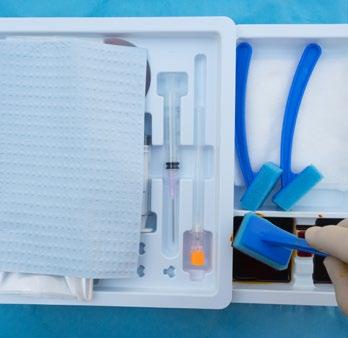
5 minute read
Designing sustainable packaging
Designing for sustainable packaging
By Alison Bryant, Communications Director Healthcare Plastics Recycling Council
Advertisement
With pressure from customers, investors and society, it is not always easy to set the right targets and to keep control over activities that will drive companies to a sustainable future.
he global market for plastic healthcare packaging was £14.6 billion in 2020, and market analysts project that it will grow by 5%+ annually to £18.8 billion by 2025. While healthcare plastics only make up 6% of the global market by volume, this is not an insignificant amount, especially when most of it is clean, noninfectious material heading straight to landfill.
There are a number of reasons why healthcare plastics are not being recycled more widely and consistently. The reality is there are barriers to recycling healthcare plastics at every point along the value chain – from product design and manufacturing through product use, disposal and recycling. Design guidelines While the most critical requirement for all medical applications is patient safety and product efficacy, design considerations to improve recovery and recycling of healthcare plastics are also important. The Healthcare Plastics Recycling Council has developed design guidelines based on multiple pilot studies and input from industry experts, including resin manufacturers, device and packaging designers, healthcare sustainability professionals, and recycling experts.
These guidelines concentrate on the context of recyclability, but also consider the broader context of functional requirements, hospital operations and protocols, overall business requirements and many other design and manufacturing requirements. Medical device and packaging designers and engineers should prioritise product performance and functionality, sterility, efficacy, safety, and ease of use when there is a conflict between these requirements and the ability to recycle.
These guidelines are also considerate of the new opportunities presented with the rapidly growing advanced recycling industry. Healthcare plastics are well suited and can be a valuable feedstock for advanced recycling. Because of the increased environmental impacts associated with advanced recycling compared to mechanical recycling, advanced recycling is a complementary solution to mechanical recycling. These design guidelines are focused on enabling mechanical recycling first, with advanced recycling as a secondary and complementary solution.
Desirable design practices for healthcare plastics • Design with mono-material whenever possible. • Use polyolefin seals or gaskets on polypropylene bottles. • Combine chemically compatible or jointly processable plastics, if multiple materials are required. • Use materials easily separated during automated recycling processes, if multiple materials are required. • Use breathable plastics as alternative to paper. • Minimise paper labels and components. • Use water-based adhesives.
• Allow for bottles and bags to be fully drained with ease before disposal. • Provide information on content for easy identification of residual liquids. • Minimise use of pigments.
Less desirable design practices for healthcare plastics • Using rubber seals on polypropylene bottles. • Combining incompatible bioplastics and petroleumbased plastics into one product. • Welding, gluing or molding two components of unlike plastics. • Combining plastic film with paper in packaging. • Using metallised plastics, metals screws, or grommets in plastic. • Using lead. • Using PVC.
Eliminating multiple material types within one discrete healthcare product The best practice is to utilise mono-material designs wherever possible. Currently, the most marketable recycled plastics are thermoplastics, such as polyester, polyethylene, polypropylene, and high impact polystyrene. If a healthcare product can be made with just one of those polymer types, there will be less labour and resulting expense, at every level in the plastics lifecycle. If multiple material types must be used, materials easily separated in recycling processes (eg in a sink/ float tank, optical sorter, air jet, etc) are more desirable. If monomaterial options are not available, a good practice is to only use thermoplastics. A thermoplastic elastomer seal on a polypropylene bottle is a good example of this. While it does not provide the value of a mono-material recycled polymer stream, it still avoids any necessary labour of separation, and the recycled material can be utilised for a number of future applications.
Marketable thermoplastic recycled resins and blends • Polyethylene terephthalate and variants (PET, PETE, PETG) • High density polyethylene (HDPE) • Low density polyethylene (LDPE) • Polypropylene (PP) • Polystyrene (PS) • Blends of polypropylene and polyethylene (PP and PE) • Blends of polypropylene and thermoplastic elastomers (PP/
TPE)
Eliminating multiple material types within healthcare packaging The use of multiple materials in healthcare packaging presents some unique challenges and opportunities. Much of the sterile product used in operating rooms is packaged in a thermoplastic film laminated to a micro-porous label made of paper. The paper provides two functions in that it allows for printing of the product information and for the sterilant to enter and exit the package during gaseous sterilisation processes. A breathable thermoplastic, such as DuPont’s TYVEK, could be used as a replacement for the cellulose-based label. Additionally, some sterilisation methods, such as gamma radiation and e-beam radiation, do not require breathable films and could also be potential alternatives for certain products. However, not all product and packaging materials are compatible with the radiation methods of sterilisation. Overall, both alternative films and methods may provide solutions to this design challenge.
These design practices are focused on maximising the opportunity for mechanical recycling. Advanced recycling technologies can be successfully used to recycle multi-material products and multi-laminate packaging at higher energy inputs and corresponding costs, although yields may be reduced, depending on the technology.
Conclusion Products designed to limit the use of multiple plastics without sacrificing their intent for use will increase their recyclable potential. Additionally, the largest challenge to optimum yield of a viable, economic mixed plastic waste stream is the reduction or elimination of common contaminants, such as paper, metals, rubber seals and liquids. Elimination of these contaminants would increase the end product value and improve processing and separation equipment capacity and efficiency. Ultimately, designing healthcare products and packaging with recycling in mind is an important part of the solution to reducing waste and providing a valuable material stream for recyclers.
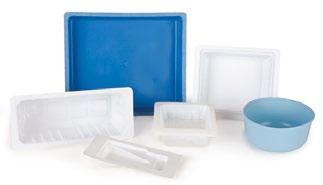