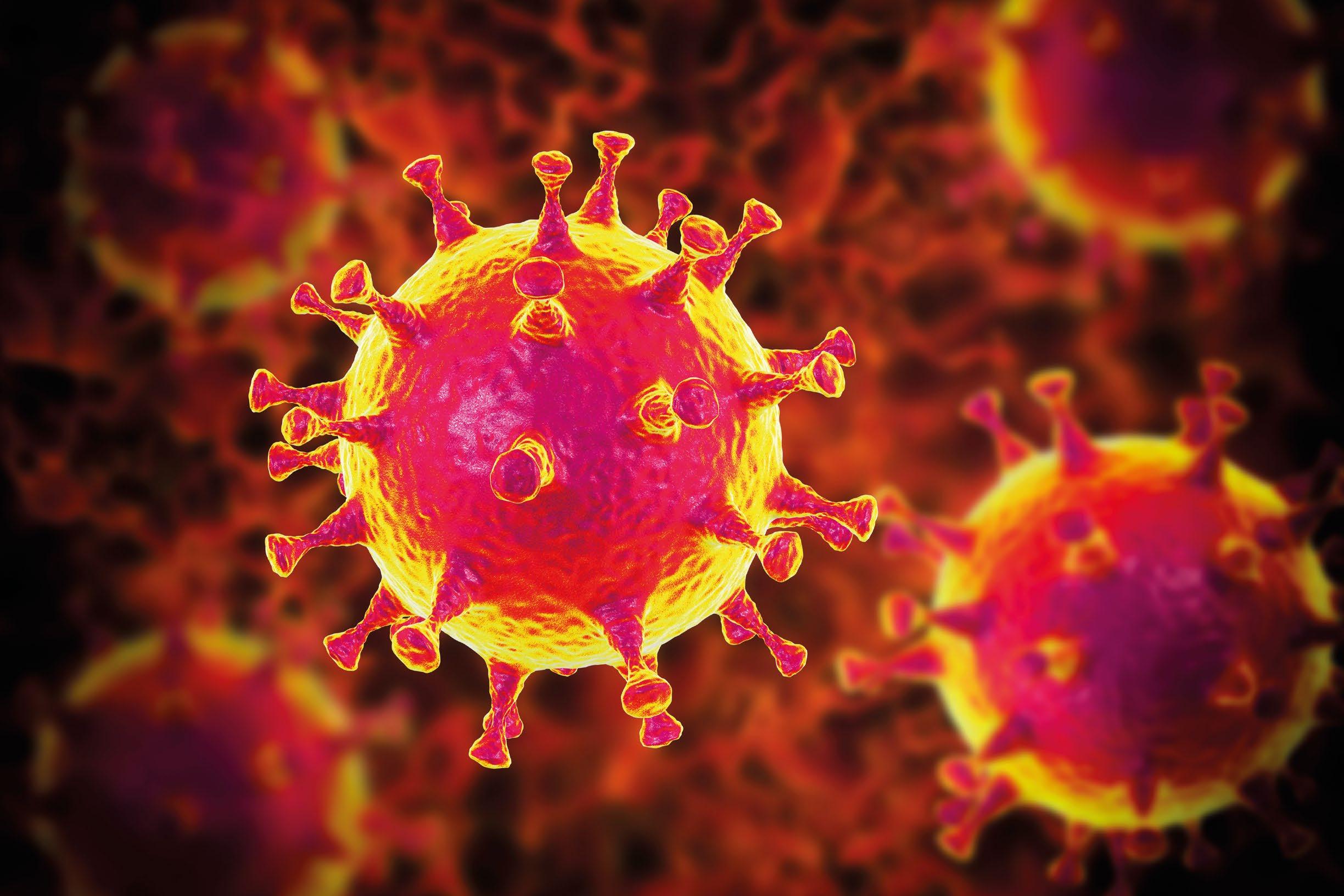
12 minute read
Coronavirus
Within the last month, we have received a massive influx of news surrounding the coronavirus pandemic: How it is affecting the packaging industry across all sectors, and how companies are rising to meet unprecedented challenges. It may seem like the packaging industry is “on hold”, with major exhibitions such as interpack and drupa moving to 2021, however we are witnessing the industry adapting in an impressively agile and flexible way to support the crisis on a European and global scale. Libby Munford explores key trends and issues that have arisen from this new world.
CORONAVIRUS: CHALLENGING TIMES IN A FAST-CHANGING WORLD
SUPPLY CHAIN MANAGEMENT T he packaging industry welcomed news with open arms when the European Commission confirmed that the transportation of packaging materials for essential industries such as food and pharmaceuticals will be able to use its “green lanes” – essentially fast-tracking the movement of materials.
Looking across the board, Simon Ellin, Chief Executive of The Recycling Association, says, “Our members are hearing reports from all corners of the world that essential cardboard, paper, glass, metal cans, and plastics are in very strong demand. We’ve got to keep our supply chains open to ensure food and medical supplies can reach those who need it.”
However, President of Pro Carton, Horst Bittermann states: “There will inevitably be challenges ahead. To ensure wide availability of goods, the supply chain needs to work smoothly from its start right through to the consumer’s home. For us that means having sufficient raw material, both virgin and recycled fibre. It is essential that the supply of wood pulp is maintained and equally that paper based packaging and other paper products are sent for recycling (with separate collection where this is practised). It is imperative that local Governments and Councils maintain the operation of these recycling systems to guarantee that sufficient recycled paper fibre is available.
“The haulage industry is under pressure to supply the numbers of drivers, vehicles and containers that are required. This is likely to be even more of a problem after the Easter break when some drivers may be required to quarantine before returning to their duties.”
FINAT Managing Director Jules Lejeune updates us on the self-adhesive labels market and short run packaging in particular, “Presently, the European label value chain is facing considerable challenges, as businesses are struggling to keep up with excessive short term demand due to hoarding, while at the same time, companies are coping with labour shortages and restrictions on the availability of critical raw materials and chemicals in the manufacturing process.”
It remains to be seen if European and global supply chain models will be able to sustain themselves throughout this crisis, and it appears crucial that the industry responds across material sectors with a unified approach.
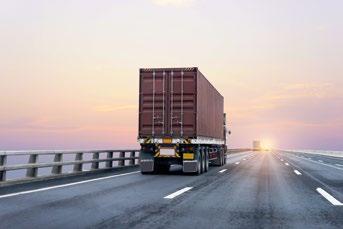

According to the British Coatings Federation, printing ink manufacturers across Europe are reporting reduced availability of ethanol and n-propanol. These are key inputs into the production of printed packaging inks and other materials, like varnishes, which, in turn, are vital in the production of consumer product packaging.
Availability issues are arising because ethanol, along with other industrial alcohol solvents like n-propanol, is also used in the production of disinfectants and sanitary products such as hand gels. With the obvious increased demands for sanitary, medical, and pharmaceutical products as a response to COVID-19, resources are increasingly being diverted into this area.
Sun Chemical has said it will implement surcharges affecting its solvent liquid inks in Europe, effective 1 April 2020, outlining its reasons: With supply already limited in the second half of 2019 due to a bad crop of raw materials increasing the demand for fuel ethanol, the coronavirus has caused further increased demand for pharmaceutical and sanitized products, with governments considering allocation measures. While availability is reducing globally, prices are increasing quickly.
Siegwerk, one of the leading global providers of printing inks for packaging applications and labels, has implemented price surcharges for solventbased packaging inks and varnishes in EMEA with immediate effect, whilst Flint Group Packaging Inks Europe has also announced a solvent surcharge across all solvent-based inks and coatings. INK SHORTAGES
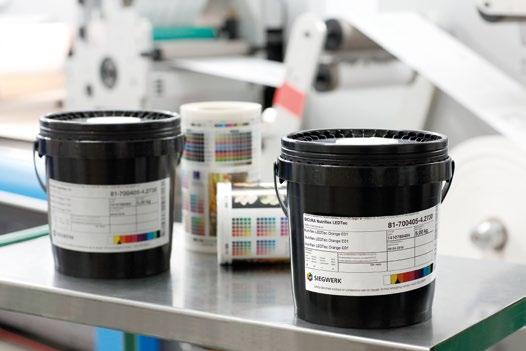
Siegwerk states that demand for these products, in particular ethanol, continues to outstrip supply which has led to reduced global availability and rapid price increases. In addition, due to the industry shutdowns in China and India, disruptions to freight and logistics, and many other isolated supply disruptions, Siegwerk is not always able to avoid price increases without increased risk of supply disruption.
The progressively worsening global economic situation caused by the current coronavirus pandemic is placing untenable pressure on the supply chain for packaging inks and coatings in particular.
Industry bodies from across the packaging value chain are warning of a shortage of cardboard and paperboard, due to decreased recycling collection rates during the coronavirus crisis.
Jori Ringman, Director-General of Cepi told Packaging Europe, “Recently, individual cities in some Member States have announced that they might have to reduce separate collections or even close sorting centres due to the current COVID-19 crisis, especially in relation to health and hygiene concerns for workers.
“If we fully understand the concerns for worker safety, we have warned authorities of the risk of stopping separate collection of paper for recycling from households and supermarkets, as recycled fibres are an essential part of our supply chain.”
Dr. Adam Read, external affairs director at SUEZ, talks to us about the challenges of operating waste and recycling collections during the coronavirus pandemic:
“SUEZ is maintaining municipal services as best we can, where we are working for local authorities. Collection, treatment services and disposal are currently running pretty much as close to close to full capacity as possible. Some of the ancillary, marginal services such as green waste or food waste or bulky waste collection has stopped, as well as most of our commercial collections, as many businesses are closed or working from home.”
Of note, some recycling companies are making direct calls to the public to remember to recycle. Delphis Eco, a leading eco-friendly plant-based chemical company, and leading recycling company, First Mile, for example, are calling on homes throughout the UK to recycle all of their plastic bottle closures - such as trigger sprays, hand soap pumps and flip top caps - via a free RecycleBox courier collection.
China and Northern Italy are the two main manufacturers of plastic bottle closures for cleaning and personal care products. As a result of COVID-19, there is now a global shortage of pretty much all bottle closures, including trigger sprays, hand soap pumps, and spray pumps. This shortage is causing issues in getting anti-bacterial hand soap and sanitisers to those that need them the most. RECYCLING CHALLENGES
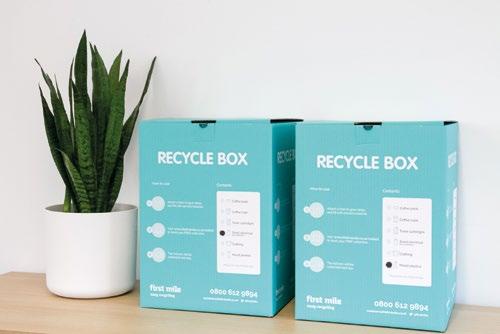
With new and critical logistical issues, companies are innovating under pressure to ensure safe delivery. DS Smith has developed boxes for example for safer delivery during COVID-19.
Stefano Rossi, CEO of Packaging at DS Smith said: “We were approached by several of our food supply customers to design a new packaging solution that would maximise efficiency and provide everyday essentials to many of society’s most vulnerable.
“We worked very closely with our customers to design and produce a solution which allows for a ‘stack, drop and go’ approach that is more time efficient, more hygienic and frees up time for more deliveries. Our sustainably designed solution is also fully recyclable at home.” LOGISTICAL INNOVATION
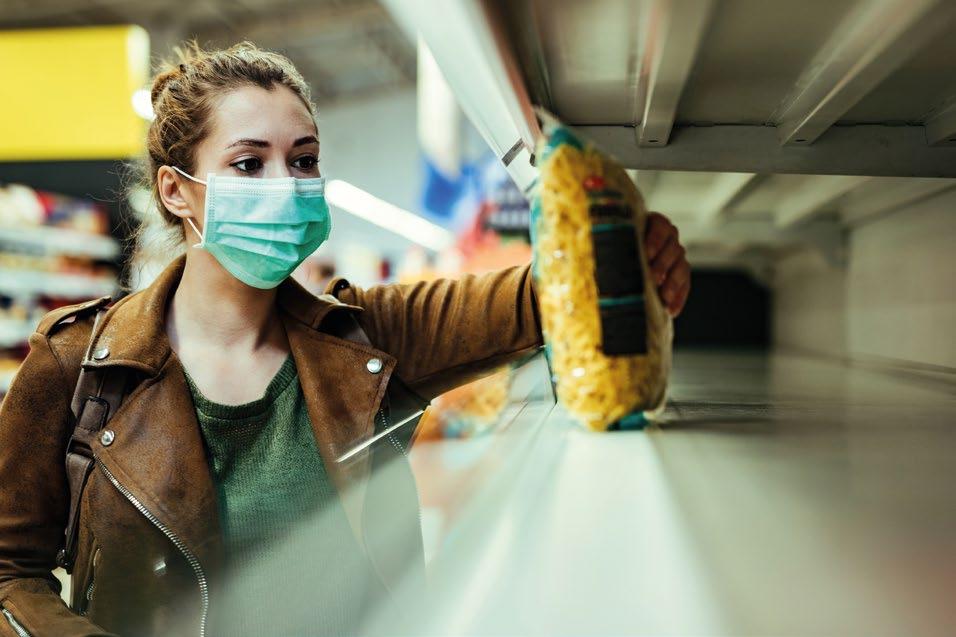
CONSUMER ANXIETY
Dominique Alhäuser, head of communication at CEFLEX member Windmöller & Hölscher KG, shares with Packaging Europe her company’s industry outlook during the corona crisis:
“Packaging for food and medical supplies is very important for our safety - that fact has become more clear during the corona pandemic, and has changed public opinion of flexible packaging. We are convinced that this will permanently impact the view on packaging and therefore increase the demand for flexible packaging.
“With regards to CEFLEX, I foresee challenges due to shifting priorities and restrictions, but on the other hand, projects might even benefit from the new mindset that is more open to new solutions and the growing feeling of community.”
Tri-Star managing director Alex Noake explores further the effects of the coronavirus on the food service packaging industry, highlighting that the agenda has shifted from sustainability to endurance:
“It’s fascinating watching the agenda change so fast. Suddenly disposable single-use plastic is in demand again and with a focus on hygiene, there is an expectation for food to be wrapped and even double-wrapped.” CHANGING ATTITUDES TO PLASTIC
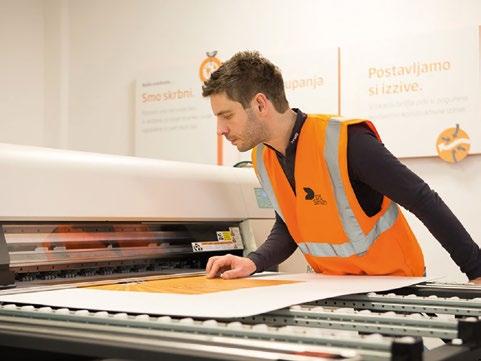
Astudy from Princeton University and the USA National Institutes of Health claims to show how long the novel coronavirus can survive on plastic, stainless steel, and cardboard.
According to the study, the virus could still be detected on polypropylene and stainless steel up to 72 hours after it was applied. Meanwhile, the virus could apparently be detected on cardboard up to 24 hours after it was contaminated.
However, The FDA has published guidelines on food safety and coronavirus, stating: Currently there is no evidence of food or food packaging being associated with transmission of COVID-19.
It may be possible that a person can get COVID-19 by touching a surface or object that has the virus on it and then touching their mouth, nose, or possibly their eyes, but this is not thought to be the main way the virus spreads.
CDC notes that in general, because of poor survivability of these coronaviruses on surfaces, there is likely very low risk of spread from food products or packaging that are shipped over a period of days or weeks at ambient, refrigerated, or frozen temperatures. It is more likely that a person will be exposed by person-to-person transmission involving close contact with someone who is ill or shedding the virus. This news comes amidst rising anxiety amongst consumers around the safety of packaging.
Synergies between packaging production and key components needed in the fight against coronavirus have become clear.
Following news that Reifenhäuser Reicofil has converted two of its test plants to produce components for face masks, the company has now announced that it has found a customer for these components.
However, in order to actually solve the wider problem of PPE shortages, the company argues that Europe needs its own industrial production sites with closed European supply chains and decisive political action. In its view, the aim must be to supply Europe with protective material independently and competitively, both now and in the long term.
Bernd Reifenhäuser, CEO of the Reifenhäuser Group, says, “We need a strategic production reserve for medical protective clothing in Europe. We have to quickly build up the machine capacity for the industrial production of masks in high volumes, but at the same time, the corresponding capacities for the production of the necessary high-quality nonwovens in Europe must be created. Otherwise, our dependence will remain at a crucial point in the supply chain. Other nations have recognized this, in some cases much earlier, and have already ordered equipment”.
Meanwhile Mondi has adapted production line in Germany to make much-needed face mask components.
The plant was able to quickly adapt one of its manufacturing lines to produce a three-layer, laminated strap that binds a stretchable plastic film between layers of soft, nonwoven material. The straps, which Mondi supplies to its CONVERTING PRODUCTION LINES

mask-making customers on a reel, are then cut and attached to each side of a mask, which can loop comfortably over the user’s ears to hold the mask in place.
“Mondi Gronau is working to provide straps that will fit more than one billion nonwoven face masks. As there is increasing demand for such types of face masks, we are building up our capability to meet this demand. By producing this soft elastic strap, we are able to produce more volume to meet growing demand,” says Dr. Michael Trinkaus, director of R&D and application engineering for Mondi’s Personal Care Components division.
The packaging industry has been notable for supporting the global response to this crisis. For example, the Tetra Laval Group will donate €10 Mio to various voluntary organisations supporting the health care systems across the countries that it operates in.
While maintaining important measures to ensure the health and safety of its employees, the Tetra Laval Group which comprises Tetra Pak, Sidel and DeLaval, is fully committed to play its part in ensuring uninterrupted food supplies during these difficult times.
EngView has takan steps to help its customers: packaging houses, display producers, and diemakers transition their employees to work remotely without sacrificing quality or efficiency. The company is giving its customers free homeoffice editions of the EngView Package & Display Designer Suite for the duration CHARITABLE EFFORTS
of the COVID-19 restriction period. With the free software, EngView will help structural and graphic designers, diemakers, and other packaging professionals maintain high productivity while working from their homes.
Label design and management software provider, NiceLabel has announced it will provide free label cloud software to organisations that have joined the fight against COVID-19.
This non-profit-based initiative offers free subscriptions of NiceLabel’s cloudbased solution and technical consulting services in a bid to help organisations get vital deliveries of medical equipment and supplies (such as respirators, disinfectants and masks) to those in need as quickly as possible. The cloud solution aims to help manufacturers and food producers to speed up supply and ensure their equipment and products arrive on the frontline without delay.

IN China, the biotech company CanSino is working together with the military medical department to develop a vaccine against the COVID-19 virus.
The researchers are supported by products from Minebea Intec: These play an important role in the manufacturing process and ensure that high-precision weighing and dosing is possible.
CanSino previously relied on Minebea Intec in 2014, when it developed a vaccine against Ebola.
The Tianjin-based company is one of 41 companies worldwide working on a vaccine against the virus. CanSino was one of the first institutions to start working on a vaccination against COVID-19 and just recently secured permission from the Chinese government to start tests with humans in a clinical trial.
Prior to this, Minebea Intec’s products ensured reliable weighing results, precise dosing and rapid transmission of the measured data during the production of the first substances.
Whilst we collectively await a vaccine to solve this crisis, Packaging Europe supports you to stay home, and stay safe. SUPPORTING VACCINE DEVELOPMENT
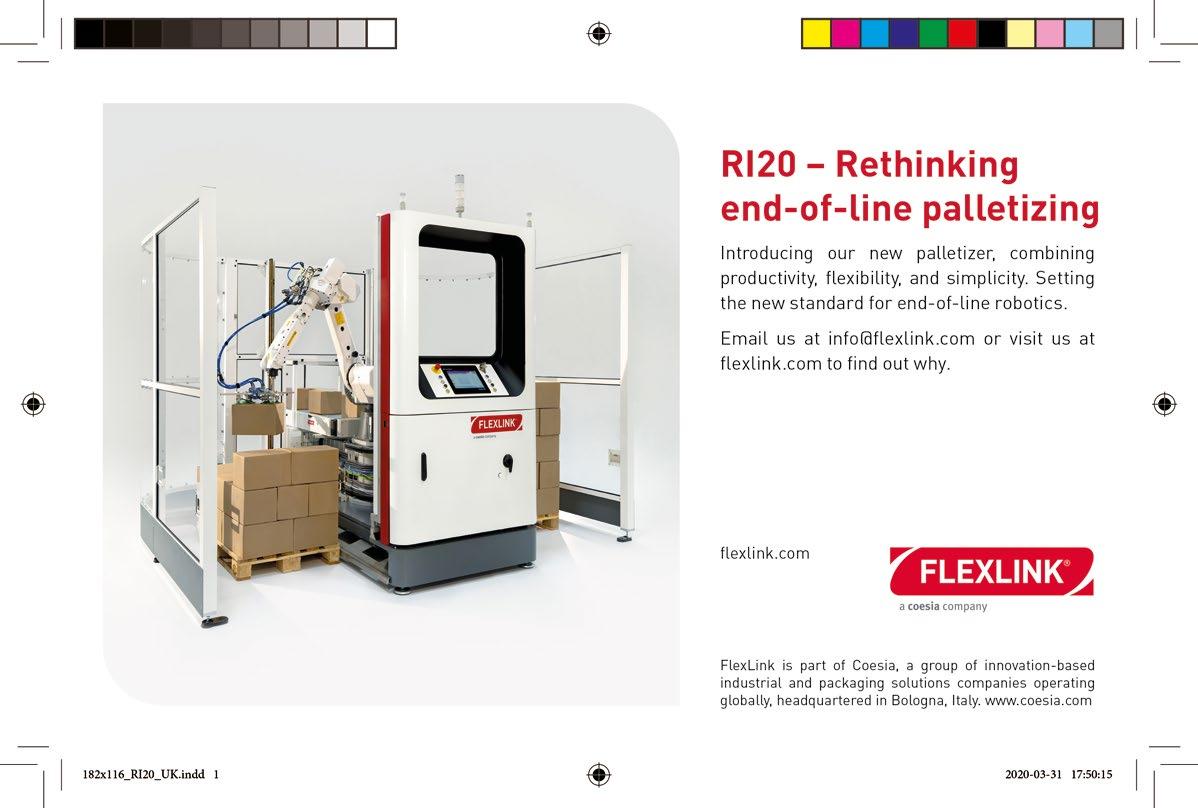
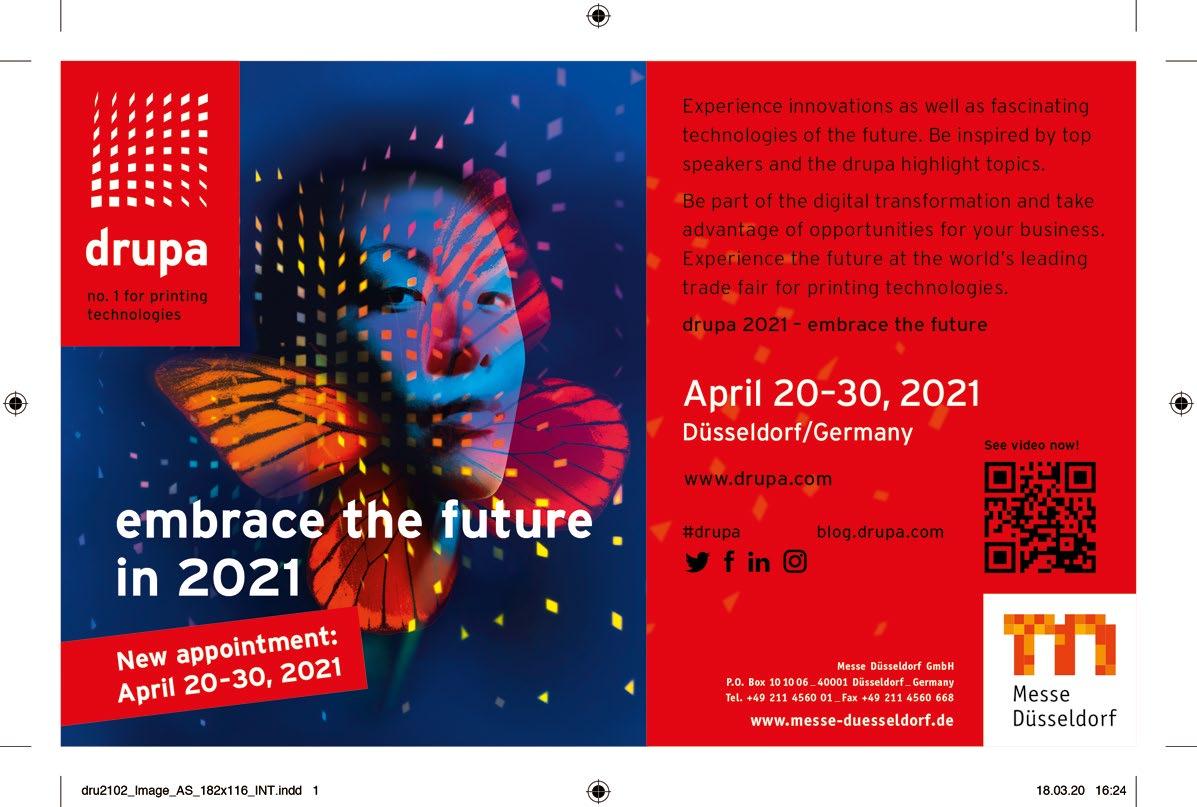