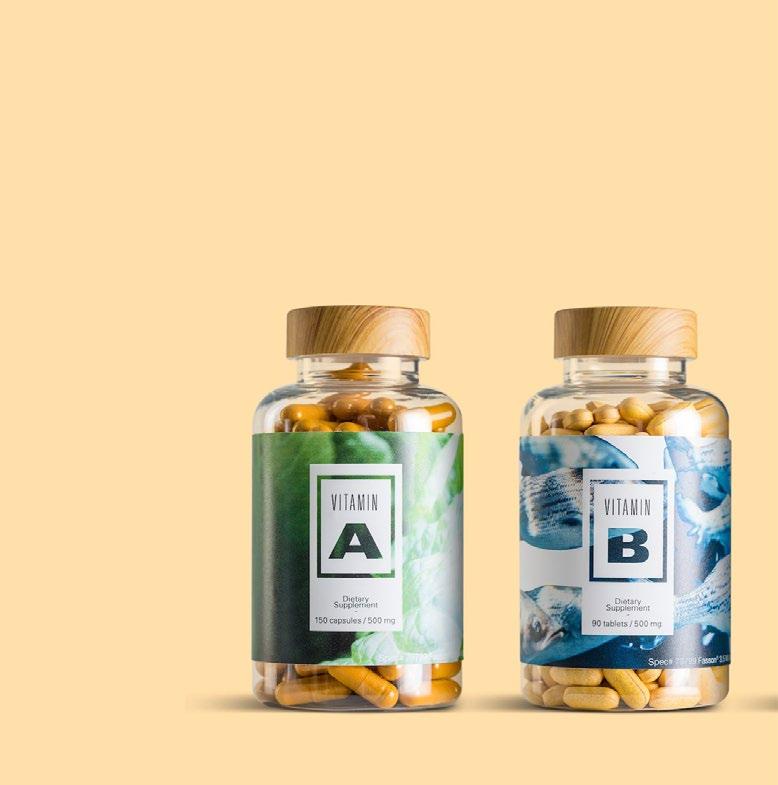
6 minute read
Labelling for pharma
Labellingin the pharmaceutical industry
By Neel Madsen, Journalist
Advertisement
Printing, coding and labelling errors can have serious consequences when it comes to pharmaceutical products. Recalls are costly and can damage the brand owner’s reputation in an industry where reliability and compliance are paramount.
hile some commercial printers have adapted their production to making facemasks, the upsurge in the use of hand sanitiser has seen demands for durable labels rocket during the COVID-19 pandemic. In the pharmaceutical industry, millions of vials filled with the newly developed vaccines have needed printed labels, as well as boxes in which they are supplied. This unprecedented high level of demand has tested label and packaging manufacturing, and the associated supply chain, to the limit.
Normally medicines sold within the EU must be printed in the local language, but such has been the pressure on the manufacturers during this crisis that the Member States agreed a temporary exemption from this obligation allowing outer and inner labelling, as well as the leaflets included, to be printed in English only.
However, each individual product must still carry a unique code that enables full verification and traceability, as well as quality control and product recalls. These requirements are met by using variable data printing that can assign a number of different codes and marks, which are recorded and verified. The labelling process is monitored by 100% inspection systems, so that each label or folding carton box is error-free, and every single one accounted for.
These rigid demands should be seen in the light of a forecast by Allied Market Research predicting that the global pharmaceutical packaging market will grow from $88,880 million in 2019 to $144,233 million by 2027, equivalent to a CAGR of 6.1%.
Labelling and coding For pharmaceutical products, a printing system must be able to produce extremely fine details and small text in high resolution for excellent readability and scanning. Digital printing is ideal for overprinting with variable data, for smaller batch sizes and when producing multiple SKUs.
Serialisation and adhesives used for pharma products must be fit for purpose. Avery Dennison has recently introduced a new pharmaceuticals portfolio of materials with compliant adhesives. The range of facestocks has been specifically designed for digital printing with UV inkjet, water-based inkjet, dry toner, thermal transfer, and direct transfer.
Serialization, as required by law, assigns a unique, random code to each saleable unit. There are many inkjet digital and thermal printing systems on the market for adding this type of coding and marking. They can be integrated directly on the printing press, converting line, or on the filling line at the packing company.
The K600i from Domino is a monochrome UV inkjet printer that runs at speeds up to 200 m/ min adding alphanumeric codes, barcodes, QR codes and other variable data. It can print with a variety of inks, including UV LED ink cured by a Phoseon FireJet module, for increased productivity and reduced energy costs.
Medical technology company Becton Dickinson in Spain chose this high-speed printer to digitally add unique codes onto the outer paper packaging of needles and syringes used for COVID-19 vaccines. Incorporating the K600i printer into their packing line resulted in drastically reduced miscoding rejects, with no compromise in print speed, and significantly improved printing costs for Becton Dickinson, according to Domino.
Tactile marks such as obligatory warning triangles and Braille can also be produced with inkjet printing with special varnishes applying a thicker layer of ink for a raised effect. One example is Xaar’s inkjet Print Bar System, which is capable of laying down high-build varnishes at high speed in one single pass. This High Laydown Technology, which is compatible with a range of Xaar’s printheads, produces a variety of tactile effects and satisfies the dimension specifications for Braille and warning triangles for pharma packaging.
Extended functions The applications in pharmaceuticals are extremely varied. Printed labels are not only applied to various shapes of bottles and jars, but also in more challenging applications for syringes, pens, inhalers, cartridges, ampules and medical fluid bags. With other types of packaging, such as folding cartons and blister packs, the print is most often applied directly to the pack by dedicated converting systems.
One of the most difficult applications in this sector is multilayers labels. These come in a variety of versions under different names and consist of multiple layers of substrate printed and folded, or glued together, to extend the surface space available. Whether they are peel & reveal labels or booklets labels, they can be used to provide information about dosage, usage, side effects and other statutory information in multiple languages. For the ultimate in utilisation, the substrate is often printed on both sides, including on the adhesive.
Servo-driven narrow web flexo and hybrid presses can be fitted with delam/relam, turner bars, extra towers for over-laminating substrates and crossover modules to produce multi-layer labels inline in one pass, but these functions can also be incorporated on the finishing line and performed offline. Multiple pre-printed webs can be joined and then laminated on top of one another using in-register lamination.
Labels that perform a security function are also commonly used to protect the product, the brand and the end user from counterfeiters. Since 2019, all pharmaceutical packaging in the EU must include a form of tamperevident closure. This secures the content so that any attempt to open the packaging will destroy the label and/or part of the box itself.
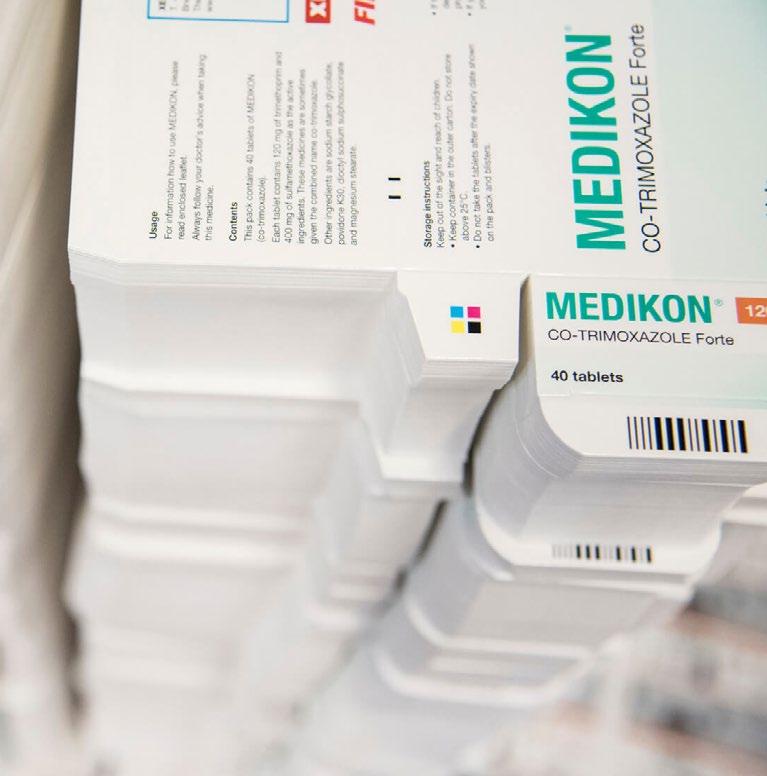
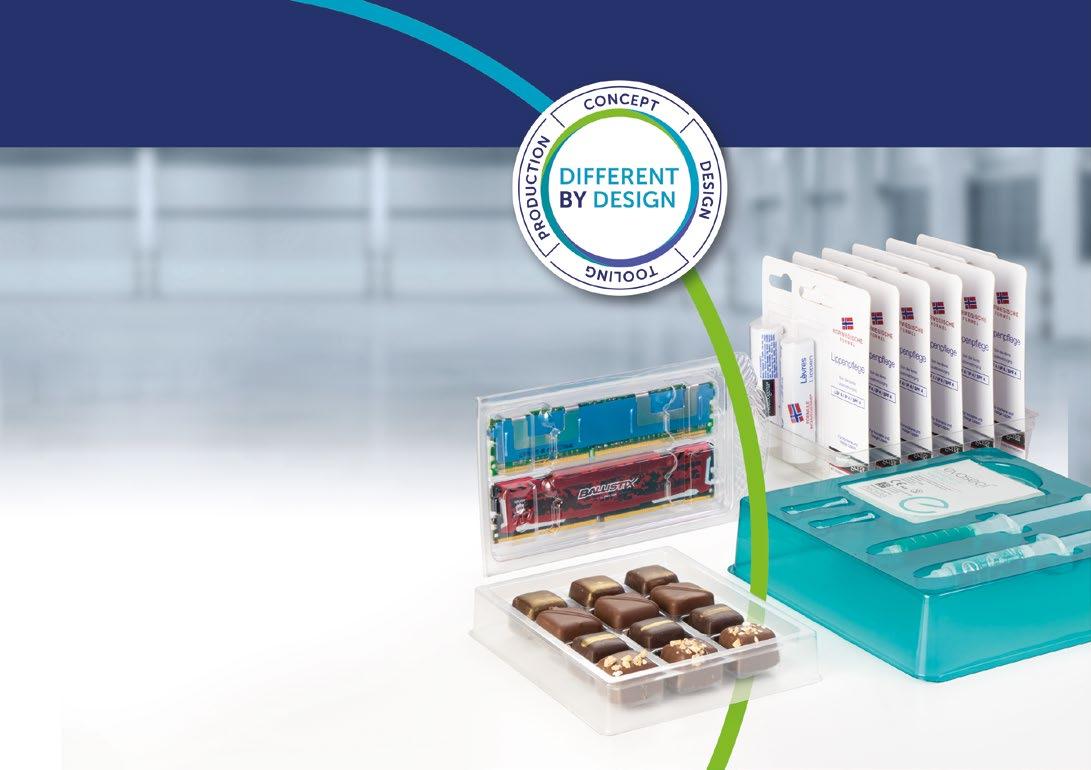
Sealing labels are manufactured with strong adhesives that are resistant to water, heat and solvents, and can be printed for extra security or branding purposes. The trademarked Label-Lock range from Mercian Labels even reveals an ‘opened’ message on the pack once the label has been removed and can be customised according to the specific application.
Printing for pharma The onus is on the printing company to produce fault-free labels and packaging in this highly regulated sector. The exact requirements imposed depend on the type of pharmaceutical product. Narcotic drugs and patent-protected prescription drugs are tightly controlled with only certified pharma converters allowed to manufacture labels and packaging. Morphine, benzodiazepine and similar high-value narcotic drugs are, in addition to control by pharmaceutical regulators, also subject to law enforcement supervision. Prescription drugs are vulnerable to counterfeiting and therefore of high value to the brand owner, so must also be produced at printing companies that specialise in pharma. The labels and outer packaging usually display basic graphics, in one or two colours with low ink coverage, to identify the contents at a glance, with multiple types of codes and often tamper-evident labels or smart technology added for safety, traceability and brand protection. In print factories where these types of pharmaceuticals products are made, strict regimes are in place with complete line clearance implemented between jobs, full reporting in place and every label and pack accounted for.
Labels and cartons for prescription drugs that are out of patent can be printed at general converters able to comply with regulations. Again, the design will be fairly simple, but the control level is less demanding. When it comes to over-the-counter medicines and nutraceuticals, the level of control is lower, and a much wider range of converters are active in this market. In addition, these products are competing for the consumers’ attention, so more complex graphics are deployed for instant shelf appeal. High-value products will still need to be protected against counterfeiting.
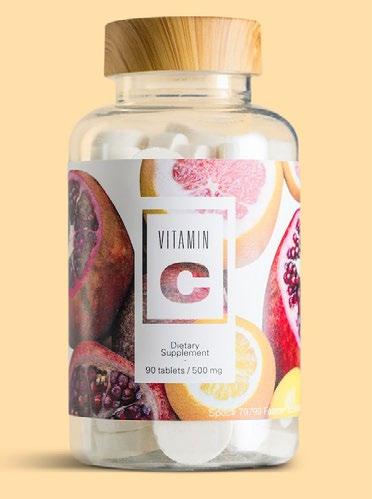
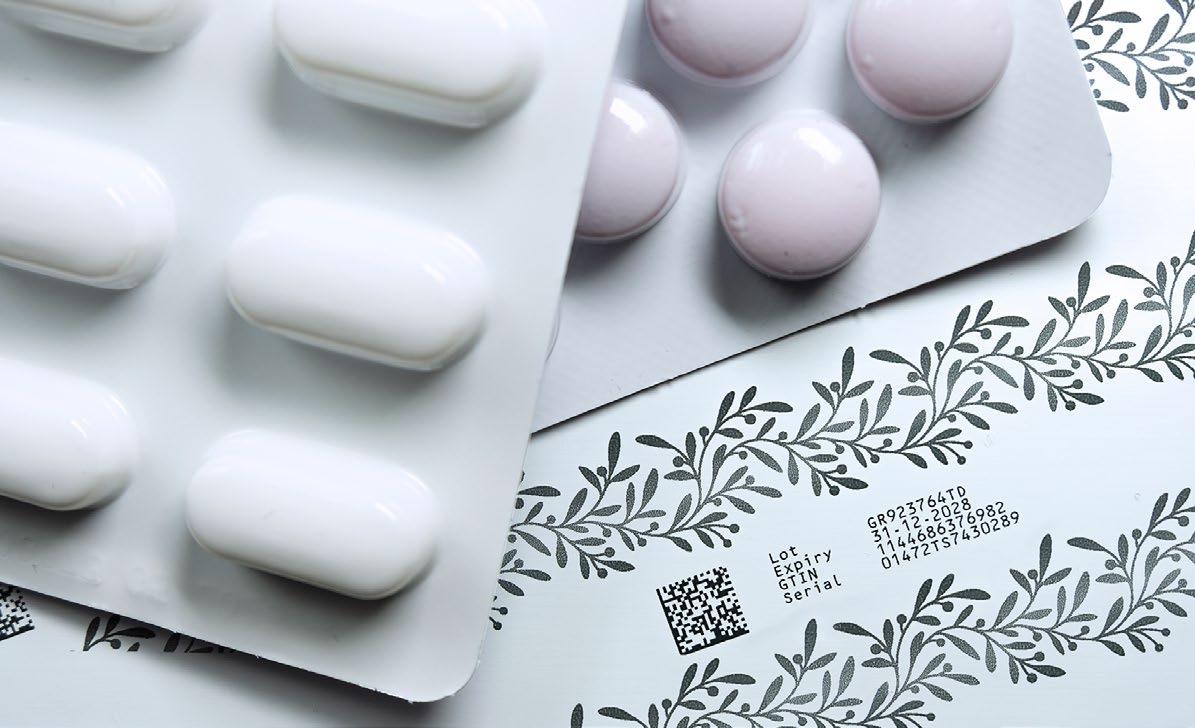