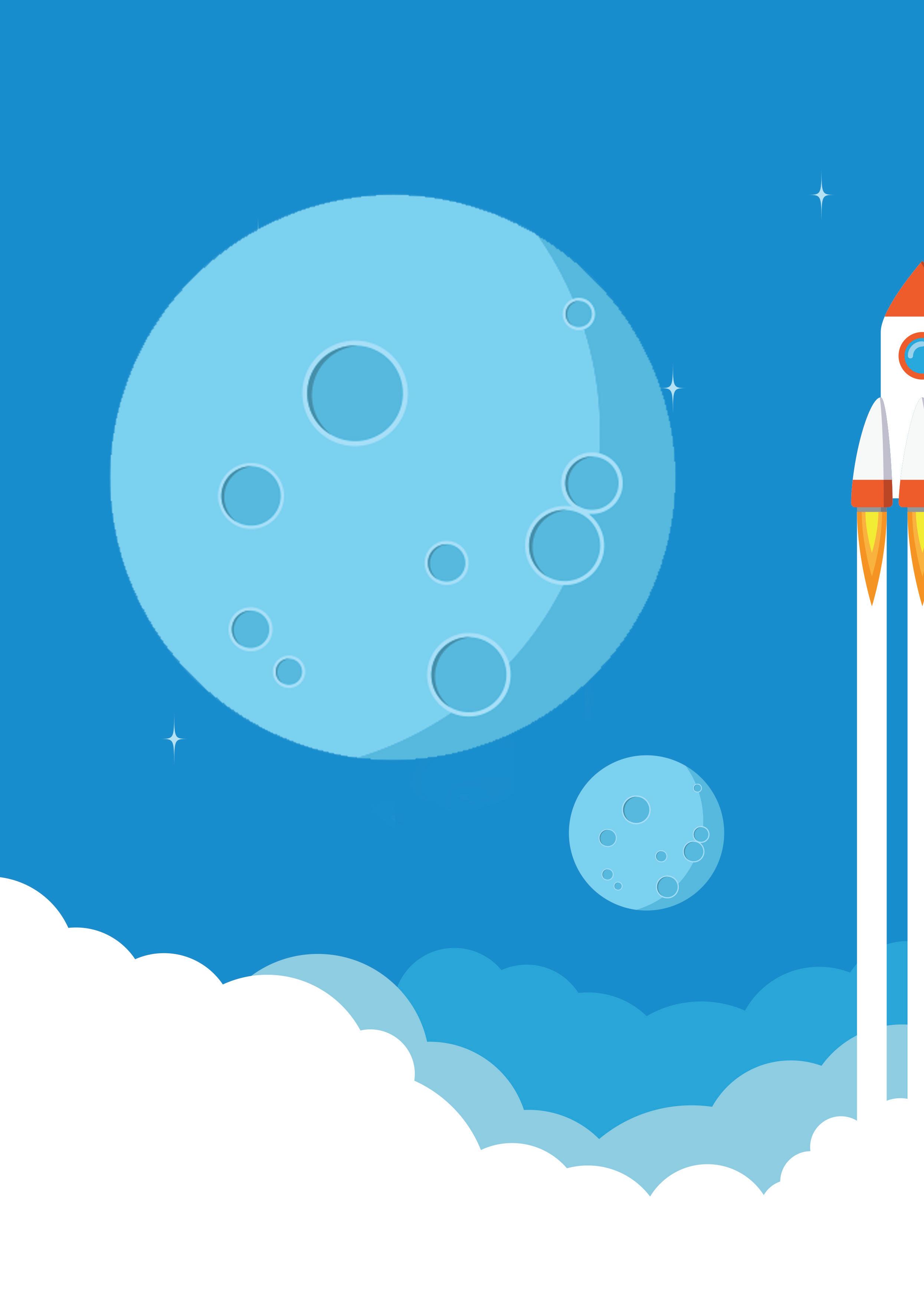
8 minute read
A boost for green hydrogen
The main target of this year’s 26th UN Climate Change Conference is to secure global net zero by the middle of the century and keep 1.5˚C within reach. Hydrogen (H2) is set to play a key role in the defossilisation of various sectors and industries and in realising climate-friendly mobility options. It is produced by using electricity to electrolyse or split water into hydrogen and oxygen. When the energy is sourced exclusively from renewables, it is called green hydrogen (green H2), which prevents both local and global carbon emissions. While many market players believe that the pathway to cost parity with grey (SMR-based1) or blue (SMR-based, combined with CCS2) hydrogen involves significant CAPEX reduction and efficiency improvement in the electrolysis technology, the truth is that the levelised cost of hydrogen (LCOH) is much more dependent on:
F The right location, where renewable electricity is widely available at an attractive levelised cost of electricity (LCOE) and high load factors.
F The availability of a suitable H2 infrastructure for efficient transport and storage over the next 5 - 10 years.
When considering the example of a 100 MW PEM electrolysis system with a 2021-level project realisation cost and the current technology maturity/efficiency, and comparing both to the 2025 outlook, it can be shown that the
Andreas Rupieper and Dr. Volker Goeke, ITM Linde Electrolysis,
Germany, explain how hydrogen can support defossilisation and outline the steps needed to make it happen, providing insights into the enabling technologies and measures, the costs, and success stories.
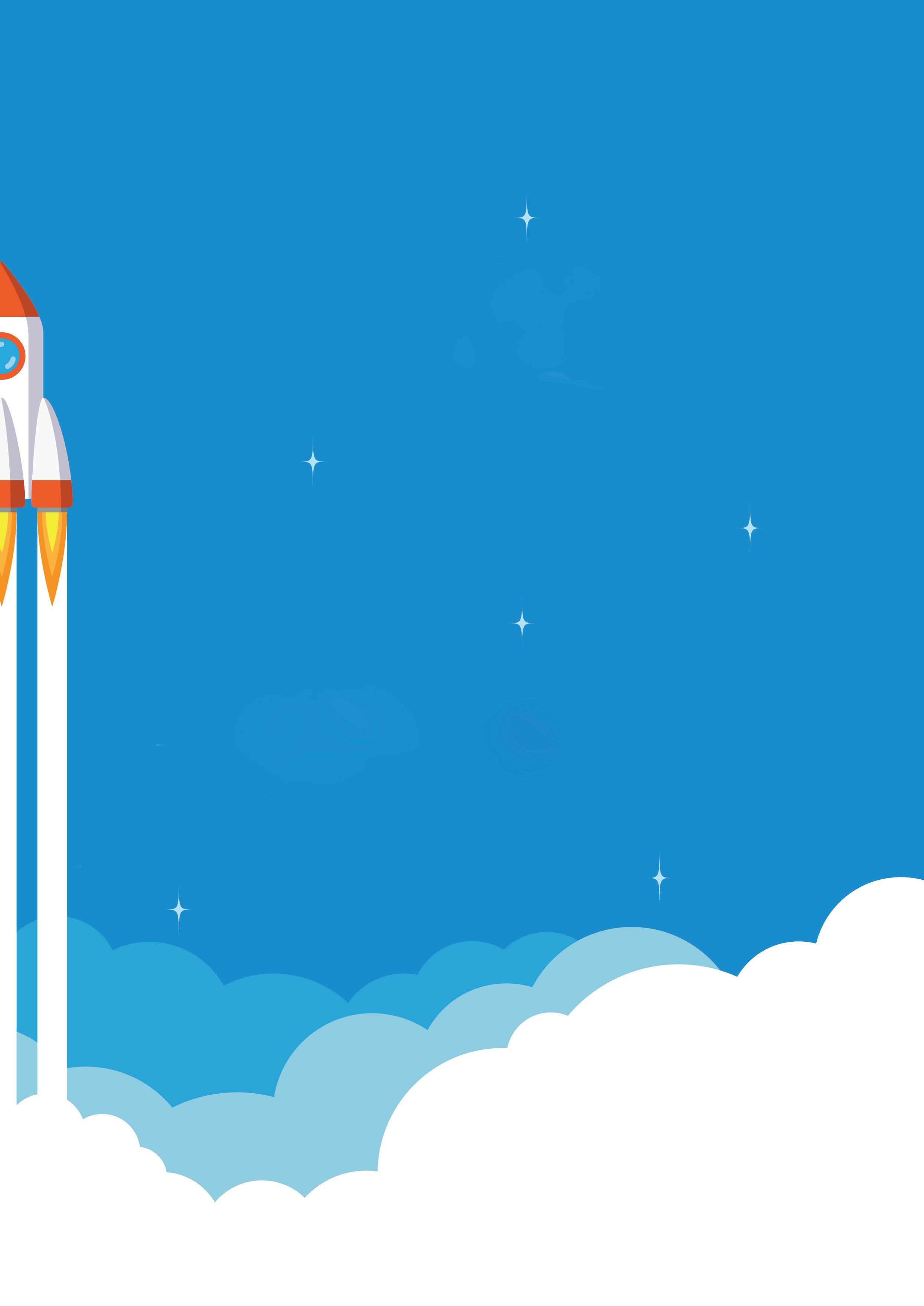
efficiency and CAPEX improvement from expected innovation and industrialisation would only reduce the LCOH by approximately 15%. This is not nearly enough for cost parity.
Favourable renewable energy conditions on the other hand allow a >40% reduction in LCOH, which is an important and much-needed step to reach the €2/kg hydrogen target.
At today’s natural gas prices in Central Europe and without penalties from emissions trading systems, the LCOH for green H2 tends to be up to three times higher than for grey hydrogen, subject to the employed power cost. The LCOH of green H2 can drop to cost parity over the next five years, but only if the renewable LCOE comes down to values between €20 - €30/MWh, and if combined with the expected CAPEX improvement and efficiency increase as result of product maturation and industrialisation. In any case the LCOH is much dependent on the power cost.
Under this scenario, the main challenge is how to achieve an acceptable LCOE to reach the targeted LCOH and improve the overall economic viability of green H2. Linde sees three main contributors:
The electrolysers must be located in places with a favourable electricity cost
Today’s typical SMR-based hydrogen production is located beside large primary industry consumers, e.g. refineries, and chemicals manufacturers. The molecule is delivered as ‘over-the-fence’ via a short pipeline connection from a central production plant.3 Such plants are often piggy-backed with bulk consumers, where the molecule is transported by trailers to the distributed consumers of the secondary industry (metals, glass, food, paper, electronics, etc.). So, the central hydrogen production plant is located where the largest single-point consumption occurs, and this can be done because natural gas as the primary feedstock is made available via an unbelievably dense pipeline infrastructure. Unfortunately, when changing hydrogen production from fossil to green (with electricity now becoming the number one feedstock), the business cases typically suffer from high LCOE of >€50/MWh. This inhibits investment and defossilisation.
Hydrogen consumers committed to defossilisation now have two alternatives: F Moving the hydrogen-consuming value chain to areas with a low LCOE, which is costly and difficult in many aspects.
F Connecting the point of hydrogen consumption with the areas of industrial use with a dedicated hydrogen pipeline.
The second option requires the political will by governments, e.g. in Europe, to set up a Europe-wide hydrogen pipeline infrastructure to connect attractive renewable energy locations for central green H2 production with the areas of industrial use. Instead of the electrons, the molecule is transported. This has a number of advantages: F Hydrogen pipelines represent the most cost-effective option for long-distance and high-volume transport, with costs ranging from €0.11 - €0.21 per 1000 km per 1 kg of hydrogen; the existing natural gas pipeline grid can be converted to pure H2 use in acceptable time frames.4
F Extra power grid congestion is prevented: the non-avoidable energy loss of electrolysis (today approximately 25% of gross power consumption), resulting in waste/off-heat, does not need to be transported via the power grid.
F With a dedicated hydrogen pipeline grid, today’s large scale industry consumers, as well as future consumers (e.g. steel sector for direct reduction of iron) can be efficiently procured.
F Road transportation of molecules to procure distributed secondary consumers can be significantly reduced.
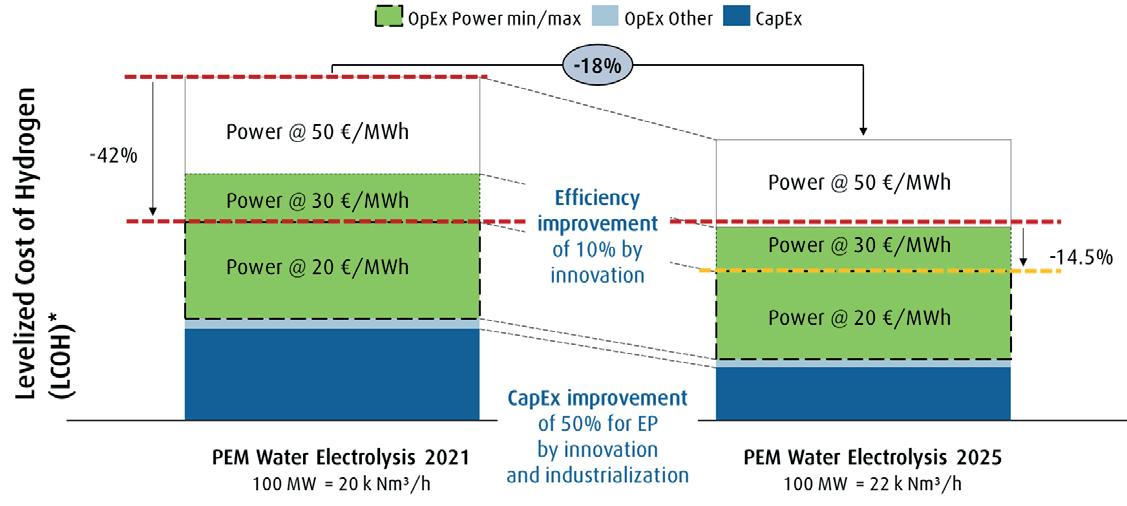
Figure 1. Levelised cost of hydrogen – 100 MW central plant in 2021 vs 2025.
Figure 2. Electrolysis as a solution provider when taking the upstream optimisation and the byproducts valorisation into account.
The electrolysers must be flexible for the intermittency of the renewable power
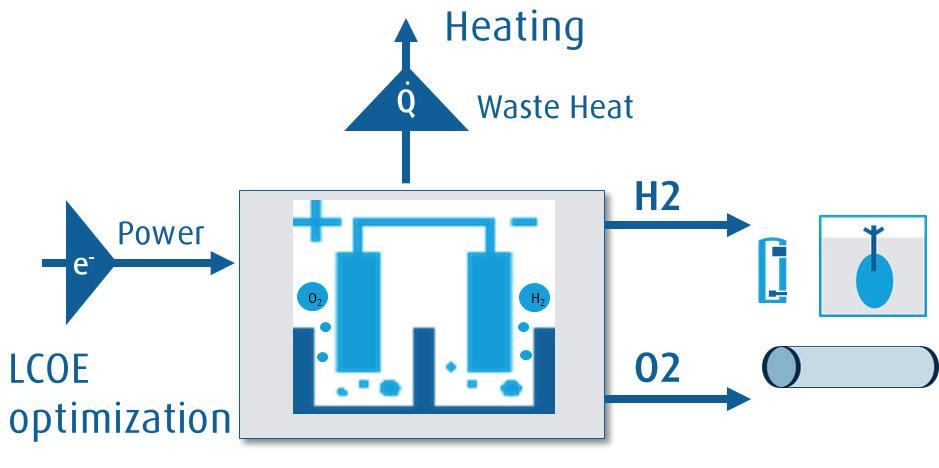
Designing an optimally configured electrolyser under renewable energy conditions is challenging since renewable energy does not flow 24/7 at peak power like natural gas, and power costs are not constant if engaged in the spot market. Accordingly, the sizing of an electrolyser must consider both gas demand and renewable power availability: F On the supply side, customers typically specify the renewable energy via an annual power profile, using an hourly or 15 min. time resolution.
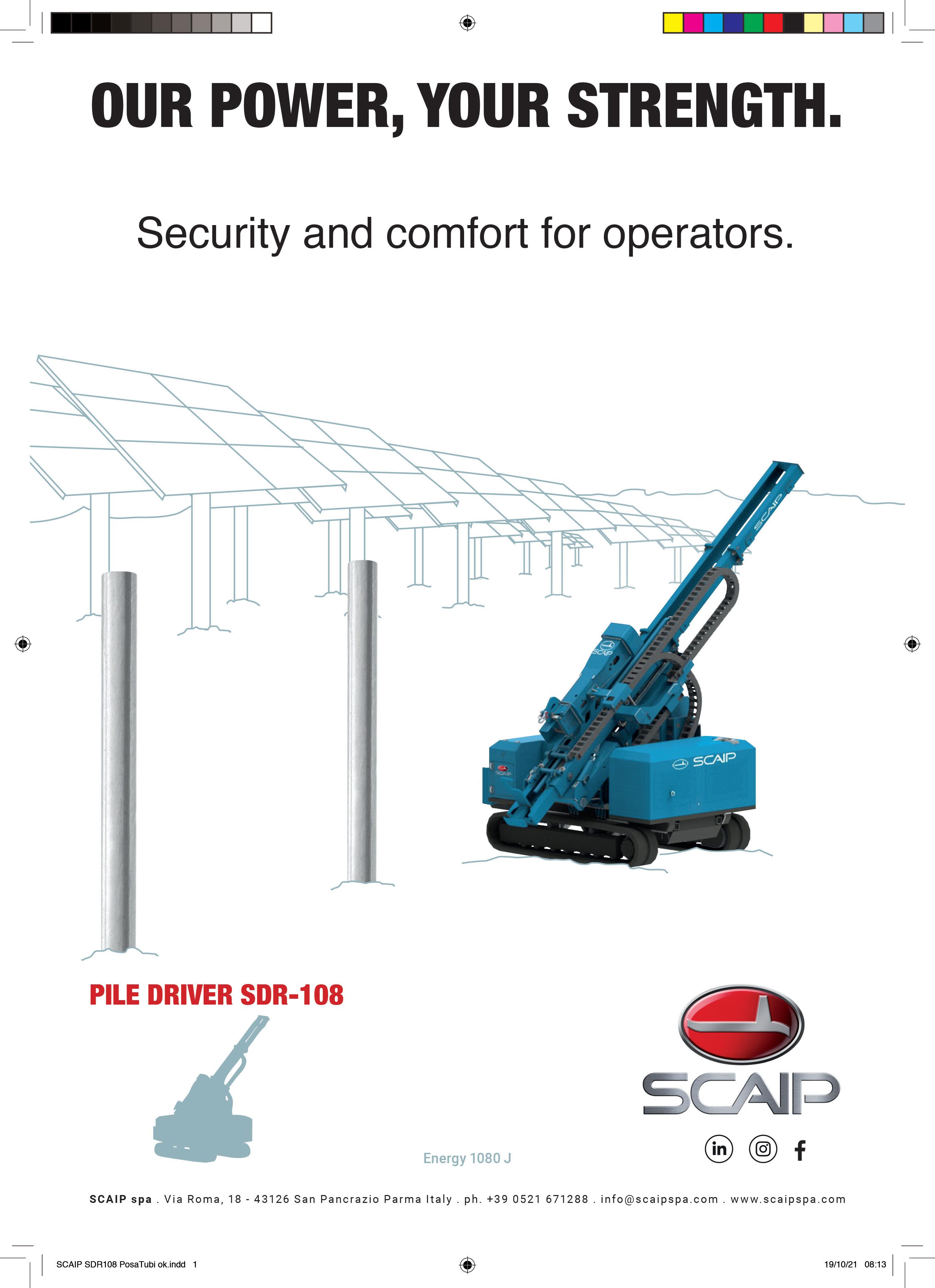
F Also, the gas demand side may be more discontinuous than experienced, since new green H2 applications such as H2 mobility specify highly fluctuating refuelling patterns, both from a weekly and seasonal point of view.
Hence, choosing the configuration leading to an optimum LCOH is not straightforward, but rather the result of a dedicated optimisation run.
Linde has developed a software product called Clean Hydrogen Business Modeller (CHBM), which does exactly this job. For better balancing of the demand-supply equation, two storage options, electrochemical batteries and compressed hydrogen tanks, are considered – variable in size.
Besides renewable energy pricing and gas demand profiles, the tool considers further basic financial assumptions as specified by the user and of course including downstream requirement such as H2 pressure.
CHBM features a results page, where the improvement in LCOH reduction is broken down into single contributions, such as LCOE or optimum load point operation of the electrolyser. The tool is currently being extended to cover the upcoming electrolyser technology for XXL plants, and provision to give expert users more flexibility in specifying inputs, boundary conditions, and cost optimised production of green H2 based chemicals, such as green ammonia.
The electrolysis is beyond hydrogen supply
When extending the revenue streams of an electrolysis by operational flexibility towards grid services or when optimising the LCOE by curtailed power management and arbitrage, the whole value chain and electrolysis operation must be adjusted accordingly.
Linde uses its CHBM to analyse and optimise the overall plant configuration, starting with the green power profiles to match the demand of the green gases. The modeller factors in volatility in the power price and availability, and the customer’s molecule demand.
For byproduct valorisation, converting waste heat to off-heat use not only improves the overall efficiency, but can also help to close the growing gap in district heating when coal-fired power plants are shut down in Central Europe. Alternatively, the heat can be exported to greenhouse farming.
Also, (green) oxygen as a byproduct can be used as an additional revenue stream in different applications such as oxyfuel (pure oxyfuel or combustion air enrichment) or wastewater treatment or sustainable fish farming (when the electrolysis plant is in coastal regions).
Green hydrogen – a success story
Linde has been systematically investing in hydrogen technologies and advancing them to market maturity for more than four decades. The company is a leading provider along the entire hydrogen value chain – from production to the application.
All discussions about a greener future powered by hydrogen come down to one core technology – the electrolyser. Linde decided in 2015 to partner with the British company ITM Power, a leader in the area of proton exchange membrane (PEM) technology. In 2019, the two companies set up the joint venture ITM Linde Electrolysis (ILE) to bundle the complementary core competencies. Through this joint venture, Linde can deliver end-to-end green hydrogen solutions, covering every step in the project lifecycle from concept engineering and feasibility studies through EPC proposals and cost estimates to engineering services and turnkey handover to the operator.
Linde can point to several flagship projects that clearly illustrate the fact that green H2 is on a growth path. Establishing a broader production base for green hydrogen is the aim of one reference project based at the Leuna chemicals complex in Germany. This is where the world’s largest PEM electrolyser operated by Linde is set to commence operations in the second half of 2022. Linde Engineering together with ILE are building the plant to supply industry customers with green H2. Leuna’s current capacity for hydrogen produced by electrolysis is 4500 m3/h. When the PEM electrolyser, which will initially operate using certified eco-power, switches to renewable energy generated locally mid-2022, the plant will be able to produce up to 3200 tpy of green H2. This would be enough to fuel approximately 600 fuel-cell buses, allowing them to travel 40 million km while reducing carbon dioxide emissions by up to 40 000 tpy. More sucess stories can be found on Linde Engineering’s website.
Figure 3. Clean Hydrogen Business Modeller (CHBM) stage 1: Key system components and configuration.
Notes
1. Steam methane reforming (SMR) is where CO2 emissions are typically approximately 10 t of CO2 per tonne of hydrogen. 2. Steam methane reforming with carbon capture and storage (SMR with CCS) where the CO2 emissions from the SMR process are captured at a rate of between 55% and 95% and sequestered in safe geological formations for permanent storage of the CO2. 3. Industrial scale = 20 - 100 000 Nm3/h hydrogen production capacity. 4. According to a recent study by the European
Hydrogen Backbone (EHB), Gas for Climate press release, 13 April 2021, ‘European Hydrogen
Backbone grows to 40 000 km, covering 11 new countries.’
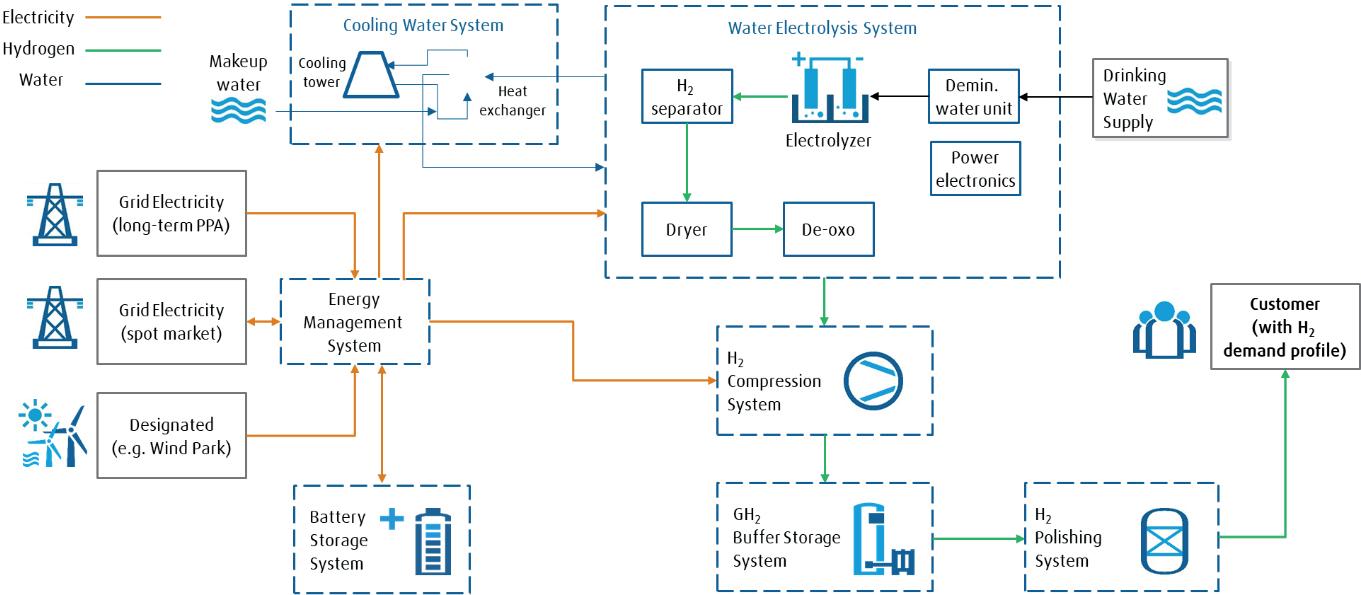