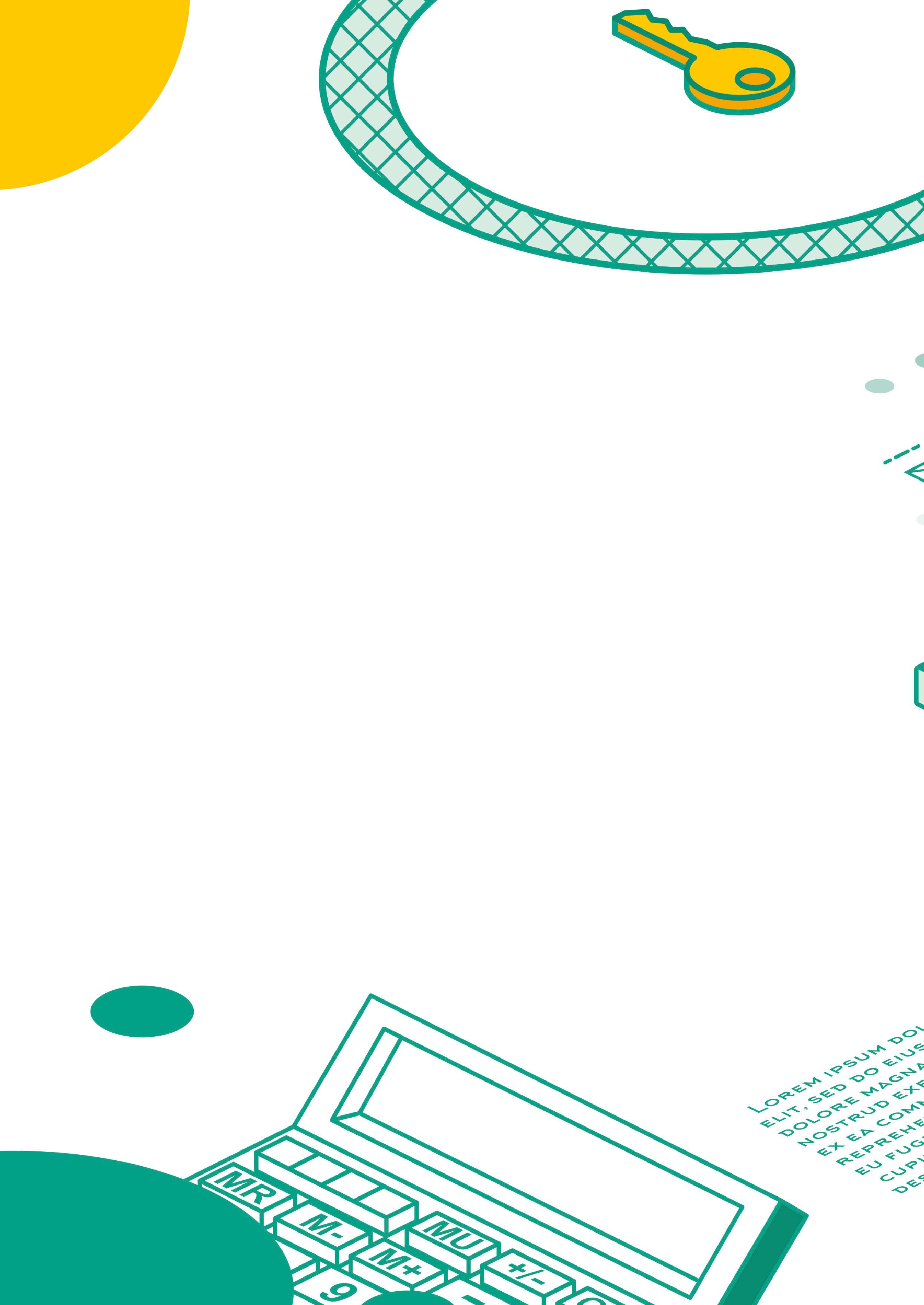
8 minute read
Waste not, want not
David Richardson, Business Development Manager Global Renewables, Yokogawa, UK, details how to improve the performance operation and profitability of waste-to--energy plants.
waste-to-energy (WtE) plant is a complex process involving numerous interconnecting systems and processes. Unlike the conventional coal and/or gas power producing plants, the hugely varying calorific value of the waste being burned generates considerable problems for the operators of such plants, with the combustion process being considered somewhat unstable. To prevent plants from tripping, many WtE plants run below their design setpoints, and therefore project returns on investment subsequently suffer. Compounding the problem and contributing further to the process
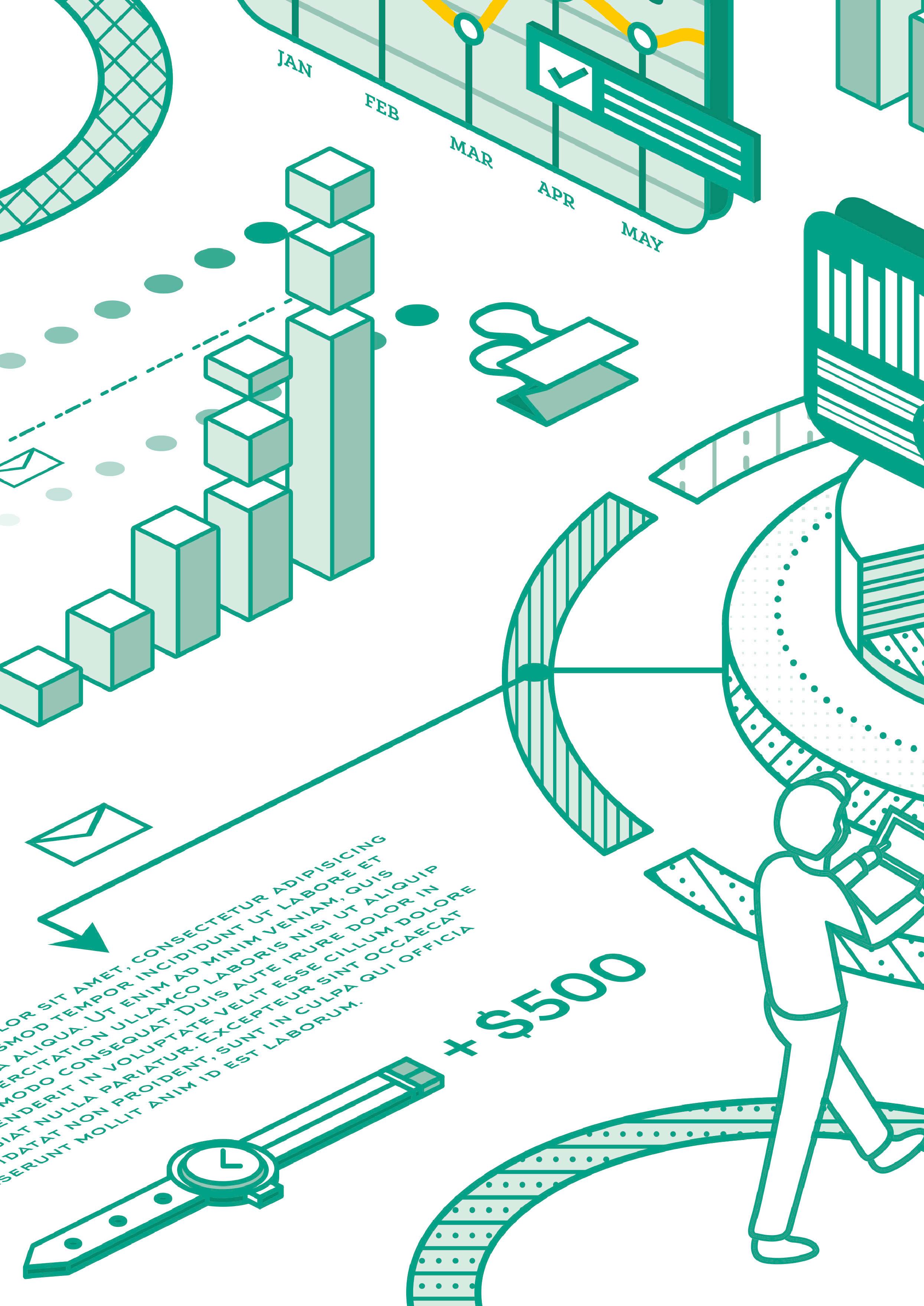
instability are issues associated with fuel feeding where overfeeding and starvation are both common.
A WtE plant can be split into a number of constituent processes/operations: fuel feeding, combustion control, boiler efficiency, corrosion, and emissions. There is considerable overlap between how these elements relate to each other, and total process understanding is necessary if the performance of either new-build or existing plants is to be firstly addressed and then improved. A simple example can be seen from the relationship between combustion control, flue gas temperatures, and both boiler efficiency and corrosion. Corrosion is inextricably linked to temperatures. Whilst it is easy to clean open pass boiler sections, cleaning of the congested superheater sections of a boiler is less straightforward, and with sticky and corrosive fly ash accumulating on superheater tubing, explosion cleaning is an expensive and necessary operation to be undertaken by many plants. Combustion and temperature control, flue gas temperatures, and open pass boiler section cleaning solutions all impact on the rate of boiler corrosion. Without a detailed understanding of the interactions of the plant sub systems/processes, the improvement in one area can easily have a detrimental impact elsewhere in the plant.
The pressures on the process
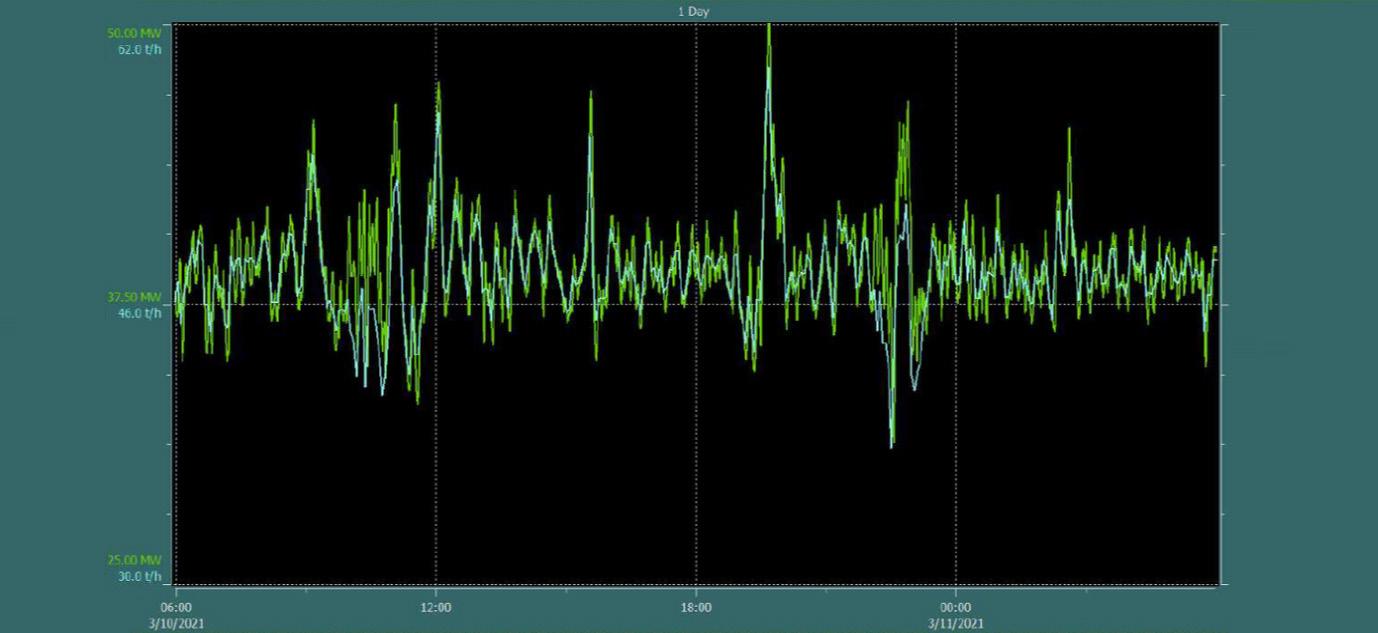
Figure 1. Typical (unstable) steam production data showing both steam and power production over a 24-hour period in a waste-to-energy plant. WtE plants represent a considerable financial investment. Suppliers of such plants feature considerable pricing pressures when bidding to supply new-build plants. These pressures impact upon margins, and so plants will feature the technologies that are necessary to pass plant performance tests. Additional solutions and technologies that could be integrated into the plants and which would maximise plant operation performance and profitability, unfortunately, are often missing. To the owner of a WtE plant, a 5% increase in the amount of waste processed can lead to significant additional earnings. In many cases, and particularly as plants increase in size, such performance improvements can lead to considerable additional revenues. As the price of power also increases within the open market, these annual increases to the revenue stream are repeatable and consistent throughout the lifecycle of the plant. They are not a one-shot single benefit.
Finding solutions to control the combustion process
Figure 2. Typical roof-mounted boiler installation. It has previously been stated that the WtE plant is a difficult process to control. The varying size, shape, and calorific composition of the waste being processed all contribute to considerable instability to the heart of the process – the combustion. There are many techniques and solutions that have been developed and implemented over the years with varying degrees of both sophistication and success. The conventional methodology for controlling the combustion process involves the traditional three-term PID controller. Whilst this works well for steady-state operational conditions, this type of control struggles to deal with the significant process delays seen by many of the control loops. Some of which, following a change to a particular control action, will fail to register a change in process conditions for prolonged periods of time (sometimes anything from 5 – 15 mins). Some solutions have implemented very complicated evolutions of the PID controller, others have tried a more conventional approach using techniques from other industries. Model predictive control, fuzzy logic control, adaptive self-tuning controls, and artificial intelligence are all solutions that have been tried and tested to varying degrees of success. In almost all cases, the final solution has been complicated, requires
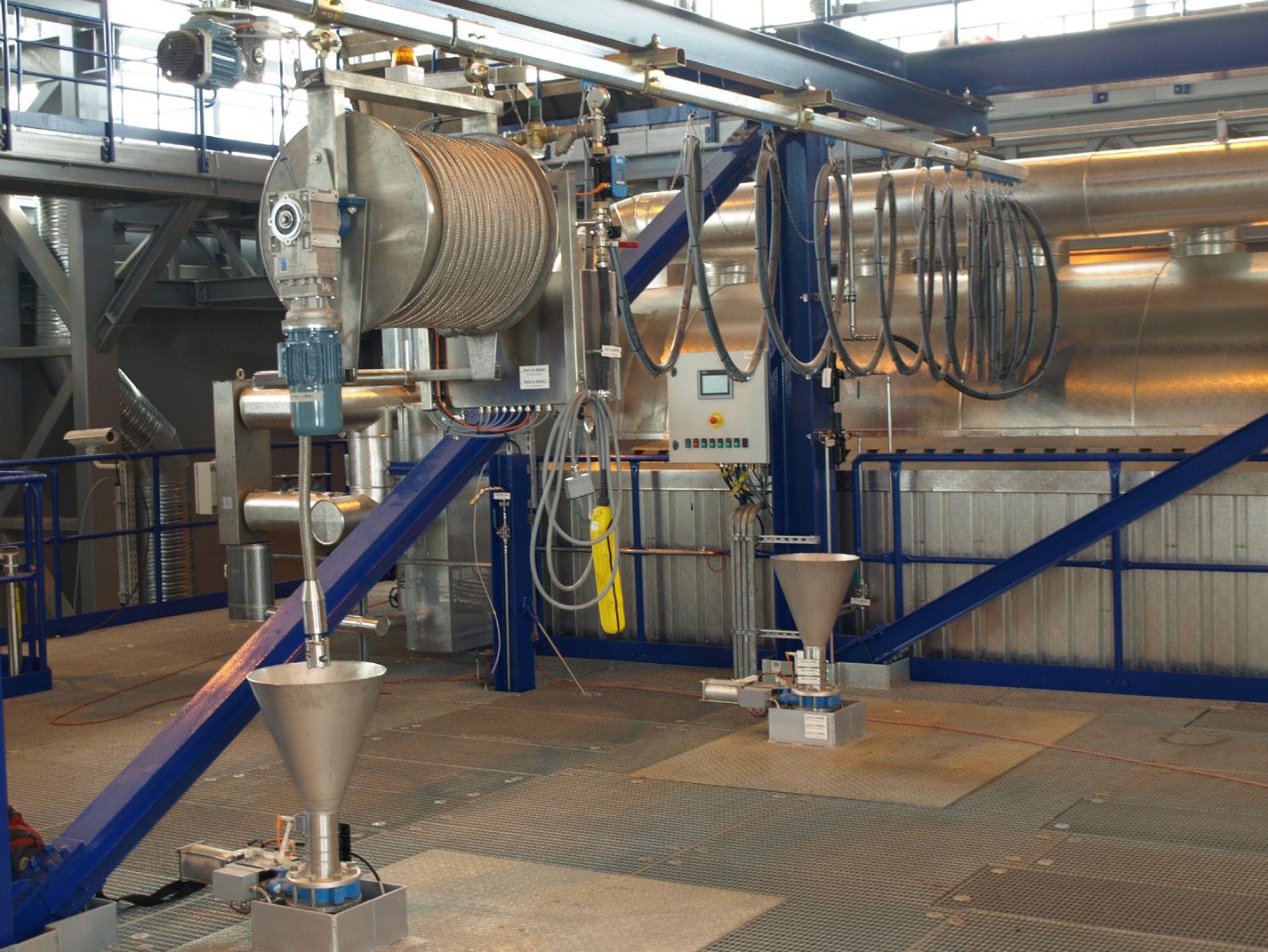
significant mathematical prowess from the author/designer, and the solution has been a ‘secret’, meaning that only the supplier can make changes/adaptations/modifications. And, of course, such solutions are normally accompanied by a significant financial consideration.
When investigating solutions for the improvement of WtE plant combustion control, truly open solutions should be investigated as a matter of course. A WtE plant is complex, meaning its performance and operation will change during its 20 – 25 year lifecycle. Complex control situations are difficult to understand and even more complex to modify. Simpler is best. Solutions exist within the marketplace where plant process engineers can be trained to implement performance improvement projects and where project/solution implementation and ownership can be retained in-house.
The heart of any power plant is the combustion process and the production of steam. Instability in steam production can be improved typically by approximately 20 – 25%. Improving such steam stability allows setpoints to be raised and will typically see an increase of 5 – 10% in the amount of waste processed, 3 – 5% increase in the amount of both steam and power generated, and significant improvements into the plant emissions levels. Nitrous oxide (NOX) reduction levels of 15 – 20% are readily achievable, and in a number of cases improvements to NOX emissions through the combustion control process have allowed a number of existing plants to retain and renew their operational permits in the light of tightening national emissions levels, without the need to provide complex and costly selective catalytic reduction (SCR) technology. The use of advanced controls to operate existing NOX reduction equipment (SNCR) has also proven to be a considerable success where again temperature is a critical contributing factor to the successful operation of such equipment.
Preventing corrosion
As a conventional WtE plant ages, lifecycle costs become a very serious consideration. A huge area of interest, focus, and attention can be found in the prevention and/or reduction in the levels of boiler performance and corrosion. Waste is often clearly acidic in its nature. Featuring varying levels of chloride content, sticky corrosive fly ash adheres itself to boiler walls and superheater tubing. Over time, this fly ash builds up on the boiler surfaces and heat transfer rates are seriously impacted, boiler efficiency deteriorates, and levels of corrosion accelerate. Furthermore, chlorides, especially zinc chlorides, form low melting eutectic liquids which are extremely corrosive for superheater boiler tubes.
An efficient ‘shower’ or water jet cleaning system can be effectively utilised to clean the open pass sections of the boiler, water jets impact upon the boiler walls, flash off to steam, and break up the fly ash deposits. An added benefit from such a cleaning process is then a reduction in flue gas temperatures and a corresponding reduction in temperature-related corrosion.
Such technology, however, does not work in the congested superheater section of the boiler. Here, the most widely accepted and practiced solution is the use of explosion cleaning. This is an established technique for cleaning the restrictive areas within a WtE plant boiler, but it is an expensive and time-consuming process.
Following extensive development over a six year period, a patented solution for cleaning the congested superheater section of a boiler has emerged. The results have shown reductions in corrosion within boiler superheater sections in excess of 55%. This patented solution utilises the principle of sulfatation. Sulfur is injected alongside the secondary air of the combustion process. This results in a chemical reaction taking place in which the chlorides within the flue gas are transformed into sulfates. The rate of conversion depends upon the concentrations of sulfur used, and the conversion is designed to take place prior to the sulfates making contact with the boiler tubes. The reaction takes place in the initial part of the boiler, and requires high temperatures and a high local oxygen excess rate. The results are significant, with considerable reductions in both corrosion levels and the necessity and expense for explosion cleaning.
The operation of a WtE plant is carried out by a number of operators and a plant-wide computerised control system. There are a number of manufacturers with experience in having delivered such systems but there is a huge variety with respect to performance improvements to the operation of such plants and the necessary accompanying process knowledge. For new-build plants, this is something the plant builder/EPC contractor is responsible for, but once the plant has met its post-contract performance requirements and the plant builder has moved on to the next project, performance improvements become the responsibility of the plant owner/operator. Performance improvement projects can be carried out by interfacing to almost any plant-wide computerised control system, regardless of manufacturer, and do not require significant additional replacement costs to be a consideration.
Yokogawa Electric has invested considerably in technologies and solutions for improving the performance operation and profitability of both WtE and biomass power plants. Recently, Yokogawa Electric acquired the shares of Dublix Technology, a Danish company with approximately 30 years of expertise in both product and solutions dedicated to the performance improvement of such plants.
Yokogawa solutions improve the performance of WtE and biomass plants with solutions dedicated to:
F Increasing the stability of the combustion process.
F Increasing the tonnage of waste processed.
F Increasing both the steam and power production.
F Reducing plant emissions, specifically NO
X and CO.
F Improving boiler efficiency.
F Reducing levels of plant corrosion.