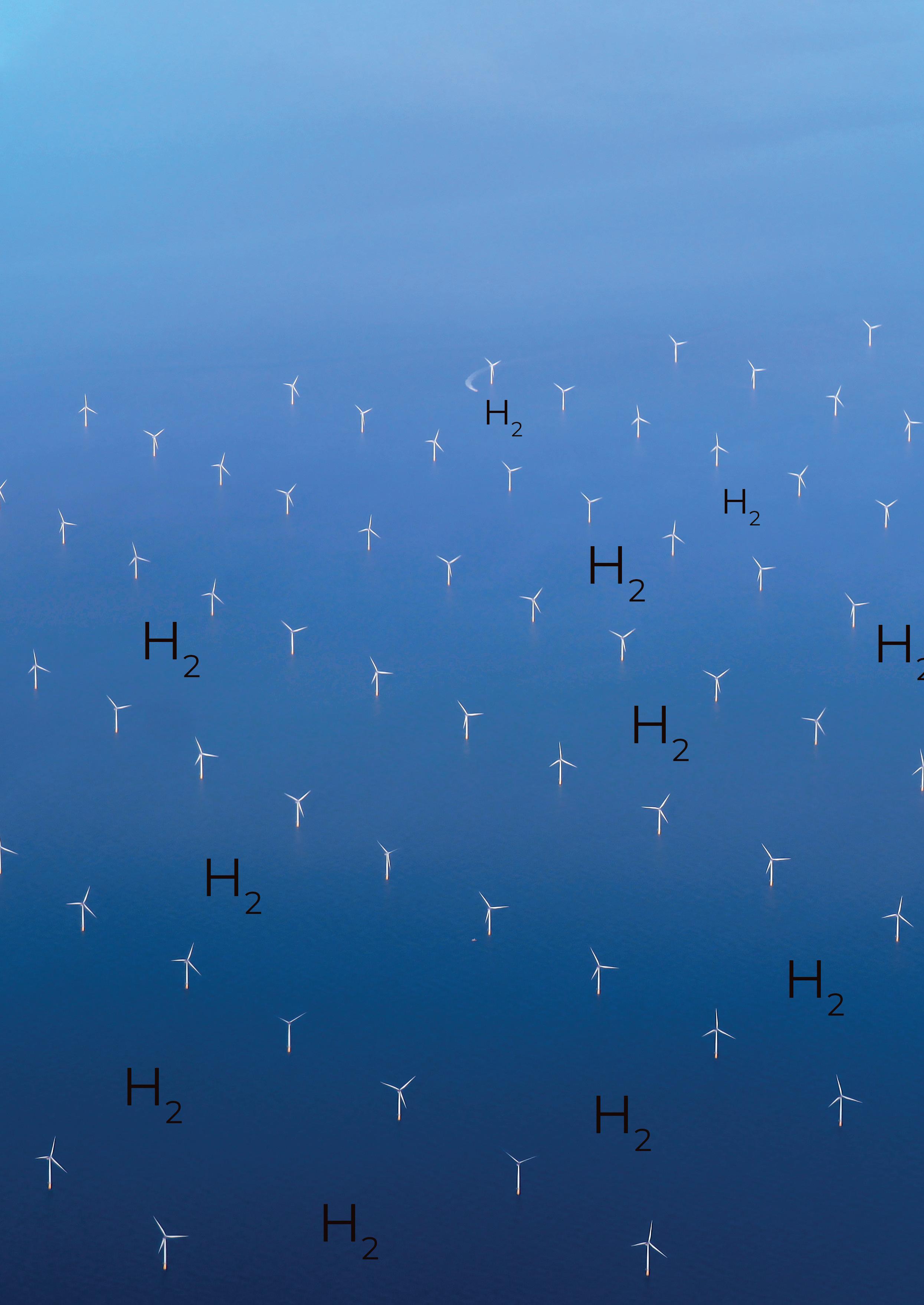
11 minute read
Offshore wind + hydrogen = the future?
Nigel Curson and Neil Service, Penspen, UK, detail why making informed decisions on whether reusing existing infrastructure or starting afresh to bring green hydrogen onshore could make the greatest economic and environmental sense.
Life – business and personal – has not been without its challenges in recent years. But there is another one facing many organisations as offshore wind becomes the world’s fastest growing renewable energy source. Estimates suggest the sector is forecasted to expand from a generating capacity of approximately 30 GW today, to 190 GW by 2030. But with challenges comes opportunity.
Supported by environmental policy targets and falling technology costs, the International Energy Agency has predicted offshore wind will become a US$1 trillion industry over the next two decades. The size of this potential market is encouraging asset owners to weigh up the potential for repurposing existing offshore oil and gas assets for wind – or to consider building new infrastructure.
In the UK, the Offshore Wind Industry Council says there is potential for the generation of up to 1000 GW – well above the 75 - 100 GW likely to be needed for UK electricity generation by 2050. This opens up the potential of growing the offshore wind industry beyond local electricity requirements, to the production of green hydrogen as offshore wind costs continue to fall.
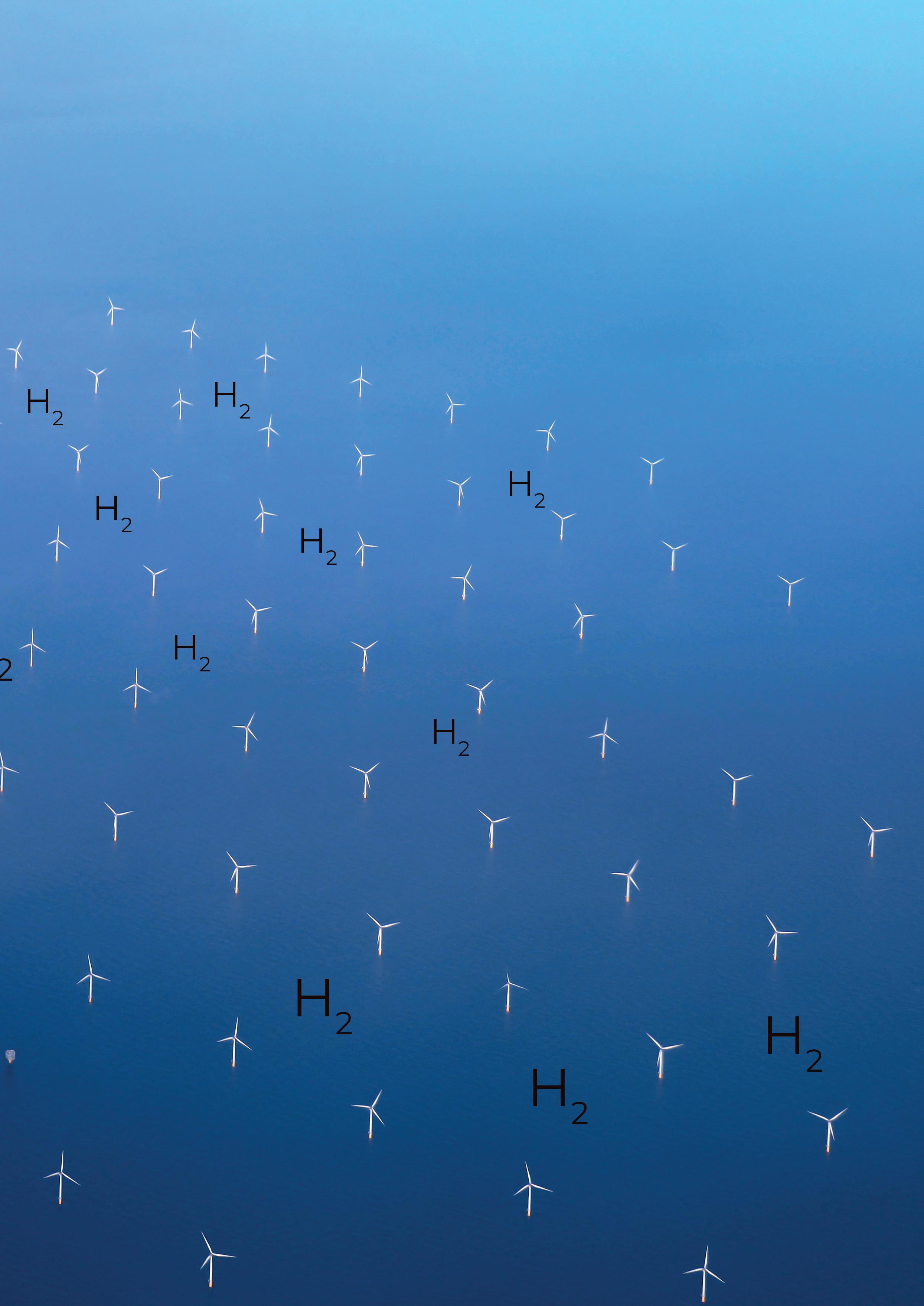
Support for hydrogen
The international community – including the UK – is committed to the benefits of a hydrogen-based energy economy.
F According to the Global Wind Energy Council, of all renewable energies, offshore wind and wind/solar hybrid projects have the highest potential to improve the economics of green hydrogen projects due to cost competitiveness and scalability.
F Onshore wind became one of the cheapest new sources of electricity in 2020, while offshore wind has delivered a global levelised cost of electricity (LCOE) reduction of more than 67% over the last eight years.
F The Hydrogen Council estimates the market for hydrogen and hydrogen technologies will reach revenues of more than US$2.5 trillion/y and create jobs for more than 30 million people by 2050.
F Overall demand for hydrogen in the UK is predicted to increase up to 300 TWh, comparable to the nation’s electricity system today.
Environmental benefits of green hydrogen
Various colours are used to identify hydrogen production, from blue to green, brown, pink, yellow, white, grey, etc., with carbon neutral green hydrogen produced by electrolysis using a renewable energy power source such as offshore wind.
The Offshore Wind Industry Council estimates green hydrogen from offshore wind could cost less than blue hydrogen (produced using natural gas) by 2050.
Electrolytic hydrogen production splits water into hydrogen and oxygen. However, electrolysis currently faces several challenges: F Alkaline electrolysers do not work well with intermittent renewable sources, but alternative technologies such as proton exchange membranes (PEM) are being developed to address this.
F The efficiency and lifespans of electrolysers need to be increased to make them more economically viable and scalable, and the development of new electrodes and catalysts will lead to improvements and decreased costs.
F Despite these challenges, the production of hydrogen at scale using electrolysis is an essential long-term requirement in achieving net zero carbon emissions objectives.
Whether to reuse or build new
The significant increases anticipated in demand for both offshore wind and green hydrogen are key components in the energy transition as the global focus shifts from hydrocarbons to renewable sources. However, it creates several important questions for existing offshore oil and gas asset owners, asset developers, technology owners, and integrity engineers to consider. These include: F Can renewed value be found from redundant assets or infrastructure such as pipelines and platforms by reusing them for green hydrogen? F Is doing this technically feasible or economically viable based on a through-life cost basis compared with a cabled supply?
F What are the economic benefits of deferring abandonment (for example, 20, 30, or 40 years) by repurposing the asset?
F Would the deferment of abandonment result in cheaper energy?
There are several challenges when it comes to examining the reuse of existing infrastructure. However, key considerations include asset safety, the costs of maintenance, asset capacity, and infrastructure compatibility.
The most important issue relating to hydrogen and pressure containing equipment compatibility is embrittlement or material degradation through enhanced fatigue and mechanical joint leakage. This can lead to a reduced operational pressure in the pipeline and reduced capacity, a problem when also considering the relatively lower energy value of hydrogen on a volumetric basis.
Using wind power to generate energy offshore which is then transported for use onshore will require high voltages and DC to avoid significant losses.
A world-first pilot project using wind power to generate hydrogen offshore and transmitting via the use of an existing gas pipeline system – PosHYdon – is being developed off the coast of the Netherlands. Using the Neptune Energyoperated Q13a-A platform 13 km offshore Scheveningen, electricity generated by offshore wind turbines will power the containerised hydrogen plant on the platform, converting seawater into demineralised water and then into hydrogen by electrolysis. The green hydrogen will be mixed with produced natural gas and transported via an existing gas pipeline to the coast. The 1 MW electrolyser will produce a maximum of 400 kg/d of green hydrogen.
The aim of PosHYdon is to gain experience of integrating working energy systems at sea and the production of hydrogen offshore. However, the offshore hydrogengenerating process raises several points for consideration relevant to its more widespread adoption in the future.
A high degree or purification of water is currently required for electrolysis whether onshore or offshore. Although there are some seawater-capable electrolysers currently in research and development, there are none on the market. The question of how practical and cost-efficient it is to build and maintain a water purification plant offshore, compared to running a pipeline from the shore to the platform, is important. Consideration must also be given to disposal of the high volume of produced solids. Likewise, a thorough assessment of whether an existing platform is suitable for mounting an electrolyser, in terms of the weight and space required, will be critical.
When it comes to investment, decisions on the most appropriate method for offshore green hydrogen production will be driven by which solution delivers the most appropriate through-life cost. With existing assets or infrastructure, this must include an assessment of the cost savings in deferred
Connecting the world of hydrogen –
From source to service
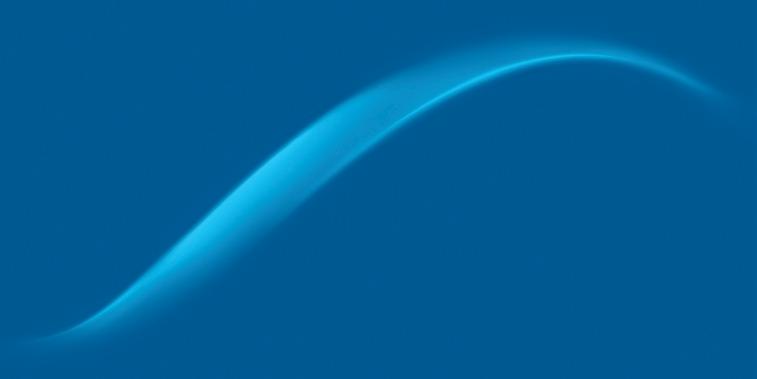
The hydrogen future is here now. And Linde can deliver it. The company covers every link in the hydrogen value chain from source to service – whether it be used as a zero-emissions source of fuel for trains, buses and cars; a feedstock gas for industries such as steel and refining. And the best bit: Hydrogen can be generated at scale with a zero carbon footprint by using renewable energy such as wind power to separate water. Regardless of your target application, we have the technologies and expertise to support your project.
Think hydrogen. Think Linde. linde-engineering.com/hydrogen
abandonment – which may be put off for 20 years or more – compared to how long the asset can be expected to last and what the cost of maintenance would be.
The production of hydrogen offshore will be complex and capital-intensive: F Electrification will require cables, j-tube to protect the cable from the seabed to the topsides and electrical isolation, rectifiers, and controllers.
F The hydrogen process requires desalination of the seawater.
F Production will require electrolysers, a buffer tank, and a compressor.
F Static equipment will include piping, valves, a flare stack or vent stack, metering, and instrumentation.
F Rotating equipment will include a non-centrifugal compressor and power generation – either hydrogenfuelled gas turbines (if powering the platform by hydrogen) or stand-by diesel generators.
On top of these aspects, all the existing standard offshore platform components will be required, such as a lay down area, cranes, a heli-deck, accommodation, and life boats.
The condition and integrity of existing pipelines will also have to be assessed. These may not have much operational life left in them as many have been in operation beyond their original design life. In addition, the size of the pipelines and safe operating pressure may limit the energy throughput.
When considering the jacket structure, many jackets have been in place longer than they were designed for, thus creating integrity and degradation issues. Furthermore, the jacket will have a limited load bearing capacity. This will ultimately limit what can be installed on the topsides (by weight), which in turn could limit the production output from the electrolysers.
Upgrade complexity, asset location, topsides configuration, plot space, and even the insurance implications of using a repurposed asset have to be taken into consideration. Pipes must be piggable so that an inspection tool can be run to check for hydrogen embrittlement and other degradation issues.
Hydrogen accelerated fatigue is another limiting factor. Whilst electrolysers may be able to increase or reduce production as renewable energy supply fluctuates, the potential constant cycling of topside plant and the subsea pipelines will need to be addressed.
With all the above points taken into consideration, asset owners will be better able to make informed decisions on whether reusing an existing asset or infrastructure vs a new
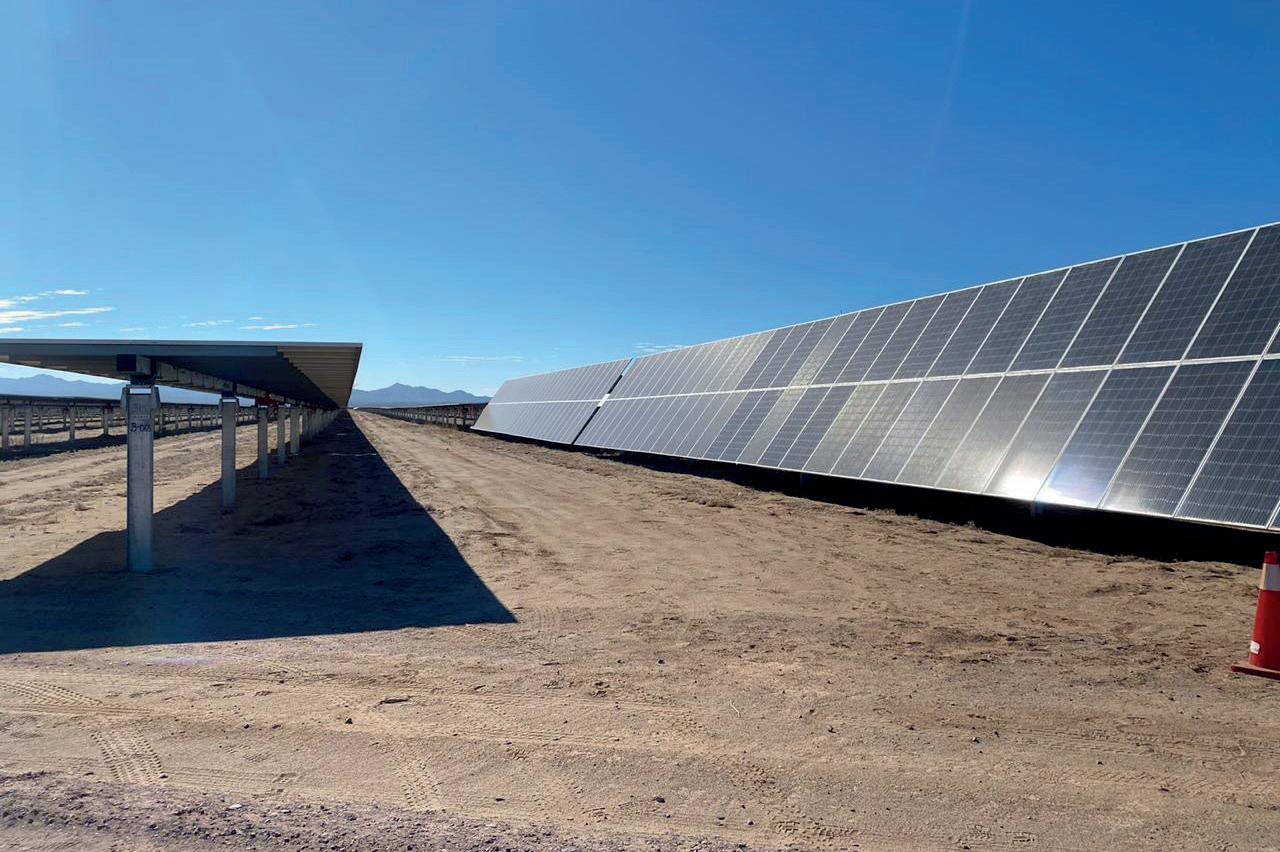
Figure 1. Solar can play a powerful role in amplifying green hydrogen production.
build makes the greatest economic and environmental sense.
Meeting the challenge
In making such decisions, it is important for asset owners to enlist the support of a partner with solid expertise and a full understanding of hydrogen-related projects. This may include: F The design and installation of hydrogen pipelines, storage systems, and production systems.
F The maintenance of hydrogen, blended hydrogen, and CO2 networks.
F Regulatory support.
F Technical specifications and material selection recommendations.
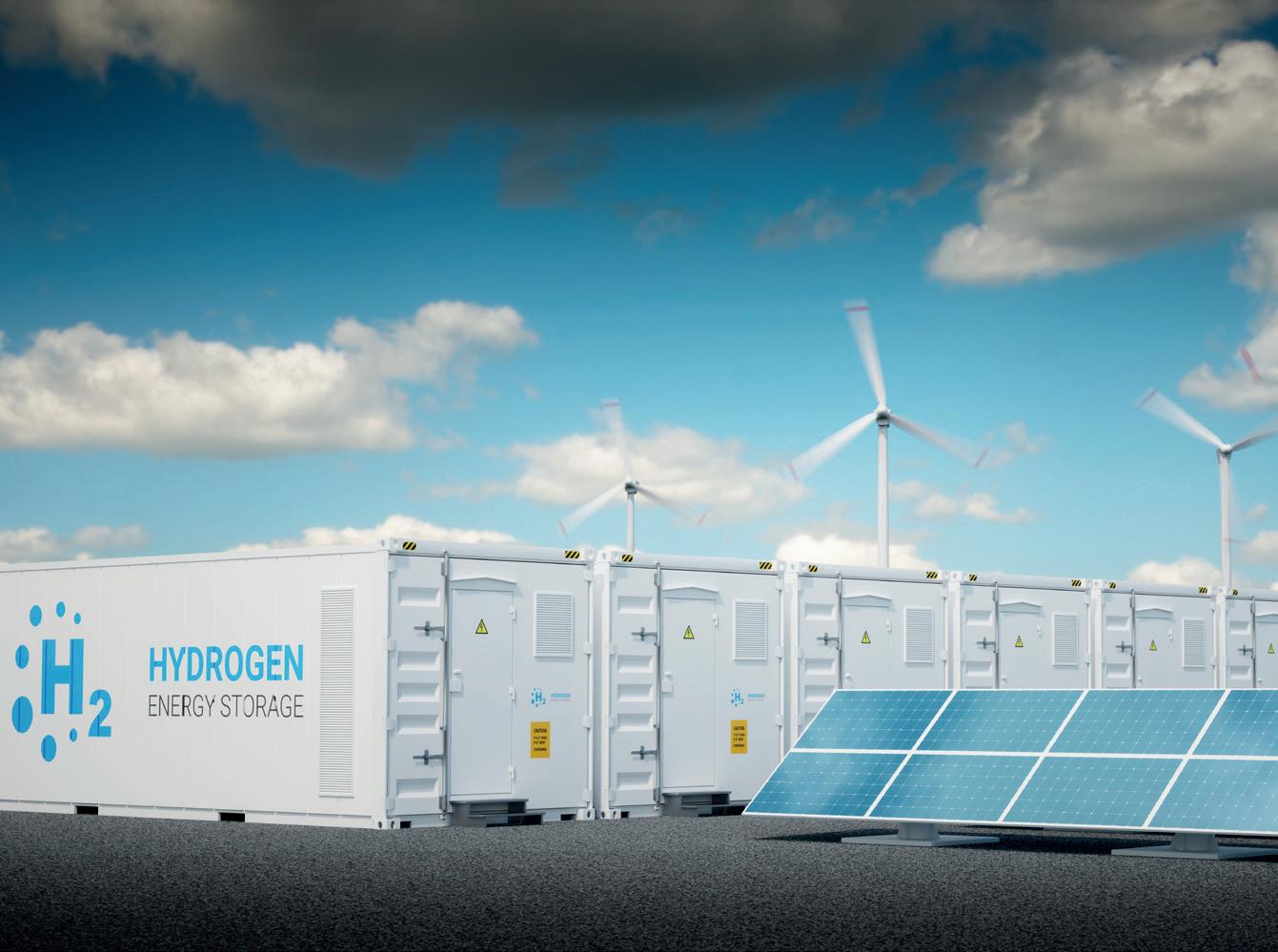
Starting the process
Figure 2. Green hydrogen has been identified as a key potential route to speed up the transition to a carbon neutral future.
The transition work required to bring green offshore hydrogen onshore is complex and requires detailed preparation. For asset owners, a critical component of this initial work is a feasibility assessment and review of existing onshore assets.
As an example, Uniper UK Ltd recently commissioned Penspen to carry out a fitness for continued service assessment, site audit, hydrogen feasibility technical report, and design and integrity review for the Theddlethorpe to Killingholme (KIPS) and Blyborough to Cottam (BCot) pipeline systems. These systems are designed to provide gas to Uniper’s owned and operated power plants at Killingholme and the Cottam Development Centre (CDC) respectively. The CDC is a combined cycle gas turbine plant, with a generating capacity of 400 MW.
Uniper is investigating the possibility of blending hydrogen with natural gas at various ratios, up to 100% hydrogen, together with the suitability of the existing BCot and KIPS system assets.
The hydrogen percentages in natural gas to be considered are 5%, 10%, 15%, 20%, 30%, 50%, and 100% hydrogen. Uniper requested a study to determine the feasibility and system compatibility with hydrogen.
The study incorporated all pipeline system elements, including the pipeline, inlet and outlet points, block valve stations (BVS), above ground installations (AGI), pressure reduction stations (PRS), and off-takes.
The services delivered included a site audit and the undertaking of assessments at various levels. These included a collation and review of asset documentation; an equipment inventory audit; system flow assurance and thermal input assessment; hydrogen degradation mechanisms; AGI equipment, pipeline design and integrity reviews; safety assessments, including venting and hazardous area zones; maintenance and inspection changes; a pipeline quantitative risk assessment (QRA); personnel competency and training, emergency response, and regulatory requirements.
The compatibility of equipment and assets with hydrogen at different blend increments was determined through codes and standards requirements, relevant industry and academic research, industry best practices and lessons, as well as engineering assessments.
Penspen provided Uniper with a hydrogen feasibility technical report, containing fitness for continued service evaluations of the above ground equipment and pipelines within the two systems. This determined at what percentage of hydrogen the existing system components are suitable and at what point further assessment, modifications, or replacements are required to continue operations.
Penspen also produced an extensive list of recommendations, highlighting further work required to ensure the assets are safe and ‘hydrogen ready’ prior to transitioning, plus an implementation plan of the next steps to be taken.
Conclusion
Offshore wind has been identified as a rapid growth energy source, and hydrogen as an important energy vector. The combination of the two represents an exciting prospect for the UK’s expansion of renewable energy. It creates significant business growth opportunities, too.
To facilitate that growth and to maximise economic returns, asset owners, asset developers, and technology owners/integrity engineers have key decisions to make on whether to reuse existing offshore infrastructure or build anew, a challenge that Penspen is well-equipped to help them rise to, whilst driving positive change for a greener, more sustainable energy future.