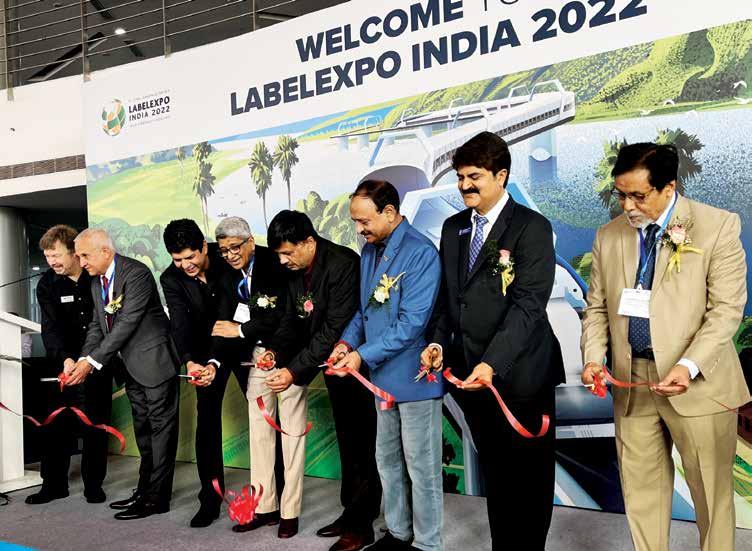
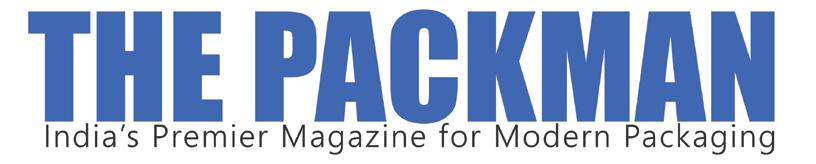
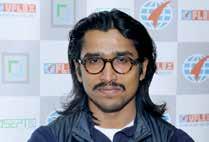
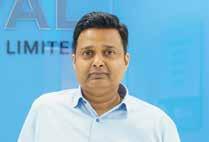
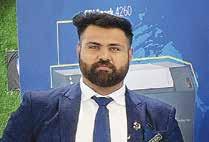

Labelexpo India 2022, South Asia’s leading exhibition for the labels and packaging printing industry, from 10 to 13 November 2022 at India Expo Mart & Centre, Greater Noida markedly exceeded both exhibitors’ and visitors’ expectations and also prompted satisfied face in the organizer Tarsus.
Packed with more than 250 exhibitors, this year’s show had more new technol ogy than ever before and was an unmissable opportunity to experience the latest launches from leading industry names including Avery Dennison, BST, GEW HP, Konica Minolta, Bobst, DuPont, Esko, Miraclon, Monotech Systems and more.
The show was opened by Pradeep Saroha, event director of Labelexpo India; Rajesh Nema, president of Labels Manufacturers Association of India (LMAI); Jaideep Singh, honorary secretary, LMAI; Raveendra Joshi, president of All India Federation of Master Printers; Kamal Mohan Chopra, president, World Print & Communication Forum; AVPS Chakravarthi, global ambassador of World Packaging Organisation; Mohammad Shamsul Islam, senior vice chairman of Printing Industry Association of Bangladesh; Peter Deckker, president of Sri Lanka Association of Printers; and Andy Thomas-Emans, strategic director of Tarsus Labels, Packaging and Brand Print Group.
Saroha said, “We are very happy to be back with Labelexpo India after a gap of four years. Despite the challenges of Covid, the label and package printing industry did not stop innovating in the past couple of years. We are thankful to all of our exhibitors for their unwavering support for Labelexpo India. This year’s show is packed with innovation and technology developments that took place in the past four years.”
Rajesh Nema, president of Labels Manufacturers Association of India, said, “I am very happy to be a part of the opening ceremony of Labelexpo India 2022. I look forward to meeting the whole label fraternity during the four-day show. The show is a crucial event for growth and development of the labels and packaging printing industry. The Tarsus team has done an excellent job of organizing the show. I am
looking forward to seeing new technologies and products from some of the leading manufacturers in the industry.”
The 4-day show featured new exhibitors, live demonstrations and new developments in label and packaging technologies. Proving that digital printing has advanced from a complementary technology to a competitive one, India has adopted the conversion to digital printing quicker than anyone could have predicted. Labelexpo India 2022 featured demonstrations from key digital players such as HP, Konica Minolta, Esko, Epson, Domino, Pulisi and Monotech.
The show was a catalyst for machinery launches and numerous sales achieved by many of the 250 exhibitors on the show floor to Indian converters, including Indian company Monotech Systems, which sold a ColorAqua Hybrid to Wonderpac, one of the prominent manufacturers and exporters of an exclusive range of labels and hologram; followed by HP Indigo, which sold an HP Indigo 6K to the same company; Esko, which sold CDI Spark 426 and XPS Crystal 4260 to VeePee Graphic Solutions, CDI Spark 4260 and Crystal XPS 4260 to Alpha Flex, CDI Spark 4260-C with flexo and imaging engine to Anam Graphic Images; Acme Rolltech, which launched its new engraving technology called Advanced Channel Engraving (ACE ); H.B. Fuller, which launched its first filled hot melt pressure sensitive adhesive (PSA) to address tape and label die-cutting challenges, amongst others.
Also reflecting the buoyant mood of the industry, several strategic partnerships were announced, including Domino and UV Graphic Technologies, who have en tered into an agreement for Domino N610i digital hybrid label solution. UV Graphic demonstrated its new hybrid press with built-in digital embellishment capability, The Dominator. N610 integration digital module has been built into this new hybrid press for enabling digital functionality.
Hazarika, Editor, editor@thepackman.inLabelexpo India 2022 reports a successful show 3
Lakanto brings Monkfruit-based sweetener to India 6
TekniPlex launches PCR dip tube 6
In conversation with Sachit and Tarun Katyal of Anupama Printing Solutions 8
“The world can no longer deny the importance of sustainability” –Rahul Nene, Huhtamaki India 12 Pack the ‘sustainable way’ 14 Mondi develops recyclable high-barrier packaging for Felleskjopet 16
World premiere of Heidelberg Speedmaster XL 106 18
Avery Dennison inaugurates Rs 250-crore plant in Greater Noida 20
Kwality Offset Printers wins Flexo Tech Award 21
Fineflexo focuses on productivity with a brand-new Gallus Labelmaster 22
Sigma Middle East Labels installs Lombardi flexo press 23
Printrays installs Brotech DL420 24
Konica Minolta to unveil AccurioLabel 400 in India soon 26
Apex International displays GTT and anilox technologies 26
Standard Printers Providers promotes Taiyo flexo presses 27 HP introduces innovative printing solutions 28
Alpha Flex invests in CDI Spark 4260, Crystal XPS 4260 28
Acme Rolltec launches new engraving technology 29
Chiripal Poly Films commissions BOPET line and Bobst metallizer in Hyderabad 30
If we are successful in collecting plastic waste, recycling will not be a problem –Ashok Chaturvedi 33
“There is positive sentiment in the flexible packaging industry despite shrinking margins” – Gaurav Talwar 34
Flexible packaging has revolutionized the Indian milk industry – RS Sodhi 36
Daetwyler SwissTec India doubles production capacity 37
Max Speciality Films in Punjab invests in Bobst Master CO 8000 37
Flexible packaging – moving to a sustainable reincarnation 38 Huhtamaki, Milliken partner to design for circularity 39
Kamakshi Südpack’s new plant launched in Ahmedabad 40
Brückner Group Asia-Pacific officially opened 41
Serialization beyond compliance 42
How mineral oil-based inks contradict the concept of food safety 44 Yansefu boosts production of innovative mono-component polyurethane adhesives 45
Toyo Ink to double laminating adhesives production capacity in Asia 46
Inkmaker installs new Inktrasyst system in Beijing 46
H.B. Fuller launches adhesive for precise die-cutting 48
Storopack introduces FOAMplus protective packaging solution 49
Flex Films exhibits its range of innovative packaging films at Pack Expo 2022 50 K 2022 – Trade fair results fulfill highest expectations 54
GMS Pacific appointed distributor for Domino N730i label press 56
Comexi enters digital printing sector with new digiflex press 56
Heidelberg India appoints Kapil Dev 57 Huhtamaki India appoints Dhananjay Salunkhe as India managing director 57
Lakanto, a leading global brand from Saraya Japan has brought the benefits of Monkfruit-based sweetener to Indian consumers. Lakanto comes from the house of Saraya, which is into manufacturing and sales of health and hygiene products and services. The company is a global leader when it comes to consultation on food and environmental sanitation and development. It is one of the leading names in the manufacturing of natural sweeteners worldwide. In India, the brand is part of Saraya-Mystair Hygiene.
The story of Monkfruit dates back over a thousand years in remote mountain highlands of Asia, where monks discovered a fruit that was prized for its sweet ness and rare abilities to raise ‘chi’ or ‘life energy’. This sacred fruit was named ‘Monkfruit’ and was used for centuries to increase chi and well-being, earning it the nickname ‘The Immortals’ fruit’.
The company claims that Lakanto Monkfruit Sweeten
ers have zero calories, zero net carbs, a low glycemic index and are keto and paleo-friendly. They are report edly great for both diabetics and those looking to live a healthier lifestyle.
Sweetener industry is now not limited to tea and coffee and expanding its usage to baking and cook ing. The brand has made a conscious effort to make the switch from sugar as convenient as possible by offering a 1:1 ratio for replacing sugar in all forms of consumption. The sweetener is ideal for cooking and baking because it mimics the sweetness of sugar by combining fruit extract and erythritol.
One of the major reasons for success of Lakanto globally stems from the fact that the sweetener doesn’t compromise on taste in the name of health, the company says.
Rajesh Gupta, CEO; and Vipul Sachdeva, India busi ness head, Lakanto India, said, “We are quite excited
about providing our products to customers in India. The sweetener industry in India is going through a dynamic shift from diabetic-centric to wellness and lifestyle oriented. Our goal is to bring ‘chi’ to all life by creating innovative, delicious, sugar-free products. We inspire people to reach their highest potential in health and wellness by helping them discover their ‘chi’. Our organic Monk fruit sweetener is a symbol of our devotion to quality ingredients and our commitment to respecting the environment. Since we completely avoid pesticides in our monk fruit farms, customers can freely choose any Lakanto product, regardless of the organic certification.” z
TekniPlex Consumer Products has intro duced a new PCR dip tube in European markets that can be made of up to 100% post-consumer recycled content. Designed for use in industrial aerosol and household cleaning product applications, the company says that its ProTecFlow dip tube offers a reduced environmental impact compared to dispensing tubing products made from virgin materials, while maintaining the same high-quality performance characteristics.
“Consumers are increasingly calling on brand owners to provide more eco-friendly products and packaging,” said Dirk De Mulder, sales di rector for the liners business in Europe and Asia. “Producing dip tubing with virgin materials is an energy-intensive process. A dip tube made of PCR reduces both natural resources usage and overall environmental impact. ProTecFlow is an example of our commitment to supporting a circular economy model.” z
Anupama Printing Solutions is among the largest prepress service providers in India having plants across two sites in North India. Sachit Katyal, chief operating officer; and Tarun Katyal, director of Anupama Printing Solutions get candid about their business during an interview and share interesting insights about the flexo industry. The Katyals also speak about the contribution of Miraclon’s Kodak Flexcel NX solutions in the success of their business. Here is an excerpt from the interview.
Describe the journey of Anupama Printing Solutions.
Sachit Katyal: Our business was into the trading of consumables for the offset printing industry. In 2008 we visited drupa with a plan to grow the business and made the investment in a Basys CtCP imaging device. We later added more imaging equipment, including a Kodak imager in 2012.
After growing the offset trade shop business and building up a steady base of clients, we were planning to diversify around 2014 when we discussed with the then-Kodak team the possibilities in flexo, who played a consultative role in helping us understand the capabilities of Flexcel NX technology.
Our initial interest in Flexcel NX technology was brought up by a need to cater to customers that required DITR film for certain print applications. When we installed the Flexcel NX Mid system in 2015, we got a really good response and support from these DITR customers as well as flexo converters that we supplied Flexcel NX plates to. As our newly diversified business grew, we added more capacity with an investment in the Flexcel NX 4260 system. Both these systems are at our Delhi-NCR unit.
Our third Flexcel NX, a mid-size configuration, is now running at our Baddi unit to provide quick support to our local customers in that region. All three Flexcel NX systems are hybrid in nature, capable of imaging for flexo as well as offset. We have 60 employees across our both sites.
What prompted the expansion of your service to wide web flexible packaging players?
Tarun Katyal: Our primary customer base was narrow and mid-web customers. However, as the business expanded, we developed expertise to also supply to wide web flexo converters. This allowed for better optimization of resources and grow our market.
What would you say are the keys to the growth of your business?
Sachit Katyal: Our ability to respond to market de
mands and provide quality service. Our investments into wider imaging device sizes and opening up a new location at Baddi are examples of how our business has responded to market demands and customer needs.
How important is it to build contingencies in business?
Tarun Katyal: During a very dynamic period at the beginning of the pandemic, we were able to navigate through multiple challenges. Having backup equipment to keep production on track, having a determined and involved internal team that went above and beyond to deliver on customer promises, and having supportive customers who collaborated closely to maneuver through issues.
Even now, we run multiple shifts to deliver on cus tomer promises and to ensure that we always meet or beat expectations. Speed of turnaround is one of the most critical pieces in this line of business. Hav
“Our focus is on the consistent improvement of prepress to stay ahead of the curve. There is a higher collaboration between us and our customers to identify the best approach towards achieving excellent shelf impact, which means we need to work closely during the prepress stage and chalk out innovative methods to push the bar” – Tarun Katyal
ing multiple hybrid imaging devices also allows us to further enhance our capabilities to take on probable contingencies that may arise.
What services and products do you offer?
Sachit Katyal: In the offset space, we are a plate bureau that can supply thermal CtP as well as CtCP plates. In flexo, we can supply digital flexo technology like Kodak Flexcel NX plates from Miraclon, analog flexo, LAMS as well as letterpress plates and film.
What investments in software have you made over time?
Tarun Katyal: With a growing business, we invested in the Esko automation engine + Artpro+ in 2020, which helped us improve our efficiencies in pre-press significantly. The combined automation option also helps us reduce manual error to a large extent.
Which businesses would form your customer base?
Sachit Katyal: We cater to label converters, corruga tion, lamitubes, offset printing, line jobs, paper cups, wide web flexibles. There is significant growth in labels and lamitubes, especially in the pharma and cosmetics space. This is due to an organic growth run, increased consumption and the opening up of new markets, and the influx of new brands into these segments.
Tarun Katyal: Our focus is on the consistent improve ment of prepress to stay ahead of the curve. There is a higher collaboration between us and our customers to identify the best approach towards achieving excellent shelf impact, which means we need to work closely during the prepress stage and chalk out innovative methods to push the bar. This allows both, us and our customers, to differentiate ourselves and also bring about value addition to the packaging.
It’s equally important to understand printing equipment capabilities, which helps us in optimizing prepress for the job, which may otherwise lead to complications if not taken care of. Another element of consulta tive relationship-building we bring to the equation is checking in with our customers on the performance of our plates from time to time, which brings in more confidence on our support capabilities.
We have received samples of offset jobs which we are expected to match to flexo. While these instances are rare, we have had to develop our team to even cater to such tricky jobs.
Sachit Katyal: Reliability and efficiency are a given with Flexcel NX plates. The finest dots that enable excellent ink transfer. Quality and dot reproduction is the biggest differentiator in the narrow web segment. Difficult to prove efficiencies around ink savings or run length owing to extremely short print runs in narrow web.
The expanded tonal range that can be reproduced with Flexcel NX plates has aided in transitioning offset jobs to flexo. On a single NX plate, we can use Standard as well as Digicap NX. That helps in improved utilization and customization, so we can gang up jobs that suit different converter sites.
From a prepress point of view, it’s the simplest setup to work with. Because we can get the best results on press with the least amount of effort in prepress.
You recently expanded into Baddi. Your thoughts on Baddi as a labels and packaging hub?
Tarun Katyal: A lot of pharma companies are expand ing operations, while new ones are setting up shop, owing to conducive government policy. This has a direct bearing on the growth of label and packaging print for the pharma segment.
You have labels and narrow web, corrugation, lam itubes, as well as other specialized print service provid ers in the Baddi belt, to support the pharma industry, as well as other consumer and industrial goods that are produced in the region.
What is that one thing you think the local flexo industry needs?
Sachit Katyal: All converters would place blame for any print defect on the flexo plate before analyzing whether the press setup or any other consumable is at fault. So we have to be immediately involved even in resolution and play a guiding role. We have been able to do so with expertise gained over time, part credit of which does go to the Miraclon team for their support.
There is a need for a demo facility where trade shops as well as converters can get a deeper understanding of the fundamentals of platemaking and printing. This will help the industry progress. You can have the best and latest technology, but unless the people know how to implement it right and get the most out of it, it’s not helping much. A lot of second-hand informa tion floating around, which is dangerous and causes frequent issues. Remote support is an option, but the effectiveness of remote support relies on a technically sound operator on the other side.
What are your thoughts on Miraclon as a supplier?
Tarun Katyal: The technical applications team at Miraclon has always been extremely engaged and supportive, whether it was the resolution of prepress or on-press queries, or in upskilling our team on flexo prepress and application knowledge.
Sachit Katyal: Our focus is on technical support and marketing of our expertise, to provide even better service to the flexo industry. Our strength in prepress continues to support our value proposition. z
How do Miraclon’s Kodak Flexcel NX solutions contribute to your success?
The Packman: Please tell us about two recent developments by Huhtamaki directed towards sustainability.
Rahul Nene: At Huhtamaki, sustainability is an integral part of our strategy and everyday work. We embed sustainability in everything we do and strive to do business in a financially, environmentally, and socially responsible way. In India, we have been working on a wide range of areas when it comes to sustainability, from the product stewardship perspective and our operational footprint. Two such key developments that we have undertaken at Huhtamaki India are:
A. Drive to make our products recyclable, reusable, or compostable: Through our program called Blueloop, massive efforts are being taken across teams to develop packaging solutions that enable circularity in the flexible packaging eco-system. We have a 2030 target to make 100% of our products either recyclable, reusable, or compostable and we have been making significant progress on this front. We have been innovating to develop recyclable packaging while ensuring their robust functionality, thus leading towards fulfillment of our sustainability goals as well as those of our customers.
B. We recently established a state-of-the-art multilayered plastics recycling plant under the Huhtamaki foundation, which aims at recycling post-consumer use MLP waste that otherwise would have gone to landfills and dumping grounds. Located in Khopoli,
Maharashtra, the idea behind setting up this plant has been to recycle multi-layered plastic which is said to be difficult to recycle and hence, ends up in landfills otherwise. We have been working to collect post-consumer waste from nearby cities like Pune and have been recycling it into either value-added products or granules, which can further be used in place of virgin plastic. The focus has also been to maintain good control on the recycling process and ensure ethical processes to run the plant.
The Packman: What according to you are the challenges in the overall ecosystem in the implementation of sustainable practices?
Rahul Nene: I would not like to call out any particular aspect as a challenge, but, more of an opportunity. A
“At Huhtamaki, sustainability is an integral part of our strategy and everyday work. We embed sustainability in everything we do and strive to do business in a financially, environmentally, and socially responsible way” – Rahul Nene, sustainability head, Huhtamaki India.
lot of organizations – public and private, regulatory bodies, non-profit organizations and individuals are doing a lot many things when it comes to sustainability. What I feel is that at times, a holistic and cohesive effort is missing. Through collective actions and sharing of best practices, entities can look at tackling issues and making an impact on a larger scale, beyond their own footprint. An example of one such collective effort is the India Plastics Pact of which we are a part. Stakeholders from all sections of the plastics value chain are coming together to develop and implement strong standards and processes for managing plastics and plastic packaging. So, I would look forward to the development of more such cohesive actions in the field of sustainability.
In an interview with Rahul Nene, sustainability head, Huhtamaki India, we discuss sustainability, and how Huhtamaki has been responding to the increasing demand for sustainable and innovative technology in the packaging industry.Rahul Nene, sustainability head, Huhtamaki India
The Packman: How should the government and regulatory bodies intervene in helping the packaging industry achieve its sustainability potential?
Rahul Nene: Especially in the last six years, the regulatory bodies have been taking significant steps to implement sound practices to manage the ecosystem of plastic packaging. The plastic waste management rules, the Extended Producers’ Responsibility (EPR) mandate, ban on single-use plastics are all exam ples of these. So, this has been a great start. A key aspect that the regulatory bodies need to look at is the possibility of standardization. If policies can help encourage standardization of packaging, at least in some sectors, it could really boost the development of a circular and sustainable economy around plastic packaging. Additionally, some terms like ‘Sustainable packaging’ and ‘recycling’ end up being used loosely when not clearly defined. If regulations are able to define them in the Indian context, it will help provide
clarity and ensure that every organization stays on a common goal.
The Packman: Looking ahead, how do you think the sustainability debate will evolve in the coming years
Rahul Nene: Honestly, there is no debate anymore on sustainability. The world can no longer deny its importance of it, in fact it now remains as the single biggest agenda for the human race at large. In the coming years, I see sustainability touching professions that traditionally were not thought to be anything related to it. Today, we are seeing finance profes sionals, marketing professionals getting involved in the development of sustainable practices. I see the need for ‘sustainability’ to be a value and not a priority and I hope that we progress in that direction in the days to come.
The Packman: How do you envisage your company changing the industry in the coming years?
Rahul Nene: Packaging in itself is a concept that helps sustainability. The negative social and environmental impacts of spoilt food for example are massive and sound packaging helps avoid this. What the world of packaging is now progressing is implementation of a circular and sustainable economy, and Huhtamaki is at the forefront of this drive. Innovation has been a strength of Huhtamaki and by harnessing it, we envision ourselves to be the leader in developing sustainable packaging solutions. We look to work with our customers and other members of our value chain to develop path-breaking packaging solutions that are able to create a benchmark in the industry when it comes to sustainable packaging. At large, we look to work beyond our footprint to create a positive social impact through our products and operations. z
Asustainable approach is the need of the hour in view to providing ‘green’ future and therefore every manufacturer is now concentrating on adapting to support and create prod ucts and services in a sustainable manner. Packaging contributes to a major share of the economy and as per a recent market research published, packaging generates the maximum global waste as well. Thus, it is the responsibility of packaging manufacturers to start by taking proper steps to adapt to ‘sustainable packaging’.
The packaging industry is consumer driven and with recent demands, the importance of adapting to sus tainable awareness has increased, this has led the manufacturers to focus on their active projects which are mainly designed to look at sustainable material options for their products. Every section of the mar ket is switching to building a sustainable future or strategizing its ways to build one. Consumers too are becoming more aware of the environmental impacts of the products they consume and thus complying with the growing desire for eco-friendly products.
The Sustainable Development Goals set out by the UN in 2015 are adopted as the 2030 agenda for sustain able development in manufacturing, especially for the packaging sector. Globally, sustainability has created a great stir in the packaging world and as per recent reports by 2030, the major players will ‘go green’ with their sustainability approach which will further help to develop and build a strong customer base and gain a major portion of the market. This will lead packaging industry manufacturers to invest a lot in their products offering. Every year the manufacturers look for add ing value to the brand – sustainability adds value to the brand, apart from securing a better future, it also draws the consumer market.
Considering the pressure from the regulatory bodies for a greener and ecofriendly future end users and OEMs
are finding solutions to implement ‘smart factory’ solutions that merge automation and IT technology and help improve the life cycle of their products, transparency throughout the supply chain, increas ing efficiency, optimizing costs, and opening up new opportunities for improvement.
B&R has always addressed how companies can best meet the challenges of a sustainable future. Industry 4.0 calls for an adaptation to newer technologies and innovations for OEMs, end users and system integra tors, mainly to help them evolve through sustainable innovation. B&R offers innovative products and so lutions for all types of packaging machinery – from primary and secondary packaging to end-of-line solu tions. Innovation’s product portfolio adheres to unique requirements and helps OEM set new standards for flexible, productive, efficient packaging technology and creating adaptive machines that bring real competi tive advantages.
Today, to remain competitive, one must create a platform for continuous innovation. It is believed innovations around artificial intelligence, machine and factory automation will play an essential role in unlocking the potential of future industrial production in manufacturing sectors. They will increase produc tivity and flexibility, helping customers become more sustainable and produce closer to their end markets. All the above are related to packaging solutions which will boost more innovations by providing a sustainable approach. Small batch is a sustainable and more eco-friendly method as per recent research papers published because it doesn’t require assembly lines and large amounts of raw materials. There is very little waste involved and it doesn’t require large amounts of electricity or water.
To meet the sustainable demands of a packaging manufacturer, if we look into new inventions, the path breaker ACOPOS 6D is fully integrated into the B&R ecosystem that helps manufacturer achieve sustain able goals. ACOPOS 6D is based on the principle of magnetic levitation – shuttles with integrated perma
Toyo Ink India wishes all its patrons a very happy Diwali! May it illuminates your life with endless lights and colours.
nent magnets float over the surface of electromagnetic motor segments. The modular motor segments are 240 x 240 millimeters in size and can be arranged freely in any shape.
A variety of shuttle sizes carry payloads of 0.6 to 14 kilograms and reach speeds up to 2 meters per second. They can move freely in two-dimensional space, rotate and tilt along three axes and offer precise control over the height of levitation. Altogether, that gives them six degrees of motion control freedom. It also allows the
shuttles to be synchronized with servo axes, robots, track systems and machine vision cameras with microsecond precision.
Path planning for the shuttles occurs in a dedicated controller, connected to the machine network via POWERLINK which means it has no impact on the performance of the network or machine control system. The shuttles offer a positioning repeatability of ±5 µm, making ACOPOS 6D perfectly suited for applications with strict positioning requirements, like those for
example in the electronics packing and in the assembly of mechanical and electronic components packaging.
ACOPOS 6D offers nearly limitless possibilities in machine design yet is remarkably easy to set up. Sophisticated algorithms ensure the shuttles follow an optimal path while avoiding collisions and minimizing energy consumption. Thus, this small changes inside the manufacturing hub are the solution every packag ing manufacturer is looking for today to help create a secure and sustainable manufacturing system. z
Mondi, a global leader in packaging and paper, has developed a recyclable high-barrier packaging solution for Norwegian pet food manufacturer Felleskjøpet, that keeps material in circulation and avoids waste.
Felleskjøpet is using Mondi’s FlexiBag Recyclable, a premade mono-material polyethylene (PE) bag, to relaunch its Appetitt range of dry cat and dog foods. It will replace the previous unrecyclable multi-layer solution, delivering packaging that is designed for recycling, according to CEFLEX D4ACE guidelines, and is recyclable in existing Norwegian plastic recycling streams.
Mondi’s FlexiBag Recyclable provides excellent product protection and preserves premium pet food, thanks to its high barrier material. A slider enables easy opening and closing for the bigger bags to ensure long-lasting freshness, while a handle allows for convenient transportation. FlexiBag Recyclable has excellent print qualities that guarantee good visibility on-shelf and can communicate all product and re cycling information clearly.
Pal Wikstrom, Sales Manager Nordic Consumer Flexibles, Mondi, says: “This partnership was all about designing appealing packaging for the Appetitt pet food, meeting the consumer needs of convenience and product protection, as well as helping Felleskjøpet
meet its sustainability goals. It meant working together closely and asking all the necessary questions at each stage of the manufacturing process to deliver a solution that works for the customer, the product, the planet – and of course the pets.”
Hege Rosenhaug, Product and Development ManagerPet Food, Felleskjøpet, adds: “Our relaunched Appetitt range packed in FlexiBag Recyclable will be available in stores from October. The pet food is delivered in its best condition, it is both protected and kept fresh by the new packaging. This is an important step in our journey towards being a more environmentally responsible organization.” z
Heidelberg is once again underlining the company’s technology leadership in its core business with a world pre miere. The option to increase the printing speed of the Speedmaster XL 106 to 21,000 sheets per hour makes this high-performance system the world’s fastest sheetfed offset press and means an annual output of over 100 million prints is now also possible in folding carton production.
The press is a particularly good option for companies producing packaging in the 70 x 100 format, who are calling for ever higher machine outputs and end-toend automation. The increase in printing speed from 18,000 to 21,000 sheets per hour on the Speedmaster XL 106 is especially attractive to these users. The economic benefit is an 8 to 10% higher net output and – provided the full potential productivity is utilized – amortization in around two years.
In order to achieve this, Heidelberg has optimized some 200 components throughout the entire system, from feeder to delivery. For example, two servo motors now drive the feeder directly and, in the delivery, the weight of the gripper bars has been reduced and they have been adapted to the new printing speed to ensure stable and reliable operation.
“Right from its market launch in 2004, XL technology from Heidelberg has set the benchmark in terms of productivity, performance, and reliability for high-end applications in our sector. Heidelberg has continuously enhanced this successful machine platform ever since,” says Dr. Ludwin Monz, CEO of Heidelberg. “With the newly unveiled Speedmaster XL 106, Heidelberg is taking sheetfed offset printing performance to the next level and enabling folding carton manufacturers in particular to become more competitive.”
Cardbox Packaging has commissioned the first Speedmaster XL 106 from Heidelberg with a maximum speed of 21,000 sheets per hour, making it the world’s fastest sheetfed offset press
Cardbox Packaging, an international packaging manufacturer headquartered in the Austrian town of Wolfsberg with over 250 employees, makes highquality and technically sophisticated carton packag ing – primarily for the food, beverages, confectionery, tobacco, and cosmetics industries, and also for the healthcare market. The company enjoys a long and successful partnership with Heidelberg. Cardbox mainly uses technologies from Heidelberg when it comes to further expanding press and postpress operations at its international sites.
Consistently high productivity and maximum machine availability are among the keys to success. Whenever
possible, Cardbox maximizes the potential of the equip ment it uses. This includes the Speedmaster XL 106 that has been in operation at the Wolfsberg site since 2018. That makes Cardbox the ideal pilot user for the new Speedmaster XL 106 with its maximum speed of 21,000 sheets per hour. The company recently took this high-performance press into operation.
“Competition is fierce on the international packaging market. We make no compromises when it comes to quality, reliability, and keeping to delivery deadlines. Consistently high productivity is a key competitive factor in this regard,” says Roland Schöberl, managing director of Cardbox Packaging. “We are therefore delighted to be working with Heidelberg and piloting the new Speed master XL 106, currently the world’s fastest sheetfed offset press. Following the start-up phase, we expect it to give us a big productivity boost.” z
Signaling strong confidence in the growth of the Indian packaging industry and its long-term commitment to the Indian market, Avery Dennison, a leader in global materials science and manufacturing, has inaugurated its state-ofthe-art manufacturing facility in Greater Noida. Avery Dennison has made an investment exceeding Rs 250 crore (approximately US$ 35 million) in this plant taking its investment in India to Rs 1,000 crore plus (approximately US$ 125 million).
Spread over an area of 12 acres, the new plant will produce technologically-advanced, pressure-sensitive materials for the labeling and packaging industry, incorporating best practices available across Avery Dennison globally. The new facility is equipped with the latest high-speed coating technology and stateof-the-art coating and lamination lines, along with high-speed sliters and sheeters. The land for the new plant has been allotted to Avery Dennison by Yamuna Expressway Industrial Development Authority (YEIDA).
With this key business milestone, Avery Dennison celebrates 25 years of business operations in India and is looking for the next growth phase. Twentyfive years ago, the company was largely reliant on imports. With its increased foothold in the market, it has now moved to almost 100% localized production capability in India. With this plant, the company also plans to consolidate its manufacturing operations in order to better serve customer demands while optimizing the new technology and leveraging the improved efficiencies.
Saurabh Agarwal, senior director and general man ager, label and packaging materials, South Asia for Avery Dennison, said, “We are extremely delighted to inaugurate our world-class manufacturing facility in
Greater Noida and with this latest expansion, we are looking for the next big chapter in our growth in India. Our new facility is built on one of the most sought-after lands allotted by the UP Govt. and by expanding in UP, we will be able to serve the requirements of our customers better and also enhance the company’s production capacity to meet the growing demand of the Indian market.”
Agarwal added, “With the new state-of-the-art manu facturing plant, we will be able to deliver the kind of consistency that we have been known for – we should be only taking it to the next level now. The plant will also allow us to double our production capacity.”
Speaking to The Packman, Pankaj Bhardwaj, vice president – marketing, Asia Pacific and Sub Saharan Africa, labels and packaging materials, Avery Dennison, said, “With the current capacity of the plant, we are now well poised to cater to the majority of the growth
of the market for next three years. We have invested in a technology [coating operation] which has a very low tolerance for any deviation and is almost humantouch-free. With inbuilt robotics and automation, the machine elevates the level of safety, reliability, quality and productivity.”
Bhardwaj said that there is significant headroom for growth in the label industry in India, which has much lower per-capita consumption of pressure-sensitive labels compared to Europe, Australia, the US or even Malaysia and Thailand.
Speaking about sustainability, Bhardwaj added, “Our commitment to sustainability has really dialed up and reflects in almost everything that we do – the plant is Leed certified and we have also installed 500 KW solar panels on the roof of the plant.”
Having a presence in India for over two decades, the
The new plant will produce technologically-advanced, pressure-sensitive materials for the labeling and packaging industry, incorporating best practices available across Avery Dennison globally.
company has consistently led the way in transforming the Indian labeling and packaging industry. The company started its first plant operation in Gurgaon in 1997 with a hot melt coating line. Since then, it has expanded its operations across India in major cities – Pune, Banga lore, Kolkata, and now in Greater Noida. z
Kwality Offset Printers, a leading label specialist based in Delhi, India, has won a Flexo Tech Award (FTA) in the ‘Best Em bellishment’ category at global level. Kwality is the only Indian company to win an FTA this year. The awards ceremony was held in the UK on 12 October 2022.
Kwality Offset Printers’ Kamet Whisky label that won the award was printed with a multi-step process. The label represents three different foil shades along with 3D tactile effect on all intricate patterns and images.
The jury while appreciating the winning label, said, “The Kamet Whisky label truly stands out among other entries. Using foiling, embossing and matte effects, Kwality Offset has produced visually stunning results on the label.”
Krish Chatwal, director at Kwality Offset Printers, said, “It is always hard to put this feeling into words. Nevertheless, we are glad for such an important
and momentous occasion in our lives. It is a huge honor for us to receive the Flexotech Award for Best Embellishment of the year. We are honored to be the only Indian company to win a FlexoTech Award this year. Cheers to many more International awards and recognition.
“We thank FlexoTech for this amazing opportunity and also team Kamet Whisky (Peak Spirits India) for believing in us and partnering with us to create an international award-winning label.”
Established in 1972, Kwality Offset used to produce cartons and cups for the ice cream industry using a letterpress. A decade later it installed an offset press and entered the label printing business, producing beer labels. Since then the company has added flexo and digital technologies to its existing offset unit. And all three technologies are currently being used at its Naraina plant, Delhi, to produce a wide range of labels to cater to various customer needs. z
Fineflexo has installed a brand-new Gal lus Labelmaster flexo press at its plant in Baddi, Himachal Pradesh. Fineflexo is a joint venture between Medi Sales Group and Bhavani Group specializing in the extended supply chain of pharmaceutical business and logistics.
Ritesh Shetty, director at Fineflexo, said, “Fineflexo embodies ultimate excellence, adaptability, and ser vice. We are endlessly working to nurture and upgrade the standard of the whole self-adhesive market in the country with premium quality, performance, and JIT deliveries in our product segment. We focus on developing a robust product portfolio for our clients and fostering trust and customer satisfaction.”
In 1989, Narendra Srisrimal formed Medi Sales Group and further strengthened the operation with Bhavani Group, which Balakrishna Shetty formed in 1979. A joint venture between the two organizations extends its business gamut with Fineflexo.
Aayush Srisrimal, director at Fineflexo, said, “We are dedicated to distributing sustainable, efficient, competitively priced products that a print buyer needs. We also serve the clients with our knowledge and expertise by analyzing how their product should look so that we can prepare the best suitable labels for it and create a ‘brand appeal’ and enhance it.”
In the past, Fineflexo used to outsource its print jobs and later decided to install a Gallus Labelmaster 440 after accessing the technical advantages such as diverse substrate handling, 200 m/minute produc tion speed with registration accuracy, user-friendly operation among other features, which can add more value to their labels, tube laminates and aluminum foil printing.
Elaborating on the different business verticals and explaining the need for the press, Ritesh Shetty said, “Our core business is manufacturing roll on pilfer proof cap, pet bottles, and metal printing. We manufacture these products at our plants in Rabale Navi Mumbai and Baddi, Himachal.”
He added, “We have been into metal printing for the last four decades. However, the metal printing venture was a backward integration for caps printing. In 2009, we started manufacturing pet bottles in Baddi. Cur rently, we are manufacturing approximately two million bottles daily for the pharmaceutical segment, bottle sizes vary from 10 ml to 1 liter. In 2017, we ventured into the manufacturing of tube laminates. The Gal lus Labelmaster 440 will be used to print labels for pharma bottles, tube laminates, and aluminum foils.”
Speaking about the Gallus Labelmaster 440, Ritesh Shetty, said, “Gallus is a robust machine that gives us speed with stability. We saw the live press dem
onstration of Labelmaster 440 at ‘Avery Dennison Innovation & Knowledge Centre, Pune. However, we did analyze other label presses but eventually, we finalized Gallus Labelmaster because of Heidelberg’s reliable service support. Stable printing on composite substrates like aluminum-based laminates and plastic-based laminates at high speed, faster job changes, and quick setup times gave us confidence. To be consistent on quality, it is better to have inhouse production facilities. With the Labelmaster, we can achieve the same along with significant waste reduction controls and JIT deliveries with the perfect finish and print quality.”
“The Labelmaster is designed to print on everything that we require. With this, we print on supported and unsupported labels, aluminum foils, light cardboard, tube laminates, shrink sleeves, IML, etc. Labelmaster can handle a wide range of materials with different micron calipers. It was one of the reasons for choosing this press. The press is user-friendly, the setup time is significantly less, and the registration is at par. Its’ a beautiful press, and we got everything we expected from Gallus,” added Shetty.
Aayush Srisrimal, said, “Fineflexo is working towards being the leading supplier of labels in India. We focus on developing a robust product portfolio for our clients and fostering trust and customer satisfaction.”
“We offer smart label solutions through close col laboration with our customers, from idea to finished product. As a comprehensive printing company, we want to be a part of shaping the present and future of label and packaging solutions. With dedicated employees who have ambition and a great passion for their work, we print labels for everyone, today and in the future. We create art with a scientific approach and top-notch technology. We believe that a label makes a product’s first impression and is a significant factor in consumer decision-making.”
The packaging for tablets and capsules requires different types of foils and laminates. A new division started by the Fineflexo group, Finepharmapack, allows them to add aluminum-based films and foils to its product offering.
This includes a 1,300 mm wide coating and laminator from Italy capable of producing 12,000 tonnes every year. Ritesh Shetty, said, “We have an ambitious project to manufacture all kinds of foils needed for pharmaceutical packaging, like blister foils, includ ing 90 varieties of cold-form foils, child-resistant, senior-friendly, peel-push, suppository/tropical, and adhesive laminates.
“The project is presumed to be complete by the second quarter of 2023. After the completion of the project,
we will be a one-stop solution for all pharmaceutical needs. Excellent sales and service with a dedicated team and technical consultation are the key factors in making our decision for Gallus Labelmaster. We are proud to be associated with Heidelberg India and Gallus.”
Narendra Kulkarni, regional product manager, Gallus (Asia), said, “The versatile Gallus Labelmaster assists the user in reduction of cost per label. An Extremely shorter web path of just 1.4 m between printing units and a material reduction with the ‘Labelmaster – 2 platform’ reduces the production wastage.”
Gallus Labelmaster has automation functions such as job pre-set, job data storage, format length corrections, print cylinder with bearer ring technology, and integrated direct servo-driven systems, which helps users to do easy job setup and produce materials from 15 microns to 450 microns, even more. Water-cooled impression rollers and electronic cabinets benefit the user with a maintenance-free operation.
“Technology and automation are the keys to success in any business, and the Gallus Labelmaster helps in our growth. With this thought, we went ahead with the latest generation Gallus Labelmaster which makes us ‘future ready’. This has given us great peace of mind that we can now focus on building the business without worrying about machine issues, we believe in the Gallus quality,” concluded Shetty. z
Sigma Middle East Labels Industries, based in the UAE, has installed a Lombardi Syn chroline 530 flexo press. The machine was supplied by Vinsak, a distributor of Lombardi presses in the region. Vinsak is a supplier of printing and packag ing technologies in India, Africa, and the Middle East. Sigma is one of the leading manufacturers of selfadhesive labels in the industry since 2010 started by Jagannath M Wagle. Starting with 4-color printing,
Sigma provides multicolored label printing on narrow web flexo presses.
Sigma specializes in several label types including self-adhesive and shrink sleeves for markets such as product labels, industrial labels, price stickers, cargo labels with facilities like cold foil stamping, lamination, and UV printing in sheet/roll form and supplies them to various industries as pharma, cargo, industry, steel
industry, food industry, plastic industry.
“In Vinsak we found a reliable partner who has sup ported us in deciding the specifications of the equip ment to suit our current and future needs as well to supply the correct tooling, ancillaries as well as complete installation and training support of this project and enabled us to start production in the shortest possible time,” said Wagle.
“Their consultative approach is very different to some of the hard-nosed sales teams with whom we have dealt in the past. In fact, our decision to move from another Global brand to Lombardi was greatly driven by the service provided by Vinsak.”
Vinsak supplied the Lombardi Synchroline 530 mm wide 8-color flexo press with options of web cleaner, double-sided corona treatment, turn bar, cold foil, UV dryer and hot air tunnel for meeting the diversified needs of the client in narrow web shrink sleeve and IML production. The press, with its capability to print on a wide variety of substrates from 12-micron film to 450 GSM board. Its maximum repeat of 1000mm is the largest in the industry.
Lombardi Converting Machinery is a 30-year-old Italian company and is known for the production and distribution, narrow web and wide web flexographic in-line presses. With this new installation, the UAE alone has 10 machines installed in the last 4 years. All over, Lombardi has installed more than 500 inline flexo presses globally with more than 125 being sold in the Vinsak territories. Lombardi has also recently launched its I2 series of Mid and wide web inline Flexo presses for flexible packaging. z
Printrays, manufacturer of labels, monocartons and corrugated board packag ing based in Jalandhar, has been on a continuous growth path. The company has been steadily adding capacity and expanding its product offerings in the rapidly growing and fast evolving packaging industry. Recently, the company installed a Brotech finishing and converting machine DL420 to enhance its converting capabilities to include IML, shrink sleeves, flexible packaging and pre-folded inserts. Printrays is run by father-son duo Vikrant Kapoor and Ankit Kapoor.
Ankit Kapoor, partner at Printrays, says, “We are satisfied with the Brotech. The Weldon engineers have done a prompt and efficient installation. We look forward to a very fruitful ongoing association with both Weldon and Brotech.”
The sale and installation of the machine was handled by Brotech’s New Delhi-based agent Weldon Celloplast. Kanwardeep Sahni, managing director of Weldon, said, “Printrays has been steadily growing to add to their vast product range. They have been carefully evaluating their options for converting equipment. We are happy that they selected the Brotech DL420.”
The Brotech DL420 features semi rotary die-cutting unit and a conveyor. It is suitable for offline finish ing of in-mold labels and other varieties of labels, according to the company. The machine is manu factured and supplied by Brotech Digital Graphics, with headquarter in Shenzhen, China. Brotech has a newly established state-of-the-art modern manu facturing facility in Zhenjiang (near Shanghai), and subsidiary offices and show rooms in Italy, USA, Mexico and Thailand.
Ramon Lee, managing director of Brotech, said, “Printrays is a deeply committed converter of labels and packaging. We are proud to have them as a valuable customer.” z
Konica Minolta showcased its AccurioLabel 230 digital label press and Accurio Pro workflow for digital label production process at Labelexpo India, Greater Noida, from 10 to 13 November 2022. The company also displayed a digital die-cutting solution at its stand. The company also printed live jobs of customers on the AccurioLabel 230 digital label press at Labelexpo India 2022.
AccurioLabel 230 is the latest roll-to-roll digital label press from Konica Minolta. The company recently celebrated the 1000th installation of its AccurioLabel digital label printing press in less than seven years after entering the labels market. The AccurioLabel press of fers an affordable entry to high-quality digital printing. The press was originally targeted at small to mid-size label converters but is now more widely accepted by various label converters including large-size converters.
“Ever since we entered the labels market, we have been launching new digital label presses every 1-2 years. This shows Konica Minolta’s commitment to the label industry,” said Vijay Kamat, national product marketing manager, industrial print, at Konica Minolta. “Very soon we are going to launch AccurioLabel 400
in India which is a CMYK + White digital label press. This press has already been launched in the US. At the event, we are displaying samples printed on the AccurioLabel 400.”
The AccurioLabel 400 incorporates all of Konica Minolta’s technology, including the Intelligent Quality
Optimizer (IQ-520) color management functionality for real-time color stability and registration control. The new press features a fifth well for white toner to expand creative label applications, plus a resolution equivalent to 3,600 x 2,400 DPI and many automated control features for highly productive output. z
– Manash DasApex International displayed a range of products during the seventh edition of Labelexpo India, organized at the India Expo Centre, Greater Noida, from 10 to 13 Novem ber. “Since it is a label show, we are displaying our
products from the perspective of the label industry. We are displaying our wide range of anilox and our unique technology called Genetic Transfer Technol ogy (GTT). GTT is a patented technology from Apex, which provides a lot of benefits to customers,” said
Mangesh Bhise, sales director, Asia-Pacific and ME, Apex International,
“GTT was launched almost a decade ago. We are always exploring new capabilities to do more with the
GTT technology,” Bhise added. Apex International is one of the global leaders in anilox technology offering products for labels as well as sectors such as the wide web, corrugation, coatings and offset. Its product offering includes anilox, sleeves, glue set, metering products and print maintenance solutions.
Apex’s FlexoKITE is a state of art, fully equipped flexo facility that was designed and set up to provide a sup portive base for the flexo industry in Asia. FlexoKITE runs a fully-equipped integrated workflow of the latest-version equipment from Apex International (anilox), Bobst (inline flexo press), DuPont (plate, Cyrel Fast thermal plate-making equipment), and Esko (prepress).
“FlexoKITE can offer live dedicated training or sup port to visitors at the state-of-the-art Apex facility in Nashik India or remotely through web links and webinars ensuring that all locations can benefit from the opportunity. The flexo technical center runs a fully integrated workflow including the latest flexo equip
ment and can take a converter completely through the flexo process – from design idea through the finished printed label,” concluded Bhise. z
– Manash Das
At Labelexpo India 2022, Standard Print ers Providers which represents Taiyo in India highlighted state-of-the-art Taiyo shaft-less flexo narrow web label presses capable of handling a wide range of substrates including paper, films, light-weight cartons, and laminates with high productivity and ease of operation.
Standard Printers Providers is a multi-product company having over 40 years of standing in the graphic machinery market. The company deals in a wide variety and range of imported printing and packaging machines – Taiyo-high speed servo driven UV flexo press for labels, films, laminates, mono cartons, etc. z
At Labelexpo India 2022, HP Indigo in collaboration with Technova Imaging Solutions showcased innovative and engaging printing solutions for the growing and dif ferentiating labels and packaging businesses. HP featured live demonstrations from the entire HP label and packaging solutions portfolio including workflow, printing, and converting. This included the latest tools and innovations for top-quality printing of labels, shrink sleeves, and flexible packaging in its wideranging portfolio.
In addition to machines and innovations being dis played at the show, HP also showcased around 250 live job samples produced by its customers in India. “At Labelexpo India, we are showcasing interesting and unique projects implemented by our esteemed HP Indigo users in India. We have a team of experts who work with brand owners untiringly and look at what new can be done with our machines. Today we are working with several brands who walk in to see what new can be done on our machines which then are translated into businesses for converters who are using our machines,” said A Appadurai, country man ager, Indigo and Inkjet Business Solutions, HP India.
Another attraction of the HP stand was the HP Indigo 6K digital press. “We have installed over 2000 HP Indigo 6K digital presses across the world. One of the biggest features of this press is its automation in terms of color management. The press offers faster time-to-color with the most advanced color-matching tool in the industry – HP Indigo Spot Master. The press can achieve perfect color registration with HP Indigo
One Shot Color technology,” said Appadurai.
HP also hosted live sessions where its industry experts took visitors through a journey of growth, new tech nologies, and transforming businesses, concluding with a live demonstration on how to produce a digital label or shrink sleeve in minutes. z
– Manash DasOn the first day of Labelexpo India 2022, Esko announced the installation of a CDI Spark 4260 and a Crystal XPS 4260 at Delhi-based pre-press company, Alpha Flex. Raghav Madan, managing partner, Alpha Flex,
said that the latest addition from Esko will help them deliver consistent results to their customers. In addition, the CDI Crystal 4260 XPS reduces training requirements and increases operator efficiency and better throughput.”
Alpha Flex was earlier using UV lamp technology for producing plates but was not happy with the output and consistency. Thus, the company was looking for a technology that could provide a uniform and strong intensity. However, we are now witnessing this with
the LED-based technology. It is more consistent and it is a fully flat top technology. We are now able to produce high-quality flexographic plates,” Madan said.
“Alpha Flex is a company that deals with high-quality flexo plates. Along with the CDI Spark 4260, the company invested in Esko’s CDI Crystal XPS 4260. It is for the first time that both systems are being installed together in Delhi-NCR. There are around 12 such machines installed in India so far,” Karan Talwar,
South Asia, Esko, said. z
At Labelexpo India 2022, Acme Rolltech launched its new engraving technology called Advanced Channel Engraving (ACE). “Under this technology, we are showcasing four new structures – ACE Ecell, ACE Xcell, ACE Hex and ACE Xtm. These are special structures that help in providing HD printing, improved ink release, and extended life span. They are also able to address cer tain issues that are faced by flexo printers – pinholing, mottling etc. specifically with UV inks by reducing those significantly. These structures also help in increasing ink efficiency by delivering better depth with low ink consumption and are much easier to clean,” said Sandeep Sharma, director, Acme Rolltech.
At the event, the company also promoted its ATAC or Acme Tactile high-density anilox rolls, which offer the highest release of lacquers and varnishes available in flexo printing. Launched just a year ago, this is already a huge success in the market for customers looking for raised effects like screen. Another product promoted by the company at the event is Acme high-density white or AHDW for high-density white and AHDC or Acme high-density color. AHDW or acme high-density white is a special roll for high opacity white ink printing in a single pass for achieving high deposition and smooth flow of white.
In addition, the company also promoted its Refurbish
ment Programme at the event. “Under the Refurbish ment Programme, we refurbish the old rolls of our customers. It is a sustainability initiative by us wherein we ensure that old rolls lying at the dump yard of our customers are not wasted. The refurbished rolls are as good as the new ones and offer the same quality and efficiency. This has turned out to be a very successful program for our customers and us alike,” said Sharma.
A pioneer in ceramic anilox rolls and sleeves, Acme Rolltech manufactures ceramic rolls and sleeves, refurbish old rolls, and offers cleaning solutions and roll auditing services. The company caters to various markets and industries such as narrow web flexo, offset coating, corrugation, CI flexo, and specialty coating applications. z
Chiripal Poly Films has commissioned a new BOPET line at its Hyderabad plant. The 8.7-meter line will double Chiripal’s BOPET film capacity and boost its reach to domestic and international markets with specialty products including matte BOPET and twist-grade films, and in-line coated products. Our editor Mahan Hazarika recently visited Chiripal’s Hyderabad plant. Here is a report.
Chiripal Poly Films recently commissioned a new BOPET line at its Hyderabad plant. The 8.7-meter line will double Chiripal’s BOPET film capacity and boost its reach to domestic and international markets with specialty products including matte BOPET and twist-grade films, and in-line coated products. Sumant Singhal, CEO of Chiripal Poly Films said that the new line is in line with the company’s decision to double its capacity –both BOPP and BOPET – by 2024. This is Chiripal’s second BOPET line – the first one already running at the company’s Ahmedabad plant.
A decade ago, Chiripal Poly Films started as a singlelocation, single-product company with a small but committed team. In just a decade, it has grown into a significant player in film manufacturing both in India and globally. Today it produces multiple products with a global footprint in more than 50 countries clocking a turnover exceeding Rs 3,500 crore.
Earlier this year, the company celebrated its 10th
anniversary. In the last 10 years, the company has overcome many challenges and achieved several successes and milestones. In 2021, the company inaugurated its latest state-of-the-art film manufac turing plant in Hyderabad which currently employs around 600 employees. The company’s Ahmedabad plant employs around 1,000 employees.
In line with the 2024 goals, the company has further investments planned. The company is investing around Rs 1,000 crore in the Hyderabad plant of which 8085% has already been utilized where it commissioned a BOPP line last year and the BOPET line in September 2022. The company will utilize the remaining amount to commission a CPP line at the plant in early 2023.
The strategic location of the new plant, spread over an area of 35 acres, will help Chiripal to cater to the extreme Southern as well as Eastern markets. “It will be a new geographical market added to our portfolio. Hyderabad and its surrounding areas have huge consumers of BOPP, BOPET and CPP films. The demand for packaging films has been growing at a fast pace in Southern India over the last few years and there were no packaging film plants situated in this part of the country to cater to this demand. Even in Hyderabad, there were no BOPP/BOPET lines until we started it last year – we are the first to start BOPP/ BOPET lines in Hyderabad.
“The decision to start a new plant in Hyderabad was an outcome of our desire to be closer to these markets and provide world-class products to our customers. Another reason was to become multi-location to mitigate business continuity risks of operating from a single site,” said Singhal.
The new line will increase the company’s overall BOPET capacity to around 75,000 MT per year. Currently, the company has an annual capacity to manufacture 133,000 MT BOPP, 40,000 MT BOPET, and 220,000 MT PET resin in addition to value-added capabilities of metalizing and coating.
In addition to the BOPP line that was commissioned last year, and the BOPET line this year, Chiripal has also commissioned three Bobst metallizers and a host of other machinery at the Hyderabad plant. Another
Bobst metallizer is planned for the Hyderabad plant which will be commissioned along with the CPP line. This will increase the number of Bobst metallizers at the plant to four. Singhal added that Chiripal is currently the second-largest producer of metalized films in the country. The Hyderabad plant currently produces 36,000 tonnes metalized films a year while the Ahmedabad plant also produces a similar volume taking the overall production of the company to around 68,000 tonnes a year.
According to Singhal, Chiripal has mapped out a wellplanned expansion strategy for the coming years. “In addition to the capacity expansion of film lines, we also plan to ramp up the capacity of our bottle-grade PET resin and chip production as well as our coating line. We are also diversifying with a greenfield aluminum foil plant. The investment phase for these all will be over in 3-4 years from now. The investment will help us not only in increasing our capacity but also in introducing new products and substrates in addition to adding new markets. We will be able to add more value to our customers by supplying almost all kinds of flexible packaging substrates required by them. Once the investment phase is over, we will clock a turnover of Rs 6,000-6,500 crore by 2027,” said Singhal.
As new and more sustainable structures are being developed in India, several Brückner and Dornier film
lines are on order. While several have been recently installed, some are under installation or about to be installed. Speaking about the increased film line installations in the country, Singhal said, “As far as film capacity installation is concerned, companies are investing heavily and in coming days, more invest ments will come up. However, there is no denying that this may eventually lead to over-capacity. Hence, along with capacity expansion, it is also important that the packaging film industry focuses on exports as well. Export markets provide ample opportunities for specialty products and high-quality films. So, the industry as a whole should ensure that it is capable of exporting a good volume to international markets so that the balance remains maintained.”
Chiripal exports around 3,000 tonnes of films a month which is roughly 30% of the total film volume that it
produces every month. Going ahead, the company aims to add another 2,500 tonnes per month to its export volume.
Sustainable practices at its manufacturing plants is a critical element of Chiripal’s sustainability com mitments. The company ensures that it maintains momentum in reaching ESG ambitions across all its plants. At present, the company has five recycling plants from Erema – two in Hyderabad and three in Ahmedabad – these are used to recycle all film wastes generated in the plants. In addition, the company is setting up a facility at its Ahmedabad plant to demetallize scraped metallized films allowing its reuse or producing plastic granules. After Ahmedabad, a similar facility will be set up at the Hyderabad plant as well. z
At the 9th Speciality Films & Flexible Packaging Global Summit – 2022, Ashok Chaturvedi, chairman and managing director, UFlex, said, “There is no alternative to multilayer flexible packaging. So, we have to look at the solutions to tackle its waste.”
Terming mono-layer packaging solution as yet another myth, Chaturvedi said that it doesn’t help in reducing plastic waste. He cautioned in his keynote speech that if we keep believing that monomer is the answer to reducing waste, we will end up spending another couple of years in it before going back to square one because it will not reduce waste. “Flexible packag ing waste will never get reduced unless we recycle it,” he said.
“Recycling is the only answer whether it is mechanical or chemical. Big companies are claiming that they are zero carbon neutral but still the waste is going up and it will continue unless we recycle waste,” he added. “Collecting flexible packaging waste is a mammoth task – but once you are able to collect it, you will be able to recycle it as well easily. I don’t have any doubt that if recyclers can get the raw material [plastic waste], they can definitely recycle it. We did this 25 years ago and it is still working very well. At all our plants, we have set up a recycling center and all the waste that we produce and whatever we can get nearby, we are recycling it and producing new plastic items.”
During his speech, Chaturvedi lauded the strict EPR rules laid by the government. However, he said that the government should also help in plastic waste collection. Chaturvedi even urged the government to
work with municipal bodies – of their own or under a PPP model – to collect plastic waste.
Highlighting the universal problem of the unavailability of plastic feedstock, Chaturvedi said that it’s time we focused on waste collection. Solutions to recycle this waste – be it rigid plastic, monolayer or multi-layer plastic – are already there. Hence, recycling is not
the main issue. In his keynote speech, Chaturvedi even shared how his company’s pyrolysis plant has been a failure and economically unviable due to the unavailability of plastic waste. India needs over 1000 waste collection centers. The responsibility of such centers will be to provide waste plastics, both flexible and rigid, to recyclers. “So, I request everyone to focus on collecting plastic waste.” z
Speaking to The Packman on the sidelines of the 9th Speciality Films & Flexible Packaging Global Summit in Mumbai in September 2022, Gaurav Talwar, managing director of Brilliant Polymers, said, “Solvent-free lamination has made rapid inroads recently becoming the top pick for companies that are looking at sustainability seriously. Solvent-free laminating adhesive is now the new technology that the flexible packaging industry is moving toward. It enables the manufacture of various sustainable structures such as low monomer, ultra-low monomer, aliphatic system, etc. – this is the direction the industry is heading towards.”
“In solvent-based lamination, we typically have to dilute the adhesives to 35% solid while 65% solid is evaporated into the environment for which we need heat energy. This has huge carbon emissions. In solvent-free lamination, however, this can be avoided,” said Talwar.
Talwar, an assertive proponent of source reduction, said, “While talking about sustainability, we also need to strongly consider source reduction. We should use less carbon, volume and mass at every step of the product life cycle and track the impact of a product at each stage. For example, to improve hand hygiene in a way that it is both effective and eco-friendly, Godrej Consumer Products recently came up with its
innovative powder-to-liquid handwash Magic – the world’s most affordable and sustainable handwash. Converting the handwash to powder form allows them to significantly reduce the plastic used in packaging. Compared to a regular handwash refill, we need only half as much plastic.”
“Right now the industry is very much engrossed in things like monolayer, plant-based films, recycling of plastics, etc. That is absolutely fine although these structures are yet to be fully vetted, evaluated and tested. But the real question arises after these lami nates are being used – how are we going to collect them? That question is yet to be answered. I think a lot of focus is needed not just on mono-material, but also
on finding a solution to collect, segregate, process, recycle and reuse this material – that is how a circular economy will happen. I think a lot more needs to be done in this direction and the government has to lead the initiative – be it through a PPP model or with the help of local bodies.”
Brilliant Polymers recently inaugurated a new plant in Ambernath which has doubled the total capacity of the company to 45,600 tonnes. Talwar said, “Our strategy for India and global markets is to expand geographically and technologically. Geographically we are now exporting our products to several more countries – earlier it used to be just Africa and Gulf. Now we are catering to all of South Asia, South East Asia, and we are also looking at Europe and the US. Our strategy, especially for India, is to remain focused on solvent-based and solvent-free adhesives. However, we are also evaluating heat seal coating, cold seal coating, and water-based adhesives as the growth areas for the coming years making ourselves a fullservice supplier in laminating adhesives.”
Talwar is bullish about the Indian flexible packaging industry. He said, “As far as the flexible packaging industry is concerned, I don’t see any real threat. There is going to be more demand for food, consumer goods, pharmaceuticals products etc. in the coming days. So the demand for flexible packaging will increase even further. Moreover, the industry is talking about expansion and growth. There is a positive sentiment in the industry despite shrinking margins.” z
Preserve the taste and looks with a 100% natural grease-repellent paper for bags & wraps
Packaging that looks beautiful and stays beautiful Healthy for consumers – food remains fresh
A sustainable choice – paper from cultivated forests
In the competitive Indian snack and fast food business, you are what you serve. Packaging from BillerudKorsnäs makes the food look just as good in the wrap or bag as it did in the frying pan. The packaging paper is free from optical brightening agents – good for consumer health and the environment.
Protect your brand, not just the product. Scan the code for more info.
billerudkorsnas.com
Mail: Zaheer.Abbas@billerudkorsnas.com Mobile: +919599225212
In his keynote speech at the 9th Speciality Films & Flexible Packaging Global Summit 2022, RS Sodhi, managing director, GCMMF (Amul), said, “Flexible packaging has revolutionized the way milk is distributed to consumers in small milk pouches. I believe the future of the plastic industry in India is what the future of the food industry is: the future of the food industry is extremely bright being directly proportional to the number of stomachs in the country.”
Amul sells about 1.5-1.6 crore liters of milk daily. Sodhi said that Amul could deliver such huge milk volume only because of plastic packaging. “The volume that we produce is impossible to sell in any form of packaging other than the plastic pouch. Today, whatever we sell is sold in branded form – Amul. Of around 30 million liters of milk that we get, 94-95% is sold in branded small packs mainly using plastics. Only 3-4% is sold as a commodity.”
“Plastic is a system which can be used for scaling. It is not cost-effective – it is cheaper. For packing 6 crore liter milk in pouches, the annual expense would be only Rs 1600 crore. Whereas, the same milk when packed in bottles would incur an annual expense of Rs 37,000 crore. Therefore, packing 6 crore liter milk in plastic pouches would provide a cost saving of Rs 35, 000 crore – the benefit of which would go to Indian consumers and farmers. Moreover, if the same milk is packed in bottles, many would not afford it. Hence, you can imagine how the plastic industry is helping the milk industry.”
Milk production in India has increased 10 times since 1970 from 21 MMT to 209 MMT in 2022. During the same period, the per capita availability has increased almost 4 times from 110 gm per day to 427 gm per day – despite a 2.5 times increase in population. “This
is a clear example of self-sufficiency, possible because of supply-chain efficiency,” Sodhi said.
As of today, the total value of the milk market is Rs 8.5 lac crores (USD 110 billion) of which the pouched milk market is about Rs 1.5 lakh crore (USD 20 billion) while the organized dairy sector is 3 lac crore. “However, with increasing population, the organized sector may easily become 10 lac crore in next 10 years.”
Explaining the success model of Amul, Sodhi said that his company follows a very simple business model. “Last year, our turnover was 61,000 crore (around 8.5 billion dollars) while this year we are expecting around 75,000 crore – simply with a model where around 200 farmers form a cooperative society pull their milk, check electronically, process it at the district level, add value, and sell across India under one common brand name – Amul. Sodhi said that Amul’s success model
is backed by consistency, commitment to farmers and consumers, marketing, technological and marketing innovations, and professionalism.
“In last 75 years we have been consistent in whatever we have done – be it consistent business objective, value for many and value for money, providing stable remunerative to millions of farmers day after day so that they are encouraged to produce more, provide to consumers the best food processed and packed in the best way using natural ingredients at a very affordable price. If you can take care of these two stakeholders – especially in the food business – no one can beat you.”
Sodhi said that the leadership roles played by Amul’s Dr. Verghese Kurien, known as the Father of the White Revolution in India; and Tribhuvandas Patel, known as the Father of the Cooperative Movement in India, were also vital for the stupen dous success of Amul. z
Daetwyler SwissTec has doubled the pro duction capacity of its Pune facility and has added more machinery to produce standard doctor blades. Sudhir Dhotey, MD, Daetwyler SwissTec India, says that the expansion will increase the output of the Pune facility significantly meeting the growing demand in the market.
Daetwyler SwissTec is a global leader in coated and uncoated, precision doctor blades. The company has production facilities in Switzerland, the USA, China and India, and distribution partners all over the world.
“We utilized the last two years in developing new products. We are currently working on new types of doctor blades. In addition, we will launch two new doctor blades this year – a specialized high-end
doctor blade and an entry-level coated doctor blade. The company also aims at releasing three to four new coated doctor blades for special needs in the beginning of the next year,” said Markus Resing, deputy head of marketing and sales, Daetwyler SwissTec.
Speaking on the Indian market, Resing said, “The Indian market is quite important for us. With the growing population in India, the packaging market is growing too. In fact, the country’s packaging market has tremendous potential. Despite the challenges during the Covid, our business was very much stable in 2020. We were able to achieve our targets and fulfill all our orders. The demand for coated blades grew significantly in 2021 and we expect even higher growth in 2023. We are also now well prepared than ever for any kind of inevitable crisis like Covid.” z
Max Speciality Films recently invested in a Master CO 8000 coating ma chine from Bobst to expand its bar rier coating manufacturing capability at its plant in Nawanshahr in Punjab, India. Founded in 1990, Max Speciality Films has grown into a leading supplier of specialty packaging including sustainable ultrahigh barrier solutions, and value-added products for labels, coating, and thermal lamination films) for the Indian and overseas markets. Toppan which earlier had a 49% stake in the company increased it in February 2022 to make Max Specialty Films a consolidated subsidiary. Max Speciality Films currently operates
five Bobst vacuum metallizers with the recent addition of two Expert K5 machines – one equipped with the AluBond process and the other equipped with both the AluBond and the new AlOx GEN I processes. With substrate functionality and sustainability driving the industry, the trend to replace non-recyclable multilayer packaging structures with mono-layer coated substrates that have high barrier properties is gathering strength at a fast pace.
Navneet Malhotra, head of the Max Specialty Film plant said, “We are looking forward to receiving the Master CO 8000 to further increase our production
capacity. We have been associated with Bobst for over two decades and it was a very natural choice when we were looking to further advance in the coating section of the transparent barrier film market that is globally booming, driven by the current sustainability trend.
“With our goals and objectives in sight, our company has entered the next phase of its growth, propelled by innovation, capacity expansion, ‘best-in-class’ customer service, and rising equity in new markets for which investing in the new Bobst coating machine was apt for us at the time.” z
The 9th Speciality Film and Flexible Packag ing Global Summit by ElitePlus Business Services held on 5-6 September 2022 in Mumbai attracted over 1,600 delegates representing 680 companies from 18 countries, making it probably the largest packaging summit of the world.
The theme of the Summit was ‘Flexible packaging – moving to a sustainable reincarnation’, a topic immensely relevant in current context. The 2 day Program included nine power-packed business sessions and interactive Q&A sessions. Huge push towards sustainability in Europe was outlined through a panel discussion giving overview on R-Cycle. The most important issues facing the world today were deliberated in depth by outstanding professional and business leaders.
Panel discussion on ground realities of environment issues, EPR and sustainability demystified PWM and other relevant topics on circular economy, sustain ability and carbon footprint print, and the challenges and opportunities arising out of them provided deep insights into these vital areas.
The third panel discussion on ‘Brand Owners’ Per spective’ served as the weather-vane, a direction pointer to the industry, as the real users – the leading FMCG companies’ leaders shared their thoughts and path forward for sustainability hand in hand with the plastics industry.
The summit brought another unique angle by bringing in the role of private equity in spurring growth explosion in the flexible packaging industry and India’s role in consolidation through M&A and evaluating takeover opportunities and risks in the flexible packaging industry by Blackstone and Premji Invest leaders. The optimistic view on India economic landscape was addressed by Nilesh Shah, group president and MD, Kotak Mahindra Asset Management.
The richly curated content was the main highlight of the Summit with distinguished speaker lineup, covering gamut of latest technologies and application aspects such as mono polymer family laminate, transparent metallizing with coatings, plastic barrier paper, MDO film or BOPE or even
PET/PET laminates. Government’s perspective on EPR and raw materials were shared by Food and Safety Standards Authority of India (FSSAI).
Nidhi Verma, founder and MD, ElitePlus Business Services, who was at helm of the 2-day summit opened the summit with the inaugural keynote speakers outlining the future of circular economy and packaging from machine makers’ perspective by Peter Steinbeck, CMD W&H; converters view by Ashok Chaturvedi, CMD UFlex; and brand owners’ view by Sitapati, MD and CEO Godrej Consumer Product and RS Sodhi, MD, Amul.
Developments in oriented films were presented by the CEOs of Cosmo First and Max Speciality Films; and converters perspective by leaders from Constantia Flexibles, Paharpur and Jupitor Laminators.
Latest trends and innovations in technology were brought by Bobst, Colines, Reifenhäuser, Hosokawa Alpine. Innovations in printing and slitting were pre sented by DuPont, Comexi, Uteco, Siegwerk, Pelican, SP Ultraflex, Brückner and GOEBEL. z
Milliken & Company is partnering with Finnish flexible packaging gi ant Huhtamaki Group to develop a more sustainable, mono-material laminate for use in tubes targeting cosmetics, toothpaste and other personal-care applications.
The results of this joint effort, designed to create a healthier future, was on display at the K 2022 trade fair in Dusseldorf from 19-26 October. Milliken displayed high-density polyethylene (HDPE) tubes produced using Huhtamaki laminates optimized with Milliken UltraGuard Solutions technology the event.
With the market’s keen focus on recycling and circular ity, it is more vital than ever to find technologies that can eliminate the typical metalized (usually aluminum) layers while maintaining the necessary barrier prop erties, especially against water vapor and oxygen transmission needed in personal-care applications.
By improving the barrier properties of HDPE film by up to 50%, UltraGuard Solutions contribute to sustain ability by enabling more mono-material construction of popular products such as stand-up flexible pouches and tubes and making them ultimately more recycla ble. These improved barrier properties also allow for
downgauging of the polyethylene (PE) film, resulting in a lighter-weight end product and a reduction in the amount of resin needed to achieve the desired result.
Huhtamaki’s work on this project fits in perfectly with its blueloop initiative for sustainable, flexible packag ing. Huhtamaki blueloop is a product portfolio aiming to make flexible packaging circular by introducing a range of recyclable solutions with mono-material structures using polypropylene (PP), PE and paper. The blueloop program contains recyclable and sustainable laminate solutions, with dedicated criteria, to ensure the resulting mono-HDPE-laminate is fully recyclable and approved by RecyClass.
“The tube resulting from this joint development work is opaque with a silver shine, making it ideal for beauty product applications,” said Dr. Detlev Schulz, senior manager – sustainability and business development for Huhtamaki’s global tube laminates business. “White would work as well, offering outstanding moisture barrier and improved oxygen transmission for all who don’t need a shiny silver option.” The most likely end uses will be in 40 to 200-ml tubes. z
Kamakshi Südpack, a joint venture be tween the Germany-based Sudpack and Ahmedabad-based Kamakshi Flexiprints has commissioned a new plant in India. The modern production plant was launched near Ahmedabad on 14 October 2022 in a ceremony attended by senior officials of both companies.
Südpack manufactures high-performance films for the packaging of food, non-food and medical products and for use in technical applications. Kamakshi Flexiprints produces printed flexible packaging materials and serve the food and non-food industry with innovative, and flexible packaging solutions.
The new site is a key component of Südpack’s internationalization strategy as well as a stra tegic hub for the intensified development of the growing market of the Indian subcontinent and for meeting the demand for high-quality flexible films in a broad range of industries with a comprehensive product and service portfolio.
Asia, in addition to Eastern Europe and Africa, is becoming increasingly important for food produc tion as well as medicine and technology. The joint venture is thus an important element for Südpack in its internationalization strategy.
The opening ceremony was held for the new Kamakshi Südpack production site after approximately a year and a half of construction. Südpack’s managing partner Carolin Grimbacher and its managing director Thar cisse Carl, and the managing directors of Kamakshi Südpack, Harish Goel and Narendra Dhupar were present at the opening ceremony.
Grimbacher provided a brief overview of the company group’s strategy. The presentation was followed by a presentation about Südpack’s sustainability roadmap – a subject that is also of growing relevance in India. Carl presented his vision for Kamakshi Südpack and
highlighted the outstanding cooperation in recent months among everyone involved.
The new Kamakshi Südpack plant is equipped with extrusion, printing, coating and laminating machines for the production and finishing of high-performance films. The company said the plant complies with the IGBC Standards for green building. The site will also comply with future international regulations and standards.
The complex covers a total area of approximately 47,000 square meters and is divided into areas for extrusion, printing, laminating and pouch production. In recent weeks, the individual lines were gradually commissioned and powered up to make it possible to already produce flexible packaging solutions at the site that meet the highest standards of quality.
“Our well-considered site concept is designed so we can gradually expand its capacities in order to meet the ever-increasing demand for multilayer films that are both innovative and sustainable for flexible packaging on the Indian subcontinent,” explained Carl who was responsible at Südpack for the new construction of the production site.
“Our well-considered site concept is designed so we can gradually expand its capacities in order to meet the ever-increasing demand for multilayer films that are both innovative and sustainable for flexible packaging on the Indian subcontinent,” explained Carl who was responsible at Südpack for the new construction of the production site.
The company also shared its additional goals, including improved market penetration, more rapid response times to the shifting needs of the packaging industry and the prompt supply of local customers.
Goel said, “Südpack’s unparalleled and long-standing expertise in coextrusion and film finishing in combina tion with our excellent knowledge of the market opens up opportunities for us that we had not been able to exploit in such a way until now.”
“With our broad portfolio in the area of recyclable and particularly material-efficient high-performance films and packaging concepts, we are in an excellent position – and can therefore optimally support our Indian customers in meeting statutory requirements in terms of sustainability,” said Grimbacher, whose position also includes overseeing the R&D department at Südpack. z
The platform strategy of the Brückner Group with a clear presence in the key markets is one of the strategic priorities: being on the spot and close to the customer, know ing the local and regional conditions as well as the language – this has proven itself even more during the Corona pandemic. The latest member in the series of platform companies – alongside Brückner Group China, Brückner Group India, Brückner Group USA and Brückner Slovakia – was now officially opened: Brückner Group Asia-Pacific.
The company in Thailand has been in operation since 2022 and is ideally located in the geographi cal center of the ASEAN region, in an industrial area in the Chonburi/Rayong region. A team of about 30 people is employed at the site, which is designed for further growth in the region to strengthen its position in the long term.
Brückner Group Asia-Pacific ensures optimum sup port for the emerging region of South-East Asia as a sales and service hub for the various film stretching technologies and services of Brückner Maschinen bau and Brückner Servtec. Plastic film producers in the region benefit from the globally high standards, procedures and services, which are applied locally in
accordance with the motto: ‘thinking global, acting local’ and guarantee the fastest and best possible support in all areas.
The main focus of the Brückner Group Asia-Pacific at the moment is the support of installation and commis sioning of film stretching lines as well as upgrades and on-site services. There is also a fully equipped center for the reprocessing of clips and chains and a quality assurance system for high-precision components.
The medium and long-term plan is to strengthen the presence of all Group companies in the AsiaPacific region through the platform company. Brückner Group Asia-Pacific’s managing director Walter Stroeder says, “Our goal is to establish our company as a reliable and innovative partner in all our core areas for all Brückner Maschinenbau and Brückner Servtec, Kiefel and PackSys Global customers in the ASEAN region.” z
Product-level serialization has historically been associated with compliance man dates within highly regulated industries such as pharmaceuticals, medical devices, and to bacco. Its central premise was to prevent counterfeit goods from entering these markets.
However, as organizations within these sectors have realized, having full traceability within the supply chain offers benefits beyond compliance alone, providing opportunities for greater visibility, data exchange, and information sharing that can present a significant competitive advantage to brands.
Moreover, as more advanced labeling and serialization systems become more widely available at lower price points, and integration into existing lines and systems becomes easier, organizations across all sectors and of all sizes can now reap the benefits, as Lee Metters, Group Business development director, Domino Printing Sciences, explores.
Through product serialization, brands can allocate a unique identity to each saleable product item. This identity is typically contained within a machinereadable 2D code, such as a data matrix or QR code.
Until recently, the high cost and perceived complexity of implementing serialized solutions has stood as a barrier to widespread implementation. Examples of organiza tions adopting serialization have been limited mainly to those with a regulatory compliance obligation – such as pharmaceuticals, medical devices, tobacco – and high-value, luxury goods manufacturers seeking to protect their brand and reduce the risk of counterfeits.
Despite the early cost of implementation, these manu facturers rapidly found that serialization unlocked significant business benefits beyond brand protection and compliance. As the foundation for data sharing and enabling digital capabilities in physical products, serialization has opened opportunities for improved
supply chain management, personalized consumer engagement, and improved brand positioning.
Today, the cost of serialization through 2D codes is no longer a barrier to implementation. The technology is available and accessible across a wealth of markets, including low-cost sectors such as fresh fruit and vegetables and even postage stamps. In addition, as the benefits of serialization beyond compliance become more evident, specialist companies such as Second Thought and Neurotags have emerged to provide ready-made support for serialization to reduce the cost further, making the application of the technology even more appealing.
In short, the world is awaking to the opportunities associated with serialization using 2D codes. The time is ripe for data sharing, and those without the technological capabilities may soon find themselves left behind.
The rich vein of data that companies gain access to as a result of serialization can be used to enhance consumer protection, prevent counterfeiting, improve supply chain management, reduce waste, facilitate recycling, and optimize consumer engagement for better brand awareness and positioning. By enabling the tracking of products down to the individual item, serialization also simplifies returns processing and
the management of recalls. In the event of a product recall, alerts can be set, so consumers scanning codes on recalled products are made aware of the changed status and advised on where to return products or how to claim a refund.
Effectively, serialization allows each partner in the supply chain to work together to track a product at every step, from the point of manufacture to when it arrives in a consumer’s hands – and back again. The unique serial number can be used on all shipping documents to provide touchpoints and status updates at both ends of the supply chain.
When it comes to counterfeit protection specifically, serialization gives brands in all industries the tools they need to counter the threat of supply chain fraud and diversion – that is, when product stock is sold in a different distribution channel from where it was intended. By tracking to the unit level using unique codes, consumers can quickly validate the authenticity of their purchased prod uct, and brands can identify instances of product divergence and trace diverted products back to their last known location within legitimate supply chains. The same technology can lend a hand in to fight against product adulteration – where highvalue products are contaminated with lower-value ingredients – by allowing product processors to verify the authenticity and provenance of the source materials or ingredients.
Beyond the obvious traceability benefits, the data sharing between the partners within a supply chain could also enable future efficiencies in terms of stock and inventory management, facilitated by knowing exactly where within a supply chain a product is and the exact age of this product.
Serialized codes also unlock substantial opportunities for improvements in marketing and consumer engage ment. As consumers become more accustomed to scanning 2D codes, marketing teams will be better equipped with timely information regarding sales of their products, allowing them to adjust marketing tactics as needed.
For example, customer feedback about positive prod uct characteristics can be used in future advertising campaigns, while changes in product design, advertis ing or loyalty campaigns can be tested, measured, and altered much faster with a serialized track and trace system.
Similarly, inviting customers to register their product purchases on a brand’s website can provide the op portunity for targeted personalization programmes, where the consumer gets information or rewards that are relevant to them. The company gets the op portunity to create brand loyalty and increase sales opportunities through cross- and up-selling of other products within its brand portfolio.
Within fresh food, in particular, there is also the op portunity to grow a brand’s sustainability credentials by providing consumers with batch-specific advice on product provenance or serving suggestions to ensure that the product is enjoyed at its best. The same 2D code can also house recycling advice, potentially utilizing geo-location to provide information on nearby recycling centers – all of which reinforces brand reputation.
every step of the supply chain to the consumer, and indeed to its decomposition.
Serialized codes also unlock substantial opportunities for improvements in marketing and consumer engagement. As consumers become more accustomed to scanning 2D codes, marketing teams will be better equipped with timely information regarding sales of their products, allowing them to adjust marketing tactics as needed.
Of course, as relevant and important for operational efficiency and competitive differentiation as these op portunities are today, they also arguably only scratch the surface of what might be achieved using 2D code-enabled serialization in the future.
Supply chains have become far more efficient in recent years, but they are also more complex and volatile, with products shipped through channels faster than ever and the global demand for supply chain traceability increasing. Unique 2D codes are a digital gateway that links any physical product to its supply chain signature, helping brands collect and share supply chain data, which can be used to identify global trends and support planning to minimize waste.
And, perhaps in its most exciting visionary capacity, product-level serialization may lead to a future where individual products come with their own product pedigree: with imagery of the product’s lifecycle from its source components or raw ingredients through
In addition to reinforcing a brand’s credentials, from a recall or waste management perspective, this will help to identify the exact place where is sues may have arisen or, indeed, where customer complaints may be unfounded. It also offers the unique capability for brands to actively contribute to environmental and sustainability targets by identifying wasteful processes and driving out causes of waste during manufacture – as well as taking steps to reduce packaging waste at the consumer end of the supply chain.
Globally, manufacturers realize the opportunities of 2D code-enabled serialization. Cost is no longer a barrier: more advanced labeling and serialization systems are available at lower price points, and many manufacturers will find that their current coding and marking technologies are already fit for purpose. With only minor upgrades, an expert coding and marking provider can support you to identify the most reliable option for your business.
Yet, for many organizations, the benefits of this tech nology in the supply chain remain unrealized. The time to act is now. Companies must embrace the next exciting step in supply chain management to keep pace with the competition and create ground-breaking opportunities for differentiation. z
Producing food packaging as well as print ing on food contact materials inevitably involves exposure to specific consumer safety concerns. These are triggered from various sides, such as from regulatory authorities all over the globe, which aim to protect consumers from potential risks originating from the food packaging – from brand owners, who strive to protect their precious brand from all negative influences also resulting from packaging material alerts – and last but not least from NGO’s representing consumer concerns and not to forget, from critical consumers themselves.
Packaging is an essential tool to make products stand out from the competition. Beyond the shelf appeal, packaging also provides protection to the contents from physical, chemical and microbiological hazards. However, a lesser-known fact is that the same pack aging material could also be a source of chemical contaminants and hence may impact food safety as well as food quality. Among the different components of packaging material, packaging inks play a critical role as they might hamper product and consumer safety. Each packaging ink is a mixture of different chemicals and some of these chemicals might be harmful with the potential to migrate through the packaging to the foodstuff. In terms of hazard, the chemicals could be toxic, carcinogenic, mutagenic, toxic to reproduction and even endocrine disruptors.
The toxicology of MOH depends very much on its mixture and the substances involved. The most criti
cal fraction is represented by PAH with three to seven rings and no or little alkylation. These substances are genotoxic carcinogens, whereas some highly alkylated MOAH can act as tumor promoters but are not able to initiate cancer themselves. Nevertheless, MOAH can accumulate in the human body and therefore the German BfR recommends, that the migration of MOAH into food should not be detectable.
In humans exposed to MOSH, microgranulomas have been observed in different organs for substances with a range between C16-C35, whereas no adverse effect was observed for MOSH between C10-C13. Even if these microgranulomas are considered of lower toxicological concern, the German BfR recommends, in this case, the minimization of the migration of MOSH into food according to the As Low as Reasonable Achievable (ALARA) principle.
Mineral oils as a huge group of chemicals have earned disrepute globally for their bad toxicological profile. Several research studies have confirmed the migration of mineral oils into the food, even from outer packaging, while some of the recent studies have even got wide attention from the media as well as consumers. The uptake of specific MOHs is seen as a potential health hazard, as some saturated mineral oils (MOSH) may accumulate in human tissue while some Aromatic Mineral Oils (MOAH) may cause cancer. The manifold adverse effects make it an issue related to consumer safety and occupational safety. This is also the reason why several global brand owners have restricted or even completely banned the usage of mineral oils in ink formulations intended for the food packaging material of their products. For several years now, even global ink manufacturers don’t recommend the use of these hazardous mineral oils for food packaging at least in developed markets like Europe.
Food Safety and Standards Authority of India (FSSAI) has already raised the bar on packaging safety by bringing in Food Safety and Standards (Packaging) Regulations, 2018, which has made it mandatory to make use of safe inks, for which the reference is outlined as IS 15495 as well as defined the concept of Food Grade for the market. In India, FSSAI has given the primary responsibility to food business operators to ensure that the packaging material complies with the Food Safety and Standard (Packaging) Regula tions, 2018.
Furthermore, BIS has also upgraded the IS 15495 making the following amendments, which are now enforced since 1 July 2021:
The Sum of concentration levels of lead, cadmium, mercury and chromium (VI) shall not exceed 100 ppm for printing inks.
Addition of toluene, DBP, DiNP, titanium acety lacetonate to the existing Annex A, which lists
the materials and substances that need to be excluded from printing ink formulations.
As per the amendments made, toluene will no longer be allowed to be used as a solvent in printing inks intended for food applications thus ensuring safe packaging for consumers.
Mineral oils free inks contradict the food safety concept FSSAI has defined the term, Food Grade. The standard clearly indicates that packaging material is to be considered food grade when the material is made of substances that are safe and suitable for their intended use, and shall not endanger human health or result in an unacceptable change in the composition of the food or organoleptic characteristics.
The uptake of specific MOHs is seen as a poten tial health hazard, as some saturated mineral oils (MOSH) may accumulate in human tissue while some Aromatic Mineral Oils (MOAH) may cause cancer. Mineral oil-based inks use mineral oils as a solvent and for the same reason, mineral oils are added in the ink formulations in significant amounts. While using Mineral oil-based inks, it will be difficult for any packaging supply chain (with brand owners having the legal obligation) to demonstrate the compliance of their packaging material to the Food Grade concept proposed by FSSAI.
Additionally, we should understand that the growing concerns around mineral oils have pushed betterregulated markets like Germany and France to act
on the subject. While Germany has drafted a mineral oil ordinance, France has also proposed to prohibit the use of mineral oils for packaging inks in general through their circular economy law.
Globally, mineral oil-free inks are being recommended for food-grade packaging for over a decade at least. However, we have now these mineral oil-free inks available in the Indian market itself, which are being locally produced to support the packaging supply chain. z
The author is Head, Product Safety & Regulatory, Siegwerk India
Flexpack lamination adhesives based on polyurethane technologies are preferred due to their adaptability towards wide range of multi-ply laminate structures, low-odor, superior ad hesive properties and excellent transparency, thereby allowing the packaged goods to be clearly visible.
During last two decades, flexible packaging industry has seen majority of innovations towards establishing low-VOC or solvent-free polyurethane adhesive sys tems to provide a greener touch to our mother-earth. Solvent-free adhesives can be 2K (two-component or two-pack) or 1K (mono-component or one-pack) based on prepolymers containing reactive terminal groups either to react with one-another or with moisture.
In 2K procedures, the hardener is usually added before machine operation, using a mixing or metering system; once the hardener has been added, the processability time is limited. The solvent-based lamination adhesives containing organic solvents is more complex because the solvents must be eliminated by evaporation along
the lamination line operations. On the contrary, solventfree lamination adhesives, involving almost negligible volatile matter, have the benefit of being usable at higher line speeds than those containing solvents.
In addition to the advantages of the solvent-free concept, 1K adhesives have the suitability for the user of eliminating complicated procedure of mixing highly viscous components before application, decreasing machine investments, and controlling errors at the metering and mixing stage.
“As a promoter and believer towards development of sustainable chemistry, Yansefu team not only established advanced mono-component adhesive technologies but also started encouraging its valuable customers and channel partners to augment the use of 1K adhesives. Recently, Yansefu increased it’s 1K adhesive production towards achieving it’s commit ment in the direction of making greener technologies in India,” said JK Sharma, CEO, Yansefu Inks and Coatings.
“Our state-of-the-art mono-component adhesive removes the hassles of NCO/OH mixing, and is suitable for paper, film and alu foil applications. This is especially suitable for transfer metallization applications. Low viscosity, higher press speed and better thermal resist ance properties are making our customers happy,” concluded Neelakamal Mohapatra, president-R&D, Yansefu Inks and Coatings. z
Toyo Ink SC Holdings, the parent company of the Tokyo-based specialty materials manu facturer Toyo Ink Group, has announced plans to double the laminating adhesives production capacity from the current level at its Malaysia-based subsidiary Toyochem Specialty Chemical. By strength ening its global supply chain, the Toyo Ink Group plans to expand sales of high-functionality and environmen tally friendly solutions such as solvent-free adhesives, the demand for which is expected to grow worldwide.
Expansion work is now under way at the Malaysian site with full operation slated to begin in the third quarter of 2023. Once in operation, Toyochem Spe cialty Chemical is expected to serve as the mother factory of laminating adhesives to the Asian region, especially high-performance products, an area of core competency for the group.
At present, the demand for laminating adhesives,
which are mainly used to coat multilayered films in flexible packaging structures, is expanding in use for retort food pouches and pharmaceutical packaging primarily in Asia. This includes applications such as press through package (PTP) sheets, a common form of blister packing for drug tablets. Rising populations in countries across Asia are expected to further propel the growth of the retort pouch sector by about 10% over the next five years.
“The Toyo Ink Group has long been a pioneer in developing high-performance adhesive solutions together with our subsidiary Toyo-Morton, which is Japan’s largest producer of laminating adhesives,” said Toshinori Machida, executive operating officer of Toyo Ink SC Holdings. “We’re now looking to bring our unique brand of packaging adhesives, coatings and inks to other regions of the world, in line with our global expansion plan. In addition to Malaysia, we’ve recently bolstered our production infrastructure in China and
Turkey. And our Turkish facility is set to serve as the supply hub for markets in the Middle East and North Africa, Central Asia, and Eastern Europe. To ensure a stable supply to meet future demand, we’ve set a target to increase our global production capacity for laminating adhesives by one-and-a-half times the current level by the end of 2027.” z
Inkmaker Shanghai, Chinese subsidiary of IM Group, has completed installation of its latest automatic ink-transferring system for a leading packaging multinational in Beijing.
Branded as ‘Inktrasyst’, the new system, is the top of the range of Inkmaker’s ink-transferring technology and was installed with pre-blending, storage, transfer,
and inline automatic-viscosity adjustment for process color; CMYK + White in three different series.
The system is powered by, ‘IMPRIMO’, the latest of Inkmaker’s legendary software; for managing ink stock, formulation blending, real-time storage monitoring, instant-accurate transferring and automatic inline ink-viscosity adjusting, as well as consumption and
traceability by work order – a result of IM Group’s increased investment in Industry 4.0 technology and IIoT R&D.
As part of several key objectives related to sustainabil ity, Inkmaker’s new system had to abide by the concept of environmental protection. Inkmaker achieved this by maximizing current operations towards automation
thus reducing human intervention; as well as reducing carbon emissions and wastage; achieving absolute ink-supply consistency; activating automatic ink traceability; implementing an always-fresh-ink-blendto-demand facility and applying bridging-to-printing machinery. Manpower was also reduced for the moving of ink – between ink room and presses – thus further reducing operational costs.
“Traditionally operators would manually refill the ink tray and adjust the viscosity. However, with the Inktrasyst, the ink always arrives at the press in its optimum condition,” explained Lau Kar Seng, general manager of Inkmaker Shanghai and board member of IM Group, “Additionally, the viscosity is automati cally consistent throughout the printing process; this not only increases confidence in achieving a perfect final print out, but also the leftover ink is reduced to practically zero, which is an incredible saving for the environment.”
“We are proud to be part of this environmental-upgrade project with this major installation, we are able to contribute Inkmaker’s technology to the greenenvironment target of Beijing – one of the largest economic and technological development areas in
China – and with this our commitment, of achieving a greener and more sustainable world, is gaining momentum,” concluded Roberto Guerra, CEO Asia Pacific of IM Group. z
H.B. Fuller has launched its first filled hot melt pressure sensitive adhesive (PSA) to address tape and label diecutting challenges. The new Swiftmelt 1401-I delivers exceptional performance on various types of label stocks and baggage tags while ensuring that bonds will not fail during production, transport, or storage, even during high temperatures.
The industry has been evolving very fast in recent years, and the new product meets the current growing needs of the die-cutting sector of the label industry, as well as the ever-changing demands of label converters. The adhesive plays a key role to ensure proper die-cutting. During this process, the adhesive needs to break at the right time, so that the label can be cut in the outlined shape, precisely and accurately. If the adhesive fails to do so, the production line may need to shut down, causing lower productivity for label converters.
Designed by a group of scientists, in collaboration with manufacturers, the addition of Swift melt 1401-I to H.B. Fuller’s portfolio, together with filled thermoplastic hot melts and PSA hot melts, brings differentiated value into the market. This new technology offers high heat resistance, precise die-cutting performance with less bleeding and oozing, and delivers a great balance of peel, tack, and cohesion at very fast melt rates, ensuring increased yield.
“Label stock materials, in particular release liners, are becoming thinner, mostly to save costs and waste. With substrates and release liners getting ever thinner, diecutting has become unavoidable and a precision science to the label market,” says Manish Dwivedi, business manager for India flexible materials. “You will see that today, cost reduction also has become another driver for competitiveness, and our filled grade helps optimize the production cost with operational efficiency gains.”
One of the main differences between filled and unfilled hot melt adhesives is that filled adhesives contain pure adhesive resin, as well as fillers, such as calcium carbonate, which influence processing properties, especially in the label industry. “With that in mind, H.B. Fuller developed this new filled hot melt PSA, to offer superior die-cutting, less bleeding, and high heat resistance, which are all important requirements for our customers, particularly in some parts of the world where the weather is warm,” adds Dwivedi.
This major announcement meets the current grow ing needs of the label industry. The product delivers exceptional performance on various substrates and conditions, making it ideal for general-purpose labels. The new grade is currently being commercialized in India and the sub-continent market. z
Storopack’s FOAMplus foam packaging is a high-quality protective packaging solution that adapts to the contours of the product and protects goods against possible transit damage due to impact shock and vibration. Whether they’re heavy, fragile or awkward shapes, FOAMplus offers the protection required for any product, the company says. Made from expanded polyurethane, the high-quality packaging foam is resistant, robust and thanks to it being lightweight, reduces transport costs.
With the FOAMplus bag packer and hand packer foam dispensing systems, protective foam packaging can be produced directly at the packing station and placed into the carton. As the foam expands, it molds to the contours of the product and encapsulates it in a highly versatile packaging medium.
FOAMplus is available in a range of strengths to suit a product’s weight and fragility. FOAMplus, polyurethane foam packaging is an ‘on demand’ packaging solution that, when the two components mix together, will expand up to 250 times their liquid volume negating the necessity for large storage areas required for pre-fabricated packaging.
With the FOAMplus bag packer and hand packer foam dispensing systems, protective foam packaging can be produced directly at the packing station and placed into the carton. As the foam expands, it molds to the contours of the product and encapsulates it in a highly versatile packaging medium.
Reuse: FOAMplus foam packaging can be reused for multiple shipments of the same products.
Reduce: FOAMplus foam packaging and the corre sponding production process are designed to reduce the use of natural resources. During transport, light weight packaging also helps reduce fuel consumption.
Recycle: Post-consumer or production waste from FOAMplus foam packaging can replace primary raw materials: Within the general waste flow, FOAM plus foam is an outstanding fuel for modern wastecombustion plants producing energy from waste. z
Flex Films, the packaging film arm of UFlex displayed its range of BOPET, BOPP and CPP films at Pack Expo 2022, held from 23 through 26 October in Chicago. The highlight of the company’s exhibit included transparent, coated, metalized BOPET, BOPP and CPP films. Transparent and high barrier BOPET, BOPP and CPP are the new products that UFlex group has added to its portfolio recently, targeting the barrier films market in a new way using the latest technology and process. Tra ditionally, barrier property on BOPP is added using offline coating methods and is very much popular in the Anglo-American and Anglo-European markets. In addition, the company also displayed its range of CPP packaging films.
Speaking about the new Barrier BOPP film, Apoorvs hree Chaturvedi, director EU operations and sustain ability, UFlex Group said, “At present, adding barrier properties on BOPP involves multiple steps. So we are trying to consolidate these production steps for creating the film with barrier properties that offer bestin-class OTR and WVTR values. We are focusing both on producing best-in-class barrier and productivity in terms of speed on the filling line as well as the speed in which the equipment can run.”
Chaturvedi added, “Using metalized laminate with aluminum foil is the best barrier quick-fix but it is not easy to recycle. In contrast, polymer films always had a good barrier but they never had best-in-class barrier properties (like aluminum foil). So what we are envisioning is a new film that will replace certain flexible packaging structures where aluminum foils are being used as a barrier and we can replace and
use a polymer film with a barrier that has OTR and WVTR values close to aluminum foil.”
Chaturvedi said that replacing aluminum or metal ized foil with a polymer film for the barrier will make the structure fully recyclable. “If you have PE as barrier and printing layers, then you have a
homogeneous flexible packaging structure. In ad dition to fulfilling the sustainability requirements, these structures can provide more yield – you can do packs of different sizes because polymer films serve as a barrier and are easier to handle when compared to aluminum foil. It is a futureready product that answers both the questions of sustainability and performance. Aluminum foil can crack and can be difficult to handle in small pack sizes.”
Launch of the new barrier film in India, however, will take some time as the Indian packaging market has different barrier requirements. “We are focusing on barrier property for BOPP in India in a different manner. We have the technical capability to produce it at our Indian facilities anytime without requiring to depend on imports from our overseas plants. However, in India, the barrier requirements are not as advanced as what is required in the global markets. I think the standards and requirements will change by 2025 considering the kind of capital investment people are doing in packaged food and branded beverages. Right now, we have a full low-key manufacturing solution for the Indian market,” said Chaturvedi. z
“At present, adding barrier properties on BOPP involves multiple steps. So we are trying to consolidate these production steps” –Apoorvshree Chaturvedi
The joy of the plastics and rubber industry at finally being able to exchange ideas in person on a global level again after three years characterized K 2022 Düsseldorf and ensured an excellent mood among the 3,037 exhibitors. The companies reported good leads and a marked will ingness to invest among trade visitors, mentioning promising new customer relations and the conclusion of numerous, in part, spontaneous business deals.
“K in Düsseldorf has once again fulfilled the highest expectations. It continues to be the most international, complete and innovative trade fair of the global plas tics and rubber industry,” said Erhard Wienkamp, managing director at Messe Düsseldorf. “The trade fair has impressively demonstrated just how valu able face-to-face networking, chance meetings and physical brand and product experiences are. We are very satisfied to see that K 2022 succeeded in send ing out strong signals as an innovation driver of the industry and that our exhibitors did business with a high number of international customers with great decision-making powers.”
176,000 trade visitors from all continents traveled to their most relevant sectoral event in Düsseldorf. At over 70% the proportion of international guests at K 2022 remained at a constantly high level.
Ulrich Reifenhäuser, chairman of the exhibitor advisory board at K 2022, said, “After hardly any trade fairs could take place worldwide also on a national level over the past three years, K 2022 was all the more eagerly anticipated as the world’s No. 1 trade fair of the plastics and rubber industry and succeeded in providing fresh impetus in all sectors of our industry. The many, in part, unexpected concrete contract ne gotiations held at the trade fair speak for themselves!”
The current unpredictability and uncertainty of events does make for a tight situation in the sector overall, but this did not do any harm to exhibitor commitment
and visitor interest, quite on the opposite. “Especially now in turbulent times and where the plastics industry is undergoing transformation towards the circular economy K 2022 was the ideal place to jointly and actively chart the course for the future,” sums up Reifenhäuser.
It was especially the wealth of new technology de velopments that raw materials producers, machine manufacturers and plastics processors presented for implementing the circular economy, resource conservation and climate protection that thrilled the trade visitors. Commenting on this Reifenhäuser said, “It can be clearly felt that all companies have embraced the need to take on social responsibility and think about plastics in a sustainable way from the beginning of the process chain. The variety of solutions, machinery and products for transformation towards a circular economy presented at K 2022 was incredible.”
The trade visitors at this year’s K traveled from 157 nations to the Rhine. Next to Germany, those Euro pean countries strongly represented on the visitors’ part included the Netherlands, Italy, Turkey, France, Belgium, Poland and Spain. With 42% of visitors coming from overseas, the reach of K is as high as usual among the international trade audience. While visitors from the East Asian region, in particular, were less well represented than at K three years ago due to the currently more difficult conditions in those countries on account of quarantine regulations, nu merous visitors from the USA, Brazil and India were welcomed at K 2022.
The K regulars from India included Alok Master batches, C Trivedi, Cosmo Films, Echaar Equipments, Expert Industries, HPCL-Mittal, Kohli, M Plast, Mamata Machinery, Mundhra, Plastindia, Pelican, Rajoo, Reli ance, SP Ultraflex, Specialty Polyfilms, Technoshell Automations, Welset, and XL Plastics among others.
For around two-thirds of all visitors polled machinery and plant construction ranked first in terms of interest. 57% and, hence 5% more than at K 2019, said they were interested in raw and auxiliary materials, with recyclates and bioplastics being particularly popular.
For 28% semi-finished products and technical parts made of plastics and rubber were the main reason for coming (multiple responses possible). Over 70% of all visitors come from top and middle management.
Top marks were given by visitors to K 2022 for the completeness of its ranges and its mapping of the en tire supply chain. 98% of all professionals stated they
had fully achieved the goals associated with their visit.
During the eight trade fair days, it became clear that this year’s K was right on target with its selection of hot topics, circular economy, climate protection and digitalization. In terms of investment intentions, machinery and equipment for processing and recy cling stood out at 43%. The focus was particularly
on sustainability, but also on circular economy and energy/resource efficiency in production. Around 40% of decision-makers said they were looking into the topic of decarbonization.
The K specials, which also focused on the three hot topics, were also very well received. The official spe cial show, ‘Plastics Shape the Future’, focused on the economic, social and ecological challenges and potential solutions around the K guiding topics in high-caliber discussions and lectures, and this show was well attended throughout. The Circular Economy Forum, where the VDMA and 13 of its member com panies impressively demonstrated the importance of technology in the implementation of the circular economy in the plastics industry, scored points with the international audience with live demonstrations and a great deal of well-founded knowledge as well as detailed information on the topic.
At the event, there was also a lot of discussion about the global production language, OPC UA. This standard allows the processing parameters of the machinery and equipment involved to be coordinated more precisely and in a more targeted manner. This, in turn, is considered an important prerequisite for optimized circular management. 40 companies from eight countries participated in an OPC UA demonstration project at the trade fair.
The next K Düsseldorf will be held from 8 to 15 October 2025. z
Domino Digital Printing Solutions has appointed GMS Pacific as the distributor of the N730i in Australia. The new partnership will extend Domino’s presence in Asia-Pacific with GMS Pacific responsible for expanding the brand position in Australia and driving sales, service and support for Domino’s N730i digital color inkjet label press.
GMS Pacific was established in the late-1970s by Founder Peter McNamara. Headquartered in Mel bourne, the company delivers intelligent solutions across a range of printing sectors, serving Australian and New Zealand manufacturers in the narrow-web label industry, wide-web flexible packaging, cor rugated and carton packaging – as well as paper
mills and the sign and display market.
“GMS Pacific’s strategy continues to actively partner with leading companies and new technologies, to expand and evolve product offering where we see that the products offer superior value to the market and a competitive advantage,” says Andrew McNamara, managing director at GMS Pacific. “Domino Digital Printing is a recognized global leader in its markets, and we are proud and delighted to be cementing our relationship with Domino. Together, helping our customers achieve success and growth through distributing, supporting and servicing this leading range of digital printing solutions and technological advancements.”
Mario Fanton, director for Domino Digital Printing Solutions in Asia-Pacific, says, “We are delighted to welcome GMS Pacific as a distributor of the N730i label press. GMS Pacific has a strong presence in the label and packaging market and has always placed great emphasis on delivering exceptional service and support. This new partnership now represents an exciting opportunity to drive growth and sales for digital color inkjet presses in Australia. We are confident that the industry expertise and the common values shared by both businesses will prove to be successful to our existing and future customers.” z
At K 2022, Comexi presented the Digiflex press, its first digital printing solution that enables the flexible packaging industry to meet the current needs of a changing and increasingly demanding market.
Comexi claims that the new digital press uses lowmigration inks suitable for food packaging printing and offers excellent results in regard to quality tests (tape, ethanol, and scratch). The machine allows for the possibility of double-sided printing without treat ment, as well as printing on pre-printed material. The press can reach a maximum speed of 220 m/min, reduce material waste, and improve lead time. The machine offers a resolution of up to 1200x1200 dpi, a minimum code size of 8 x 8 mm, as well as printing and registration consistency.
“The Comexi Digiflex is the machine that currently offers preeminent digital printing of variable data, such as Datamatrix variable codes, QR codes, barcodes,
alphanumeric text, as well as other numbering and marking applications with high quality requirements,” explains Pedro Jiménez, digital technical sales director at Comexi. “It is a digital variable data print press that offers extremely high printing speed, superb quality
results, as well as the highest level of performance and production. Digiflex is an all-in-one solution that includes the integration of the curing process, tension control, printing registration, corona treatment, and a video inspection system.” z
Heidelberg India has appointed Kapil Dev as the senior regional sales manager for the Northern region. Dev started his career over a decade ago as a sales manager in the graphic arts industry and has an impressive successful track record.
On his career graph, he has demonstrated an excellent ability to turn businesses around, motivate sales teams, meet organizational goals, and enhance profitability.
Dev has immense experience in selling UV curing systems, LED auxiliary for sheetfed offset and flexo presses. His area of expertise also covers roller coating lines, flexo coating and screen-printing equipment.
During his tenure at Alpna as Head of Sales, he man aged operations in India, Nepal, Sri Lanka, Bangladesh, UAE, Africa, Egypt, and Thailand – covering technical nd commercial sales.
“I am happy to be a part of Heidelberg India, the Industry leader in printing. I will use my business network to enrich the business and add value to the organization. I look forward to driving the Heidelberg equipment business for the Northern region,” said Kapil Dev.
Samir Patkar, president – Heidelberg India, said, “We are excited to have Kapil Dev in our Team and wish him all the best in his new role. We are sure, his sales and strategic experience will help to achieve our goals and increase our market coverage.”
Kapil Dev will be responsible for Equipment Business in the Northern region and will be reporting to Harish Gogia, cluster sales head (North & East, Nepal, and Bhutan). He will be operating from Heidelberg’s New Delhi office. z
Huhtamaki India, a leading provider of primary consumer packaging and labelling solutions in India and part of Huhtamaki, has announced the appointment of Dhananjay Salunkhe as the managing director of Huhtamaki India. Salunkhe is a seasoned business leader with a track record of growing and building businesses in India. In his previous stint, Salunkhe has worked as the CEO of packaging and printing business at ITC, where he led the packaging business and supervised four manufacturing plants producing cartons, flexible packaging and rigid boxes.
Salunkhe said, “I am impressed with Huhtamaki’s principle and high-performance culture that focuses on the core values of Care Dare Deliver. I am excited and looking forward to developing the company further by harvesting new opportunities, accelerating growth with a vision to deliver on its 2030 ambitions.”
Marco Hilty, president, flexible packaging at Huhtamaki,
leadership experience from the packaging and printing business and holds great records in driving businesses towards significant growth. We are certain that his rich experience and knowledge will play a vital role for the India market as we continue to grow and ac complish our goals towards becoming the first choice in sustainable packaging solutions.”
Prior to ITC, Dhananjay spent nine years with 3M, starting as plant head for their Pimpri manufacturing unit. As a Lean Six Sigma Master Black Belt holder, Salunkhe has been instrumental in driving significant process improvements and was recognized with the ‘Transformational Leader’ Award in 2015.
Salunkhe started his career as a graduate engineer trainee at PMP Auto, followed by stints at Sulzer India, a Swiss pumps and compressors company, and GKN Sinter Metals. z
08 to 10 October 2022
IndiaCorr Expo Bombay Exhibition Centre, Mumbai, India
19 to 26 October 2022 K 2022 Düsseldorf, Germany
24 to 26 October 2022 Asia CanTech Bangkok, Thailand
10 to 13 November 2022 Label Expo India 2022 India Expo Centre & Mart, Greater Noida, India
17 to 19 November 2022 Asia Coat + INK Show 2022 Bombay Exhibition Centre, Mumbai, India
23 to 25 November 2022 pacprocess India Bombay Exhibition Centre, Mumbai, India
26 to 28 November 2022 North East Print Tech 2022 Maniram Dewan Trade Centre, Guwahati, India
5 to 4 January 2023 Plast Focus 2023 India Expo Centre & Mart, Greater Noida, India
20 to 22 January 2023 North East Print Pro Pack 2023 Maniram Dewan Trade Centre, Guwahati, India
1 to 5 February 2023 Plastindia 2023 Pragati Maidan New Delhi, India
9 to 11 February 2023 Labelexpo Southeast Asia Bangkok International Trade & Exhibition Center, Bangkok, Thailand
9 to 13 February 2023 Plastvision India 2023 Bombay Exhibition Centre, Mumbai, India
27 to 30 March 2023 Pamex 2023 Bombay Exhibition Centre, Mumbai, India
4 to 10 May 2023 interpack Düsseldorf Trade Fair Centre, Dusseldorf, Germany
28 – 30 September 2023 IndiaCorr Expo India Expo Centre & Mart, Greater Noida, India
6 to 9 December 2023 Paperex 2023 India Expo Center & Mart, Greater Noida, India
1 to 5 February 2024 Plastfocus 2024 IICC, Dwarka, New Delhi
28 May to 7 June 2024 drupa Düsseldorf, Germany
RNI UPENG/2018/76741
Editor
Mahan Jyoti Hazarika editor@thepackman.in Cell: +91 9910189285
Senior Desk Editor Sunil Jain
Senior Associate Editor Dev Kumar Dutta
Associate Editors Pranay Mathur Manash Das
Guest Editor Anwesh Koley Design and Production Biswajeet Chaliha
Sales and Marketing Mahan Jyoti Hazarika
Subscription Address
C8, 1303, Eco Village 2, Greater Noida West, Gautam Buddha Nagar 201 306, Uttar Pradesh, India
Issue Published on 8 November 2022 Printed at JK Offset Graphics Pvt. Ltd.
Printed, Published and Owned by Mahan Jyoti Hazarika, and Printed at JK offset Graphics Pvt. Ltd., B278 Okhla Phase I, New Delhi 110 020, India and Published From C8, 1303, Eco Village 2, Greater Noida West, Gautam Buddha Nagar 201 306, Uttar Pradesh, India
Editor: Mahan Jyoti Hazarika