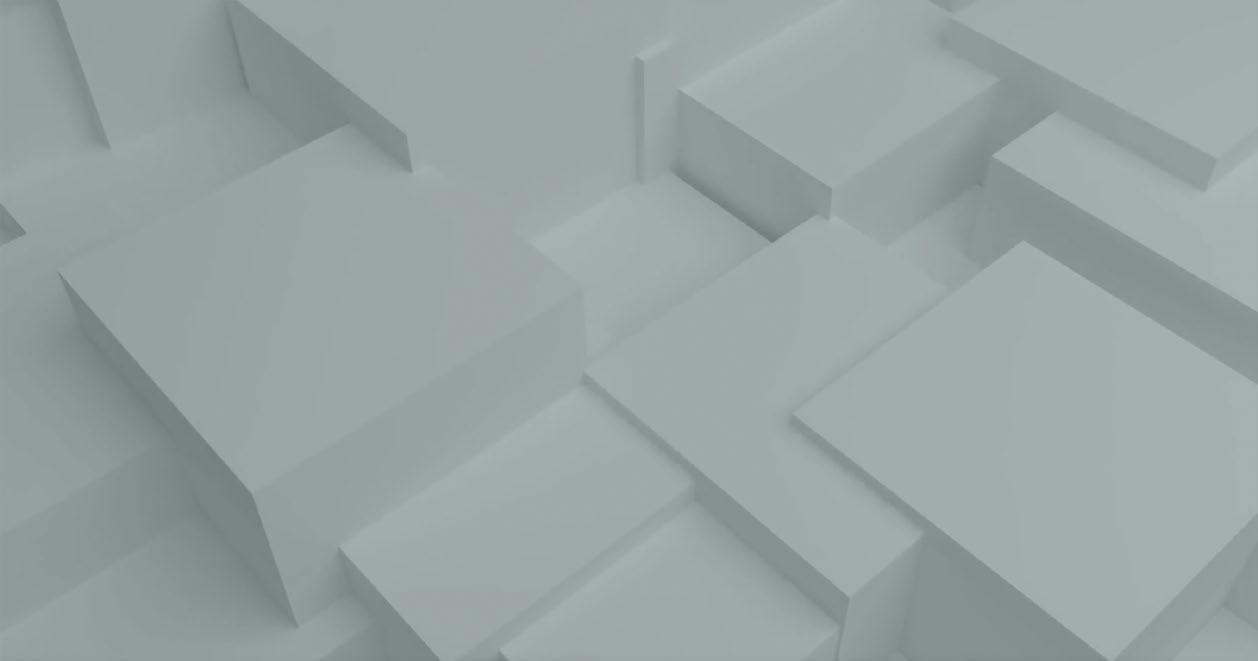
7 minute read
Koehler: The future for barrier papers
KOEHLER: THE FUTURE FOR BARRIER PAPERS
Our last Wider View article with Koehler Paper tackled, and we hope dispelled, some of the prevalent misconceptions around paper packaging. This year, it’s all about looking to the future of barrier papers: how far have they come and what will the third, fourth – even fifth? – generations bring in terms of functionality? Victoria Hattersley finds out.
Every week we hear of new innovations, collaborations and areas of application in the field of high-barrier papers, driven by ever-greater market pull and demand for sustainable packaging solutions. According to a Smithers Pira report, ‘The Future of Functional & Barrier Coatings for Paper & Board to 2024’, volume demand for functional and barrier coating applications in paper and board packaging reached almost 3 million tonnes globally in 2018, with a value of $7.8 billion. The same report says the market is forecast to grow at a rate of 5.0% to 2024, pushing market value to almost $11.0 billion and worldwide consumption to just under 4 million tonnes.
Compared to older iterations of paper packaging, the newer generations of barrier papers offer far more in terms of safety, hygiene and product protection. So what attributes can we expect the third and even fourth generations of materials to bring us?
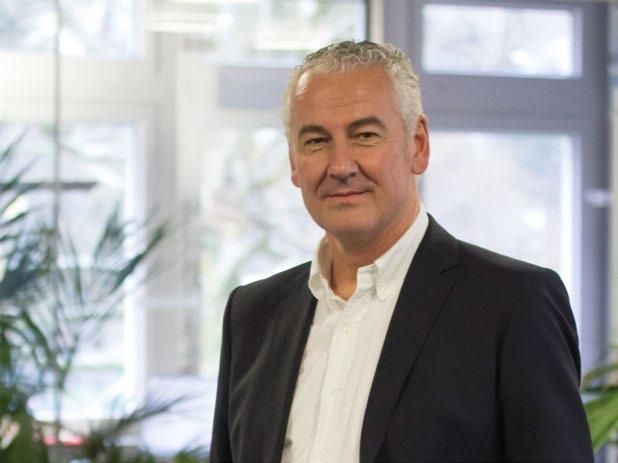
“In general, we can say that the next generation of barrier papers is gaining speed. The next ‘big’ move is to launch a coated paper with a very good water vapour barrier under tropical conditions in combination with a mineral oil protection barrier,” says Eckhard Kallies, Director of Flexible Packaging. “We expect full market implementation of this in the second half of 2022. We are also involved in a strategic alliance with leading flexible packaging converters to develop the next generation of functional coated barrier papers for specific end-use applications.”
Other areas of innovation for these new generations of papers include the development of biodegradable coatings, and a focus on weight reduction to further reduce the CO2 burden.
Barrier papers for food: Case studies
According to Eckhard, opportunities for barrier papers to take a more significant hold in the food industry – particularly confectionery – are wide open, as Koehler’s latest collaborations demonstrate. The company recently teamed up with Alfred Ritter to supply its NexPlus® barrier-coated paper for the confectionery producer’s new ‘Mini Mix’ pouches. NexPlus® can be seen as a real step forward in terms of product protection, providing a barrier against oxygen and mineral oil, among other things, as well as being resistant to grease. These pouches have been available on all international markets since January 2021, and have also been available in Germany since early March.
In another high-profile collaboration, confectionery producer Südzucker has changed the packaging material of its sugar sticks to Koehler NexPlus® Seal paper. After passing the qualification phase and initial test quantities, all of the sugar stick packaging was changed over to Koehler NexPlus® after just a four-month test period. The new sugar sticks have been in stores across Germany since late February 2021.
Yet some brand owners are still concerned that the challenge of adapting their existing packaging lines to paper will be too great. This, as we showed in our previous Wider View article with Koehler, is by no means the case anymore. For Alfred Ritter, while the switch certainly involved some careful test runs and minor adjustments, ultimately it was able to arrive at an optimal solution.
Expanding range of applications
But while the food industry may be the biggest end-use sector it is by no means be the only important one for the barrier paper sector moving forward. While uptake is still slower in non-food applications when it comes to adopting paper over plastics or other materials, according to Eckhard, “Even here there is much more room for optimism as we see younger generations constantly asking for more sustainable products and packaging.
“The main challenge, as always, is to build the right mindset to make changes and foster innovation. We are now seeing the ‘first & fast movers’ and these companies will create value and gain market share. Their market approach is different as they are very open to collaborate to combine expertise from all angles.”
Is legislation fit for purpose?
On a practical note, I was interested to explore what further changes must be made to increase uptake across all potential end-use sectors. One issue that comes up again and again is the need for greater legislative harmonization across Europe.
If we take the example of Germany, here a packaging monomaterial is defined as one which consists of 95% or more of the same material. This ‘5%’ rule goes back to the 1990s but many would argue that it does not meet today’s reality, in which barrier paper technologies have changed so significantly. What should matter, arguably, is not the percentage of a non-paper ingredient in the waste material, but how much that non-paper material interferes with the paper recycling stream. We have seen several instances in the past year or two of functional barrier papers that can be placed in existing streams – Koehler’s NexPlus® barrier paper being just
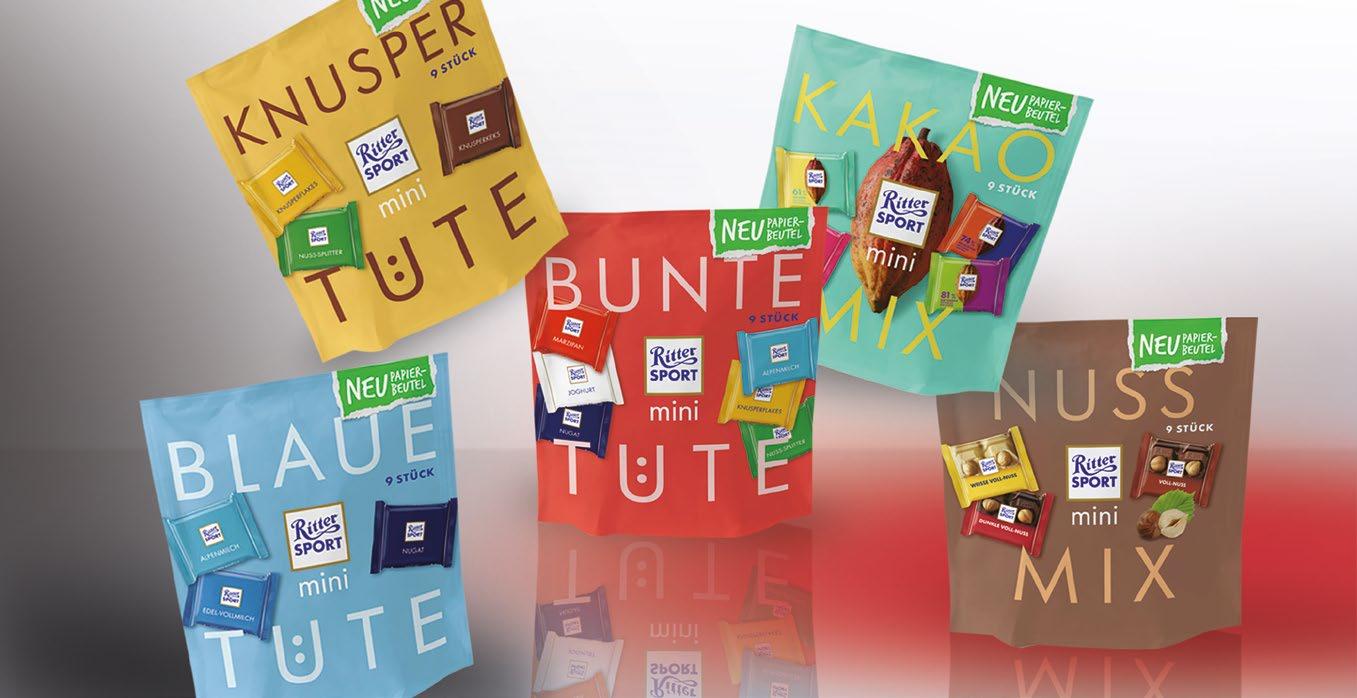
one example of this. Clearly there is still work to be done to ensure a more robust recycling stream for all flexible paper packaging containing laminated composites, but the market is moving in the right direction.
The definition of a polymer in the Single-Use Plastic Directive (SUPD) is also, to many, a questionable one. Certain kinds of packaging paper that are considered as monomaterials – paper substances such as modified starch or latex binders, let’s say – could also fall under this directive. Is there a strong argument for a rethink?
“More legislative harmonization is key for transformation,” confirms Eckhard. “The current status of the SUPD is not supporting change and even more, brings much more uncertainty to the whole industry as nobody really knows in which direction to invest. We need much more clarity and a pragmatic approach rather than contradictory guidelines.”
What this requires, he says, is a collaborative approach across the entire European paper industry. “The industry needs to align much more strongly and drive innovation across all sectors. We have so much in common and one, if not the most sustainable raw materials in our hands.”
What comes next?
So far we’ve talked about what the emerging third and fourth generations of barrier papers can – and will – achieve. We’ve talked about the obstacles the industry faces to ensure the market and the recycling infrastructure is ready for these materials. But as we conclude, let’s look further ahead. What, we ask, might a fifth generation of barrier papers look like?
“We are always talking about the evolution of materials,” says Eckhard, “and the same is true with paper. In a time span of 5-10 years, functional coated barrier papers will look very different. Certainly we will be seeing significantly lower grammages with higher performing barriers. The barrier itself might be biobased and therefore biodegradable, and overall the footprint will be improved year-on-year.”
Indeed, Eckhard is even confident that paper will come to ‘dominate’ the flexible packaging market for most applications, but he adds that “all developments must be ready for paper recycling and therefore feed the fast-growing needs of packaging from, for example, the rapidly growing online business sector. We might also see recycling fibres in flexible packaging for secondary packaging needs, although I’m still anticipating virgin fibres being used for primary food application due to the high food safety requirements.”
Will paper really dominate the flexibles market in the next few years? What I think we can say for sure is that, in the future, it will no longer be just plastics that can provide the product protection and shelf life required for FMCG goods. But as ever, it’s not necessarily a case of pitting one material against another – rather of ensuring that in the future each material can reach its full potential within a circular economy. n
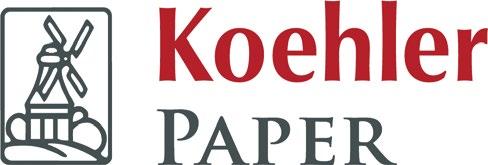