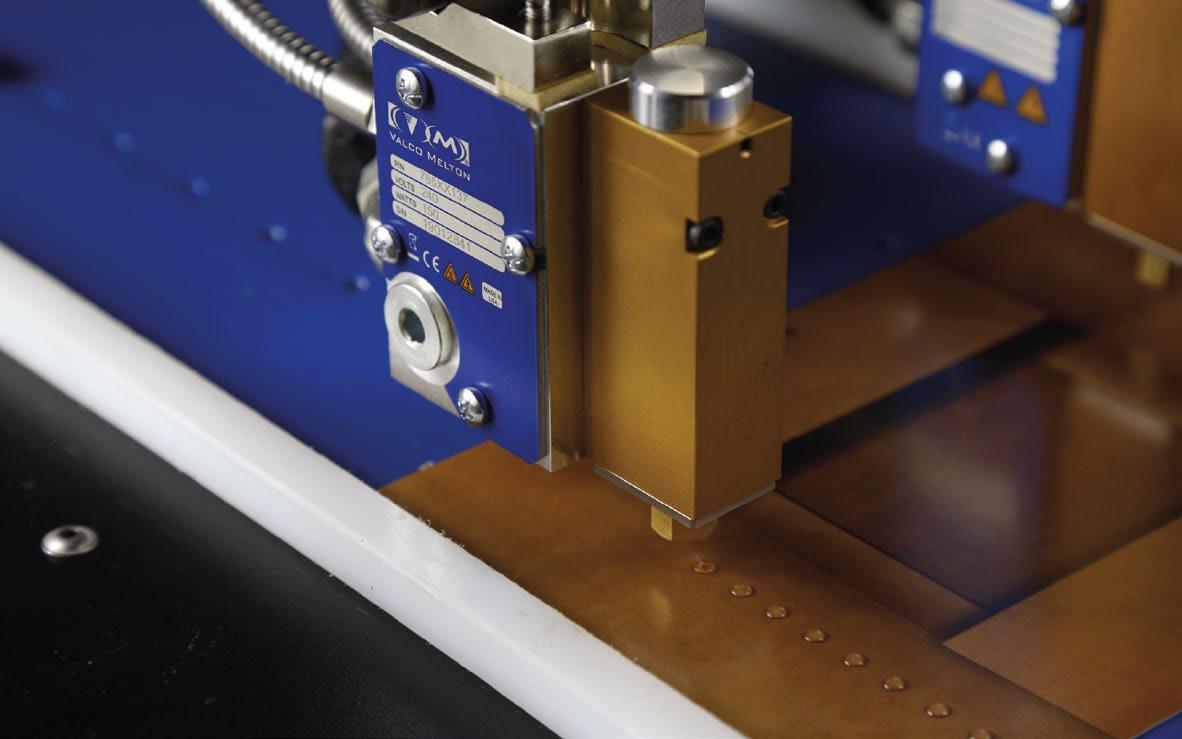
6 minute read
Digital Transformation: Creating a secure, efficient and sustainable supply chain
DIGITAL TRANSFORMATION: CREATING A SECURE, EFFICIENT AND SUSTAINABLE SUPPLY CHAIN
How will increasing levels of automation and digitalization shape the future of the packaging landscape? Victoria Hattersley spoke to David Swedes, Vice-President Engineering & Manufacturing at Valco Melton, about the transformative effect automation is having on vital processes in the production chain such as dispensing, inspection and monitoring.
The terms ‘digital transformation’ and ‘Industry 4.0’ are ones we are all now very familiar with, but they can mean different things to different people depending on where they are in the value chain. Increased automation is one obvious factor, of course, but they also encompass tracking along the supply chain from producer to consumer, AI, vision inspection and much, much more. All of this is with the aim of creating a more secure, efficient and sustainable production infrastructure for the future.
“Transforming an entire supply chain can include everything from full plant automation and control to inventory tracking with barcodes/RFID to integrated transportation and distribution solutions that allow tracking of products from vendors through to end-users,” says David Swedes of Valco Melton – one of the world’s leaders in adhesive dispensing machinery, vision inspection and electronic monitoring systems. “For Valco Melton, that transformation includes remote monitoring of packaging adhesive application systems, supervisory PLC control of previously machine-level systems, quality monitoring of packaging lines and packaging manufacturing machinery.”
The packaging industry has been somewhat lagging behind other sectors when it comes to digital adoption and while there have been many advancements in robotics, smart packaging, AI and so on it’s still very much in the early stages. However, according to a recent survey by McKinsey it will be a clear
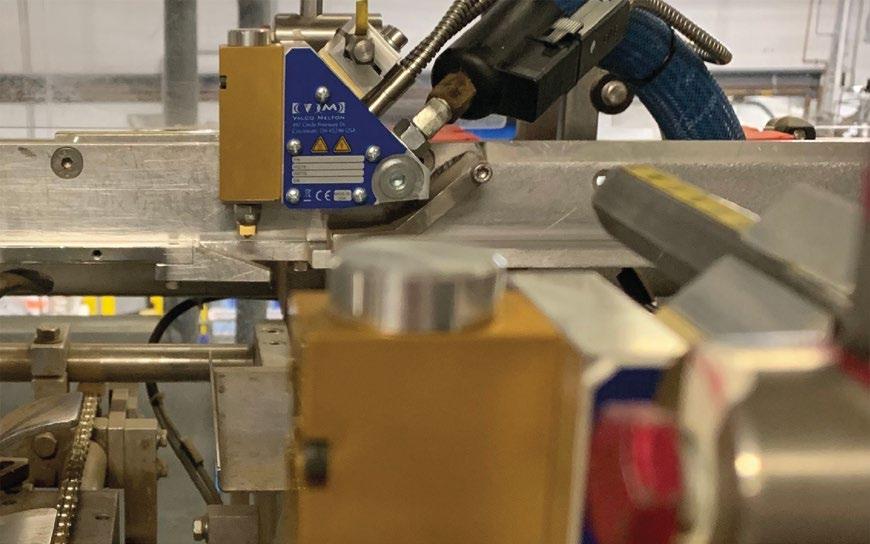

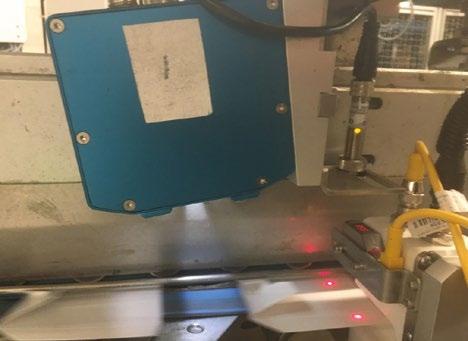
priority for industry stakeholders moving forward. It found that while technology adoption in the sector is largely limited to applications such as consumer interaction and track & trace, we can expect to see it being leveraged to improve packaging recyclability, circularity and data collection in the future.
The COVID-19 crisis, while wreaking untold havoc, has also served to accelerate the process of digitalization – for example by creating the need for more space between workers, which means increased adoption of automation. And then, ongoing lockdowns across the world have obliged many consumers to rely more heavily on e-commerce, increasing demand for packaged goods and putting greater pressure on the industry to increase output and efficiency.
The importance of vision systems
And how is the industry meeting this demand through digitalization? First, let’s look at the vital topic of data and vision technology: accumulating information on the performance of packaging machines can enable quicker analysis and correction of production issues. Continuous improvements in vision technology are also key to improving efficiency and reducing waste on the factory floor. Systems such as Valco Melton’s ClearVision installed on case-makers aim to remove defective products from the stream before they create downtime at a packaging facility or are shipped to customers. Producers can, for example, monitor glue application, case score-line locations, fold quality, print and barcode quality before shipping.
“However,” says David Swedes, “there is a second level to the importance of vision systems that is of great interest to quality and continuous improvement managers – process improvement. Manufacturing processes, by nature, follow certain statistical patterns and improving those processes always requires study
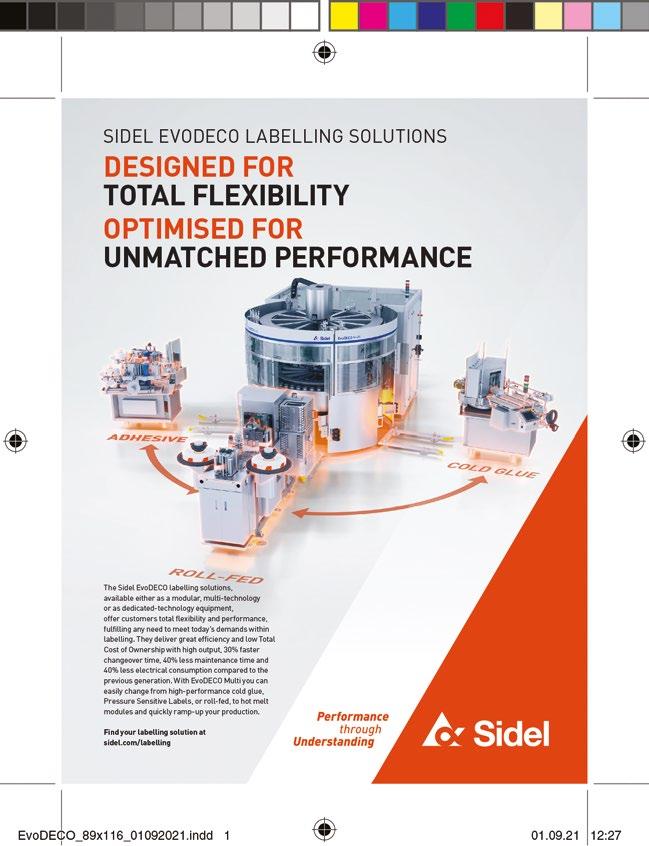
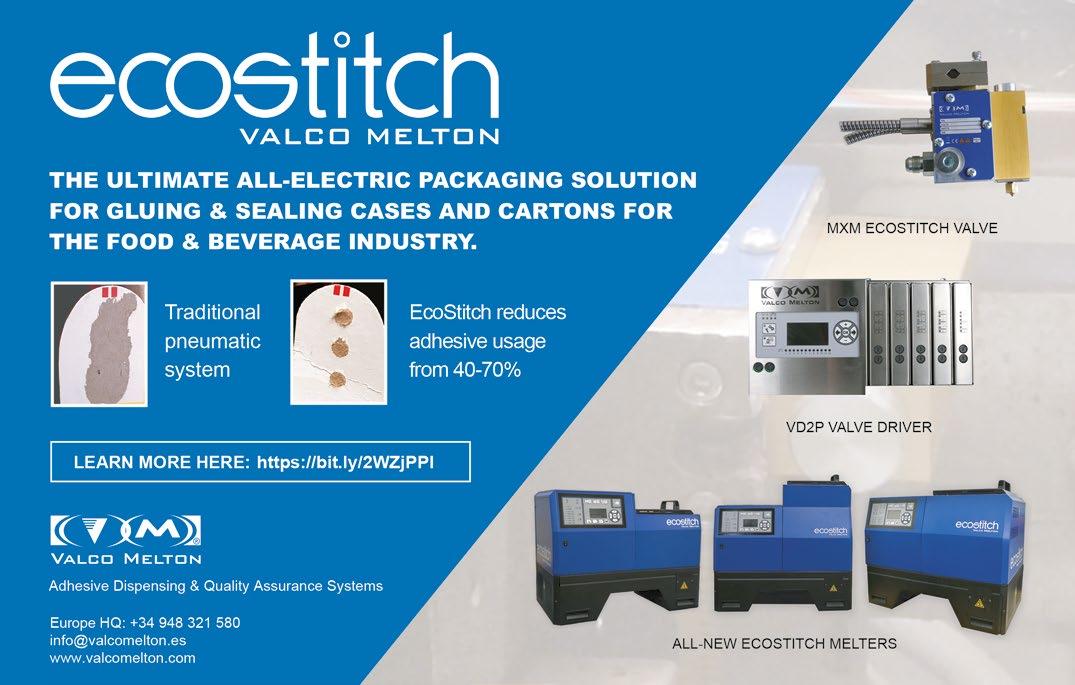

and data. Vision systems provide volumes of images as well as measurements to recognize those patterns, prioritize issues and spend more time taking appropriate corrective action than attempting to recognize root causes.
“But having a vision system that simply stores images and data that are not easily accessible or easily sorted and interpreted can be an impediment to using that data as it is simply too much and too difficult to get to. Tools like ClearVision’s MeasurementChek provide access to vision measurements from anywhere in a plant’s secure IT eco-system and allow data to be sorted in multiple ways to quickly locate relevant information.”
Furthermore, hot melt beyond verification systems such as those offered by Valco Melton play a key role in terms of security by helping to ensure that cases and cartons have been properly glued and closed. “By utilizing combinations of images from different cameras, the applied adhesive is ‘seen’ through the closed flaps and verified to be in sufficient quantity and in the correct position. There is a second benefit of knowing that the flap is in fact closed. Clearly, assurance that cases are properly glued and closed prevents warehouse tip-overs and spills and more important, frustration with packages that fall apart in the distribution or retail space or even in transit or at the point of use. This is important not just for safety and security but also brand protection.”
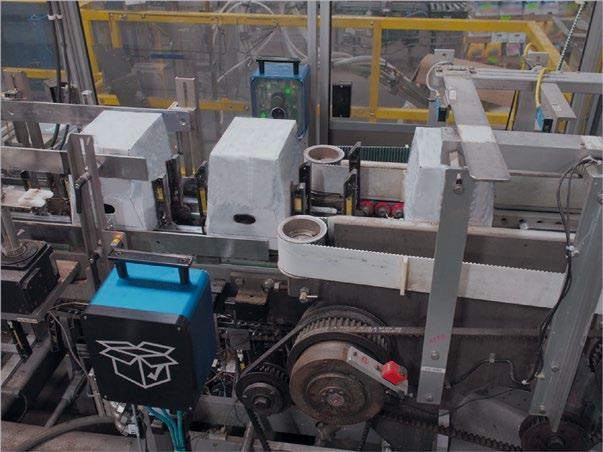
The trend towards mass customization
Let’s also bear in mind that demands are constantly changing, and the production infrastructure must adapt to these while keeping an eye to efficiency and sustainability. The ongoing trend towards mass customization, so much discussed, is a case in point including targeted branding, flavours, scents, sizes and so on. Incidentally, this is one area of innovation that the COVID19 crisis doesn’t seem to have speeded up – as David Swedes points out, consumers have been ‘happy to obtain the product at all’ during this fraught time – but once things get back to ‘normal’ the appetite for more personalized offerings and increased flexibility will return.
“Long term, the need for flexibility in packaging equipment and variety in products will not disappear,” says David. “Equipment makers must accept the reality that the quicker a line or system can be changed over, the more valuable it will be. This is particularly evident when one sees packaging and manufacturing in Asian markets where batch quantities that would normally be 10,000 or 50,000 in a European market are closer to 1000. This small-lot approach influences the whole chain down to distribution and transportation where the last kilometre of distribution is often on a motorbike.”
In the past, shop floors were fairly static, producing one product, or line of products for long periods of time with minimal turnover. Today, mass customization and rapid innovation are driving factories to produce many more products in the same environment at faster rates with higher throughput. To keep up and stay competitive, manufacturers need machines and production lines that are substantially more flexible, versatile, scalable, and cost-effective than ever before.
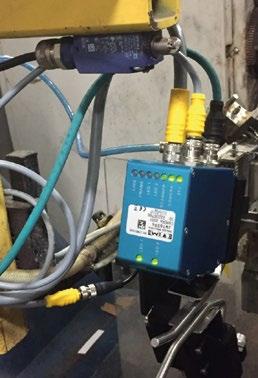
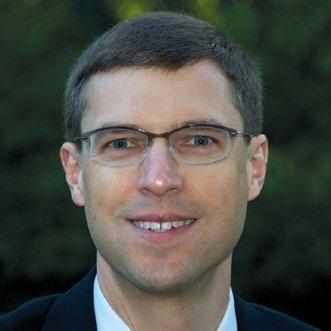
David Swedes
Still some way to go
While the packaging industry still has a long way to go before it reaches digital maturity, David tells us he has seen good reason to be optimistic that it is heading in the ‘right’ direction.
“I recently saw a fully automated manufacturing site making cartons for high-volume beverage packaging. It was clear that this investment required a tremendous amount of work and cooperation on the part of the company running it, its vendors and partners and the local community around it. This factory relied on robotic technology for packing and material handling, supervisory scheduling, control and monitoring of production rates, barcoded identification of inventory batches and a stable workforce. With an advanced mill on site, it is reducing its transportation footprint by shortening the raw material to finished product cycle time. When I see this level of commitment to the goals of a sustainable, efficient factory, I am encouraged that there are good days ahead for this industry.” n
