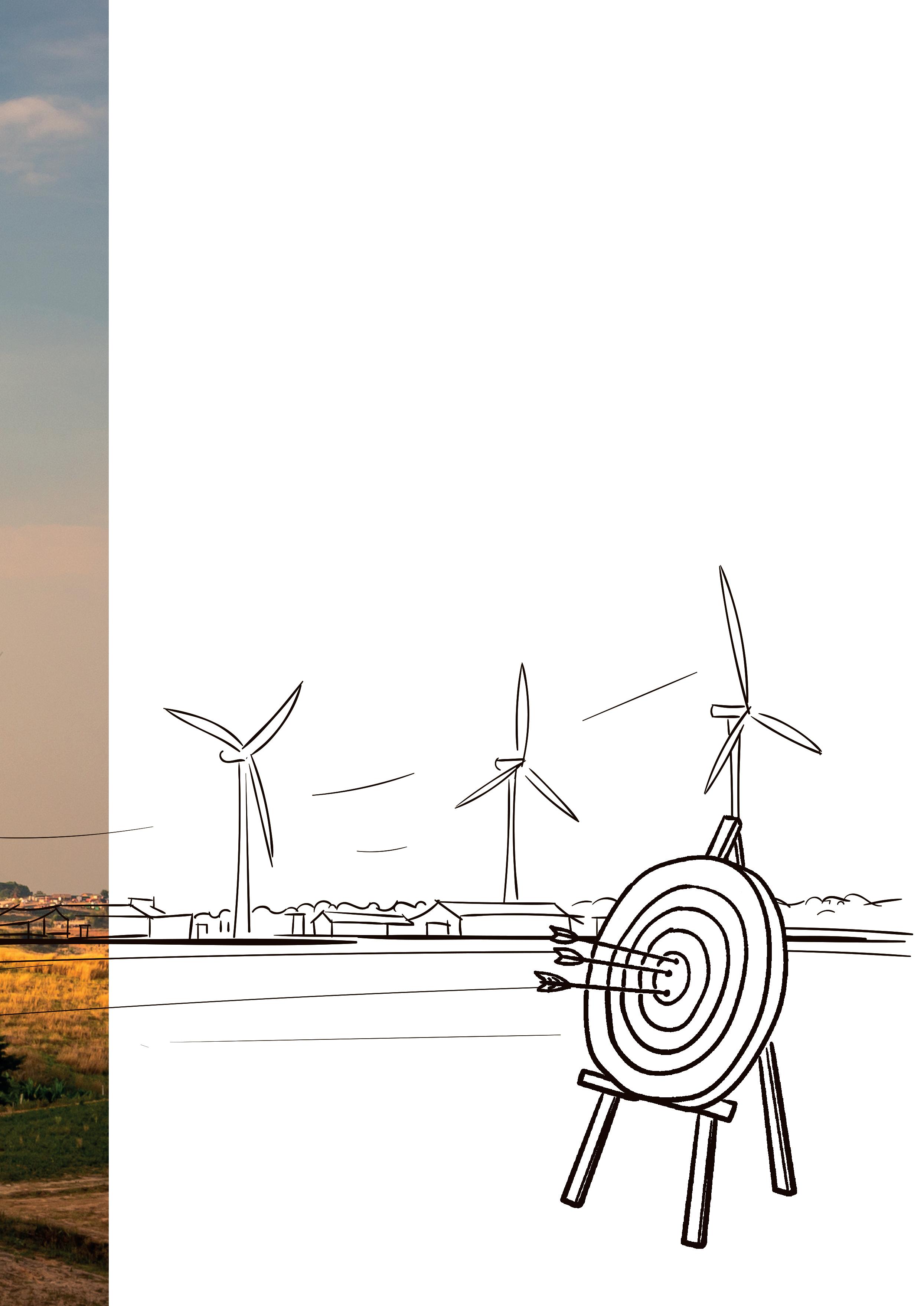
9 minute read
The goal: hit the sustainability targets
Emma Mallinson, Shell Naturelle, UK, explains why the world needs an effective and environmentally sensitive wind power industry, and how lubricants can assist on this journey.
With every passing year, the need for more sustainable sources of power becomes clearer. Roughly two-thirds of global greenhouse gas (GHG) emissions were associated with heating, electricity, transport, and industry energy production in 2016, reports the European Environment Agency. Since then, considerable steps have been taken to decarbonise the energy supply chain with renewables leading the way in reducing emissions.
In 2020, CO
2 emissions in the power sector dropped by 3.3% – the greatest reduction on record, according to the International Energy Agency (IEA). Although there has been less demand due to the COVID-19 pandemic, the increased use of renewable sources was the driving factor behind the drop in emissions.1
Renewables supplied 29% of global electricity in 2020 while increasing their contribution to emission reduction in the power sector by 50%, according to the IEA. Across Europe, renewables exceeded fossil fuels as the main power source for the first time in 2020, reported Euractiv.
This transformation is mirrored by the advances in wind power over the last 12 months. Despite the global pandemic, 2020 was a record-breaking year for the wind industry as it saw the installation of 93 GW of new capacity – a 53% y/y increase on 2019, reported the Global Wind Energy Council. Wood Mackenzie explained how this growth was largely driven by the US and China, which accounted for close to three-quarters of new installations.
This means there is now 743 GW of wind power capacity globally.2 In real terms, wind power is helping to avoid over 1.1 billion t of CO2 emissions around the world, which is equal to the annual carbon emissions across the whole of South America.
As new turbines are installed, and older models repowered, those working within the sector are faced with the daunting task of maintaining and optimising this record capacity. And this sits alongside the priority of ensuring that wind power continues to be as sustainable as it is reliable.
The continued growth of offshore wind
Within this boom, offshore wind is making rapid progress. Annual installations are set to quadruple by 2025, meaning 21% of new capacity will be offshore compared to just 6.5% in 2020.2
In fact, by the end of 2020, there was a total of 35 GW of offshore wind across the world, which is 14 times higher than just 10 years ago.3 This remarkable pace is only set to accelerate further as countries and companies alike search for a wider pool of renewable energy projects.
Interestingly, when this optimistic projection of offshore wind’s future is broken down into greater detail, it becomes clear that the sector is extremely diverse. For example, DNV – an independent assurance and risk management provider – suggests in its 2021 Energy Transition Outlook that, by 2050, 9% of global hydrogen produced for energy purposes will come from fixed offshore wind farms.
Alongside this, there is floating offshore wind. Though dependent on more complex infrastructure than its fixed counterparts, including everything from dynamic electric inter-array cables to single point anchorage (SPAR) buoys, floating offshore turbines have a huge potential upside. This is because approximately 80% of the world’s offshore wind resources are located in waters deeper than 50 m – waters that only floating offshore wind can reliably access.4
However, this growth outlook underlines a wider issue. With an increase in demand for wind turbines comes a rise in the need for the operations that manage the end-to-end lifecycle of a facility, including installation, maintenance, and decommissioning.
Achieving these efficiently is vital when one considers that logistics alone can account for up to 17% of the annual operational budget for offshore wind farms, while maintenance and servicing costs can reach 19%.5,6 But this cannot happen at the expense of the local environments these facilities operate in, especially when it comes to managing the impact that fossil-fuel-based lubricant products can have on ecosystems should a leakage occur.
Operators face two critical challenges in this area: improving the impact of their marine installation and maintenance operations while working to create a sustainable supply chain for the maintenance of internal turbine components.
Challenge 1: Navigating rough regulatory seas for installation and maintenance
Figure 1. Biodegradable lubricants by Shell Naturelle. Around offshore facilities, much of the focus tends to be on the turbines themselves: how many there are and how much power they can generate. However, it is also important for operators to have a clear grasp on the full lifecycle of their new and existing wind farms.
Within this, the installation, external maintenance, and – where needed – decommissioning of facilities are key elements. Each of these require the extensive use of heavyduty marine equipment, from the vessels themselves to the cranes that carry out the actual installation of large and complex components.
Building and maintaining offshore wind facilities at scale is a significant challenge, even with the ideal weather conditions in place. It requires specialised vessels and machinery that regularly comes into contact with the sea water. This is why marine operations are heavily regulated, making the protection of local ecosystems a high priority for operators working to create new wind capacity or maintain the output of existing facilities. For example, the Vessel General Permit (VGP) requires vessels longer than 79 ft that travel through US waters to
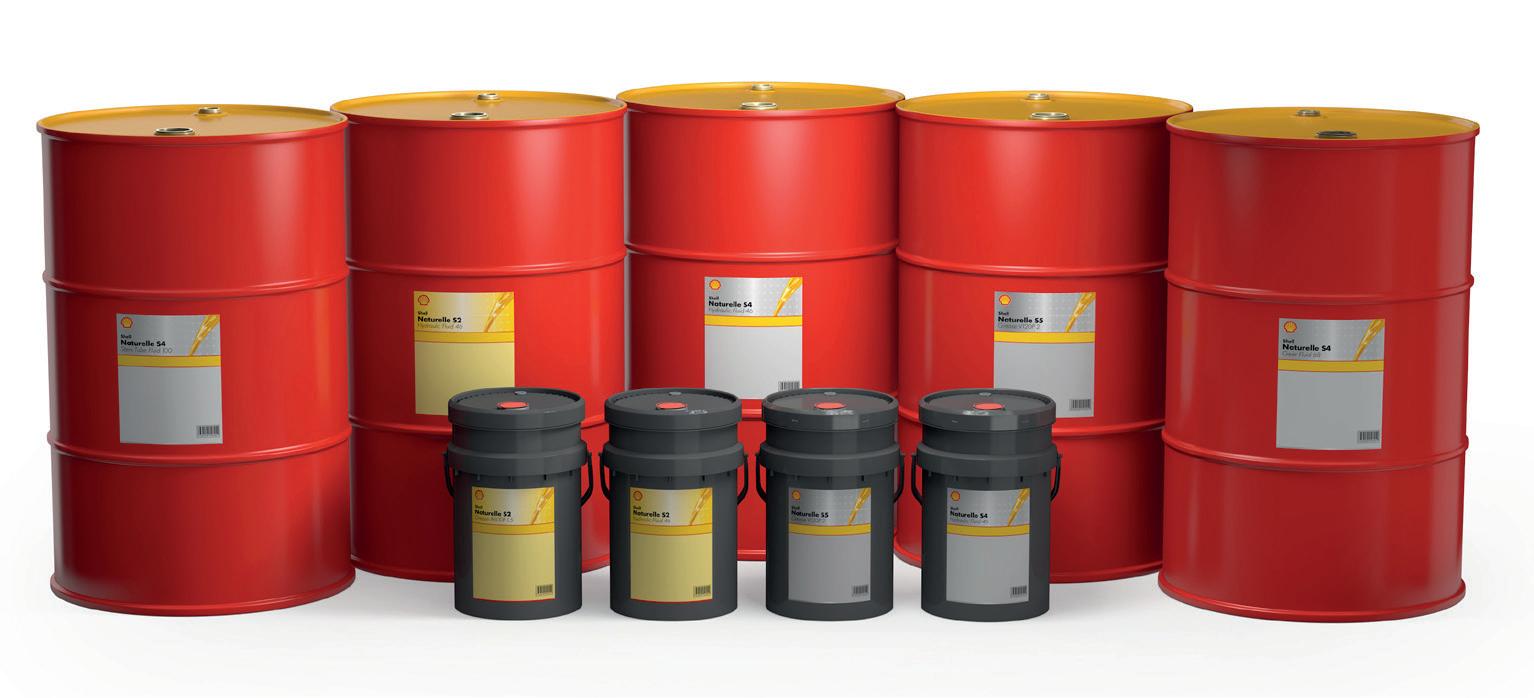
use lubricants that are biodegradable while having low ecotoxicity and no bioaccumulation in their oil-to-water interfaces.
Many other regulations globally have their own criteria for the standards that operators must work to when installing, maintaining, or decommissioning an offshore wind farm. The complexity of this is why many countries and regions have ecolabels in place (such as the EU’s Ecolabel and Japan’s Eco Mark) to guarantee that lubricants with those labels meet the specific standards in each regulatory jurisdiction.
Ultimately, operators need to demonstrate that they can protect the sensitive ecosystems that exist around their installations. Providing net zero emissions energy is a critical target to hit but, if it is achieved at the expense of the local environment, companies will suffer significant reputational damage and risk harming their license to operate.
Challenge 2: More turbines mean more internal maintenance
Once a wind farm is in place, operators need to be sure that it is running as smoothly as possible. They are under pressure to provide efficient and reliable power – with little room for error as demand increases. And this makes the maintenance of the components inside each turbine a critical element in avoiding downtime and maximising power generation.
To put this challenge into context, Wood Mackenize reports how 2019 saw global onshore wind operations and maintenance (O&M) costs reach nearly US$15 billion, more than half of which (US$8.5 billion) was spent on unplanned repairs and correctives caused by component failure.
Of these component failures, it is generally estimated that 1200 each year are related to gearbox failures – a costly problem to fix when the gearbox accounts for roughly 13% of the overall cost of the turbine itself.7
Fortunately, this is where the right lubrication can help. When faced with access issues and equipment strain that are part and parcel of wind turbine maintenance, operators cannot afford to deploy an ineffective lubricant that may lead to unplanned downtime.
Alternatively, an effective lubricant can: extend oil and grease life; prolong equipment lifetime; and improve system efficiency and energy yields. In turn, these benefits can contribute to increased uptime and optimal turbine performance. And, as the size, power, and capacity factor of turbines increases, the role of lubrication becomes magnified.
Most often the lubricants used in wind turbines today are fossil-fuel based and in use for at least 10 years, if not for the lifetime of a turbine. Although the risk of leaks in this area are low, there is a solution available to help OEMs and operators further mitigate risks to their license to operate and improve the sustainability of their supply chains.
How environmentally acceptable lubricants can support performance and sustainability targets
Biodegradable lubricants offer an effective way for operators to ensure compliance with environmental regulations and standards and meet their sustainability targets, whether onshore or offshore. To be certified as an environmentally acceptable lubricant (EAL), products must comply with strict environmental criteria and meet minimum technical performance standards. These requirements are set out by key regulation and approvals bodies within each respective region.
In line with this, Shell Naturelle products are readily biodegradable (in accordance with OECD 301 B, >60% degraded by the end of the 28-day test) while featuring low aquatic ecotoxicity (meeting the requirements of OECD common acute toxicity tests for assessing EALs according to US Environmental Protection Agency requirements) and no bioaccumulation, thereby reducing the impact should an accidental leak or spillage occur – avoiding harm to wildlife and ecosystems (compared to conventional mineral oils).
How it is made can also have an effect on the sustainability of the EAL itself. For instance, the use of solar power in the Shell Naturelle production process in Bern, Switzerland, where 90 MWh of electricity is generated from solar energy, representing 19% of the plant’s total electricity use and avoiding an estimated 0.004 ktpy of GHG emissions (2019 data) – lowers the carbon intensity of its manufacture.8
Additionally, the combination of reductions in plastic waste and use of carbon-neutral products enables operators to further reduce their environmental impact. In participating locations, carbon neutral indicates that Shell has engaged in a transaction where an amount of CO
2 equivalent to the CO2e amount associated with the raw material extraction, transport, production, distribution, use, and end-of-life of the product has been avoided as emissions through the protection of natural ecosystems or removed from the atmosphere through a nature-based process. CO2e refers to carbon dioxide, methane, and nitrogen oxides.
As operators experience a growing pressure to deliver more, while contributing to a more sustainable future, EALs can help them to strengthen their license to operate and reach the ambitious net zero targets that the industry is racing to achieve.
Making the switch to EAL usage can help a business adapt to this rapidly changing industry landscape, by meeting changing standards and regulations confidently without needing to compromise on performance – an outcome that will become increasingly important if global projections for wind power growth continue to be met.
References
1. World Economic Forum, ‘These 3 charts show what COVID-19 has done to global energy demand’, August 2020. 2. Global Wind Energy Council, ‘Global Wind Report 2021’, March 2021. 3. Global Wind Energy Council, ‘Global Offshore Wind Report 2021’, September 2021. 4. ETIPWind, ‘Floating offshore wind: delivering climate neutrality’, 2020. 5. MDPI, ‘The Role of Logistics in Practical Levelized Cost of Energy Reduction Implementation and Government Sponsored Cost Reduction Studies: Day and Night in Offshore Wind Operations and Maintenance Logistics’, April 2017. 6. Catapult Offshore Renewable Energy, ‘Wind farm costs’, 2019. 7. FireTrace International, ‘Top three types of wind turbine failure‘, May 2020. 8. Shell, ‘Shell uses solar energy to help power lubricant plants in Europe and Asia’, August 2019.