
13 minute read
A Misty Plume To Beat The Dust

A MISTY PLUME TO


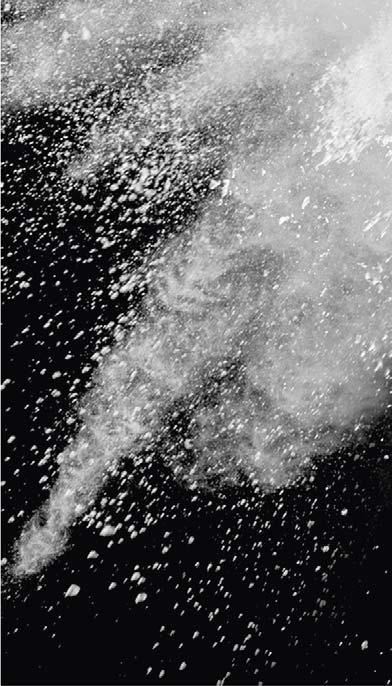

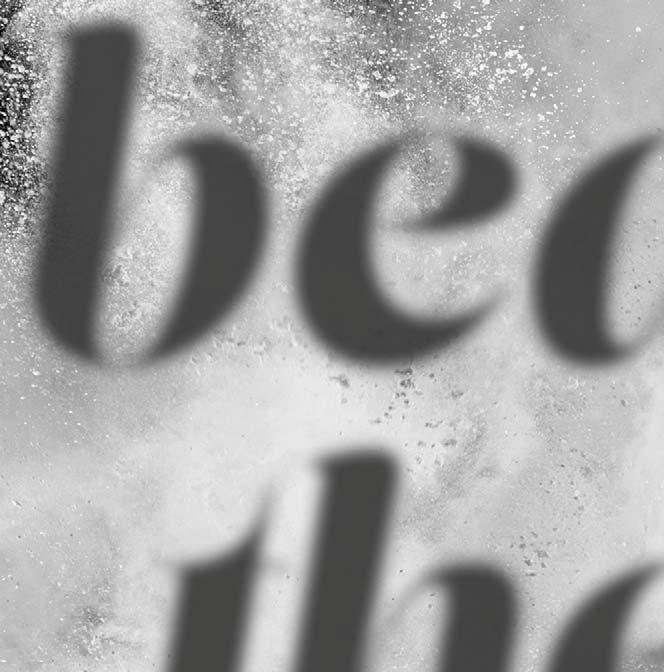
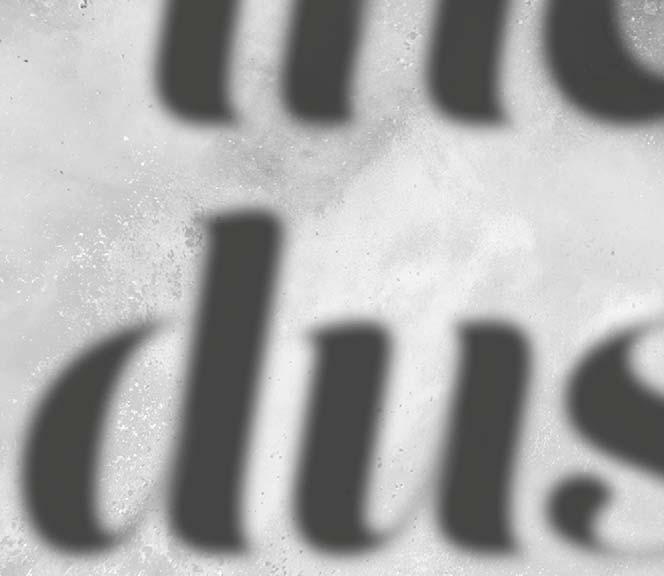
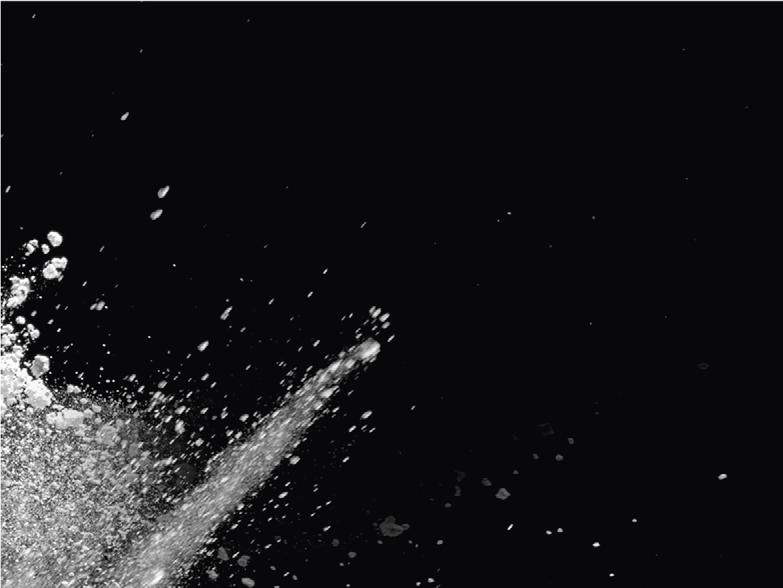

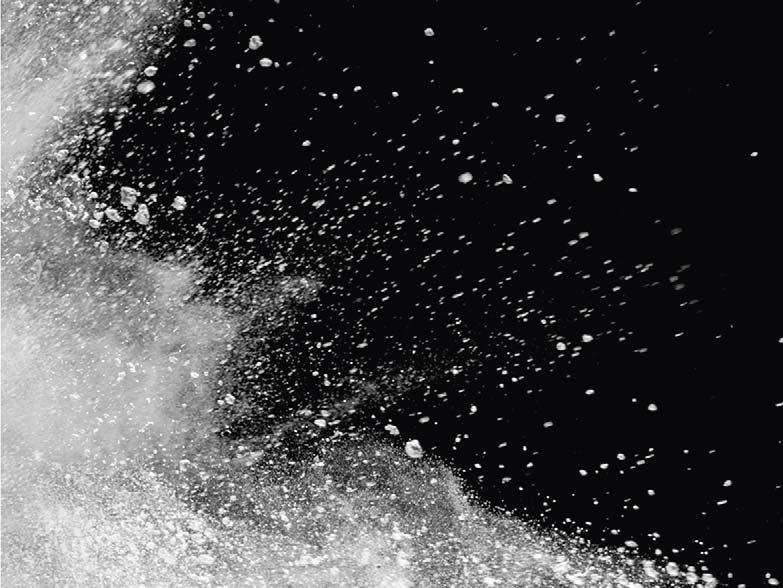
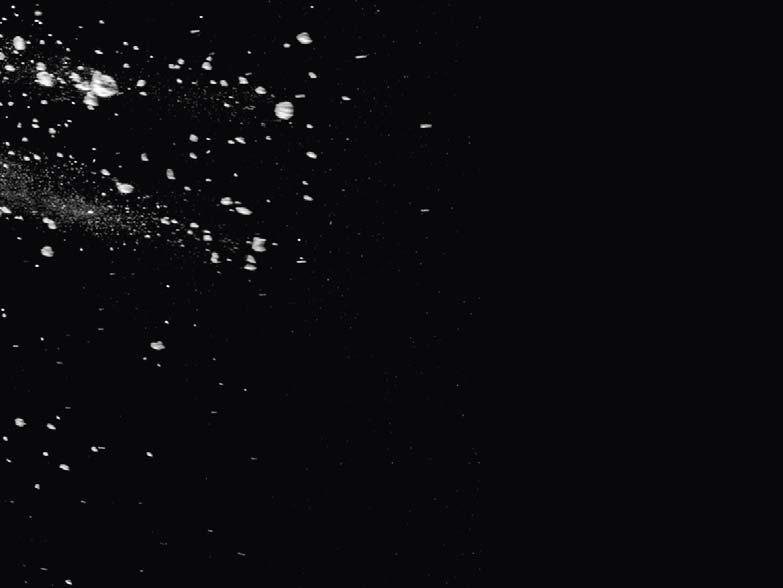
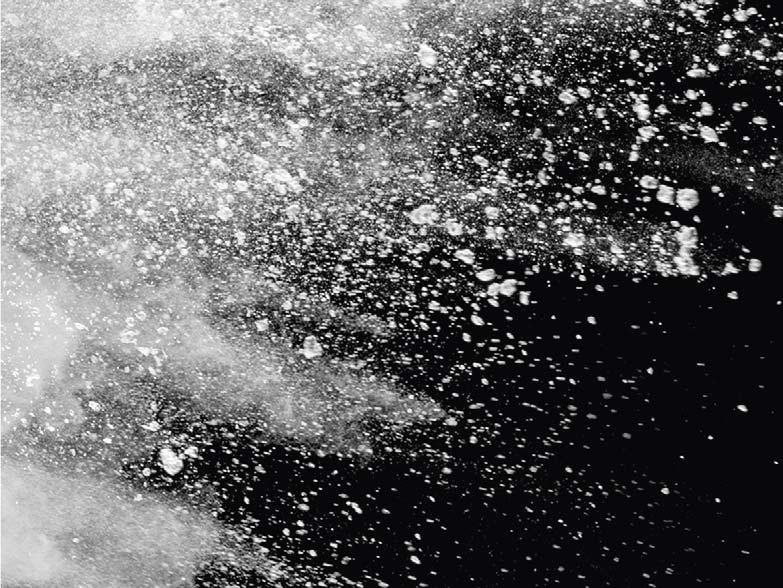
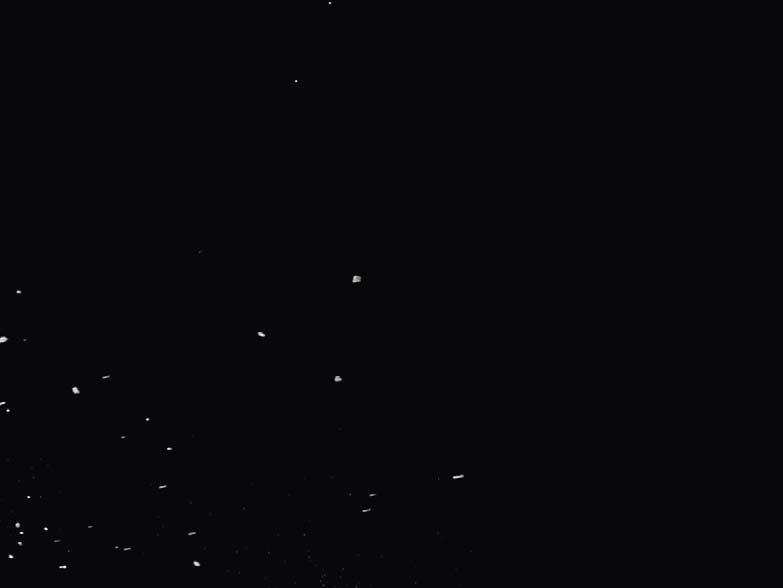
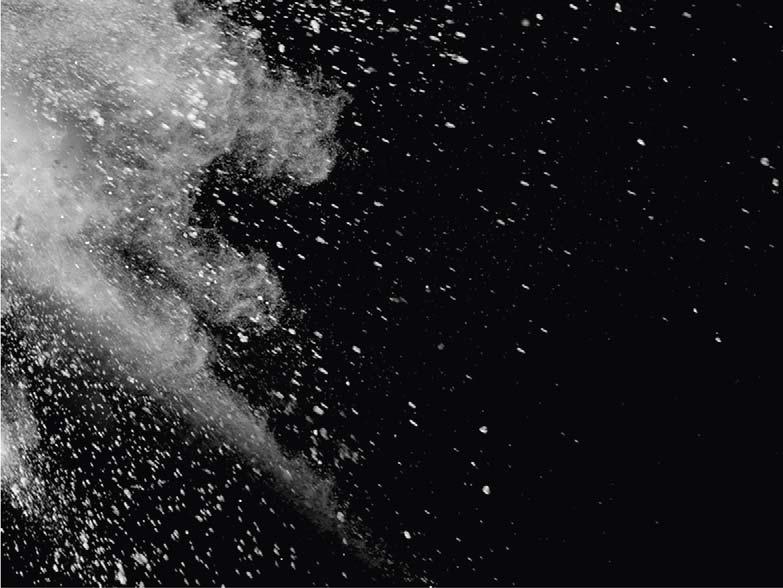
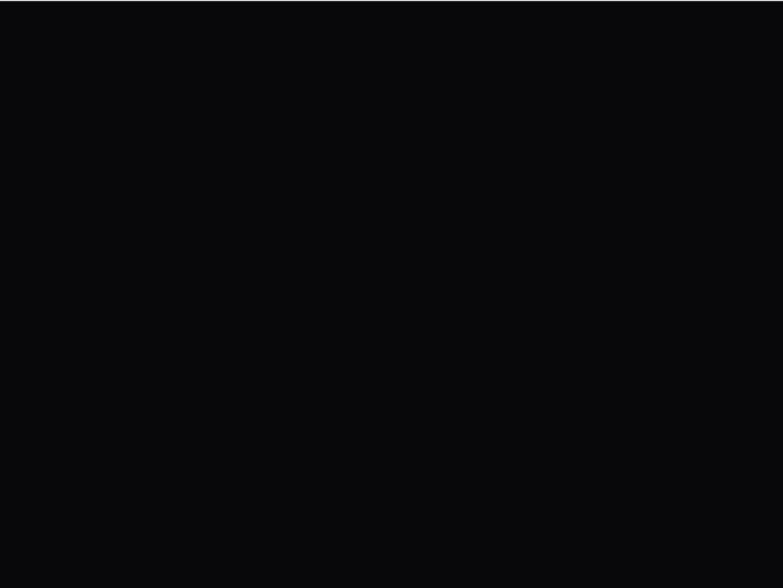
Mike Lewis, BossTek, USA, details dust management in bulk material handling operations, specifi cally looking at atomised mist.
Dust management is an ongoing issue faced by virtually every company transporting or processing dry bulk materials. Effective dust control has become an increasingly important challenge in bulk handling applications, with raised awareness and tighter regulatory standards both contributing motivation for operations to employ effi cient, cost-effective methods of particle control.
Depending on the source and ambient conditions, airborne dust can contribute to a number of concerns, including potential health or safety hazards, environmental issues, regulatory challenges, explosion risks, higher equipment maintenance costs, and poor community relations. Some of the issues are fairly obvious: dust inhaled by workers or members of the surrounding community can irritate airways and exacerbate conditions such as asthma. From a purely fi nancial perspective, signifi cant amounts of dust can lead to more frequent maintenance and faster equipment wear, causing operating costs to rise. Fugitive dust can also generate complaints from local residents and businesses, affecting neighbour relationships and potentially creating obstacles to future operating permits.
According to the US Occupational Safety and Health Administration (OSHA) and most global safety organisations, a safe and compliant workplace around conveyors includes open walkways clear of debris, dust-free air, guarded belts with safe access points, signage, and suffi cient lighting.1 Violations can result in fi nes and downtime, but a workplace injury can carry substantial penalties affecting operations and insurance.
Many substances that are not flammable can be explosive, as evidenced by the explosion at a Georgia, US, sugar refi nery that killed a dozen workers and critically injured 11 others in 2008. Despite more than a dozen relevant OSHA directives, there have been more than 250 fi res and explosions caused by combustible dust in the past 25 years, resulting in more than 100 deaths and 700 injuries.
In addition, it is estimated that for every accidental death in industry there are 20 deaths due to the long-term effects of dust exposure. These deaths are not as sudden – but just as traumatic – and often do not show up as fatalities in the company injury statistics because a worker can be on disability pay for years before passing.
There have been many methods developed to control dust over the years, and the solutions are as numerous and different as the materials being handled. Because of the number and diversity of methods employed to control fugitive particulates, material handlers need to do some homework on their individual processes and the potential dust management techniques available to them in order to arrive at the optimum approach for their specifi c set of conditions.
What is dust?
In an industrial context, dust is a generic term for small, dry, solid particles ranging from approximately 1 - 100 μm in diameter. In bulk material handling, these particles are often created in a wide range of sizes, with larger, heavier particles tending to settle out of the air, while smaller, lighter solids may remain airborne for long periods of time. These tiny solids are easily projected into the air by a variety of forces, settling slowly under the influence of gravity. For occupational health purposes, airborne solids are categorised by size as either respirable or inhalable.
The inhalable dust classifi cation is applied to particles which are typically trapped in the nose, throat, or upper respiratory tract. The EPA describes this category as particles with a median diameter of approximately 10 μm. In contrast, respirable dust is small enough to penetrate deep into the lungs, usually identifi ed as particles under 10 μm in size. These small particles that migrate deep into the respiratory system are generally beyond the body’s natural cleaning mechanisms (such as cilia and mucous membranes) and are likely to be retained. To put that into perspective, a dime is 1000 μm thick, so the most potentially hazardous dust particles are the ones too small to see.
In most bulk handling applications, primary attention is generally focused on dust particles smaller than 100 μm (0.004 in.), based on the observation that particles under that size have a tendency to stay aloft once they become airborne.

Figure 1. The majority of respirable dust particles are too small to see.

Figure 2. The slipstream effect.
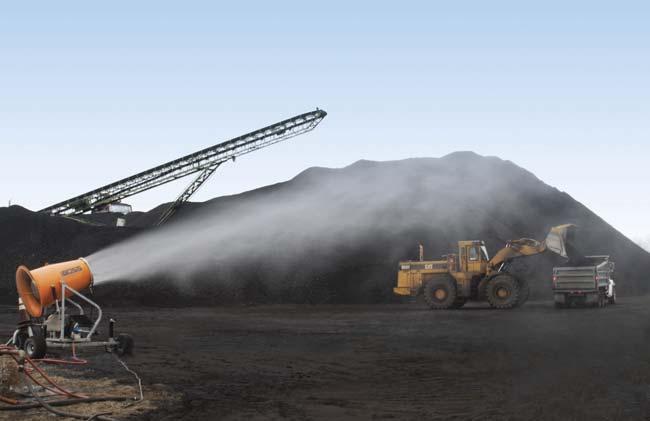
Figure 3. Atomised mist is one of the few techniques able to control both surface dust and airborne particulates.
Sources of dust in bulk handling
Virtually any activity that disturbs a bulk material is likely to generate dust. Substances composed primarily of smaller, lighter particles can create signifi cant volumes of airborne material if left uncontrolled. Bulk conveying operations and trucks or railcars dumping loads of raw material often struggle to manage this fugitive material. And any activity involving front-end loaders or other heavy loading equipment is almost certain to release airborne particles.
In operations where containment is impossible and the creation of dust is not preventable, suppression may be the best option. Suppression involves treating the dust particles once they have been released from the bulk material stream, typically using plain water or a water/ chemical solution. Airborne droplets combine with the dust particles, making them heavier so they fall out of the air stream.
Some operations may use hoses or industrial-sized sprinklers on outdoor applications, which can be effective at immobilising ground-level particles. Unfortunately, these options usually require large volumes of water, which can create additional complications such as run-off. Aside from the cost of the water, hoses and sprinklers are also fairly localised methods, often requiring frequent repositioning or manual spraying.
Their greatest drawback, however, is droplet size: water droplets produced from hoses and sprinklers are simply far too large to have any meaningful effect on airborne dust particles. The size of the droplet is important: hoses and large sprinklers common to large bulk handling operations typically produce droplets between 200 - 10 000 μm in size, which are large enough to create a phenomenon known as the slipstream effect.
A slipstream is created when a mass moves swiftly through the air. Like the air moving around an airplane wing and keeping the craft aloft, a slipstream also travels around a large falling water droplet. Smaller dust particles
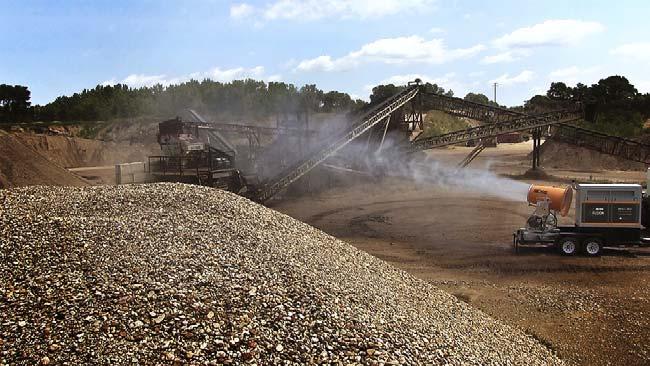
Figure 4. Raising the humidity at the point of emission helps control dust at the source.
Figure 5. This atomised mist design employs a 60 hp fan and diesel generator on a roadworthy trailer. can get caught in this slipstream and get directed away from the droplet, remaining airborne. Very small droplets produce virtually no slipstream and linger in the air much longer, increasing the chance of a collision with an airborne dust particle.
For this reason, a more effective option for large open areas is an atomised mist, which relies on the principle of creating tiny droplets of a specifi c size range and delivering them at relatively high velocity over a wide coverage area, inducing collisions with dust particles and driving them to the ground.
For large open areas such as storage piles, crushing operations, and loading/unloading stations, basic spraying techniques such as sprinklers or handheld hoses have a tendency to saturate target surfaces, often resulting in excess water that can damage sensitive cargo. The range of these techniques also tends to be quite limited, frequently requiring signifi cant staff time to man the hoses or reposition sprinkler heads. In contrast, atomised mist has proven to be one of the few technologies capable of delivering dust control via airborne capture and surface wetting.
Because all of the elements in atomised mist dust control equipment tend to have an effect on each other, each component must be designed to achieve an optimum balance, including pump, nozzles, barrel, and fan. Changing any element can have consequences on droplet size, velocity, spray angle, pattern, and range, and all of these must work together for maximum effi ciency.
In large operations or facilities that store signifi cant amounts of material outdoors, atomised mist technology delivers highly effective suppression over large open areas, with some equipment capable of covering as much as 280 000 ft2 (more than 26 000 m2 – nearly six football fi elds) with a single machine.
Some manufacturers have even developed turnkey systems that include a diesel generator and electricpowered atomised misting unit mounted together on a roadworthy trailer. Designed for large open-air applications, these systems deliver effective particle control in a highly-mobile platform that can be positioned directly at the source of dust-generating activities. With a range of up to 100 m, the systems can deliver effective particle management on remote sites without an available power supply. Some of these new designs can even be specifi ed with a high-lift pump for drawing water from a stationary source, such as a private pond.
Unlike industrial sprinkler systems used for dust management, which can require as much as 500 gal./min. (1893 l/min.) of water, even large atomised mist equipment typically uses less than 40 gal./min. (151.4 l/min.) to help avoid pooling or run-off. Many of these can also be outfi tted with a dosing pump to accurately meter in surfactants or tackifi ers to further enhance binding of dust particles. Standard designs are typically engineered to use a potable water source, but many can also be outfi tted with a selection of fi lters to handle non-potable water. For applications in which the water contains high amounts of sediment, additional external fi lters are available.
While some atomised mist designs are engineered to run directly from diesel engines as their power source, experience has shown that an electric motor delivers quieter and more durable performance. Maintenance requirements for the electric units are typically minimal, and some suppliers provide a three year or 3000-hour warranty.
Of particular interest in certain applications is the evolution of atomised mist technology for odour control. With the development of specialised vaporising nozzles, these systems can create an engineered fog comprised of millions of tiny chemically-enhanced droplets as small as 15 μm in diameter (approximately twice the size of a human red blood cell).
Delivered by a special open-ended barrel design containing a powerful fan, these devices can also be mounted on a towable roadworthy trailer fi tted with a dedicated water tank that gets fi lled with a pre-mixed solution of water and highly-effective odour treatment chemical. The water content of the solution quickly evaporates once dispersed into the air, leaving behind the deodorising vapour, which can hang suspended for long periods of time as the microscopic droplets attract and counteract odour-causing molecules. The devices can also be used for active odour control spread over wide areas, as well as topical treatment or a perimeter barrier.
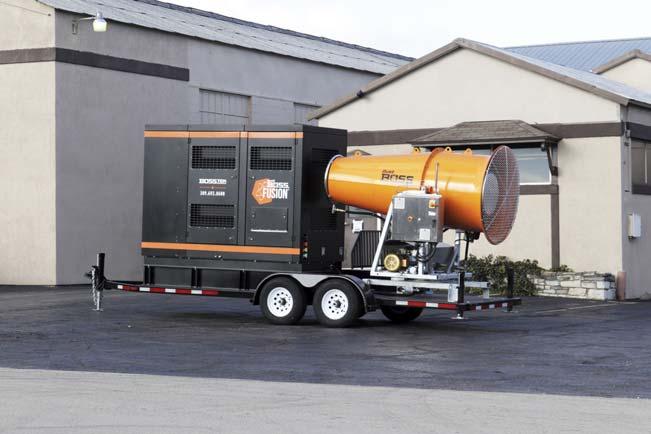
Summary
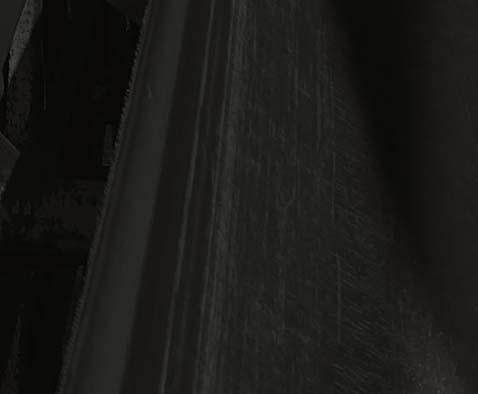
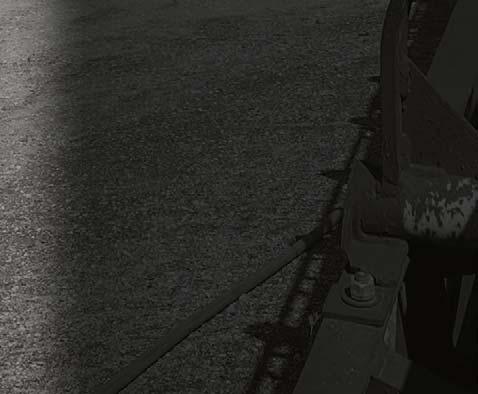
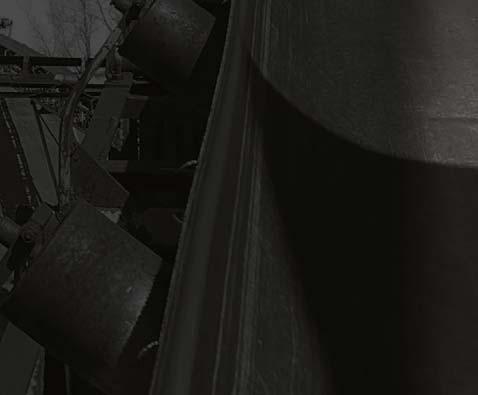
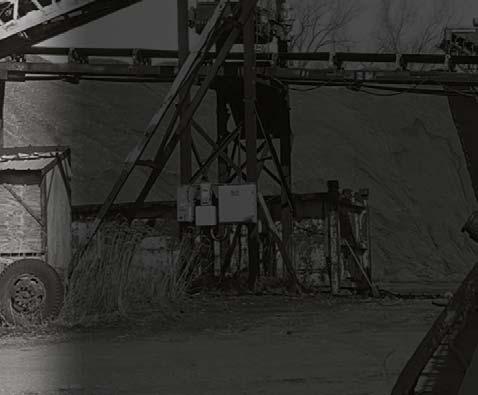
Users of atomised mist technology can choose from a variety of different designs, including low-turbulence models for applications in which a large airflow would be undesirable – indoor operations, tunnels, conveyor transfer points, etc. – and they can be customised according to the application.
Fan-driven units employ a cone-shaped barrel with atomising nozzles in front, a powerful industrial fan in the rear, and can be mounted on a mobile trailer, skid, or fi xed tower. These fan-driven machines are typically manufactured in a standard 480 V confi guration for the US market, and users can specify voltages to suit their region. They can be direct-wired or powered by a generator set. Self-contained, transportable units can be mounted on a roadworthy trailer, with a generator and highly durable electric motor.
Modern atomised mist cannons are engineered to deliver portable one-touch operation, with workers able to manage the settings for specifi c conditions via touch keypad or remote control. They can run unattended for extended periods when connected to a suitable water source, reducing labour and the overall cost of operation vs manual suppression methods.
Before making a commitment to a particular dust suppression design, it is a good idea to see the units close-up and get a demonstration of the equipment in service, rather than relying solely on spec sheets and videos. Renting a unit before buying can be a valuable experience, especially if the supplier will credit a portion of the rental fee toward the purchase.
Inspect the materials of construction: is the unit built with heavy-duty materials that are likely to withstand the rigours of everyday use, or does the manufacturer use thin sheet metal housings and light-duty components? Does the supplier employ a durable frame and fasteners that lend themselves to removal and replacement, if a repair becomes necessary? Or is the unit assembled with light-gauge rivets and sheet metal screws that are unlikely to survive many years of fi eld service?
As with many types of equipment, good indicators of overall quality are the supplier’s warranty and guarantee, not to be confused. The warranty is the manufacturer’s pledge to replace failed parts within a specifi ed period of time, while the guarantee is that supplier’s assurance of a buyer’s satisfaction. A manufacturer willing to warranty its products for signifi cantly longer than its competitors is demonstrating confi dence that the equipment is durable and reliable. Likewise, if a supplier promises customer satisfaction with a money-back guarantee, it is a good indication that the products have been fi eld-proven to perform as advertised.
References
1. Standards: 1926.555 – Conveyors, U.S. Occupational Safety and Health Administration (OSHA), Department of Labor, Washington, D.C.
MARTIN® CLEAN BELT SYSTEMS & SERVICES
Eliminate material carryback and increased cost of operation involving manual cleanup, damage to belts and systems, and downtime and lost production. Martin® clean belt systems and services ensure your conveyor belts are cleaner, safer, and more productive by providing unsurpassed cleaning performance and remote monitoring with industryleading technology, experience, and knowledge. FACTORY DIRECT SALES & SERVICE CALL 800-544-2947 VISIT MARTIN-ENG.COM ® Registered trademark of Martin Engineering Company in the US and other select locations. © 2021 Martin Engineering Company. Additional information can be obtained at www.martin-eng.com/trademarks and www.martin-eng.com/patents

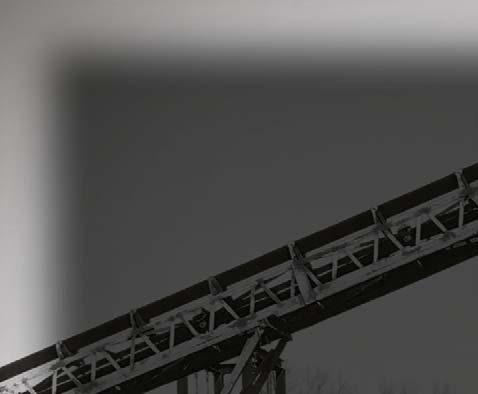
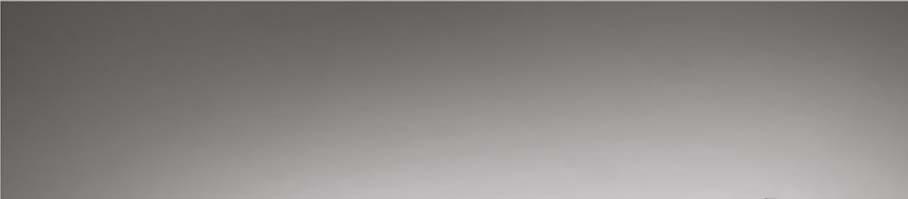
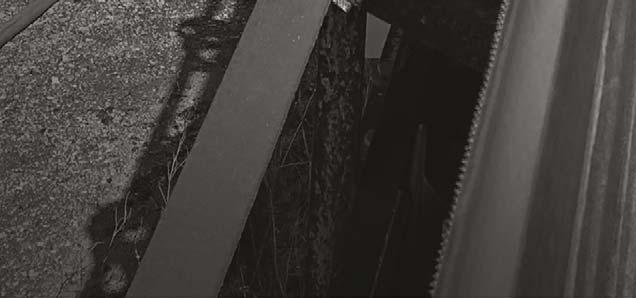